
31 minute read
Heavy Equipment Review
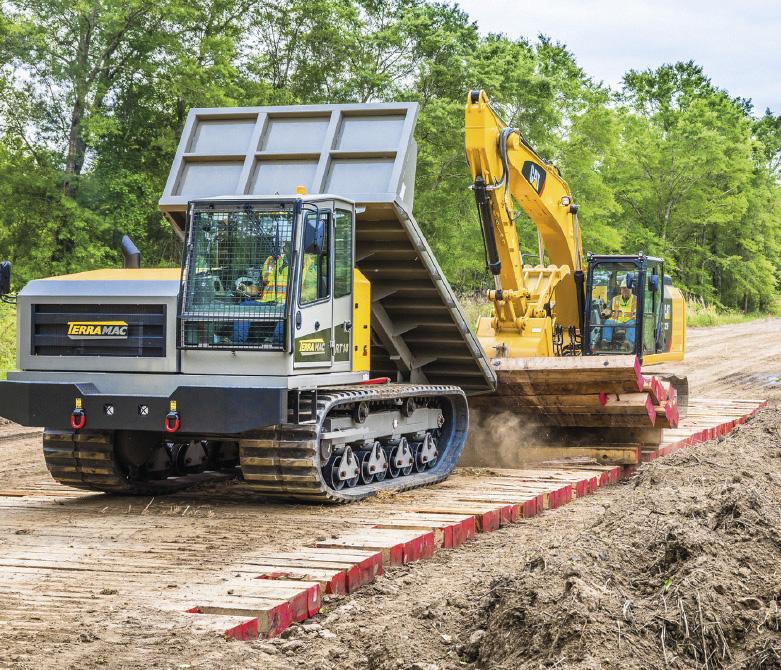
In World Pipelines’ fourth Heavy Equipment Review, 13 companies present a selection of heavy equipment for oil and gas pipeline construction projects. Showcasing pipelayers, land clearing equipment, bending machines, trenchers and more, the companies offer details on the product specifications and capabilities of large scale heavy equipment designed to tackle the biggest of production, site and environmental needs.

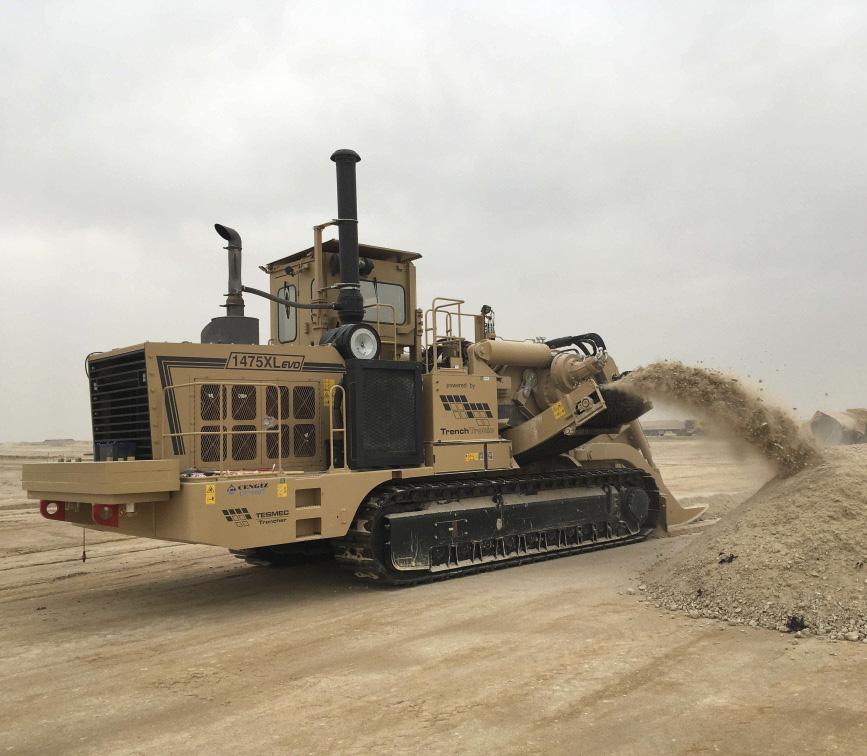
BAUMA, GERMANY
BAUMA Germany has a traditon spanning three generations for trading in construction machinery. BAUMA buys and sells mainly wheel loaders, bulldozers and articulated dump trucks, as well as skid loaders, mobile excavators, industrial and crawler excavators. All machines are from well-known manufacturers such as VOLVO, CAT, Komatsu, Liebherr, Hitachi, Bomag and
Hamm. BAUMA is a regional dealer for Volvo and Hamm compact class machines (up to 10 t) and holds dealerships of several other equipment manufacturers. Presently, the company owns approximately 85 pipelayers and welding tractors for manual and automatic welding. With its fleet of equipment, BAUMA can bridge the temporary need for pipeline equipment for pipeline construction companies worldwide. Last year BAUMA extended its fleet by buying 14 pipelayers, LIEBHERR RL64 with a lifting capacity of 91 t. All units have an arctic package so that they can be deployed in harsh weather conditions. BAUMA strives to enhance its activities overseas by entering into co-operations with either contractors or a representation in for example the USA and Canada. It is clear that by having a local representative office or agent, both the user of the machines and BAUMA benefit. Communication lines are shorter and local repair and maintenance is guaranteed.
BAUMA recently became a dealer of VACUWORX lifting systems for Germany, not only for the pipeline industry to safely handle pipes, but also for concrete industry applications through the Compact Equipment Attachment (CEA) product line which pairs up with the smaller compact host machines such as skid steers, mini-excavators, mini-loaders and smaller cranes BAUMA rents and sells. BAUMA is open to discuss flexible solutions with customers, such as straight sale, rental only, rental with purchase option, or sale with buyback. This flexibility is appreciated by contractors as they are often unsure whether or not they need the machines for future projects. BAUMA tries to maintain the spirit of a family business with limited overhead and follow an attractive approach offering added value. Until now, fortunately, the company maintained more or less its level of turnover during the COVID-19 pandemic as regional construction projects kept on working. Having customers from different sectors is truly a blessing, as the pipeline business is a cyclical business and politically sensitive. The new workshop will be ready in 1Q21, giving full support to both workshop people and the customers who use BAUMA’s equipment. It will include no less than five workshop bays to maintain and repair the equipment when necessary.

BAUMA’s new workshop.
Komatsu D355 lowering in 56 in. pipe at EUGAL.

BRANDT EQUIPMENT SOLUTIONS, CANADA
Since the introduction of their first pipelayer in 2017, Brandt Equipment Solutions has virtually owned the large pipelayer market in Canada. Now, after introducing two mid-sized models in 2020, they are poised to make a significant impact in the small/ mid-diameter pipeline market across the US and Canada. The new models employ Brandt’s innovative low-mount sideboom design, first unveiled with their larger machines and created in co-operation with John Deere engineers. This platform has quickly built a reputation across the industry for exceptional safety, stability and productivity Based on Deere’s 850 crawler dozer, the new
BPL100K and BPL100L models deliver 30 000 lb of linepull capacity at a rated hook speed of 60 ft/min, making them perfectly suited for mid-diameter pipe installation. Both models deliver 100 000 lb of maximum lift capacity for safe, effective positioning of mid-diameter pipe.
“Productivity has been a key focus for us with these new machines,” says Brandt Industries Senior Vice President, Sales – Manufactured Products, Neil Marcotte. “Our winch placement optimises operator sightlines for easier positioning and ensures better tracking to reduce cable wear. Symmetrical winch-mount locations deliver equal weight distribution and lower centre of gravity for increased stability and easier positioning for specialised pipe-specific attachments.” Brandt has included their SmartLift™ Dynamic Stability Monitoring System – an OHSA 1926.1401-compliant approach to load monitoring that replaces traditional static monitoring systems with a continuous stream of real-time terrain and machine data, allowing operators to effectively monitor and manage capacity under all conditions. Additional camera and radar packages are available with up to four cameras and three radar units to keep the operator aware of their surroundings. An automated warning system gives visible and audible machine-tipping warnings, adjustable anti-twoblock warnings, and low-rope warnings. To ensure maximum operational efficiency, Brandt has leveraged Deere’s dual-path hydrostatic drive system while Deere’s ECO mode automatically adjusts engine power settings, based on load, optimising fuel economy. These models deliver up to 9309 in.2 of total ground contact, minimising right-of-way impact, reducing soil contamination and the time required to smooth over ruts. A simple hook-block storage system and counterweight installation further facilitates quick set-up and tear-down.
