
26 minute read
POWERING ANROCHTE BIOGAS
HZI’s Kompogas technology converts organic waste into electricity and heat or biomethane.
Powering Anröchte with biogas
A NEW KOMPOGAS PLANT IN ANRÖCHTE, GERMANY IS GENERATING CARBON-NEUTRAL BIOGAS TO INJECT ELECTRICITY INTO THE GRID. HITACHI ZOSEN INOVA’S RAIKO KOLAR EXPLAINS.
On the site of an old quarry in Anröchte, Germany, a state-ofthe-art composting facility and Kompogas biodigester plant now sits.
In February this year, electricity from the plant started being fed into the grid, marking an important milestone for green energy transition in the North Rhine-Westphalia municipality.
In 2018, facility operators ESG Soest awarded the tender to construct a plugflow digester with gas conditioning at its composting facility to international dry anaerobic digestion pioneers Hitachi Zosen Inova (HZI).
HZI’s Kompogas technology converts organic waste from municipal, commercial and industrial sources into electricity and heat or biomethane. Synonymous with continuous dry anaerobic digestion technology, the Anröchte facility is the 25th Kompogas plant delivered by HZI in Germany.
According to Raiko Kolar, HZI Sales Manager, before developing the facility, ESG evaluated all types of technology on the market, including batch technology. He explains that after extensive investigations, ESG recognised plug-flow technology presented the best business case.
“The tender evaluation was based on capital investment, and HZI had the best price performance ratio, as well as being able to meet all the regulations, guarantees and requirements set in the tender documents,” Kolar says.
Prior to the construction of HZI’s Kompogas plant, ESG operated two small composting facilities at the site.
“They wanted to develop a new modern plant in line with emissions standards and regulations, as the composting plants were 15-20 years old and not in line with current regulations,” Kolar says.
He explains that minimal losses of biogas, a greenhouse gas if released into the atmosphere, are integral to current regulations and can only be met by continuous technologies.
“The district also has a plan in place to contribute to the Regional Climate Protection Plan, so it was important for them to begin producing renewable energy.”
Furthermore, Kolar explains that ESG wanted to be prepared for future challenges, such as changing waste volumes and quality. The project has a range of specificities, he adds, with plants of this kind typically producing compost and liquid digestate for
application on agricultural fields.
“In this region, however, the agricultural fields left to spread the liquid is limited, so HZI developed a plant that would produce no liquid digestate, which is an important speciality of the project,” Kolar says.
The plug-flow digester has a capacity of 15,000 tonnes per annum, which will produce 1.5 million kilowatt-hours of energy from digested-source-segregated organic waste. HZI has been working on the project for seven years, from first contact with ESG to the plant’s 2020 commissioning.
Incoming waste at the facility is shredded and screened, with the smaller post-screening fraction possessing the highest biogas potential. The smaller faction is then feed to the digester in small portions 24 hours a day, at 30-minute intervals.
“By feeding a small amount of organic waste into the digester at regular intervals, you ensure a stable biological process. And because the bacteria are being feed continuously, the digester creates an uninterrupted biogas flow rate and quality,” Kolar says.
The digester features an internal agitator, which turns at a rate of one round per minute.
“The agitator turns very slowly, which helps the gas to be released from the porridge-like material and avoids sedimentation inside the digester,” Kolar says.
After drying and desulphurisation, the raw biogas from the Kompogas digester is either upgraded to up to 99.9 per cent methane content and fed into the gas grid, or in the case of the Anröchte facility, used directly to generate electricity.
The Kompogas plant was finished on time, Kolar says, with HZI now beyond the halfway mark of its 20-week facility trail-run. Within the 20-week trial, HZI were required to show a three-week performance test, which Kolar says produced positive results.
“Within the test we demonstrated the efficiency, availability, throughput capacity and compliance with emissions standards required. More importantly, the customer is very satisfied with the plant,” he says.
Kompogas plants are extremely reliable, Kolar explains, with the robust design ensuring they continue to work at their original rate throughout the plant’s lifecycle.
“Kompogas has been on the market for 25 years, and we have built more than 100 plants. In total, there are 200 digesters modules currently installed, and all of them are performing and running well,” he says.
“The reliability also applies to the biological stability of the plant. With this technology, operators can be flexible when it comes to changing waste material volumes and quality, which will shift throughout the life of the plant.”
Additionally, Kolar highlights that organic input material often changes, meaning the flexibility offered by the Kompogas system is crucial.
“Plus, all of the investigations from universities in Europe show plug-flow technology has the best carbon footprint compared to other technologies,” he says.
With Australia’s waste-to-biogas market still somewhat in its infancy, Kolar stresses that operators should learn from Europe’s mistakes.
He explains that when the market was first developing in Europe 25 years ago, many operators looked towards cheaper technologies.
“These plants were not able to cope with the wood, stones and glass that comes in with the food and green waste and therefore failed to achieve throughput capacity and were shut down in 5-8 years,” Kolar says.
“It’s also important not to go with technologies that have a low biogas production efficiency. To facilitate purchasing of the produced energy, it is critical to have high biogas yields, and anaerobic-dry-continuous-plug-flow technology provides the highest biogas yields on the market.”
