DECEMBER 2021
« FOLLOWING HURRICANE IDA
« SUCCESS IN CYPRUS
« S.A.R. LATIN AMERICA
« TECH TOOLS & SAFETY SUPPORT
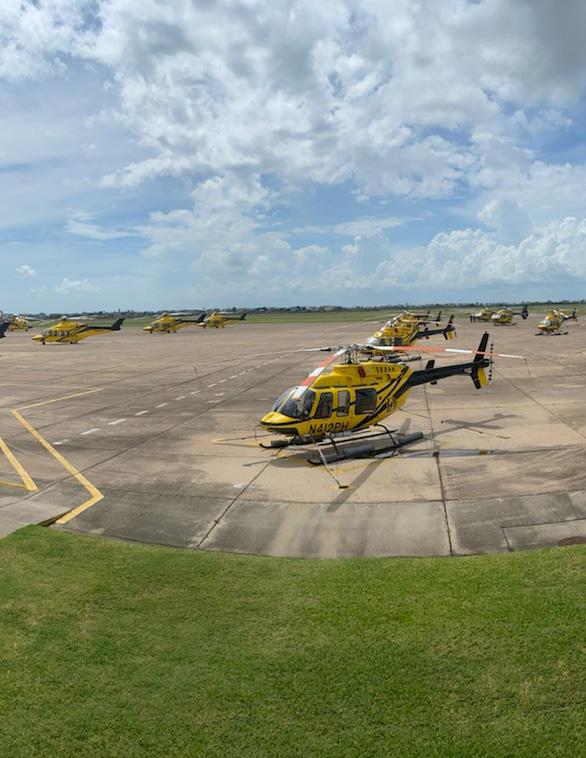
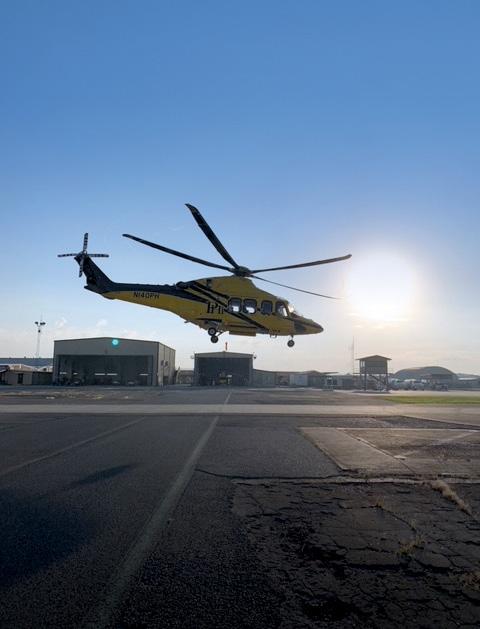

« FOLLOWING HURRICANE IDA
« SUCCESS IN CYPRUS
« S.A.R. LATIN AMERICA
« TECH TOOLS & SAFETY SUPPORT
As we move toward the end of quarter four of 2021, my first thought is to thank all employees for the resilience you’ve shown this year. Despite many challenges, some long-term and some unexpected, our business remains in a strong position. We continue to maintain positive relationships with our customers, we have grown and renewed customer agreements and we have won new customers. Hurricane Ida, a devastating event for our US teams, has shown the remarkable strength of our people and your willingness to work together to achieve the safest outcome for us all. Turn to page 4 for a summary of the planning, preparation and teamwork in the lead up to the storm.
A common thread running through this issue is our people. We often talk about the success of our business, but it is the teams and individuals behind this success that is so important. I am incredibly proud of the work of those who are featured in this issue and our whole PHI Aviation team. This Homebase shares a selection of great stories about our people, and I know there are many, many more out there.
I am especially excited for our team in Cyprus, who is soon beginning a contract with ExxonMobil. Flick to page 12 to learn more about the region, meet the team and gain insight into the leadup to the new contract starting.
Turn to page 22 to learn how our 145 Repair Station team has in the past 12 months successfully returned 14 aircraft to service in support of our customer contracts and operations.
As always, we are committed to improving the safety of our people and our customers—hear from Patrick Bosman on our Global Standards System on page 20, and on page 28 find out more about how teams across PHI International will now have access to a new digital safety support system to help with fatigue risk management—regardless of whether they are in the hangar or in the office.
Our Spotlight Interview this quarter is with PHI International Chief Pilot, Mark Cook, who shares some amazing stories and insights from his career and the journey he has taken with PHI.
We then move to the next generation of aviation talent that PHI is looking to nurture and inspire, with an interview with one of our latest interns, Alisa Izumi. She spoke to HomeBase about her time with the Safety and Quality team.
Finally, some acknowledgements for long-service employees at PHI Aviation on page 30. Well done to you all.
Thank you to everyone who contributed to this issue. I hope you enjoy it. This magazine is one way that we can all stay connected at PHI.
Sincerely,
THANKS TO OUR DAILY VOLUNTEERS, WE WERE ABLE TO DISTRIBUTE ESSENTIAL SUPPLIES AND FUEL FOR OUR IMPACTED TEAM MEMBERS.
It’s been a few months since Hurricane Ida made landfall as a major and historical storm in southeastern Louisiana. Ida’s impact on the Gulf Coast will be felt for some time. Lives and livelihoods were disrupted, and our oil and gas community took a particularly strong hit. But above all, we’re grateful that our employees and their families are safe.
