













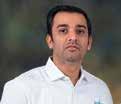



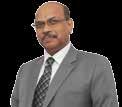


























- September
- September
A cracker of an issue...as POLYMERS Communiqué celebrates its 8th anniversary...coinciding with the pre-K 2022 issue! Editions as these are conceived rarely...an absolute processors’ delight. Constellation of stars on the cover page have dug deep to bring out some fantastic content to share their latest advances as the industry gears to converge at K 2022.
It’s all about a cohesive movement to prove time and again to humanity as regards the enormous benefits that plastics bring to our planet. We are proud to be a part of this wonderful plastics industry which willingly stretches to innovate and support the cause of sustainability, circular economy, recycling and more without compromising the functionality of products that drive our lives. The actions and analysis are driven purely by a scientific approach. ‘Material Science’ forms the foundation of this movement and thus the focus of this very special issue of POLYMERS Communiqué before the much acclaimed and awaited ‘K-Fair 2022’! The world is getting ready to visit ‘K’ with ideas to fructify new approaches and new businesses! See you at Düsseldorf! Happy Diwali, wherever you are!
India on the Cusp of a Consumption Explosion Will Require 30 Million Tonnes of Polymer by 2030
Ajay Shah, President - Polymer Chain, Reliance Industries Ltd., Navi Mumbai
Petrochemicals: A Step Towards a Greener Tomorrow
Sujoy Choudhury, Director (Planning & Business Development), Indian Oil Corporation Ltd., New Delhi
Shailesh Sheth, Corporate Strategy Advisor, Management & Manufacturing Technology, Ahmedabad
vishal Mehta, Managing Director, Aquent Advance Material Technologies Pvt. Ltd., Mumbai
office.in@br-automation.com | +91-20-41478999
Sponsored by Pankaj Poddar Group CEO, Cosmo First Ltd., New Delhi
Pradip Chokshi, Managing Director; Jagat Chokshi, Director; Mirang Chokshi, Director; Basil Prompt Vinyl Pvt. Ltd., Ahmedabad
Sustainability Through Recycling of Materials and Waste as Feedstock - Part III: Battery Recycling
Professor (dr.) G. d. Yadav, National Science Chair (SERB/DST/GoI), Emeritus Professor of Eminence, Former Vice Chancellor & R.T. Mody Distinguished Professor, Tata Chemicals Darbari Seth Distinguished Professor of Leadership and Innovation, Institute of Chemical Technology, Mumbai
Sponsored by Kairav Engineer Vice PresidentBusiness Development, Astral Ltd., Ahmedabad
Polypropylene: The Most Versatile Polymer Poses Many Challenges to Achieving Circularity
dr. S. Sivaram, Former Director, CSIR-NCL, Honorary Professor Emeritus and INSA Emeritus Scientist, Indian Institute of Science Education and Research (IISER), Pune
Marvels of Material Science
Rakesh Shah, Probity Consultants, Delhi NCR
Material Innovations: Driving the Industry
Chintan R. Joshi, Kaushalya Reputation and Brand Consultancy, Mumbai
A Lot More at ‘STACK’ Going from 3 to 5 to 7 to 9 to 11 Layers: Because Layers Matter
Sponsored by Rajesh Sonar General Manager - Sales & Marketing, Mamata Machinery Pvt. Ltd., Ahmedabad
Indian Rotogravure: Globally Comparable
Kaku Kohli, Managing Director, Kohli Industries, Ambernath
Exciting Times Ahead: Toys, Renewal Energy, Automotive, Healthcare to Present Growth Opportunities
Amit v. Pendse, President, Electronica Plastic Machines Ltd., Pune
Medical and Pharmaceutical: The New Focus Areas
A. dayanand Reddy, Managing Director, Vasantha Tool Crafts Pvt. Ltd., Hyderabad
Immense Opportunities for PVC, the Construction Polymer: Leadfree Stabilisers, the Way Forward vivek Kale, SBU Head - PVC Additives, Baerlocher India Additives (P) Ltd., Mumbai
The Indian Toy Story: An Industry Gearing Up for Global Prominence
Gaurav Mirchandani, Director, Candytoy Corporate Pvt. Ltd., Indore
Process Automation: A Crucial Role to Play in Waste Reduction and Sustainability
Arun Pundir, Director & CEO, Aerodry Plastics Automation Pvt. Ltd., Noida
Energy Efficiency: A Clarion Call for the Industry
varun Ramsisaria, Director, Viva Petrochemical LLP, Tamil Nadu
Screen Changers: The Game Changers in the Plastics Industry
hardit Parikh, Director, Rajhans Plastic Machinery Pvt. Ltd., Ahmedabad
In-mould Labels: The Future of the Packaging Industry
Manish desai, Director, MUDRIKA Labels Pvt. Ltd., Mumbai
Special Processes, Skilled Workforce and Material Knowledge: Vital for Manufacturing Screws, Barrels, Nozzles and Injection Heads
Bharat Makwana, CEO; Siddhant Makwana, COO; Shreeji Corporation, Ahmedabad
S. K. Ray, Hon. Secretary & Member of Executive Committee, Indian Centre for Plastics in the Environment (ICPE), Mumbai
Manish Chawla manish@custage.com
Jyoti jyoti@custage.com
Chairman and Managing Director
Welset Plast Extrusions Pvt. Ltd. Prof. (Dr.) N. C. Saha
Jigish N. doshi, President, Plastindia Foundation
formerly Director at Indian Institute of Packaging N. K. Balgi formerly President & Director at Ferromatik Milacron India Pvt. Ltd.
Pushp Raj Singhvi
formerly Vice Chairman and Managing Director at Borouge (India) Pvt. Ltd.
Rajesh Nath Managing Director, German Engineering Federation (VDMA) India Office
INDOPLAS, INDOPACK and INDOPRINT 2022: Fulfilled High Expectations
l 50 Years of Kündig Control Systems: A Success Story
l Leistritz Presents Myriad of Solutions at INDOPLAS 2022, Jakarta
Flexible Packaging - Moving to a Sustainable Reincarnation: Big Discussion at the ElitePlus Summit
Rakesh Shah formerly Managing Director at Windmöller and Hölscher India Pvt. Ltd. S. K. Ray formerly Sr. Executive Vice President (Polymers) at Reliance Industries Ltd.
dESIGNEd BY Custage Marketing Solutions LLP 406, Vikas Centre, Dr. C. G. Road, Chembur, Mumbai 400 074, INDIA
PRINTEd AT Silverpoint Press Pvt. Ltd. A-403, TTC Industrial Area, Near Anthony Motors, Mahape, Navi Mumbai - 400709, District - Thane
AdvERTISING SALES - NATIoNAL Hyderabad Vani +91-93924 28927 vani@polymerscommunique.com Mumbai Vinisha +91-88790 50327 vinisha@custage.com New Delhi Vijay +91-98100 15111 vijay@polymerscommunique.com
PAgeS
Printed and Published by Manish Chawla, and printed at Silverpoint Press Pvt. Ltd., A-403, TTC Industrial Area, Near Anthony Motors, Mahape, Navi Mumbai - 400709, District - Thane and published from 406, Vikas Centre, Dr. C. G. Road, Chembur, Mumbai 400 074, INDIA. Editor: Manish Chawla.
Domestic Subscription: Single Issue Price: Rs. 150; Annual Subscription: Rs. 1200 (including shipping)
Overseas Subscription: Annual Subscription: USD 60 (including shipping)
Views and opinions expressed in this magazine are not necessarily those of POLYMERS Communiqué. Readers are advised to seek specialist advice before acting on information contained in this publication, which is provided for general use and may not be appropriate for the readers’ particular circumstances and so POLYMERS Communiqué does not take any responsibility for any loss or damage incurred or suffered by any of its subscribers / readers / advertisers of this magazine. The publisher makes every effort to ensure that the magazine’s contents are correct but do not take any responsibility for the absolute accuracy of the information. Subject to Mumbai Jurisdiction. Some of the images used in this issue are from Shutterstock. The maps, if used, in this document are only a pictorial representation, not to scale and do not indicate any geographical boundaries.
No part of this publication or any part of the contents thereof may be reproduced, stored in a retrieval system or transmitted in any form without the permission of the publisher in writing. POLYMERS Communiqué reserves the right to use the information published herein in any manner whatsoever. The ownership of trademarks is acknowledged.
Vadodara D. S. Bhumra +91-81289 90887 devinder@polymerscommunique.com
AdvERTISING SALES - INTERNATIoNAL Dubai
Pritam +971-5548-32330
pritam@polymerscommunique.com USA
Manisha +1-908-720-3510 manisha@polymerscommunique.com
SUBSCRIPTIoNS
Bhavesh +91-22-2520 4436 bhavesh@custage.com
In the current ‘era of technology’, materials play a very significant role in our daily life as these are applicable in almost all segments like transportation, housing, clothing, communication, food production and, of course, in packaging. In fact, every segment of our daily life is influenced by materials. Hence, material science is considered to be one of the very important subjects in today’s context. Material science allows one to understand the characteristics of any material for making a proper design by using a particular material for a specific application. Moreover, material science would also help to overcome the constraints of any particular material by combining these materials with other similar or dissimilar materials to achieve the required properties and to meet the purpose.
However, the constant demand of various requirements in our daily life has compelled one to specialise in material science. More importantly, the specialisation in material science has become an urgent need in the packaging industry for the development of alternative materials with high degree of functional properties for packaging applications in compliance with environmental regulations. It is a fact that modelling and simulations for the development of new materials and analysing their properties / performance would definitely dominate in the years to come with special focus on the materials with high energy efficiency, reduction of carbon emission and meeting the requirements of a circular economy.
Arvind Mehta Chairman and Managing DirectorWelset Plast Extrusions Pvt. Ltd.In a global scenario of multidisciplinary domains, materialscience is turning out to be a ground-breaking domain.
According to material scientists, computing power is beingwidely used. If one requires a specific material, he just needs tofeed the properties of the material into the computer programand run the simulation, and this type of innovation will help theworld to develop materials according to their needs.
Till date, the major breakthroughs the world has experiencedin material science in terms of speciality materials are lithium,graphene and perovskite.
Speciality materials developed by material scientists byunderstanding the complex structures and various properties ofthe materials are catching the eye of the entire globe.
A shift in focus towards speciality material has been observedin fields like aerospace, automotive, medical and construction.
You have raised a very pertinent topic of material science.
To begin with, polymer science evolved as a replacement for traditional materials like paper, board, glass, tin, rubber etc.
Over a period of time, polymer scientists all over the world saw its immense potential in all critical uses; be in aeronautics, automobiles, medical equipment, computer assembly, cell phones, photographic equipment to almost every important application it would have been impossible to have any one of these without speciality polymers. Like a common person can’t survive without plastics, these applications would be next to impossible even to imagine. Polymer technologists and polymer scientists are continuously researching special materials to help its modern use and enhance the quality of life.
Rakesh ShahRajesh Nath N. K. Balgi S. K. Ray Prof. (Dr.) N. C. Saha Arvind Mehta Pushp Raj Singhvi Pushp Raj Singhvi formerly Vice Chairman and Managing Director at Borouge (India) Pvt. Ltd.With the advancements in science, new possibilities emergedin products and services to meet human needs. These productsdemanded new materials with specific or enhanced properties.Carbon steels evolved into the family of alloy steels with enhancedstrength, wear resistance etc. Non-metals such as insulatingmaterials got evolved to withstand high voltage power transmissionsystems. Material science has always ‘moved to speciality’.
Now, it is the turn of the youngest member of the materials family -‘plastics’ to evolve into its speciality avatar. Born as polymer from thepetrochemical family which can be melted with heat and shapedby applying pressure to produce parts of common use got namedas commodity plastics. Compounding it with other materials toenhance the properties, we got the family of ‘engineered plastics’now used in transportation vehicles, furniture etc. Born wasthe family of engineering plastics for meeting specific needs ofstrength, rigidity, heat resistance etc.
Current demands of the society on environmental sustainabilityhave led to the development of biodegradable polymers. ‘Missionnet zero’ demanded moving away from the use of fossil-based fuelsfor the transportation system and gave birth to electric vehicles(EV). EV construction and powering system batteries have led to thedevelopment of a host of polymeric materials with special properties.Thus, the ‘need’ and a creative mind ‘visualising possibilities’ to meetthe needs will keep material science moving to ‘speciality’ always.
Rajesh Nath Managing Director German Engineering Federation (VDMA) India OfficeThere have been changes in the choice of materials for engineering activities. Materials went through the ages of activities on the earth like the stone age, the iron age and the current silicon age. But the challenges of the current world’s needs are constantly fuelling the need for discovery and development of new kinds of materials with the desired properties and the relevant cost to meet the challenges in the engineering world. The present trend is towards lightweight, robust materials which have reduced wastage in manufacturing ultimately leading towards circularity.
S. K. Ray formerly Sr. Executive Vice President (Polymers) at Reliance Industries Ltd.
The key differentiator of humans from other forms of life is the intelligent use of materials. As civilisation evolved, the range of materials used also expanded. Copper age dating back to 8700 BC ushered in the dawn of material science. A rudimentary understanding of metallurgy helped humans leapfrog to a new level of sophistication in the production of various tools and implements. The next transformative phase was the age of synthetics - fibres, rubber and plastics. The field of material science witnessed dramatic expansion during this phase. New-found knowledge helped in designing products with unprecedented features. There is a constant endeavour to develop materials with new features which, over time, get commoditised. Therefore, the field of material science would continue to be in perpetual flux in its quest for ‘speciality’.
Material science is an interdisciplinary field of study and focuses on research, discovery, applications and replacement of materials to achieve higher performance and lower costs. This developed as a separate field of study in the 1940s and combines physics, chemistry, engineering and other areas of research. Plastics is a field that is rapidly transforming due to the development of speciality materials that offer unprecedented performance.
Besides the development of various basic polymers, newer materials have revolutionised the world. A simple and early example is Teflon which is today used in applications ranging from domestic cooking pans and toasters to space and aeronautics components. Kevlar is another early and outstanding example that has moved from the punched tapes for NC equipment to bulletproof body armour and myriad applications, and is one of the strongest materials known.
Medical applications, biodegradable implants and permanent implants such as for knees, thighs, other joints and spinal components are all results of advanced research in material science.
All kinds of additives help create plastic alloys or composites and impart a range of characteristics to plastics to achieve targeted results ranging from colouring to high performance, light-weighting, processability or machinability and so on.
Current developments are towards more sophisticated materials such as nano-composites, further moving to graphene and biomaterials. Material science has been finding and crossing new frontiers of applications and unprecedented possibilities that we can classify as speciality applications.
Rakesh Shah formerly Managing Director at Windmöller and Hölscher India Pvt. Ltd.I and my colleagues are good readers of the POLYMERS Communiqué magazine and appreciate the efforts behind this publication. It is well-designed, excellent and informative magazine which keeps us updated. Content is very informative and we find a lot of interesting articles where business owners, marketers and sales personnel can learn how to use technology, new products etc. for enhanced profitably in their businesses.
Further, I can say that sitting at my own office, POLYMERS Communiqué provides the highest quality posts / articles to read without wasting time to search on the net.
Praveen Sachdev Krypton Polymers Pvt. Ltd.
‘POLYMERS Communiqué’, the title of themagazine is likely to appeal to those who areinterested in the converting business andplastics industry. As the magazine doesn’tdepend on advertising, it has become awell-established informative magazine in itsown right.
Most of the articles, if not all of them, actuallyhave pictures to go with the content of the textnot only making it very informative throughreading, but also through observing the detailedpictures. Such qualities allow magazines to wellexpand as regards target audience. All editionscover new and informative subjects. The digitalversion is a value addition and user-friendly.
Hiten P. MehtaPrintgraph Converting Machinery LLPAny business runs in power when your goods are commendable and anothermain factor with the help of publicity. POLYMERS Communiqué is such aplatform where they encourage new ventures and help the old ventures staycompetitive. This magazine has not only enhanced my contacts, but also hasgiven me great patrons.
Jimit Sheth Shri Ambica PolyfillPOLYMERS Communiqué is a great magazine that helps its loyal reader base keep up with the polymer industry. It’s a must-read for stakeholders.
Gaurav Saraogi Chemco Group of CompaniesWe go through the POLYMERS Communiqué publication regularly and would like to put forth the following opinion on the same. It provides good knowledge sharing with the real experience of the entrepreneurs and wellknown multinationals and their innovative work. Mind speak is also a good read. Innovations and solutions for recycling are also impressive, but much more needs to be done.
Ganesh H. DevadigaNilkamal Ltd.PC is one of the few industry publications dedicated to polymers as a subject. The magazine has good print production quality. I have seen some good interviews and well-researched stories whenever I have picked it up.
My best wishes to the publication for keeping up the good work.
Nitin Agrawal Vacmet India Ltd.
Thanks for the e-magazinecopy. I was very muchupdated after reading thesame. The content by theindustry experts is very muchrelevant to the current topics. Ihave benefited from the same.
Trushar BhavsarBritex PlastochemThe magazine is great to read. The quality of the articles is crisp and inspiring to stay connected with the industry. With everything online, this is probably the only physical polymer magazine published.
Rajesh Jain Arihant Goldplast Pvt. Ltd.Leverage your competitive advantage with our collective expertise.
