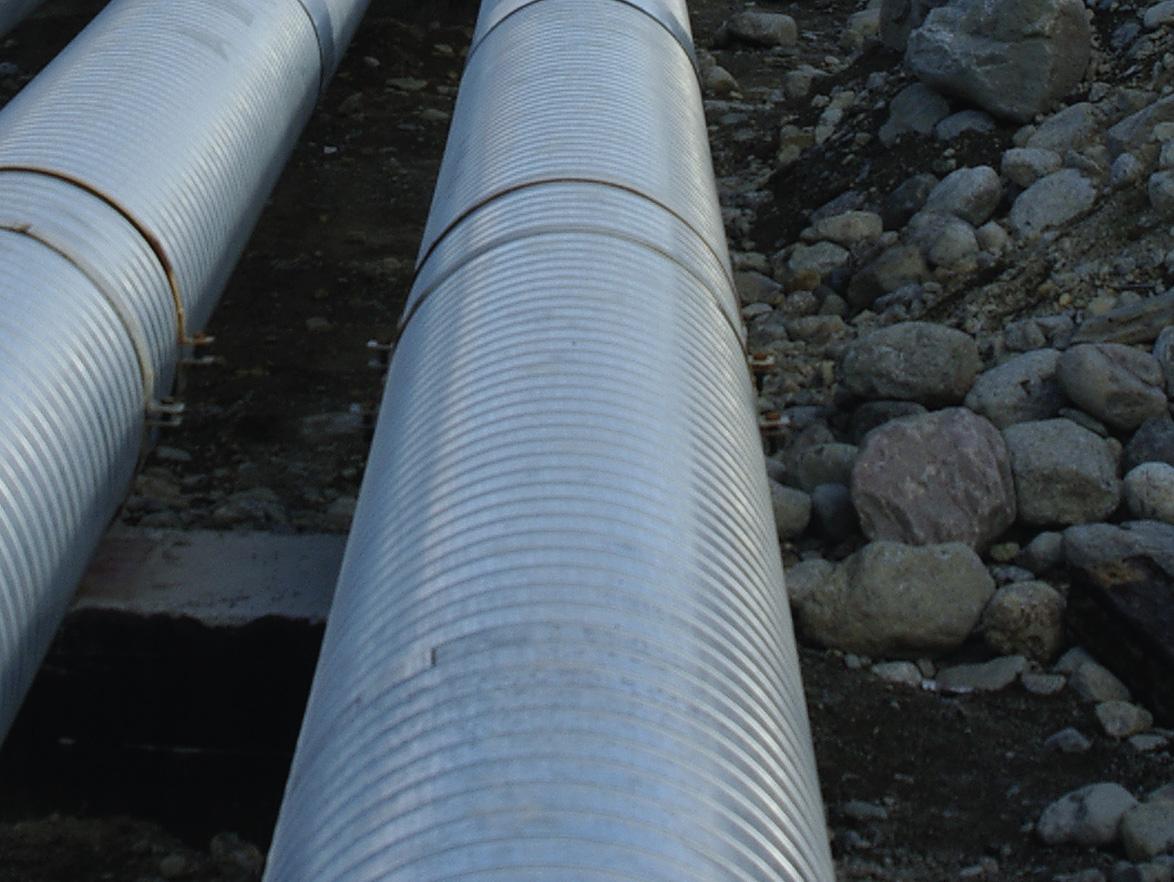
8 minute read
Pipeline isolation for the 21st century
Angus Bowie, Regional Director for the Middle East & Asia Pacific at STATS Group, explains how the pipeline industry has turned a corner when it comes to utilising hot tap isolation.
When STATS first investigated hot tap isolation back in 2005, it was discovered that the existing technology was based on equipment which had not changed since the 1950s and did not meet current standards. There was a single high-pressure lip seal with an acceptable leak-rate, an open vent and a low pressure gas bag to hopefully divert the lip-seal leak to the open vent.
