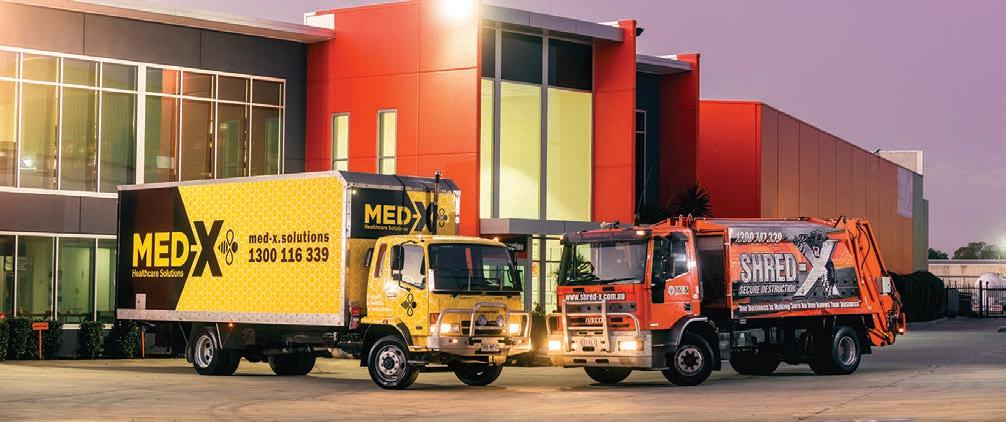
12 minute read
BEYOND DESTRUCTION
Beyond the destruction
SHRED-X DIVERTS ALMOST 50,000 TONNES OF PAPER PER ANNUM FROM LANDFILL, PARTNERING WITH AUSTRALIAN RECYCLING ORGANISATIONS TO RECOVER AND REPURPOSE THE MATERIAL IT COLLECTS.
Shred-X’s Med-X operations ramped up during COVID-19, with the company’s investment in robotic technology encouraging contact-less waste recovery.
Australians throw out 2.7 million single-use coffee cups every day, adding up to almost one billion coffee cups a year.
Van Karas, General Manager at Shred-X, says to efficiently recover and repurpose products, there has to be flexibility to enable current business capabilities to increase landfill diversion.
“It’s in our DNA to ensure wherever possible, following the required destruction process, the products we collect are recycled or repurposed,” he says.
Although Shred-X started out in the document destruction and paper recycling industry 20 years ago, Karas says the company has since expanded, pursuing recycling for an array of products other than paper including used coffee cups, QSR waste, e-waste and textiles.
Karas stated that following some recent tests, it has partnered with an Australian packaging company to collect and process their 100 per cent recyclable coffee cups.
“We’ve also invested in new ways of processing millions of ‘non-recyclable’ coffee cups, partnering with another Australian company that’s leading the way finding innovative solutions for recycling and repurposing use coffee cups aiding a circular economy,” Karas says.
Shred-X is continuing to align itself with the United Nations Sustainable Development Goals (SDG’s), which were first implemented into the global sector in 2016.
“One of the SDG’s Shred-X is actively working towards is building resilient infrastructure, promoting sustainable industrialisation and fostering innovation,” he says.
By 2025, Australia has committed to National Packaging Targets ensuring 100 per cent of packaging is either reused, recycled or repurposed. Further to this, an Australian chain of quick service restaurants (QSR’s) are also aiming to recycle its customer packaging and waste.
According to Karas, Shred-X has
always been a business that collects and processes specialised waste in line with recyclers needs.
“We’re working very hard with resilient partners to achieve common goals. Following an upcoming trial, we will be looking at smart innovations that add value to processing QSR waste, ensuring it goes to recyclers that will continue to add value to the waste product,” he says.
“It’s pretty impressive that we’re able to help companies achieve national targets by finding a new home for waste besides landfill. Shred-X are working with a range of partners and have begun undertaking trials with quick service restaurants to achieve their sustainability targets.”
Shred-X has achieved the highest industry certifications for its secure destruction facilities and operations located in every state and territory which incorporate the latest and most environmentally sustainable shredding technologies. Through the company’s partnership with Australian recyclers, Shred-X recovers 98.5 per cent of the material collected and processed through its facilities. Shred-X has also introduced a range of innovative secure destruction solutions for textiles and uniforms, high-end garments and accessories, seized goods, recalled items and liquids with an aim to ensure ethical disposal and landfill diversion whenever and wherever possible.
