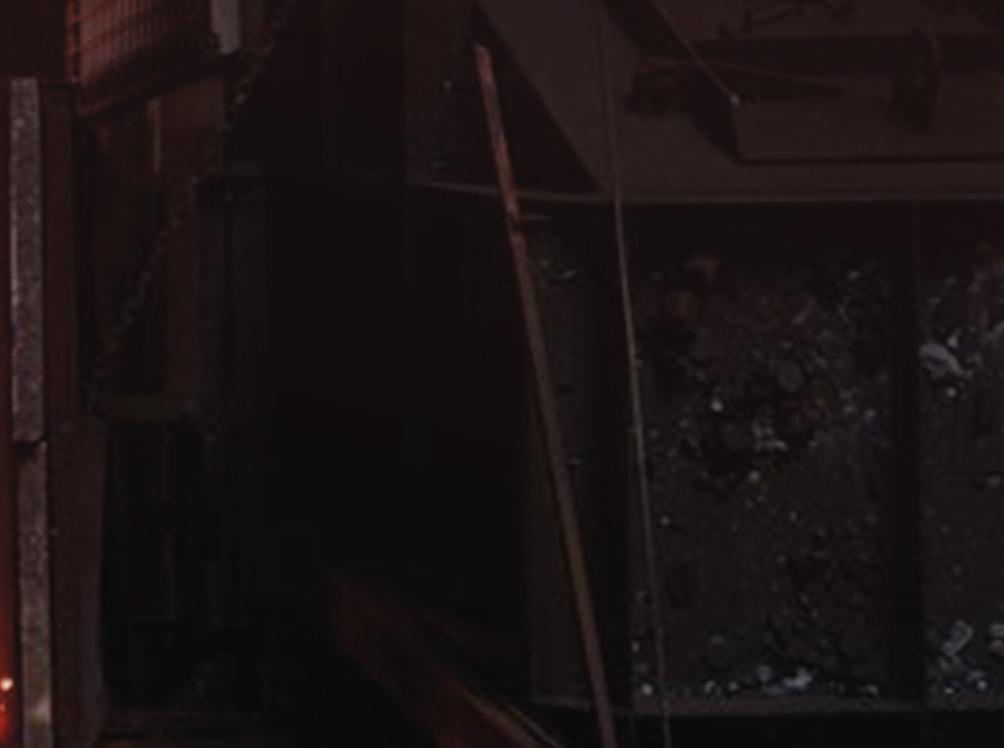
9 minute read
Sustainable steel in the making
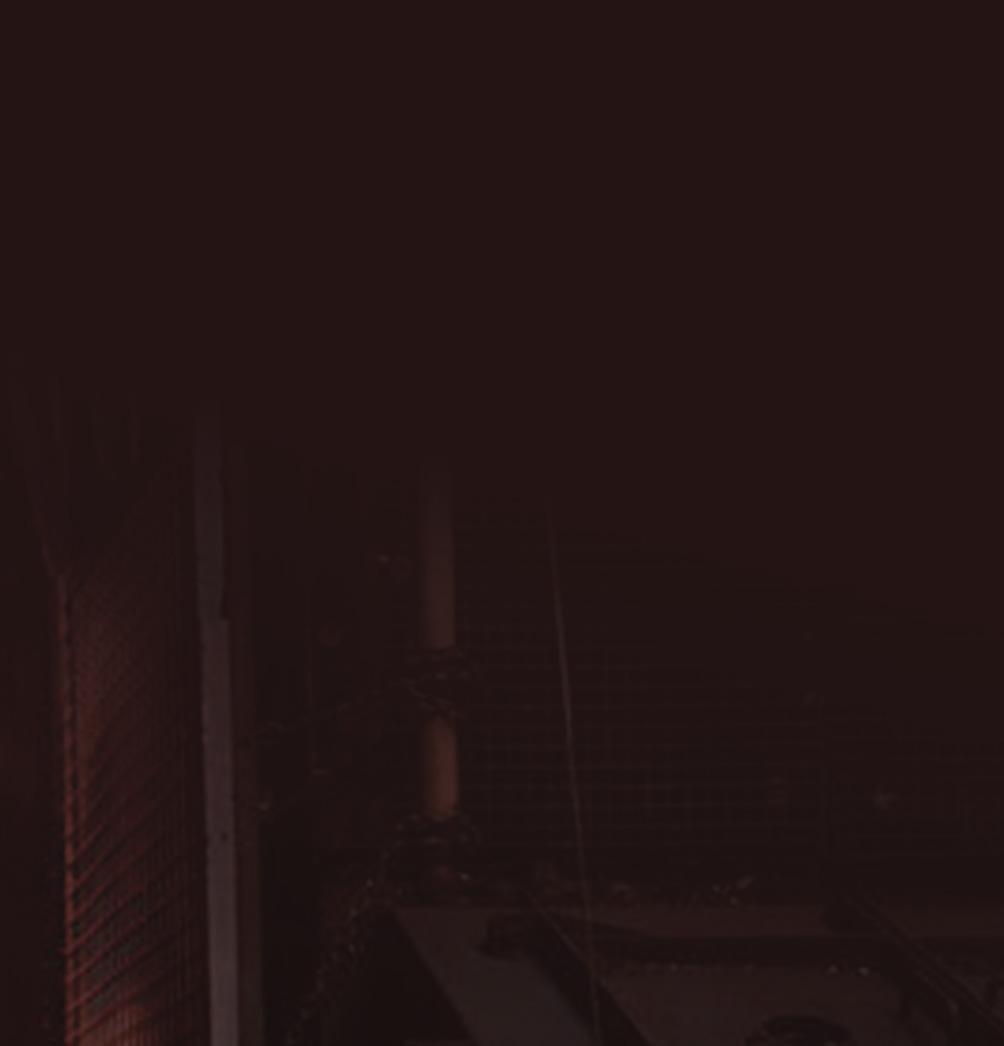
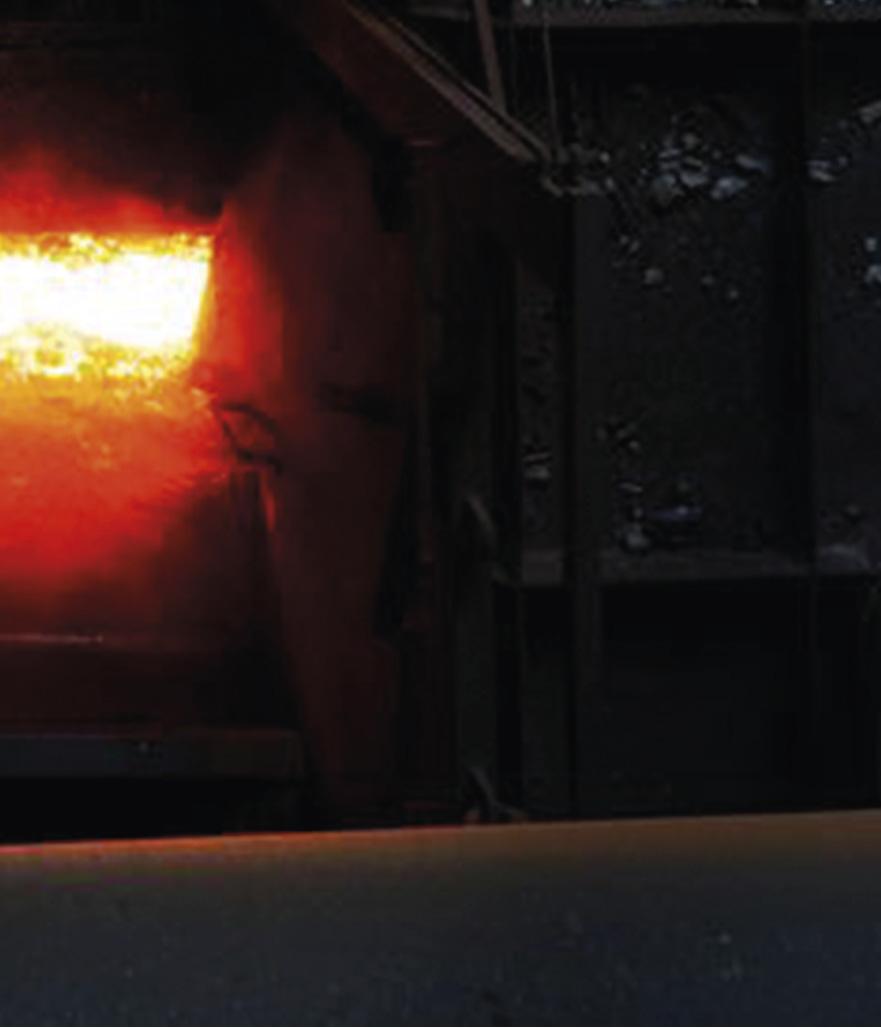

Barry Rust, Energy & Sustainability, Tata Steel, UK, looks at how the steel and pipeline manufacturing industry can reach its goals of decarbonisation.
While COVID-19 has led to a short-term decline in global crude steel output, longer-term forecasts suggest demand for steel will rise. Indeed, the International Energy Agency (IEA) has suggested that the global requirements will increase by more than a third through to 2050 as the world’s reliance on steel as the foundation for economic and social development grows.1
Steel is part of modern life. It has been a mainstay in the industrial development of many countries and it will have a vital role to play in our energy future. It is integral for the construction of pipelines for the oil and gas industry, the construction of many public and private buildings, and has an important role to play in the transition to greater renewable energy adoption through its use in the manufacture of wind turbines, solar panels and tidal lagoons.