We’ve made tremendous and encouraging progress over the last couple months, developing alternate base operations, initiating ongoing recovery efforts to support our storm-affected colleagues and successfully transitioning normal operations back to our Houma facilities. Our rapid response to help our people and our customers would not have been possible without our effective disaster plans, well-rehearsed drills and the incredible support and outstanding work of our teams.
Our US Gulf Coast operations are no stranger to hurricanes. In fact, built into our Emergency Response Guide (ERG) is a detailed plan to get our people, customers and assets out of the path of danger. Our hurricane evacuation plan consists of five phases based on the severity of the threat of a potential storm: 0 – operations normal; I – alert; II – pre-evacuation; III –evacuation; and IV – remobilization.
During the Atlantic hurricane season, which lasts from June through November, our teams keep a close watch for potential hurricanes or tropical disturbances that could threaten our operations. Each season brings a level of uncertainty as we try to predict the number of active storms, their paths and the severity of each developing disturbance. Therefore, planning remains a year-round effort for our Americas teams, especially for our Gulf of Mexico operations. Each year, we review and, if necessary, revise our plans to incorporate lessons learned from previous storms and any new base-specific information or safety precautions.
Our teams begin their annual preparations well before June so that by the start of hurricane season, we have identified potential evacuation locations, secured sufficient transportation for our teams and equipment, planned long-term scheduled maintenance and much more. At the start of the season, teams at each base facility spend time testing backup generators, taking stock of emergency supplies and securing loose materials and equipment in preparation for the season ahead.
Once a system begins to develop and forecasts begin to take shape, we leverage our custom weather monitoring subscription and work closely with expert meteorologists to get real-time predictions on the development, path and intensity of the storm system.
Using predictive modeling and forecasting data from our partners and the National Hurricane Center, we issue regular advisories to our teams and customers notifying them of potential threats to our Gulf of Mexico operations and, if needed, determining when to issue evacuation orders. Our Program Directors and leaders stay in close contact with customers to communicate our plans and support their own offshore evacuation needs.
Ida began as Tropical Depression Nine on August 26, 2021, while south of the Cayman Islands. Just over six hours later, it was upgraded to Tropical Storm Ida where it continued to rapidly intensify from a Category 1 (sustained wind speeds of 74-95 mph/119-153 km/h) to a Category 4 (sustained wind speeds of 130-156 mph/209-251 km/h) storm in just 24 hours.
WEDNESDAY I AUGUST 25
Our teams worked closely with our customers to begin offshore evacuations in preparation for Hurricane Ida’s landfall. Beginning Wednesday, PHI had calls twice daily with meteorologists from our weather monitoring partner to discuss forecast tracks and potential impacts to our Gulf of Mexico operations and facilities. We began sending daily communications to our customers and employees, updating them on the status of PHI’s Hurricane Evacuation Plan and anticipated impacts.
PHI placed our Gulf of Mexico facilities in Hurricane Evacuation Phase II – Pre-Evacuation and began relocating our aircraft, materials and crews from Houma and Boothville to our Galveston and Lafayette facilities—a 350-mile (536 kilometers) and six-hour trip. We notified our customers that flight operations and offshore evacuations would need to be complete by Saturday morning, for the safety of our people and passengers as outer rain bands began making their way across the region.
Our teams and their families started making evacuation arrangements, and those who chose to stay were bracing for the intensifying storm.
Around 10:30 am, all customer offshore evacuation flights were complete. From August 25-28, we evacuated more than 2,000 passengers on board (POB) from offshore. At this time, our eastern Gulf of Mexico locations moved to Phase III – Evacuation, and by close of business, we had evacuated 54 aircraft and approximately 120 employees to our Galveston and Lafayette bases where they remained safe through the storm.
Hurricane Ida made landfall as a high-end Category 4 storm on August 29 near Port Fourchon, Louisiana—about 60 miles (97 km) southeast of Houma. Maximum sustained winds were 150 mph (241 km/h), tying Ida with two other hurricanes for the strongest landfall on record in the state of Louisiana.
Final flights ahead of Hurricane Ida on Saturday, August 28—bands to the south east are outer bands from Ida.
Once it was safe to do so, our team conducted an initial flight and walkthrough assessments of our Houma and Boothville bases. Our Houma facility sustained considerable structural and water damage, and our Boothville facility sustained minor, superficial damage. Local utilities (water, power, natural gas) and infrastructure were heavily impacted with more than one million Louisiana residents and businesses without power, including our own facilities. Many roadways remained flooded and downed power lines and debris created additional hazards.
At this time, we also began deploying some of our aircraft, materials and crews to stand up alternate operational bases. Using the alternate locations that we identified as part of our annual hurricane evacuation plan, we established temporary operational bases while we worked toward reopening our Houma and Boothville facilities. We mobilized our Safety, Operations and Maintenance teams to conduct risk assessments of each new base location to ensure the proper controls were in place and that our high operational standards were met.
As we continued our post-hurricane assessments, our Human Resources team also continued outreach to all our employees in Houma and the surrounding areas to confirm their safety. To support our relief and recovery efforts, we established an Employee Relief Team to help collect and distribute supplies, collaborate with volunteers and assess how we can best help our impacted team members.
