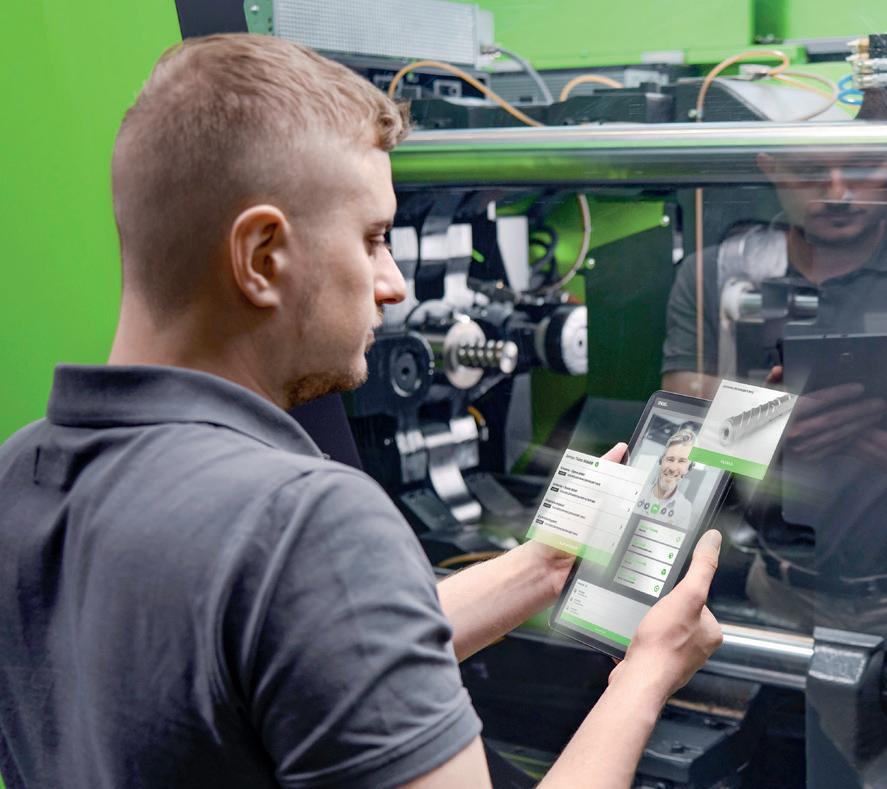
20 minute read
Soluzioni digitali ENGEL per la smart factory
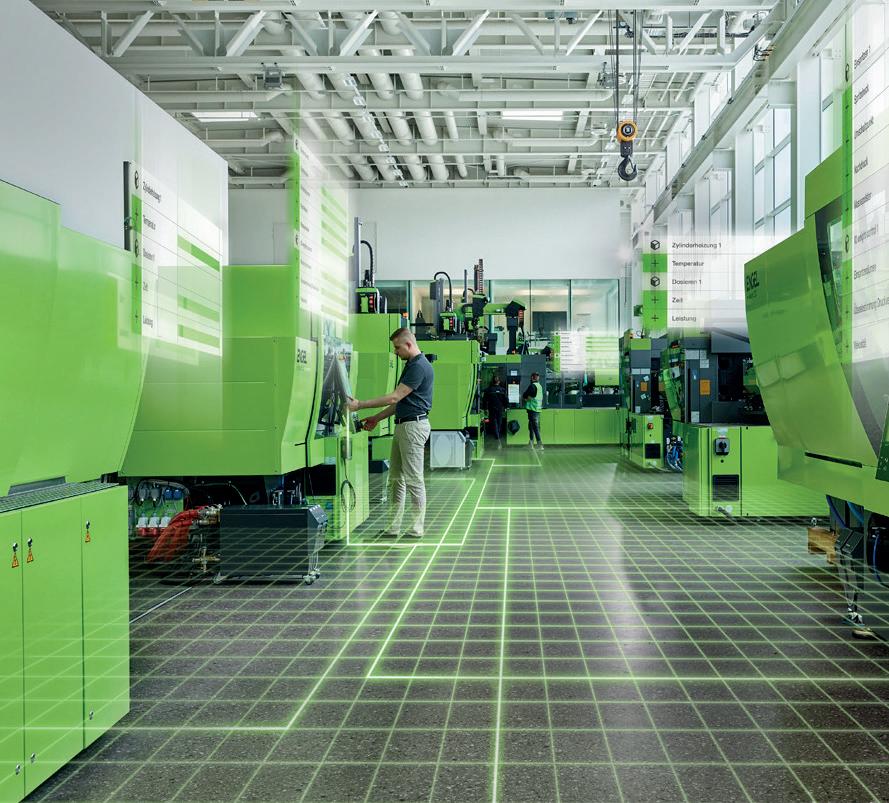

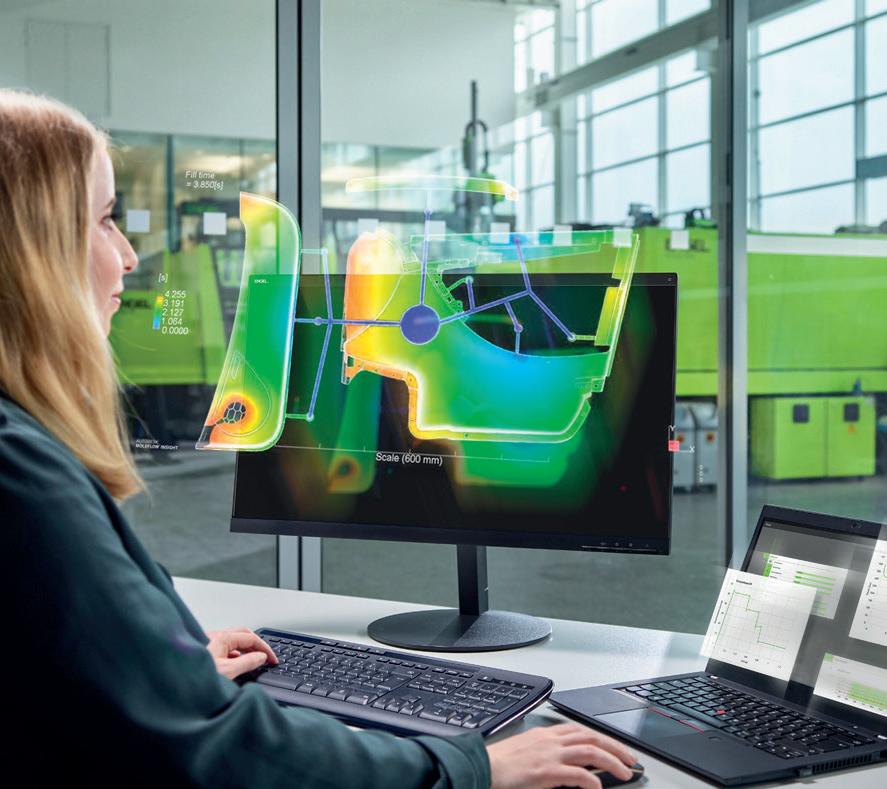
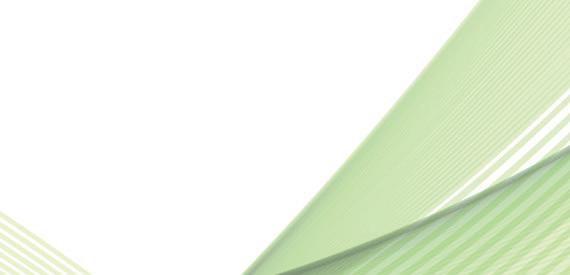
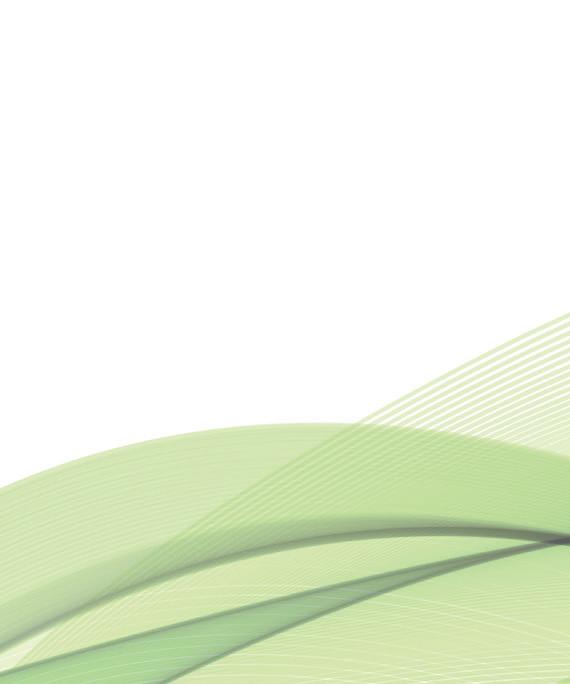
I prodotti e i servizi digitali ENGEL offrono un valido supporto lungo l’intero ciclo di vita del prodotto, dalla progettazione alla campionatura, alla produzione fino alla manutenzione e assistenza. Le soluzioni digitali ENGEL permettono di sfruttare al massimo il potenziale del sistema di stampaggio a iniezione ENGEL e di ridurre in modo sostenibile il CO2 footprint.
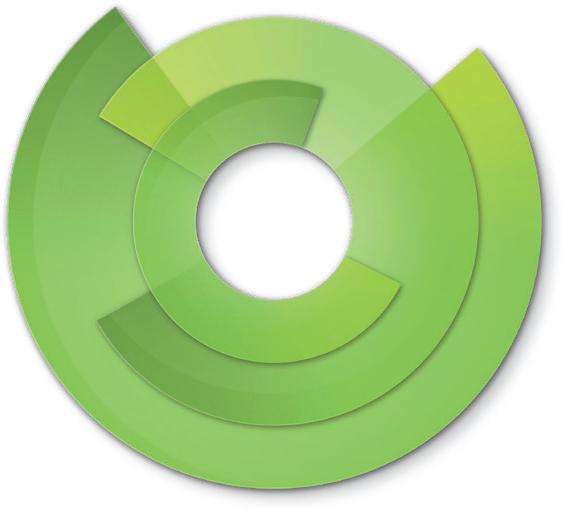
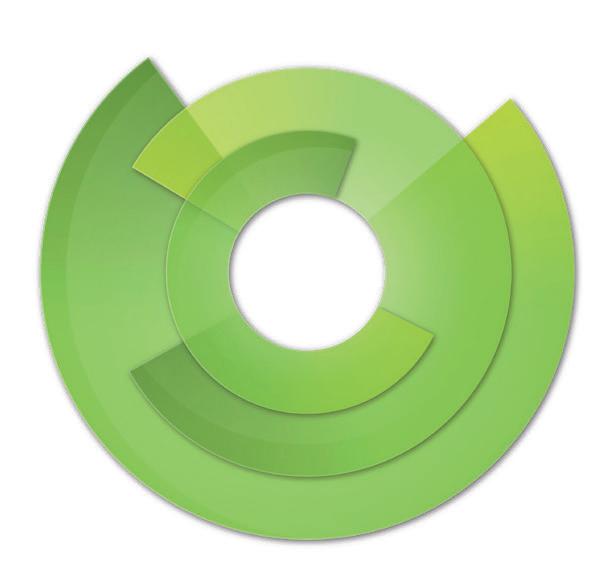
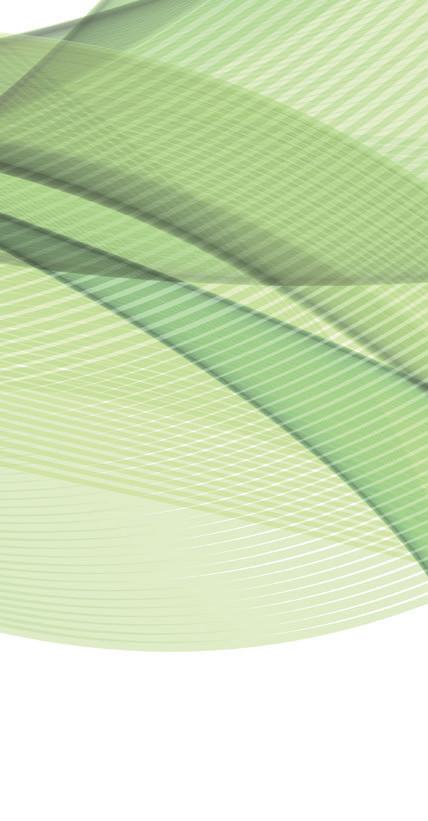