However, the steel industry is one of the biggest producers of carbon dioxide (CO2). Every tonne of steel produced in 2018 emitted on average 1.85 t of CO2, which equates to approximately 8% of the world’s carbon dioxide emissions.2
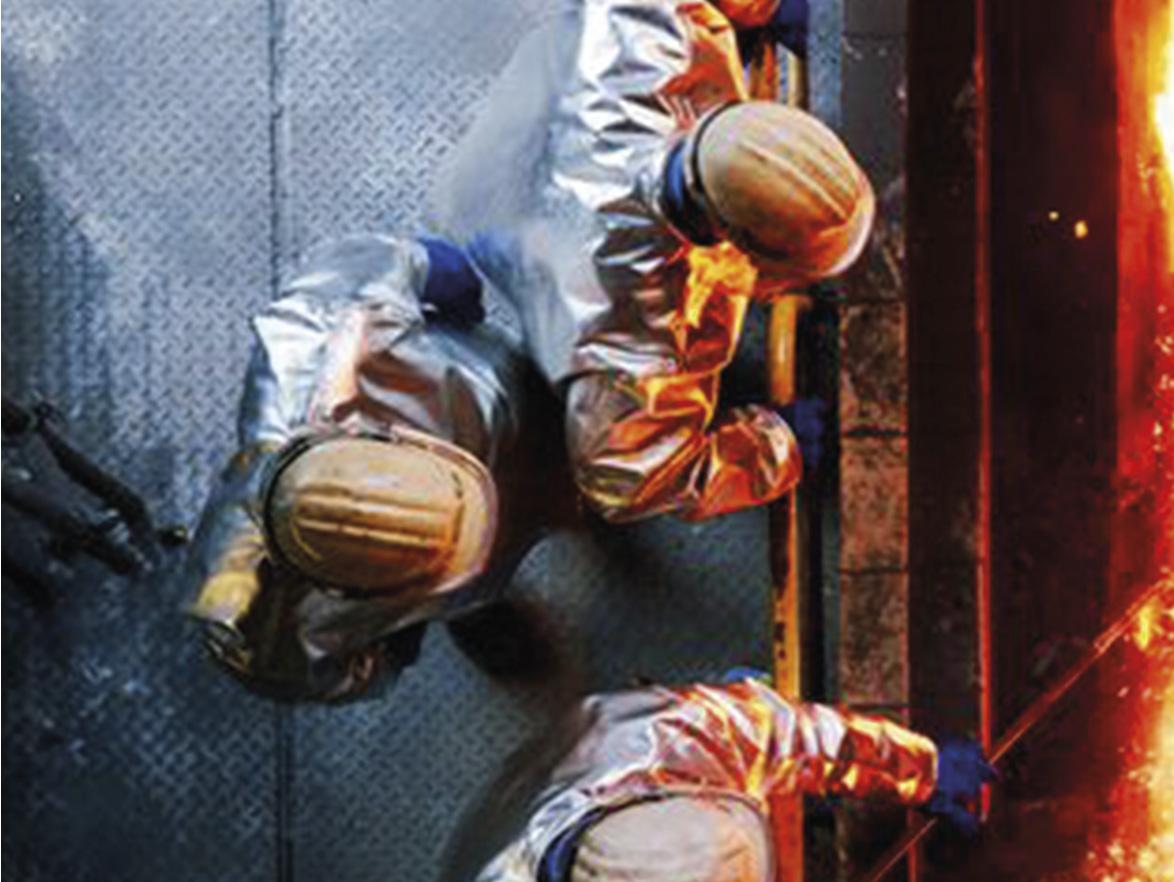
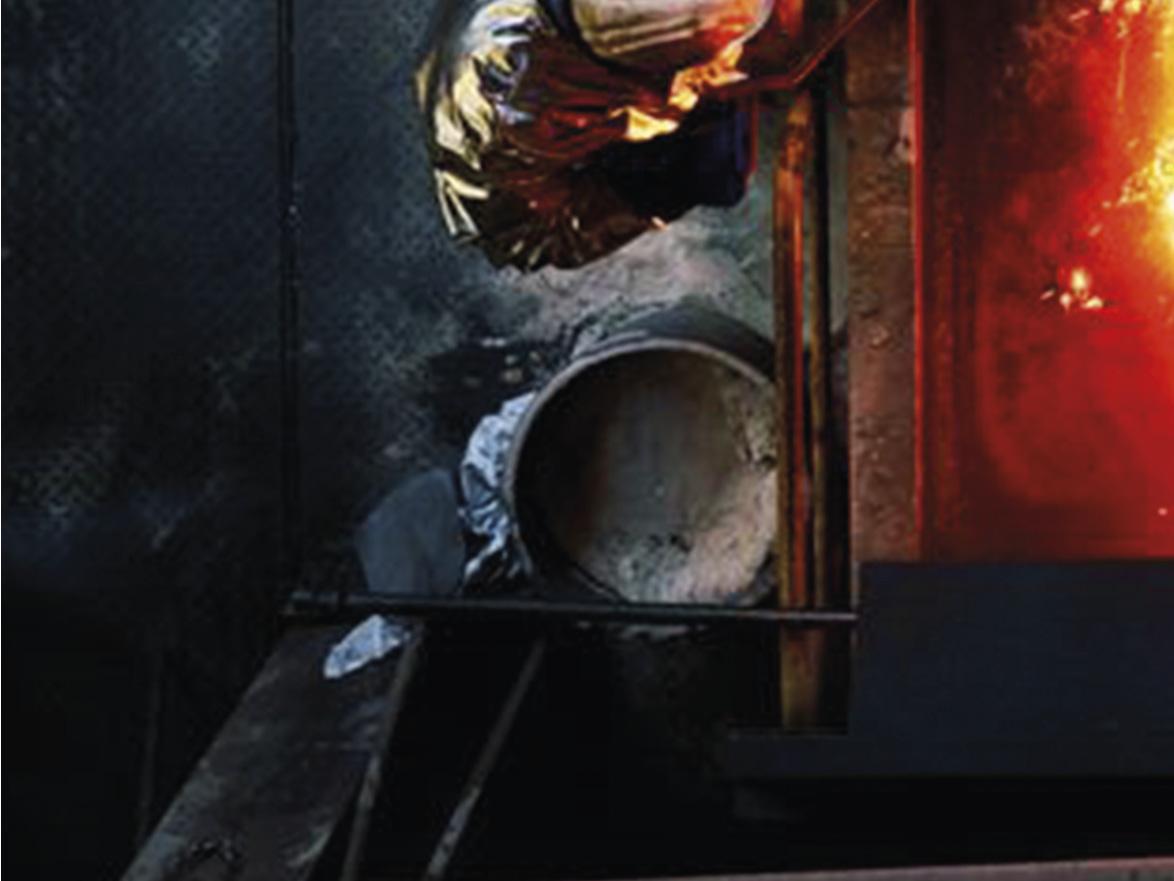

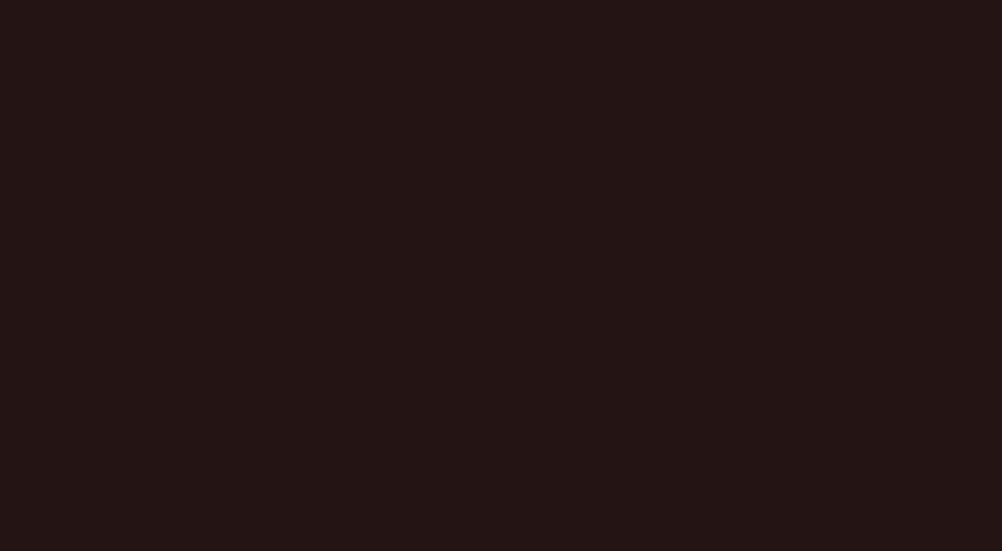
Such figures make difficult reading in a world increasingly committed to climate change. The United Nations’ Paris Agreement of 2015 set the tone on greenhouse gas emissions reductions by calling for a limitation on global temperatures to well below 2˚C on pre-industrial levels. In 2019 the UN announced over 60 countries, including the UK, had committed to carbon neutrality – or net zero – by 2050. However, a number of other countries and companies are working towards an earlier deadline (in Scotland the target date is 2045, Microsoft plans to be carbon negative by 2030,3 and Apple has promised to become fully carbon neutral by the same time).4
The steel manufacturing industry therefore faces the dual challenge of meeting anticipated increases in demand while promoting greater decarbonisation within its products and processes.
The need to decarbonise pipeline manufacture as part of a wider programme of industrial decarbonisation is accepted by steel manufacturers. That is certainly the case for Tata Steel. The company has a target to reduce CO2 emissions by 30% before 2030 and aims to be a carbon neutral steelmaker by 2050. Tata Steel is already one of the world’s most CO2 efficient steel companies. During the last 30 years it has reduced its CO2 emissions per tonne by approximately 20%, but its ambition is to continuously improve its production processes and efficiencies.
When considering how to generate greater decarbonisation in the steel industry there are several factors to consider, but two stand out. The first is the specific impact the industry can have in terms of new technologies, processes and greater supply chain and operational efficiencies. The second is the role of policymakers and regulators in providing the necessary support and infrastructure as part of a more widespread commitment to decarbonisation per se.
In both cases the message to producers and policymakers would be the same: do not wait when it comes to your decarbonisation plans. Big inroads can be made today. In steelmaking and pipeline manufacture, the race is on to fundamentally change its core processes. It requires partnerships with other industries, political support, developing breakthrough technologies, and new infrastructure to meet the 2050 zero emissions targets.
