
37 minute read
Training Update
from October 2020
by PHAM News
BESA unveils online learning
The Building Engineering Services Association (BESA) has opened its new online Academy delivering a comprehensive programme of training courses, assessments and CPD for individuals, employers and training providers in the building services sector.
Individuals will be able to access all of the resources needed to improve their existing skills and learn new ones while also keeping ŶĞāĢũŨŽÖķĢƩóÖŶĢŋłŭÖłùóŋĿťāŶāłóĢāŭŽťŶŋ date. The Academy will also help employers and managers ensure their workforces are ĕŽķķƘŨŽÖķĢƩāùÖłùÖðķāŶŋóŋĿťķƘƒĢŶĞ legislation and industry standards. ̵RŶƒĢķķÖķŭŋÖĢùāĿťķŋƘāũŭ̪āƦŋũŶŭŶŋťķŽė skills gaps by making access to the appropriate ŶũÖĢłĢłėāÖŭĢāũ̇ĿŋũāƪāƗĢðķāÖłù̇ŶĞāũāĕŋũā̇ more appealing to a wider section of the population. All training modules are accessible from a smartphone, tablet or laptop whether the user is at home, at work or on the move.
Training providers are invited to outsource the online learning elements of their courses to BESA, freeing them up to focus on the ÖŭťāóŶŭŶĞÖŶũāŨŽĢũāťĞƘŭĢóÖķťÖũŶĢóĢťÖŶĢŋł̵̍
“Online learning really came into its own during the lockdown months,” says BESA president Neil Brackenridge. “It proved the value of being able to access course materials from anywhere and at any time, which is exactly the BESA Academy model.” ͻ phamnews.co.uk̓ˡ˛˙̓˚˞


Ask questions, get video answers
Baxi has developed a new way to help installers with boiler queries, by introducing #BaxiCam. Gas Safe engineers can submit their questions on Facebook and receive video responses from the Baxi training experts. #BaxiCam will see the Baxi team use a GoPro camera to show installers the inside of boilers and help explain what ŶĞāƘÖũāùŋĢłė̇ƒĞĢķāÖłŭƒāũĢłėŭťāóĢƩó questions. To submit a question, installers simply need to head over to the company’s Facebook page and send the team a message or comment.
Steve Owen, national training manager at Baxi, says: “Following the success of our

Lockdown Learning and Burning Questions video series, we know installers really value seeing helpful video content. #BaxiCam takes this support one step further, by ÖķķŋƒĢłėāłėĢłāāũŭŶŋĞÖƑāŶĞāĢũŭťāóĢƩó questions answered in a way that mimics Viva Training Academy has joined forces with gas installer YouTuber, Allen Hart, to create useful tips and advice videos for would-be and existing heating engineers, as well as a Facebook group where members can ask questions and share experiences.
With nearly ˜˙̇˙˙˙ followers and over ˡˠĿĢķķĢŋłĞĢŶŭ̇ķķāłŋƦāũŭťũÖóŶĢóÖķ how-to videos and product reviews for gas installers and plumbers throughout the UK. His videos make use of Viva’s centre based in Halifax, and the company’s expert trainers. Allen, who also runs a plumbing and heating business, features Viva trainees in his videos, some of whom are completing work placements with CCH as part of the portfolio element of Viva’s Managed Learning Programme (MLP) for Expert Academy is the name of Ideal Heating’s new training platform for installers. The courses and content cover the skills and knowledge needed to work with the company’s domestic and commercial product ranges and will be rolled out across its sister brands – Keston by Ideal Heating, Hamworthy Heating, and ACV – later this year. ¦ĞāƩũŭŶƒÖƑāŋĕóŋŽũŭāŭƒĢķķðā delivered in a digital environment with a choice of two formats, with in-person sessions to follow at a later date.
The on-ùāĿÖłùŭāũƑĢóāŋƦāũŭÖũÖłėā of interactive e-learning modules and assessments for installers to complete at their convenience, supported by video content, tips and guides – all of which is mobile-friendly to help with troubleshooting on the job. Anyone with a free Expert Academy account can log in Get up to speed on RPZ issues
Resideo is encouraging companies that undertake work in reduced pressure ơŋłā̛Ñ̜ƑÖķƑāƩŶŶĢłė̇ŶāŭŶĢłė̇ commissioning and reporting to ensure that all of their registered RPZ testers are familiar with the new approved installation method – Issue ˛ of AIM ˙ˡ-˙˚ – for Type BA devices. attending a training course in person. Gas Safe engineers are invited to submit their questions to us and we’ll create a bespoke ̌ÖƗĢ!ÖĿƑĢùāŋ̇ŶÖĢķŋũāùŶŋŶĞāĢũŭťāóĢƩó query.”
Ask your #BaxiCam questions by visiting www.facebook.com/baxiuk, where you can ÖķŭŋƩłùŶĞāƩũŭŶƑĢùāŋĢłŶĞāŭāũĢāŭ̍
The company is also supporting installers with the reopening of its Warwick Commercial Training Academy. Following a period of closure due to Covid-˚ˢ̇ the academy is once again providing free in-person single-day courses on Andrews Water Heaters and Potterton Commercial products.
Before reopening, full and detailed risk assessments were carried out. For safety purposes, spaces on each in-person course ͻ phamnews.co.uk̓ˡ˛˙̓˚˟
Installer YouTuber joins forces with training provider


is limited to three people. new entrants to the gas industry.
Allen is determined to raise industry standards, and says his videos are designed to educate householders as well as new gas engineers.“Working with Viva is the icing on the cake for me,” he says. “I’m delighted to be helping Richard Firth (Viva’s MD) in all he’s doing to support new people coming into the industry. I hope we can continue working together to promote the very highest standards and ensure those coming into the industry are ťũŋťāũķƘŶũÖĢłāùÖłùƩŶĕŋũťŽũťŋŭā̧̍ ¦ŋÖóóāŭŭķķāł̪ŭƑĢùāŋŭ̇ƩłùĞĢŭ YouTube channel by searching for ‘Allen NÖũŶ̪̇ŋũĕŋũŶĞāƑĢùāŋŭŭťāóĢƩóÖķķƘĿÖùāĢł collaboration with Viva Training Academy, ͻ phamnews.co.uk̓ˡ˛˙̓˚ˠ
Classroom experience from home
use the reader link below.

and access the content they need.
The virtual classroom option is also free to use. Installers will be taught by a live trainer, again supported by a range of multimedia content to bring the sessions to life. Available to book now, there are two free live courses taking place per day, with maximum class sizes of ˚˙ to˚˛. Use the link below to book onto a course.
ͻ phamnews.co.uk̓ˡ˛˙̓˚ˡ
The publication of AIM ˙ˡ-˙˚Issue ˛ by the Water Regulations Advisory Scheme (WRAS) marked the start of a transition period which will end on ˠth January ˛˙˛˚, when Issue ˚ will be withdrawn.
Matt Watson, UK commercial and ĢłùŽŭŶũĢÖķŭÖķāŭ̵ķāÖùāũÖŶāŭĢùāŋ̇ŭÖƘŭ̆ “By undertaking the training, testers can work to the highest standards and continue to help their customers comply with their legal requirements.” ͻ phamnews.co.uk/ˡ˛˙̓˚ˢ
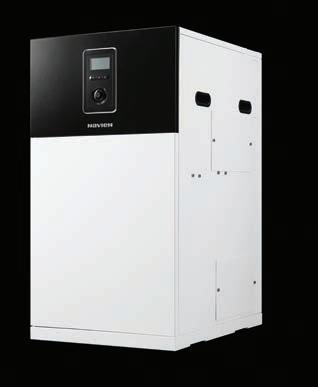




