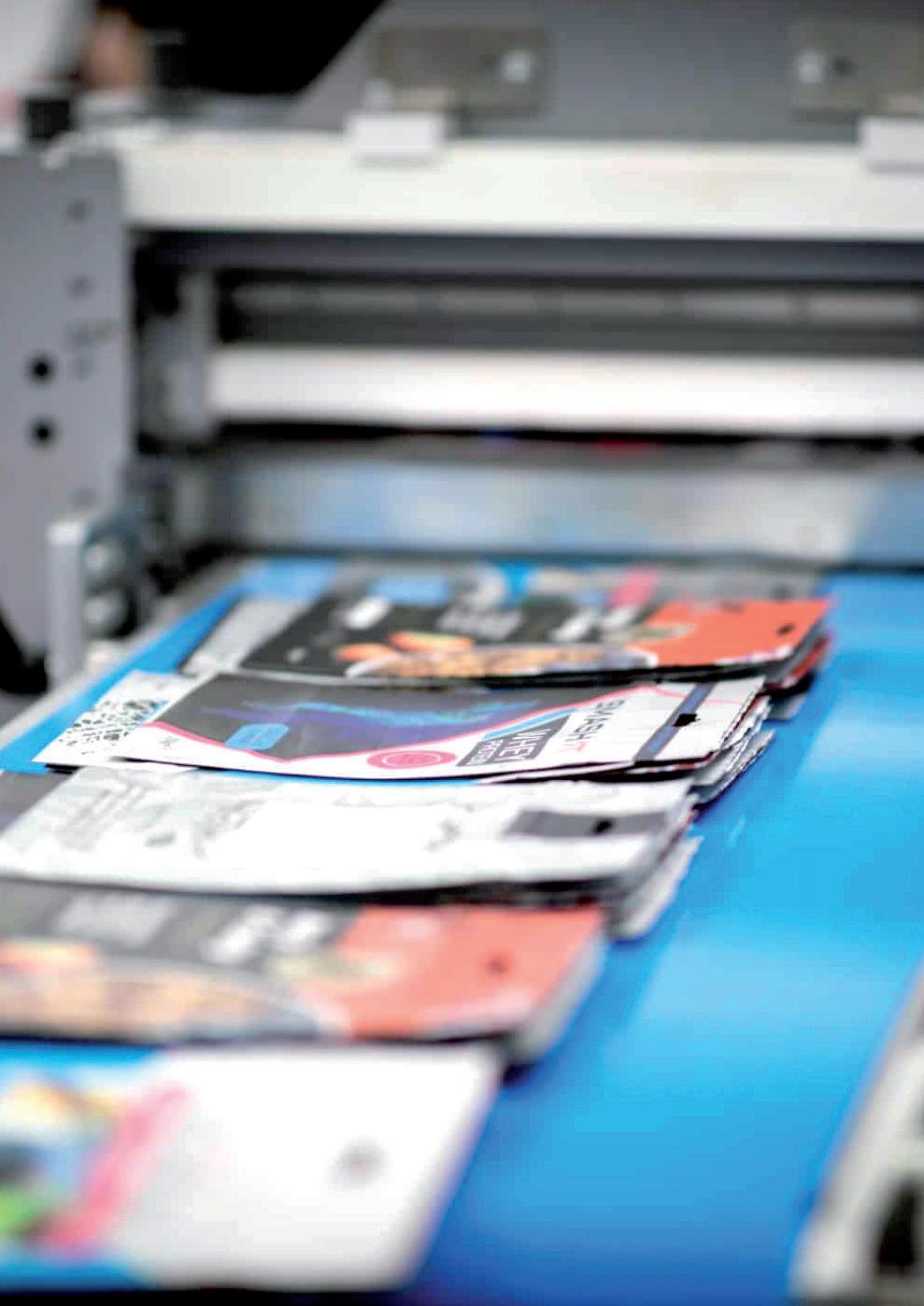

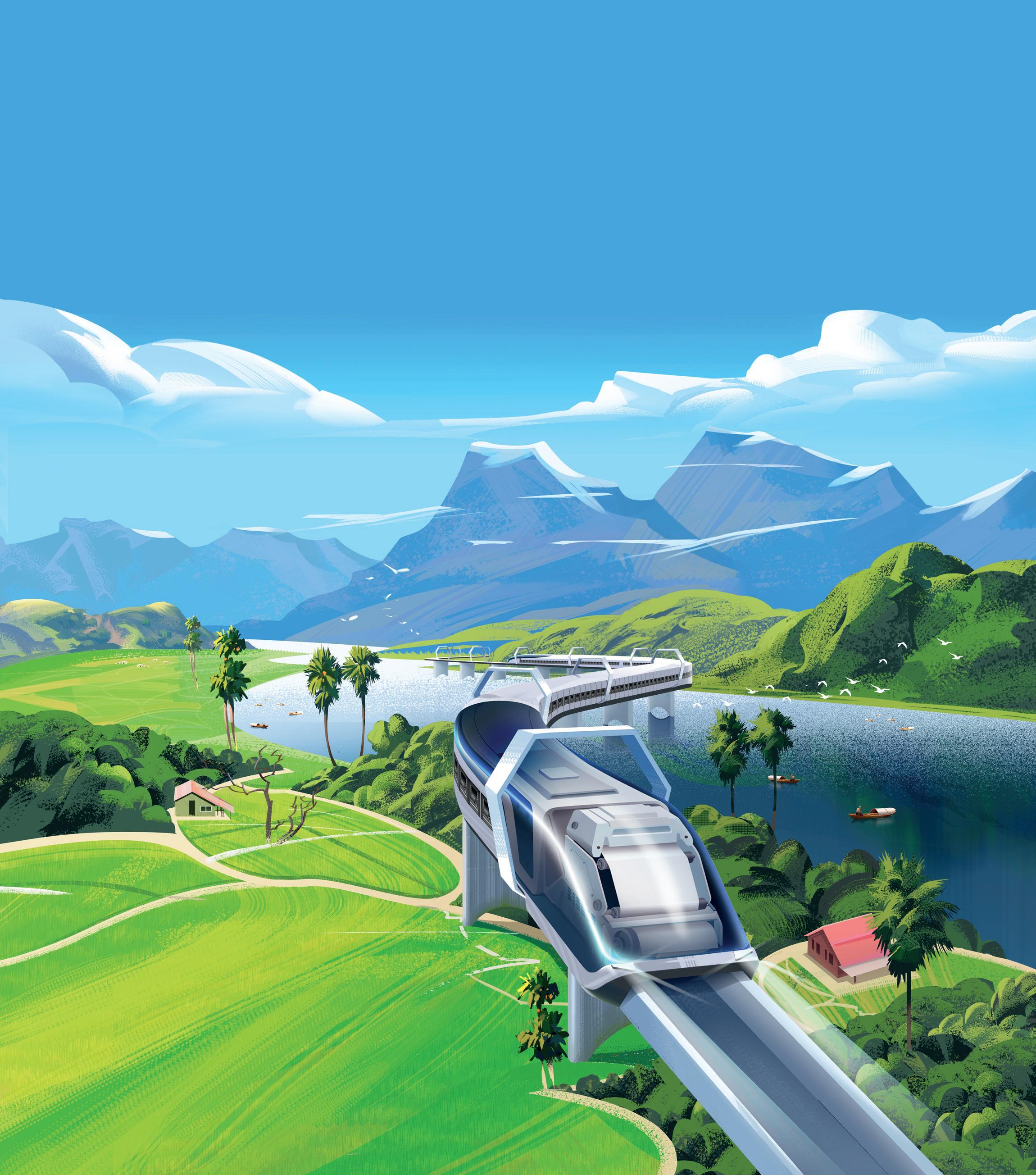
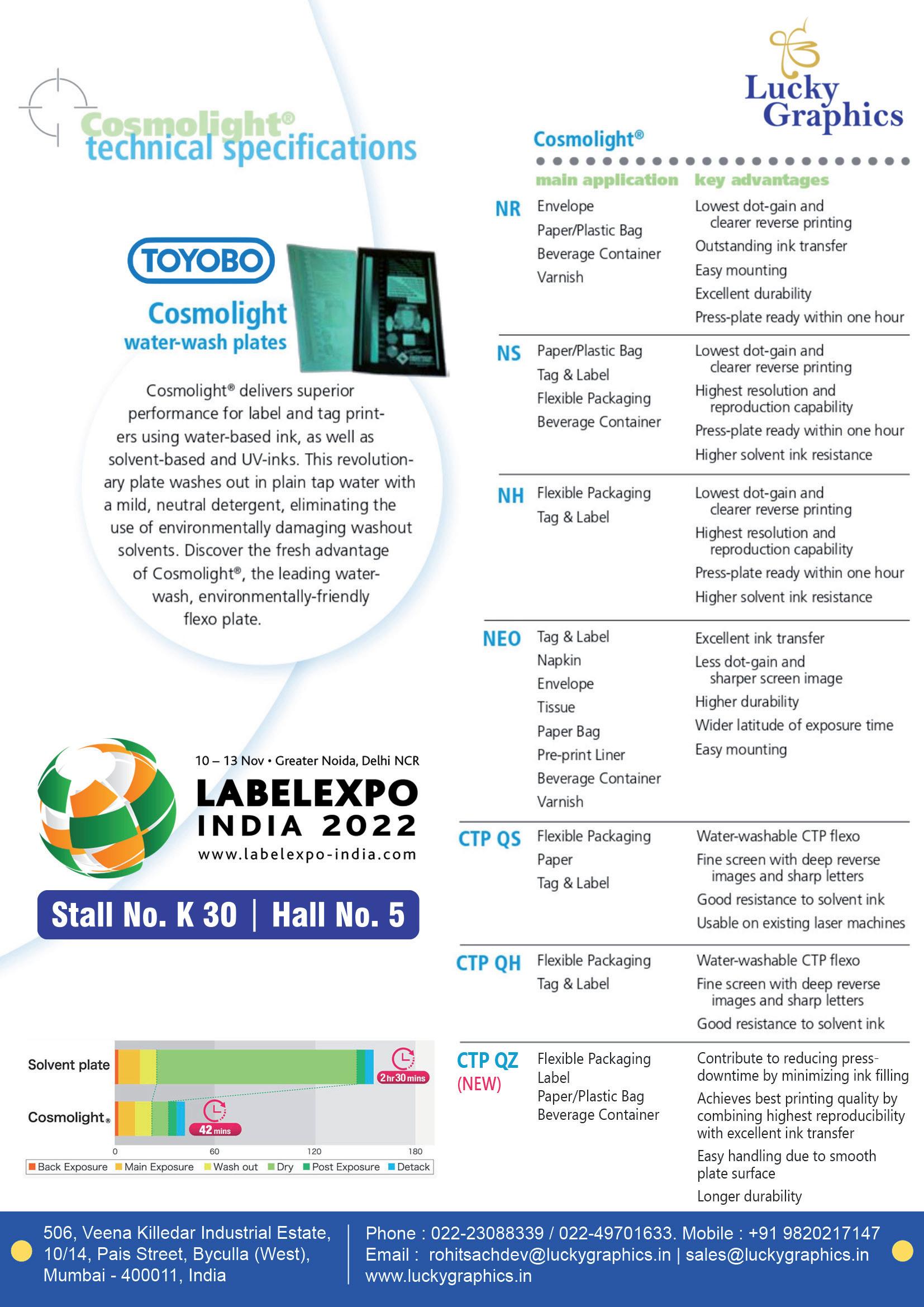
From All Sides: Autonomous Push To Stop
Walia is the new MD of manroland
facilitates teachers on
drupa Global Trends
meeting takes place at
founder
leadership
PageWide
at
powered by
Achieve at Leo: Smooth transition
installs
KODAK ACHIEVE at Campolina is a Smart Choice
Foreman joins OnPrintShop
Ambay Containers takes a leap in Prepress with
Seminar explains intricacies of
of Singapore opts for
UV inkjet
introduces Vistaflex
Traxx to
Pharma
the
with
of Surat goes for
Label Award
India launches
Systems
phase of
Jasmeet D. Editor & Publisher (jasmeet@pressideas.com)
Vineet K G. Associate Editor (vineetkg@pressideas.com)
Jasvinder S. Sub-Editor (jasvinder@pressideas.com)
Jacob George Marketing and Sales (jacob@pressideas.com)
M.S. Mukundan Advertising and Sales Southern and Western India (aims@pressideas.com)
Anil Kumar Networking/ Hardware Consultant Sukhdeep Singh
USA Correspondents
Tensi M., Preeti
European Correspondent Rimi, Yadhu Morphine
Production Thomas K Alex PRESSIdeas September 2022
Vol. 22, Issue 09 Printed by Jacob George and published by Jasmeet Singh on behalf of PRESSIdeas Publishing Pvt Ltd. Printed in India at Hues and Colors 363, Industrial Focal Point, Phase-IX Mohali, and published at PRESSIdeas, 437-A 1st Floor, Industrial Area, Phase-2 Chandigarh-160002 (India)
Every effort has been made to ensure that credits accurately comply with information supplied. All material supplied is compiled from sources believed to be reliable or solely an opinion of the authors. PRESSIdeas is not responsible for any steps taken based on the information provided herewith.
