
23 minute read
FUTURE FACILITIES
Future-proofing your facility
WITH WASTE MANAGERS FACING INCREASINGLY COMPLEX OPERATING ENVIRONMENTS, MANDALAY TECHNOLOGIES’ ROSEMARY BLACK OUTLINES THE STREAMLINING CAPABILITIES OF CLOUD-BASED FACILITIES MANAGEMENT.
Regulatory environments are constantly changing and are variable state-to-state. As such, it can be challenging for waste managers and councils – often dealing with external pressures – to keep on top of changes and how they affect their day-to-day operations.
In June, for instance, the Queensland Government announced a six-month deferment to the waste levy increase, which was set to begin in July. The deferment falls in line with industry requests to temporarily halt regulatory changes in the wake of COVID-19. However, the 11th hour notification raised concerns, with industry given little time to adapt to pricing impacts.
“Reporting data to meet state and national regulatory requirements is complicated and involves a lot of manual work,” explains Rosemary Black, Head of Customer at Mandalay Technologies.
“Added to this is the often-rapid nature of change, as illustrated by the Queensland levy, which highlights the complex operating environment faced by waste managers and councils.”
To mitigate these challenges and ensure facility compliance, Mandalay has integrated levy and chain of responsibility reporting that matches legislation requirements into its Facility Product Suite.
“We believe in approaching facility
Rosemary Black says data is critical to the success of an organisation.
management from the front foot, providing practical solutions to take the pain away from clients,” Black says.
“Mandalay’s Facility Product Suite complies with various state and national regulatory bodies and regulatory requirements, and as requirements change, the system is updated to suit.”
In today’s digital economy, data functions much like oil in the 18th century – an immeasurably untapped valuable asset. In the waste sector, data extraction benefits extend beyond economics, with the role of big data increasingly understood within the context of positive environmental outcomes.
The NSW Government’s March 2020 Cleaning Up Our Act issues paper, for example, suggests significant opportunities exist for data and analytics to drive improvement in waste management efficiencies.
According to Black, the role of data towards a successful circular economy transition is well understood by Mandalay.
“Mandalay is committed to a world without waste – where materials generated by the community transition from a cost centre to a revenue generator,” she says.
“The right data is critical to the success of an organisation and so too are the processes that utilise and audit that data.”
An awareness of the latent value hidden in waste data was the central driver behind the development of Mandalay’s Facility Product Suite, Black explains.
“The system integrates a range of products for waste and facility applications to capture and process vehicle movements in and out of sites, delivering critical functions including hardware interfaces, transaction capture and point-of-sale payment processing,” she says.
Designed for landfills, transfer stations, resource recovery facilities, tip and buy back shops, recycling centres and material recovery facilities, the Facility Product Suite can be configured to suit all facility situations.
Black adds that software products can operate with or without a
Extracting the latent value hidden in data was the central driver behind the development of Mandalay’s Facility Product Suite.

weighbridge and be configured for automation at unmanned facilities.
“Facilities located in remote locations often require site access and transactions to be managed through automated systems,” she says.
“The Facility Product Suite enables automation by using various types of electronic IDs to identify preconfigured load attributes so only a ‘weight’ and ‘time’ requires capture once on site.”
By combining the functionality of a driver control station with Mandalay’s Facility Product Suite Extension Products, such as image capture and license plate recognition, Black explains that Mandalay can offer a fully automated experience.
“Including several extension products and services, the Facility Product Suite will not only drive efficient facilities, but offer detailed reporting, dashboarding and management capabilities,” she says.
Mandalay’s Facility Product Suite is more than simple weighbridge software, Black explains.
“It’s a cloud-based solution offering an interface to process transactions, capture data at manned and un-manned facilities and record data according to both state-based and national regulatory requirements,” she says.
“At the same time, the system provides admin and management teams with the ability to access and manage data across multiple facilities and locations.
“Working in conjunction with Mandalay’s range of extension products, waste data can be transformed into powerful information.”
With over 29 years’ experience as a sales professional, Black is well placed to understand the complex and localised needs of clients across the waste sector.
A key client pain point, she explains, is the issue of out of date software.
