
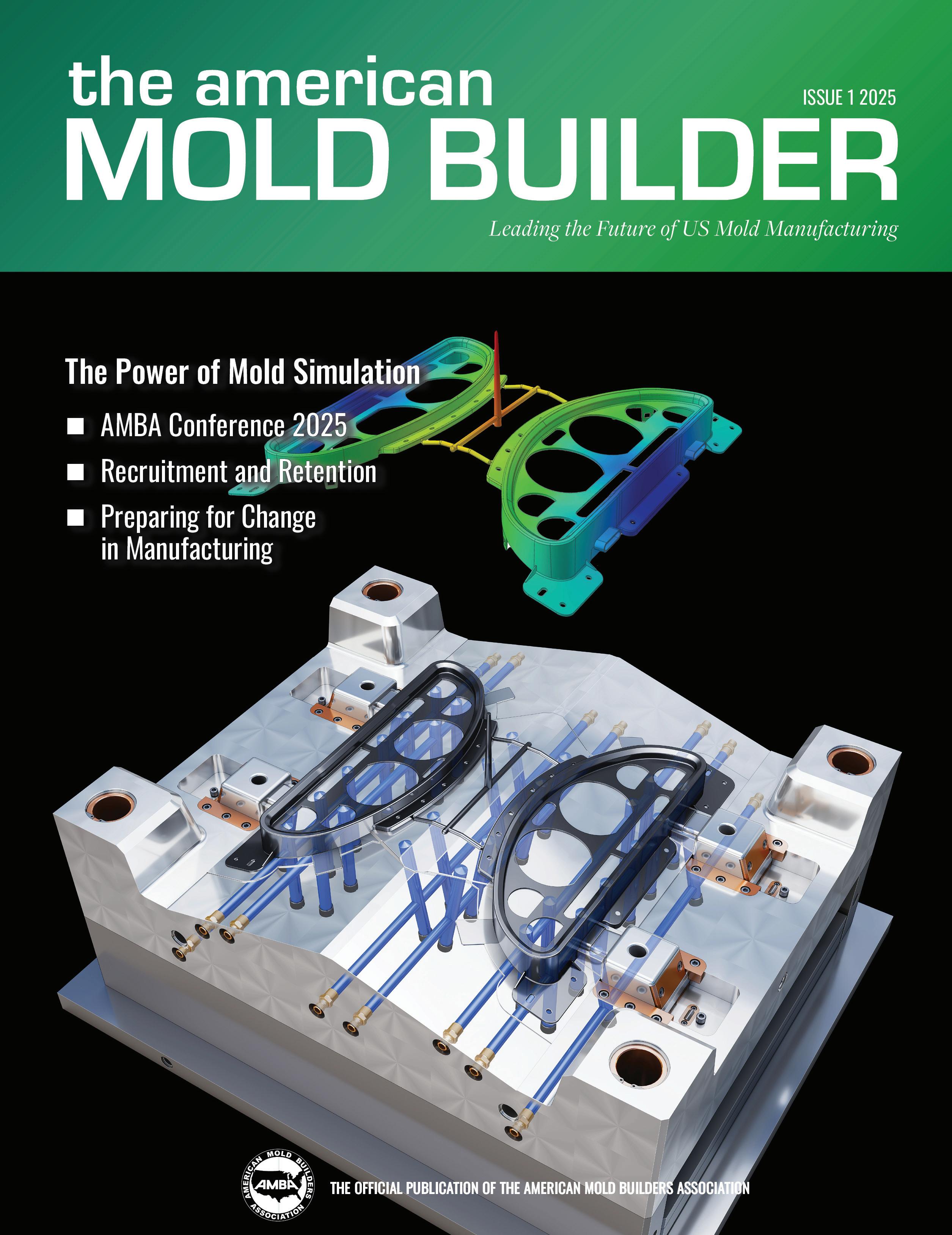
Kenny Skar, Vincent Tool Technologies Corp.
By calling on Progressive for components for hundreds of mold bases each year, Kenny Skar has gotten to know Pro’s team over the years:
“The dimensional consistency of critical components is spot on, and Pro’s Customer Service team is like family. And, we appreciate that Progressive steps up and gives back to strengthen our industry.”
For industry-leading innovations and precision component standards, Progressive delivers the service and performance your company deserves. Call 1-800-269-6653 to discuss putting these advantages to work for you.
AMBA TEAM
Troy Nix, Executive Director Kym Conis, Managing Director Susan Denzio, Business Manager
Rachael Pfenninger, Director of Strategic Execution
Olivia Shotts, Public Relations Development Coordinator
Advising Editor: Kym Conis Advertising/Sales: Susan Denzio
PUBLISHED BY:
2150 SW Westport Dr., Suite #101
Topeka, KS 66614 P: 785.271.5801
Vice President, Editorial: Dianna Brodine
Editor: Lindsey Munson
Vice President, Design: Becky Arensdorf
Graphic Designer: Hailey Mann
Opinions
TYLER VANREE AMBA President, LEGACY PRECISION MOLDS, INC.
Hello, AMBA! Can you believe 2025 is here and off to a fast start? The new year always feels like a fresh beginning to me and full of potential. Whether it’s setting New Year’s resolutions, rolling out a fresh strategic plan for your business or welcoming new opportunities and connections, there’s so much to look forward to this year.
AMBA is kicking off the year looking for ways to help your business maintain a competitive edge, and the spring lineup of events is packed with opportunities. AMBA is continuing its Financial Literacy Series, broken down into a two-part series from a Michigan CFO on building a deeper understanding of financial statements and from Wipfli on learning how to create a business that is valuable and ready for a future sale. If you’ve missed any of the previous CFO webinars, I’d strongly encourage you to check out the replays. AMBA also will be hosting roundtable discussions throughout the year, be sure to register as they become available.
The ITR Economics Q1 Report Deep Dive occurred on February 26, providing insights into the future economic outlook and acting as an excellent resource to help businesses plan for what lies ahead. It’s a great way to look out the windshield of your business instead of through the rearview mirror. In addition, the State of the Industry webinar took place on February 27, offering another valuable set of data to help guide your business toward success in 2025. If you missed either of these events, I highly recommend you access these webinar recordings from AMBA’s website.
We remain committed to giving members a strong voice on Capitol Hill – backed by new resources and information sources coming in 2025 from Omar Nashashibi, Inside the Beltway Solutions. Navigating federal developments can be complex, but AMBA is here to cut through the noise and help you identify the key issues that impact your business.
AMBA will be exhibiting at PTXPO 2025 – stop by booth #1436 and say hello! The team always enjoys meeting members face-to-face. AMBA will host two receptions during the show: AMBA emerging leaders on March 18 from 4-5:30 p.m. at Crust Brewing, and a members appreciation reception at booth #1436 on March 19 from 2:30-4 p.m.
Finally, registration is open for AMBA Conference 2025. The highlight of the year for many will happen in Grand Rapids, Michigan, on May 7-9. Be sure to secure your spot. With an exciting speaker lineup, breakout sessions and peer networking opportunities, this event offers something for everyone in your organization to get involved, learn and grow. For more information, visit www.ambaconference.com.
I’m looking forward to what’s ahead in 2025 – let’s make it a great year together! No matter what lies ahead, AMBA is here to help you navigate both the opportunities and challenges that you might face. You are the AMBA. We are the AMBA. Together, we are stronger.
OFFICERS
National President
Tyler VanRee, Legacy Precision Molds
Vice President Andy Peterson, Industrial Molds
Secretary and Legal Counsel
Alan Rothenbuecher, Benesch, Fiedlander, Coplan & Aronoff LLP
Treasurer
Hillary Thomas, Westminster Tool
Tom Barr, TK Mold & Engineering
Ed Francis, Crystallume Engineered Diamond Products
Justin Gregg, Dramco Tool Co., Inc.
Mike Hetherington, Franchino Mold & Engineering
Kyle Klouda, MSI Mold Builders
Chad LaMance, United Tool and Mold
Troy Roberts, Tolerance Tool
Camille Sackett, Accede Mold & Tool
Scott Smith, Tessy Tooling
John Stocker, Swiss Steel USA, Inc.