With the slogan “Perfect from all sides”, Heidelberg has launched its next generation Speedmaster SX 102. Enhanced in line with customer requirements, the SM SX 102 is aimed primarily at commercial print shops that require a high level of productivity and top quality perfecting printing.
Recent introduction by JETSCI is its KnowzzleJet, which aims print-ondemand applications like transactional, direct mail, trans-promotional, books, security printing, and bespoke articles, etc. with variable data printing of barcodes, serial numbers, Images, and more. The solution is powered by Memjet’s next generation DuraLink printhead technology and water-based pigment inks.
Other key product launches include the second generation Vistaflex fully automated CI printing press by Windmöller & Hölscher; Monotech Systems’ Pixeljet LEO 3200 Roll-to Roll printer for printing high quality indoor and outdoor signage applications; and PageWide Advantage 2200 by HP offering a new solution for print service providers to drive profitable growth with quality, productivity, and versatility.
“Process-free is fast catching up with Indian printers. CtP devices are being installed pretty quickly and regularly,” observes Manoj of Campolina Offset, one of the many recent Kodak Achieve Process-free CtP customers we covered in a series of exclusive stories. Today the entry point of an organization to go for a CtP in-house has drastically come down to one having around Rs. 5-6 Cr. turnover today. “Processfree is getting greater acceptance now. We have customers with about 500 plates’ consumption successfully running CtPs in their facilities. Today, we have over 250 Process-free CtP devices running across the country,” confirms Natesh Puri, Eastman Kodak Company.
Besides Campolina, we have in this issue the Kodak Achieve CtP story about Nalagarh, Himachal Pradesh-based packaging and label
converter Leo Designs & Packaging. The company has gone for the state-of-art Kodak Achieve CtP to simply go for chemical free process – moving along their environmental friendly commitmentsand to have Kodak capabilities by way of quality and technological superiority.
Another customer, Jai Ambay Containers has taken a leap in Prepress with KODAK. The packaging producer of Kala Amb has not only standardized its process but also taken advantage of the capabilities of the KODAK Achieve Process-free CtP like compact footprint and run-length flexibility.
Baddi based White Print O Pack had to meet the plate needs of their five workhorses offset machines – Heidelberg & KBA – and which came out to about 1200 plates per month. “We use three different sizes of plates for our five different offset machines. We had been looking for a solution to end dependence on outside sources for quite a fair time,” says Amit Gera, CEO of the company.
Apart from the Kodak Achieve, we have a story of Cron CtP from Nippon Color, recently installed by WeePac of Surat. They Thermal CtP capability has been brought in-house to save time, manpower and job secrecy.
Autoprint has installed a fleet of three Dextra 80 Die Punching solutions at VMOM of Singapore. Mr. Keng Swee TAN, Director VMOM visited Autoprint factory in Coimbatore to have a firsthand experience of the state-of-the-art Die Punching machine.
Self-adhesive specialist Fineflexo has installed a Gallus Labelmaster 440. Don’t miss the article on Industrial UV Inkjet. Dieter Finna explains how well equipped is the Gallus Labelfire “Tube Edition” and the UVF01 inkjet series for use in industrial laminate printing.
- Jasvinder Singh, Sub-editorHeidelberg launches new-generation Speedmaster SX 102; can be ordered with other assistance systems transferred from SM XL technology.
With the slogan “Perfect from all sides”, Heidelberg has launched its next generation Speedmaster SX 102. Enhanced in line with customer requirements, the SM SX 102 is aimed primarily at commercial print shops that require a high level of productivity and topquality perfecting printing. Typical areas of use range from brochures and commercial print products to inserts for pharmaceutical packaging, and therefore include applications involving very thin materials that need to be produced in a single pass.
The basic model offers an excellent priceperformance ratio, with configurations extending all the way through to an autonomous Push to Stop perfecting press. The new 92 format option (650 x 940 millimeters) cuts printing plate costs by up to 20 percent compared with the conventional 102 sheet format (720 x 1,020 millimeters), which is also available. This is a key economic consideration, especially given the sharp rise in raw material prices.
“Perfect from all sides” – the new Speedmaster SX 102 makes hightech solutions from HEIDELBERG affordable to a great many of print shops.
The new Speedmaster SX 102 is designed as a scalable press. Depending on the range of applications and the output/automation requirements, the basic model – already equipped with the tried-
and-tested HEIDELBERG perfecting technology – can be ordered with many other assistance systems transferred from Speedmaster XL technology. These include Intellistart 3, Intelliline, Intellirun, Wash Assistant, Powder Assistant, and many more besides. If required, the configuration can be extended all the way through to Push to Stop for autonomous printing. With the help of artificial intelligence, the
Key Notes :
> Numerous assistance systems with artificial intelligence for automation extending all the way through to autonomous printing.
> New 92 format option (650 x 940 millimeters) cuts printing plate costs by up to 20 percent.
> New ergonomic design combined with HEIDELBERG User Experience (UX).
Each story we create, or for that matter, each press release that you share with us, not only goes on our popular website but also is shared on all above Social Media pages of PRESSIdeas.
Your social media content is the embodiment of your brand and each social network brings in it's own set of challenges. Well, we take of several factors that go into producing and publishing social media content.
We can help you not only in Content Creation - where and how to Start with but once created, to schedule them on the Social Media and then optimizing it to attain the expected success is also our job. Last but not the least, analyzing the results of the Social Media Campaign too shall be shared with you.
If you’re looking to get started, allow us to walk you through it. Allow us to hand hold you all along.
Write to digital@pressideas.com or WhatsApp on +91 9780036854 to know more!
Note: Our online editorial team holds the right to decide on the selection of posts to be included on our social media pages. The FREE offer is for a period of 45 days. It is advisable to have only a post in a week.
digital assistance systems also achieve a further significant reduction in the number of manual interventions by operators. Besides saving time, this also means there is less risk of errors. Thanks to the Prinect Press Center XL 3 and the Prinect workflow, the Speedmaster SX 102 can be fully integrated into a print shop’s overall workflow, which ensures efficient data management, precise presettings, up-to-date production data, and informative reports. The Preset Plus feeder and delivery have also been taken over from XL technology, along with further proven solutions. The maximum printing speed is 14,000 sheets per hour in perfecting mode.
The Speedmaster SX 102 features an innovative, ergonomic design with a new gallery and guards that also come from the Speedmaster XL series. The HEIDELBERG User Experience (UX) provides staff with a modern working environment. The end-toend ergonomics extends to the operation of every single component. By making life easier for operators with its user very friendly navigation, the Prinect Press Center XL 3 with Speedmaster Operating System delivers predictable results and boosts performance. The various Prinect colour measurement systems that are available focus on reproducible colour stability and minimal paper waste.
“With the new Speedmaster SX 102, we are once again emphasizing our technology leadership,” says Stefan Hasenzahl, Head of Product Management at HEIDELBERG.
“Our customers benefit from a scalable press that can be fully integrated and, if necessary, adapted to their precise requirements using a whole host of established assistance systems from our Speedmaster XL solutions,” he adds.
HEIDELBERG 102 format class a popular choice for decades
HEIDELBERG has been offering the 102
format class since back in 1975. In this segment, too, it is the market leader by some margin. To date, the company has sold well over 100,000 printing and coating units in this format class.
“I’m confident we will continue this success story with the new Speedmaster SX 102. The press makes high-tech solutions affordable to a great many print shops, who also benefit from the industry’s largest and most efficient service network,” concludes Hasenzahl.
Deepak takes over from Neeraj Dargan as Managing Director of the manroland Sheetfed Indian subsidiary.
Deepak Walia has joined Manroland Sheetfed’s India operations taking over as Managing Director from Neeraj Dargan who left from the position recently and had established the India subsidiary in 2014 to start Manroland’s own operations in the region.
“I am excited to be heading the Manroland Sheetfed subsidiary to expand the company’s operations,” says Mr Walia on taking up his new role.
The management qualified Mr.Walia brings with him a vast experience in various printing streams. Having spent more than 24 years in the field of sales, marketing, technical
and operations in capital goods and consumables for the print and graphic arts sector and management qualifications for the new role.
“My local-market experience will enable us to better serve the group’s existing client base and with objective of year-on-year growth in India’s printing industry, I am looking forward to drive sheetfed machines and consumables market in the fast lane for Manroland with new ideas,” says Mr.Walia.
Manroland Sheetfed GmbH, the German producer of sheetfed offset printing presses was founded in 1871 and is one of the oldest producers of printing presses in the world.
Today the company has own subsidiaries in over 40 countries. Manroland Sheetfed GmbH is a wholly owned subsidiary of the privately owned UK engineering group, Langley Holdings plc.
Three eminent print teachers get Presidential Print Award during Printed Electronics and Smart Packaging Conference at DCRUST.
To celebrate teachers’ day on 5th of September, 2022, Offset Printers’ Association (OPA) felicitated 3 eminent print teachers with ‘Presidential Print Award’ during international conference on Printed Electronics and Smart Packaging at DCRUST, Murthal. The awards were presented by Prof (Dr) Rajendrakumar Anayath, Vice Chancellor of the Deenbandhu Chhotu Ram University of Science and Technology, Murthal to Prof (Dr Ambrish Pandey, Shri B D Mendiratta and Shri B R Chaudhary.
Acknowledging the foundation our teachers lay for our life, Prof.Kamal Chopra, General Secretary of OPA said, “Whatever we are today, we owe it all to our teachers. With this facilitation, we can honour and recognize the teachers’ contribution towards the
development and evolution in printing in India. We at OPA took up this initiative to remember the contribution of the masters of this great art.”
Presenting the awards, Dr Anayath said, “Printing is considered to be one of the biggest inventions of mankind and has a long and vast history; in fact, printing existed centuries before the era of Christ. We know of the Cuneiform, one of the earliest known writing systems developed in Sumer (modern day Iraq). We also know wedge-shaped marks made on clay tablets by a blunt stylus cut from a reed which belong to 3100 BC. Then there is Papyrus plant that is paper-like material
and was used as a writing surface in Egypt. Ink from lamp-black made in China was in use during 3000 BC.” Dr Anayath thanked OPA for recognizing the work done by print teachers, who have dedicated their precious energy and time towards training the technicians who remained an important part of transformation of the printing history of India.”
Global print industry shows post Covid recovery and resilience in face of fresh challenges.
“Socio-economic pressures are increasingly important to printers and suppliers alike, so much so that 59% thought these were now either as important or more important than print market pressures.”Richard Gray, Operations Director at Printfuture
> Over 500 senior decision makers on the part of print service providers and machine manufacturers/ suppliers worldwide completed an extended survey in spring 2022.
> Findings say, the Packaging market is strongest, but Commercial, Publishing and Functional markets all show signs of recovery in 2023.
> Investment fell inevitably during the last two years, but printers and suppliers both reported strong plans for capital expenditure.
The results from the survey show an industry that is on average across the globe a little more confident for the future than when last surveyed in 2019, before the pandemic. The Packaging market is strongest, but Commercial, Publishing and Functional markets all show signs of recovery in 2023. Regionally, confidence levels vary e.g. Asia and South America expect better trading in 2023 while Europe is downbeat given the Russia/Ukraine war and its consequences.
Investment fell inevitably during the last two years, but printers and suppliers both reported strong plans for capital expenditure. Sabine Geldermann, Director Print Technologies at Messe Düsseldorf, commented: “Printers and Suppliers know they must innovate to succeed in the longer term. The shocks of the last two years pegged back investment, but the survey indicates that the industry expects recovery to start in 2023. All regions and markets forecast higher investment in the coming year.”
The findings come from the 8th Global Trends online survey, when over 500 senior decision makers on the part of print service providers and machine
manufacturers/suppliers worldwide completed an extended survey in spring 2022. The survey was conducted by the commissioned partners Printfuture (UK) and Wissler & Partner (Switzerland) on behalf of drupa.
Globally 18% more printers described their company’s economic condition as ‘good’ compared with those that reported it as ‘poor’. For suppliers the net positive balance was even stronger at 32%. As always, confidence varies between regions and markets. The Packaging market is thriving with Publishing and Commercial facing structural changes from digitisation but with signs of confidence returning. Regionally the picture is mixed with Europe clearly concerned about the consequences of the Russia/Ukraine war but others e.g., Asia and South/ Central America, expect trade to pick up further in 2023 as economic momentum builds post pandemic.