“Software deployed in places like a resource recovery centre or landfill can be 10 years old, and clearly, technology and software has advanced significantly since then,” she explains.
“With the Facility Product Suite’s cloud subscription, featuring deployment and release management tools, the latest developments, updates and new features are automatically added to users’ systems.”
An additional challenge for customers is a lack of trust in the data, and a subsequent unease about the accuracy of reported figures.
“Despite the idiom that data is more valuable than oil, many working outside the technology space are still unaware of how data functions – and are often dealing with data setup structures that lack an alignment to the needs of their organisation,” Black says.
“By utilising client feedback, Mandalay has designed reports and dashboards with data security and accuracy built into the core system.”
Furthermore, Black highlights poor and inadequate reporting. She adds that the multiple sources of data that make up the waste landscape are separate and need to be manually integrated.
“There is a pressing need for appropriate and accurate reporting to the council, without accurate data, planning for the future in facilities, contacts and needs is impossible,” she says.
“We launched our new data and analytics suite this year to address this, developed from customer feedback which meets their needs and also has in-built flexibility to customise specific requirements if necessary.”
The inability to integrate software to finance systems is another concern, Black says. As numbers come from multiple sources, manual compilation of data is required.
“Transferring data to a finance system means there are often discrepancies when changes are made in either system,” she says.
“Mandalay has integrated into or created a finance export for every finance system requested by our customers. Where each one has been uniquely defined to match customers’ finance implementation.
“We understand that each organisations need is slightly different, and our approach is to deliver the right solution for the organisation.” This article is the first in a three-part series exploring Mandalay’s Facility Product Suite. To find out more about how Mandalay can support your business, email: enquire@mandalaytech.com
A next generation solution
THE NEW 2020 AXTEC ONBOARD LOAD INDICATOR IS ENABLING WASTE TRUCK DRIVERS TO BE DIGITALLY SAVVY WITHOUT THE PUSH OF A BUTTON.
Optimal routing is essential to making point-to-point pickups eco-friendly and financially viable, which is why companies are investing in advanced systems and optimisation software.
However, technological advancements are only truly valued when safety is enhanced. This is especially important for waste management companies whose load and weight distribution are constantly changing. This can catch drivers out and leave them at risk of an axle overload.
Onboard Load Indicators provide critical data by displaying individual axle and gross vehicle loads and have been praised by operators as an essential tool.
According to Chris Coleman of Transport & Waste Solutions Australia (TWS), a simple installation can go a long way.
He says constantly displaying axle and gross weights enables drivers to distribute their loads safely and legally at all times.
Having formed a strategic partnership with TWS, Axtec products are currently helping several state utility companies meet their Chain of Responsibility obligations.
Axtec OnBoard provides drivers with real-time information on axle and gross vehicle loads via an intuitive traffic light configuration.
Visual and audible warnings can prompt the driver when overloads are present, while load data can be simultaneously written to the built-in logger and transmitted to a tracker system.
In February this year, Axtec, a privately owned and managed UKbased leader in axle weighing and load monitoring solutions, launched its latest Onboard Load Indicator.
Coleman says the 2000 model Onboard Load Indicator is Axtec’s most advanced, accurate and reliable load indicator yet, and is already utilised by some of Australia’s most well-known waste and transport operators.
“We think the new Axtec OnBoard model offers several key advantages over the previous model,” he says.
“Axtec Onboard powers up with the vehicle and requires no driver input, reducing the risk of tampering or accidental damage, and eliminating the need for additional driver training,” Coleman says.
He adds that clients have noticed reduced driver distraction and fatigue, as the display can automatically dim when safe to do so.
Axtec’s OnBoard Axle Load Indicator was first introduced in 2007 and Coleman says he is impressed with advancements since the first model.
“The 2000 model Axle Load Indicator increases security, reduces
OnBoard provides real time information on axle and gross vehicle loads.
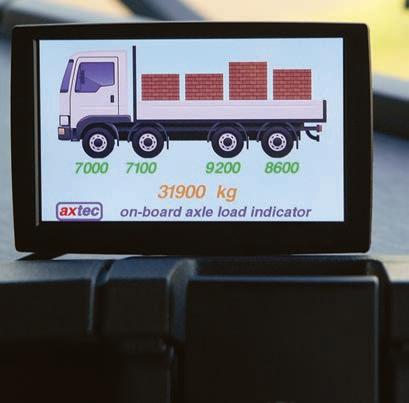
cab clutter, and with a clear 5 inch widescreen display, improves images from camera inputs and gives clearer information,” he says.