By Lindsey Munson, editor, The American Mold Builder
In this era of modern manufacturing, molding simulation services and mold flow analysis are pivotal in shaping the virtual effects of a mold to real-world precision, efficiency and cost savings. By using advanced simulation technologies, manufacturers can analyze and optimize the parameters that accompany mold design and production. From the flow of materials to the cooling channels, these tools give engineers and designers the ability to foresee challenges, fine-tune and troubleshoot designs and deliver superior molds that meet or exceed the manufacturers’ standards for performance and durability.
To offer a deeper look and give reality to the complexities, value and innovation behind mold simulation and analysis, The American Mold Builder interviewed three industry experts who collectively have decades of experience in this specialized area.
Danny Branch is a CAD/mold product owner with Cimatron, Novi, Michigan, a company that provides toolmakers with an end-to-end solution for designing and manufacturing tools. One of the old sayings, “Try before you buy,” brings the reality of mold simulation full circle. Branch said, “It’s like performing a ‘mold tryout’ before cutting any steel.” He shared that simulation and analysis allow critical mold design decisions for gating, venting and cooling to be tested and quickly optimized; and that the simulation can be used to verify decisions based on the collective design experience at a shop. “It even can be a big help in educating and guiding the next generation of designers,” said Branch.
The benefits of mold simulation are well-known in the industry; however, it is important to connect the dots as to “why” manufacturers should incorporate this step in the moldmaking process. Branch said, “Experimenting with gating scenarios ensures that parts have the best orientation in the mold, that runner systems are optimized and that the mold itself will be compact and efficient. Having to rework a mold creates extra costs and slows down the other jobs on
the production floor. By providing ‘empirical evidence’ for the successful design of specifics, like gate sizes and vent positions, flow simulation helps a shop make decisions that increase the chances of success right from the start. It also can point out potentially severe molding flaws, like visible weld lines, warping or incomplete filling. Identifying these issues early in the process minimizes design adjustments and reduces the cost of tooling corrections. Overall, flow simulation increases confidence in favorable results. It even can reduce the need for physical prototypes – and fewer prototypes translate to reduced material and labor costs.”
Alongside the advantages of mold simulation, Cimatron shared best practices to build structure within the process:
• Run a simulation using the exact material that will be used to mold the part. Branch said, “Simulation software includes access to a large materials database, so if the plastics have fillers or fibers, using the correct material for simulation ensures that the true flow behavior will be estimated.”
• Take time to represent the cavities and cooling lines. This allows the simulation to provide better data about how fast the part can cool and any warp it might experience. “Performing a comprehensive simulation,” said Branch, “means that there should be no surprises when the real mold gets to the press.”
• Adopt an easy-to-use mold simulation solution early in the process. In doing so, it gives a significant advantage over competitors who may be hesitant to invest.
The results from a mold flow analysis provide metrics for designers and engineers to use (e.g., cycle time, design issues, resource usage) against real-world production, advancing the product from ideation to conceptualization. Branch said, “When performing mold simulation, designers should pay special attention to the fill time, the mold temperatures and the packing pressures – as these values should match the initial assumptions. We often hear only the success stories, but a lot can be learned from simulating a failed mold design. If simulation is used to take a closer look at past mistakes, companies typically find that the results match their real-world experiences – and the solutions needed to fix the problems.”
Branch said, “Especially helpful for toolmakers is streamlined simulation software that reduces the learning curve and empowers toolmakers to achieve ideal results without having to be CAE specialists. Modern simulation software is becoming more like CAD, with user interfaces that are easy to use. Mold designers don’t want to spend time on the mechanics of part quality or mesh density, so simulation software is getting better at importing 3D models and fixing what needs to be repaired before simulation.”
As the molding industry looks to the future, Artificial Intelligence (AI) is an emerging trend that can help inexperienced manufacturers make good decisions and become productive quickly. Using AI in the design phase to automatically detect part features makes the design process more efficient and empowers companies to apply their best practices consistently.
In summary, by helping identify potential design flaws, predict material behavior and evaluate the performance of molds under real-world conditions – simulation reduces the need for “physical tryouts” and helps ensure better results. “Placing trust in simulation software,” said Branch, “comes easily once a company has seen it back up the real-world results!”
Torsten Kruse, founder and president of Kruse Analysis and Training, Naples, Florida, provides innovative, fullcapacity filling-to-warpage Computer-Aided Engineering (CAE) simulation services. From idea to finished product, Kruse develops custom injection molding simulations, allowing companies to evaluate essential aspects that impact part moldability before a part is designed and a mold is built. Kruse said, “By integrating CAE mold-filling simulation software into workflows, mold manufacturers can enhance efficiency, reduce costs and deliver optimized part designs and high-quality molds that meet demanding industry requirements. It has become a vital tool for staying competitive and innovative in modern manufacturing.”
“Injection molding simulation software provides manufacturers with advantages that enhance efficiency, quality and scalability,” said Kruse. Here are three key benefits:
1. Reduction in Design and Production Phase Risks
Optimized Part and Mold Design: Simulation software allows manufacturers to predict and analyze the behavior of materials during the injection molding process. This helps identify defects, like warping, sink marks or voids, before the mold is physically produced.
Error Mitigation: By visualizing flow patterns, pressure distribution, cooling efficiency and stress distribution, manufacturers can address potential issues upfront, reducing the likelihood of defective products.
Faster Iterations: Virtual testing enables quick modifications to the design, eliminating the need for multiple physical prototypes, saving time and minimizing production risks.
2. Cost Reduction
Decreased Prototype Costs: By simulating the molding process digitally, manufacturers significantly reduce the number of physical prototypes needed, saving material and labor costs.
Minimized Waste: The software helps optimize material usage and part and mold design to ensure minimal scrap and avoid overuse of raw materials.
Reduced Machine Downtime: Design of Experiments (DOE) simulation insights allow better machine set-up and parameter adjustments, leading to fewer stoppages and lower maintenance costs.
3. Operational Efficiencies and Scalability
Shorter Development Cycles: By streamlining the design and testing phases through simulation and scalability analyses, manufacturers can bring products to market faster.
Improved Process Control: The software provides precise insights into parameters such as injection speed, pressure, packing pressure, time and cooling time, enabling fine-tuned processes for maximum efficiency.
Adaptability for New Projects: Simulation software is scalable and adaptable, allowing manufacturers to handle diverse materials, complex geometries or changes in production volume with minimal disruption.
In addition to knowing the benefits of conducting a mold simulation, Kruse said, “It is essential that manufacturers align and implement several best practices that assist
engineers and designers in producing optimal outcomes and efficiencies within their operations. These best practices include accurate material data from suppliers and databases; high-quality mesh that balances detail and computational efficiency; realistic process parameters (e.g., melt temperature, injection pressure, cooling times); comprehensive mold design, as this influences simulation accuracy; boundary conditions to mimic real-world scenarios; validate with physical data from real-world molding trials; consider warpage and shrinkage analysis to predict dimensional stability and ensure final part quality; iterate and optimize by running multiple DOE simulations; collaborate across teams; and leverage advanced features (e.g., fiber orientation prediction, multi-component molding or conformal cooling analysis).
“To evaluate the effectiveness of a mold simulation,” said Kruse, “selecting appropriate performance metrics, aligning the simulation with real-world conditions and leveraging the data for continuous improvements are crucial.” He broke this down into two parts: 1) performance metrics for evaluating mold simulation and 2) guidelines to align simulation results with real-world conditions. Kruse said, “By focusing on these metrics, adhering to validation guidelines and leveraging simulation data effectively, manufacturers can ensure mold simulations are a valuable tool for achieving lean manufacturing goals and continuous improvement.”
Our Roughing Stones are designed to remove material quickly and efficiently, making them the perfect choice for tackling tough machining marks, EDM scale, and other challenging surfaces.
If looking to enhance operations and utilize resources in connection with mold simulation software, Kruse said, “The integrations of enterprise resource planning (ERP) and manufacturing execution systems (MES), as well as automated robotics, are growing common in modern manufacturing environments to streamline operations, enhance precision and optimize production processes. If considering such an integration, it is crucial to ensure compatibility between the systems and select software solutions that support open standards and interoperability.”