Always ahead in providing
Alpla and PTT Global Chemical realise Thailand’s largest plastics recycling plant equipped with state-of-the-art technology
Amcor expands innovation centre network with opening of world-class facility in Asia Pacific
Armacell launches unique, non-combustible aerogel insulation blanket
Avient completes acquisition of DSM Protective Materials
BASF and ARCUS sign an agreement on the production and procurement of pyrolysis oil from mixed plastics waste
Covestro has some good news for the Asia-Pacific region as it is investing here in the production of more sustainable polycarbonates. There has been a surge in the demand for sustainable materials from this region and to honour that demand, Covestro has committed to deliver over 60,000 tonnes per year of recycled polycarbonates annually by 2026. To prioritise this mandate, Covestro is setting up its first dedicated line for the mechanical recycling (MCR) of polycarbonates at its integrated site in Shanghai. The new MCR line will address the growing demand for more sustainable solutions, in particular with PCR products, to be used primarily for the compounding step in the manufacture of electrical and electronic products, automotive applications and consumer goods. The line, which represents an investment of over EUR 27 million, will be capable of delivering over 25,000 tonnes of high-quality polycarbonates and blends containing mechanically recycled content annually when it is planned to be commissioned in 2023. Overall, the company aims to be capable of delivering over 60,000 tonnes of polycarbonates with recycled content in Asia Pacific per year until 2026.
Covestro will also be repurposing an existing compounding line at its Map Ta Phut site in Thailand to a plant for mechanical recycling, which will pave the way and meet market demand for polycarbonates from PCR content across multiple industries in the ASEAN region.
Davis-Standard welcomes the industry to real-time preventative maintenance and cost savings at your fingertips with the DS Activ-check™. Take advantage of the cloud-based IIoT system for improving extrusion line productivity.
Analytical tools based on long-term cloud data storage and process technology algorithms support realtime preventative maintenance and line efficiencies. High-level digital security, configurable for mobile applications, continuous monitoring and performance dashboards are just a few advantages of this user-friendly platform. Smart processing is the smart choice to leverage competitive advantage. Learn more about digital transformation and how it can help your operational efficiencies and your bottom line.
Get started on your digital transformation journey to see how you can benefit!
Berry produces lightweight pack solution for cream spreads
Borealis and Trexel develop new reusable and fully recyclable lightweight bottle
Datwyler positions itself for the future with electroactive polymers
Evonik is introducing a new sustainable highperformance plastic to its eCO product line Glenroy Inc. and Nature Nate’s Honey Co. partner to provide consumers a sustainable packaging solution
Greiner Packaging buys Serbian PET flake producer ALWAG
Haitian PET solution, setting up a ‘protective barrier’ for your food safety
Kandui has developed a thermochromic masterbatch, a kind of additive masterbatch, which brings reversible colour-changing properties to fibre or moulded items.
These masterbatches have an activation temperature. The end-product becomes fully coloured below the activation temperature and colourless above the activation temperature.
winder with a maximum line speed of 150 mpm. It includes thickness control by air and temperature. It is Industry 4.0 compliant with remote diagnostics and support through smart glasses.
The event was well attended by processors from all over the country and even neighbouring nations.
Commenting on this announcement, Khushboo Chandrakant Doshi, Managing Director, Rajoo Engineers Limited says, “We are pleased to share with you all the launch of the latest addition to our portfolio. This product exemplifies our relentless efforts towards product development offering the most ‘appropriate technology’, which is the core motto of Rajoo Engineers.”
This property is utilised in the secret coding of fabrics and other moulding items, adding a security feature to the original branding. It is also extensively used in children’s toys such as bottles / ice-cube storage containers wherein the toy will change colour when refrigerated.
Pentafoil POD - The New Generation 5-layer Blown Film Line
Rajoo Engineers Limited announced at their open house event at Rajkot on 9th September, 2022, the launch of their new product, Pentafoil® POD - the 5-layer blown film line.
Pentafoil POD comes with several advanced features. It incorporates relEX 4.0 extruders, leading to 27% increased output; CSD 3.0 with a 550 mm die delivering an output of 720 kg/hr and Flexiwind 3.0 surface-centre-gap
“I would like to take this opportunity to thank everyone in the Rajoo family who has worked relentlessly towards continuous product development and innovation to enable us to offer not just new products, but help us evaluate our customers’ needs and endeavour to meet them and walk the extra mile ensuring customer satisfaction,” conveys Khushboo Chandrakant Doshi.
Windsor KL - A Real TwoPlaten Technology KL - A real two-platen technology has been synonymous with serving privileged customers in the automotive and white goods industry. KL is also preferred in other plastic applications like furniture, material handling, industrial, household and city civic, PVC fittings etc. due to its smaller footprint, cost-effectiveness and efficiency with minimal resource consumption.
The KL two-platen machine series (available from 350 T - 8,000 T) has the most advanced specifications in the world relating to the clamp and
Henkel acquires advanced materials start-up NBD Nanotechnologies Inc.
Henkel celebrates inauguration of adhesive technologies’ Inspiration Center Düsseldorf
INEOS Styrolution introduces range of new sustainable ABS speciality solutions
ISCC and Circularise pilot blockchain technology with 10 companies to complement mass balance certification
Koch Technology Solutions and Ioniqa Technologies partner to disrupt plastics industry through advanced PET upcycling technology
Kraiburg presents sound TPE solution for hearing aid applications
Largest Baltic PET recycler PET Baltija agrees to acquire leading Czech fibre producer
injection area. The KL two-platen machine series provides immense value-added features and flexibility to customers.
Attributes like patented synchronised movement of tie-bar nuts, smaller footprint, unique tie-bar regulation mechanism, higher mould life, lesser lubrication demand, higher mould weight carrying capacity, 15” touch screen display, faster machine operations, higher uptime, lesser maintenance, lesser energy demand, excellent repeatability costeffectiveness and efficiency etc. add value to your business and raising the bar of performance for injection moulding machines.
The KL series was honored with the 7th National Award for Technology Innovation in Plastic Processing Equipment by the Department of Chemicals & Petrochemicals, Government of India in 2017.
Controlling the dimensions of the pipe during production is an important factor in keeping the pipe to the required specifications. Rollepaal offers a wide range of scanners with various features covering pipe sizes from 10 to 1,600 mm (1/2” - 60”) diameter. Rollepaal scanners immediately identify any irregularities in the dimension.
Rollepaal offers two types of scanners: l Rotating: Measures wall thickness.
l Compact (Static): Measures wall thickness and diameter.
Features and benefits of the Rollepaal scanners include:
l Integrated software in the central controls.
l Usable in other production lines.
l Continuous in-line wall thickness measurement.
l User-friendly operator interface.
l Self-adapting to the pipe diameter, no diameter-related parts.
Rollepaal rotating scanner (RRS).
Rollepaal compact scanner (RCS).
l Manual and automatic calibration capabilities.
l Continuous in-line wall thickness and outside diameter measurement.
l Excellent return on investment.
l Reduced start-up time and scrap.
l Overweight reduction.
l Minimum amount of space required with multiple lines.
l Suitable for solid wall PVC, PE, PP, CPVC and PVC-O pipes.
High-quality tear-proof plastic sacks save tonnes of dry bulk goods that would otherwise go to waste or contaminate the environment. Made of woven polypropylene tape fabric, Starlinger’s AD*STAR® block bottom valve sacks are highly resistant to breakage and can help to reduce product loss in the dry bulk industry.
AD*STAR sacks were developed and patented by the Austrian machine manufacturer, Starlinger & Co. GmbH, the leading supplier of machinery and complete plants for the production of woven plastic packaging. The sacks are used for packaging a wide range of freeflowing goods such as cement and other building materials, fertiliser, chemicals or
M. Holland’s 3D Printing Group expands portfolio of Braskem PE and PP filament
Mauser Packaging invests in multi-layer plastic drum machine expands capacity for growing demand of its Infinity Series products
Moog X700 Series 2-way servo cartridge valves with superior flow performance
MULTIVAC’s new production factory in Japan: An important building block in its expansion strategy
Mura Technology and Dow plan to locate Europe’s largest advanced recycling facility at Dow’s site in Böhlen, Germany
Novolex invests US$10 million in Indiana recycling expansion
Polyplastics’ new 3D printing technology for DURACON® POM accelerates product development cycle
Starlinger AD*STAR® block bottom valve sacks are perfect for fully automatic filling and can be equipped with various convenience features such as handles or easy-open flap.
resin, and also for foods like flour, sugar and animal feed.
AD*STAR sacks are block bottom valve sacks made from coated polypropylene tape fabric and sealed with a patented hot-air method without the use of glue or sewing threads, making them a mono-material packaging that is easy to recycle. The sack bottom and top are closed in a special conversion process by means of hot air welding. The use of high-strength polypropylene for fabric production and the tight sealing of the sack bottom and top ensure low breakage even during rough handling, dropping or after contact with water. The precise production process on Starlinger’s AD*STAR sack conversion lines ensure high-quality sacks with minimum size variations. Currently, over 17 billion AD*STAR sacks are produced on Starlinger lines installed on five continents every year.
Skills Engine Projects (SEP), located in Vadodara, Gujarat, is a provider of plants for compounding, masterbatches, calendaring and customised materials handling solutions.
As a part of its vision and to support
ALTERO recycling line.
the industry, SEP ventures into the recycling business. SEP has joined hands with Aranow Altero, Spain for sales and services of recycling plants for various post-industrial and postconsumer applications. ALTERO’s specially designed, optimised infrared heating solution will benefit the industry with lower specific energy and lower running cost of production. It will support stakeholders for their EPR initiative.
To end the environmental problems associated with the misuse of plastics waste, it is key to bet on innovation from different perspectives, providing a comprehensive and integrated vision. The European strategy emphasises the prevention of the generation of plastics waste and the increase in recycling rates, as well as stimulating new business, production and consumption models that cover the entire value chain.
Polyblendz Pvt. Ltd. (PIPPL), is a specialised producer of custom engineering plastics compounds of PA, PBT, PC, ABS, PP, PPO etc. used in many industrial applications. It is 100% privately owned with a capacity of 12,000 MTPA for engineering plastics, in its state-of-the-art facility in Vadodara, Gujarat.
As a part of its business growth plan to cater to the masterbatches industry, we are happy to announce 100% slump acquisition of Palvi Masterbatches (part of Palvi Industries Ltd.). Palvi is a specialised manufacturer
Researchers at Queen’s University Belfast have developed a groundbreaking plastic film that can kill viruses with room light
Röchling expands portfolio with sustainable vacuum forming materials for railway technology applications
SABIC launches new short-glass fibre-filled PP compounds with enhanced performance for automotive structural applications
Last May, RadiciGroup announced this important action aimed at strengthening its internationalisation strategy with an investment of around EUR 35 million. The transaction allows RadiciGroup - in India since 2006 - to further reinforce its local presence through this acquisition.
Sinochem International, ELIX Polymers’ parent company, opens its compounding factory in Yangzhou, China
Solvay partners with Inaventa Solar for more efficient solar collector designs
Teijin Frontier develops world’s first tire cord made from eco-friendly adhesive and recycled polyester
For RadiciGroup, this is a significant industrial investment in which Ester Industries Ltd. sells its newly built production plant in the city of Halol (Gujarat), West of India: compound lines, R&D laboratories, customers / suppliers contracts as well as its leading brand ESTOPLAST which includes different types of compounds used primarily in the electricals / electronics and telecommunications markets.
TR -Ester Industries Ltd. - one of the leading Indian producers of polyester films, engineering plastics and special polymers - has seen in RadiciGroup an ideal partner to follow up on its consolidated experience in the engineering polymers business, in order to focus on the packaging film sector, a business the Indian firm intends to continue and strengthen.
The new production site, under construction, will become operational at the beginning of 2023, following
the various transfers of tangible and intangible assets. As a result of the acquisition, the Group aims to achieve total annual sales in the Indian market of more than EUR 50 million.
DPL Group is the primary producer, wholesale supplier and exporter of blowing agent, calcium carbonate, pigment powder, zinc stearate, China clay, talc, TPE and TPU to the polymer industry which aids countless secondary and tertiary industries of rubber, EVA sheets, EVA sole, rexine, XLPE foam, plastics, paint etc. With passing years, we have gained faith in the polymers and elastomers field across India and in nearby countries, while extending production and sales of industrial TPE, TPV and other distinct compounds of thermoplastic elastomer materials.
Under the umbrella of DPL Group, there are 10 flourishing brands namely, DPOFOAM (blowing agent), DPOCELL (modified ADCL), DPOSHADES (basic and premix pigments), DPOBLEND (thermoplastic elastomers), DPOSOLE (shoe sole compound), DPLOMAX (premium shoe sole compound), DPOFLOW (granular zinc stearate), DPOCAL (activated, precipitated and natural calcium carbonate powder), DPOFILL (China clay and talc), DCP90% (dicumyl peroxide) and synthetic rubber to cater to the wider supply and demand of the polymer industry.
“The three market segments that will witness steep growth in coming times are the Indian retail sector, backed by robust growth in e-commerce; the other being pipes, tubes and hoses, driven by the government infrastructure projects; and polymer usage in agriculture, and is expected to see a 4% growth,” opines Ajay Shah, in dialogue with
Q. How does the Indian polymer industry compare with its global counterpart?
India is one of the largest polymer producers in the world. It is the fifth largest producer of polypropylene (PP) and ranks among the top 10 high-end polymer producers globally. The two largest drip lateral manufacturers have their production bases in India.
India ranks third in polymer consumption globally, after China and the US. However, there is a big difference in per capita consumption.
India has strong potential for growth as it has a low per capita consumption of about 14 kg polymer per annum - one-tenth of that of the US and less than a third of that of China. With rapid urbanisation across the country and the Indian government’s stressing on ‘Make in India’ to turn the country into a manufacturing hub, segments like retail, automobile, construction and
infrastructure will strongly boost polymer demand and bridge the demand-supply mismatch.
India’s current polymer consumption is around 20 million tonnes, having more than doubled from around 8 million tonnes in 2010. With the nation on the cusp of a consumption explosion, we will require 30 million tonnes of polymer output by 2030. To meet this requirement, Indian producers need to either ramp up their brownfield capacity or set up new greenfield units.
As per industry data, 1 million tonne of capacity addition requires USD 5 billion of fresh investment. India must invest around USD 75 billion in the next 10 years to build the required capacity equivalent to meet the burgeoning consumption.
Along with India, the entire Indian sub-continent is expected to witness a strong growth in polymers. India is expected to lead the growth in the Indian sub-continent, offering a plethora of investment
The COVID-19 pandemic and the subsequent disruptions have put the polymer industry at the centre of VUCA world challenges. Commodity prices have been surging in tandem with international crude prices. Amid these uncertainties, it’s a challenging task to navigate business to success. We are adopting all risk containment measures to tide over these challenges.
opportunities. The sub-continent has a larger population than China but has 20% less polymer demand. Over the next five years, the region is expected to see one of the fastest growth rates in polymer demand in the world and will outstrip China and other emerging economies.
Q. Commodity to speciality... how do you see developments of players for the niche market segments?
The Government of India is implementing policies to drive economic reforms, creating a conducive environment for healthy growth of the economy. The ‘Make in India’ initiative is expected to provide a fillip to the manufacturing sector. With the polymer industry’s thrust on development of research-based innovative products which provide greater strength, durability, aesthetics, light-weighting and barrier properties, the usage of polymer applications will increase substantially in the construction, electronics, automobile and aerospace industries.
The expanding automotive and electrical industries, combined with infrastructure development, are expected to further drive the growth of speciality polymers market in India.
Q. Three market segments that you believe will witness steep growth in coming times...
The Indian retail sector is booming,
As per industry data, 1 million tonne of capacity addition requires USD 5 billion of fresh investment. India must invest around USD 75 billion in the next 10 years to build the required capacity equivalent to meet the burgeoning consumption.
backed by robust growth in e-commerce. This phenomenon has generated a robust demand for packaging materials. Currently, India imports materials worth USD 265 million, which is 5% of the total imports of finished goods. With focus on manufacturing products with additional functional features, simultaneously keeping the cost competitive, the Indian industry is poised to grab the opportunity of import substitution.
The other segment that is expected to see robust growth is pipes, tubes and hoses. These products have seen imports worth USD 193 million3% of the total imports. Growth in this segment will be driven by the government infrastructure projects like roads, railways, airports and ports. R&D-based polymer products in these categories offer more durability, ease of transportation, as well as ease of installation, and hence they are the most sought-after among alternatives.
Polymer usage in agriculture in India is very low compared to developed economies, despite India being the second largest producer of fruits and vegetables. This segment is expected to see a 4% growth. There is a huge potential for plasticulture in India as its share in the global market is only 1%. Polymer applications helping water conservation, wastage reduction and yield improvement are expected to drive the growth in this segment.
Q. Engineering applications for polymers have attracted a lot of investment and research. How do you visualise the evolution of this sector?
Polymers are transforming various industries in terms of efficiency improvement, while also reducing operating costs and carbon footprint.
Reinforced plastics have become an effective alternative to metal
components. Reinforced plastics are lightweight, stronger, adaptable and durable. A robust increase in demand is expected for this wonder material across applications. Reinforced plastics applications are most sought-after in automobile, aerospace, medical and construction sectors.
Polyester is currently showing the highest growth rate, driven by its applications and substitution of polyamide in certain electrical and electronic segments.
Polypropylene and reinforced polypropylene demands are growing rapidly due to research-based product development in high-volume applications for the automobile industry. This product category is expected to register 10 - 15% per annum growth rate; demand traction for highperforming polymers like polyphenylene sulfide (PPS) and liquid crystal polymer (LCP) to see rapid growth.
Q. How do you see the dynamics of the evolution of material science in the coming 5 - 10 years? The change that could have the biggest impact...
The R&D teams at leading polymer companies, including Reliance Industries Ltd., are working to make innovative products that can improve the quality of life, provide performance enhancement, cut costs, enhance durability, improve aesthetics, reduce carbon footprint and improve performance.
For so many years, advanced composites have been growing at a very good rate, especially in the aviation and aerospace sectors. Of late, modern composites are being used in almost all industries, including transport, packaging, renewable energy and construction. We expect that carbon fibre reinforced
To know more, please subscribe to PolymErs Communiqué at subscriptions@polymerscommunique.com
“Petrochemicals present a high-value proposition for the company’s future growth. There are several benefits of investing in this space including immense growth potential, high margins, synergy with the core business and a hedge to the long-term slowdown in oil demand as forces of energy transition gather pace,” says Sujoy Choudhury, in dialogue with POLYMERS Communiqué.