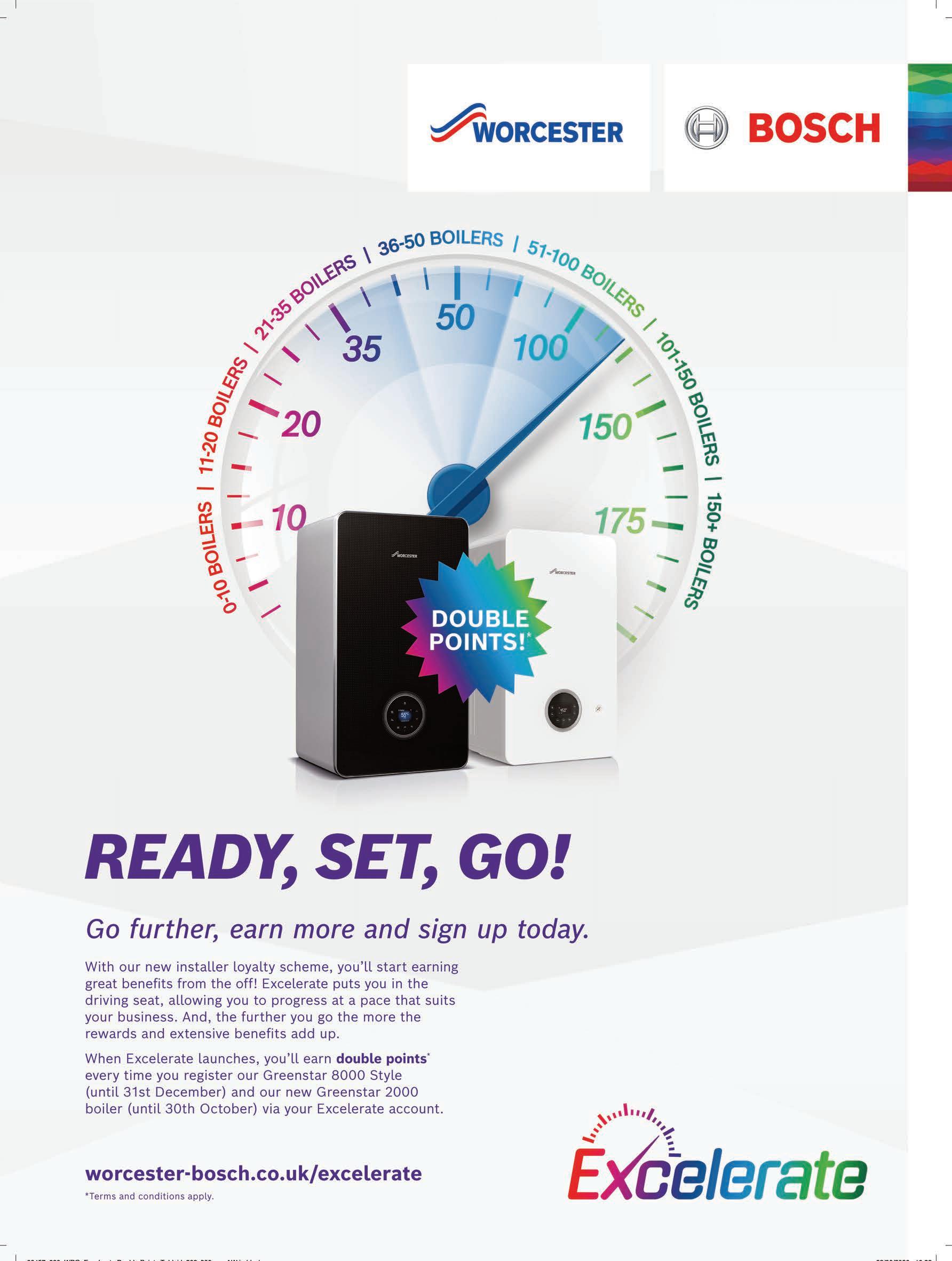
Benchmark app to reduce paperwork
Benchmark is unveiling a new app that is set to ease admin around boiler installation and servicing. Billy Wilgar from the Benchmark Steering Group explains how it will work and why it will benefi t installers and their customers.
Most engineers will be familiar with the Benchmark code of practice, the universal checklist developed to ensure best practice and accountability in the plumbing and heating industry.
Life in lockdown has resulted in an accumulation of routine maintenance jobs and servicing demand, leaving less time than ever to complete the allimportant paperwork. So in a bid to streamline the process and make the lives of busy engineers easier, Benchmark is going digital.
Since its introduction in 1999, the Benchmark checklist has played a critical role in boiler installation, commissioning and servicing, from raising industry standards and enhancing accountability, to off ering consumer protection and peace of mind.
Winter is inevitably a busy time for the heating and hot water industry, but this year, engineers are set to be busier than ever. With a backlog of routine maintenance to catch up on as a result of lockdown, and an increase in home heating and hot water use as people continue to spend more time at home, there is a clear need to streamline the installation process, to make it quicker without a drop in standards.
Billy Wilgar
Deputy chair of the Benchmark Steering Group
APP OBJECTIVES
Remove the need for paperwork by digitising vital information
Act as a data hub by storing unit-specifi c records available to any engineer working on a boiler
Reduce the time engineers spend on fi lling in the checklist by hand Create a ‘boiler passport’ for consumers so that they know when their boiler is due for a service
Data delivery Recognising that time pressures and ways of working have evolved since its original launch, the Benchmark app is designed to bring the administration side of boiler maintenance up to date by off ering engineers a way to complete and store the paperwork digitally – all at the touch of a button.
Free to download on either a phone or tablet, the app will serve as an information hub for each boiler’s history, allowing unit-specifi c access to the records of a heating system, even if the engineer has not previously worked on the appliance.
This means engineers can use the app to get up to speed on a boiler in a matter of minutes before completing a service, and signifi cantly reduce time spent fi lling in the checklist by hand. The app can also be used with or without connection to the internet, with data automatically uploading once connection occurs.
As part of its launch, an early version of the digital checklist will be available for engineers to trial and provide feed back, enabling Benchmark to tailor the application to the preferences,
T The app can facilitate new installation and servicing by recording vital information on a data hub
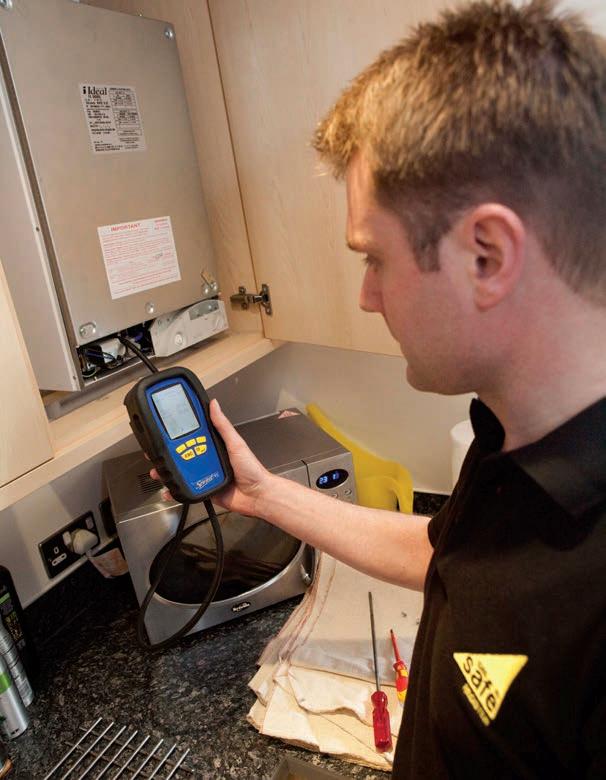
needs and expectations of industry professionals.
As we move closer to a paperless society, there is a growing acceptance that the plumbing and heating industry must do likewise. After all, it is no stranger to technological advancement, with conversations surrounding the future of heating systems particularly prevalent, and the need to refl ect this in everyday plumbing and heating protocols is increasingly apparent.
Revenue opportunity Aside from the more obvious benefi ts, which include a boost in the effi ciency and quality of boiler servicing, the digitisation of Benchmark will also off er engineers an additional opportunity to increase revenue. The digital checklist will help to generate more registrations, as well as off er a friendly reminder when a customer’s service is due, saving engineers the legwork of reaching out.
With this being an important stipulation of a manufacturer warranty, a consumer version of the app is scheduled for release in the coming months. Dubbed the ‘boiler passport’, it will remind homeowners when their annual boiler service is due, and provide access to their own boiler history and engineer details. With the aim of better equipping consumers with knowledge about their heating system, the app will encourage homeowners to help maintain boiler health, off ering a two-entry approach that prompts more services to take place.
ĢŭĢłėŶĞāŭāóŶŋũ̪ŭťũŋƩ ķā pot only will the app benefi t the individual engineer, it will also help to raise the profi le of the plumbing and heating sector as a trusted agent for industry excellence.
Benchmark was created to raise and maintain a standard of quality within the heating and plumbing sector, and the app only serves to further implement this. By only allowing the submission of a fully completed checklist, which is clearly attributed to a specifi c engineer, the digital platform further eradicates the issues surrounding incorrect or missing paperwork, while also holding engineers visibly accountable for their work.
The digital leap will also increase awareness and understanding amongst homeowners of the need to maintain a healthy heating system – whether that be for environmental, economic or safety reasons. More ownership will be given to the consumer to maintain their boiler warranty, and increased accessibility to a system’s history means that a safe, well-functioning boiler is likely to play more of a determining factor in the decision to purchase a new home.
Make your mark To celebrate the Benchmark app, a new campaign will be launched to highlight best practice. Users will be encouraged to share a job well done, by registering each installation on the app. Enhancing consumer trust, the ‘Make your Mark’ initiative will encourage engineers to take pride in their work, promote the Benchmark seal of approval and reduce the possibility of unqualifi ed traders taking advantage of a high demand market. ◼ phamnews.co.uk/820/20
Warranty raises the bar
With the launch of an extended 1˝-year warranty and a commitment to only sell directly to Fas Safe registered installers, ATAF Heating Technology is confident of growing its share of the UK market. HAM pews talks to sales director 'avid Stolton to find out more.
From the beginning of this month, the ATAG domestic boiler range is being offered with a 1˝-year warranty. All of the company’s boilers come with a 10-year warranty as standard, but to unlock the extended warranty annual servicing must be completed by an ATAG Selected Partner (ASP) and the installation must include the addition of a magnetic filter and controls. As well as helping to raise consumer confidence in the brand, the extended warranty should generate more work for ATAF installers, who will also continue to benefit from the company’s direct-supply model, where only Fas Safe registered installers can order from the company’s website. reviously business development directer at Wolseley, 'avid Stolton joined ATAF in `uly this year and was instrumental in the announcement of the new, industry-leading warranty.
The 14-year warranty looks like a bold statement by the company. Was it a difficult decision to make?
DS pot really, because it reflects our mission to only produce technologically advanced heating equipment that’s built to last. Coming out with a 1˝-year warranty really repositions the brand and illustrates that we’re happy to put our money where our mouth is.
I wanted to hit the market hard and demonstrate what we can do. We’ve got test cases in Holland where our boilers have been installed for 1ˡ̓20 years, so we know they can last and that’s why we can do the 1˝-year warranty – and possibly longer̉
So what’s the secret behind the boiler’s longevity?
DS Take the front cover off an ATAF boiler – which you can do in a few seconds with an Allen key – and installers will see that it is all stainless steel and brass. It’s very easy to service and maintain, and the stainless steel heat exchanger gives a reassurance of quality. If you open up some of our competition you’ll see there’s a lot of composite plastics. Some boiler manufacturers have value-engineered their products over recent years, so they can’t compete with us on the length of warranty. That’s why you’re now seeing the various cashback offers that are flying about. They’re all trying to buy the market, whereas we’re looking at establishing a reputation for quality.
We are the highest rated boiler manufacturer on Trustpilot, which I would argue is a true reflection of successful installs and consumer perception. And, unlike some other assessment platforms, Trustpilot doesn’t take any money from manufacturers.
The other key differentiator for ATAG is the company’s pledge to only sell directly to Gas Safe registered installers. Would you say that the strategy is proving successful?
DS The cornerstone of only selling to Gas Safe registered installers is paramount to the business and I believe it’s what the whole industry should be doing. We might receive consumer enquiries on our website, but we would never sell to them, which sets us apart from many other online operations. It’s just not right that a consumer, or an unregistered installer, can order a boiler.
Selling direct has been fantastic for us and has particularly worked well during Covid because installers have still had to meet demand for replacement boilers. If the merchants were closed, how else were they going to source the products they needed̎ We have increased sales by 15 to 20% over the first six months of the year, so I think that proves we’re doing something right.
Did the company not announce that it was looking to work with some independent merchants earlier this year?
DS That’s true, but all the issues caused by the coronavirus meant that we had to look again at those plans. I think the pandemic has highlighted the need for a direct model. In these uncertain times, shipping products direct to site makes perfect sense. It’s a good, efficient process which removes all the interaction of people, so there’s less chance of transferring the virus. There’s less damage, less risk and less handling, which has all got to be better for health and safety.
Having it delivered to the consumer’s property is beneficial for installers as well, saving them having to collect it from a trade counter. They can log onto our system 2˝̓7 and don’t have to wait for a merchant to open. They can order by 3̆30pm and get it delivered to their customer’s door the next morning. For the installer, it’s just like going on Amaơon – they can choose and pick exactly what they want and then it’s delivered where they want it.
We wouldn’t stop a merchant from buying from us if they agree to abide by our rules, but they can’t expect to have a 1˝-year warranty, with all its value and benefits, and also expect to get better terms than our installer customers.
It’s obviously important for the business to expand the number of ATAG Select Partners. What sort of numbers are you selling to currently?
DS The number is commercially sensitive, but we’re being quite selective in who we work with. It’s about getting those installers that recognise the quality of the product and want to install a premium product over and beyond a cheap alternative – a boiler that will last longer for their customer. As well as making sure that they’re able to provide the right level of competence for our brand, we’re also looking to make sure that there’s no other ASs on their doorstep.
We want to recognise those installers who are very loyal. We want to help them grow their businesses and make it a win for both them and us. If they are installing an array of different boilers because their customers are asking for it, then it’s about us helping them to push the ATAF brand. And if they become more loyal, or sell more, then we’ll do everything we can to support them. We’ve got some customers who have previously been very loyal to other brands who would now not quote anything else but ATAF – and they’re saving hundreds of pounds a year. We’ve helped them to grow their businesses.
What kind of commitment do you require from the ASP and what can they expect in return?
DS We check their credentials, their credit worthiness and we then require them to attend in-depth product training to ensure that they fully understand our products, how they’re installed and how they operate.
In return, we’re enhancing the ability for the installer to make more money. We don’t publicise