On Tuesday, August 31—less than 48 hours after Hurricane Ida made landfall—we flew our first passenger flights in support of our customers’ disaster recovery needs.
Hurricane Ida impacted nearly every aspect of our business, but despite the challenges, our teams came together to care for each other and our customers. Thanks to the quick action and support of our teams, we safely and successfully transitioned our operations from one main base location to three new bases across two states. In addition, we initiated ongoing recovery efforts for 146 PHI employees and contractors who were directly impacted by the storm.
Through those efforts, we provided more than 9,000 gallons of fuel for home generators and vehicles; more than $12,000 worth of relief supplies (nonperishable food, toiletries, essential goods, cleaning supplies, etc.); 16 hotel accommodations; volunteers to support daily employee relief efforts; and financial assistance for 14 employees through the Yellow & Black Giving Back Foundation.
Throughout September and October, we developed and implemented a phased approach to safely return to normal operations from our Houma and Boothville facilities. As part of our repopulation plan, we evaluated the damages to our facilities and worked closely with insurance adjusters, engineers and construction crews to restore our facilities. Once we cleaned and removed debris, we conducted a thorough area and facility assessment to ensure essential services (hospitals, emergency response and firefighting services) and local infrastructure (gas stations, grocery stores, restaurants and roadways) were restored. Our teams secured temporary facilities to replace buildings that were destroyed, completed necessary repairs to restore damaged facilities and secured contracts with local hotels while we continue to repair and replace our damaged on-site employee housing.
On September 14, we reopened our Boothville base facility with capabilities equal to pre-hurricane levels, and on Friday, October 22, we began our initial move back to Houma with repopulation efforts continuing the following weekend.
In just over two months after Hurricane Ida, we successfully resumed all pre-hurricane flight operations in Houma on Monday, November 1.
Our response in the aftermath of Hurricane Ida would not have been possible without the unwavering support and dedication of our teams. Over the last few months, we delivered near-uninterrupted service, support and maintenance to our valued customers. Many of our employees took on different roles and additional responsibilities as we operated in unfamiliar locations, but despite these challenges, we continued to operate safely and successfully thanks to our teams and their commitment to our core values and our customers.
We are extremely proud of everything we have accomplished over the last few months. You have showed unbelievable character and resolve in the face of adversity. Your unwavering commitment and dedication to each other and to our customers is a true reflection of what makes us a leader in the aviation industry. As always, our mission and core values drive our actions, and you have fully embodied these values and acted with an incredible sense of purpose, resourcefulness and dedication.
Thank you for your extraordinary efforts.
Through an exciting new partnership with the Massey University School of Aviation (Massey), we have welcomed our first student from Massey’s Aviation Management course, Alisa Izumi, into the PHI International (PHI) Safety and Quality team.
Alisa has spent the last three months supporting the implementation of safety cases (initiatives) in Ghana, Cyprus and Onslow (Australia).
“ “
I’ve definitely found more of a passion for safety and quality culture.
The partnership with Massey aims to launch the careers of the next generation of aviation professionals by equipping them with real world experience in the industry. Typically, students going through the programme at Massey are exposed to major airports and airlines, with a focus on commercial operations. Now, through its involvement, PHI is providing students a unique insight into helicopter aviation.
Anke Smith, the School’s Business Development and International Programmes Manager, said as the first helicopter operator in its network of host organisations, PHI offers students exposure to a new type of aviation.
“Being at the coalface of a globally successful company like PHI, our students will see first-hand the value PHI offers to its clients. Students will also get exposure to an expert, diverse workforce from a wide range of backgrounds and experiences.”
The opportunity with PHI has opened a door for Alisa into an area of the aviation industry that she previously knew little about.
HomeBase spoke with Alisa about her background and experience with PHI.
Alisa was born in Japan and has lived in Palmerston North since the age of three, crediting her Japanese heritage and experience of travel from a young age with sparking her interest in aviation.
“Ever since I can remember, I have always loved everything about travel—from the experience of being in an airport to arriving somewhere new,” said Alisa.
“The global nature of aviation is what most appeals to me—the opportunities are endless.”
When asked about the opportunity with PHI International, Alisa said she hadn’t actually heard of PHI prior to Anke Smith proposing the opportunity.
“I’m incredibly glad I know of PHI now and I hope this partnership opens the door for others studying at the School of Aviation. The awesome thing about the experience with PHI is that it’s an international organisation—it exposes you to more than just the operational side of a business. Before doing this role, I didn’t ever consider that safety and quality would be a pathway I could take—it’s definitely something I would consider now,” said Alisa.
Alisa has been working with Rob Cavers, Safety and Quality Director and the Safety and Quality team, and credits Rob for the warm welcome she received.
“The team is so supportive and nice. Working remotely, people might think ‘how would than pan out?’ but Rob is an amazing boss—I know I can just flick him a message, and he will always get back to me. The experience has been incredibly rewarding.”
Alisa spent one week in Nelson at PHI’s New Zealand headquarters for her initial training and says the experience with the team there couldn’t be matched.
“In my Aviation School studies we learn a lot about culture, which is one of our core papers, and having done this paper the semester prior to starting at PHI, I was more aware of culture and the impact it has on an organisation.