Analysis of print volume in 2022 by press type, shows continuing decline in Sheetfed offset among Commercial printers matched by increases among Packaging printers. Flexo volumes continue to accelerate for Packaging printers, while all markets reported increased volumes using Digital toner cutsheet colour and all but Publishing with Digital inkjet rollfed colour.
Despite the active decline in the volume of Sheetfed offset in Commercial markets, this was the most popular press type for investment in 2023 across all markets except Packaging, where Flexo led, followed by Sheetfed offset. Digital toner cutsheet colour was the second most popular target for all other markets. Finishing equipment is the second most popular target for investment after new presses.
While there was virtually no increase in the proportion of turnover won by Web-to-Print installations between 2014 and 2019, over the last two years the proportion won by that means has shot up for those with such installations. Globally, since 2019 there has been an increase from 17% of turnover to 26% and this major increase is reflected to varying degrees across all markets.
having a major impact across the globe, although they vary in influence between regions. For example, 62% of printers in Asia chose Pandemics as the biggest threat, while in Europe this was chosen by 51%. And while 32% of European printers chose Physical wars, this was chosen by only 6% of those in South/Central America. Instead, 58% of them chose the threat of economic recession. Richard Gray, Operations Director at Printfuture, stated: “Socio-economic pressures are increasingly important to printers and suppliers alike, so much so that 59% thought these were now either as important or more important than print market pressures.”
The global economic market has experienced more shocks in the last two years than at any time since the Second World War. Yet this survey shows that print is still a central means of communication in all markets and regions and that while there are challenging times ahead, the industry has both the confidence and the determination to succeed. Wise strategic investment will ensure that printers and their suppliers will thrive.
Socioeconomic pressures and the global economic market Socioeconomic pressures are
Meeting of the National Committee of Bureau of Indian Standards, Ministry of Consumer Affairs, Ministry of Food and Public Distribution, Central Government, that fixes the Printing machinery standards, was conducted on 16th September in the Department of Printing Engineering. The first meeting was concluded in person post-COVID 19 with the Chairman of the Committee, Savitribai Phule Pune University Press Manager and Examination Department Special Task Officer, Dr. Dattatray Kute, the Member Secretary of this committee of Bureau of Indian Standards, Assistant Director Mr. Lokraj Meena and in the presence of other committee members.
This committee meeting was organized under the guidance of Hon’ble Mr. Sunil Redekar, Chairman of Pune Vidyarthi Griha.
In this meeting, offset printing machinery, CTP plates, digital printing machines, rubber rollers, and many other topics were discussed. Eminent personalities attending the meeting included, Mr. Prasad Pathak from Sakaal NewsPaper; Navneet Ahuja from ToI; Mr. Ravindra Joshi, President, AIFMP; Mr.
Datta Deshpande, IPAMA; Dr. Anjan Baral from GJ University, Hisar; Deepak Verma, SPMCI; Dr. K. Senthil, Anna University; Mr. Joshi, Manugraph and many others. The participant dignitaries took up the task of fixing the standards of printing machinery. For the first time, students got the opportunity to participate in the meeting and saw the working of the meeting.
The members present in the meeting guided
the students studying in the subjects of Printing Engineering and Diploma about the career opportunities and challenges of printing profession. The committee members also answered students’ queries. Besides the Chairman Mr. Sunil Redekar, Prof. Dr. Kaduskar (Director), Dr. Manoj Tarambale (Principal) and Professor Madhura Mahajan were also present along with other faculty and non-teaching staff of the college.
- Kazuo Inamori, a well recognized figure in business management, leadership and philosophy, and an inspiration for many other business figures passed away at 90.
Charismatic business leader Kazuo Inamori, founder of Kyocera, left for his heavenly abode on August 24 at 90. Inamori, a native of Kagoshima Prefecture, established Kyocera in 1959 in Kyoto when he was 27. The firm started with 28 staffers, but eventually turned into a major electronics and parts maker boasting more than 80,000 employees globally.
Kazuo Inamori, one of Japan’s most influential and respected business leaders, also co-founded DDI in 1984, a predecessor of KDDI, to facilitate competition in the telecommunications market, then dominated by NTT. KDDI is now one of the top three mobile phone carriers in Japan.
After Japan Airlines went bankrupt in 2010, Inamori was asked by then-Prime Minister Yukio Hatoyama to lead and turn around the ailing airline. Inamori accepted the job with no compensation and tackled JAL’s reconstruction as chairman for about three years.
Under Inamori’s leadership and management reforms, JAL experienced a revival and went public again less than three years after its bankruptcy.
Inamori is known for his creation of the “amoeba management method,” under which workers are divided into small groups called amoeba.
Each group is provided with real-time figures on their business operations and achievements, and they are encouraged to work as if they are an independent entity within the company.
Some firms formerly led by Inamori — including Kyocera, KDDI and JAL — that have adopted the amoeba system have successfully grown into major players in their fields.
“I have spent many years in management and know from my experience that it’s important to have a system to allow you to grasp details of real-time figures and results
so that all employees can pitch ideas to improve business operations,” Inamori told a news conference in October 2010 when he was restructuring JAL.
Inamori, who was also an ordained Buddhist monk, published numerous books on business management, leadership and philosophy, and inspired many other business figures.
Sachio Semmoto, one of Japan’s best-known entrepreneurs and a fellow co-founder of KDDI’s predecessor, told The Japan Times in an interview in 2018 that Inamori changed his life.
“Meeting with such a great business leader was the trigger. I don’t think I would’ve founded (DDI) if I hadn’t met Mr. Inamori,” Semmoto said, adding that Inamori taught him a great deal about business leadership.
Inamori ran a business school between 1983 and 2019, and spent his personal fortune on philanthropy.
In 1984, he spent about ¥20 billion to establish the Inamori Foundation. The organization gives awards to individuals who have made remarkable contributions to society and offers financial support for unique research.
HP PageWide Advantage 2200 offers a new solution for print service providers to drive profitable growth with quality, productivity, and versatility.
Digital production printing solutions provider HP has launched a new HP PageWide Advantage 2200 series press. The press has been designed to meet the needs of print service providers of all sizes and offers high level of productivity, quality and media versatility for various industry segments including publishing, direct mail and commercial print.
“This new PageWide Advantage platform is a game changer for the commercial print industry,” said Annette Friskopp, Global Head and General Manager at HP PageWide. “HP has listened to our customers, and we realize ease of use and up-time are critical success factors. This new press offers configurations to enable customers to optimize the press for their quality, productivity, versatility, and economics to grow their digital production businesses.”
The HP PageWide Advantage 2200 is capable of speeds up to 500 ft/min colour and 800 ft/min mono and printing high coverage jobs at up to 90 million US letter sized mono images per month or 214,000 personalized A3 colour duplex sheets per shift. It offers high impact full coverage jobs’ productivity for thicker stock applications including postcards.
With the ability to print using HP Brilliant Ink and 2400 native nozzle per inch printheads, the HP PageWide Advantage 2200 offers top notch quality to address a wide range of higher value applications, from more colourful trade and educational books to high-coverage, impactful direct mail pieces that differentiate clients in the market. It handles a wide range of media weights from 40 gsm (27 pound) up to 300gsm/14point stocks, giving printers the versatility they need. Its innovative single print arch design, with a robust paper path with fewer components, reduces the number of parts to manage and therefore overall maintenance and servicing time, increasing reliability and maximizing uptime.
The modular design of PageWide Advantage 2200 offers high configuration flexibility for customers to start with a lower capacity
machine and enhance the machine as their business grows or their application mix shifts. Customers can select 1, 2, or 3 dryer modules along with passive or active web cooling modules to fit their needs. In addition, the press features a compact single engine duplex design, providing high quality and productivity while saving floor space for customers.
The HP PageWide Advantage 2200 comes equipped with HP’s innovative High Efficiency Drying (HED) system that minimizes power usage at higher print speeds by recirculating up to 80% of the air heated during the drying process..
Kevin Hughes, Chief Operating Officer at SG360º said, “We were pleased to see the HP PageWide Advantage 2200 team wrap up installation in one week. Time is money in our business and this accomplishment is terrific for both SG360º & HP customers. Additionally, within weeks of this press being in operation, we have printed over 20 million
images, and are absolutely excited for future possibilities using its terrific print quality.”
Ann Gayou, Senior Vice President of Plant Management at O’Neil Digital Solutions said, “As a longtime customer and partner with the HP PageWide team, we have purchased 13 PageWide web presses and we are quite excited to have installed the very first HP Advantage in the world! Our operators were able to easily learn the latest features and simplicity of operations and were producing millions of pages a week in no time. We selected a 2 HED dryer configuration and are thrilled with the press’s productivity and the quality of HP Brilliant Ink.”
The HP PageWide Advantage 2200 is expected to be commercially available worldwide on October 19, 2022.
HP will be showcasing the PageWide Advantage 2200 at Printing United in Las Vegas October 19-21, 2022, where visitors can see the inkjet web press in live action.
Fujifilm India announces changes in the leadership of the Graphic Arts Business.
Fujifilm India has announced a spate of changes in its Graphic Arts division leadership team. Mr.Kentaro Imafuku who headed the GA division for past 2 years moves into a new role as the DGM of GA division Asia Pacific based out of Singapore. A veteran of the GA industry, Mr.Imafuku has been credited with spearheading the division successfully and navigating it through the tough covid years. Mr.Imafuku will continue to support Indian team along with a group of other countries of Asia Pacific region.
Mr.Imafuku has been replaced by Mr.Priyatosh Kumar as the new HOD(Head of Division) of Graphic Art division for Fujifilm India. He had earlier headed the digital business within the GA vertical. Mr. Kumar brings with him wealth of experience in the domain of business operations and product Management across various industries.
Commenting on the changes, Mr. Koji Wada, Managing Director, Fujifilm India said, “We are extremely thankful to Imafuku San for his
excellent contribution to India GA business and wish for his continuous support as part of AP region. We also believe that Mr.Priyatosh will successfully carry the baton forward and carve a niche for FF in the GA space. Graphic Arts is one of the critical business divisions of FFIN and the company is totally committed to the industry with wonderful products and solutions.”
On this new development, Mr.Imafuku commented, “India has been one of the best
experiences of my career and I would like to take all my learnings to the global markets. I have a special affinity towards Indian distributors and customers and look forward to continue working with them.”
Mr. Priyatosh mentioned that it was an honour to lead the GA division that has many of Fujifilm’s flagship solutions. He strongly believes that the Indian economy is on an upward swing, and it is the right time to seize the opportunity.
Today’s inkjet enables growth & profitability for commercial print applications.
The long-term trend towards smaller run lengths has been putting stress upon commercial printers for years. Digital printing’s ability to print in economical quantities, all the way down to just one unit, offers publishers a powerful tool to address variations in demand and has inventory and distribution cost savings.
Moreover, there are revenue advantages that these new technological advances bring. Publishers can significantly expand sales overseas because they are able to deliver digital files to printers that can print short, on-demand runs in growing markets. Printers can expand their profitability by offering new and different services including micro-runs and personalization allowing the development of new application areas.
JETSCI Global brings a comprehensive range of digital printing solutions that fit book
or label printers’ requirement of volume as well as quality. The range of solutions stands out for being innovative, productive, and cost-effective choice for inkjet printing and anti-counterfeiting solutions providers.
The recent introduction, knowzzleJet is a durable and efficient solution powered by Memjet’s nextgeneration DuraLink printhead technology and water-based pigment inks.
JETSCI knowzzleJet is perfect for print-ondemand applications like transactional, direct mail, trans-promotional, books, security printing, and bespoke articles, etc. with
variable data printing of barcodes, serial numbers, Images, and more. It is equipped with a high-speed PDF workflow RIP engine with advanced features for accurate and high-quality printing without loss of speed irrespective of the application. The Smart Solution Platform also comes with optional folding, gathering, and booklet making.
Leo Designs & Packaging installs Kodak CTP. Standardizes plate production and brings the process-free plate production capability in-house.
“Leo has been a trendsetter in the Indian market by being among the first installers of this trendsetting technology,” declares Natesh Puri, National Manager- Plates & Chemical and Packaging Segment at Eastman Kodak Company.
Nalagarh, Himachal Pradesh-based packaging and label converter Leo Designs & Packaging had gone for the state-of-art Kodak Achieve CtP to simply go for chemical free process – moving along their environmental friendly commitmentsand to have Kodak capabilities by way of quality and technological superiority. One key factor that played an important role in their decision to go for Kodak Achieve CTP was its being virtually a plug & play device. While comparing different options before deciding to install Kodak, they observed that there were many process steps involved in the nearest competitor model, which also required more manpower. Moreover, the other option didn’t meet their core objective of eco-friendly technology adoption.