Per saperne di più: engelglobal.com/inject-4-0
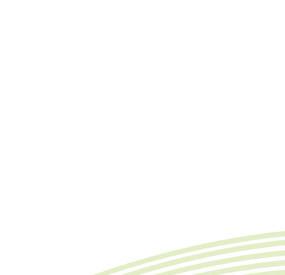
Oltre 45 anni di attività ed esperienza, consensi in Italia e in Europa, Tecnomatic approda adesso in Giappone con una linea per tubi in polietilene ad alto tasso tecnologico che ne fanno già un punto di riferimento nel mercato del Sol Levante. Ecco i particolari della fornitura.
Come nel titolo della hit degli anni Ottanata, con l’espressione anglofona “big in Japan” viene solitamente indicato qualcuno o qualcosa che ha successo ma non nel proprio Paese. Non è questo il caso di Tecnomatic, che, anzi, ha ribaltato tale modo di dire e prima di conquistare il mercato orientale con la fornitura di una propria linea a una primaria multinazionale giapponese, ha mietuto consensi in patria e in Europa nel corso di oltre 45 di attività ed esperienza, in cui si inseriscono i recenti progetti per tubi a 2 e 3 strati con diametro massimo fino a 1.200 mm.
La più grande linea in Giappone
La fornitura giapponese consiste in una linea per l’estrusione di tubi in HDPE monostrato con diametro fino a 1200 mm realizzata su misura secondo le specifiche del trasformatore e diventa la più grande linea per l’estrusione di polietilene mai venduta nel mercato del Sol Levante. La linea è dotata della più moderna tecnologia disponibile per l’estrusione di tubi, a partire da un sistema di alimentazione e dosaggio gravimetrico completamente integrato nel controllo della linea stessa, con un componente per ciascun materiale, PE vergine e rigenerato.
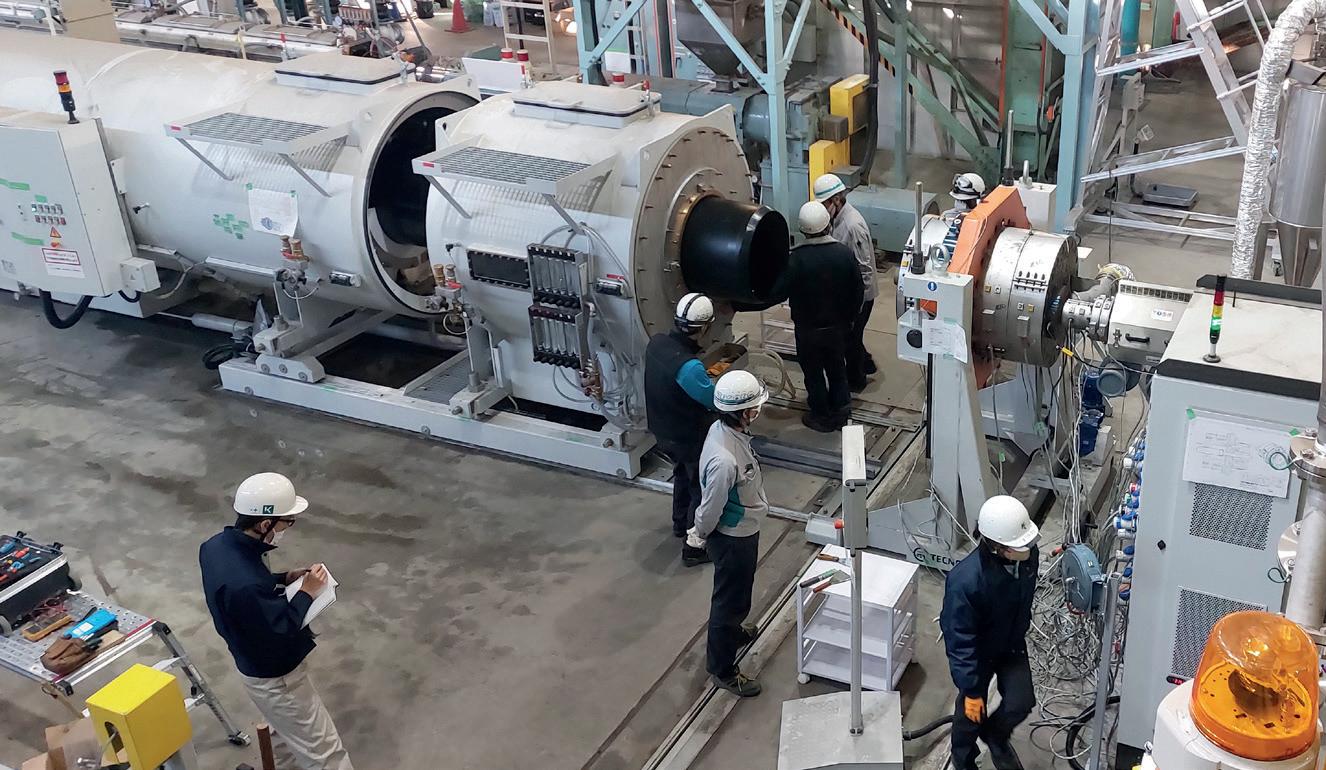
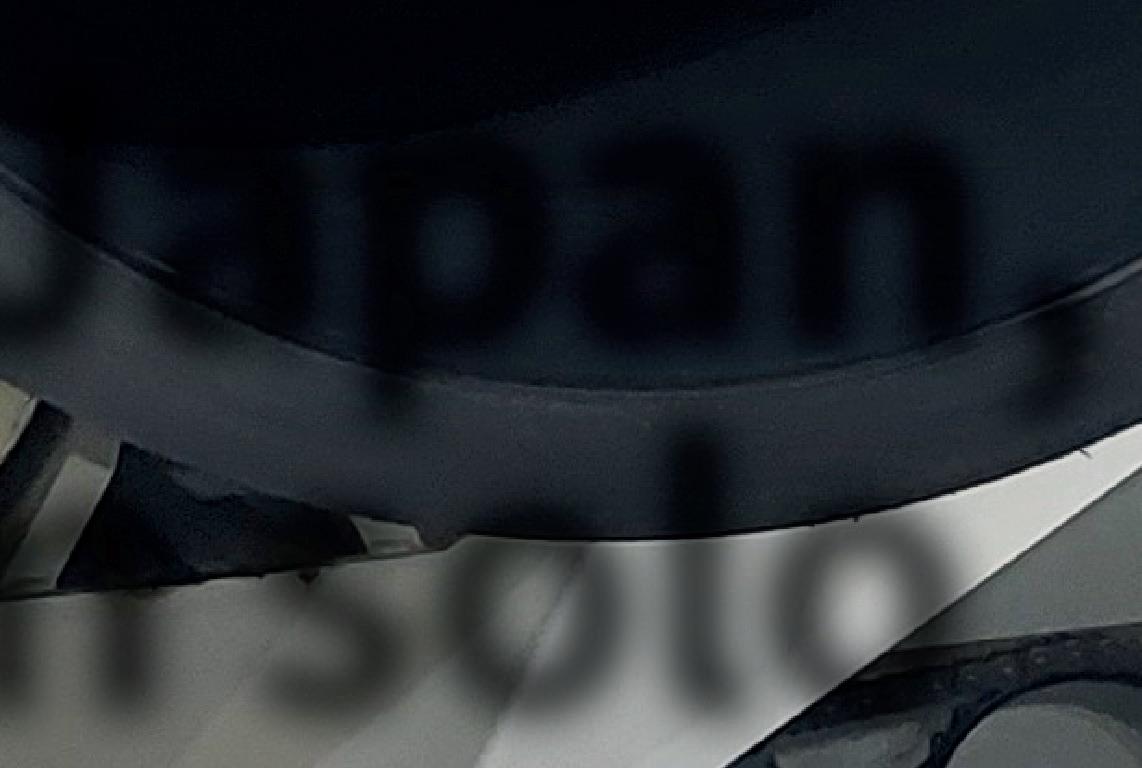
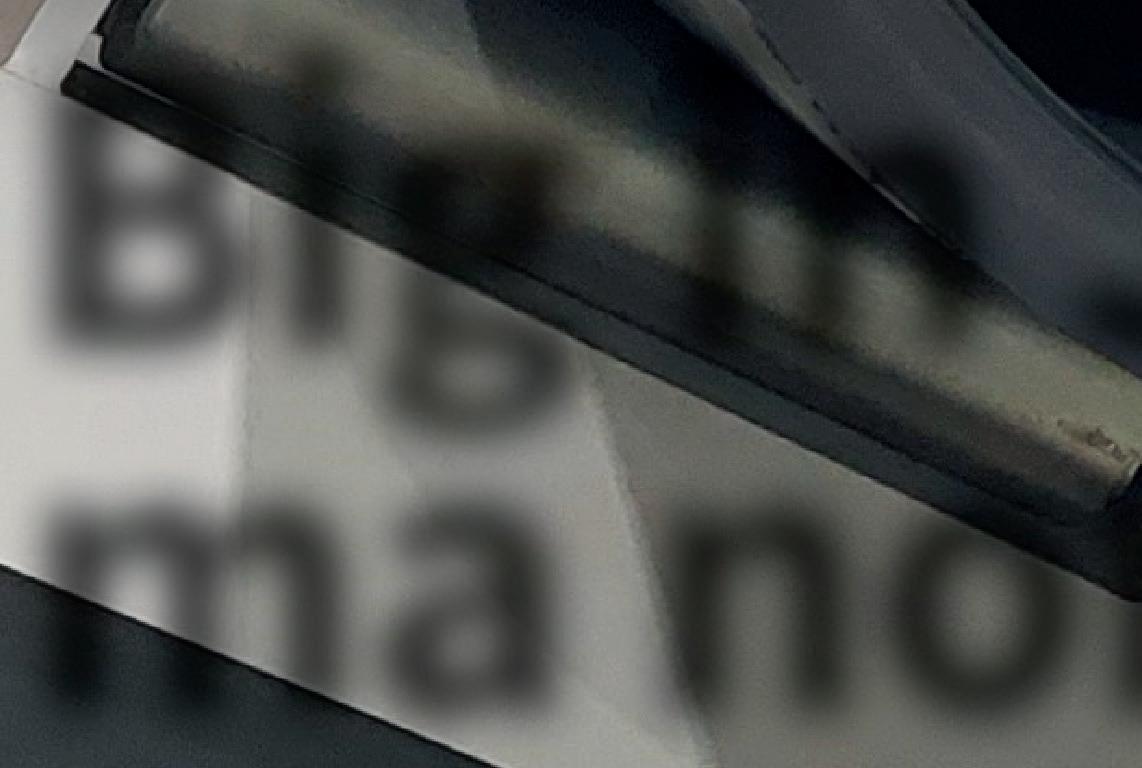
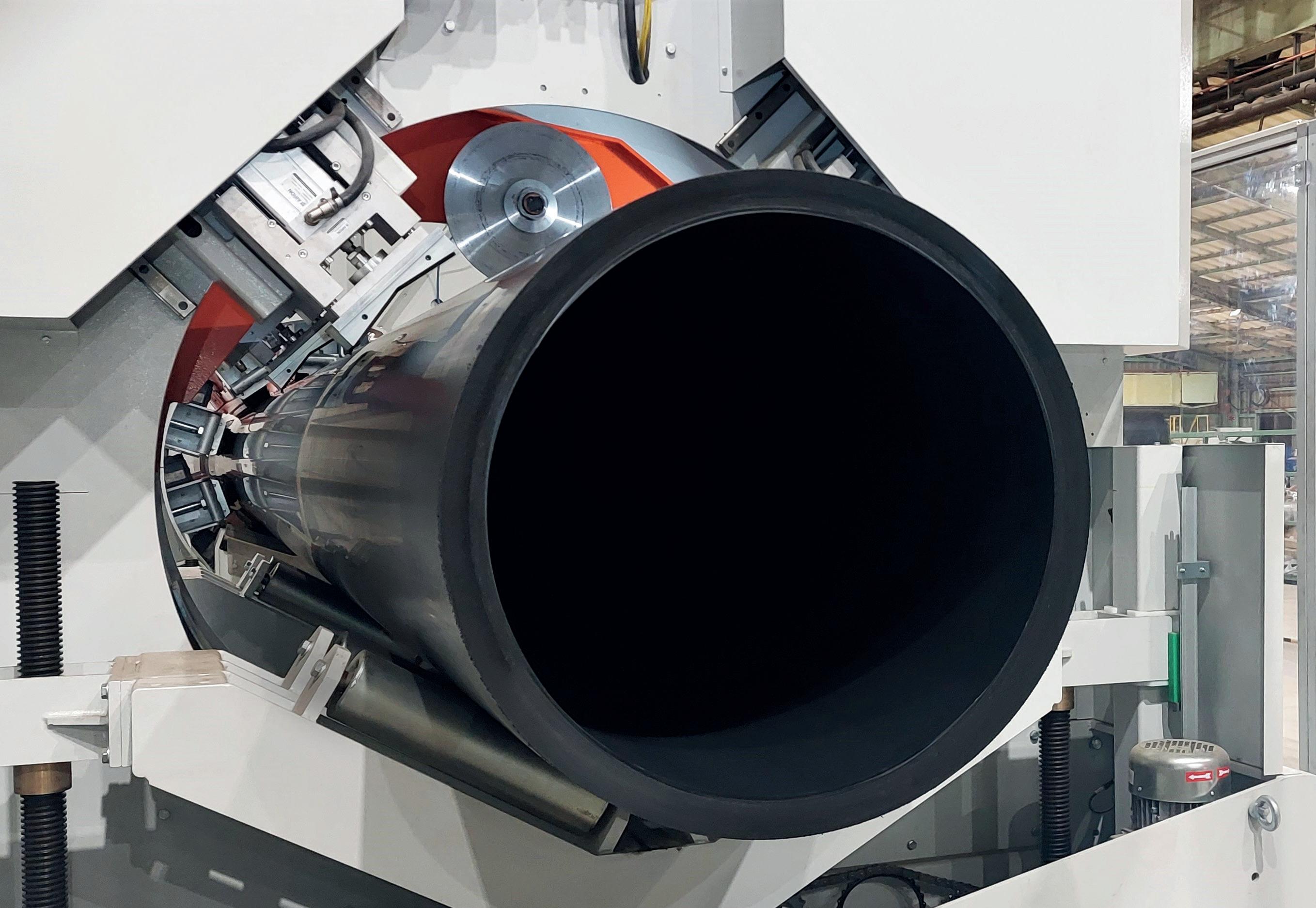
L’estrusore monovite da 90 mm della serie Vega 37D a forma di “Z” che equipaggia la linea, è in grado di plastificare fino a 1.100 kg all’ora di resina, con una ottima omogeneità del fuso. La macchina è dotata di bocchetta e cilindro con rivestimento antiusura e di una vite con una sezione ad alta miscelazione, specifica per le tipologie di materiale utilizzati in queste applicazioni. Il motore AC sincrono Siemens e un solido riduttore, caratterizzato da un corpo monoblocco in ghisa con unità di raffreddamento dell’olio indipendente e gruppo cuscinetti ad alte prestazioni (fino a 500 bar), assicurano inoltre la massima affidabilità nella trasmissione della potenza.
L’estrusore e la linea sono controllati dal nuovo dispositivo EPC I evo (Extrusion Process Control), dotato di nuova piattaforma PC “Multitouch Capacitive Panel”, web server integrato e connettività 4.0 certificata UL. Il nuovo display LED TFT da 21,5 pollici, con un ampio angolo di visuale e sistema operativo Linux, abbinato a processori Risc quad core a 64 bit - 1,6GHz, garantisce elevate prestazioni delle librerie grafiche integrate e permette di avere a disposizione numerosi plugin e widget, come browser html, visualizzatori PDF e video, nonché la possibilità di creare e stampare reportistica. Sviluppato sulla base di specifiche esigenze degli operatori, consente l’integrazione e il controllo di tutti i componenti, quali sistemi gravimetrici, coestrusori e corrugatori, pompe a ingranaggi, cambiafiltri, vasche di calibrazione, traini e taglierine. L’integrazione e la gestione possono avvenire attraverso i più comuni protocolli di comunicazione analogica o il più moderno OPC-UA, in accordo con Euromap 84.
Il cuore è… la testa
Il cuore della linea è la testa di estrusione Venus 1200 che, in questa versione, è stata concepita totalmente cromata e con il sistema di raffreddamento interno ad aria PAC (Pipe Air Cooling). Come per le altre teste della serie Venus, anche questa versione si basa su un design a spirale che garantisce un flusso ottimale del fuso per una ampia gamma di diametri e spessori. Le misure compatte e una ridotta contropressione assicurano, oltre alla ottima qualità dell’estruso, un risparmio energetico nelle fasi di lavoro e riscaldamento.
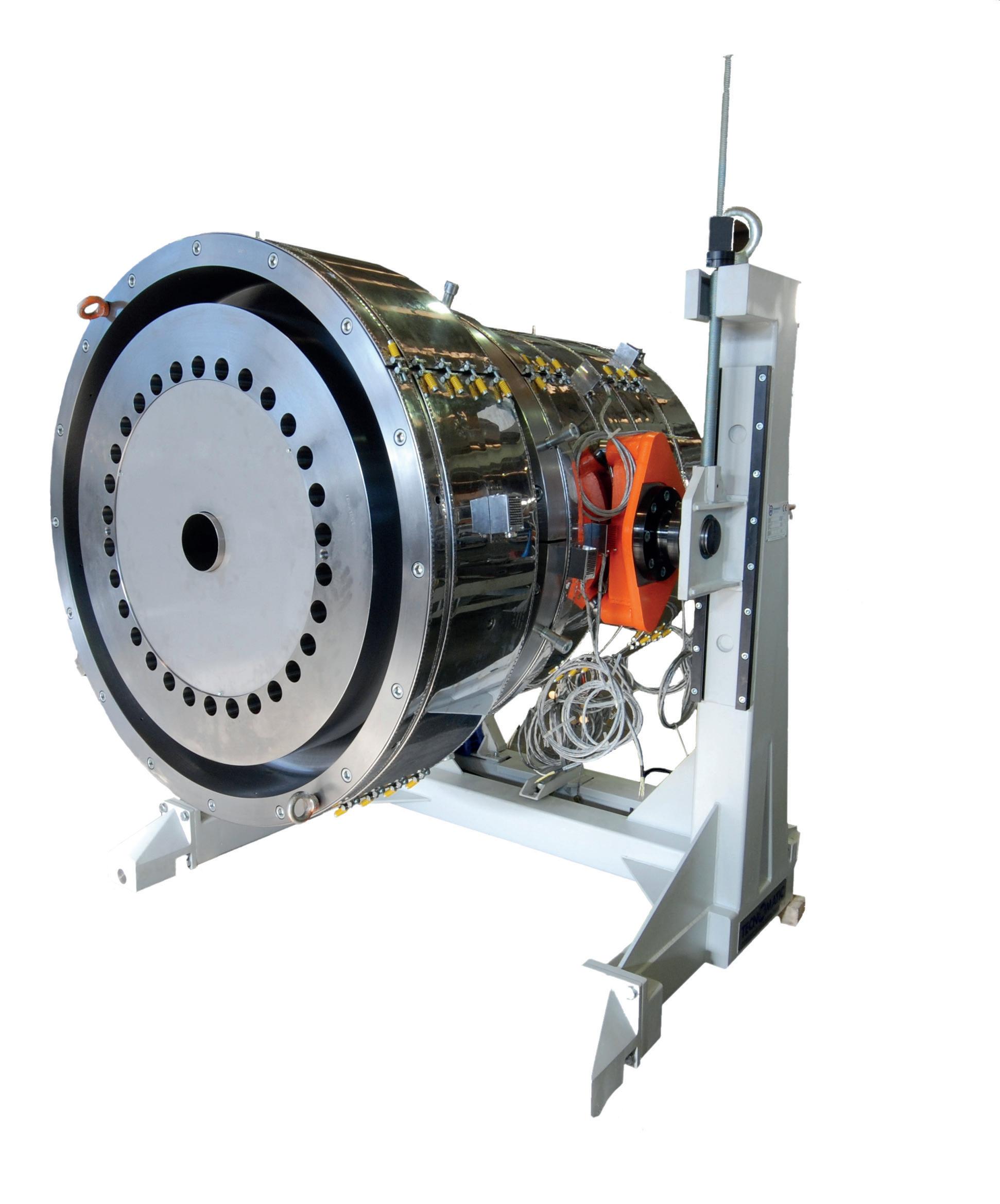
La testa, in grado di coprire diametri dei tubi da 250 a 1.200 mm, utilizza una filiera ogni tre diametri per dimensioni fino a 800 mm, secondo il classico modo di operare in riduzione, mentre per dimensioni maggiori opera con un rapporto filiera/calibrazione prossimo a 1:1, per un ottimale controllo della distribuzione dello spessore della parete e dell’ovalizzazione del tubo, garantendo produzioni fino a SDR (Standard Dimension Ratio) 09 nella misura 1.200 mm.
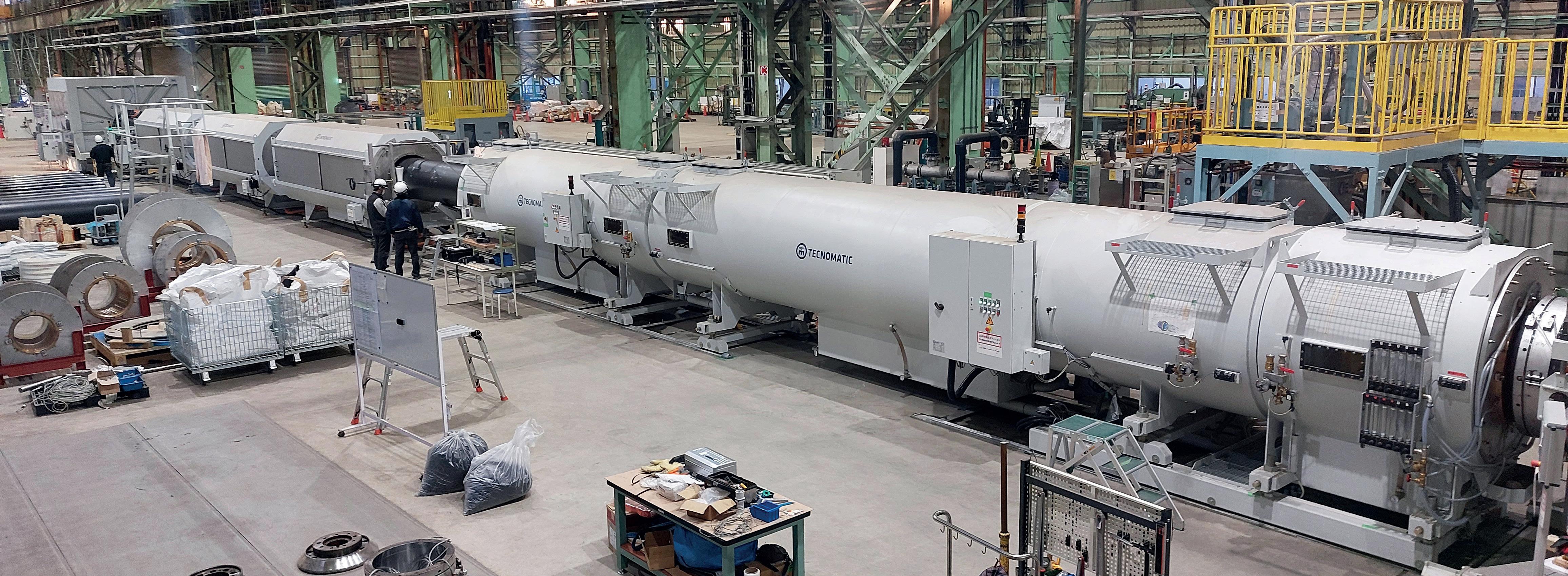
Le matrici sono composte da due sezioni con un piccolo anello terminale per definire lo spessore, consentendo rapidi cambio e regolazione. Il sistema PAC fornisce un raffreddamento intensivo della superficie interna del tubo aspirando aria nella direzione opposta a quella di estrusione. Forzando il flusso d’aria garantisce un raffreddamento uniforme attorno al tubo e attraverso lo spessore della parete, diminuendo le differenze nella velocità di solidificazione del tubo e riducendo le tensioni interne residue.
Garanzia di prestazioni
Le prestazioni di una linea di estrusione di questo tipo traggono indubbi vantaggi dalla corretta progettazione e dal corretto utilizzo di vasche di calibrazione e calibratori e delle attrezzature ausiliarie a valle, quali traini e taglierine. La linea, infatti, è dotata di due vasche sottovuo- to lunghe 16 metri e tre vasche di raffreddamento lunghe 6 metri, per un totale di 32 metri.
Il traino è dotato di lunghi cingoli ad azionamento indipendente comandati da motori vettoriali. Una taglierina planetaria con lama circolare assicura un taglio perfetto del tubo senza produrre trucioli anche quando gli spessori sono elevati. La taglierina è dotata di braccio di taglio ad azionamento idraulico, motore di taglio bilanciato, morse universali con cuscinetti in gomma per una presa efficiente e sincronizzazione OPC-UA per la regolazione della velocità del carrello al variare della velocità di estrusione, così da garantire sempre la massima precisione della lunghezza di taglio.
In conclusione, Tecnomatic è riuscita ad assicurare la cura dei dettagli che sposasse perfettamente la precisione e la rigorosità tipiche giapponesi, sviluppando e consegnando un progetto di riferimento per la produzione di tubi in plastica in Estremo Oriente.
La specializzazione delle applicazioni richiede la specializzazione delle tecnologie, possibile solo se si può contare su una vasta esperienza al servizio di molti settori. Quello che non manca a Bausano, che per la realizzazione di un tipo di tubi le cui prestazioni li rendono sempre più diffusi è in grado di proporre linee dedicate e all’avanguardia allo stesso tempo.
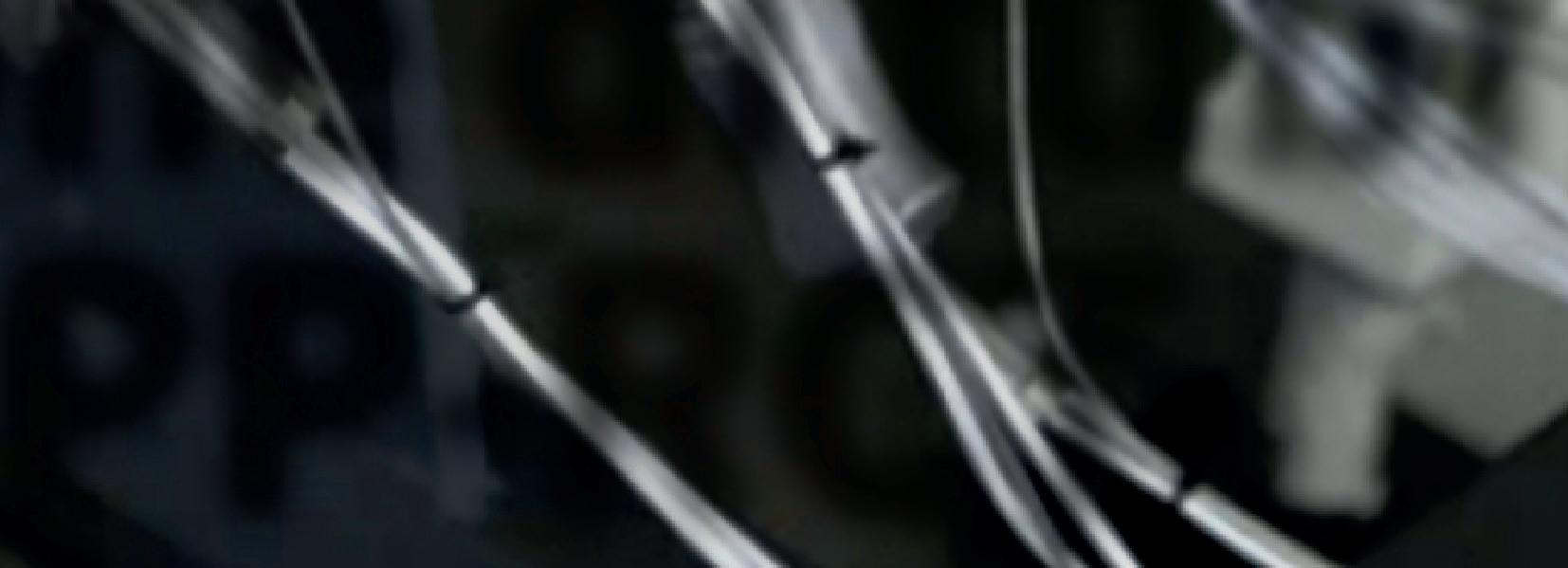

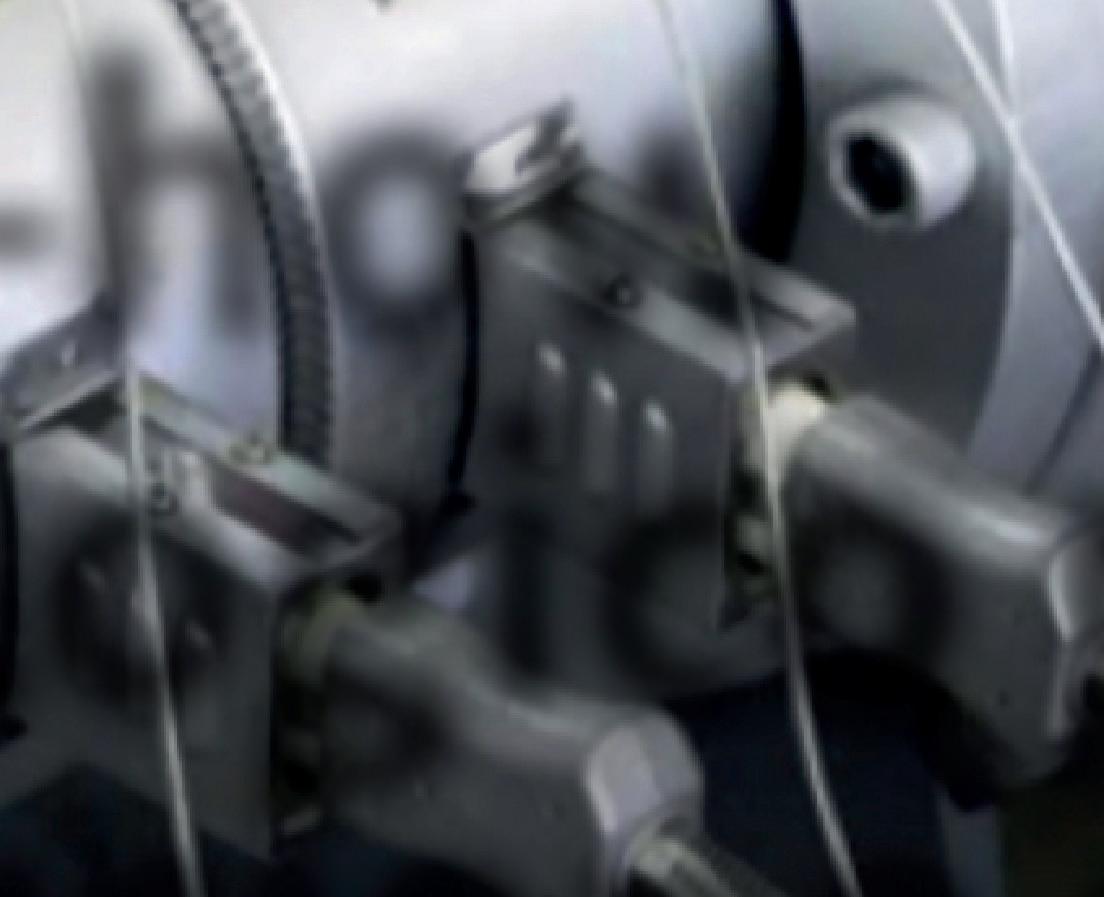
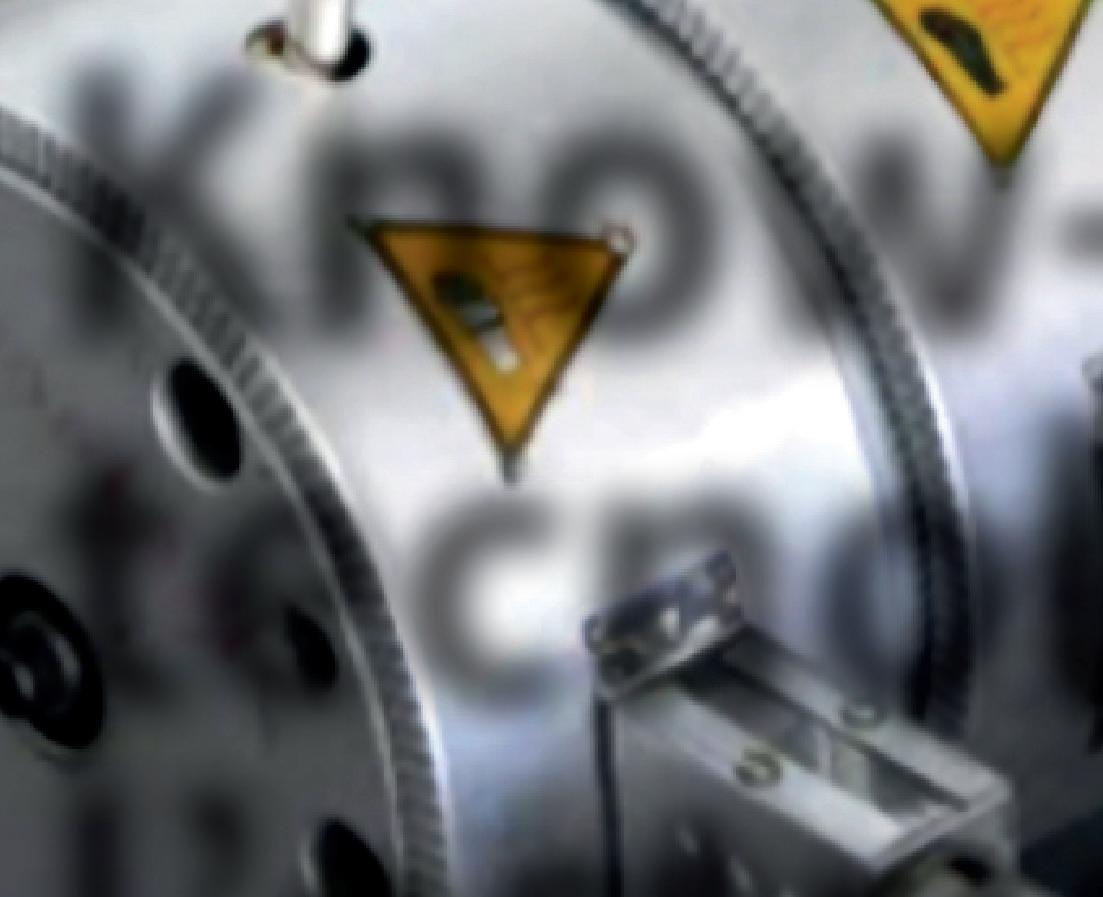

Itubi in PP-R (Random) e PP-RCT (Random Cristallinity Temperature), copolimeri di polipropilene, negli ultimi anni si sono affermati rapidamente nel mercato, grazie a proprietà chimiche e meccaniche uniche e ai relativi benefici che ne derivano in termini di prestazioni e basso impatto ambientale. Richiesti anche in configurazioni multistrato rinforzate con fibra di vetro, i tubi in PP-R trovano sempre più largo impiego in applicazioni che spaziano dall’ambito domestico a quello industriale: nella costruzione di sistemi di distribuzione di acqua calda e fredda e di depurazione dell’acqua, negli impianti di riscaldamento, nel trasporto di aria compressa e di fluidi chimici. In questi ambiti, Bausano, allo scopo di rispondere prontamente alla crescente domanda di diversi operatori, mette in campo una esperienza ultra-settantennale con lo sviluppo di linee di estrusione dedicate alla produzione di tale tipo di tubi.

