
8 minute read
REPURPOSED FUEL TO THE FIRE
Alvan Blanch’s Materials Conveyor Drier is processing 20,000 tonnes of wood waste derived fuel a year for Boral.
THE MATERIAL DRYING PROCESS IS ESSENTIAL TO IMPROVING EFFICIENCY. ROBUST SYSTEMS BY ALVAN BLANCH ARE REPURPOSING MATERIALS TO BENEFIT AUSTRALIAN INDUSTRIES BEYOND THE WASTE SECTOR.
Cement is primarily used for concrete, the world’s second most consumed material after water. It’s no secret that concrete has one of the highest CO2 emissions of all building materials, making it a focal point for companies looking to innovate and experiment with its production and application in construction, while decreasing its environmental impact.
Brandown Resource Recovery Centre in NSW was approached by Boral in 2018 to help them explore opportunities to integrate solid waste derived fuels (SWDFs) into the heat energy process at Boral’s Berrima Cement Works.
Typically, SWDFs are made from materials which would have been destined for landfills, space for which comes at a premium in the populated areas of NSW.
As the state expects to reach its landfill capacity in the next 10-15 years, exploring repurposed fuel will positively contribute to the NSW 20-Year Waste Strategy, set out by the state government.
Located in the Southern Highlands region of NSW, the Boral Berrima Cement Works produces up to 60 per cent of total cement products consumed within the state.
Wood Waste-Derived Fuel (WWDF) was added to the site’s planning approval for use in 2016.
WWDF consists of the off-cuts and leftovers of processes working with wood, such as furniture manufacturing.
By the end of 2018, when Brandown was utilising its Alvan Blanch Materials Conveyor Drier (CD) for Boral’s WWDF, the NSW site’s SWDF system was functioning at a rate of 20,000 tonnes per year of WWDF.
During the present 2019-20 financial
year, the site aimed to increase its annual SWDF usage rate to 75,000 tonnes per year. It is projected that the target of 100,000 tonnes per year could be reached as early as 2021.
Woodchip drying is a vital part of biomass fuel production which adds to bio solid fuel quality.
A Biomass Energy Centre study indicates that the wetter the intake fuel is, the less responsively the boiler operates. Therefore, the drying process becomes essential to improving woodchip usage efficiency.
Terry Martin, General Manager at Brandown recycling facility, says it was vital to find a CD that met the specific drying requirements set by Boral, as well as being an overall economically viable system.
Martin travelled over 16,000 kilometres to the other side of the world to investigate CD machinery operations.
Following two site inspections in London, England to see the CD’s in action, the Alvan Blanch UK team flew to NSW to assist installing Brandown’s CD in mid-2018.
According to Jim Duncan, Queensland based Manager at Alvan Blanch Australia, Brandown had done a lot of market research and were primarily after a system that reduced moisture in a quick and simple manner.
Duncan credits Alvan Blanch CD’s simplicity as the winning factor that inclined Brandown to order the system within weeks of the company’s initial machinery inspection.
He says the running cost of annual maintenance is very minimal compared to other systems, which is appealing for clients such as Brandown, who are churning tens of thousands of tonnes of material at a rapid pace.
“It’s an extremely robust system and I think the team at Brandown recognised the benefits of a fully automated system, that could integrate into their existing process,” Duncan says.
Once the Alvan Blanch team understood Brandown’s requirements, Alvan Blanch looked further into the heating system to ensure it was as effective as possible.
For Brandown’s specific woodchip drying needs, to be repurposed into WWDF, Alvan Blanch ensured the system’s heat exchange collaborated with their external electricity generation system, which is powered by diesel generators.
“The system is designed to recover some heat from the generation island on site within the CD, allowing the Brandown crew to control the temperature and reduce moisture from its material,” Duncan says.
According to Duncan, reducing moisture from materials is becoming an interesting consideration for Australian waste and manufacturing companies,which is why robust systems are crucial to meet material requirements.
He says more companies are expressing interest in reallocating human resources into smart machinery following the recent pandemic.
“A lot of people are curious about what they need to do in terms of machinery that can be customised to its materials requirements,” Duncan says.
Most recently, Alvan Blanch has been approached by a client in far north Queensland that is interested in a CD for a material the company had never worked with before, all Australian banana waste.
Queensland accounts for 94 per cent of Australia’s banana production. Duncan says that Alvan Blanch’s client is recovering waste from banana production and processing lines and repurposing the content from its CD system as animal feed to the agriculture sector.
“From helping clients service Australia’s largest infrastructure projects to the nation’s largest mammals, it’s safe to say we’re continuing to supply engineered systems that are designed to meet any expectation.”
The drier allows operators to control temperature and reduce material moisture.
