
19 minute read
Ready when you are
and south pipelines as well as the shore approach sections that were laid independent to the main line.
Potential safety risks were presented by performing the hydrostatic tests from the deck of an offshore jack-up with around 4000 psi (275 bar) and such large volumes involved. In these limited spaces and conditions, a component failure could be catastrophic. Baker Hughes’ Red Zone policy leads the industry into safer working practices – requiring the use of technology to remove all personnel (from Baker Hughes, the client, and other contractors) from the line of any potential pressure loss. To accomplish this, Baker Hughes designed and built a Remote Hydrostatic Test Manifold (RHSTM) that let Baker Hughes pressurise the pipeline, hold that pressure, top it up, and bleed it without any human contact with pressurised equipment. Traditionally, this would all require manual manipulation of pressurised valves connected to hose but Baker Hughes completely removed any potential injury risk from unexpected pressure loss.
Live stream hydrostatic testing During the hydrostatic test, Baker Hughes also utilised the Nanoplex data management system that has the technical capability to live-stream via satellite a dynamic graph showing pressure and temperature at various points along the pipeline. With a simple web link and password, the client could monitor the test in real-time from PCs and mobile devices anywhere in the world. When undertaking such a large test on an asset of this significance, many stakeholders are very interested in tracking progress – Baker Hughes’ use of Nanoplex made that easy.
Drying Baker Hughes provided two epic dry-air spreads, both in excess of 20 000 ft3/m, located at Brownsville and the Tamiahua beach site. Drying time for the two pipelines were estimated and agreed on during pre-engineering with Baker Hughes. Actual drying time for the north line was significantly shorter than planned, which saved valuable days. This efficiency gain was attributed to the high quality of dewatering pigs that Baker Hughes designed and manufactured specifically for this pipeline, and the consistent dryness of high-volume injected air.