Q. The COVID-19 pandemic and the recent geopolitical scenarios have impacted even the most formidable organisations. How did Indian Oil Corporation Ltd. (IndianOil) manage to tide over these difficult times? The last year was extraordinary in many ways and it altered our perspective on how to survive even in the most disruptive times. The post-pandemic era has witnessed a steep rise in crude demand and the Russia-Ukraine war has further fuelled a massive surge in feedstock prices including fluctuation in product prices, foreign exchange, interest rates etc. IndianOil has been continuously monitoring the macro- and micro-economic environments that can potentially impact our business. However, proactive and predefined control measures enable us to identify, analyse and mitigate risks that can affect our future operations.
IndianOil’s diverse product portfolio, flexibility in refinery operations and robustness in its internal business processes have allowed us to sustain during these disruptive times. Through sheer grit and determination of our workforce, we were able to supply POL products, especially LPG, seamlessly even during the pandemic. We went beyond our normal call of duty and supplied liquid oxygen for medical purposes at a time when our country needed it the most. This is why we call ourselves, ‘Pehle Indian, Phir Oil’.
Q. Give us some insights about the upcoming projects that shall further the IndianOil story in the coming decade.
IndianOil has been relentlessly working to meet the rapid growth of India’s energy needs, while
also pursuing the aspiration for a sustainable future. We have been investing assiduously across various facets of the energy spectrum. From natural gas, renewable resources or biofuels, to cutting-edge fields of hydrogen, CCU (carbon capture and utilisation), advanced biofuels and battery technology. All this has been done while consolidating our fuel business. The COVID-19 pandemic has strengthened our resolve to respond faster to new projects that promote cleaner energy along with our conventional fuel portfolios while pursuing downward integration into petrochemicals.
Petrochemicals present a high-value proposition for the company’s future growth. There are several benefits of investing in this space including immense growth potential, high margins, synergy with the core business and a hedge to the long-
In 2021, the value of gross imports for the petrochemical end products (top 52) was Rs. 1,08,681 crores, which is expected to rise further in the coming years. Although a few mega capacities are going to be on stream very soon, the proposed capacity addition is far less than the demand deficit.
term slowdown in oil demand as forces of energy transition gather pace.
IndianOil has invested over Rs. 24,000 crores in petrochemicals in the past and is currently the second largest player in the domestic market. We are committed to investing further in this sector by increasing our petrochemical intensity index. IndianOil is planning to double its capacity in the next 5 - 6 years from the existing 3.2 MMTPA to 6.4 MMTPA. This is in line with Prime Minister Narendra Modi’s vision of ‘Make in India’, ‘AatmaNirbhar Bharat’.
These expansions are based on integrating petrochemicals with refinery expansions and entering the niche and speciality segments. These projects include revamping of existing units47 KTA of purified terephthalic acid (PTA) plant and 121 KTA of monoethylene glycol plant in Panipat, 42 KTA of linear alkyl benzene plant in Vadodara, construction of the new 357 KTA of mono ethylene glycols and 1,250 KTA of purified terephthalic acid in Paradip, 200 KTA of PP in Barauni, 450 KTA additional PP in Panipat, 500 KTA PP in Vadorara, 475 KTA PP at CPCL, Nagapattinam and 60 KTA polybutadiene rubber plant in Panipat. We will be the first company in India to manufacture styrene with a capacity of 387 KTA.
IndianOil is also planning further integration in the polyester downstream space through a 300 KTA of the textile project at Bhadrak, Odisha.
Q. How do you look at the evolution of materials science in the coming 5 - 10 years? A change that could have the biggest impact...
An organisation that can predict future technologies, future customer requirements and their behaviour better, will emerge victorious. Change is imminent and we have already witnessed the evolution of plastics in the last century. Plastics will drive
the development in agriculture, healthcare, automotive, infrastructure and packaging industries for the next 5 - 10 years. Amongst all, the packaging sector, which is under tremendous transformation, is likely to have the biggest impact of these developments. The growth of materials science is largely driven by the development of technologies to support the upcoming challenges of evolving applications and existing supply chain limitations. Some of the top emerging trends in this field are sustainable materials, smart and responsive materials, nanotechnology, 3D printing or additive manufacturing, advanced composites, graphene etc.
The recent implementation of the Plastic Waste Management (Amendment) Rules, 2021 saw a nationwide prohibition on the manufacturing, importing, stocking, distribution, sale and use of identified single-use plastic commodities, effective from 1st July, 2022. This policy has also mandated Extended Producers’ Responsibilities (EPR) for petrochemical producers and processors, a step that would ensure the emergence of better technology for recycling.
Q. The focus on a 360-degree approach to sustainability seems to be getting stronger with materials science companies. What are your views on this and its impact on the processing industry?
A 360-degree approach to sustainability means rethinking the entire production and distribution process and looking
at them through a green lens. This would ensure removing every potential threat to the environment. Materials science companies need to redefine their product portfolios to meet diverse demands. In my view, the processing industry will also be impacted by:
l Re-designing the product at the same cost to meet the recycling standards such as producing them in a single colour, avoiding multi-colour printing, using a single polymer, increasing the thickness etc.
l Biofuels from agricultural waste to complete circularity.
l Energy saving, sustainable materials for higher productivity.
l Investing in making the process more flexible to blend various recyclable materials into end products.
l Waste to wealth, recycling of synthetic products, green chemistry for green products etc.
Q. In times of prevalent variability, what are your plans to modify or reinforce your existing systems to maximise your customer connections?
IndianOil has one of the most extensive customer interfaces and we are constantly striving to improve customer experiences. Each of IndianOil’s new products, such as premium petrol products - XP100 and XP95, XtraGreen diesel, winter-grade diesel, XtraGreen lubricants like Servo Green Mile and Servo Raftar are designed to keep the customers connected to innovation.
IndianOil always maintains sectorspecific retail marketing campaigns as well as regular industry meetings for institutional business customers. We are also leveraging digital innovation,
To know more, please subscribe to POLymers Communiqué at subscriptions@polymerscommunique.com
The chemical and petrochemical deficit in the short, as well as the long run, will continue to be a reality in India. However, it provides enough headroom for expansions.
It is clear that smart materials offer greater opportunity as well as may prove to be the most drastic disruptor of existing products / businesses. However, R&D continues to be focussed on ‘what’ to produce, rather than ‘which’ materials to use. However, it’s not yet too late. Let us begin ‘today’.
Shailesh Sheth Corporate Strategy Advisor, Management & Manufacturing Technology, AhmedabadMaterial science has been evolving ever since the stone age. Tools made of stone, utensils made of base materials like copper and bronze, extensive use of the natural resource of wood, and later, iron and steel. The modern era saw the development of newer materials like aluminium and ceramics. More recently, you see wide usage of composites, polymers, semiconductors and the like. It is not the intention of this article to delve deep into the technical aspects of material science, but to analyse what drove their development and peep into the future as to how newer materials would impact manufacturing, and where?
With rapid industrialisation, the materials which were based on natural sources of minerals, started to attract attention. Fossil fuels are a classic example. Asbestos is another. The world is concerned about depletion of natural reserves of such minerals and the negative impact on the environment, health and safety. We want to leave a better world for our future generations. At Bangalore International Exhibition Centre, they have used a lot of fly ash and
less of cement precisely with this in mind.
Manufacturing too has to go green! If this has to happen, first the materials used must change. Thus, sustainability will be the key driver of new developments in material sciences going forward.
In an article titled, ‘More from Less for More, The Power of Inclusive Innovation’, Dr. Raghunath Mashelkar argues that the MLM concept must have a wide impact on the manufacturing system design across a range of products. The concept encompasses:
M = More performance (Harness sophisticated technology and quality),
L = @ lesser cost (Affordable to all strata of society),
M = To benefit more people (Inclusiveness).
The need to pursue the MLM concept is obvious. But to do so, apart from design and engineering, materials used will have a significant contribution to make, making MLM the next important driver that will emphasise the need to develop newer materials.
This concept converges multiple objectives. Reducing the cost of products, enabling a reduction in the quantum of energy used, improving process efficiency and, most importantly, achieving lower carbon footprint and aiding a shift towards sustainability. Considering that the use of aluminium reduces the mass by between 30 - 60%, carbon fibre composites can reduce it by 50 - 70% etc. These materials can be used in four ways to achieve the objective:
l Increasing understanding of the materials themselves through modeling and computational materials science,
l Improving their properties (such as strength, stiffness and ductility),
l Improving their manufacturing efficiency (material cost, production rate or yield),
l Developing alloys of advanced materials. (Source: U.S. Department of Energy)
Widely used in the automobile industry, the concept of light-weighting is gaining popularity across product segments, making it a crucial driver for the development of material science.
Scientists continue to invent advanced materials with highly specific properties that outperform existing materials and enable more innovative product designs.
Manufacturing companies prefer to use tried-andtrue materials for their products - these materials are already validated and their chemical and mechanical properties well-studied. However, product performance and functionality can often be improved with new materials that, once tested and approved, deliver highly specific engineered properties that enhance product performance and create product design options that were not available before.
Source: Mark Crawford, Technology Writer
This new concept of manufacturing intricate parts reverses the process of their manufacturing
To know more, please subscribe to Polymers Communiqué at subscriptions@polymerscommunique.com
Scientists continue to invent advanced materials with highly specific properties that outperform existing materials and enable more innovative product designs.
Manufacturing companies prefer to use triedand-true materials for their products - these materials are already validated and their chemical and mechanical properties well-studied. However, product performance and functionality can often be improved with new materials that, once tested and approved, deliver highly specific engineered properties that enhance product performance and create product design options that were not available before.
Source: Mark Crawford, Technology Writer
Rare earths will drive the future of material science. We are only at the beginning of a new revolution that may happen in the next decade.
“Functional polymer market globally is a specialised technical market with very few players operating in this field, and India is now becoming a significant player. The functional polymer demand is going to substantially increase in India and across the world with the increase in demand from automotive, wire and cable, optic fibres, recycling and packaging industries,”
highlights Vishal Mehta, in dialogue with POLYMERS Communiqué.
Q. Share with the readers, in short, an overview of your business today.
Aquent Advance Material Technologies is into research and manufacturing of functional polymers, in collaboration with a technology partner from the US. Functional polymers has been a growing segment globally and in India as well. Today, most of the materials are imported from different parts of the world.
Aquent produces high-quality functional polymers, impact modifiers and coupling aid for engineering plastic compounding for automotive and consumer goods markets, coupling agents for the wire and cable markets, coating resins for optic fibre FRP rod, tie layer resins for multilayer packaging,
Functional polymers for EP and PP compounding are currently the growth drivers; packaging and cable would add to the future growth. Furthermore, optic fibre coatings is most certainly going to contribute to our growth plans; so is recycling and biopolymers.
coupling and resins for CPP and BOPP, recycle resins and tie layers, lamination resins, biopolymer coupling agent and chain extenders as well as elastomers for high-performance footwear.
Q. A young company engaged in a very niche and demanding segment of the plastics industry, what drew you towards this industry and how has the journey been so far?
Global compounding, cable and packaging OEMs are looking at India as a manufacturing base. Today, most of the quality functional polymers are imported with a lead time of 3 - 4 months mainly from Europe and US. Aquent identified the need of customers due to supply chain constraints and established a state-of-the-art manufacturing and testing facility to manufacture functional polymers in India. Most of the domestic and global customers have welcomed Aadibond functional polymers with open arms. They found high-quality products at the lowest lead time and reasonable value for money. Many customers agreed to join the development programmes that led to new product innovations and application developments. The journey so far has been quite exciting and the future looks more promising. Aadibond functional polymers are now approved by multinationals in India and their plants in Europe and the USA as well.
Q. Sound knowledge of the properties of various polymers partnered with excellent knowhow of chemistry is the key to making a mark in this niche segment. How should a company stay abreast of the latest developments?
We have invested in R&D and application laboratories along with continuous updates on graft technologies through international collaborations; various joint development programmes with customers in various applications namely cable, optic fibre, packaging and EP compounding; and working closely with them has helped develop new polymer solutions. To address the sustainability challenges, we have developed new functional polymers for biopolymers, recycling and EPR requirements.
Q. With such a diverse solution system, what strategies do you follow for business forecasting?
We work very closely with our customers for forecasting and planning; most customers work on annual programmes and have benefited from such engagements. Long-term mutual commitments with customers have helped in planning and forecasting for such a range. This also has helped customers with JIT availability in tough supply markets. Aquent comes with 15 years of supply chain and distribution experience in speciality elastomers and polymers which has come very helpful in catering to customers’ planning.
Q. Which are the verticals / applications that you envisage as being major contributors to your business over the next 2 - 3 years?
Functional polymers for EP and PP compounding are currently the growth drivers; packaging and cable would add to the future growth. Furthermore, optic fibre coatings is most certainly going to contribute to our growth plans; so is recycling and biopolymers.
Q. The material of the future, your views.
Optic fibre FRP coating, biopolymers and recycled resins for EPR and sustainability are surely the product of the future. Our compatibilisers and tie layers for recyclable
To know more, please subscribe to PolymerS Communiqué at subscriptions@polymerscommunique.com
Friday night to Monday morning, a time to unwind, rejuvenate and be geared to face another grueling week. Each one of us use this ‘my time’ is different ways. And why not, weekend is a time for expressing ourselves. We all have known the personalities featured here as astute business stalwarts; as life is more than just business, we at POLYMERS Communiqué, have started this section called ‘WEEKEND DELIGHTS’. Live life...
The weekend is very precious as I spend a lot of time talking on the phone to my children in the USA and watching my grandson growing in new skills. The morning ‘Dev Pooja’ is done in leisure and thereafter I spend some time in the kitchen preparing either breakfast or lunch. I like to drive out with my wife on a short trip to some nearby destination for some fresh air and rejuvenation.
On Sundays, I like to read articles and books which I mark and set aside during the week for weekend reading. Many times, I watch some good TV shows over lunch, but do not like to miss my nice afternoon nap.
On weekends, I like to play musical instruments like the guitar and piano. Music gives me peace of mind from my workaholic nature on weekdays. The guitar improves the grey matter in the brain resulting in improved memory power. Playing some tunes takes me back to the old days and relaxes me; it creates a therapeutic experience and reduces stress.
One of the health benefits of playing guitar is that I feel positive and energised by my own progress.
I like to start my weekends by giving a big cheer to the life that I am blessed with by having a walk and feeling the fresh air. A good cup of coffee with my brother discussing a bit of work and family, spending quality time with my mother, wife and kids and catching up with friends are an integral part of my weekend.
Playing cards and cycling are activities that I normally indulge in.
Venture Automotive Tooling India Pvt. Ltd.
Weekends are so special for me. I wake up early in the morning and visit the beach with my family; we practice yoga in the breeze from the seashore. After enjoying the beachside yoga, we relish a special breakfast at the platform shops on the beach wherein we get to have organic and healthy soups and snacks.
Most weekends, I sit at home and the family has lunch together and over dinner, it’s movies on OTT.
Every Sunday, I prepare myself with the ‘To Do’ list for the upcoming days.
Wow! Weekend comes to me as a big boon to unwind me, ending the hectic work schedule of the week.
I love to start my weekend with an energetic long morning walk in the lush green Cubbon Park, Bengaluru. I enjoy watching different breeds of pet dogs there, having fun; it really destresses me a lot.
My love for cooking gravitates me to experiment with different types of sandwiches for breakfast and spend good time with my family, which really rejuvenates me fully for the next gruelling week ahead.
Being a Punjabi, I am a big foodie and love dance and music. I enjoy dining out and exploring different cuisines with my family. Finally, it’s time for relaxing on my favourite couch, binge-watching the latest TV shows.
“In the current market, a lot of PVC manufacturers opt for selfcompounding - a process that involves sourcing all the essential components of additives and measuring them separately. Several risks and uncertainties meander around this process. Generally, in self-compounding, chemical proportions differ and the final products eventually get affected. However, manufacturers realise this fact after they are done with producing and testing their products,” shares the Basil
Prompt Vinyl team, in dialogue with POLYMERS Communiqué.
Q. A first from Silvin in India is the SUPER1Pack, what prompted this initiative? It all began when we visited our customers and observed that they were initially buying ready-touse compounds. However, when they switched to self-compounding, it was a struggle for them to adjust the formulation, which was mainly due to insufficient in-and-out knowledge of the additives. Also, due to the lack of necessary understanding, there was a lot of chemical wastage. These observations helped us to come up with this unique concept of Super1Pack.
At Silvin, we believe in providing customised solutions with a detailed understanding of the customers’ requirements to produce PVC and CPVC pipes and pipe fittings. Identifying market trends and developing these solutions has been one of our core values. For instance, our Super1Pack is an all-in-one additive containing stabilisers, internal and external lubricants, impact modifiers and other essential chemicals or additives other than PVC resin, CaCo3 (filler) and pigments. This is a universal, unique, free-flowing powder formulation, particularly for the PVC and CPVC
piping industry. Therefore, this additive simplifies the manufacturing process and helps bring more uniformity to production. This ensures that we leave no room for error in the PVC and CPVC manufacturing process. In recent times, with the introduction of a new guideline that restricts the usage of lead-based additives, Silvin has become an even more relevant and indispensable factor in PVC and CPVC manufacturing.
Q. Since the waning of the pandemic, real estate and construction activities are on the upswing; what is your business growth that you anticipate over the next 2 - 3 years? In the overall market scenario, there is an evident chance of 40 - 50% growth. As we look inwards, our inventory management system, on-time deliveries and no price fluctuation are also some of the reasons for envisioning our progress. That’s why we believe that we too will witness huge growth in the coming 2 - 3 years. We are constantly solving the challenges of procurement and supply chain, and bringing convenience to the customers successfully.
