
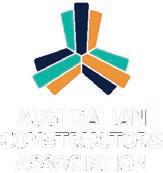
One of our projects welcomes a local school for a site visit on a community open day.
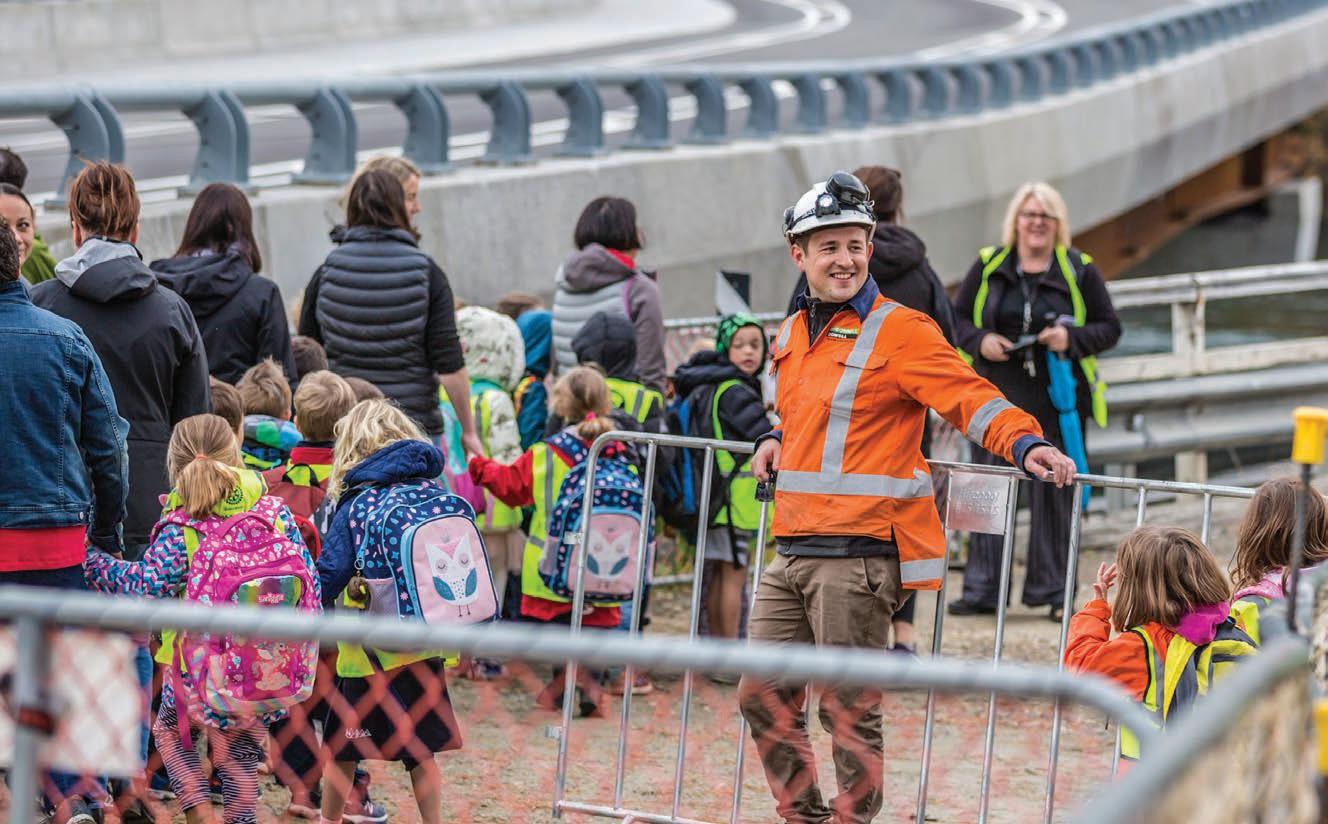
One of our projects welcomes a local school for a site visit on a community open day.
We’re making a positive and meaningful difference to the health, well-being and prosperity of our people and our communities.
Scan here to find out more.
16
APRIL/MAY 2023
This
Construction Industry Solutions explores how its software helped Balance of Plant company Zenviron improve productivity and efficiency.
21 Beyond the surface
Find out how Trimble’s augmented reality technology is helping Survey Management Solutions streamline the delivery of its projects.
24 Building bridges
McConnell Dowell and Australian disability enterprise Vivid look into the positive outcomes of their partnership on the Echuca-Moama Bridge Project.
29 The
Women in Construction announces its sponsorship of the Excellence in Construction Award at this year’s Women in Industry Awards.
The National Association
32
Advocacy Australia’s Alice Collins delves into the importance of asbestos waste management and awareness.
CDE Group provides insight into how its wet processing equipment and technology is reducing construction waste around the world.
36
Dr. Gretchen Gagel discusses the waste associated with relationship breakdowns on construction projects.
If one thing is clear in 2023, it’s that the Australian construction industry is taking long overdue action to address the major challenges its facing – and the future is looking bright.
We entered 2023 facing a skilled labour shortage, rising costs and poor productivity, among other challenges. Despite this, the construction industry came into the new year ready, with innovative solutions and an invigorated fire for breaking old industry moulds.
Businesses are introducing a wave of new technologies and processes to tackle these industry challenges head on. As the movement towards sustainability and zero carbon emissions accelerates across the nation, we’re seeing a lot of these innovations in the construction waste and recycling sector.
During the 2020-21 financial year, Australia generated an estimated 75.8 million tonnes of waste, with building and demolition materials making up over 30 per cent of the total, according to the National Waste Report 2022 That’s a whopping 25.2 million tonnes of waste in Australia being generated by building and demolition works.
But the construction industry isn’t standing idly by in the face of these staggering statistics.
This month, our Construction Waste Showcase puts a spotlight on the companies, organisations and industry leaders driving the reduction and improved management of construction and demolition waste. It highlights the solutions that will enable construction businesses to harness the power of material re-use and recycling, to create a brighter future for our industry.
The decline of productivity in the construction industry in recent years is another serious form of waste that needs to be addressed as soon as possible by industry and government.
McKinsey & Company’s 2017 report, Reinventing Construction: A Route to
Higher Productivity, finds $1.6 trillion of additional value could be created through higher productivity in the construction industry.
We share how businesses are driving improved productivity in the construction industry by delivering advanced technologies and support.
A wealth of solutions to the major challenges currently being faced by the industry will also be on show at Melbourne’s premier construction and infrastructure event – Inside Construction Expo 2023. Expo Events Manager Lauren Winterbottom delves into everything the expo has to offer, including how to plan your attendance, and the Foundation Awards which will celebrate the individuals and businesses promoting initiatives, innovation and safety throughout major and local construction and infrastructure projects.
Whether you want to attend more industry events, improve the productivity of your business, adopt technology or join the industry movement towards sustainability, this edition will provide a range of solutions that can help make it possible. Enjoy!
Chief Executive Officer John Murphy
Chief Operating Officer Christine Clancy
Group Managing Editor Andrew Hobbs andrew.hobbs@primecreative.com.au Editor Ashley Grogan ashley.grogan@primecreative.com.au
Sales Director Brad Buchanan bradley.buchanan@primecreative.com.au
Art Director/Design Daz Woolley
Head of Design Blake Storey blake.storey@primecreative.com.au
Design Production Manager Michelle Weston michelle.weston@primecreative.com.au
Business Development Manager William Jenkin william.jenkin@primecreative.com.au p: +61 0478 820 221
Client Success Manager Glenn Delaney glenn.delaney@primecreative.com.au
Cover image credit Komatsu
Head Office
Prime Creative Pty Ltd 379 Docklands Drive, Docklands, Victoria 3008 Australia p: +61 3 9690 8766 f: +61 3 9682 0044 enquiries@primecreative.com.au www.insideconstruction.com.au
Subscriptions +61 3 9690 8766 subscriptions@primecreative.com.au
Inside Construction is available by subscription from the publisher. The rights of refusal are reserved by the publisher
Articles
All articles submitted for publication become the property of the publisher. The Editor reserves the right to adjust any article to conform with the magazine format.
Copyright Inside Construction is owned by Prime Creative Media and published by John Murphy. All material in Inside Construction is copyright and no part may be reproduced or copied in any form or by any means (graphic, electronic or mechanical including information and retrieval systems) without written permission of the publisher. The Editor welcomes contributions but reserves the right to accept or reject any material. While every effort has been made to ensure the accuracy of information, Prime Creative Media will not accept responsibility for errors or omissions or for any consequences arising from reliance on information published. The opinions expressed in Inside Construction are not necessarily the opinions of, or endorsed by the publisher unless otherwise stated.
Hybrid technology significantly reduces the impact of equipment on the environment, without adversely impacting the economic feasibility of a project.
According to McKinsey & Company’s 2017 report, Reinventing Construction: A Route to Higher Productivity, the construction sector’s annual productivity growth has only increased one per cent over the past 20 years.
Komatsu General Manager - Smart Construction James Muir shares how the company is addressing this industry decline in labour productivity growth with its advanced Smart Construction technology range and extensive customer service. Pages 10-13.
Balance of Plant company Zenviron specialises in the design and construction of large-scale renewable energy projects and has adopted the COINS Enterprise Resource Planning software system to improve productivity and efficiency across all its operations.
Zenviron Chief Financial Officer
Richard Clark, COINS Principal Solutions Architect Wayne Kemp and COINS Australia Managing Director
Jim Farrer discuss the key features of the software system and how it has enabled Zenviron to better deliver its renewable projects. Pages 16-19.
Survey Management Solutions (SMS) has adopted Trimble’s augmented reality technology, with the help of Trimble dealer SITECH Construction Systems.
Joe Lloyd, National Technical Manager at SITECH Construction Systems and SMS Business Unit Manager Travis Gains delve into the value of augmented reality to surveyors and construction crews. Pages 21-23.
McConnell Dowell recently partnered with Australian disability enterprise Vivid – an organisation that provides paid, meaningful employment for people with disability through its social enterprise, Vivid Work Crew –
Showcase. Pages 29-37. As part of this month’s Waste Showcase, Advocacy Australia Director Alice Collins shares her expertise about the dangers of asbestos in the construction industry.
Clare Collins, Chair of the Asbestos Education Committee (AEC), Director of the annual National Asbestos Awareness Month Campaign and of asbestosawareness.com.au; Phillip Smith, a member of the AEC and Group Executive for Environment, Health, Safety and Quality at SHAPE Australia; and Bret Baker of the AEC, President of the Asbestos and Hazmat Removal Contractors Association of NSW, and the Managing Director of Beasy also provide their expert advice on asbestos waste management, education, and the health and safety risks associated with improper handling or protection.
CDE Group is a provider of wet processing equipment and technology, and its solutions are facilitating the
diversion of millions of tonnes of construction, demolition and excavation (CD&E) waste from landfill around the world. Melbournebased materials recycling company Repurpose It has adopted CDE Group’s solutions to launch what is said to be an Australian-first CD&E waste recycling wash plant.
CDE Group Regional Manager –Australasia Daniel Webber explores how transforming waste into new resources can change the landscape of the Australian construction industry for the better, as evidenced by Repurpose It’s venture.
On the topic of construction waste, Dr. Gretchen Gagel takes a unique look at the waste associated with breakdowns in relationships on construction projects. She shares real-life examples of breakdowns in project relationships that have caused multi-milliondollar losses, and on the other hand examples of project relationships flourishing that have led to outstanding results.
on the Echuca-Moama Bridge Project. Up to 20 Vivid Work Crew-supported employees were engaged in the project, working in excess of 25,000 hours over the course of 24 months.
McConnell Dowell Communications and Stakeholder Engagement
|Manager Jacqui Mott, and Vivid Business Development Manager
Andrew Thomson highlight the importance of inclusive social procurement in the construction industry and the positive outcomes it presents for all involved. Pages 24-27.
PEOPLE. Pages 38-41.
Throughout her career, Clare Quinlan has worked in several environmental roles in the construction industry, dabbled in jewellery making and today owns her own workwear business.
Throughout her journey, Quinlan has showed ambition every step of the way and this month shares her story with hopes of inspiring others.
As a fully qualified Air Conditioning Service Technician, Lauren Campbell has gained a wealth of experience in the heating, ventilation, and air conditioning sector. With 6 years of experience under her belt, she has some great advice for those looking for a career in construction.
Pages 42-51.
Hacia Atherton, Chief Executive Officer and Founder, Empowered Women in Trades is calling for women to take advantage of the large number of job openings across the Australian construction industry.
Jon Davies, Chief Executive Officer, Australian Constructors Association looks at the theme of the Future of Construction Summit 2023, and discusses the new audience set to be in attendance – ‘the disrupters’.
Formwork Industry Association (FIA) Chief Executive Officer Michael Sugg, President Jason Andrijic and VicePresident Stefano Calautti announce how the industry has secured funding to improve formwork safety on construction sites, as well as the launch of FIA’s new safety program.
Christina Yiakkoupis, Chair, The National Association of Women in Construction calls for safer learning environments for young women looking to start a career in construction, whether it be at university, TAFE or high school.
National Precast Concrete Association Australia Chief Executive Officer Sarah Bachmann unpacks how the construction industry needs to improve efficiency and reduce waste by seeking smarter ways to build.
EVENTS. Pages 52-58.
Melbourne’s premier construction and infrastructure event Inside Construction Expo is launching for the first time this September and this month Expo Events Manager Lauren Winterbottom showcases everything the event has to offer.
The Australian Constructors Association and Engineers Australia announce the seven project finalists competing for the coveted Australian Construction Achievement Award 2023
The National Association of Women in Construction (NAWIC) has come on board as the sponsor of the Excellence in Construction Award at the 2023 Women in Industry Awards
NAWIC General Manager Lauren Fahey shares why the organisation chose to show their support through sponsorship.
CDE is here to transform waste materials into valuable recycled products. Our innovative wash plants give you the power to divert tonnes of waste from landfill and create new revenue streams. Move into new, high-value markets, like certified, in spec concrete sand, recovered from CD&E waste.