“Seeing this in practice is invaluable. Especially PHI’s safety culture—you can learn by reading about it—but unless you experience it first-hand, you don’t grasp the concept as well,” said Alisa.
The project has introduced her to bow-tie methodology, which is a way of identifying and understanding the impacts of hazards—commonly used in aviation.
“The work I am doing will help ensure the safety management system is in place and the teams have everything they need to prevent incidents from occurring,” Alisa said.
“The reporting culture at PHI is especially impressive—you can see how it really works to help prevent further incidents happening in the future.”
When asked if she has a dream role in the industry Alisa said the most important thing to her would be a matter of enjoying the role as well as the culture and team environment.
“There is a vast amount of work that goes on behind the scenes that people don’t know about. For example, when people travel through an airport—they have no idea about what is really going on to make sure things run smoothly. Getting involved in an opportunity like the PHI/Massey partnership opens your eyes to other types of roles in the industry.
“I have always been interested in scheduling—however, I know I’ve definitely found more of a passion for safety and quality culture which is exciting,” said Alisa.
Rob Cavers said he has been impressed with Alisa’s hard work and is looking forward to seeing other students join the programme.
“Alisa is the first of many students PHI will help to build the knowledge, analytical and research skills of and help establish themselves within the industry, setting them up for a long and successful career in our diverse and essential industry,” Rob said.
PHI will offer internships to Aviation Management students on an ongoing basis from November and plans to open up the same opportunity to Bachelor of Aviation students in the near future.
• Water wells discovered by archaeologists in western Cyprus are believed to be among the oldest in the world, dated at 9,000 to 10,500 years old.
• Legend has it that the Greek goddess of love—Aphrodite—was born in Cyprus.
• The Capital city of Cyprus—Nicosia—is the only capital in the world that is divided between two nations: the Republic of Cyprus and the Turkish Republic of Northern Cyprus.
• Mount Olympus is the highest point on the island and is also a ski resort.
• It is one of only four countries in the EU that drives on the left-hand side of the road.
Following a small campaign in 2011-2012, PHI officially began operations in Cyprus in September 2014. HomeBase spoke to Kyriacos (Kerry) Petsas, Director/Accountable Manager for PHI in Cyprus about the history of the country, PHI’s commitment to the region and the exciting upcoming contract with ExxonMobil.
Kerry is the Director/Accountable Manager for PHI’s Cyprus operations. Kerry was a line pilot when PHI started out in Cyrpus, and initially, operations were run via PHI’s US office. Throughout 2016 and 2017, Kerry took up a more active role as base & country manager, and since 2017, Kerry has been PHI’s main contact in Cyprus. Kerry oversees the day-to-day operations of the base.
George is Head of Maintenance and has previously worked for different organisations across the island, including as head of maintenance (fixed wing) for a local carrier. In 2019, George joined PHI, switching to rotary operations and, since then, has been doing an excellent job supporting our operations.
Spyros is the base Compliance Quality Manager, taking care of all compliance with the EASA regulations and new amendments regarding the regulations we must follow. He is also in charge of both flight operations and airworthiness (compliance with regulator). Spyros has a similar background to George and began with PHI at the same time in 2019.
Andreas is our Safety Manager in Cyprus. He is also deputy Flight Operations Manager. Andreas has approximately 25 years’ experience as a helicopter pilot and captain. Working across Search and Rescue, VIP transfer and offshore oil and gas, it’s safe to say he’s very experienced.
Since 2018, Natalie has worked as the Administration Officer for PHI’s Cyprus base. She can easily be described as the ‘Swiss army knife’ of the operations. Natalie also recently took up the role of parts store officer, and works closely with Pierre Lavoie’s team from Nelson for parts and tools in Cyprus to ensure the correct ongoing support is provided.
Chris is a Flight Operations Manager and Crew Training Manager and has been working part time with the team for the past year, joining the Cyprus team on a more permanent basis from the beginning of September. Chris is very experienced having spent more than 30 years in the industry as a Chief Pilot and Head of Training in various organisations.
Andy is the Senior Base Engineer in Cyprus and has worked for PHI since 2019— between Ghana and Cyprus. Andy has over 30 years’ experience in the industry, starting out in the British Army, then moving to civilian services with the UK Police, Bristow Helicopters, Bond Offshore Helicopters, Weststar Aviation and Leonardo Helicopters.
For those who don’t know the country well, Cyprus has seen considerable disruption for centuries. The Roman Empire, the Ottoman rule of Cyprus, and then the British Empire. The island was eventually annexed, and war declared between the Ottoman and British in 1914. In 1960, the Independent Republic of Cyprus was formed, however in 1974, Greek nationalists formed a military coup and Turkey invaded, which led to the displacement of thousands of Cypriots.
The de facto state of Northern Cyprus was proclaimed in 1975, now ‘the Turkish Republic of Northern Cyprus’ — recognised only by Turkey. To the international community, Northern Cyprus is considered part of the Republic of Cyprus.
In 2002, negotiations began to unify the north and south; however, this never came to fruition. In 2004, the Independent Republic of Cyprus became a member of European Union, but the two parts of the island remain divided.
Cyprus is a beautiful country with Mediterranean beaches, hilly fields covered with vineyards and forest-covered mountains. Our PHI team has a headquarters in Nicosia and base in Larnaca International Airport on the island.