New technologies, improved performance It sounds simple, but one of the key ways to reduce CO2 in steel making and pipeline manufacture is to make less steel.
In the manufacture of pipelines for the oil and gas industry, the need for high integrity hydrocarbon production at an appropriate lifecycle cost is a trend that permeates throughout the sector, and one of the ways for the supply chain to meet these challenges will be through improved performance. In pipeline manufacture this includes enhanced properties and corrosion resistance, with products designed to support lower temperatures and provide enhanced weld toughness.
While there will always be a significant demand for seamless pipelines in the oil industry, the current adoption of welded solutions is anticipated to grow in the future. As an example of this, Tata Steel has seen a considerable rise in demand for welded solutions in the past 10 years. This is because of a range of factors including the potential for quicker lead times and faster manufacture, enhanced tolerances and improved surface conditions for coating. The challenge is to continue to improve the performance of welded solutions to deliver the benefits outlined above and replace more seamless pipe applications in the market.
Tata Steel continues to invest significant time and money into developing steels with higher strengths and/or excellent tolerances, allowing for the construction contractor or fabricator to weld at a faster rate, and for the development of thinner walled pipelines.
Another key goal is carbon avoidance, and here an experienced steel manufacturer with expertise in client engagement can support customers in project design optimisation to avoid excessive carbon production.
Carbon capture usage and storage (CCUS) is a key carbon avoidance strategy. Steelmakers need to reduce CO2 emissions as quickly as possible. As part of this drive, Tata Steel intends to build a plant that captures the CO2 currently emitted. In line with the company’s ongoing commitment to working with external partners, this could be offered to a new build

Figure 1. Tata Steel’s HIsarna pilot plant cast house.
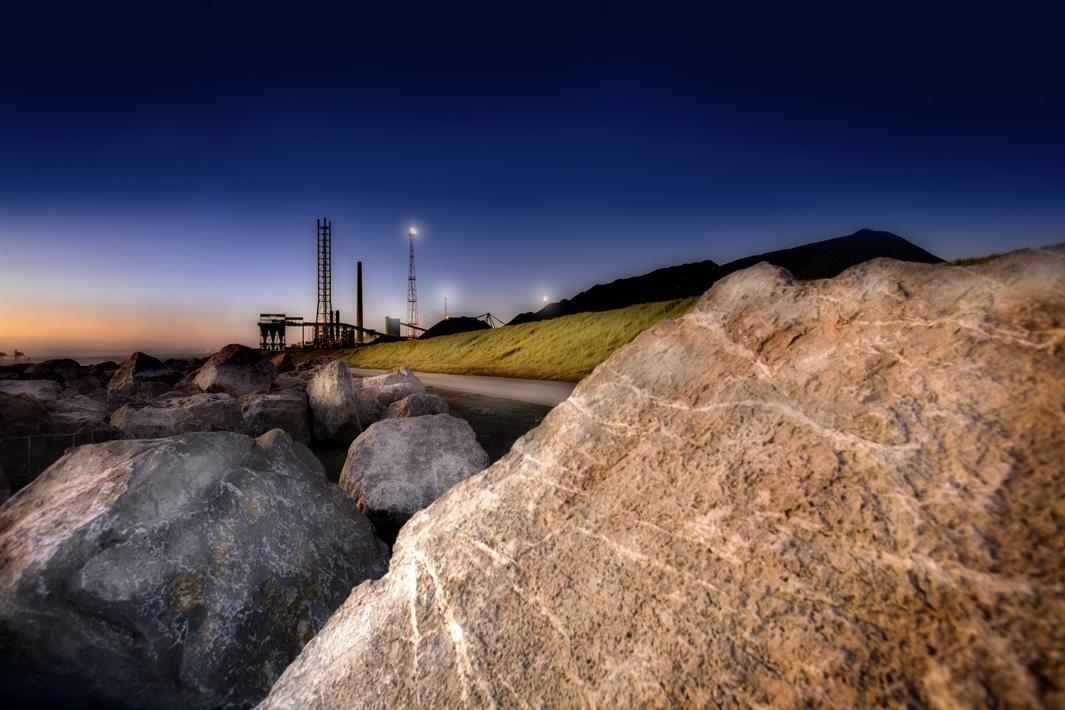
Figure 2. Port Talbot coast.