STATS had secured a project in the North Sea which required leak-tight double isolation of 32 × 10 in. pipes within the platform utility shafts. With current technology, this would have required 64 full bore hot taps, 32 reduced bore gas bag hot taps and 96 vent and purge penetrations. Additionally, no existing supplier could be confident in providing a leak-tight seal in the ageing pipework with poor internal conditions and the presence of scale.
At that time STATS was supplying mechanical isolation plugs with dual, full pressure, compression seals with a 98% leak-tight seal record. Where leak-tight seals could not be achieved during installation, our seal monitoring capability identified any leakrate. These leak rates were miniscule and could be vented with a ¼ in. vent hose. However, in most cases simply un-setting and relocating the isolation plug would rectify the issue before retesting the seals and issuing an isolation certificate. The seal barriers are both tested upon installation to the full pipe differential pressure and provide isolation at least equivalent to that of a double block and bleed valve.
STATS utilised the Tecno Plug® sealing technology, with its extensive track record, to develop a hot tap deployed isolation tool capable of providing the safe isolation required to isolate the 32 pipes and minimise the number of hot taps required.
This led STATS to develop the patented BISEP® (Branch Installed Self-Energised Plug) which was deployed through a single
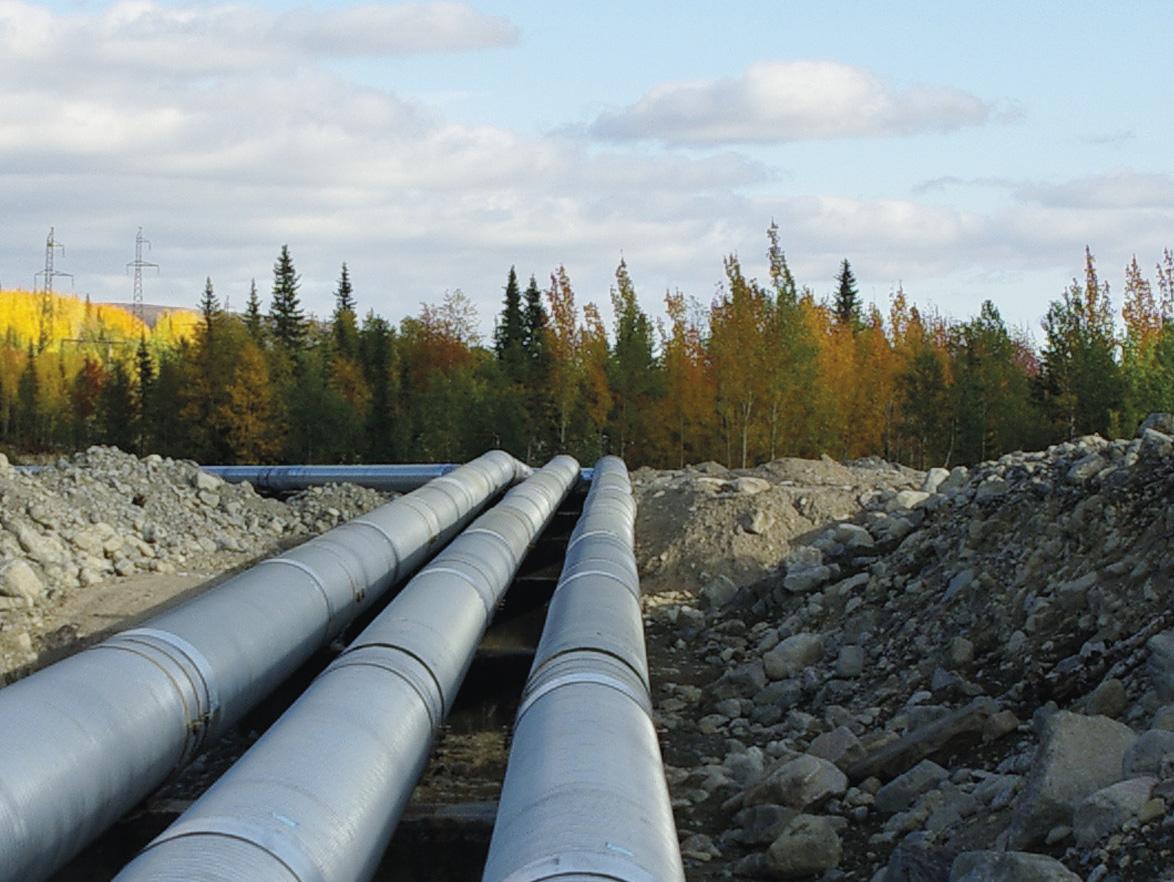
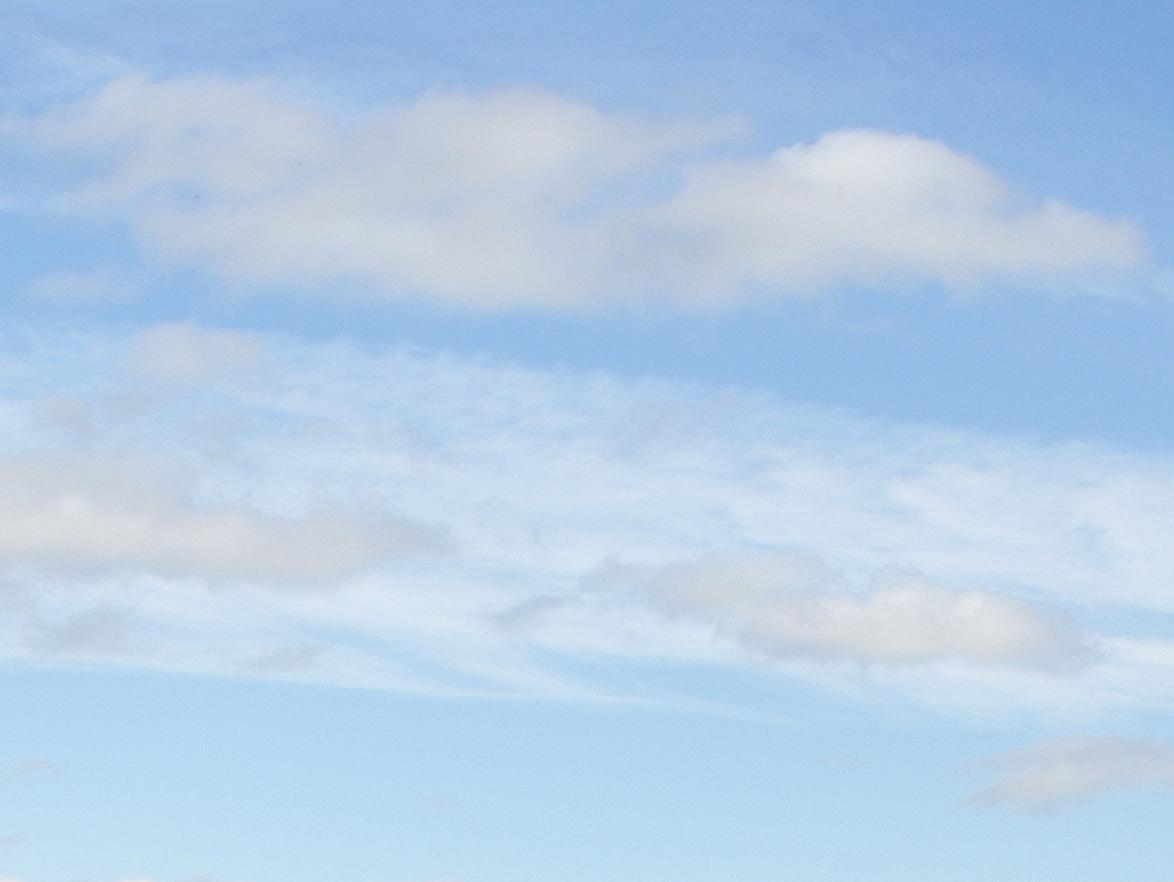


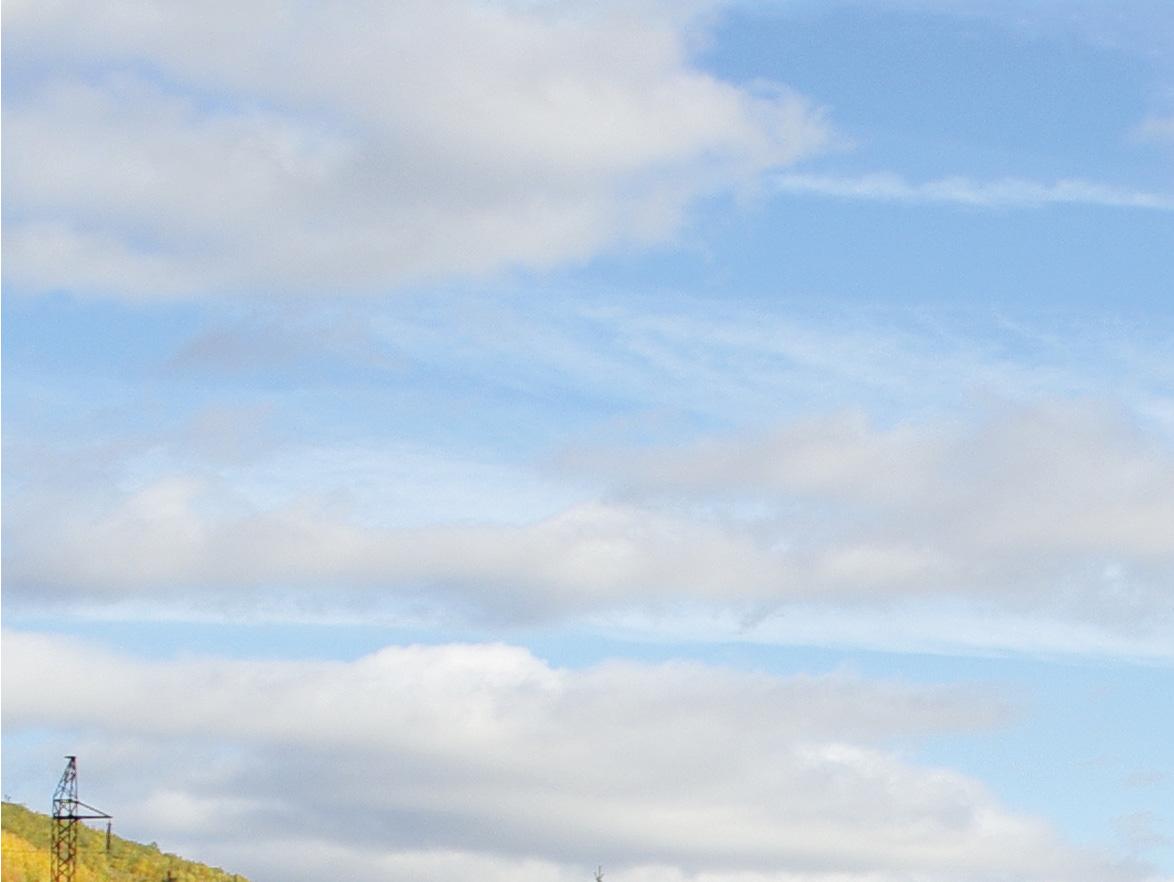
full-bore penetration with dual compression seals. The monitor between the seals is ported through the launcher, so there is no requirement for additional hot tapping. As the seals offer proven leak-tight integrity there is no need for the additional gas bag either.