PHI has the only local base in Cyprus with local employees. PHI is also the only operator with a secure and enclosed hangar, based out of Larnaca International Airport. Kerry is excited for the team as the new ExxonMobil win is their first offshore contract. After what has been a trying time for the team over the last 18 months, they are now looking forward to supporting one of the largest offshore oil & gas operations that the region has seen.
In 2010, seismic surveys were conducted off the coast of Cyprus and in 2011, PHI supported the first exploration campaign for Noble. Licences were then released for different exploration blocks. ExxonMobil won what is known as “Block 10” to explore for oil & gas. Based on preliminary data, Block 10 is the biggest discovery in Cyprus to date. There are now only two operational blocks: 10 and 12.
In 2020, PHI undertook discussions with ExxonMobil regarding the potential to work together again, and in quarter four of 2020, PHI was awarded the contract. It was a long and difficult process for our team, but they remained transparent and committed. ExxonMobil believed in the team and had experience working with PHI in the Gulf of Mexico. PHI International’s General Manager for Europe, Middle East and Africa (EMEA), Jamie Mitchell, has been pleased to take the Cyprus team under his wing and is looking forward to watching the team support the contract.
“After what I know has been a difficult couple of years for the team in Cyprus due to Covid-19, it is great to see them all in good spirits and ready to get stuck into this important piece of work for the region. I know that all their colleagues across all of PHI Aviation would be proud of their achievement,” says Jamie.
Kerry says the relationship between Exxon and PHI has been excellent, with consistent communication to ensure both sides can plan for the upcoming campaign as best as possible.
“What’s really unique for our team is to have one of the aircraft (AW139) from our New Plymouth/Taranaki base in New Zealand shipped over to the base in Cyprus for us to use for this contract,” says Kerry. There is plenty of work to do in the lead up, and things are set to kick off later in the year. PHI will be using two AW139’s for passenger support, cargo and delivery of Medivac support 24/7.
Kerry and the Cyprus team are keen to keep the good work coming their way. The team will ready themselves for an expected tender from ENI/Total later this year (initially awarded to PHI in Q4 2020 but cancelled due to Covid-19) and will be keeping an eye out for the release of a tender from Chevron early in 2022, for a campaign later next year.
When it comes to assisting rescuers in remote and challenging environments, there’s no better tool for the job than helicopters. When it’s a situation where every second counts, helicopters allow Search and Rescue (SAR) teams to quickly reach and transport passengers from some of the most inaccessible and harsh environments. Helicopter rescues are a pivotal capability of all offshore emergency response plans, and PHI has partnered with Heliservicio and Shell to establish a solid foundation for helicopter Search and Rescue (SAR) operations in the southern Gulf of Mexico.
In collaboration with key industry stakeholders, PHI and the SAR training company Total Response Solutions (TRS) are pioneering a new, multi-phased developmental SAR training model for regions that currently do not have dedicated SAR helicopter assets. The new program uses a tiered approach, taking an ab initio (no experience) rescue swimmer (RS) candidate and coaching them toward becoming qualified, safe and effective Rescue Crew members, with some progression to Hoist Operator (HO).
HELICOPTERS ALLOW SEARCH AND RESCUE TEAMS TO QUICKLY REACH AND TRANSPORT PASSENGERS FROM SOME OF THE MOST INACCESSIBLE AND HARSH ENVIRONMENTS.PHOTO ABOVE: A RESCUE CREW MEMBER DESCENDS OVER OPEN WATER
Through extensive planning and investment with our partners, we are assisting in building a comprehensive SAR program that is designed to be both an obtainable and sustainable development model for aircrew and technical positions including Rescue Swimmers and Hoist Operators. The program also includes a detailed support and maintenance program customized for SAR operations.
The SAR training includes all skillsets required to safely and effectively support offshore platform and marine operations including land, water, decks and small vessel hoisting scenarios. Working closely with industry partners and the experts at TRS, the program was developed not only to be compliant with industry best practices but to also exceed published AFAC, FAA and EASA standards for hoisting operations. The introduction of the new SAR program provides a sustainable funnel for the specialized training needed in these areas to extend the reach and number of people who can receive life-saving service when every second counts.
The SAR training program is ongoing for the newly-qualified SAR personnel and is supported by oversight, guidance and mentorship from our partners at Total Response Solutions (TRS). By importing and leveraging the use of highly skilled and experienced SAR operators, this program facilitates and fosters a talent pipeline for future home-grown rescue crew professionals. And, in addition, Heliservicio developed an improvement cycle to continue expanding operational capabilities and enhancing professional development.
The SAR program is a significant investment for the people of Mexico and represents not only an improved emergency response for the region but also provides new and meaningful career opportunities for local young people.
At PHI, we strive to be a catalyst for change by investing in our core values of safe, efficient, quality, service. Together with our partners, we are challenging industry standards and redefining the SAR model with innovation backed by experience.
This improved program is a pivotal moment for the SAR industry and the communities in which we operate, and we’re excited and proud to be a part of the future of SAR. As a company, we continue to look for new and innovative ways to do business and better serve our people, customers and the communities where we work and live.