Environmental Policy and recycling partnerships reflect the company’s ongoing commitment to improving the sustainability and resilience of the business, while also ensuring its services remain cost-effective and best practice.
The company has applied these same foundational goals of sustainability and innovation to the medical waste industry through its Med-X Healthcare Solutions brand. Shred-X and Med-X have continued to invest in technology and innovation that

support the reduction of landfill and promote recycling, even amid essential operations during the peak of the COVID-19 pandemic.
Karas says Med-X operations ramped up during the COVID-19 pandemic, spotlighting the company’s investment in robotic technology to encourage human contact-less waste disposal and recovery.
“Plastic is infinitely recyclable and we like to think if people choose us, they know they’re part of a sustainable chain that positively impacts the wider community and environment,” he says.
On the other hand, the e-waste sector has its challenges. Shred-X pioneered IT asset management, destruction and recycling solutions when Australian businesses were beginning to go paperless.
“People thought we were just taking their paper and not doing anything with it, but beyond secure shredding, we’ve been a firm leader in removing all information contained on electronic and IT assets and responsibly recycling or repurposing the end components.”
As more offices convert to digital only businesses, Shred-X has been continually exploring further opportunities with ewaste, textile and fibre recycling and repurposing partners, plastic product developers and waste-to-energy processors.
“Shred-X works with our partners to recycle all electronic components of ewaste including precious metals, glass and plastic, as well as repurposing assets once the confidential information contained on the assets is removed,” he says.
“We’ve been led to so many avenues from beginning with just pieces of paper. Our exploration of sustainable recycling and destruction is undertaken in the most ethically responsible manner, to suit even the most stringent sustainability targets and government regulations.”
Managing OTR in the Pilbara
A NEW JOINT VENTURE BETWEEN TYRECYCLE AND KARIYARRA CONTRACTING WILL SPECIALISE IN END-OF-LIFE OFF-THE-ROAD MINE-SITE TYRE PROCESSING WITHIN WESTERN AUSTRALIA’S PILBARA REGION.
Establishing partnerships and joint venture opportunities that will create wealth and employment for Kariyarra people is one of eight key outcomes listed in the Kariyarra 2019-2022 Strategic Plan.
Since the plan was released, a new joint venture has been formed between Tyrecycle and Kariyarra Contracting.
The venture will focus on processing end-of-life (EOL) off-theroad (OTR) mine-site tyres within Western Australia’s Pilbara region.
Thereby linking to the Strategic Plan’s mission to create opportunities and effectively manage the land of the Kariyarra People.