After drying the lines, a pipeline nitrogen purge with on-site generated nitrogen was also successful – thanks to Baker Hughes’ highly efficient membrane N2 technology, which removed the cost and potential delays to truck in traditional liquid nitrogen.
Conclusion From start to finish, Baker Hughes used its highly trained workforce, specialised equipment and extensive knowledge to engineer solutions to challenges, reduce risk to personnel and property and customise a solution to produce the best possible result for our customer.
Note Baker Hughes would like to thank TC Energy and IENova for their permission to publish this article.
Heavy Duty Through-wall Reference Electrode
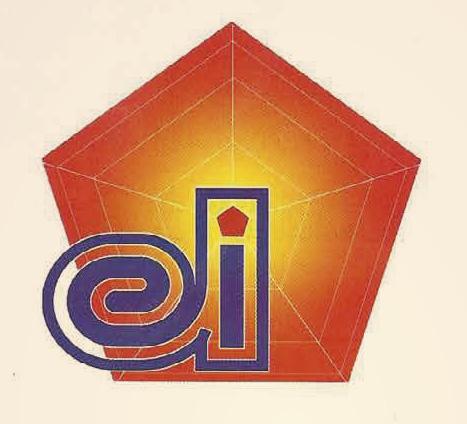
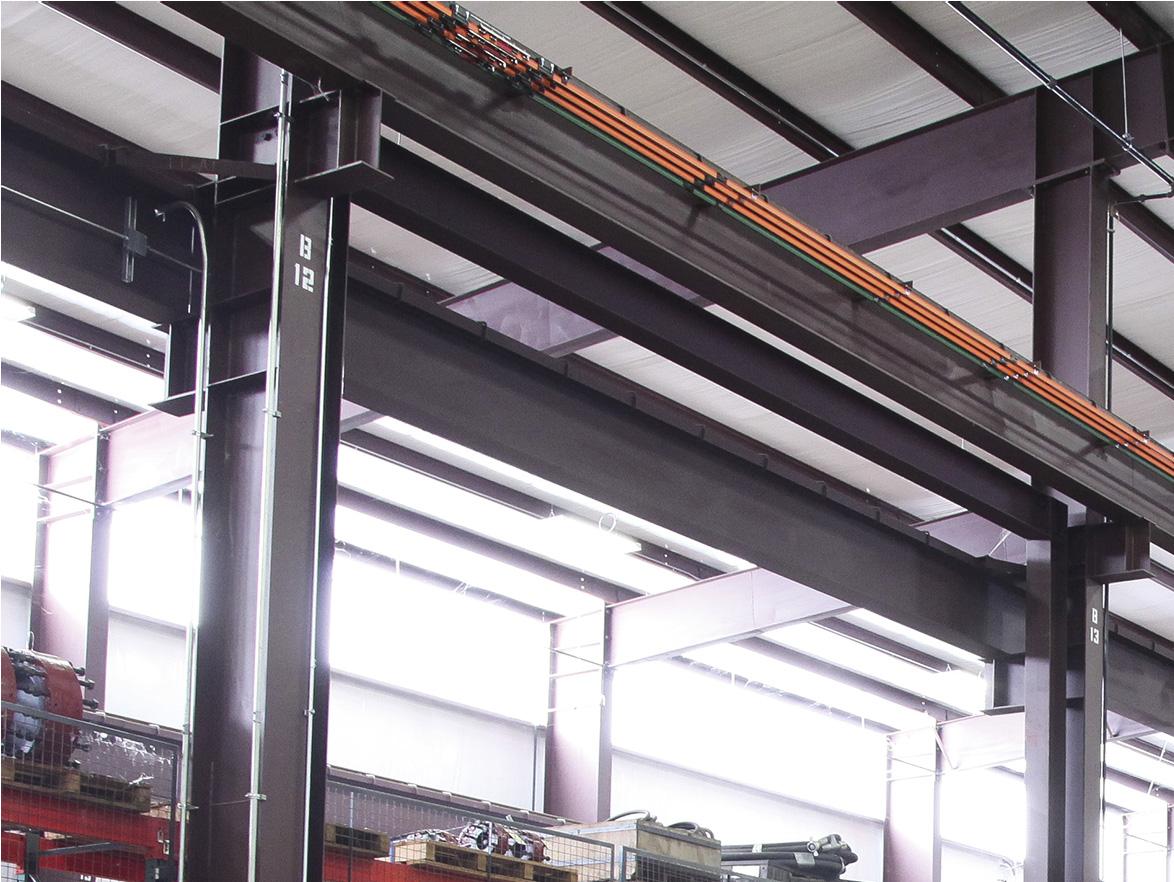
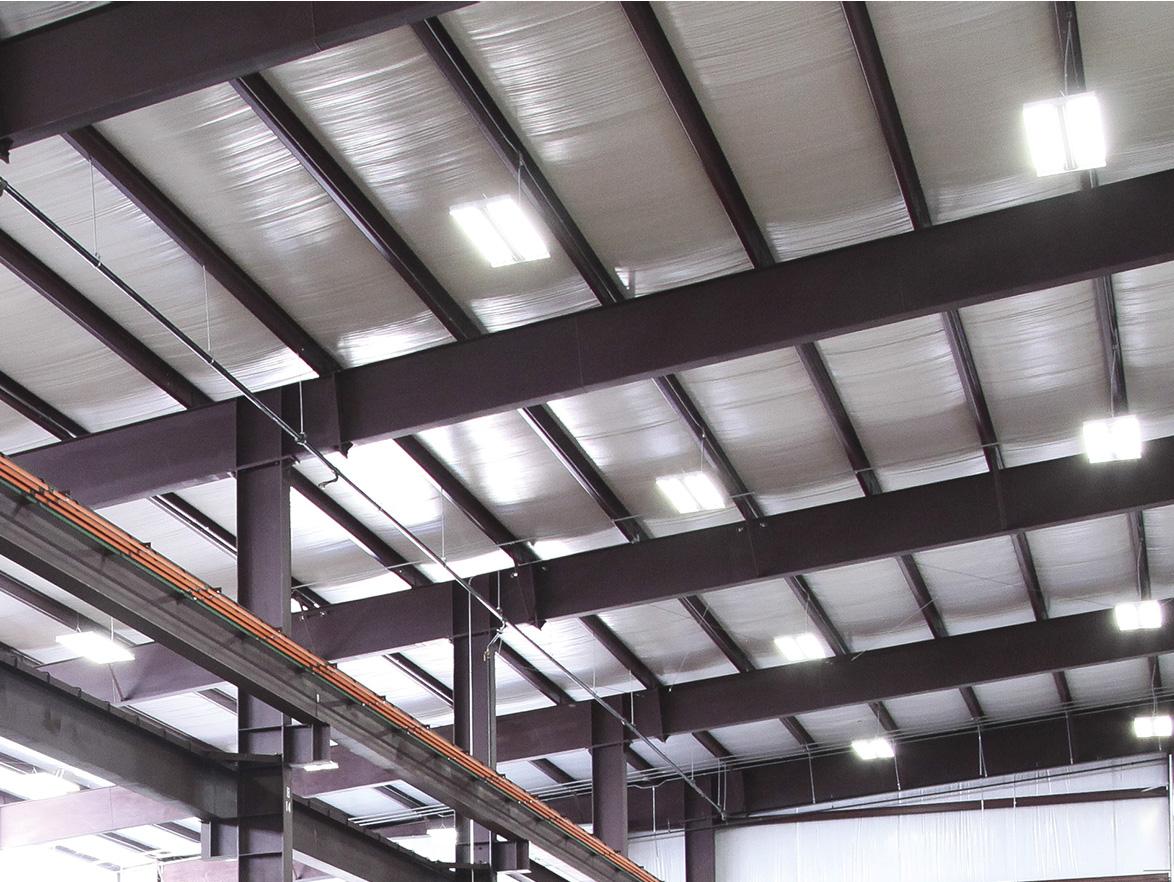
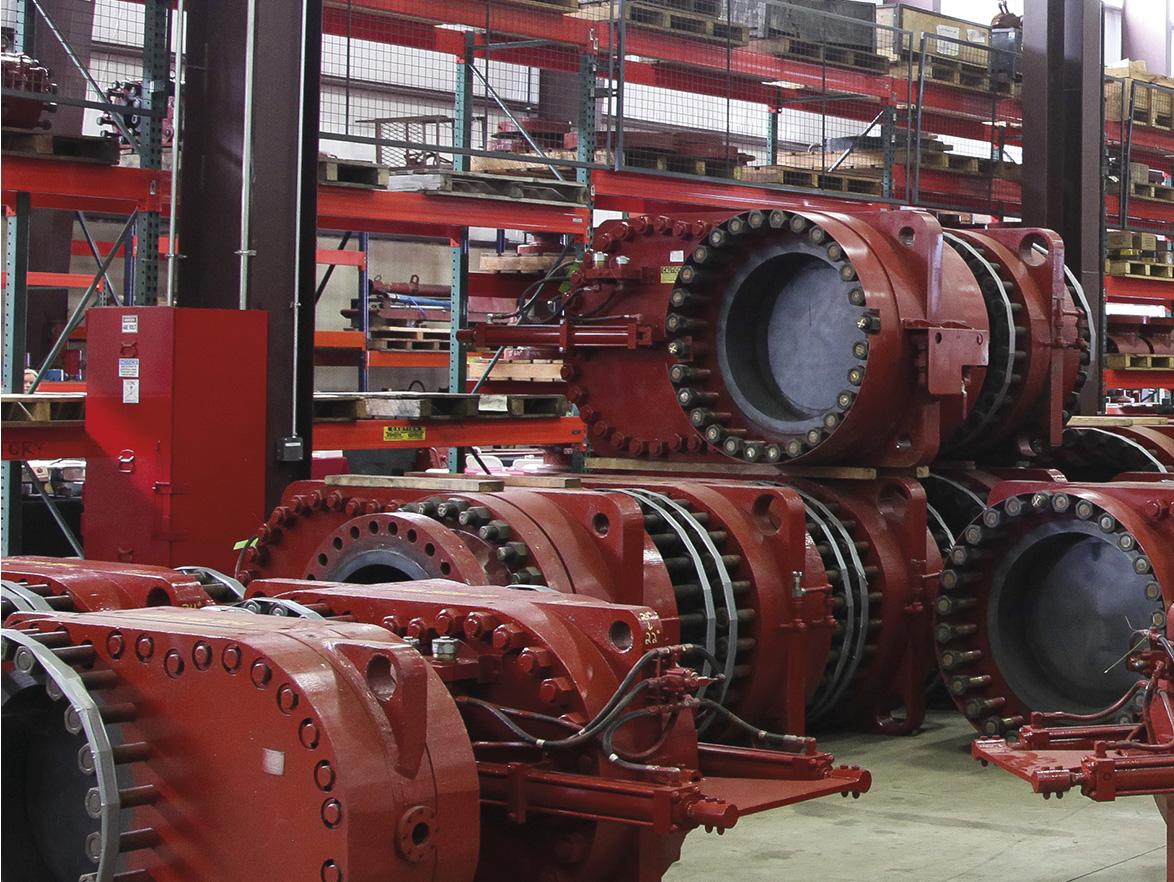
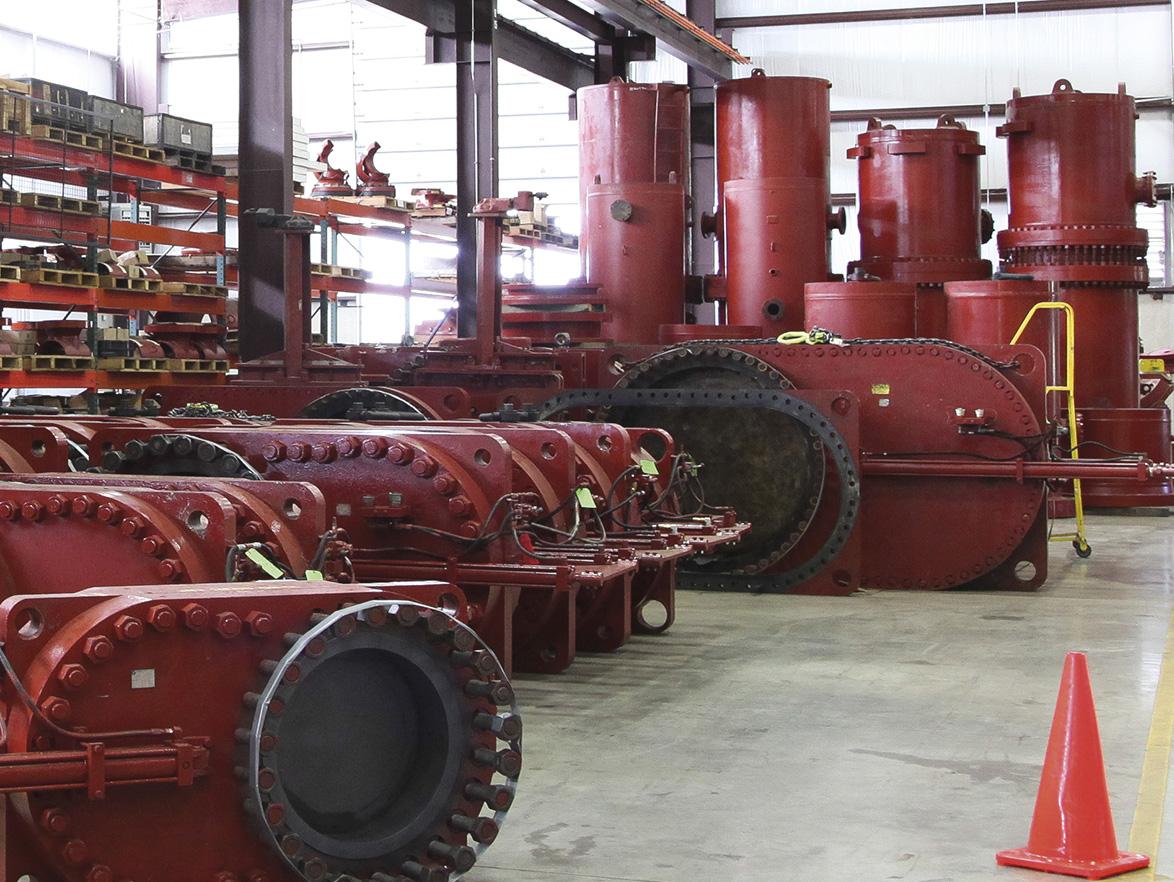
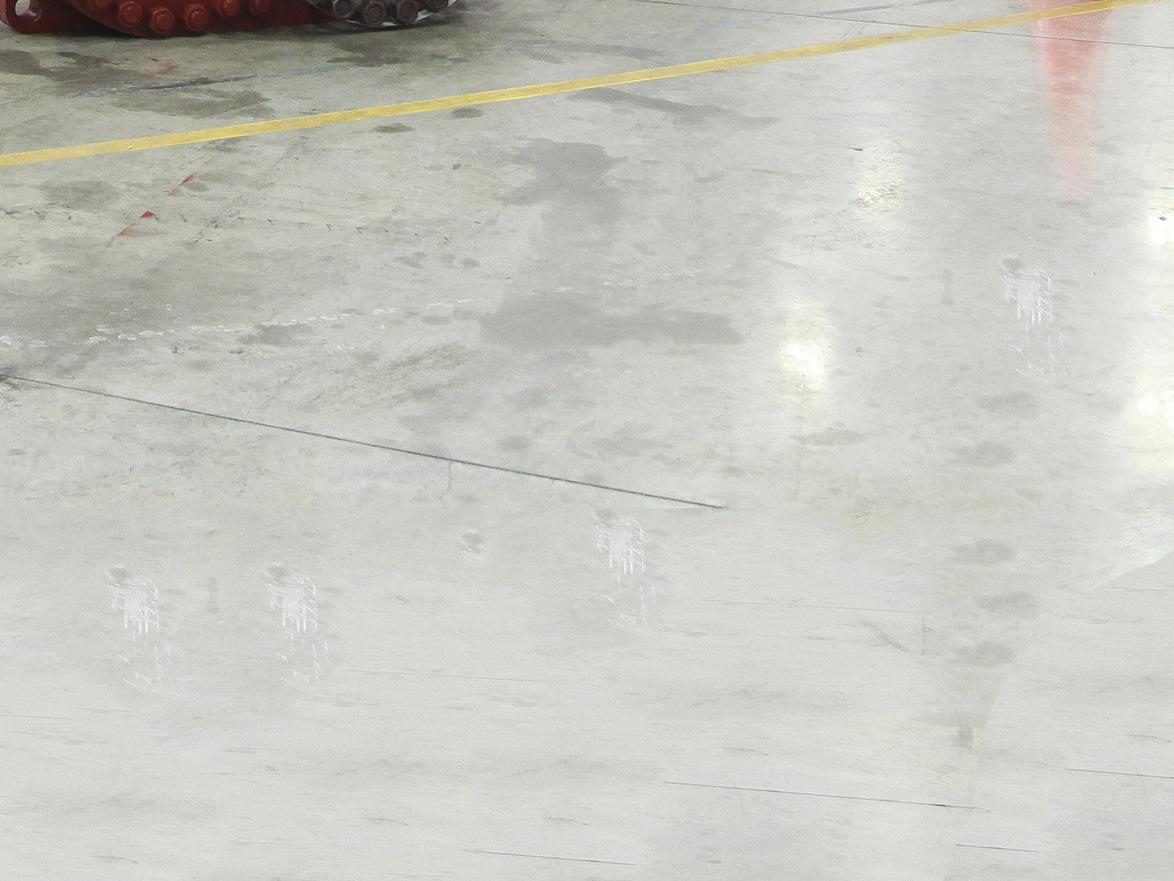
Aaron Madden, T.D. Williamson, USA, details aftermarket services designed to ensure that HT&P equipment is in prime operational condition.
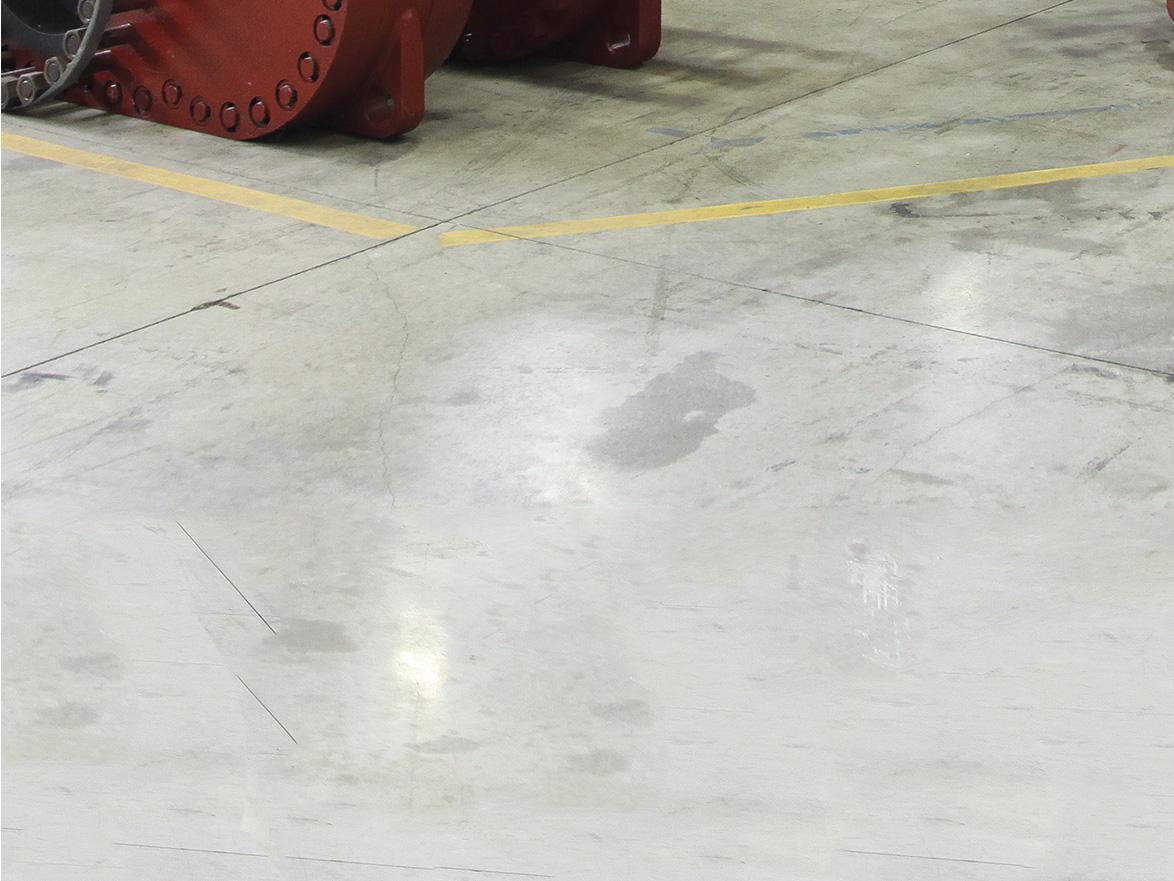
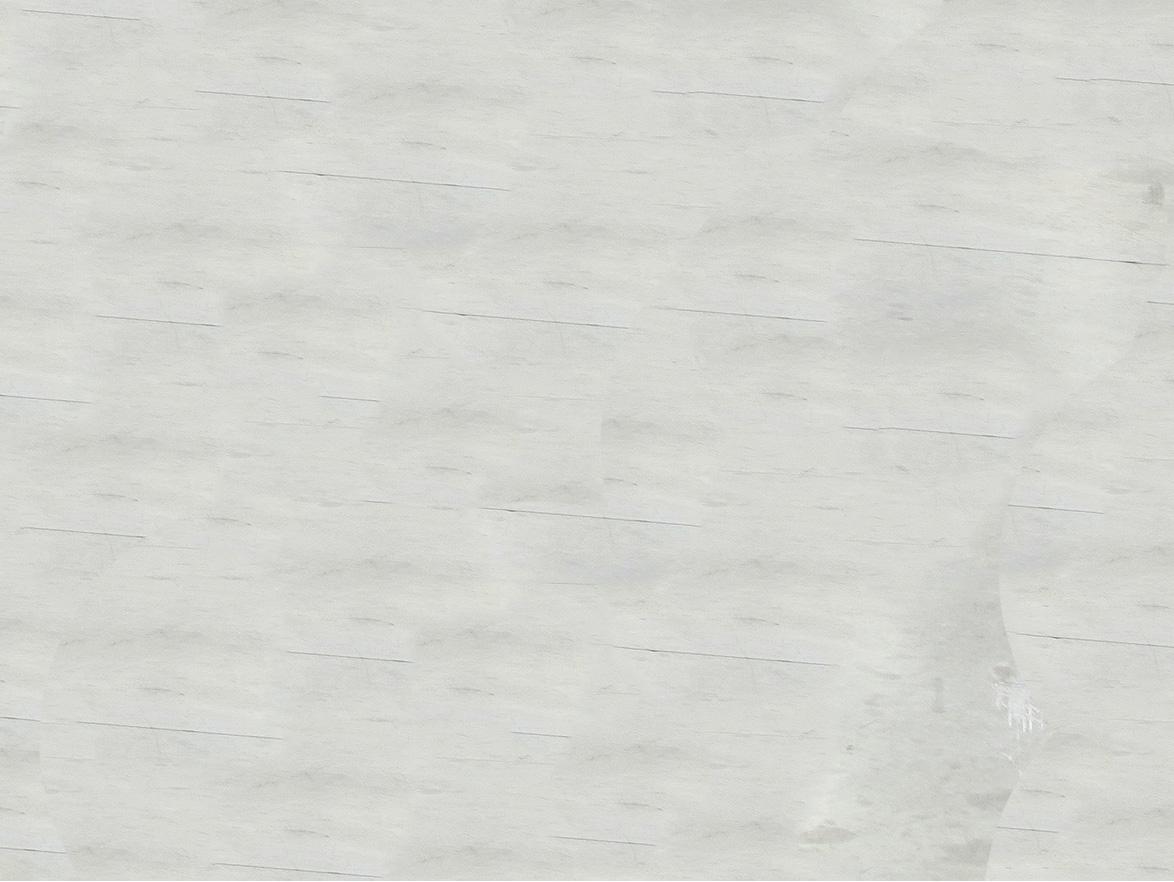
An excavator strikes a pipeline, causing an immediate incident that needs to be addressed quickly. A natural gas pipeline has to be moved to accommodate the construction of a federal highway. A valve change-out requires the decommissioning of a pump house while the system remains in service.
These real-life situations may seem vastly different, but a fast and effective intervention and isolation solution was part of the successful response to each. Without a hot tapping and plugging (HT&P) isolation to create a safe work zone, other activities would have ground to a halt, which would cause additional cost and a reduction in throughput.
Whether you’re faced with an emergency or you’re planning a repair or replacement project, it’s no time to find out the intervention and isolation equipment you own isn’t in prime operating condition.
Yet without regular maintenance, your HT&P isolation tools might not be up-to-date and ready to press into service when needed.
