ALUMINIUM 2022 Newspaper
www.aluminiumtoday.com continued on page 3 ••
Three days, one topic: when ALUMINIUM 2022 will open its doors in the Düsseldorf exhibition halls on 27 September one of the most exciting materials of our day and age will be centrestage. Sustainability, new mobility, additive and digital manufacturing, digitalisation, construction and engineering – ALUMINIUM will shed light on the most urgent issues of our time and flag up the versatile solutions aluminium has to offer for these as a material.ALUMINIUM 2022 will cover the complete spectrum of the aluminium industry in six exhibition halls. The big renowned companies will take part as exhibitors just as much as numerous SMEs and start-ups that make an invaluable contribution to the diversity and innovation of the sector. In this sense, the trade fair, which is already nearly fully booked, will serve as a truly comprehensive showcase. Norsk Hydro, HAI Hammerer, AMAG, ALVANCE, Rio Tinto, Alcoa, Trimet and Assan Alüminyum have confirmed their participation, to name but a few. Alongside many other household names there will also be a plethora of SMEs and start-ups ensuring enormous variety.
- Sustainability: Industries are facing increasing pressure to make their product lifecycles more sustainable and the circular economy a reality – and the material that is aluminium is almost ideally suited to do this. At the trade fair numerous innovations involving climate-neutral aluminium will be presented.
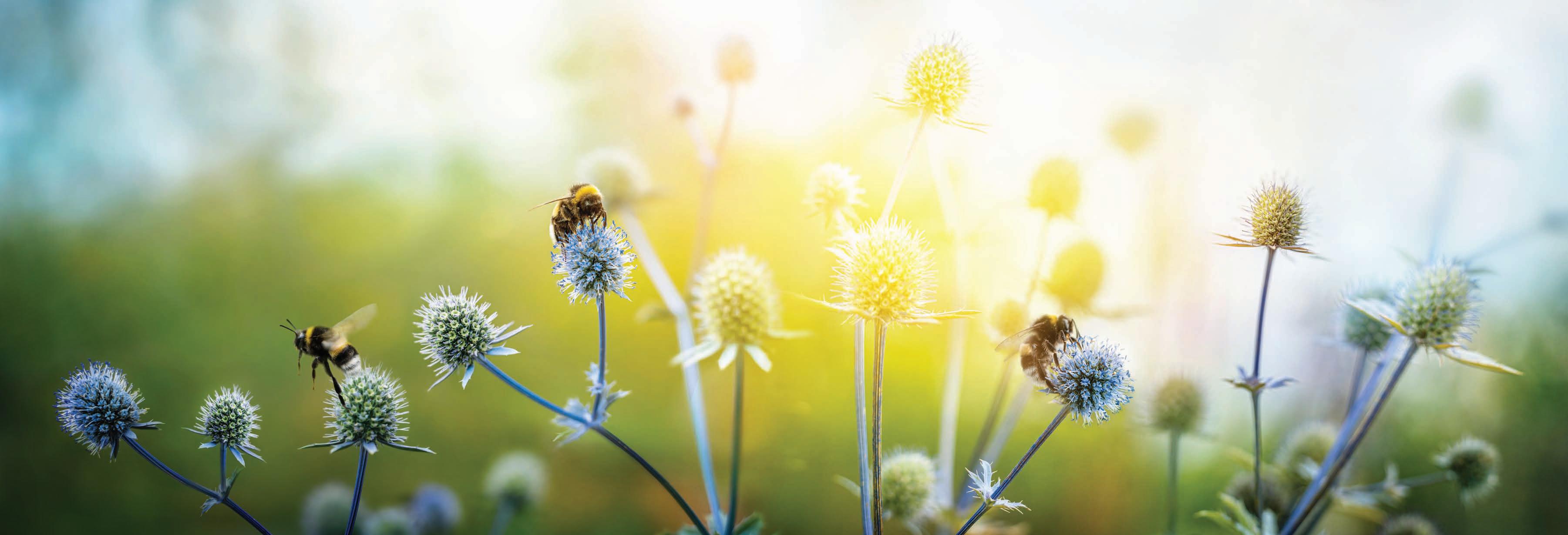
Solutions for the major questions
• Additive and Digital Manufacturing: 3D printing has long left behind its prototyping image: this manufacturing process has become long established in the industry – and is still far from being fully exploited. It provides a wide variety of technical possibilities allowing the material properties of the metal to be combined with the design freedom of additive manufacturing. In Düsseldorf large corporations as well as start-ups will highlight exciting avenues of how additive manufacturing opens up completely new opportunities.
