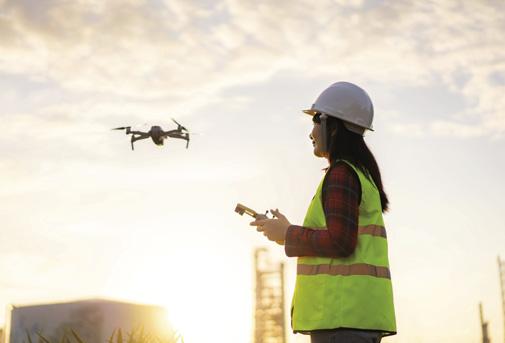
9 minute read
Making way for hydrogen
) Only alerting operators when an event of interest has taken place. For example, learning which incidents are unusual activity and warrant a response and further investigation.
A key issue to address with monitoring technology is nuisance alarms. For example, if spill detection technology is too sensitive, it can raise many false positives and operators stop paying attention to these. ML is critical to reducing these. The algorithms in DAS are smart enough to ignore activities that are of no concern, therefore reducing false alarms.
With smart sensors that incorporate ML, an operator can know in real-time what happened, exactly where and when it happened and have confidence in their system.
Integrating smart sensors and automatic responses ML plays a large part in advancing monitoring, but what if the alert could automatically feed into a dedicated response? That is the next step towards achieving true digitalisation, where digital technologies talk to each other to create efficiencies for operators.
DAS technology can alert a pipeline operator of a threat within a few seconds, but the challenge is how personnel respond to the alarm. Pipelines cover long distances, often in remote and inhospitable