As part of the evolution of equipment maintenance, a growing number of manufacturers, including those who make intervention and isolation technology, are offering aftermarket services to owners of OEM products. Like encouraging someone to get an annual physical or take their car for regular oil changes,
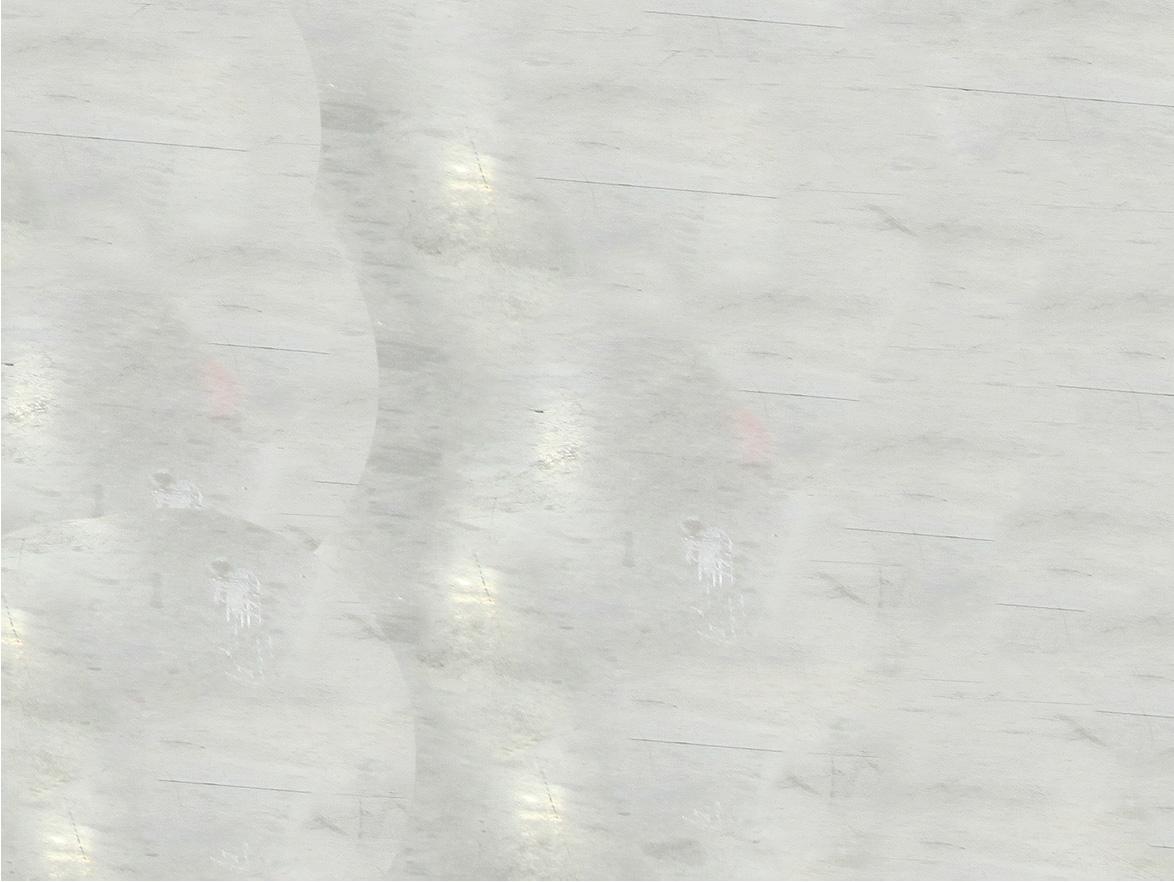
the idea is to provide an equipment wellness check – with the ultimate goals of ensuring operational readiness, maximising investment value and minimising unexpected downtime.
For intervention and isolation equipment, aftermarket services often include maintenance, repairs, overhauls, spare parts, training and emergency response contracts. Whether you use these services in conjunction with your own in-house maintenance efforts or on their own, the result is the same. They allow you to: ) Reduce total cost of ownership.
) Extend the life of your tools.
) Focus on core business functions.
) Reduce warehousing of spare parts and tools required to perform maintenance.
) Improve labour productivity.
) Ensure parts and equipment availability.
) Engage in flat expense budget planning.
Part of continuous improvement The impulse to ‘do better’ has been a driving force in the pipeline industry since the first wildcat well hit pay dirt in the 1850s. Our never-ending quest for improvement, reliability and risk reduction has led to innovations in all areas of the industry, including equipment maintenance and asset management.
At the start, the emphasis was on reactive maintenance. When something stopped working properly, it was taken out of service, and a mechanic restored it to normal operating conditions.
Although many companies still subscribe to this reactive approach, over the past three decades, the industry has also adopted more proactive models. The aim is to identify and fix the reasons things go wrong.
The first significant shift was to preventive maintenance. The idea that you could perform regular maintenance to reduce the probability of failure was considered somewhat revolutionary when it was introduced. Today, though, it’s so entrenched that most young people probably can’t imagine there was ever any other way of doing things.
More recently, two even more forward-looking approaches have followed. The first is predictive maintenance, which is datadriven, condition-based and highly effective.
Often used in coordination with preventive maintenance, predictive maintenance relies on continuous or routine measurements to identify variations from predetermined conditions – signals that failure may be pending, but there’s still time to do something about it. A report from audit and consulting firm Deloitte suggests predictive maintenance – which it defines as “utilising a wealth of process data and advanced analytical methods to predict failures well before immediate action has to be taken” – reduces breakdowns by 70%.
But even a figure like that still leaves room for improvement. Predictive maintenance isn’t the terminal point in the journey towards ‘better’, but it did help lay the groundwork for the next step: prescriptive maintenance.
The next level of better A mix of the best features of predictive maintenance and Industry 4.0, prescriptive maintenance uses artificial intelligence (AI) and machine learning to define root cause issues, identify what will fail and how, and present the user with specific options to avert failure and lead to the best outcome.
Where the evolution leads from here isn’t easy to say, but it seems evident that forward-thinking models will prevail. Regardless of where you are on the maintenance continuum – or where you’re going – aftermarket services can add a level of ‘better’.
MRO programmes Maintenance, repair and overhaul (MRO) programmes help you avoid unscheduled downtime by ensuring your assets are available when you need them.
In general, MRO programmes protect against failure stemming from overuse (mitigated by turn-based maintenance); infrequent use (mitigated by time-based maintenance); lack of robust maintenance and tracking; and unauthorised modifications.
Without parts, machines don’t run, and work doesn’t get done, which is why spare parts inventory control is often an important part of the MRO plan. It’s been estimated that as much as 50% of prolonged unscheduled downtime across all industries can be traced to a lack of spare parts. MRO helps ensure spare parts supply chains can be adequately configured for ultimate efficiency. This begins by understanding your project demands,
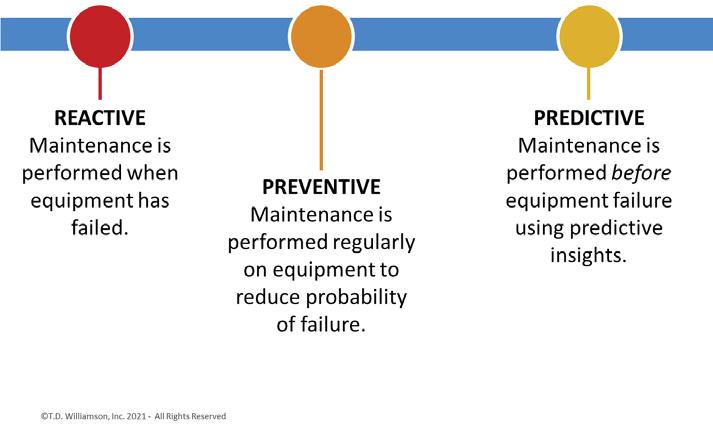
Figure 2. AMS progression.
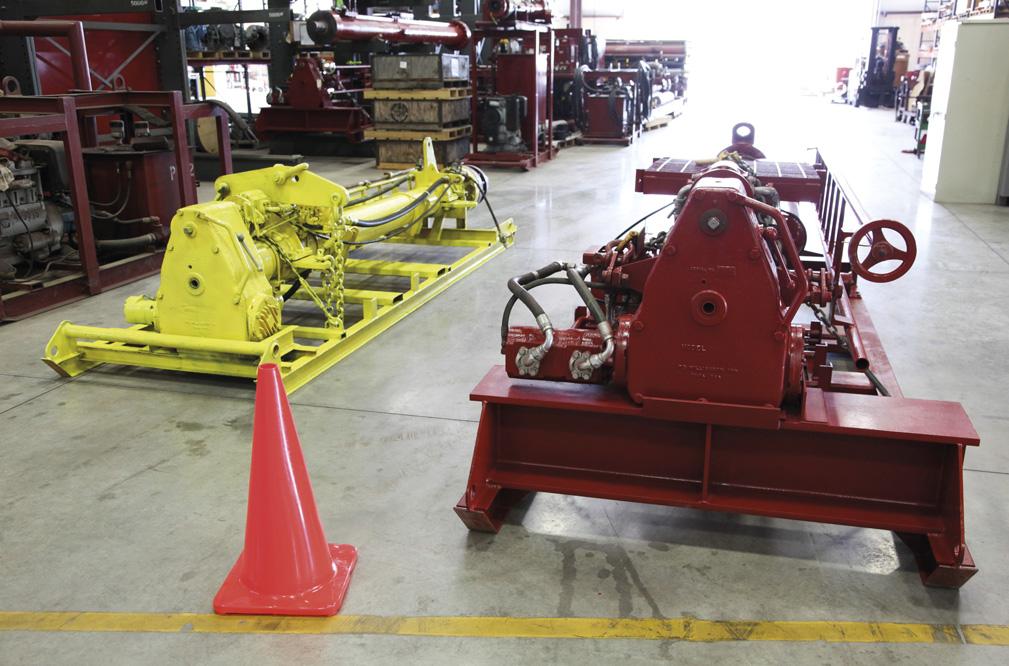
Figure 3. Two tapping machines awaiting maintenance.
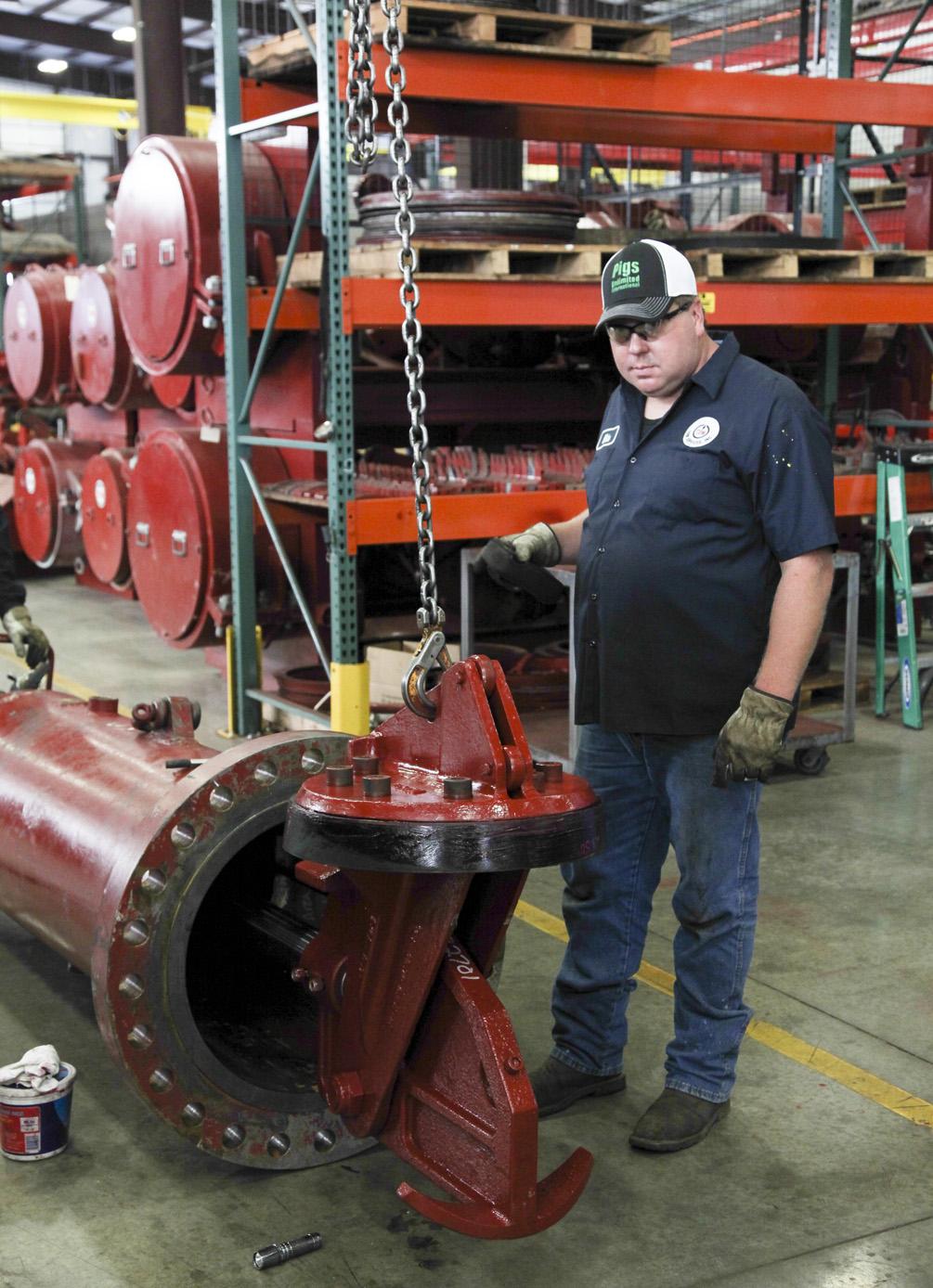
Figure 4. STOPPLE® isolation machine in for routine maintenance.
tooling capacity, tool utilisation and maintenance plans early in the resource budgeting and strategy cycle.
Training Without a qualified driver who understands all the bells, whistles and safety features, a brand new car might as well just sit in the garage. The same is true for fleet investments. When unqualified operators are at the controls, not only is the equipment being underutilised, accidents can happen. Technician training courses ensure a competent operator is maximising your tooling investment.
Maintenance-contractual service agreements These agreements are a prescriptive solution for customer-owned isolation equipment. Tools receive pre- and post-job, minor and major maintenance actions that are proven to lower the overall cost of ownership while extending the life of your investment. At T.D. Williamson (TDW), for example, these agreements allow the adoption of the OEM Fleet Maintenance programme, which has benefited from continuous improvement for more than 50 years.
Emergency response programmes Emergency response programmes are strategic solutions designed to reduce the chaos and overall exposure when operations do not go as planned. These programmes typically begin with an evaluation of customer assets, including where they’re located and expected timelines for response, to inform strategic warehousing and delivery planning. Usually, the OEM will inventory and maintain the customer’s equipment at strategically located facilities, enabling delivery to meet customer requirements. The TDW emergency response solution also includes a maintenance agreement to ensure customer equipment is in prime operating condition.
