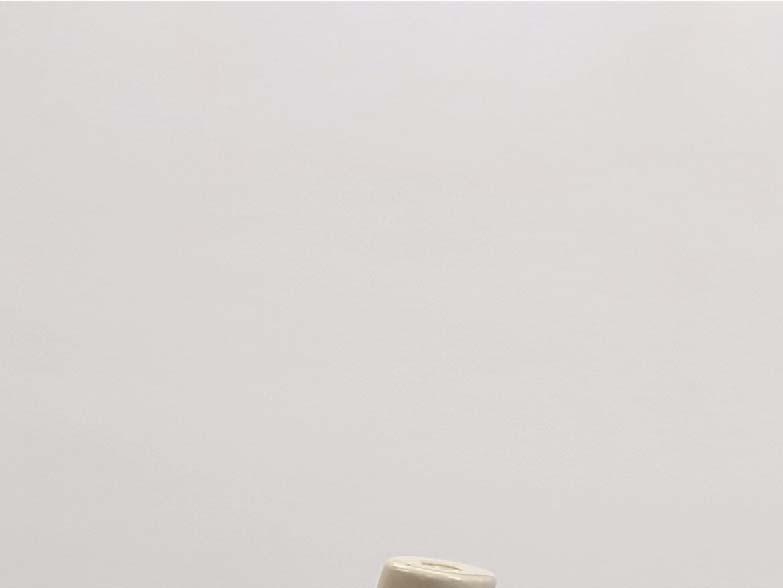
8 minute read
A Strong, Healthy Barrel
A STRONG,
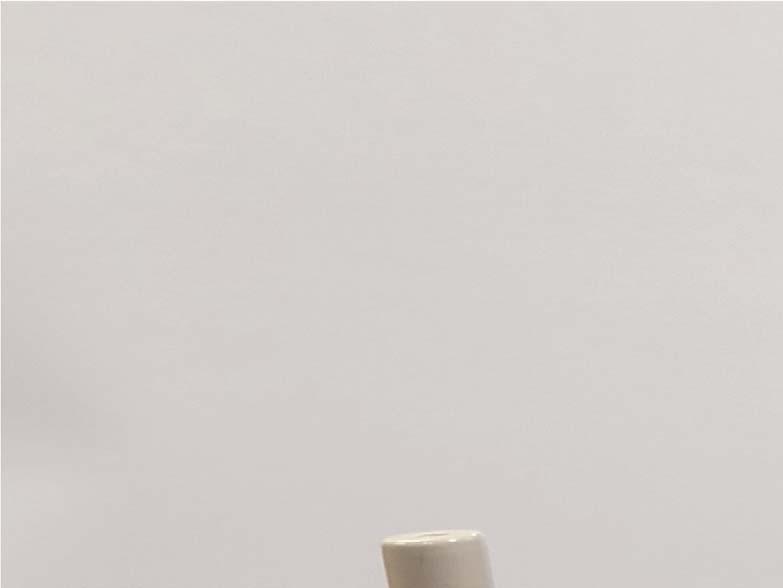
HEALTHY BARREL
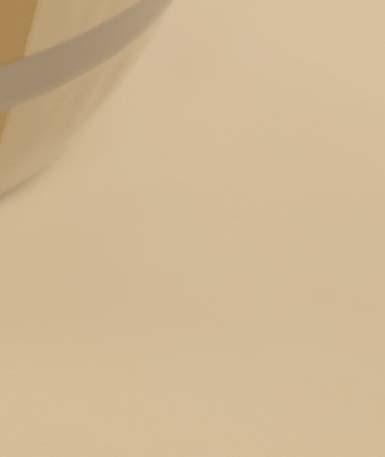
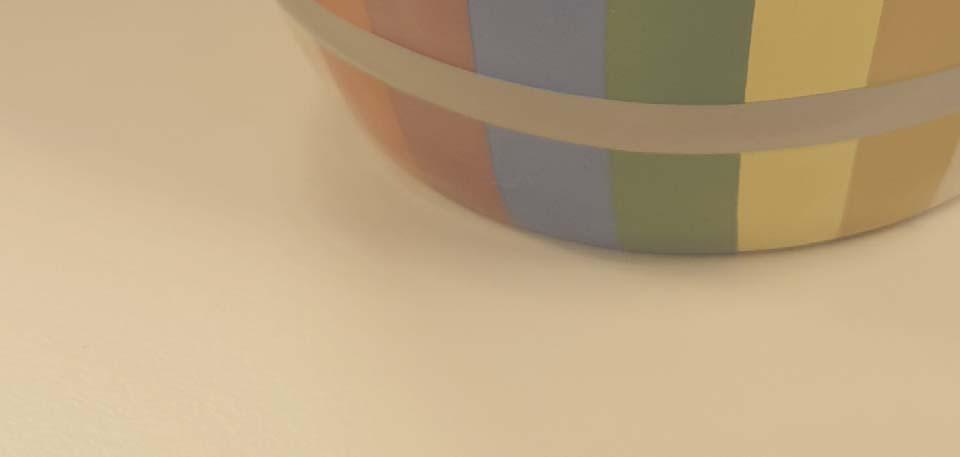

Zico Zeeman, EMT,
the Netherlands, explores how the fertilizer industry can follow the lessons of Liebig’s Barrel and achieve added value and reduction in handling through the use of blending and bagging lines.
The constantly increasing demand for food and changing environmental requirements from companies and governments worldwide has led to an increase in the demand for specialised fertilizers. Who in the industry has not heard of Liebig’s Barrel