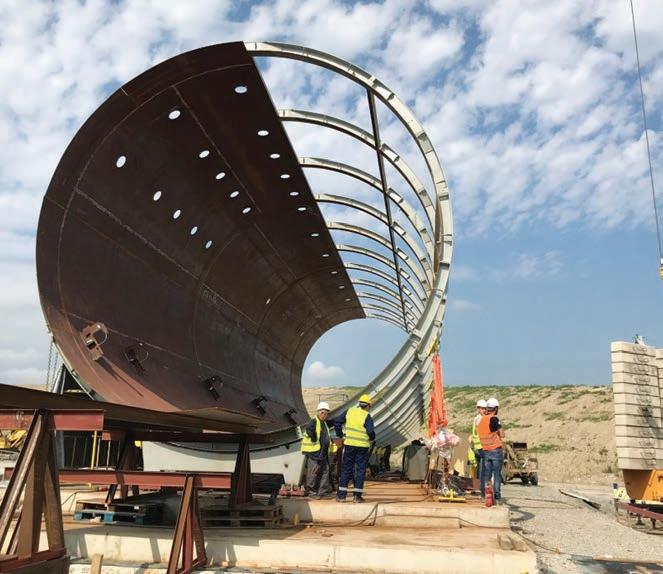
HZI’s plug-flow digester will produce 1.5 million kilowatt-hours of energy from fermented biogas.
A clearer vision on waste trucks
IFM’S COLLISION WARNING SYSTEM FOR MOBILE MACHINES IS PROVIDING PIECE OF MIND TO WASTE OPERATORS THROUGH AUTOMATED COLLISION AVOIDANCE.
The waste industry is increasingly looking towards technology to improve safety and drive operational efficiency. With this in mind, ifm has developed a next generation 3D collision warning system to increase the automation level of mobile machines.
Designed to improve the safety of roads, ifm’s collision warning system is based on ifm’s established 3 dimensional sensing technology. The system precisely detects obstacles and visualises them in a 2D image on a monitor. This keeps drivers informed about the trigger of the alarm and the area to be monitored at all times.
According to an ifm spokesperson, drivers of heavy municipal waste vehicles can feel more at ease when operating their trucks, knowing that ifm’s 3D collision avoidance system is at work.
“Haul trucks, refuse trucks, baggage loaders and road building machines are also using this technology for obstacle detection,” the spokesperson says.
“ifm offers an assistant with the O3M sensor, which works as an extra set of eyes to assist the machine operator. It can see blind spots, even if the operator has not seen an object or person in the mirrors and video display, ifm’s sensors can react to those objects and people.”
The active obstacle detection monitors danger zones around the vehicle and warns the driver of imminent collisions in good time. For this purpose, a tried-and-tested 3D optical time-of-flight system from ifm is used, which reduces false alarms to a minimum thanks to a sophisticated algorithm. Warnings are provided visually, acoustically and in the form of icons via the supplied 7-inch monitor.
The collision system is used in waste disposal vehicles for automatic recognition of dangerous situations.
Waste trucks can be fitted with ifm’s 3D sensor with video overlay, which displays an image of the vehicle’s surroundings on a hi-res screen to the operator. This gives warning to the driver if an object comes within a set parameter of the vehicle.
“The machine can also be configured to automatically apply the braking system if the driver fails to react in time,” the spokesperson says.
“Improving driver and human safety can also reduce expenditure on legal and insurance costs. The aim is reducing risk to people and property, but there is also damage to brand and reputation if an accident occurs.”
The 3D sensors are suitable for robust applications in indoor and outdoor areas. The O3M has a high protection rating against water and dust ingress and a wide temperature range of -40°c to 85°c. It is also able to handle shock and vibration, which is well suited to the high demands of the Australian environment, meeting all requirements for use on mobile machines.
The collision warning system package includes all the components to set up a fully functioning collision warning system on a mobile machine. ifm’s collision avoidance package helps not only pedestrians, but also the drivers and crew who frequently moving about the vehicle.
“ifm is leading the market for Anti Collision Systems on waste trucks in Germany, with approximately 60 systems on order each month to retrofit garbage trucks,” ifm says.
“The new normal will be to see these systems as a standard option in production on all waste trucks going forward in Germany, Australia and world over.”
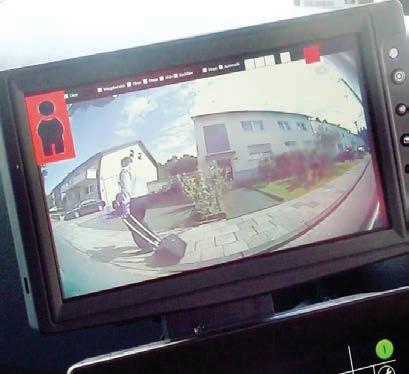
The package includes all the components to set up a fully functioning collision warning system.
Packaging the new normal
WITH MUCH DEBATE SURROUNDING HOW COVID-19 WILL SHAPE AUSTRALIA IN THE LONG-TERM, APCO IS EXPLORING OPPORTUNITIES TO ACCELERATE SUSTAINABLE PACKAGING, WRITES CEO BROOKE DONNELLY.
As businesses look to rebuild, Brooke Donnelly says there are powerful insights to be taken from COVID-19.
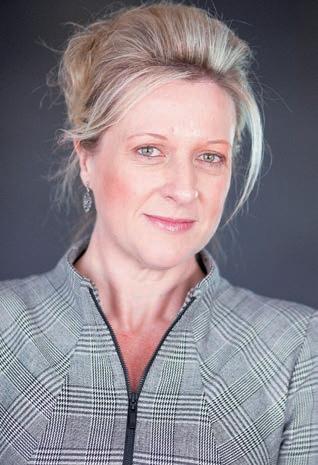
At the time of writing this article, lockdown restrictions are starting to ease, and Australia is looking forward with a cautious sense of optimism to rebuilding in a postCOVID landscape. There has been much debate about how this time will shape our country in the long term. For professionals in the packaging and resource recovery industries – one of the most persistent questions has been whether COVID-19 will accelerate or hinder efforts for packaging sustainability in Australia?
