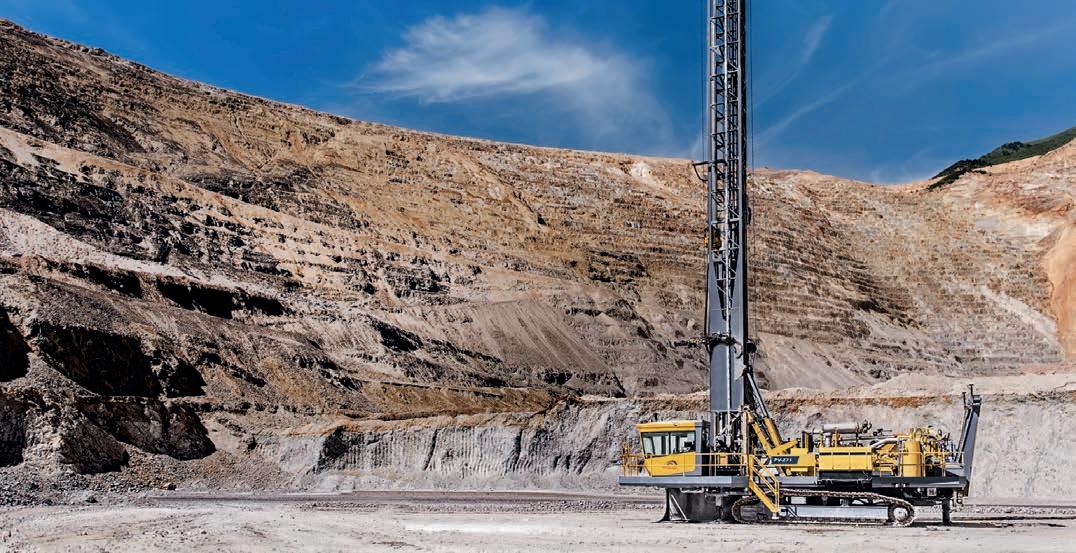
4 minute read
Maintaining the Pit Viper is a team effort
EPIROC’S DRILL RIG IS A ROBUST AND RELIABLE PIECE OF EQUIPMENT, REINFORCED BY A TEAM-BASED APPROACH TO MAINTENANCE THAT EMBRACES SAFETY WHILE ACHIEVING REDUCTIONS IN DOWNTIME.
Epiroc’s Pit Viper series of drill rigs is highly regarded in the global resources industry.
Pit Vipers are renowned as safe, flexible and cost-effective blasthole drilling machines that are extremely efficient, productive and, with rigorous planned maintenance, incredibly safe.
Epiroc’s machines are built in stateof-the-art facilities, and the high-quality fabrication ensures the capacity to last through multiple re-powers.
The PV-271 can operate in almost any surface mining application, whether it is gold, copper, coal, iron ore or silver, and is regarded as the drill that put the Pit Viper on the map.
The drill rig is available in diesel or electric and is automation-ready, which means system upgrades and addons can be completed without major machine rebuilds. It is equipped with a standard Rig Control System (RCS) operating platform, setting a high bar for efficiency and productivity.
Now in its fifth generation, Epiroc’s RCS platform is the foundation of Pit Viper automation. RCS 5 has an enhanced control hub with improved usability, allowing operators to switch seamlessly between screens in a well organised and dynamic manner.
The new drilling data screen on the RCS 5 features real-time depth monitoring, while operators can now create and edit drill plans on-board or from a remote location quickly with the drilling plan manager.
Critical maintenance is completed through a flexible approach, with major componentry placed within a module – effectively a frame – that can easily be inserted into the Pit Viper upon the removal of ageing components.
“On that frame is the engine, drive train, compressor, pumps and fire suppression equipment, essentially the heart of the machine,” Epiroc’s national service operations manager – parts and services Steven Hayes told Safe to Work
“The way the PV-271 has been manufactured has made it easy for us to create these modules for significantly shorter periods of planned maintenance, resulting in significant uptime.
“The modules are pre-built in a workshop environment before being transported to site, where a brief shutdown occurs. The old module is removed and the new module inserted.
“The beauty of this approach is that it removes the requirement for an extended period of on-site maintenance, where the harsh and sometimes unstable environment of the Pilbara can lead to unforeseen problems and delays.