depicting the Law of Minimum, which perfectly demonstrates the need for soil and crop-specifi c fertilization?
But how can the industry achieve this goal of tailor-made fertilization while still benefi ting from scale economics and the low prices of standard fertilizers or compound fertilizers?
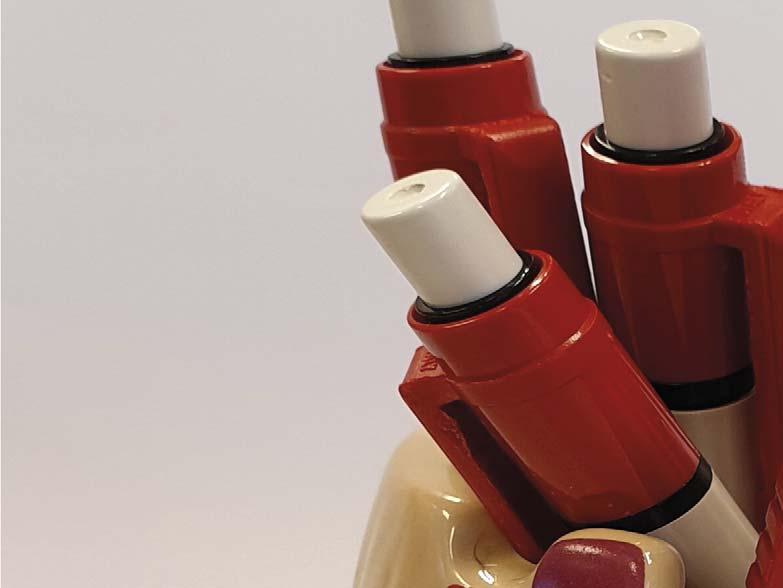


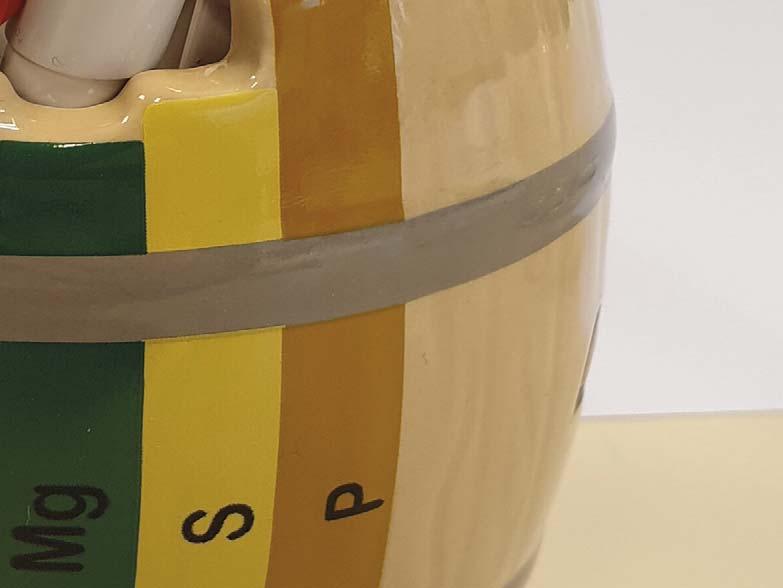
The answer is target market specifi c blending. This entails using globally available raw materials and blending these close to the target market, where knowledge of the soil, crop types and other area-specifi c requirements are known and can be tackled through the use of the correct raw materials.
