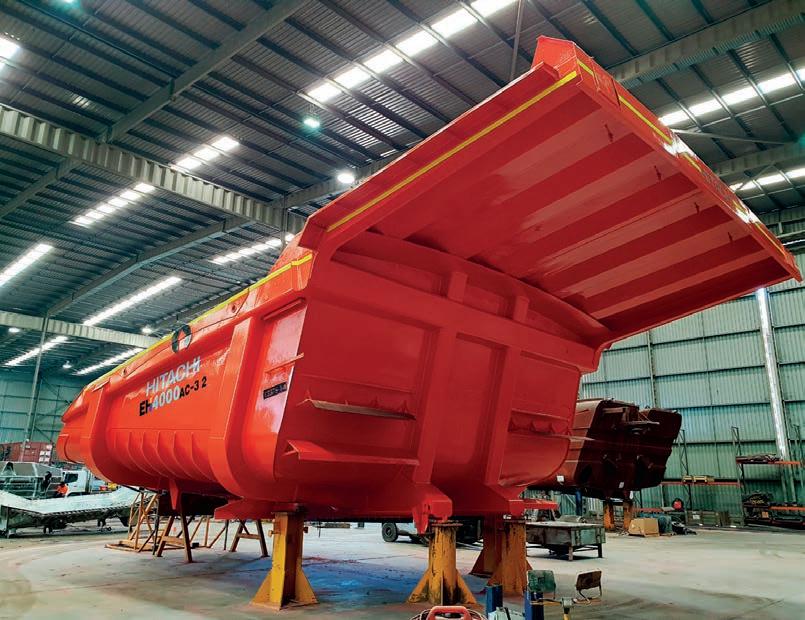
3 minute read
Going isocyanate-free to improve maintenance performance
Maintaining the reliability of equipment remains one of the most important considerations on a functional mining operation, almost indistinguishable from the need to ensure the health and safety of the workforce.
Corrosion remains a constant threat to equipment, plant and infrastructure across the resources sector. And that corrosion is often encouraged by environmental or chemical conditions that come from operating amid harsh surface conditions or deep underground.
The quality and functionality of equipment is crucial to successful mining and the requirement for consistent and efficient maintenance is vitally important.
Major rebuilds and ongoing repairs remain critical to the sustainability of machinery, and a key consideration for effective maintenance remains the suitability of paint for the protection machinery surfaces.
“We have engineered the optimum formula, ideally suited to the harsh environment of the Australian mining industry,” A&I Coatings business development and customer satisfaction manager Bill Chesterfield told Safe to Work
With decades of experience engineering polyurethane coatings for mining equipment, A&I Coatings is consistently providing the local and global market with leading paint solutions for heavy plant and machinery.
In many applications where machinery needs to be painted, safety is paramount. It is essential that maintenance workers are not exposed to harmful chemicals such as isocyanates.
“Over the last 18 months our research and development team have been developing the first isocyanate-free polyurethane coating, called Vitrethane 650,” Chesterfield said.
Utilising patented technology, Vitrethane 650 is considered a breakthrough in the coating industry. With a quality-control system run by A&I Coatings, the new product complies with ISO 9001: 2015 and is a registered manufacturing unit with the Australian Paint Approval Scheme. It represents a significant advancement in protective coatings, specifically topcoats used for new builds, major repairs and the ongoing maintenance of surface and underground mining gear.
This new technology completely removes the risk of exposure to isocyanates found in polyurethanes. This results in a safe and environmentally friendly coating that provides zero exposure to harmful chemicals during application while retaining the hard-wearing and maintenance-friendly characteristics of an isocyanate-cured polyurethane.
A&I Coatings has engineered Vitrethane 650 to be more durable and more sustainable than traditional isocyanate-free coatings.
Many companies are using enamels, catalysed acrylics, or modified epoxies to reduce workplace harm; however, these coatings can be brittle and often have poor impact-resistance.
These coatings are also said to be less able to withstand atmospheric elements such as acid-rain, salt sulphates, or ultraviolet (UV) exposure, all of which can lead to an early breakdown of the coating and, in turn, expose the machinery to corrosion and increase maintenance costs.
In some cases, this may lead to a shortened machine lifecycle or a reduction in its ability to function properly.
“As these coatings break down, the integrity of the paint and the substrate is affected,” Chesterfield said.
Mining haul trucks are a classic example of equipment where the body of the machine is often subject to scrapes and impacts.
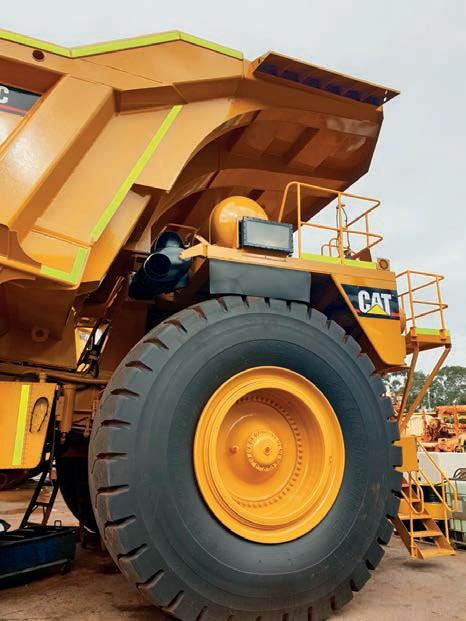
“Modified epoxy and catalysed acrylics are examples of commonly used coatings that retain poor reverse impact (resistance), typically shattering and deaminating on the exterior of machine bodies caused by the impact of rocks or other hard materials falling into the tray,” Chesterfield explained.
Compared to current coatings used on mining equipment, Vitrethane 650’s resistance to adverse damages remains critical to achieving the best value from the truck body.
Vitrethane 650 allows mine sites to function at peak productivity, avoiding higher levels of downtime associated with constantly repainting and maintaining machinery, or similarly removing machinery for repairs due to corrosion or damage at off-site locations.
Complementing A&I’s isocyanatefree polyurethanes is Vitrephos 560, an isocyanate-free epoxy primer.
Vitrephos 560 has high-quality application and drying properties in cold weather, wet-on-wet properties with ease of sanding, and effective film builds that have seen a significant reduction in the number of hours required to complete projects.
As a smooth-drying application, the enhanced topcoat achieves significant surface coverage, ensuring reductions in planned downtime are consistently achieved.
With Vitrephos 560 primer and Vitrethane 650 topcoat, A&I Coatings offers a complete isocyanate-free coating system that is versatile and can be used across most mining equipment and machinery applications.
By displaying the desired balance of mechanical properties, such as flexibility, impact resistance, surface hardness, toughness and adhesion, Vitrephos 560 and Vitrethane 650 exceed the service requirements for a specific application and withstand the adverse effects of corrosion and other damage.
Companies can be assured there is no risk of exposure to harmful chemicals for employees, and no need to compromise on quality.
Vitrethane 650 is available in high-gloss, semi-gloss and satin finishes, and in an unlimited colour range, including fleet, construction, agricultural and earthmoving machinery colours. Users can expect the topcoat to function like any high-performing polyurethane, from chemical-, abrasion-, and adhesion-resistance to weathering performance and flexibility, all without endangering the health of workers while removing the requirement for ongoing maintenance.
“We saw there was a need in the market for a high-performing and extremely durable coating that could withstand harsh environments and, importantly, did not contain dangerous isocyanates and significantly reduced maintenance costs,” Chesterfield said.