The aluminium sector is undergoing massive transformation. This is why in terms of content ALUMINIUM 2022 will focus on the issues that will also continue changing this industry; and for which this material offers a host of exciting solutions.
• New Mobility: The development of e-mobility is rapidly changing the face of the automotive industry. At the same time, pressure is rising to reduce vehicle weight to cut greenhouse gas emissions. Both trends favour aluminium, which is getting more and more important as a material for the automotive industry. Vehicles are more environment-friendly with aluminium.
Curtains up:
• Digitalisation: More efficiency, more effectiveness – digitalisation is a long way from being exhausted. There are still many powerful levers waiting to be
The Journal of aluminium production and processing www.aluminiumtoday.com
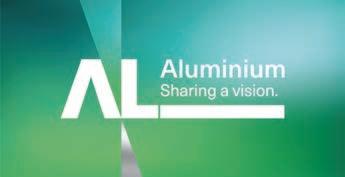
Aluminium Show Newspaper 1••
exploited by the aluminium industry – in a smart and environment-friendly way demonstrates the versatile technical
•
StockAdobe/EVERSTPhoto:
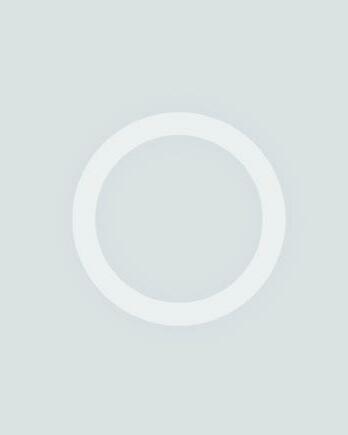


hydro.com Every step matters on the path to zero
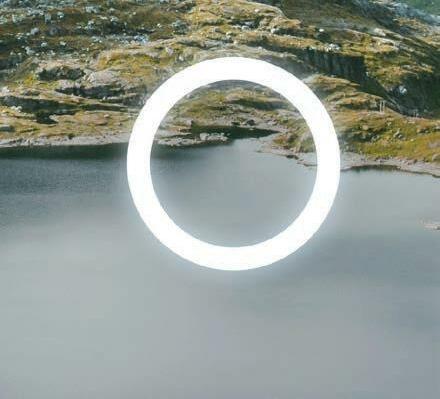
Visit us at ALUMINIUM Exhibition 2022
Come to booth #4C52 in hall 4 and experience our sustainability ambitions at the stand, exploring our exhibits, seminars and workshops.
•
There are many challenges ahead in producing in a way that will not harm our planet. We don’t have all the answers yet, but we can be your trusted partner in that everything we do works to create a fair and more circular economy with people and planet in mind. Contact us today to see what materials is most suitable for your next project.

•
•
•
We
Achieving climate-neutral products is the next design challenge. Low-carbon aluminium ticks all the boxes. can help your designs with: 100% recyclable material Eco design for your products EPD and full transparency, including all scopes, in our calculations Aluminium with a high percentage of post-consumer scrap Low-carbon aluminium
manufacturing with aluminium, organising the “Future Aluminium Forum”. Both partners will share intriguing insights and contribute to this focal theme with exciting speakers.Hall6of ALUMINIUM will be all about sustainability and recycling. Against the background of the outstanding properties this material boasts for the circular economy, the “Innovation Plaza Sustainability and Recycling” will await trade fair visitors with plenty of examples of best practice and innovations. And for this topic another excellent partner could be enlisted: the leading business intelligence company CRU with its highly specialised analysts – a household name for the aluminium industry. Both special shows will be accompanied by Speakers’ Corners with a packed programme of expert lectures, focused content and insights on the key questions related to additive manufacturing and/ or sustainability. They will provide more in-depth information and set the stage for presenting products and solutions. These themed stages will be curated by high-calibre industry partners who will also contribute to the theme with their expertise. Content drives the trade fair The ALUMINIUM Conference organised by Aluminium Deutschland will form an integral part of the trade fair from 2022. It will be staged under the heading of “Aluminium – the Solution Provider” in Hall 3 and its content will be guided by the central focal themes of the trade fair. The ALUMINIUM Conference will follow on from the extremely successful ALUMINIUM Business Summit and invite experts, key players and above all also the customers of the aluminium industry to the stage. More sustainability in new halls Sustainability will not only be one of the focal themes covered by ALUMINIUM – but the event as such is also committed to this goal. In the wake of the new exhibition concept all pavilions and special shows will be planned with a new stand construction concept developed by the trade fair organiser’s own company StandOut: the materials are selected in such a way that they can be completely dismantled after the trade fair and be re-used for following RX trade shows. Only damaged items or those customised for individual needs will have to be disposed of. Beyond this, ALUMINIUM 2022 will be held for the first time in Halls 1 to 7 of Messe Düsseldorf – a “move” that is also welcomed by exhibitors. This makes it possible to ensure new and even better hall segmentation as well as visitor guidance.