Brandt’s flexible design approach allows the BPL100K to be configured for specialised roles as a support tractor for larger machines. They can be adapted for end prep, pipe joint welding, or for sandblasting and coating activities. A weld-shack configuration employs a structure attached to the load hook to create a controlled environment and guarantee successful welds. The symmetrical winch design optimises weight distribution and ground contact, making it fast and easy to position specialised pipe-specific attachments.
In addition to their growing pipelayer lineup, Brandt also delivers a popular lineup of built-for-purpose mat and pipe grapples. These units feature a visibility-enhancing design, intended to increase operator efficiency and comfort and deliver enhanced application flexibility with full-width adjustable forks.
“Our commitment to the pipeline industry runs deep,” concludes Marcotte. “Our customers operate in a very competitive market; they deserve the best and we’re working very hard to give them every possible advantage.”
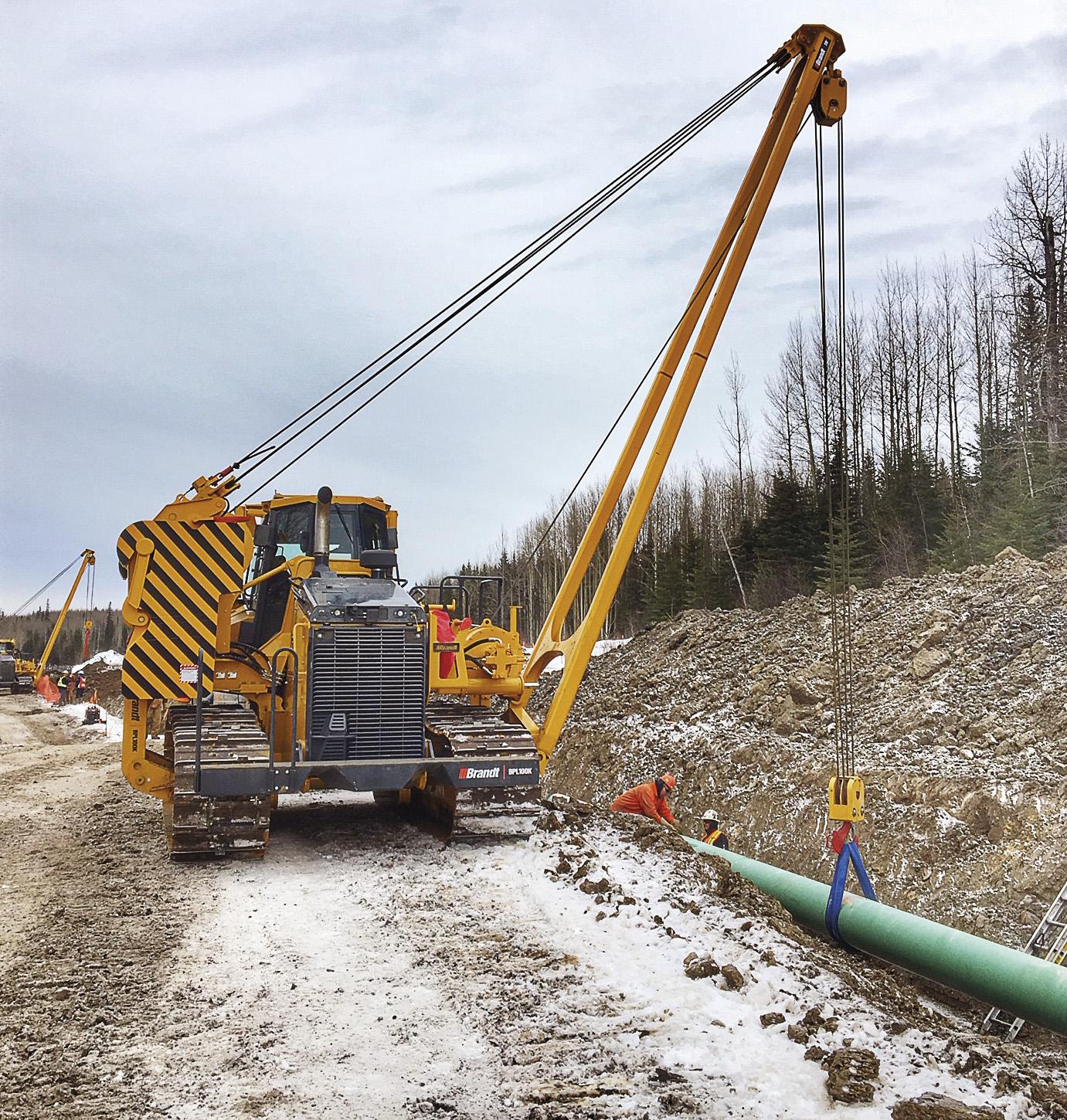
Brandt pipelayers deliver unmatched stability in all conditions.
CRC-EVANS, USA
For more than 80 years, CRC-Evans has provided equipment and services for virtually every aspect of onshore and offshore pipeline construction. CRCEvans maintains comprehensive pipeline equipment solutions that include, but are not limited to: automatic welding machines, pipe-bending machines, ditch-padding equipment, pipe handling and support equipment (Deckhand by LaValley Industries), pipe facing and beveling machines, and internal line-up clamps. By continually reviewing, analysing, and improving equipment performance, CRC-Evans ensures a line of advanced products and services. “We manufacture our equipment in Tulsa, Oklahoma within a High Quality
Management System that is certified to the internationally recognised ISO 9001:2008 standard and includes CRC-Evans’ own Quality Policy,” states Chuck Henson.
“We have had a long history with building and maintaining pipeline equipment like our bending machines. We are constantly listening to our customers’ feedback so that we continue to deliver the best equipment in the industry”.
CRC-Evans has made a study of the needs of pipeline construction contractors, and they invest heavily in the research and development of their equipment offerings. In the case of meeting, and exceeding, pipe bending requirements they developed the newer Centurion Pipe Bending machinery. The systems are available in four distinct pipe diameter sizes: PB6-20, PB16-30, PB22-36, and PB32-42. The development work completed by CRC-Evans ensures that the Centurion easily handles the use of higher yield pipe. To date the Centurion Pipe Bending systems provide an 80% improvement in cylinder travel speed and 30% more bending power than competitive machinery. Our bending machines also feature outstanding hydraulics and quick-starting engines with reduced noise and cold start packages. A single operator is able to oversee all functions. The benefits are faster and more robust bending operations that will reduce time and cost for meeting required completion time.

PB32-42 Centurion ready deployment.
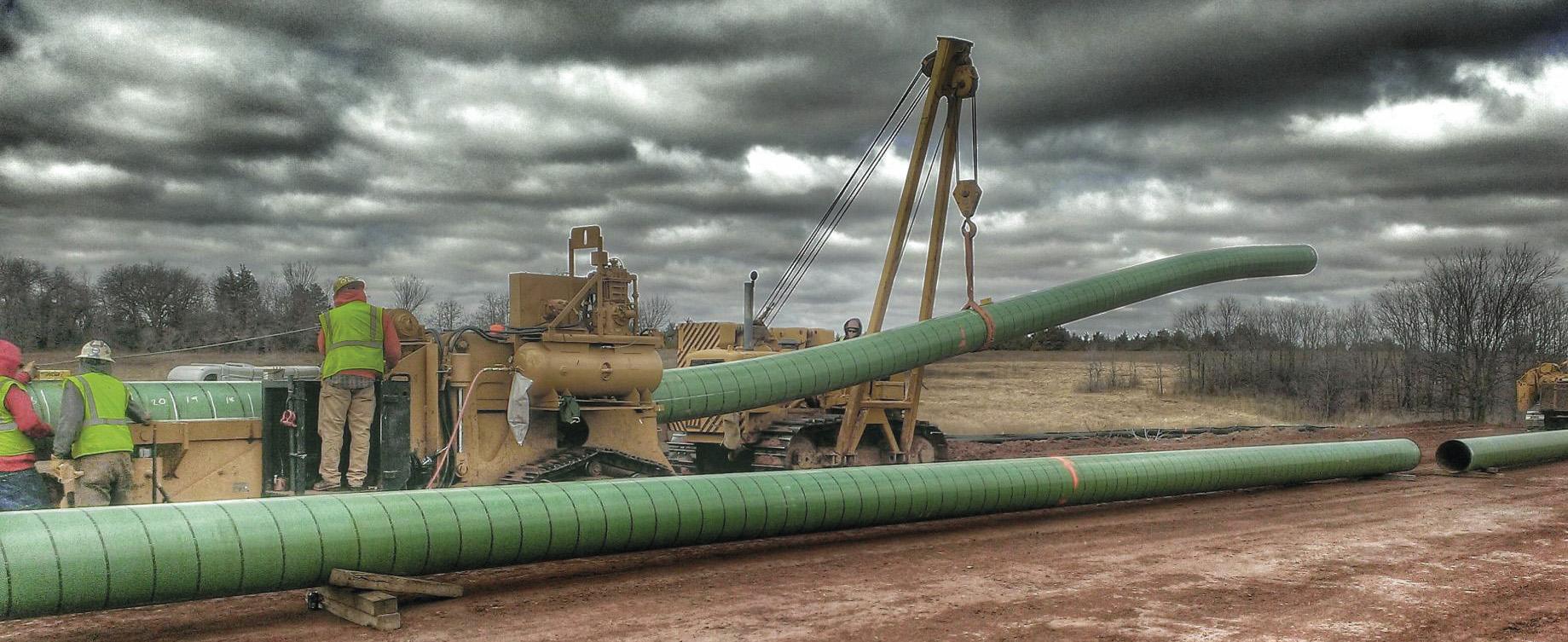
PB16-30 Centurion Bending Machine working on the 24 in. Tallgrass Prairie Project.