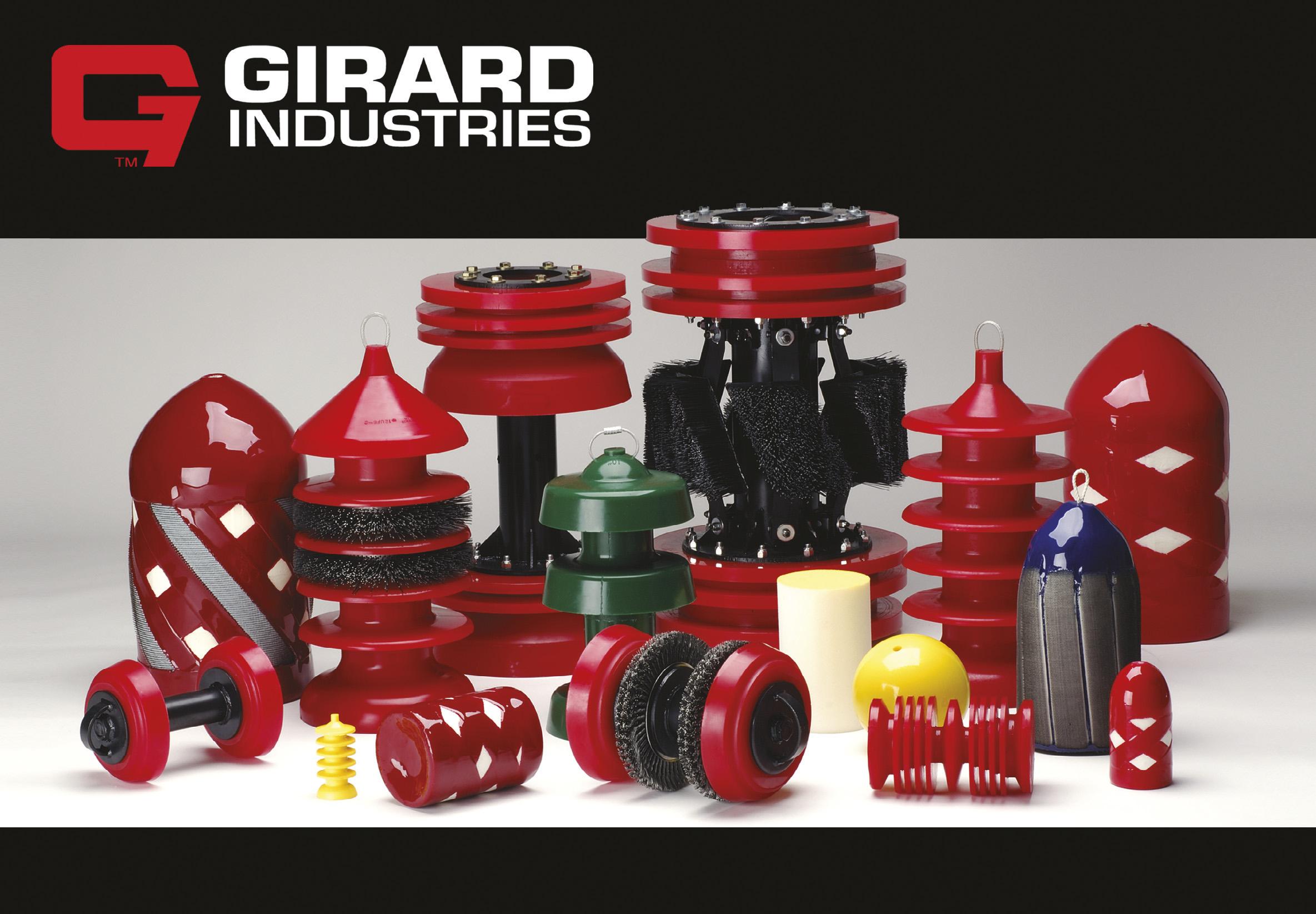

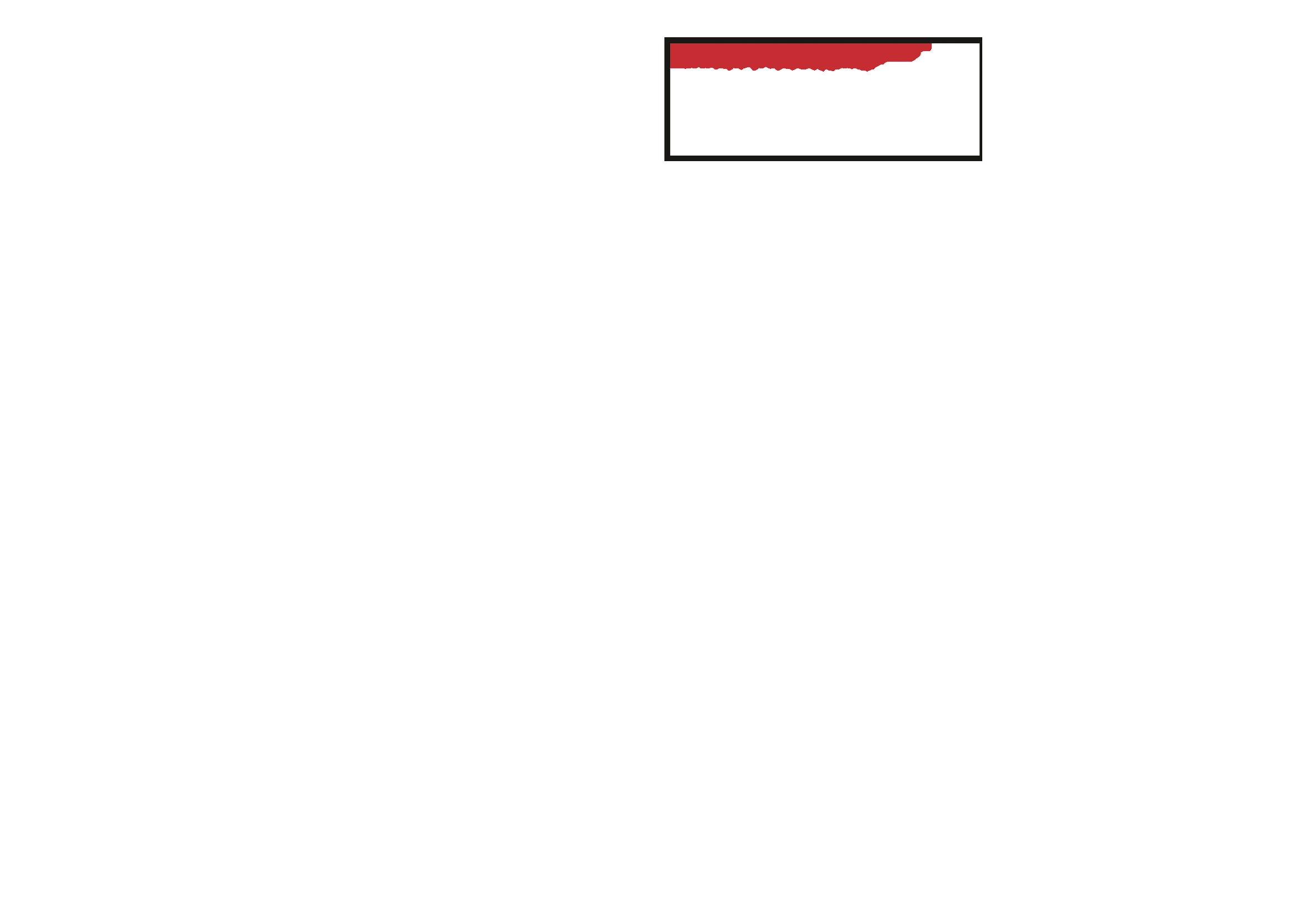
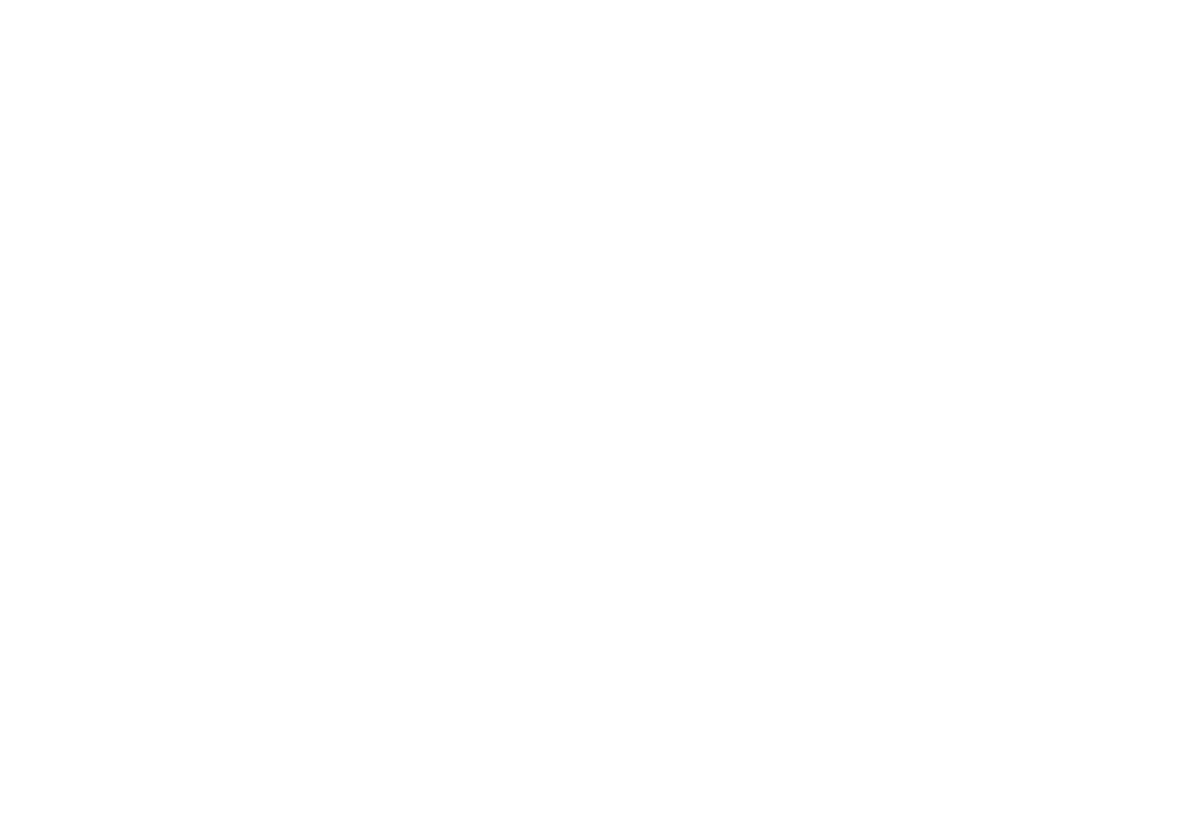
network to transport it for storage in depleted gas fields in the North Sea and the Irish Sea. By 2027, this could reduce CO2 emissions by 3 million t. Tata Steel plans to cut a further 1 million t of CO2 through removing and converting more of the company’s waste gases into products such as hydrogen, methanol or naphtha.