High integrity hot tapping It took a few years to get the industry to understand that high integrity hot tap isolation was available, with resistance from both competitors and operators. However, now the industry has turned the corner and most operators are expecting and demanding dual full pressure barriers with less penetrations on the pipe. Our leading competitor has even developed its own technology to address this concern, the latest incarnation finally addressing the lip-seal leak rate. However, STATS still remains the market leader in double block and bleed hot tap isolation, with solutions to suit both high and low pressure applications while maintaining high integrity sealing.
The BISEP also allows the isolated pipework to be pressure tested after the workscope is completed, as the seals are bi-directional. The ability to resist back pressure also allows the pressure between the seals to be raised above the pipeline pressure, ensuring the test on the secondary seal is valid. If the void is equal or below the pipeline pressure then there could be a leak past both seals. However as pressure can only leak from high to low, locking-in pressure between the seals to above the pipeline pressure or venting it to ambient with pressure on both sides proves the seal integrity, as any leak would be detected.
The BISEP is Type Approved by DNV GL up to 56 in. and has been deployed all round the world from 3 in. up to 54 in.
Recent developments Recent developments include a dual set configuration, known as the DS BISEP. This tool is deployed on the isolation side of the fitting and comes complete with an integrated bypass to maintain flow while providing high integrity dual barrier isolation through a single hot tap penetration. This configuration also has a contingency hydraulic lock, therefore maintaining 100% redundancy even on a low pressure or ambient system where the seals are not retained by pipeline pressure.
However, the BISEP and DS BISEP both have seals energised by pipeline pressure, providing a fail-safe isolation independent of the hydraulic control circuit. The BISEP also incorporates a hydraulic set for any application where the pipeline pressure drops below the pressure required to maintain leak-tight sealing. The DS BISEPs are often used in a quad configuration, with two BISEPs deployed at either end of a re-route to allow flow to be maintained while a new pipe section is commissioned.
Applications The BISEP has been used for oil, gas, NGL, LNG, CO2, steam and many other compounds, including use at solar plants to isolate Therminol heat transfer fluid. The success of these often challenging projects is to identify a compatible seal material, something STATS has vast experience of and works in partnership with specialist suppliers to select and test the most appropriate material. Although high pressure isolation is not so important for utility companies, we have built a significant track record with them over the years. However, the main demand remains from oil and gas.
The BISEP is a little more complicated than traditional line stop equipment to deploy, as it has an active rotate circuit as well as a hydraulic deployment ram and seal set circuit. This does however allow the BISEP to be deployed at any pipeline incline or orientation, and provides robust rigid operation. It also has pressure monitoring capabilities between the seals which can be used to raise or vent the pressure during seal testing. Although the BISEP could be deployed and left similar to a traditional line stop tool, we can also constantly monitor the isolation and verify the seal integrity. Where a traditional line stop isolation would have a fire marshal sniffing for

Figure 1. BISEP isolating a live 36 in. gas pipeline operating at 65 bar, leak-tight isolation despite significant build-up of oily silt in the line.
Figure 2. 10 in. DS BISEP assembly with integrated bypass. Pig launcher used to de-oil the old line, displacing oil through the second bypass into the new pipeline.
