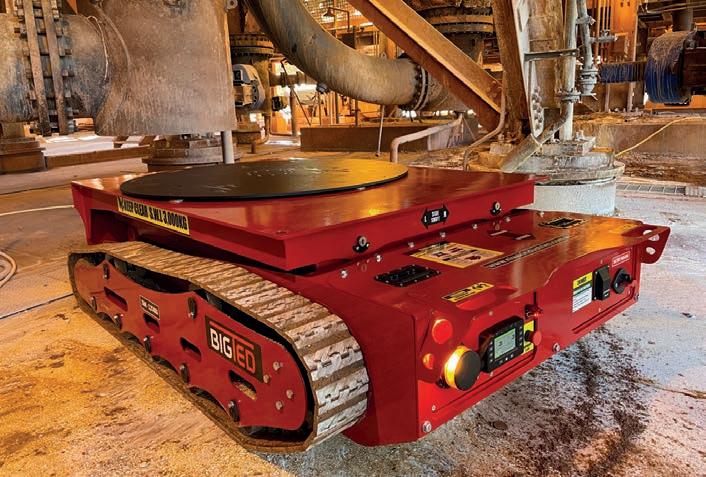
3 minute read
Removing workers from the crush zone
NIVEK INDUSTRIES’ NEW, LARGER AND MORE POTENT TRACKED ELEVATING DEVICE – BIG TED – IS AN ESSENTIAL PIECE OF SAFETY GEAR FOR MAINTENANCE PERSONNEL WORKING ON SUSPENDED LOAD HAZARDS.
When Kevin Cant narrowly avoided serious injury while conducting routine maintenance back in 2008, he realised the traditional way of doing things could stand to improve.
Cant was placed in harm’s way as a result of a belly plate slipping and falling from a dozer, and over the next three year he undertook detailed research and concept design and ultimately developed the first tracked elevated device (TED) prototype in 2011.
That same year saw the launch of Nivek Industries, an Australianowned manufacturing and fabrication company that prides itself on quality products utilised in mine and industrial maintenance applications.
Safety in the workplace is paramount, especially when working around heavy machinery, and the outcome of an incident is usually catastrophic. Kevin understood that the old methods of removing mobile plant components such as belly plates – a difficult, dangerous, and time-consuming task involving hoists, slings and chains – was no longer acceptable.
Nivek’s TED is a self-propelled belly plate jack designed to take the weight out of belly plate extraction and replacement while removing personnel from suspended load hazards, safeguarding against potentially fatal crush injuries.
“TED enables the safe removal of machinery components by removing the suspended load hazard and transferring the manual handling element onto the TED,” Kevin’s brother and Nivek general manager Derrick Cant told Safe to Work
The device incorporates several key design features, including remote-control operation, all-terrain capability, and low profile. It is also easily adaptable through the use of its ever-expanding range of practical attachments designed to increase the safety, efficiency and reliability of worksite operations.
TED can make myriad maintenance jobs safer and less physically stressful for technicians and other personnel, reducing planned maintenance times and driving cost-efficiencies.
“TED fundamentally improves the safety and working conditions of maintenance personnel using the TED, when either deployed in the field or in workshop,” Cant said.
Big TED is a new a larger version that features an expanded capacity to move heavier loads. The bigger unit can comfortably handle weights up to 3000kg, while maintaining a relatively low profile and enhanced manoeuvrability.
“We’ve received strong interest from the market for a bigger version of the TED and that’s been the motivation to make the Big TED, especially for clients with specific maintenance requirements,” Cant said.
“Due to its increased lifting capacity, we envisage Big TED being used primarily on fixed plant maintenance tasks, or in conjunction with heavy mobile machinery and mining equipment,” Cant said.
“Essentially, it is a mobile scissor lift that can be easily modified by way of attachment to suit a wide variety of specific needs.”
