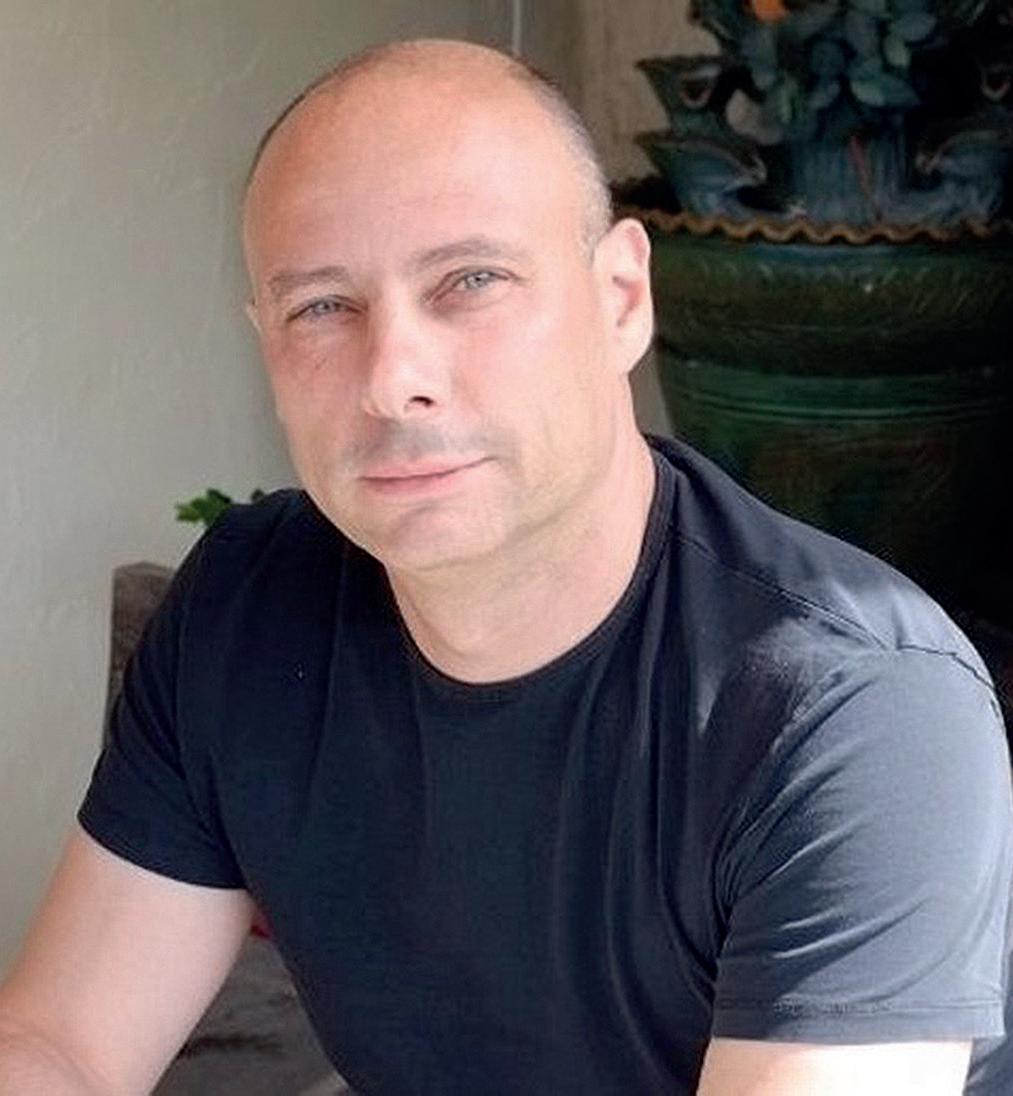
7 minute read
Rassegna internazionale di scienza e tecnologia
Ventiseiesima puntata della rubrica dedicata agli articoli di stampa estera selezionati dal comitato di redazione di Elastica, composta da Fabio Bacchelli, Rino Gilotta e dal team di Cerisie, coordinati da Maurizio Galimberti.