Reversing a decline in productivity growth in the construction industry won’t happen overnight, but Komatsu customers are ahead of the curve, thanks to its technical advances and comprehensive customer support.
As slow labour productivity growth continues to sting parts of the construction industry nationwide, Komatsu is actively delivering solutions to ensure its customers can reap the benefits of its technologies today.
Komatsu General Manager - Smart Construction James Muir has a wide breadth of experience in the construction technology space. His over 30 years’ experience has seen him work in leadership roles across the United Kingdom and Australia before joining Komatsu in 2019.
Now leading the company’s Smart Construction Division, Muir says new technologies mean the time to improve labour productivity growth in the Australian construction industry is now.
“Komatsu’s Smart Construction range is a game changer for construction productivity,” says Muir. “Through the application of
as well as Komatsu iSite, a fleet management solution that gives the user a complete, real-time overview of all of their machines throughout the working day. Also in the Smart Construction range, Komatsu’s Dashboard combines 3D design data with aerial mapping and intelligent machine data, providing operators with a digital view of their job site. Smart Construction utilises Internet of Things (IoT) technology to gather data, software to analyse it and to create information, and then uses that information to optimise and improve the processes for the customer. It makes full use of Komatsu’s Intelligent Machine Control technology and provides comprehensive project planning and logistics – for a stunning improvement in productivity. At the heart of the concept lies a central operation control system, a cloudbased platform, that creates a flow of real-time
at worksites around the world, and as part of a company spearheading solutions in this area, Muir says the industry has a major opportunity to find a solution to its productivity challenges.
But many companies are reluctant to embrace the changes, he says, and a great deal of government and industry are still putting this issue on the backburner.
According to McKinsey & Company’s 2017 report, Reinventing Construction: A Route to Higher Productivity, constructionrelated spending accounts for 13 per cent of the world’s GDP, but the sector’s annual productivity growth has only increased one per cent over the past 20 years. Further, the report finds $1.6 trillion of additional value could be created through higher productivity – that would meet half of the world’s infrastructure needs.
In 2023, the statistics have barely improved, if at all. “There’s a number of different elements to how this can be addressed and applying technology is at the top of the list,” says Muir. “If we were to achieve technology adoption across the industry, our taxpayer dollars would be better spent because we could build more with less.”
Today the entry point to apply technology in construction is lower than ever before, as increased competition and innovation have lowered the cost of investment, opening up more opportunities for more businesses to take the technology leap.
Muir says the gains of technology far outweigh the initial investment cost.
“Whereas a traditional machine would dig and rely on the skills of a very good operator, now you can have a machine that does the majority of the work for you,” says Muir. “It eliminates human error in the way that it won’t allow things like over-digging resulting in rework.”
“Our smart machines mean a business can hire an operator that doesn’t have 20 years’ experience who ordinarily would cost further dollars to upskill, because even newer operators can be brought up to speed very quickly on our intuitive and user-friendly technology.”
Komatsu’s digital monitoring technology (digital twin) can be adopted by the industry right now, explains Muir. A digital twin is an
accurate, virtual representation of a real-world physical object such as a piece of equipment or even an entire building. These exact replicas allow the operator to measure things like project progress and cost in near real-time to better manage resources, make accurate predictions and estimates, and improve safety on site.
When it comes to technology adoption in the construction industry, government action could inspire positive outcomes, Muir says.
“We need a fundamental government policy change within the construction and infrastructure sectors to encourage the adoption of technology,” he adds.
“These policy changes need to address, at the very least, risk sharing to allow contractors and various entities to utilise more capability into applying technology rather than having to worry about the ‘all on them’ cost if something goes wrong on a project.”
Muir explains that in Japan, the government is working together with the construction industry through the i-Construction initiative. Introduced in 2016, the initiative promotes the use of automated machines and information and communication technologies (ICT) on construction sites to improve productivity across the local industry. The Japanese Government provides concessions to the engineering firms and contractors that adopt more ICT or semi-autonomous machines within their business.
“The successful implementation of the i-Construction initiative in Japan is proof that with more government support, the industry can thrive,” says Muir. “It’s not that the technology doesn’t exist, the technology is absolutely there, it really comes down to why we haven’t applied it.”
“There used to be an argument that technology can’t be applied into the infrastructure or construction industries because we’re out in the elements and there’s too many variables that we have to factor in.
“That used to be a valid argument probably 20 years ago – now we have machines that are so intelligent, in terms of their ability to operate in the field, that we can measure a job down to the millimetre.”
Muir explains that it comes down to
“Through the application of our unique technology and integrated products, businesses can improve the entire construction process by utilising accurate and instant data, and insights.”Komatsu iSite gives the user a real-time animated overview of every movement of production machines –and the material they are extracting, shifting or placing.
enabling the industry to benefit from these technologies and encouraging the application of that technology in the field.
Another challenge contributing to low labour productivity is attracting and retaining people in the industry, a challenge Muir says technology can play a huge role in addressing.
“We don’t want to be putting people into construction roles that are not going to interest them and technology itself helps with that,” he says. “If a business applies new solutions and technologies across its operations, it makes employment opportunities that arise within the company more interesting to current and future generations.”
“Whereas if we’re still using antiquated methods and policies, people are just not going to be interested in joining our industry.”
Further to its range of technology, Komatsu’s approach to supporting the customer is paving the way for improved labour productivity across the industry.
“We believe support of the customer is paramount,” says Muir. “We have a whole series of support layers that we introduce now as part of our smart technology, because it’s not good enough to just deliver the technology to our customers – we need to be there to help them apply it or else we believe it’s not going to be applied to its full potential.”
As well as ensuring every piece of smart technology is easy-to-use, Komatsu has cultivated a dedicated support team of Smart Construction consultants available 16 hours a day to instantly assist customers. These experts can dial into the screen in the cab of a machine and show the operator in real-time what buttons to press, propose solutions using ICT and, as a result, improve productivity and safety across the workplace. This provides customers immediate guidance without them having to visit a support centre.
“As well as having that frontline support, Komatsu has technology advisors on call to visit customer sites when needed,” says Muir. “Our Smart Construction machines connect to satellites and base stations, so if the customer needs support outside of their machine, we can have a Komatsu technology advisor to their site within hours.”
But the support doesn’t stop there. Komatsu
has a team of customer technology advisors that can join a business as part of the team. The difference being, a technology advisor is a troubleshooting expert who will visit a customer’s site to assist with the immediate problem or challenge at hand, whereas a customer technology advisor is an expert Komatsu customers can hire into their team. Whether they’re needed once a week or once a month, a customer technology advisor can be embedded into the team to teach and help direct the company towards technology adoption and improved productivity.
“For an earthmoving contractor for example, a Komatsu customer technology advisor can help move the business into the digital era,” says Muir. “They will help integrate Komatsu technology, assist with training, help with application and strategy, and ensure overall the business’s journey to technology adoption runs smoothly and efficiently.”
The construction industry has the capability and capacity to step up to the productivity challenge, but even more so with a high level of support from construction technology providers. Komatsu’s customer-centric approach proves that with the right support, improved labour productivity is more achievable than most realise. Rather than simply introducing Smart Construction technology to the market, Komatsu is making the path to new productivity gains seamless and inviting by not only providing the latest in intelligent technology and products, but also supporting its customers into the digital era.
“Unlike some companies that will look to outsource support, we find that providing multiple layers of support and services in house is vital to helping our customers throughout the entire process of technology adoption,” says Muir.
Adding to the labour productivity challenge, Environmental, Social and Governance (ESG) standards play a huge role in the success of a construction business. The impact a business has on the environment and society is becoming ever more important. Owners, investors and project owners are placing an increasing importance on ESG factors and it is something that business operators need to keep top of mind in order to be competitive.
“The successful implementation of the i-Construction initiative in Japan is proof that with more government support, the industry can thrive.”
With a vision of reducing the carbon footprint of the construction industry worldwide, Komatsu is looking at multiple different power generation opportunities and methods, from electric to hydrogen cell, to keep its equipment on the move.
“There are many ways in which technology coming into the industry can improve overall ESG,” says Muir. “On the environmental side, our Smart Construction machines reduce rework, they reduce the amount of fuel you’re burning and therefore the amount of carbon you’re emitting, and they get the job done in two thirds of the time.”
“The ESG benefits of our smart machines are tremendous, especially in the environmental space.
“Helping with ESG is the ability to measure it – our Dashboard can measure litres per tonne, emission clouds and can show you, depending on the number of machines which we track by satellite, what the emissions balloon would look like all the way down to the type of engine that it’s running.”
On the social side, Komatsu’s Smart Construction machines improve workplace conditions by strengthening employee health and safety. By improving efficiency, the technology enables the operator to get the job done quickly and reduces the need for manual labour. Machine surround cameras can alert operators if someone is standing too close to a machine and eliminate oversights that may have resulted in an incident. Further, new generation electric excavators emit next to no external noise emissions ensuring minimal impact to society.
“Our Smart Construction machines get the job done in less time,” says Muir. “We’ve seen instances where a project has gone on for more than five years when our technology could have helped the contractor complete it in three.”
Though the future of the Australian construction industry is uncertain, Muir says he is confident that over the next five years we’re going to see an uplift in overall labour productivity.
“We’re already seeing an increasing adoption of machine control and machine guidance as well as design tools and digital twin
future we’ll see an upturn in technology application.”
In the next 10 years, Muir says the productivity benefits of technology could be exponential. “Technology adoption needs to become the norm across the construction industry if we want to tackle the labour productivity challenge,” he adds.
“We believe there’s a market here for the technology, and innovation investment in the construction industry is climbing rapidly – it’s a key indicator that we’re moving in the right direction.”
Looking again at McKinsey & Company’s Reinventing Construction: A Route to Higher Productivity report, it names seven levers to drive improved labour productivity across the construction industry. Komatsu’s smart technology and approach to customer support bolsters two of the most important levers: the improvement of on site execution; and the infusion of digital technology, new materials and advanced automation.
The report names four key methods of improving on site execution – the introduction of rigorous integrated planning, implementation of collaborative performance management, the effective mobilisation of projects, and collaboration to reduce waste and variability. From a customer support perspective, Komatsu readily enables these four courses of action.
In terms of infusing digital technology, new materials and advanced automation –Komatsu goes above and beyond to ensure its consistently innovating its technology offering to provide forward-thinking solutions to the construction industry. The company’s ever-evolving Smart Construction range is a testament to Komatsu’s goal of improving productivity, efficiency and safety for its customers.
“If we were to achieve technology adoption across the industry, our taxpayer dollars would be better spent because we could build more with less.”
iMC 2.0 is the next generation of the Intelligent Machine Control that will deliver step changes in daily operation. This Komatsu fully factory integrated technology enables operators to get the job done right the first time, every time.
Inside Construction Expo will deliver
Targeted messaging in over 19 industry-leading publications that reach more than 80,000 decision makers across multiple sectors
Digital communications to 28,000+ engaged readers
Premium networking opportunity with industry leaders at the Foundation Awards gala dinner
With a growing focus on renewables, Balance of Plant company Zenviron is getting ready to hit the ground running as the sector expands, supported by the innovative COINS Enterprise Resource Planning software system.
Zenviron is a highly experienced, full-service Balance of Plant (BOP) contractor specialising in the design and construction of large-scale renewable energy projects across Australia and New Zealand.
With new government targets set in Australia, the company is busily building itself to cater for a market that it anticipates will expand rapidly in the next two to five years.
To help it do that, Zenviron Chief Financial Officer Richard Clark sought out a way to help improve productivity and efficiency across all its operations and the answer, he says, was the Construction Industry Solutions (COINS) Enterprise Resource Planning (ERP) platform.
The system, he says, lets Zenviron combine its invoicing, project management and financial control systems into one easy-to-use software system.
“Prior to implementing COINS, we were using another system and it didn’t have several of the integrated modules we were looking for, such as accounts payable, vendor management, or the workflows,” says Clark.
“We used external support overseas and the reporting side was predominantly in Excel.”
“The old system was quite archaic, inefficient, very time consuming and not all in the one place like COINS is now.”
Combining plant and asset management, invoicing, procurement, payroll, forecasting, daily costs and cash flow, and subcontractor management in one software system allows Zenviron to meet its current demand for project management needs, confidently tackle large projects and handle increased demand well into the future.
Clark says Zenviron has every confidence COINS will be able to support the company’s rapid growth. “COINS allows us to have certainty that we’ll be able to build the business – not just with the platform, but also the support network behind it, right up to COINS Managing Director Jim Farrer.”
“If we want to try something different or ramp up operations, we know we’re going to be supported by the COINS support team.”
Clark adds that he is also confident in the infrastructure of the system. “We know that it’s able to easily handle what we have today and it’s a no-brainier that it will be able to cope when we increase activity,” says Clark.
“We’re looking to ensure our business is at the right size to be able to cope with the influx of renewable projects that are coming online,
One of the key features of the COINS
ERP+ system is its innovative Business Planning and Forecasting systems, which gives Zenviron the ability to immediately access accurate data in real-time for project performance reviews and financials –creating opportunity pipelines and overhead
This feature allows COINS customers to streamline their end-of-month reporting and forecasting to improve margins and profits, as well as manage risks and opportunities across
Clark says this feature has been a transformative one for Zenviron.
“The end-of-month reporting, the Business Planning and Forecasting and the
“COINS allows us to have certainty that we’ll be able to build the business.”Zenviron has been contracted by Tilt Renewables to carry out the design and construction of the civil and electrical Balance of Plant works of the Rye Park Wind Farm in NSW.
standardisation of the way the COINS platform reviews and aggregates data is absolutely critical to Zenviron,” he says. “In our old system, Excel was the main reporting tool, and it was very hard to enquire what managers or project managers wanted.”
“No one else in the business had access to the system – other than the accounting department.