The venture is a 50 per cent Indigenous controlled joint partnership, with direct input from the traditional owners of the Port Hedland area.
Kariyarra Contracting is a wholly owned subsidiary of the Kariyarra Aboriginal Corporation, which is the Registered Native Title Body Corporate for the Kariyarra People.
Stephen Stewart, Kariyarra Aboriginal Corporation CEO, says caring for the environment is important to all Traditional Custodians
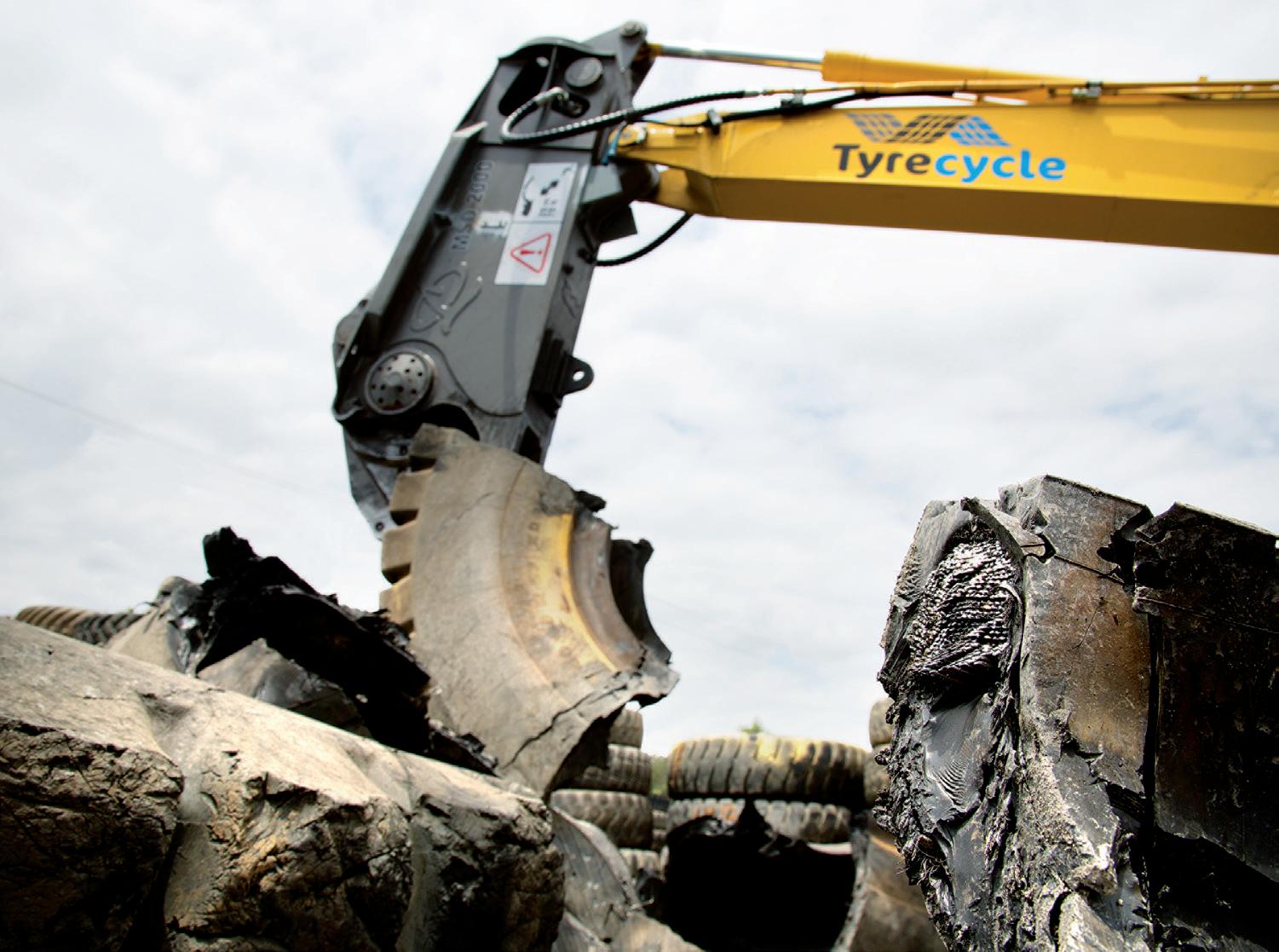
Almost 100 per cent of the Kariyarra-Tyrecycle workforce will be comprised of people from the Kariyarra community. in the Pilbara region.
“The responsible reclamation and processing of waste that would otherwise be disposed on country will help care for the land in a way that preserves it for future generations,” he says.
According to Jim Fairweather, Tyrecycle CEO, the venture provides a strong economic development opportunity for the region and the Kariyarra People.
“It’s a commercial operation, so it will be providing new opportunities for revenue and employment, while also tackling an important environmental issue,” he says.
“The project will not only prevent land from being destroyed, but will also repurpose all material for use across a range of end-markets.
“The recent developments in the expansion of local Pilbara-based ports, along with new opportunities to ship non-bulk commodities into and out of Port Hedland, have made this partnership possible.”
Fairweather says the Kariyarra People have well established relationships with the ports, which has advanced arrangements to ship processed waste rubber directly out of the region.
“It’s a local solution towards recycling EOL OTR tyres, which is now economically viable,” he explains.
“It avoids the cost-prohibitive
alternative to transporting the processed material over long distances to Fremantle Harbour for export, which simply isn’t a feasible option.”
The EOL OTR tyres will be transported to Kariyarra-Tyrecycle’s soon to be constructed secure processing facility in Port Hedland.
The tyres will then undergo primary processing and be containerised for direct export from the region.
With strict documentation and process controls to ensure full chain of custody requirements, the size reduced material will be supplied into Tyrecycle’s overseas processing facility.
From there, the material will be converted into rubber crumb for repatriation back into Australia for domestic consumption, or sold into other markets.
“What this delivers is a local Pilbara-based approach towards the environmentally and socially conscious management of OTR waste,” Fairweather says.
In Australia each year, OTR tyres from mining represent one third of EOL OTR tyres, amounting to well over 100,000 tonnes of waste rubber. Currently, only four per cent of these tyres are recovered for recycling, due to a lack of viable recycling options available to mining companies.