In thinking about the future of moldmaking, Kruse said, “Emerging trends in injection molding simulation focus on enhancing precision, speed and sustainability. Advances include AI-driven predictive modeling, real-time simulation tools and cloud-based platforms facilitating collaboration and scalability. Enhanced material modeling now accounts for complex polymer behaviors, enabling more accurate predictions of part performance and defects. Additionally, simulations increasingly integrate with Internet of Things (IoT) systems and digital twins, eLearning initiatives, and virtual reality and mixed reality applications, allowing manufacturers to optimize parameters using accurate production data.”
• MOLD FINISHING
• LASER WELDING
• LASER ENGRAVING
• HOT RUNNER REPAIR
• MOLD MAINTENANCE
• LASER MACHINE SALES
er mold finishing, laser welding, laser graving, mold maintenance, and hot runner manifold repair all under one roof. We also manufacture and sell the only fully American made laser welding and laser engraving systems, custom built specifically for your toolroom
Let Alliance make a di erence for you.
EVERY PART OF THIS MACHINE IS EASILY ADJUSTABLE TO ALLOW YOU THE VERSATILITY AND FLEXIBILITY YOU NEED TO MEET ALL OF YOUR DEMANDS
CONTACT US TODAY ABOUT AN IN-HOUSE DEMO, TO SEE THE ALLIANCE DIFFERENCE.
t“In the future, this evolution is expected to drive smarter decision making, lower production costs and enable customized solutions with greater speed and reliability, fostering more agile and sustainable manufacturing processes,” said Kruse.
Michael Thiessen is the North American sales manager at Tebis America, Inc., Troy, Michigan, a software company that specializes in CAD/CAM systems for manufacturing and design. “In today’s moldmaking environment, it is crucial to have an accurate and virtual representation of all the available equipment used for the machining,” said Thiessen. He continued the scope of “why” mold simulation is a critical and beneficial process in the developmental phase for manufacturers by covering three main areas, including planning, safety and optimization.
First, moldmakers do not have time to “play around” on the milling machine to see if the part fits on the machine, how many setups are required for the part and what type of tooling or fixturing is required – all so that the mold can be machined without stopping. Thiessen said, “Therefore, accurate virtual CNC machines are used for the ‘planning’ and selection of additional supporting equipment (e.g., work holding fixtures, special tooling). A digital twin is the key to replicating the product or system within the simulation. Not only does the machine need to be represented virtually, but the tooling also needs to be realistic and data-rich, the workholding solutions need to be parametric and accurate, and every motion that the machine makes needs to be accurately represented (e.g., the tool changer, tool laser, manual tool change positions, traverse motions).”
Second, the cost of milling machines is quite high, and thus manufacturers can’t afford to have mistakes happen on their machines that could cripple production. “If a machine crashes, the cost is not only the repair of the machine, which is quite expensive, but every part of the process also associated with meeting production and customer demands has a huge impact on the operations,” said Thiessen. “This includes the cost to repair the part, the cost to outsource the part/machine to a supplier because there’s not another machine available, the potential risk of not delivering on time, labor and the reshuffling of other parts. These factors play a crucial role in the ‘safety’ and well-being of the company. Mistakes happen, it’s human to make mistakes; however, finding the mistakes early on and rectifying them is priceless. That is what a good simulation solution can deliver.”
Third, a simulation solution, if correctly used, can harbor a lot of information within its model. “It is not just a geometrical representation of the machine – it is much
more!” said Thiessen. It can be a storage container of data because it has information on the limits of the machine, the amount of travel available, rotational restrictions, look ahead of the machine controller, acceleration parameters of the machine, tool change location and more. He said, “Knowing which way the machine will rotate when submerged in a deep cavity is crucial. If a mold simulation can ‘optimize’ the movement of the machine, then a manufacturer has the best option to succeed and possibly increase its chances of getting the part off the machine earlier than expected. In addition, if the simulation solution can use this data and provide a highly accurate machine time, then the machine managers can forecast accordingly and schedule one more mold during the day shift. Time is everything for a mold shop!”
As manufacturers look to mold simulation for precise data in the initial stages of mold development, Thiessen shared five best practices:
1. Scan the numerical control machine and have a 100% accurate representation available.
2. Have a post-processor that mimics every motion of the machine, accurately and dependably.
3. Create a virtual tool crib of all tooling and create a standard of these tools to include necessary data (e.g., feeds, speeds, step-over values, step-down values) for the machines.
4. Use parametric solutions with work-holding fixtures so that it’s as realistic and adaptable as possible.
5. Utilize a software solution that applies an “inline” virtual simulation, not a simulation based on the G-code of the posted output.
“For the future, I see a great use of AI in the world of machining and simulation. We tend to do the same actions that we did about a year ago with some small modifications. If AI was present,” said Thiessen, “then it could define and predict the course of action and strategies to be used for these types of parts. It also could dictate which machine it could fit, and which machine is the fastest for these types of parts. Therefore, integration of AI in manufacturing is crucial – especially due to the knowledge and experience this new workforce harbors. Many of the experienced experts have retired or are on their way to retirement, along with their knowledge. Companies must retain and capture this knowledge so that the NextGen workforce offers the same quality and excellence.”
More information: www.cimatron.com, www.kruseanalysis.com, www.tebis.com
A look at Computer Numerical Control (CNC) equipment, encompassing a set of machines and tools used in the manufacturing processes to produce parts and components with high precision, accuracy and consistency.
HEIDENHAIN
847.490.1191
www.heidenhain.us
machining, optimization of toolpaths and the ability to run machines unattended.
HEIDENHAIN, Schaumburg, Illinois, develops, manufactures and sells components for the core industries of machine tools, electronics and automation. It offers the TNC7, which is a CNC system designed to enhance precision machining. HEIDENHAIN provides a user interface that adapts screen contents to the task at hand.
Intuitive, task-focused and customizable, the TNC7 allows users to draw contours directly on the touchscreen. Familiar elements like the TNC keyboard ensure ergonomic comfort. The TNC7 excels in task-focused support with advanced cycles, smart probing and 6D-alignment guidance. Reliable process monitoring detects irregularities, while component monitoring protects spindle bearings and detects wear. With predictive maintenance capabilities, the TNC7 ensures high process quality and efficiency, making it an indispensable tool for precision machining.
Hexagon Manufacturing Intelligence
937.668.2578
www.hexagon.com
Hexagon Manufacturing Intelligence, North Kingstown, Rhode Island, is a global supplier of digital reality solutions combining sensor, software and autonomous technologies. Its CNC simulation software builds real-life machining environments before production, assisting manufacturers in avoiding errors, decreasing setup times and switching CNC programs between machines to increase productivity and reduce costs. Hexagon offers NCSIMUL, a CNC machining verification and simulation software that helps validate G-code and optimizes machining processes in a virtual world. NCSIMUL has several benefits, including safe and collision-free machining, reduction in CNC downtime, proving out G-Codes on the computer before
Makino, Mason, Ohio, offers a comprehensive range of solutions, including horizontal and vertical machining centers, wire and ram EDM and graphite machining centers. Its D200Z 5-axis Vertical Machining Center is designed for tighter tolerances and flawless blends and matches in complex 3D-contoured workpieces. The speed and precision of the D200Z supply a foundation for responsive high-speed cutting and surface finishes that reduce or eliminate handwork. Its 30,000-rpm spindle and integral direct-drive table provide quick, precise and full 5-axis machining. This capability is tied together with Makino’s proprietary SGI.5 motion control software for accuracy and quality in the blends, and matches of intricate surfaces and 3D requirements typical of today’s die and molds.
Zimmermann, Inc., Wixom, Michigan, is a German precision manufacturer of CNC milling equipment. Zimmermann stands for innovative, high-quality and efficient milling solutions serving customers worldwide. Its modular machine system provides flexibility for individuality, and the thermal symmetrical gantry provides maximum accuracy. Zimmermann develops its milling machines with passion and precision. Zimmermann finds the right solution to fit individual company requirements, the specific industry served and all components/materials that are encountered in the machining process.