“Whereas today with COINS, everyone has their own access based on permissions and we can either run a report or make a real-time enquiry on the screen to understand various aspects of our current projects.”
The integrated project control and financial management architecture of the COINS ERP+ system provides Zenviron with ‘one source of truth’ to guarantee accurate, timely and verifiable information is available for all stakeholders in the business.
Clark says the system is remarkably userfriendly and easy to navigate, allowing for report automation to save time. “I personally like the reports that are autogenerated,” he says. “They are my chosen summaries that I can see on a daily basis without having to jump directly into the system.”
He adds that the COINS platform is easy to navigate, enabling him to look up information in less time than it takes to ask someone else to do it. “The level of detail that you can go to – right down to the invoice – is a real plus for us at Zenviron,” says Clark. “We can scale up using the same platform knowing it has the ability to improve what we’re doing now.”
Kemp worked on the implementation of the COINS ERP+ platform for Zenviron and says his team understood the company’s key needs right from the start. “We work closely with Zenviron in an open, honest, collaborative manner to ensure that our solutions add both value to its business and deliver a competitive advantage,” says Kemp. “There was an alignment of values and culture from the start.”
“We use a collaborative software development model which allows our customer-specific priorities and requests to be fast-tracked in the COINS global development pipeline.”
Kemp says COINS Australia has proven
“We’re looking to ensure our business is at the right size to be able to cope with the influx of renewable projects that are coming online, and COINS helps us do that.”Zenviron completed the design and construction of the civil and electrical Balance of Plant works of the Dundonnell Wind Farm Substation in Victoria. Rye Park Wind Farm is set to be one of the largest constructed wind farms in NSW to date.
time and time again it delivers customer implementations on-time and on-budget.
“Our track record speaks for itself – our average customer life span exceeds 10 years,” he says. “That shows that successful construction companies are not only choosing COINS but are able to expand their use of COINS’ solutions over many years as their needs change and grow.”
Kemp says because the COINS ERP+ platform is specifically developed for the construction industry, the team could better understand the challenges faced by civil construction companies like Zenviron.
“It’s challenging to meet reporting format obligations and timelines,” says Kemp.
“When you have reporting deadlines to a parent company, like Zenviron does, they don’t
“At COINS we understand that at the end-ofmonth, the business planning and forecasting and the standardisation of the way COINS reviews and aggregates data is absolutely
not just about the product. “The impressive part about the COINS ERP+ implementation was the team we dealt with,” says Clark.
“They’re real people.”
“That’s another tick box when you’re choosing a new software system, it’s not just about the product, it’s about the team that’s going to implement it and the support team who will assist you going forward.
“The consistency, the technical detail and the understanding within the COINS team is excellent – it enabled us to have quite a smooth transition in moving to COINS.”
The COINS ERP+ platform is specifically developed to handle the complexities of the Australian construction industry and the COINS team endeavours to simplify the way construction and engineering companies manage business.
From finance and operations, project delivery and time management, to controlling supply
With the construction industry experiencing ongoing challenges, the right technology is essential to forecast, manage and operate a successful construction business.
COINS Australia Managing Director Jim Farrer says COINS’ construction solutions significantly improve the quality, depth and accessibility of business information, enabling informed and confident decisionmaking across all levels.
“Our COINS technology is scalable, fosters transparency and simplifies regulatory compliance, supporting commercial and civil contractors to successfully grow and maximise returns,” says Farrer.
“Infrastructure investors are increasingly demanding businesses demonstrate lowrisk, governance-controlled operations before committing to a venture, and that is exactly what COINS empowers organisations to do.
“The COINS Australia team looks forward to continuing to support a highly innovative
Construction Industry Solutions’ Enterprise Resource Planning platform is an easy-to-use software system transforming project management and financial processes in the construction industry.
• Integrated project control and financial management - accurate, timely and verifiable data available to all staff in the business.
• Business Planning and Forecasting focused on project performance reviews, opportunity pipeline and overhead management capability, streamlining end-of-month processing and forecasting to optimise margins and commercial.
• Compliant Australian payroll, human resource and employee self service capability.
• Advanced procure to pay processing and commitment control.
• COINS Analytics – visualisation and business intelligence reporting of key metrics to better access key information to successfully run the business.
• Fully integrated asset management and plant control.
• Industry compliance and governance functionality including Project Bank Accounts, Security of Payments Act, Taxable Payment Annual Report and Payment Times Reporting to the Australian Taxation Office.
Embracing the latest in surveying innovations since its inception, Survey Management Solutions has now adopted Trimble’s augmented reality technology to streamline the delivery of its projects.
After being introduced to augmented reality (AR) by Trimble dealer SITECH Construction Systems in 2021, Survey Management Solutions (SMS) quickly saw the value of integrating the technology into its business. The practical and purposeful application of AR on its machines has enhanced SMS’s operations, enabled by the computer generated, real-time view of its teams’ physical surroundings both on and beyond the surface of a project.
The surveying company has built a reputation for its ability to handle challenging infrastructure projects in a timely and costeffective manner. That skill set is, in part, due to its commitment to investing in and applying advanced technology and stateof-the-art equipment to deliver innovative solutions.
AR is one of the industry’s most anticipated technologies and SMS says it has directly improved workflows when put in the hands of its surveyors and the cabs of its heavy equipment.
at SITECH Construction Systems and was the first to get in touch with SMS when the new technology became available. He says SMS has been adopting Trimble technologies for over 10 years.
“SMS has always been an innovative, forward-thinking company and is always keen to hear about Trimble’s latest offerings,” says Lloyd. “When SITECH Construction Systems first introduced Trimble SiteVision, an outdoor AR system, three years ago, SMS was one of the first to invest in the technology.”
As the industry continues to see more construction businesses jump on board the AR bandwagon, SMS has positioned itself ahead of the pack by adopting the technology early on.
Industry experts have predicted that AR will be one of the top technologies to watch in construction for its ease of use and expanding integration into commercial solutions such as smartphones. According to a Research
Survey Management
Solutions (SMS) provides surveying and digital engineering services to the construction sector, utilising innovative technologies and equipment. The company is a driver of innovation in the Australian construction industry by pioneering and investing in the latest technology.
Demonstrate the value of augmented reality to surveyors and construction crews.
• Trimble Earthworks Grade Control Platform with augmented reality.
• Trimble SiteVision.
• Trimble WorksManager Software.
• Trimble Business Center.
• Improved operator confidence.
• Reduced risk of hitting underground utilities.
• Better decision making.
• More streamlined workflows, particularly when issues arise.
reality market is projected to account for a revenue of US$1.2 trillion in 2030, rising from US$37 billion in 2019 – that’s a compound annual growth rate of 42.9 per cent during the forecast period (2020-2030).
Much of that growth is likely to be in the construction space, where technology adept owners and project teams are using it to better visualise design intent relative to real-world conditions, simulate changes and adapt more readily to on site conditions.
In the past three years, Lloyd says the demand for AR technology in the construction industry has increased significantly. “The market for AR continues to grow and for good reason,” says Lloyd. “This technology can solve many of the complex challenges currently being faced by the industry from productivity issues to lack of safety on site.”
“By improving productivity, safety and efficiency, and enabling professionals to identify problems before they arise, AR is changing the construction game.
“The companies like SMS that are taking advantage of this technology now are the companies that will have the competitive edge in the fast-moving world of construction.”
For SMS, the early introduction to AR has been through workflow visualisation technology, such as Trimble SiteVision.
SiteVision is a user-friendly outdoor AR system that is lightweight for handheld operation. It incorporates a high precision (centimetre accuracy) global navigation satellite system (GNSS) with an electronic distance measurement laser rangefinder that works with a smartphone’s AR capabilities. The AR application provides a 3D model of a project site at a true-to-life scale, above and below the ground, by overlaying 3D digital content with a camera-captured live image. The sensors track the movement of the system and adjust accordingly, allowing the user to walk around the worksite and visualise a model of the project from any angle.
SMS bought its first system two years ago when SiteVision was first released and has since invested in many more. Today, every SMS foreman has a SiteVision system that is used regularly to assure construction is proceeding according to specifications. It takes measurements and records information
that can be fed back to the construction and survey team to support decision making.
Travis Gains, Business Unit Manager - SMS, says SiteVision is a game changer. “Before we start any activity, we require a preconstruction commencement walk with engineers and stakeholders that includes SiteVision and ground penetrating radar (GPR), so that everyone understands the requirements for the project, has clarity about what’s underground and recognises the potential risks,” says Gains.
The use of SiteVision and GPR before and during construction is essential to reducing the chance of hitting utilities on projects.
“It’s standard practice to use the system on every project, but especially on complex projects where damaging utilities can be extremely unsafe, is costly, creates project delays for necessary repairs and can damage reputations,” says Gains. “For us, SiteVision is an essential safety improvement and risk mitigation strategy.”
SMS has also invested in Trimble WorksManager and Trimble Business Center to move project data back and forth from the field. SiteVision works with data from both Trimble WorksManager and Trimble Business Center and brings that data to life in a digital 3D model for the machine operator. Trimble Business Center is a survey computer-aided design software that integrates with WorksManager and helps surveyors deliver high-accuracy GNSS data to create 3D models. WorksManager is then used to remotely transfer those construction-ready models to machines in the field.
“As soon as we get a new design or updated survey of underground assets in Trimble Business Center, we can get it to the machine operators very quickly through WorksManager,” says Gains. “No more USB’s or trips to the jobsite.”
The success of AR-enabled SiteVision raised expectations about the potential of AR on machines.
This led to a partnership between SMS, SITECH Construction Systems and Australian-based manufacturer Webbair to develop 3D avoidance technology. A civil construction company, working closely with
“By improving productivity, safety and efficiency, and enabling professionals to identify problems before they arise, AR is changing the construction game.“Joe Lloyd, National Technical Manager for SITECH Construction Systems, a Trimble distributor.
SMS, introduced 3D avoidance technology on an excavator on one of its projects in Melbourne when it was introduced to the market last year. The technology relies on a digital map of utilities prepared by the SMS survey team. If the excavator attachment gets too close to a defined ‘avoidance zone’, the onboard sensors restrict and then immobilise the digger, thus minimising the chance of costly subsurface strikes and project delays while improving crew safety.
According to Gains, the operators also receive real-time updates on underground services from surveyors working remotely, which allows work to continue without needing to wait for new data. Gains explains that allowing for the operator or supervisor to add in any new hazards or high-risk areas on the fly without requiring them to be defined digitally is potentially one of the biggest benefits of the system, which was demanded from the market at the start of the due diligence phase.
The next step was introducing AR in the cab. As part of the Trimble Earthworks AR Camera and a Workflow Optimisation Demonstration Program facilitated by SITECH Construction Systems and Trimble, the civil construction company also took the opportunity to see how precision grade control, 3D avoidance technology and AR can combine to support operator actions.
SITECH Construction Systems’ Joe Lloyd says during the demonstration program, his team mounted a camera on the outside of one of the civil construction company’s excavators with the 3D avoidance technology on a project in Melbourne. “The camera enables the operator to view a 3D model of the real-world site environment,” says Lloyd.
“Through the Trimble Earthworks display, the model is then overlaid onto the existing ground to give the operator an accurate understanding of all cut and fill information, slope data and the work that needs to be done.
“The display also provides visibility of the bucket improving safety, precision and efficiency on site by making the operator aware of the people and objects around them.”
Gains says the implementation of these technologies is the next level of integration and a great addition to the excavators. “We
gets an understanding of the job, the faster the build,” Gains adds. “With Trimble Earthworks and AR, our operators see an alignment in 3D and the software also provides options for multiple views.”
“Overall, the addition of AR raises the level of awareness relative to the design model – we also think it will be essential for getting less experienced operators up to speed on the job.”
That raised awareness is particularly valuable for the civil construction company, where some of its projects have large numbers of underground service requirements in tight work areas. According to Gains, when an issue arises, they can quickly get the utilities modelled accurately and back to the operator to keep work progressing.
“A big part of my job is to push innovation,” says Gains. “We’re a big investor in technology and we’re always looking for innovative solutions and want to lead the industry.”
As a civil contractor, Gains says SMS always wants to do things safer, faster and more cost effectively by continuing to work with and invest in the latest in Trimble products – fostered by the strong relationship the company has with SITECH Construction Systems.
“We’re definitely going to invest in any solution that can help us get a better understanding of the job and also help the crews build faster, safer and with greater precision,” says Gains. “Our workflow visualisation system, the 3D avoidance system and the Trimble Earthworks AR camera are prime examples of that focus.”
“With Trimble Earthworks and AR, our operators see an alignment in 3D and the software also provides options for multiple views.”On the Trimble Earthworks Grade Control Platform display, the model is overlaid onto existing ground, giving the operator a better understanding of the work that needs to be done. Visibility of the bucket gives operators better situational awareness to be able to keep surrounding people and objects safer.
McConnell Dowell works hard to make a difference in the communities where it works – and a recent partnership with Australian disability enterprise Vivid is helping make a lasting difference to a group of workers in the Echuca-Moama region of Victoria and New South Wales.
The regionally based Vivid Work Crew supported employees ready to work at the Echuca-Moama Bridge Project site compounds with their Vivid Employment Mentors.
McConnell Dowell and Vivid worked together on Stage 3 of the Echuca-Moama Bridge Project, a new Murray River crossing connecting Victoria and New South Wales.
Completed in April 2022, the project has been one of the largest transport infrastructure projects in northern Victoria, jointly funded by the Australian, Victorian and New South Wales governments.
Contracted for the design and delivery of the new bridge by Major Road Projects Victoria (MRPV), McConnell Dowell sought ways to collaborate with, and address the needs of, the local community.
McConnell Dowell Communications and Stakeholder Engagement Manager Jacqui Mott says she was driven by her company’s inclusive approach to social procurement, finding ways to contribute to the project that
were fostered by mentorship and supported employment.