“One of the most commonly adopted practices is to manage the waste ‘in-pit’, essentially referring to burial of the waste rubber,” Fairweather says.
“Recent political, commercial and environmental developments have shown that maintaining the status-quo concerning the low-rates of recovery for heavy duty waste rubber is simply unsustainable.”
Fairweather adds that both state and
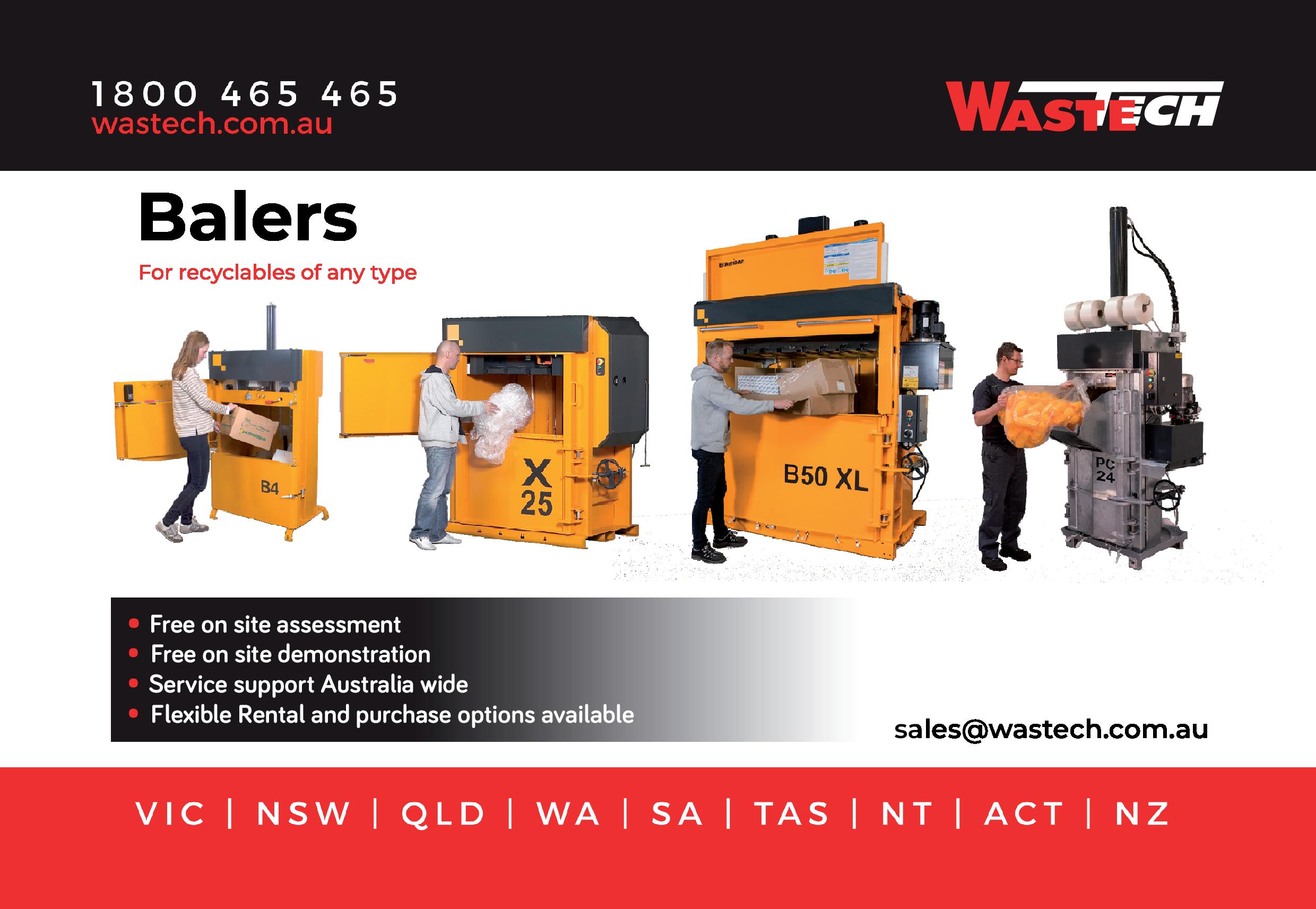
Federal Governments have expressed their aspirations for a sustainable, lowwaste, circular economy.