> Chemical free process, Kodak capabilities, quality and technological superiority.
> Kodak – meeting the core objective of ecofriendly technology adoption.
> 15-20 percent saving on capital and chemistry and 30-35 percent on power bills.
It was a smooth transition for Leo Designs & Packaging to shift to CTP in-house; earlier they were either outsourcing plates’ requirement or preparing them on their in-house PS imagesetter. “Kodak team has been especially helpful in creating the right set-up which matched perfectly to our needs and existing workflow,” says Varun Rao, MD of the company. Sharing his installation experience, he adds, “They calibrated the system as per our need and everything was working in no time. Before we installed it, we already had this impetus of having extremely flexible payment options; then during the installation, we found the transition extremely smooth; and even after installation, we received the perfect Kodak backing for the robust system – with extended warranty and service offerings.”
Kodak and Leo association has been longer than their recent CTP. They had been using digital
flexographic plates from Kodak for their flexo printing unit. Mr.Ashish Sharma from Aarushi Agencies (Kodak’s representative) used to visit Leo facility for technical guidance on those plates. Their discussion on the prospects of bringing a plate production facility in-house first took place during those times.
“With Kodak process-less system, they had the foremost advantage of saving 15-20 percent on capital and chemistry that the Kodak eliminated by way of doing away with the processor,” points out Ashish. The second key advantage was the device’s attractive figures of power saving – it stood about 30-35 percent less than other available options. Besides, Leo was not only seeking an environment friendlier technology, but also keenly looking for the standardization of their plate production. They very much did so by eliminating the need for a processor and associated processes, labour, time and consumables with their Kodak. The press got calibrated with the CTP and they had a clean green technology in place for their press. “Leo has been
a trendsetter in the Indian market by being among the first installers of this trendsetting technology,” declares Natesh Puri, National Manager- Plates & Chemical and Packaging Segment at Eastman Kodak Company.
Leo started in 2008 with a small setup and doing flexo labels. Starting with Mark Andy, they added Nilpeter and then Gallus down the years. They presently boast a full-fledged digital printing setup for a wide range of solutions it offers to its equally diverse clientele. In the last five years Leo has invested in some of the best technologies and has come up as one of the top leaders in the segment. The packaging giant has regularly consulted with its clients to know about their upcoming demands and areas where they could both expand. Defying the notion that ‘a jack of all trades is master of none’, Leo has tried to expand to diverse fields so that they are their clients’ onestop-shop for all their needs. “We not only provided them a single window opportunity to meet their printed products’ needs but also ensured that we deliver them a complete product package and save them the hassle of running about many shops to get different constituents of their final product,” says Varun. Leo has a full range of packaging and labeling solutions that include labels, mono cartons, boxes to lamitubes and much more, all under one roof. In the cartons division they have Heidelberg, Dominant and Polygraph for printing and automatic die-cutters (semi and fully automatic), gluing and pasting machines along with other equipment for finishing and converting. Each division of Leo is independently managed and run by a team of professionals adept in their respective fields.
– Handling 1500 to 150000 impressions with ease Varun is very happy with the results of the Kodak Achieve and the quality that their processless plates bring out on printed products. “When you have good plates, you get the result quickly – there is less waste while sorting; you get your registration right with less waste of paper; all in all, saving on manpower, time and energy!” emphasizes Varun. The processless plates do an average of 15000 to 20000 print runs though the capacity can go well up to 150000 impressions. With the flexibility and economy the plates offer, Leo easily caters
to the short run job demands of as little as 1500 print runs. However, print-runs are not a deciding factor for Leo to decide whether to do a job on Digital or Offset, according to Varun. Though they have both capabilities always ready to produce and their Digital Press capability can easily handle heavy carton material, the cartons have been kept exclusively for Offset production. “The process, efforts, quality of printing and economies involved are some of the factors that we put as criteria before classifying print technology to be used for each job,” he summarizes. “We have clients who usually get long-run big volumes from us and they also have their short run jobs. We accordingly decide which ones to put on the Offset and which ones on the Digital machine as per machine availability and available deadlines,” he adds.
Before the Kodak CTP installation, Leo would use its plates for repeat jobs. But, after Kodak installation they have found it convenient to use the plate just for a single job and have instead used a fresh plate for each repeat job. “The plates re-used tend to have some issues with texts, the loss of time and money by way of press stops, material and paper wastage and redoing things was a nuisance. We can easily avoid these issues by simply using fresh plates for repeat jobs,” maintains Varun. “Though short-run jobs are a challenge this way because the same run capacity plates have to be used for both
short as well as long run jobs,” he says.
Leo has a diverse client base – there are regular major customers, small volume customers and there are also walk-in nonrepeat customers. Varun believes more in long term relations than in price based competition. He caters to a significant number of new customers and keeps adding to his repeat customers’ list. This is how he sees at expansion and a sustainable business model. “For printers based in metro cities, it can be ok to start a business and depend upon walk-in variable clientele, but it is quite different here (Nalagarh region). We have to keep building long term relations with the customers and continue providing ever better service to them,” emphasizes Varun.
Leo is a first generation company. Varun’s elder brother, who is a high court lawyer also, looks after the technical aspect of the business; including the creative and production part. Pharmaceutical is a flourishing industry in their region and they cater to the industry in a big way. They also create printed packaging products for the FMCG and cosmetics industries. Varun looks forward to expanding further into FMCG and cosmetics segments along with adding more products and applications to their portfolio. He also plans to expand into the lamitubes including those for the oral healthcare segment in near future.
Fineflexo focuses on productivity with a brand-new Gallus Labelmaster Press.
“Technology and automation are the keys to success in business, and the versatile Gallus labelmaster helps in our growth.” – Ritesh Shetty
Fineflexo installed a brand-new Gallus Labelmaster flexo press at Baddi, Himachal Pradesh. Fineflexo is a joint venture between Medi Sales Group and Bhavani Group, specializing in the extended supply chain of pharmaceutical business and logistics.
Mr.Ritesh Shetty, Director at Fineflexo, said, “Fineflexo embodies ultimate excellence, adaptability, and service. We are endlessly working to nurture and upgrade the standard of the whole self-adhesive market in the country with premium quality, performance, and JIT deliveries in our product segment. We focus on developing a robust product portfolio for our clients and fostering trust and customer satisfaction.”
> Fineflexo brings print jobs inhouse with Gallus Labelmaster 440.
> Finalizes Gallus Labelmaster because of Heidelberg’s reliable service support.
> Labelmaster at Fineflexo – prints supported and unsupported labels, aluminum foils, light cardboard, tube laminates, shrink sleeves, IML, and much more.
In 1989, Mr. Narendra Srisrimal formed Medi Sales Group and further strengthened the operation with Bhavani Group, which Mr. Balakrishna Shetty formed in 1979. A joint venture between the two organizations extends its business gamut with Fineflexo.
Mr.Aayush Srisrimal, Director at Fineflexo, said, “We are dedicated to distributing sustainable, efficient, competitively priced products that a print buyer needs. We also serve the clients with our knowledge
and expertise by analyzing how their product should look so that we can prepare the best suitable labels for it and make a ‘Brand Appeal’ and enhance it.”
In the past, Fineflexo used to outsource the print jobs and later decided to install a Gallus Labelmaster 440 after examining the technical advantages such as diverse substrate handling, 200 m/minute production speed with absolute registration accuracy, userfriendly operation, and features, which can add more value to their labels, tube laminates, and aluminum foil printing.
The Finepet & Caps is a sister concern company, which is the largest converter for aluminum and tin stock in India with metal printing, petbottles, and ROPP caps. Medi Sales Group is one of the fastgrowing integrated pharmaceutical supply chains. The company offers a complete pharmaceutical business and logistics system that includes sleek warehousing, C&F, distribution, and wholesale operations.
Elaborating on the different business verticals
and explaining the need for the press, Mr. Ritesh Shettysays, “Our core business is manufacturing roll on pilfer proof cap, pet bottles, and metal printing. The manufacturing unit for the above products is at Rabale Navi Mumbai and Baddi, Himachal.”
He added, “We have been into metal printing for the last four decades. However, the metal printing venture was a backward integration for caps printing. In 2009, we started manufacturing pet bottles in Baddi. Currently, we are manufacturing approximately two million bottles daily for the pharmaceutical segment, bottle sizes vary from 10 ml to 1 Litre. In 2017, we ventured into the manufacturing of tube laminates. The reason to acquire Gallus Labelmaster 440 is to print labels for pharma bottles, tube laminates, and aluminum foils.”
The magnificent performance of Gallus Labelmaster 440
Talking about Gallus Labelmaster 440, Mr.Ritesh Shetty, says, “Gallus is a robust machine that gives us speed with stability. We saw the live press demonstration of Labelmaster 440 at ‘Avery Dennison Innovation & Knowledge Centre, Pune’. However, we did examine different brands of label presses, but eventually, we finalized Gallus Labelmaster because of Heidelberg’s reliable service support. Stable printing on composite substrates like Aluminum based laminates and Plastic based laminates at high speed, faster job changes, and quick setup times gave us confidence. To be consistent on quality, it is better to have in-house production facilities. With Labelmaster, we can achieve the same along with significant waste reduction controls and JIT deliveries with the perfect finish and print quality.”
“The Labelmaster is designed to print on everything that we require. With this, we print on supported and unsupported labels, aluminum foils, light cardboard, tube laminates, shrink sleeves, IML, etc. Labelmaster can handle a wide range of materials with different micron calipers. It was one of the reasons to have such a versatile press. The press is user-friendly, the setup time is significantly less, and the registration
is at par. Its’ a beautiful press, and we got everything we expected from Gallus,” added Mr. Shetty.
Shetty, says, “The Labelmaster is indeed a true ‘Work Horse,’ with technical upgradation and innovations from Gallus, our press is the latest generation ‘Gallus Labelmaster’ which gives extra savings in material, due to reduction in web length than the earlier version. Thanks to all the Gallus R&D team and their passion for making user-friendly equipment.”
On the development plan, Mr.Aayush Srisrimal, says, “Fineflexo is working towards being the leading supplier of labels in India. We focus on developing a robust product portfolio for our clients and fostering trust and customer satisfaction.”
“We offer smart label solutions through close collaboration with our customers, from idea to finished product. As a comprehensive printing company, we want to be a part of shaping the present and future of label and packaging solutions. With dedicated employees who have ambition and a great passion for their work, we print labels for everyone, today and in the future.”
“We create art with a scientific approach and top-notch technology. We believe that a label makes a product’s first impression and is a significant factor in consumer decisionmaking.”
The packaging for tablets and capsules requires different types of foils and laminates. A new division started by the Fineflexo group called ‘Finepharmapack’ allows them to add aluminum-based films and foils to its product offering.
This includes a 1300 mm wide coating and laminator from Italy capable of producing 12000 tons per annum. Mr. Ritesh Shetty, says, “We have an ambitious project to manufacture all kinds of foils needed for pharmaceutical packaging, like blister foils, including 90 varieties of cold-form foils, child-resistant, senior-friendly, peelpush, suppository/tropical, and adhesive laminates.”
“The project is presumed to be complete by the second quarter of 2023. After the
completion of the project, we will be a onestop solution for all pharmaceutical needs. Excellent sales and service with a dedicated team and technical consultation are the key factors in making our decision for Gallus Labelmaster. We are proud to be associated with Heidelberg India and Gallus.”
Mr.Narendra Kulkarni, Regional Product Manager, Gallus (Asia), says, “The versatile Gallus Labelmaster assists the user in reduction of cost per label. An Extremely shorter web path of just 1.4 m between printing units and a material reduction with the ‘Labelmaster r - 2 platform’ reduces the production wastage.”
Gallus Labelmaster has automation functions such as job pre-set, job data storage, format length corrections, print cylinder with bearer ring technology, and integrated direct servodriven systems, which helps users to do easy job setup and produce materials from 15 microns to 450 microns, even more. Watercooled impression rollers and electronic cabinets benefit the user with a maintenancefree operation.
Labelmaster can be configured to suit business needs and scalable at any point in time. Labelmaster presses are available in 340 mm, 440 mm & 570 mm printing widths. Simplicity, operator friendliness, diverse material & application flexibility, and stable performance guarantee investment security over the entire lifetime.
Gallus Labelmaster is a high-precision press with a solid build and industry-leading automation features, customization options, and technical enhancements, offering one of the highest price-to-performance ratios.
“Technology and automation are the keys to success in business, and the versatile Gallus labelmaster helps in our growth. With this thought, we went ahead with the latest generation Gallus Labelmaster which makes us ‘future ready’. This has given us great peace of mind that we can now focus on building the business without worrying about machine issues, we believe in the Gallus quality”, concluded Ritesh Shetty.