Q. What are the perils of selfcompounding and how does Silvin plan to combat that?
PVC additives are a very important part of PVC manufacturing. However, their combination matters a lot. Anything more or less can affect the process immensely, ultimately impacting the final product. In the current market, a lot of PVC manufacturers opt for self-compounding - a process that involves sourcing all the essential components of additives and measuring them separately. Several risks and uncertainties meander around this process. Generally, in self-compounding, chemical proportions differ and the final products eventually get affected. However, manufacturers realise this fact after they are done with producing and testing their products. Apart from the risk of getting the combination incorrect, there are uncertainties like a sudden price hike by the dealers, variation in quality, delay by suppliers, availability of key ingredients etc.
Salesforce, a CRM software, and SAP, an ERP solution, ensure that the end-toend process stays wellcontrolled. By integrating them, we have developed our ecosystem so we can maintain timely delivery, the right purchase at the right price as well as keep the supply chain management intact and efficient. One of the major benefits is that it helps improve the bottom line. Mainly 80 - 85% is the raw material cost.
As the rejection percentage increases, processors constantly change their formulations. To make things right, they always need an expert for the right combination. And their biggest challenge is to fix the formulations by trial and error.
Our greater goal is to completely eliminate this process with our Super1Pack formula. Over the years, we have been successful in coming up with a device that challenges this practice, and we are constantly innovating to achieve this goal.
We guarantee the best quality, timely material delivery and consistent availability of our products. We always buy in bulk and maintain 2 - 3 months of inventory at any given point in time. Additionally, we have a professional purchase team in place that monitors international prices. This is why our customers never have to face the impact of sudden price fluctuation as compared to the ones who prefer self-compounding.
Q. You have invested significantly in IT infrastructure. How do you see its impact on business? Your message to other business owners...
Salesforce, a CRM software, and SAP, an ERP solution, ensure that the end-toend process stays well-controlled. By integrating them, we have developed our ecosystem so we can maintain timely delivery, the right purchase at the right price as well as keep the supply chain management intact and efficient. One of the major benefits is that it helps improve the bottom line. Mainly 80 - 85% is the raw material cost. So, processing margins are narrow, and if there is even a slight difference of 5 - 7%, there will be a chance of loss. If anyone wants to make their business scalable, it is necessary to implement modern software like inventory and customer-relationship management in their system.
Q. As one of the world’s leading additive suppliers, one message that you would wish to convey to the processors would be...
We feel that processors should really invest in making products that are ecofriendly and cause no harm to humans or the environment. Thus, in future, the approach should be on manufacturing ‘harmless’ products, rather than just the R&D or, for that matter, simply replacing hazardous additives.
Q. You are a strong believer in branding. Share with us the kind of impact it has had on your growth.
Collectively, we believe that branding is necessary along with following highquality standards. We have ensured that our processes give us an identity that matches up to the kind of innovation we bring to the table. For the past few years, we have been able to create a product that is unique and has helped the industry immensely. Thus, we call it magic. That’s what we say whenever there’s a mention of our brand. That’s why Silvin, as a brand, believes in adding magic to additives.
We have been dominating the market for quite a long time now. Earlier, we lacked brand recognition and even those who admired our formula didn’t know of us. But as we started building an identity and an effective way of communication, the recall value has increased multifold.
In the past, it took hours to make people understand the USPs of our brand. Now, it takes a few seconds to tell and remind people of the benefits or the rewards of using Silvin. This has only been possible because of our thoughtful communication and identity design.
To know more, please subscribe to PolYmERS Communiqué at subscriptions@polymerscommunique.com
During the period 2019 - 2030, 1,000 GWh of remanufactured and second-life batteries will be in the market. The highly recyclable nature of the battery product is still often overlooked, as well as its suitability for second-life repurposing, making it an important technology for sustainability and climate change mitigation. Comprehensive recycling, including recovery and reuse is the potential option to obtain the maximum utilisation of spent power LIBs.
Prof. (Dr.) G. D. Yadav
National Science Chair (SERB/DST/GoI), Emeritus Professor of Eminence, Former Vice Chancellor & R.T. Mody Distinguished Professor, Tata Chemicals Darbari Seth Distinguished Professor of Leadership and Innovation, Institute of Chemical Technology, Mumbai
We are talking a lot about electric mobility in India in order to meet the demands of the Paris Agreement 2015 and the net zero goal. The high demand for electric vehicles (EVs) has led to a rapid increase in power lithium-ion battery (LIB) production, which has consequently led to an explosive increase in the number of spent power LIBs. Spent battery management consists of comprehensive recycling, including recovery and reuse to obtain the maximum utilisation of spent power LIBs which were introduced by Sony in 1991. LIBs are excellent for energy storage due to their high specific energy, high voltage and high reversibility compared to conventional lead-acid batteries. Because LIBs are an important component in EV, the current increase in demand for green transport has led to an increase in the production of LIBs, which in turn means massive production of minerals, such as Li mines.
The International Energy Agency (IEA) predicts an annual average growth rate of close to 30%; that is, the global EV stock (excluding two / three-wheelers) will continue to increase, expanding from ~8 million in 2019 to 50 million by 2025 and close to 140 million by 2030, in which China will be the major player.
Obviously, there will be a huge challenge in how to manage the waste of spent power LIBs. LIB failure typically happens after 3 - 10 years of service which will lead to large number of heavy metals and hazardous waste. Spent power LIBs can be viewed as ‘artificial minerals’ which calls for a reasonable recovery process to reduce the associated concerns and
Lithium-ion Batteries Available for Recycling, Worldwide (Tonnes)
forecast to grow at CAGR of
Figure 1: Worldwide trend for lithium-ion batteries. (Source: Circular Energy Storage)
realise resource conservation. The traditional mineral extraction processes, including pyrometallurgy and hydrometallurgy, have both been employed for the recovery of spent power LIBs. Additionally, a regeneration technique has also been developed, in which the spent cathode material is directly recycled without complex separation. Preceding
Figure 2: Battery recycling market. (Source: www.researchandmarkets.com)
these recovery processes, a pre-treatment method including deactivation and mechanical treatment is required to separate the components in spent power LIBs. Considering that spent power batteries still hold 70 - 80% of their nominal capacity, their reuse in other low-demand purposes has also been extensively developed.
EVs are normally classified into four main categories: Hybrid electric vehicle (HEV), fuel cell electric vehicle (FCEV), battery electric vehicles (BEV) and plug-in hybrid vehicles (PHEV). In 2020, the EV
second-life
remanufacturing/second-life
Figure 3: Second-life applications.
Hyperform® HPN® 900ei is a performance additive designed for use by thinwall injection molders in polypropylene homopolymers and mini-randoms.
PP modified with Hyperform HPN 900ei yields parts with lower haze, good optical attributes and an overall cleaner look. At the same time, it exhibits an excellent balance of physical properties with both good stiffness (flexural modulus) and impressive impact performance.
Such resin also provides for isotropic shrinkage (similar shrinkage in both directions, thereby reducing warpage) and less overall shrinkage, leading to higher-quality parts. The material’s higher heat deflection temperature, meanwhile, offers the improved heat resistance for those applica tions that require it.
The resin’s higher crystallization temperature enabled by the additive allows injection molders to cut their energy use by reducing cycle times and realizing faster over all processing. With the resulting energy savings certified by the independent agency UL (Under writer Laboratories), parts molded with the mate rial can bear the UL Environmental Claim Validation label. Displaying this UL label allows brand owners to promote their commitment to sustainability.
Hyperform HPN 900ei reduces the haze and the yellow ness index, yielding final parts that are cleaner, clearer and more transparent, which can further enhance sustainability by allowing for more inter-material replacement.
• MILLIKEN HYPERFORM HPN PRODUCTS ENABLE 5% TO 8% ENERGY SAVINGS WHEN USED AS A NUCLEATOR FOR PRODUCTION OF THIN-WALL INJECTION MOLDED CONTAINER LIDS OR SIMILAR POLYPROPYLENE PRODUCTS ULCOM/ECVindustry continued its growth trend, and 1.16 million EVs were sold in China, accounting for 39% of world sales, signaling that China has become one of the most important EV markets in the world. Thus, China will dominate the recycling and second-life battery market worth US$ 45 bn by 2030. During the period 2019 - 2030, 1,000 GWh of remanufactured and second-life batteries will be in the market. While portable electronics batteries will be the overall biggest sector lithium battery waste will come from, 75% of electric vehicle batterieseverything from e-scooters to buses, forklifts and trucks by 10 years’ time could be remanufactured into other vehicles or stationary energy storage systems. The worldwide trend for liion batteries is shown in Figure 1, whereas Figure 2 shows the worldwide recycling market.
The International Energy Agency (IEA) predicts an annual average growth rate of close to 30%; that is, the global EV stock (excluding two / threewheelers) will continue to increase, expanding from ~8 million in 2019 to 50 million by 2025 and close to 140 million by 2030, in which China will be the major player.
The highly recyclable nature of the battery product is still often overlooked, as well as its suitability for secondlife repurposing, making it an important technology for sustainability and climate change mitigation (Refer Figure 3).
According to Grand View Research, the international battery recycling market size was valued at USD 8.74 billion in 2016. Stringent government regulations and the growing end-use industries including transportation, consumer electronics and industrial applications are expected to raise the demand. The
To know more, please subscribe to PolyMeRs Communiqué at subscriptions@polymerscommunique.com
Q. Congratulations for the expansions at Baerlocher India. Could you provide the readers with a brief about Baerlocher India and an update on the upcoming expansion? Baerlocher made their first footprint in India in the late 1990s when they acquired a running unit of National Peroxide Ltd. Over the last twenty-five years, the facility has transformed from a small local manufacturing unit with a capacity of less than 5,000 TPA to a modern manufacturing site with four production plants producing over 50,000 TPA of products. We offer a diverse product range for all PVC as well as CPVC applications, producing various intermediates, lead-based and calcium-based solid one-pack PVC stabilisers as well as a range of liquid stabilisers.
An additional state-of-the-art 30,000 TPA manufacturing plant shall be dedicated entirely to producing calcium-based PVC stabilisers on the newly acquired 25 acres of land adjacent to the current facility. We should be placing the material from the new plant into the market by mid of 2023.
The focus is now on investing only in calcium-based stabiliser capacity whilst continuing to provide choice for convertors with traditional systems so as to enable their transition.
Q. Indian PVC pipe sector is in the process of transition to lead-free stabilisation. How does Baerlocher India look at this challenge? Lead-based stabilisers are the most rugged and efficient stabilisers and hence probably, except for the US, the entire world was on this specific stabilisation system for PVC processing. Slowly and steadily almost all these countries are changing to a lead-free system and India is no exception. The domestic PVC pipe sector will have to move to a lead-free stabilisation system, in a phased manner over the next few years.
“The focus is now on investing only in calciumbased stabiliser capacity whilst continuing to provide choice for convertors with traditional systems so as to enable their transition,” opines Vivek Kale, in dialogue with POLYMERS Communiqué.
The first and foremost challenge in this context was the availability of an alternative stabilisation system and, as mentioned earlier, Baerlocher has already taken steps to meet this challenge.
The next challenge was of the actual transition at the processors’ end, due to the difference in behaviour of the two stabilisation systems. On one hand, the processors were afraid that they would have to change the processing equipment; while on the other hand, quite a few of them believed it to be just a one-to-one replacement of the stabilisers.
In India, we have a very wide spectrum of processors in terms of processing capacity, number of machines, and age and type of machines. Developing a stabiliser system for such a kind of To know more, please subscribe to Polymers Communiqué at subscriptions@polymerscommunique.com
Vivek KaleSBU Head - PVC Additives, Baerlocher India Additives (P) Ltd., Mumbai
Figure 2: Before and After: Black polypropylene pellets made from recycled carpet fibres are purified and transformed into clear plastic resin through the solvent dissolutionprecipitation process.
(Source: https://www.nationalgeographic.com/ science/article/partner-content-innovationsin-recycling)
Of the many single plastic endof-life reprocessing technologies that have attracted attention, polypropylene (PP) has proven to be notoriously difficult. Less than 1% of PP is recycled back as of today. Read on, on how available technologies help make recovered PP as good as virgin...
Former Director, CSIR-NCL, Honorary Professor Emeritus and INSA Emeritus Scientist, Indian Institute of Science Education and Research (IISER), Pune
The plastics packaging industry is literally in the eye of the storm and is increasingly becoming a poster child of unsustainable consumption. Plastics packaging became ubiquitous in our everyday life due to its excellent functionalities, low weight, durability and low cost; and now, their end-of-life questions have come to haunt us. Brand owners and the packaging industry are bearing the brunt of a slew of new legislations and regulations that is likely to make the cost of compliance high for this segment of the industry.
New solutions are being examined, right from re-design of products for circularity; simplification of the packaging structure; processes for waste segregation at source; technology for sorting, aggregation and plastics identification; advanced recycling technologies for a single stream of plastics with minimum product degradation; compostable polymers as well as a host of chemical and biological recycling technologies. Many of these technologies are in either the proof-of-concept stage or, at best, at a demonstration level. Only very few of the technologies have been scaled up to levels to meet the demand for accumulating plastics waste in the environment.
Some of the technologies that were in commercial operation had to close down due to many unforeseen technical barriers (for example,
At Shreeji, it’s not about making a screw barrel, it’s about understanding your needs. Your applications drives our solutions, be it:
• The material used – German or MUSCO make
• Elaborate and stringent manufacturing processes followed
• The choice of screws – Nitrided, Bimetallic, HVOF coated, Hardened and customised; coupled with suitable barrels
It is not very easy to remove residual solvents from solid polymers.
Accomplishing this will require expensive devolatilisation steps to eliminate all traces of solvents from recovered polymers.
the VinyLoop PVC recycling process shut down its 10,000 TPA plant in 2018). Some of the key technical barriers have been non-availability of waste plastics in adequate purity, energy costs in reprocessing and the hazardous nature of waste streams produced in chemical recycling, which result in higher cost of recycled or reprocessed material compared to virgin resins. So, there is no significant market pull for high-quality recycled or reprocessed materials. It is worth noting that reprocessing of commingled plastics waste with nominal separation of plastics type, the kind practiced widely in India, is not considered as the most desirable end-of-use solution since it progressively degrades the property of the reprocessed material. Furthermore, ‘recycling’ of this type only postpones the problem, since at some point of time in the life-cycle of the material, there is still a need for a safe and acceptable resting place (grave).
Increasingly, globally (and in our country too) legislations have been enacted to ensure a percentage of recycled material in all plastic packaging. EU packaging levy on non-recycled packaging waste (Euro 0.80 per kg of plastic packaging waste that is not recycled), implemented since January, 2022. The EU directive that 55% of all packaging waste be recyclable by 2030 and requiring 25% post-consumer recycled materials in virgin products have spurred several studies on how to generate recycled materials (single plastic) with quality as close as possible to virgin plastic. Many FMCG companies have voluntarily disclosed targets for the use of recycled materials, both in food contact and other packaging applications with stiff targets to be accomplished by 2025 [1]. The
The process uses supercritical n-butane to dissolve PP at room temperature and after purification simply depressurising the vessel to remove n-butane as the gas leaves behind pure PP. The process involves no chemical reactions. The polymer characteristics are not significantly altered or degraded, and the recovered PP is as good as virgin PP with nearly identical properties
technology challenges across the entire value chain from the disposal of packaging by the consumer to its reprocessing to recover nearvirgin quality materials are complex and beset with many unsolved challenges. The next few years will be crucial and will determine which of the many solutions that are currently being explored will stand the test of technical and economic viability and which will fall into the valley of death. Several comprehensive reviews of the many challenges facing the industry and academia in the area of plastics packaging circularity have been recently published [2].
Of the many single plastic end-of-life reprocessing technologies that have attracted attention, polypropylene (PP) has proven to be notoriously difficult. Less than 1% of PP is recycled back to virgin quality PP as of today. PP is a thermally sensitive hydrocarbon polymer, prone to facile degradation during thermal reprocessing, and is present in diverse material types (homopolymers and copolymers, with widely varying MFIs on account of its wide applications). In addition, PP has several classes of additives such as colours, pigments, inorganic fillers, impact modifiers, antioxidants, anti-UV, fire retardants and clarifiers. Many of these attributes of PP interfere adversely in reprocessing. Thus, mechanically recycled PP is either grey or black, odourous, with a reduced MFI and cannot be used in food grade applications. While technology exists to lower the molecular weight of PP (example, visbreaking), there is no technology for increasing the molecular weight of PP, analogous to solid state processing of PET to increase viscosity. Consequently, there is a need for a process that can recover PP from waste streams, without molecular weight degradation, as well as purify it from the plethora of additives contained in them.
One such technology was developed by P&G in 2013 and was licensed to PureCycle Technologies LLC in 2015 [3]. Since then, PureCycle has spent close to USD 100 million in technology development and refinement over a ten-year effort and has announced that the first commercial plant with a capacity of 55,000 TPA at
POLYMERS CommuniquéWith our new engineered materials facility in Chennai, India we are bringing some of the most advanced polyamide chemistries to our customers. See how we’re advancing together at K 2022. ascendmaterials.com
Materials science has driven, and been driven by, the development of revolutionary technologies. Material science has been finding and crossing new frontiers of applications and unprecedented possibilities that we can classify as ‘speciality’ applications.
Probity Consultants, Delhi NCR
Material science is an interdisciplinary field of study and focuses on research, discovery, applications and replacement of materials to achieve higher performance and lower costs. This developed as a separate field of study in the 1940s and combined physics, chemistry, engineering and other areas of research. Materials science has driven, and been driven by, the development of revolutionary technologies such as rubbers, plastics, semiconductors and biomaterials, besides all other fields of industry and engineering.