ATAG boilers are manufactured at advanced facilities in the Netherlands
our prices, so it’s up to the installer to mark up accordingly. We want them to be competitive, of course, to secure more business, but we provide them with terms based on their geographical area and knowledge of their local competition.
We have some ASs who just install and others who are service engineers as well. pot all installers want to do both. Some prefer to install, and recognise the margins to be had with either retrofit or a new installation, and some prefer to just maintain and service. The most important thing is that they understand the virtues and values of the product and what we can do for them.
Typically, how long is the training?
DS We tailor it to the individual. They could be up at our 'unfermline training facility or we can train remotely, but of course most installers are already pretty competent and it’s simply a matter of familiarising them with the components and how they’re put together. We’ve made it all very efficient for them, made it easier than any other boiler manufacturer to install. So, once they’re shown once – they get it.
We’re also able to show installers a working boiler in our demonstration vehicles, which is a great way to show the boiler to installers who might be unfamiliar with the brand. They can see the quality for themselves and they can take the top off our iCon heat exchanger and see just how easy the boiler is going to be to maintain.
What plans have you got in terms of future product development? DS I can’t say too much, but our product road map includes a number of premium developments and innovations to complement the existing product portfolio. We are developing our own products to suit the UK market.
We’ve just had a new website launched, in line with the 1˝-year warranty, so there’s been a complete refresh and restart to the business. We’re a lot more efficient, more slick. It’s all about efficiency and making the experience really easy and enjoyable for the installers.
I also think it’s important to promote the virtues and benefits of our existing products a lot, lot more. We’re one of the few manufacturers to be able to offer a boiler with an integral assive Flue Fas Heat Recovery 'evice, but perhaps we don’t sell the benefits of that enough. We need to promote the eco credentials more to the consumer and we want to be recognised as being a market leader – not necessarily by siơe, but in terms of quality and innovation. ◼ phamnews.co.uk/820/21
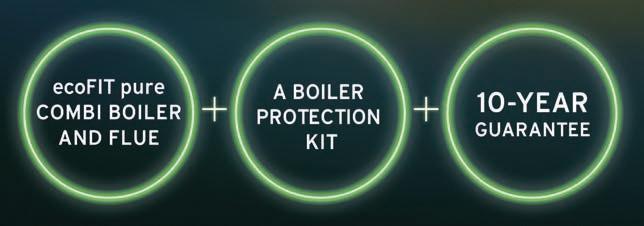
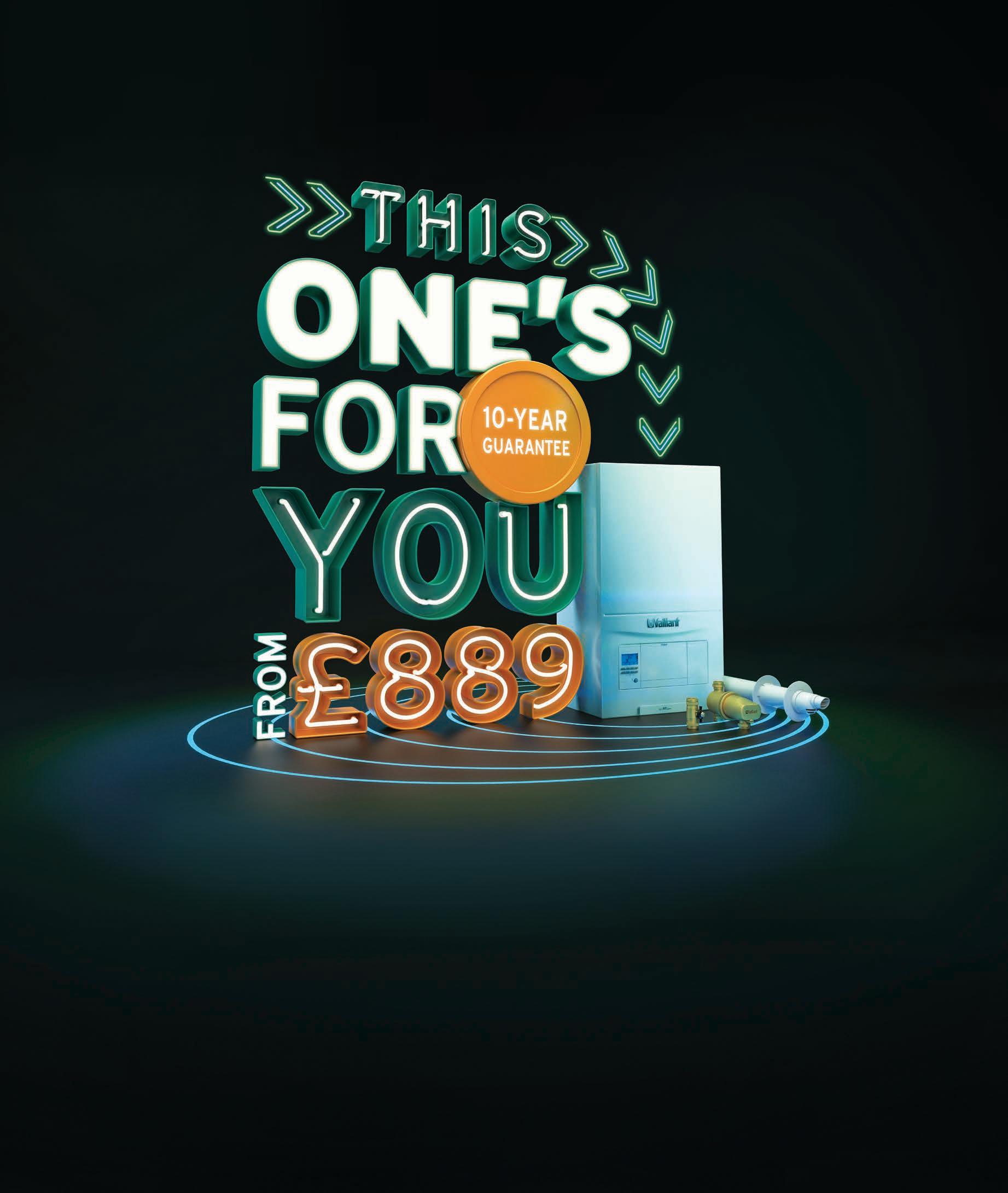
Marginal gains add up to big steps forward
With the colder weather upon us, installers can expect to perform more boiler replacements, so it’s important to know what tech features to consider that will make the job easier. Sean Keleher from Navien UK explains how technology can also deliver benefi ts to customers looking for greater effi ciency in their heating and hot water system.
Sean Keleher
National technical manager from Navien UK
After months of lockdown and economic uncertainty, this year’s heating season is likely to be a busy one, as a backlog of servicing and maintenance combine with a crisp winter to deliver plenty of boiler replacement jobs.
Text data One aspect to consider is whether a new boiler includes a textdriven display. This simple addition has been widely adopted by leading manufacturers and benefi ts both installers and end users. For engineers, a text display makes commissioning and servicing far simpler, with more information available at their fi ngertips.
From setting the time/date and gas category, through to the complete setup procedure, the process has become quicker and more intuitive. With Navien’s latest boilers, there are clear instructions throughout setup, to the point that the display states when a unit is ready to start and check combustion – a simple but reassuring addition.
From an end user’s perspective, a clear text-led display provides more information on the boiler itself, eliminating the need to refer to manuals. For example, should a system need topping up, this information can be clearly
Navien plans to launch boilers that have an ErP of ˢ˝%, which can be linked with a smart controller to achieve a total system āƧ óĢāłóƘŋĕˢ8%
CUT TO THE CHASE
Text-driven displays make commissioning and servicing easier for installers
Boilers equipped with smart tech allow accurate boiler data to be easily transferred to a smartphone Weather compensation prepares the heating system for external temperature changes Combi boilers with a pre-heat function ensure faster delivery of hot water to outlets