•• aluminium-messe.com CONTENTS www.aluminiumtoday.com Aluminium Show Newspaper 3•• Newspaper We are a company capable of supplying and improving your material handling and process flow through the carbon plant, pot room and casthouse. Mobile equipment solutions, descaling arms, ASCM + 1 514 687 7678 epiqmachinery.com info@epiqmachinery com Automation, robotisation, Heavy-duty material handling, processing and packaging Carbon plant and rod shop equipment Heavy duty automated guided vehicle (AGV) DISCOVER OUR BRANDS 1 Curtains up: ALUMINIUM 2022 4 Welcome to ALUMINIUM 2022 6 Industry Q&As 8 The time to reinvent the aluminium industry for a sustainable future is now 10 Plugging in to greener power for sustainability 12 Celebrating its 35th Company Anniversary 14 There is more to EPIQ than meets the eye 16 Roll Texturing for the Aluminium Industry 16 Celebrating 10 years 18 30 years already, and a new generation takes flight 20 Sorting Aluminium: Separating the brilliant from the good 24 Applying ‘thru-process’ optical profiling to fully understand, what is happening in your aluminium CAB furnace 26 Vortex® technology: frequently chosen by the industry 28 Aluminium’s journey to ZERO Carbon 30 Assan Alüminyum Continues to Invest in Sustainability Oriented Activities 32 The implementation of Fives’ SMARTVibro solution in Green Anode Plants 34 Maximise Productivity of your Cast House with RiA: Charge at the earliest and safest time, every time 36 Smart Solutions for a green, lean, and digital future 38 Higher efficiency and energy savings through high saw blade life and low chip waste 40 Aluminium decarbonisation – from pathways to action
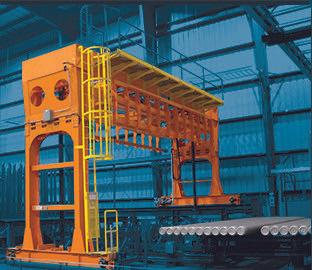
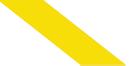

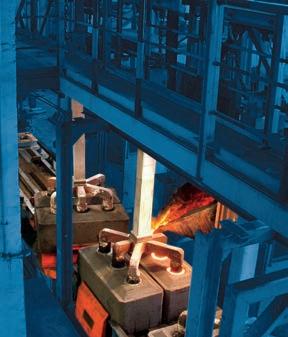
A showcase of superlatives Like all trade shows organised by RX, ALUMINIUM will also include hybrid elements and make available a digital trade fair portal. In addition to digital exhibitor profiles it will also be possible to follow the ALUMINIUM Conference stream live. Add to this, Audio Guided Tours, digital trade fair bags, Matchmaking, Emperia Leadscanning of all visitors and dashboards for exhibitors, to name but a few of the digital features.
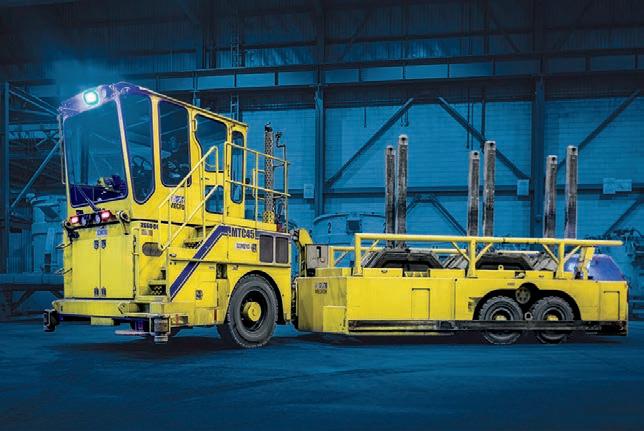
•• 4 Aluminium Show Newspaper www.aluminiumtoday.com Newspaper
Editor’s welcome
There are also a number of new initiatives and experiences taking place this year over the three days. One of which is the Additive and Digital Manufacturing Innovation Plaza, which I will be helping to host.