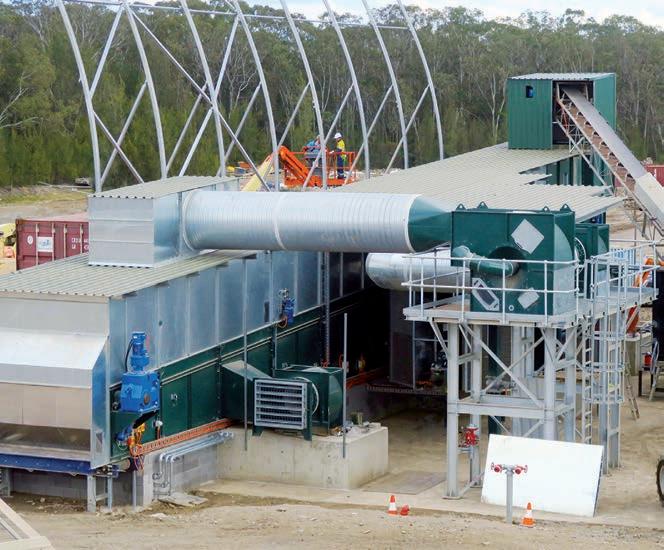
Scrubbing sands
TEREX WASHING SYSTEMS DETAILS THE SPECIFICATIONS OF A NEW STATEOF-THE-ART AGGREGATE WASHING PLANT IN THE SOUTH OF ENGLAND.
Construction and demolition waste management specialists R Collard have opened a new state of the art aggregate washing plant at its recycling facility in Eversley, Hampshire, UK.
The new washing plant, designed and supplied by Terex Washing Systems (TWS), incorporates the latest technology to enhance the quality and efficiency of the facility’s recycling process.
The installation was specified and project managed by TWS’ England and Wales distributor Duo Plc.
Capable of throughputs up to 120 tonnes per hour, with an annual production capacity of around 250,000 tonnes, the system will provide a local source of high-grade recycled aggregate products 12 months of the year.
The goal: to enhance the efficiency and environmental performance of regional construction and civil engineering developments in the South of England.
“Transport is a major factor in the cost of aggregate, so our investment in this plant is a direct response to increasing demand for high quality, affordable recycled product in our catchment area throughout the South East England,” says Robert Collard, Collard Founder and Managing Director.
“The refinements to the technology involved will enable us to process more waste than we collect from local sites, and create a truly closed-loop recycling system for construction waste in the South of England.”
TWS’ recycling processes are
The plant can operate all year round due to a new feeder system, which processes cohesive material even when its moisture content changes.
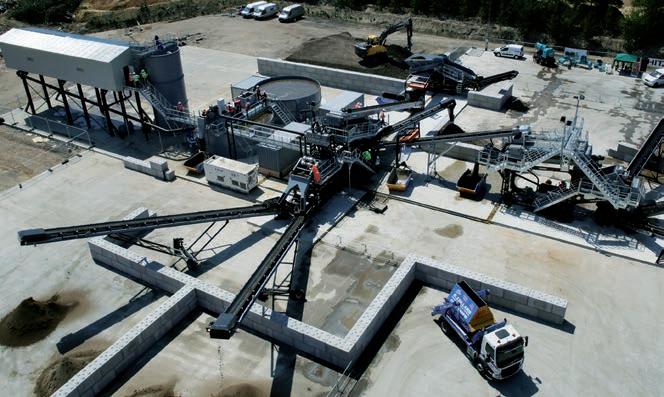
designed to transform construction and civil engineering waste into clean, homogenous recycled products. This is achieved by removing lightweight and deleterious contaminants and extracting silt and clay, which can bind otherwise commercially viable aggregates together.
According to TWS’ Elaine Donaghy, the plant boasts a number of innovative new features, including hydrocyclone technology that produces high-grade coarse sand product with less than two per cent silt content.
Furthermore, the plant features integrated sorting systems that remove non-mineral contaminants to a greater extent than conventional dry systems, enabling more waste to be used as feedstock.
“The plant can operate all year round due to a new feeder system, which processes cohesive material even when its moisture content changes. Fully adjustable and modular components also enable bespoke products to be generated,” Donaghy says.
“The wash plant set up at R. Collard’s is an innovative, effective and coherent approach for the recycled aggregates industry.”
AGGREGATE WASHING
The R. Collard’s plant draws from TWS’ extensive range of washing equipment, incorporating the Warrior 1400 scalper, AggreeSand 165 3D2S and AgreeScrub 150. The plant also utilises a Thickner and Filterpress for water treatment and recycling.
“The process starts with an AggreScalp heavy duty scalping unit, particularly suited to claggy and clay contaminated, high soil content feeds,” Donaghy explains.
“This unit removes excess oversize before passing the bulk of material to the subsequent washing equipment.”
The AggreScalp includes a magnet to capture ferrous metals, specifically located to allow ferrous metals to be extracted in free fall before transfer to the AggreSand. The AggreSand
incorporates a 16x5 three deck screen to produce clean 50-millimetre aggregate for subsequent crushing, delivering the mid and bottom deck outputs to its partnering AggreScrub 150 for attrition and sizing.
Typical feed material contains high root content, Donaghy says, which is effectively removed by the AggreScrub.