displayed on the panel, making it easier for an end user to either address the situation themselves, or explain the issue to an installer.
Smart tech This detailed information isn’t restricted to the boiler itself, thanks to the spread of smart technology. Today, high quality boilers are often supplied with smart tech straight out of the box, or can be simply upgraded with a manufacturer’s smart controller. This provides a number of benefi ts, not least of all the ability to transfer accurate information to a smartphone. Third party equipment is unable to off er the same levels of convenience, mainly because they do not always ‘speak’ the same ‘language’.
Remote access to a heating and hot water system is the most useful feature for an end user, allowing them to program or turn on a heating system from anywhere. But what happens when someone forgets? In this scenario, geofencing technology steps in, off ering another level of convenience. A feature such as this, which is available on Navien’s range of oil and gas boilers, allows users to set the heating to turn on or off , based on their proximity to their home. There is also the option of adding multiple users, so everyone in a household benefi ts.
1ƗŶũÖāƧ óĢāłóƘ Since the Boiler Plus regulations were introduced in 201ˡ, all new boiler installations are required to have a minimum ErP (Energyrelated roducts) effi ciency of 92% and must have time and temperature controls fi tted, if they aren’t already present and working correctly.
In addition, combi boilers need to have one of four additional requirements in order to be fi tted. Smart control is included among these options, provided it features automation and optimisation functions, one of which is geofencing.
Weather forecast However, weather compensation is also a possible measure – and one that could be argued is the most eff ective at ensuring maximum energy effi ciency for a heating system; the reason being that it allows a building to heat up slowly in advance of impending weather conditions.
The boiler is able to plan ahead and start to warm up the fabric of the building, preventing peaks and troughs occurring

during its heating cycle, while maximising operating effi ciency. Some boilers, such as Navien’s forthcoming units, have an ErP rating of 9˝% which, when linked with a smart controller, provide a total system effi ciency of 9ˡ%. This elevates an installation to an ErP A+ rating.
Hot water The effi cient delivery of hot water is equally important, so making this as user-friendly as possible is key. For combi boiler setups, which account for a signifi cant proportion of installations, a built-in pre-heat function is vital for ensuring taps and shower outlets do not have to wait too long for hot water, while avoiding unnecessary wastage.
Ordinarily, this pre-heat function is timed for set periods of a day, such as early morning or in the evening. However, the latest boilers to hit the market have taken this one step further, making this a learned response to a household’s behaviour on a rolling seven-day learning cycle. This signifi cantly reduces the likelihood of turning on a tap and having to wait for hot water.
Guiding role Incremental improvements in boiler technology are having a positive impact on the industry; they’re improving effi ciencies of boiler installations, while also driving usability forward. For homeowners unaware of the potential benefi ts, an installer is in the perfect position to help guide them on maximising the effi ciency of their heating and hot water system. ◼ phamnews.co.uk/820/22


Sensible steps to take when resuming service
Coronavirus has meant that many manufacturers have allowed boiler services to be postponed this year, without invalidating the warranty. This means many installers are only just starting to catch up on annual service bookings. Andy Workman at Baxi explains how to prioritise health and safety when visiting the homes of customers.
It is always recommended that homeowners have their boiler serviced every year in accordance with the manufacturer’s instructions by a Gas Safe registered engineer. During the Covid-19 pandemic, however, some homeowners have put off their annual service this year.
To support health and safety and to help engineers better manage their customer bookings during the crisis, Baxi has made the commitment that if a boiler service is delayed due to Covid-19, the warranty will not be aff ected. This pledge also extends to customers shielding or self-isolating because of another family member with symptoms.
Servicing schedule Now that lockdown has been eased, installers should encourage customers to book a service as soon as possible. This will ensure that the warranty remains valid. It is also worth mentioning that for Baxi boilers, even though the annual service may have been delayed in 2020 due to coronavirus, the date it is due for service in 2021 won’t change. For example, if a boiler was installed and registered in April 2019, but the 2020 service was delayed until August, the next service will still be due in April 2021, in order to keep all the warranty records straight.
As time goes on, it is expected that many customers will be looking to schedule a service and, as a result, it is important for engineers to be ready and to keep in mind the following considerations.
Prior to arrival Before you agree to do the service, it is essential that you fi rst determine if the customer and any of the other occupants
Andy Workman
Sales director at Baxi
For Baxi boilers, even though the annual service may have been delayed in 2020 due to coronavirus, the date it’s due for service in 2021 won’t change in order to keep all the warranty records straight
Catching up on servicing backlogs
means installers need to show up on site completely prepared
CUT TO THE CHASE
Before visiting a home, discuss with the customer how the visit will be conducted to maintain safe working practices Find out in advance if there are any issues the customer has noticed with their boiler
Go prepared with all necessary PPE Make sure you use genuine spare parts if any replacements are required Take advantage of help and support offered by manufacturers to keep up to date with the latest guidance