CRACKING DA OZONO NEGLI ELASTOMERI - UNA PANORAMICA
Testata: Kautschuk Gummi Kunststoffe, 1, 61 (2023) Titolo originale: Ozonrissbildung bei Elastomeren - Eine Übersicht
Autori: F. Lotz, D. Flügel
A C URA DI FABIO BACCHELLI
L’invecchiamento da ozono e la protezione da esso rappresentano importanti fattori per lo sviluppo applicativo di materiali elastomerici e molti studi di letteratura hanno descritto le varie fasi del processo di degradazione E analizzato le singole variabili che lo influenzano. L’ozono è una molecola presente nella stratosfera, utile a proteggere la superficie terrestre dalle radiazioni UV. Quando radicali idrossilici reagiscono con idrocarburi in presenza di ossigeno, si formano radicali perossidici in grado di reagire con monossido di azoto per formare biossido di azoto. A sua volta, il biossido di azoto può decomporsi per fotolisi in ossigeno atomico e monossido di azoto. L’ossigeno atomico è poi in grado di formare ozono tramite il normale ossigeno bimolecolare. Poiché la reazione principale per la formazione di ozono dipende dalla radiazione solare, la concentrazione di ozono dipende sia dall’ora del giorno sia dalla stagione. Il massimo inquinamento da ozono si raggiunge, pertanto, da aprile ad agosto.
Poiché l’ozono è in grado di reagire molto rapidamente con i doppi legami C=C, la molecola può attaccare le gomme insature, modificarne le proprietà fisiche e causarne l’invecchiamento. Tipicamente, in presenza di un carico tensile, si formano crepe, che corrono perpendicolarmente alla direzione della sollecitazione. Senza una appropriata tensione, non è possibile rilevare alcun cambiamento dopo esposizione all’ozono. Questa particolarità può essere spiegata considerando la reazione chimica dell’ozono con i doppi legami C=C dell’elastomero. Attraverso una ciclo-addizione si forma un ozonide primario instabile, che decompone molto rapidamente, portando alla rot- tura della catena polimerica della gomma. Se non c’è tensione esterna, viene generato un ozonide secondario. Se, invece, il materiale è sottoposto a stress tensile, avviene una scissione dell’ozonide primario in un composto carbonilico e un ossido carbonilico (zwitterione), con insorgenza di fessurazioni macroscopicamente visibili. A causa dell’elevata velocità di reazione, questi fenomeni avvengono solo sulla superficie dell’elastomero. Sulla base di questi meccanismi, risulta esistere uno stress critico, al di sopra del quale ha luogo il cosiddetto “cracking”. La crescita delle fessurazioni è strettamente legata alla dinamiche di formazione delle crepe e al numero di punti di nucleazione. In definitiva, il numero di crepe determina la redistribuzione dello stress. L’analisi degli elastomeri trattati con cere e/o agenti di protezione dall’ozono richiede solitamente tensioni più elevate per osservare problemi in presenza di stress da ozono. Più in generale, all’aumentare dell’entità del- la tensione diminuisce il tempo necessario alla comparsa delle prime fessurazioni. È invece dimostrato che la temperatura non ha un’influenza lineare sul tasso di crescita della cricca, mentre ha impatto variabile in funzione della tipologia del materiale. Analizzando l’influenza dell’umidità dell’aria sul cracking da ozono, si osserva che un aumento di umidità favorisce la nucleazione delle cricche, dando luogo a un maggior numero di fessurazioni. Al di sopra del 50% di umidità è possibile osservare la comparsa di polvere nera sulla superficie del materiale, a seguito della formazione di radicali idrossilici, che derivano dalla reazione dell’ozono con l’acqua. Con l’aumento del contenuto di ozono, la crescita delle crepe aumenta quasi linearmente, anche se la velocità dipende dal materiale. Questo fattore conferma la necessità di monitorare accuratamente la concentrazione di ozono durante tutta la durata di un test predittivo di laboratorio. Gli additivi utilizzati per la protezione dall’ozono includono tipicamente cere o antiozonanti, le cere, paraffiniche e microcristalline, formano un film sottile sulla superficie dell’elastomero, che agisce come barriera fisica impedendo la reazione dell’ozono. Lo spessore e la densità dello strato, nonché la solubilità della cera nella matrice polimerica determinano la capacità protettiva. Lo svantaggio delle cere è rappresentato dallo stress dinamico, che può rompere lo strato e vanificare l’effetto protettivo. Gli agenti antiozonanti sono in genere parafenilendiammine, che reagiscono con l’ozono più velocemente rispetto ai doppi legami dell’elastomero e impediscono cineticamente la scissione delle catene. creano le condizioni determinanti il deterioramento degli elastomeri: si ha così l’invecchiamento da ozono e termo-ossidativo. L’effetto di tali agenti dipende anche dalla durata, dal tempo di esposizione, dal tipo di polimero e dai contaminanti.