“This approach is fundamentally safer and faster, as the Pit Viper is offline for a minimal amount of time.”
The PV-271 can be configured with the XC (extra capacity) package, boosting its bit load capacity from 34 to 42.5 tonnes.
In October, Epiroc announced it had won a large equipment order from CITIC Pacific Mining, with a fleet of automated PV-271XC rigs to be used at the Sino Iron open-pit mine in the Pilbara region of Western Australia.
The drills bound for CITIC Pacific Mining will feature Epiroc’s exclusive autonomous drill plan execution (ADPE) technology, a unique feature in that it enables the rigs to complete full drill patterns rather than single rows.
The PV-271XC drills will also be installed with AutoDrill, which allows for up to 100 per cent of the drilling cycle to be in automatic mode. This is alongside AutoLevel, which minimises the time it takes to level and de-level, enabling more drilling time in the process.
“If any component doesn’t meet expectations or fails on the PV-271, we have a dedicated team located in Newman (in the Pilbara) supporting mining operations,” Hayes said.
“We can move quickly to undertake any unplanned repairs or servicing as required or, alternatively, provide the necessary support and expert advice to our customer’s on-site maintenance personnel.”
The PV-270 series of drill rigs also includes the 275 model, which has become a staple for its capability in coal overburden drilling and hard rock applications like copper and iron ore.
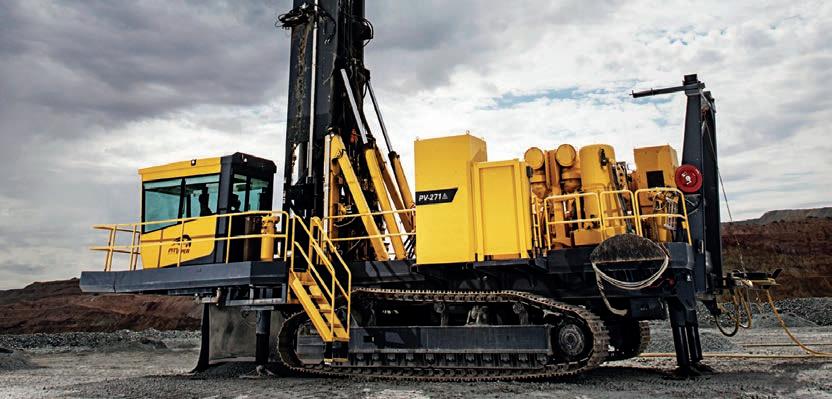
The original Pit Viper – the PV-351 –offers 56.7 tonnes of bit load capacity, making it the most powerful drill rig in the Pit Viper range.
While Epiroc can offer diesel and electric options for the Pit Viper, more and more customers are opting for the zero-emission route.
There are now 116 electric PVs globally, split between Latin America, Africa, Europe and North America.
Recent orders by Tier 1 mining companies highlight the global reputation of the PV range, and the increased electric push of the drill rigs reflects Epiroc’s broader decarbonisation strategy.
Epiroc has become a market leader in automation, digitalisation and electrification solutions.
The company places a premium on safety, achieved through a sophisticated approach to the maintenance and servicing of mining machinery such as the Pit Viper series of drill rigs.
Whether scheduled maintenance or unplanned repairs, Epiroc’s dedicated professionals understand the machinery and are dedicated to ensuring it is fully operational.
“Completing maintenance via a modular approach means that when the major components on the PV271 reach their 20,000 hours of service, everything gets changed at once,” Hayes said.
“Essentially, it’s the equivalent of resetting the machine and with Epiroc’s quality control we’re confident the machine is able to perform its next 20,000 hours without the requirement for significant maintenance-related downtime.
“Before utilising a modular approach to undertaking planned maintenance, a great deal of perceived pressure would impact upon maintenance teams as they felt they had to complete a significant amount of work on-site over a relatively short period of time.
“The impending deadline to complete the work would create undue pressure and lead to safety issues. So what would once take 12 days to accomplish can now be completed in three or four days.
“Today, the pressure is on the maintenance team to install just the one module and once completed the PV271 Pit Viper can quickly re-commence operation, demonstrating superior reliability and productivity, ultimately contributing to the lowest total cost of ownership in the blast hole drilling industry in its class.”