“The flotation capabilities of the AggreScrub are ideal for addressing the variable contaminants found in recycled aggregate sources such as paper, wood and light plastics,” she adds.
“These contaminants, together with most of the water and liberated sand particles, are passed from the rear of the AggreScrub to the integrated trash screen. This step recovers the lightweight contaminants as a waste and allows the water and sand to be collected.”
In addition to flotation, Donaghy says the AggreScrub’s other key purpose is heavy attrition, which liberates adherent clays to produce clean organicfree aggregates for a wide range of construction requirements.
A 12x5 part rinser integrated within the AggreScrub modular chassis then provides the final product splits, as requested by Collards. Underflows from the trash screen and the aggregate sizing screen are collected and pumped back to the AggreSand to recover any saleable fine material, ensuring maximum efficiency of water management.
“The 120 tonnes per hour sand plant integrated within the AggreSand produces two high quality sands from the recycled feed material, suitable for concrete, pipe bedding and general construction requirements,”
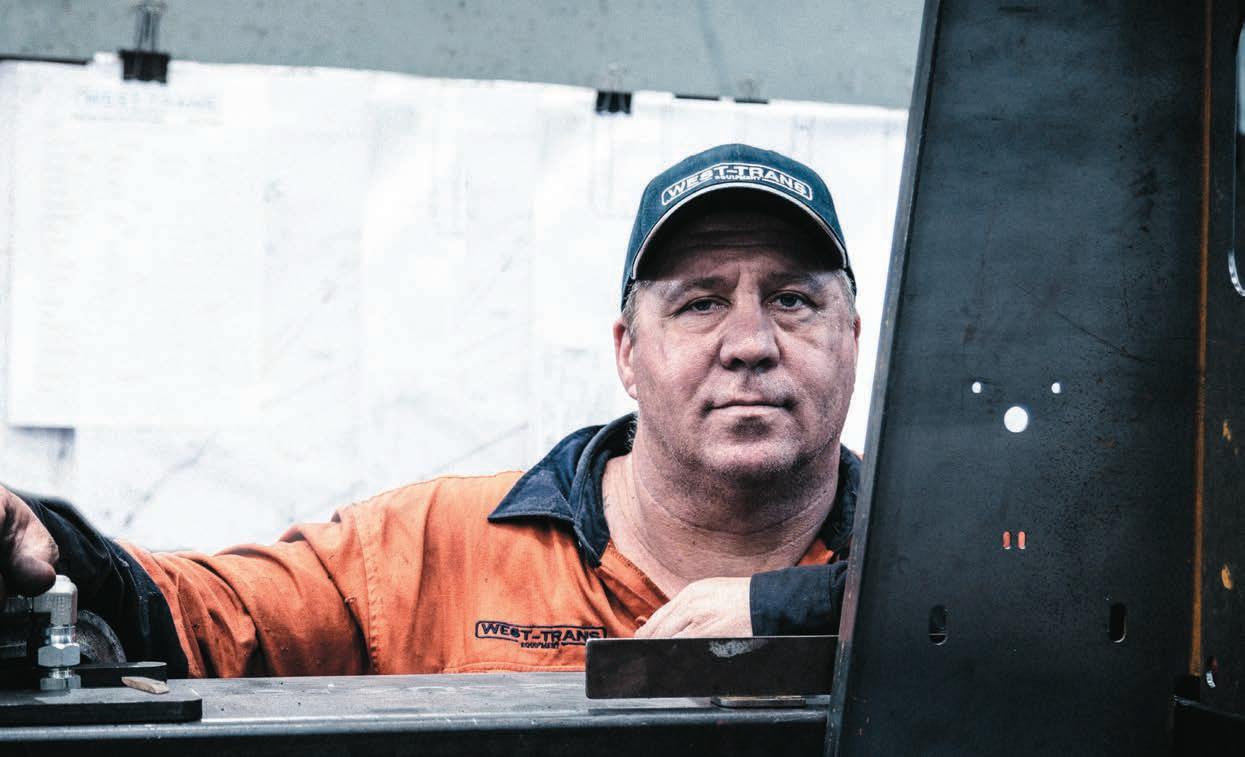
Donaghy says.
“Sand and water from the AggreSand screen, together with return water and fines from the AggreScrub, is recovered via the integrated hydrocyclones, producing coarse and fine sand fractions.”
Sand fractions are then dewatered by the system to ~12 per cent m.c., providing clean and ready to handle material stockpiles.
All dirty water gravity flows from the AggreSand’s cyclones to the congruent water management system.
“By incorporating the very latest technology to enhance the quality and efficiency of the recycling process, the plant significantly reduces cost, fuel consumption and the carbon footprint of supplying recycled aggregate to a number of key developments in the UK,” Donaghy says.
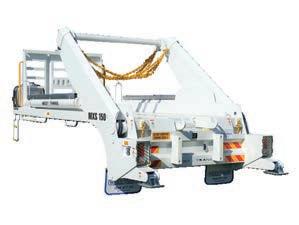