Almost 100 per cent of the Kariyarra-Tyrecycle workforce will be comprised of people from the Kariyarra community, with Kariyarra Contracting providing a key point of access to the local labour market.
Brenda Alec, Kariyarra Aboriginal Corporation Chair, says the project will provide stable, high-quality employment opportunities.
She adds that the project will also provide the community with an ongoing revenue stream to help support the long-term sustainability of the Kariyarra Aboriginal Corporation.
“It will enable us to reinvest in other activities, as well as support the philanthropic programs that directly support the Kariyarra People,” she says.
A rubberised archetype
WASTE MANAGEMENT REVIEW SPEAKS WITH MOLECTRA TECHNOLOGIES’ JOHN DOBOZY ABOUT HIS UNIQUE APPROACH TO TYRE RECYCLING AND NICHE PRODUCT MARKET DEVELOPMENT.
While innovation and new technologies are abound in the waste and resource recovery sector, in the age of regulation, trials and collaborative research, the Jungian artist-scientist archetype is rarely discussed.
Distracted by thought, impulsive yet cautious, the artist-scientist functions as a source of change.
While like all archetypes, the artistscientist is an abstraction of real life, John Dobozy, innovation architect and founder of Molectra Technologies, comes close.
Established as a private company in Queensland in 2000, Molectra’s unique processing technology transforms discarded tyres into their component parts.
Molectra’s technology extracts high quality resources from tyres to produce fuel, carbon for diamonds and other commodities including over 50 value-added products.
These include, Dobozy says, uncontaminated rubber, high tensile wires and useful fibres “stronger than steel.”
“We also use a unique microwave processor to distil jet fuel, diesel and lubeoil from decontaminated ground rubber, which powers the recycling and manufacturing process of Molectra.
“The residual carbon is 97.4 per cent pure and can be crushed to form carbon black, which is used to manufacture new tyres, plastics, paints, inks and batteries,” Dobozy says.
Alternatively, he adds that the carbon can be converted into activated carbon for water purification, gold extraction and air filtration.
“Another clever development is to fuse fertilizers and soil microbes into biochar,” Dobozy says.
This process activates inert char and turns it into biochar, or what Dobozy calls, CarbonEater Fertiliser.
“This product locks up fertilisers
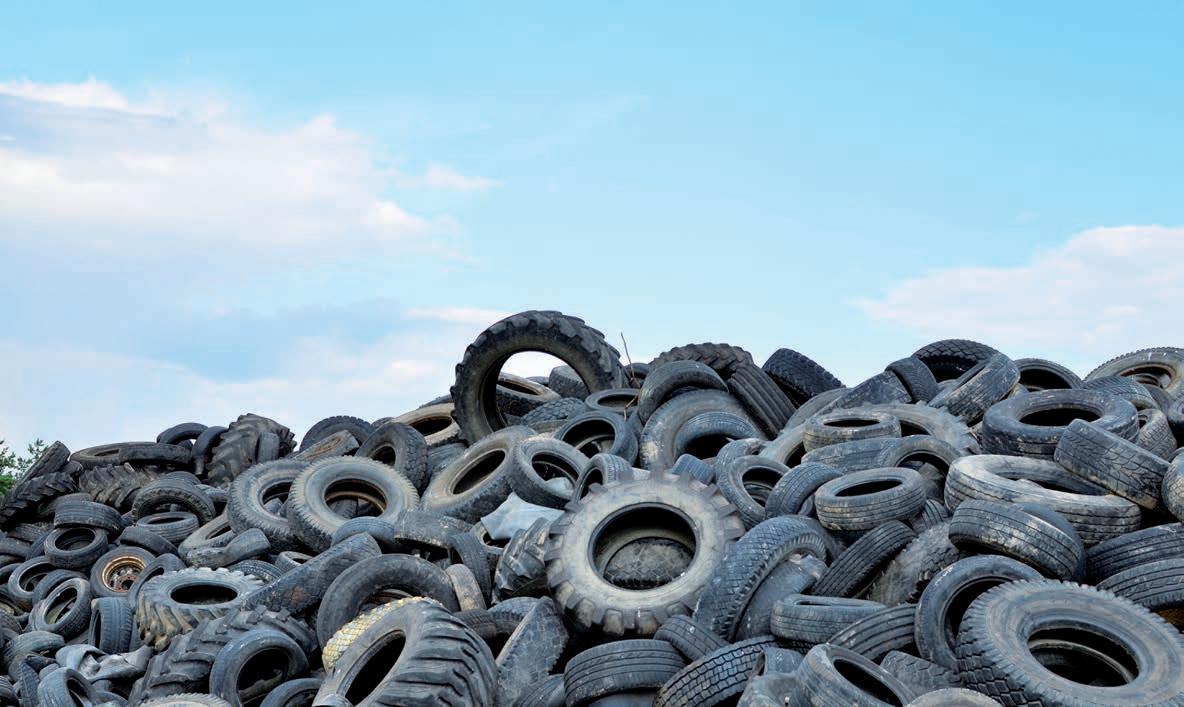
within the soil, preventing washout into waterways,” he says. “The greatest ecological and social benefit is replenishment of carbon poor soils and increased food production capacities.”