It’s a challenging question to unpack. We are after all in largely uncharted territory. In the short term there has certainly been consequences. Under lockdown many consumers faced a greater reliance on single use products, while greater restrictions emerged around reusable packaging formats, most notably coffee cups.
Once the immediate risks are gone, it will be imperative that industry provides a united voice to discourage these from becoming long-term behavioural patterns. For the recycling industry, lockdown conditions have also meant added stress to the kerbside system. In May, ACOR reported a 10 per cent growth in household kerbside recycling, as well as unprecedented levels of contamination in some locations, especially from soft plastics. Meanwhile for the food industry, many businesses have been required to navigate takeaway packaging for the first time. With many industries across Australia adversely affected, or even shut down due to COVID-19, it has been a timely reminder of the essential role packaging plays in the Australian economy.
Despite these challenges, progress is continuing at a remarkable rate. At APCO we launched Our Packaging Future , the strategic roadmap for delivering the 2025 Targets, and Considerations for Compostable Plastic Packaging , a new report developed in partnership with ABA and AORA.
Our events program is one of APCO’s most important industry engagement tools, so we were particularly proud of the decision to move these events to a weekly webinar format. These sessions cover all things sustainability and give our community a regular opportunity to stay in touch and keep collaborating.
It has also been inspiring to see some members rise to the challenge of COVID in creative and inspiring ways. As we all prepare to re-enter the new ‘normal’ world of work, it has been inspiring to see people ask, how can this challenge be embraced as an opportunity?
Looking ahead, many businesses facing financial strain will need to find operational efficiencies. By changing our mindset to view waste as a strategic and operational flaw, circular design could provide a powerful opportunity for businesses to financially navigate this challenging time.
As governments and businesses look to rebuild, there are powerful insights to be taken about how deeply connected and systemic our solution to Australia’s waste and recovery challenges needs to be.
While it’s a devastating example, the pandemic has illustrated the potential of collective action. So let’s harness that approach for building a sustainable future for Australia.
Expanding the baler market
AS THE EXCLUSIVE AGENT FOR GODSWILL BALERS IN AUSTRALIA AND NEW ZEALAND, MARCUS CORRIGAN OF MATERIAL RECOVERY SOLUTIONS DETAILS THE COMPANY’S APPROACH TO ROBUST AND HIGH-THROUGHPUT BAILING.
With the Council of Australian Government’s export ban on paper and cardboard set to take effect in 2024, a raft of opportunity is opening up to develop Australia’s domestic processing capacity.
This is highlighted in the NSW Government’s recent call for an industry partner to co-develop a funding proposal for new paper and cardboard processing capacity, with similar calls expected in other states and territories.
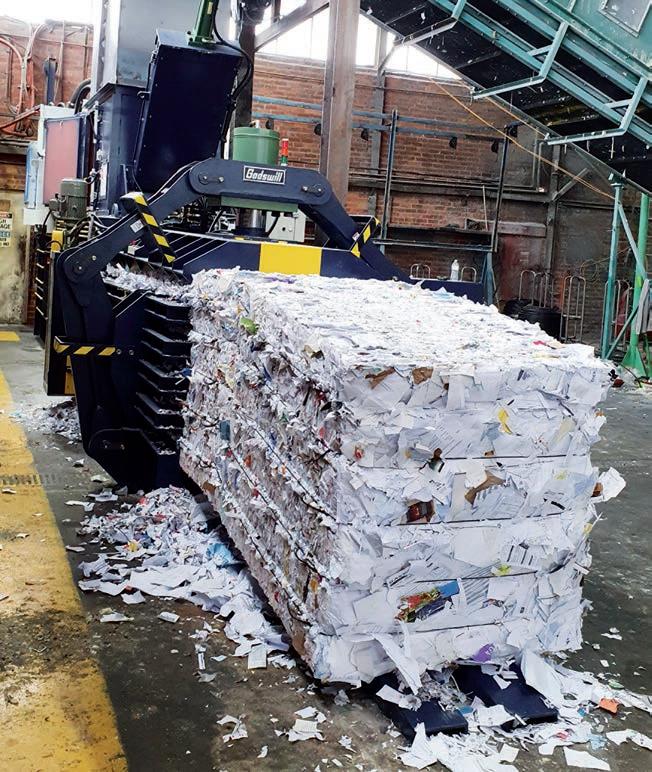
All of Material Recovery Solutions’ Godswill Balers feature modular hydraulic systems.
According to Marcus Corrigan, Material Recovery Solutions (MRS) Managing Director, current waste sector developments present an opportunity to expand market scope for the Queensland-based company.
With the ability to bale material efficiently and at maximum capacity a priority for facilities dealing with large volumes of recyclable material, Corrigan highlights MRS’ role as the exclusive agent for Goodwill balers in Australian and New Zealand.
“We at MRS have built a strong professional relationship with Godswill and work closely with them to ensure all Godswill Baler products are specifically tailored to meet the needs of the Australian and New Zealand Markets,” he says.
MRS offer an impressive range of Godswill balers, including but not limited to, auto channel balers, semi closed length balers and auto two ram balers. Corrigan adds that MRS can custom design balers to meet specific customer needs.
“It is imperative that all our products are robust in design, built for longevity, offer export level bale weights and confirm to the relevant Australian and New Zealand Acts and standards,” he says. “With over 200 balers in operation since 2004 in Australia and New Zealand, we have built a strong customer base where reliability and
extensive after sales are the corner stone of our business model.”
Corrigan says that 90 per cent of MRS’ new sales come from existing customers, highlighting the quality of the Godswill product and MRS’ customer centric approach.