Dear Exhibitors and Visitors of ALUMINIUM 2022

Nadine Bloxsome Editor, Aluminium International Today T: +44 1737 855 115 E: nadinebloxsome@quartzltd.com

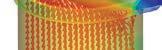
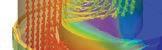
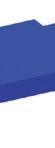
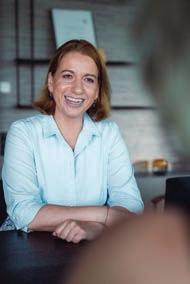

ALUMINIUM occupies a special place in our portfolio. On the one hand, because, as a truly world-leading trade fair, it is characterised by an exemplary international flair. On the other hand, it is dedicated to a material that is more promising for the future, more exciting and more likeable than any other. Aluminium has the amazing ability to provide great answers to several of the pressing questions of our time, especially in the context of sustainability, such as circular economy, mobility turnaround, recycling, and the development of more people-friendly urban centers. In all these areas, aluminium is a fundamental part of the solution and will be even more so in the future. The same applies to the topics of digital and additive manufacturing: Here, too, there will be no avoiding way around Ataluminium.thesame time, this industry seems to have given birth to a community in the truest sense of the word. A common desire has emerged around this exciting material, a joint pursuit of a better future and with this, a collective way of Whencommunicating.weputALUMINIUM 2022 under the motto “Sharing a Vision”, we also understand it in this sense as a clear message: As trade fair organisers, we are part of this community and we are definitely proud of that. Of course, a trade show like this is only possible if many partners work together in a spirit of trust. I would therefore like to take this opportunity to express my sincere thanks to all exhibitors, visitors, and partners – from associations to leading scientific institutes and trade media, like Aluminium International Today. They have all contributed to the permanent development of ALUMINIUM and to making it what it is Mytoday.special thanks go to those partners who, together with us, have ensured that we can experience a content program of unique density and quality at the show: Aluminium Deutschland, whose conference will be an integral part of the show starting this year. European Aluminium. The CRU Group, whose renowned experts play a key role in shaping the program of the Speakers Corner Sustainability & Recycling, the Aachen Center for Additive Manufacturing, and – last but not least – Quartz Business Media, the media company behind the newspaper you are holding in your hands right now. Together they are behind the program of Speakers Corner Additive & Digital AllManufacturing.thatisleftfor me is to wish you a successful, exciting, and informative ALUMINIUM 2022. We wish you a warm welcome!
When you hold this special edition of Aluminium International Today in your hands, you are part of an event that a great number of people have been looking forward to for a long time –including us as organisers.
Welcome to this very special edition of Aluminium International Today: The ALUMINIUM 2022 Newspaper.
I hope you enjoy this special publication, and it gives you an insight into some of the companies you can meet with at the show and learn more about their products and services.
The Aluminium International Today team, on behalf of Quartz Business Media, are honoured to work alongside the show organisers to create publications like this and work to share as much interesting content and information as possible across all platforms.
Make sure to stop by to hear from a great line-up of speakers and find out what opportunities additive and digital manufacturing offer the aluminium sector. Which new technologies are in the starting blocks, and which are already appearing on the horizon?
WELCOME TO ALUMINIUM 2022 InternationalJoin@AluminiumTodaytheAluminiumToday Group www.dewinterengineering.com SURE, WE COULD TALK ABOUT THE EFFECTIVE, TAILOR-MADE AND TURN-KEY SOLUTIONS WE REALISED ... But honestly? We´re engineers ... New furnace issues to tackle just interest us more. So, challenge us! New 60 t furnace with ultralow energy and maintenance costs Furnace upgrades: bath capacity, temperature control, fume extraction, door systems. etc. Pressure regulation E E E E Barbara Leithner COO RX Austria & Germany

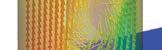
As you’ll see throughout these pages, we were inundated with contributions from companies exhibiting at the show and it looks like this year is set to not only display the most innovation the sector has ever seen, but we are all mainly looking forward to seeing friends and colleagues from across the industry again.
It feels like only yesterday we were producing the first edition of this newspaper for the 2018 show, but as we all know, a lot has changed in four years!