The advent of plastics itself is a marvel achieved by material science research and study. Polymer science has made rapid strides and newer polymers, homopolymers, copolymers, terpolymers as well as new materials with enhanced performance have been created through focused research. New materials and performance plastics in thermosets and thermoplastics represent advances in material science in the polymer field. Plastics as an industry is rapidly transforming due to the development of speciality materials that offer exceptional performance. Besides the development of various basic polymers, newer materials have revolutionised the world.
For a long time, acrylic sheets have replaced glass in many applications owing to their high transparency and being virtually unbreakable. Acrylic, polyamide and polyester fibres replace many other fibres in apparel, furnishing, sport, defence, space and many other applications. Elastomers replace rubber and perform in advanced applications. Teflon is today used in applications ranging from domestic cooking pans and toasters to space and aeronautics components. Kevlar is another early and outstanding example that has moved from the punched tapes for NC equipment to bullet-proof body armour and myriad applications, and is one of the strongest materials known.
To know more, please subscribe to Polymers Communiqué at subscriptions@polymerscommunique.com
It’s been widely acknowledged that materials will be an important link for the next industrial revolution as well as in bringing innovative solutions.
As the world’s view on sustainability and green alternatives firms up, there will be increased demand for alternative and advanced materials that can provide environmentally sensitive solutions for the world’s needs. In this regard, an important contribution will be from synthetically made alternative materials as well as bio-based materials that will help the industry to move away from fossil fuel dependency.
For the world to be on the path of building a sustainable ecosystem based on the principles of a circular economy, next-generation materials will play a marketchanging role. In this regard, plastics as a material resource have huge potential to make a difference and be the material of choice for most of the industrial sectors.
Most of the world economies, including emerging and developing economies, have carbon neutrality as one of their core focuses and 2050 is the year, more or less, wherein the world wants to have achieved significant progress in the direction of becoming carbon neutral. For the world to be on the path of building a sustainable ecosystem based on the principles of a circular economy, nextgeneration materials will play a market-changing role. In this regard, plastics as a material resource have huge potential to make a difference and be the material of choice for most of the industrial sectors. Since plastics belong to the petroleum family, there are inbuilt risks it has from a fossil fuel consumption perspective. However, research and innovation in this space are at a highly advanced stage and multi-dimensional solutions are now becoming available; be it recycling innovations, bio-based possibilities, manufacturing process streamlining or, finally, chemical recycling that will reduce the dependence on crude directly and make the entire product value chain much greener. It’s the interdependency of various science streams and collaboration of multiple stream experts that has made synthetic materials production possible and has become an integral part of all industries’ sustainable business existence.
There are many synthetic innovations available that have the potential to make a great difference in making the world a better place.
Chintan R. Joshi Kaushalya Reputation and Brand Consultancy, MumbaiFirst among this scientific beauty is the self-healing polymers. As the name suggests, researchers have mimicked the natural concept in creating polymers that will heal themselves and recreate themselves after wear and tear. This will
To know more, please subscribe to Polymers Communiqué at subscriptions@polymerscommunique.com
“Cosmo First is all poised to enhance its abilities and capacities across its business of BOPET, BOPP and CPP,” updates Pankaj Poddar, in dialogue with POLYMERS Communiqué.
The Indian packaging market is anticipated to expand by 27% yearly to USD 205 billion in 2025. With increasing demands for consumer durables during the pandemic, there is an increasing scope for production and innovation of packaging products.
Pankaj Poddar Group CEO, Cosmo First Ltd., New DelhiSponsored by
Q. To kickstart, what prompted the change of name from Cosmo Films to Cosmo First?
Cosmo has always strived to be ahead, which has helped us build relationships and create growth for all of our stakeholders. Until a few years back, we were more focused towards manufacturing products for packaging and lamination. We have strategically expanded into three different verticals, with more on the way. The entities include Cosmo Films, Cosmo Speciality Chemicals, Zigly (a pet care company), are all part of Cosmo First Ltd., the holding company. Through its many operations, the group has a broad product portfolio that ranges from B2B to B2C and serves a variety of customers across industries. Cosmo First is perfectly aligned to our identity as an organisation with businesses in multiple sectors.
Q. With many significant initiatives in the films business, that also includes the world’s largest BOPP line, how does Cosmo Films plan to capitalise on this investment over the next two years?
With several expansions and diversifications in different verticals and sectors, we are also expanding our films business to achieve new heights. A new BOPET film line will be commissioned by the 2nd quarter of 2022, and this will help the company expand its bandwidth into speciality BOPET films as well.
Cosmo Films has also announced the commissioning of the world’s largest BOPP film production line at Aurangabad, India, with an annual rated capacity of 67,000 metric tonnes. The BOPP line will require investment of about Rs. 350 crore (USD 47.5 million). This will greatly help the company to ramp up the production and sales for its BOPP-based speciality films.
We are also commissioning a line for cast polypropylene with an investment of about Rs. 140 crore in Aurangabad. The production line which is to be funded through internal accruals and debts is expected to commence commercial production in the next two years. The new production line for cast polypropylene (CPP) films in Aurangabad will have a rated annual capacity of 25,000 metric tonnes. In Aurangabad, the new production line will result in the addition of 50 new direct jobs and numerous indirect jobs.
Cosmo’s strategic investments are aimed towards
capitalising the change in packaging industry trends. Moreover, as an environment conscious business, Cosmo’s values are aligned towards pioneering this shift for sustainable packaging.
Q. In continuation, with recyclability pushing the demand of BOPP films, how do you see your capacities change from where it is today? What is the current capacity utilisation?
Recyclability has become the industry norm when it comes to the packaging sector. The BOPP films used for packaging are made from polypropylene that provide for sustainable packaging without compromising on aesthetics and performance of the pack. Post our expansion slated to be launched in FY 2025, we will reach an annual production capacity of 2.6 lakh tonnes. Our current capacity remains fully utilised, but for any maintenance shutdowns or rare occasions where the line is shut for any specific objective.
Q. As regards speciality films, the vision of Cosmo that you wish to share?
Cosmo First has always believed in running enterprises of the highest caliber that enrich people’s lives, with our principles serving as the institution’s foundation. Cosmo First’s aim is to develop cost-effective solutions in packaging and lamination, polymers, textile chemicals, masterbatches, pet care and other industries. We aim to produce cutting-edge and high-quality goods and services throughout Cosmo’s several verticals by focusing on people and the needs of our customers. This is a step forward in our ambition to pivot our staff for greater growth and better serve our clients. At its core, Cosmo has always been a leader in ground-breaking inventions that improve lives.
Q. “India going global as regards production of speciality films.” Your thoughts on this statement.
The Indian packaging market is anticipated to expand by 27% yearly to USD 205 billion in 2025.
While Cosmo Films exports to over 80 countries, the company is diligently working to establish India as a significant hub for packaging materials, in addition to placing the country on the supply chain map for packaging. There is robust demand for packaging within and outside the country. With increasing demands for consumer durables
during the pandemic, there is an increasing scope for production and innovation of packaging products.
Q. Cosmo has been a strong believer in ‘branding’. What approaches do you embark on?
As a four-decade-old global business group with entities such as Cosmo Films, Cosmo Speciality Chemicals, Zigly and Cosmo Foundation, we have always recognised the importance of building quality and credibility for our products. Cosmo has always been at the forefront of ground-breaking ideas which has aided in the brand’s expansion. We have taken great satisfaction in our capacity to offer industry-first specialised solutions in the fields of packaging, laminating and labelling applications throughout our journey. In order to lead these hitherto fragmented industries, we have made inspiring diversifications into speciality chemicals, personal care and direct-to-consumer retail. With unity and trust, we move forward with a people-first approach. Cosmo First has been built on quality, innovation and integrity. Through our values, we provide the best for our customers.
Q. How do you address the issue of sudden spurts in material and freight costs? What was your contingency to address the same?
There is still a lot of cooling down to happen for raw material prices and freight costs. Making accurate predictions has been a little difficult due to the unprecedented occurrences that have affected the global economy over the past two years. However, in light of how we’ve previously performed, Cosmo has succeeded and generated good earnings every quarter. Despite difficulties, Cosmo First is nevertheless upbeat about future demand and anticipates higher profit margins as a result of continuous demand and falling raw material prices. Over the coming quarters, the prices will decrease. It
A new BOPET film line will be commissioned by the 2nd quarter of 2022, and this will help the company expand its bandwidth into speciality BOPET films.
Cosmo Films has announced the commissioning of the world’s largest BOPP film production line at Aurangabad, India, with an annual rated capacity of 67,000 metric tonnes. The BOPP line will require investment of about Rs. 350 crore (USD 47.5 million).
We are also commissioning a line for cast polypropylene with an investment of about Rs. 140 crore in Aurangabad and is expected to commence commercial production in the next two years.
will assist us in freeing up a significant amount of trapped working capital.
Q. Your take on AI and IoT gaining popularity across production lines and their advantages over conventional floor management.
Digitisation has been uplifting the manufacturing landscape. Companies are looking to transform their ecosystems through innovative technology and the internet of things (IoT). This is a step towards making traditional factories into smart spaces. IoT in manufacturing is driving unprecedented disruption and can help make factories safer for frontline workers, increase productivity and efficiency.
Artificial intelligence offers an advanced level of analytics to enterprises that they can use to evaluate the performance of their individual components. The AI-based data analytics is much more effective than the traditional systems and can, hence, be used to boost the overall efficiency of a facility and elevate the production rate. Also, artificial
intelligence and machine learning are powerful tools to minimise the consumption of resources and energy in the manufacturing industry by continuous improvement in the present work process.
Some of the IoT and AI advantages include:
l
Complete autonomous environment.
l Improved overall efficiency.
l Production forecasting.
l Predictive maintenance.
l Quality management.
Q. How do you see the future of the pet care market? How global is your vision for this segment?
India has over 30 million pets, making it one of the fastest-growing sectors. The pet-care market is anticipated to increase to about Rs. 10,000 crore over the next three years. Cosmo sees this as a huge market opportunity and plans to take advantage of it via their D2C platform in addition to offline experience centres. We have already opened five experience centres in the Delhi NCR region and are looking forward to expanding in other metropolitan cities in our country. Our goal at Zigly is to offer a one-stop solution for all things pertaining to pets and pet care. We aim to be the largest pet care company in the next 3 years. In the upcoming 12 to 13 months, we plan to open 15 to 16 more stores, while digital will continue to grow and bring Cosmo presence across the country.
Q. A failure that taught you the most...
Failures are part of the process and I believe it is an integral part to grow and learn. Having experienced failure pushes you to go after your dreams. It teaches you to keep trying and trying until you get it right. This is what eventually leads to success. Like Winston Churchill once said, success is moving from failure to failure without loss of enthusiasm.
Sponsored by
“While there are no challenges in terms of growth and opportunities in the piping industry, yet we would like to emphasise here that all manufacturers should stick with the quality of piping being supplied to the market and that no sub-standard materials are being produced or supplied to the market which can give a negative impact to the product category at large,” expresses Kairav Engineer, in dialogue with POLYMERS Communiqué.Kairav Engineer
Vice President - Business Development, Astral Ltd., Ahmedabad
Q. From aiming to cater to the plumbing and drainage systems to being the pioneers and establishing a brand in the real estate segment; some key turning points that you wish to share in your journey this far.
It has been an exciting journey. Right from introducing the CPVC piping system in India to launching many innovative products in the category, Astral has stood at the forefront of the category. We have many industry firsts in our name and have tried to improve the plumbing standards in the country. Launching CPVC Pro, thereafter low-noise Silencio and then launching anti-viral water tanks have been major milestones. Astral now is not just a pipe company, but has ventured out into adhesives, bathware, water tanks and paints as well. It has been a remarkable growth story.
Q. The pipe industry has evolved over the years with a variety of applications and materials that are specific to the applications. Your views on the same and how do you envisage the coming years for the pipe industry?
The piping industry has come a long way and has witnessed many improvements and changes. There are many materials and applications specific to our country and the market. For this, Astral has done considerable value engineering in terms of product designs and manufacturing techniques. Many product designs are improved upon by considering specific feedback from the market and the fraternity. Also, in coming years, the pipes category will witness many changes. There are many aspects where there will be new technology applications and many products will improve considerably.
The machines conceptualised, designed and manufactured by Vihan play a crucial role in the manufacturing of the high-quality PVC pipes supplied by Astral. Vihan machines are robust and are designed to accomplish the goal of producing quality and accurate end products.
There are no challenges in terms of growth and opportunities, yet we would like to emphasise that all manufacturers have to stick with the quality of piping being supplied to the market and no sub-standard materials are being produced or supplied to the market which can give a negative impact to the product category at large.
Q. The real estate business is showing strong signs of revival after the lull period experienced during the pandemic. What are your projections as regards your business trends over the next 2 - 3 years?
We hope to grow at a decent pace. In the coming 2 - 3 years, we will be able to widen our portfolio in terms of building materials. We will be able to offer consumers many building material products under one roof. This will help us grow and consolidate our position in the market.
Q. What are your current capacities? Any new plants are in the pipeline?
Our current capacities for the piping segment including the tank business is around 2,75,000 MT per annum. This is spread across 8 manufacturing plants PAN India. Our east plant in the state of Odisha has just started and, at present, we would like to stabilise the same before expanding with any new plants.
Q. What new products in the piping business can the market expect from Astral?
In the piping business, we have just launched the PP mineral-filled pipes with density of 1.4 gm/cc - named as Astral DrainPro - used for non-pressure drainage and sewerage applications. These pipes are an ideal replacement for PVC pipes where some bottlenecks of PVC pipes like temperature resistance and chemical resistance are observed. Apart from this, we are going to add
We have just launched the PP mineral-filled pipes with density of 1.4 gm/cc used for non-pressure drainage and sewerage applications. These pipes are an ideal replacement for PVC pipes where some bottlenecks of PVC pipes like temperature resistance and chemical resistance are observed.
some more products to our existing product range of CPVC, uPVC and other piping categories, including speciality products like valves and flow control products.
Apart from piping, we have just launched our faucet and sanitaryware products. Market will see a range of world-class premium products to affordable economy range products in this category from the house of Astral.
Q. The contribution of Vihan in delivering quality products to your end customers; the key aspects that you wish to highlight of Vihan being your dependable supplier.
The machines conceptualised, designed and manufactured by Vihan play a crucial role in the manufacturing of the high-quality PVC pipes supplied by Astral. Vihan machines are robust and are designed to accomplish the goal of producing quality and accurate end products.
Q. Your impression about Vihan when it comes to delivering the most innovative solutions and their prowess in applying technology for providing you solutions to suit your needs. Any example?
The recent emphasis of Vihan team to dispense with ‘hydro-pneumatic systems’ is a praiseworthy initiative. It has brought in a paradigm shift in managing the process and control parameters of the socketing process. The servo-controlled technology also offers high productivity with low power consumption.
Q. How do you see your adhesives business today? Any unrelated market segment that excites you?
The adhesives segment has countless opportunities. There are a few organised players with nationwide presence. We have made considerable inroads into the same, but we think we have miles to go. We are currently in the phase of setting up our new state-of-the-art facility in Dahej, Gujarat and also strategising our distribution network.
Q. You have been one of the early users of most Vihan innovations. How do you look back at the relationship you share?
Well, it’s close to a 2-decade long association with Vihan’s unflinching commitment to continuous product development and rendering total solutions for automation. The products supplied by Vihan from its facility in Ahmedabad are comparable to any world-class European supplier.
Q. As an organisation, you have placed a lot of emphasis on brand building and visibility. What is your message to the industry as regards investing in branding?
Brand building is an essential part of the business. We have scaled up the matrix and now are into ‘the consideration set’ of the buying target group. Even we can say that our brand now is most likely to be bought from the options available. So, it’s not only just top-of-mind awareness, we have evolved as a brand that tends to become a recommended and trusted brand.
“The current Indian government has provided tremendous support to our industry in terms of subsidies and grants and the government is providing us with the right platform to become as established as some of the biggest toy industries in countries like China and Japan. Even though the competition is really stiff, India is developing well in specific areas like educational toys and we are hopeful to become a force to reckon with very soon,” opines Gaurav Mirchandani, in dialogue with POLYMERS Communiqué.
Q. What, according to you, are the three most important attributes that have contributed to the exponential growth of your company in such a short span of time? Firstly, we operate in a niche market and our topmost priority is to give the best quality productsour toys to our customers - the children. Secondly, we strive to bring innovation and interactive nature into the toys. We have been very clear right from the beginning that we want to provide toys so that children can engage with and do some kind of activity like solving a puzzle etc. rather than simply playing with them. This encourages physical and mental stimulation in children. And the third most important attribute is the support of the Indian government. Before we got involved in this business, most of the toys were imported from China. However, since PM Narendra Modi has taken charge, the government has developed extremely profitable policies to support the Indian toy industry. The import duty, which was earlier just 5 per cent, has now been increased to 60 per cent.
This has given a real boost to the home toy industry as manufacturers now feel more encouraged to produce toys in India itself rather than importing them from other countries. So, a combination of these three factors has resulted in our success.
Q. From food packaging to making toys, what made this shift happen? Actually, it is the other way around. We were first in the toys business and then we introduced our own confectionery brand. We started our toy factory back in 2016-17, and later we started with Hoppin, our brand of confectionaries.
Q. How do you see the current trends in the Indian toy market? What are the top three reasons for the toy industry not getting its due in terms of development and infrastructural investment?
The toy industry is a trillion-dollar industry, and yet, 95 per cent of the toys come from one city in China named Shantou and the infrastructure there is
The toy industry is a trillion-dollar industry, and yet, 95 per cent of the toys come from one city in China. The sheer varieties and categories of toys that are produced make it a unique industry, posing several challenges.
Gaurav Mirchandani Director, Candytoy Corporate Pvt. Ltd., Indore
tremendous. It is really vast in terms of the kind of products it manufactures. The sheer varieties and categories of toys that are produced - Barbie dolls, electronic toys, promotional toys etc.make it a unique industry, posing several challenges.