terrain. They might pass through desert, forest or icy tundra, where response by road or by foot is not easy and may take several hours or more. Response by helicopter might be the fastest and most direct route to the location of a detected incident, but this is a costly option and not suitable for pipelines where a tree canopy would make landing impossible. In this case, UAVs provide an attractive alternative to launch a fast response, to fly a direct route from base to the threat location. They can easily be used to capture visual and thermal images of activity and if there are theft attempts, let the criminals know that they have been detected.
Figure 3. DAS can automatically notify a UAV flight management system to a threat.
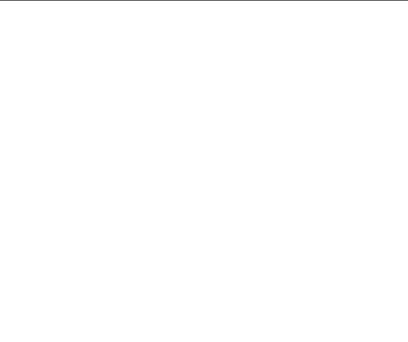
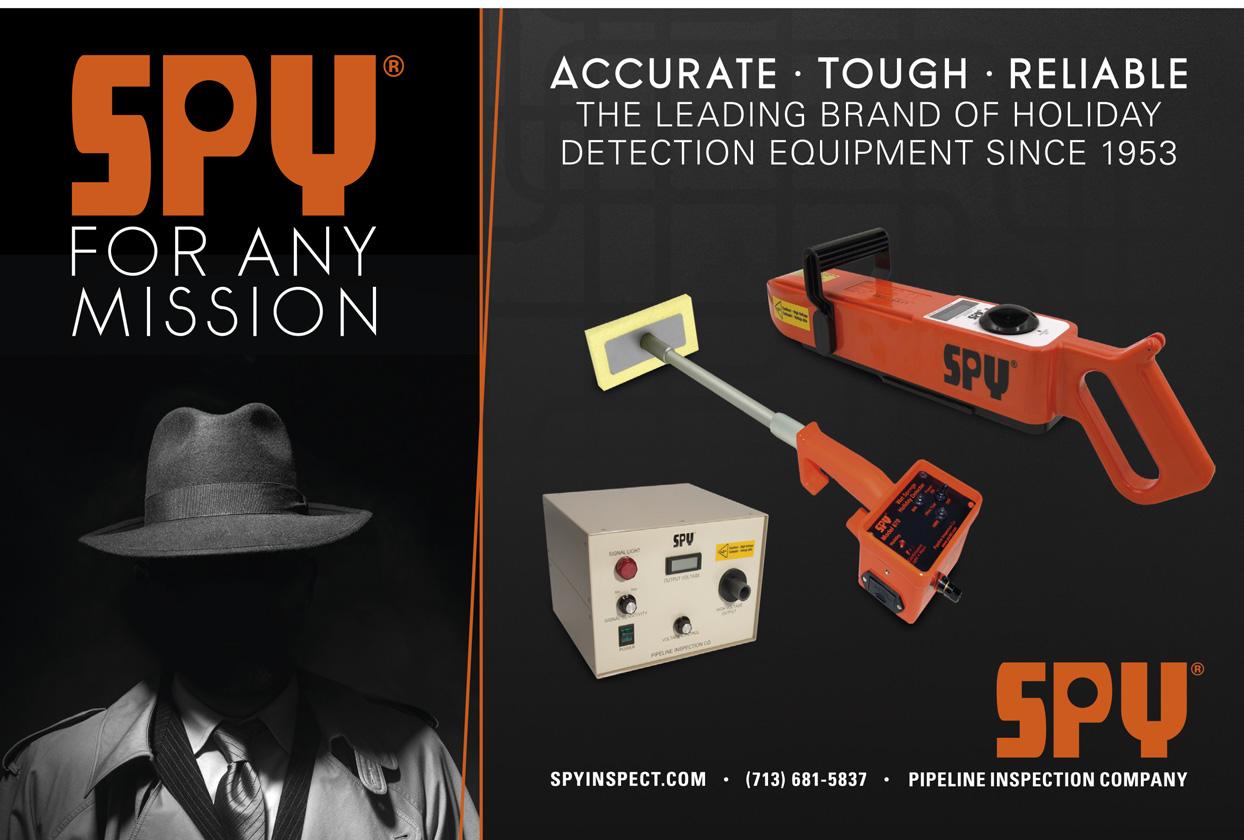

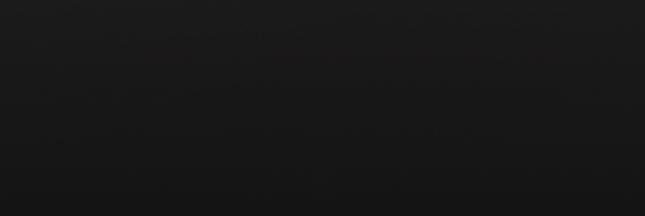

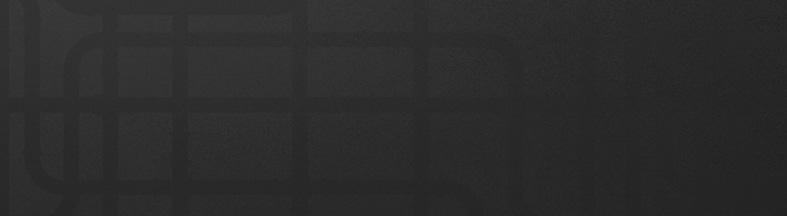
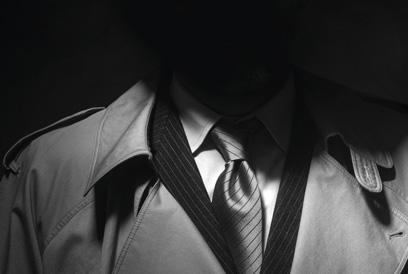
Accurate • Tough • reliable
THE LEADING BRAND OF HOLIDAY DETECTION EQUIPMENT SINCE 1953
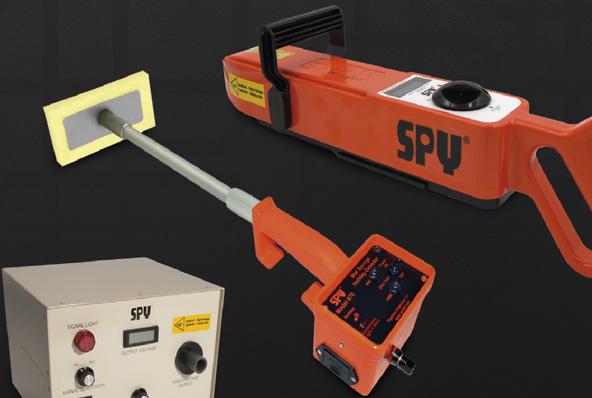
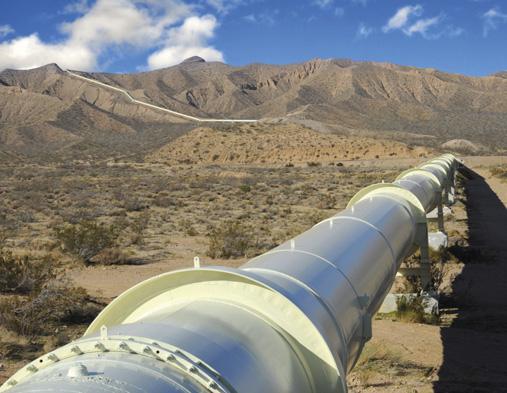
Figure 4. DAS harnesses artificial intelligence and cutting-edge ML computing to detect, to classify and to raise the alarm on pipelines events.