The key to local blending is adding value for customers by supplying exactly the fertilizers needed to keep their barrel strong and healthy and avoid spillage of their precious yield.
Worldwide, the industry has seen a shift from compound or single fertilizers to blended fertilizers. This is shown in the large number of new blending facilities opening up around the world. It is important, therefore, to be aware of the different types of blenders available, as well as knowing what are the key choices to make when looking to invest in blending equipment.
Thorough understanding of the market’s needs and wants is important, as this may defi ne the rough requirements of a blending plant. What type of blends will need to be made?
What are the soil properties and plant requirements of the target market? Will micronutrients such as boron or zinc need to be added to the blends? The required capacities the blending plant needs to run at also need to be considered: knowing the capacities per year is important, as is knowing what are the minimum daily requirements in the peak season. Looking at future expansion can also help determine which specifi c type of machine to purchase. There are various types of blenders, but they can be separated into two specifi c groups: batch blenders and continuous blenders. Batch blenders consist of the types of blender that work in batches normally varying from 2 to 16 t per batch. Each batch blender works in cycles, starting with a fi lling moment, following a blending moment and then discharging. Capacity normally ranges between 20 and 70 tph.
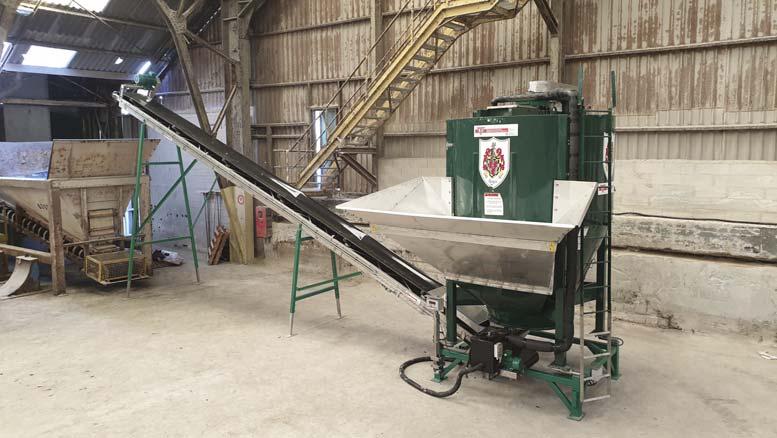
Figure 1. Vertical blender with conveyor.