Mott says that during early discussions with community members, multiple locals pointed her towards Vivid, a regionally based notfor-profit Australian Disability Enterprise that empowers local people living with disability and which, as part of its range of disability support services, provides paid, meaningful employment for people with disability through its social enterprise, Vivid Work Crew.
“With all of our projects, our priority is to connect with community and gain an understanding of community priorities, drivers and values,” Mott says. “Through strong community engagement and listening to the Echuca-Moama community, the McConnell Dowell project team found a unique opportunity to provide employment and
educational pathways to supported employees at Vivid Work Crew.”
“Through our partnership with Vivid, young people living with disabilities were employed to fulfil roles including site maintenance, office and vehicle cleaning, and environmental duties under the guidance of Vivid Work Crew Mentors and the Stage 3 project team.”
Vivid Business Development Manager
Andrew Thomson says up to 20 Vivid Work Crew supported employees were engaged in the project, working in excess of 25,000 hours over the course of 24 months.
Undertaking general cleaning duties at the four worksite compounds, the supported crew worked a maximum of two shifts each day, on sites in Victoria and across the Murray River at the New South Wales section of Stage 3 works.
“COVID-19 then unfortunately struck, but McConnell Dowell supported us every step of the way to ensure our crews met all health and safety guidelines and could continue to work,” says Thomson, who worked closely with McConnell Dowell throughout the partnership.
“We needed four separate crews going to the different worksite compounds, which put a drain on our resources, but with the help of McConnell Dowell we were able to upskill some of our supported employees to meet the demands of the project.”
On top of delivering employment opportunities, McConnell Dowell, in collaboration with regional educational provider Bendigo TAFE, helped nine supported employees gain formal
qualifications through Certificate II study at TAFE’s Echuca campus during the project, providing employees with on site construction induction training and an opportunity for all members of the crew to obtain their industry-recognised White Cards.
Obtaining White Cards for all supported employees on the project was a challenging process in that it was something Vivid had never tried before, explains Thomson. “But with a local training provider and McConnell Dowell, we were able to get those formal qualifications for our Work Crew supported employees, all of whom are extremely proud of that achievement,” he says.
“With all of our projects, our priority is to connect with community and gain an understanding of community priorities, drivers and values.”Vivid Work Crew supported employee Luke Peters enjoyed his role as site ‘Peggy’, which saw him assist with the site maintenance across Stage 3 works. Photo: Brendan McCarthy.
the bridge’, or even played a small part in its construction – particularly on a large-scale project that is expected to be there for decades, if not hundreds of years,” he says.
“As an organisation, this taught us to be more ambitious with the projects that we engage our supported employees in.
“Even though we’re only a small disability
Forming long-lasting relationships in the regions where it works is the cornerstone of McConnell Dowell’s social procurement strategy, and is what is at the heart of the company’s purpose – providing a better life With an overall goal of delivering projects that connect, sustain and enhance communities, it’s the relationships formed from working with organisations like Vivid that underpins McConnell Dowell’s continued success.
Thomson says these values shone through in the way the McConnell Dowell team welcomed, encouraged and championed Vivid supported employees on site.
“When we reflect on the project, we’ve found the biggest takeaway from the opportunity to work with a company like McConnell Dowell was the relationships that were built,” he says. “The McConnell Dowell staff and management were unbelievable in understanding what our crew’s capabilities were and provided clear lines of communication from day one.”
“We still talk with McConnell Dowell today in regard to other projects that it is undertaking around Australia – I regularly get calls from its project managers to ask for advice on similar partnerships.
“With thisexperience
we’venow been part of a large-scale project, and we’re confident that we can work with large-scale companies in the future.”
proud that we’ve had a positive influence on the way it works with different communities.”
The Vivid and McConnell Dowell partnership highlights the brilliant outcomes that can come from placing a high importance on community engagement and social procurement in the construction industry. In 2018, the Victorian Government released the Social Procurement Framework in an effort to encourage the state’s construction industry to consider how it can support regional small and medium enterprises, such as Vivid.
The framework provides guidance to construction businesses and development owners to embed social and sustainable procurement into existing processes. The goal is to have a standard of procurement contracts that make a real difference to communities by providing opportunities like support, employment and training to Aboriginal businesses, social enterprises, people with disability, women and the longterm unemployed.
It’s through these kinds of frameworks and initiatives that all Australians will thrive, says Thomson. “Vivid’s partnership with McConnell Dowell is a perfect example of how social procurement can change lives,” he
having faith in us, and also the Australian and Victorian governments for including social procurement in their tender requirements – it helps organisations like ours to promote our abilities and our people with disabilities.”
McConnell Dowell’s Jacqui Mott is equally impressed with the outcomes of the partnership. After the completion of the project, the parents of Vivid’s participating supported employees advised her that they could easily gauge personal gains brought about by being part of the workforce – as these young adults they care for were now improving social and communication skills, and developing practical competencies and self-confidence.
“What’s more, the response from the McConnell Dowell project team was fantastic,” says Mott. “Our project team across the board was very supportive, many friendships were formed, we learned more about diversity within a community, and as a result we fostered a very inclusive workplace.”
“McConnell Dowell is proud of the farreaching benefits the partnership has delivered to both our team and Echuca-Moama.
“We continue to build on our strong social procurement approach by enhancing the value we deliver to the communities we work in.”
“Vivid’s partnership withMcConnell Dowell
is a perfect example of how social procurement can change lives.”The project team were joined by the Vivid Work Crew supported employees and Mentors as they gathered to celebrate the joining of the crossing over the Murray River. Photo: Flat Out Surveying.
Melbourne
The Foundation Awards recognise both individuals and businesses who excel in the industry and bring together different industry segments to one room on one night for a glamorous night of celebration.
Waste is an unavoidable component of construction, yet many professionals in the field are still neglectful of hazardous waste materials. The risks of asbestos in particular have been known for decades, and the Asbestos Education Committee wants the entire industry to be aware of its dangers.
Despite asbestos being banned in Australian commercial and non-residential properties since the 1980’s, asbestos-containing materials (ACMs) continued to be used in multiple locations in the non-residential built environment until the end of 2003. With a wide range of ‘legacy’ ACMs remaining in a significant number of properties, it’s not only a legal obligation for people to manage and dispose of asbestos safely; it may well save their lives.
Clare Collins, Chair of the Asbestos Education Committee (AEC), Director of the annual National Asbestos Awareness Month Campaign and of asbestosawareness.com.au says currently around 4,000 Australians die
annually from preventable asbestos-related diseases. These include mesothelioma, lung cancer and asbestosis and are a result of exposure to asbestos fibres in past decades.
“The AEC was founded to help prevent today’s workers from becoming tomorrow’s deadly statistics by increasing awareness of the dangers of asbestos and providing a wide range of practical resources,” says Collins.
“Developed in association with industry experts and government regulators, all AEC resources are free to download from asbestosawareness.com.au.”
Asbestos can be located anywhere in commercial and non-residential properties built prior to 2004 – including in the more
“To enable tracking of all asbestos removal and ensure it’s disposed of according to regulations, we’d like to see a more coordinated approach between state regulators and waste disposal facilities.”Words Alice Collins, Director, Advocacy Australia. An example of asbestos cement external wall cladding, roofing, and roof and corner capping.
well-known locations such as walls, ceilings, roofs and vinyl floor coverings. But it can also be found in less obvious locations such as soils, electrical switchboards, service risers, fire protection and mortar products, bitumenbased water proofing, adhesives, sealants, heaters and boiler gaskets, fire doors, lift shafts and plant rooms. Asbestos could be anywhere.
When asked about the issues associated with asbestos in non-residential properties, Phillip Smith, a member of the AEC and Group Executive for Environment, Health, Safety and Quality at SHAPE Australia, says complacency and a lack of knowledge are among the major factors resulting in mismanagement and illegal dumping of ACMs.
“Although work health and safety (WHS) legislation and Codes of Practice are in force nationally to protect workers and anyone nearby from exposure to dangerous asbestos fibres; in the commercial and non-residential space, improper handling, non-compliant removal, illegal disposal and dumping of ACMs is alarmingly common – due to people either not knowing or not understanding their obligations,” says Smith. “There are also those who deliberately breach regulations trying to minimise costs.”
However, Smith says poor and illegal asbestos management can come at a hefty price. “Breaching regulations not only puts people’s lives at risk, but it can also lead to work disruptions, project delays, budget blowouts and even the closure of commercial
and non-residential properties,” Smith adds.
“Significantly, breaches can also lead to legal liabilities and financial penalties with building owners, employers and contractors facing fines, legal action and damage to their reputations and businesses as a result.
“Adherence to regulations including the WHS Act and asbestos Codes of Practice is absolutely critical.”
Among the dangers associated with poor asbestos management are increased occupational health and safety risks for building occupants and workers, such as electricians, plumbers, and other contractors who may unknowingly disturb asbestos while carrying out their work.
“Implementing strict asbestos management policies and procedures is the starting point of a process that includes developing an Asbestos Management Plan (AMP) and an Asbestos Register which must be updated at least every five years,” says Smith. “Engaging an occupational hygienist or a licenced asbestos assessor or removalist will help identify various ACMs and assist in developing a mandatory Asbestos Register.”
“The Register must record ACMs that have been identified or are assumed while the person responsible for the site must ensure the Asbestos Register is maintained, reviewed and revised as required.
“This includes whenever additional ACM locations are identified, when asbestos is removed, disturbed, sealed, enclosed or labelled, and importantly, the Register must be stored on site and be accessible to contractors, workers and their health and safety representatives.”
Smith says it’s also important to note that while some Australian state legislation allows certain types and quantities of ACMs to be legally handled, managed and removed by tradies and/or property owners – such as bonded asbestos – he strongly advises against it. This is because the risks of exposure are significantly higher when the work is not carried out by licenced professionals.
When asbestos is disturbed its microscopic fibres become airborne and can be inhaled or settle on clothing and equipment. These fibres can easily be spread throughout properties and transferred to family homes. These can pose significant health risks to anyone who
comes into contact with them, including children. Smith says the only way to ensure the safety of workers and families is to engage licenced professionals.
Bret Baker of the AEC is President of the Asbestos and Hazmat Removal Contractors Association of NSW (AHRCA) and the Managing Director of Beasy. When it comes to the most common breaches of asbestos regulations in commercial and non-residential properties, Baker says there’s a range of significant issues that must be addressed to effectively manage the asbestos hazard and prevent deaths caused by inhaling asbestos fibres.
“Often Asbestos Registers are not updated after asbestos is removed, and many Registers are not always accessible to tradespersons who need to enter the site when the person responsible is unavailable,” says Baker. “To address the issue we encourage state and local governments nation-wide to adopt a policy of making all Asbestos Registers readily available digitally via a QR code located in the site’s power box or via a website.”
“This would be a simple and highly effective method of giving access to all those who enter the site such as trade workers.
“Significantly, it would also be available to emergency services attending the site including firefighters.”
While providing access to digital registers can be easily solved, the 10-square-metre rule is the primary issue that can impact the health of property owners, managers and visitors. In some states where it’s permitted to remove up to 10-square-metres of bonded asbestos; some are doing small amounts of asbestos removal work themselves rather than engaging a licenced contractor.
While some may have Asbestos Awareness training, they’re often not licenced asbestos removalists armed with the right knowledge, skills or equipment (such as an H Class vacuum) to remove asbestos safely in accordance with regulations. Abolishing the 10-square-metre rule as has been done in the ACT will go a long way towards preventing avoidable exposure to asbestos fibres due to mismanagement.
Baker says illegal removal and dumping also poses severe risks to anyone who comes into contact with ACMs. “To enable tracking of
all asbestos removal and ensure it’s disposed of according to regulations, we’d like to see a more coordinated approach between state regulators and waste disposal facilities,” he says.
“This can be done through an integrated system incorporating SafeWork/WorkSafe’s compulsory notification of asbestos removal and Environmental Protection Authority systems that record transportation and disposal of asbestos waste.
“This combined system would enable effective regulation of all licenced asbestos removal and disposal to minimise its illegal dumping.”
Clare Collins says the AEC will continue to increase awareness of the dangers of asbestos and develop vital resources which are freely available from the Asbestos Awareness website as long as asbestos remains in the built environment, to help save lives. The website, asbestosawareness.com.au, was launched in 2011 and provides an extensive source of asbestos information and resources available to homeowners, renovators, tradies and owners and managers of commercial and non-residential properties. By visiting the website, property managers can download the free Asbestos Management Handbook for Commercial and Non-residential Properties and user-friendly templates to develop an Asbestos Management Plan, Asbestos Register and model Asbestos Policies for managers, contractors and builders to ensure they manage asbestos safely in line with regulations.
Additional information on best practice for asbestos management can be sourced from:
Asbestos and Hazmat Removal Contractors Association of NSW (AHRCA). www.ahrcansw.arcansw.asn.au
SHAPE Minimum Standards for Asbestos Management. www.sms.shape.com.au
SHAPE is also available from mobile device app stores – search for SHAPE
Minimum Standards to download the free app.
The Asbestos Education Committee is the Asbestos Awareness arm of the registered charity, Advocacy Australia. www.advocacyaustralia.org.au
CDE Group lays the foundations for a circular economy by delivering leadingedge equipment and technology that transforms waste into new resources, providing an ideal opportunity for the Australian construction industry to jump on the sustainability train.
As one of the leading providers of wet processing equipment and technology globally, CDE Group delivers innovative, materials washing solutions for a variety of products in the waste recycling and construction materials sectors, with projects in place around the world.
CDE Group celebrated its 30th year in business last year, saying its wet processing technologies have facilitated the diversion of over 100 million tonnes of construction, demolition and excavation (CD&E) waste from landfill globally since its inception. As the Australian construction industry continues to shift towards sustainability, CDE Group’s waste solutions present an opportunity for fundamental industry change.
Daniel Webber has been with the company for the past five years and as Regional Manager – Australasia, he says there’s no better time for the Australian market to realise the benefits of CDE Group’s wet processing systems.