If you’re looking for all-round improvements in efficiency and sustainability across your entire plant – as well as a lower carbon footprint – then ALTEK’s complete, end-to-end Dross Management Solution is the answer. It recovers, recycles, reduces and repeats – creating the perfect circular economy. With no more need for specialist treatment centres or landfill. Even the Non-Metallic Product (NMP) becomes a valuable resaleable resource. ALTEKadvance: end-to-end Dross Management Solution. Altek Europe Limited, Lakeside House, Burley Close, Chesterfield, Derbyshire, S40 2UB, UK +44 (0) 1246 383737 altek-al.com/advancedsolutions Partnering | Thinking | Insight | Solutions Alu

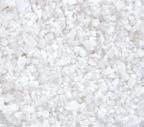
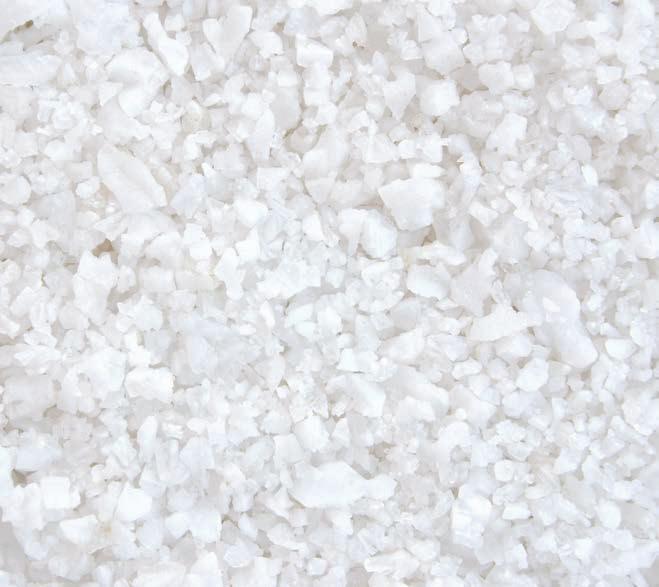
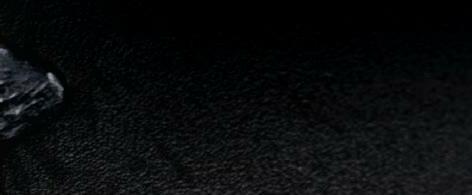
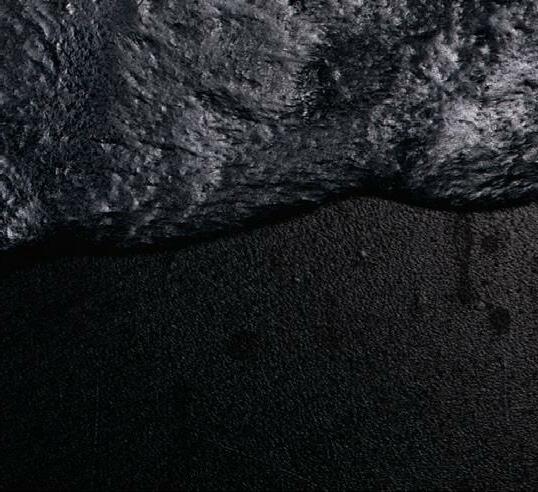
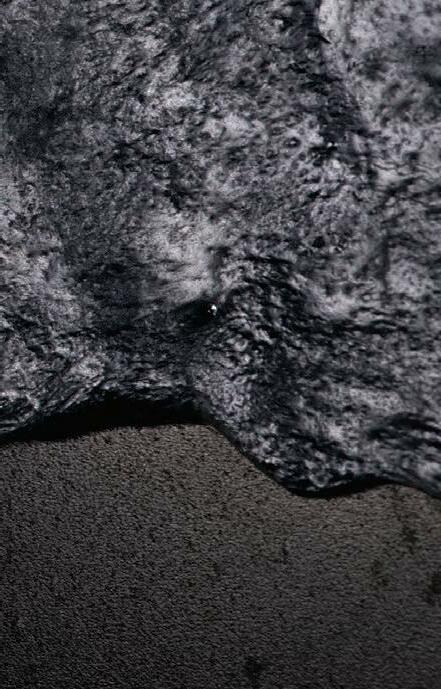
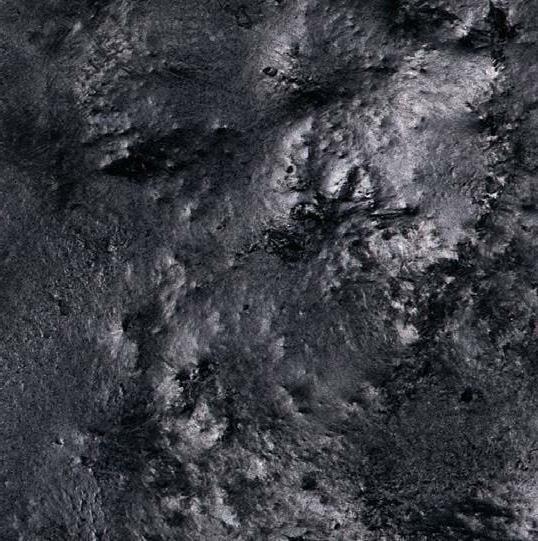
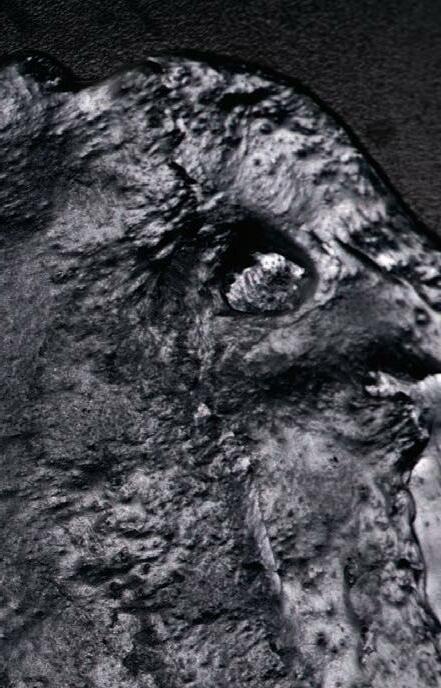
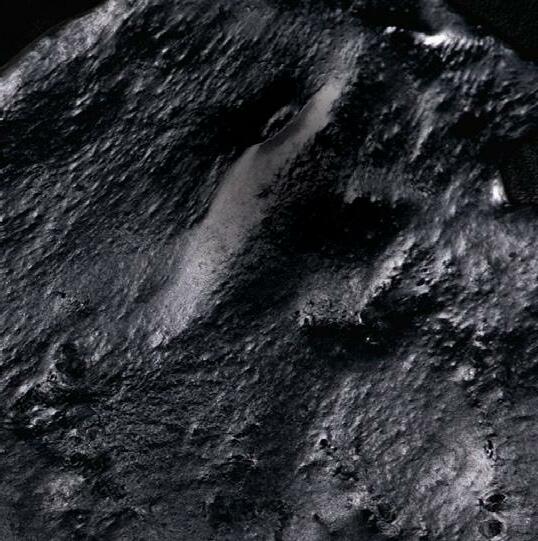
I highlight communities because so often when we talk about the industry, environmental issues and challenges are the most prominent with less focus on the local communities or the industry workforce but they are critical. We must ensure we are enhancing their lives, that they have opportunities, along with the skills and resources needed to aluminium is used is also a key part of an ‘ideal industry’. It is imperative that we use aluminium in sustainable applications that benefit the world, and once those applications reach the end of their life, we need to see the material coming back in a circular economy.
From what I see, it is something that has been embraced by the industry from blockchain for responsible sourcing to wearable devices to monitor occupational exposures, and this will continue to be adopted across the industry over the coming years.
How would you see Industry 4.0 and sustainability? Do you see them coming together?
What is your vision of an aluminium smelter or processing plant in five to 10 years’ time? Today Aluminium like all industries is being challenged to go green, pushing everyone out of their comfort zones which I think is a great. As discussed, heavy industry operates within rigid policies and procedures and the only way you to change this will be challenge people. My view is if it doesn’t challenge you, it doesn’t change you so if you want real change it has to be a