The bringing of plate production in-house, brings along a lot of advantages including the hassle free Process-free plate production for the Kala Amb based label and packaging converter.
Campolina is a Brazilian race horse known for its large size, colours and elegant movements. Manoj Arora took the inspiration from the speed, strength and elegance of the beautiful beast to lay the foundation of an inspiring printing business in Kala Amb, Himachal Pradesh. It was in the year 2010 when Manoj decided to quit his job in an export house to set up a printing business. One of his close relatives was running a pharma unit and they both worked on the idea of establishing Campolina Offset.
Process-free is getting greater acceptance now; customers with about 500 plates’ consumption are successfully running CtPs; over 250 Process-free CtP devices are running across the country.” – Mr. Natesh Puri, National Manager- Plates & Chemical and Packaging Segment at Eastman Kodak Company.
Those were the days of the Adast Dominant presses in India and he started with a 2 colour press producing labels and packaging for the pharma sector. Soon Campolina expanded capabilities with pasting and die cutting equipment and the manual pasting was converted to automatic in following years. It kept adding die cutting machines and had added another 4-colour Dominant press by 2015. Then it was the addition of an Autoprint Offline UV machine which was followed by a drip off UV machine, also from Autoprint. Autoprint technology played a crucial role in the initial journey of Campolina’s growth – due to the value addition, the packaging and converting business could strongly put off the competitive challenge and offer better solutions to its customers.
The latest milestone at Campolina is its recent Kodak Achieve Process-free CtP device installation. What makes the installation special is that the idea to install a CtP first came about a decade ago – when Manoj actually booked a CtP to eventually cancel it for quite interesting reasons. “We worked from a location which was adjacent to a heavy iron forging unit,” he shares. “The regular stamping there used to produce lot of vibrations in our whole facility. It actually made it impractical for us to install the sophisticated CtP then. Therefore, we dropped the idea for the time being,” he adds.
Now, when they have finally installed their CtP, the decision was instant and based on Manoj’s fondness for a process-free platform. “Going Process-free was the foremost reason. As we were suffering from many issues like inability to meet time schedules, quality and consistency, we were desperately looking for a way to bring the plate production in-house,” asserts Manoj.
“Though the cost factor was just a little downside, yet everything else was better about it. We were bringing an eco-friendly technology, which brought along ground breaking ease of operation and required fewer staff for even enhanced production,” praises Manoj.
Key Notes :
> When Campolina Offset went for Kodak Achieve CtP, going Process-free was the foremost reason.
> An eco-friendly technology featuring ground breaking ease of operation and requiring fewer staff for even enhanced production.
> CtP adoption today at earlier than ever entry-point of plate consumption as well as turnover.
Campolina Offset is led by the father and son duo of Mr. Manoj Arora and Mr. Vikrant Arora, who chose to join the family business instead of going to the US, the other carrier path he didn’t. Right now he is focused on the printing business and has his sight set on doubling their turnover in next 4-5 years. “The future of Campolina is in the next generation,” says Manoj, gesturing towards Vikrant. Under the vastly experienced guidance of his father, Vikrant looks forward to a growth driven by further streamlined processes. He sees ERP as the next step in their expansion/ standardization. The father plans to add a high-end printing press to expand the production capacity. “First step in standardization has been taken with Kodak Achieve CtP. Now further standardization of processes and streamlining them will create the smooth path ahead. The obvious course should be the press upgrade, then the ERP and so on,” envisages Vikrant.
The jobs, from order to delivery, are meticulously planned at Campolina. The jobs for the coming day are already forwarded to responsible people on the preceding day. Everything is finely laid out and tight schedules are followed to keep everything in order.
Both Majoj and Vikrant are very enthusiastic about their latest Kodak CtP. When asked about the entry point for printers to go for a CtP, Majoj fervently puts it anything around a Rs.5-6 Cr. turnover. “Process-free is fast catching up with Indian printers. CtP devices are being installed pretty quickly and regularly,” he confirms.
“Process-free is getting greater acceptance now. We have customers with about 500 plates’ consumption successfully running CtPs in their facilities. Today, we have over 250 Process-free CtP devices running across the country,” adds Mr. Natesh Puri, National
Manager- Plates & Chemical and Packaging Segment at Eastman Kodak Company.
“With the increased interest in environmental friendly technology of Process-free plate production by printers in India, we see a bright future for both the adoption of the technology as well as the success of its adopters” added Ashish Sharma of Aarushi Agencies who was instrumental in installing the Kodak system at Campolina Offset. It not only reduces process time; saves on labour, energy and chemistry costs; and brings consistency in quality; but also reduces the pressure on environment by conserving energy and reducing discharge of pollutants. With many leading the CtP adoption today at earlier than ever entry-point of plate consumption as well as turnover, there is an ample scope for thousands of print businesses to make this economically smart choice.
Former CEO of Aleyant, Trent Foreman joins Web-to-Print solution provider OnPrintShop as Regional Sales Manager, North America.
Web-to-Print solutions provider OnPrintShop has recently named Trent Foreman as the Regional Sales Manager for the North America region. Trent Foreman is an acclaimed print software and SaaS specialist. The former CEO of Aleyant, Trent Foreman will oversee OnPrintShop operations in the U.S. under the leadership of VP, Naresh Bordia.
Trent will resume his position in person during the Print United Expo to be held in Las Vegas, where OnPrintShop will be exhibiting its product enhancement innovations and capabilities in web-to-print software solutions. Trent is supposed to lead breakthrough changes in sales and corporate operations and for in-person support for OnPrintShop clients in the region.
Trent, with his niche knowledge about the core needs of the print service providers, is an advocate for leveraging technology tools for workflow automation and efficiency in production. Mr. Naresh Bordia, VP, OnPrintShip, mentioned, “With Trent on our boat, we expect curating strategic partnerships and flawless customer journeys
to our North America-based customers. We aim at dissolving the cultural barriers and want to extend seamless in-person support to our clients.”
He added, “Trent is a dynamic guy who believes exponentially in leveraging the power of collaboration and deserves to be the face of our expertise. The leading businesses of today are looking at disruptive ways to minimize operational silos and engage better with customers. And Trent
has a proven track record of building relationships and designing meaningful customer journeys. With Trent, ours is going to be a very mutually beneficial relationship, that will result in greater good for our venture.”
Having both - a custom licensed version and a hosted SaaS version, OnPrintShop is not just a solution for managing print order cycles but also provides custom web-to-print capabilities and web-to-print SaaS solutions.
The packaging producer of Kala Amb not only standardizes process but also takes advantage of the capabilities like compact footprint and run-length flexibility of the KODAK Achieve Process-free CtP.
In the year 1999, one of Kala Amb’s leading packaging businesses got established when Sh. Vijay Kumar Aggarwal decided to diversify from his ‘Kirana’ family business. His son, Mr.Anirudh Aggarwal was doing his graduation at that time and has remained a part of the business ever since. The young business had already installed its first fully automatic 5-ply corrugation plant by the year 2008. In 2010 they installed their first Offset Printing machine which brought their printing also ‘in-house’; earlier it had been outsourced to Narayana (Delhi). The company today produces mono cartons, flute cartons, fancy cartons and master box cartons and supplies to leading industries in the entire region.
Kodak Achieve process free CtP at Jai Ambey Containers – a perfect solution in terms of space, absolutely flexible in terms of offering runlength variability and standardization of the whole process with just one device.
All these years the plate requirements of Jai Ambey Containers Pvt. Ltd. were being met through PS (Pre-Sensitized) plates based workflow. Down the years when they started facing issues of quality and non-availability of films, they procured an old CtP. That CtP helped them to familiarize with the Computer-ToPlate process. They used that old CtP, also a Kodak, for quite some time. The present Kodak, the Achieve CtP is a state-of-the-art, process-free, advanced technology and absolute production friendly device.
hassles – including disposal of harmful chemicals as is the case with conventional systems. Moreover, Himachal Pradesh has stricter environmental norms than other places and having a chemical free production environment keeps you out of the usual passing, certification, approvals and audits etc. pressures.”
What played a deciding role in favour of the Kodak Achieve process free CtP were the device’s multifaceted advantages. It proved a perfect solution in terms of space, thanks to its compact profile. Another advantage was the run-length advantage –the device is absolutely flexible in terms of offering run-length variability to customers. Last but not the least was standardization of the whole process with just one device. “Anirudh and his team has been reprinting with the Sonora process free plates for almost all repeat jobs thus saving costs and adding to their bottom line – another advantage of having a Kodak process free CTP,” informs Natesh Puri, National Manager Plates & Chemicals and Packaging Segment at Eastman Kodak Company.
> Kodak Achieve –a process-free, environmentally friendly device and chemical free plate production platform.
> Eliminates associated hassles including disposal of harmful chemicals as is the case with conventional systems.
> Offers absolutely flexible in terms of offering runlength variability to customers.
“We are very impressed with the quality it produces,” says Anirudh. They installed the latest Kodak CtP last year in 2021. Describing the Kodak device, he says, “Being a process-free device, it went perfectly in line with our requirements – we wanted an environmentally friendly and chemical free plate production platform. It eliminates all the associated
“As demands increased and production expanded, it was high time to go for standardization of processes. CtP was one of the foremost areas we focused and hence the Kodak Achieve happened for us,” says Anirudh.
Though cost difference of a processed-plate and a process-free-plate was up by about 7-8% with the
new device, the advantages outweighed this marginal cost increase. Besides, there was less expense on processor as well as chemicals, which eventually led to more savings for the company. And, now they needed fewer operators for same production, and saved significantly in production time too. Environmental footprint and quality came in as extra bonus.
The Kodak Achieve platesetter has been supplied by Aarushi Agencies of Chandigarh. Ashish Sharma, MD of Aarushi is very happy about Jai Ambey Containers carving success under the able management of the son and father duo and coupled with the latest technology. The association between Jai Ambey Containers and Aarushi Agencies has been quite a long one. “We are associated with Ashish Ji since 2004. In fact, we were brought into Offset printing by Mr. Ashish,” says Anirudh.
Speaking about the Kodak Achieve installation, Ashish says, “We had been discussing the possible solutions to the issues of outsourcing, machine downtime as well as quality. Outsourcing to those who have different or non-standardized processes would create huge quality issues in final products.”
“Besides, there were security issues while sending customers’ crucial and trusted resources for outside job work. We took it as a moral responsibility to further strengthen our customers’ confidence in us,” asserts Anirudh. He corroborates with this particular incidence, “One of the tobacco products we did required a mono carton with high security features – it had features like heat transferred holographic sticker with foiling. Even that product faced duplication issues in the market with fakes surfacing as usual. This requires continued upgrade in security features to safeguard customer products.”
He showed us a few high security hologram sample they procured which carried a hidden image which revealed itself when put under bright light. He informs us that the highly secured hologram is for a client who usually gets it changed every 3 months to ensure that the product remains impeccably secure against counterfeits.
The business is ably managed by competent management, technical and other staff. There is also an ERP system to manage accounts, purchase, orders, sales, stock and reporting etc. Production, they are presently managing manually.
Besides, they have API Drugs, their Pharma division which manufactures drugs for the Pharmaceuticals Industry. Active Pharma Ingredients (API) supplies drugs to pharma manufacturing companies. The business was established in 2008.
The combined turnover of the automatic 5-ply plant and the Offset facility producing mono cartons, fancy cartons and other products presently stands at around INR 80cr. In 5 years Mr.Anuridh aims to achieve the INR 300cr mark. For this he is clear about infrastructural and other expansion plans. One of them is to set up another Offset mono carton plant in a year or so. All the different business divisions are collectively managed by the father and the son duo. The father chiefly handles the pharma business that comprises three units – one each in Kala Amb (HP), Panchkula (Haryana) and Lalru (Punjab). The latest being the Lalru unit which is coming up on a recently bought 10 acre land in the area.
They have a 6-colour Heidelberg and a 2-colour Heidelberg machine in the Printing division.
Printers’ queries on difficulties in making bills and filing returns get answered.
In order to clear the various doubts of members about GST and to explain the applicability of the constantly changing rates, categories, etc. on different printed products after the issuance of a number of notifications by the GST Council in the recent past, Delhi Printers’ Association organised a Seminar on 17th September 2022 at Har Krishan Singh Surjeet Bhawan in New Delhi. It was attended by a large number of concerned members. The initiative for the event was taken by the enthusiastic and energetic immediate former President of DPA Mr. Sunil Jain who was mainly instrumental in planning and perfect execution of all arrangements.