By Liz Stevens, writer, The American Mold Builder
Workforce development, a perennial requirement in mold building, is a hot topic in 2025. Effective employee recruitment is necessary for filling empty slots with well-matched candidates in a timely manner, thereby limiting recruitment costs and reducing downtime due to a lack of staff. Effective employee retention equally is important, especially with team members who are key players or who have become a company’s most knowledgeable and experienced gurus. Mold builders are changing how they recruit new team members, and their retention strategies may be relying less on financial-driven incentives and more on employee development, growth and opportunity.
The American Mold Builder talked with Elizabeth Lasanen, HR manager at Dynamic Group, and Todd Steging, general manager at Prestige Mold, to get insight into what mold builders are doing to recruit new workforce members and to retain their valued employees. Dynamic Group, Ramsey, Minnesota, provides innovative design solutions for complex plastic, powder and metal injection molds and serves a range of industries, including medical, electronics, technology and firearms. Prestige Mold, Rancho Cucamonga, California, provides design, manufacture and testing of precision injection molds and turnkey system solutions for the medical, closure and technical markets.
Dynamic Group and Prestige Mold use several strategies for identifying and recruiting job candidates. “One of the most effective recruitment strategies we’ve found is leveraging internal referrals,” said Dynamic Group’s Lasanen. “These candidates tend to stay with us longer, and the cultural fit often is pre-vetted because they’ve come to us through an existing employee who understands and values our workplace culture.” Dynamic Group trusts that
its employees know what the company is looking for and will recommend like-minded individuals who align with its values.
“Another successful strategy,” said Lasanen, “has been partnering with a recruiting agency that truly understands our culture and hiring needs.” She acknowledged that building rapport with an agency takes time but stressed that finding the right partner can be invaluable – especially when recruiting for niche or hard-to-fill positions. “Agencies with a solid understanding of our business act as an extension of our team, and they provide the support we need when recruiting bandwidth is limited,” she said.
Prestige Mold uses several recruiting avenues. “For most positions,” said Steging, “we use traditional recruitment methods, such as online ads, word of mouth, referrals, local high schools and traditional trade schools.” For engineering positions, however, the company has changed its approach, he said. “Our strategy for engineering team members has shifted from recruiting within the mold building trade to recruiting candidates straight out of college.”
Prestige Mold seeks team members who possess a high energy level and a desire to meet the company’s standards for manufacturing high-quality plastic injection molds. During the interview process, the company shares information about its culture and listens carefully for whether job candidates mirror and embrace aspects of that culture. “Our main approach,” said Steging, “is treating potential candidates like we treat potential customers. Like potential customers, candidates need to hear why we’re the best while, in the background, we are determining if they are a good fit for us. We try to engage the candidates in ways that may indicate the type of environment they will thrive in.” For Prestige Mold, the winning candidates
express a desire for a highly autonomous position also while signaling their desire to develop their skillsets and be the best at what they do. “The idea of a good fit,” said Steging, “must be mutual.”
Dynamic Group prides itself on a culture rooted in core values, such as compassion, integrity, gratitude, respect and determination. To convey its company culture during recruitment efforts and gauge a candidate’s reaction, careful attention is paid to key questions as well as to a candidate’s physical aspect. “We use behavioral-based interview questions designed around our core values,” Lasanen explained. “For example, we ask candidates about a time they worked on a challenging project or goal that seemed impossible, and how they overcame obstacles to achieve success.” The candidates’ responses to this question give the company insight into their determination, problem-solving skills and resilience. “Beyond structured questions,” said Lasanen, “part of telegraphing our culture is observing body language and listening carefully during interviews. It’s a subtle, yet critical, ‘vibe check.’ Additionally, we ensure candidates experience our culture firsthand by walking them through our facility. This allows them to see our commitment to excellence and teamwork in action, and we can assess their suitability by gauging their level of enthusiasm for our environment.”
Both companies have made changes in their recruiting strategies in the last several years. “As previously mentioned,” said Steging, “we go straight to the local university for engineering candidates instead of relying on recruiting within this seemingly shrinking industry.” For the shop floor and other candidates, Prestige Mold has started looking outside the mold building industry. “We used to rely on our reputation as the best mold builder in the area to recruit those who want to be the best,” he said. “We’ve exhausted that avenue, and we now look outside the industry for those who align with what we offer as an employer.”
Lasanen described the changes in the recruiting strategy at Dynamic Group. “One significant change was reintroducing a dedicated HR professional after several years without one,” she said. “This brought a renewed focus to recruiting and employee experience.” The company also adopted recruitment and onboarding modules in Paylocity. “What once was a cumbersome paper-based system now is fully electronic,” Lasanen said, “improving efficiency for both candidates and the HR staff. These updates have modernized our approach and ensured we stay competitive in today’s talent market.”
In the mold building business, as in many manufacturing businesses, it remains important to emphasize that the
With over 160 years of steel production experience backing their brands, Swiss Steel Group is not only a pioneer, but also a market leader in specialty steels. Their comprehensive range of Formadur®, Thermodur®, Cryodur®, and Mold Die® grades, produced by Deutsche Edelstahlwerke / Germany and Finkl Steel USA / Canada, allows you to choose the ideally suited mold material for your application. In addition, an extensive range of value added services provides you with more alternatives from one source, Swiss Steel USA / Canada.
www.swisssteel-group.com Info-USCA@swisssteelgroup.com +1 800 323 1233
industry has largely modernized, now substituting clean, bright, highly automated plants for the dingy, laborintensive operations of days past.
“This topic excites me,” said Lasanen, “because I love showcasing the innovation and pride within mold manufacturing. During interviews, we emphasize that candidates are interviewing us just as much as we are interviewing them. As part of the process, we take them on a walkthrough of our facility, where they see firsthand how high-tech, clean and safe our operations are.” Lasanen pointed out the value of employee word-of-mouth for spreading the news about Industry 4.0 and advanced manufacturing. “Beyond the physical space, our employees play a crucial role in telling this story,” Lasanen said. “Their pride in their work and the cutting-edge technology we use speak volumes. By interacting with our team, candidates quickly grasp the stimulating challenges and modern advancements that define mold manufacturing today. We’re passionate about what we do, and we look for candidates who share that enthusiasm.”
At Prestige Mold, Steging also uses plant walkthroughs, letting the spotless environment and the advanced innovation make an impact. “We must sell ourselves to potential candidates, so knowing how to compare and contrast the various industries is extremely helpful,” he said. “For example, after giving a machinist candidate a tour of our clean, climate-controlled environment and showing all the high-end equipment and automation, I’ll describe the typical aerospace manufacturing environment – a typical job shop environment. Then I’ll describe our business as dynamic and creative while noting that aerospace and other industries are repetitive widget producers, and their work often is carried out in uncontrolled environments. Being matter of fact about that stark contrast is the best tactic.”
Job seekers, as a group, sometimes lean toward employment opportunities that offer stability and a steady path for expanding trade skills. At other times or among other demographics, candidates want jobs that offer a chance to advance on a professional career path or to move into supervisory or management roles. “Prior to and during the COVID pandemic,” said Steging, “we had frequent inquiries about career paths and the potential for advancement, even though we were not specifically recruiting for supervisory or manager positions. Recently, however, we’ve seen a shift in candidates – toward valuing stability and skills development more – which is right in line with what we are seeking.”
Lasanen described what Dynamic Group has observed. “Candidates today are highly motivated by opportunities to gain new skills and advance their careers,” she said, “and they seem to be seeking this growth at a faster pace than in
the past. This eagerness is exciting because it reflects a new workforce that is engaged and ready to learn.” Dynamic Group offers robust opportunities for skill development, particularly through its apprenticeship program, which allows employees to develop expertise across various departments. “Beyond apprenticeships,” said Lasanen, “we also identify employees interested in career advancement through our performance conversation process, where they can express their goals for growth. This emphasis on skillbuilding and advancement aligns well with what today’s job candidates are seeking, making it an essential part of our recruitment and retention strategy.”
Holding onto good help is as important as attracting it in the first place. All the recruiting ingenuity in the world is for naught if a company cannot retain its employees. “At Dynamic Group,” said Lasanen, “retention starts with leadership accountability; employees value leaders who follow through on their intentions and promises.” She stated that for employees, being heard and acknowledged is crucial, as is providing flexibility when employees need it. “Whether it’s time off or simply being understanding on a tough day,” she said, “compassionate leadership fosters loyalty.”