The widescreen display also boosts surveillance by accepting input from up to six vehicle mounted cameras.
“Not only can the display show the vehicle type, but the new touch cam facility also offers uninterrupted viewing of a priority camera,” he says.
Coleman credits the two-piece design with only a single cable input to the much sleeker drivers’ display.
“Automation is driven to guide driver precision. You don’t have to be tech savvy to benefit from all the features of this system, as you barely have to push a button, it is automatically user friendly.”
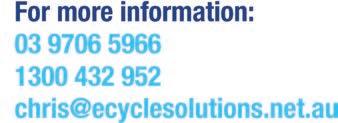

200 million bottles
A NEW GLASS ADDITIVE BIN AT ALEX FRASER’S CLARINDA RECYCLING FACILITY IS BOOSTING ITS REPROCESSING CAPACITY BY 40,000 TONNES A YEAR.
With the new additive bins, Alex Fraser are able to blend recycled glass sand and brick into a product that meets Vicroads specifications.

Prior to the of the Victorian Government’s February announcement that it would roll out separate kerbside glass bins from 2021, several councils had proactively implemented similar measurers. The rational, largely, stemmed from an understanding that glass waste in the mixed recyclable bin is problematic – contaminating material when it inadvertently shatters.
Additionally, while most recyclable materials face the challenging problem of end-markets, the demand for glass waste reprocessed into road base is stark and significant.
Delivering on end-market demand is a central focus for Alex Fraser, with the company’s Clarinda recycling facility currently processing hundreds of thousands of tonnes of recycled products for use on road construction and maintenance projects across Victoria.
“Both glass fines and brick are priority and problematic waste streams, and our Clarinda recycling facility is a perfectly positioned outlet for these recycled products,” Peter Murphy, Alex Fraser Managing Director says.
“We are not only reprocessing waste materials, but ensuring that the material is recycled into a valuable resource that is needed and contributes toward Victoria’s growing circular economy.”
Late last year, Alex Fraser was among 13 recipients of the Victorian Government’s $4.67 million Resource Recovery Infrastructure Grants program.
It used the $336,500 grant towards the construction of the new glass and brick additive bins at its Clarinda facility recycling facility, where they are used to blend recycled glass sand and brick into a new, sustainable roadbase product.
This single piece of recycling infrastructure is markedly increasing the distribution of recycled glass and brick into road and rail projects throughout Melbourne’s south eastern suburbs.
Murphy says the project will help reduce the landfill and stockpiling of problematic glass by 40,000 tonnes per year – the equivalent of 200 million bottles.
“By reprocessing this priority waste into high quality sand, we’re able to supply rail and road projects with a range of high-spec, sustainable materials that cut costs, cartage and carbon emissions, and reduce the strain on natural resources,” he says.
“We’re pleased to be working with the Victorian Government to overcome one of the state’s biggest recycling challenges.”
Matt Genever, Resource Recovery Director at Sustainability Victoria, says
SV recognised the Clarinda recycling facility as an important site for resource recovery in Melbourne.
“Processing up to one million tonnes of recycling per annum, the site serves a dual purpose, both as a hub for C&D waste in the south-east and through supply of aggregate and sand into new construction activities,” he says.
“We are acutely aware of the shortage of quarried materials to supply the state’s significant infrastructure program and having a site of this scale located in close proximity to these major projects is essential in ensuring ongoing supply of recycled construction products and materials.”
Recently, the Southern Program Alliance opted to utilise almost 200,000 tonnes of tonnes of Alex Fraser’s recycled materials on the Mentone and Cheltenham Level Crossing Removal Upgrade (LXRA).
The project, expected to be completed in early 2021, is set to save 170,000 tonnes of material from landfill and will reduce the strain on natural resources by 185,000 tonnes.