The Seminar was conducted by renowned CA Mr. Mohit Golchha of AGMS & Co., Ghaziabad. Former senior President of DPA Mr. Vijay Mohan welcomed the participants. Other eminent people included, former
President Mr. Mukesh Kaushik, President
Mr. Atul Goel, Hon. General Secretary Mr. Prakash Dass and Treasurer Mr. Puneet Talwar. Mr. C.L. Golchha, himself an eminent CA and father of Mr. Mohit Golchha, was felicitated. Mr. Mohit Golchha is known for his well-researched GST related services which he provides free for the benefit of printers. Mr. Golchha is President of the Ghaziabad branch of Terapanth Professional Forum.
Mr. Mohit Golchha explained the intricacies of the recent notifications in a simple and easily comprehensible way with the help of a power-point presentation. In a highly charged interactive session, he invited the audience to ask their questions. By citing relevant examples he successfully answered different queries including those pertaining to the difficulties faced by printers while making bills and filing returns.
Mr. Vijay Mohan praised Mr. Golchha praised for his dedication and efforts, which include his studying the complex mechanism of GST with special focus on printing industry. Mr. Golchha explained everything in a candidly simple way and was greeted by the audience with a standing ovation.
Mr. Dipeesh Arora, representing the the sponsor J.N. Arora Trading Company, got felicitated during the event.
2 Automatic Die Punching machines with Hot Foiling and one Dextra 80 Die Punching machine with standard features.
M/s. VMOM PTE LTD, Singapore, putting its trust in leading Indian brand Autoprint, has installed three of its Dextra 80 machines. Mr. Keng Swee TAN, Director VMOM visited Autoprint factory in Coimbatore to have a firsthand experience of the state-of-the-art Die Punching machine. He was so impressed with the machine’s performance that he placed order for three Dextra 80 machines simultaneously. Apart from installing one Dextra 80 with standard features, VMOM has also installed 2 Dextra 80 machines with Hot Foiling capabilities.
“Autoprint DEXTRA 80 – die punching machine can be used for various applications like Diepunching, creasing, perforating, kiss cutting, Blind embossing, Braille embossing and Hot- foil stamping” – K.G. Suresh – Joint Managing Director Autoprint Machinery Mfrs, India.
“We have recently added 3 nos. of DEXTRA 80 die punching machines, out of which 2 nos. of DEXTRA 80 have the special feature of hot foiling with creasing and embossing,” says Keng Swee TAN. “Another one is with standard features. All the three machines are to be installed by the 1st week of October 2022 at our premise M/s VMOM pte ltd., Singapore,” he adds.
M/s VMOM, Singapore is a well established and highly reputed packaging unit in Singapore serving the industry for the past 25 years. Mr. Keng Swee TAN leads the company with his rich experience in printing and packaging with an equally rich educational background of N. ARCH (Hons) UGS, GLA, UK.
Autoprint produces Dextra Die Punching machines in 2 sizes 22x32 inches & 19x26 inches. VMOM has opted for the 22x32 size which, says Keng Swee TAN, suits all their present and upcoming packaging jobs requirements.
“Autoprint DEXTRA 80 – die punching machine can be used for various applications like Die-punching, creasing, perforating, kiss cutting, Blind embossing, Braille embossing and Hot- foil stamping,” says K.G. Suresh – Joint Managing Director Autoprint Machinery Mfrs, India. “The main advantage of the machine is ‘maximum features with affordable price’,” he declares. “This has got commercial benefit of less space due to compactness, less power consumption, less make ready time, Easy to change various jobs and easy to operate with minimal training,” he further explains.
VMOM has decided in favour of the Autoprint Dextor fleet chiefly because of the machine’s capability to do smaller foot prints. VMOM will also be benefitting from swift switch of jobs with their new Dextor setup.
“Autoprint Dextra 80 is “Value for money”. The sincere support and coordination extended by Team Autoprint
> Singapore’s leading printing & packaging company installs three advanced Die Punching machines from Autoprint.
> VMOM’s Director personally visits Autoprint’s Coimbatore facility to finalize the esteemed order.
> “It is a true ‘value for money’. The reliability of the product is unmatched. Autoprint support is excellent,” says Keng Swee TAN.
in terms of clarifying all the technical aspects and their reputation for quality and after sales support, tipped the decision in their favour,” Keng Swee TAN commends.
Starting from digital printing to support F&B printing needs, VMOM has expanded to a vast range of products and application including those for amenity and operational needs. Their major milestones, according to Keng Swee TAN, include extending their gamut from ‘just ink on paper’ to value addition beyond ink, for example, Hot Foil on paper and other substrates.
Focusing largely on the F&B industries, VMOM has a technologically advanced setup housing the latest equipment that include capability to do Spot UV, lamination, paper bag making, book cover making and box making etc.
With the new capabilities enabled by the recently installed Autoprint Dextor 80, VMOM aims expansion into new areas of products and markets and chiefly sees seasonal festival items, especially Chinese red packets and similar products.
Keng Swee TAN is quite enthusiastic about his Autoprint Dextor 80 and readily recommends the technology to his fellow printer friends. “It is a true ‘value for money’. The reliability of the product is unmatched. Autoprint support is excellent,” says Keng, who sees obvious benefits for his customers by way of fast turnaround time and 3D emboss & 3D foil capabilities. “In addition, the special features of the machine will support to achieve OTD,” he adds.
As for their own special benefits, Keng underlines, “The machine has got special
features to reduce the make ready time and produce more no. of copies or jobs. In due course, it will surely bring improved efficiency in our day to day operations and would also help in getting faster ROI.”
The Autoprint Dextor 80 is built to handle the thickness of paper from 80 to 600 gsm. The double sheet detector and cross feed sensor minimize wastage. The heater plate for foil stamping has been innovatively designed to reduce the power consumption. Conforming to the CE standards, the machine competently answers operator safety and the overall machine safety. The machine features high level of operator friendliness and can be operated with minimal training.
Concluding by summarizing his whole Autoprint experience so far, Keng Swee TAN says, “The journey with Autoprint – from
the day of searching for the product till the final inspection of the machine – has been excellent. I found the entire company driven by systems. I hope that team Autoprint will reach greater heights in global printing industry. I wish them All The Very Best!”
Keng Swee TAN came to know about the Dextra 80 from a product video on the YouTube platform. He researched more and saw it for the first time at an existing customer place in Pinang. He was immediately impressed by its small foot print as well as robustness. Then he visited Coimbatore, met Autoprint people, had a firsthand experience, finalized the deal and now he has just one thing to say about Team Autoprint India and their worldwide support, particularly in his country Singapore, “It is Fantastic!”
Dieter Finna explains how well equipped is the Gallus Labelfire “Tube Edition” and the UVF01 inkjet series for use in industrial laminate printing.
It is no surprise that well-known laminate printers have entrusted product development at Gallus Ferd. Rüesch AG with the challenging task of bringing out a seamless printing solution for tube laminates. The printing press manufacturer was able to adopt some of the solutions for the complex task from the results of another development project. On folding cartons, where the solids extend beyond the ink edges, there are comparable requirements for the flexibility of UV inkjet inks as for tube laminates. The challenge lies in preventing the UV inkjet film from cracking under mechanical stress. For a long time, the only way to avoid cracking of the brittle ink film was to avoid solids that extended beyond the folds by necessity in the packaging design.
The cost-intensive substrate requires a machine concept that includes the shortest possible web paths as well as the option of print finishing.
For this reason, Gallus launched the “Flexible UV Inkjet Ink” project for folding carton printing along with a well-known brand manufacturer at the start of 2019. The complex development project took three years to complete, including all the development steps, suitability tests and six months of ink qualification. For product qualification, the brand manufacturer printed more than 900 km of board on a Gallus Labelfire 340 and produced around 8 million blanks.
The requirement criteria in printing were for the ink film to be fully cured at a printing speed of 70 m/ min and for a scratch-resistant, flexible ink film. In the packer test, blanks printed over the entire surface had to be able to be processed at 1,000 packs/minute without ink cracking. In addition, the UV inkjet printing ink had to pass the sensory test
> Printing on tube laminates using UV inkjet poses several application-specific challenges.
> The tubes, which are bent and crushed during squeezing, require a flexible ink film.
> It must adhere well to the substrate, must not crack during handling and must meet all compliance requirements.
programme in the tobacco sector and fulfil all the requirements in the Regulatory Compliance & Toxical Assessment. This included the composition of the UV inkjet ink according to Swiss Ordinance requirements, the REACH conformity test for chemicals, the requirements of the RoHS Directive 2011/65EU and the EUPIA exclusion list for defined raw materials as well as proof of freedom from substances with carcinogenic, mutagenic or reprotoxic effects. The UV inkjet ink system developed in the project with the product name “UVF01” passed the tests and has been released for commercial production in the brand manufacturer’s folding box production since the beginning of this year. This provided the prerequisites for transferring the results of flexible UV inkjet inks from folding carton printing to the
solution approach for tube laminates.
Modifications to the Gallus Labelfire 340 were necessary to use the UVF01 ink system. These related to the drying technology and web guide. The latter had to be designed for the shortest possible web paths for the costintensive substrate.
Gallus has broken new ground in radiation curing. In the Gallus Labelfire version for the new flexible UV ink system, UV-LED curing systems replace the mercury vapour lamps previously used. The advantage of UV-LED technology is that the energy penetrates the ink layers more effectively thanks to the high
intensity of the UV-A beams, resulting in more uniform curing. Due to the high intensity of the UV-LEDs, the use of boosters to intensify drying can be dispensed with. This means that the temperature-sensitive tube laminate can be processed without heat effects. As an additional measure, inert gas is used for fast and complete curing of the ink film wherein cross-linking of the ink film in the inert chambers takes place in the absence of oxygen, which has been replaced by nitrogen in the sealed environment. The oxygen content in the inert chambers is continually monitored by sensors and kept below 500 ppm. The increase in curing performance achieved, as well as the reactivity of the photo initiators result in complete curing of the ink film at a printing speed of 70 m/ min. An added benefit is that a very good adhesion of the ink to the substrate is achieved without the use of primers.
The machine layout of the modular Gallus Labelfire “Tube Edition” was designed to keep the web path in the machine as short as possible. Therefore only a single rewinder is used instead of the double rewinder. When selecting the flexographic printing units, the company opted for the Gallus ECS series. The main advantage of these printing units is that they have an ultra-short web path of just 1.1 metres from printing nip to printing nip, which significantly reduces waste during makeready and production. Given the high material costs of tube laminates, this is a major factor contributing to high profitability in the printing process. For example, the web path between unwinding and rewinding on the “Tube-Edition” is only around 25 m, compared to around 80 m on a comparable press for tube laminate printing. What’s more, the servo-driven Gallus ECS
printing units allow for maximum substrate flexibility when using different thicknesses of laminates. The press layout of the Gallus Labelfire “Tube Edition” features the centrally arranged UV inkjet digital printing unit DEU, with an upstream and a downstream flexographic printing unit. The arrangement combines high print quality in digital printing with the cost benefits of flexographic printing, even for motifs with high ink coverage. The
The family-owned company, founded in 1958 and headquartered in Rorschach, Switzerland, is divided into the divisions “Labels & Flexible Packaging” and “Construction, Industry, Retail”. Labels and packaging are printed in the in-house print division, with a growing share of laminate films for tube production. The target markets are the non-food, food and cosmetics sectors. Collaboration with Gallus in the print sector dates back to the company’s early days and continues to find expression in innovative products. To this end, Permapack’s printing experts make use of the technical possibilities offered by the company’s modern machinery and create highly unusual designs and products. The European Tube Manufacturers Association (etma) named Permapack’s paper tube “Tube of the year 2021” in the sustainability category.
(Image source: Gallus Ferd. Rüesch AG)
upstream printing unit is used to apply spot colours, cold foil or a primer (if required), while the downstream unit is used to apply the protective coating over the entire surface. At the user’s request, the digital production system can also be supplemented with an additional cold foil unit.
Once the press concept and the ink series were available, the next step in the project was a practical comparison of digitally and conventionally printed tubes. This allowed an evaluation to be made as to whether, or to what extent differences between the designs were recognisable based on defined quality criteria. To this end, Permapack AG contributed its printing expertise in laminate printing to the project producing the conventionally printed tube samples. These were printed on a Gallus RCS 330 as a benchmark for digital printing and joint assessment with Gallus. The digital benchmark samples were printed on a Gallus Labelfire 340 running in industrial use and equipped with the “UVF01” inkjet series and modified dryer technology. The designs for the benchmark and the different tube laminates were selected according to typical market requirements.
“During the tests, we found that the adhesion and flexibility of the new flexible UV inkjet ink showed good values. The digitally printed tube material could be processed in the same way as conventionally printed material,” Günther Forster, Prepress Manager, Business Unit Printing Product Manager Cosmetics at Permapack AG, describes the evaluation of the test results.