Per il responsabile tecnico di Bausano, Massimiliano Fenili, alla base della diffusione dei tubi in PP-R si trova anzitutto il connubio tra le loro prestazioni elevate e i minori costi della materia prima, possibile però solo quando si è in grado di predisporre la tecnologia necessaria per sfruttare gli uni e ottenere le altre.
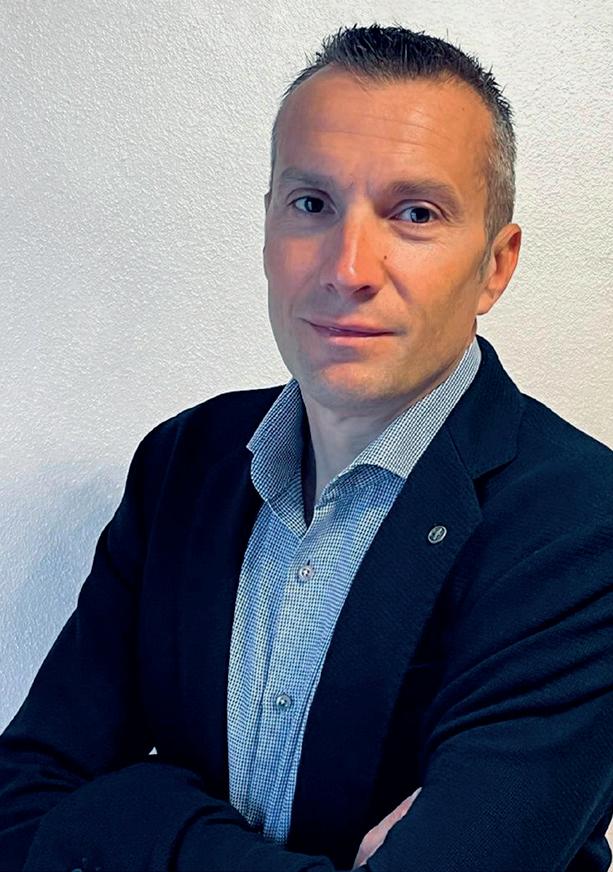
Caratteristiche dei tubi in PP-R
La bassa conducibilità termica è la prima caratteristica distintiva dei tubi in PP-R, a garanzia di un maggiore isolamento e, conseguentemente, di una riduzione della perdita o dell’incremento del calore, nel caso di trasferimento rispettivamente di fluidi caldi o freddi. I vantaggi che ne derivano consistono, pertanto, nella elevata efficienza energetica e nei minori costi di coibentazione. Una seconda caratteristica è rappresentata dalla resistenza, anche in condizioni ambientali mutevoli, in un ventaglio di temperatura da 20 a 95 °C, all’abrasione da particelle solide e a un’ampia gamma di liquidi, tra cui anche sostanze chimiche aggressive e soluzioni alcaline.
Grazie a queste caratteristiche i tubi in PP-R possono mantenere inalterate le loro funzionalità anche per più di cinquant’anni in molteplici situazioni d’impiego. Inoltre, la bassa rugosità interna si traduce in un minore coefficiente di attrito, contribuendo ulteriormente all’efficienza dei sistemi in cui vengono impiegati. Nel caso di tubi in PP-R multistrato, lo strato intermedio è costituito da un composito in fibra di vetro che ne incrementa ulteriormente la resistenza e ne limita la dilatazione termica. Tra le caratteristiche di questi tubi rientrano anche la salubrità, in quanto non rilasciano sostanze tossiche e sono meno soggetti a elettrolisi, e la leggerezza, che ne facilita l’installazione.
Realizzati in copolimeri di polipropilene, i tubi in PP-R e PP-RCT si sono affermati rapidamente grazie a un mix di proprietà chimiche e meccaniche uniche e ai relativi benefici che ne derivano, che, in configurazione mono e multistrato, li rendono adatti a svariate applicazioni domestiche e industriali.
Tubi in PP-R di elevata qualità
Le linee proposte da Bausano per la produzione di tubi in PPR, a seconda della produzione richiesta, presentano uno o più estrusori monovite con vite dal design speciale, che permette di raggiungere elevate prestazioni nel processo di lavorazione grazie a ottimali plastificazione della massa fusa e dispersione dei masterbatch, laddove impiegati. I banchi di calibrazione e di raffreddamento in acciaio inossidabile integrati nella linea garantiscono un efficace raffreddamento finalizzato al raggiungimento della misura del tubo, cui al contempo viene conferita una superficie impeccabile.
Completano le linee il sistema di traino, che esercita una trazione continua e priva di vibrazioni, l’unità di taglio e il fasciatore per l’imballaggio, che contribuisce all’elevato grado di automazione dell’impianto. Quest’ultimo si configura, infatti, come un sistema automatico, in grado di formare fasci del numero prestabilito di tubi, da 16 a 125 mm di diametro e da 1 a 6 m di lunghezza.
Infine, grazie al sistema Digital Extruder Control 4.0 a bordo macchina è possibile monitorare costantemente la linea, per controllare i diversi stadi di processo e analizzare i dati raccolti.
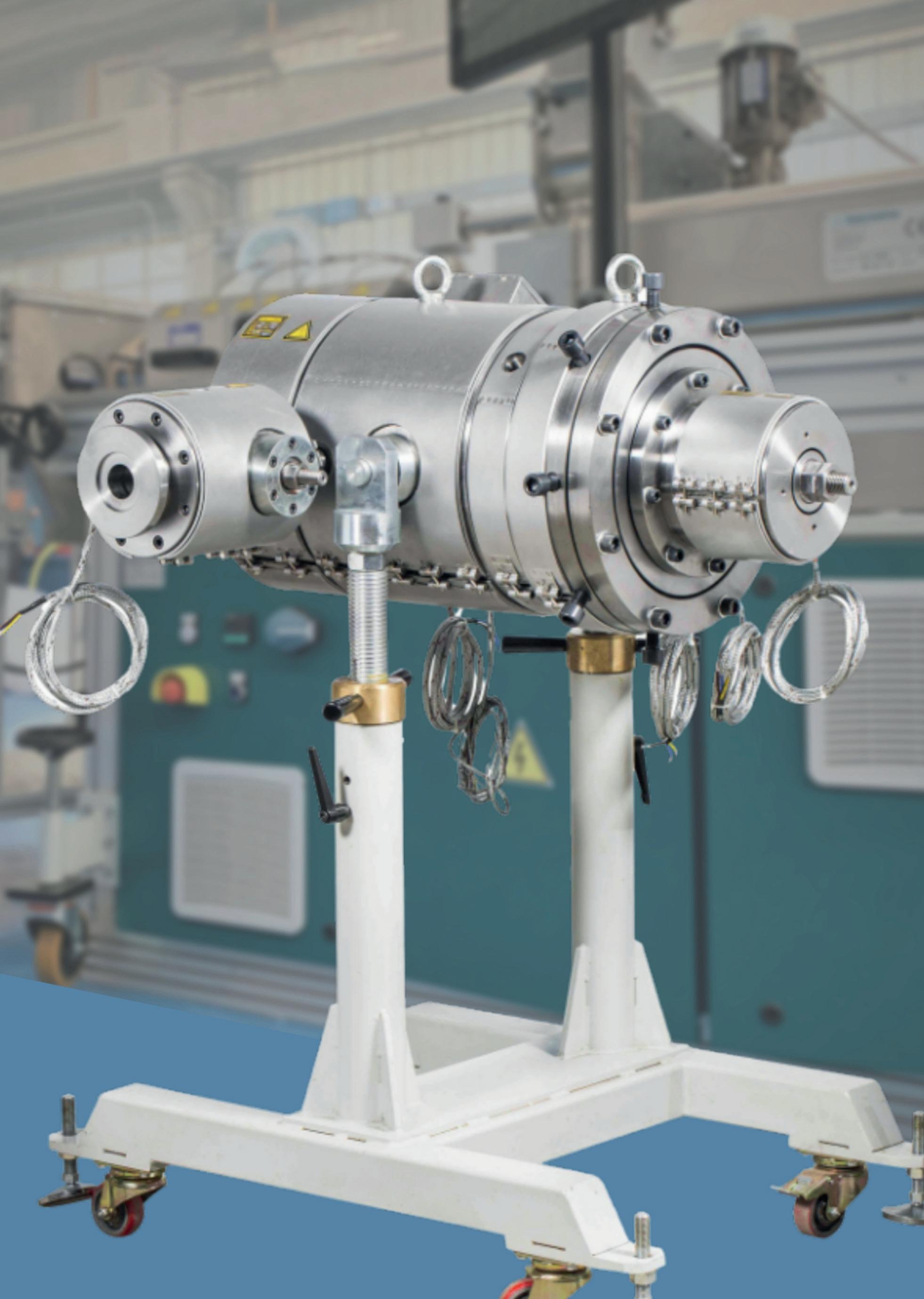
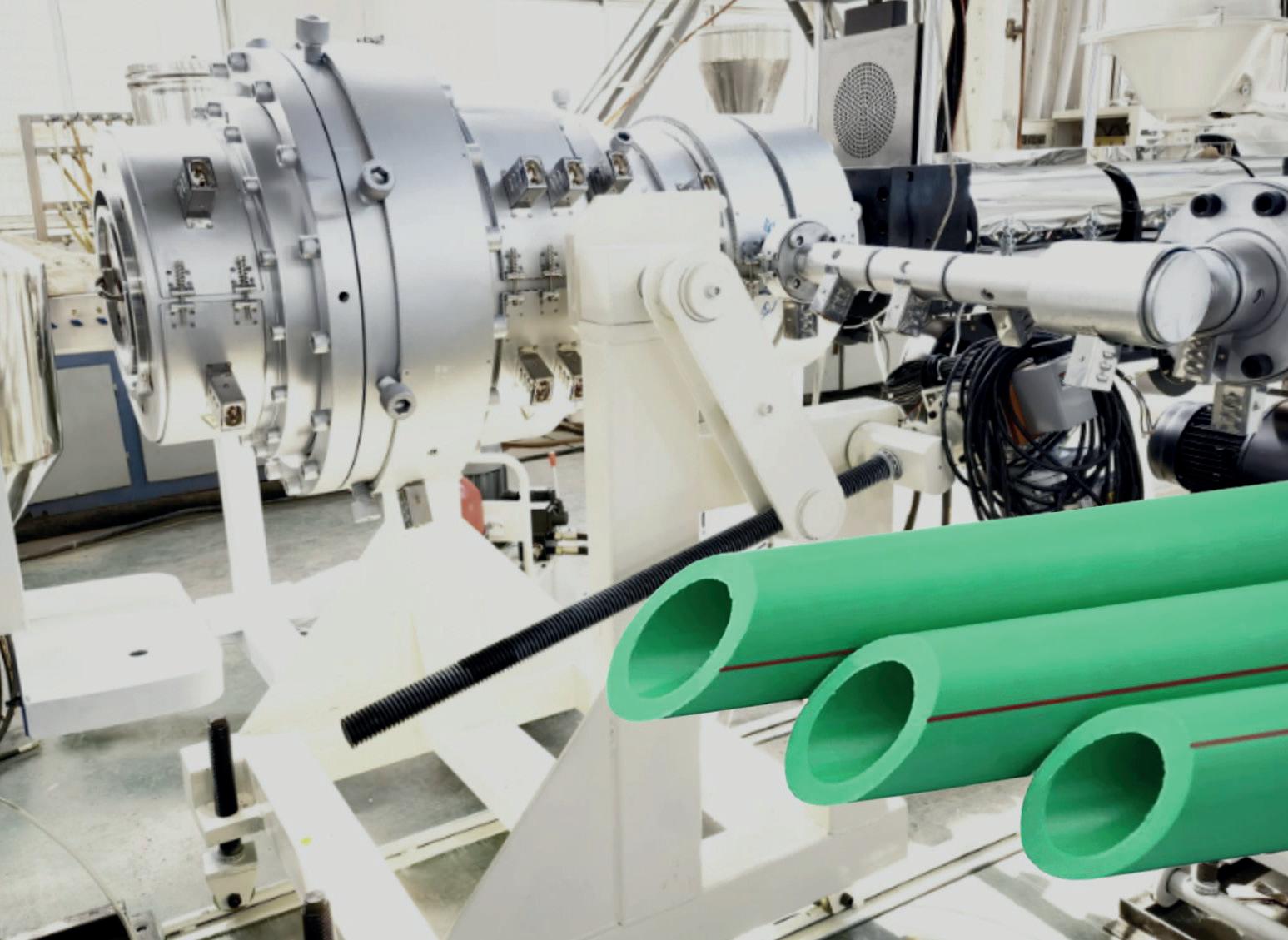
Dosaggio gravimetrico al servizio di alti standard produttivi
Per quanto riguarda il sistema di alimentazione, l’adozione di una tecnologia avanzata ed estremamente precisa, come il dosatore gravimetrico, si traduce in importanti vantaggi e rappresenta il presupposto per una produzione costante, riducendo l’utilizzo di quantità eccessive di materiale e mantenendo inalterati diametro e spessore. In particolare, questo sistema si basa su una cella di carico in grado di misurare in tempo reale il peso del materiale processato dall’estrusore, inviando continui feedback al Digital Extruder Control 4.0 (PLC), il quale calcola e determina la velocità di rotazione della vite dell’estrusore in funzione della massa rilevata. A sua volta, la velocità di estrusione viene adattata in base a questo parametro, mantenendo costante il rapporto peso/metro del tubo, particolarmente importante laddove si verifichino eventuali variazioni a monte del processo di lavorazione.
In questo modo, le linee del costruttore consentono di estrudere ogni metro di tubo nel rispetto di specifiche predefinite. “Il connubio tra superiori prestazioni e minori costi della materia prima sta conducendo a un crescente impiego dei tubi in PP-R, in sostituzione delle meno performanti tubazioni in metallo”, ha spiegato Massimiliano Fenili, responsabile tecnico di Bausano.
“Per questo motivo, in Bausano da tempo ci stiamo specializzando nella progettazione di linee di estrusione dedicate, che possano soddisfare le richieste più sfidanti dei nostri clienti. L’obiettivo che teniamo costantemente a mente è infatti quello di offrire una soluzione completa, mirata a garantire i massimi risultati e studiata nei minimi dettagli per processare in modo ottimale il materiale prescelto, con particolare riguardo al comportamento reologico di quest’ultimo. L’inserimento del dosatore gravimetrico che fornisce interessanti dati sulla quantità di plastica processata, abbinata a un’automazione del downstream come il fasciatore per barre, testimonia il nostro impegno nel personalizzare la nostra tecnologia in funzione delle specifiche istanze di produzione”.
Conducibilità termica e resistenza sono le due caratteristiche principali che stanno assicurando ai tubi in PP-R un sempre più largo impiego.
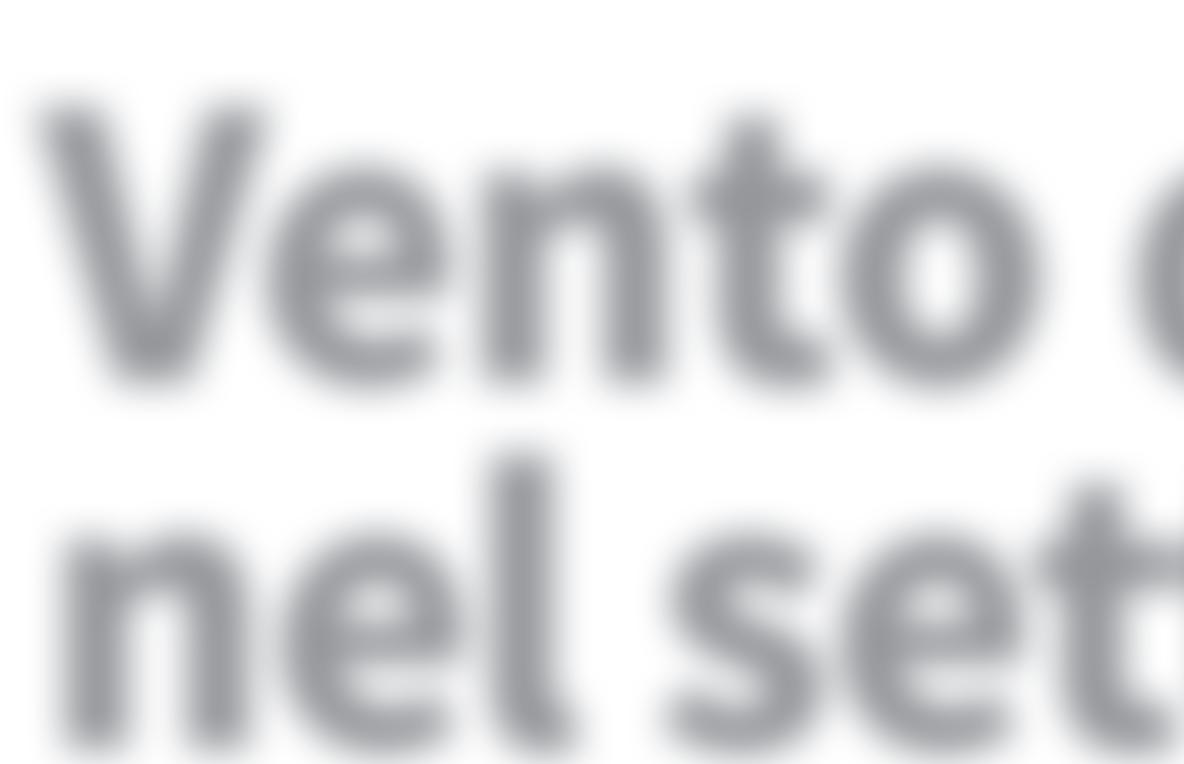

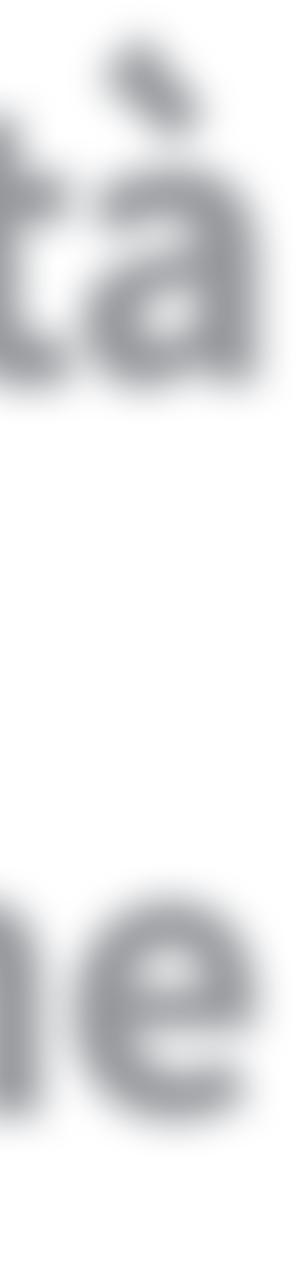
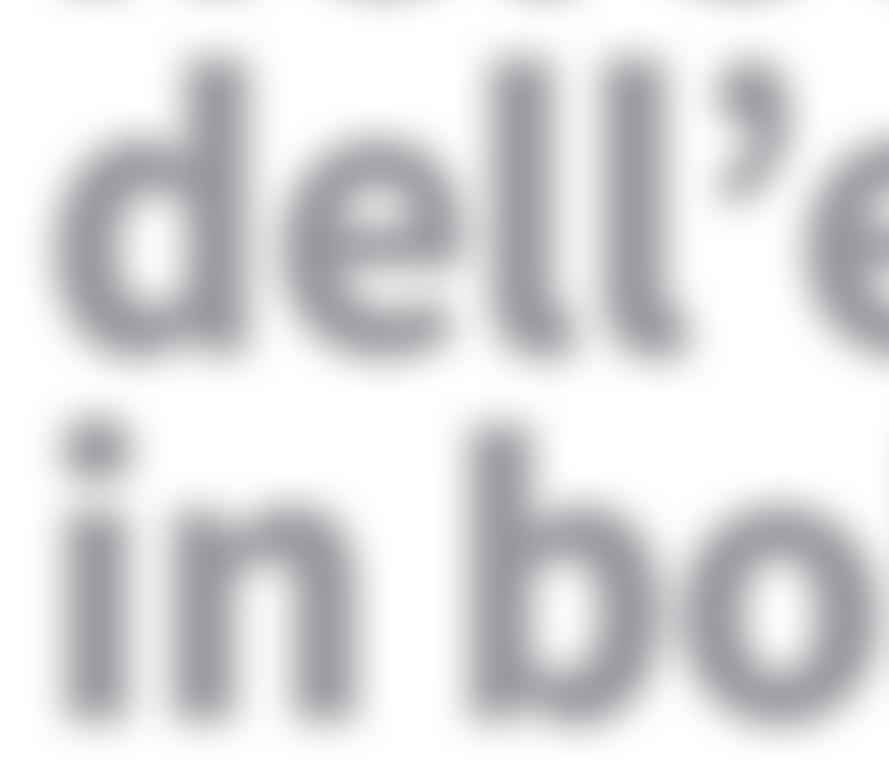