“We deem Godswill to be the standard in Australia for medium to high throughput applications were reliability and longevity is paramount,” he explains.
Corrigan emphasises the GB1111F baler as a particular standout of the MRS Godswill range. The auto channel baler – 1.1 metres squared by 1.8 metre bale size – runs on a 135-kilowatt hydraulic system, with real world throughput when complemented with a suitable feed conveyor.
The machine configuration can bale cardboard and paper at a rate of 18 and 22 tonnes per hour respectively.
All Godswill Balers have a Human Machine Interface that allows operators to monitor or adjust the machine parameters for different materials, as well as troubleshoot problems.
Corrigan adds that MRS’ range of Godswill balers feature modular hydraulic systems, which allow MRS
Marcus Corrigan says current waste sector developments present an opportunity to expand market scope for the company.
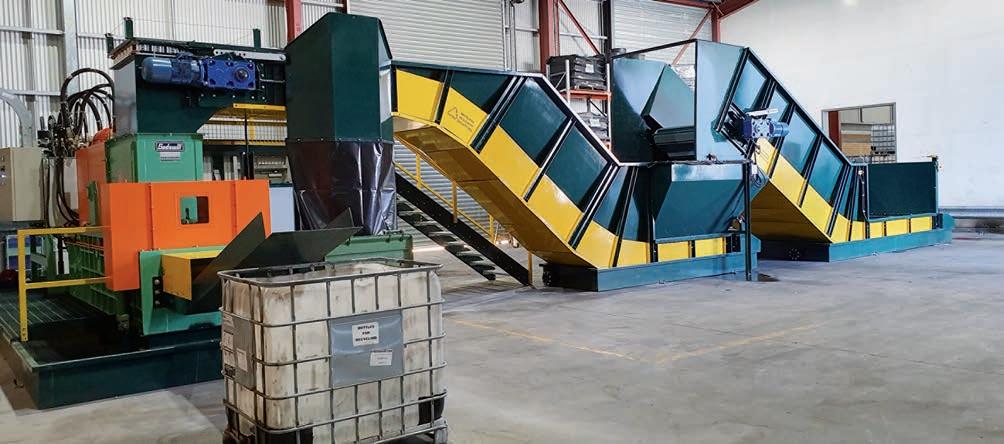
to increase kilowatt packages to tailer the baler’s configuration to suit customer requirements.
“Hydraulic systems are designed to be highly efficient, offering regenerative oil management, energy efficient components and variable frequency drives, with variable speed controllers to optimise low-load stages of the baling cycle,” he says.
“Additionally, our baler platen (pushing trolleys) are mounted on heavy duty rollers to minimise frictions and boost efficiency.” As an added value proposition in light of current supply chain disruptions, Corrigan notes that MRS manufacture a suite of equipment inhouse to complement its Godswill baler range.
Australian-made MRS equipment includes feed conveyors, access and structural devices, screeners, separators and automated collection truck bodies. MRS also provide a range of turnkey solutions, including but not limited to, material recovery facilities and document destruction.
“We have invested over $400,000 in the past 12 months on machinery to bring as much of the manufacturing process inhouse as possible,” he says.
“With the correct machinery, developed work force and efficient design choices we are proving, MRS is committed to growing onshore manufacturing and local employment.”
With a dedicated team of 10 experienced engineers, technicians and fabricators based in SouthEast Queensland, and experienced contractors in most metro areas nationally, MRS are able to support their customers with fast turnaround times.
“To enable our aftersales, we stock $500,000 worth of spare parts for Godswill Balers and Accent Wire Tie, with a fully fitted machine shop to manufacture any additional parts including custom items when needed,” Corrigan says.
Furthermore, MRS provide regular service and maintenance, in addition to supplying competitively priced consumable item such as baling wire.
“MRS is fully committed to maintaining close relationships with our customers from the point of install, throughout the equipment operational life,” Corrigan says.
Contact - Material Recovery Solutions
P 07 562 900 92 E sales@MaterialRecoverySolutions.com.au W www.materialrecoverysolutions.com.au/
WASTECH ENGINEERING’S BRAMIDAN BALERS
Manufactured in Denmark and highly regarded for their design and quality, Bramidan Balers are globally recognised for delivering efficient waste management solutions.
Available in Australia exclusively through Wastech Engineering, Bramidan Balers are capable of compacting a wide range of materials including cardboard, plastic, e-waste and metals.
With a broad choice of Bramidan Baler models available, the crushers are ideal for businesses with a wide range of waste volumes, from small retail outlets to high capacity waste transfer stations.
For larger demands, Wastech offer the X25, which is equipped with cross cylinders to give operators stable compression and superior press force. Combined with a long stroke, a high bale weight can be achieved.
The cardboard and plastic baler is designed with easy servicing in mind, with the hydraulic unit mounted below the control panel on the side of the machine.
For service users with smaller amounts of waste, but who still need a machine to handle bulky materials, Wastech suggests the B5 W baler.
The machine is characterised by a wide filling opening of one metre, which is an advantage when handling larger
Bramidan Balers are available in Australia exclusively through Wastech.
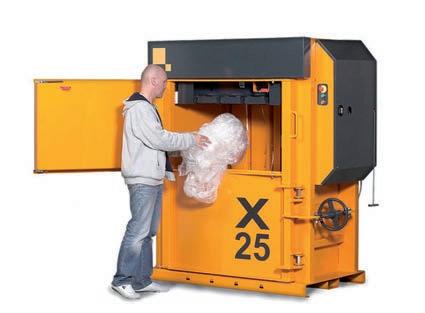
cardboard boxes. The chamber is equipped with rows of efficient barbs, which keep the material back and ensure optimum filling.