However, the Indian toy industry has done tremendously well in a very short span of time. And the credit goes to the Indian government which has provided amazing support in terms of policies and subsidies. There are definite challenges ahead of the Indian toy industry like if we need electronic elements in the manufacturing of toys, we still depend on importing those items from countries like Japan, Taiwan and China. But I am hopeful that we will be able to overcome such challenges very soon. Currently, the Indian toy industry is doing really well in terms of growth.
To reduce our carbon footprint, one of the main things that we have adapted is the use of solar energy. Our plant is laden with solar panels and is well used across the plant.
the chocolate sector, we are bringing candy and toys together for the Indian market.
Q. What is the importance of facets like the quality and treatment of feedstock for manufacturing toys?
diversifying into a different vertical or launching your own toy brand?
Since we are into B2B business, we don’t want to venture into something that our clients are already doing. For example, if we are supplying to Kinder Joy, we don’t want to get into the chocolate or ‘namkeen’ sector. However, we have got into our own confectionary brand where we are making candy toys. These are attractive little toys attached to candy. So, we are doing something similar to what the brands like M&M’S in the USA and Kinder Joy in Europe are
The single most important facet of this business, even before the price, is the safety and hygiene of our kids. And we make no compromises in this aspect. We ensure that whichever polymer we use in our toys is completely food grade, certified by the Bureau of Indian Standards (BIS) and EN71 for export to the US. We understand that children have the tendency of putting toys in their mouth. Whether it is candy toys, promotional toys or freebies, we ensure that they are absolutely safe
know more, please subscribe to
“The Indian market has changed quite drastically in the last decade. Today, Indian customers demand world-class products as there is more exposure and availability. They expect the same printing quality and production output from an Indian machine that a European counterpart provides. While this is a challenge for the Indian manufacturers, it also gives us a chance to get better at our products,” shares Kaku Kohli, in dialogue with POLYMERS Communiqué.
Q. From paper to plastics, manual to stateof-the-art technology and normal to super high speed, you have done it all during your majestic journey of fifty years. Which, according to you, have been the top three defining moments of this journey?
Over the last fifty years, we have faced several challenges, and yet, have managed to overcome them all with a lot of resolve, grit and determination. It has been a successful and satisfying journey for us and the fact that we have managed to accomplish so much on our own is a matter of pride for us. But what makes this success even more worthwhile is that our efforts and milestones have been acknowledged, appreciated and praised by all top European manufacturers. It shows that we have been
making the right efforts in the right direction and it also motivates us to continue doing well.
I also received the honour of being invited by the European Rotogravure Association (ERA) to speak on a topic that I am really passionate about –‘Gravure in India’ during their annual conference held in Italy this year. This reinforced the fact that our brand has made a positive impact on the industry and it has made a difference across the globe. Lastly, we were awarded a Silver Trophy by the Engineering Export Promotion Council (EEPC), India for being the top Indian exporter, yet another feather in our hat that I am really proud of.
Q. Which is the product that you consider to be your flagship product and why? Undoubtedly, it would be our new gravure press, ‘Thea-9one8’. It took us more than two years of dedicated research and development before we could come up with the latest design. And it has received an amazing response from the industry.
Through continuous research and development and adaptation of the latest electronics and automation, Indian machines can deliver almost the same results as any European machine. This shows that the Indian market and manufacturers have come a long way, which is a great sign for our local market.
Q. How does a change in substrate affect the quality or method of printing? Please walk us through the built-in features of the press that take care of this aspect. Practically speaking, it is not possible to change
To know more, please subscribe to Polymers Communiqué at subscriptions@polymerscommunique.com
More the layers, the bigger is the challenge. The invention of newer grades makes it even more challenging and a lot more is needed than just a mathematical calculation on cost saving when you want to process your magical film formulations. That is the key point and SCD is the way to go!
Since the late 1990s, there have been efforts worldwide to go for more and more layers on film extrusion processes to leverage advantages for end product properties and raw material cost savings. The trend of the market had been to shift from 3 layers to 5 layers which has become a common phenomenon in recent times. Attention to shifting from 5 layers to 7 layers and 7 layers to 9 layers is very interesting for specific end applications and film structures. With increasing interest in sustainable packaging using recycled material and still achieving the required end application property has become a major challenge. For both the
Rajesh Sonar General ManagerSales and Marketing, Mamata Machinery Pvt. Ltd., Ahmedabad
above challenges, the major bottleneck had been the processing challenges arising primarily due to multifold increase of material residence time for the innermost and outermost layer in the multilayer die head (3 - 5, 5 - 7, 7 - 9 and 9 - 11). Challenges include flexibility to use a variety of polymers, control of melt temperature and, therefore, viscosity of each layer, possibility to process minimum layer ratio for different polymers side by side and achieve high outputs etc. More the layers, the bigger is the challenge.
So why is it difficult to go for more layers? The primary reason is increasing the wetted surface area and longer material residence time in conventional die heads as you go for more and more layers. An increase in residence time increases the melt temperature and excessive stretching of polymers which are at different viscosities. The second important bottleneck as a result of this primary limitation is the increased possibility of polymer degradation / oxidation while processing itself. The flexible packaging industry being an ever-evolving industry to address issues, processors overcome the bottlenecks by either using different polymers or using their experiences to set up process parameters. All this leads to
change of film formulations for a given end property requirement and the ability to handle process requirements on a blown film line. Eventually, it becomes a forte of knowledge and experience of every processor which itself emerges as a limitation often to organisations.
Mamata Machinery and its ex-JV partner, Brampton Engineering, Canada worked together from 1997 to 2012 introducing the technology of ‘Stackable Coextrusion Die’ (SCD) in India.
The invention of newer grades makes it more challenging since molecular weight distribution and polymer rheology are very different for every grade. This is leading to a scenario where each layer is very different from the adjacent layer in terms of polymer combination and process behaviour. Therefore, each layer has different flow behaviour, viscosity, response to temperature and shear rate. The biggest challenge for a processor is to be able to have predictive control over these parameters while processing.
One of the examples to take for ease of understanding is what happens when you run materials like nylon and a sealant layer side by side? Nylon needs a temperature of 250°C, while the sealant layer needs 200°C as the set temperature. While running these side by side, the challenge is to control the melt temperature and, therefore, prevent degradationnot in short runs, but over longer runs.
With increasing interest in sustainable packaging using recycled material and still achieving the required end application property has become a major challenge. Challenges include flexibility to use a variety of polymers, control of melt temperature and, therefore, viscosity of each layer, possibility to process minimum layer ratio for different polymers side by side and achieve high outputs etc.
As most processors experience, either regular flushing or cleaning of the dies is always needed. All this results in higher operating costs and lower OEE.
Streamlined Co-extrusion Die
(SCD) head is the solution to overcome these processing challenges (Refer Figure 1).
SCD has plenty of unique propositions as listed here:
l Direct extruder connection to the die stack for individual layers reduces melt path substantially, resulting in lower wetted surface. No feed block is required and, therefore, all process limitations arising out of a feed block are absolutely eliminated.
l Every die stack is insulated by an air gap and/or insulation between stacks. Hence, significant temperature isolation of each process layer is achieved. A huge advantage is that temperaturesensitive polymers and/or thinner layers can be easily processed with great ease, side by side as compared to conventional die heads. Polymer degradation possibilities are reduced from 50% to 100%
Figure 2: 7-layer barrier blown film extrusion line.
depending upon the polymer type and formulations.
l Lower wetted surface helps in quicker cleaning of dies when needed. Reduced flushing time and material needed, coupled with quicker changeovers are possible.
l For the needs of processing thinner layers, it is possible to optimise each die stack’s flow channels resulting in having the desired control on each layer, independently.
l It performs far too well for processing thinner and thicker layers side by side. This is useful not only to run barrier films, but also for POD films with functional polymers to achieve specific layer properties.
l It is possible to run POD film with low SIT (seal initiation temperature) and, at the same time, with required surface properties. SCD gives a huge advantage to process polymers at required process temperatures and
create that difference of processing temperatures needed.
l It is easier to handle the die for cleaning and flushing.
l Changeovers are much quicker which is a very important advantage for processors who have shorter runs.
l For any number of layers (5 or 7 or 9), the die diameter can be the same. Die diameter defines the output capabilities of the line. With SCD, less emphasis is required to invest in very expensive air rings to achieve higher outputs with smaller die heads. Optimising capex is possible for a given required output target.
l Unique advantage is to upgrade the line from 5 layers to 7 layers and 7 layers to 9 layers just by adding die stacks and extruders. This is going to be a major benefit for the industry as it strives to
go from 5 layers to 7 layers and 7 layers to 9 layers; at much lower additional investments, compared to multilayer blown film lines that use conventional dies. A big boon for the processor should be with changing market scenarios, the line will not go redundant.
In addition to the SCD’s contribution to processing excellence, another key contributor to processability is the technology of extruders. The ability to handle today’s showstoppers mLLDPE, LLDPE (octane and butane grades), LDPE, nylons, EVOH etc. can perform better on extruders with smooth bore barrels.
When two capabilities - SCD and extruders with smooth bore barrelsare combined, the processors can be sure of processing with optimum melt temperature and accurate input
material being delivered to the die head. This can indeed do wonders.
If processing limitations are taken care of, there is a lot more possible with reduction of the cost of material which has been of great interest in the flexible packaging industry - to work on input raw material cost. The reason is very simple that depending on the location, polymers account for more than 82% of the total product cost (Refer Figure 3). Hence, processors always find it more rewarding to work on reduction of raw material costs. If we see a typical formulation in Tables 1 and 2, savings on raw material can be upto INR 3,200 per tonne (i.e. USD 40 per tonne). In case of barrier films, this savings is substantially higher as the barrier layers should be processed as per required barrier properties (mostly as thin as possible) and the polymers are much more expensive.
Implementing SCD, the unique advantage is to upgrade the line from 5 to 7 to 9 layers just by adding die stacks and extruders. This is going to be a major benefit for the industry at much lower additional investments, compared to multilayer blown film lines that use conventional dies. A big boon for the processor should be with changing market scenarios, the line will not go redundant.
Cost saving can be extremely rewarding when someone is using expensive functional polymers and are focused on downgauging with properties kept intact. Using recycled material or less expensive polymers is an option that is increasingly becoming very interesting. For special purpose films, reducing use of special additives can save when you use it judiciously by splitting functional layers and body layers. Instances where specific polymers or compounds are
essential for processing it on specific equipment is a completely different scenario. So, a lot more is needed than just a mathematical calculation on cost saving when you want to process your magical film formulations.
That is the key point and SCD is the way to go!
Mamata Machinery Pvt. Ltd. (Mamata) is a globally leading manufacturer and Exporter of extrusion blown film lines, converting machines and end-of-line packaging machines. With an installed base of nearly 5,000+ machines in more than 88+ countries, Mamata enjoys close customer relationships across the globe. Mamata operates from Ahmedabad, India with a facility spread over 4,50,000 sq. ft. area with in-house electronics department, a fully equipped paint shop, in-house demonstration centre and installed capacity to make over 250 machines a year. In the USA, Mamata operates from two locations and caters to the needs of both, converting and packaging industries. Our Montgomery, IL facility is a pre-sales and after-sales service centre for converting machines. Our Bradenton, FL facility focuses on the design and manufacture of state-ofthe-art horizontal form, fill and seal pouching machines and multilane sachet packaging machines. Both the facilities are also showrooms of Mamata Machines for North, Central and South America.
write to rajesh.sonar@mamata.com
It was in 1995 that Prakash made his foray into business and today leads the Suraj Group with over 5,000 team members. The retro picture also highlights the ‘straight in the eye’ look!
Change being the only constant, we thought it would be wonderful to capture this and freeze ‘time’. We associate with the ‘current look’ of our industry colleagues and would it not be exciting to know of their persona, decades ago. That’s what we did, had them dig deep into their archives and share this just for your ‘read’... or should we say ‘see’! A visual delight!
An uncanny resemblance then and now, Haresh, today a Partner at Total Packaging Services loves to travel and explore new places.
With an astute vision that both his pictures clearly indicate, Shripal started Uma Group in 1988 with a desire to make it (Uma Polymers) amongst the top 3 flexible packaging companies in India.
Truly retro, the 1984 picture at Shimla clearly carries the ‘Pradip look’ which is evident in his persona even today. Today, he is responsible for the business at Kumar and has contributed immensely to the growth of the plastics industry.
Graduating in 1987, Parag started his own business in the even then-growing plastics and rubber industry. He has come a long way (a satisfied look which his picture clearly highlights) from his initial manufacturing of a unique polymerless masterbatch that was compatible with any plastic or rubber product.
“The last few years have been great for the Indian manufacturing economy, which has seen tremendous yearon-year growth, thanks to initiatives like ‘AatmaNirbhar Bharat’, ‘Make in India’ and many more by the Indian government. Such schemes have encouraged the Indian players not only to manufacture products locally (rather than importing them from foreign markets), but also to boost Indian exports to various countries globally,” opines Amit V. Pendse, in dialogue with POLYMERS Communiqué.
Electronica Group has been in the business of making metal cutting machines for the last more than 50 years and it has been an extremely rewarding journey. Many customers were engaged then and are still engaged in mould manufacturing for the plastic injection moulding process. As an obvious step, Electronica Group then diverted into manufacturing plastic injection moulding machines way back in 1992-93. We faced several challenges in the beginning in our pursuit to develop and manufacture quality machines and we were able to overcome them with our dedication, grit and determination.
Like most beginnings, we also had a slow start. Our real journey and progress began after 1997-98. It was at this stage that we actually started establishing ourselves. We made a lot of changes in our machine designs and the best part is that everything was done indigenously.
We made it a practice of upgrading and innovating our machines regularly. Since then, we have kept on introducing a range and type of new machine series and models over the years. We started with the toggle-type machines, which we continue to manufacture to date. Later, we introduced the ram-type machines and, a few years back, we introduced the latest generation twoplaten injection moulding machines as well.
Q. Please share some more insights into the features of the 5-point toggle-type machines and the advantages they will bring to the users?
The 5-point toggle-type machines are very energy-efficient by virtue of their design itself and produce high-quality, consistent products. When we started, there was only one company making plastic injection moulding machines,
but those were ram-type machines and nobody else was manufacturing toggle-type machines. However, toggletype machines, especially the 5-point toggle-type, that we started with, provide a 16 - 17 per cent energy savings over the ram-type machines. What makes toggle-type machines a dominant player in the market is their ability to exert uniform and positive clamping force over the entire mould area and provide ideal mould movement dynamics during mould opening and closing functions.
Q. With your range of injection moulding machines, is there a sub-sector that really excites you as regards the growth potential in the coming years?
The last few years have been great for the Indian manufacturing economy, which has seen tremendous yearon-year growth. Thanks to the great
initiatives like ‘AatmaNirbhar Bharat’, ‘Make in India’ and many more by the Indian government. Such schemes have encouraged the Indian players not only to manufacture products locally (rather than importing them from foreign markets), but also to boost Indian exports to various countries globally.
One of the prime examples of this change is the Indian toy industry. Earlier, a major portion of the toys sold in India was imported, which is now changing very fast as a lot of conventional jobwork moulding operations are getting into specialised toy manufacturing. Newer manufacturing hubs are being set-up and developed and we are getting good response and support from this industry.
To know more, please subscribe to Polymers Communiqué at subscriptions@polymerscommunique.com
A. Dayanand Reddy Managing Director, Vasantha Tool Crafts Pvt. Ltd., HyderabadGROWTH
“We find the medical segment to be the most demanding as a failure of the product can have far-reaching consequences; this is a challenge that excites tooling,” explains A. Dayanand Reddy, in dialogue with POLYMERS Communiqué.
Q. A smart woodcutter invests more time in sharpening his axe before felling a tree; how true and synonymous is this proverb when it comes to mould designing and superior execution? Very true and apt! We always say that every extra hour spent in reviewing the final design with the CFT team, saves 10 hours of manufacturing time later!
Q. With respect to the current market trends, which is the segment of your business that shall be contributing the most to your growth, considering a span of 2 - 3 years?
We continue to focus on the FMCG segment, but more on niche markets. At the same time, we will also start focusing more on the medical and pharmaceutical sectors, though right now we do some business for these sectors.
A lot of demand comes from the customers on lower cycle times, longer life and faster schedules based on the application; case to case, one must apply
enough importance for the steels to be used, heat treatment and other special coatings.
Q. As per current market trends, which is the market segment that you find the most demanding in terms of price, precision and delivery. What is the reason?
To know more, please subscribe to Polymers Communiqué at subscriptions@polymerscommunique.com
Q. How do you see the medium-term growth prospects for plastics auxiliary equipment and automation solutions in your markets and which industry segment is looking most potential?
Consumption of plastics continues to increase by double-digit in infrastructure, automotive and transport, electrical and electronics, consumer goods, healthcare and packaging industries. Auxiliary equipment and process automation solutions play a critical role in sustainable production systems of plastics components and assemblies by lowering energy consumption, while providing consistent quality and improved process efficiency. We are experiencing strong demand for our products and services from our existing and new customers. Our customers now have full appreciation for the catalyser role played by auxiliary equipment for high-efficiency plastic product manufacturing. We, at Aerodry, have upgraded our technologies and production capacity to meet up with the present and future demand from our customers.
Q. What are the major technological trends of automation in plastics auxiliaries in the
next 3 - 5 years and how is Aerodry planning to respond to be a preferred vendor? As awareness in the market is increasing, more and more small and medium companies are adapting to automation solutions so as to enhance productivity with zero defects. Customers are opting to use material storage and central conveying, drying and dehumidification systems, gravimetric dosing and mixing solutions, loss in weight (kg/metre) and GSM control to tie plastic moulding machines and raw materials together to build up reliable and high-efficiency production lines. We see this trend to further grow as our customers face demand for high-quality reliable production at optimum costs. We are further modernising and expanding our manufacturing facility supported by cutting-edge, superior European technologies to meet the increasing demand while keeping cost competitiveness in mind.
