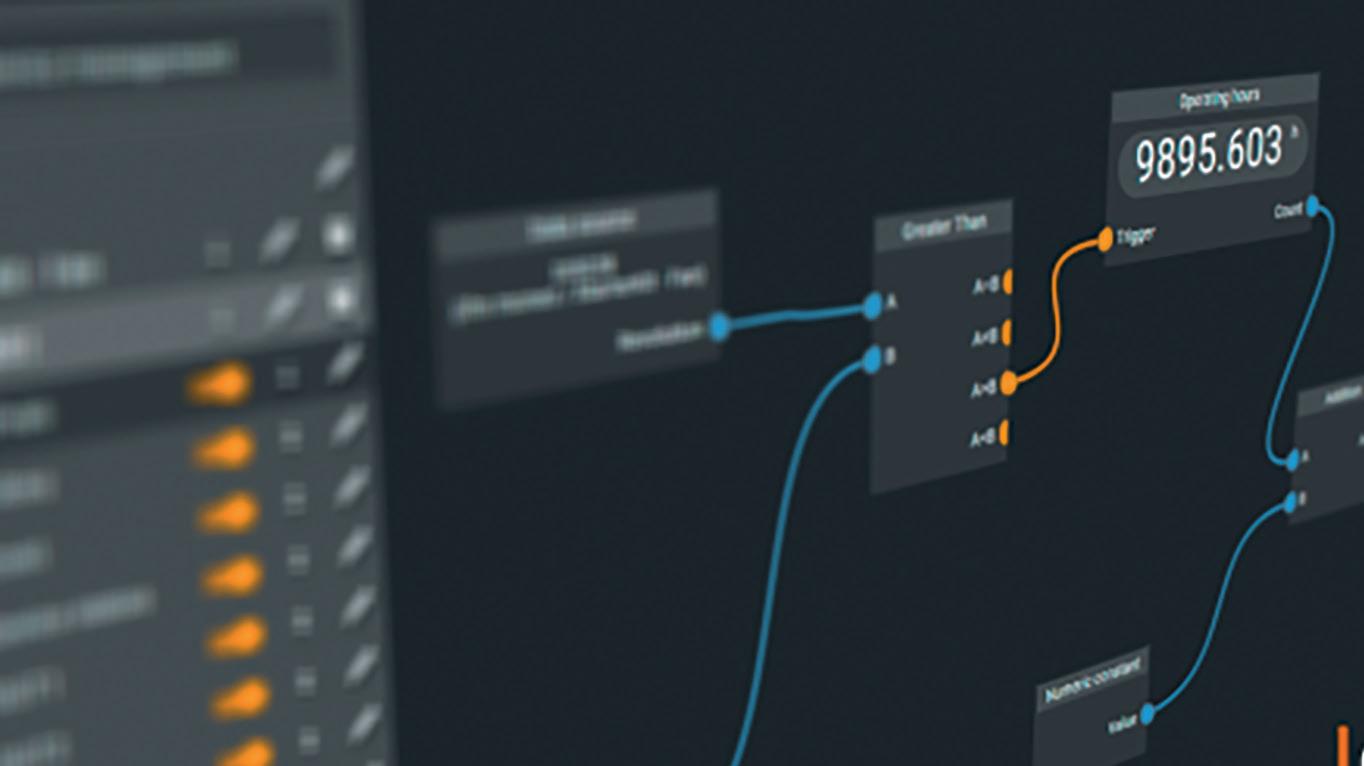
2 minute read
Inspecting on a small footprint
IIoT is currently seen as a technology that has enormous potential, but IIoT solutions have the reputation of being costly and difficult to implement. The moneo system eliminates these problems by making it easy to implement powerful and scaleable IIoT solutions at a modest cost, says ifm.
At the heart of the system is moneo OS, which provides flow modelling and automatic alarm functions as well as facilities for managing all of the other moneo software modules. These include moneo RTM which can be used to implement fully customisable user interfaces presenting plant and machine information in numeric, graphical or dashboard formats; moneo configure, which offers powerful configuration and management facilities for connected IO-Link sensors and devices; moneo infopoint which collects data from connected devices; and moneo edgeconnect which allows easy and secure interchange of data with IT systems.