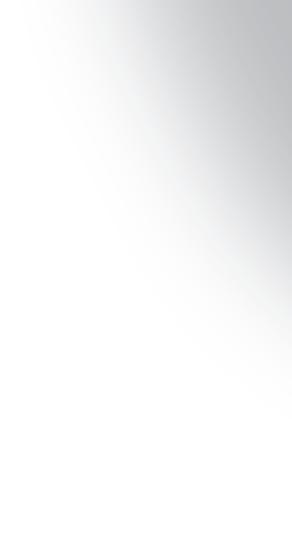





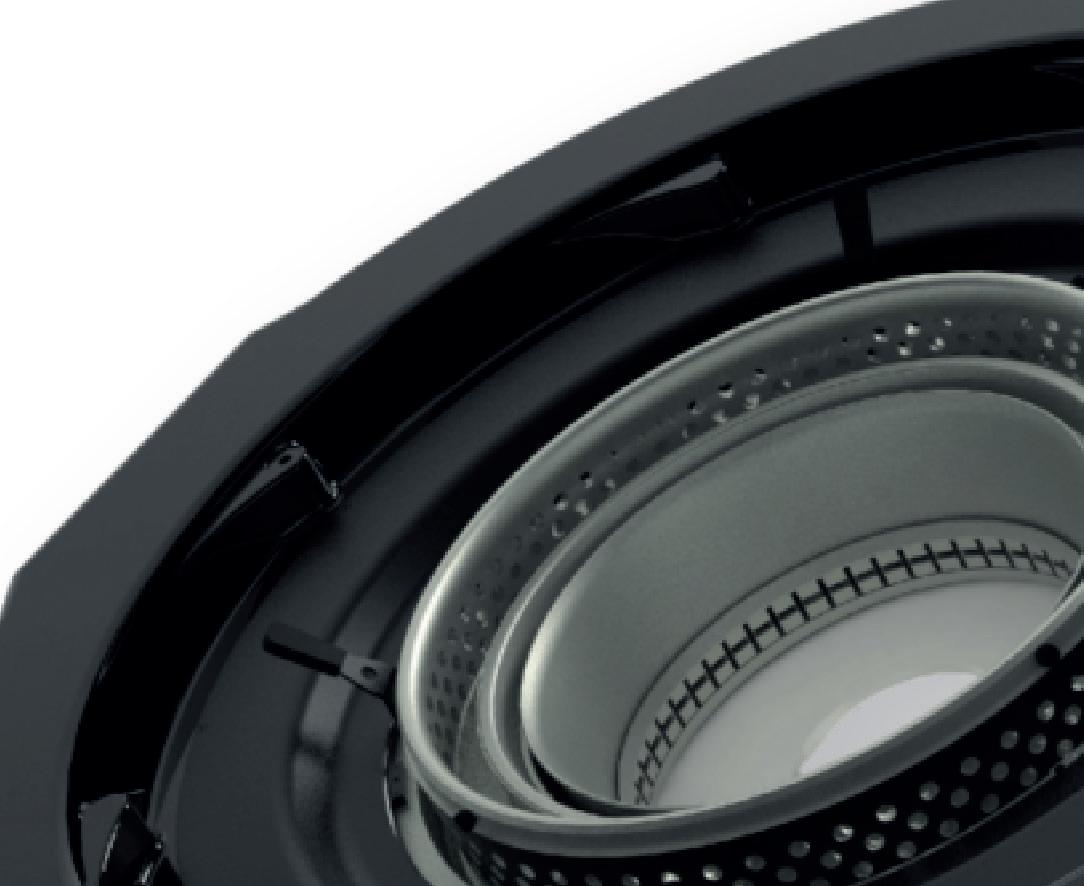

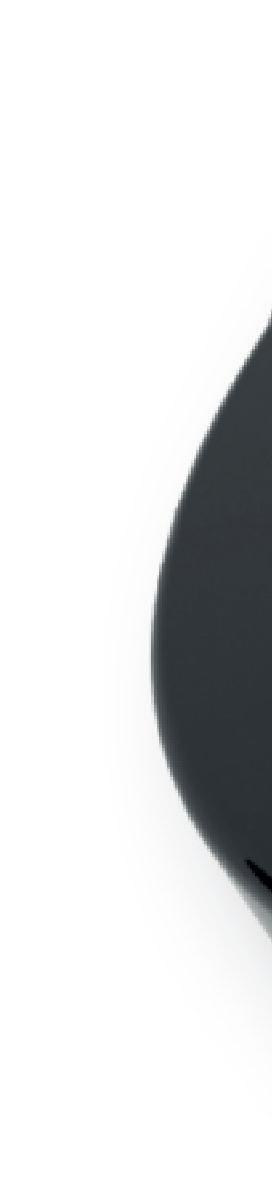
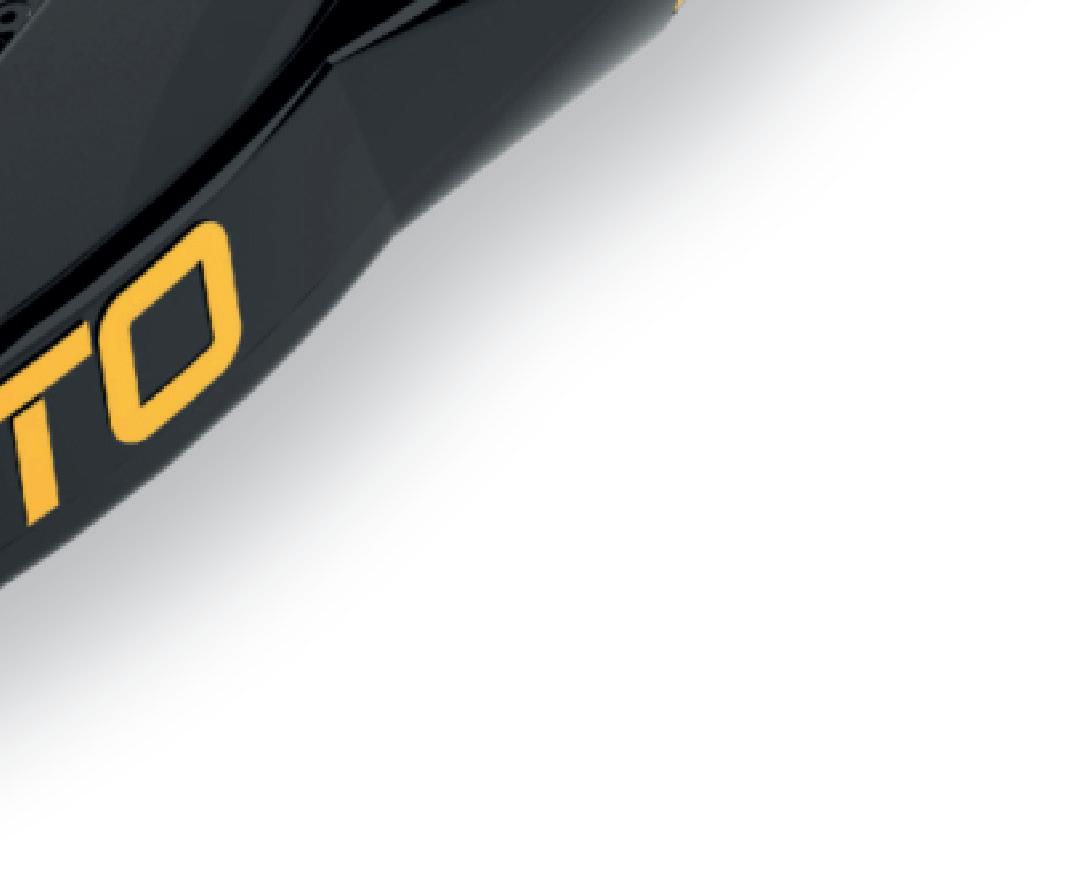
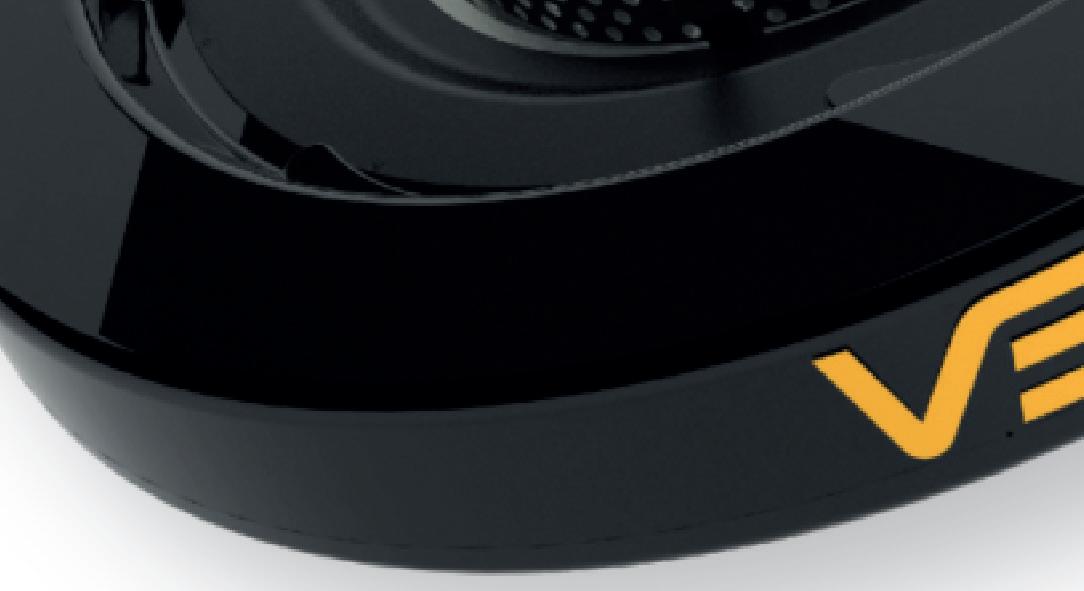
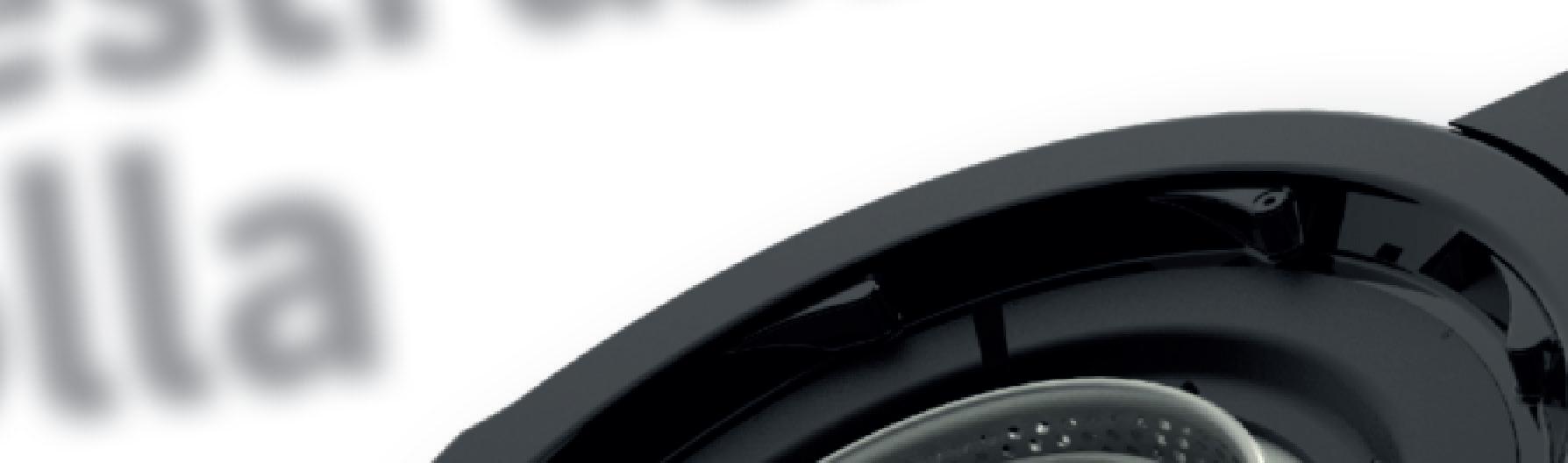
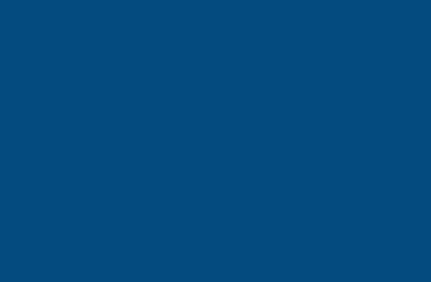
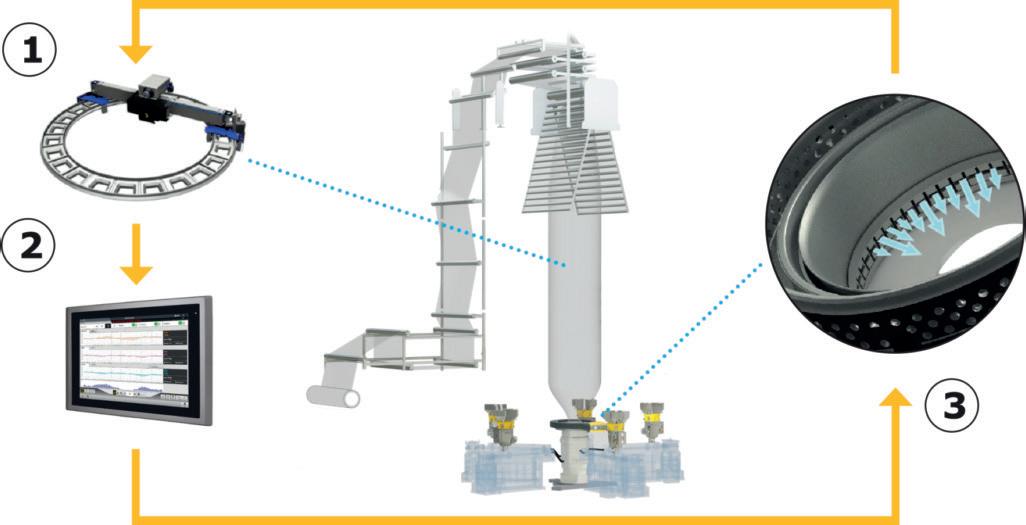
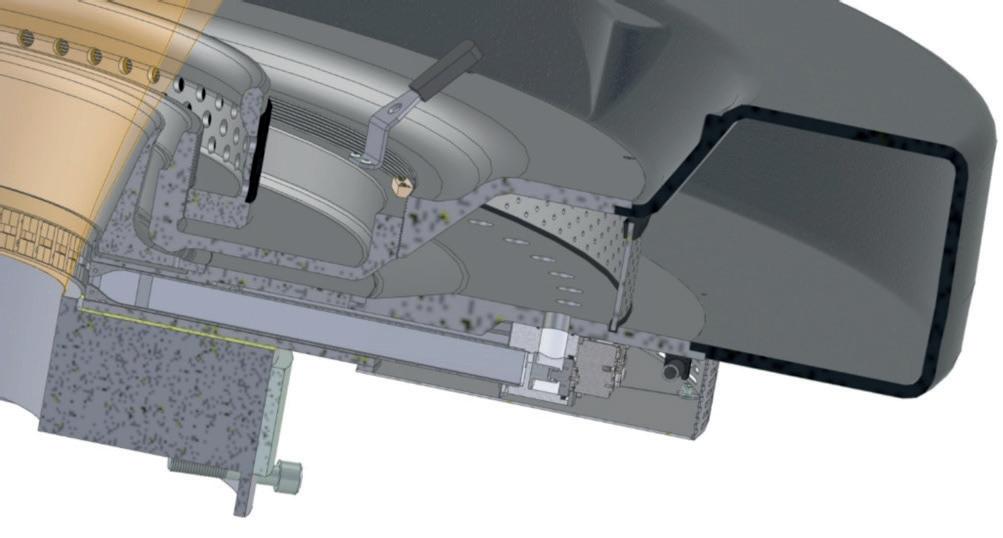
Per promuovere la cultura del lavoro e stimolare la creatività dei dipendenti, Barbara Ulcelli, amministratore delegato di IMG, ha invitato lo scultore Stefano Bombardieri a esporre nei reparti produttivi e nel cortile dell’azienda alcune delle sue opere incentrate sul rapporto tra realtà e finzione, tra vita e immaginazione, tra uomo e natura. Ne è nata una insolita e curiosa, ma, certamente, interessante mostra sperimentale.
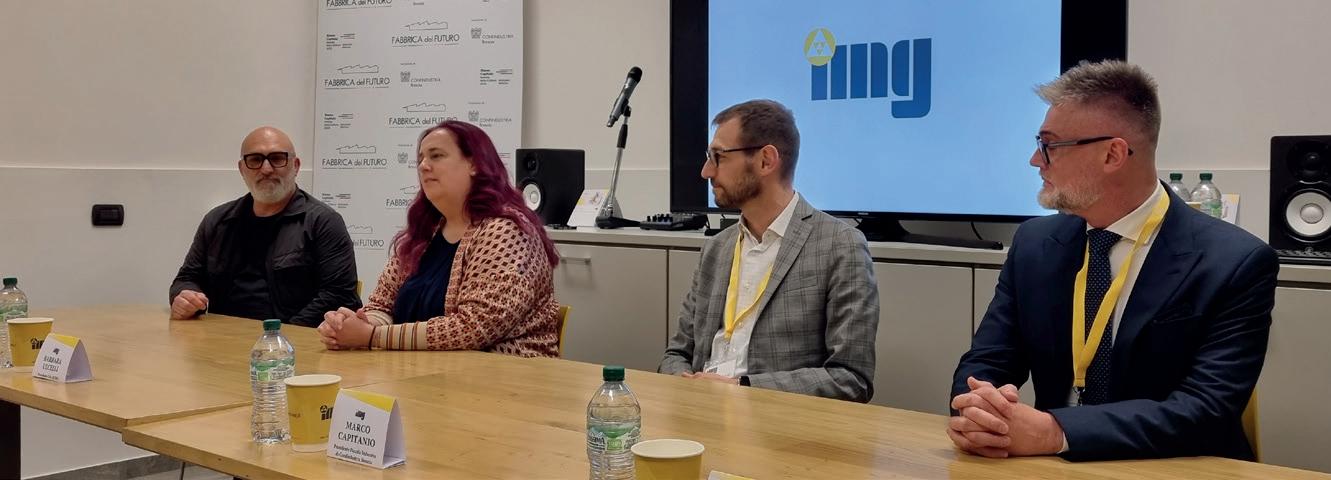
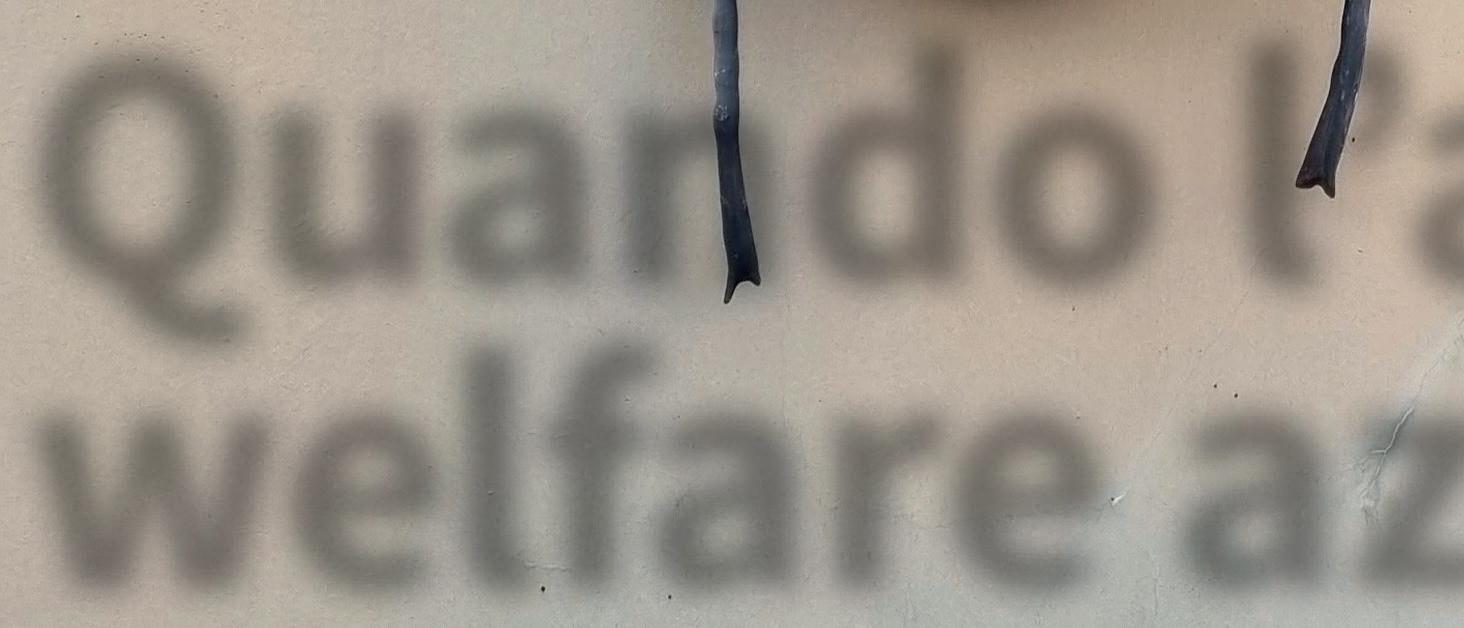
Barbara Ulcelli, seconda da sinistra, durante la presentazione della mostra di opere d’arte esposte in IMG dal 21 aprile al 20 maggio; alla sua destra lo scultore Stefano