JARRAFF INDUSTRIES, USA
The Jarraff All-Terrain Tree Trimmer is no stranger to challenging terrain, which makes it well-suited for maintenance applications in pipeline rights-of-way (ROW) where conditions can range from difficult to extreme. The Jarraff is now better equipped than ever to handle any conditions of the ROW. Jarraff Industries Director of Sales, Kenny Jones, explains that Jarraff operators have the ability to match tyres and undercarriage options to their terrain. He said, “A variety of tyre options are available for the Jarraff All-Terrain Tree Trimmer. No matter what the conditions encountered, Jarraff has tyre options that can deal with any situation. In addition to tyre options, the Jarraff is available in
Quad Track and Full Track configurations.” The Jarraff’s standard Primex Xtreme LS tyres offer stability, traction and durability. The Primex Xtreme LS tyres are highly durable thanks to its 20-ply design. The Xtreme LS operates effectively in the rain-soaked lowlands to rocky hills. With a 6.5 psi ground pressure, this tyre option provides operators maximum machine control with minimal ground disturbance.
Many Jarraff Tree Trimmers equipped with the Primex HF4 tyre option are able to move safely across loose soil, while maintaining stability with Kevlar reinforced sidewalls. ROW maintenance contractors often utilise this tyre option to access areas that have been traditionally inaccessible.
According to Jones, a high-floatation tyre is another option. This tyre provides 5.1 psi ground pressure and works well in pipeline ROW conditions across a wide spectrum, from roadway surfaces to swamplands to roadside ditches.
For Jarraff units that wander out of the pipeline ROW and into more urban areas, Jones says a turf tyre option is available for road and residential applications. With increased manoeuvrability on road and residential applications, this tyre lets the Jarraff All-terrain Tree Trimmer move across residential areas without tread marks.
Beyond the traditional tyre options, operators can choose from track options. Jones said, “A full tracked Jarraff will make quick work of the soft ground conditions and provide the ability to climb difficult hills and inclines. The steel-cleated, rubber track design is effective in demanding grades, as well as swampy conditions.”
Jones says a quad track Jarraff model provides another level of capability. He said, “The quad track Jarraff is one we’ve added recently. This unit features a four quad track undercarriage and that’s an industry exclusive feature. The quad track design provides low ground pressure and excellent traction, as well as road-ability and maneuverability in a single machine, in addition to the extreme mobility.”
Each Jarraff provides a dynamic field of operation. A rotary manifold offers a 360˚ plus range of motion. The unit also provides lateral tilt and 75 ft cutting height. Two four-way joysticks and fingertip controls offer optimal precision. In addition, every Jarraff model’s cab is completely ROPS and FOPS certified.
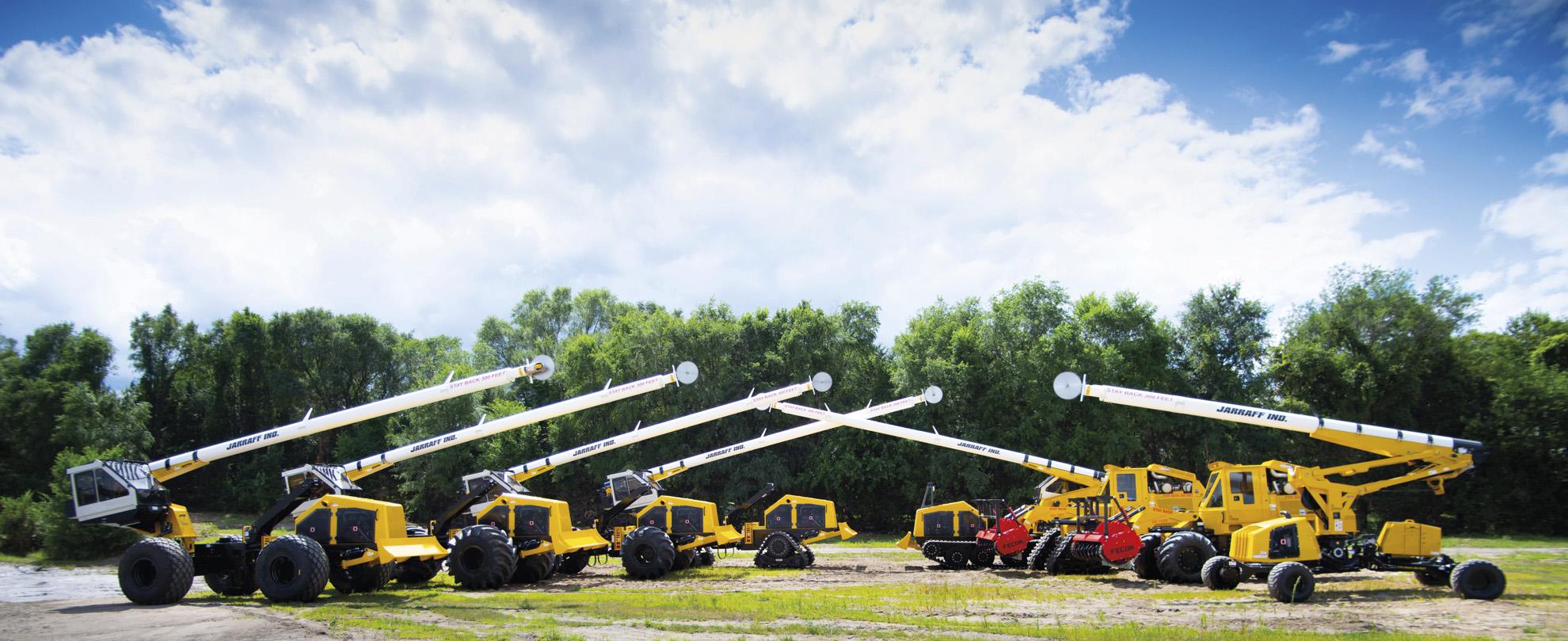
All models of Jarraff Industries’ All-Terrain Tree Trimmer.
LAURINI OFFICINE MECCANICHE, ITALY
The name of Laurini Officine Meccaniche’s pipelayer, ‘SansOne’, immediately brings to mind the Biblical hero Samson of prodigious physical strength. It is that legendary power that has inspired Laurini to pick the name of its pipelayer: introducing SansOne, where the capital O is not a typo, but a play on words that refers to the hero’s name and the English word for ‘number one’. So, right from its name the expectations for this new machine are very high.
Marco Laurini points out that the idea of creating SansOne came from listening to market needs. Furthermore, this type of machine was not yet part of Laurini’s offer, and it seemed right to introduce equipment that represents the sector in which the company is globally recognised.
SansOne has something more compared to existing pipelayers. The main goal was to improve the key aspects of this type of machine, such as visibility. As the virtual reality programme shows how SansOne gives the operator perfect visibility in all directions: ahead to unload the pipe, and also behind and sideways to check the movements of other operators. To reach that, it was necessary to ‘scramble’ the layout and move the position of some components: modifying radiator shape and position, lowering the bonnet and the diesel tank.