Another key strategy at Dynamic Group involves being open and giving honest feedback. “Even difficult feedback,” she said, “when delivered kindly and constructively, helps employees feel valued and builds trust.” The company prioritizes timely conversations rather than waiting for formal reviews, addressing issues as they arise while celebrating wins and accomplishments along the way. “This proactive, transparent approach,” said Lasanen, “creates a healthy culture that helps us keep employees.”
“At Prestige Mold,” said Steging, “maintaining employee engagement is valuable for retaining highly motivated individuals. We know that it is key to provide internal and external resources for development and to present challenges regularly that result in a sense of achievement.”
Some companies have changed their workforce retention strategies in light of the wave of retirement by Baby Boomers. This, fortunately, has not been a problem at Prestige Mold. “We haven’t been impacted by this,” said Steging. “Our succession planning is regularly addressed.”
Dynamic Group has made changes. “About a decade ago,” Lasanen said, “Dynamic Group proactively addressed the anticipated retirement wave by establishing our apprenticeship program for mold builders.” The program spans three to four years and offers students or recent graduates in the field an opportunity to gain hands-on
experiences across all Dynamic Group departments, including custom and production mold building. “During this time, our leadership team recognized the invaluable knowledge of our veteran employees and encouraged them to become mentors,” Lasanen explained. “Many of our highly skilled employees nearing retirement embraced the challenge, sharing their expertise and preparing the next generation of mold builders. This mentorship has created a strong legacy of knowledge transfer and significantly softened the impact of retiring employees.”
The company also has reached out to retain or bring back retirees. “We offer flexible work schedules for those who are open to continuing in a part-time or consulting role,” Lasanen said. “This allows us to retain their expertise while providing them with the flexibility they may desire post-retirement. These strategies have helped us preserve the brain trust of our experienced team members while preparing for a strong future workforce.”
Dynamic Group has changes in the works. “In 2025, one of our primary focuses will be on developing leadership plans for employees who are interested in growing into leadership roles,” Lasanen explained. “This initiative represents the
first step toward implementing tailored development plans for a broader range of employees across the organization. By providing clear pathways for leadership growth, we aim to foster engagement and retain employees who are eager to progress in their careers.”
At the same time, Dynamic Group wants to acknowledge and celebrate its employees who value consistency and reliability over rapid advancement. “Not everyone wants to climb the career ladder at a fast pace,” said Lasanen, “and that’s okay. These steady and dependable team members are just as critical to our success as those who seek leadership roles. Recognizing the importance of stability and consistency as a form of development is a key part of our retention strategy. By balancing opportunities for growth with recognition of every employee’s unique contributions and goals, the company hopes to create an environment in 2025 where all team members feel valued, supported and motivated to remain with Dynamic Group.”
More information: www.dynamicgroup.com, www.prestigemold.com
May 7-9, 2025 | Grand Rapids, Michigan
A breakthrough idea can come from anyone, any place and from any business, large or small. One idea can unleash a realm of possibilities!
Set to take place at the Amway Grand Plaza Hotel, AMBA Conference 2025 – Breakthrough Innovation – will tackle the tough challenges faced by mold manufacturers today through content and connection opportunities.
On May 7-9, 2025, US mold manufacturing executives, managers, emerging leaders and industry suppliers will connect in Grand Rapids to identify new business opportunities, problem-solve challenges, share profitability and growth strategies, explore innovative technologies and so much more!
Highlighted programming will include a pre-conference session for up-and-coming AMBA Emerging Leaders, topicfocused pre-conference roundtable discussions, inspiring keynote presentations, breakout tracks addressing industry pain points and relevant industry trends, and best practices in profitability, continuous improvement, workforce development strategies and more!
How are others doing it better? Learn more and register at www.ambaconference.com.
Troy Nix is the executive director of the AMBA and serves as the emcee for AMBA Conference 2025. Known for his spirit, enthusiasm and belief in American manufacturing, Nix delivers an opening address that never fails to spark emotion in each attendee’s inner core. This year’s message will focus on Nix’s personal life experiences and the best practices that can power personal and professional growth. Nix’s tag line – “America Is What America Makes” – is an essential ideal that motivates those attending the conference to strive for excellence.
WEDNESDAY
1:00-3:50 p.m. Emerging Leaders Pre-Con Session (Optional)
4:00-5:00 p.m. Topical Rounds –All Conference Attendees
» Financial Performance Strategies
» Best Practices in Cybersecurity Measures
» Retention Strategies in the Workforce
» Continuous Improvement Initiatives
5:00-5:30 p.m. Supplier Meeting
5:30-7:00 p.m. Welcome Reception and Supplier Trade Fair
THURSDAY
7:00-8:00 a.m. “Business over Breakfast” Connections
8:00-8:20 a.m. Welcome Kick-Off
» Troy Nix, AMBA Executive Director
8:20-9:20 a.m. Opening Keynote Breakthrough
Innovation: How to Unleash Your Hidden Ingenuity
» Bill Stainton
9:20-9:50 a.m. Networking Break/Supplier Trade Fair
9:50-10:40 a.m. General Session Opportunity in Uncertainty: Navigating Changes in Today’s Global Supply Chain
» Omar Nashashibi, Inside Beltway
10:40-10:50 a.m. Member Recognition
11:00-11:50 a.m. Breakout Track – Industry Trends
12:00-1:00 p.m. Networking Lunch Or Lunch and Learn with Bill Stainton
1:10-2:00 p.m. Breakout Track – Business Tools
2:10-3:00 p.m. General Session Preparing for Economic Challenges and Opportunities in 2025 and Beyond
» Michael Fuez, ITR Economics
3:00-3:30 p.m. Supplier Trade Fair / Networking Break
3:30-4:30 p.m. Closing Keynote “Breaking Through Adversity: The Power of Purpose and Possibility
» Joe Roberts
4:30-5:00 p.m. Awards Celebration
5:00-7:00 p.m. Awards Reception
FRIDAY
7:00-8:00 a.m. “Business over Breakfast” Connections
8:00-9:15 a.m. Peer-to-Peer Roundtable Discussions
9:15-9:30 a.m. Networking Break/Supplier Trade Fair
9:30-10:15 a.m. The Balancing Act – New Hire Development and Company Performance (Panel Discussion)
10:15-10:30 a.m. Event Wrap Up
» Troy Nix, AMBA Executive Director 10:30 a.m. Conference Adjourned
Bill Stainton, keynote speaker and author
The manufacturing industry lives on innovation and ingenuity. From collaborative robots and automation to big data and analytics, innovation and ingenuity have defined US mold manufacturers. But what about those who don’t consider themselves “the creative ones?” What about those who think – as so many do – that innovation and ingenuity are for the others, but not them? In those members of the industry, Bill Stainton, a 29-time Emmy Award-winning keynote speaker, would like to have a word. Innovation, creativity and ingenuity are NOT part of a private club but are instead an open playground – and everyone is invited! Come hear what Stainton has to say and learn how everyone can unleash their hidden ingenuity.
Joe Roberts, keynote speaker and author
In this impactful keynote, Joe Roberts, leadership coach, motivational speaker and author, takes his audience through a journey on how to build the resiliency needed to succeed in the face of adversity and change. Sharing the story of his catastrophic failure and extraordinary success, Roberts empowers leaders to see beyond their perceived limitations to connect with their purpose and passion; achieve more with fewer resources, while overcoming roadblocks and a limiting mindset; and lead others to seek clarity on their potential and confidence to accomplish an endless realm of possibilities.
Omar Nashashibi, Inside Beltway
In his first few months in office, President Trump has shaken supply chains around the world and has begun creating opportunity for American manufacturers. Omar S. Nashashibi, founder of AMBA’s lobbying partner Inside Beltway in Washington. D.C., will report on how the tariff actions and trade negotiations the White House is undertaking impact US mold manufacturers. From Canada and Mexico to the European Union and China, the President is expediting negotiations and acting quickly to impose tariffs and/or use them as negotiating tools. With access to recent insights on trade and taxes, attendees will be better able to navigate uncertainty over the tax on R&D, expiring individual rates and lower expensing for equipment and identify opportunities to reshore work as a result of the US trade actions.