Q. Automation solution providers have a big task of convincing customers on the basis of
To know more, please subscribe to
at
“Auxiliary equipment and process automation solutions play a critical role in sustainable production systems of plastics components and assemblies by lowering energy consumption, while providing consistent quality and improved process efficiency,” suggests Arun Pundir, in dialogue with
Communiqué.
AI-enabled IoT is revolutionising the plastics processing industry, allowing for intelligent and smart manufacturing with a focus to reduce waste material produced and improve processes by making it easier to collect and analyse data, strengthen weaknesses and mitigate problems.
Arun Pundir Director & CEO, Aerodry Plastics Automation Pvt. Ltd., Noida
Varun Ramsisaria, Director, Viva Petrochemical LLP, Tamil Nadu
“India is a price-sensitive market and the changes in technology were accepted at a slower pace; things are changing rapidly now as the industry is becoming more tech-savvy. With younger and more tech-aware entrepreneurs entering the market, we are witnessing a slow, but steady shift in the mindset and that is sure to make a huge difference,” opines Varun Ramsisaria, in dialogue with POLYMERS Communiqué.
Q. The organisation was founded by experts from the polymer industry. Please state the most important and impactful milestones in the progress of the company this far.
To start with, there are two products that we manufacture. One is under Virgo Polymer India Ltd. (VPIL) which produces FIBC (jumbo bags) and the second is Viva Tech which provides eco-solutions. As far as Viva Tech and its eco-solutions are concerned, it’s still at a very nascent stage with energy solutions coming in the form of infrared heaters and IE5 motors. It started with the idea of providing energy-saving products to the polymer industry that was earlier using only ceramic heaters in the heating process of the extrusion barrel. These ceramic heaters required stronger insulation and still, there was a huge amount of energy loss in the process. So, when you heat the barrel with a ceramic heater, it takes a much longer time to heat it as compared to an infrared heater. We are amongst the first ones to introduce infrared heaters that are completely insulated from the inside.
As regards FIBC, India is the largest manufacturer. However, in terms of operational efficiency, Turkey is far ahead of us because of the various processes they follow.
Although these heaters are far more effective and energy-efficient, the shift from ceramic to infrared has been rather slow because of the pricing. We also introduced the IE5 motors in the market that was predominantly using IE3 motors at that time. This was a huge milestone for us as these motors are quite efficient and ensure better productivity. Despite the fact that this shift has been a slow-moving process, we have got approvals from several companies. We also have future polymer solutions where we act as a bridge between small-time plastic material processing units and our clients to provide the required materials.
Virgo Polymer, on the other hand, is an old and established company that started almost three decades ago from a small shed. From such humble beginnings to now manufacturing almost 6,000 tonnes per annum of FIBC is something that we take pride in. Since our inception, we have emphasised on producing the best quality products and that has been our most consistent trait. To ensure that we continuously get better, we have established an in-house R&D centre, complete with the latest test laboratory equipment. And being based in Chennai, the port city of India, enables us to provide quick and timely deliveries. These are some of the salient features of our company that give us a competitive edge over our contemporaries.
Q. Efficiency is the name of the game today. Share with us a case study in the polymer industry wherein efficiency improvement was the cornerstone of business success. We have conducted many successful trials in the polymer and engineering industries. I would like to highlight 2 cases of our trials.
One such application was replacing IE2 induction motors with IE5 motors on Lohia looms. Operating this loom for 24 hours had given a saving of 8% on electricity consumed, which was reduced from 99.04 units in 24 hours to 90.85 units in the equal number of running hours.
To know more, please subscribe to PolymErS Communiqué at subscriptions@polymerscommunique.com
Melt pump systems play an important role in the extrusion process and provide a quick payback due to linear and non-stop production.
“Screen changers help recycle all kinds of plastics waste, providing the best quality, reworked material. Over the years, a large number of recycling units have been established due to a good filtration process with screen changers that provide almost the same quality as virgin material. They are also necessary for generating good quality and quantity of granules at all stages of the extrusion process,” shares Hardit Parikh, in dialogue with POLYMERS Communiqué.
Q. From being the first company to introduce the concept of screen changers in India to the various engineering machines designed to support the plastics industry, how would you summarise this journey of almost three decades?
It was a proud moment for us to make the first screen changer for the plastics industry. Although we faced several obstacles during the manufacturing process, we were able to overcome them all, thanks to our strong engineering background. Despite all the challenges, we continued our pursuit to develop this product and started supplying it to a renowned company in Windsor India Ltd. only after we were completely sure of what we had built.
Within a span of 30 years, we have successfully supplied more than 10,000 units globally and we have been able to achieve this feat through the unwavering support of our result-oriented team. We supply screen changers for all kinds of plastic processing applications in India and abroad, and we see this as one of our greatest achievements.
Q. The use of recyclate in the plastics industry has increased owing to the new norms and mandates. What is the impact on the design and quality of screens and related equipment as compared to the virgin material?
Rajhans Plastic Machinery is the only company to support all recycling process plant customers by providing standard, affordable and result-oriented screen changers. These screen changers help recycle all kinds of plastics waste, providing the best quality, reworked material. Not just that, our product delivers a 50 per cent increase in quality and quantity. Over the years, a large number of recycling units have been established due to a good filtration process with our screen changers that provide almost the same quality as the virgin material. All of this has resulted in
a significant rise in the number of our customers reaping the benefits of our screen changers and earning high profits. Our screen chargers are also necessary for generating good quality and quantity of granules at all stages of the extrusion process. This is why, all machine (extrusion) manufacturers are willingly installing screen changers in their plants, as it has made a huge impact on the market.
Q. What is your current capacity and plans for capacity expansion? Are you planning any investment in technology and infrastructure? Rajhans’ motto is to satisfy all customers using our products. We invest each Hardit Parikh Director, Rajhans Plastic Machinery Pvt. Ltd., Ahmedabad
To know more, please subscribe to
at
Manish Desai Director,
Labels Pvt.
Mumbai
“In my view, the IML market is booming in the present scenario and it will achieve greater heights in the coming future. Aggressively investing in newer technologies helps overcome any hindrances on the way,” highlights Manish Desai, in dialogue with POLYMERS Communiqué.
Q. The purpose and types of labels have gone through a complete transformation, more so in the recent past. What are your views on this?
Instead of the purpose and types of labels, we must focus on the decorating technology that has undergone a massive transformation in recent times - the decoration technology used in rigid plastics like screen printing, shrink films, self-adhesive labels, in-mould labels and heat transfer labels.
We have seen an industry-wise shift in the decoration process. The bigger containers, ranging from 1 - 20 litre buckets have shifted from screen printing to heat transfer labels. The mould labels, typically used in the food industry for packaging of ice creams, sweets and dairy products, have shifted from dry offset / screen printing to in-mould labels (IML). The writing industry has shifted from screen printing to
To know more, please
to
Earlier, self-adhesive labels were pasted manually. However, the entire process has now shifted to automatic labelling machines. So, for the packaging industry, IML automation has been the most significant development.
Q. Manufacturing screws and barrels for the plastics industry that can be used in injection, blow moulding or extrusion, is a very niche segment in the machinery division. What prompted you to venture into this business?
There comes a time in every person’s life when they have to make a lifechanging decision. I also faced a similar situation when I had to make the choice of leaving a comfortable job and pursuing my dream. Such decisions are never easy, but a few of my close friends motivated and supported me to start something of my own since I always wanted to do that. I already had a lot of technical experience and a good background in injection moulding machinery while working in different MNCs. That apart, I also possessed in-depth technical and practical knowledge which provided me a great platform to start something in this industry.
So, I started by doing some general job work in machinery spare parts along with some maintenance work before starting my own venture. That was the time when I was looking for some inspiration to take that leap of faith, and I again found it in my friends and some companies I was on good terms with. They really helped me pursue my dream and pushed me to do something in an area I specialised in.
Q. Screws, barrels, nozzles and injection heads demand a lot of precision and skill. As an industry expert, which are the few parameters that are critical to manufacturing these?
Precision and skill are required in all kinds of manufacturing work. However, when it comes to screws, barrels, nozzles and injection heads, the material type, heat treatment process, machining and design as well as some other special processes determine the quality of the end product. In addition, the choice of material to be processed plays a vital role.
Q. What is your take on the role of continuous upgrade in terms of machining and skill development of people on the shop floor?
In today’s marketplace, machining and skill development are undoubtedly the main driving forces for the success of any industry. We definitely feel that it’s always a good idea to force yourself to adapt and step outside your usual routines. Our industry is extremely robust and skilled employees are essential throughout the value chain. Hence, we as a company, have always pushed our workers to acquire new skills - from learning to handle new equipment to getting familiar with new processes. Moreover, in order to identify misprocessing, they must learn new methods and contribute to the system flow. It can help them learn the new skills that are required to meet new expectations, both formal and informal.
Our workplaces are constantly evolving with new technology and processes being introduced regularly. If workers don’t adapt, learn new skills or familiarise themselves with newer technology, they will not
“In today’s marketplace, machining and skill development are undoubtedly the main driving forces for a business or individual to succeed. It is always good to step outside your usual comfort zone and learn something new. Our industry is extremely robust and skilled employees are
essential throughout the value chain,” share Bharat Makwana and Siddhant Makwana, in dialogue with POLYMERS Communiqué.
To understand and address any potential hazards posed by ‘microplastics’, broader participation from the scientific community would be helpful. Two publications have concluded minimal health hazards posed by ‘microplastics’. While research activities should continue in this field, we may need to tone down the narrative.
their beneficial roles in food, medical and other areas of human endeavour, plastics attract negative public glare. Vivid images of waste in terrestrial and aquatic environments generate adverse perceptions. To this, has now been added the frenzy of research, debates and publications on microplastics. Majority of these voices are concerned about the possible impact on human health. Do these tell the full and true story? Let’s explore this new frontier.
The debate, even amongst scientific communities, includes all microparticles derived from various synthetic polymers. Occasionally microparticles of other man-made fibres are also included under the overarching definition of microplastics - be it fragments of plastics, as understood by common man, or fragments of synthetic fibres and rubber. Any of these microparticles in the range of 5 mm to 1 micron in size, irrespective of their shapes or polymer types, are included in the definition of microplastics. Larger particles are categorised as meso-plastics and macro-plastics. The latter being plastic articles or large fragments of plastic articles. Particles smaller than 1 micron are put under the category of nano-plastics. As far as sizes are concerned, there, fortunately, is some broad agreement.
Using the criteria of size alone is inadequate for studying microplastics. Both shape and polymer types are critical determinants. These were
S. K. Ray Hon. Secretary & Member of Executive Committee, Indian Centre for Plastics in the Environment (ICPE), Mumbai
often overlooked in the past and are now being included for a better understanding of the issue and are necessary to understand probable risk factors to inform possible mitigation strategies. When we use a wider brush to define microplastics by including synthetic fibre and rubber microparticles, it creates confusion. Strategies to address challenges, if any, posed by these microparticles would be different than those posed by ‘microplastics’. At the definitional stage itself, we face ambiguity.
Would regulating the use or elimination of single-use-plastics (SUP) help make an impact on microplastics in the environment? Don’t fault an ordinary citizen if she or he thinks so. To begin with, the share of SUPs in the overall use of all types of plastic material is small. Hence, their contribution to the generation of microplastics is also miniscule. Most findings on
‘microplastics’ from field surveys in the terrestrial, atmospheric and aquatic environments point to predominance of synthetic fibre and rubber microand nano-particles. Including shapes and polymer types can help scientists provide meaningful direction to public policies and mitigation strategies.
The ambiguity about shape and polymer types in microplastics complicates health hazard studies. Polymers are a wide range of materials, both natural and synthetic. Many synthetic polymers with identical chemical structure exist as plastic materials as well as fibre or even elastomers. Prominent types are polyethylene terephthalate (PET), acrylic, polyamide 6 (nylon-6) and polyamide 66 (nylon-66). These are widely used as fibres in the textile industry - as fabrics, fibres and twines. While a consumer would view them differently, studies on microplastics aggregate them. We, thus, are not on
the same page in our understanding of potential health hazards posed by microplastics. Despite all the debates surrounding microplastics, our current science-based understanding points to very low hazards as compared to many other microparticles present in the environment.
While the presence of macro and meso-plastics in marine and terrestrial environments is widely explored, there are limited studies on microplastics in terrestrial and atmospheric compartments. There is a plethora of studies on micro- and nano-plastics particles in marine biota and their perceived potential to impact human health. Most of these experiments are carried out in laboratory settings
“We provide accurate, reliable and transparent data related to the plastics industry which acts as a guidepost to a number of industry sectors, helping in realistic and meaningful growth,” conveys Jigish N. Doshi, in dialogue with POLYMERS Communiqué.
Q. What are your thoughts on the recent ban on the use of single-use plastic by the government? What do you think will be the impact of this move on the plastics industry at large?
The plastics industry wholeheartedly supports the initiative by the Government of India that is in tune with the betterment of the environment. However, it is also a well-known fact that the plastics industry is one of the biggest sectors in India, which is not only labour intensive, but also involves huge capital investment in terms of plant and machinery, providing employment opportunities and contributing significantly to the national economy. The industry comprises a number of MSMEs that manufacture single / standalone plastic products. These businesses stand to face the brunt of this ban. What the plastics industry collectively believes is that the government should extend support in the form of fiscal incentives and policy building. Secondly, the industry needs some more time to find the right alternatives to single-use plastic. It is not only about increasing the thickness of plastic carry bags to 120 microns, but also about finding the right alternatives for plastic plates and cutleries. We are looking at viable alternatives for thermocol (polystyrene) based products. However, implementing these changes will require time and
that’s what the industry requests the government to provide. India is a huge country with every region operating in its own way. So, one solution might not work for everyone. We need localised solutions to ensure that plastics waste is collected and treated properly.
A complete ban is not the only solution. Everyone, including the government, the plastics industry and the people need to work together in finding the right alternatives, streamline waste management and improve recycling technology. Through collaborative efforts, we are sure that we will be able to effectively fight plastic pollution.
Q. What is the latest update on the Plastindia International University and what is the vision of the Plastindia Foundation for the next few years?
The Plastindia International University is almost on the verge of completion. We recently appointed Dr. D. D. Kale
as the Provost of the university. Most other prominent positions have been gracefully filled with experienced and prominent personalities. We are happy with the progress as the functioning of the university is in good hands. If everything goes as planned, we will be able to start physical classes by April, 2023.
Furthermore, the land price in India is too high. Stability in foreign currency rates, export incentive policies on the lines of what our neighbouring countries such as China offers will help exporters with a level playing ground, while competing in the global markets.
The Plastindia International University will provide expert industry knowledge and training to make the students industry-ready. They can go out and make a difference in the plastics industry as they will be well-equipped to do so. The plastics industry also stands to benefit greatly from the university as we will provide the right manpower with appropriate skills.
Plastic businesses will not have to spend time, effort and money to train their staff anymore.
Q. What kind of initiatives are being taken by the Plastindia Foundation for furthering the growth of the plastics industry?
Plastindia Foundation is working on several long-term initiatives that will have a huge impact on the growth
To know more, please subscribe to Polymers Communiqué at subscriptions@polymerscommunique.com
Strong performance of Indonesia’s leading 3-in-1 exhibitions representing the plastics, printing and packaging sector wrapped up successfully with 126 exhibitors from 14 countries, and 14,905 visitors from 23 countries.
Onceagain, INDOPLAS, INDOPACK and INDOPRINT have proven to be Indonesia’s leading trade exhibitions for plastics, packaging and printing industries. Almost four years since the last edition of the synergistic co-located exhibitions took place, INDOPLAS, INDOPACK and INDOPRINT 2022 wrapped up successfully with 126 exhibitors from 14 countries, and 14,905 visitors from 23 countries. Jointly organised by Messe Düsseldorf Asia and its local partner, PT. Wahana Kemalaniaga Makmur (WAKENI), the much-awaited The Indonesian International Plastics, Processing, Packaging and Printing Exhibitions were held between 31st August and 3rd September, 2022 at Jakarta International Expo, Kemayoran, Indonesia.
With the 2022 success, co-organisers Messe Düsseldorf Asia and PT. Wahana Kemalaniaga Makmur (WAKENI) have already announced that the next edition of The Indonesian International Plastics, Packaging and Printing Exhibitions will take place between 4th and 7th September, 2024. The 3-in-1 trade show of INDOPLAS, INDOPACK and INDOPRINT are modelled after the top global trade fairs, ‘K’ - The world’s no. 1 trade fair for plastics and rubber, interpack and drupa for the packaging and printing sectors, respectively.
“We were optimistic and confident about this year’s edition; the exhibition delivered added value to both, exhibitors and visitors. As a 3-in-1 platform, the exhibition served the full end-to-end value chain and encompassed the total processing packaging, printing and plastics sector - from raw materials, machinery,
For over three decades, Lohia Corp, besides standing for innovation and precision has stood for maximum customer satisfaction. A company that offers end to end solutions for the raffia industry, be it extrusion, winding, weaving, coating, printing, conversion or PP yarn spinning, Lohia Corp has gone the distance and has always put customers first.
Today if the company has delivered a processing capacity of 6.8 million metric tons per annum of PP and PE for customers across 92 countries, it’s only because of efficient after-sales support and optimized cost of ownership for customers. Lohia Corp continues and in future too, will be committed to customers for great value and complete peace of mind.
ancillary equipment, through to industry services. After a long hiatus, the exhibitions were held at the right time to bring the industries together across the spectrum of processing and packaging at one location,” says Gernot Ringling, Managing Director, Messe Düsseldorf Asia.
The exhibitions presented an international showcase with leading brand names across the three sectors such as printing technology leaders - Heidelberg (Asia), Movacolor (Netherlands), and closer to home were representations from regional players and leading domestic distributors such as Perdana Jatiputra and PT. Perdana Bangun Pusaka Tbk, representing brands such as Konica Minolta and Ricoh respectively, among many others.