EROR plan speeds response Though rare, pipeline emergencies are urgent – and something operators prepare for day in and day out.
Despite every precaution, every regulation and every live fire exercise, things can still go wrong. Third-party contractors can miss the markings indicating a buried line. Natural disasters such as floods and earthquakes can erode soil structures which could compromise pipeline integrity.
A few years ago, the operator of a 30 in. pipeline in the Midwestern United States activated its TDW Emergency Response and Operational Readiness (EROR) agreement following a crude oil spill. The EROR agreement – which is still in place today – provides equipment and personnel when there is a leak or other pipeline problem requiring an HT&P solution and can include any or all of these features: ) Stocking of essential fittings to cover all system pipe diameters.
) All HT&P equipment necessary to perform a double STOPPLE® operation with a bypass.
) Welder qualifications.
) Strategic mobilisation locations and mobilisation plan.
) Equipment storage, maintenance and repair.
) Complete training and readiness drills.
In this case, the operator owns a full suite of TDW HT&P equipment, including tapping machines and fittings. Most of it is stored and maintained at TDW facilities in Tulsa, Oklahoma. And although that is 600 miles from the site of the leak, distance wasn’t an obstacle. Crews mobilised the fittings within three hours after the operator notified TDW of the leak; the rest of the equipment was staged and loaded for shipment within 17 hours. In slightly more than a day – just 27 hours – the technicians and equipment arrived at the worksite, and tie-ins were conducted during a 24-hour outage. The STOPPLE isolation plugs were removed and the completion plugs set in one day.
The speed with which the isolation was carried out limited total downtime so the operator could reinstate service as quickly, and safely, as possible.
If you want to improve your operational readiness plan, partnering with an OEM to ensure your equipment is in prime operational condition is one of the most valuable moves you can make. It enables you to maximise your equipment investment, reduce your exposures and ensure everything is prepped to perform when the need arises.
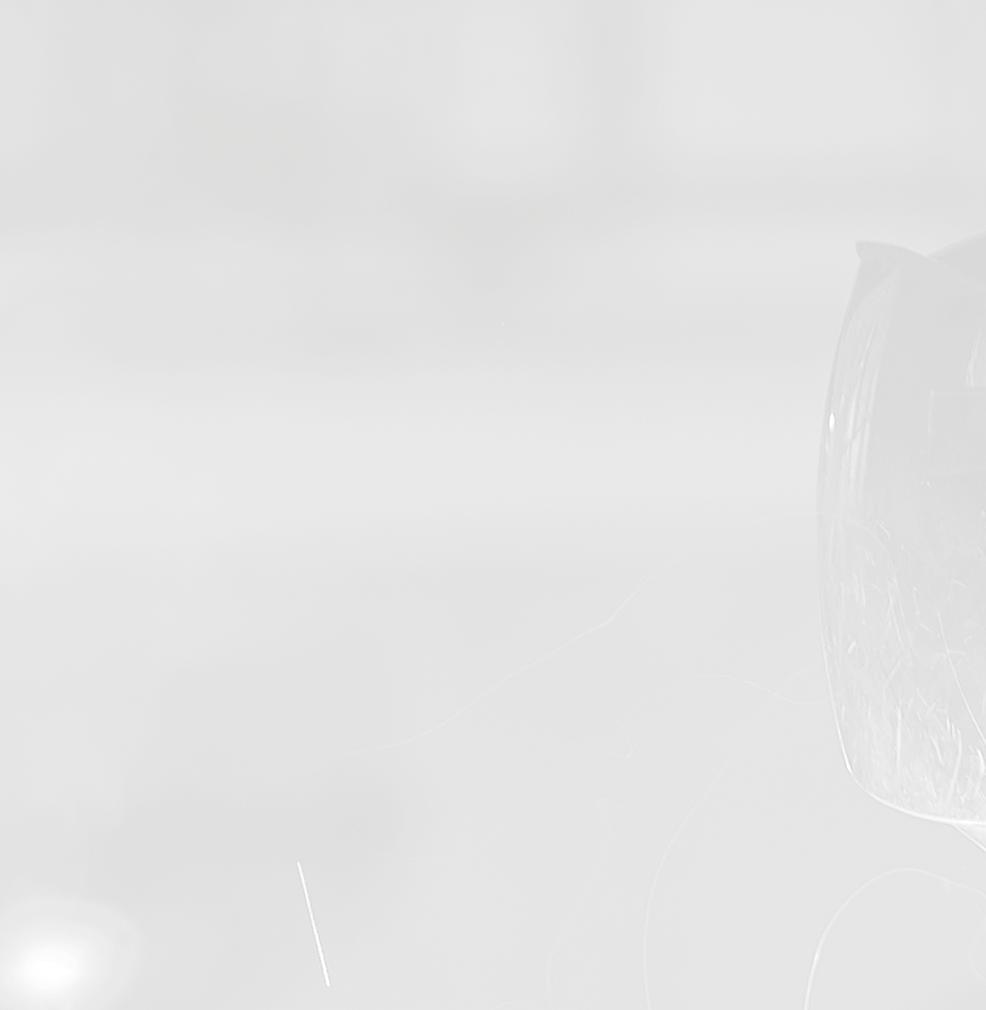
World Pipelines asked Miller Electric Mfd and Huntingdon Fusion Techniques to answer some questions in relation to welding. WELDING

Dr M J Fletcher is a qualified Metallurgist with extensive experience in welding and nondestructive testing. He works as an independent consultant, providing support to a wide range of manufacturing industries on a global basis.
DANNY MORTENSEN, Construction/Fabrication Segment Manager, Miller Electric Mfd. LLC
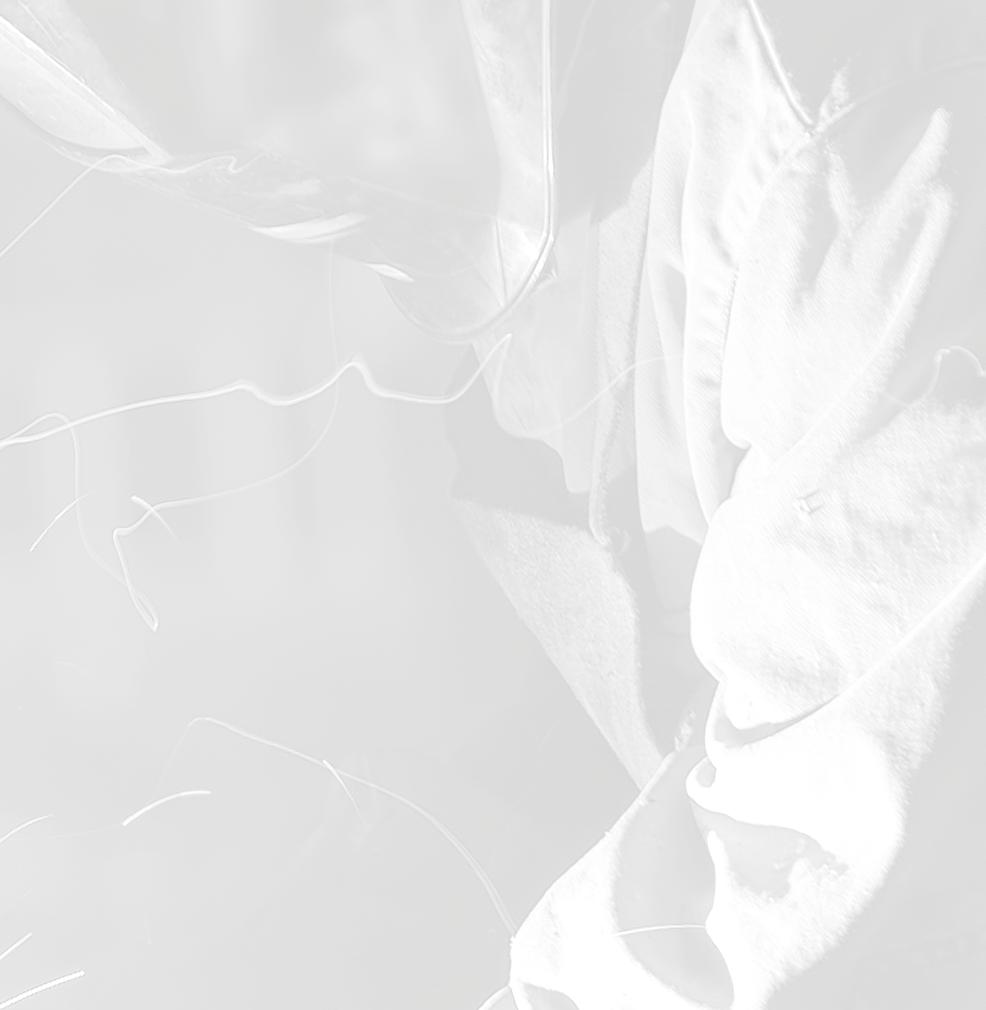
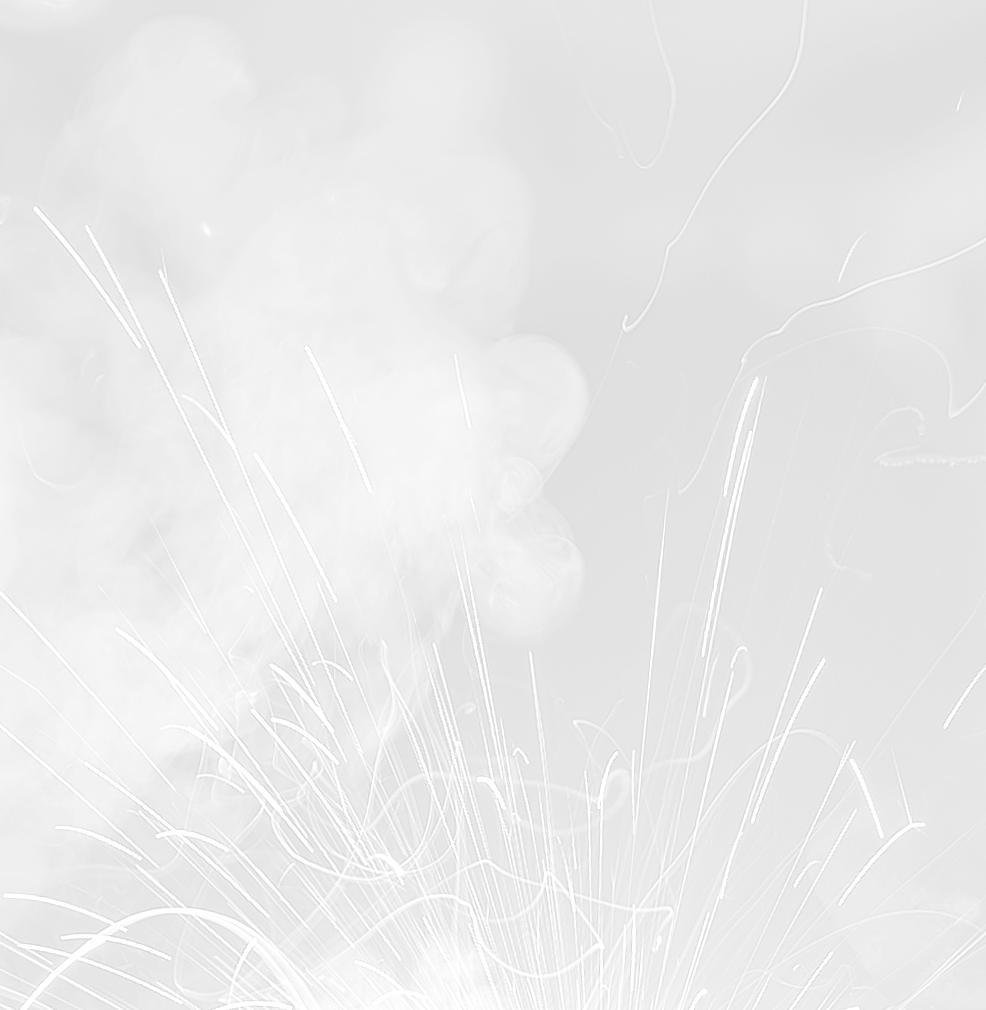
Danny Mortensen is the Construction/Fabrication segment manager with Miller Electric Mfg. LLC. He’s a second-generation welder who has been with Miller in various roles for six and a half years.