real stretch target. I feel the green revolution is here to stay and you see this with most companies putting forth significant targets to reduce carbon emissions. Another thing which will accelerate both the digital and green transformations is getting CEOs (and CFOs) to make investments which may not have a clear financial payback. Being a CEO I fully understand that this is easier said than done but this is the mindset shift that needs to take place if we are to truly have a revolution. There will be times where you need to approve an investment but may not be able to justify it right away. The world is changing and changing fast, and we all must embrace this change if want to survive.
There are all sorts of technologies that are infiltrating day-to-day operations – some assist with addressing the many challenges we have, and I’m sure new challenges will also arise. What is your opinion on ‘headline’ issues?
What would you like to see from companies in the aluminium?
I think that Industry 4.0 technology is overdue in our industry. Unfortunately, there has not been a big focus on such initiatives in the past given the tough financial conditions in commodity markets per COVID. Also, within heavy industries you typically have many generations of technology around a plant. Smelters are a good example where you have multiple pot lines of different generations operating on different technologies. Therefore, it is not as simple as doing a Microsoft Windows update on your PC to bring everything up to speed.’. A second issue is that you can’t just start and stop some manufacturing processes, a smelter is a good example given it is a process flow operation which operates 24 hours a day 365 days a year. But there is an acceptance that the industry needs to move forward on digitalisation and Customers are demanding it. Customers and downstream companies will embrace Industry 4.0 technologies faster because they’re closer to the customer, and their demand dictates their successes. And this will push up stream companies like smelters out of their comfort zone to make it happen. I do believe Industry 4.0 will be fully adopted, I think the customers will push smelters that move faster and embrace such technologies. And for this to be successful the tone will have to come from the top with CEOs driving the vision and getting the buy-in of the whole organisation, so it becomes part of the company culture.