“We have proven the success of our wet processing systems with a portfolio of over 2,000 successful projects installed globally,” says Webber. “In Australia, governments are amplifying the importance of sustainable
construction and development; owners are seeking contractors with an environmental, social, and corporate governance (ESG) centric approach; and contractors are seeking materials suppliers with sustainably sourced products.”
“There is vast potential for the Australian construction industry to create a future of sustainability, and CDE Group can help transform that potential into reality.”
With a local presence based out of Queensland, CDE Group has a clear focus on being the best in the world for wet processing technology in the quarrying and recycling sectors. The company’s modular solutions can be deployed, built and commissioned on a customers’ site quickly and efficiently. Its products, ranging from wash plants to conveyors and dewatering screens, cover a range of applications including sand and aggregates, waste recycling and wastewater management.
Together with its customers, CDE Group is diverting millions of tonnes of material from landfill and Melbourne-based building materials recycling company Repurpose It is proving the success of CDE Group’s solutions in Australia.
Repurpose It takes on waste from a number of sectors including construction and demolition, excavation and drilling, road and rail, and infrastructure. In 2017, the company sought new ways to transform CD&E waste into recycled products that meet the requirements of the local industry – leading them to CDE Group. By the end of 2018, CDE Group had supplied and installed a selection of modular elements to enable Repurpose It to launch what is said to be an Australian-first CD&E waste recycling wash plant.
The site has changed the landscape of the industry in Melbourne, explains Webber. “Repurpose It is a company that’s investing to turn construction waste materials around to make the highest end products that it can send straight back out the gate,” he says. “It’s a business that’s targeting large infrastructure projects, making long lasting industry relationships, and making good stewardship of the materials that are coming in to maximise recovery – it’s a pioneering company that CDE Group is proud to work with.”
“Our solution at Repurpose It incorporated several elements including an AggMax
logwasher in the Infinity screening range, a ProGrade H2-60 screen, an EvoWash sand classification and dewatering system, conveyors, a decanter centrifuge and an AquaCycle thickener, and today the plant processes up to 150 tonnes per hour of a single waste input.”
According to Victorian waste flows, Blue Environment’s 2019 report prepared for Infrastructure Victoria, from 2017-2018 CD&E waste made up around 46 per cent of all waste generated in Victoria, which is estimated to be about 6.1 million tonnes. During this time, around 2.7 million tonnes of CD&E waste was landfilled. Backed by CDE Group’s solutions, Repurpose It is striving to improve these statistics, turning this waste into reusable materials for building and infrastructure projects across the state.
The success of the Repurpose It project is a typical result of CDE Group’s solutions. As a company with a commitment to delivering excellence and world class solutions,
“There is vast potential for the Australian construction industry to create a future of sustainability, and CDE Group can help transform that potential into reality.”Repurpose It – AggMax and pile system. Repurpose It harnessed CDE Group’s wet processing solutions to deliver what’s said to be an Australian-first construction, demolition and excavation waste recycling wash plant – this is a back view of the site’s end materials.
CDE Group ensures that by co-creating with its customers, it can deliver imaginative wet processing systems that exceed expectations.
One of the company’s main objectives, explains Webber, is to maximise the recovery of materials by repurposing them into sellable, high-quality products.
Further bolstering CDE Group’s offering is its ability to tackle the more complex waste streams – the “tricky stuff”, as Webber puts it.
“Concrete crushing and screening for example is very much commoditised, and there’s a lot of people out there doing it very well,” he says.
“But when waste streams get a bit trickier – they might be contaminated with wood, plastics, chemicals or hydrocarbons – that’s when we come to the fore.”
“We can still show a recycling route for that tricky material back into the circular economy, and that’s something we’re extremely proud of.”
Its companies like CDE Group that will make Australia’s National Waste Policy Action Plan to recover 80 per cent of all waste by 2030 attainable. As natural resources continue to move further away from metropolitan areas, there arises an obvious business case for the use of recycled materials, because they’re a regenerating source in a metropolitan
setting. The alternative of having to transport sand and aggregates in from out of town is unsustainable.
In the next 10 years, Webber says CDE Group will continue to tackle the more complicated CD&E waste streams. “A lot of the heavy fraction of CD&E waste is contaminated with masonry and low strength materials, so we’re putting a big focus on rejecting that material and separating it out to enable the more recyclable materials to go back into full strength aggregates,” says Webber. “There’s a lot of this kind of waste being handled in regional parts of Australia, so we endeavour to unlock those areas and deliver them the technology that can address contaminated materials.”
“We want to see the generators of CD&E waste, such as Tier 1 and Tier 2 contractors, drive the procurement of recycled materials; we want to foster the relationships between CD&E waste generators and CD&E waste recyclers where the benefits go both ways.
“We want to close the loop directly to enable waste generators to sell their recyclable materials, that otherwise would have been put in landfill, to recycling companies that will take those materials in the gate and sell back the recycled products to be reused in future buildings and infrastructure.”
“We want to see the generators of CD&E waste, such as Tier 1 and Tier 2 contractors, drive the procurement of recycled materials; we want to foster the relationships between CD&E waste generators and CD&E waste recyclers where the benefits go both ways.“
Relationships can make or break construction projects and conflict can have dire consequences. Dr. Gretchen Gagel looks at relationship breakdowns as one of the largest sources of waste in the construction industry.
We’ve all been there on a construction project. At the start, everyone is getting along. We all agree on the goals and the metrics, and then something goes wrong. Then we all start collecting our own data to make sure we are not hung out to dry in claims court. We stop being transparent, we stop collaborating and maybe we even stop constructing.
If you’ve been reading my columns, you know I love to write about a topic that aligns with the theme of the edition. This edition’s theme, construction waste, offered up so many potential topics. One of the largest sources of waste in our industry is the waste associated with breakdowns in relationships on construction projects. The cost of conflict in our industry is enormous. I believe we all
know how to fix it, and yet many times we do not.
About a decade ago a project team called me in to help resolve what turned out to be a $20 million change order on a $40 million guaranteed maximum price (GMP) project. What had gone wrong? In this instance the contractor was too nice to a client that arguably shouldn’t have been executing their extremely unique project as a design/ build project. When the client wasn’t keeping up with the decisions necessary to keep the construction ahead of design, the contractor did not explicitly explain the cost of doing so until each small change and slow decision had resulted in a very big number. That is not helpful.
Or there is the situation I’ve come across many times where different people from different organisations on a project were hung out to dry on their last project, sworn
“Our subcontractors have many valuable ideas, and we should be leveraging these people through strong relationships to reduce waste.”
that wasn’t going to happen on this one, and started covering their you-know-what from day one. These project cultures that lack trust and collaboration are stressful, and enormous amounts of time and energy are wasted.
A different story
Fortunately, I’ve seen many projects that reduce this waste in the following ways:
• Aligning project executives on values and behaviours – If the executives of a project are not aligned it is really difficult to align the rest of the team. As President of Continuum Advisory Group in the US, I had the good fortune to lead a team working with General Motors, Barton Malow and Gensler on a multi-billion-dollar program –three brownfield sites in the US and one in Mexico, sole-sourced (no tender) because speed to market was critical. We spent weeks up front ensuring that the seven executives from these three organisations were 100 per cent aligned on the values (lean, collaboration, win/win), identifying the behaviours that would or would not be tolerated, and discussing the metrics of success. We then met with the next 25 leaders of the projects, and then 60 more leaders of the projects, and gained their buy-in. We documented all of this, put it on big poster boards, and had all 60 people sign huge copies to be posted at each jobsite. We then indoctrinated every subcontractor so that they were in alignment as well. We had to make some tough personnel changes because not everyone got on board, and it sent a strong message. When a significant issue arose on one of the sites, it wasn’t swept under the rug, it was dealt with in a collaborative manner that focused upon solving the problem. We achieved outstanding results relative to safety, budget, schedule, and quality.
• Involving subcontractors – During my time at Continuum Advisory Group, we worked with Procter & Gamble to assist it in implementing lean practices on its projects throughout the world. I was able to see firsthand how involving subcontractors in the constructability of the project paid big dividends and reduced waste. On one project, the internal marketing client for P&G rejected the original 13-month schedule.
During a lean ‘pull planning’ session involving the client, the construction manager, the designers/engineers and all major subcontractors, it was the steel erection subcontractor that stepped up with incredible leadership that resulted in resequencing the project to deal with an equipment delay and achieving a ninemonth schedule. Our subcontractors have many valuable ideas, and we should be leveraging these people through strong relationships to reduce waste. Lean practices are focused entirely upon waste reduction, a good starting point as well. You can hear more about this example on the Greatness Podcast on Spotify, Episode 16.
• Training for collaboration – Most of us learned absolutely nothing during our formal or informal education about how to build relationships and collaborate. In the above example I asked Mike Staun, then Head of Construction at P&G, about how he was going to equip his people to better collaborate via lean practices. The thought had not crossed his mind. Investing in your people and giving them the skills they need to build strong relationships and collaboration can pay big dividends in reducing waste and improving project results.
There are a multitude of other ways to reduce the waste associated with breakdowns in relationships and trust in our industry. The first important step is to be mindful of this relationship-related waste and to put in place concrete strategies and tactics to reduce it.
Dr. Gretchen Gagel is Chair of Brinkman Construction (US), a member of the National Academy of Construction (US), a member of the Construction Industry Culture Taskforce (AUS), and an affiliate professor at the Australian National University and the University of Denver. As President/Managing Director of Greatness Consulting Pty Ltd she continues to advise organisations within the construction industry on optimising capital program delivery and developing talent. You can hear more from Gretchen on her Spotify podcast, “Greatness”.
“One of the largest sources of waste in our industry is the waste associated with breakdowns in relationships on construction projects.”
After almost a decade of experience in construction working for some of the industry’s biggest names, Clare Quinlan has now launched her own workwear company Salus Workwear.
Melbourne local Clare Quinlan has worked in environmental roles for Tier 1 construction companies, established multiple businesses and today steers the success of her latest venture, Salus Workwear.
Proving her ambition has no bounds, the zealous construction professional has moved from state to state and coast to coast completing projects for the likes of McConnell Dowell and Lendlease. She has juggled pregnancy and motherhood along the way, having to move house while six months pregnant for one project and again with her six-week-old and two-year-old in tow for another.
But the construction industry wasn’t always on the cards for Quinlan. “Initially I wanted to be a marine biologist and so I completed a Bachelor of Science at the University of Melbourne,” she says. “Unfortunately, there aren’t many jobs in pure marine biology that involve diving and collecting specimens, so I did some travelling and lived in England for a while before returning home in search of a career.”
As luck would have it, Quinlan fell into a role at McConnell Dowell’s head office in 2008, sparking her enthusiasm for the construction industry and its vast opportunities. Soon after, she moved over to the environmental team within the business.
“I had a science degree that I really wanted to use, and I love the environment, so I was excited to be able to merge the two at McConnell Dowell,” explains Quinlan. “I didn’t even realise there was an opportunity within a construction company to do environmental advising before I started in the industry.”
Her new role as Environmental Advisor led Quinlan to work on the Adelaide Desalination Plant project in 2010, assisting in the management of contractual environmental specifications, legislation, and compliance –where she also met her now husband who was working with Abigroup.
“McConnell Dowell delivered the project in joint venture with Abigroup, and it was great,” she says. “I loved being on site because it’s a completely different world as opposed to working in an office; I’d never experienced anything like it.”
Quinlan recalls in one instance; she was asked by her superintendent to give the
environmental toolbox talk to a room full of 85 men. As a young woman in the first week of her first on site project, she gave the talk with her hands shaking.
Looking back, she says it was extremely daunting, but a rewarding experience. “At the end of the toolbox, everyone applauded me,” says Quinlan. “I was clearly nervous, but at the end of the day everyone is there to do a job and the support I received was second to none.”
When the project was complete in 2011, Quinlan was sent back to Melbourne at the same time as her partner, who was moved to the Peninsula Link Freeway project. She found herself without a project to move to, and so joined Abigroup as an Environmental Coordinator to work alongside him.
As an environmental professional in the construction industry, Quinlan’s key responsibility was to ensure the company was working within the environmental laws and constraints of the site it was working on. She strategically planned ways to minimise or eliminate disruption to sites with Aboriginal heritage areas, First Nations artifacts, protected flora and wildlife habitat zones. Her role also involved monitoring water quality, dust, noise and the effects of weather such as excessive rain on a worksite, as well as controlling and minimising project impacts on surrounding areas.
As an Environmental Coordinator on the Peninsula Link Freeway project, Quinlan says she was given more responsibility. “It was amazing,” she says. “I felt like I was being thrown into the deep end, but in a good way.”
“I enjoyed educating the workforce, through toolbox talks and pre starts, on what the environmental team was doing and why we were doing it.
“It was great to be able to share information and educate, as well as come to a middle ground as a collective where everyone can work together to get the job done.”
After her time on the Peninsula Link Freeway, Quinlan was assigned various projects along the eastern coastline of New South Wales as part of the Pacific Highway Upgrade. This led her to move to Coffs Harbour in 2013 to work on the Nambucca to Urunga section and move again later that year to Byron Bay to work on the Tintenbar to Ewingsdale section. These projects involved Quinlan moving from
“I loved being on site because it’s a completely different world as opposed to working in an office; I’d never experienced anything like it.”Clare Quinlan, Founder of Salus Workwear.
a more boots on the ground role into an office role writing environmental policies, tenders and control plans. Then, in late 2014 she moved to Port Macquarie to work on the Oxley Highway Kundgebung section, six months pregnant with her first born, Heidi.
“Heidi was born in March 2015, and I went on maternity leave,” says Quinlan. “I had established a jewellery business a few years before as a side hustle, so I set up my own home studio for handmaking jewellery and continued selling it to local stores in Port Macquarie, Byron Bay and surrounds.”