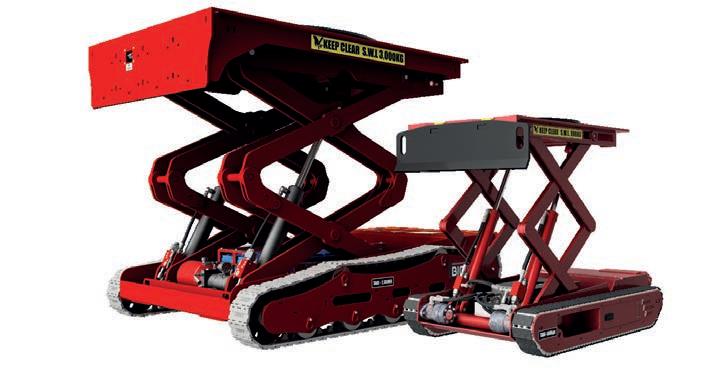
The drive system, comprising two independent 3.5kW infinite control electric drive motors, is controlled by a proportional joystick on the remote control. Not only do the motors provide sufficient torque to carry the heavy loads across any terrain, the machine is also extremely responsive and operator friendly.
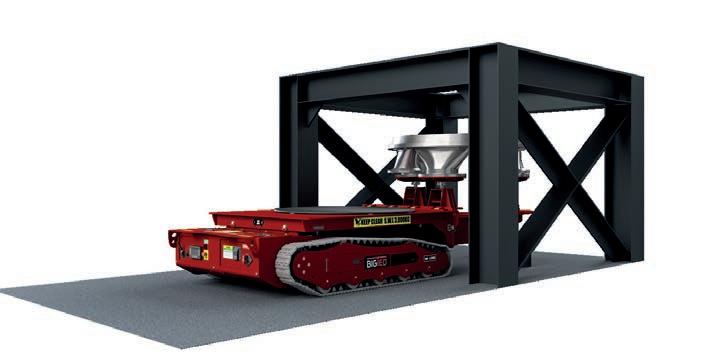
The 24V, 448Ah rechargeable battery system provides operators with at least two hours of continuous operation.
“We have taken all the feedback received over the years from customers using TED and have incorporated many of the features into the Big TED design,” Cant said Some additional features of Big TED include remote-controlled side shift, powered turntable and AUX (auxiliary port) functionality to enable the utilisation of smart attachments. The machine also has built-in load cells to measure the load and a tilt sensor to ensure it is operating within design parameters.
“Attachments for the Big TED can be designed and manufactured to the client’s specific requirements.” Cant said.
A large resources organisation recently embarked upon a trial of the Big TED, aiming to improve safety and efficiency in a challenging operational environment.
The Big TED was utilised in the removal and installation of large vessels (digestor pots) undergoing scheduled maintenance, a time- and labour-intensive activity that can be difficult and dangerous.
The use of Big TED significantly increased workers’ ability to undertake their maintenance in a safer way, while halving the time it usually takes to complete the task.
Due to its increased load-bearing capacity and functionality, Big TED is being trialled on other maintenance tasks by the same organisation, also making traditionally difficult-tocomplete maintenance safer, easier and more efficient.
Designed by a fitter, for fitters, the TED and Big TED are becoming widely sought-after among both workers and management throughout the mining industry.
Cant and his team at Nivek seek to provide a tailor-made solution based client requirements, and their willingness to embrace feedback has led to ongoing improvements to the TED and its range of attachments.
“We are committed to creating innovative products for heavy industry that enhance workplace safety and efficiency,” Cant said.
“With attachments designed in all different shapes and styles, the range of tasks that Nivek’s TEDs can complete is endless.
“We have attachments designed for general maintenance, as well as more specific jobs on Liebherr Ultra Class, Caterpillar, Hitachi, Komatsu, LeTourneau, Terex and many other types of machinery.
“Whether you’re working on haul trucks, dozers, graders, scrapers, service carts, push carts, water carts or any other heavy machinery or fixed plant, TED or Big TED and the tailored attachments provide a stable base to safely conduct maintenance from.”