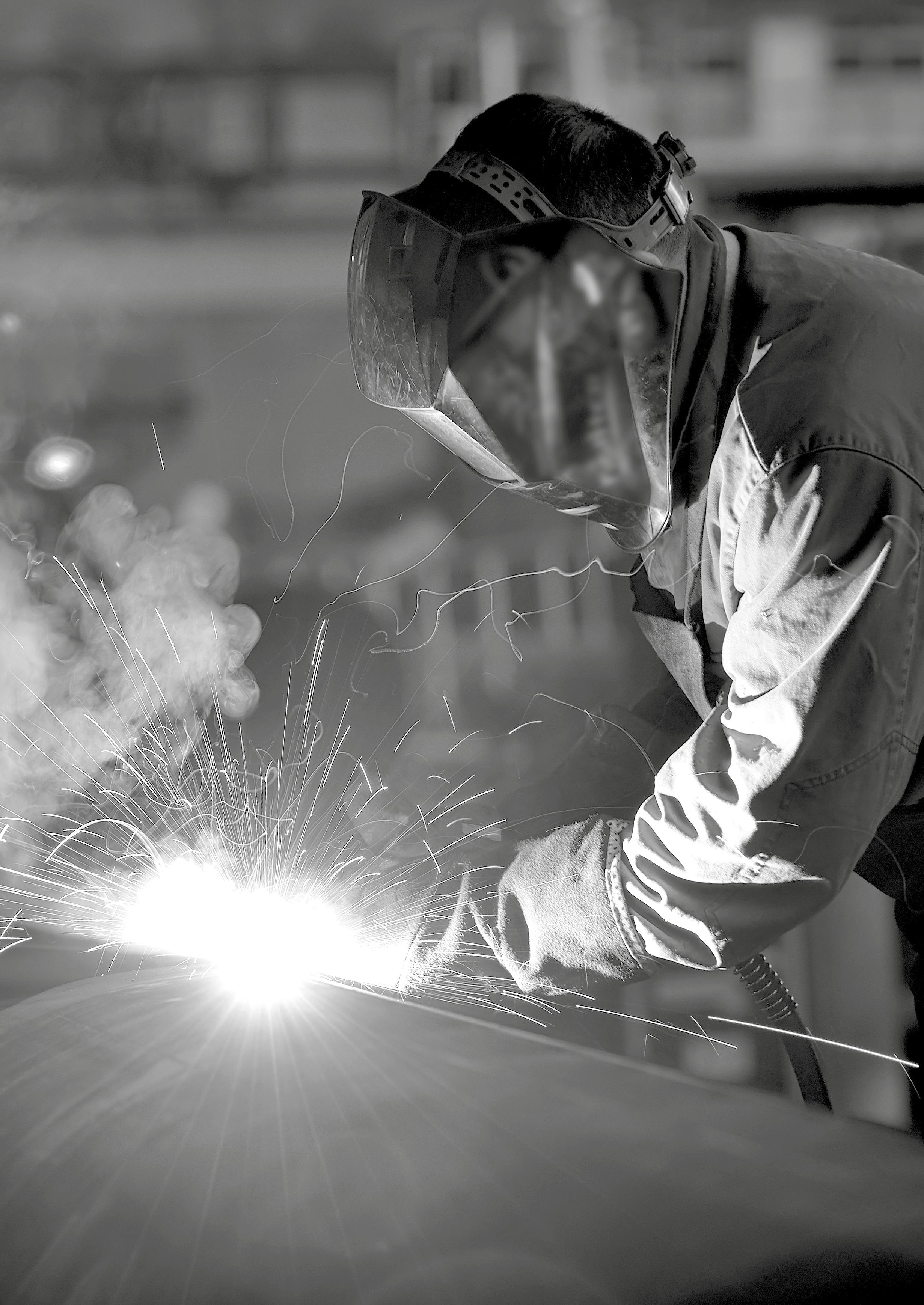
JAKE ZWAYER, Industrial Product Manager, Miller Electric Mfd. LLC
Jake Zwayer has spent seven years with ITW Welding, the last three years as an industrial product manager for the Miller Power Systems Division, where he is responsible for the Trailblazer® and Big Blue® product lines.
What are the most common causes of welding quality issues? What can be done to reduce these?
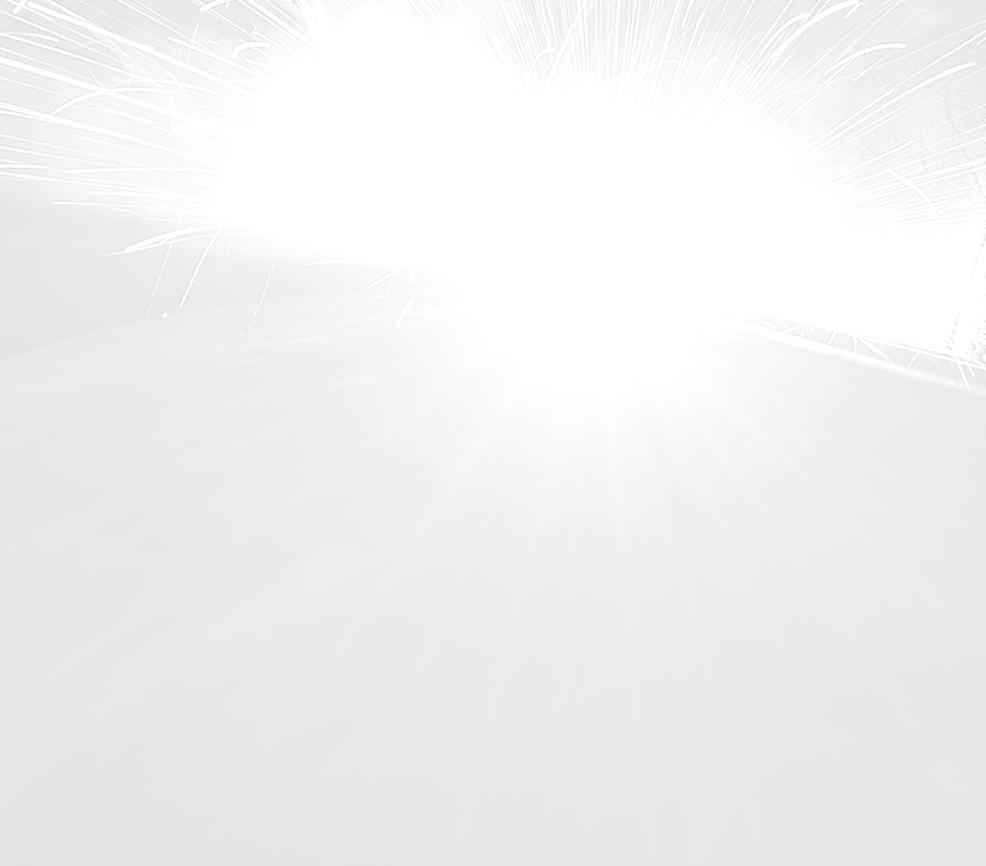
DR M J FLETCHER, Huntingdon Fusion Techniques A significant cause of poor quality is a lack of knowledge about loss of material, particularly chromium, because of oxidation during the welding process. This can be avoided by ensuring that an adequate inert gas environment is provided.
Welds carried out on most metals with inadequate inert gas coverage oxidise. The effect is even noticeable with many stainless steels. To some, the discolouration due to oxidation is an inconvenient feature that can be removed after welding, but this may be difficult and, in any case, costly, especially if access is restricted. Unfortunately, any oxidation can result directly in a reduction in corrosion resistance and in some cases loss of mechanical strength.
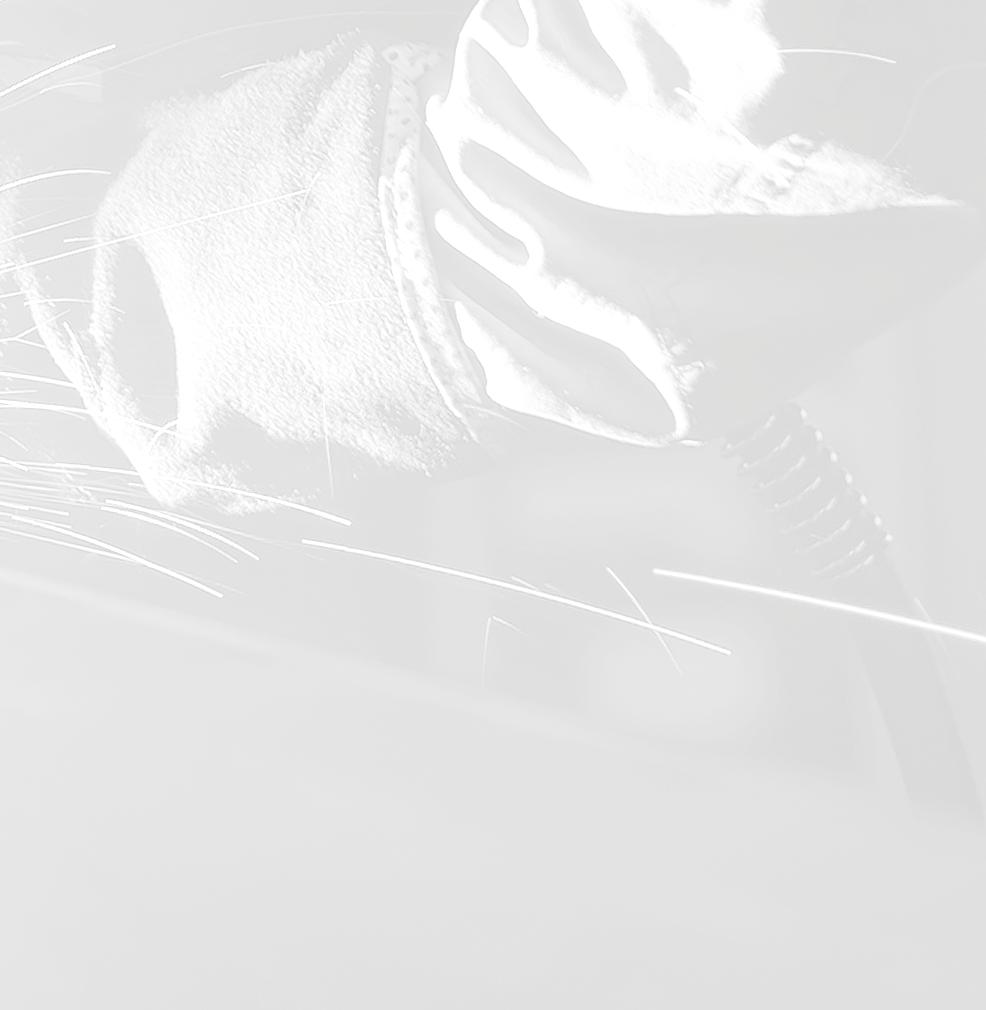
Protection against oxidation needs careful consideration. It will come as a surprise to many that oxygen contents as low as 50 ppm (0.005%) in this protective gas is rarely totally effective. The solution is to use a weld purging system.
JAKE ZWAYER, Miller Electric Mfg. LLC Problems with the root pass or the hot pass are where you see most failed tests for pipeline welders. If there is too much heat used or if the welder does not get through the bevel enough, it can result in a faulty weld. With too little heat in the hot pass, they can also get slag inclusion. The best way to overcome it is making sure the arc is tuned up based on the joint. This is where solutions like Dynamic DIGTM technology from Miller can come in handy, since they allow the operator to tune the arc based on their general preference, while also allowing for in-process adaptability to overcome things like changing joint conditions.
DANNY MORTENSEN, Miller Electric
Mfg. LLC A lot of the issues can be traced to joint prep, whether it be fit-up, the bevel and landing or setup. Then you’re going to have a problem with lack of fusion or suck back or blow back, and then not being able to burn the slag out on the hot pass.
JAKE ZWAYER, Miller Electric Mfg. LLC When you introduce variables caused by bad joint prep or lack of fit-up, it can take a more experienced operator to overcome it.
Detail some recent developments made in welding equipment/ technology.
DR M J FLETCHER, Huntingdon Fusion Techniques The importance of monitoring has been addressed through the introduction of advanced techniques, particularly continuous oxygen and dew point measurement.
Weld purge oxygen monitors using rapid response, accurate instruments, introduced from 1996 satisfied the need for measurement as low as 50 ppm oxygen. Later developments led to instruments capable of meeting site applications whilst reading oxygen levels down to 10 ppm. Many of these products now incorporate software for downloading of data for quality control purposes, fault finding diagnosis, alarm features to warn of high oxygen levels, full colour touch screen control and IP65 rating.
Methods for measuring dew point are well established and equipment is available. However, recent development work has resulted in the production of instruments specifically designed for welding applications. Since integration with oxygen monitors is now possible, this development allows welders to measure and control purge gas oxygen and dew point with a single instrument.
JAKE ZWAYER, Miller Electric Mfg. LLC Dynamic DIG technology from Miller addresses arc adaptability, giving operators the ability to overcome joint obstacles. It provides a smoother, more consistent arc that can be tailored to match application, material, fit-up and welder technique.
New Wireless Interface Control technology from Miller provides the operator with complete control of their machine in the palm of their hand so they can make adjustments where they are working. This provides benefits for weld quality, productivity and safety. In addition, wire welding technologies have progressed rapidly over the years with Smart Feeders and advanced capabilities, like pulsed MIG. We are starting to see contractors realise its benefits in terms of quality and speed of production. The throughput from a wire-based process can really impact a job timeline and the amount of pipe you can lay in a certain amount of time.