The company recently started the first phase of its Everest project to capture CO2 from blast furnaces and to transport it to former gas fields in the North Sea for storage. The second phase will see the company use blast furnace emissions for conversion into sustainable raw materials for the chemical industry and synthetic fuels.
A separate project from the company has examined the feasibility of carbon capture and storage in the North Sea as well as carbon usage. The transport and storage system aspect of the project will build new infrastructure as well as using existing infrastructure as much as possible. This will be owned and operated by a third party.
A key element of Tata Steel’s decarbonisation programme is the development and adoption of new technologies now and in the future.
The company recently announced that HIsarna, its groundbreaking reactor for lower carbon steel making, had exceeded expectations in sustainable steel production, with the possibility of achieving a CO2 reduction of more than 50%. HIsarna has been in development since 2011, and by 2033 the ambition is for it to be operating at full scale with the potential to replace an existing blast furnace. HIsarna can cut up to 100% of CO2 emissions when combined with carbon capture and in combination with an electric arc furnace can allow for zinc recovery – often found in scrap – for reuse. HIsarna is expected to play a pivotal role in meeting the ambitions of the circular economy.
Tata Steel is also working with external partners to take the waste outputs from its steel making processes to be used as valuable inputs into other industrial processes in order to reinforce the circular economic capability of steel.
Further out into the future, the use of hydrogen as a no/low carbon feedstock offers significant potential in the manufacture of steel and wider industrial decarbonisation. When burned, hydrogen emits only water and can be used in a number of processes. Producing hydrogen in large enough quantities is currently a challenge and it is important from a renewable energy perspective to ensure that the hydrogen used is ‘green’ (produced from water) where possible. However, the industry is investing significant expenditure into the development of hydrogen-derived steel and its future is promising.
Supply chain efficiencies A sustained low oil price, exacerbated by the impact of the COVID-19 pandemic on hydrocarbon demand, has intensified the oil and gas industry’s focus on efficiency savings where possible. This debate has predominantly centred on cost reduction, but in the sustainability arena, carbon reduction becomes the main consideration.
In this sense, many of the solutions for cost reduction apply to carbon reduction and it could be argued that carbon is tantamount to cost. Reducing waste in steel manufacture and project delivery can be equated to reducing the amount of carbon produced. Therefore reducing the amount of carbon waste as early as possible in the project, for example by optimising the design phase to minimise carbon use, will release the potential for greater efficiencies down the line.
A webinar to mark the launch of the IEA’s Iron and Steel Technology Roadmap5 heard that technology performance improvements and material efficiency in iron and steel could deliver 90% of annual CO2 emission reductions by 2030.
Effective supply chain integration will be critical to achieving such benefits. Unfortunately, hard organisational boundaries can impede greater levels of engagement, increased exchange of information, and partnership. It is important to overcome such boundaries if total cost of project ownership, a reduced carbon profile, and appropriate legislative compliance are to be achieved.
Notwithstanding legislative and customer sustainability requirements, in an era when the oil and gas industry’s social licence to operate is under more intense scrutiny than ever on a global scale, a visible commitment to carbon reduction as part of the energy transition can represent an opportunity for operators to reinforce their sustainability credentials.
As the first steel manufacturer to become an Environmental Product Declaration (EPD) programme operator, Tata Steel has been a long-standing supporter of sustainability. The company focuses on three main pillars: to be leading in CO2 neutral steel production; being a responsible steel supplier and enabling its customers to become more sustainable. Its sustainability strategy aligns with the UN’s Sustainable Development goals.
Alongside sustainability developments in the industry, it is important for policymakers to maintain a keen focus on legislation that supports greater decarbonisation. Governments have an essential role to play with steelmakers and other stakeholders in sustaining the debate and creating the appropriate conditions for greater decarbonisation and sustainability.
Conclusion Successful solutions to decarbonising steel production for the oil and gas industry and other industrial sectors will require working in partnership. From industry-led carbon reducing supply chain efficiencies and cost savings, to the implementation and enforcement of legislation and support that promotes decarbonisation and sustainability across society, steelmakers and policymakers both have an important role to play. In driving towards a more sustainable future, it is important that both act now and that neither waits for the other to take the initiative. The world cannot wait.
References
1. https://www.iea.org/reports/iron-and-steel-technology-roadmap 2. https://www.mckinsey.com/industries/metals-and-mining/our-insights/ decarbonization-challenge-for-steel 3. https://blogs.microsoft.com/blog/2020/01/16/microsoft-will-be-carbonnegative-by-2030/ 4. https://www.theguardian.com/technology/2020/jul/21/apple-promises-tobecome-fully-carbon-neutral-by-2030 5. https://www.youtube.com/watch?v=ly8O79x_kXM&feature=emb_title