2025 and beyond will present opportunities as well as challenges to US mold manufacturing executives. Inflation and interest rates will return on the wings of government spending and will be compounded by a tightening labor market, global demand and higher cost production inputs from raw materials to electricity. During this session, Michael Fuez, ITR Economics, will discuss the timing and actions necessary to navigate the twin challenges of inflation and interest rates as executives prepare for what’s coming this year and beyond. Attendees will walk away with information on the domestic and global economic landscape, a sense of how conditions may vary by industry and the ways in which they can position their companies for maximum return in the coming years.
Joe Roberts, keynote speaker and author
Facilitated by Joe Roberts, this powerful, hands-on workshop will equip emerging leadership with the strategies and tools to help build exceptional mental resilience, identify self-limiting beliefs and develop the confidence necessary to pursue personal and professional goals with clarity and purpose. Attendees will learn how to implement a process for identifying the unconscious drivers that block productivity and goals; build a simple framework for tackling goals; minimize conflict while conducting productive performance and accountability discussions; navigate personal and situational roadblocks and see themselves, their teams and their goals through a new “Possibility Mindset.”
HISTORIC LUXURY IN DOWNTOWN GRAND RAPIDS
Bill Stainton, keynote speaker and author
In this roll-up-your-sleeves, hands-on session, attendees will take the techniques and ideas presented during Bill Stainton’s keynote and apply them directly to their business! Together, attendees will explore strategies to identify and tackle their biggest challenges.
Discover historic charm and modern comfortsattheAmwayGrandPlaza Hotel,CurioCollectionbyHilton.Nestled downtownbytheGrandRiver,thehotel isperfectlysituatedforexploringthe city’smanyattractions,restaurants,craft breweriesandmore.Thepropertyoffers nine on-site restaurants and bars, indoor pool,fitnesscenterandonsitespa.The specialAMBArateis$194/night.Toget the AMBA rate, reservations should be madeonorbeforeApril15.
For reservations, visit www.ambaconference.com.
This session is back by popular demand! Growing peer-to-peer networks is a primary component of AMBA Conference 2025. Attendees will have the chance to interact with peer groups during this session on topics that are unique to their job functions in their specific groups. Areas covered will be operations, owners/presidents/CEOs, sales and marketing and workforce development.
By Rachael Pfenninger, director of strategic execution, AMBA
The year is 2025, and President Trump has ordered additional tariffs across the board on goods from Canada, Mexico and – most crucially – China. At the time of publication, only the additional 10% tariff had been placed on China, while Canadian and Mexican tariffs each are pending further negotiation. This complicates matters for US mold builders because, while some industries – like defense and aerospace – continue to boom, others – like automotive and consumer products – are more uncertain, as their destinies are tied to the various tariffs or other government regulations that may or may not be put in place.
These changing conditions mean that many domestic mold manufacturers must consider changing with them. Whether that means finding new ways to reduce overhead and improve profitability or pursuing new customers and/ or new market opportunities, it all must be considered alongside other existing challenges, like continuing foreign competition and the need to attract and develop an untrained workforce.
Data from AMBA’s recent 2025 Business Forecast Report, which gathered inputs from nearly 80 US mold manufacturers from early December 2024 to late January
2025, points to these many considerations of today’s industry executives. For example, while the automotive, consumer products and medical/dental/optical markets continue to be those most served by report respondents, a whopping 72% of respondents are considering diversifying into new markets – specifically, aerospace/aircraft and defense/military (Chart 1).
Although foreign competition, healthcare and benefits costs and new business development are weighing heavily on US mold manufacturers, workforce development and cost pressure continue to be the biggest challenges for the industry (Chart 2). Despite identifying these challenges, when asked what single major activity is planned to improve company competitiveness in 2025, over a third of report respondents – 39% – cited either investments in new or updated equipment or a strategic sales focus as their top priority. In contrast, only 26% cited adding/restructuring personnel or workforce development as a main focus in the coming year, even though these areas are related to the top challenges cited.
In light of the opportunities that do exist for US mold manufacturers, not all facilities responding to this year’s
tAlthough foreign competition, healthcare and benefits costs and new business development are weighing heavily on US mold manufacturers, workforce development and cost pressure continue to be the biggest challenges for the industry.
survey are reporting positive business conditions. For example, 53% of respondents report that their company’s overall state of business is good or excellent and almost one-fifth (19%) report business conditions that are bad or poor.
However, of those that report sales up over the last quarter, 81% report changing conditions to new programs and/ or volume increases with current customers – a positive indicator for those that have been waiting on the progression of promised purchase orders and on-hold programs.
Conditions for the domestic mold manufacturing community will continue to change dramatically in the coming days and months. In order to stay in tune with the state of business and to dive more deeply into some of the information covered in the 2025 AMBA Business Forecast Report, particularly trends related to quoting, sales, business performance, planned investments, workforce conditions, the state of the plastics industry and more, visit AMBA’s website to access a recording of the 2025 State of the Industry address.
AMBA’s 2025 Business Forecast Report is available for purchase ($399 for members; $899 for non-members) at www.amba.org. This report utilizes data from 33 economic indicator questions to showcase sales trends, profit levels, capital expenditures, shop and design employment levels and challenges, as well as 2024 performance, fourthquarter performance forecasts and expectations for 2025. Additionally, the 2024 Wage and Salary Report also is available for purchase. To view these reports and others, visit the Publications page at www.amba.org.
May 7-9, 2025 | Grand Rapids, Michigan
The AMBA Conference 2025 – “Breakthrough Innovation”–is designed for US mold builders and industry suppliers looking to drive business growth, build executive connections and exchange insights with peers.
Don’t miss this opportunity to explore industry best practices, tackle shared challenges and gain valuable insights into economic trends shaping future business opportunities
For more information, visit www.ambaconference.com.
Nominations for AMBA’s Emerging Leaders Rising Star, Mold Builder of the Year and Tooling Trailblazer of the Year Awards now are being accepted.
AMBA members may nominate themselves or a peer and should be from member companies in good standing. Award recipients will be recognized at AMBA Conference 2025 in Grand Rapids, Michigan, May 7-9, at the Amway Grand Plaza, and will receive a prestigious award and a $5,000 scholarship grant from Progressive Components to be given to the educational institution, project or initiative of choice. The Rising Star winner will receive an award and a $500 endowment to be used toward professional development.
For more information or to submit a nomination, contact Olivia Shotts at oshotts@amba.org
Health and Benefits Survey Now Open
AMBA has launched its 2025 Health and Benefits Survey, which will gather data related to health and benefits packages offered to employees by mold manufacturers across the US. Collected data will include the following:
• Company cost and employee participation
• Strategies to control cost
• Current plans offered to employees
• Additional benefits and retirement programs offered
Compiled data and results will be shared at no cost with survey participants. To participate and gain access to the final report, visit www.amba.org/events.
Available for Purchase – AMBA 2025 Business Forecast
AMBA’s annual 2025 Business Forecast Report showcases data on sales trends, profit levels, capital expenditures, shop and design employment levels and challenges faced in the industry. Data from this year’s report is pulled from surveyed responses on 33 economic indicator questions that cover 2024 performance, fourth-quarter performance and forecast expectations for 2025.
For access to the State of the Industry webinar recording, visit www.amba.org/events.
Available for Purchase – AMBA 2024 Wage and Salary Report
AMBA’s annual Wage and Salary Report is the premier compensation study for the US mold building industry, providing an in-depth analysis of over 50 job classifications across diverse market sectors. This year’s report also includes benchmarks on cost-of-living adjustments, vacation benefits, employee incentives, salary changes, hiring trends and more, offering mold manufacturers critical insights to remain competitive in today’s market.
For more information or to purchase this report, visit www.amba.org/publications
Connect with AMBA at PTXPO 2025, March 18-20, Rosemont, Illinois, in booth #1436 for the latest resources and upcoming events. Use promo code AMBA100 for a FREE expo hall pass. Be sure to connect with AMBA’s Emerging Leaders over drinks at Crust Brewing on March 18 from 4-5:30 p.m. (CST) and at AMBA’s Member Appreciation Reception at booth #1436 on March 19 from 2:30-4 p.m. (CST).