Next to visibility, stability is the other key feature of the Laurini pipelayer range: considering the machine weight, the centre of gravity is lower, which helps to stabilise the machine, especially when working at an incline. Stability has also increased thanks to the patented articulated boom: the joint-pin system at the centre allows it to move forward or backward, and not just sideways, according to the direction of travel; hydraulic pistons featuring slow and precise movement shift the centre of gravity back or forth to maintain the machine’s stability as it proceeds uphill or downhill. This movement is not automatic, so the operator can decide whether to shift the load and move the pipe by millimetres, without moving the machine at all.
SansOne will be manufactured in three models with three different maximum lifting capacity: 45, 70 and 100 t. Transportation matter is handled in the smaller 45 and 70 t models by extending the undercarriage, the tracks widen during operation and retract during the transport phase; while in the larger 100 t model, the tracks can be even removed with a hydraulic quick hook up system. In half a day two people can disassemble, and later reassemble, all the components of a SansOne 100 t and place them in the container.
Other special features make SansOne stand out from the other pipelayers currently on the market, such as the machine controls housed on the seat armrest and controlled by two multi-function joysticks, and some finger controls. Thanks to the 12 in. touch screen, fixed to the seat with a small support bracket, the operator can monitor all parameters and have full view of the camera without turning or leaning out.
Having concluded the prototype phase at the end of 2020, the tests on the prototype of the bigger model will be executed starting from January 2021, in order to be able to put on the market SansOne first units in spring of 2021.
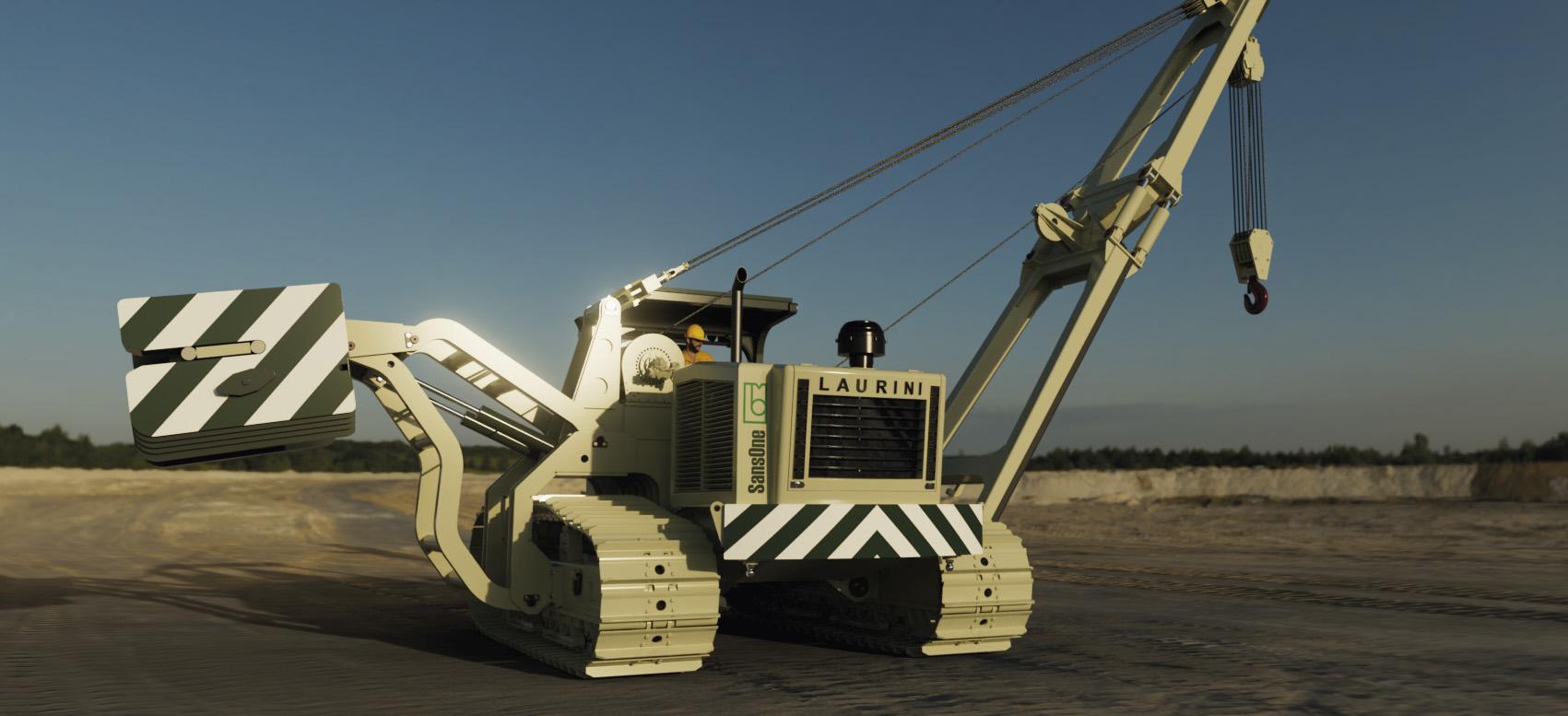
Laurini Pipelayer: SansOne 100.
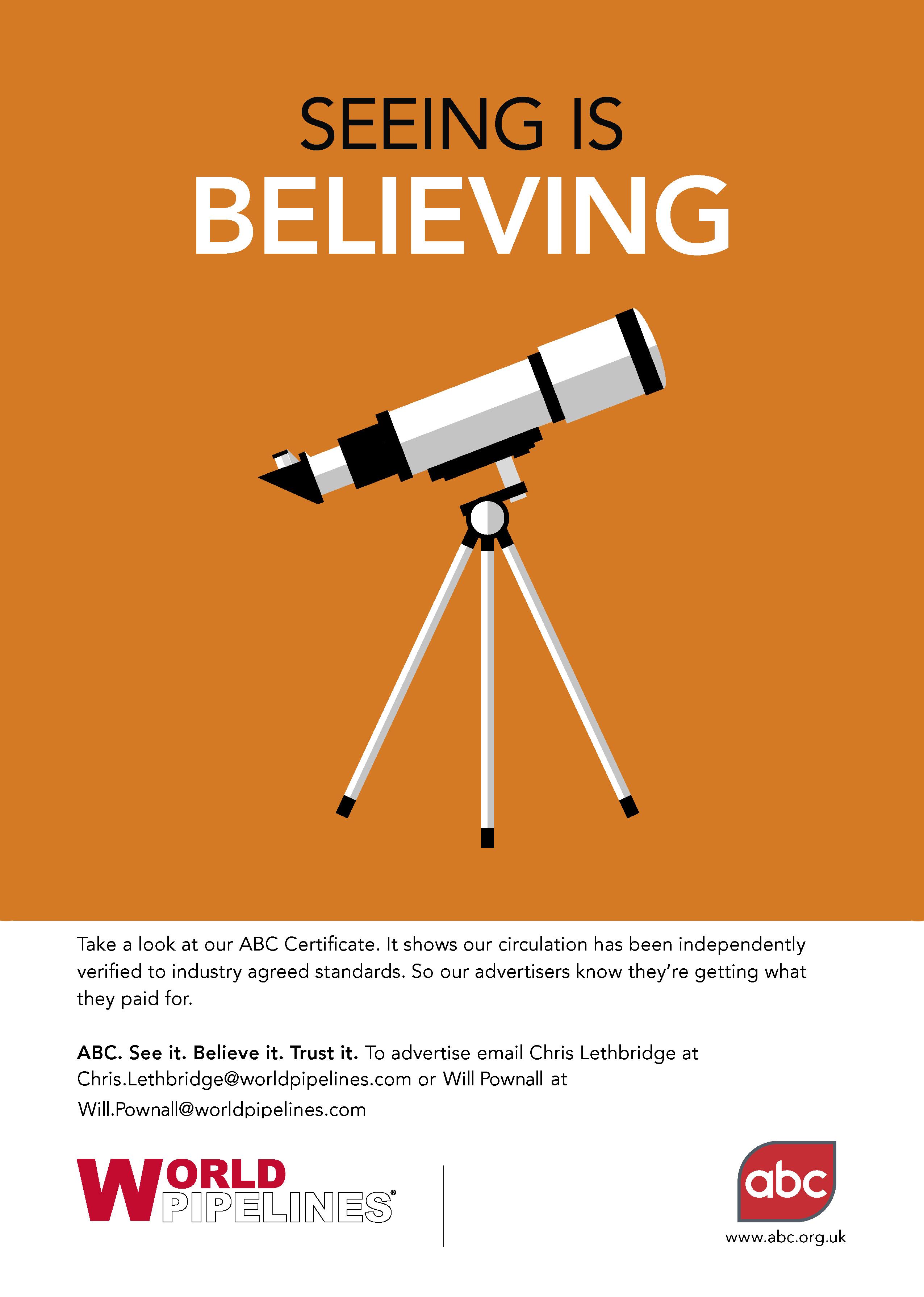
LAVALLEY INDUSTRIES, USA
LaValley Industries is a Bemidji, Minnesota, USA based manufacturer of specialty pipeline equipment products that provide greater safety and production for pipeline contractors around the world. Since its formation 15 years ago, LaValley Industries has continued to advance the technology and capabilities of its flagship product – the DECKHAND® pipe handling attachment – expanding its capabilities while continuing to bring new standards of safety and efficiency to the industry. Recently LaValley
Industries introduced two new models to the marketplace,
DECKHAND®5HP (DH5HP) and DECKHAND®LT (DHLT). The DH5HP features a high-performance rotary drive system allowing for maximum torque in the most challenging horizontal and vertical applications. The DH5HP’s versatility provides contractors a tool for handling pipe along the most challenging right-of-ways, including mountains and uneven
terrain. In vertical applications, the DH5HP’s high-performance rotary drive coupled with sophisticated telemetrics allows the operator to precisely position pilings and utility poles with accuracy and control.