Degrado termico e ossidativo degli elastomeri
Quando la gomma viene esposta ad alta temperatura in presenza di aria o di ossigeno, perde proprietà meccaniche come la resistenza alla trazione e l’allungamento.
Il tipo di cambiamento delle proprietà durante l’invecchiamento del materiale non è facilmente determinabile, perché ci sono due possibili reazioni: l’indurimento causato da un’ulteriore reticolazione con una maggiore densità di legami e l’ammorbidimento prodotto dall’accorciamento della catena polimerica. Oltre alla struttura di base della catena polimerica, anche il sistema di vulcanizzazione gioca un ruolo nella stabilità termica. In generale, gli elastomeri vulcanizzati con perossidi, che formano legami C-C, hanno una maggiore resistenza al calore rispetto a quelli vulcanizzati allo zolfo perché l’energia di legame di C-C, è molto più alta di quella di C-S e dei legami polisolfuri.
Meccanismo di degradazione termica
La degradazione termica avviene in tre fasi:
• l’invecchiamento termico ossidativo inizia rompendo i legami covalenti lungo la catena polimerica o le catene laterali per produrre radicali di carbonio instabili (R*);
EFFETTI DEL DEGRADO PER INVECCHIAMENTO DI UN MASTERBACH IN GOMMA NATURALE SUI PARAMETRI REOLOGICI E SULLE PROPRIETÀ FINALI
Testata: Rubber World, novembre 2022
Titolo originale: Effect of natural rubber masterbatch aging conditions on rheology and properties of a final compound
Autori: Ali Vahidifar and Steven Yu, AirBoss of America
A C URA DI ROSARIO GILOTTA
Introduzione
Esistono diversi tipi di degradazione della gomma, come la degradazione termica, fotochimica, idrolitica, biologica, meccanica e ossidativa.
Gli iniziatori del processo di deterioramento e i relativi agenti degradanti sono: temperatura; campi elettrici; stress meccanici; idrolisi (acqua); bio (microorganismi); agenti ambientali; radiazioni.
L’azione congiunta di ozono, ossigeno e temperatura elevata
• la propagazione, ovvero una serie di reazioni radicaliche. Questi radicali sono così instabili che reagiscono con l’ossigeno per formare radicali perossidici. Successivamente il radicale perossidico estrae un atomo di idrogeno da un’altra catena polimerica per formare un gruppo idroperossido instabile, che produce un altro radicale carbonio per propagare il ciclo;
• la fase finale avviene quando due segmenti con un elettrone spaiato formano un prodotto inattivo. Questa può essere una reazione tra due radicali perossidici, radicali alchilici o due diversi radicali nel sistema.
