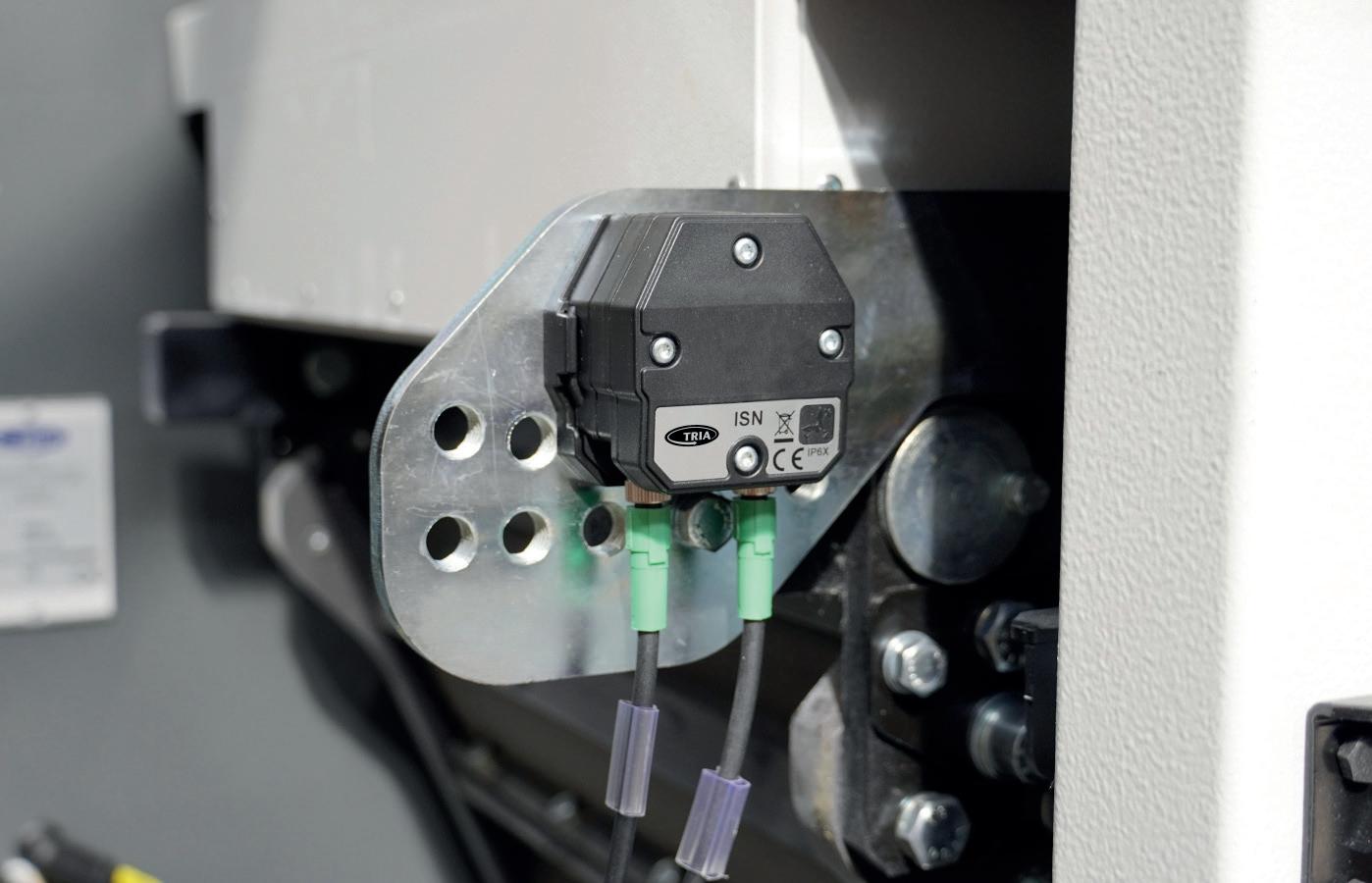
4 minute read
Evoluzione della camera di taglio
Introdotta recentemente da CMG, la nuova camera di taglio dei granulatori Evoluzione si caratterizza per un rotore che consente alle lame rotanti di tagliare il materiale plastico perpendicolarmente contro le lame fisse, ottenendo un elevato livello di precisione di taglio. Le lame sono montate direttamente sull’estremità della staffa di supporto anziché su
Granulatori in cloud
Il costruttore italiano di macchine per il recupero di scarti in materiale plastico Tria ha messo a punto, in collaborazione con l’azienda svedese CombiQ, il nuovo un blocco lama, soluzione che permette non solo di ottenere benefici dall’elevata inclinazione delle lame, ma anche di eseguire interventi di manutenzione e sostituzione facili e veloci, grazie all’accessibilità alla camera di taglio dalla parte frontale della macchina.