For more information on AMBA receptions taking place on March 18 and 19, visit www.amba.org/events.
The Financial Literacy Series Continues
y How to Increase Enterprise Value for a Future Sale – March 26, noon-1 p.m. (EST)
y Understanding Financial Statements (Part 2) – April 16, noon-1 p.m. (EST)
All sessions will provide actionable insights to help mold manufacturers improve financial health and long-term stability.
Lean
Manufacturing Case Studies
March 27, April 3, April 10 and April 24
Join AMBA Emerging Leaders as they hear real-life case studies from manufacturing members on the implementation of continuous improvement initiatives within their facilities. Attendees will walk away with insight into the challenges that have driven continuous improvement, the process of implementation and each facility’s method for evaluating program success. The sessions will include a live, peerdriven activity alongside the member presentation.
These events are available to AMBA members at no cost. For more information and to register, visit www.amba.org/events
Nearly 30 golfers gathered on February 7, 2025, at the Navy Golf Course – Seal Beach, Cypress, California, for a charity golf outing to benefit iWarriors. Hosted by M.R. Mold & Engineering, the event raised nearly $15,000 in support of severely injured members of every branch of the Armed Forces by providing them with personalized tablets to aid in their return recovery and reintegration.
For more information, visit www.iwarriors.org.
AMBA proudly introduces The Capitol Beat. Delivered monthly from Inside Beltway, AMBA’s advocacy partner in Washington, D.C., this email newsletter provides information on the latest happenings in Washington that are important to the mold manufacturing industry.
Join AMBA members on March 13, noon-1 p.m. (EST) for the first-quarter Advocacy update provided by Omar Nashashibi, Inside Beltway, to stay up-to-date on the latest issues impacting the industry. For more information and to register, visit www.amba.org/events.
Steenson Enterprises 126 Army Rd. Leonard, Michigan 48367
Robert Ellerman, president
Email: rellerman@ellermaneng.com
Phone: 248.628.0036
Website: www.steenson-enterprises.com
Steenson Enterprises engineers, designs and manages the build of injection molds, with specializations in plastic injection, metal injection and low-pressure wax molds for the investment casting industries. Steenson also provides custom CNC machine work to other mold shops and suppliers to help when capacity issues arise. Industries served include automotive, DoD, firearm/hunting, medical, consumer products and more.
Hexagon Manufacturing Intelligence 250 Circuit Dr. North Kingstown, Rhode Island 02852
Dick Allen, North American sales manager – Mold and Die Email: dick.allen@hexagon.com Phone: 937.668.2578
Website: www.hexagon.com
Hexagon’s mold suite provides a complete design-to-manufacturing workflow for plastic injection mold manufacturers. Hexagon’s industry-specific CAD/ CAM tools power advanced mold design, simulation and CNC programming for precision and efficiency. With VISI, WORKNC and automation powered by Nexus, manufacturers can optimize toolpaths, verify processes and streamline collaboration from design to final delivery. Serving automotive, aerospace, medical devices and consumer goods, Hexagon helps moldmakers improve quality, cut costs and accelerate production.
At Plastic Engineering & Technical Services, we are.
We define performance. For nearly 30 years, we’ve helped our customers to produce more e ciently, with lower cycle times and lower per unit costs.
Our new compact stainless steel, modular unitized system features exible heaters that can be utilized o n multiple designs, so you don’t have to stock custom bent heaters Our new drop heaters provide more uniform heating and feature smaller pockets and no clamps They have in-line ow restrictors
for better process repeatability, and no over-pressurizing the cylinders. It all adds up to a reduced sized hot runner system, shorter heating times and better tool performance.
We deliver value. We complement our hardware with leading-edge analytical tools, including Mold ow® and MOLDEX3D so ware. We’ll work with you on design issues and optional gating solutions before the mold or hot runner manifold system is ever built. Use us for the mold ow analysis and the manifold build, and we’ll do whatever it takes to make your hot runner/manifold system work to your complete satisfaction.
We’re committed to your success. Find out more. Call us today at 248.373.0800 or visit us at www.petsinc.net.
ANCA, Melbourne, Australia, a manufacturer of CNC grinding machines, has released an advanced peel grinding solution on its MX7 platform that offers seamless finished tool grinding in a single setup, including the initial blank preparation phase. This set-up features the P-axis Arobotech, which supports blanks at the grind point, enabling the efficient production of various tools with a surface finish below 0.2 Ra. The MX7 platform is equipped with sixwheel packs and supports the grinding of various tool shapes in a single set-up, eliminating the need for wheel changes. For more information, visit www.machines.anca.com.
integrated fountain ensures efficient cooling to the cavity and helps to reduce cycle-times. The two-stage ejector E 1850, which can be used both as a leading-type two-stage ejector and as a latch lock, comes in sizes from 14-50 mm. For more information, visit www.meusburger.com.
CAM-TOOL, Oldcastle, Ontario, a company specializing in die and mold manufacturing tools, has released Version 20 of its software, which introduces features that streamline the machining process, enhance precision and reduce setup time for CNC machinists and engineers. The Version 20 includes a 5-axis roughing capability, AI-driven data mining methodology, adaptive roughing mode to manage tool load and settings for optimization, stock calculation and transforming machining workflows. For more information, visit www.camtool.com.
HASCO, Fletcher, North Carolina, a supplier of standard components and accessories for the tool and moldmaking industry, has launched a line of innovative plug inserts and cables that allow fast and space-saving wiring of power/ signal plugs to the mold. The extended product range includes an aluminium-shielded cable, a tool-free cable, a space-saving plug for 12 control zones and a compact plug for seamless integration. For more information, visit www.hasco.com
Meusburger, Mint Hill, North Carolina, a company that provides high-precision standard parts, has added an inclined ejector unit E 3280 and two-stage ejector E 1850 as solutions for the areas of demolding elements and slide systems. The new inclined ejector unit E 3280 enables simple demolding for very large undercuts up to 70 mm. Its
Progressive Components, Wauconda, Illinois, a company that develops and distributes components for the production tooling industry, has expanded its blade ejectors with new features to reduce in-house machining. Referred to as “MoldReady,” this component arrives with features completed and a configurable part number that eliminates the need for a print to be provided. With Progressive’s configurable part numbers, ordering blade ejectors with radii is simplified. Start with the original part number (BE125-046L6.155) and add the radius size to the part number (BE125-046L6.155-K.094-R.020, as an example with a .020" radius). For more information, visit www.procomps.com.
Seco Tools, Troy, Michigan, a company that provides metal cutting solutions for milling, stationary tools, holemaking and tooling systems, has delivered the Jetstream Tooling® Integrated (JETI) toolholders. The benefits of the JETI toolholders include high-pressure coolant to round, positive turning inserts for effective profiling and pocketing in difficult-to-cut materials. JETI toolholders eliminate hoses and spare parts associated with high-pressure coolant, and 3D-printed coolant clamps provide internal coolant channels for effective cutting-zone cooling and chip control. For more information, visit www.secotools.com.
Globeius, Miami, Florida, a supplier to the plastics industry and the exclusive distributor of Mouldpro products for North America, now distributes a complete line of Mouldpro soft tools and gate cutters. Mouldpro’s line of soft tools includes bronze pliers, brass non-scratching scrapers, brass hand tools, knock-out bar, deburring tools, deburring blades, ceramic knives, copper gauze and brass hand brush. In addition, Mouldpro heated nippers are handheld tools with built-in heaters for trimming sprues from molded parts. For more information, visit www.globeius.com
amba members saved an average of $6K in mro spend in 2024$4,800 more than average member dues.
Get involved to start saving today.
By Rachael Pfenninger, director of strategic execution, AMBA
It has been nearly a year since AMBA Conference 2024, where AMBA’s Emerging Leaders gathered in Grand Rapids, Michigan. There, members of the AMBA community developed skills in assertiveness, peer connection and leadership and stepped off the shop floor to forge industry connections. But what has the Network been up to since? Well… it’s been busy!