Bombardieri, alla sua sinistra, Marco Capitanio, Confindustria Brescia, e Stefano Sala, sindaco di Capriano del Colle.
“Personalmente credo che la cultura del lavoro sia un valore fondante dello sviluppo civile, e che l’impresa sia un luogo di osservazione privilegiato dal quale poter vedere progredire la nostra società. Personalmente credo che già di suo l’ambiente di lavoro sia sinonimo di bellezza e che lo spendersi nel contaminarlo con più e più forme d’arte lo renda ancora più gradevole”. Ha esordito con queste parole Barbara Ulcelli, amministratore delegato di IMG, il 20 aprile scorso inaugurando l’esposizione in azienda di sette grandi opere dell’artista bresciano Stefano Bombardieri, alcune delle quali visibili anche dal- la strada, rimasta aperta per dipendenti e pubblico esterno dal 21 aprile al 20 maggio. L’iniziativa ha rappresentato la prima tappa di un più ampio progetto di contaminazione culturale tra imprenditoria e mondo del lavoro e produzione artistica denominato “L’arte ImPressa: che bello lavorare”, come ha spiegato la stessa Barbara Ulcelli, che sta lavorando ad altre due mostre in programma a ottobre e a dicembre e che si inserisce nel programma “Fabbrica del Futuro” elaborato da Piccola Industria di Confindustria Brescia in concomitanza con “Bergamo Brescia Capitale italiana della Cultura 2023”.
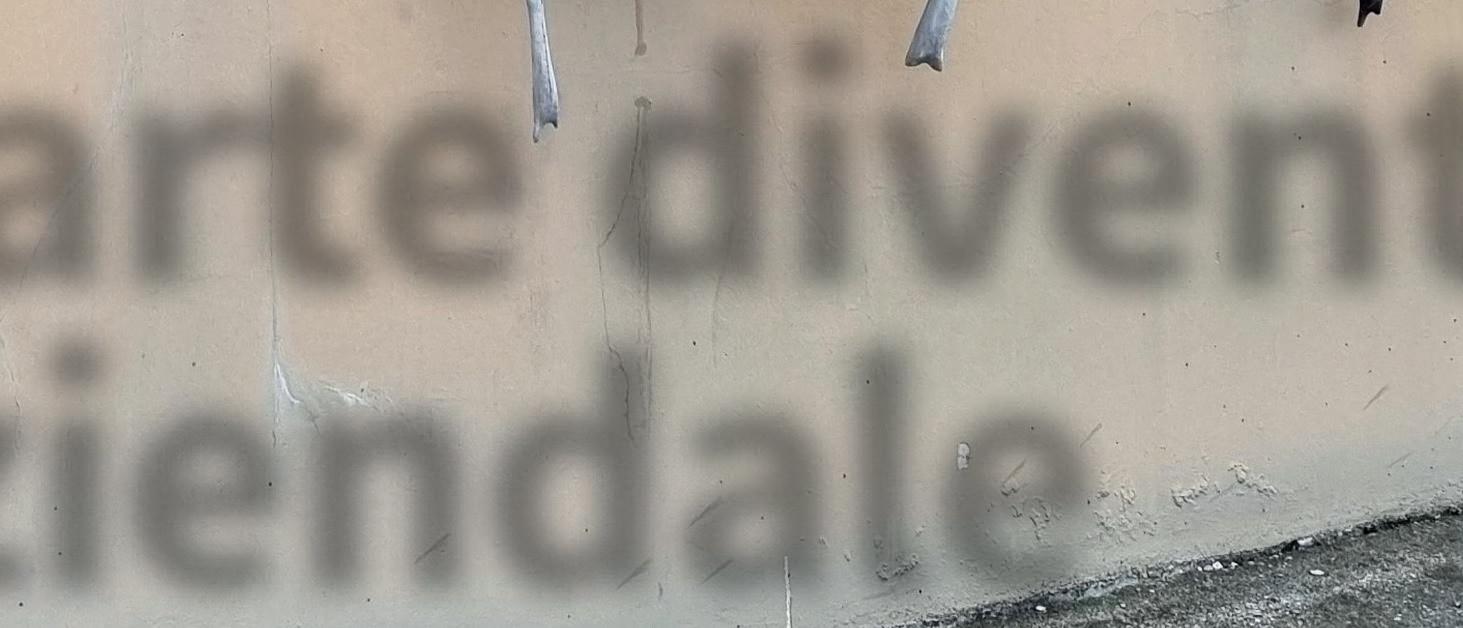
Il territorio come riferimento
“Le aziende come IMG sono aperte al territorio. Le aziende come IMG hanno bisogno di farsi conoscere soprattutto dalle nuove generazioni. Dato poi che Capriano del Colle ci ha dato gran parte delle maestranze, questa mostra di opere d’arte noi l’abbiamo intesa anche in chiave di restituzione morale verso il territorio che ci ospita”, ha dichiarato Barbara Ulcelli prima di dare spazio ai suoi ospiti, Marco Capitanio, presidente di Piccola Industria di Confindustria Brescia, e Stefano Sala, sindaco di Capriano del Colle, oltre all’artista Stefano Bombardieri.
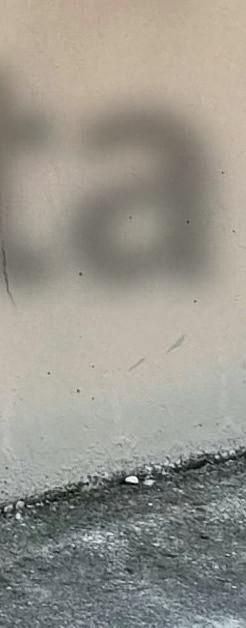
“È importante che le aziende del territorio si aprano, che comunichino, perché spesso e volentieri ci sono eccellenze sul territorio che noi stessi non conosciamo. Ringrazio quindi Barbara, che è pure collega in associazione, non solo per aver aperto IMG al territorio, ma anche per averlo fatto con questa squisita connotazione culturale”, ha commentato Marco Capitanio. “Grazie a Barbara Ulcelli il nostro Palazzo Comunale è ora impreziosito di una delle opere di Stefano Bombardieri che la cittadinanza può ammirare. Si tratta dell’opera “Bagaglio Rinoceronte” dove l’enorme animale è raffigurato catturato e legato, tolto dal suo habitat e trasportato come un souvenir, a ricordarci che la mancanza di umanità è una sorta d’ineludibile spada di Damocle”, ha spiegato Stefano Sala.
Riprendendo la parola, Barbara Ulcelli ha sottolineato ancora il concetto che il territorio è un riferimento imprescindibile nelle azioni d’impresa e che “è vitale evitare il depauperamento industriale e culturale delle nostre aree periferiche, la cui attività è strategica per le filiere manifatturiere di Brescia e provincia”.
Tra Bergamo e Brescia, infatti, si concentra il principale distretto italiano della gomma, quello del Sebino, dove operano centinaia di aziende ad alta tecnologia che coprono tutte le fasi della filiera: dalla produzione di mescole allo stampaggio o estrusione di articoli finiti, dalla realizzazione di stampi alla progettazione e costruzione di macchinari per farlo. In questo contesto si distingue IMG che, nella sua sede di Capriano al Colle, progetta e realizza la “regina” delle macchine per il settore gomma: la pressa a iniezione.
Opere grandi per generare cortocircuiti inaspettati
“Quando mi immagino una scultura, mi immagino anche il contesto in cui essa deve vivere ed esprimersi. E devo dire che la fabbrica è un contesto che trovo congeniale. Qui c’è una sorta di cortocircuito naturale. Entrare in un’azienda e trovarsi di fronte a un rinoceronte o a un gorilla quantomeno di dimensioni reali non è certo la cosa più normale di questo mondo. Ed è bello che l’industria si apra all’inaspettato”, ha raccontato Stefano Bombardieri per far intendere i motivi per i quali ritiene che, appunto, lo stabilimento sia l’habitat naturale per le sue opere. A ben guardare anche i materiali usati dall’artista sono affini, se non sovrapponibili, a quelli per la cui lavorazione le macchine di IMG vengono costruite. Va da sé che si parla in questo caso di plastica e di gomma.
Lo scultore utilizza principalmente due tecniche per realizzare le proprie opere, sempre in equilibrio tra saper fare artigianale e tecnologia industriale, che sembra un tratto tipico del suo lavoro. In una il polistirene espanso serve per modellare anime (o calchi) ricoperte di poliuretano, come nel caso dell’opera “Testa di Gorilla”. Nell’altra “fogli” di vetroresina, ossia poliestere rinforzato con fibra di vetro, comunemente utilizzati in ambito industriale per realizzare scafi nautici o tettucci automobilistici, sono adottati per realizzare figure di geometrie complesse o dimensioni mastodontiche, come per l’opera “Grande Testa di Rinoceronte” (uno degli animali iconici di Bombardieri). Capita anche che il modello sia realizzato nello stesso modo e che con esso venga ottenuto un calco in gomma siliconica, come per l’opera “Struzzo Rubik”, una variante che l’artista utilizza quando la scultura originale serve per replicare copie.
Stefano Bombardieri accanto alla scultura gigante “Grande Testa di Rinoceronte” modellata utilizzando fogli di poliestere rinforzato con fibre di vetro, con cui in ambito industriale vengono normalmente realizzati scafi nautici o tettucci automobilistici.

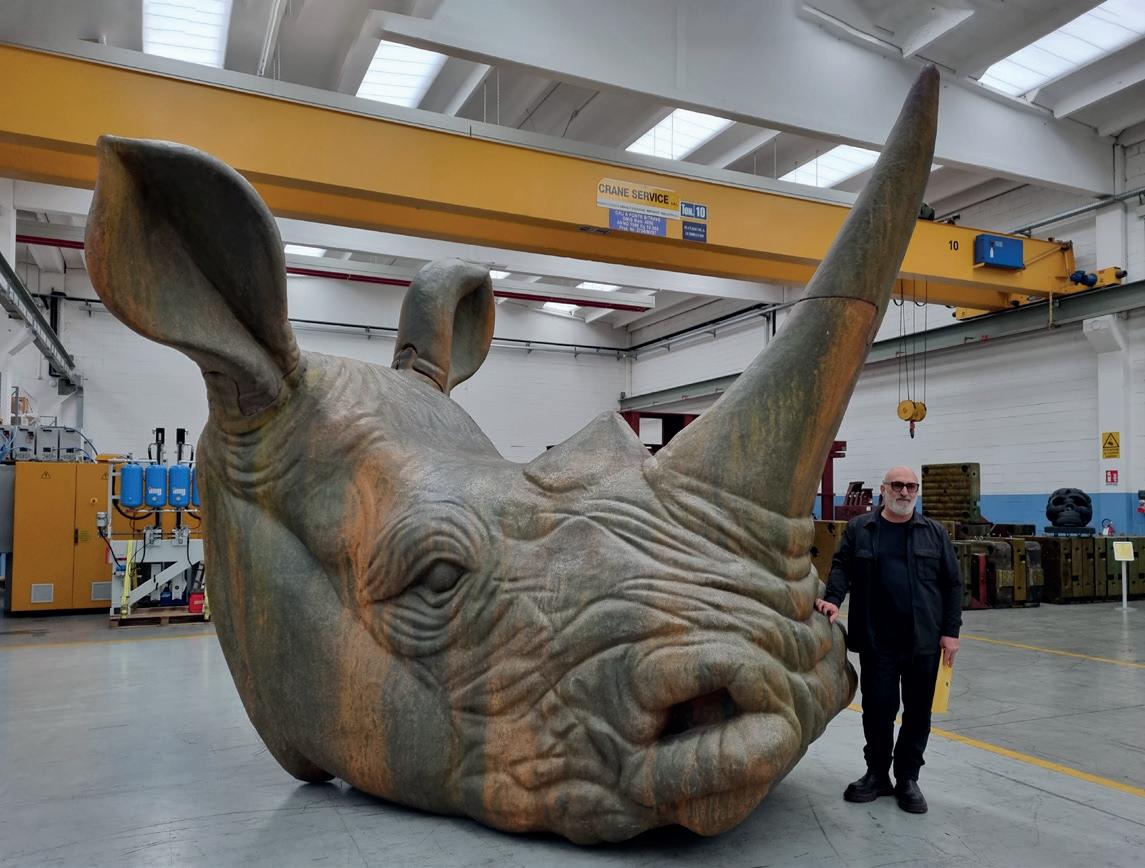
“La scelta di questi materiali polimerici è sì legata al fatto che sono molto meno costosi rispetto al bronzo o al marno, ma anche al fatto che fin dall’inizio ho voluto fare solo opere che si potessero trasportare a mano. Considerando poi che le opere di grandi dimensioni sono quelle che mi danno più soddisfazione, il loro trasferimento era un fattore niente affatto banale”, ha aggiunto Stefano Bombardieri.
Una scelta ardimentosa
IMG da tempo si pone il problema di come i collaboratori si sentano sul posto di lavoro e l’idea di portare l’arte e la bellezza in azienda è da tempo un suo tratto caratteristico: nei suoi ambienti di lavoro, reparti produttivi compresi, sono già esposte stabilmente diverse opere di vari artisti. Si tratta di una sensibilità che passa attraverso numerose azioni, dalla formazione all’inserimento di personale giovane anche nel “middle management”. “Sostenibilità non è sinonimo solo di attenzione ecologica”, ha spiegato ancora Barbara Ulcelli, “sottintende anche una profonda sensibilità nei confronti del benessere sociale, dai dipendenti fino alla comunità in cui un’azienda è inserita. Fare impresa oggi significa anche stimolare riflessioni sui temi attuali, offrire opportunità di crescita, lavorativa e personale. Un’azienda si deve porre come incubatrice di talenti e di opportunità”. Un’indagine pubblicata sulla rivista sta- tunitense d’economia Forbes spiega che il 78% di 800 dipendenti di aziende americane interpellati ha dichiarato che la presenza di una qualche forma d’arte nell’ambiente di lavoro riduce i momenti di stress. Una ricerca condotta dall’Università di psicologia di Exeter rileva che i dipendenti inglesi sono fino al 32% più produttivi quando nei loro ambienti lavorativi ci sono opere d’arte. Sarebbe quindi lecito dedurre che il binomio “arte-luoghi di lavoro” risulti (quasi) ovvio, eppure non tutte le aziende espongono opere nei loro uffici o nei loro reparti. L’impatto dell’arte sulle condizioni lavorative è tuttora sottovalutato dai più. A fronte di tali considerazioni, quindi, la scelta di Barbara Ulcelli può essere considerata ardimentosa e riassunta in conclusione prendendo a prestito le parole del fisico tedesco Erwin Schrödinger (1887-1961), uno dei padri della meccanica quantistica, secondo cui “il nostro compito non è vedere quello che gli altri non hanno ancora visto, ma è pensare quello che gli altri non hanno ancora pensato in merito a ciò che tutti vedono”.
Lo “Struzzo Rubik” esposto in un reparto di IMG rappresenta il connubio perfetto tra macchine e attrezzature industriali e opera d’arte.
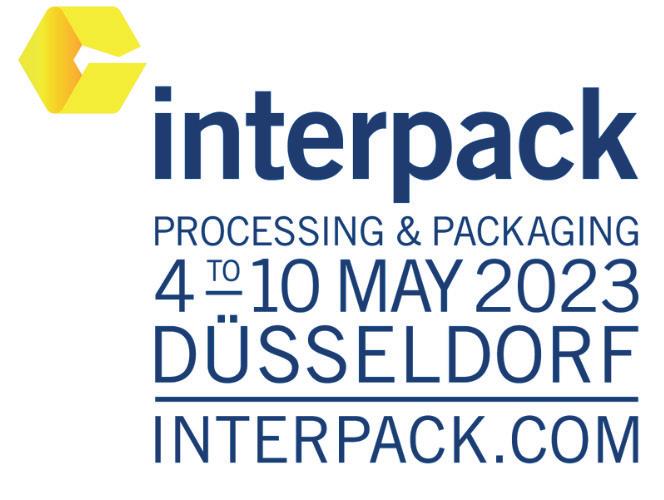
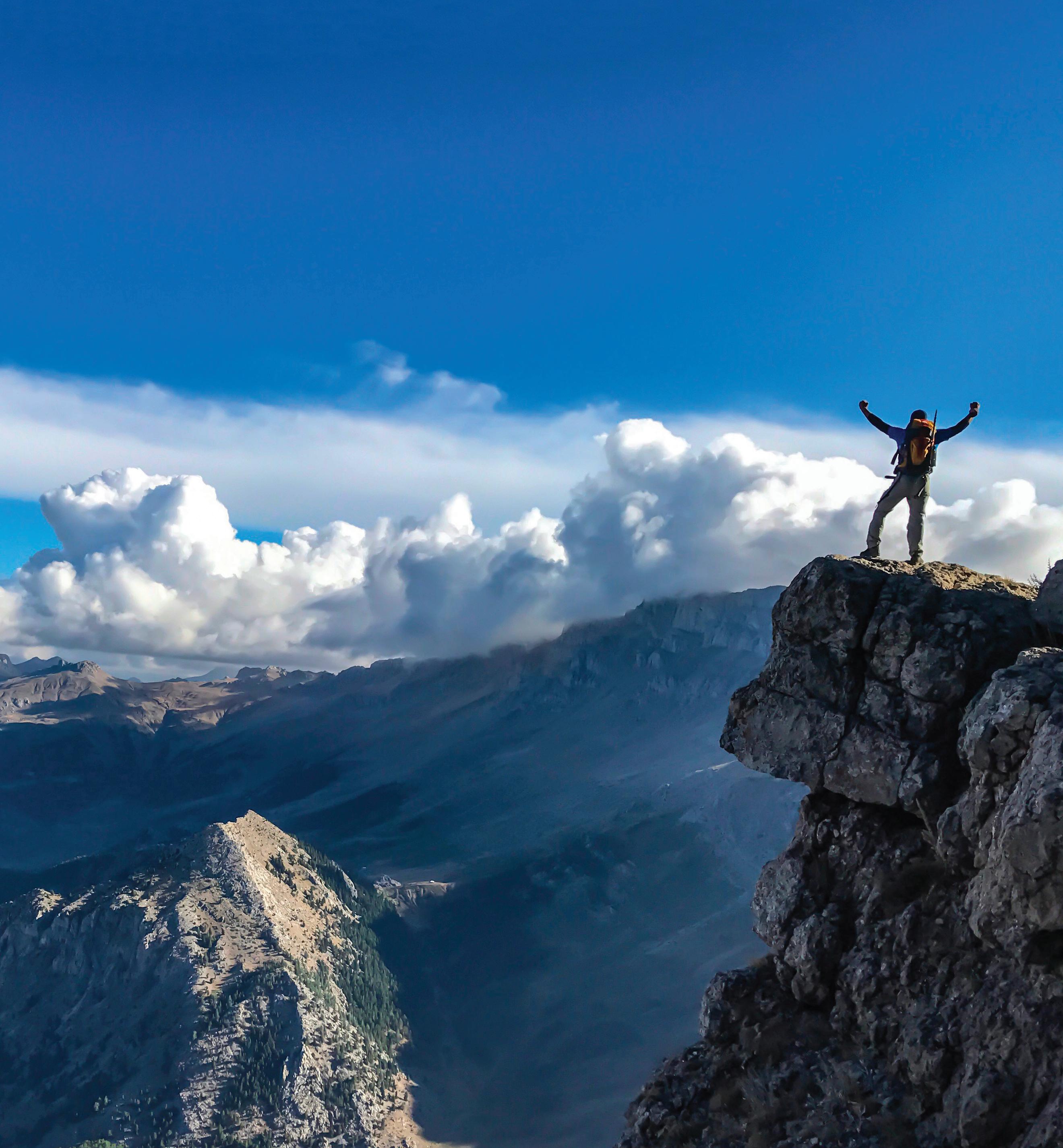
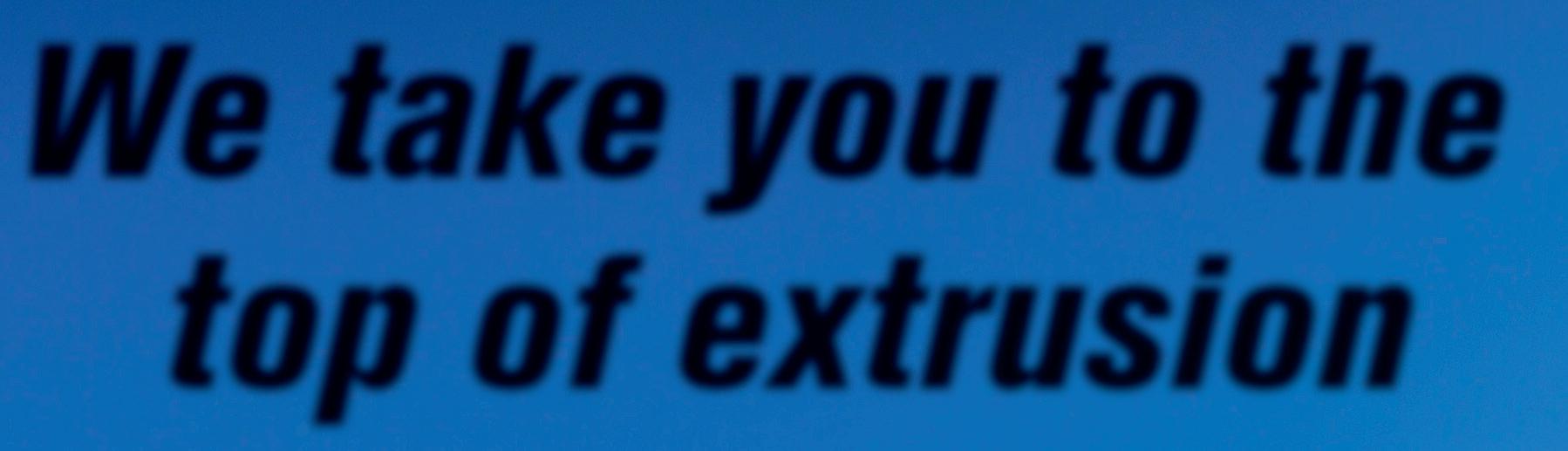
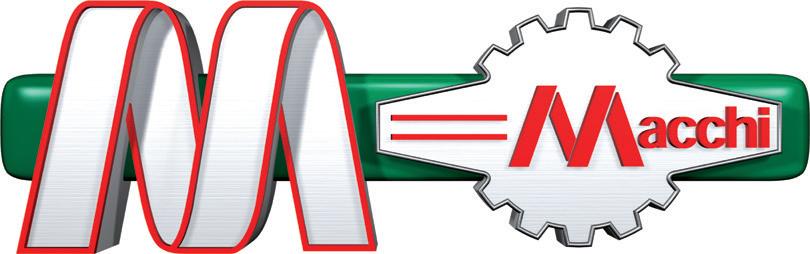
Con 145 anni di esperienza nella progettazione e realizzazione di impianti industriali, Rodolfo Comerio è un primario costruttore di impianti per la lavorazione gomma e plastica che propone tecnologia all’avanguardia e innovazione, i cui elevati standard qualitativi si riflettono anche nella scelta dei componenti: compresi i giunti rotanti, per i quali l’azienda si affida a Johnson-Fluiten.
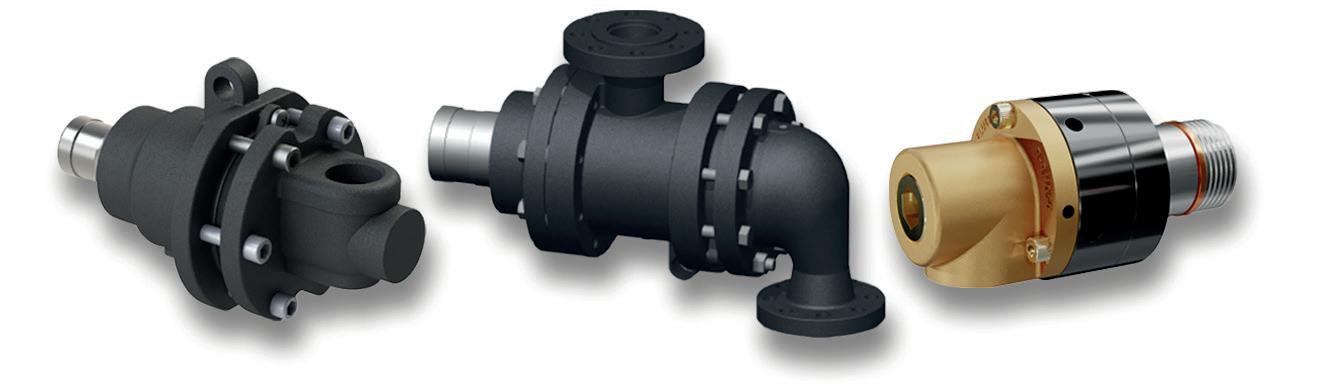
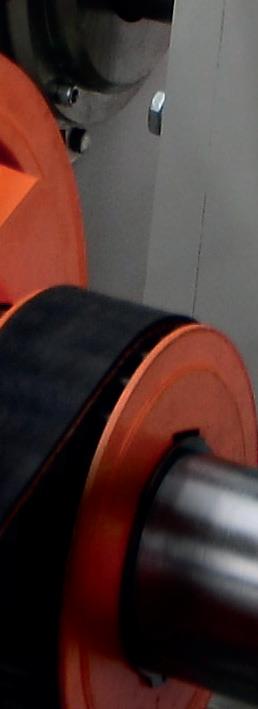
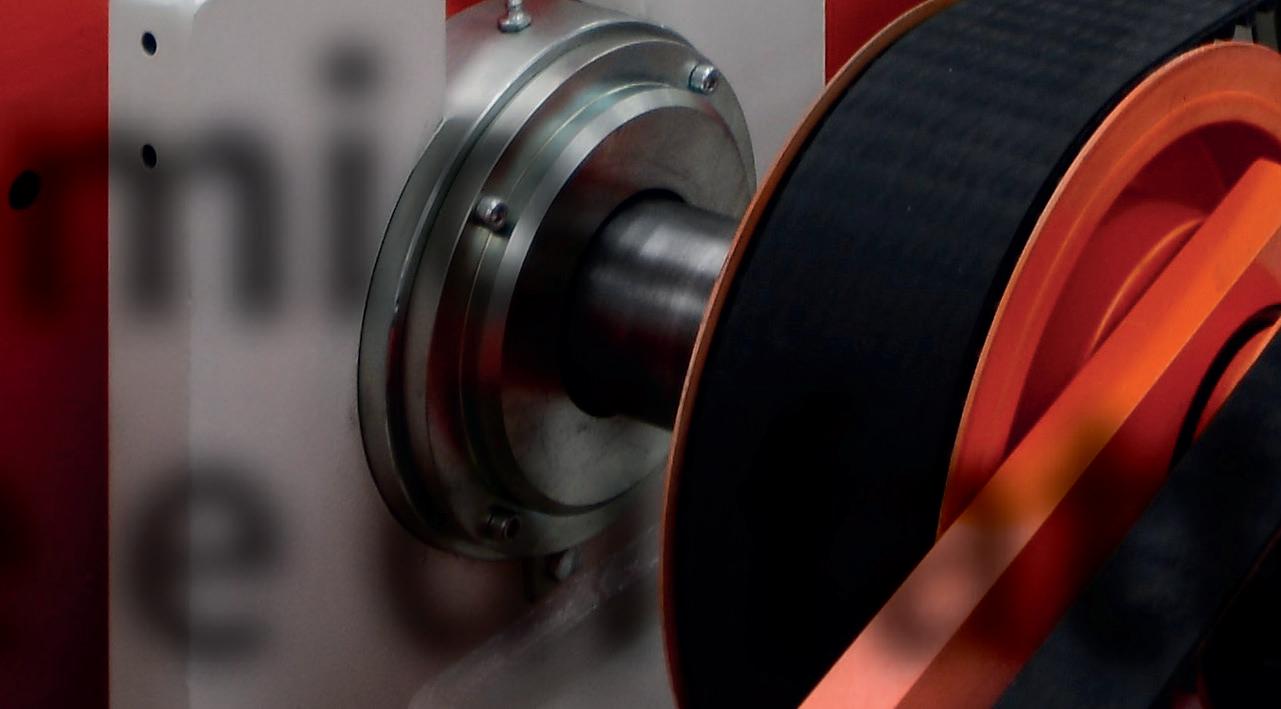
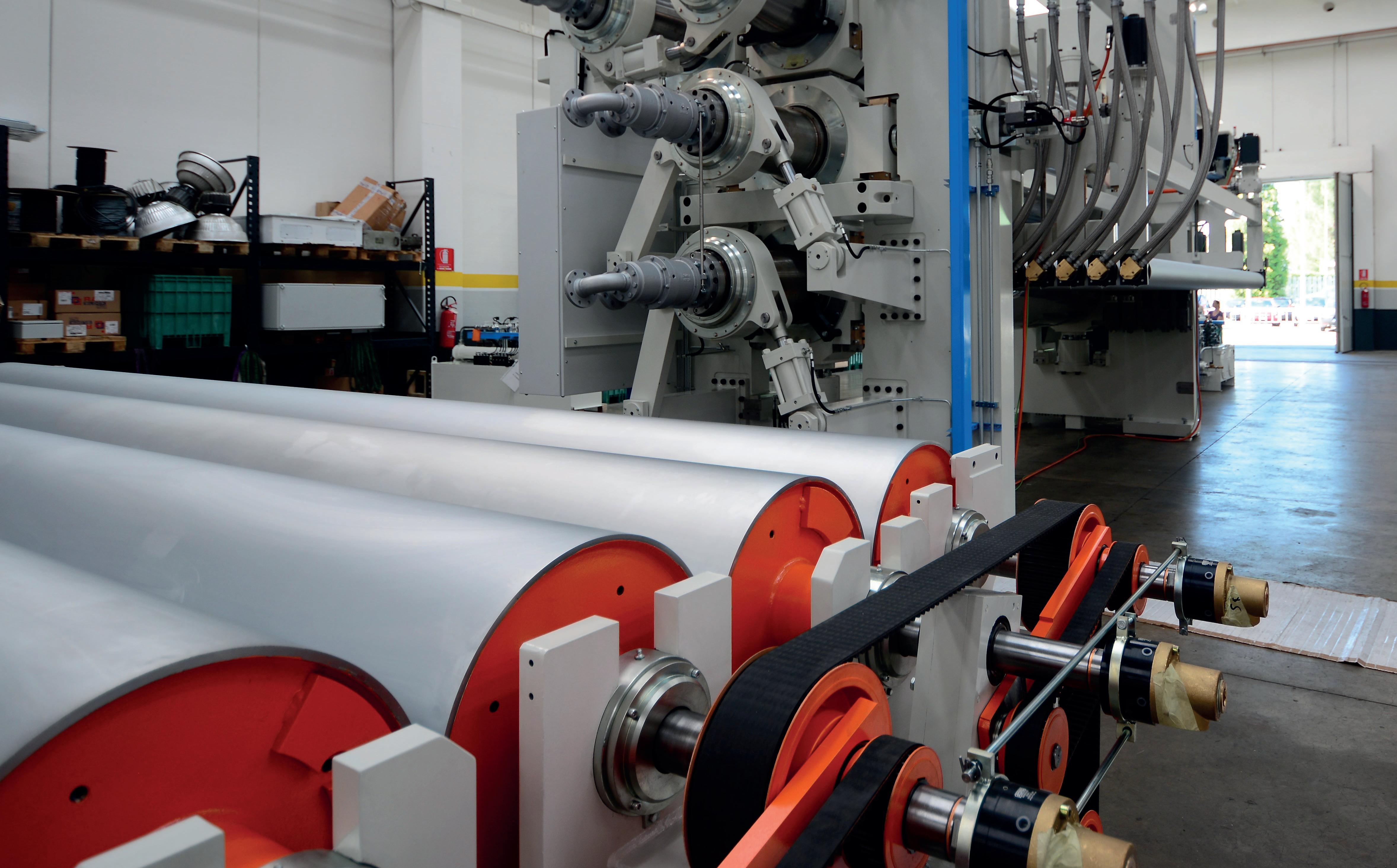
Fondata nel 1878 a attiva nella costruzione di impianti per la calandratura e per l’accoppiamento e la goffratura di foglie termoplastiche e in gomma, Rodolfo Comerio è un’azienda di livello mondiale al passo con l’evolversi delle esigenze tecnologiche contemporanee che negli ultimi anni si è marcatamente indirizzata verso lo sviluppo di innovazioni di processo finalizzate a conferire ai propri prodotti, e a quelli degli utilizzatori di questi ultimi, caratteristiche peculiari. Indirizzo che si riflette anche nella scelta dei componenti installati sulle proprie macchine, come, per esempio, i giunti rotanti, per la fornitura dei quali l’azienda si affida a Johnson-fluiten.