La rotazione del rotore non produce l’effetto “trascinamento” che si verifica quando la massa di materiale da macinare non ruota con il rotore, evitando così la generazione di polvere e piccole particelle, che diventano materiale di scarto nella fase di lavaggio. La produzione di microparticelle è ridotta a pochi punti percentuali, contro il 15% e oltre di un granulatore convenzionale. Il design a rotore aperto, inoltre, consente di occupare solo il 30% dello spazio all’interno della camera di taglio.
Il rapporto tra il volume del rotore e della camera di taglio è pari a 30/70, in confronto a quello di 70/30 dei granulatori convenzionali, cosicché nella camera di taglio possa essere introdotto oltre il doppio di materiale. Maggiore è la quantità di materiale nella camera di taglio e maggiore sarà la capacità di granulazione. La camera di taglio presenta il cosiddetto “sviluppo tangenziale”, che conferisce voracità e garanzia di ingestione del materiale da macinare senza dover ricorrere e sistemi di alimentazione forzata, comunemente utilizzati nei granulatori convenzionali.
Un rendering della nuova camera di taglio dei granulatori Evoluzione di CMG servizio Tcloud per connettere i suoi granulatori, sia nuovi sia già in funzione presso gli utilizzatori, al cloud. Per mezzo dell’installazione di un dispositivo a sensori sulle macchine sarà possibile trasmettere, attraverso il cloud appunto, a una piattaforma web appositamente sviluppata per questo impiego i parametri dei granulatori ed estrapolarli e analizzarli per monitorarne in tempo reale il funzionamento e programmare per tempo gli interventi di manutenzione ordinaria.
In pratica, le macchine, mediante notifiche personalizzate, vengono messe in grado di avvisare autonomamente il servizio di assistenza di Tria sugli interventi programmati o qualora si rendessero necessari. Per l’utilizzatore questo si traduce in fermi macchina minori e più brevi, con conseguenti risparmi di tempo e riduzioni dei costi.
Svilluppo congiunto tra Colines e TotalEnergies
Buste stand-up non laminate e riciclabili
È andata a buon fine la recente prova di fattibilità effettuata congiuntamente da Colines e TotalEnergies per realizzare una busta stand-up non laminata e riciclabile adatta ad applicazioni a contatto con alimenti. Attualmente il riferimento di mercato per tale tipo di applicazioni è costituito da film multimateriale e, di conseguenza, non riciclabili. I due partner hanno sviluppato una busta stand-up non laminata in PE completamente riciclabile, che consente anche di ridurre lo spessore dell’imballaggio.