HOBBIES: SURFING, SCUBA DIVING, CLIMBING AND OUTDOOR ACTIVITIES
Previous Experience: Bachelor’s degree in physical fitness and sport, university of Guadalajara, Mexico. 4 years as a professor in the university of Guadalajara, teaching Aquatic Rescue. Dennis is also Rescue diver qualified, paramedic and has been a life-guard instructor for the past 7 years.
HOBBIES: SWIMMING, TRAVELING AND OUTDOOR ACTIVITIES
Previous Experience: Medical Technician, studied at Guadalajara University. Sandy is also a Lifeguard Instructor.
Our teams operate in some of the most complex environments. We provide helicopter transport, search and rescue, and helicopter air ambulance services in more than seven different countries on four different continents, all while coordinating operations under varied local regulatory supervision and delivering services to our wide customer base. We understand that each Air Operator Certificate (AOC) holder must meet the local minimum regulatory requirements to maintain their certificate and retain their license to operate. Our Global Standards System (GSS) adds and improves on those minimum regulatory requirements, helping to achieve uniformity and consistency of PHI’s culture and internal standards across these varied services. The GSS sets us apart by exceeding not only the minimum local regulatory requirements but also our customer’s expectations. The GSS is a critical next step in achieving Destination Zero globally; embracing our core values of safe, efficient, quality, service; integrating our policies, processes and procedures; and transcending PHI to a state of global excellence.
PHI’s leadership originally identified the need for and started this ambitious journey to excellence in 2011. Over the past ten years, we have continued to grow and improve the system, and today, our leadership team continues to endorse this program in its mission to help make us “One Company Globally.” Initially pulling from best practices and key learnings from across our long history, we identified areas of improvement that could benefit our company not just at the local level, but throughout our organization globally. Global Standards is a critical component of our decades-long evolution to becoming and remaining a leader in the helicopter transportation industry.
Our Global Standards System and its integrated assurance process ensure standards conformance, making us “One Company Globally.” By exceeding the minimum regulatory requirements and industry standards for each operator certificate, our customers can enjoy the benefits of a reduced contract management workload. We have closed the gap on customer requirements and industry-recommended best practices worldwide
to provide our customers a streamlined experience while working with PHI across the globe. As such, our customers and partners can expect increased confidence that they are working with the best helicopter transportation service provider in the industry, allowing them to shift their focus to future improvements and innovation opportunities.
We are rapidly approaching the end of the initial phase of the program by completing the implementation of the first set of standards that were developed. These risk-based standards were developed from our historical accidents and associated learnings. We have also been working on developing the next phases of the GSS by focusing on industry learnings and comparing industry-recommended practices and customer requirements. This has led to the creation of a draft conformance standards document that defines the broad set of topics that PHI’s leaders envision to be the right path forward for our global processes and procedures.
The draft PHI conformance standards document will be validated against the different PHI Air Operator Certificate (AOC) holder organization’s manual suites to verify if the aspirational objectives are met or what needs to be done to locally meet the individual conformance standards. The results from this operational gap analysis will provide our leadership teams with the information they need to evaluate, prioritize and further develop our global standards.
We encourage all PHI employees to discuss improvement opportunities with their manager and, where applicable, contact their local GSS focal point to submit potential suggestions for improvement opportunities to solve a global problem.
After a recent review of our Global Standards System, it became clear that while the GSS is a critical part of our organization, we must ensure it reflects the latest organizational structure within PHI and compliments activities underway across our business. The results of our review include a series of exciting changes that better position the GSS for the future and strengthens its integrations across all of PHI.
We look forward to sharing these updates with you in the coming months!
Resiliency—the ability to recover from challenges and push forward in the face of adversity—is a hot topic, especially during the COVID-19 pandemic. But over the years, our teams have shown much more than resilience. They’ve shown courage, compassion, adaptability, selflessness, innovation and strength.
In a time when most businesses were experiencing a drop in demand, PHI was able to strengthen partnerships with our customers and continue to build our position as a leader in aviation—a feat that would not have been possible without the commitment of our teams and their dedication to our core values: safe, efficient, quality, service. And while our success as an organization requires all our teams working collectively together, our 145 Repair Station has always been there to support the operation.
JOHN ELLYSONBased at our Lafayette, Louisiana, facility, our 145 Repair Station has always been a critical part of our welloiled operations, but their recent efforts have pushed them further into the spotlight. Over the past 12 months, our Repair Station team has successfully returned 14 aircraft to service in support of our customer contracts and operations. Although the journey wasn’t always easy, the 145 Repair Station rose to the occasion, facing every challenge head-on to support our teams and ensure the success of our operations along the way.
After emerging from Chapter 11 bankruptcy in 2019, PHI underwent significant operational restructuring so that we could better support our teams, customers and future growth. Our priorities were moving forward with the right-sized capital structure, streamlining our operational footprint and ensuring proven teams were in place to meet our customers’ needs. As part of our strategy, we focused on more appropriately sizing the organization for our current and planned operations.
Then came 2020.
When the COVID-19 pandemic became a global reality, our customers forecasted a 50 percent reduction in flight hours and aircraft, and our business, like so many others, had to once again restructure in response to the impacts of the pandemic. As a result, we decided to park aircraft based on our customer requirements. Our teams worked to identify which aircraft to park based on age, total time and time since last visit to repair station. Together, our fleet of parked aircraft increased by more than 20 helicopters. Once parked, we proactively removed aircraft components that had time remaining from parked aircraft and reallocated the components to operational aircraft. We also reinstalled the components on parked aircraft, allowing us to maintain long term preservation on the parked aircraft and continue operating if needed.