Un sodalizio consolidato Essere conosciuti e, ancor più, apprezzati in tutto il mondo significa aver ottenuto e dover mantenere elevati standard di consapevolezza e reputazione del marchio, da cui deriva la necessità di dover esercitare uno stretto controllo sulla qualità dei componenti inseriti nei propri macchinari. Per questo motivo nella scelta dei giunti rotanti l’azienda si è orientata sull’offerta di Johnson-Fluiten, che da sempre realizza tali componenti per tutti i segmenti dell’industria meccanica.
“Johnson-Fluiten è un nome ben conosciuto nel nostro settore, che sempre più spesso ritroviamo anche nelle specifiche di richiesta del cliente finale. I giunti rotanti Johnson-Fluiten sono stati ormai adottati come standard in tutte le nostre soluzioni perché sinonimo di garanzia e affidabilità”, ha spiegato Nicola Fedele, responsabile commerciale e marketing di Rodolfo Comerio.
Da sinistra a destra, i giunti rotanti serie SX, ELS ed R.
Per conferire caratteristiche peculiari alle proprie macchine e ai prodotti ottenuti con il loro utilizzo, Rodolfo Comerio ha scelto di affidarsi ai giunti rotanti di Johnson-Fluiten anche per la loro capacità di adattarsi in modo versatile alle diverse esigenze applicative.
Al consolidarsi del rapporto con Rodolfo Comerio hanno contribuito anche le consulenze pre e post-vendita e la rapidità delle consegne. “Siamo estremamente soddisfatti della collaborazione con Johnson-Fluiten per l’affidabilità, la varietà dei prodotti offerti e l’assistenza costante”, ha commentato a riguardo Nicola Fedele.
Un’offerta versatile
Gli impianti che Rodolfo Comerio realizza spaziano dalla lavorazione di materie plastiche come PVC, PP, PE, TPO e TPU, per la produzione di film plastificato, multistrato e rinforzato per diverse applicazioni, a quella di gomma, per ottenere tessuto gommato per pneumatici, nastri trasportatori e diversi altri componenti in gomma impiegati in vari ambiti industriali. La gamma di soluzioni proposte si riflette nell’esigenza di disporre di componenti dalle prestazioni diversificate. Infatti, la gestione di più tipi di fluido, come olio diatermico (per riscaldare) e acqua (per riscaldare e raffreddare), può richiedere ai giunti rotanti prestazioni molto differenti in termini di velocità, pressione e temperatura.
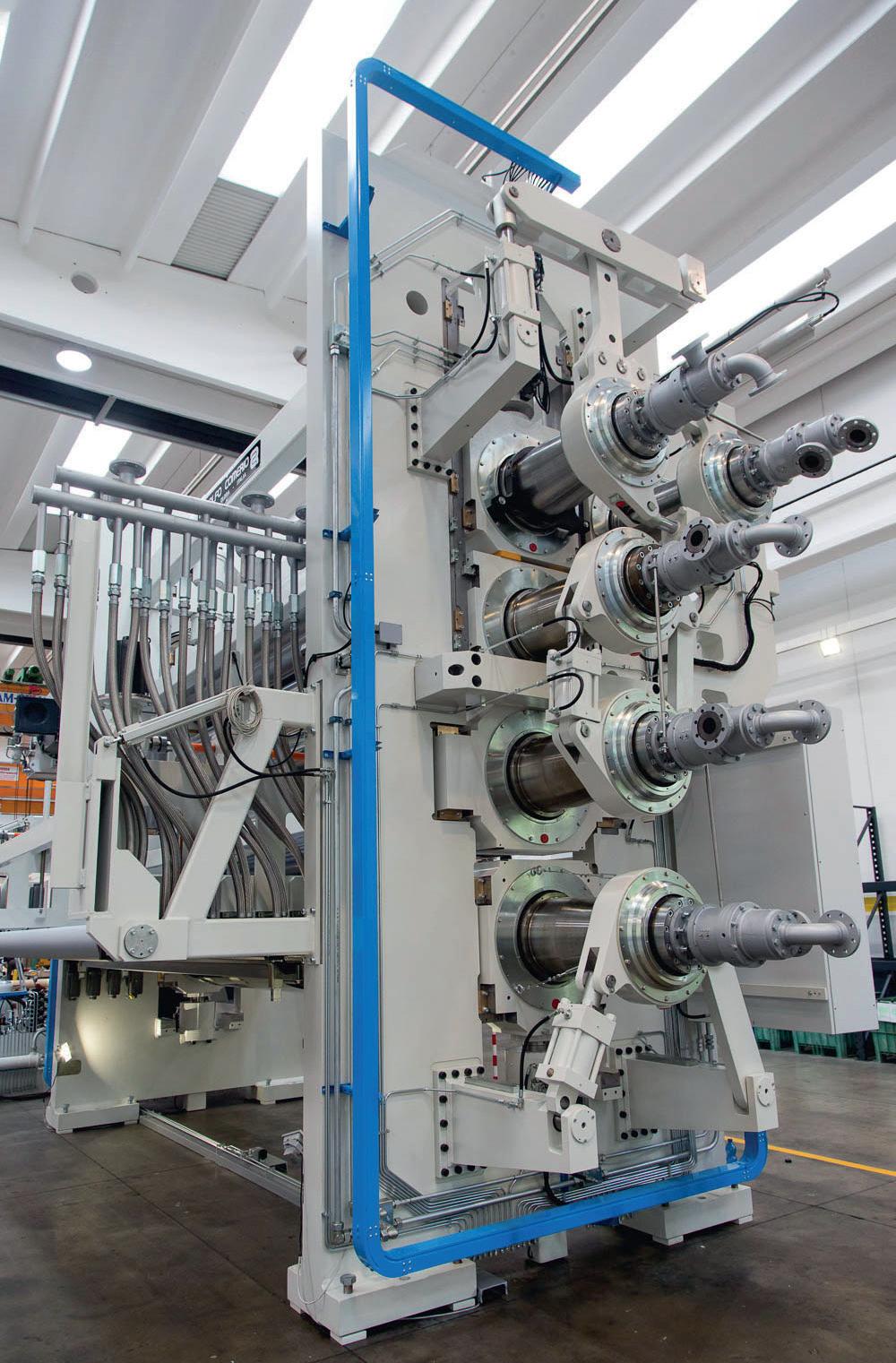
Da questo punto di vista Johnson-Fluiten ha dimostrato di essere un partner ideale: non solo la gamma di giunti rotanti a catalogo comprende soluzioni per ogni esigenza, ma, essendo parte del gruppo Kadant, la versatilità delle soluzioni per la gestione dei fluidi è tale da poter trovare sempre il prodotto giusto per ogni specifica necessità costruttiva. Rodolfo Comerio può quindi utilizzare un numero relativamente ridotto di referenze e trovare il componente ideale per ogni impianto, semplificando la gestione del magazzino.
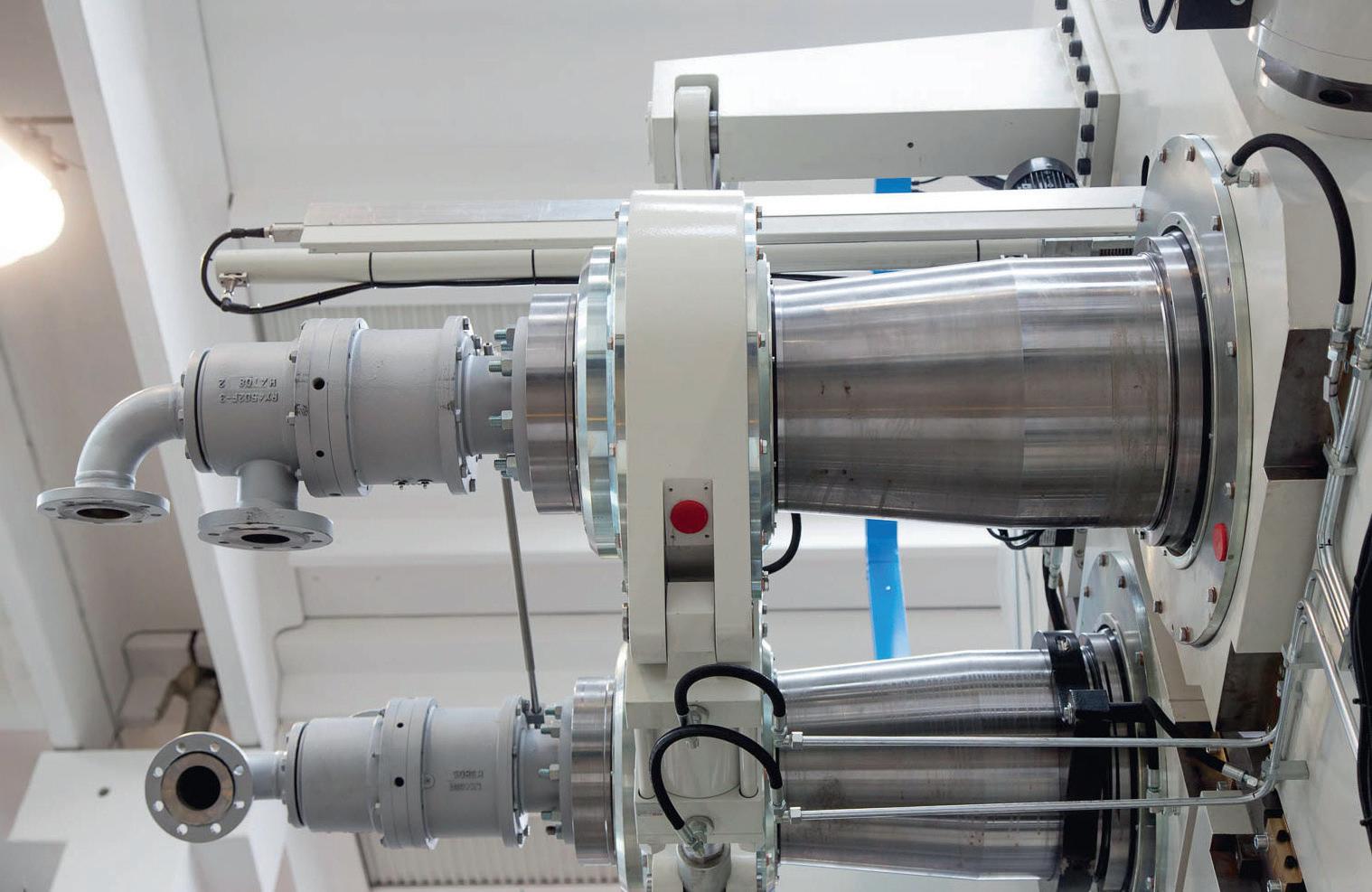
Per ogni applicazione, una soluzione
Olio diatermico
Ottenere la massima efficienza nella gestione dei fluidi negli impianti per la lavorazione della plastica e della gomma è possibile solo adottando i giusti giunti rotanti. In questo caso specifico i prodotti utilizzati per il riscaldamento con l’utilizzo di olio diatermico sono i giunti rotanti serie SX e i giunti serie ELS di Kadant.
Il giunto rotante SX è dotato di due guide in carbonio-grafite che consentono un facile allineamento e assicurano una lunga vita del giunto anche quando installato su cilindri non concentrici. Grazie al design semplice il giunto rotante SX garantisce elevate affidabilità e adattabilità in diversi tipi di applicazioni con olio e vapore.
ELS (Extended Life Series) è invece un giunto rotante con supporto interno progettato per risolvere i problemi di usura riscontrati con l’uso di giunti rotanti tradizionali nelle applicazioni che presentano vibrazioni elevate. Il giunto è realizzato con un design a due guide che offrono un migliore supporto interno e permettono al giunto di mantenere un corretto allineamento anche quando il rullo o il cilindro non sono perfettamente concentrici. Grazie alla sua tecnologia e al suo design, questo componente garantisce una maggiore durata e affidabilità rispetto ai prodotti standard.
Acqua
Nelle applicazioni in cui è richiesta la gestione dell’acqua a diverse temperature (sia calde che fredde) i giunti della serie R rappresentano la soluzione ideale. Il giunto R è impiegato per collegare una tubazione stazionaria a un dispositivo rotante e il fluido al suo interno è sigillato da una tenuta meccanica micro-lappata che garantisce la totale assenza di perdite. Il giunto è supportato da due cuscinetti a sfera ampiamente distanziati, ma la caratteristica che lo contraddistingue è rappresentata dall’esclusivo design a sostituzione rapida (QRD). Questo componente è stato progettato per consentire di intervenire sul giunto mentre è ancora installato sulla macchina, ma questa soluzione tecnica permette anche di adattarlo rapidamente ai fluidi che richiedono diversi materiali di tenuta qualora ci fosse una necessità produttiva differente.
E per quei macchinari dalle caratteristiche fortemente innovative, per i quali non è sempre possibile avere il giunto con le qualità richieste Johnson-Fluiten è in grado di fornire una pronta assistenza e di trovare nuove soluzioni idonee alle diverse esigenze. “Collaboriamo con Johnson-Fluiten ormai da molti anni e da sempre si è dimostrata un partner affidabile. Utilizziamo svariate soluzioni, soprattutto in base all’entità del progetto”, ha concluso Fedele.
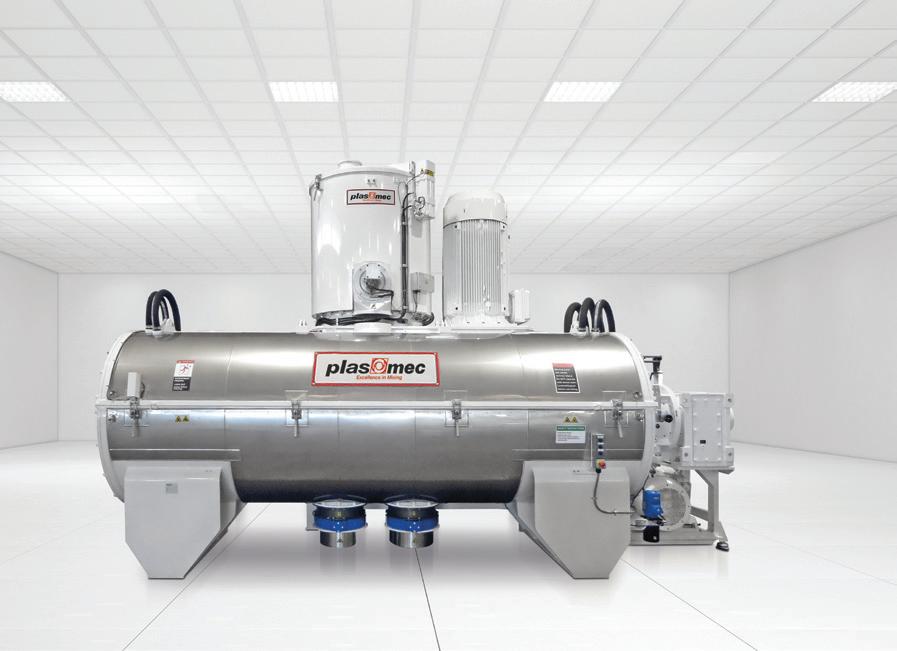
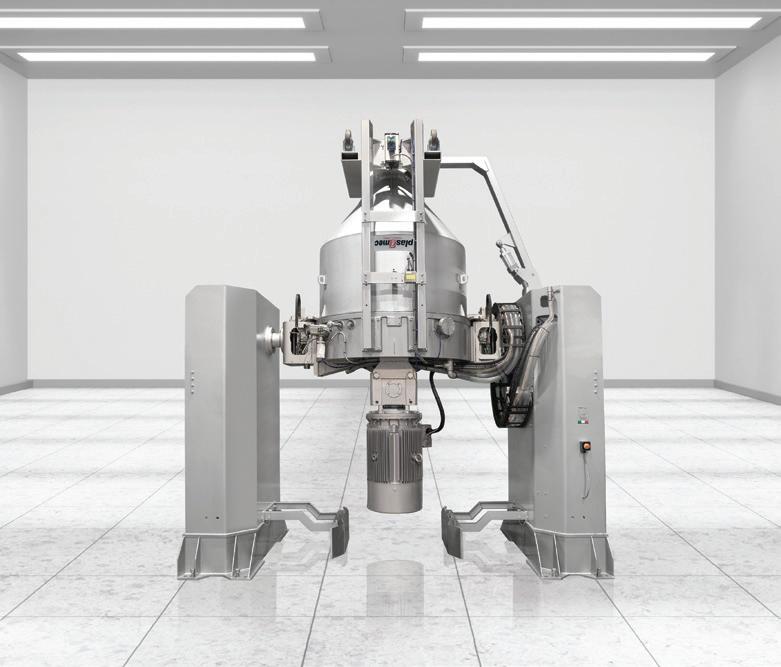
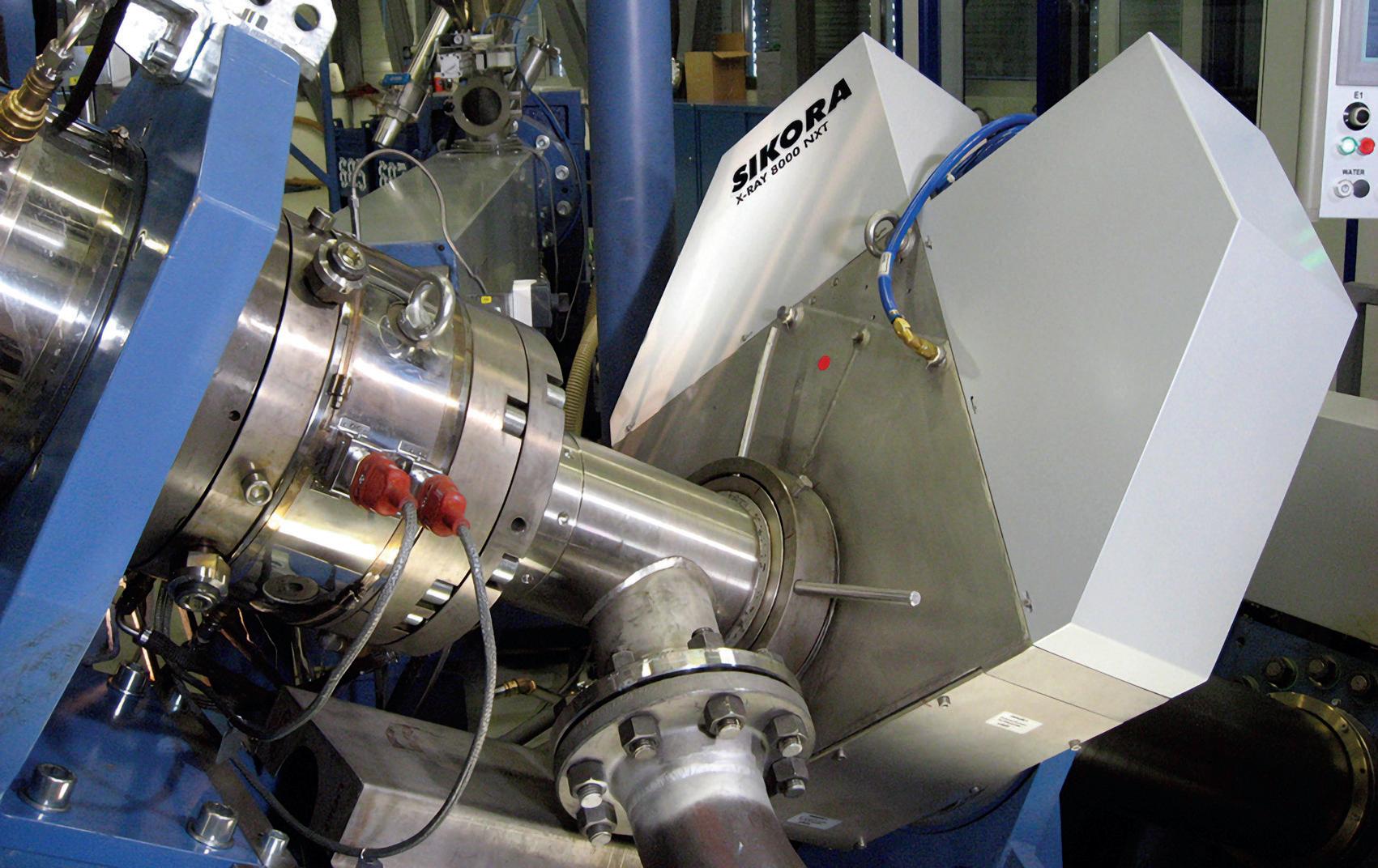
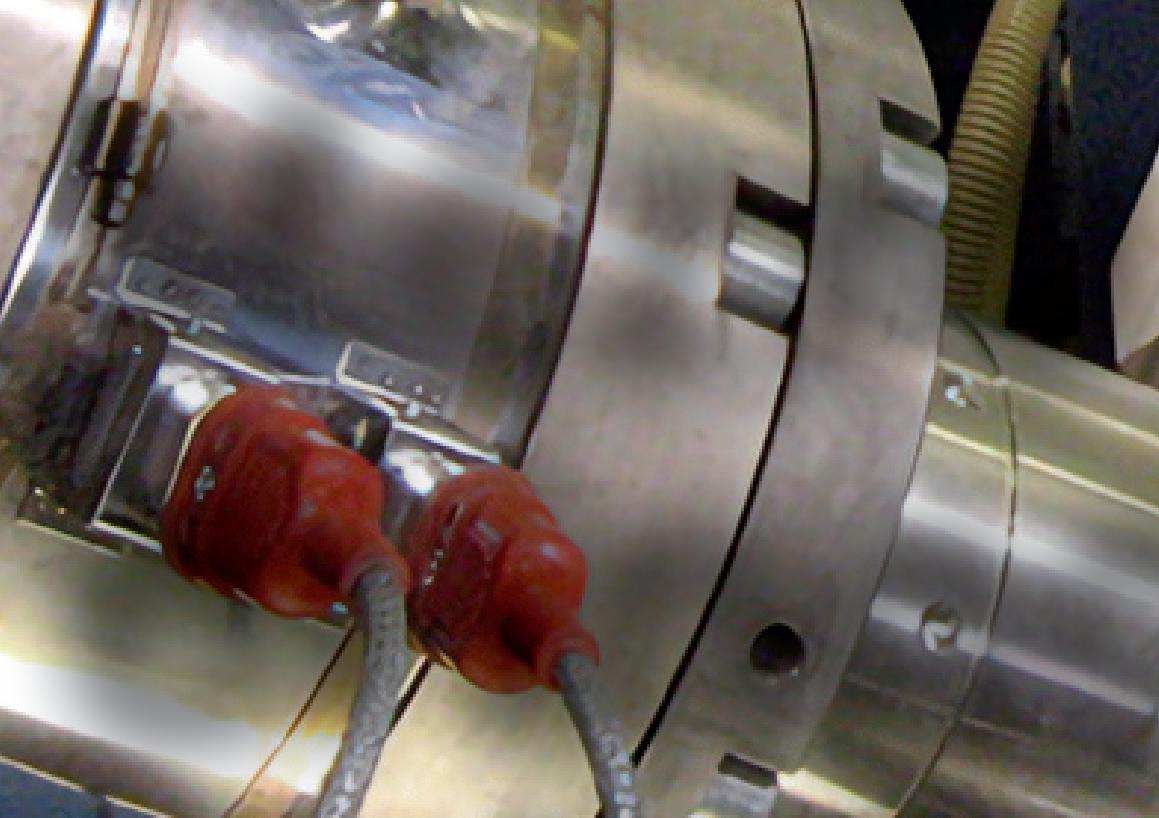