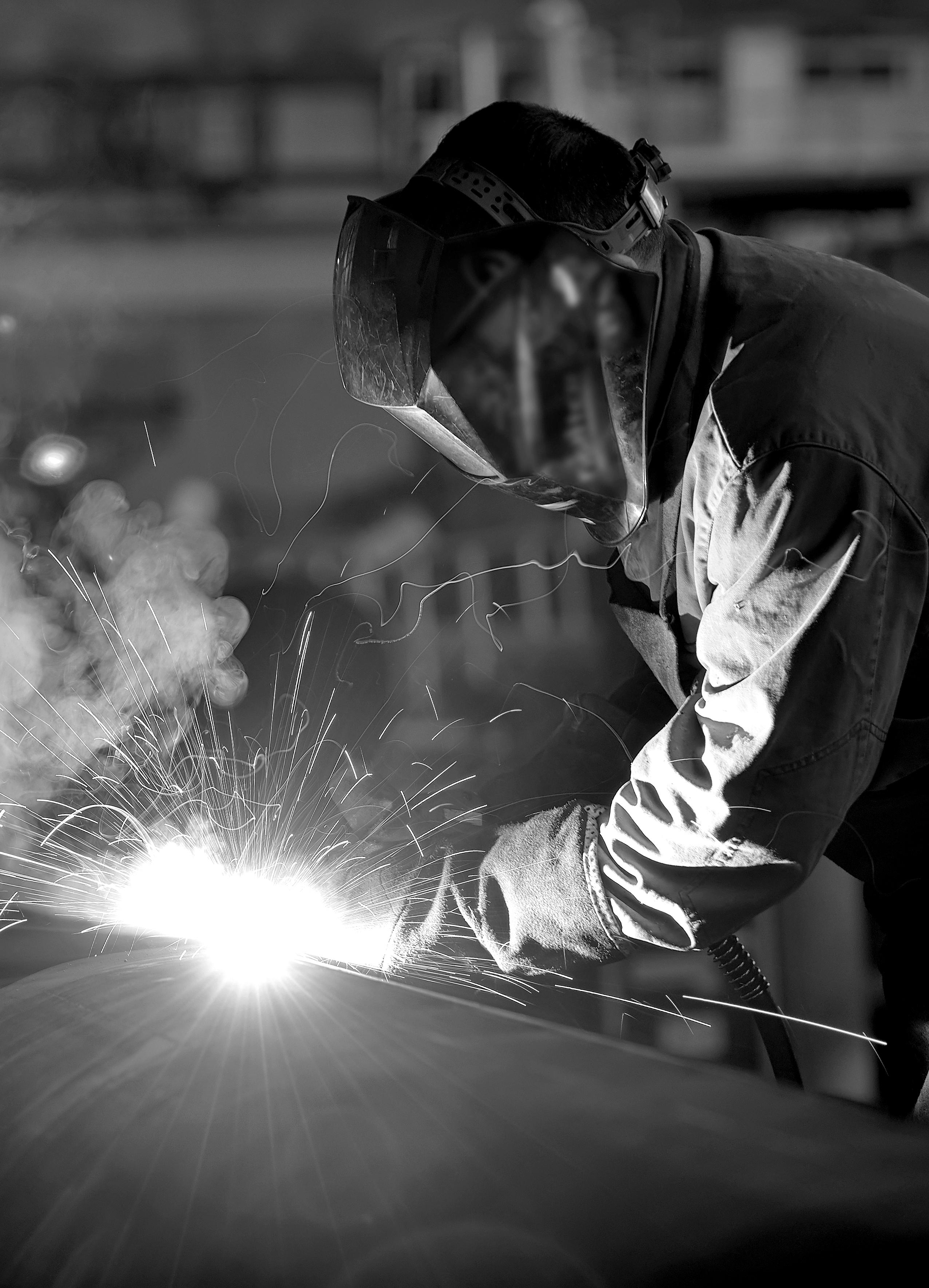
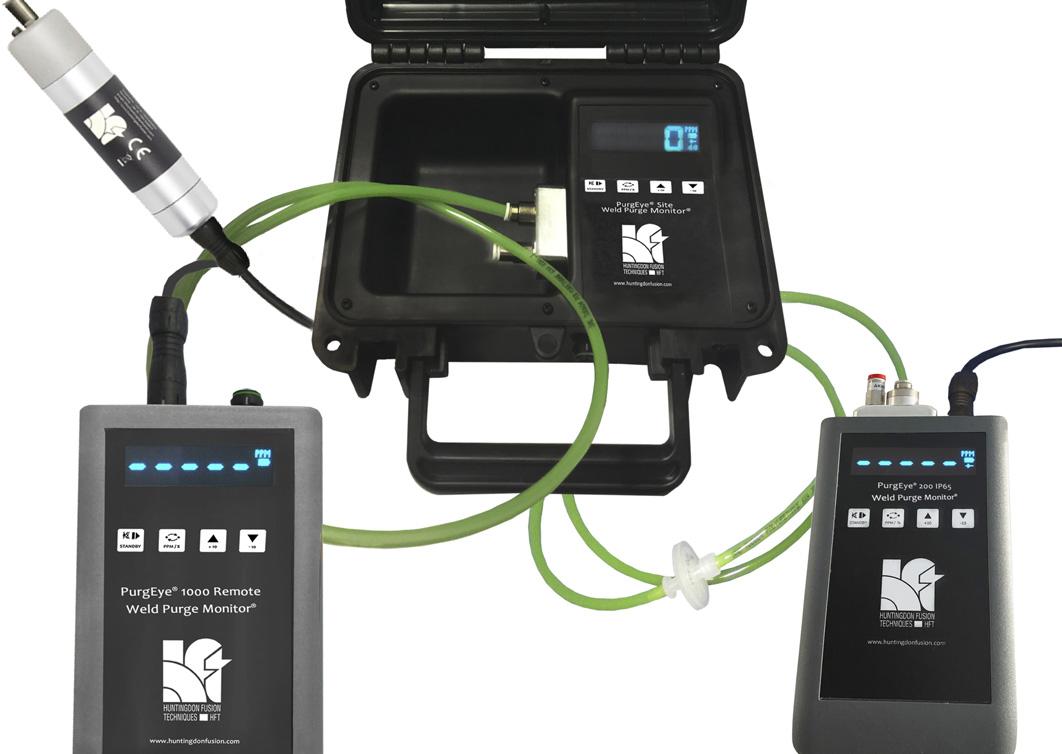
HUNTINGDON FUSION TECHNIQUES: PurgEye API200 PHO-14C API 200,1000 and site. DANNY MORTENSEN, Miller Electric
Mfg. LLC Induction heating is not necessarily new, but it is gaining greater traction on pipelines. They’re able to heat more efficiently, quickly and safely with induction for preheating.
How is the quality of a weld tested? What options are available?
JAKE ZWAYER, Miller Electric Mfg. LLC There’s destructive testing and non-destructive testing. Most pipeline welders will have their welds X-rayed. An X-ray will expose any defects from root to cap. for other, less critical types of welding, they might use non-destructive testing that is less thorough, such as magnetic particle testing or dye penetrant testing.
DANNY MORTENSEN, Miller Electric
Mfg. LLC Phased array testing is becoming more popular in pipelines. It provides clear 3D images.
How are welders kept safe in a potentially hazardous working environment?
DANNY MORTENSEN, Miller Electric
Mfg. LLC Each company has safety protocols in place for many different potential hazards, including environmental and personal safety. Welding equipment manufacturers provide safety precautions in their Owner’s Manuals and on the equipment that contain the basic information needed to install, operate and maintain the equipment. Welders are kept safe by following company procedures and protocols and the equipment manufacturer’s safety precautions. On pipeline rights-of-way, safety meetings happen almost every morning.
What are the biggest hurdles still to be overcome in the welding process?
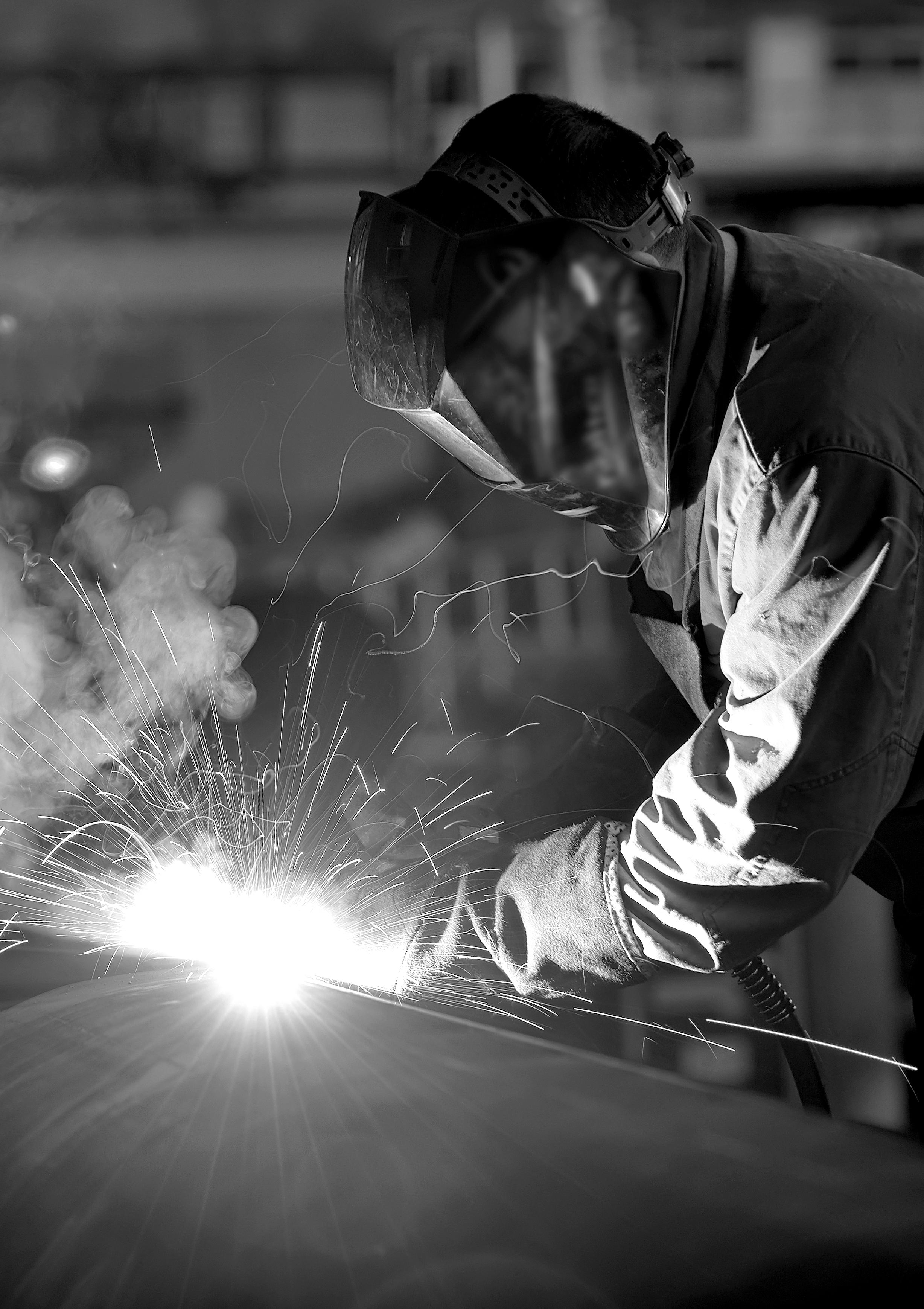
DANNY MORTENSEN, Miller Electric
Mfg. LLC History can often be a big problem in welding. People are reluctant to try new things and adapt because something they tried 20 years ago didn’t work. The technology has changed but the perception hasn’t.
JAKE ZWAYER, Miller Electric Mfg. LLC The metrics that every person in welding is always trying to improve upon are quality and throughput. Whether it’s because joint prep wasn’t done perfectly or some other reason, there will always be factors that affect quality. And as pipe chemistry changes over time, materials get harder to weld and can be more sensitive to welding parameters. Throughput is also a main concern because, with today’s business atmosphere, operations are trying to get jobs done sooner.
DANNY MORTENSEN, Miller Electric Mfg. LLC I think the other challenge that pipeline companies specifically have is public perception. What the public does not recognise or know is how much detail and care goes into a pipeline project. The amount of detail from the welding to the routing to the excavation to the boring is something most people don’t understand.
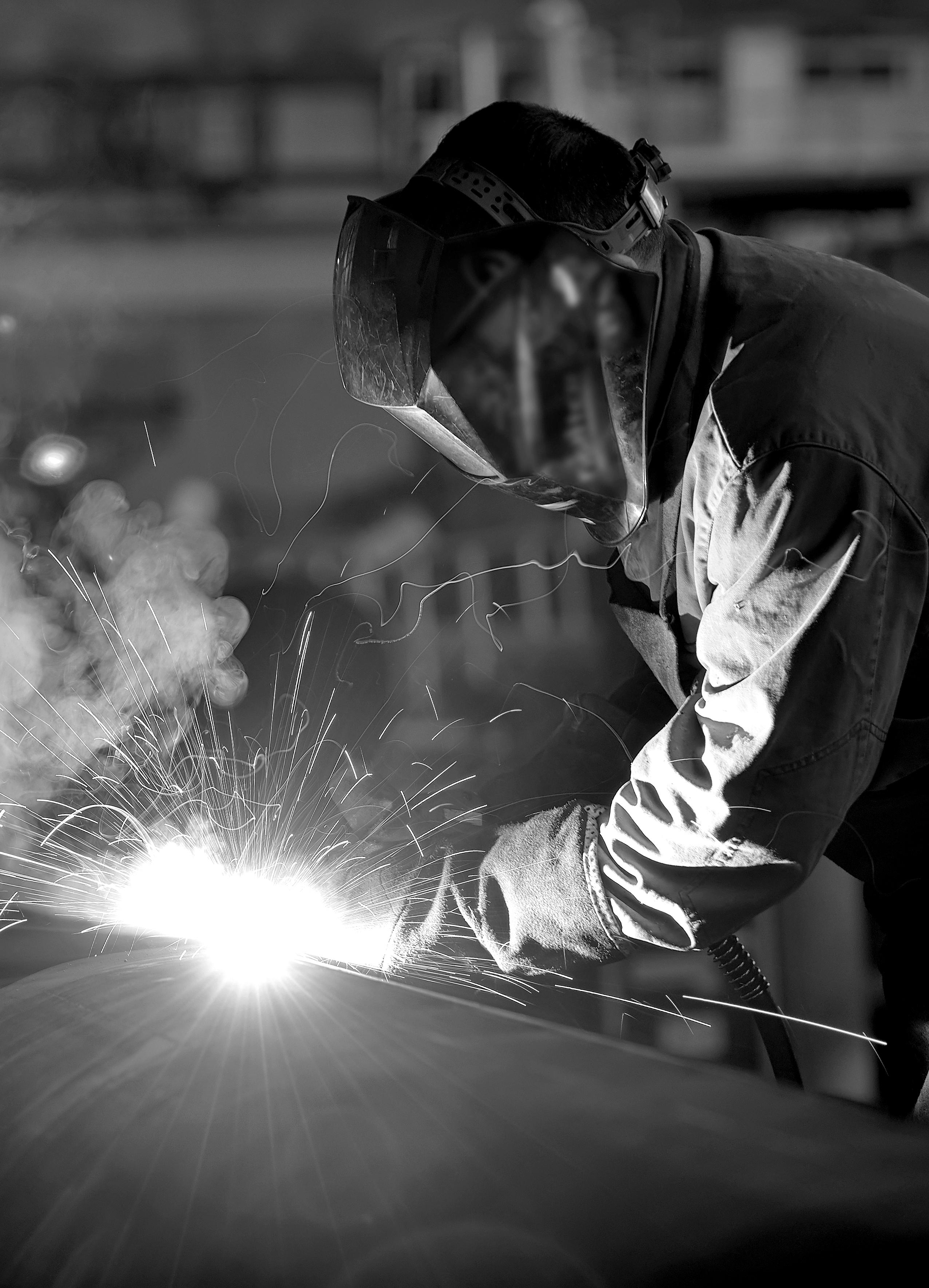
What challenges differentiate welding in offshore and onshore environments?