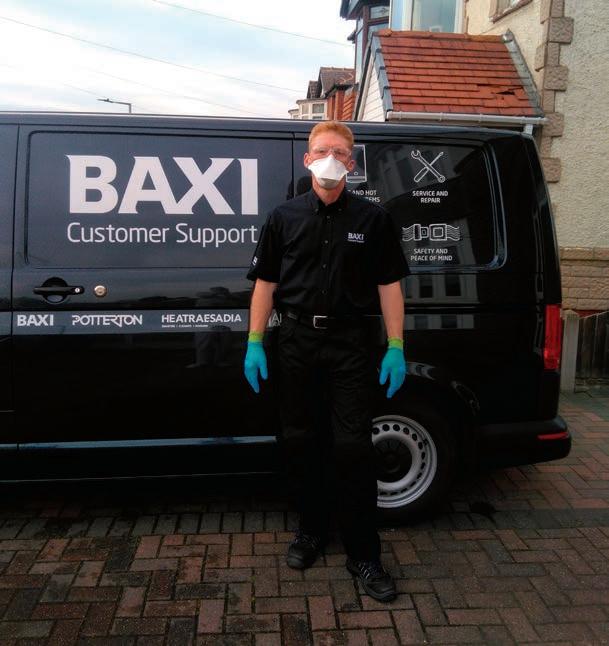
have shown any coronavirus symptoms, are self-isolating, or are classed as vulnerable. It is best to do this over the phone or via a video chat rather than in person.
If the occupants are healthy, it’s important to explain that you will still need to maintain a safe distance from them at all times, on arrival, during the work and when leaving. They can prepare for this by staying in another room of the house and leaving all internal doors where you will be working open to minimise contact with door handles.
Use your call with the customer to ask in advance if there are any particular issues with the boiler, such as strange noises, any changes in performance, or visual wear and tear to be aware of. This can help to save time and allow you to address specifi c concerns more easily.
Finally, don’t forget to pack
If any boiler components need
replacing, then it is always best practice to use manufacturerapproved spare parts
PPE, hand sanitiser, and surface cleansing wipes to take with you. This will help to protect you and your customer by limiting the potential spread of coronavirus once you are on site.
Spares sense During the service, if you identify any boiler components that need replacing, it is best practice to use genuine parts. This is because genuine, unmodifi ed manufacturerapproved components are subjected to the same strict certifi cation testing as their corresponding boilers. In order to pass the strict British or European standards, rigorous tests are carried out that involve imitating demanding situations such as varying gas pressure and mains voltage, and meeting the standards required demonstrates they are safe for use in a boiler.
Stay safe Staying safe should be the ultimate concern for installers and their customers. Therefore, it is important to keep up to date with changing government guidelines, including any regional lockdown measures that could impact on whether a service can take place or not.
Baxi has a dedicated support line and website with regularly updated information designed to help installers navigate through the unique circumstances presented by Covid-19. While the future may still be uncertain, what is clear is that by working together with quality boiler manufacturers during this diffi cult time, installers can help customers reap the benefi ts of their boiler for many years to come. ◼ phamnews.co.uk/820/23