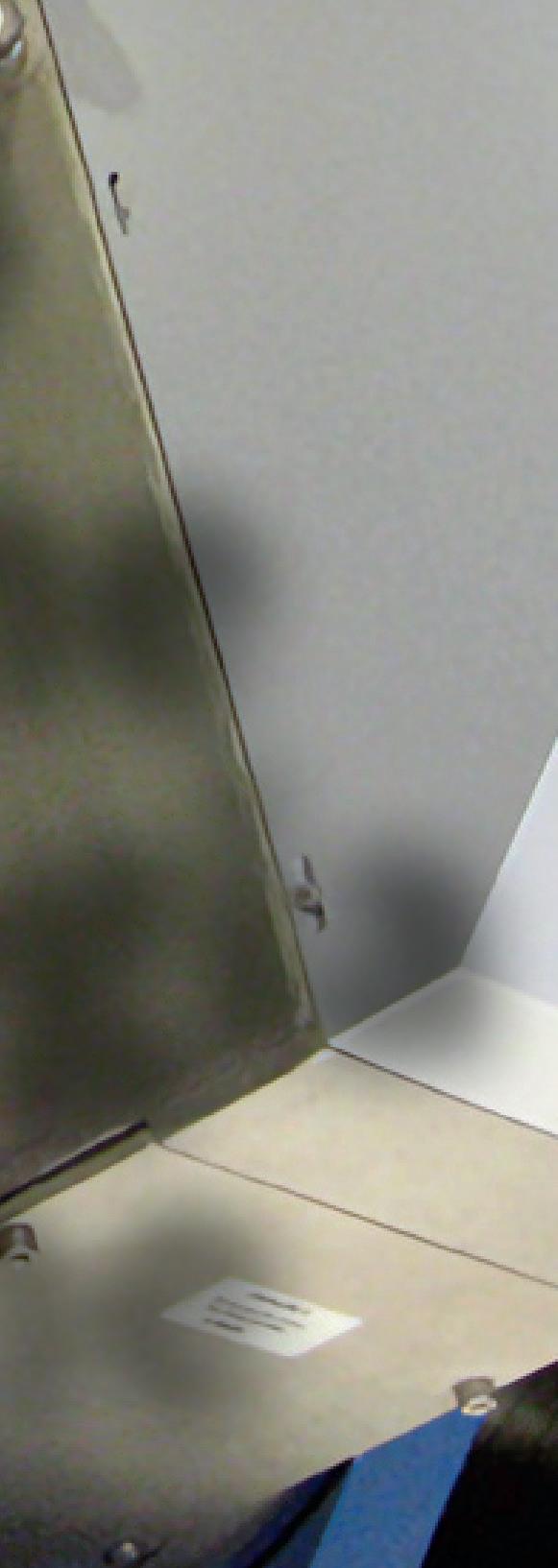

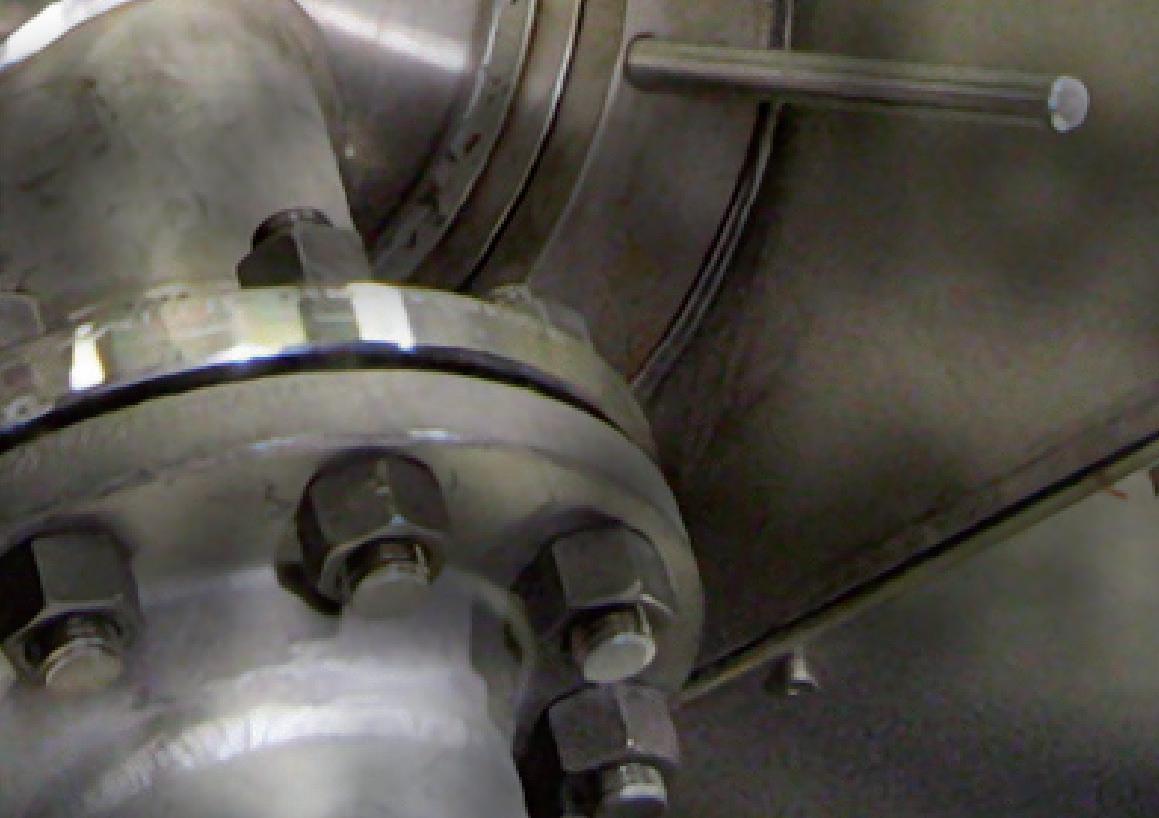
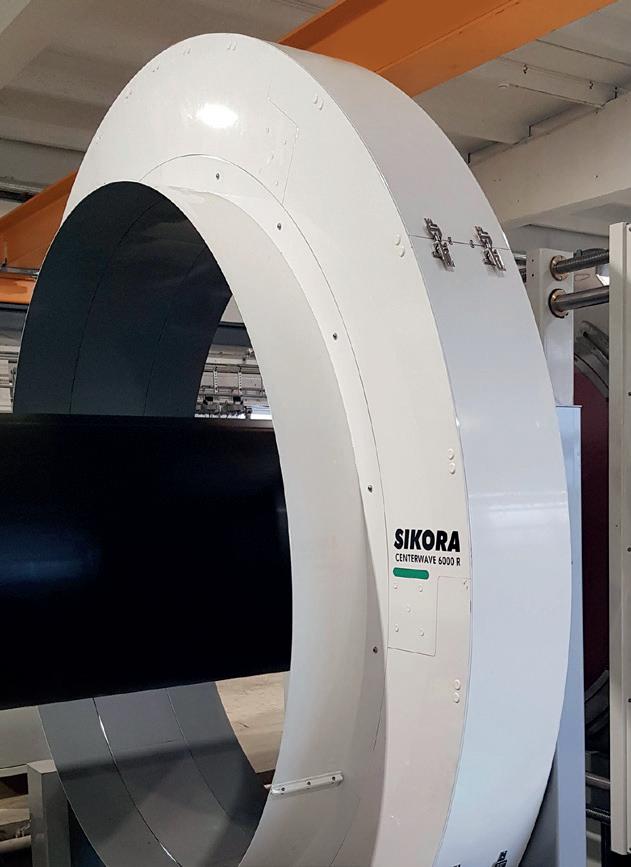
A gentle spark can start a strong fire

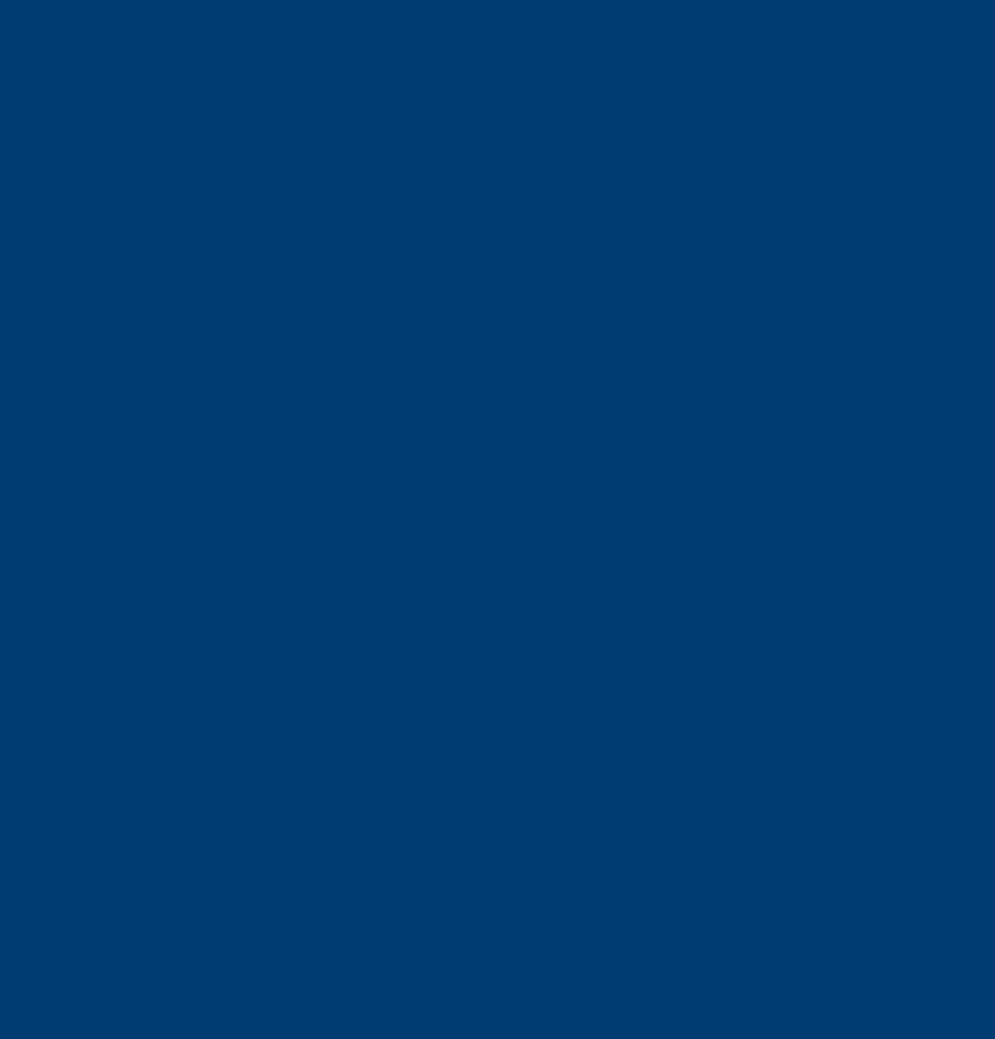
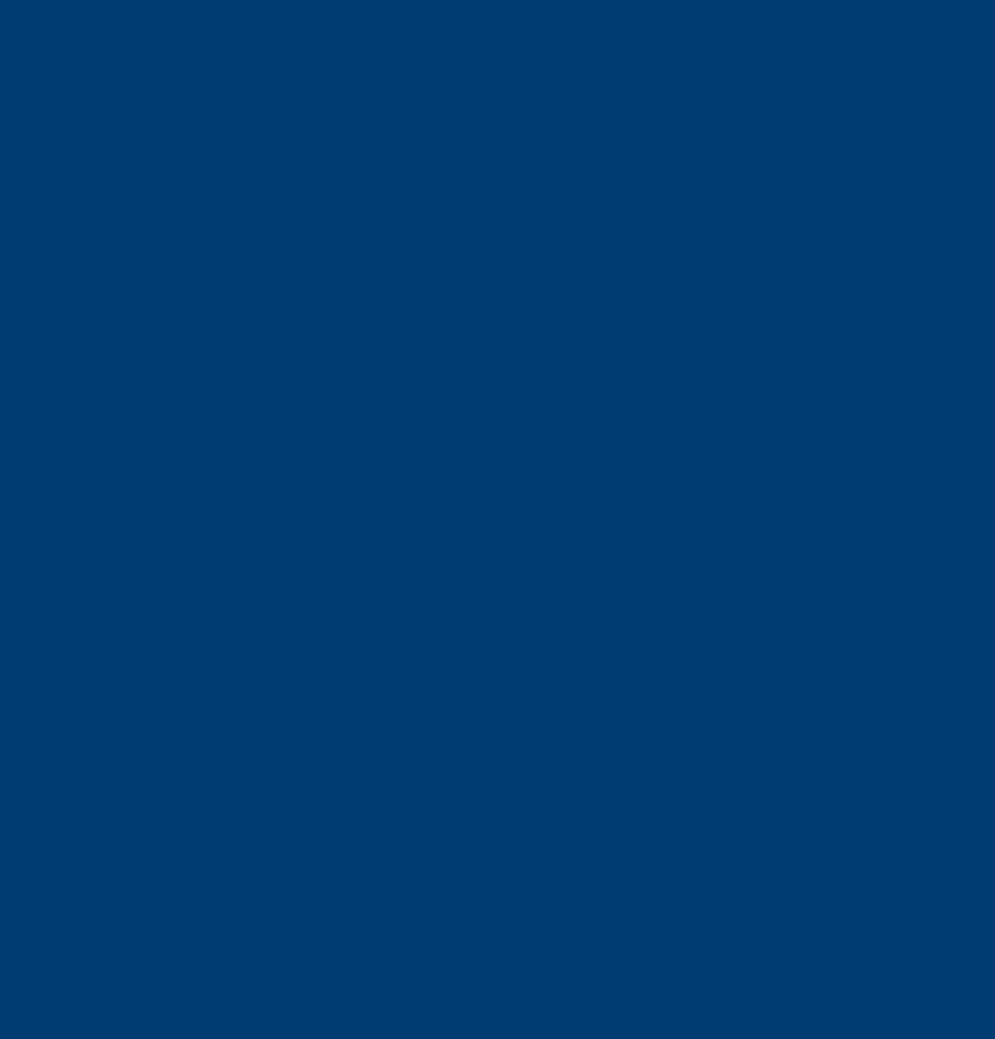
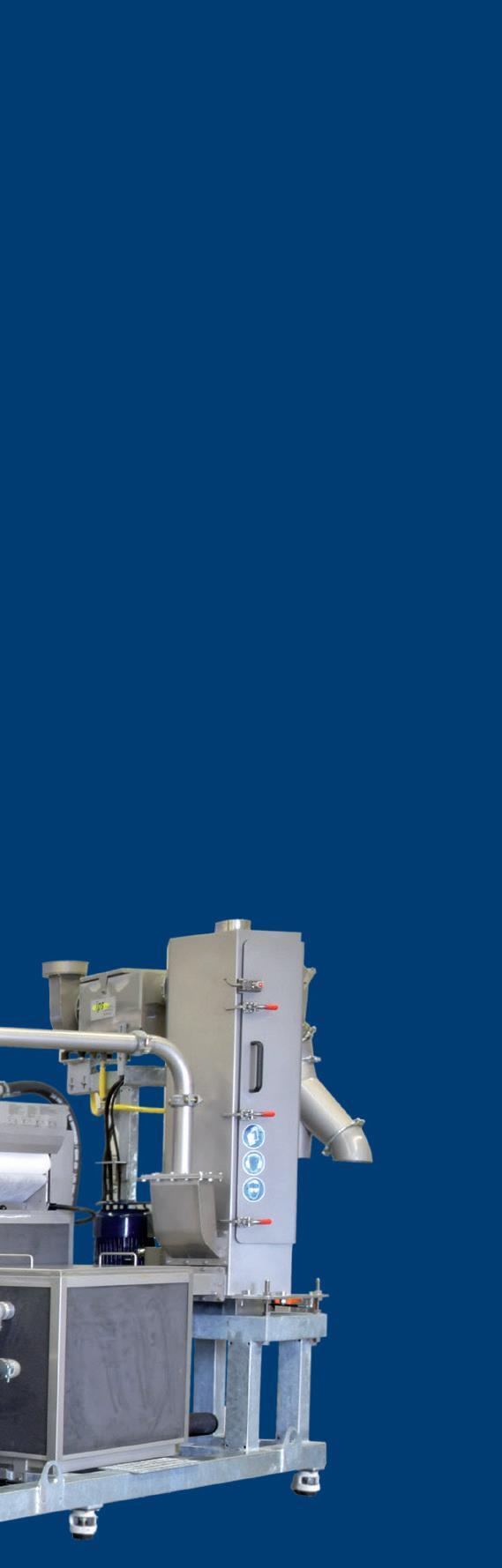
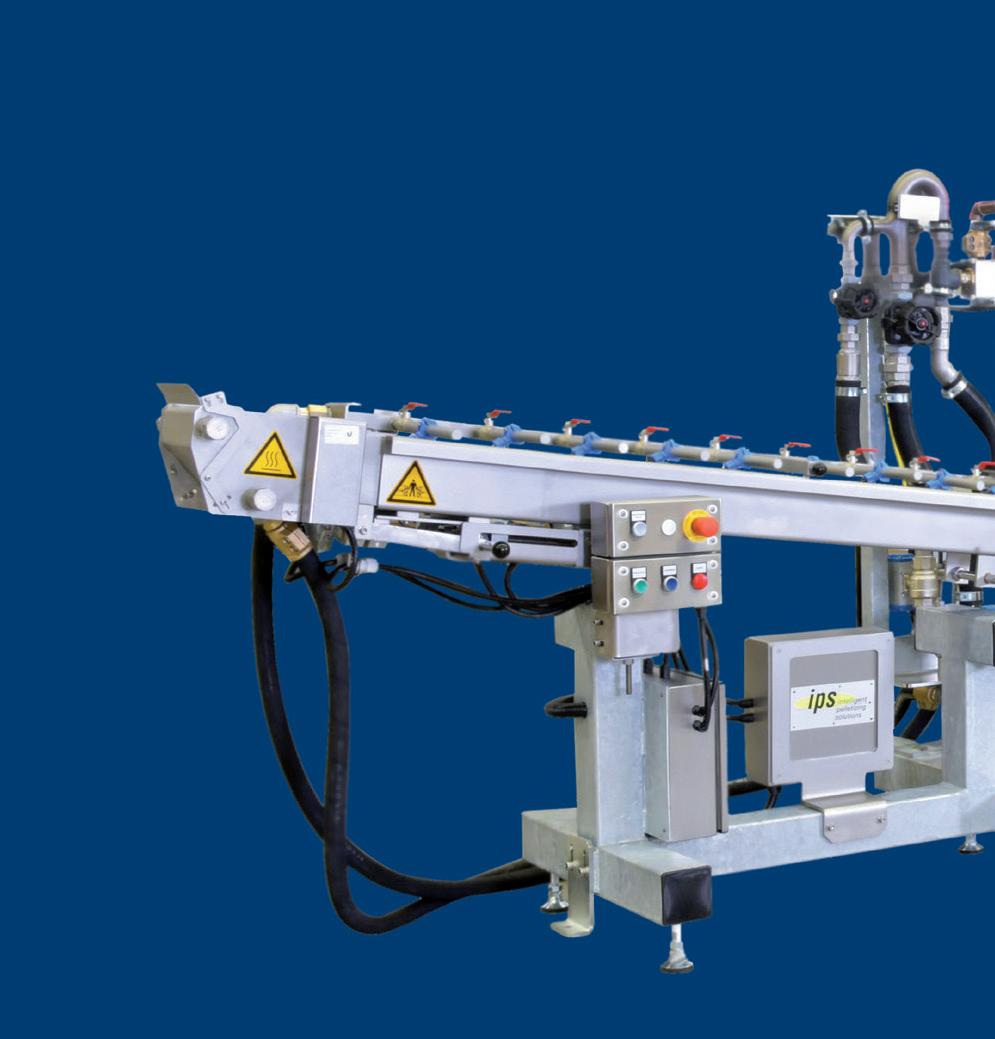