T 020 8213 0000
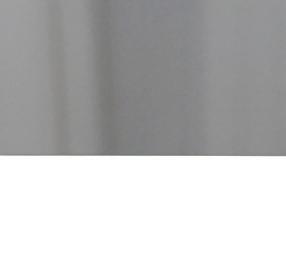
W www.ifm.com/uk
Many food SMEs are increasingly seeking compact, high performance, and energy efficient contaminant detection equipment which is why Fortress Technology showcased several of its small footprint solutions which are intentionally designed to save processors valuable production space without compromising on sensitivity. Offering detection of magnetic and non-magnetic metals in flour, rice, cereal, corn, grains, sugar, seeds and spices, the Fortress mini gravity metal detector, featuring a 75mm anti-static in-feed pipe with a high-speed reject valve, is one example on show. It was created specifically for busy ingredient lines where space is limited.
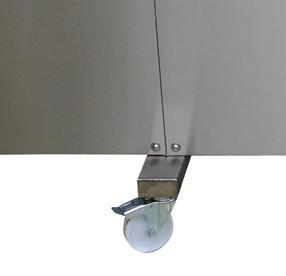

On conveyor inspection lines, a retail-spec combination metal detection and checkweighing system provides an alternative spacesaver. Mounting these systems on the same conveyor results in a far smaller footprint than stand-alone units would occupy. At the exhibition, Fortress presented its most compact option, the 100 mm belt width Raptor Combi.
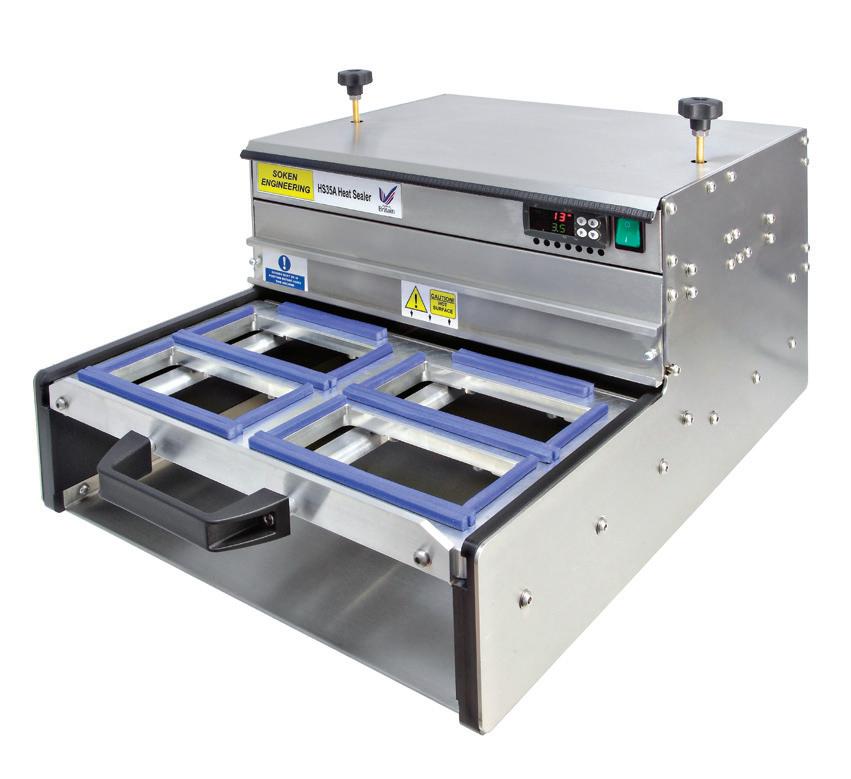
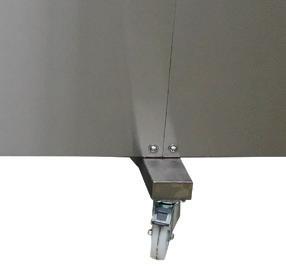
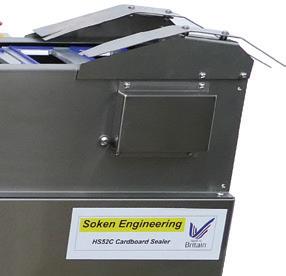
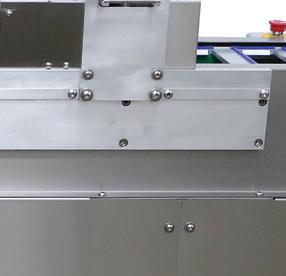
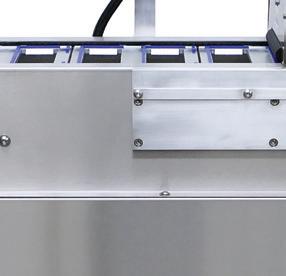
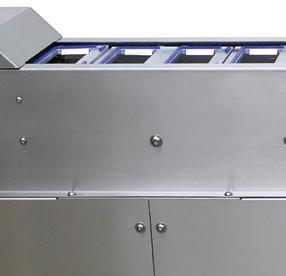
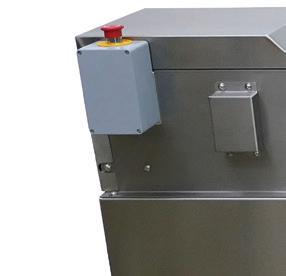
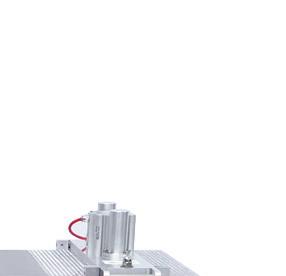
T 01295 256266
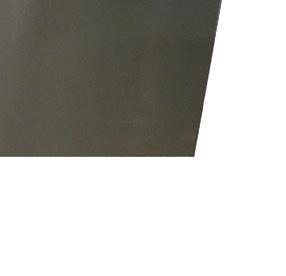
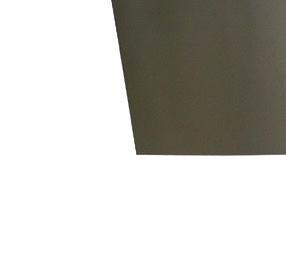
W www.fortresstechnology.com
• Increases shelf life (for up to 3 days)