“A few years later whilst still on leave, I fell pregnant with my daughter Emma who was born in April 2017.
“By the time Emma was six-weeks-old, my partner was moved to a project in western Sydney, so we moved again – something I don’t recommend doing with a baby and toddler.”
Interested in finding another job in the construction industry after the birth of her two daughters, she looked for an appropriate role but says being expected to be on site at early hours and finishing late as she was in previous site roles wasn’t feasible.
Quinlan didn’t want to put her kids into care every day and with her partner still working long hours as a superintendent in the industry, it wasn’t conducive for her to also take on those long days. “It just couldn’t have worked – to bring up our family in the way that we wanted and have two parents in the construction industry,” she says.
Although Quinlan says flexibility for working families is an ongoing challenge that needs to be addressed by the construction industry, she asserts that the industry provides vast opportunities and positive career paths.
“Construction is a great industry to get into as it can really propel people forward in their career,” she says. “I also love its diversity –there’s an abundance of diverse projects and, like my husband and I, you can travel and work around Australia.”
“We would never have lived in Port Macquarie or Coffs Harbour, or possibly even Byron Bay if it wasn’t for our construction careers, and to live in a number of different communities along the way was amazing.”
The move to Sydney was difficult for Quinlan, given she didn’t know anyone in
the city and had two young children to care for. She explains it wasn’t the best move for her family due to the distant location from her extended relatives, so they packed up again and moved back to their home city of Melbourne in early 2018.
Still there to this day, Quinlan is currently studying her Masters of Education at Swinburne University of Technology, but her grassroots remain in construction. Launching her construction industry branding and workwear business in July 2022, Quinlan has received a flood of support from her previous construction employers and colleagues.
Building Salus Workwear with a focus on increasing the visibility of women in the construction and workwear industries, Quinlan has further expanded her business’s offering to provide work apparel, safety, corporate and leisure wear, and promotional merchandise and uniforms to the health and wellness, sports, education and transport industries.
But she says the construction industry is still at the heart of her business. “I networked and made many connections throughout my years working on various construction projects around Australia,” says Quinlan.
“One of my first clients was McConnell Dowell which is incredible; it is a company I loved working for – it’s as though my construction career has come full circle.”
Having her own business has provided her the means to stay connected to the industry she loves and has been a part of for most of her career. It’s also allowed her the flexibility to care for and spend time with her children.
As a professional who has let little to nothing get in the way of her ambition, Quinlan has one piece of advice for those aspiring to work in the construction industry.
“You’ve got to get in there, jump in and be open to learning as much as you can,” she says. “There’s absolutely going to be challenges and really difficult times, but if you’re assertive and apply yourself the opportunities for growth, both professionally and personally, are limitless.”
You can check out the female-led branding and workwear company at www.salusworkwear.com.au
“Construction is a great industry to get into as it can really propel people forward in their career.”
Lauren Campbell started with building services company A.G. Coombs QLD straight out of school, and now she has a trade and multiple achievements under her belt at just 24 years of age.
As an Air Conditioning Service Technician at A.G. Coombs QLD, Lauren Campbell works on an extensive range of commercial buildings, from small shopping centres to large-scale universities.
Providing ongoing servicing of heating, ventilation, and air conditioning (HVAC) equipment, as well as covering HVAC breakdowns and repairs, Campbell has excelled in her role, completing her Air Conditioning and Refrigeration Apprenticeship in 2020.
Her career journey has been full of experiences since joining A.G. Coombs QLD in 2017 – including a lot of firsts, she says. “Gaining my first full-time job has allowed me to take my first flight, travel for the first time to places like Melbourne, Sydney and Port Douglas and also achieve smaller firsts such as backing a trailer and composing a quote,” says Campbell. “My journey at A.G. Coombs QLD has always brought me great joy.”
“I love the team I work in, and I am excited to see where I can go in this industry as there are vast opportunities – you just need to know how to grab hold of them.”
Looking back, Campbell says she loved being outdoors and being active from an early age. She would follow her dad around and ask questions about what he was doing, something she says she still does to this day.
This passion for learning continued into her school years, and as graduation loomed, Campbell started to think about what she wanted her future to look like. During school she worked at Kmart, but she knew she wanted to branch out of retail into a more hands on industry. She also didn’t want to jump into a university degree or career on a whim.
“I was still unsure about where I wanted to take my career, so my father suggested I do some work experience in the construction industry alongside my retail job,” says Campbell. “I jumped at the chance because I simply wanted to experience the unknown.”
The opportunity arose to do work experience with A.G. Coombs QLD during the September school holidays of her Grade 12 schooling, and she’s thrived within the company ever since.
“I loved it,” she says. “I saw the potential to learn and thought that it would be, at worst, a
great starting point in life and, at best, a career that could see me progress all the way to the top.”
Today, as a fully qualified tradesperson, Campbell’s workday typically consists of repairing and servicing HVAC equipment, which can range from washing filters and changing belts, to investigating issues and faults in equipment. She also mentors the apprentices within the company, teaching them the various tasks that are required to maintain a building’s HVAC system.
Currently on light duties due to an injury, Campbell is working on a lifecycle report for a building she looks after as part of her role with A.G. Coombs QLD, requiring her to attend the building site and complete a condition report on all of the HVAC equipment for the building manager. The report’s findings predict the life expectancy of each piece of equipment, enabling the building manager to prepare a budget for replacement or repairs.
Campbell says it’s these kinds of tasks that remind her how versatile her job is. “Every day is different,” she says. “I am able to be outdoors and interact with people all day long.”
“Problem solving is my favourite part of what I do – there is nothing better than being faced with a challenge, figuring it out and seeing the satisfaction on the clients’ faces when you present them with the solution.”
It’s no secret that Campbell loves what she does, and the sector has recognised her hard work and dedication along the way. In 2021, she won the Air Conditioning Mechanical Contractors Association (AMCA) Onsite Tradesperson Award. Also in that year, Campbell was named Harry Hauenschild Apprentice of the Year at the Queensland Training Awards, winning against apprentices from a number of sectors across the state.
But closest to her heart, she says, was winning A.G. Coombs QLD’s highly prestigious Apprentice Award – the Alan Coombs Training Award – in 2020. “To win this award with the recognition of the entire company was amazing,” says Campbell.
In her six years in the construction industry, Campbell says she has gained an abundance of new knowledge, had a wealth of opportunities and has been supported by A.G. Coombs
“I love the team I work in, and I am excited to see where I can go in this industry as there are vast opportunities –you just need to know how to grab hold of them.”
QLD to be the best Air Conditioning Service Technician she can be. When she first joined the company, she says she didn’t even know that air conditioning was its own sector in the construction industry. “I didn’t realise how much of the city is run by air conditioning,” says Campbell. “People rely on us.”
Now, knowing the vast opportunities the industry presents, Campbells advice to those looking for a career in construction is to be open.
“The construction industry can be challenging at times, and I’m not going to sit here and say it was a breeze for me being
a female that entered into a predominantly male workforce, but I love it,” she says. “The opportunities the industry can bring you is amazing – there are endless paths you can go down.”
“But ultimately, my advice would be to complete some work experience, as without doing work experience myself I would never have known about the air conditioning sector.
“In just six years, I’ve completed my four-year apprenticeship, have become a fully qualified Air Conditioning Service Technician, and have set the groundwork for many more opportunities to come.”
“My journey at A.G. Coombs QLD has always brought me great joy.”
Lauren Campbell, Air Conditioning Service Technician, A.G. Coombs QLD.
Attracting workers to the Australian construction industry has been a cornerstone of our nation for generations. Although we are facing rising interest rates, the sector still faces a growing population and increased demand. This trend has led to enhanced requirements for housing and infrastructure in 2023 and beyond. With intensified investment in the construction sector, there is an opportunity for significant growth across all areas of the industry. This presents an exciting prospect for those wanting to enter the construction industry and those wishing to progress their career. With the skills shortage, there has never been a better time to take advantage of these new opportunities.
Women entering the construction sector
landscape, driving change, and shaping the future of this great industry. By getting involved, women can help address the gender gap by inspiring others, bringing fresh perspectives and ideas to the table and creating an inclusive environment for all. Women in construction can be the driving force behind positive change, helping to reduce conflict, raise morale and improve mental health in the industry. In addition, by sharing their knowledge and experiences with men, women can help create a culture of respect, trust and collaboration. However, women in construction face unique challenges due to the male-dominated nature of the industry. Although we have seen a slow and gradual increase in the number of women
Despite the host of challenges facing the construction industry, job openings in the sector are booming, and Empowered Women in Trades is calling for women to take advantage of the opportunities available.
“Women entering the construction sector have a unique opportunity to be involved in projects shaping the country’s economic landscape, driving change, and shaping the future of this great industry.”
Executive Officer and Founder, Empowered Women in Trades.The Empowered Women in Trades team at the inaugural Gala. L-R: Chairperson of the Board Tina Wyer, Head of Commercial Hannah Keirl, Founder and Chief Executive Officer Hacia Atherton, and Head of Programs Melinda Davis.
and retention in the industry. There is still a culture of discrimination, harassment and a lack of female role models. Many women also report feeling like they must work harder than their male counterparts to prove themselves. Despite these challenges, many women have successfully navigated the construction industry and succeeded in various roles, including project management, engineering, architecture and trades such as carpentry, plumbing and electrical work.
To support women in construction, it is important to promote diversity and inclusivity within the industry and provide resources and support for women to succeed. This is one of our key focuses at Empowered Women in Trades (EWIT) –to run educational programs tailored to the unique needs of women entering the construction industry. Early this year, we held our inaugural Awards and Fundraising Gala, raising $19,000 towards delivering programs
for vulnerable and at-risk women to support them into skilled trade career pathways.
EWIT is also passionate about working with like-minded companies to support them to actively recruit and retain women in their workforce whilst creating a culture of respect and inclusion for all employees through our culture renovation programs.
There really has never been a better time for women to pick up the tools and enter the construction industry, which will help propel the industry forward, creating an impact that will be felt across all generations. With so much potential for growth and development, this is a chance to make history and for Australia to become a world leader in supporting women in construction, particularly within skilled trades.
Let’s break down gender stereotypes and encourage more people to pursue careers in construction – regardless of their gender or background.
“There really has never been a better time for women to pick up the tools and enter the construction industry.”Empowered Women in Trades’ Inaugural Award winners.
This year’s Future of Construction Summit (FCON23) is set to ignite positive change. It will see government, industry and union leaders come together to discuss a collective and disruptive response to the industry’s challenges.
Appropriately themed ‘FCON Disrupted’, this year’s event is based on the premise that the industry cannot afford to continue down the path of slow incremental change. It is time to fundamentally disrupt how it operates, if for no other reason than to ensure the industry has sufficient workers to deliver the infrastructure that Australia can afford. With both influencers and decision makers in the room, a new audience will be descending on the summit, the disrupters. Yes, the voices of the industry’s emerging leaders will be amplified – Gen Z. FCON23’s Gen Z panel discussion is highly anticipated with five industry graduates and undergraduates set to send a compelling message to the audience.
Over the two days of the summit, speakers will tease out themes from the Australian Constructors Association’s report, Disrupt , released in late 2022. What disruption is most required – industry diversity and inclusion, working hours and flexibility, environmental sustainability, productivity or risk allocation? Maybe the answer is all. Disrupt or die report, productivity improvements are identified as the critical link to the future success of Australia’s construction industry. The Australian Constructors Association believes the biggest opportunity to improve industry productivity lies in improving how projects are procured, delivered and governed – essentially white-collar activities. Fortunately, there are many opportunities to improve whitecollar productivity quickly whilst blue-collar productivity will likely take more time and, arguably, is reliant on the former. Technology has a role to play in this. There is no shortage of technology solutions available to improve the efficiency of the construction industry and many of these will be exhibited at Day 2 of the summit. The issue is, however, there are many barriers to using them. Several of the Day 1 panels will
investment in technology.
Imagine
FCON23 is about thinking big and committing to bold new ways of working.
Imagine if we could close the productivity gap between construction and other major industries? We could be saving $47 billion annually and, most importantly, improving the lives of workers.
Imagine if the industry could deliver a $1 billion project with a two-page contract? We could build an industry based on trust that innovates and finally achieves digital by default.
Imagine if women made up 30 per cent of the industry’s workforce? We would enjoy a
In the lead up to the 2023 Future of Construction Summit, Australian Constructors Association CEO Jon Davies looks into this year’s theme – FCON disrupted – and the benefits that could come from the radical overhaul of obstructive industry practices.
“FCON23 is about thinking big and committing to bold new ways of working.”
bedroom? Even site engineers could have flexibility to work from home. Imagine if the construction industry could reach net zero in just five years? We could all breathe easy.
It is all possible, but the industry needs to shift its mindset around change. Incremental change and 10-year horizons are out. Change must happen now.
A transformed industry
Disruption is daunting but it is less risky than continuing the current course. Everyone has a part to play – government, industry and unions.
The government, as the nation’s largest infrastructure client, has great power to
environment and unleashes innovation. It is positioned to incentivise the states to procure in a way that promotes training and upskilling of the workforce. It could even mandate adoption of initiatives that promote greater participation of women in the industry. The opportunities are endless.
Industry and unions also have the power to disrupt. That is why the Australian Constructors Association will be making a pledge to do things differently and attendees at FCON23 will be the first to hear.
Join us and together we will make Australia’s construction industry the envy of the world.
For more information on FCON visit futureofconstructionsummit.com
”With both influencers and decision makers in the room, a new audience will be descending on the summit, the disrupters.“Jon Davies presented on Day 1 of last year’s Future of Construction Summit.
The SafeWork Australia Work Health and Safety (WHS) Strategy 2023-2033 report, which was released in late February, is a national WHS strategy agreed to by all states and territories aimed at reducing workplace fatalities, injuries, and illnesses. It sets a national vision of safe and healthy work for all, providing a platform for delivering key WHS improvements.