The DHLT is a cost-effective solution that has been engineered to precisely handle drill rod and smaller diameter pipe at an economical price point. As with all Deckhand products, DHLT allows an operator to work safely from inside the excavator cab using in-cab controls and touch display to control all movements and adjust all operating parameters. Load locking valves ensure that pipe is always held securely regardless of hydraulic pressure. DHLT has a lifting capacity of 10 000 lbs, connects to any brand excavator in the 20 - 36 metric t range and is powered by the excavator’s auxiliary hydraulic circuit. Designed with 360˚ continuous rotation, tilt, and shift functions, DHLT delivers unmatched safety and efficiency to load, un-load, and position pipe. Utilising a variety of different Arms,
DHLT can handle pipe and drill rod ranging from 4.5 in. to 16 in. In the face of an ever-changing world, LaValley
Industries works hard to listen to our customers while anticipating their future needs. “Contractors face a myriad of challenges on their jobsite every day and our goal is to place the right tool in their hands to get the job done. Our team of industry experts are always working towards the next innovation that will meet our industry’s needs while maintaining the safety and efficiency our products are known for,” states Jason LaValley, Founder and CEO of LaValley Industries. “It’s been a pleasure to see our product line continue to create safety on jobsites around the world for the last 15 years and I look forward to watching as the DH5HP and DHLT bring the same unparalleled safety as the generations before them.” LaValley Industries continues to make waves as they expand into their new division –
EMPOWERTM – where the focus is on the electrification of products for the oil and gas industry.

DECKHAND®LT handling drill pipe in Minnesota, USA.
DECKHAND®5HP unloading pipe in the mountains in Pennsylvania, USA.
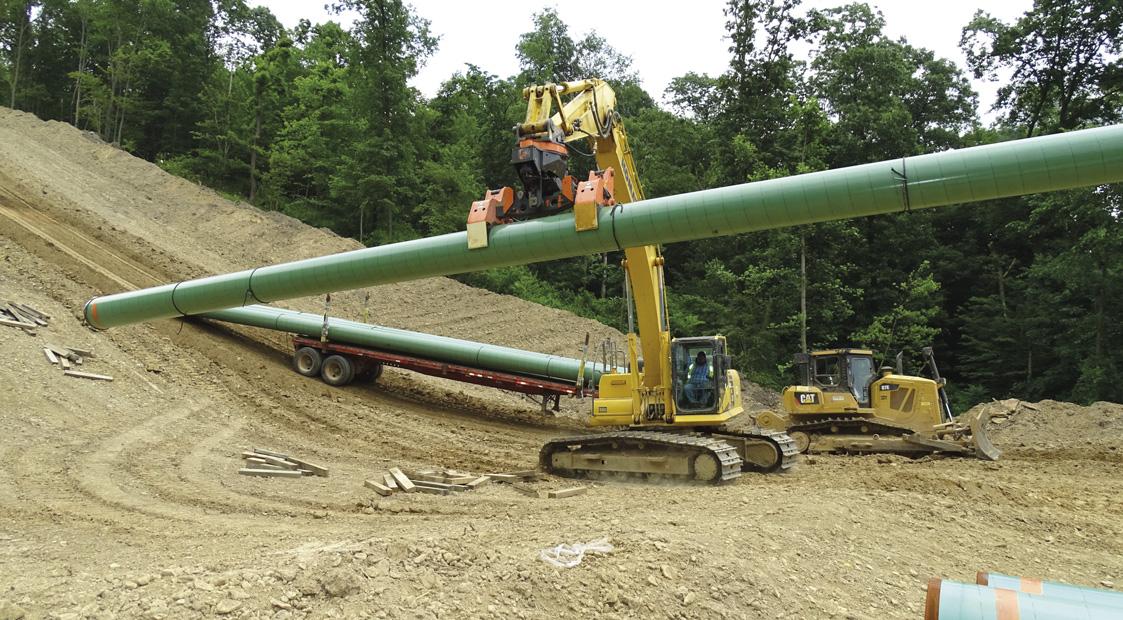
MASTENBROEK, UK
Mastenbroek has added a new engine to its innovative CT12 Crawler Truck. The UK-based designer and manufacturer of self-propelled trenchers manufactured the first CT12 in 1983 to install aggregate backfill for sub-surface land drainage. Over the years, Mastenbroek has improved the CT12, increasing its performance and versatility and today, the crawler truck offers the perfect combination of features demanded by construction companies operating in the oil and gas industry. The CT12 is one of ƒMastenbroek’s most versatile machines thanks to its tipping hopper and forward conveyor.
The hopper allows the CT12 to be used as a dump truck to haul aggregate along pipeline right-of-ways. The discharge conveyor system is designed for controlled, accurate placement of backfill material either directly into a trench or a hopper mounted on the trencher.
The front swing conveyor is controlled by a joystick for left and right-hand discharge through 180˚ and variable height up to 2.75 m. A hydraulic hopper door combined with variable speed control on all conveyors allows the flowrate of the material to be adjusted as well.
For 2021, Mastenbroek has upgraded both the CT12’s engine and improved access for on-site service and maintenance. The machine is powered by sixcylinder, 252 Hp (185 kW) EU Stage V emission compliant Volvo Penta D8 engine, which features a highly advanced exhaust aftertreatment system, based on SCR technology, uncooled EGR and a diesel particulate filter. Mastenbroek has invested a great deal of time and effort in making the CT12 as versatile and user-friendly as possible. The cabin features hydraulic elevation to afford the operator good all-round visibility of the conveyor discharge and also into the hopper. As Mastenbroek’s CT12 features a low ground pressure suspended and oscillating undercarriage with high tracking speeds, it can be used in environments where wheeled vehicles are unable to operate. “The CT12 has proved itself over the years, operating successfully in some of the most arduous conditions, such as on saturated soils while minimising soil compaction,” says Christopher Pett, Mastenbroek’s
General Manager. “It is a popular machine in utility applications as well, where a backfill aggregate must be placed efficiently and consistently into the trench. We are pleased to have seen increased demand within the pipeline and cable trenching industry over the last few years and believe the introduction of the D8 engine and maintenance upgrades will make the
CT12 even more attractive to those operating in the oil and gas industry.” Mastenbroek manufactured its first trencher in 1977, and since then the company has grown into a globally respected name in trenching, machine automation through its partnership with Trimble® , subsea cutting technology, ground stabilisation and groundwater control.

Mastenbroek CT12.

Mastenbroek CT12.
PROLINE PIPE EQUIPMENT INC., CANADA
Proline Pipe Equipment is proud to be a leading international supplier of pipeline solutions for the oil and gas industry. Based in Edmonton, Alberta, Canada, Proline offers an extensive inventory of high-quality products designed to meet the needs of our customers worldwide. Since 1967, our dedication to innovation, uncompromising craftsmanship, and unbeatable customer service have helped us earn a reputation for excellence. Designed and manufactured by Proline Pipe Equipment our horizontal pipe rollers have been used throughout the industry for years. We take great pride in the quality of our rollers and thoroughly inspect each unit before it leaves our shop. The rollers come in several sizes to accommodate almost every project. Benefits include: multiple sizes and ranges for different pipe diameters with one roller; heavy duty options for tougher jobs; stackable up to three high on larger models; heavier models include lifting hooks; and urethane rollers to help protect a multitude of coatings.