An efficient and silent ejecting system ensures easy handling of the compressed bale, while the strap rolls are simple to replace in front of the machine.
Free on-site trials and flexible rental options are available.
Contact - Wastech Engineering
P 1800 465 465 E info@wastech.com.au W https://wastech.com.au/
GREENLINE ENGINEERED RECYCLING SOLUTIONS
Terex Washing Systems’ (TWS) GreenLine solutions are a packaged suite of end-to-end washing equipment offerings targeted at the recycling market.
Comprising standard equipment along with specialised recycling tailored products, they are packaged together in a pre-determined and balanced system based on TWS’ long running applications experience.
GreenLine solutions are designed to provide an easy entry to wash recycling processing for new entrants looking to develop a footprint in the expanding sector, as well as established customers in a replacement/expansion phase who require proven rugged out-of-the-box solutions.
For well in excess of a decade, TWS has provided specialist tailored equipment to customers recovering usable, sellable sands and aggregates from recycled or muck-away material that otherwise would have been destined for landfill.
While these ventures were somewhat pioneering, this segment of the industry, and its equipment scope and ability, have grown significantly over time; alongside the breadth of contaminants and composition of feed material.
TWS products packaged with AquaClear, Water Management Solutions and patented specialist units, launching in the coming months, allow TWS to simplify the
TWS’ GreenLine solutions are designed to provide an easy entry to wash recycling.
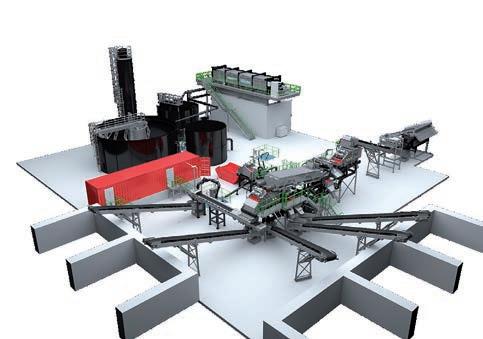
waste recycling market.
The system couples TWS equipment with their expertise into fixed solutions for various materials from 60tph through to 300tph, while maintaining the ability to easily tailor for particularly specialist applications, demystifying the seemingly complex world of wash recycling.
Contact – Terex Washing Systems
E TWS.Sales@terex.com W www.terex.com/washing
HYVA’s RCM range is fitted with widecomb bin lifters to enable spill free loading.
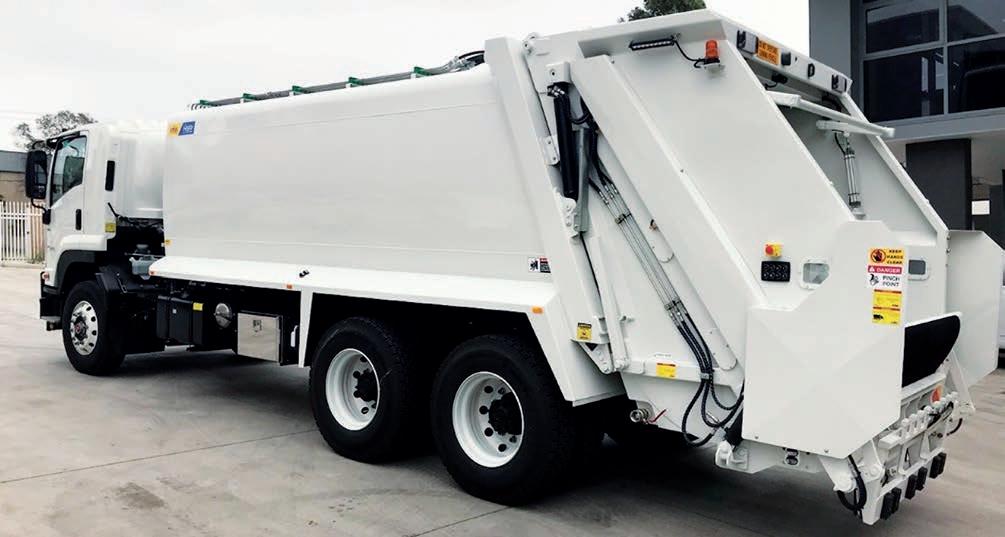
Global waste sector assistance
A PARTNERSHIP BETWEEN HYVA EQUIPMENT AND HSR SOUTHERN CROSS IS REALISING SECTOR-WIDE BENEFITS FOR WASTE HANDLING AND COMPACTION.
Established in the Netherlands in 1979, HYVA Equipment installs in excess of 300,000 telescopic and double acting cylinder kits worldwide each year. The company currently operates in more than 130 countries, with its waste products distributed in Australia by HSR Southern Cross.
“In 2015, we had the opportunity to meet with Andre Bremmer, Managing Director at HYVA Pacific, to discuss the distribution of their waste equipment in Australia,” says Martyn Cross, HSR Managing Director.
“It was immediately evident that HYVA shared HSR’s core value of providing exceptional customer experiences. A synergy was born.”
In 2017, HYVA Pacific and HSR representatives travelled to Europe to inspect HYVA’s Waste Equipment range, Cross says.
He adds that first impressions were extremely promising.
Following the successful European trip, HSR and HYVA partnered to release the HYVA Press range of waste equipment to the Australian market.
Providing compaction solutions for a range of multinational waste companies, HSR Southern Cross operates primarily as a fabrication and engineering company, with a specialisation in hydraulics and auto electrical.
“Before working with HYVA, we identified a gap in the Australian market, whereby operators wanted to look at other models, due to a level of dissatisfaction with readily available compaction technology,” Cross says.