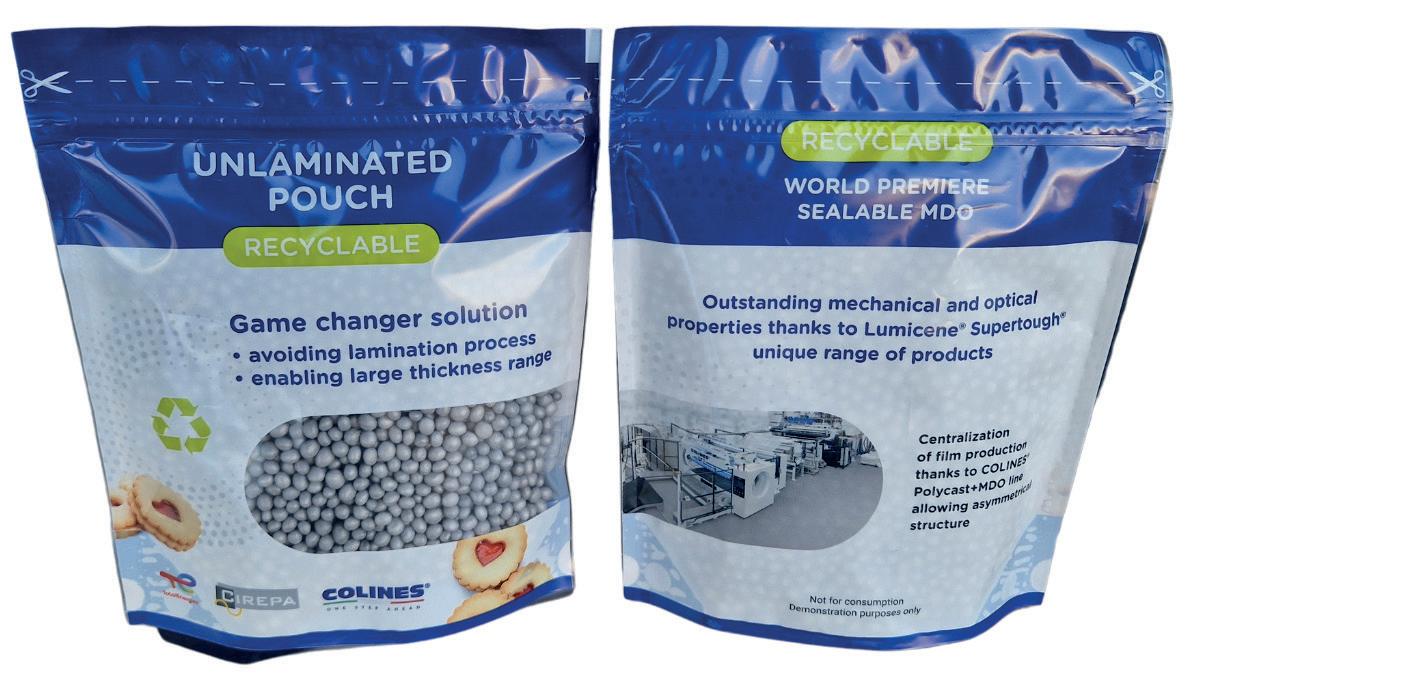
Il film MDO (Machine Direction Orientation) utilizzato a questo scopo è stato prodotto su linee Colines a testa piana delle serie Polycast ed MDO, ottenendo una struttura asimmetrica (strato sigillante a bassa densità su un lato, strato rigido ad alta densità sull’altro). La formulazione del film si basa su PE ad alta densità Supertough e Lumicene di TotalEnergies, che offre una vasta gamma di spessori con cui assecondare varie esigenze applicative. Al progetto hanno preso parte anche Cirepa, azienda attiva nel settore della stampa di imballaggi flessibili, che ha provveduto alla stampa del film, e Dry-Top, produttore di imballaggi che ha realizzato la busta stand-up.
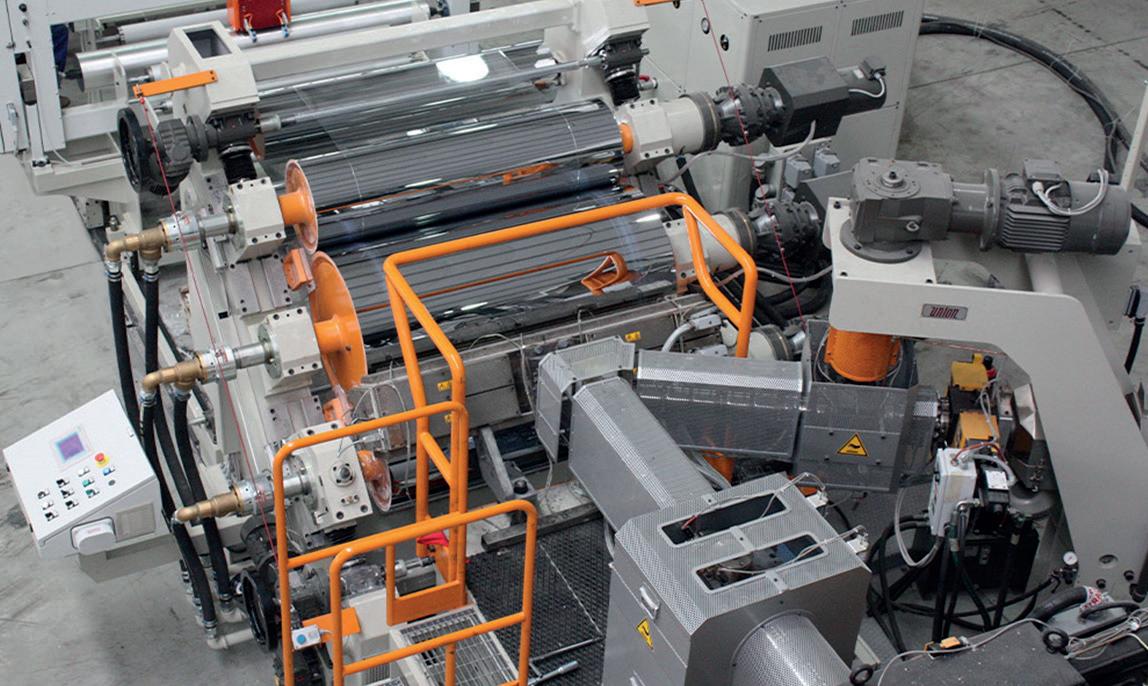
“Siamo orgogliosi di far parte di questo importantissimo progetto, reso possibile anche dalla tecnologia proprietaria Colines nel campo dell’MDO, nonché da soluzioni innovative e brevettate per la produzione di film MDO-PE con tecnologia cast. Il nostro portafoglio comprende diverse soluzioni per la produzione di film “verdi”, ad alto contenuto di riciclato o adatti al completo riciclo, in modo da soddisfare praticamente tutte le richieste del mercato”, ha dichiarato Nicola Lombardini, direttore della ricerca e sviluppo di Colines.
“Questa collaborazione è in linea con i recenti sviluppi per fornire soluzioni di imballaggio completamente riciclabili meccanicamente, con l’obiettivo finale di portare sul mercato un prodotto più qualitativo. Quest’ultimo potrebbe essere utilizzato come “materia prima” per l’industria del riciclo e infine diventare polimero RE:use, parte della gamma RE:clic che sostiene il nostro obiettivo di produrre il 30% di polimeri circolari entro il 2030. Questo sviluppo è stato reso possibile grazie alle nostre famiglie di Lumicene e Supertough che offrono eccellenti lavorabilità e proprietà meccaniche e ottiche”, ha aggiunto Olivier Greiner, vicepresidente della divisione Polymers Europe & Orient di TotalEnergies.