The latest DAS systems, such as Fotech’s LivePIPE II, can be easily set up to operate with UAVs. DAS can automatically notify the UAV flight management system where the threat has been detected by providing GPS co-ordinates in a message. The flight management system automatically determines the flight path, taking into consideration the topology and obstacles, the endurance of the battery and the weather conditions. The lid of the storage box in which the UAV is kept on standby opens automatically to let the UAV out. The UAV takes off autonomously and flies to the designated co-ordinates with the flight monitored from an operations room either at the pipeline operator’s security centre, or at the UAV service provider.
Conclusion Integrating DAS into a pipeline monitoring system enables operators to gain accurate intelligence quickly and efficiency, helping them to overcome one of their major challenges. These smart sensors, which incorporate ML techniques, allow pipeline networks to advance on their digitalisation journey ultimately to prevent commercial and environmental disasters, to streamline pipeline integrity maintenance while optimising pipeline efficiency.
DAS harnesses artificial intelligence and cutting-edge ML computing to detect, to classify and to raise the alarm on security, integrity, and leak detection events along a pipeline as they happen. Further, integrating a DAS monitoring system with UAV technology creates a powerful detection and response system to help prevent pipeline threats, to safeguard security and to reduce potentially catastrophic events.
References
1. Investigation: Giant N.C. spill shows gaps in pipeline safety – Thursday 25 February, 2021, www.eenews.net
IPLOCA - promoting health, safety and environmental mitigation methods globally
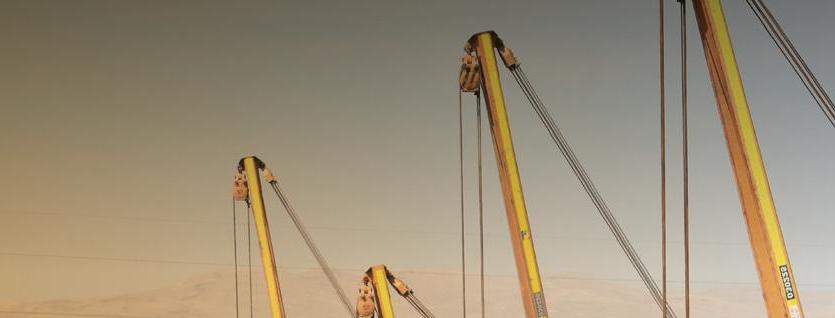
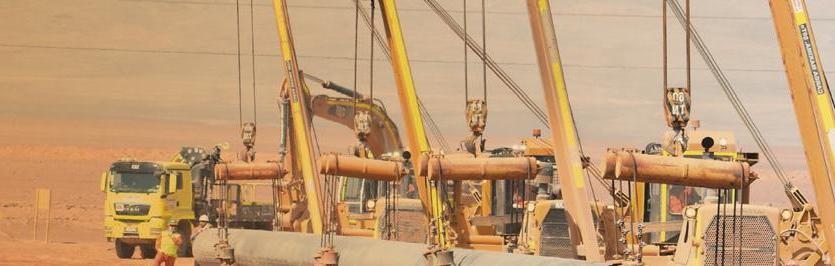
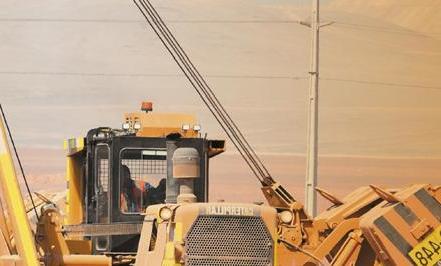
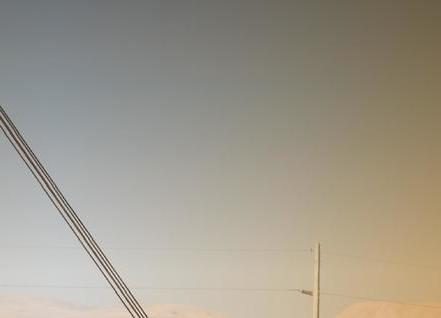

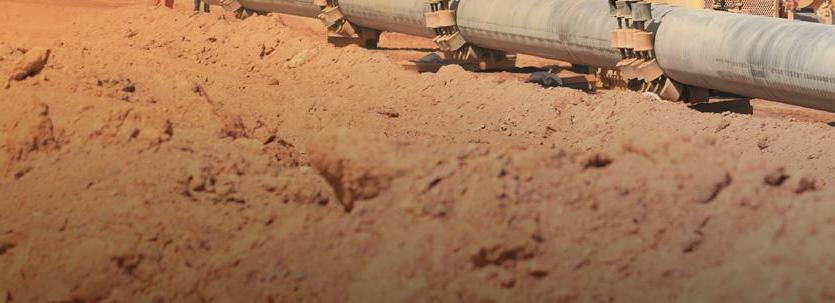
Dr. Mike Kirkwood and Neil McKnight, T.D. Williamson, UK, discuss the pigging and inspection of repurposed pipelines prior to hydrogen service.
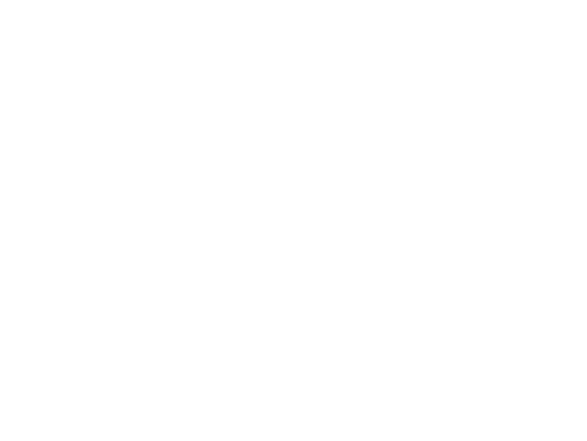
An energy-dense alternative fuel that produces no direct emissions of pollutants or greenhouse gases, hydrogen is being called the key to decarbonisation, the next big thing for generating electricity, power and light.
However, since its discovery in 1766, hydrogen has had somewhat of a checkered past – a past that includes the infamous 1937 destruction of the Zeppelin Hindenburg, which exploded over Lakehurst, New Jersey, filling the sky with smoke and fire.