Servicing Veolia, Remondis, SUEZ and JJ Richards, Cross says HSR’s relationship with HYVA allows them to provide products that facilitate higher payloads, longer lifespans and efficient and faster collections.
“HYVA continues to stand out as a world leader in container handling systems, with its range of hookloaders – the TITAN and Classic models – both ranging in capacity from 3.5 to 30 tonnes,” Cross says.
“HYVA hookloaders are industry standouts, with built-in tough reliability, performance and low whole of ownership costs.”
In addition to HYVA’s hookloaders, Cross highlights the company’s range of RCM satellite collection units. He explains that the units are an economical and efficient solution for narrow city streets and laneways.
“The HYVA RCM3, when fitted to a vehicle of 4.5t GVM or less, stands out as a solution to domestic missed services, providing exceptional fiscal and environmental savings when compared to the running costs of a full-sized waste collection vehicle,” Cross says.
Fitted with in-cab controls for safe discharge of refuge, the RCM range is designed to unload into multiple units including rear load, mobile and stationary compactors and transfer stations.
Cross explains that the RCM range is fitted with wide-comb bin lifters, allowing spill free loading for all mobile waste containers up to 1100 litres.
“The closed body eliminates leakage, making it perfect for high liquid content refuge including foods,” he says.
“Optional compactional panels are available for all units, facilitating increased payload and load security.”
HSR also distribute a range of HYVA Mobile Compactors, which Cross says are used in several industries including shopping centres, restaurants, manufacturers, hospitals and events.
Set to be released at the 2020 Coffs Waste Conference, and now scheduled for the 2021 event, Cross also notes the HYVA Solar Powered Mobile Compactor. He adds that the compactor is well suited to temporary installations requiring no fixed infrastructure.
HSR’s range of HYVA mobile and static compactors are designed to suit a wide range of applications and waste types.
“These compactors have high volumetric efficiency due to the cylindrical container shape and compaction ratio, rubber seals and power pack with frequency control design,” Cross says.
“These features deliver many benefits, including faster compaction, no leakage, better hygiene, higher
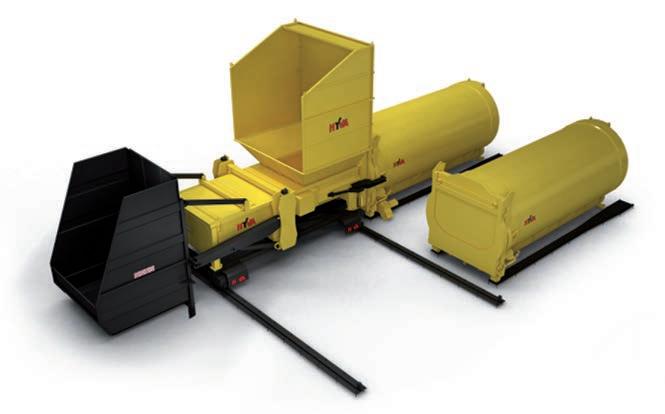
HYVA mobile and static compactors have high volumetric efficiency due to their cylindrical container shape and compaction ratio. payload, lower noise and energy consumption and easier maintenance.”
HYVA complement their equipment with Australian application engineers, ensuring truck and equipment combinations are analysed for stability, payload and Aust Design Rule compliance prior to fitting.
According to Cross, HSR does not build to order, but to stock, meaning they maintain a range of HYVA Compactors and parts that can be customised to suit individual customer needs.
“With that in mind, we cover the whole range of truck mounted wheel loaders and compactors from six cubic metres all the way up to 24,” he says.
Cross says all HYVA units are elaborately transformed by HSR in Australia, which is helping to ensure future generations of Australian manufacturers benefit from their investment in local highly skilled labour. To support its customers, ranging from sole trader operators, multinational waste companies, small and large regional and local government councils and utility companies, HSR’s service department operates 24 hours a day, seven days a week.
Additionally, HSR’s fleet of Service Vehicles work to ensure customers are supported locally, regionally, inter-state and internationally.
“HSR offer an unrivalled customer experience from concept, design, application and mechanical engineering, manufacture, and installation,” Cross says.
“This allows our customers the peace of mind that HSR intimately understand the product that they have purchased and will be supported long after the initial delivery.”
Contact - HYVA Equipment
P 02 4966 3777 E enquiries@hyva.com.au W www.hyva.com/en-au/
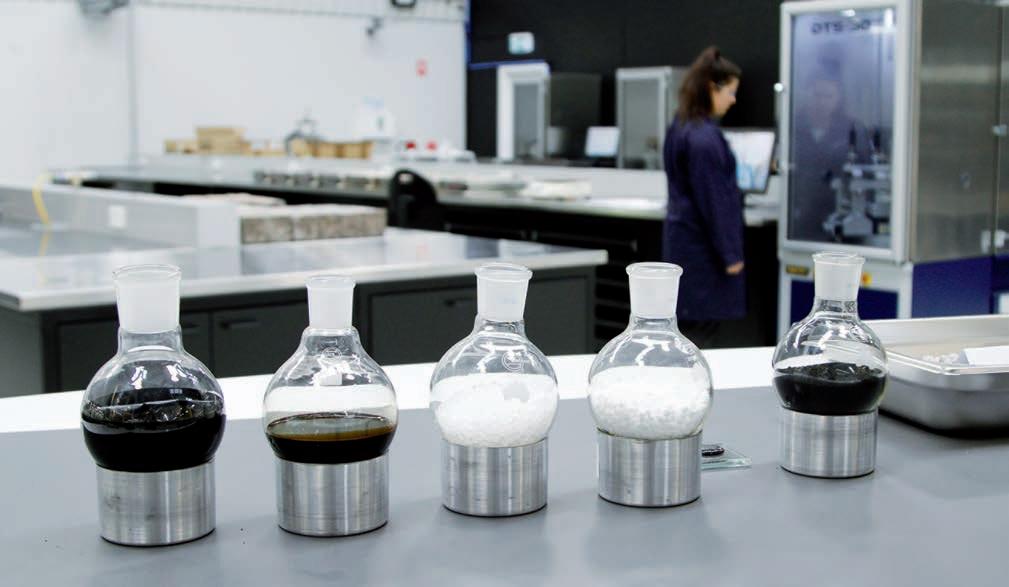
ARRB are undertaking trials and developing standards and guidelines to ensure the smart implementation of recycled materials.