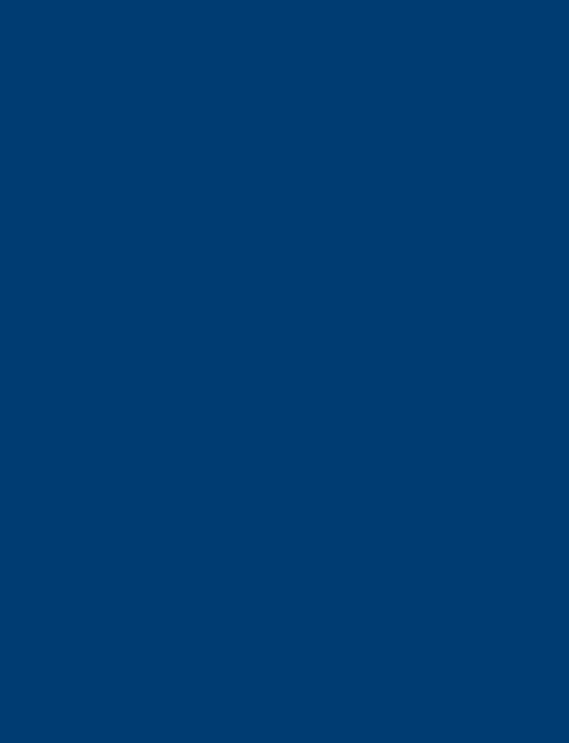
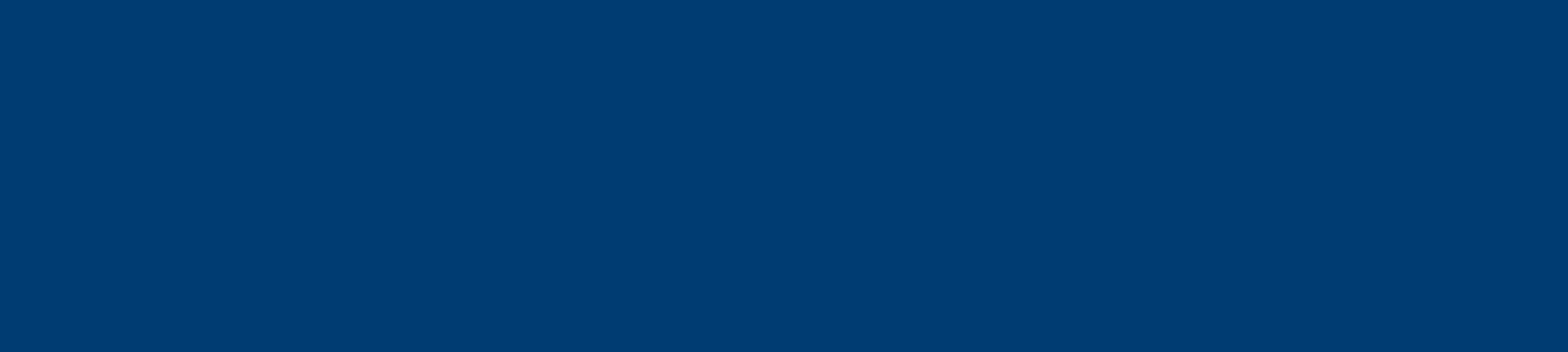
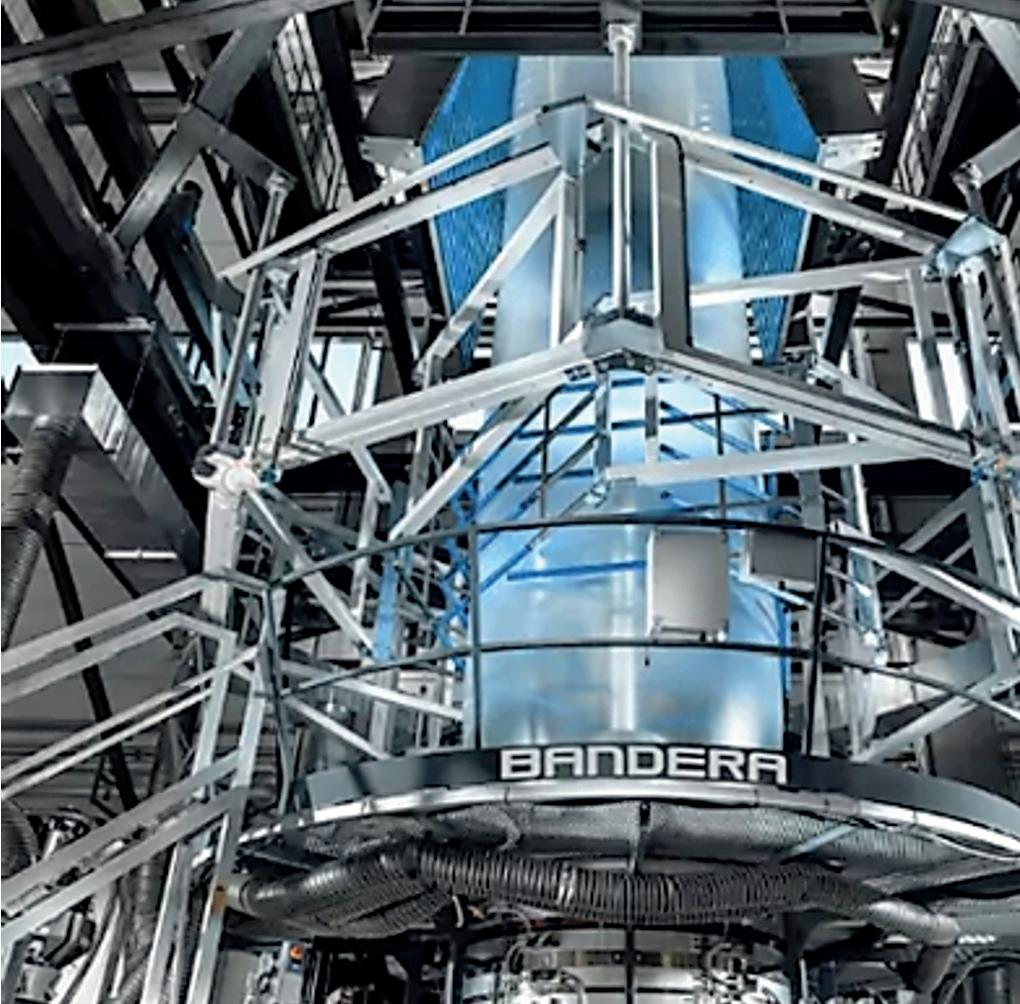
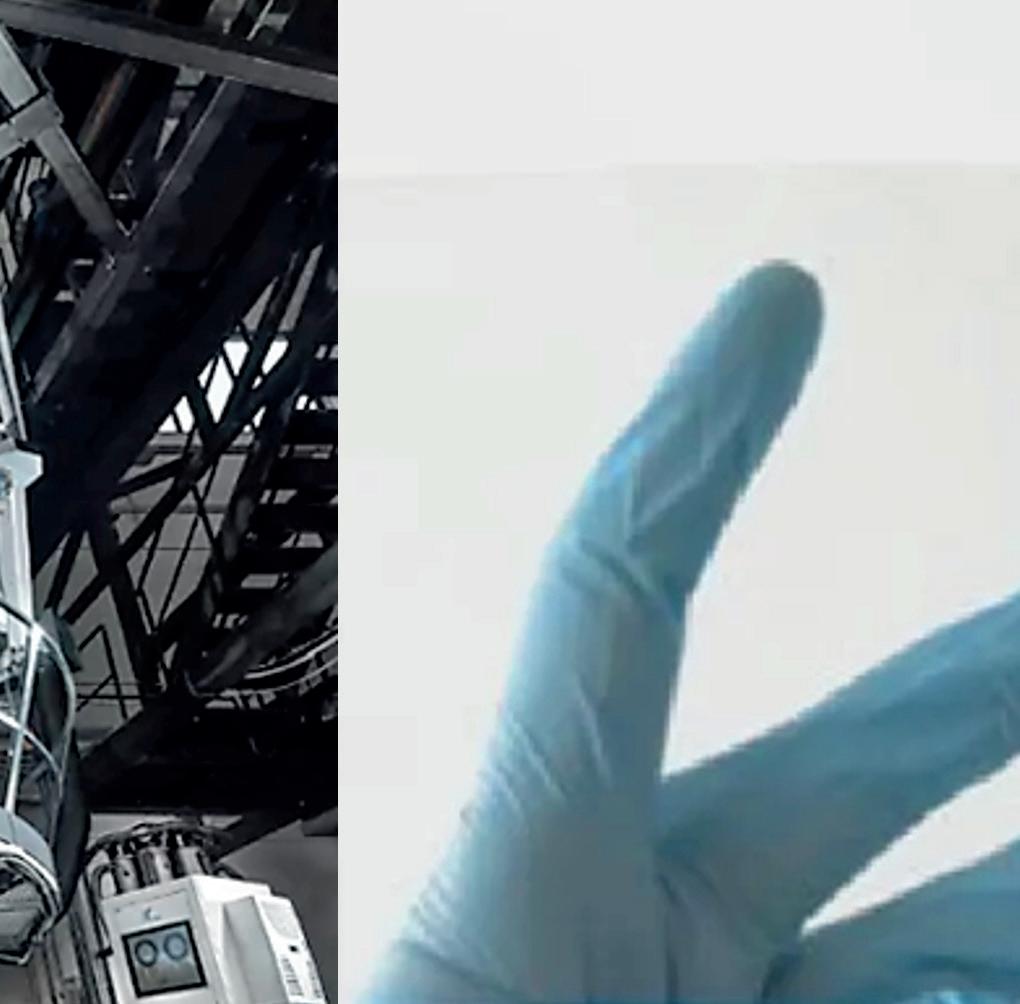
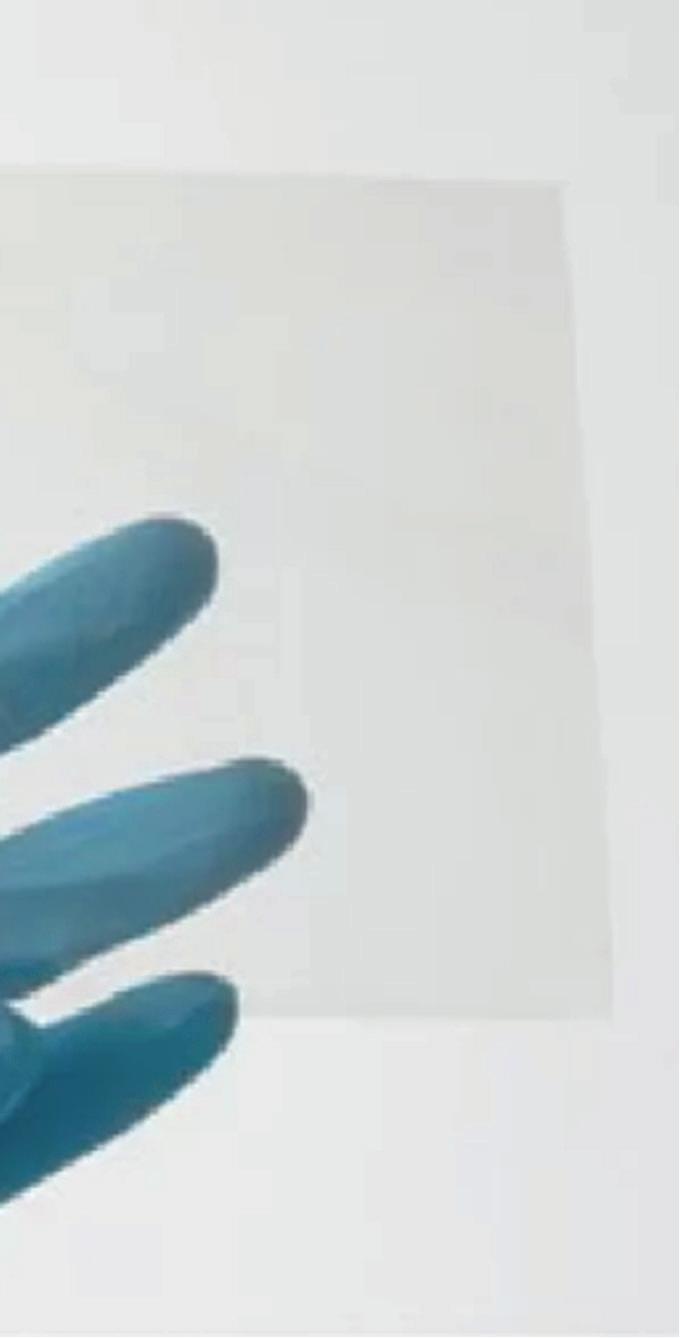

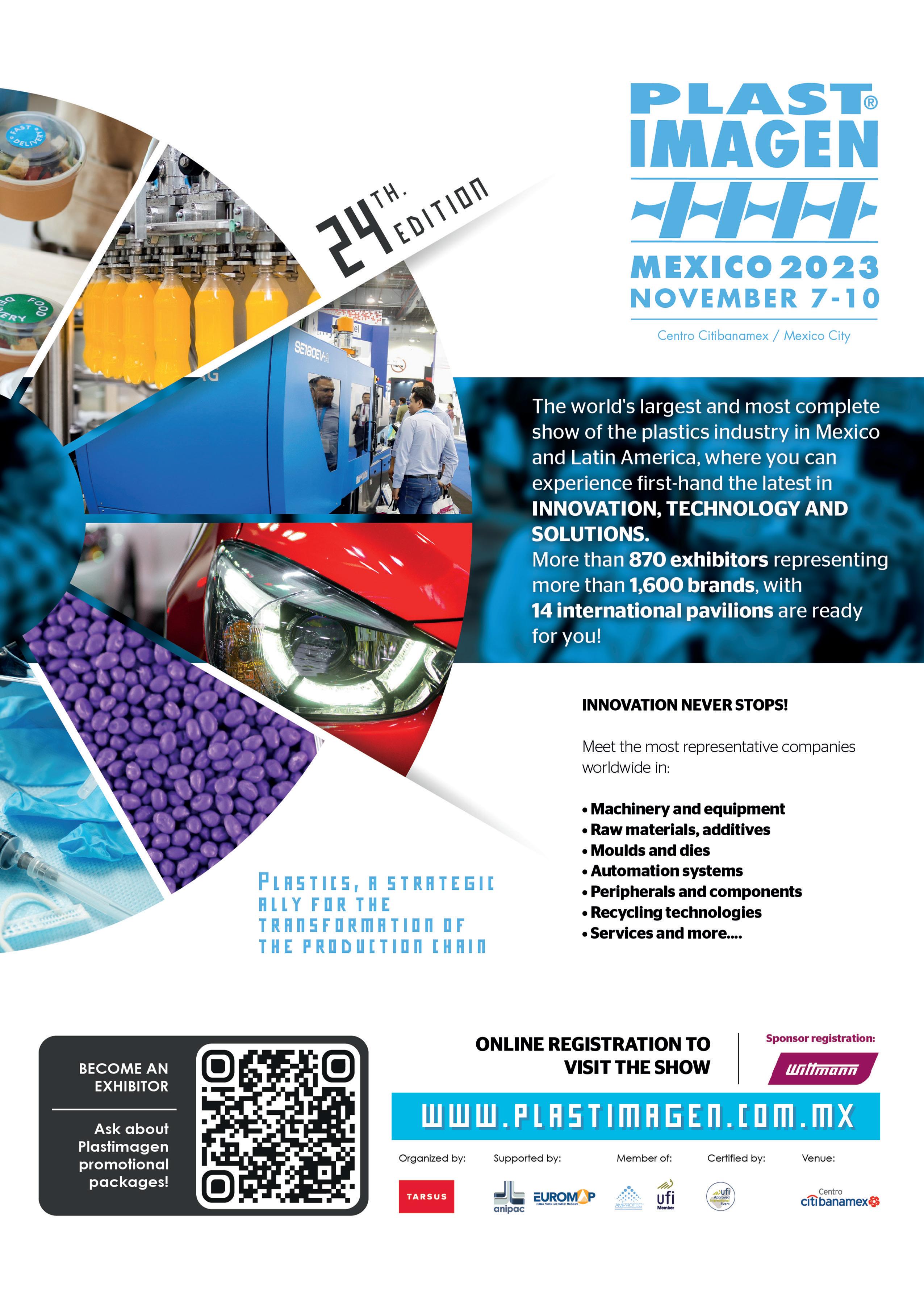
L’utilizzo dei canali caldi consente di ottenere componenti automobilistici con superfici stampate impeccabili nel rispetto degli elevati standard qualitativi imposti da tale settore. Oerlikon HRSflow propone alcuni esempi applicativi per dimostrare come i suoi sistemi siano in grado di garantire una produzione efficiente senza sprechi e con un elevato controllo del processo e i vantaggi ottenibili dalla tecnologia a otturazione servo-controllata Flexflow. Tra i primi rientrano la produzione di un pannello posteriore bi-materiale di un’automobile dal design all’avanguardia e un guida-luce realizzato con la nuova tecnologia CTC per un’estetica ottimale del punto di iniezione, mentre tra i secondi troviamo una cover per un fanale anteriore e un’applicazione leggera realizzata con la tecnica della retro-iniezione su film. Per realizzare il pannello posteriore “smart” di un’automobile è stata utilizzata una tecnologia bi-fase. Nella prima fase una cornice in PC/ABS è stata prodotta mediante iniezione con un sistema idraulico a due iniettori, nella seconda sono stati sovrastampati PMMA o PC utilizzando un ugello singolo della serie Ga. Infine, il componente è stato decorato direttamente nello stampo con un film. La complessità di questa applicazione ha richiesto analisi reologiche approfondite, per le quali Oerlikon HRSflow ha collaborato con Kurz, Engel e Schöfer.
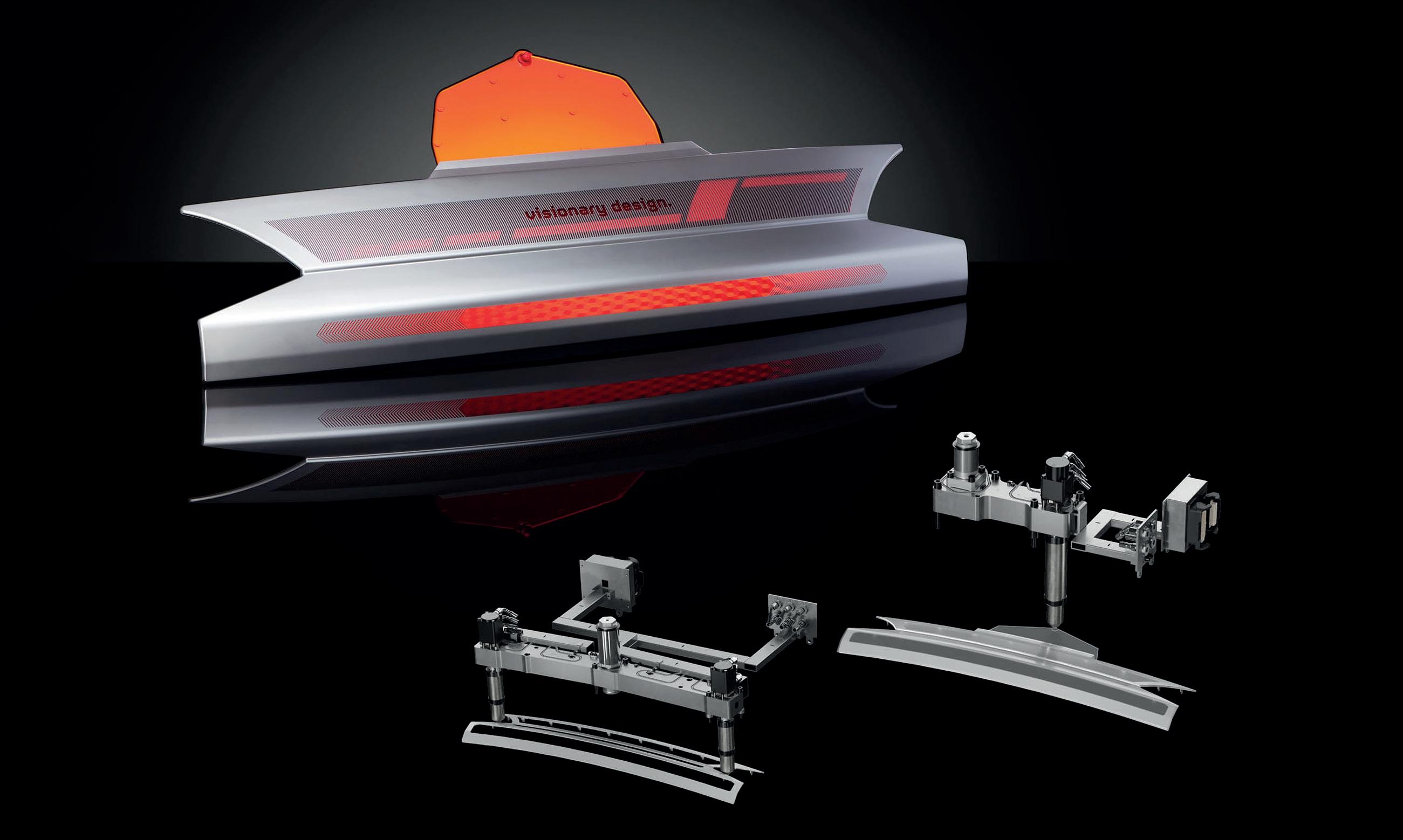
Per lo stampaggio a iniezione di un guida-luce è stato utilizzato il nuovo inserto CTC (in attesa di brevetto), realizzato in acciaio con elevate proprietà meccaniche e resistente alla corrosione.
Grazie al controllo termico ottimale nell’area del punto di iniezione e a una chiusura cilindrica è possibile evitare la formazione di bave, ottimizzando la produttività. Si tratta di una soluzione che permette di facilitare il ripristino dei punti di iniezione e le operazioni di manutenzione. Le applicazioni ideali del nuovo inserto CTC in generale sono rappresentate da componenti che richiedono una finestra di stampaggio ampia, dati volumi ridotti, lunghi tempi di impaccamento o alte pressioni di mantenimento.
I fari a LED in PC trasparente sono un’applicazione collaudata della tecnologia Flexflow. I motori servo-controllati consentono movimenti sincronizzati degli otturatori per un controllo preciso del flusso del materiale durante la fase di stampaggio. Le improvvise cadute di pressione, che solitamente si verificano con l’allontanamento dei punti di iniezione, vengono evitate, garantendo il riempimento uniforme delle cavità e la riduzione al minimo delle zone di stress sul componente. Durante la fase di mantenimento della pressione viene assicurato un alto livello di flessibilità, poiché il profilo di chiusura dell’otturatore (velocità e corsa) può essere regolato per soddisfare i requisiti dimensionali della parte.
Le potenzialità della tecnologia a canale caldo nel design degli abitacoli del futuro sono state infine oggetto di un progetto realizzato in collaborazione con Koller Group e Dietfurt utilizzando come esempio la realizzazione di una cover per laptop. Su un film preformato è stato iniettato policarbonato utilizzando la tecnica chiamata FIM (Film Insert Molding). Lo sviluppo dello stampo è stato effettuato in collaborazione con Koller Formenbau, mentre il processo di retro-iniezione è stato sviluppato con Koller Kunststofftechnik, trasformatore specializzato nella realizzazione di componenti leggeri per l’industria dell’auto. Mentre inizialmente il film si trovava sotto il punto di iniezione, la precisione della tecnologia Flexflow permette di evitare “l’effetto sbiadito”.