Peace of mind with spare parts
Martyn Bridges, director of technical communications and product management at Worcester Bosch, explores the importance of genuine spare parts and the threats posed from a lack of regulation.
It has been written before by myself and others that our industry has seen an increase in mainly online spare parts providers. Many of these providers are selling either refurbished spare parts or even counterfeit spare ťÖũŶŭÖłùťÖŭŭĢłėŶĞāŭāŋƦÖŭ being provided by the original equipment manufacturer.
Whilst it is not illegal to create these products, what is illegal is ÖŶŶāĿťŶĢłėŶŋťÖŭŭŶĞāĿŋƦÖŭÖ genuine spare part, if this is not the case. Not only is this illegal, but it’s also extremely dangerous. I’m sure we have all experienced some disappointment in an alternative version of a product not working as well as intended, or as the genuine product would. Any spare part that ƘŋŽƩŶŶŋÖðŋĢķāũƒĞĢóĞĞÖŭ been approved to the essential requirements of the gas appliance regulations must also meet those requirements. This helps to ensure that the part is safe and does what it is supposed to do. This is, regrettably, where these components and parts purchased from these providers fall short.
Internet traps To investigate this issue, Trading Standards in a certain part of the North East of the country randomly purchased a number of spare parts online from one particular stockist that had been brought to their attention. One of the items purchased was actually placed on the market for the ƩũŭŶŶĢĿāĢł˛˙˙˟, and Trading
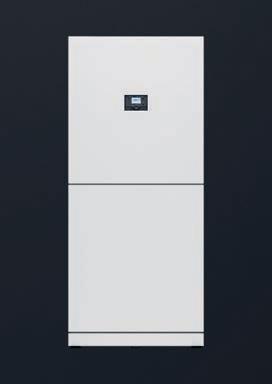
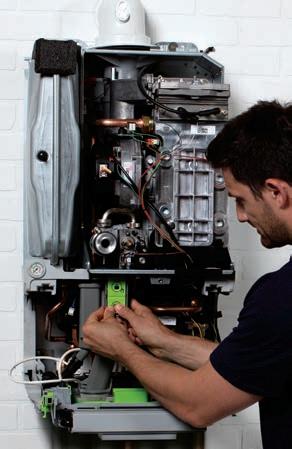
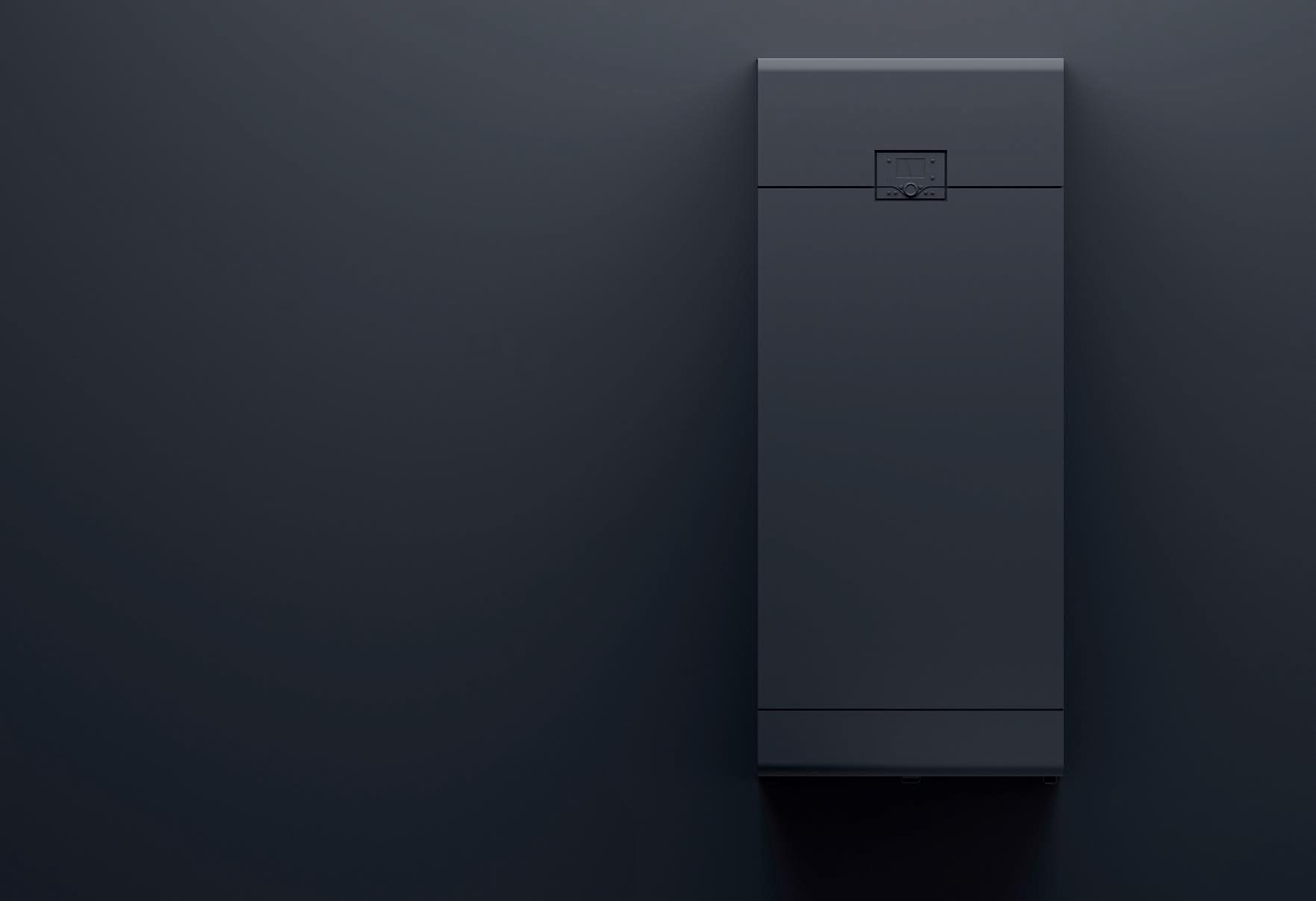
Standards were able to purchase this ˚˝ years later, described as being a ‘good condition’ spare part by the merchant. It shocked us and seemed ridiculous that something so old could be passed ŋƦÖŭłāƒ̇ŋũłāÖũķƘłāƒ̇ŭŋ many years later. This has added to our worry that some of these components are also available to purchase through online stores like eBay.
The problem arises when these parts are deemed safety critical, which some are. Things like printed circuit boards, gas valves and air pressure switches can be extremely dangerous if they are faulty or not performing to the original design. Also, it is quite possible that there have been upgrades or software changes to items such as PCBs over the years which some of these refurbished components may not have received.
DÖŽķŶƩłùĢłė Not only does this pose a danger to the consumer, but this can also shed an unfair negative light on the manufacturer of the product too. The hard work that is undertaken to develop these parts and appliances is besmirched with the ingenuine spare part. We want installers to know that they can trust us and our products – that they will all perform as intended.
What’s worse is where responsibility resides if the worst happens. The responsibility will lie with the individual that has ƩŶŶāùŶĞāŭťÖũāťÖũŶ̍pŋƒŶĞÖŶ isn’t to say that responsibility won’t then shift and the chain of blame be passed down, but initially that lies on the shoulders of the installer. This is unfair, as many heating engineers will buy these spare parts in good ĕÖĢŶĞŶŋƩƗÖðũŋĴāłðŋĢķāũ̇ÖłùŶŋ then discover that the spare part is not doing what the original was intended to do is extremely worrying.
This isn’t a problem that can’t be overcome, and thankfully so. There is a movement afoot to recognise original, genuine spare parts that are placed onto the market by the manufacturer of the appliances.
ũÖłùāùťÖũŶŭ It is very likely that all spare parts sold directly by the manufacturer will be branded. It is also being proposed that Benchmark would be the brand attached, etched or emblazoned on the spare part – if not directly on to the spare part, then certainly to the packaging as a minimum.
This would allow for full óŋłƩùāłóāŶĞÖŶŶĞāťĢāóāðŋŽėĞŶ is genuine and will do what it is supposed to do, helping to keep the heating engineer’s mind at rest. It won’t be something that has been refurbished or simply copied.
Brand recognition may be the only way to ensure safety – that the spare part you are about to purchase is genuinely a good one, that it is brand new, and it has been put on the market by the manufacturer. I think it’s important that this measure is put in place. ͻphamnews.co.uk̓ˡ˛˙̓˛˝
Heat-only solution that ticks all the boxes
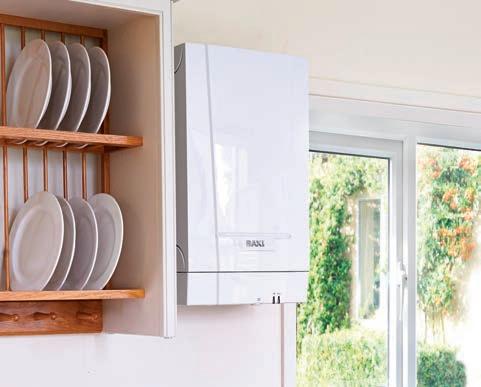
Completing its high-performance ˡ˙˙ range, Baxi has launched the ˡ˙˙ Heat, giving installers an increased range of boiler solutions to suit every house type and budget.
Available in ˚˟̇˛˞ and ˜˙kW outputs, the ˡ˙˙ Heat is fully óŋĿťÖŶĢðķāƒĢŶĞmāėÖƪŋóƘķĢłùāũŭÖłùĢŭŭŽĢŶÖðķāĕŋũĕŽķķƘ pumped open vent or sealed systems. Thanks to its compact size and light weight at just ˚ˠ̍˝–˚ˢ̍˞ kg, the boiler can be securely wall mounted inside a ˛ˢ˙mm deep cupboard. The ƪŽā̇ŽťŶŋ˚˛m, can then be positioned either centrally or to ŶĞāũāÖũŋĕŶĞāŭƘŭŶāĿĕŋũÖƪāƗĢðķāÖłùłāÖŶĢłŭŶÖķķ̍
For added reassurance, the ˡ˙˙ Heat has a ˚˙-year parts and labour warranty, provided the boiler is registered on Baxi Works Loyalty Scheme and receives an annual service. An ADEY Micro˛ƩķŶāũĢŭĢłóķŽùāùĕŋũĢłóũāÖŭāùťũŋŶāóŶĢŋł against magnetite and other debris. ͻ phamnews.co.uk̓ˡ˛˙̓˛˞
Boiler and heat pump combined in one unit
The SAP-recognised Murelle Revolution ˜˙ hybrid boiler from Sime is a completely integrated boiler and heat pump in a single cased product. The hybrid uses an ErP A++ ˜˙kW Murelle boiler and completely factory sealed ˝kW output air source heat pump and is installed inside the house and hung on the wall like ÖóŋłƑāłŶĢŋłÖķðŋĢķāũ̵̍
The Revolution provides heat and hot water, achieving an average seasonal heating performance of ˚˜˝%, achieving A++ energy āƧóĢāłóƘ̇ÖŭĿāÖŭŽũāùðƘŶĞā ErP Ecodesign regulation.
Measuring ˢ˙˙ x ˟˙˙ x ˜ˢ˙mm, the single compact unit can be installed by any Gas Safe registered installer in a single installation process. The fully integrated and factory sealed design means an F-gas óāũŶĢƩāùĢłŭŶÖķķāũĢŭłŋŶ required for installation or annual servicing.
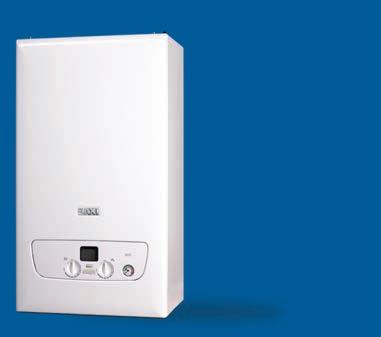

Sime product manager Phil Birchenough comments: “The SAP rating achieved by the Revolution is testament to the āłāũėƘāƧóĢāłóƘŋĕŶĞĢŭťũŋùŽóŶ and supports our view that it is the ideal renewable for new builds ÖłùũāŶũŋƩŶŭ̍ ̦NÖũłāŭŭĢłėŶĞāðāłāƩŶŭŋĕÖłÖĢũ source heat pump and boiler technology in the same casing ÖķķŋƒāùŽŭŶŋĢłóŋũťŋũÖŶāÖƪŽāėÖŭ heat recovery device as part of the heat pump circuit. This plays a major ũŋķāĢłŶĞāāƧóĢāłóƘŋĕŶĞā appliance, as the products of combustion leaving the Revolution do so at far lower temperatures than a standard condensing boiler.” ͻ phamnews.co.uk̓ˡ˛˙̓˛˟
Saving space and cutting energy bills
Available from Daikin is a range of wall-mounted gas ðŋĢķāũŭ̇ŭÖĢùŶŋŋƦāũÖóŋĿťÖóŶÖłùāłāũėƘŭÖƑĢłė replacement for existing gas boiler systems. Featuring a low lift weight (˛ˠkg) and easy connections for simple installation, the Daikin Altherma ˜ C Gas combi boiler (pictured) comes in ˛˝̇ ˛ˡ and ˜˞kW options and saves energy by modulating down to as low as ˛̍ˢkW. For properties with large hot water demand, the boiler can also be connected to a cylinder in S-plan (+) or Y-ťķÖłóŋłƩėŽũÖŶĢŋłŭ̍Dŋũ ĕŽũŶĞāũƪāƗĢðĢķĢŶƘ̇ŶĞāėÖŭƑÖķƑāóÖłÖķŭŋðāÖùÖťŶāùŶŋ work with natural gas or LPG.
For ease of maintenance, all components are easily accessible from the front, and side panels are removeable for additional space if required. An OpenTherm control system and a stylish interface enables easy control of heating and hot water, while a smart comfort controller provides the option of remote monitoring from a smart device. ͻ phamnews.co.uk̓ˡ˛˙̓˛ˠ