A big part of this issue is that everyone is managing from their own spreadsheets and systems are not integrated. If everyone would be more open and share their information in a real-time there would be a lot less of these issues or even if there are issues everyone would be aware of them and can adjust their plans accordingly.
So, I think as we move to digitalisation, we want to integrate everything, but this comes with a risk, such as cyber-attacks which could take down certain operations. In the case of a smelter this can lead to disaster very quickly if there is a power interruption for more than 3-4 hours. If this happens the pots “freeze” very quickly which can lead total stoppage of production and take many months to recover with a loss of many millions of dollars. However, I do feel the pros far outweigh the cons, but we just need to be conscious of the risks and manage those risks accordingly.
How have companies reacted to a more sustainable production?
The past few years have been incredibly challenging for companies. But it has been a really good few years in terms of companies focusing on sustainability and the risks to their operations or business models. As a result, we’ve seen a lot of action and momentum building around applicationssectorchallengesthefrombeen announcementsThereproduction. sustainablehavecompaniesacrosskeysustainabilityforourwithmanynewandsolutions.
Theprogress.waythat
The aluminium industry is a diverse industry. There are companies operating differently in many different parts of the world and with different levels of operational maturity.
Show Newspaper
What are customers looking for terms of the Industry 4.0/digital manufacturing concept? In terms of natural innovation, I think what you’re going to see customers demanding more real-time information. This means suppliers are going to have interfaces in place to talk with the Customer’s systems. For example, supply chain is a perfect example, today all we hear about is shipment delays.
There are probably one or two issues that often grab the headlines when we talk about sustainability in the aluminium industry. And actually, I think we as an industry have made some great strides over the past few years. With greenhouse gas emissions, for example, a couple of years ago we didn’t really know what a 1.5 degree aligned emissions trajectory meant for the sector and now we do because of the work we’ve done on the IAI GHG Pathways. The next big challenge is how we keep progressing – how do we implement new technologies, or push innovation?
This is also true with respect to waste management which is an area where the sector needs to keep finding new ways to deal with waste effectively and It’ssustainably.goingtobe important for us as a sector, to make sure that we don’t drop the ball on things because we’re only focused on the headline issues – we need to keep progressing all of the sustainability issues and keep looking for new ways to deal with them. What is your vision of the aluminium industry, or where would you like to see the industry in 10 years’ Intime? 10years’ time, I think I go back to my ideals for the industry, I expect an industry that is operating efficiently, and has minimal impacts on the environment and on people. I want to see an industry that has embraced its challenges and is dealing with them, but at the same time is growing and its community is stronger.
Pernelle Nunez, Deputy Secretary General and Director of Sustainability, International Aluminium Institute
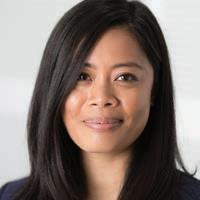
What does the ideal aluminium industry look like to you?
The ideal future for me is one where the impacts on both the environment and the communities that we are engaged with are minimal. A future where we have production happening in a sustainable way, meaning we are managing our waste, reducing our emissions, and engaging and enhancing the lives of both the workers on our sites and as well as the local communities and partners in those regions.
The other key thing that stands out for me is that over the past few years we’ve seen more companies moving out of the mindset that “this is a company issue. We’ll deal with it as a company. We’ll find a solution as a company” and moving towards strategic partnership. This is happening both across the industry and beyond the industry and is helping to ramp up some of the actions and goals for these Whencompanies. weare all working towards a shared vision, it really helps to accelerate progress.
What place does Industry 4.0 take in assisting with manufacturing?sustainable In my view sustainability should be at the heart of everything we do, so anything that we can digitalise should also improve sustainability as well. They should not be considered mutually exclusive rather a natural extension of your business. Are there any negatives to the digital age?
•• 6 Aluminium www.aluminiumtoday.com
Q&As Industry 4.0
In terms of what I’d like to see, it would be continued openness to sustainability. It’s not necessarily always about which technology or which solution you are implementing, but more about where you’re going and what are you trying to It’sachieve. alsoimportant we see continuous improvement across all the different sustainability issues. For our industry, greenhouse gas emissions always get the spotlight because it has the highest profile but I think, as many companies have said before, we can’t just have low carbon aluminium, we need aluminium that considers all other sustainability aspects.
Tim Murray, CEO, Cardinal Virtues Consulting (former CEO of Aluminium Bahrain)
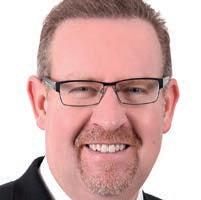
So, in conclusion you have 2 options “Change or be Changed”!