Our design team is always hard at work coming up with the best products for our customers. They always take into account what field application would look like and design around that premise. That’s why Proline is very excited to announce a new ground-breaking product to its pipe roller lineup, the new Adjustable 16 - 48 in. HD Horizontal Roller. This roller was designed with the end user in mind and allows the customer to adjust the roller to fit their specific job. Adjustments can be done in-house before the pipe rollers are shipped out to site. Despite being adjustable these rollers are the most rugged we have ever built, with a whopping 50 000 lb. (22 680 kg) capacity. This allows them to be spread out farther than typical rollers for large diameter pipe, which helps to cut costs. Heavy duty urethane rollers help protect coatings on large diameter pipe during river/ road crossing installations. Other benefits include: forklift pockets for positioning under pipe and loading on flatbed from all sides; two lifting eyes; angled iron pockets for ease of stacking; easy adjustment for different pipe sizes; low ground profile, and wide footprint. Its dimensions are: 69 ¼ in. x 37 ¼ in. x 26 ¼ in. (1759 mm x 946 mm x 667 mm), and its weight is 1605 lb (728 kg).
With this versatile range of equipment, multiple sized pipeline jobs can be completed with this multi-sized roller.

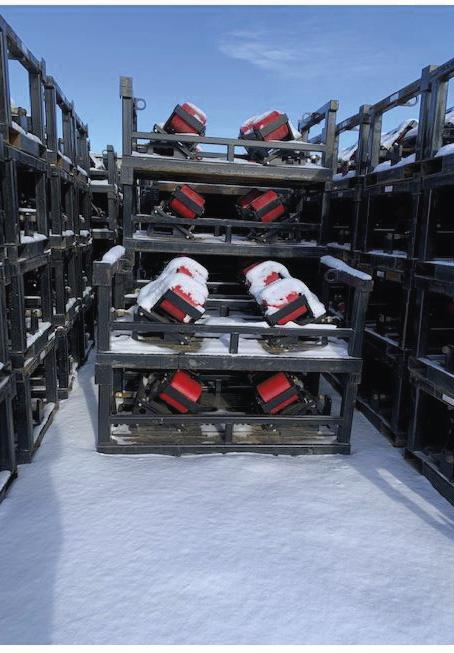
Proline’s Adjustable 16 - 48 in. HD Horizontal Roller.
SCAIP S.P.A., ITALY
SCAIP designed its first model of self-loading padding machine in 1997 (the SPD 45). Since that time several improvements have been accomplished. The SPD line today includes five sizes: 150, 160, 250, 350 and 450. All of them have been subjected to significant revisions in the past two years.
This article will highlight the technological features that characterise the self-loading machines with a newly designed cabin (SPD 250EVO, 350EHD and 450EVO).
The machine has maintained essentially the same design in the rearward area, the main changes have occurred in the forward area where the sliding cabin has been redesigned and replaced, taking into consideration a completely different idea. The goals during the R&D were to improve the visibility of the operator, without any compromise regarding safety and comfort.
The new cabin can function according to the operation: in transport and starting position the cabin is positioned at the ground level in front of the escalator. During operation the cabin can be raised and turned 90˚ right or left to carefully oversee the padding process. The new design did not affect the centre of gravity; in fact the machine has the same stability as the previous models. The interior of the cabin is well equipped, on the armrests there are all the function controls and on the left-hand side of the operator seat there is an additional folding seat in case the situation requires it.
This new design allows the operator to stay seated during all operations. In the older model the cabin was sliding length wise and the operator was required to stand in order to oversee the process and operate the machine from one of the two control stations. The size of the new cabin also improves the efficiency of the A/C system by 50%.
In terms of safety, the SPD is equipped with five cameras, to cover the perimeter of the machine offering the operator a view also of the corners that otherwise would be blind. Furthermore, the inclinometers are able to monitor and automatically level the escalator boom and the shaker frame during the work and adjust it automatically if necessary (the two auto-lev. can be activated separately).
SCAIPNET is also available to remotely control the status, position and other parameters of the machines and send an alarm in case of necessity.
The radio control system has been extended to these models (SPD 250, 350 and 450), so that it is possible to operate the machine without the operator being in the cabin. This allows full operation of the machine and adds this option in order to improve functionality and safety.
All improvements discussed above have been possible due to the increased technology that is now included on these machines therefore resulting in an optimisation of hardware and software design. The first five machines have been tested in early 2020 in North America with positive feedback and results from the end user.

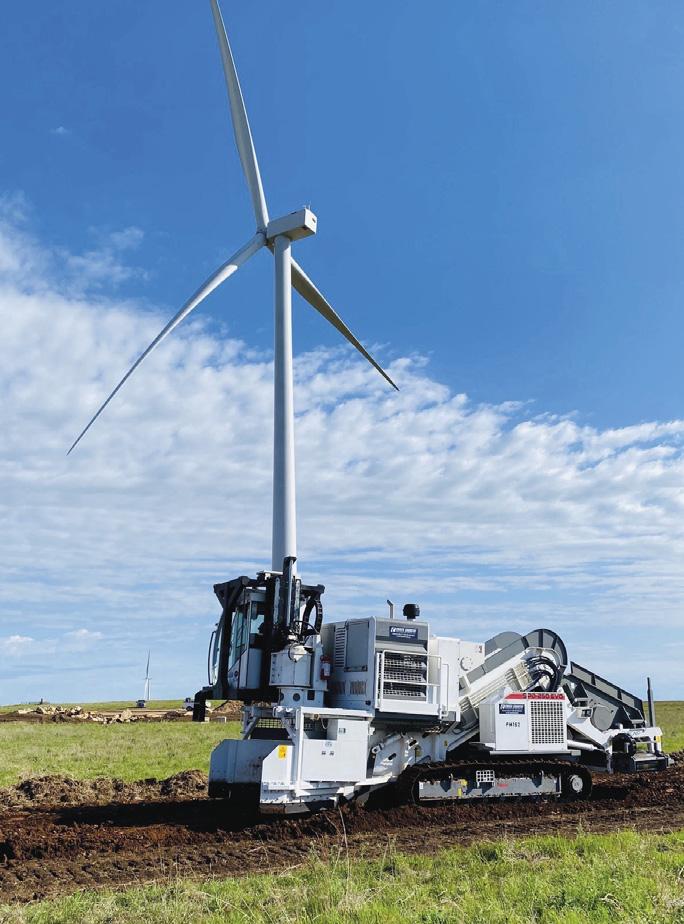
Left: old SPD 350 – Williams NW Pipeline Projects, 2009. Right: new SPD – 250EVO Mill Creek, Oklahoma, 2020.
TERRAMAC, USA
Pipeline contractors around the world benefit from rubber tracked carriers and their innate ability to access and conquer remote right-ofways. Terramac’s line-up of carriers exert minimal ground pressure and offer the largest selection and most versatile equipment options for conquering every stage of the pipeline process. From clearing, to installation, to reclamation and everything in between, these carriers are equipped to traverse pipeline terrain with ease while providing contractors reliable equipment solutions that improve productivity by maximising efficiency and minimising downtime. Terramac’s built-in telematics management system comes standard on units, which echoes the brand’s emphasis on innovation and streamlines the management of off-road equipment on pipeline projects. Powered by Trackunit, Terramac’s telematics system provides a holistic view of carrier performance for enhanced fleet management, maintenance, and service. Through extensive tracking and data collection, carrier units are thoroughly monitored from afar which makes both large- and small-scale pipeline equipment management more convenient and effective. Using GPS, carrier locations can be observed no matter where they are stationed along the right-of-way providing increased fleet visibility and on-site usage tracking. “We’ve been using telematics, including TrackUnit for many years and are partial to it because it provides complete visibility of our fleet, and allows us to manage equipment for a larger service area while minimising the risk of lost or stolen equipment,” explains Paul Desombre, General Sales Manager at Power Motive Corporation. “Due to its significance, we always appreciate when niche manufacturing partners such as
Terramac recognise the importance of this feature and equip their machines with it so we don’t have to after-the-fact.”
The telematics on Terramac track trucks also provide live machine and engine data streams for diagnosis, service, and repair information. Tracking live carrier data alerts owners and operators of possible issues early on so preventative measures can be taken to safeguard the carriers.