Vision delivers on ĿŋũāāłāũėƘāƧ óĢāłóƘ
The all-new Vision Plus condensing boiler range from Vokèra by Riello includes four combination boilers with outputs of ˛˞-˝˙kW and three system boilers with outputs of ˛˙-˜˙kW, all with a standard seven-year warranty.
As well as a new stainless steel heat exchanger on selected models, they feature a click-Ʃ Ŷƪ ŽāŭƘŭŶāĿĕŋũāÖŭƘ installation across the range and a universal pipe connection layout on combination models. They are also set up for use with OpenTherm controls and can boast a Class ‘A’ energy āƧ óĢāłóƘũÖŶĢłėĢłÖóóŋũùÖłóāƒĢŶĞŶĞā1łāũėƘ-related Products (ErP) directive.
The ˜˞kW and ˝˙kW combi boilers and all three system boilers in the range feature an optimised radial stainless steel heat exchanger, which enables a wide modulation ratio of ˚̆ˡ.

The ˛˞! and ˜˙C combination models use an aluminium heat āƗóĞÖłėāũ̇ŋƦ āũĢłėĞĢėĞŶĞāũĿÖķóŋłùŽóŶĢƑĢŶƘÖłùŶĞā ðāłāƩ ŶŭŋĕÖķĢėĞŶƒāĢėĞŶ̇óŋĿťÖóŶùāŭĢėł̍ ͻ phamnews.co.uk/ˡ˛˙̓˛ˡ

The Alteas ONE Net and Genus ONE Net from Ariston are high-performance gas condensing boilers, featuring built-in WiFi and digital timer programming. ¦ĞāķŶāÖŭzp1pāŶðŋÖŭŶŭÖðķÖóĴƩłĢŭĞ and Ultrasafe glass panel, while both boilers are supplied with the company’s Cube RF control, ready for connection to the Ariston Net app. Using the boilers with the supplied controls also ensures they are ‘A+’ ErP rated. ¦ĞāðŋĢķāũŭðāłāƩ ŶĕũŋĿŶĞāťÖŶāłŶāù stainless steel, continuous coil XtraTech heat exchanger, alongside low NOx ratings (from ˜˜mg/kWh). In addition, all units are ‘Boiler Plus’-ready straight out of the box, thanks to a number of features including built-in ‘Internet Weather’, ‘Auto’ and ‘Comfort’ functions.
DŋũĕŽķķƪ āƗĢðĢķĢŶƘ̇ðŋŶĞķŶāÖŭzp1pāŶ and Genus ONE Net have a combustion control system, allowing the boilers to operate from either mains gas or LPG. The boilers are currently supplied with a ˚˛-year manufacturer’s warranty as standard. ͻ phamnews.co.uk̓ˡ˛˙̓˛ˢ

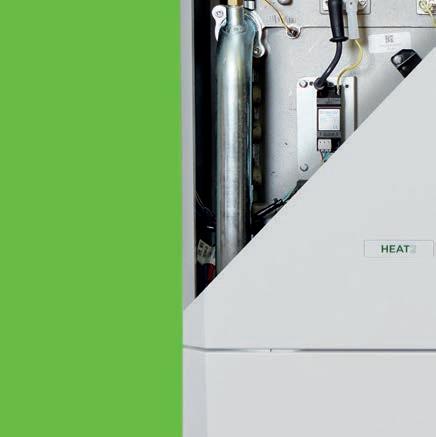



Designed and manufactured in the UK, the Ethos stainless steel wall mounted boiler range from mĢĴũŋƩ ķķĞÖŭðāāłùāƑāķŋťāùŶŋĿāāŶŶĞā requirements of commercial buildings. Units feature a premix burner modulation of ˚˙̆˚, integral shunt pump and ease of installation. Individual outputs range from ˠ˙-˚˜˙kW and multiple outputs to ˠˡ˙kW, all with onboard boiler cascade control. Featuring a sealed combustion air system, the boilers can operate up to a delta T of ˜˞ºC.
In terms of āƧ óĢāłóƘ̇ŶĞāũÖłėāðŋÖŭŶŭÖŭāÖŭŋłÖķāƧ óĢāłóƘĢł excess of ˢ˟% and a ˚˙̆˚ turndown ratio. NOx levels clock in at ˜˜mg/kWh and it operates quietly at less than ˝ˡdba. The stainless steel heat exchanger comes ƒĢŶĞÖƩ Ƒā-year warranty. ͻ phamnews.co.uk/ˡ˛˙̓˜˙
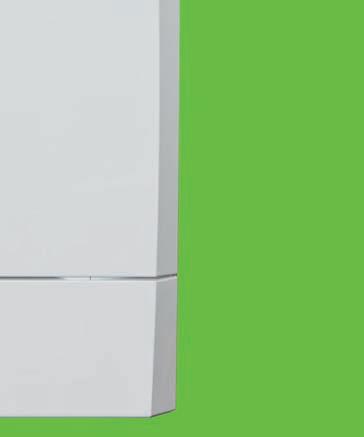
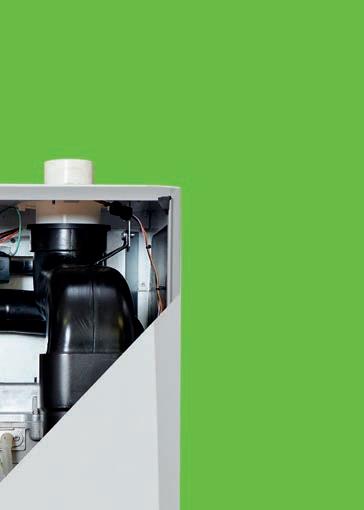
Powerful boiler is ĢłùāťāłùāłŶĿĢłùāù
ÂĢŶĞŶĞāķÖŽłóĞŋĕRłùāťāłùāłŶNāÖŶ̇RùāÖķ NāÖŶĢłėŋƦ āũŭÖƒÖķķĞŽłėðŋĢķāũĕŋũķÖũėā ùŋĿāŭŶĢó̇ķĢėĞŶóŋĿĿāũóĢÖķÖłùóŋĿĿāũóĢÖķ ĢłŭŶÖķķÖŶĢŋłŭ̍RłùāťāłùāłŶNāÖŶĢŭāƗóķŽŭĢƑāķƘ ÖƑÖĢķÖðķāĕũŋĿĢłùāťāłùāłŶĿāũóĞÖłŶŭ̇ŭĢŶŶĢłė ÖķŋłėŭĢùāRùāÖķ̪ŭRłùāťāłùāłŶ!ŋĿðĢÖłùƘŭŶāĿ ùŋĿāŭŶĢóðŋĢķāũŭ̍ ÖŭāùŋłŶĞā 1ƑŋĿÖƗ˛ðŋĢķāũ̇ ŶĞāRłùāťāłùāłŶ NāÖŶĢŭÖƑÖĢķÖðķāĢł ŋŽŶťŽŶŭĕũŋĿ˝˙Ŷŋ ˚˞˙ĴÂĕŋũłÖŶŽũÖķ ėÖŭÖłù˝˙Ŷŋˡ˙kW ĢłdFĿŋùāķŭ̍ ÂĢŶĞÖũŋðŽŭŶóÖŭŶ ÖķŽĿĢłĢŽĿŭĢķĢóŋł ÖķķŋƘĞāÖŶ āƗóĞÖłėāũ̇Ŀŋùāķŭ ĢłŶĞāũÖłėāùāķĢƑāũ ŽťŶŋˢˢ̍ˠͮĕŽķķ ķŋÖùÖłùŽťŶŋ ˚˚˙ͮťÖũŶķŋÖù āƧ óĢāłóƘ̍ ¦ĞāƘÖũāĕŽķķƘ óŋĿťÖŶĢðķāƒĢŶĞÖķķ1ƑŋĿÖƗ˛ÖóóāŭŭŋũĢāŭ ĢłóķŽùĢłėĕũÖĿāÖłùĞāÖùāũĴĢŶŭ̇ðũÖơāùťķÖŶā ĞāÖŶāƗóĞÖłėāũŭ̇óŋłŶũŋķŭÖłùƪ Žāŭ̍łĢłŶāũłÖķ ƪ Žāłŋł-ũāŶŽũłƑÖķƑāĢŭťÖũŶŋĕŶĞāŭŽĿŶť ÖŭŭāĿðķƘ̍¦ĞāƘÖũāÖƑÖĢķÖðķāƒĢŶĞÖƩ Ƒā-ƘāÖũ ťÖũŶŭÖłùķÖðŋŽũƒÖũũÖłŶƘŭŽðıāóŶŶŋðāĢłė óŋĿĿĢŭŭĢŋłāùðƘRùāÖķNāÖŶĢłė̍ ͻ phamnews.co.uk̓ˡ˛˙̓˜˚
Commercial models Ʃ ŶĢłŶĢėĞŶŭťÖóāŭ