PAVING OUR RECYCLED FUTURE
THE ROAD CONSTRUCTION INDUSTRY CAN CONTRIBUTE TO THE CIRCULAR ECONOMY BY CREATING SUSTAINABLE ROADS FOR A SUSTAINABLE SOCIETY, WRITES MELISSA LYONS, SENIOR PROFESSIONAL LEADER, THE AUSTRALIAN ROAD RESEARCH BOARD.
Sustainability, recycling, circular economy – these are the current buzz words in the road construction industry.
The road construction industry is under pressure to help solve Australia’s recycling crisis. The makeup of roads lends itself well to the incorporation of recycled materials. However, this is not as simple as replacing raw road construction materials with recycled materials such as glass, plastic or rubber. The right approach must be taken.
We need to think about how we can incorporate recycled materials into our roads in way that will make the road more sustainable in the long term, rather than a way to help solve the recycled material stockpile issues we have now. Without the right research, development and planning, we risk creating a new waste stream in years to come if we can’t reclaim the road.
Roads play an important role in our transport system. They keep our economy moving. We need to ensure we are not de-valuing or degrading them. Roads are not ‘just’ asphalt, they are valuable assets that need to meet certain requirements for our society to function.
The road construction industry should be designing and constructing our roads with the confidence that they will meet or exceed current standards. Society still expect our roads to perform well, if not better, especially as technology progresses. However, these roads also need to be sustainable in order to support a more sustainable society.
Standard asphalt is 100 per cent reusable as reclaimed asphalt pavement.
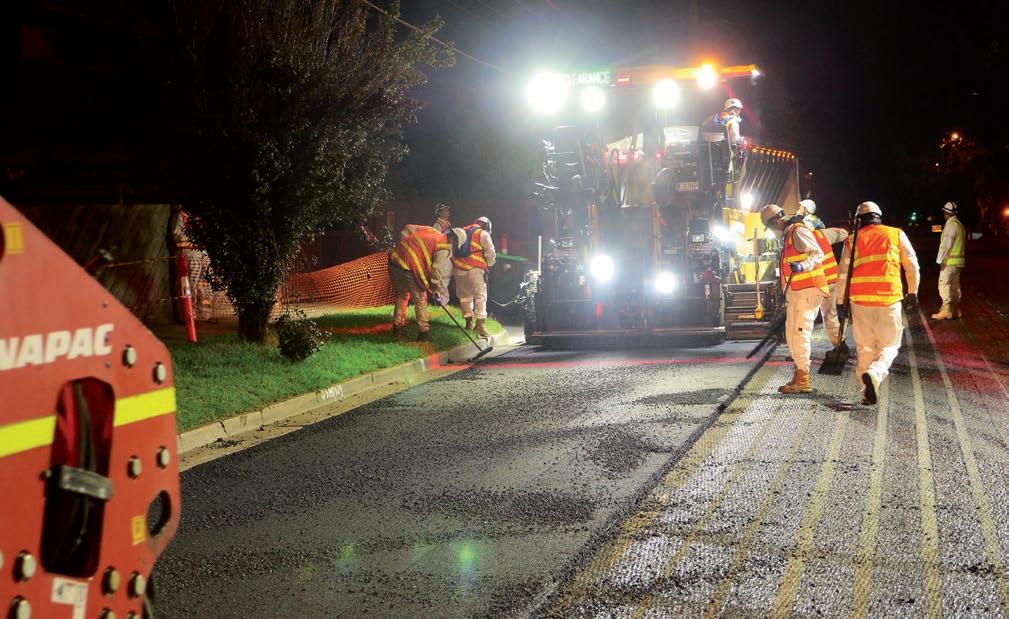
Society is heavily influenced by marketing and it is also influencing the way our industry is embracing sustainability. It is important that the road construction industry support the basic principles of the waste hierarchy – reduce, reuse, recycle. We need to be careful to not give society justification to keep generating recycled waste.
Standard asphalt is 100 per cent reusable as Reclaimed Asphalt Pavement (RAP). The use (and reuse) of RAP reduces the amount of virgin materials used in maintenance, rehabilitation or new construction of asphalt and pavements. This means valuable materials are used over and over again and do not end up in landfill, directly contributing to a circular economy.
There are many aspects to consider across the pavement lifecycle. There are many innovative products using recycled materials on the market and laboratory tests that show positive performance results. However, many of these products have not considered the full cradle-to-grave lifecycle of the recycled materials and the road. Recycled materials in some cases may increase the performance of the road, but it may also change how it is processed and manufactured and how we can reuse it. Therefore, we need to make sure we think about how our current processes and equipment will need to be updated to be compatible with the new products we are creating.
There may be trade-offs and risks with adding new recycled materials. There are costs and benefits of each material, use and design. For some recycled materials there may be more valuable and lower risk road infrastructure applications that can use more recycled materials e.g. bike paths or roadside furniture. Full life-cycle assessments of road technology options can assist in the best technology selection for the right situation.