After the Network’s pre-conference session at the annual AMBA Conference, it held its second Leadership Retreat, which featured a live, in-person workshop alongside two facility tours. The year continued with a virtual leadership series shared with young professionals from other manufacturing associations, offering abundant peer connection and learning opportunities that have gone on to shape the supervisory and peer connection skills of AMBA members.
As it approaches the end of the first quarter of 2025, the growth of the Network shows no signs of slowing down. In addition to adding three new mold manufacturers to the Emerging Leaders Advisory Board and two new supplier members, AMBA has forged ahead with its next Emerging Leaders virtual series. Launching April 2025 (and now open for registration at www.amba.org/events), this series will detail a variety of lean practices and continuous improvement initiatives from member facilities.
As virtual programming for 2025 takes off, planning for AMBA’s next pre-conference session already has begun.
Registration now is open for AMBA Conference 2025 and, specifically, the Emerging Leaders pre-conference session, “The Brain Science Behind Achievement.”
Facilitated by Joe Roberts, keynote speaker and fourtime author, this hands-on workshop will equip emerging leadership with the same systems and brain science leveraged by Roberts as he walked across North America during the Push for Change campaign. Roberts will share evidence-based strategies and proven methods that can help AMBA’s emerging leaders build exceptional mental resilience, identify self-limiting beliefs and develop the confidence necessary to pursue personal and professional goals with clarity and purpose.
During this session, attendees will learn how to implement a process for identifying the unconscious drivers that block productivity and goals, build a simple framework for tackling one’s goals through the use of a practical, sciencebased model, minimize conflict while conducting productive performance and accountability discussions and navigate the personal and situational roadblocks common to challenge and change.
For companies interested in advancing the leadership development and supervisory ability of its emerging leadership, an exclusive offer now is available for those interested in attending the pre-conference session, along with the entire conference. To learn more about the programming at the conference and the offer available to interested conference attendees, visit www.ambaconference.com or contact the AMBA team at info@amba.org.
Young professionals are vital to the moldmaking industry, and it is important to acknowledge those making strides in shaping the industry’s future. MoldMaking Technology is recognizing our industry’s young talent through our 30 Under 30 honors program.
By Lindsey Munson, editor, The American Mold Builder
The Plastics Technology Expo (PTXPO) is a three-day showcase encompassing cutting-edge technologies and innovations set to take place on March 18-20, 2025, at the Donald E. Stephens Convention Center in Rosemont, Illinois. The expo will offer attendees an expansive exhibit hall, educational sessions, a first look at the newest plastics machinery and a variety of networking opportunities.
The Convention Center will open on Tuesday from 10 a.m. to 4 p.m., on Wednesday from 9 a.m. to 4 p.m. and on Thursday from 9 a.m. to 3 p.m. PTXPO tickets can be purchased online through March 20, 2025, for the price of $70; use promo code AMBA100 for a FREE expo hall pass.
American Mold Builders Association (AMBA) will be exhibiting at the event – stop by booth #1436. AMBA will be promoting two of its premier benchmarking reports, including the 2025 Business Forecast Report and its recent 2024 Wage and Salary Report. The 2024 AMBA Wage and Salary Report features high, low and average rates of pay across over 50 job classifications commonly found in mold building. The 2025 AMBA Business Forecast
AMBA MEMBER EXHIBITORS:
Alliance – Booth #1426
American Mold Builders Association –Booth #1436
Bales Metal Surface Solutions –Booth #1231
Crystallume – Booth #1234
Custom Etch, Inc. – Booth #1509
Decatur Mold – Booth #1524
DME Company – Booth #1314
DMS – Booth #1614
Duro-Chrome Industries, Inc. –Booth #1535
Dynamic Tool – Booth #1338
Report provides an in-depth analysis of past, current and anticipated business conditions. The reports are available to purchase for AMBA members and nonmembers; however, “sneak peeks” can be viewed by attendees at PTXPO.
The American Mold Builder also will be at booth #1436, and attendees will be able to pick up the latest issue of the magazine.
AMBA member exhibitors are gearing up to showcase the latest innovations, giving a firsthand look at cutting-edge technologies and equipment within the molding industry. For three days, it’s a prime opportunity to join fellow molders, moldmakers, brand owners, OEMs and their suite of suppliers to explore, learn and connect. Examples of the newest machinery and applications to be showcased include blow molding machines for packaging, extrusion-specific dies, conveying systems and more. Processors in the moldmaking pavilion will be available to provide real-time solutions and valuable insight to attendees regarding their operations. Be sure to stop by the AMBA member exhibitors featured in the box below.
Eden Mold Company – Booth #936
HASCO – Booth #909
INCOE Corp. – Booth #1330
Kruse Analysis – Booth #1337
Legacy Precision Molds – Booth #1035
M.R. Mold and Engineering –Booth #1236
Mastip, Inc. – Booth #1219
Maximum Mold Group – Booth #1240
Minco Tool and Mold – Booth #1518
Moldmaking Technology –Booth #1235
Oerlikon HRSflow – Booth #821
Omega Tool, Inc. – Booth #1331
Osco, Inc. – Booth #1715
PCS Company – Booth #1123
Progressive Components –Booth #1109
Self Lube – Booth #1514
Slide Products, Inc. – Booth #1427
The American Mold Builder – Booth #1436
Triangle Tool – Booth #1028
Uddeholm USA – Booth #1327
Vincent Tool Tech Corp. –Booth #1326
Westminster Tool – Booth #1429
Join AMBA executives, management teams and emerging leadership as they forge peer connections at PTXPO 2025 this March.
Young Leaders
Meet Up
March 18, 4-5:30pm Crust Brewing 5500 Park Pl., Rosemont, IL
Members
Appreciation Reception
March 19, 2:30-4pm PTXPO Tradeshow Booth #1436
Thank you to our event sponsors
The expo will be organized into major process pavilions, featuring over 200 exhibitors. This gives attendees the ability to easily plan their show experience and navigate the exhibitor floor. The pavilion categories include 3D printing, auxiliary equipment, extrusion and thermoforming, injection and blow molding, materials, moldmaking, recycling, and robotics and automation.
In addition, there will be educational opportunities with leading industry experts on topics such as sustainability, workforce development, new technologies, supply chain management, sourcing and more.
In planning for the show, be sure to visit MyPTXPO Planner on the website. There, attendees can create a show account that helps them coordinate appointments, add exhibitors and products, highlight educational sessions and more.
For more information on PTXPO 2025 and to find AMBA-member exhibitors, visit www.plasticstechnologyexpo.com Services
• Finishes to all SPE-SPI standards
• Diamond Lapping
• Textured Surface Prep Benching
• Quoting from Drawings, Prints, Pictures and Parts
• On-Site Support
Capabilities
• 50+ Polishers
• 40 ton Capacity
• 24 hours – 7 days Pick-up and Delivery
• 3-D CAD File Capabilities Partnerships
• Welding
• Plating
• Texturing
Ph: 847-352-5249 Fx: 847-352-4052
First Quarter Advocacy Update, March 13, www.amba.org/events
PTXPO 2025, Rosemont, Illinois, March 18-20, www.plasticstechnologyexpo.com
Young Leaders Meet-Up Reception at PTXPO, Crust Brewery, Rosemont, Illinois, March 18, www.amba.org/events
Member Appreciation Reception at PTXPO, Booth #1436, Rosemont, Illinois, March 19, www.amba.org/events
Financial Literacy Series: How to Increase Enterprise Value for a Future Sale, March 26, www.amba.org/events
Emerging Leaders Lean Series, March 27, www.amba.org/events
Emerging Leaders Lean Series, April 3, www.amba.org/events
Emerging Leaders Lean Series, April 10, www.amba.org/events
Financial Literacy Series: Understanding Financial Statements (Part 2), April 16, www.amba.org/events
Emerging Leaders Lean Series, April 24, www.amba.org/events
AMBA Conference 2025, Grand Rapids, Michigan, May 7-9, www.ambaconference.com
Second Quarter Advocacy Update, June 26, www.amba.org/events
The 2-Stage S-Core. Designed specifically to tackle the most challenging geometry in injection-molded components, this innovative solution employs an advanced two-step release mechanism to free threads and complex undercuts prior to final ejection. By gradually collapsing in stages, the system achieves an undercut release of up to 23%!