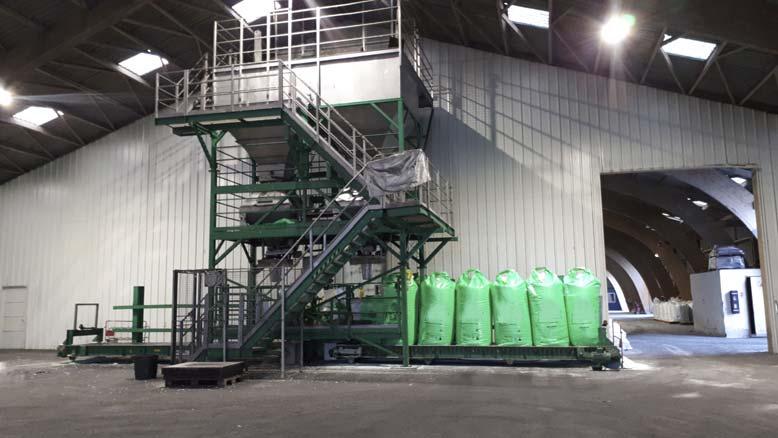
Figure 2. Big bag twin filling line.

Figure 3. Twin drum blending system.
Vertical blender
The blending principle of this blender is based upon a conical screw inside the container that blends raw materials in a wave motion, while always ensuring an accurate weighing of the product by never suspending any product. The bottom cone of the blender has a 60˚ angle to eliminate product build-up inside the container. A salem valve on the bottom of the blender, coupled with a sweep on the bottom of the auger, ensures complete clean-out of the blender. The machine can reach a capacity of 60 t/m3 per hour. The complete system is mounted on a digital weighing system.
Horizontal rotating blender
Various branches of the industry have these blenders in operation. The blending process is simple: the turning drum has internal fl ighting that blends the different raw materials in a folding action. The blend has good homogeneity, with little or no degradation or segregation.
The blending capacity varies from 2 t with a blending capacity of 2 m3 to 10 t with a capacity of 10 m3. The weigh hopper has the same capacity as the blender and is mounted on a digital weighing system. The weighing and blending process are separated in this type of blender.
Paddle blender
Different types of paddle batch blenders can be installed. Paddle blenders are well suited for blending granules but also for blending powdery material such as water-soluble fertilizers. The twin shaft high-speed paddle mixer is ideal for this type of material. Both shafts run in opposite directions at high speeds and can mix the powdery material with ease. These types of blender usually reach 1 to 4 t per batch.
Continuous blenders, on the other hand, work continuously and can be fi lled and discharged at the same time. The material is blended by a blending screw and capacities can go up to 250 tph.
The computer commands and controls the entire, continuously operating weighing and blending process by means of a variable electro system. This guarantees an optimum quality.
The system works as follows: the operator fi lls the hoppers with raw materials through a wheel loader or forklift with bucket. Each hopper is mounted on a digital weighing system; the stainless steel dosing conveyors, in combination with the digital weighing systems, ensure the proper dosing of raw materials. This system has a blending capacity of 20 – 250 t/m3 per hour, and the number of hoppers is unlimited. The complete blender is made of stainless steel with a hopper capacity of 4 – 15 t/m3 .
Adding micronutrients, inhibitors or additives
Both types of blenders can be used to add micronutrients, inhibitors or additives to the blend. It is important to know which types of products will be needed to add to the blend to make the product more valuable for customers. Depending on this, it may be worth considering installing a powder adding unit or a liquid adding unit in the blender.
Bagging
The stainless steel big bag fi lling unit is designed to fi ll FIBC bags with a range of 250 to 1500 kg. Possible height and capacity are important factors when choosing the type of bagging unit. Weighing above the bag requires more height but can reach higher capacities of 70 bags of 1000 kg per hour or 120 bags per hour of 500 kg per bag per line.
Weighing the product in the bag requires a lower height but also decreases the fi lling speed: 40 bags of 1000 kg and approximately 70 bags of 500 kg per hour.
The small bag fi lling unit can process a maximum of 1000 – 1100 bags of 25 – 50 kg per bag per hour. These rates are achieved by using a double bagging unit. The single bagging unit has a capacity of 500 – 550 bags per hour. Both machines can be equipped with either an open mouth or ventil bag fi lling system. A combination of these systems is also available.
Intermediate handling
After blending the material (or sometimes before) it might prove helpful to condition the fertilizers, depending on the quality of the raw material provided. Screening can be a good option to eliminate dust or large foreign particles from the product to ensure a good fi nal homogeneous blend. Another option is to add fertilizer conditioners, such as lump breakers, into the machinery. This can be done for one specifi c type (for example urea) or for the complete mix.
