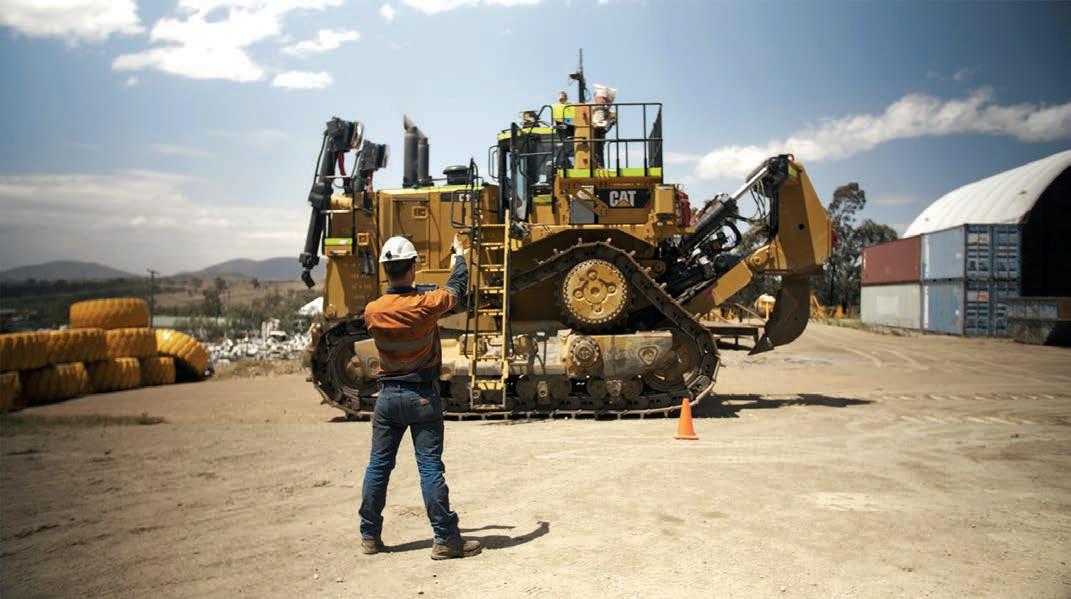
4 minute read
Avoiding the line of fire
SAFEGAUGE HAS DEVELOPED AN INNOVATIVE RANGE OF DIAGNOSTIC TOOLS DESIGNED TO REMOVE TECHNICIANS FROM DANGER WHEN COMPLETING THE LIVE TESTING OF HEAVY MOBILE EQUIPMENT.
Some of the simplest tools are the most powerful.
In the case of SafeGauge, the company has designed exactly these kinds of tools to eliminate the chances of technicians being severely injured when completing live testing on heavy mobile plant machinery.
SafeGauge founder Luke Dawson routinely tested machinery across a variety of mine sites during his time working as a heavy plant mechanic. He was concerned that workers were regularly exposed to the unnecessary risk.
“I felt there was a need to improve the safety outcomes for technicians servicing mobile equipment, and in doing so have a positive impact on the mining industry,” Dawson told Safe to Work
“There’s been far too many fatalities and serious injuries on mine sites, or in workshops, simply through technicians doing their job.
“The risk involved with human and machinery interaction has always been significant, and although many of the maintenance tasks are routine the dangers are ever-present, so I really wanted to remove technicians from those dangerous zones and, in essence, eliminate that safety risk.”
To that end, Dawson commenced research and development on a specialist wireless testing solution that would enable technicians to monitor and test heavy mobile plant machinery from a safe distance.
“My initial idea was to develop a wireless transducer, connected via Bluetooth and with a transmission distance of up to 50m, in order to complete steering and brake pressure calibrations,” Dawson said.
“In the past, a technician would have to plug a mechanical pressure gauge connected through a highpressure hose into different parts of a machine or hydraulic system in order to complete the test, and in doing so would place themselves in unsafe, potentially dangerous positions.
“By utilising a wireless transducer such as the smart pressure transducer (PT) developed by SafeGauge, a technician can complete the same diagnostic test from the same ports once used with a hand-held pressure gauge, but now at a safe distance from the machine or equipment.