• Medical, Pharma, Parts
• Greener packaging options
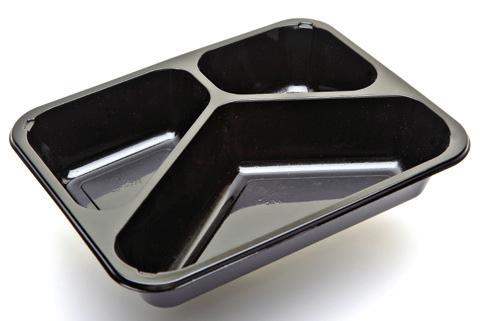
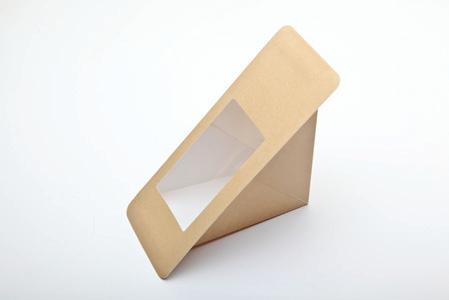
• Food-to-Go and Convenience packs
• Less food waste
Calculating waste makes perfect sense
Domino Printing Sciences (Domino) invited interpack visitors to complete its Waste Calculator to identify hidden causes of waste on their production lines and prioritise areas for investment as part of their ‘Journey to Zero’.
Part of Domino’s sustainable manufacturing showcase at the exhibition, Domino’s Waste Calculator is designed to highlight key areas where production line inefficiencies and errors can lead to excess physical and financial waste. It also demonstrates the role that smart manufacturing solutions and integrated coding and marking technologies can play in helping manufacturers to target ‘zero’ waste on their production lines.
“Our Waste Calculator helps identify where inefficient processes and errors could be contributing to wasted products and, by extension, wasted energy,” explained Jeremy Jones, global marketing director at Domino.

“We outline the steps manufacturers can take to ensure that the energy, time, and funds they invest are spent creating the maximum possible number of high-quality, sellable products.”
Domino’s Waste Calculator provides users with a bespoke in-depth report, or a simplified, industry-average-based overview centred on five hidden causes of production waste: manual data entry; manual code inspection; unreliable technology; service delays; and lack of integrated data.
T 01954 782551
W www.domino-uk.com