The Formwork Industry Association (FIA) supports this strategy and looks forward over the next decade to continuing its commitment to healthier, safer workplaces.
This strategy notes that while fatality and injury rates have generally fallen over the last decade, the progress has slowed. It states, “education, innovation and collaboration will be critical enablers of success” – something the FIA has been advocating and actioning for the past few years.
According to the strategy, construction continues to have one of the highest rates of fatalities and serious injuries and has one of the highest frequencies of serious claims per million hours worked.
FIA Chief Executive Officer Michael Sugg says if the competency of individual workers increases, improvements in safety, productivity, and quality will follow. “This has led us to look at long-term solutions to current industry issues,” says Sugg. “There is a need for the Australian formwork industry to build its own education and skills pathway.”
“We need a new education and skills pathway to improved safety and better buildings, towards a relevant formwork qualification that includes new recognition of prior learning processes.
“We need a new industry recognised accreditation scheme and micro credential learning and verification of competency processes that build on a worker’s skills and capabilities.”
This is a pathway to accredited training, but one that needs urgent steps to re-engage the learner and enable accessible education for formworkers.
Sugg says we must remember that these workers often left school and education at an early age, that there is no need (at present) for them to attain any qualification to work on site (other than a White Card), and there are no incentives for workers to upskill or improve
their competencies, or for their employers to assist.
On top of this, access to training is difficult, lengthy, inflexible, and unresponsive to industry needs and the processes for keeping track of workers’ training, competency, skills and qualifications are often costly and both time and labour-intensive.
With an ageing workforce and a future skilled labour shortage, the industry must act now to build a secure and safe future for itself and its workers.
“A key factor in improving industry safety, quality and productivity is to lift the competency of its workers,” says Sugg. “As a start, we need to re-engage the formworker in learning, build their confidence and pride and provide incentives for learning before we can ensure there is a demand for certified training provided by the Departments of Education and funded by the government.”
FIA President Jason Andrijic says that over the past two years, the Association Board has been working with industry to develop this pathway.
“Stage One proposes the re-engagement of workers in learning, focusing on WHS issues to improve safety and a pathway to certified training,” says Andrijic. “We are pleased to announce, with the support of the NSW Department of Education, that we can launch the first part of our pathway, the Safe Formworker Program.”
What is the Safe Formworker Program and how do workers access it?
Developed in consultation with the formwork industry, this program is a pathway for workers to receive micro credential learning on formwork-specific WHS issues to increase awareness of formwork safety.
Delivered via a modern mobile learning experience, the Safe Formworker Program offers bite-sized mobile courses that teams can actually enjoy, complete with gamification and real rewards built-in.
With video and image-based learning, along with gamification, it is hoped the program will re-engage workers in learning, tackle language barriers and prepare workers for further learning. It will cover the important aspects of formwork WHS issues and improving formwork safety awareness on site
The formwork industry is taking the lead and has secured funding to improve formwork safety on construction sites, with a focus on education, innovation and collaboration as critical enablers of success.
“Education, innovation and collaboration will be critical enablers of success.”
refresher courses, access to additional courses, a place to store their licences, White Card and any other training certificates – making everyone’s life a lot easier.
Feedback from a recent pilot program was exceptional with one head of safety saying: “I have been in the formwork industry for 20 years and have not come across training like this, which is easy to understand and complete, and relevant to the work I do.”
The program includes five courses and 13 lessons and can be viewed on the FIA web site. Each lesson takes only five minutes or less and can be delivered in toolbox talks or on rain affected days in the shed.
FIA Vice-President Stefano Calautti says that when the program was rolled out during toolbox talks on site, where workers were able to access the program easily via their mobile phones, he found that the change in atmosphere and attention given by workers was incredible.
“All workers were fully engaged in the learning, and the gamification aspect of the lessons delivered engagement in the room, with workers sharing their phones and scores with one another,” says Calautti. “Worker’s feedback included comments that it was ‘easy to use’, ‘relevant to my work’, and ‘it makes me feel safer that my workmates are doing the course as well’.”
After a successful pilot program and confirmed industry support from both construction and formwork companies, the FIA is pleased to announce that the NSW Government, through the Department of Education, has agreed to fund the placement of 1,000 workers through the program in the coming months.
Michael Sugg is currently presenting the program to various construction and formwork companies and discussing how it
and overcome the ‘tick box’ mentality to training that currently exists.”
The SafeWork Australia WHS Strategy 20232033 report states that achieving reduced worker injuries, illnesses, and fatalities requires embedding good WHS practices, innovating and deepening knowledge of WHS risks to broaden understanding of workers. It states that collaborating consistently to respond to WHS challenges is critical, something the FIA Safe Formworker Program certainly achieves. It also states that companies need to make sure that during projects, there is meaningful, relevant and comprehensible training for workers. It supports the continuation and strong focus on compliance and enforcement by regulators, with a particular focus on systematic WHS management.
Jason Andrijic is very positive about the new formwork education and skills pathway, which is getting off to a good start with the Safe Formworker Program. “The feedback and responses have been very promising and with 100 workers already through the program, I am sure we can hit our targets,” he says. Re-engaging workers in learning and covering important WHS aspects is a priority of the program, and, from early reports, it looks like ‘education, innovation and industry collaboration’ will be critical enablers in the success of the SafeWork Australia WHS Strategy and improvements in safety awareness on site in the formwork industry.
FIA Chief Executive Officer Michael Sugg says, “As a result, we all firmly believe we will see not only improved safety, but productivity and quality on projects.”
Details of the program can be found on the FIA web site and safety managers are encouraged to contact Michael Sugg to discuss how to achieve the target of 1,000 workers through the program to improve site safety.
“We need a new education and skills pathway to improved safety and better buildings, towards a relevant formwork qualification that includes new recognition of prior learning processes.”
The construction industry has long been a majority male populated field, with women making up only a small percentage of the workforce – currently at 13.5 per cent according to the Australian Bureau of Statistics, 2022. The industry is slowly evolving, and more women are pursuing careers in construction. At The National Association of Women in Construction (NAWIC), we are advocating to industry and government for #25by25. This means working together towards the goal of 25 per cent female participation by 2025 – a goal that gets us closer to 30 per cent participation, which is where we know real cultural change happens.
At NAWIC we take a strategic view across the career lifecycles of women, focusing on their high school education and exposure to construction career opportunities, through to the access to growth opportunities such as senior management, business scale and sale, and participation at board level. This is our industry’s pipeline of human resources. To increase female participation in construction, together we must stem the leaks across each stage of our pipeline. Together we need to develop ways that we can proactively attract,
retain and grow women so that they may enjoy the safety, economic security and career fulfilment the industry has to offer.
To encourage this trend and ensure that women can thrive in the industry, it is crucial that safe learning environments are created for young women in construction at TAFE and university.
This month at NAWIC we are drawing awareness to the challenges faced by our members at TAFE and university – those who are at the very beginning of their careers. We understand that female students are choosing not to continue their studies in the construction industry because of negative and/or unsafe experiences in the classroom and/or in the workplace. Queensland Minister for Employment and Small Business and Minister for Training and Skills Development
Dianne Farmer identified in the Breaking Down Barriers report (2022) under 50 per cent of women who commence trade apprenticeships go on to complete their qualifications in Queensland. It is evident to us at NAWIC that we are losing more than half of the pipeline for women in construction before they even have a chance to begin.
Driving awareness of the challenges faced by Australia’s youth, The National Association of Women in Construction is advocating for safer learning environments for young women looking to start a career in construction.
”To increase female participation in construction, together we must stem the leaks across each stage of our pipeline.“
Creating safe learning environments for young women is about ensuring women feel safe and supported in these environments. Intimidation and objectification are not acceptable.
The construction industry can be intimidating for young women especially. Our members commonly say they were made feel out of place or unwelcome in the early days of their career and have experienced bullying and intimidation in their learning environments. “Unfortunately, we still have instances where trainees and apprentices, in particular women, are made to feel unsafe or uncomfortable in the workplace and this is simply not acceptable,” Minister Farmer said. “We must remove these barriers so trainees and apprentices can confidently complete their training.”
In the right kind of learning environment women can focus on their studies and thrive. Learning providers need to ensure that they have anti-bullying policies in place, and that they are adhered to by their staff and students alike. Having more female teachers will help young male students observe women’s technical competence and translate to improved cultural outcomes in the workplace. Creating safe learning environments promotes diversity and inclusion in the industry. The construction industry has historically been lacking in diversity, which has led to a narrow perspective and limited creativity in the field. By encouraging women to enter the industry and providing them with a safe place to learn, construction can become more creative and innovative.
Important learning takes place in our educational environments and prepares students for the workplace. Occupational health and safety forms the start of the curriculum in most construction industry education programs. By providing women with the knowledge and skills they need to work safely in the industry, we can ensure they are protected from harm and able to succeed in their careers.
A safe learning context helps to break down stereotypes and stigmas associated with women in the industry. Unfortunately, there are still some who believe that women are not capable of working in construction or that they do not belong in the field. By providing
women with a safe learning environment and supporting their careers in construction, we can help to change these perceptions and promote equality in the industry.
The Breaking Down Barriers report delivered 12 recommendations for improvements to gender equity; Minister Farmer said seven of the recommendations relate to improvements for female apprentices.
At NAWIC we advocate for industry and government to:
• Implement the 12 Queensland recommendations from the Breaking Down Barriers report, 2022.
• Establish a National Gender Equality Strategy.
• Encourage more female teachers in TAFE and university learning environments.
• Call upon education providers to ensure safe learning environments and have policies to stamp out bullying.
We are working closely with the Australian Construction Industry Forum and our many industry and government partners to ensure that the voice of our members is heard nationally. Importantly, we are seeking confirmation that measures are being put in place to create the systemic culture that ensures the safety and economic security for women in construction, particularly those at the start of their careers. By investing in safe learning environments for young women in construction, we can help to build a more diverse, inclusive, and successful industry for everyone.
If any of this is triggering for you, please connect with the NAWIC Member Assistance Program on 1300 878 379. It’s a free 24 hours a day, seven days a week service staffed by mental health practitioners available to support NAWIC members.
”By investing in safe learning environments for young women in construction, we can help to build a more diverse, inclusive, and successful industry for everyone.“
While the construction industry in Australia is a major contributor to the economy, it faces an intractable labour productivity challenge.
conditions, less cluttered and safer sites, faster construction and cost savings. Importantly, waste produced during the manufacturing
safety performance and practices, quality processes and outcomes, and their track record generally.
With an increase in government spending on civil projects taking place across Australia, she says this has never been so important.
“The industry is busier than ever and that means the association’s members and other construction stakeholders need to be as efficient as possible and use reputable suppliers,” says Bachmann. “It’s now that companies need to be considering smarter ways to build and using more off site manufactured products.”
“Also critical is investing in upskilling workers, better time management and improved practices right across the board.
“Quality control needs to be transparent, from the developer down, and that flows on to precast manufacturers – accountability and transparency are key.”
The Productivity Commission Inquiry into Public Infrastructure Costs report (2014) points to three possible measures for the construction industry to reduce waste – better procurement and project management skills, improved supply chain integration, and using technology to enhance project outcomes.
Amid Tasmania’s civil industry post COVID-19 boom, one company has identified an opportunity to use technology to make inroads into better streamlining its own manufacturing processes while delivering benefits to its construction industry partners and asset owners.
National Precast Master Precaster Hudson Civil has engaged digital software company CONQA to introduce transparency into its quality systems and both the precaster and its clients are realising the benefits of digitising.
Located in Launceston, Tasmania, Hudson Civil manufactures precast infrastructure elements for civil, mining, building development and rural projects. The company has evolved over 20 years to become one of the leaders in major precast products and innovative design.
At the heart of the company’s operations is a robust quality assurance system to ensure that engineering design intent is realised, especially around reinforcing requirements and Australian standards, to ultimately reduce risk and maximise production efficiency.
The company has recently transitioned from a traditional paper-based system to a digital system.
According to Hudson Civil Engineering Officer Michael Ross, being guided by CONQA made the process simple.
“While our paper-based system worked well and we had minimal quality issues, going digital has taken it to another level,” says Ross. “Paper had its limitations, there were always the challenges of documents being misplaced or damaged, and they were difficult to consolidate.”
“This is not only easy for our guys to use, but it brings everything out into the open – it gives our clients access to the documentation and processes we are happy to share, and that would have otherwise taken hours to compile.
“Our clients are happy as they are kept informed of progress and it gives them confidence that we are on top of everything.”
Looking at the Hudson Civil example, Bachmann says using a Master Precaster who has invested in digitised quality assurance not only reaps the rewards of off site manufacturing, but of manufacturing processes that are transparent as well.
“Clients are rapt with the results,” she adds.
“It’s now that companies need to be considering smarter ways to build and using more off site manufactured products.”Using precast concrete minimises site waste because exact, complete elements are delivered and installed.
Inside Construction
Expo 2023 will be held from 20 to 21 September at the Melbourne Convention and Exhibition Centre.
Melbourne’s premier construction and infrastructure event Inside Construction Expo 2023 will amplify the transformation of the commercial and civil construction sectors, and with excitement already brewing it’s time to plan your visit.
An event dedicated to major commercial and civil projects in the Australian construction industry, Inside Construction Expo is being held from 20 to 21 September 2023 at the Melbourne Convention and Exhibition Centre. With a robust conference program featuring top level speakers, a world-class exhibition showcasing the latest in equipment and technology and the Inside Construction Foundation Awards celebrating talented industry individuals and businesses, Inside Construction Expo 2023 is a must-attend event.
The significant investment growth in construction and infrastructure projects across Victoria in recent years, such as the state’s Big Build, makes Melbourne the ideal location for the Expo’s launch.
Set to connect major constructors with OEMs, sub-contractors and operators, Expo Events Manager Lauren Winterbottom says the event is positioned to further foster the successful delivery of projects currently in the pipeline.