The test results with the UVF01 inkjet ink showed excellent results across all fastness requirements for the tube laminates PBL and ABL, which are predominantly used in the market, as well as on paper laminate. The evaluations exclusively show results in the “1-very good” range. “During the tests, we found that the adhesion and flexibility of the new flexible UV inkjet ink showed good values. The digitally printed tube material could be processed in the same way as
conventionally printed material,” Günther Forster, Prepress Manager, Business Unit Printing Product Manager Cosmetics at Permapack AG, in describing the analysis of the test results. Only the digitally printed PP laminate, which is only used to a very limited extent on the market, showed a deviation in the aging test. With PP laminates, printing conditions and inkjet inks still need to be modified somewhat.
The Gallus Labelfire “Tube-Edition” together with the flexible UVF01 inkjet ink presents itself as a pioneering alternative to purely conventional tube printing. Thanks to the high native resolution of 1200x1200 dpi, digital printing can score points in terms of print quality by outperforming the motifs usually printed in 54 screens in flexographic printing.
Besides print quality, the economic efficiency of a production system is the decisive criterion for its industrial use. Here the machine system meets a market situation in which run lengths in the tube market are declining. Since short to medium run lengths are a strength of digital printing, it can also demonstrate its strengths here. A break-even analysis of the costs of the print samples from the print comparison shows that the digitally conventionally printed runs up to a run length of approx. 5,000 running metres are cheaper to produce than purely conventionally printed tubes. With a standard tube of 200 ml, this corresponds roughly to a quantity of 53,000 tubes and is considered an average run length in tube printing.
This project provided all of the evidence that qualifies the flexible UV inkjet ink for use in tube printing. This means that the Gallus Labelfire “Tube Edition” and the UVF01 inkjet series are now ready for use in industrial laminate printing.
The second generation Vistaflex fully automated CI printing press is the latest introduction by Windmöller & Hölscher.
Windmöller & Hölscher (W&H) has launched the VISTAFLEX II, a wide-web, CI flexographic press with upgrades for enhanced performance, improved print quality, and easy job changeovers.
W&H launched the original VISTAFLEX in 2008 for a small segment of high-end printers in the flexible packaging market who required a workhorse wide-web press that could run jobs 24/7 at speeds of up to 800 m/min (2,620 ft/min) with quick and easy job changeovers. Unique features of the press were the ability to prepare and store four additional jobs while the press was running and to execute fully- automated changeovers with two high-speed robots by pressing a button.
The VISTAFLEX II, available as of August 2022, provides all these same features along with technical upgrades and a fresh, modern look. “When we started conceptualizing how and what to update on the VISTAFLEX, we realized, what an exceptional press it still is well over a decade after its inception. To make the press even better for our customers, who run these machines extremely hard over prolonged periods of time, we started with improving the bearing system to increase stability and print quality,” said Hermann Veismann, General Manager for Printing and Finishing at Windmöller and Hölscher.
“Automation and assistance systems are making a dramatic difference in production efficiency, by shortening changeover times, minimizing waste, and making the process more straight-forward and easier for press operators. With this top of mind, we integrated W&H systems directly into the VISTAFLEX II,” added Dr. Holger Kreilkamp, Team Leader Product Management.
These include an improved CI drum cleaning system, which is particularly beneficial for paper and non-woven products, EASY-SET and EASY-REG for automated impression and register setting, the W&H VISION for web monitoring and defect detection, and the TURBOCLEAN ADVANCED E, which is
W&H’s resource-efficient, award-winning washing and inking system.
Also available is the RUBY IoT platform. Coupled with Connect 4 Flow the system creates a direct link between a customer’s ERP system and the press, which allows jobs data to be sent remotely for automated smart job queueing and optimized workflow.
The VISTA-PORT, where prepared cylinders and sleeves are stored, then organizes the integrated cylinder magazine automatically and prepares the necessary robotic changes. This concept is unique on the market and designed to bring the future of autonomous printing closer.
In addition, W&H has developed the FILMATIC II C winder to complement the press. The new non-stop, high-performance
winder is available with an integrated slitting module. At maximum speeds, even extremely sensitive substrates that can be difficult to wind, such as breathable films and nonwovens, can be cut into very small ups and wound with straight edges.
Over 100 of the original VISTAFLEX presses are being used by customers in Europe, North America, and Asia to print on paper and film, as well as for special products from the hygiene sector such as non-wovens or back sheet films. While the press is typically used for long runs, especially in large-format printing applications such as for beverage packaging (up to 1,250mm / 49.2” repeat), it is also extremely efficient for short jobs with many changeovers due to the fast, fullyautomated changeover robots.
Label Traxx, provider of Print MIS/ERP solutions for labels and flexible packaging segment to merge and deliver unified and end-to-end solutions.
Label Traxx, provider of Print MIS/ERP solutions for the labels and flexible packaging segment, recently announced its intent to merge with two key partners: Siteline, web-to-print and sales portal/CRM, and Batched, automated scheduling and capacity planning.
This merger will create for the industry a fully integrated, end-to-end production solution designed specifically for the labels and flexible packaging market. Label Traxx participated at the LabelExpo Americas 2022, and was present at Booth 5920.
For the last six years, Label Traxx has collaborated with Siteline to develop and deploy a web-to-print solution that enables label customers and distributors to reorder, approve artwork, pay invoices, and manage their label product catalogs online. Siteline’s software integrates seamlessly with Label Traxx to provide a modern customer experience while maintaining Label Traxx as the system of record. Customer experience with this integration has reduced the time jobs spend in customer service by two days or more, resulting in jobs getting to press faster.
For the last three years, Label Traxx has collaborated with Batched to develop and deploy production optimization solutions specifically targeting the unique needs of label printing; including automated scheduling, capacity planning and operational dashboards. The Batched solution enables production teams to thrive under the pressures of supply chain constraints, the growing demand for short run digital, and shorter turnaround times along with more traditional, long run flexo operations. This integration allows production operations to more efficiently schedule and manage increasingly complex, multi-step production environments.
“We are approaching our 30th year in business; over the last six years we have cultivated partners to accelerate our innovation. Now it’s time to consolidate the portfolio and the teams to bring a wellcoordinated and seamless solution to the industry,” said Ken Meinhardt, Label Traxx Co-Founder.
The shared history and ethos of these companies make this merger a culmination of many years of partnership. All three solutions have roots back to ILS Labels of Ohio and its former owner, Jay Dollries. Label Traxx and ILS collaborated on their traditional flexo workflows as well as support for each new HP Indigo press, and Siteline and Batched were solutions built to meet ILS Labels’ evolving and growing business needs.
Label Traxx, Siteline, and Batched have similar cultures, believing that software that delivers a return on investment is built iteratively with the customer, not theoretically by committees several steps removed from the customer’s reality.
Traditionally, web-to-print as a solution segment in the print industry has either focused on direct-to-consumer applications (B2C) or specific solutions for customers who have large catalogs that need to be ordered by large groups of people (e.g., franchises, sales teams, resellers). Siteline is a web-toprint solution designed specifically for the current customers of labels and packaging printers. These brands exchange hundreds of emails daily with their labels and packaging partners, which can cause confusion, errors and delays. Siteline is specifically designed to improve how label buyers interact with printers, consolidating these communications into a single view.
“I have been in the commercial web-to-print
space for 25 years,” commented Jennifer Matt, Siteline’s founder. “In 2017, I immersed myself in the label segment with Steve Smith, founder of Lightning Labels and Wizard Labels. My company helped evolve Wizard Labels from a prototype to a scalable B2C solution as well as integrating it to Label Traxx at ILS. I saw the need for a specific solution to address the tremendous labor required in customer service as well as the need for an online portal for existing B2B customers. Siteline is designed to provide customers convenient online access which results in jobs on press days faster using less labour.”
Label converting is more than just printing, it can involve three, four, five, and sometimes six different machines in a single order. Scheduling at any scale has exceeded the capacity of even the most skilled and tenured employees. Schedulers deserve a set of tools that enable them to thrive under these complex situations.
“Batched is focused on deploying tools to support the operations and supply chain functions of the label printer,” Matt Murphy of Batched stated. “We started with automating the scheduling process and have since added capacity planning and operational dashboards. These dashboards allow the printer to literally measure their ROI daily. Our roots are in the shop floor, and we know how important it is for software to make the lives of our customers easier, as well as add real value and profit back into the business.”
The ownership / leadership group will consist of Ken Meinhardt (Label Traxx), Jennifer Matt (Siteline), and Matt Murphy
(Batched), with no outside investors. Rob Mayerson will lead day-to-day activities and the consolidation of operations as President. “Label customers of all sizes are participating in rapid consolidation,” Mayerson noted. “We are investing in the ability to service growing organizations with the upcoming
release of Label Traxx Enterprise, which will support multi-site operations. Siteline and Batched are tightly integrated into Label Traxx while at the same time ‘loosely coupled’ to Label Traxx which means that in mixed ERP environments, Siteline and Batched will be able to work across the Enterprise. The new
REST API from Label Traxx will extend the ability to connect Label Traxx to external systems.” “Label Traxx is looking forward to this new step in its journey to provide a best in class, end-to-end, solution for its customers,” Meinhardt concluded.
Mr.Amit Gera of White Print O Pack based out of Baddi in Himachal Pradesh speaks to PRESSIdeas about their installation of KODAK process free Computer to Plate (CtP) in-house at their premises.
For Amit, acquisition of plates for his unit from a service provider was turning out an expensive proposition. Moreover, the process was time consuming. There were usual incidents of plates getting spoiled in the middle of a job or worse still in the middle of the night to force them to take the whole job off the machine. Both the business as well as the customers had to suffer due to this. Amit was already looking for an in-house CtP solution to end this volatility when he came up to his decision about Kodak.
White Print O Pack is based out of Baddi, Himachal Pradesh and caters to the Pharma sector broadly present in the region. The company that started its operations in 2004, has been on the growth drive from the very first day. Mr. Amit Gera, CEO of the company has led the company to great heights with his professional acumen, readiness to adopt the latest technology and dedication towards engaging customer relationship.
With a consumption of about 1200 plates per month to cater to their five Offset printing machines (of Heidelberg as well as KBA brand), the decision, says Amit, was long overdue. “We use three different sizes of plates for our five different offset machines. We had been looking for a solution to end dependence on outside sources for quite a fair time. Though it took a while, but at the end of the day we are very happy to bring this key process in-house. It not only ended our dependency on outside sources but also brought quality and efficiency to our operations,” says Amit.
With the Kodak CtP well in place and running to feed their multiple press set-up, the workload has lightened, job handling has eased and a very environment friendly process has come about.
White Print O Pack has most of its jobs in the short run format though long runs too are a regular event. Their undertaking rarely requires the plates to be stored for repeat use. Amit finds the Kodak Achieve a real boon considering the advantages of going process free. Apart from being environmental friendly, the technology also helps them serve their customers better with quality, timely deliveries and consistency.
“The quality issues and delay in times of urgent needs of customers are gone things for White Print O Pack, thanks to the in-house plate production with Kodak Achieve,” says Mr.Natesh Puri of Eastman Kodak Company. “The wastage of time and efforts in procuring from different trade shops in the area was a key pain area in smooth day to day functioning. Amit ji was very excited about the technology from the first day because of its being a green environment friendly product,” adds Ashish Sharma from Aarushi Agencies, Chandigarh.
“Commissioning a completely green technology from the house of Kodak brand was enough for me to make a decision in their favour,” declares Amit.
White Print O Pack was the first company in the Baddi region to get the process free technology from Kodak and since then, there has been more than nine installations in the area. The advantage of installing the system in a small space without the paraphernalia of placing a plate processor plus disposal of chemicals into the drain also added to the advantages that any printer would appreciate while going for a process free technology. And the technology being a Kodak technology brings a big smile for obvious reasons.
When we asked Amit, why would one go for the Kodak CtP, he states, “Standardization of the entire pre-press is one big advantage the printers would find enticing; at least it was the case for us at White Print O Pack.”
Brings plate production in-house to save time, manpower and job secrecy.
WeePac, one of the leading names of Surat providing a wide range of quality packaging solutions has recently installed a Cron CtP from Nippon Color.
In the past 20 years, WeePac has established itself as one of the front runners in the industry. The skilled professional staff at WeePac meticulously carries out diverse jobs of their clients and ensures on-dot deliveries. They are well trained to guide customers on technical aspects and choice of right materials. “We pride ourselves in our services that are timely, swift and efficient,” says Mr. Rajesh Sangani, Director WeePac. “Our packaging range is exhaustive – from folding cartons, printed blanks and outers, litho-lamination, plastic cartons, blister packs and shelf-ready packaging. At our 30000 sq. ft. Facility, we’ve developed every service needed to make you more competitive in your marketplace all under one roof,” adds Rajesh.