DANNY MORTENSEN, Miller
Electric Mfg. LLC The types of material used is a big differentiator. It’s more difficult to weld the harder offshore steels than it is to weld the traditional materials used in cross country pipeline. Offshore pipelines also have more environmental challenges that must be considered, including corrosion of salt water, tidal pressures and fatigue. The arc tends to be more erratic, harsh and difficult to control with the steels used in offshore pipeline welding.
JAKE ZWAYER, Miller Electric Mfg. LLC The key difference is definitely pipe chemistry and the weldability of the steel. For offshore applications, they start adding less corrosive, higher strength elements, and the pipe chemistry adds a lot of complexity from a welding and weldability standpoint.
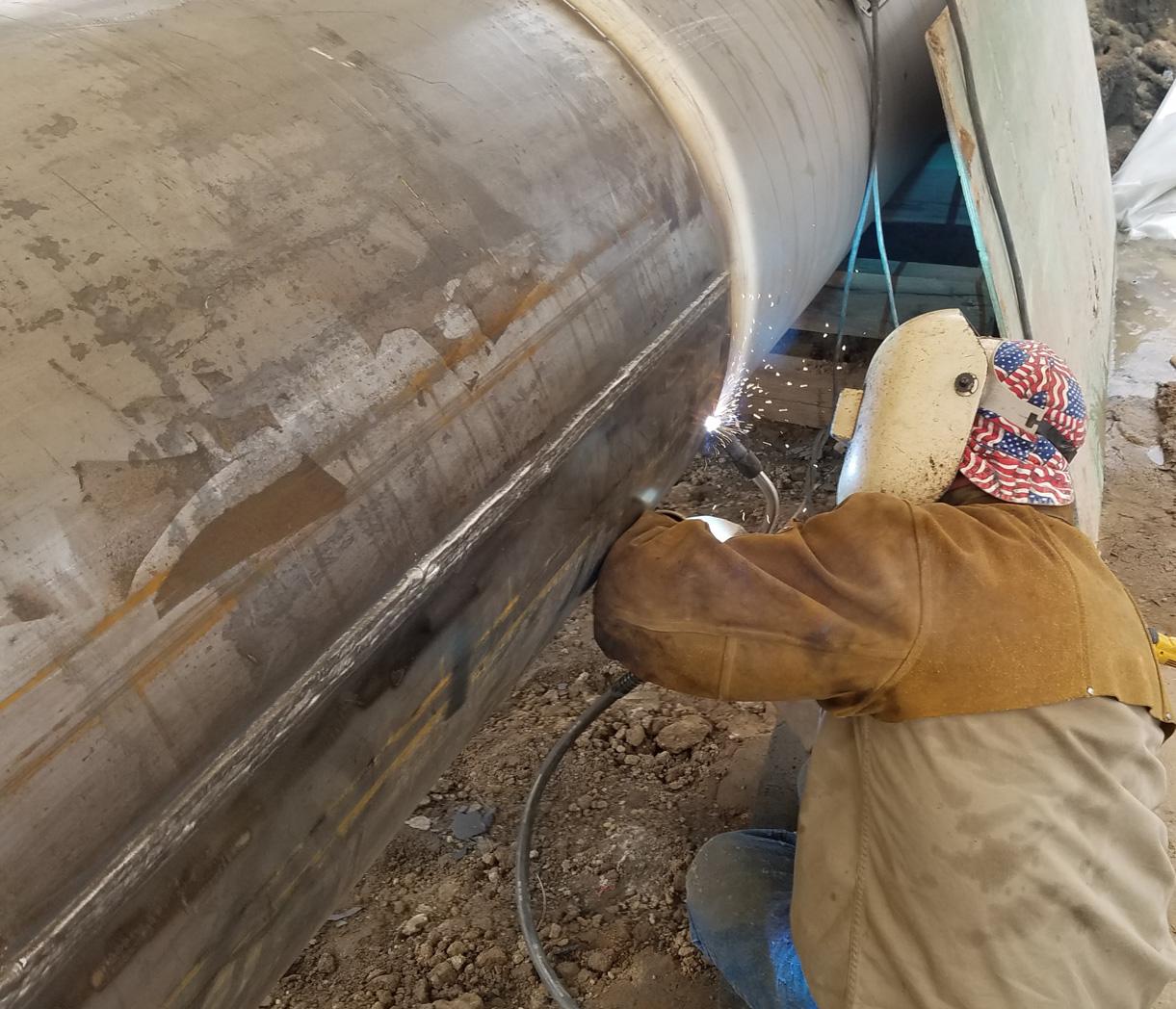
MILLER ELECTRIC MFG. LLC: Sleeve welding.
ADVERTISERS’ DIRECTORY
Advertiser Page
33
BAUMA
CORROSION 2021
DeFelsko
4
47
35
Electrochemical Devices, Inc.
Girard Industries
Integrity 2021
IPLOCA
Maats
Midwestern
NASTT No-Dig 2021
Pigs Unlimited International, LLC
Pipecare
Pipeline Inspection Company
PLCA 2021
PTC 2021
Qapqa B.V.
ROSEN Group
SCAIP S.p.A.
STATS
T.D. Williamson
Vacuworx
Winn & Coales
World Pipelines
55
47
11
59
OFC, 6
2
39
35
IBC
59
56
43
21
IFC
Bound insert
13
17
OBC
9
25
When it comes to automated
VS manual welding, what are the advantages – and disadvantages – of each?