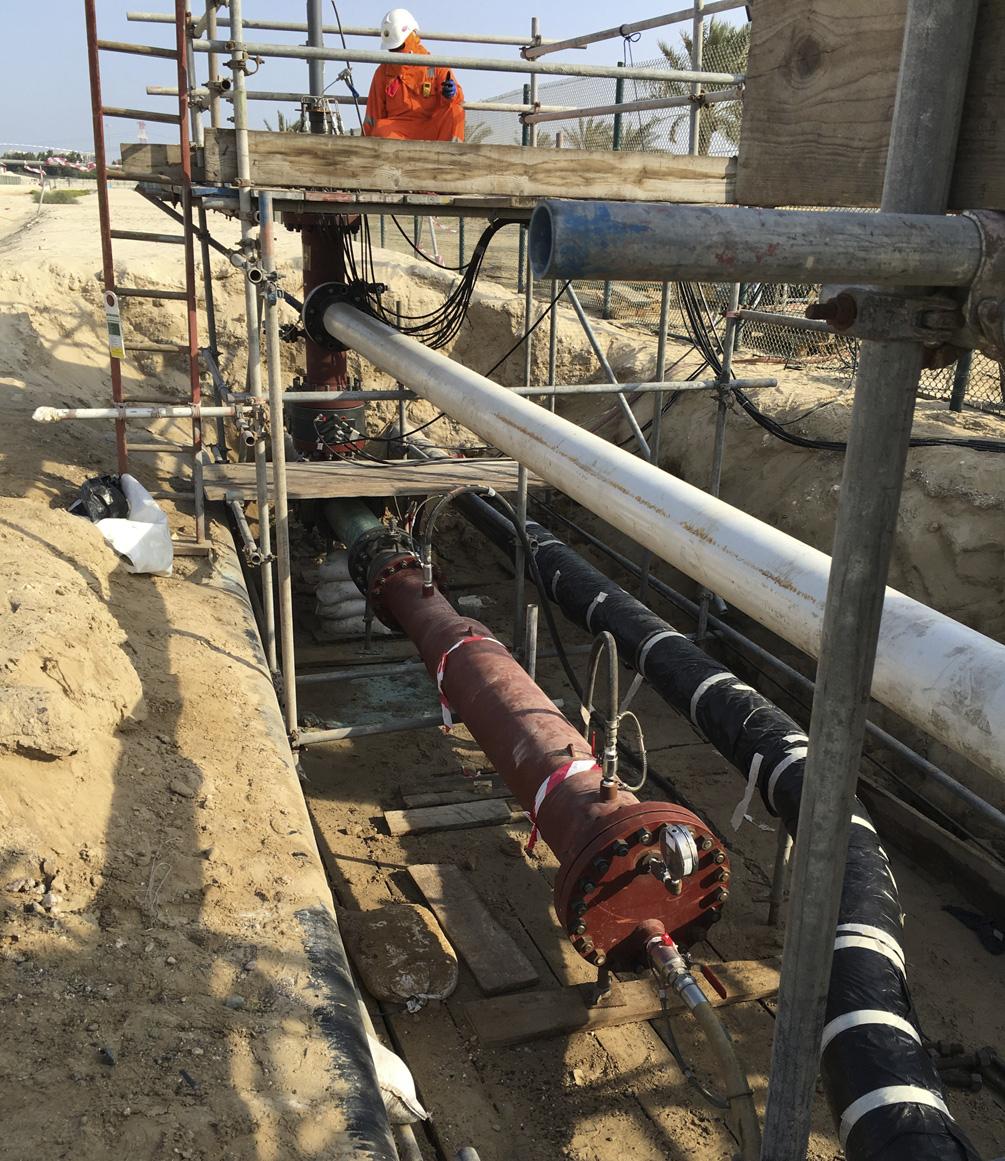
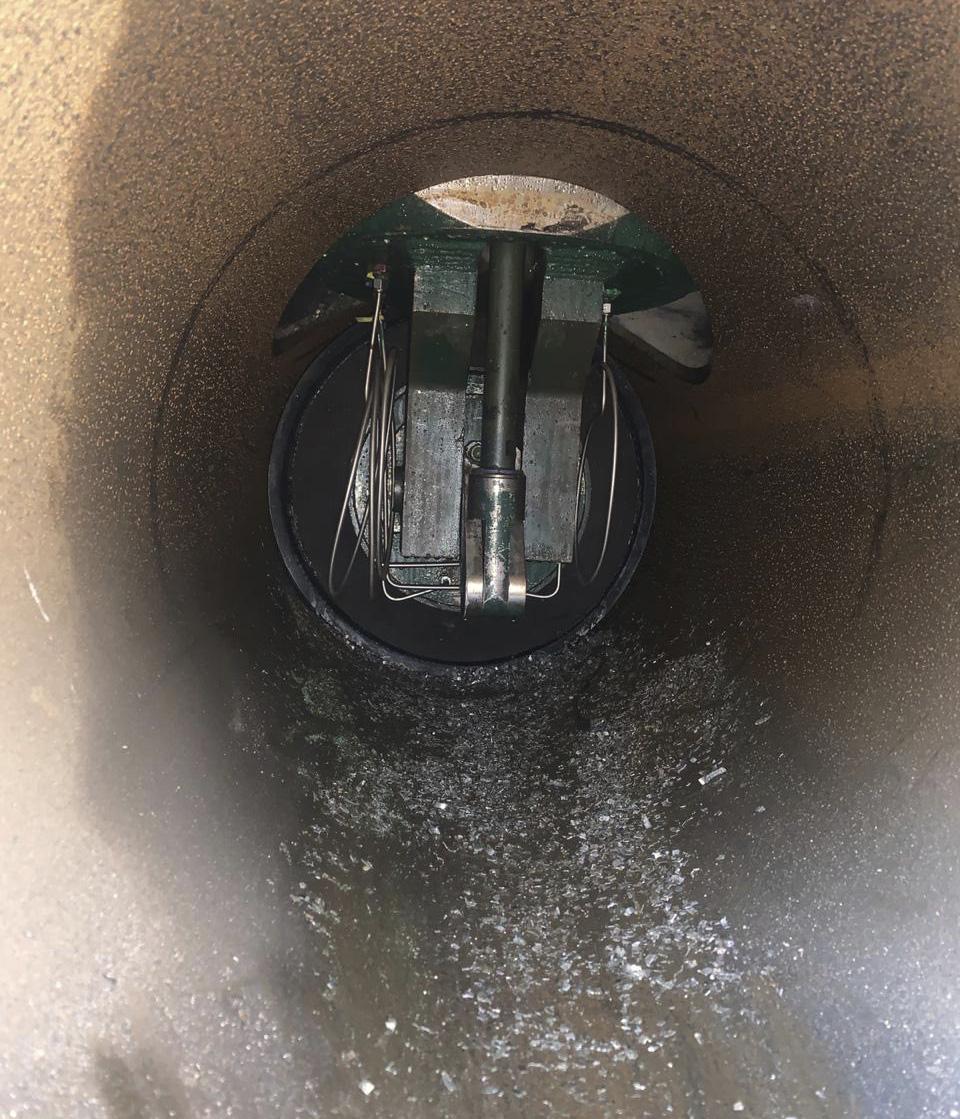
Figure 3. 22 in. BISEP positioned on hot tapping chips and swarf, elastomer seals ensure leak-tight isolation.
Figure 4. 42 in. BISEP isolation of natural gas line for seven months, production maintained through a separate bypass while new pig trap station was installed and commissioned. gas during welding, the BISEP has an ambient void between the seals that is monitored to identify any leak with a second full pressure tested barrier between any potential leak and the worksite. This provides leak-tight seals with a zero-energy zone between them that is monitored for any pressure rise. The BISEP also has the capability to vent any increase in pressure or boost the seal hydraulic set pressure in the unlikely event that a leak was detected.
“Three hydraulic circuits and two monitor lines is not rocket science and can be mastered by any hot tap technician,” is how it is often explained to clients. “At the end of the day it is much safer to identify an issue with a primary barrier when a leak-tight secondary barrier is securely in place.”