Colines e TotalEnergies collaborano per sviluppare imballaggi riciclabili non laminati che contribuiscono all’utilizzo efficiente delle risorse.
La linea per la produzione di foglia multistrato in PET riciclato da scarti post-consumo e destinata all’imballaggio alimentare venduta recentemente da Union a un trasformatore mediorientale è in grado di raggiungere produzione fino a 1.500 kg all’ora, è progettata per essere alimentata soprattutto con materiale riciclato e consente di ottenere una foglia con caratteristiche di trasparenza e brillantezza paragonabili a quella realizzata con materiale vergine. La linea è dotata di due estrusori e di un nuovo sistema di filtrazione in grado di trattenere anche le impurità di dimensioni più piccole presenti nella massa fusa. La testa e il blocco di coestrusione consentono di realizzare diverse configurazioni e numeri di strati. Completa la linea una calandra automatica orizzontale a 5 cilindri che consente di ottenere spessori da 0,15 a 1,6 mm. Tre le ultime realizzazioni di Union figura anche una linea per la produzione di lastre alveolari in polipropilene di nuova generazione e in grado di lavorare polimeri derivati dal riciclo post-consumo. La linea è in grado di produrre lastre alveolari con larghezza e spessori rispettivamente fino a 3.000 mm e 18 mm a una capacità oraria di 1.000 kg. Fanno parte delle sue dotazioni un cambiafiltri automatico autopulente e una pompa del fuso ad alta pressione, che consentono di lavorare stabilmente polimeri derivanti direttamente dal riciclo postconsumo, e un banco di calibrazione con tre coppie di piastre da 800 mm a posizionamento automatico e sistema “a velo d’acqua”.
Una veduta dall’alto della linea per la produzione di foglie multistrato in PET riciclato da post-consumo: dal basso verso l’alto si distinguono estrusori, testa e rulli della calandra.