“Inside Construction Expo was created to fill the apparent gap in events targeted at major commercial and civil projects,” she says.
“With such a large investment in infrastructure, we’re seeing the best in new
When: 20 to 21 September 2023.
Where:
The Melbourne Convention and Exhibition Centre.
Convention Centre: 1 Convention Centre Place, South Wharf, Victoria 3006. Exhibition Centre: 2 Clarendon Street, South Wharf, Victoria 3006.
Why:
To bring together all facets of the Australian construction industry to share and discuss solutions to current and future challenges – and pave the way for industry transformation.
“Throughout the conference attendees can expect to hear from executive-level representatives from Australia’s major constructors and suppliers.”
Whether you’re a project manager, superintendent or an engineer, all professionals in the field of construction are invited to attend Inside Construction Expo 2023. Registration is completely free for both the exhibition and conference. You’re welcome to come and go as you please and curate a conference experience that suits you.
As the construction industry continues
industry developments – from safety to technology – rolled out before our eyes.”
In the 2022-23 Federal Budget, the Government increased its 10-year infrastructure investment pipeline to a record $120 billion. The 2022-23 Victorian Budget outlines $85.3 billion in general government spending on infrastructure over the next four years.
There’s a plethora of projects planned nationwide for the coming years, but considerable industry challenges remain. Inside Construction Expo 2023 will provide a platform to canvass solutions to the issues hampering the commercial and civil construction sectors.
With four stages across the event focusing on Health, Safety and Wellbeing; Training, Education and Careers; Digital Transformation and Connectivity; and Construction Productivity; there will be a wealth of industry information and solutions on offer.
“Throughout the conference attendees can expect to hear from executive-level representatives from Australia’s major constructors and suppliers, alongside research and education bodies and government figures,” says Winterbottom.
• T he National Association of Women in Construction.
• T he Working at Height Association of Australia.
• T he Concrete Pumping Association of Australia.
• T he Institute of Quarrying Australia.
to face ongoing challenges, from skills shortages and lack of digitisation to poor productivity and inadequate safety management – this year’s Inside Construction Expo will encourage transformation and a brighter future for the sector.
If you’d like to attend, exhibit, submit a presentation or become a sponsor visit www.insideconstructionexpo.com.au
“The exhibition show floor spans up to 15,000 square metres across 10 bays and will display the latest in construction machinery and equipment.”
Inside Construction Expo is backed by support from a number of valued organisations and media partners. Without this support Winterbottom says the event would not be possible.
“We’re pleased to be partnering with industry associations and peak bodies to bring Inside Construction Expo to life,” she says. “Specialist in assembly and fastening materials Wurth Australia has come on board as a supporting sponsor for the Expo, and intelligent positioning solutions provider Position Partners is proudly sponsoring the conference.”
“In the lead up to the event, over 19 industry-leading publications continue to extensively cover the latest in Expo news reaching more than 80,000 decision makers across multiple sectors.”
Exclusive sponsorship packages are now available to promote your corporate identity and to advertise your products and services leading up to, during, and post-event.
“The exhibition show floor spans up to 15,000 square metres across 10 bays and will display the latest in construction machinery and equipment.”
• T he Crane Industry Council of Australia.
• T he Formwork Industry Association.
• L andscaping Victoria ‘Master Landscapers’.
• T he Piling and Foundation Specialists Federation.
Inside Construction Expo 2023
Showcasing the innovative people and projects that are making waves in Australia’s major construction and civil infrastructure industries, the Inside Construction Foundation Awards will take place as part of Inside Construction Expo on Wednesday 20 September 2023.
The Awards will recognise the individuals and businesses promoting initiatives, innovation and safety throughout major and local projects.
Nominations are now open in 10 categories.
The Rising Star of the Year category recognises an individual aged 35 years or younger at the date nominations close, who has impressed their colleagues and counterparts with their contribution to and impact on their organisation, and excellence in service.
The Industry Leader Award recognises
a leader who holds a senior position (executive, manager, director, or equivalent) in a private, not-for-profit, or government organisation who has effectively shaped their business’ success, delivered financial growth, significantly and positively impacted the business’ culture and championed the industry widely.
The Woman of the Year category recognises a woman in the industry who has driven change and continues to do so, leading to progress in breaking down barriers and creating new career prospects for the next generation.
The Operational Excellence Award recognises an individual or team that has achieved demonstrable improvements in efficiency, best practice Occupational Health and Safety, and impeccable records.
The Sustainability Initiative of the Year
category, sponsored by SAMI Bitumen Technologies, recognises a company with a product, technology, system, initiative or project that has developed and carried out an innovative, environmentally focused, sustainable program to protect, preserve and/or rehabilitate the natural environment, contributing to decarbonisation and/or reducing waste and/or waste emissions.
The Safety Program Award, sponsored by Blackwoods, recognises a program, project or initiative aimed at promoting and improving safety, either within a business or across the broader construction industry.
The Technology Solution Award , sponsored by FRAMECAD, recognises a supplier of technology to a construction business, equipment manufacturer or subcontractor that improves a process, delivering tangible benefits across financial, safety or sustainability measurements.
The Major Project of the Year – Commercial category recognises the completion of a stage of a major vertical construction project, or complete project delivery, that has been delivered with demonstrably positive results in the areas of budget, safety, social target and sustainability.
The Major Project of the Year –Government category recognises the completion of a stage of a state-funded project, or complete project delivery, that has been delivered with demonstrably positive results in the areas of budget, safety, social target and sustainability.
The Local Government Project of the Year category recognises the completion of a stage of a local government project, or complete project delivery, that has been delivered with demonstrably positive results in the areas of budget, safety, social target and sustainability.
“If you are involved in revolutionising the construction sector, providing a solution for a constructor or an individual driving positive change in the industry, we want to celebrate you,” says Winterbottom.
“Nominating is free and open until 11:59pm Friday 14 July 2023 – and all finalists receive a complimentary ticket to attend the Awards night in Melbourne.”
What’s more, the Foundation Awards gala dinner will provide a premium networking opportunity with industry leaders. Nominations can be submitted for free online at foundationawards.com.au
The Awards will recognise the individuals and businesses promoting initiatives, innovation and safety throughout major and local projects.
For the past 26 years the Australian Constructors Association and Engineers Australia have promoted the Australian Construction Achievement Award to celebrate the best of the best in Australian construction.
Following a record number of entries, seven finalists have been selected in 2023 to compete for the title of winner of the Australian Construction Achievement Award (ACAA). What makes these projects the best of the best is not just the awe-inspiring structures. The ACAA recognises projects where companies are actively contributing to a more sustainable industry. You don’t see these things when driving along a road or walking into a building. This year’s finalists are going about their work differently. They are implementing digital tools
and processes to improve productivity. They are investing in training and development initiatives to equip workers with critical skills. They are creating flexible working environments that support workers’ mental and physical health. They are breaking down barriers to entry while also building a more inclusive and diverse workforce. Collaboration is strong not just within project teams but throughout the supply chain. Moreover, these finalists are actively working to reduce the impact on the environment for future
safe access across the rail corridor for vehicles and pedestrians, upgraded station precinct surroundings and improved the commuter experience on the Frankston line.
By McConnell Dowell Constructors (Aust) and Major Road Projects Victoria. This project consisted of construction of a second Murray River crossing between Echuca and Moama, together with a bridge over the Campaspe River, earth embankments and flood relief bridges on the adjacent floodplains. It was delivered by Major Road Projects Victoria (MRPV) and constructed by McConnell Dowell in both Victoria and New South Wales on the traditional lands of the Yorta Yorta people.
By CPB Contractors and Major Road Projects Victoria.
The M80 Upgrade widened 5.7 kilometres of the M80 Ring Road between Sydney and Edgars roads, adding additional lanes, ramps, collector distributors and a smart freeway system – all in and around live traffic flows of 165,000 vehicles per day. Clever technical solutions and a strong innovation and sustainability culture saw the project completed a year ahead of schedule and $122 million under the client’s budget.
By Southern Program Alliance (ACCIONA Rail, WSP, Metro Trains Melbourne, and the Level Crossing Removal Project).
The Southern Program Alliance’s (SPA) Edithvale, Chelsea and Bonbeach Level Crossing Removal Project package removed five dangerous and congested level crossings and built three new stations on the Frankston line in Melbourne’s south-east. This created
By John Holland Group.
This world class entertainment venue seating up to 42,500 people was designed for the fans. Offering visitors and patrons an optimal entertainment experience, its enhanced
“These finalists are actively working to reduce the impact on the environment for future generations.”
generations. Australia’s construction industry will be stronger for this.
With just the one award up for grabs, the competition is fierce.
The award would not be possible without the support of ongoing industry partners Adbri, Caterpillar, CBUS, InEight and InfraBuild. Each plays a significant role in the development of the Australian construction industry.
The winner will be announced at a black-tie gala dinner presentation event on 3 May 2023, the first day of the Future of Construction
design enables accessibility, safety, sightlines and operational efficiencies. This complex structure was an integrated engineered solution, delivered to the highest quality, on time and budget as a result of its highperforming team culture.
Summit (3-4 May in Melbourne). The following day, audiences at the summit will hear firsthand the technical solutions being presented by major contractors and suppliers. Keep an eye out for the Shark Tank as five leading ConTech start-ups share their solutions to meet the everevolving challenges of modern construction.
To find out more visit: ACAA acaa.net.au
Future of Construction Summit futureofconstructionsummit.com
tunnels, representing a total tunnel length of 21,580 metres. It connected the M4 at Haberfield to the M8 at St Peters and integrated into the whole of WestConnex Integration Operation and Management Control System. The project involved excavation, civil and mechanical and electrical work over three main sites. This included the construction and energisation of six substations and two low point sumps and construction of surface ventilation buildings, cut and cover structures, local roadworks and a Water Treatment Plant.
Parramatta Light Rail Stage 1 connects Westmead to Carlingford via Parramatta CBD, with a two-way track spanning 12 kilometres long, including 5 kilometres within the existing Carlingford and Sandown Lines, along with 16 fully accessible stations and 12 new or refurbished bridges. It is expected to commence services in 2024. Parramatta Connect delivered the infrastructure works package of the project.
The WestConnex M4-M5 Link Tunnels project constructed two 7.5-kilometre underground
3, 4, 6 & 8
By Built in joint venture with Obayashi and in partnership with Walker Corporation and Parramatta Council.
Built in a joint venture, Obayashi was engaged by Walker Corporation and Parramatta Council to deliver one of Australia’s largest urban regeneration projects including four commercial towers, civic hub, and public domain for the new $2.8 billion Parramatta Square Precinct. Establishing Parramatta as Sydney’s second CBD, the works included commercial and retail builds, fit-outs, interconnecting basement, integrated transport access and public domain works.
”The winner will be announced at a black-tie gala dinner presentation event on 3 May 2023, the first day of the Future of Construction Summit.“
Recognising the success of women from across industries, the Women in Industry Awards is returning in 2023 with a special new construction industry sponsor on board.
• Social Leader of the Year.
• Rising Star of the Year.
• Business Development Success of the Year.
• Industry Advocacy Award.
• Mentor of the Year.
• Safety Advocacy Award.
• Excellence in Manufacturing.
• Excellence in Transport.
• Excellence in Engineering.
• Excellence in Mining.
• Excellence in Construction.
• Woman of the Year.
In 2023, the annual Women in Industry Awards (WII) celebrates its 10th year of acknowledging the incredible women championing positive change in their industries. This year, The National Association of Women in Construction (NAWIC) has come on board as the sponsor of the Excellence in Construction Award.
To be held on 8 June 2023 in Melbourne, it’s a premier event on the industry calendar.
After witnessing last year’s event, NAWIC General Manager Lauren Fahey says her team was inspired to show their support through sponsorship.
“The Women in Industry Awards is a significant event that celebrates and amplifies the achievements of women’s contributions to the sector,” she says. “It’s a prime example of our mantra – you can be what you can see – and we are excited to support an event that showcases the amazing achievements of women.”
Celebrating women across the construction, infrastructure, engineering, mining, road transport, logistics, rail, bulk handling and waste management industries, this year’s awards will once again present examples of industry excellence, advocacy and mentorship.
Sponsored by NAWIC, the WII Excellence in Construction Award recognises an individual who has made a positive contribution to one of the many facets of the construction sector, an accolade that strongly aligns with the important work NAWIC does as a peak industry body.
“Supporting women in industry is a significant way we all can improve female economic security, overcome the skills and labour crisis, and deliver greater profitability and innovation to industry,” says Fahey. “At NAWIC we think that’s worth advocating for.”
“Sharing stories of successful women in construction is both empowering for the
recipient and inspiring for the wider sector; this award is so important for the industry as a whole.”
Nominations for the 2023 event closed in mid-April and Fahey says the NAWIC team will be there on the night to witness the remarkable women being highlighted as nominees and winners. A free NAWIC membership will also be offered to the nominees and winner of the Excellence in Construction category.
“Our hope is to connect these women to the amazing NAWIC network that we have across the country to continue to foster the support and growth of these women,” she adds.
As well as recognising the women spearheading change in the construction industry, the WII shines a light on a number of industries where women make up a small percentage. Fahey explains that supporting and recognising women helps to change the culture of the construction industry and the other male dominated industries across Australia.
“These awards demonstrate that women do belong in industries like construction, engineering and mining, and can have a rewarding career,” she says. “WII’s purpose of supporting outstanding women driving change and breaking down barriers aligns closely with our values.”
“These women are exactly the type of women that built NAWIC; these women are our mentors, our guiding forces, our members and our volunteers.
“We advocate for change, and these women are creating change every day to help pave the way for future generations.”
To join NAWIC and other inspirational women, buy your ticket to the 2023 Women in Industry Awards online now at: www.womeninindustry.com.au
“These awards demonstrate that women do belong in industries like construction, engineering and mining, and can have a rewarding career.”The National Association of Women in Construction has come on board as the sponsor of the Excellence in Construction Award.