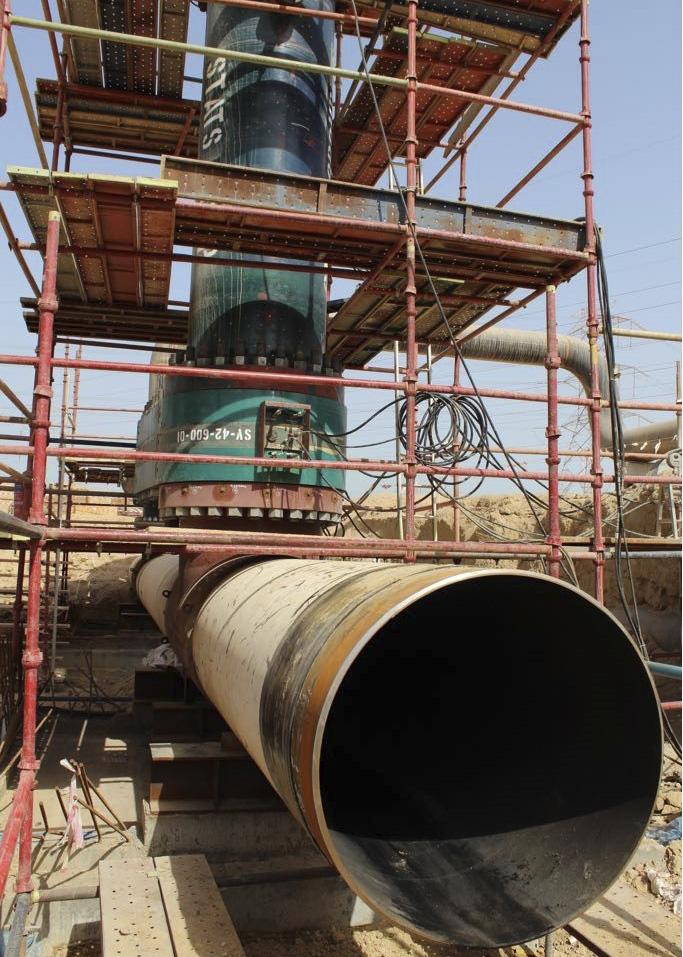
Hot tap clamps Although the BISEP is typically deployed through welded fittings similar to traditional hot tap isolations, STATS can also provide their own mechanical hot tap clamps. Many of these hot tap clamps are for subsea application and feature dual seals and a set of locks, designed to remain on the pipeline as a permanent fixture. However, they can also be used in combination with STATS’ Tecno Plug® (inline mechanical isolation plug) to provide hot tap access to pipes where online welding is not possible or desired. In this application we use a mechanical clamp, hot tap and BISEP to make the initial isolation, then once the pipe is cut, we assemble a temporary launcher and deploy a Tecno Plug past the BISEP. With the Tecno Plug now providing isolation, the hot tap clamp can be removed, and a new pipe welded to the isolated pipe. The one limitation is that we need a valve or receiver to recover the isolation plug once the job is complete. This is a common option in process plants where the client does not want additional fittings or dead legs left in the system.
Conclusion In the past three years, STATS has seen exponential growth in BISEP isolation provision, particularly in the US, Canada and Middle East markets. STATS has regional bases in Houston, Edmonton and Abu Dhabi to support the intervention market, with new facilities planned in Saudi Arabia and Australia. These are in addition to our other operational bases in Aberdeen, Doha, and Kuala Lumpur, which although primarily isolation plug bases also offer hot tap isolation services.
Recently, STATS has seen a sharp increase in a double block and bleed requirement specified in tender documents, further indicating the trend to ensure hot tap isolation meets the current industry standards. STATS actively works with clients and government institutions to improve the safety of our industry, and is continuously developing advanced products for oil and gas infrastructure. Our comprehensive Tecno Plug range is also in high demand, and our piggable inline isolation tools offer the same high integrity dual barrier, monitored isolation. However, piggable isolation tools have the additional benefit of not requiring welding or cutting into live lines, and leave no residual fittings or hardware on the pipeline.
STATS has several new products under development which will be released to the market soon. The company is constantly striving to improve the safety of its industry offering dual, proven barriers and controlled isolation, and replacing existing single seal unmonitored tooling with safer high integrity technology.