Our Repair Station managers worked with our Materials department to develop a strategic plan to meet our component forecasts. Our teams closely monitored the planned forecasts of components coming due and worked collectively to meet those requirements. The hangar staff also created a schedule to perform ground runs on parked aircraft to maintain longterm preservation status. Those ground runs still occur monthly on our remaining parked fleet which includes less than 10 aircraft.
As the global economy and aviation industry began to recover from COVID-19, our Business Development team worked closely with our long-term customers and partners to understand their current and future needs. In late 2020, we started to see an increase in activity—I believe, due largely in part to our teams’ dedication to a high quality, high service culture; our availability of aircraft; and our unwavering commitment to safety and reliability.
Our customers’ demand accelerated quicker than the industry anticipated, and we began getting requests to return aircraft to service. For each parked aircraft, the Repair Station team had to comply with all overdue inspections and component replacements prior to returning aircraft to an airworthy state—a significant task, let alone for 14 aircraft. In order to meet our customers’ needs on time and within budget, the Repair Station worked as one team to branch out of their core competencies through a cross-training initiative. This “#OneTeam” mentality has allowed our team to gain deep understanding into the needs and goals of our colleagues for more organizational flexibility and cross-functional collaboration.
Today, not only is the 145 Repair Station team supporting our current fleet in the US Gulf of Mexico, but we’re also providing support for our international aircraft and our partners in PHI Health with manpower, technology support and onsite aircrafton-ground (AOG) support.
At PHI, our people set us apart, and I truly believe that we have one of the greatest—and most resilient—teams. Your loyalty and dedication, combined with your expertise and experience, is unmatched in the industry. So, to the team in the background, showing up to support our operations day in and out, thank you—I couldn’t be prouder to work alongside you each and every day.
Since 2015, Mark Cook has been PHI’s International Head of Flight Training and, in April this year, was appointed Chief Pilot. Mark has had an illustrious career in aviation, working as a Royal Air Force Pilot for 22 years before moving to PHI (then HNZ) in 2008 as a Check and Training Captain. He spent some time away from PHI before re-joining in 2015.
HomeBase sat down with Mark to get to know him better and hear about his role at PHI.
“
“
As a young boy I imagined myself in the cockpit... There hasn’t been a dull moment since.
My interest in aviation started early. As a young boy I saw aircraft flying around and imagined myself in the cockpit. I was determined to go into the Royal New Zealand Air Force (RNZAF) and structured my education around securing a highly sought-after space. This career path was extremely competitive in the mid-80s and thousands applied for a much-coveted spot.
I then spent 20 years with RNZAF, working across a range of divisions, from instructing in helicopters to flying fixed wing and rotary wing aircraft. Very few people go through the air force and spend virtually their whole career flying like I was able to, so I feel very privileged.
I was deployed to the South Pacific, Australia and Antarctica on a few occasions, taking part in peacekeeping deployments to the Solomon Islands, Timor Leste (East Timor) and Bougainville (Papua New Guinea). All incredibly interesting operations which I was privileged to be a part of.
After an interesting and exciting career with RNZAF, I felt it was time to move on, but I wasn’t ready to stop flying completely. An opportunity came up with PHI, and I jumped at the chance, joining in 2008 as a Check and Training Captain. It was a great way to transition in the civil world of aviation, and just like in the military, there hasn’t been a dull moment since.
Busy. At the moment, I spend my day talking to other parts of the organisation, addressing any issues that arise and ensuring all our teams feel supported during the challenging nature of operating in the context of Covid-19. Prior to March 2020, I would spend a significant
part of the year travelling to our training bases and simulators around the world, which I really enjoyed. I always learn something new on my travels, and it’s great to meet our teams on the ground.
That’s an easy one—New Zealand. Being involved in training our teams around the world has meant that I would often be away for almost half the year. Whenever I’ve been away for an extended period, landing in New Zealand is always special.
It’s too hard to pick just one. During my time with the RNZAF, I was deployed on several peacekeeping missions. During a deployment to East Timor, one of our soldiers was accidently shot in the neck while deep in the mountains on a day with extremely low cloud and heavy rain. We went to extract him that day just as it was getting dark; it was satisfying to get that flight done in a challenging environment where there were multiple threats and no guarantee of achieving the task.
Flying in Antarctica was also a highlight because it’s probably one of the few places in the world that you can’t buy a ticket to. It’s a fascinating place, and I spent time at both McMurdo Station and Scott Base flying in support of both the New Zealand and US Antarctic programmes, flying scientists and support staff throughout the Ross Sea region. One thing that stands out now is just how isolated we were while out there, especially since it was in the days before the internet and satellite communications. HF phone patch was the only voice communication with the outside world.
It’s got to be the AW139. The aircraft is modern, is really reliable, has power to burn and has easy-to-use systems. However, if you’d asked me the same question 10 years ago, I would have said the Huey (UH-1H). I grew up in the era of Huey and flew it for 15 years all over the world, so it’s hard not to have an affinity with the aircraft.