There have been several theories as to the root cause of the failure, but one thing is not disputed: hydrogen leaked from the fuel cells, creating a highly flammable mixture that ignited. The reason for the leak and ignition has been subject to several hypotheses, including sabotage, a bomb, an arrow, lighting, electrostatic charge and even a weather phenomenon known as St. Elmo’s fire. Whatever the cause, the deadly accident influenced thinking about hydrogen at the time.
Of course, people have short memories. Because hydrogen is clean and can be produced from diverse sources, new interest in a ‘hydrogen economy’ emerged with the environmental movement of the 1970s. At the time, though, there wasn’t enough widespread support to propel the idea forward. Today, however, Hydrogen Economy 2.0 has government, regulatory and, most importantly, public backing.
The question is, if the future’s going to run on hydrogen, how will we transport all the product the world will need?
The answer, of course, is pipelines. Some of them will be new and designed specifically for hydrogen; others will be existing natural gas lines repurposed to carry hydrogen alone or in blended service. To ensure safety, prior to operation, those lines will need to be cleaned and inspected.
Converting isn’t easy Right now, there are approximately 4500 km (2800 miles) of operational hydrogen pipelines worldwide, mainly supplying feedstock hydrogen to chemical facilities. That number is slated to grow exponentially as hydrogen’s purpose expands.
According to a recent study by the European Hydrogen Backbone (EHB) initiative, plans are underway to develop a dedicated hydrogen pipeline transport network spanning 10 European countries. By 2040, the proposed system will be 39 700 km (24 600 miles) long. Approximately three-quarters of it will be repurposed natural gas lines.

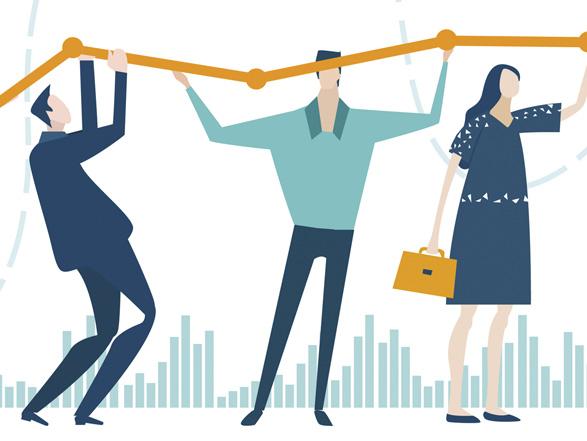
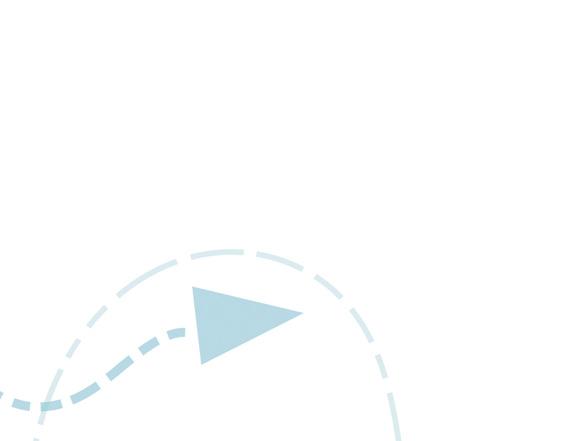
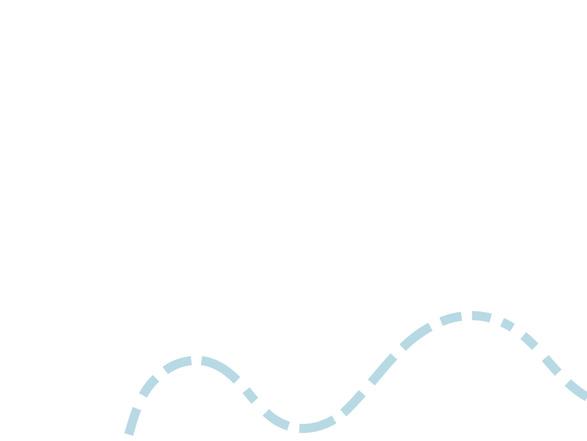
Converting an existing pipeline to hydrogen, either for blended or pure service, isn’t a simple task. There’s no on-off switch to make the transition fast and foolproof.