Preparazione del campione
L’impasto di gomma naturale è stato confezionato in un grande mescolatore interno di 350 litri per studiare l’effetto dell’invecchiamento sulle proprietà tecno-reologiche. Tutti gli ingredienti tranne i vulcanizzanti sono stati mescolati in prima fase nel mescolatore interno con velocità del rotore di 60 rpm e con temperatura di scarico di 300°F. Dopo lo scarico, l’impasto è stato ripreso e lavorato a temperatura ambiente su un mescolatore aperto lasciandolo raffreddare tutta la notte. Per studiare il comportamento dell’invecchiamento delle mescole, gli impasti sono stati invecchiati in stufa ad aria ventilata a 23°C, 40°C, 50°C, 60°C e 70°C da 1 a 60 giorni. Successivamen- te, le mescole sono state confezionate con gli impasti invecchiati in un miscelatore interno da 1,6 litri con fattore di riempimento 80% e con l’aggiunta dei reticolanti nei masterbatch. La mescolazione ha proseguito fino al raggiungimento della temperatura di scarico di 210°F. È stata poi completata al mescolatore aperto di 6” a temperatura ambiente per garantire una miscelazione uniforme. I lotti finali sono stati tenuti a temperatura ambiente durante la notte per rimuovere eventuali tensioni residue e la storia termica.
Infine, le mescole sono state vulcanizzate a 300°F per 20 minuti utilizzando una pressa AF25 a una pressione di circa 150 bar.
Caratterizzazione
La viscosità Mooney (MV) e il tempo di rilassamento della tensione per il decadimento dell’80% della viscosità Mooney (t80) di campioni non vulcanizzati sono stati misurati secondo ASTM D1646 utilizzando un viscosimetro Mooney MV2000 con rotore grande.
La curva di vulcanizzazione delle mescole è stata impostata secondo ASTM D5289 mediante un reometro a camera oscillante (MDR) di Alpha Technologies a 350°F. Le caratteristiche di reticolazione come la coppia minima (ML), la coppia massima (MH), l’inizio del tempo di scottatura della vulcanizzazione (ts) in cui la coppia sale di 2 unità sopra ML e il tempo di vulcanizzazione ottimale al quale si verifica il 90% di reticolazione (tc90) sono stati definiti utilizzando i reografi di coppia in funzione del tempo. Lo scorch Mooney dei composti è stato misurato secondo la procedura di prova di un minuto di preriscaldamento e quattro minuti di test a 280°F, e il tempo per un aumento di 5 unità al di sopra della viscosità minima è stato registrato come t5 (Mooney scorch time.)