Innovation and live demonstrations took place at numerous booths, including ‘A modern production environment: IRODORI – ‘Colouring the World Together’’ by Cyber Pte Ltd., a product launch by PT. Digital Media Grafindo and Master Plotter, as well as technical presentations by various exhibitors across all the three sectors. Trade visitors experienced a lively show floor with innovative offerings of advanced solutions delivering enhanced efficiency, automation and cost-saving
benefits across a wide range of products from the industrial ecosystem - from 3D-printing, corrugated packaging to bio-based plastics solutions.
The exhibition also included a line-up of concurrent events by supporting industry associations that have been instrumental in the success of the exhibitions, many of which also conducted on-site seminars and led various insightful programmes spotlighting trending topics, key presentations and panel discussions designed for all those involved in the printing, processing, packaging and plastics industries. These included seminars by the Indonesian Packaging Federation (IPF), Indonesian Association of Graphic Technology (ATGMI) and The Indonesia Olefin, Aromatic and Plastic Industry Association (INAPLAS), among others.
INDOPLAS, INDOPACK and INDOPRINT provide the ideal platform to share best practices and inspire collaborative partnerships promoting cross-border growth. Since the exhibitions started almost a decade ago, they continue to gain momentum as one of Indonesia’s choice exhibitions for international companies to expand their footprint in the Indonesian market.
Commenting on the relevance of the 3-in-1 exhibitions to the domestic market sectors and Indonesian
For me, it was my first time at this 3-in-1 event. A different kind of energy is what I sensed...in most cases, local companies showcasing global players! The organisers must have had restless months in between COVID lockdowns and beyond to implement this show. As has been witnessed globally, visitors continue to throng exhibitions and conferences to catchup with networking opportunities and business! Happier times lie ahead for all of us. Kudos to all stakeholder of INDOPLAS, INDOPACK and INDOPRINT!
business community, Rini Sumardi, Managing Director, PT. Wahana Kemalaniaga Makmur (WAKENI) says, “We have seen such resilience from local companies coming out of the pandemic, particularly on the back of disrupted supply chains and economic challenges. Indonesian businesses have recognised the need to drive innovation and embrace technology adoption and transformation to further strengthen the country’s manufacturing sector.”
“The healthy participation from local companies demonstrates the relevance of the exhibition as a platform to establish mutually beneficial partnerships with international companies to boost production capacity, cater to domestic demands, as well as bring about greater competitiveness to Indonesia and the global markets,” she adds.
Against this backdrop of market developments and looking ahead to the future, Indonesia’s economic outlook, market prospects and dynamic manufacturing sectors look bright, particularly in the pursuit of ‘Making Indonesia 4.0’ a nation-wide strategy to revitalise essential food and beverages, textiles and clothing, automotive, electronics and chemical sectors.
Exhibiting space application and more information on INDOPLAS, INDOPACK and INDOPRINT 2024 are available on the event website.
KCS’s guiding principle is to offer the world’s most innovative measuring and control equipment for the production of very thin, high-quality plastic films - which reduces raw material usage.
Control Systems (KCS) is a division of the family-owned company Hch. Kündig & Cie. AG (HKC) specialising in thin plastic film measuring and control devices. Since its inception in 1972, the KCS team has steadily climbed its way to being the world leader in the blown film industry.
The new KCS division got its first opportunity to solve a plastics industry problem during a spontaneous visit to the former Vinora company located in Rapperswil-Jona, Switzerland. Vinora needed a new width control device for blown film extrusion lines to replace the unsuitable devices then available. KCS decided this was a challenge they would tackle with the added assistance from a young electrical engineer. The first width control device was sold in 1972, thus establishing KCS’s foundation for the new division, which is celebrating its anniversary now.
Since these beginnings, KCS has continued to develop performance improvements in all its products, testing new scientific findings and developing new technologies. KCS’s guiding principle is to offer the world’s most innovative measuring and control equipment for
the production of very thin, high-quality plastic films - which reduces raw material usage. Clearly, an investment in the equipment from KCS is clearly both an economic and ecological decision.
The online film thickness gauge K-XRAY Rotomat KT 3G based on X-ray technology is now an established device on the global market. On several occasions, thickness gauges based on a gamma solidstate radiator have also been replaced by the K-XRAY sensor. As a result, thin foils can be measured much more precisely.
The online film thickness gauge K-XRAY Rotomat KT 3G based on X-ray technology, which was introduced at the last K trade show, is now an established device on the global market. On several occasions, thickness gauges based on a gamma solid-state radiator have also been replaced by the K-XRAY sensor. As a result, thin foils can be measured much more precisely, which, in combination with profile control, leads to decisively tighter crossprofile tolerances.
By no means will the 50-year-old KCS now rest on its laurels. The development pipeline is full to bursting and highly motivated, hard-working employees of the KCS specialist department are doing their best to ensure that new, high-precision, innovative measuring and control devices with the best price-performance ratio will soon be launched on the world market.
Finally, a huge thank you to our worldwide customers for their good cooperation and their loyal partnership over many years. Without their investments in measuring and control equipment from KCS, this success story could never have been written.
With a good experience at the Indoplas, Jakarta 2022 exhibition, Leistritz now wishes and hopes to see all of you again during the upcoming K 2022 exhibition in Düsseldorf, Germany.
The CLASSEN Group produces premium floorcoverings based on polypropylene. The recyclate quota is > 60%! Free of PVC, the boards can therefore be completely recycled in an environmentally-friendly way.
The process was designed such that only a minimum amount of scrap is produced and the ZSE MAXX extruders showed a clear advantage in material recycling. The material is mixed homogeneously within a controlled low-stress environment. Another plus point for recycling is the high degassing performance of the twinscrew extruders. In addition, the surface renewal allows efficient odour reduction and devolatilisation of the melt.
In a joint project with other companies, a research facility for the production of particularly resistant glass or carbon fibre-reinforced tapes has been realised.
2022 in Jakarta was a small, but quite active fair and we are grateful to see many of our existing, potential and also new clients. Fruitful technology meetings, project clarifications, solution-oriented new projects were discussed with our clients; and it was a refreshing experience.
We wish and hope that we can see all of you again during the upcoming K 2022 at Hall 16, Booth F22.
This year, our motto for the trade fair namely, ‘Inspire - Innovate - Integrate’ is used to demonstrate some unique, successfully implemented projects. If you visit the booth, you will be introduced to the following highlights.
The company Vinventions manufactures closures for wine bottles. Plant-based
raw materials (sugarcane) are used in the innovative compounding with direct extrusion process. Together, we have realised 15 installations.
The project combines sustainability, energy efficiency and a low CO2 footprint. With its experience in compounding and the design of extruders, Leistritz has helped to integrate the fluctuating quality of plant-based raw materials into a stable process that ensures consistently high product quality.
“The process begins with Leistritz in the production of the base material for lightweight components, so-called unidirectional tapes. For this, we have developed a highly intelligent system. In the next stage, lightweight components are produced from these tapes. In the last step, these lightweight parts are then recycled and used for the production of new tapes.
A ZSE 60 iMAXX extruder with the latest control will be shown live on the booth at K. It is equipped with a synchronous motor from Kessler.
According to the manufacturer’s data, this is one of the most energy-efficient converters currently available on the market. The gearbox is equipped with a condition monitoring system, in which intelligent sensors record the machine’s behaviour and enable a rapid overview of the state of the equipment.
Business Services attracted over 1,600 delegates representing 680 companies from 18 countries, making it the largest packaging summit of the world.
The much-awaited 9th Speciality Films and Flexible Packaging Global Summit by ElitePlus Business Services was held on the 5th and 6th September, 2022 at Mumbai became a historic event, as it marked the return of the physical conferences after the pandemic. The summit has been deemed and acknowledged as a grand success with the wholehearted participation of the entire cross-section of the worldwide packaging fraternity.
The summit attracted over 1,600 delegates representing 680 companies from 18 countries, making it the largest packaging summit of the world.
This summit truly attracted an unparalleled gathering of the brightest minds in the industry,
who spent two powerful high-level days together - networking, sharing and collaborating. The who’s who of the global packaging industry including industry-defining thought leaders, luminaries, visionaries, key influencers, innovators, veterans, strategic heads, prominent voices, subject matter experts and policy makers attended the pathbreaking summit.
The theme of the summit was, ‘Flexible Packaging ~ Moving to a Sustainable Reincarnation’. The 2-day programme included 9 power-packed business sessions and interactive Q&A sessions. A huge push towards sustainability in Europe was outlined through a panel discussion giving an overview on R-Cycle. The second important panel discussion on ground realities of the environment issues, EPR and sustainability demystifying PWM covered all relevant details on circular economy, sustainability and carbon footprint print was an eye-opener.
The Chairman, Gemini Corporation highlighted how recycling was an excellent arbitrage opportunity for the investor community.
The third panel discussion on brand owners’ perspectives was an awakening as the leaders from leading FMCG companies shared their thoughts and path forward for sustainability, hand-inhand, with the plastics industry.
The summit brought in another unique angle by bringing in the role of private equity in sparking growth explosion
in the flexible packaging industry and India’s role of M&A in consolidation and evaluating takeover opportunities and risks in the flexible packaging industry by Blackstone and Premji Invest leaders. The optimistic view on the Indian economic landscape was addressed by the MD of Kotak Mahindra Asset Management.
The well-crafted rich content was the main highlight of the summit with a distinguished speaker line-up, covering a gamut of aspects - be it on polymer laminate, transparent metallising with coatings, barrier paper, MDO film or BOPE or even PET / PET laminates, environment-related, EPR, MDO, raw materials and, of course, the FSSAI perspective. Eminent speakers covered not only the latest innovations on polymers, but chemistry, machines and their converting technologies.
These top companies presented new information on developments in polymers, engineering solutions and processing of plastic materials.
Nidhi Verma, Founder & MD ElitePlus Business Services who was at the helm of the 2-day summit opened the event along with the Inaugural Keynote Speakers outlining the future of circular economy and packaging from machine makers’ perspective by Peter Steinbeck, CMD, W&H; from the convertors’ angle by Ashok Chaturvedi, CMD, Uflex Group and from the brand owners’ view by Sudhir Sitapati, MD & CEO, Godrej Consumer Products and Dr. R. S. Sodhi, MD, AMUL.
Oriented film developments were presented by CEOs of Cosmo First and Max Speciality Films, and from the converters’ perspectives by leaders from Constantia Flexibles, Paharpur 3P and Jupiter Laminators.
The latest trends in machinery and innovations in technology were brought by Bobst, Colines, Reifenhäuser, Hosokawa Alpine. Advancements in raw material for sustainable packaging were highlighted by Reliance Industries, ExxonMobil, Borouge, LyondellBasell and Henkel. Innovations in printing and slitting were presented by DuPont, Comexi, Uteco, Siegwerk, Pelican, SP Ultraflex, Brückner and GOEBEL. Increasing profitability with ancillaries was shared by Lang Laser and DEC Impianti.
The delegates represented the entire value chain of the packaging industry including manufacturers and suppliers of raw materials, machinery, additives and adhesives, printing machinery, inks, post-extrusion finishing, automation and end-of-line solutions, besides converters. In addition, there was participation from brand owners, FMCG companies, major end users from the food, pharmaceuticals, personal care and agri sectors as well as petrochemicals, media and policy makers.
The major USP of this summit was the high participation of the brand owners as speakers, panellists and attendees.
All major associations and media bodies partnered for the summit lending their support. The gala dinner was a big highlight where all industry members networked and met physically after a gap of almost 3 years.
The ElitePlus Packaging Summit has emerged as the Mecca of the packaging industry and the most popular summit not only in numbers, but also in terms of content and value to the participants and partners.
Bry-Air (Asia) Pvt. Ltd.
Rakesh Chandra Jha, National Sales Manager 419-420 Udyog Vihar Phase 1, Gurgaon-122016, Haryana.
T: +91-124-4184444
E: rcjha@pahwa.com
W: www.bryair.com
Blend Colours Pvt. Ltd.
Sharad Rathi, Director
Plot No.35, IDA Kattedan, Hyderabad-500077, Telangana. T: +91-40-24361499 / 24360887 M: +91-9885118511
E: info@blendcolours.com W: www.blendcolours.com
Nu-Vu Conair Pvt. Ltd.
Pradeep Chudasama, Manager - Marketing Plot No. 147, 148 & 154, Devraj Industrial Park, Piplaj-Pirana Road, Piplaj, Ahmedabad-382405, Gujarat.
T: +91-79-29708147
M: +91-9712928201
E: marketingindia@conairgroup.com
W: www.conairgroup.com/india
Debbie Crowley, Global Marketing Administrator
1 Extrusion Drive, Pawcatuck-06379, CT
T: +860-599-1010
E: dcrowley@davis-standard.com
W: www.davis-standard.com
Ramesh Patel, Partner
Block No.553, Rakanpur (Santej), Kalol, Gandhinagar, Ahmedabad-382721, Gujarat.
T: +91-2764-286032 / 286450
M: +91-9825035472
E: rameshpatel@deepplast.com W: www.deepplast.com
Suresh Bajaj, Managing Director
G1/17, H21, H22, RIICO Industrial Area
Bassi, Jaipur - 303301, Rajasthan, India
M: +91-9001093913
E: jaipur@sonaligroup.in
W: www.sonaligroup.in
Dilip Prajapati, Proprietor
49, Gajanan Indl. Park, Ambica Mill Compound, Vatva, GIDC, Ahmedabad - 382445, Gujarat
T: +91-79-29628850
M: +91-9724308850
E: dilip@bladesandblowers.net
W: www.bladesandblowers.net
Debbie Crowley, Global Marketing Administrator
1 Extrusion Drive, Pawcatuck-06379, CT
T: +860-599-1010
E: dcrowley@davis-standard.com
W: www.davis-standard.com
Yizumi Precision Machinery India Pvt. Ltd.
Pramil Das, Sales Manager No.7, Mahagujarat Ind. Est., Moraiya Patiya, Village Moraiya, Ahmedabad-382210, Gujarat.
M: +91-7575009363
E: sales.india1@yizumi.com
W: www.yizumi.com
B&R Industrial Automation Pvt. Ltd.
Himanshu Sharma, Head - Marketing & Corporate Communication
8, Tara Heights, Mumbai-Pune Road, Wakdewadi, Pune-411003, Maharashtra, India
T: +91-20-41478999
M: +91-9979888790
E: himanshu.sharma@br-automation.com
W: www.br-automation.com
Abhay Upadhye, Director
703, Akik, S. G. Highway, Opp. Rajpath Club, Bodakdev, Ahmedabad-380015, Gujarat.
T: +91-79-26870825
M: +91-9327220008
E: au@mifasystems.com
W: www.mifasystems.com
Debbie Crowley, Global Marketing Administrator
1 Extrusion Drive, Pawcatuck-06379, CT
T: +860-599-1010
E: dcrowley@davis-standard.com
W: www.davis-standard.com
Debbie Crowley, Global Marketing Administrator
1 Extrusion Drive, Pawcatuck-06379, CT
T: +860-599-1010
E: dcrowley@davis-standard.com
W: www.davis-standard.com
Debbie Crowley, Global Marketing Administrator
1 Extrusion Drive, Pawcatuck-06379, CT
T: +860-599-1010
E: dcrowley@davis-standard.com
W: www.davis-standard.com
APAR Industries Limited
Kamal Sharma , GM- Business Development No 303, Welworth Regency, S. No. 24/3, Near Shivaji Nagar Bus Stand, Shivaji Nagar, Pune-411005, Maharashtra.
T: +91-20-25514720
M: +91-9823311662
E: agency.polymers@apar.com
W: www.apar.com
AWFIS, 7th Floor, Raheja Towers, M. G. Road, Bengaluru-560001, Karnataka.
M: +91-98410 20314
E: salespolymershead@gmail.com
W: www.PolymetSA.com.sg
Hassanand N.Masand , Proprietor
Shed B, Khasra No. 2/11, Nr. Bharat Petrol Pump, State Highway No. 26, Gurgaon-Patoudi Road, Jamalpur, Gurgaon - 123503, Haryana, India.
M: +91-9373067103
E: masandautomotives@ymail.com
27th September1st October, 2022
Taipei Nangang Exhibition Center Hall 1 (TaiNEX 1), Taipei, Taiwan
23rd - 26th November, 2022
Saigon Exhibition & Convention Center (SECC), Ho Chi Minh City, Vietnam
17th April - 20th April, 2023
Shenzhen World Exhibition and Convention Center, Shenzhen
17th - 21st October, 2023
Messe Friedrichshafen, Friedrichshafen, Germany
19th - 26th October, 2022 Düsseldorf, Germany
25th - 28th November, 2022
Biswa Bangla Mela Prangan, Kolkata
7th Oman Plast 2023
29th - 31th May, 2023
Oman International Exhibition Center, Muscat, Oman
7th - 11th December, 2023
Bombay Exhibition Centre, Mumbai, India
16th - 19th November, 2022
Jakarta International Expo, Kemayoran, Indonesia
24th - 27th January, 2023
IEC Expocentre, 14, Krasnopresnenskaya Naberezhnaya, Moscow, Russia
HIPLEX International Plastics Expo - 2023
4th - 7th August, 2023
Hitex Exhibition Centre, Hyderabad, India
1st - 5th February, 2024
India International Convention & Expo Centre (IICE), Dwarka, New Delhi
23rd - 26th November, 2022
Tüyap Fair Convention and Congress Center, Istanbul
1st - 5th February, 2023
Pragati Maidan, New Delhi, India
20th - 23rd September, 2023
BITEC - Bangkok International Trade & Exhibition Centre, Bangkok, Thailand
6th - 10th May, 2024
Orange County Convention CenterOCCC, Orlando, Florida, United States