For one thing, the calorific value of hydrogen is one-third that of methane. This means that a pure hydrogen pipeline requiring an operating pressure of 200 bar (2900 psi) will need a threefold increase in pressure to get the same energy transportation as a current gas pipeline. Another problem: hydrogen is eight times less dense than methane, meaning it requires eight times the energy to compress it.
These operational difficulties are not insurmountable. A more significant concern is that hydrogen is known to adversely affect the steel most commonly used for natural gas pipelines. Hydrogen-induced cracking, hydrogen embrittlement and increase in fatigue crack growth are all potentially significant concerns.
However, with careful preparation prior to and during pipeline repurposing, even those challenges can be brought under control.
Pigging, before and after Pre-commissioning cleaning of hydrogen pipeline systems is normally accomplished by running conventional pigs using water, air or nitrogen. Generally, the goal is to achieve the same level of cleanliness as natural gas pipelines. During commissioning, standard pigs can be used for water fill and hydrotesting.
Once the hydrogen pipeline is in service, pigging tools will continue to play an important part in the operators’ flow assurance and inspection plans. The European Industrial Gases Association (EIGA) suggests using only pigs fabricated from hydrogen-compatible materials, which will affect the overall design. Selecting the right components will ensure they are not damaged by the aggressive environment and will reduce the risk of sparking, which can be hazardous when hydrogen and air mix.
For example: ) Cups and discs should be carefully selected based on urethane hardness, flexibility and wear resistance.
) Because of the spark risk and potential for damaging the internal coating, conventional solutions for extending cup run time in dry environments, such as studs, cannot be used.
) To avoid damage from hydrogen embrittlement, brushes and other metallic parts must be made from either austenitic steels or aluminum.
) Using non-intrusive pig signalers will eliminate any concerns associated with direct contact with hydrogen in the line. However, intrusive varieties can still be used as long as the trigger/plug material is appropriate, such as stainless steel.
) When designing canisters that hold transmitters or data loggers for pig tracking, it’s important to select the correct material for sealing elements and O-rings to ensure hydrogen compatibility. Elastomers in particular will exhibit swelling with hydrogen exposure.
Finding susceptible defects Defects that might be relatively low risk in natural gas pipelines can be more dangerous in hydrogen service. That’s why, prior to repurposing a pipeline, it’s imperative to first detect, size and characterise defects susceptible to hydrogen attack or degradation then remove or inactivate them. Deploying a variety of ILI technology can help find everything from manufacturing defects and corrosion to metal fatigue and interacting threats – defects that are more serious combined than they are individually.
ILI technology for hydrogen pipelines includes: ) High resolution deformation (DEF).
) High field axial magnetic flux leakage (MFL).
) Low field axial magnetic flux leakage (LFM).
) Helical/spiral magnetic flux leakage (SMFL).
) Electromagnetic acoustic transducer (EMAT).
) Ultrasonic wall measurement (UTWM).
) Ultrasonic crack detection (UTCD).
) XYZ mapping.
) Inertial measurement unit (IMU).
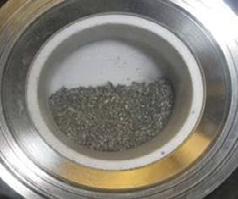
Figure 1. Rare earth magnets, like those used in ILI tools, before and after exposure to hydrogen environment.

Figure 2. Combination tool using DEF - MFL - LFM - SMFL - XYZ provides most defect detection, excluding cracks.
Figure 3. Electromagnetic Acoustic Transducer (EMAT) tool for detection of cracks. Multiple datasets improve threat characterisation Running multiple tools then aligning the data is a common method of identifying interacting defects, although the process isn’t failsafe and it’s possible to miss defects this way. Combining