Alex Fraser’s support on the LXRAs is coupled by the supply of major roads projects like the Mordialloc Freeway, Monash Freeway and Western Roads Upgrade – which include millions of glass bottles from kerbside collections.
With the additive bin now in full operation at the Clarinda Recycling Facility, Alex Fraser is increasing its handling of priority recovered materials – like glass fine and brick – to around 800 tonnes per week.
“Glass is a high-volume waste stream, so it is imperative its recycling facilities are well located close to the point of generation and close to its end-markets,” Murphy says.
He adds that as inner-metropolitan quarries deplete, natural sand is being trucked up to 100 kilometres, driving up costs, traffic congestion and emissions.
The additive bin will not only help with Melbourne’s glass waste problem, but provide an inner city supply solution that reduces these impacts.
Alex Fraser’s Clarinda facility has the capacity to recycle a million tonnes of C&D waste each year.
Murphy explains that the reprocessed material typically goes out to road and rail projects as recycled aggregates, road base or asphalt. Peter Murphy Managing Director, Alex Fraser
“With the new additive bins, we are able to blend recycled glass sand and brick into a product that meets Vicroads specifications for most road bases, which are being used in huge qualities on municipal works and Big Build projects throughout the south east,” he says.
When C&D waste material arrives at Clarinda, often as huge slabs of concrete, it is crushed by an excavator before moving to the processing plant.
The plant then crushes the material even further into an aggregate size. From there, it is transferred to a conveyer that moves the material under the new additive bins.
“The additive bins slowly release the recycled brick and glass into the mix in a ratio approved by Vicroads. It then goes through to a pug mill where the moisture content is adjusted to meet Vicroads specifications and the specified percentage of cement is added.
“Projects demand high volumes, to accurate specifications, on tight timeframes, and these bins help achieve that,” Murphy says.
The facility is not simply reprocessing 40,000 tonnes of glass waste per year, but recycling 40,000 tonnes of glass waste that cannot be
otherwise recycled.
Thereby shifting it from a low value, high volume waste stream destined to accumulate in stockpiles or landfill, into a product of immense environmental and economic value.
In regard to the forthcoming Victorian kerbside glass bin rollout, Murphy says Alex Fraser is well placed to manage a likely influx of material.
There will always be a significant portion of glass waste that cannot be recycled back into bottles or containers and we are already seeing an increase in glass arriving at us for recovery,” Murphy says.
“While that may increase or decrease depending on what measures are put in place, whatever happens, Alex Fraser has the capability to manage it.”
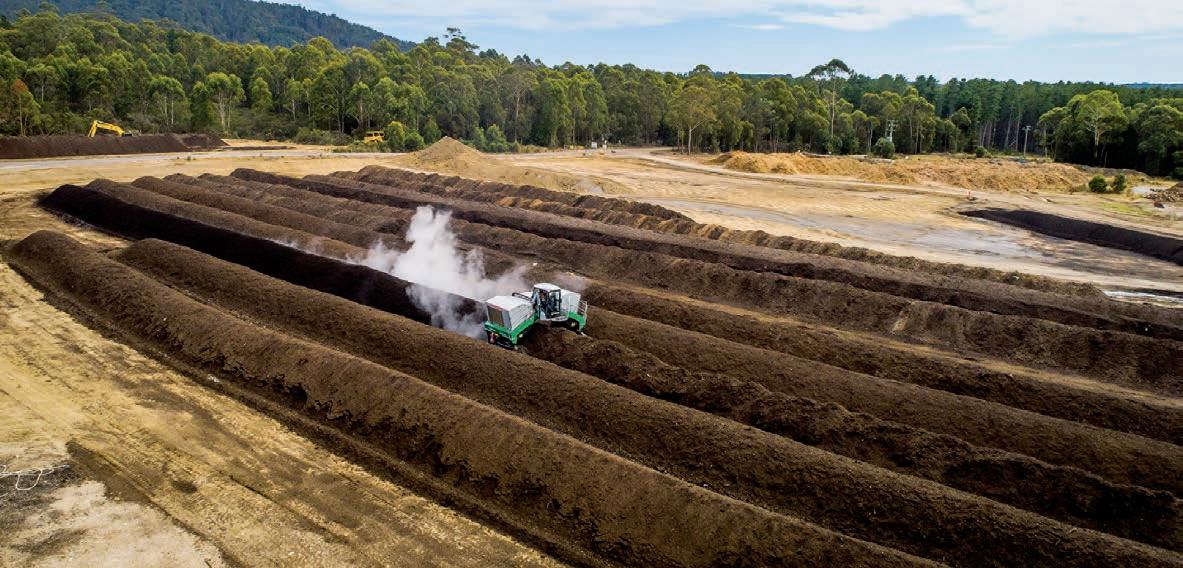
Since operating a Komptech Topturn, Dulverton has seen a dramatic increase in turning efficiency.