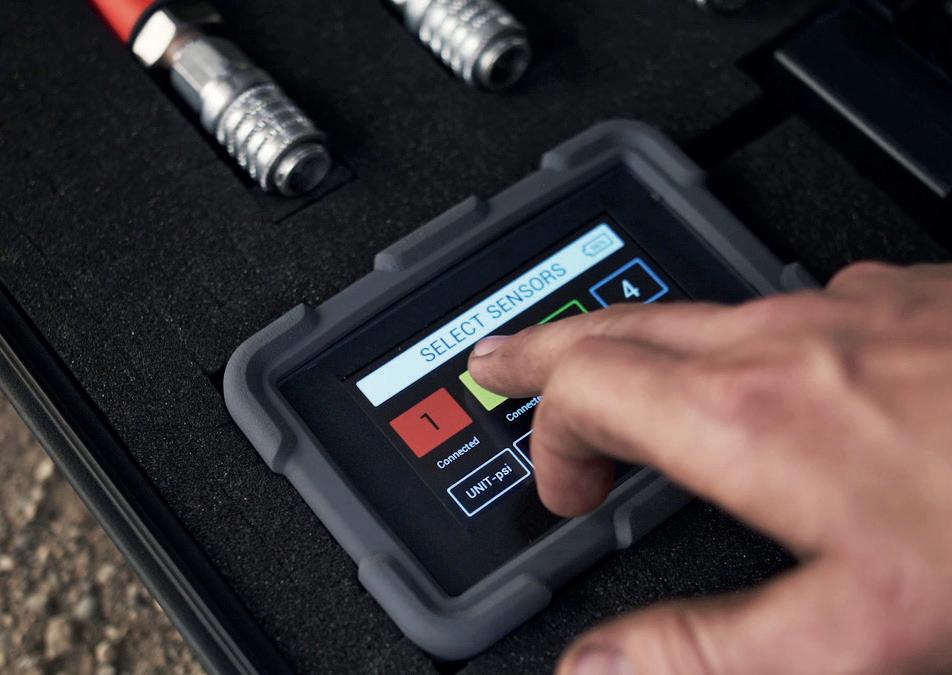
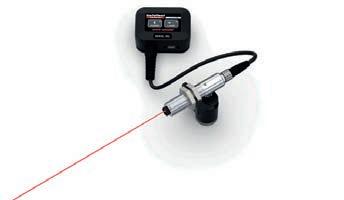
“Essentially, the requirement to hold a high-pressure hose in an unsafe spot to complete the pressure test has been removed.
“Previously, you would have to stop and start the machine or equipment in order to place the gauges on different parts to test different systems, and you’d need to be physically connected to the machine, completing one test at a time.
“Now, with SafeGauge’s solution, multiple tests can be completed simultaneously and safely by utilising several PTs connected to the Wireless MultiTool (W-MultiTool), with the technician far from the crush zone.”
The development of a dial indicator (DI), also utilising a Bluetooth connection from up to 50m away, was the next diagnostic tool that would remove the requirement for a technician to read a physical dial while the plant was live.
SafeGauge has now produced the multi-award winning SafeTest range of PTs and DIs, developed for heavy industry applications.
A SafeTest PT Series kit consists of two, four, six or seven PTs, plus the W-MultiTool and charging case. The kit is suitable for measuring gas or fluid in a variety of pressures.
SafeTest tooling functions from up to 50m away, allowing workers to stay clear from the crush zones and line of fire when live testing.
The PT connects to the W-MultiTool, which displays the live pressure readings, has a battery life of more than 20 hours, and is easily recharged using the rugged case.
Using the SafeTest MultiTool enables up to seven PTs to be tested and displayed on the device. Each connected tool has an option for a customised title, and customised software for the W-MultiTool is also available. SafeGauge can provide tailored solutions for specific customer requirements.
The latest PT Series comes with an improved design based on in-field use and customer feedback, and includes an improved rugged dual-layer housing, shock-proof silicone outer protection, an auto-sealing charging slot for increased water resistance, and a customisable labelling system for greater flexibility.