For the road construction industry to contribute to a circular economy, we need to make a conscious effort to not just offer short term solutions to our recycling crisis. When we incorporate recycled materials into our roads and road infrastructure, a rigorous research and development process should be undertaken. Learnings from international uses, laboratory testing and local demonstration trials with performance monitoring are all part of this. ARRB are working with state road agencies, local government and bodies such as Sustainability Victoria and Tyre Stewardship Australia, undertaking trials and developing standards and guidelines to ensure the smart implementation of recycled materials.
Interested in finding out more about this work and its potential application, or customisation to your needs? Contact ARRB at sustainability@arrb.com.au
Next level facility software

Mandalay's Facility Product Suite - For Smarter Facilities
Up-to-date software
Mandalay offers a cloud-based software solution combined with the offline capabilities of deployed software. Data is secure and backed-up, software versions are deployed more often and with ease, and data is synchronised between remote facilities and central admin.
Regulatory compliance
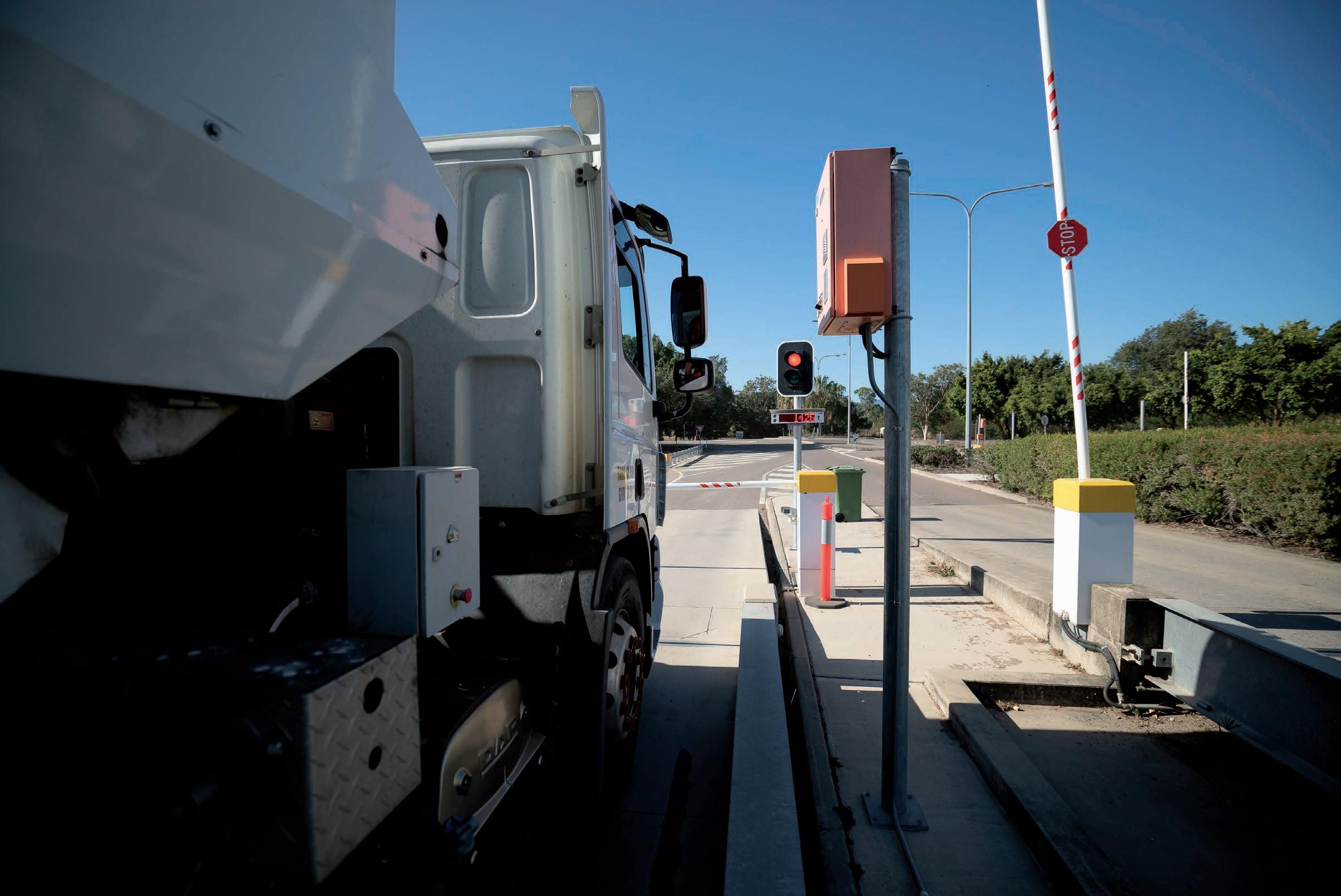
A system that complies with various EPA and regulatory requirements such as state-based regulatory reporting and HVNL. As requirements change, the system is updated to suit.
Accurate reporting
Providing admin and management teams with near real-time data that can be used to manage your business. Let us help you with data setup to ensure you get the most from the system.
Integration with finance systems Integration with finance systems will assist with payment processing and account management. Data can be exported in a format specific to your requirements.
Local support team Mandalay’s local and dedicated support team is available for assistance and troubleshooting. With significant industry experience, the Mandalay Consulting Team can provide guidance through more complex issues.
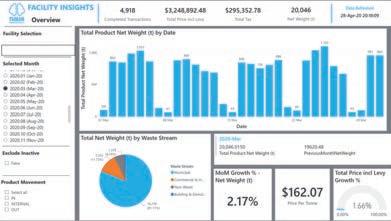