After the material is blended it is customary to transport it directly to the bagging units. In a set-up such as this, handling of the material is minimised. Different bagging units can be installed behind one blending unit; again, this greatly depends on the required output. Two types of bagging units can be distinguished: big bag fi lling units and small bag fi lling units.
Case study: Belgium
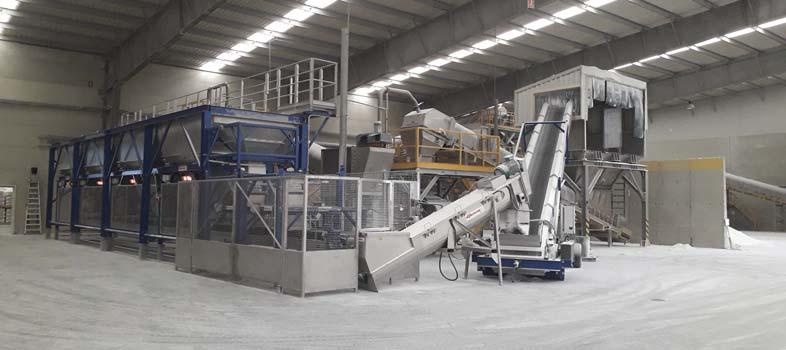
Figure 4. Blender with five hoppers.
Figure 5. Blender line at De Bruycker, Belgium. A completely new blending, bagging and handling unit was recently installed at De Bruycker NV in Blankenberge, Belgium.
The fi rst machine in the line is the continuous Weighcont blender. With four large hopper and two medium hoppers the Weighcont can mix six different granular materials in one blend.
In this set-up it is possible to run the material through the double layered screening unit, which takes out both the large particles as well as the dust, ensuring the high quality of the product. Depending on the quality of the raw materials, De Bruycker has the ability to decide to bypass the screening unit. From the screening unit or from the bypass conveyor the material enters the blending screw, where the raw materials can be coated. A weighing liquid adding unit ensures that the liquid that is used on the granular material gives exactly the correct amount per produced tonne; the blending screw distributes it evenly over the granules. The blended material is transported upwards on a conveyor belt. At the end of the conveyor belt a 2-way valve directs the material to either the bagging unit or to a bulk truck. The entire system was installed in 2020 and can reach a capacity of 120 tph in bulk and 70 tph in bags. The system is run entirely from a PC in the control offi ce, which is directly connected to the machine PLC. All blends produced are stored in the machine’s history, giving De Bruycker the possibility to retrace and store all its production reports. This completely automated system continuously adjusts the speed of the dosing to the required recipe, giving it the desired blend for each recipe.
Conclusion
The benefi ts of locally blending the exact recipes tailored to customer requirements are not only proven in theory but also in reality. Choosing the correct equipment is vital to the success of an operation.
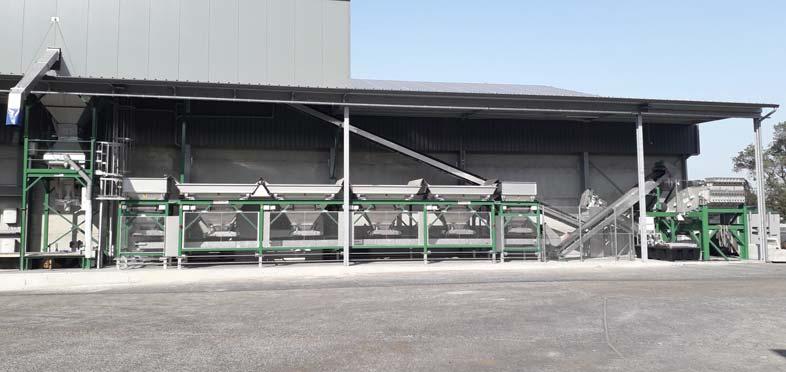