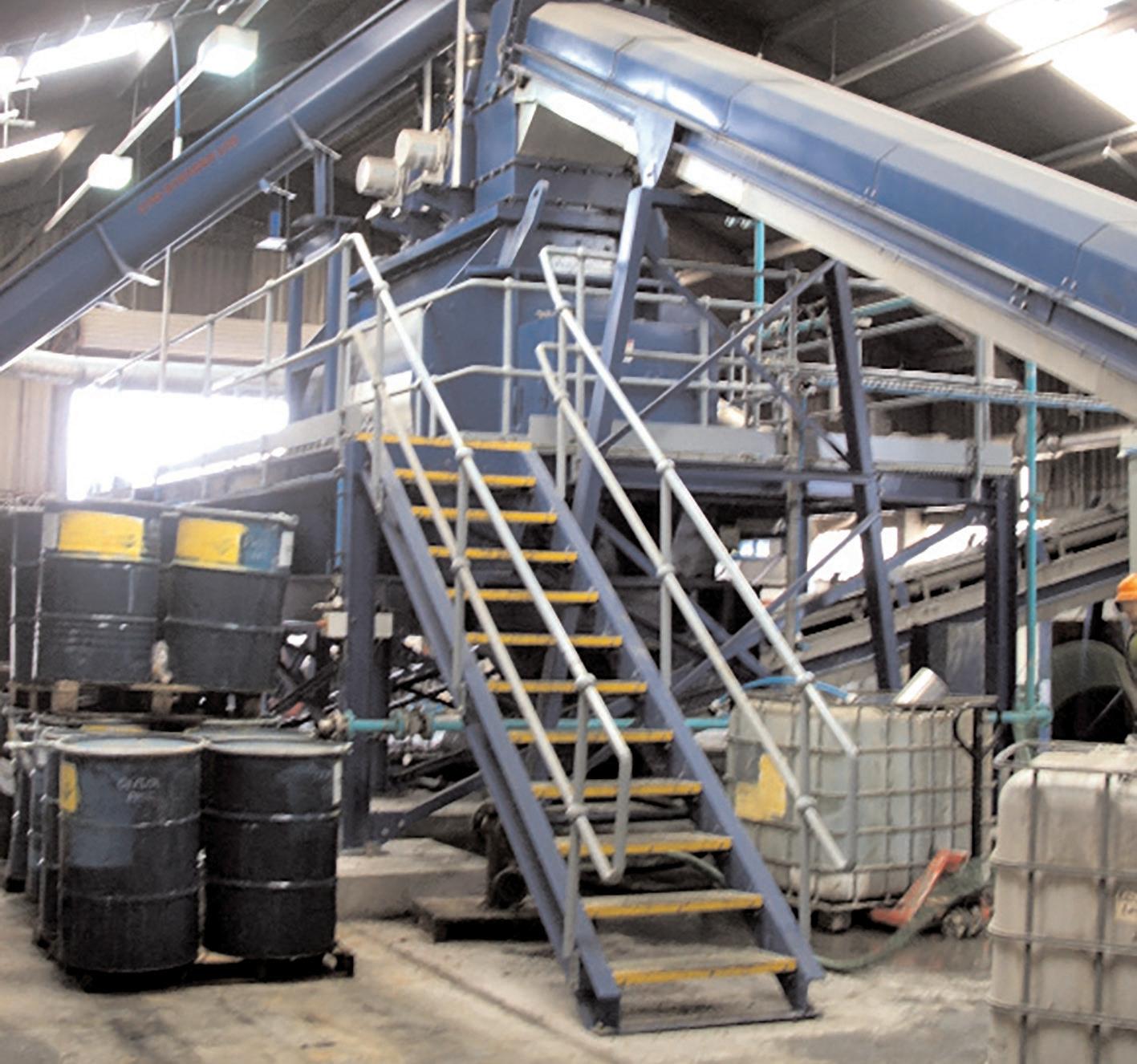
2 minute read
Mixer is handling brutal process to make hazardous material safe
Changing rules for managing hazardous wastes presented a challenge for waste management company
Augean PLC which was resolved by installing a mixing unit from J R Boone as part of a £1.2 million project.
Augean took the decision to make a substantial investment in the most advanced treatment unit for chemical waste in the UK when the legislation was pending, and the company has been pleased with the results. Its J R Boone mixing unit combines the shredded waste with cement and PFA (pulverised fly ash) to form a cake which can then be safely consigned to designated hazardous landfill sites.
The plant can accept a wide variety of waste containers ranging from 1M3 IBCs through to 200 litre steel drums and 50 litre plastics drums. In operation, the operator loads combinations of these containers onto a large infeed conveyor which delivers them to the heavy-duty shredder reducing everything to 25 mm or less. After loading the containers, the process is remotely controlled from the computerised operator panel to keep human intervention to a minimum.
The waste is then fed into the mixer with a measured amount of cement and PFA. The mixer then combines and encapsulates the waste particles with a cementitious coating and the finished product is then discharged into a skip for transport to landfill.
As the mixing is a pretty brutal process, and the mixing machine needs to be up to the job, a series of tests carried out in a pilot plant on a full range of wastes showed that the proposed design could meet the brief. This was therefore scaled up into the full-size unit, which includes a 6-tonne horizontal paddle blade mixer driven by a 132Kw motor.
The mixer consists of a semi-omega shaped mixing chamber with outboard bearings carrying a contra flow paddle blade agitator. Adjustable packed glands seal the agitator as it passes through the ends. The mixing chamber, ends and agitator are made from carbon steel with agitator blades in wear resistant ‘Abro’ steel. The discharge is via a specially designed heavy duty flush fitting valve.

Making the unit dust-tight was also a key requirement and so an extraction and treatment system for volatile components was included.
T 01260 272894
W www.jrboone.com
VMECA product specialist and UK agent for over 20 years. Vacuum challenges? Simmatic has the solutions.
Automation Uk 2023
COVENTRY BUILDING SOCIETY ARENA
Bringing Pneumatics And Vacuum Together
Simmatic’s experienced engineers will be at Automation UK on the 20 th and 21st June. We’re on stand A18 so, come and see us and say hello to our friendly team. With extensive expertise in vacuum & pneumatic industrial handling solutions, we invite you to challenge us with your difficult-to-handle products.
Watch VMECA’s NEW vertical MV-Magic Grippers in action:
- Innovative compact design
- Closer mounting centres
- Maximises surface area for handling
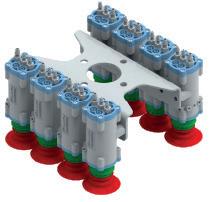