Tasmanian Topturn
AS DULVERTON WASTE MANAGEMENT EMBARKS ON A THREE-STAGE FACILITY UPGRADE, PROJECT MANAGER MATTHEW LAYTON DETAILS STAGE ONE: THE PURCHASE OF A KOMPTECH TOPTURN.
In February this year, Kentish Council in north-west Tasmania approved a Development Permit Application from Dulverton Waste Management. The permit allows the company to upgrade its existing compost facility and provide best practice leachate and odour control.
Development plans include the construction of an industrial compost cover and associated mechanical equipment to better manage aeration and moisture of existing compost windrow operations.
According to Matthew Layton, Dulverton Waste Management Project Manager, the improvements will control the effect of rain on organic input material, which includes council green waste and industry input stock from across Tasmania.
“We get 1000 millimetres of rain a year down here, which is very different to a lot of facilities on the mainland,” he says.
Dulverton, which in addition to its organics facility operates an awardwinning landfill, collectively processes upwards of 100,000 tonnes of material annually – with 40 per cent processed through an open windrow composting system.
“We’re a regional facility, so unlike many mainland composters, we need to accept everything in our region. That includes product residues from food manufacturing and green and shrinkage rates.” municipal waste,” Layton says.
He explains that the industrial compost cover is just one development in a three-stage facility upgrade plan. Stage one, he adds, was the purchase of a specialised windrow turner with irrigation, which began operating on Dulverton’s existing open-air compost piles in January.
The Komptech Topturn X63 compost turner, purchased through Australian distributor ELB
Matthew Layton, Dulverton Waste Management Project Manager
Equipment, has a throughput of up to 4500 cubic meters per hour. The combination of a large drum with thrower blades and powerful drive ensures the turner leaves a well-mixed windrow in its wake.
Before acquiring the Topturn, Layton says Dulverton used a traditional excavator to turn its compost piles. With a view of consolidating cost and making its processes as efficient as possible, Dulverton went to market to look for a suitable turner to replace its excavators.
“In the lead up to our facility expansion, we wanted to ensure our operations were more cost effective and efficient,” he says.
“There are a number of turners on the market that could achieve that, but we went with the Topturn primarily because of the service support in regional Tasmania.
“There was also the added benefit of a commonality of parts, especially with the engine.”
The Topturn’s engine meets all relevant emissions standards, with a new cooling system keeping the system running under heavy loads and high outside temperatures.
Komptech’s X63 features a largedimensioned turning drum for high throughput and complete mixing, with easy maintenance access via ladders and platforms integrated into the body.
Furthermore, ELB offer the turner either wheeled or tracked, with engine power converted efficiently into
A key feature of Dulverton’s Topturn is the ability to add a lateral displacement device at a later stage.
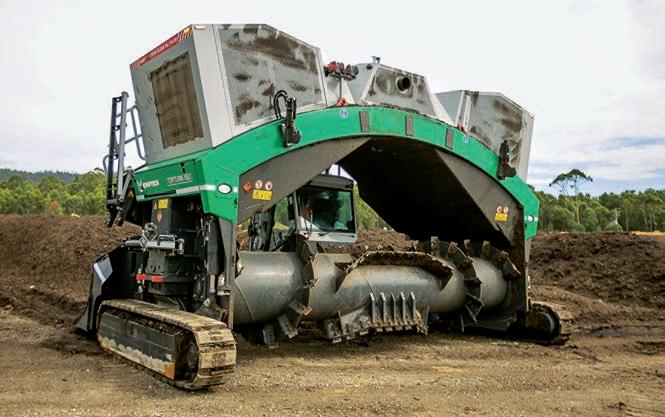
forward movement.
