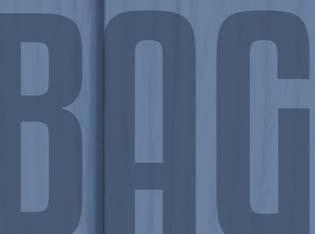
5 minute read
It’s In The Bag


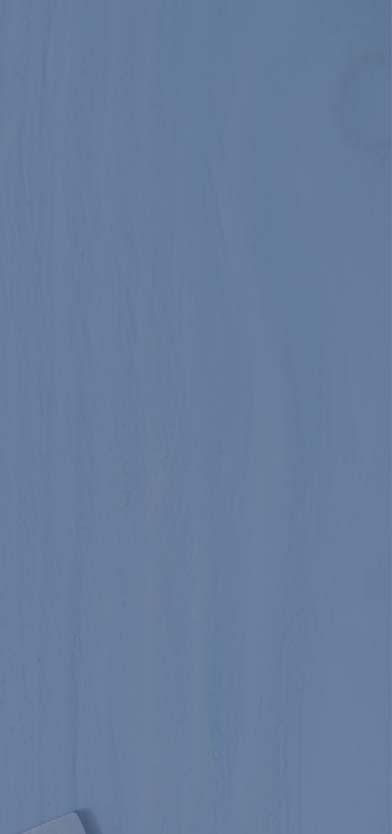

Stefanie Reifbäck, STATEC BINDER, Austria,
explains how to ensure the longevity of a fully automatic bagging machine.
The purchase of a fully automatic bagging machine involves quite a large investment. First of all, it is important to choose a strong and reliable partner with the right machine for the desired application. In addition, it is even more important to know what needs to be done to ensure that the machine is reliable and works as it should. These are basic tasks that can make a big difference. This article will explain the fundamentals of ensuring the longevity of a fully automatic bagging machine.
It is especially important in the fertilizer industry that bagging machines are designed to ensure that they remain working for a long time. Due to the corrosive nature of fertilizer, the use of stainless steel for the housing and main parts of the machine, as well as increased corrosion protection, is essential.
Over the years, machines have been continuously optimised to ensure a long service life even when packaging corrosive products. Aside from ensuring the high quality of the machines, there are several other important factors that work towards guaranteeing longevity of service for bagging machines.
Several steps are taken to ensure that machines are well-designed for the handling of corrosive products. For example, for components of the packaging system that come into contact with the product being packaged, special plastics are used instead of metals because they do not corrode.
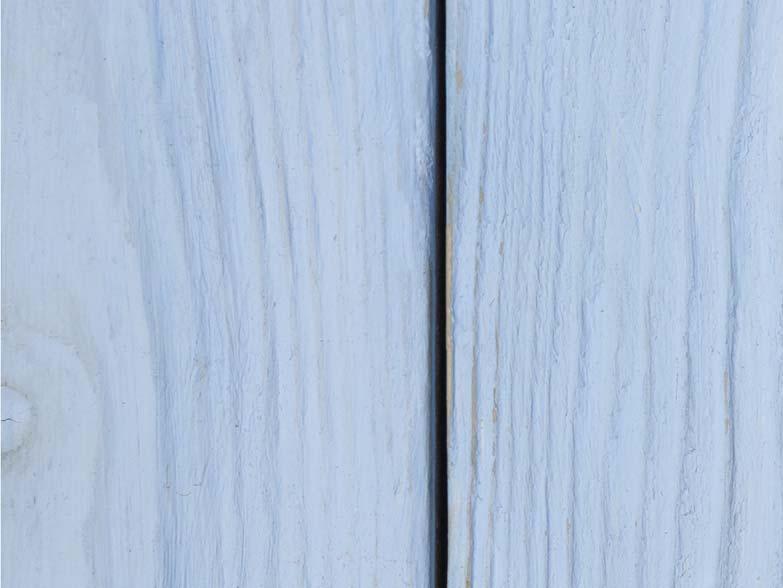
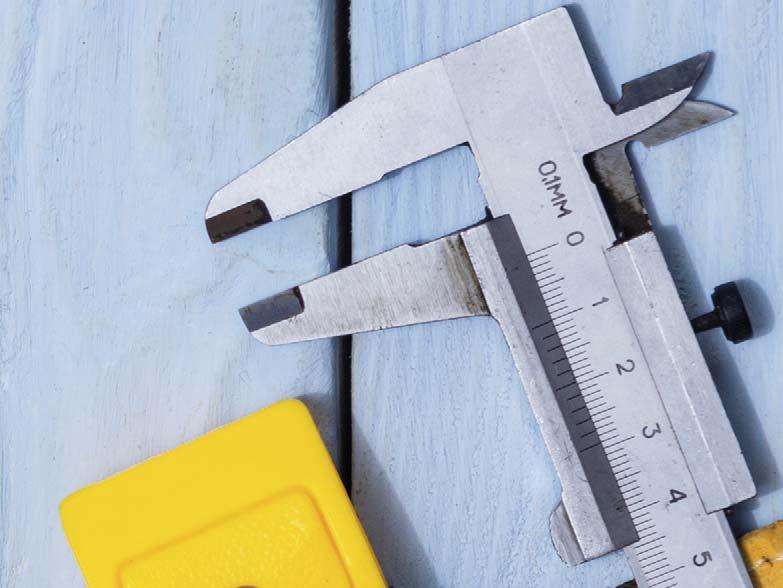
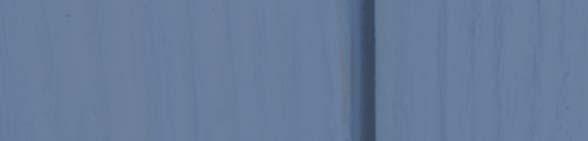



Furthermore, special measures are taken to reduce dust emissions in the product fl ow and to adapt the machines to the operating environment, such as high humidity, so that hygroscopic products do not become sticky and are always free fl owing.
When planning the plant layout, the customer should keep in mind the future location of the machine, as humidity can be drastically concentrated if the machine is located in an air-permeable building. Depending on the specifi c circumstances, heating or dehumidifi cation should take place to adjust the machine’s environment to the optimal temperature and humidity, as these measures also affect the longevity of the machine. Although machines can operate in less than optimal environments, they will run better and more reliably if this advice is followed. Moreover, the longevity of the machine will be increased.