The advanced notice also allows for more preparation time for repairs, ensuring proper parts and tools are accessible to get the units back to operating condition. These live data streams have become vital for pipeline equipment rental companies that send their fleets to remote jobsites, as well as pipeline contractors that depend on reliable track trucks not just for completing their projects, but doing so in a timely manner.
“Telematics is a necessary part of our business,” adds Paul Desombre. “We use it for everything from managing rentals to service and billing. We really couldn’t manage our fleet without it.”
As with all other aspects of Terramac carriers, their telematics can be customised with CAN data feeds and reporting to keep pertinent carrier information accessible at a moment’s notice. Fleet managers can set alerts for scheduled and preventative maintenance, creating a more efficient workflow for their tracked units which minimises downtime.
Access to Terramac’s telematics data is available from multiple sources including desktop, laptop, and mobile devices. The ease of data retrieval is advantageous for providing on-site guidance for operational prechecks, site mapping and more.

Terramac carriers with tac welders.
TESMEC S.P.A., ITALY
With the aim to be profitable, pipeline projects need to keep up with the times and follow machinery’s lastest technological progress, increasing the efficiency and maximising the profitability. Tesmec Group’s latest developments in trenchers have led to a revolutionary concept that has led to the launch of the new EVO series, available on bestseller models 975, 1150, 1475 and 1675. Thanks to an improved flywheels gearbox, new hydraulic components and the latest release of the TrenchTronic 5.0 for full digital control of the automatic digging function, EVO series machines combine higher chain-pull and lower chain-speed in order to have higher breakout force of the teeth and simultaneously reducing their consumption.
EVO machines can trench hard and abrasive rock with productivity and cost efficiency that is unmatched, combined with a significant fuel and teeth consumption reduction.
Compared to the previous generation of machines, the improvement of digging performance is applicable in the toughest conditions, hard solid rock and deep trenching. EVO machines have been already involved in various pipeline projects all around the world. Especially significant is the data collection carried out by Tesmec in Qatar during the last two years, where both 1675 old generation and 1675EVO were at work simultaneously. Tesmec specialists have compared the performance of the old generation trenchers with the new EVO series thanks to the work done together with the local partner QBC (Qatar Building Company) into the Ashghal project. Ashghal project is part of the ‘Qatar National Vision 2030’, the governmental plan that aims to develop Qatar’s infrastructures.
A total of four Tesmec 1675 trenchers have been involved in the project, both old and EVO generation.
With the new 1675EVO machine combining chain speed decrease and the resulting higher chain pull, the jobsite productivity increased up to 30% and the picks, fuel and spare parts consumption substantially decreased for a saving of 20/25% on the total project cost.
Data analysis shows a reduction on all main project cost items: teeth consumption, fuel consumption, spare parts, service and maintenance. EVO revolutionary concept is available for all kind of pipeline applications, assuring a substantial saving even under extreme conditions.
The new Tesmec trencher 1675EVO Chainsaw is a 130 t machine that, depending on the configuration chosen, can dig up to 732 cm (24 ft) deep and 183 cm (6 ft) wide. Like all EVO Tesmec trenchers, this model is equipped with the TrenchIntel 3D GPS system (to record data and position while trenching, realising an as-built map in real time) and with the new Remote Monitoring Control (Re.M) to monitor machine parameters, avoiding breakages and stops and guaranteeing predictive maintenance.
Finally, the recently released Trencher Radio Control system (TRC) makes EVO trenchers safer, removing operators from the machine cabin and allowing fully remote control.

Tesmec 1675EVO – digging section.
VACUWORX, USA
The RC Series Vacuum Lifting Systems from Vacuworx are powerful and versatile attachments capable of handling steel pipes and other materials up to 55 000 lb (25 t). All RC models feature wireless remote operation that is both faster and safer than using hooks, slings or chains. 360˚ rotation provides precise placement of materials. In addition, vacuum lifting technology provides a powerful positive engagement of the load and will not damage delicate materials and bonded coatings.
The fully self-contained RC Series units are powered by diesel engines and can be hooked up and ready to go in a matter of minutes. RC Series ‘H’ models operate using the hydraulic system of the host machine to eliminate fuel costs, emissions and noise.
As part of its commitment to continuous innovation, Vacuworx has engineered significant updates to their flagship line of RC Series Vacuum Lifting Systems. The lifters are ‘smarter’ than ever before by incorporating a Controller Area Network (CAN bus) system to provide real-time diagnostics and enhanced safety features.
Commonly used in passenger vehicles and other equipment, a CAN bus allows internal devices to communicate with each other without a host computer. Utilising a central logic controller, the system is designed to monitor for faults and quickly diagnose specific problems.
The new dashboard gauge on one side of the RC lifter shows error codes, oil and fuel levels, pressure level, number of lifts and engine hours. The logic controller increases safety by ensuring that the electronic components are operating correctly.
The simplified wiring design has fewer components and no mechanical switches. The system incorporates pressure transducers instead of a vacuum switch for greater accuracy. There are no fuses to repair or replace – all faults are reset electronically. In addition, the design helps promote safety by identifying any incorrect repairs or environmental damage.
Vacuworx has taken additional steps to increase longevity by replacing the traditional gearbox with an environmentally friendly belt drive. With no need for oil, the new belt drive system was designed to keep engine bay temperatures cooler, provide a longer service life, and all but eliminate the need for repairs.
While installation of RC Series is already quick and simple, new RC lifters feature an updated adapter with removable top caps, which allow the installer to position and secure the adapter pin easily, letting the excavator do the heavy lifting. A flow control block has been incorporated into the adapter to allow for more safe and convenient adjustment of the hydraulics. This puts the flow controls within easy reach, rather than higher up on the arm of the excavator. The part of the adapter that connects to the base plate on the lifter was also redesigned as a replacement part, minimising time delays and repair costs as the ‘tombstone’ is now bolted rather than welded on.
All Vacuworx equipment meets or exceeds global design, engineering and safety standards, including ANSI/ASME standards section B30.20 and ASME BTH-1 for below-the-hook lifting devices. The machines are built to withstand rugged jobsite conditions and perform optimally in extreme temperatures or inclement weather conditions.
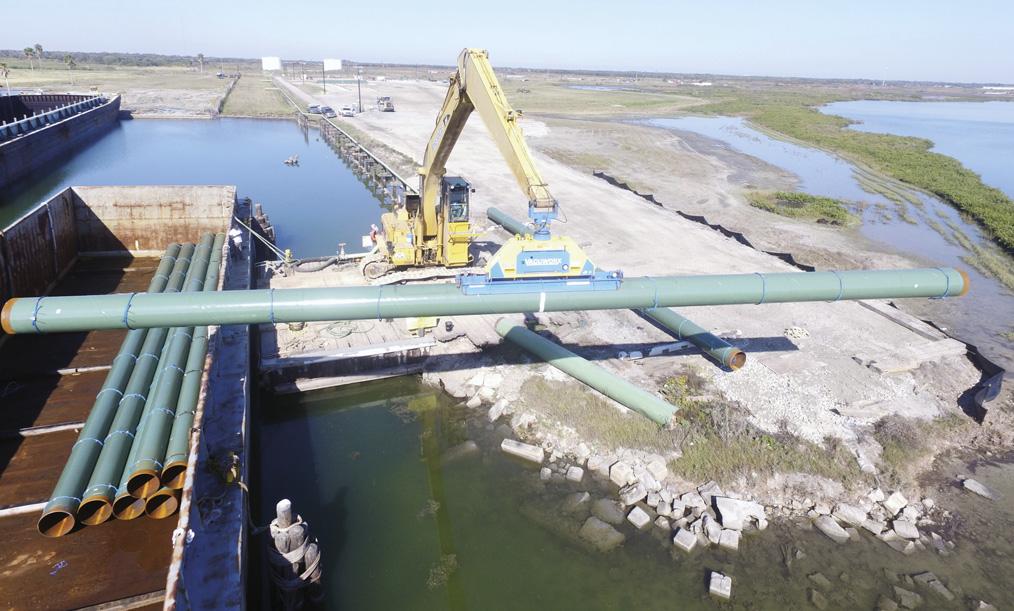
Freight Solutions RC 16 barge.