Viscosità Mooney
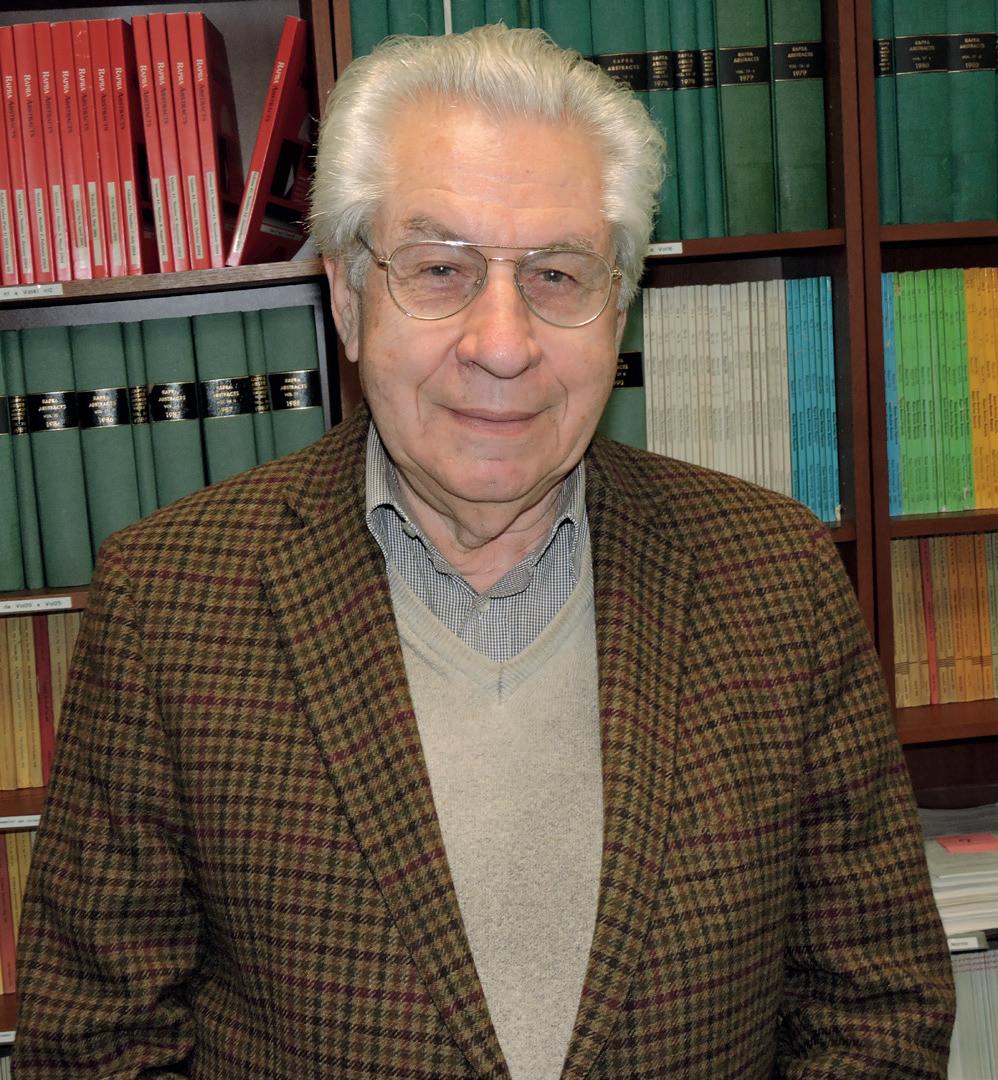
I risultati di viscosità Mooney mostrano che i composti invecchiati per un tempo più lungo e a temperature più elevate presentano un ML inferiore.
Ad esempio, la viscosità Mooney del masterbatch è diminuita continuamente da 35,5 MU per il campione non invecchiato a 35,2, 33,7, 33, 26,78 e 12,6 MU facendo invecchiare il MB per un giorno, due giorni, tre giorni, una settimana e due settimane a 50°C rispettivamente. La viscosità Mooney è sensibile alla temperatura dell’invecchiamento, si verifica quindi una riduzione Mooney più rapida all’aumentare delle temperature di invecchiamento.
I risultati mostrano che la scissione della catena è prominente a un intervallo di temperatura compreso tra 40°C e 70°C e che l’aumento della temperatura ha un effetto significativo sulla velocità di scissione della catena. Il peso Mooney/molecolare quasi invariato a temperatura ambiente e l’assenza di UV indicano che questa condizione di invecchiamento non è sufficiente per l’inizio della degradazione della gomma.
Proprietà fisico-meccaniche
Le proprietà meccaniche di MTE (Modulus, Tensile ed Elongation) di campioni esposti a un invecchiamento di tre mesi e variazione di temperatura da 23°C a 60°C mostrano valori di resistenza alla trazione e di allungamento a rottura notevolmente bassi.
Si ipotizza che la rottura delle catene polimeriche abbia ridotto le dimensioni della catena e il numero di aggrovigliamenti della stessa, così come l’aumento del tempo/temperatura di invecchiamento del masterbatch porta a una diminuzione della resistenza alla trazione e dell’allungamento alla rottura.
Conclusioni
In questo articolo, sono stati studiati gli effetti del tempo e della temperatura di invecchiamento su un masterbatch di NR relativamente agli aspetti reologici e alle proprietà meccaniche dei campioni vulcanizzati.
I risultati hanno mostrato che la temperatura di invecchiamento può essere suddivisa in tre diversi livelli: intorno ai 23°C, la mescola è stabile, anche con 90 giorni di invecchiamento e le variazioni sono state trascurabili; tra 40°C a 60°C, tutte le proprietà diminuiscono linearmente a una velocità costante e la velocità/pendenza di diminuzione aumenta con l’invecchiamento termico; sopra i 60°C, la temperatura e l’energia termica sono sufficientemente elevate da avviare una reazione autocatalitica non lineare.