DANNY MORTENSEN, Miller Electric Mfg. LLC Operator fatigue can be greatly reduced with mechanised welding, which can, in turn, help improve productivity, throughput and quality. It makes the troubleshooting and the welding much more consistent from start to finish. But there are always going to be places where you can’t put a mechanised unit, so both types of welding have a place.
JAKE ZWAYER, Miller Electric Mfg. LLC There are benefits and downsides to both. On the manual side, there’s operator error and a reliance on someone with a pretty unique skillset. The benefit of manual welding is you can send a welder out to do a job, and they can drag some leads out and make a weld. That’s one of the reasons that people have been so resistant to change, because it’s so simple at its core. From a mechanised perspective, it takes some of the skill out of the process but adds a slightly more complex setup. Instead of a welder who can go out and heat the pipe and start welding, you have more set-up time and system complexity. The upside is that once set up with a semi-automatic system, throughput and efficiency can be drastically increased compared to traditional stick welding.
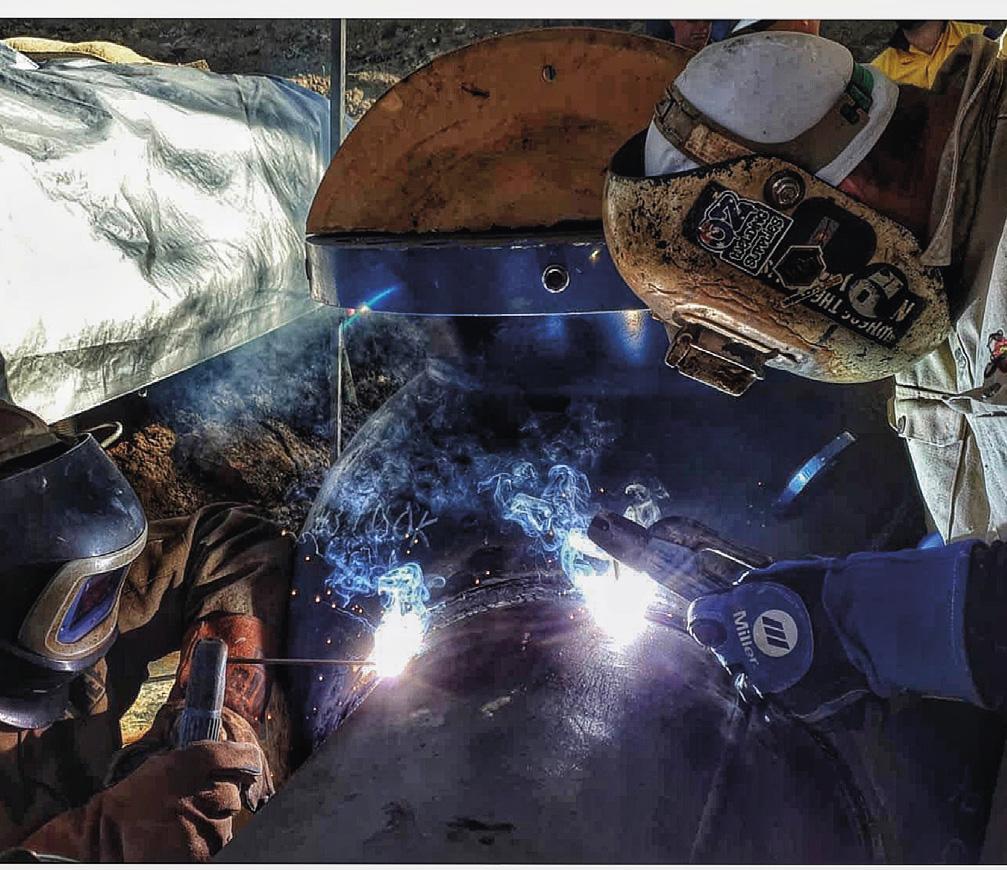
MILLER ELECTRIC MFG. LLC: Safety protocols are key for protecting welders.
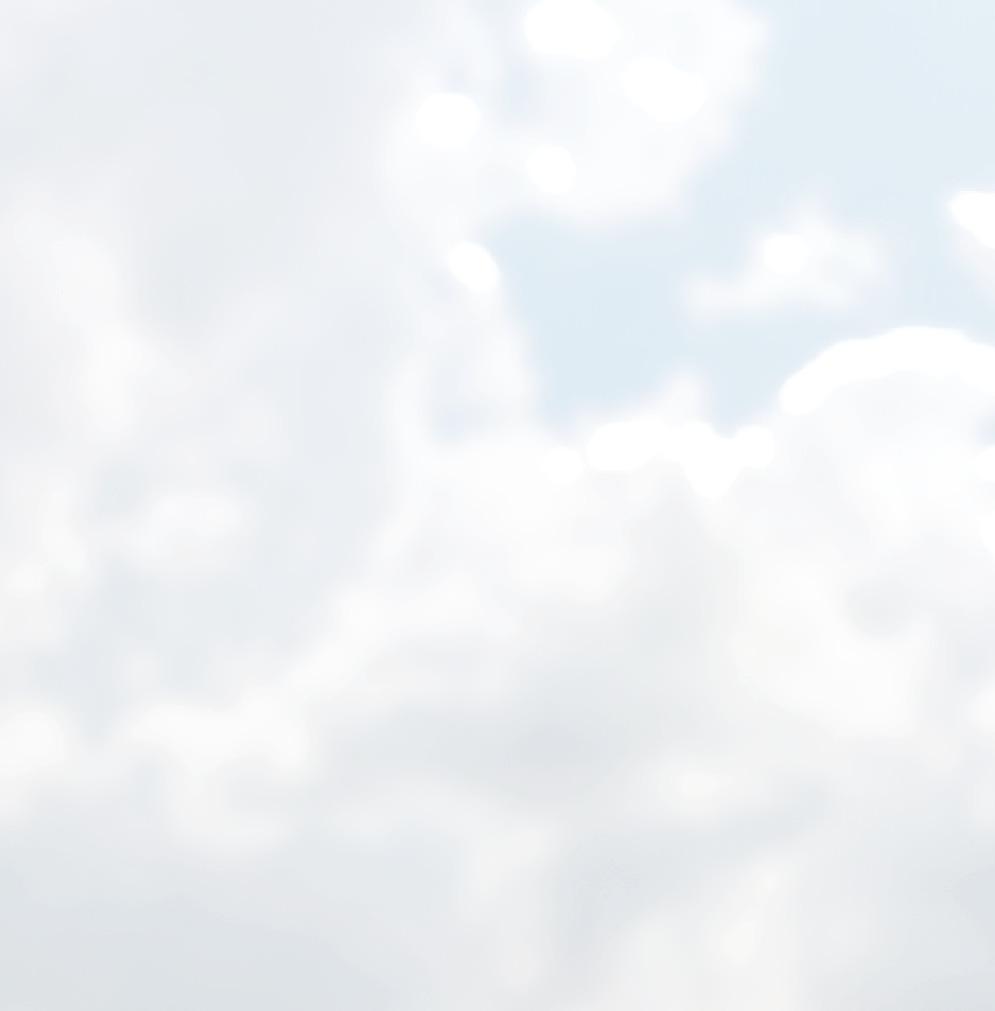
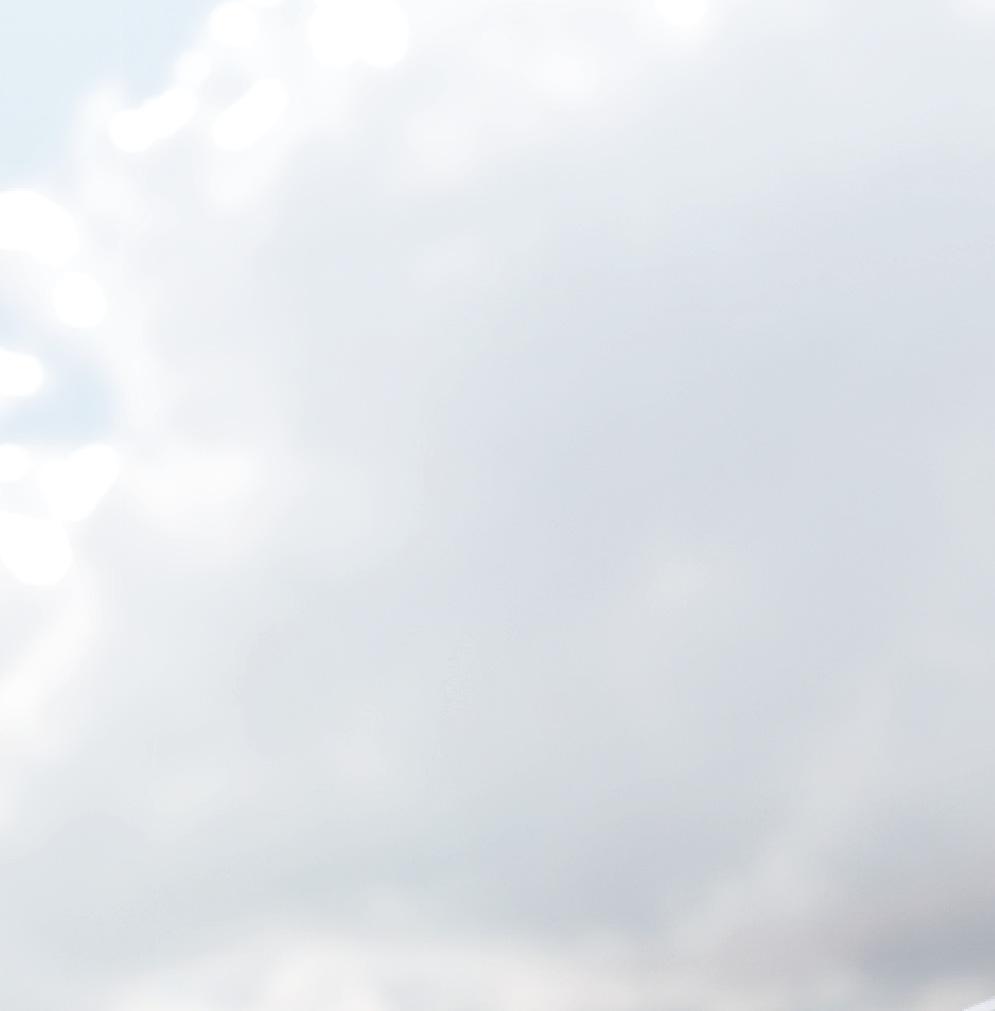
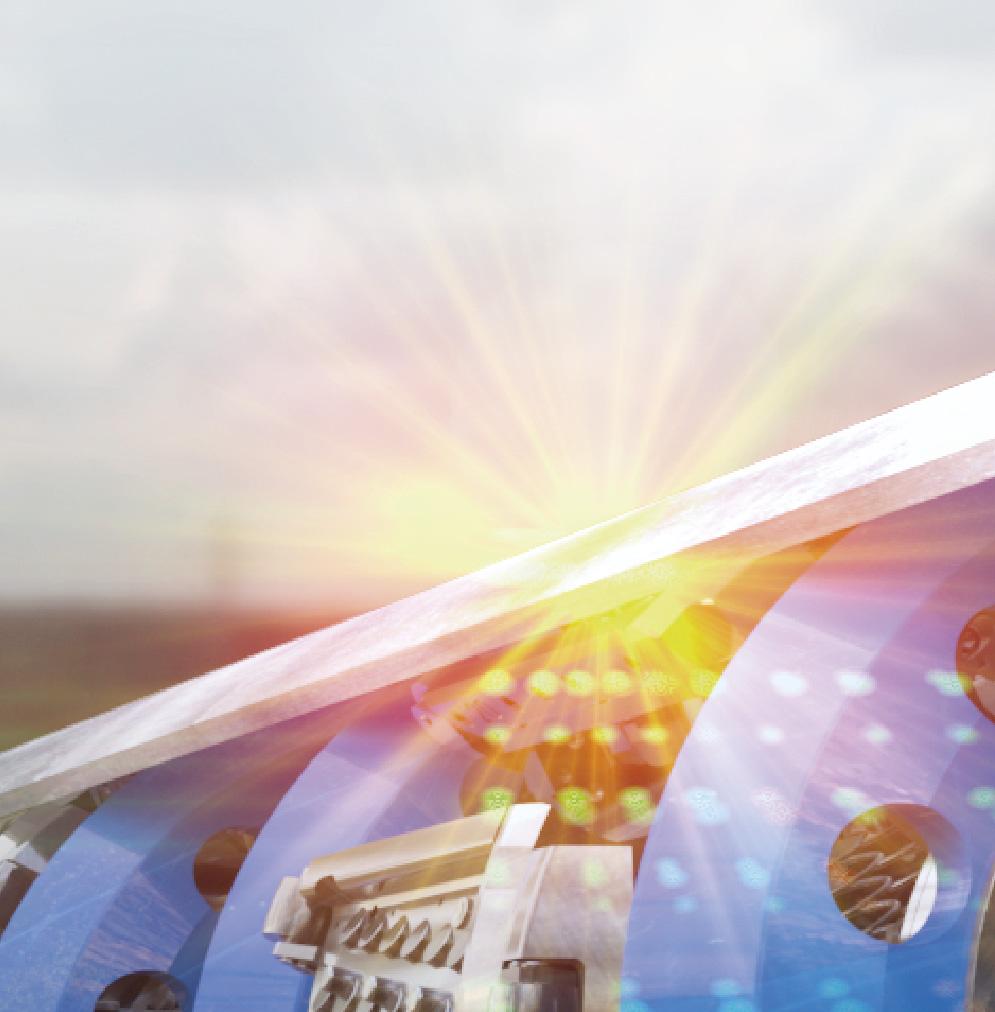
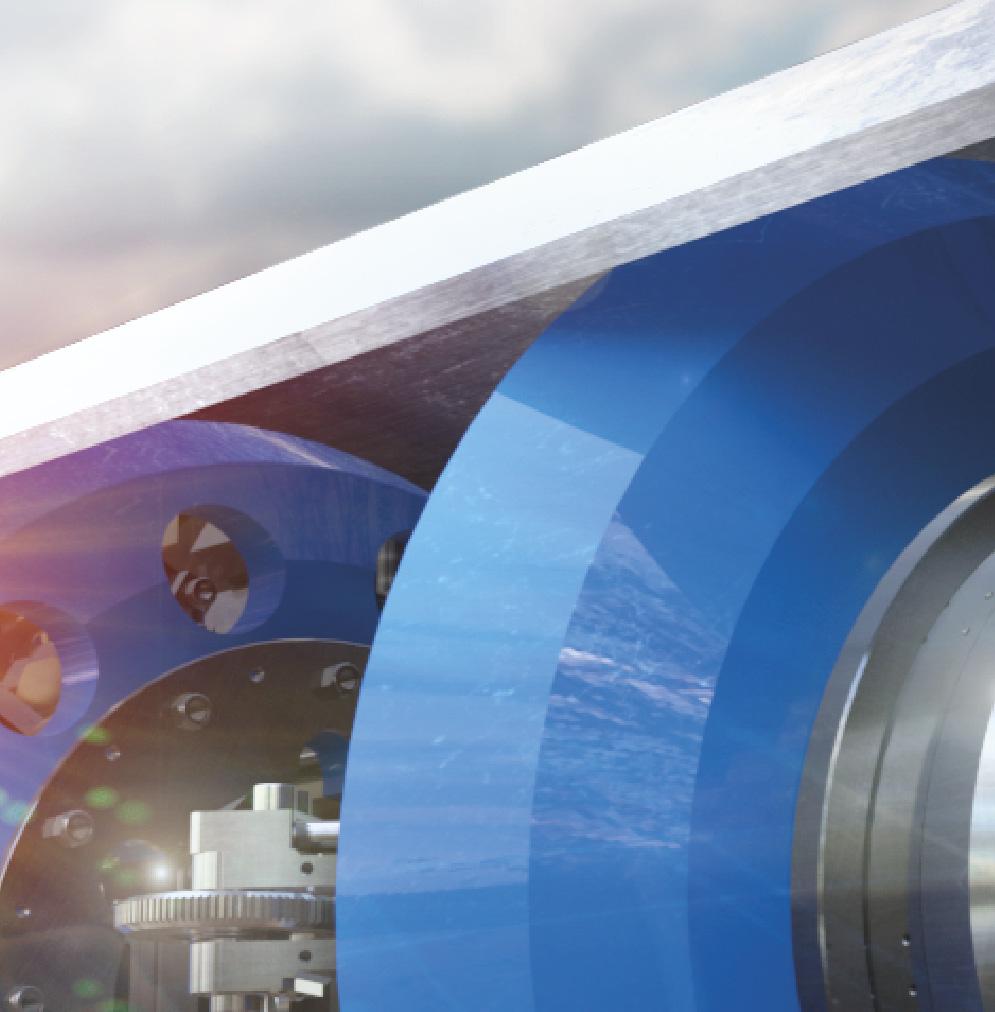

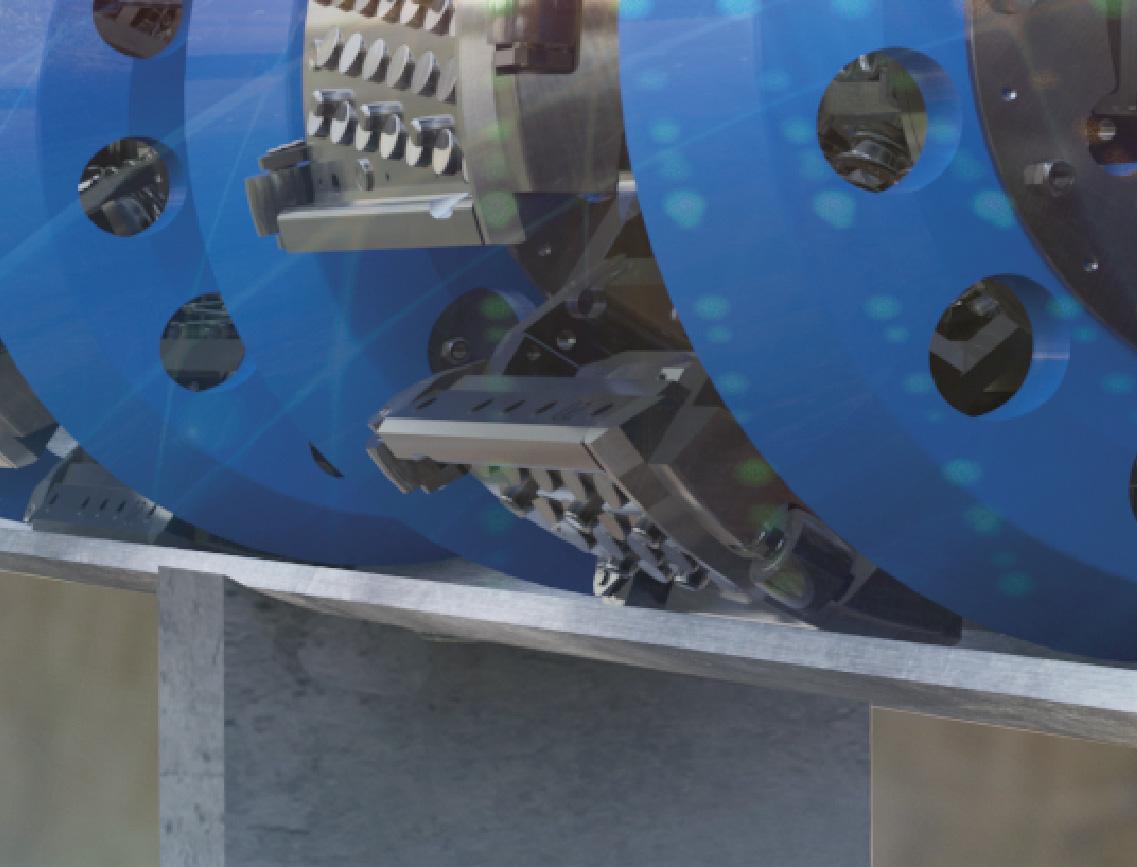
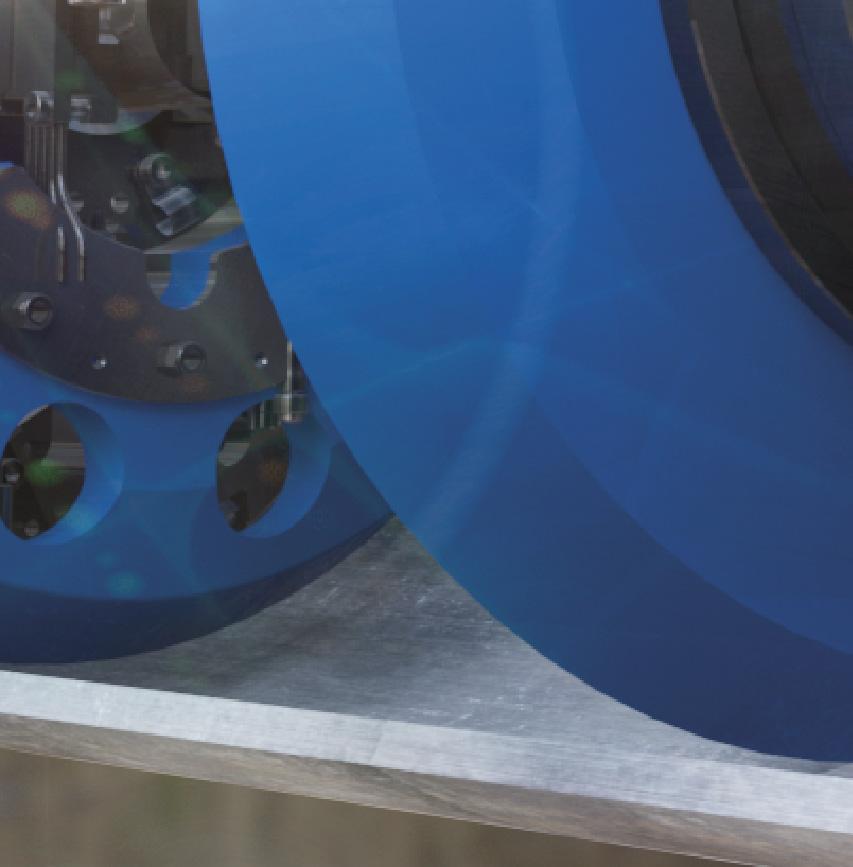