There are various pressure range options, including 25 bar, 100 bar, 300 bar and 600 bar.
The SafeGauge DI is a Bluetooth device designed to measure displacement within 0.01mm. With Bluetooth connection from up to 50m away, technicians retain the ability to complete maintenance safely and more efficiently.
“With the requirement to measure wear on large pins and bushes on various parts of the frame of a machine, the DI is also designed to move the technician away from crush areas while testing is underway,” Dawson said.
“In the past, the technician would have to be positioned close enough to be able to read a mechanical dial fixed to different parts of the machine.
“The SafeGauge DI ensures the technician can now undertake this task remotely, as the wireless transmission technology keeps the technician clear of the machinery and any exposure to potential dangers.”
DI Series kits are available in one, two and four channels, as well as a customised kit option, and are supplied with everything needed to set up and conduct testing, including high-quality mag bases.
The SafeTest FS3 series kit consists of two PTs, one DI, the W-MultiTool and a charging case, making it the perfect all-in-one kit for rapid breakdown response crews and field service teams.
Packaged in a compact hard-shell carry case, and with built-in charging harness, the SafeTest FS Kit is ready to go at a moment’s notice.
The SafeTest tachometer (TM) series enables completely wireless measurement of revolutions per minute (RPM), removing technicians from the live work area while measuring the speed of fans, pumps, drill heads and other rotating machinery components.
“A technician was previously required to stand in front of a fan, often 3m in diameter and spinning at 2000–3000RPM, operating a handheld tachometer in order to measure the fan speed,” Dawson said.
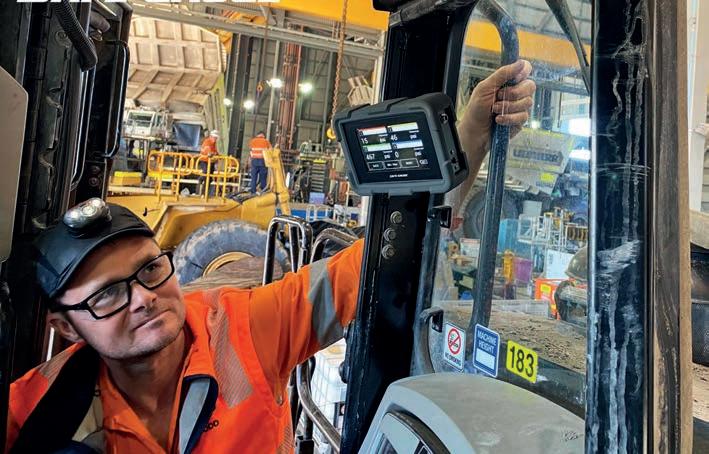
“In this instance, the technician is exposed to potential projectiles coming off the fan, exposed to failure of the fan, while being physically located on the machine, in the line of fire and unseen by the operator as the machine is running.
“The SafeTest TM has the capability, via Bluetooth, to accurately read fan speed from the operator’s cabin, further removing the technician from any form of potential harm.”
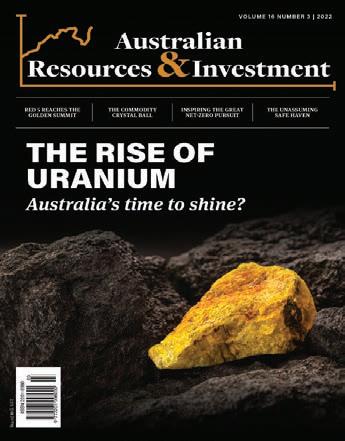
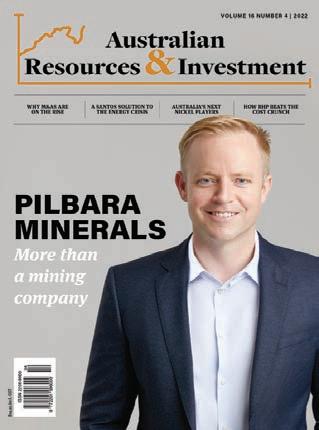