Besides ensuring a high quality of the packaging machine and the correct location of the machine within the plant, the customer must also ensure the proper maintenance and servicing of the machines. The regular cleaning of a machine and its single components is of enormous importance. Problems most frequently occur because product residues accumulate or pile up in the plant due to inadequate cleaning measures. Sticky and dusty products adhere particularly easily to machine components such as bearings, joints or pneumatic cylinders. As a result, the packaging machine ceases to run as desired, which in turn can lead to problems with the specifi ed sequence, cylinder speeds and other movements. Another negative consequence would be an additional loss of performance.
STATEC BINDER recommends that customers undertake a short cleaning of the packaging machines once per shift with dry compressed air. Regular cleaning only takes a few minutes and ultimately avoids major problems that could arise from equipment contamination. The main focus should be on the fi lling area of the machine – in other words, practically everywhere where the product is exposed and the material comes into contact with the equipment.
While cleaning is a basic measure, stocking certain spare parts on-site is another important prerequisite for successful machine maintenance. The company provides its customers with a checklist of ‘mandatory spare parts’ when the machine is delivered. Certain components should always be at hand. Similar to the tyres of a car, some machine parts wear out much faster than others, and must therefore be replaced at regular intervals to maintain performance.
In addition, the customer is provided with maintenance schedules tailored to the specifi c machine and the product to be bagged that need to be observed and adhered to. Training is also offered for the operating and maintenance personnel of the system. Existing knowledge about optimal maintenance measures on the respective machine can then be passed on to new colleagues or team members by trained employees.