The technology’s origins date back to the late 1970s, when Dobozy first discussed the problem of discarded tyres with tyre companies and suggested a recycling solution.
After early rejections, Dobozy says he became impassioned, developing novel machines and clean rubber product powders.
“Despite these early achievements, recycling was shunned by industry and the population in general. The watershed realisation came when quality rubber was rejected by tyre companies world over,” he explains.
“What needed to be done was not just developing an integrated recycling system, but innovating processes
Molectra’s technology origins date back to the late 1970s.
to manufacture other rubber-based products besides tyres.”
From there, Molectra developed a series of machines and a unique processing technique that extracts rubber in a fine powder format.
“After examining the rubber at a molecular level, I noticed that the molecular structure of the rubber was not damaged during Molectra designed recycling processes,” Dobozy says.
“Typically, granulated rubber was mixed with adhesives to form it into a useful product. That is too expensive for fine powders, as the uptake of adhesive is excessive and subsequently cost more.”
As a result, Dobozy says other methods had to be trialled to produce products from powdered rubber.
“Molectra has perfected a bonding mechanism at a molecular level, with no glue required,” he explains.
Molectra Technologies has since developed a three-part process to extract up to 13 base commodities from each tyre, he says. Dobozy adds that the process comprises mechanical, chemical and microwave treatments.
“As all the base products are uncontaminated, they are suitable to replace virgin raw materials at a fraction of the cost when using them to produce new products,” he says.
“The most important thing in recycling is to produce high quality marketable products with competitive pricing.”
According to Dobozy, independent testing has been conducted by universities, rubber, carbon and oil laboratories, Bridgestone Rubber, Allied Rubber and others.
He adds that the cost and environmental efficiency of Molectra’s technology is key, with its processes designed to lower the cost of tyre processing and value-addedproduct manufacturing.
John Dobozy says Molectra Technologies’ CarbonEater Fertiliser can prevent washout into waterways.

“Molectra is marketing integrated tyre recycling and value-addedproduct manufacturing plants, with the capacity to process two to 10 tonnes of processed tyres per hour,” Dobozy says.
“These plants incorporate mechanical and microwave processing equipment with production machines for in-house manufacturing of selected value-added-products.”
Due to the flexibility of Molectra’s technology, Dobozy explains that commodities can be produced in various ratios according to the market demand for each.
Of his 50 products, Dobozy highlights Molectra’s capability to mass produce fine rubber powders.
He adds Molectra’s technology can produce rubber sized from five to 140 mesh, the equivalent of 4000 to 100 microns. Additional recycled products include puncture proof CaviTyre’s, irrigation and agricultural pipes, construction blocks for equestrian stable and playgrounds and printed floor tiles and pavers.
John demonstrates that the replacement of virgin rubber with Molectra rubber can be used to manufacture new rubber products for niche markets.
Molectra’s turn-key-plants are tailored to meet the requirements of their clients under a licence/royalty agreement. Molectra will design, supply and commission each plant, providing training, technical support and long-term maintenance and spare parts service.
“In several geographical areas of Australia, the plants will be supported by already operating distribution agencies, currently serviced by our small capacity plant in Queensland,” Dobozy says.
Regulatory support and change paves the way for a viable future for the recycling industry, Dobozy adds.
“Molectra’s niche ability to be flexible allows us to work with industry designers and developers to design and produce purpose-built products as an environmental solution for rubber, fuel and carbon alternatives for applications normally produced from other virgin materials,” he says.
“The art of recycling is to emulate nature’s process of recreating useful compounds from the resources of planet earth.”