Along with Mr. Rajesh Sangani, Director, Mr. Naimesh Naik, Managing Director is at the forefront of WeePac.
The recently installed Cron CTP model is a Thermal 48 channel device TP-4648G+. “This is the latest redesigned model with new appearance, integrated output device, user friendly control interface and brandnew touch panel operation, which bring a more friendly human-computer interaction experience,” says Naimesh, elaborating on their latest acquisition.
The Thermal CTP is capable of churning out 24 plates per hour and can make plates of sizes up to 1030 mm. The modern device features square dot imaging, which it achieves by the adoption of optical technology, resulting in accurate reproduction of dots with minimum error rate ≤1%. Plate making resolution range includes 1800/ 2400/ 2540/ 2800 dpi, suitable for AM/ FM/Hybrid screening ≥ 300 lines per inch, 10-micron FM screening print. This highly capable machine enhances the scope of business adaptation of printing enterprises. Furthermore, higher resolutions of 9600/10160 dpi are achievable with upgrade
to cater to exquisite printing.
Earlier to Cron CtP, WeePac was purchasing plates from 3rd party which would take time and it was not possible to meet every urgent plate requirement of clients. “Moreover, as a part of our job secrecy we decided to buy one to meet the demand in-house,” says Rajesh.
In fact, they explored other brands, but found Cron as the best investment and the other key factor being the partnership with Nippon Color.
“We were looking for something which produces high quality plates at a competitive price and found Cron’s system to be very economical,” notes Rajesh.
WeePac currently offers a complete package of solutions that include personalised customer service, prepress, design, hard proofing, addressing, mailing, inventory management, logistics and distribution.
A fully equipped infrastructure caters to the production and services WeePac offers. The set-up includes 2 Offset presses, machines for punching, pasting, window patching pick & place, high speed laminator, foiling unit and coating unit etc. in addition to this plant, they are coming up with their new plant shortly.
“We were getting our plates from local supplier. Now this investment is saving time for our job and of course manpower to manage plates coming from supplier. In-house platemaking is cheaper, faster, and easier to do corrections,” sums up a happy looking Rajesh.
Sharing ‘the best thing’ about the Cron CtP, he declares, “The machine is easy to use and
is low maintenance due to its single mode fiber optics. Also the online punching unit in the CTP itself is a great feature.”
He is very impressed with the support from Nippon Color. “The device is quite easy to use as our employee got very good training from Nippon engineer. The configuration is online – meaning the plate from the CTP is automatically fed into the plate processor,” reveals Rajesh.
The Cron CtP, capable of running any thermal plate, is currently converting from 10 to 12 running meters per day at WeePac. Currently WeePac is utilizing locally sourced plates and would look into bulk purchase options once production reaches the stipulated level. “There are Nippon long run double layer thermal plates too, which is among the top options,” says Rajesh.
Along with Cron, WeePac has invested in a Shangzun TPD-1100 Plate Processor, which is a heavy duty plate processor with in-built conductivity meter, water saving and re-wash slot.
On the WeePac installation, CEO of Nippon Color, Mr. Jayant Pardiwala comments, “WeePac is a team of professional printing experts who are setting a benchmark in the Indian printing industry while matching international standards of service. We are thrilled to be associated with them. We have formed great relations with Mr. Rajesh Sangani and Mr. Naimesh Naik in a very short time and look forward to a long healthy association.”
Harveer Sahni is the winner of the 2022 R. Stanton Avery Global Achievement Award.
The results of the label industry’s prestigious global awards were announced on the opening night of Labelexpo Americas 2022.
The winners were chosen by a judging panel consisting of Lori Campbell, chairman of TLMI, Linnea Keen, president of TLMI, Philippe Voet, president of FINAT, Greg Hrinya, editor of Label & Narrow Web, James Quirk, then group editor of Labels & Labeling, and Jean Poncet, editor-in-chief at Etiq+Pack. The chair of the judging panel was Andy Thomas-Emans, strategic director Tarsus Labels & Packaging Group.
As previously announced, the winner of the 2022 R. Stanton Avery Global Achievement Award is Harveer Sahni. The judging panel felt Harveer meets all the criteria for excellence demanded by the industry’s most prestigious award for an individual’s contribution to the growth and development of the global labels industry. His history in building a company to manufacture self-adhesive labels in India, through to his central role in building the Indian label association and then acting as an influential ambassador on the world stage, all helped the judging panel to come to their decision.
The Rising Star Award went to Stijn Billiet, Global Sustainability Director, MCC Label. Stijn joined MCC in 2020 and made an
immediate impact bringing sustainability onto the agenda of the business. Early 2021 he presented a roadmap for all global production sites to reduce their carbon footprint, guiding the Belgian facility to carbon neutral production. Stijn represents MCC in its collaboration with organizations such as Holy Grail, RecyClass, APR, and CELAB. The judging panel felt Stijn has demonstrated clear potential to be a future leader and is already a strong voice within the labels industry.
The Environmental Sustainability Award was won by Flint Group Narrow Web for a new line of products designed to enable more sustainable packaging. The first product in the series, Evolution Deinking Primer, when used with Flint Group EkoCure XS inks, enables deinking of crystallisable shrink sleeves, allowing the clean sleeve label material to be recovered and recycled into PET packaging. The judging panel felt that the Evolution Deinking Primer makes a major contribution to developing a circular lifecycle for label materials.
The Innovation Award for companies with over 300 employees went to Actega for its Signite decoration technology. Utilizing the latest in UV-curable chemistry, Signite decorations are created entirely on press, eliminating the need for the
laminated constructions used in traditional pressure-sensitive label production. Signite decorations are built in register with the graphics and label content, so there is no die cutting and no matrix to dispose of. Signite decorations are applied with a specialist inline applicator developed by Actega, initially for glass straight-walled containers. The judging panel felt this to be a step change in the way label decorations are produced and a major contribution to industry sustainability.
The Innovation Award for companies with under 300 employees was awarded to S-OneLP for its ReEarth compostable flexible packaging films. ReEarth films have achieved ASTM D6400 commercial compostability standards and are both BPI and USDA Biopreferred certified. A compostable print film, adhesive, and sealant layer make up this laminated structure that can be surface printed with digital or flexographic technologies. The judging panel felt that with more label converters diversifying into flexible packaging products, a fully compostable solution is a great aid to future packaging industry sustainability.
The Rising Star award is sponsored by Avery Dennison; the Environmental Sustainability award is sponsored by Labels & Labeling; the Innovation Award for companies up to 300 employees is sponsored by Flint Group Narrow Web; and the Innovation Award for companies over 300 is sponsored by Xeikon.
- Launches the next phase of ‘NEVER STOP SCREENING TO REDUCE DIAGNOSTIC DELAYS’ Campaign to promote early diagnosis of TB.
Fujifilm India, a pioneer in diagnostic imaging and information systems for healthcare facilities, has launched the second phase of its campaign on TB “NEVER STOP: SCREENING TO REDUCE DIAGNOSTIC DELAYS”. The second phase of this campaign aims to increasing awareness on TB as a curable disease and promote screening and early diagnosis among tea sector workers, difficult to reach population in rural and urban areas including tribal population in selected districts of Gujarat, Kerala and Assam. Under the campaign, Fujifilm India will support three mobile hand held X-ray machines and implementation of project in community settings
Fujifilm aims to reach to more than 5 million people and screen around 30,000 of them by using the handheld X-ray machines. The project will also facilitate TB testing of identified presumptive cases. In association with International Union Against TB and Lung Disease (The Union), the project aims to demonstrate a model on promoting early diagnosis for TB by utilizing newer solutions in community settings. Through the campaign, Fujifilm will be offering door-todoor awareness on TB and provide mobile digital X-ray services along with Qure. ai’s computed aided radiology software application designed with deep-learning for the intervention.
The proposed districts in this phase are Sonitpur, Golaghat, Jorhat, Sivasagar, Dibrugarh, Tinsukia, in Assam, Wayanad in Kerala, and Kutch district in Gujarat starting September 2022 and conclude by August 2023.
In the first phase, Fujifilm India screened over one million people and shared around 8,000 X-ray reports. Through the intervention, 117 new TB patients were identified across 27 cities including Delhi, Dadri, Dehradun, Haridwar, Haldwani, Rudrapur, Patna, Jaipur, Indore, Kolkata, Raipur, Pata, etc.
Speaking about the success of the campaign, Mr. Koji Wada, Managing Director, Fujifilm India Pvt Ltd, said, “We at Fujifilm
have always been dedicated to offering the best medical innovations and technologies to improve the quality of life around the globe. Following the success of the first phase of our NEVER STOP: SCREENING TO REDUCE DIAGNOSTIC DELAYS campaign, we are extremely happy to complement government program in selected districts by reaching the underserved sections of society. As a diamond member of Corporate TB Pledge initiative, we’re closely working with the National Program to make India a TB-free country and will continue to support this endeavor in the coming months. We are determined to Never Stop innovating and making the world a healthier place.”
Fujifilm is a diamond member of Corporate TB Pledge (CTP), which is being implemented by International Union Against TB and Lung Disease (The Union) as part of USAID supported iDEFEAT TB project. Corporate TB Pledge initiative was jointly launched in 2019 by Government of India and USAID to galvanize corporate support in the fight against TB. More than 230 corporate
partners have joined the Corporate TB Pledge initiative.
In line with the Government’s call to achieve the SDG targets related to TB by 2025, five years ahead of global targets, Fujifilm India aims to raise awareness about tuberculosis as a curable disease among hard-to-reach groups and facilitate early diagnosis of TB ultimately improving people’s quality of life. While tuberculosis is a serious disease, it is completely curable if diagnosed in time and the treatment is completed.
Beginning as Japan’s pioneering photographic film maker, Fujifilm, established in 1934, has leveraged its imaging and information technology to become a global presence known for innovation in healthcare, graphic arts, optical devices, highly functional materials and other hightech areas. Fujifilm is continuously working towards early detection of disease and generating awareness among the general public by conducting awareness programs, for promoting TB and Cancer screening.
Roll-to Roll printer for printing high quality indoor and outdoor signage applications.
Focusing on future technologies, innovation budget-friendly products and step towards green printing, Monotech Systems has launched Pixeljet LEO 3200 a10ft. UV LED roll-to-roll printer on the first day of Media Expo, New Delhi.
“Our priority is to facilitate every mid-range users to switch to UV and this product has been designed keeping in mind those who are also looking for a migration from eco solvent to UV printing on a pocket-friendly budget. This new launch is an addition to Pixeljet Roll-to-roll category which is capable of printing high quality graphics for Signage applications. Pixeljet LEO3200 is available with the RICOH industrial grade print heads which is the most popular printhead when it comes to the UV printing technology,” says Manoj Garg, GM, Wide Format Graphics, Monotech Systems.
“The Ricoh industrial grade printhead offers enhanced productivity that enables “LEO 3200” to deliver a printing speed of up to 70sqm/hr. (based on the printhead and colour configurations). It also brings the media versatility and enables printing on a wide range of indoor and outdoor applications such as transparent materials,
self-adhesive vinyl, outdoor materials, films, leather, and also on décor applications such as wallpapers, window blinds, wall decals, canvas etc,” adds Manoj.
The New Pixeljet LEO 3200 roll-to-roll printers is available in six- and four-colour versions. The Pixeljet LEO 3200 is equipped with a UV LED lamp, allowing users to print on a variety
of media and save energy, cost and time.
One of the main features of this printer is its 6-colour optional varnish plus white and clear ink version, which can print white in different modes, improving the opacity of printed materials, increasing colour contrast and readability. It also delivers embossing effects for various digital decorations.
Labelexpo India 2022
Date: 10 NOV -22 to 13 NOV-22
Venue: Expo Centre & Mart Greater Noida - Delhi NCR
Date: 07 DEC-22 to 09 DEC-22
Venue: Nanjing International Expo Center
Date: 27 MAR -23 to 30 MAR-23
Venue: Bombay Exhibition Center, Mumbai Screen Print India
Date: 13 APR -23 to 15 APR-23
Venue: Mumbai, India
PRINT & DIGITAL CONVENTION 2023
Date: 16 MAY-23 to 17 MAY-23
Venue: Congress Center Süd Düsseldorf
Labelexpo Europe 2023
Date: 11 SEP -23 to 13 SEP-23
Venue: Brussels Expo Centre, Belgium
All in Print China
Date: October 2023
Venue: New International Expo Center Shanghai
drupa 2024
Date: 28 MAY -24 to 07 JUN-24
Venue: Brussels Expo Centre, Belgium