If there is a planned stop of the bagging machine due to a holiday, end of season or for servicing the machine, cleaning is even more important, as hygroscopic products tend to become sticky and lumpy over time, which can lead to product build-up. This could affect the performance of the machine when starting it up again after a long period of time, or even cause an unplanned stop. For this reason, thorough cleaning is absolutely necessary after stopping the machine. Before restarting the machine, it is also highly advisable to check for any product build-up, and to inspect the moving parts. This enables a smooth start-up process and reliable operation of the bagging machine.
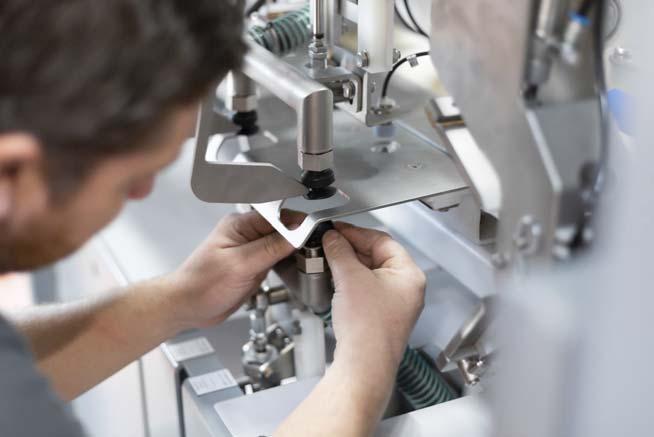
Figure 1. Regular cleaning and inspection of suction cups.
Figure 2. Easy cleaning with the already installed compressed air pistol.
Figure 3. Inspection of the bag separation parts.
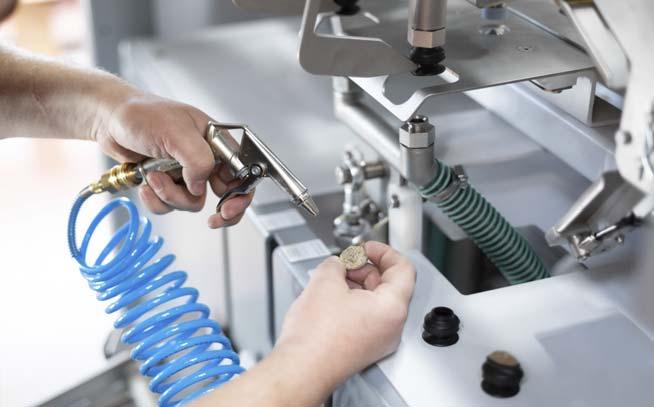
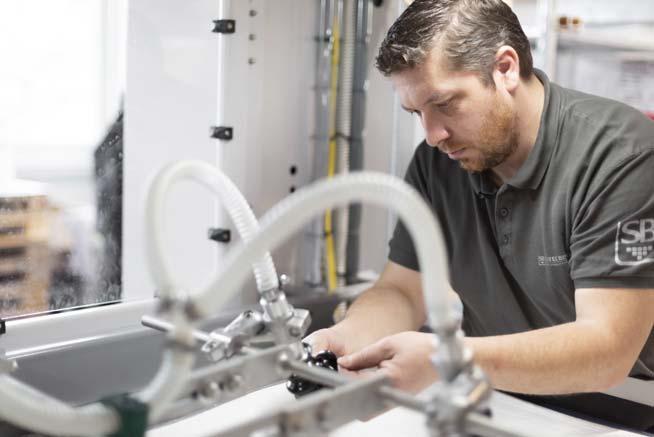
Conclusion
In summary, regular cleaning must be considered essential to the smooth operation of bagging machines, with measures adapted to both the specifi c product environment and the bagging or palletising system in question. In addition, basic maintenance is also of great importance. If machine operators listen to the machines in order to notice any strange noises, the problem can be quickly rectifi ed and damages can be avoided. Annual maintenance – which is always tailored to the particular machine, the product to be fi lled and the customer – ensures that the machine’s reliability and performance are maintained. The goal is to achieve a consistently smooth-running machine.