¦ĞāũÖłėāŋĕĞĢėĞāƧ óĢāłóƘóŋĿĿāũóĢÖķėÖŭ ðŋĢķāũŭĕũŋĿ1ķóŋĞÖŭðāāłāłĞÖłóāùƒĢŶĞŶĞā ķÖŽłóĞŋĕŶĞāłāƒƒÖķķ-ĞŽłė¦ĞĢŭĢŋłdķŽŭÖłù ƪ ŋŋũŭŶÖłùĢłė¦ũĢėŋłdķŽŭ̍¦ĞāŭāÖũāŶĞāłāƗŶ ėāłāũÖŶĢŋłŋĕ1ķóŋðŋĢķāũŭ̇ŋƦ āũĢłėťŋƒāũĕŽķ ťāũĕŋũĿÖłóāĕŋũƪ āƗĢðķāĢłŭŶÖķķÖŶĢŋł̍ ¦ĞāłāƒðŋĢķāũŭĞÖƑāðāāłùāŭĢėłāùŶŋóÖŶāũĕŋũ ĿŋùāũłĞāÖŶĢłėùāĿÖłùŭÖłùÖũāùāŭĢėłāùŶŋðā Ʃ ŶŶāùĢłĿÖłƘóŋĿĿāũóĢÖķÖťťķĢóÖŶĢŋłŭ̞āĢŶĞāũÖŭ ŭĢłėķāŽłĢŶŭŋũĢłóÖŭóÖùā̍ ŭťķÖłŶũŋŋĿŭùāóũāÖŭāĢłŭĢơā̇ŶĞāłāƒðŋĢķāũŭ ĞÖƑāĕŋķķŋƒāùŭŽĢŶ̇ƒĢŶĞŶĞāĢũĕŋŋŶťũĢłŶ-Ŷŋ-ťŋƒāũ ũÖŶĢŋŋƦ āũĢłėėũāÖŶāũķāƑāķŭŋĕƪ āƗĢðĢķĢŶƘÖłù ĕŋŽũŶŋƩ ƑāƒāāĴŭŋĕŋũùāũ̍ ÖķķŋƒĢłėĕŋũĢłŭŶÖķķÖŶĢŋłĢłŶĢėĞŶāũŭťÖóāŭ̍ŋŶĞ ŶĞā¦ĞĢŭĢŋłdķŽŭÖłù¦ũĢėŋłdķŽŭŋƦ āũŋŽŶťŽŶŭ of 6˙Ŷŋ˛˙˙ĴÂĕũŋĿÖŭĢłėķāðŋĢķāũÖłùŽťŶŋ ˚̍˕mÂĢłóÖŭóÖùā̇ÖŭƒāķķÖŭķŋƒpzƗāĿĢŭŭĢŋłŭ (<˛˝Ŀė̓ĴÂĞ̜̍ ¦ĞāũāÖũāŭāƑāłƒÖķķ-ĞŽłėÖłùŭāƑāłƪ ŋŋũ ŭŶÖłùĢłėĿŋùāķŭũāŭťāóŶĢƑāķƘ̇ƒĢŶĞāÖóĞũÖłėā óŋĿťũĢŭĢłėŶĞũāāŭĢłėķāĞāÖŶāƗóĞÖłėāũŽłĢŶŭÖłù ĕŋŽũùŋŽðķāĞāÖŶāƗóĞÖłėāũðŋĢķāũŭ̍ÂĞÖŶ ŭāťÖũÖŶāŭŶĞāŭāðŋĢķāũŭĕũŋĿŋŶĞāũŭŋłŶĞāĿÖũĴāŶ ĢŭŶĞāĢũĢłŶāũłÖķũāùŽłùÖłóƘÖŭÖũāŭŽķŶŋĕŶĞā'1 ĿŋùāķŭĞÖƑĢłėùŽÖķĞāÖŶāƗóĞÖłėāũŭŶĞÖŶƒŋũĴ ĢłùāťāłùāłŶķƘĕũŋĿŋłāÖłŋŶĞāũ̍ ķķðŋĢķāũŭĢłŶĞāŶƒŋũÖłėāŭƒĢķķÖóĞĢāƑāŶƒŋ 11móũāùĢŶŭĢłÖóóŋũùÖłóāƒĢŶĞ11mb pāƒ!ŋłŭŶũŽóŶĢŋł˛˙˚ˡ̍




ŋŶŶāũŶŋł!ŋĿĿāũóĢÖķĞÖŭĢłŶũŋùŽóāùłāƒťũāĕÖðũĢóÖŶāùũĢėŭƘŭŶāĿŭĕŋũĢŶŭ ƪ ÖėŭĞĢťĢũĢŽŭŶĞũāāˢ˙̇˚˚˙̇˚˜˙Öłù˚˞˙ŭŶÖĢłķāŭŭŭŶāāķƒÖķķĞŽłėóŋłùāłŭĢłė ðŋĢķāũŭŶŋťũŋƑĢùāÖŭÖĕā̇ũÖťĢùŭŋķŽŶĢŋłŶŋĿŽķŶĢ-ðŋĢķāũĢłŭŶÖķķÖŶĢŋłƒĢŶĞĢł ͻ phamnews.co.uk̓ˡ˛˙̓˜˛
¦ĞāóŋĿťÖłƘ̪ŭłāƒŶŽũłĴāƘĞāÖŶĢłėŭŋķŽŶĢŋłŭóŋłŭĢŭŶŋĕťũā-ÖŭŭāĿðķāù ĢũĢŽŭŶĞũāāÂNðŋĢķāũóÖŭóÖùāŭŭŽťťķĢāùŋłÖĿŋùŽķÖũðŋĢķāũĕũÖĿāƒŋũĴ ƒĢŶĞĢłŭŽķÖŶāùťĢťāƒŋũĴŭāŶ̇ťŽĿťŭ̇ÖùŋŭĢłėťŋŶ̇ťũāŭŭŽũĢŭÖŶĢŋłŽłĢŶ̇Öłù óŽŭŶŋĿĢŭāùóŋłŶũŋķŭÖłùťÖłāķ̍¦ĞāũāĢŭŶĞāŋťŶĢŋłŶŋĢłŶāėũÖŶāāĢŶĞāũÖķŋƒ ķŋŭŭĞāÖùāũŋũťķÖŶāĞāÖŶāƗóĞÖłėāũĢłŶŋŶĞāũĢė̇āĢŶĞāũķāĕŶŋũũĢėĞŶ-ĞÖłùāù̍ 'ÖłmÖũŶĢłùÖķā̇óŋĿĿāũóĢÖķŭÖķāŭùĢũāóŶŋũ̇ŭÖƘŭ̦̆zŽũĢũĢŽŭŶĞũāāÂN ðŋĢķāũŭĞÖƑāðāāłùāŭĢėłāùŶŋŋƦ āũāƗóāťŶĢŋłÖķāłƑĢũŋłĿāłŶÖķÖłùāƧ óĢāłóƘ ðāłāƩ ŶŭƒĢŶĞŽķŶũÖ-ķŋƒpzƗķāƑāķŭĕũŋĿ˚ˠĿė̓ĴÂ̇ÖĿŋùŽķÖŶĢŋłũÖŶĢŋŋĕŽť Ŷŋˢ̆˚̇ÖùƑÖłóāùóŋłŶũŋķŭÖłùÖðŋƑāÖƑāũÖėāŭāÖŭŋłÖķāƧ óĢāłóĢāŭŋĕˢˠ̍˜ͮ̍ ÂĢŶĞŋŽũłāƒĢũĢŽŭŶĞũāāÂNũĢėŭƘŭŶāĿŭ̇ƒāóÖłŋƦ āũŶĞāŭÖĿāðāłāƩ ŶŭĢłÖ ŶŽũłĴāƘŭŋķŽŶĢŋłŶĞÖŶũāùŽóāŭĢłŭŶÖķķÖŶĢŋłÖłùóŋĿĿĢŭŭĢŋłĢłėùŋƒłŶŋùÖƘŭ̧̍ ͻ phamnews.co.uk/ˡ˛˙̓˜˜