Since operating the Topturn, Layton says Dulverton has seen a dramatic increase in turning efficiency.
“We’ve seen changes in our processes for the operators working with the machine, but also the biology of the compost,” he explains.
The Topturn purchase, Layton says, was Dulverton’s first commercial

The Komptech Topturn X63 has a throughput of up to 4500 cubic meters per hour. dealing with ELB.
“They’ve been really good from a client support perspective, particularly in terms of information sharing and guiding us along the track to where we needed to be,” he adds.
“They also offer significant after sales assistance, which really supports the way we’re trying to modernise our facility.”
A key feature of Dulverton’s Komptech Topturn is the ability to add a lateral displacement device at a later stage, Layton says. He adds that in the future, this will give operators the ability to turn and move more compost at once.
When coupled with the turner, ELB’s lateral displacement device minimises transport distance and improves viability and monitoring. By collapsing two windrows, the decomposition shrinkage is smoothed out, making full use of the space.
“We expect this equipment will continue to deliver environmental benefits by providing full aeration and moisture-balance of the compost to assist the natural decomposition process,” Layton says.
“The windrow turner will continue to be used throughout our upgrade program.”
An action-plan for organics
THE AUSTRALIAN ORGANICS RECYCLING ASSOCIATION’S NEW NATIONAL STRATEGIC PLAN OUTLINES ACTION POINTS FOR SUSTAINABLE GROWTH IN THE ACCELERATING SECTOR.
Government action and funding for organics recycling has ramped up in recent months. In May, for instance, the NSW Government announced $20 million in grants for the alternative waste treatment industry and councils affected by the EPA’s controversial 2018 MWOO decision.
On the other of side of the country, the Western Australian Government has made similar commitments – injecting $20 million into the economy to support local governments transition to better practice three-bin FOGO services.
This is welcome news to Peter Olah, Australian Organics Recycling Association (AORA) National Executive Officer, who since joining AORA in 2019, has worked proactively to grow government support for the sector.
“The increases in funding for the organics recycling industry are a welcome recognition by governments of the industry’s contribution to our economy,” Olah says.
As the leading national voice for the organics recycling industry, AORA has developed a new strategic document – detailing targets and action points towards the creation of a more sustainable and profitable industry.
Approved by the AORA Board in late May, the AORA National Strategic Plan 2020-2023 seeks to further entrench public and government understanding of the role of organics recovery within a circular economy.
The plan’s mission statement highlights the role AORA will play in facilitating an operating environment that maximises the recycling and reuse of organic materials.
“Through ongoing communication with stakeholders, AORA seeks to promote the benefits of compost, soil conditioners and mulches across the Australian community,” Olah says.
As the first of three objectives, AORA plans to further develop its position as the national voice of the organics recycling industry.
According to Olah, success in this space will see governments and other stakeholders approaching AORA proactively, with the knowledge that the association provides positive direction and leadership.
“The organics recycling industry is not new. Humans have been recycling and reusing organic materials since ancient times,” Olah says.
“Today, the role of the industry is
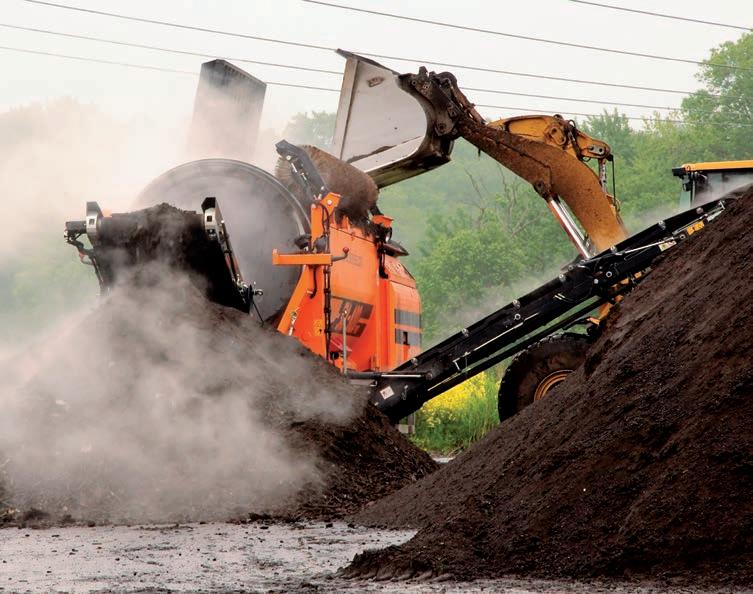
By 2023, AORA targets growth to 500 members, including at least 80 per cent of all processors nationally.