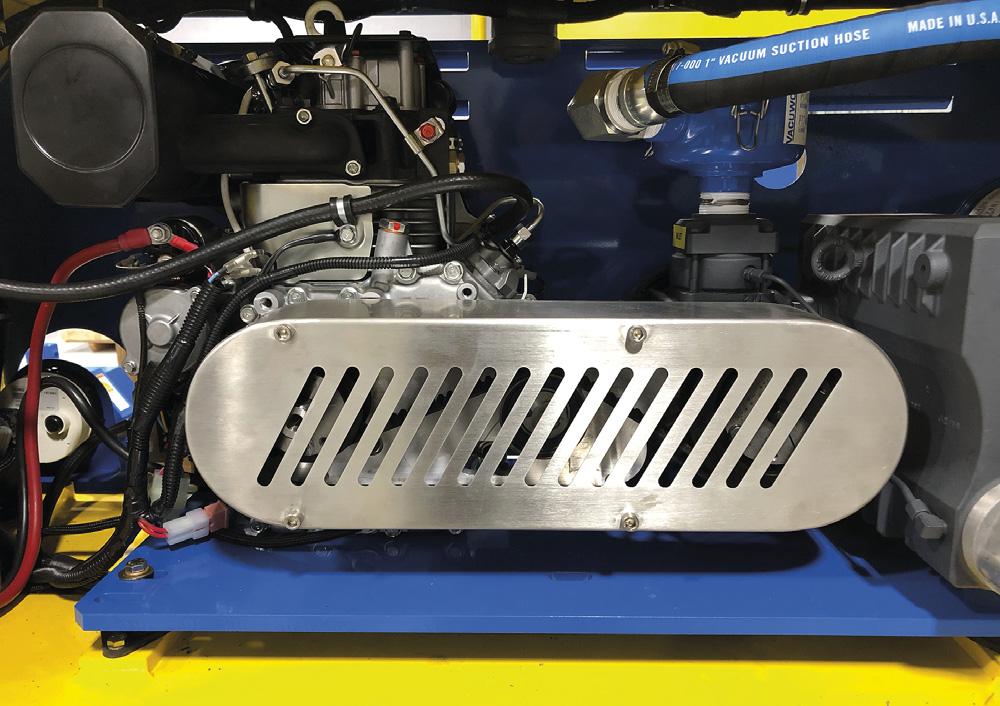
Vacuworx RC belt drive.
WORLDWIDE MACHINERY, USA
Worldwide Machinery’s extensive inventory and global presence make it an easy choice for businesses looking for dependable machines and reliable service for upcoming pipeline projects. To meet our customer’s demands for productive equipment fast and efficiently, we have made several advancements in our manufacturing process.
Worldwide has relocated many of its manufacturing operations to Houston, Texas (US). We are now able to build our Superior Vacuum Lifts, Padding Buckets, Pipe Bending Machines, Lined Bending Sets, Mandrels, Internal Lineup Clamps, Roli-Cradles, Ditch Pumps and various Crawler Carrier attachments at our Channelview, Texas, facility. Now, quicker than ever before, we have designers and engineers on staff that are able to modify equipment to meet client needs. We are also able to meet faster delivery timelines for North America, Latin America, and South America, due to our ability to manufacture in the western hemisphere.
Evidence of our increased manufacturing capabilities include our new line of Superior Crawler Carriers with changeable steel and rubber undercarriages, expandable cabins, and swappable beds. Those customisable beds include: rock and material dump bed, sand blasting deck, welding deck, heavy-duty flat bed with dump capabilities, and a personnel carrier.
The family of Crawler Carriers have load capacities ranging from 15 000 lb (6800 kg) to 30 000 lb (13 600 kg), a CAT C-7.1 engine, travel speed of 5.6 mph, and an available model with rotating cab that pivots over the centre bearing. Accordingly, Worldwide Machinery and Superior Manufacturing has the model of Crawler Carrier to fit your needs.
Furthermore, we are excited to release a newly reengineered line Superior Padding Machines, the SPD-350 and the SPD-160L and coming soon: the revamp of Superior Pipelayers. Worldwide will continue ongoing product enhancements, like adding pneumatic mandrel availability to be used with our bending machines, and creating innovative attachments to help the contractors we work with get the most out of their Superior Crawler Carriers.
Worldwide has also expanded our equipment offerings with brands like Laurini Manufacturing. Being the Laurini dealer allows Worldwide Machinery to be the one stop shop as your preferred equipment supplier. We are able to provide unique solutions through the Laurini Volcano Series of Padding Machines, Hammer and Grub Crushing Machines, Pipe Lifting Beam, Muletrax units, and various other specialty pieces of equipment.
In addition to productive pipeline specific machines, Worldwide Machinery offers a large quantity of late model Caterpillar and John Deere equipment, including dozers, excavators, motor graders, as well as fuel/lube trucks, water trucks, ditch pumps and more to lease, rent, or buy. As a result, Worldwide is able to supply an unrivaled offering of equipment for your next job.
Our ‘True North’ is to supply the best, most productive equipment to our customers. We will continue to strengthen our value by investing in top quality equipment, knowledgeable and helpful staff, and responsive service.
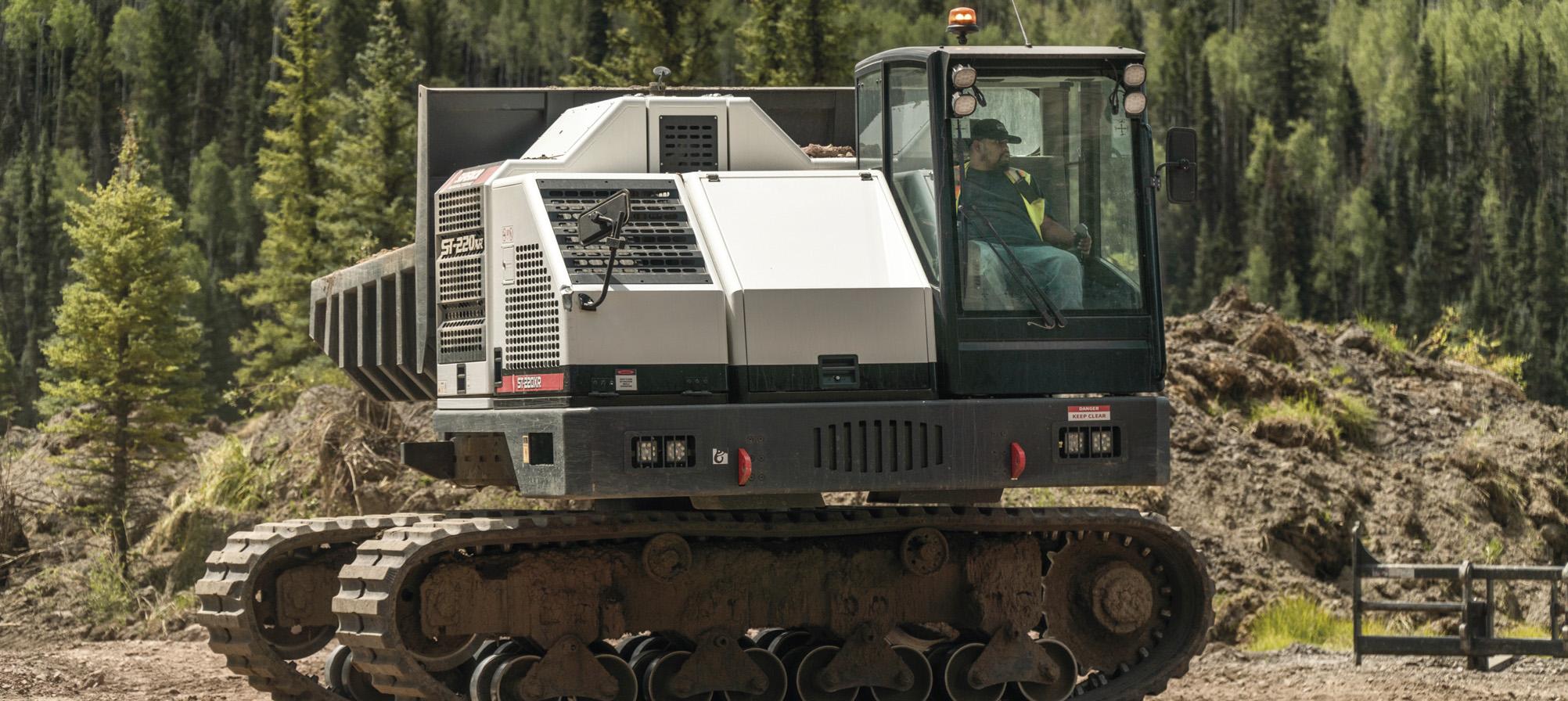
Superior ST-220XR Crawler Carrier with 360˚ rotating cab.