You had a bit of time away from PHI at Aerogulf Services and then Bristow between 2012 and 2014. What brought you back to PHI?
I had strong pull back to New Zealand and the lifestyle here. My family was living in Dubai, and we all wanted to come back to NZ. It was my opinion then just as it is now, that PHI was the company of choice in this part of the world, so I jumped at the opportunity to come back and eventually take on the Chief Pilot role.
The safety-first approach is deeply embedded across all of PHI’s operations. All employees at PHI understand their responsibilities to their passengers, the organisation and themselves. We also have a speak up culture. Our team is not afraid to step forward with any concerns they might have at any stage, and I encourage all our pilots to speak up—no matter how minor they think the issue may be.
Continuous improvement is also a key focus at PHI. We are constantly reviewing the safety procedures we have in place and adjusting them. In my role, I’m constantly on the lookout for the latest developments and research on safety in our sector, and I encourage our team to do the same.
The aviation industry has modernised at a rapid pace over the last two decades. For me, the use of new technology in our helicopters stands out. Modern auto flight systems, properly integrated avionics systems, Full Authority Digital Engine Control (FADEC) and powerful engines has provided reliable, high-performance helicopters, making our role as pilots easier and safer.
MARK AT THE ROYAL NEW ZEALAND AIRFORCE BASE IN OHAKEA (2002) WITH THE RNZAF HUEY
How would you describe being part of the PHI family?
PHI really does have an inclusive environment, and I really like the fact that while we have grown rapidly, everyone has a good understanding of who their colleagues are throughout the organisation. In my role as Chief Pilot, I get to interact with all parts of the organisation, and across all our bases, it’s very clear that everyone feels part of the same team.
Being part of the PHI community also means providing opportunities for our team to grow and learn. An example of this is the support we provide for our low experience scheme trainee pilots, hosting them at our base in New Plymouth and enabling them to get qualifications which then allows them to fly for on and offshore flying contracts. It can be really difficult in our industry for junior pilots entering the helicopter system, and by providing training, we are able to give some budding aviators a flying start, which is fantastic.
What is it that you believe sets PHI (and its pilots) apart from other operators?
PHI excels with our environmental footprint and the services we provide. We use an electronic flight bag and an electronic information management device in our aircraft, which makes our job a lot easier than having sheets of paper like we’ve used in days gone past. We also provide an extensive range of services from oil and gas support, marine pilot transfer, seismic survey, SAR (search and rescue), mineral exploration, vertical reference and utility operations. We provide all these services at a really high quality to an incredibly high safety standard, and I believe we are an industry leader in that regard.
TECHNOLOGICAL TOOLS ASSIST
A NEW SAFETY AND QUALITY INITIATIVE
OUR PHI INTERNATIONAL TEAM HAS ANNOUNCED A NEW WELLBEING INITIATIVE, WHERE WE HAVE TEAMED UP WITH INTEGRATED SAFETY SUPPORT (ISS), A WORKPLACE PERFORMANCE AND FATIGUE MANAGEMENT COMPANY, TO PROVIDE ALL EMPLOYEES WITH ACCESS TO ECLIPSE, A SUITE OF ONLINE RESOURCES AIMED AT SUPPORTING PHI STAFF’S MENTAL HEALTH AND WELLBEING.
The resources have been introduced as part of PHI’s Fifth Pillar of Safety, focusing on the human aspect of safety and in recognition of the impact that the pandemic has had on everyone as a lot of the team have faced travel restrictions, the introduction of quarantine requirements, lockdowns and working from home.
The resources cover a range of topics such as sleep, occupational alertness, fatigue management and workforce productivity. They also include several targeted training courses and smartphone apps, meaning any PHI employee can access the resources anywhere and at any time.
While safety has always been at the forefront of our flying operations, we recognise the impact the pandemic has had on fatigue and that this can affect every role in the business, from those in the field, on base, at head office or working from home. Eclipse will be offered to every PHI International employee, representing an increased focus on health and wellbeing across our business.
PHI International Safety and Quality Director, Rob Cavers, said, “The ongoing pandemic is causing many of us to feel more physically and emotionally tired, so it’s important we support the mental, social and physiological wellbeing of our people.”
Rob is encouraging all employees to give the new resources a try saying, “Safety has always been paramount at PHI, and we know the impact fatigue and stress can have on our people. Embracing the safest behaviours and practices through addressing health and wellbeing concerns is a huge priority for us.”
PHI International’s Human Resource Director, Lenore Richter, understands that the pandemic has created a lot of uncertainty and extra pressure, stating, “Our team has gone the extra mile during the pandemic, and we acknowledge it’s been a stressful time for many.”
Lenore has noted the importance of looking after mental health just as you would physical health saying, “the safety of our people is our number one priority, and a core part of this is our team’s mental health and wellbeing. We want to ensure everyone is equipped with the skills to adapt and manage challenging situations and we see these resources as being a great tool for everyone.”
EXAMPLE OF FATIGUE/ALERTNESS TEST USING ECLIPSETHANK YOU FOR ALL YOUR HARD WORK AND DEDICATION TO PHI OVER
We thank Bruce for his many years of dedicated service and wish him all the best in retirement!
OVER
OVER THE YEARS—WE LOOK FORWARD TO MANY MORE YEARS TO COME.