becoming more critical however, as the effects of climate change, urban development, agricultural practices and energy use impact the health of our soils and environment.”
Mirroring statements made in the Strategic Plan, Olah stresses the role of the organics industry in diverting material from landfill to beneficial reuse, mitigating climate change and improving the sustainability of agriculture.
“In order to perform this role effectively, the industry must work with governments and other stakeholders at all levels in setting the policy and regulatory frameworks which promote the best outcomes,” he adds.
To achieve this goal, AORA has outlined four key targets for 2023, including producing reports and original research to ensure the needs of the organics industry are clearly presented to government and other stakeholders.
“We do not want to produce unread reports, so any original research we undertake will always be about better positioning the industry with governments and the community,” Olah adds.
Furthermore, AORA plans to continue collaborating with governments to design and implement policy, regulation and legislation that optimises market conditions for the industry. To support this, AORA will begin establishing knowledge hubs for recycled organics research, development and communication.
“The number one issue for our industry is the piecemeal nature of government decision making. We must have a better alignment between the industry and government at all levels to improve the operating environment, so that our industry can invest and employ more, and provide even greater benefits to our society,” Olah says.
The association will also further develop and position Compost for Soils as a core resource for business and the community.
“Compost for Soils works to champion pathways to sustainable, resource-efficient organics recovery and agricultural reuse practices by allowing users to find composters across all Australian states and territories,” Olah explains.
The second objective, championing a future where organics recycling is maximised, seeks to increase recycling rates nationally.
“We want to see community understanding of the industry and its products grow, and as a by-product, increase profitability across the sector,” Olah says.
“In addition to growing the industry, achieving this goal will see further applications of composted and organics products to soil, thereby sequestering carbon, improving water retention, drought-proofing land, and improving agricultural productivity.
“Organics recycling closes the loop on food and other organic wastes and ultimately returns them to food production through the soil. It’s the industrialisation of a natural process, and therefore a true exemplar of the circular economy.”
Three-year targets include identifying, communicating and celebrating best practice strategies, technologies and products.
“In the first year we will formalise partnerships with tertiary institutions, CRC’s and other associations by targeted MOU’s focused on shared strategic objectives,” Olah says.
“We also plan to communicate our major policy documents so that they are well understood by governments and other stakeholders.”
As reported byWMR in May, AORA commissioned Nick Behrens of Australian Economic Advocacy Solutions to undertake an investigation into the economic impact of the organics recycling industry.
The report highlights that each year, the organics recycling industry processes around 7.5 million tonnes of waste into valuable products for further use across the Australian economy. As a result, 2018-19 saw a collective industry turnover of $2 billion.
The report, Olah explains, provides an important baseline to inform future policy discussion with stakeholders and government. He adds that further distribution of the report across government and the wider community is therefore critical to achieving the goals outlined in AORA’s National Strategic Plan.
The final objective concerns AORA’s internal structure, Olah says, highlighting the importance of operating as a sustainable and transparent business.
“In order to deliver the beneficial outcomes AORA envisions for its members and the Australian community, it must do so from the certain base offered only through a sustainable, well run and flexible business,” he says.
“To deliver this, AORA must have high quality and transparent corporate and financial governance, a broad and reliable revenue base, a wellmanaged and targeted approach to expenditure, and a strong central focus on identifying and delivering the needs of members.”
By 2023, AORA targets growth to 500 members and corporate sponsors, including at least 80 per cent of all processors nationally. To build that base, Olah says the next few years will see AORA delivering more significant events to demonstrate thought leadership for the industry.
“We will also work to regularly review our member products and services to ensure their ongoing relevance and broad appeal,” he says.