There are some negatives and I think when you look at a smelter it is considered a very rigid operation however that can be for good reasons. You have different departments operating on different technologies and there may be risks to integrating such operations. Power stations are a good example as they are generally very isolated in terms of their operating systems as unplanned interruptions are not acceptable. So historically the technology providers have operated in very closed systems to ensure stable 24 hour production.
How important is the Industry 4.0/digital concept to aluminium manufacturing and processing? Historically companies in heavy industry operate in a very slow moving and rigid environment due to the nature of the processes. So, while moving towards Industry 4.0 is important it will take some time for management to shift their mindset but there will be a payback and it will make companies more efficient and Hownimble.quickly, in terms of adapting, will it take for the aluminium industry to adopt the changes? I do think that it will take time given the nature of heavy industry and the large capx involved in such operations. However, with all the new technology initiatives today we have an opportunity embrace digitalisation and move things much faster but we as an industry must shift from a fixed mindset to a growth mindset. Do you expect the digital concept to be embraced by aluminium manufacturers?
+1-800-918-2600 | gcinfo@grancoclark.com | www.grancoclark.com Hydraulic Free : Fully Electric System. GRANCO CLARK’S ALL NEW Non-Hydraulic System utilizes servo actuators and pneumatics instead of hydraulics. This includes the Log Lift, Log Pusher, Pullers, Stretchers, Hot Saw, ECS Saw and many others. Our Hydraulic Free Systems are quiet, quick, powerful and boast incredible new features. Now that your energized, let’s talk! 1-800-918-2600 Tired of Maintaining Hydraulics?

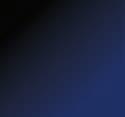




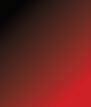

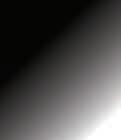
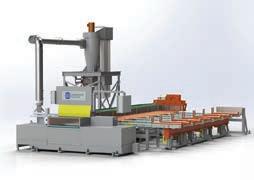
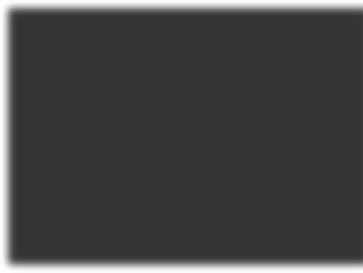
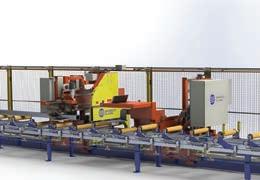
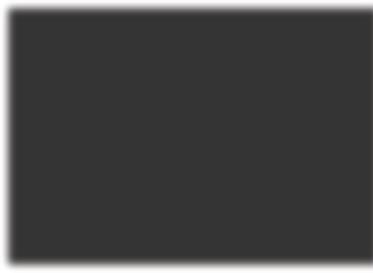


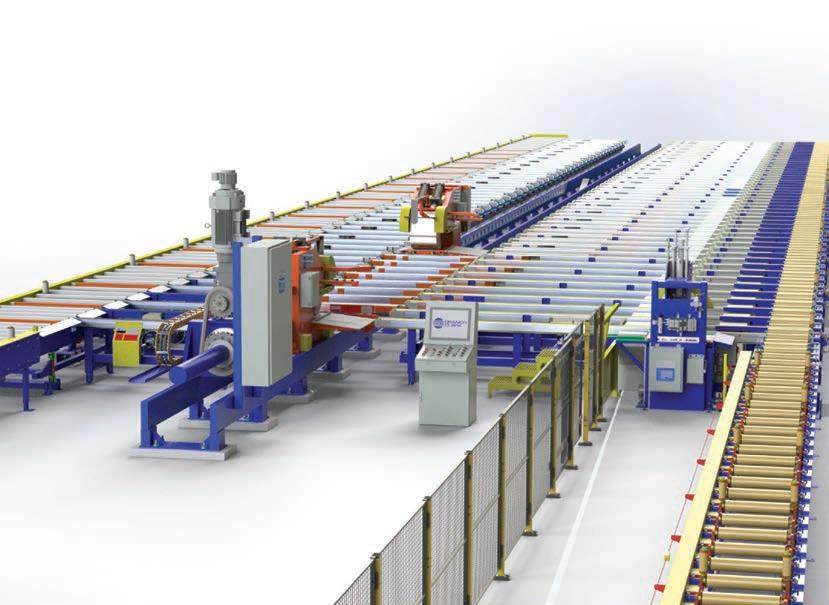
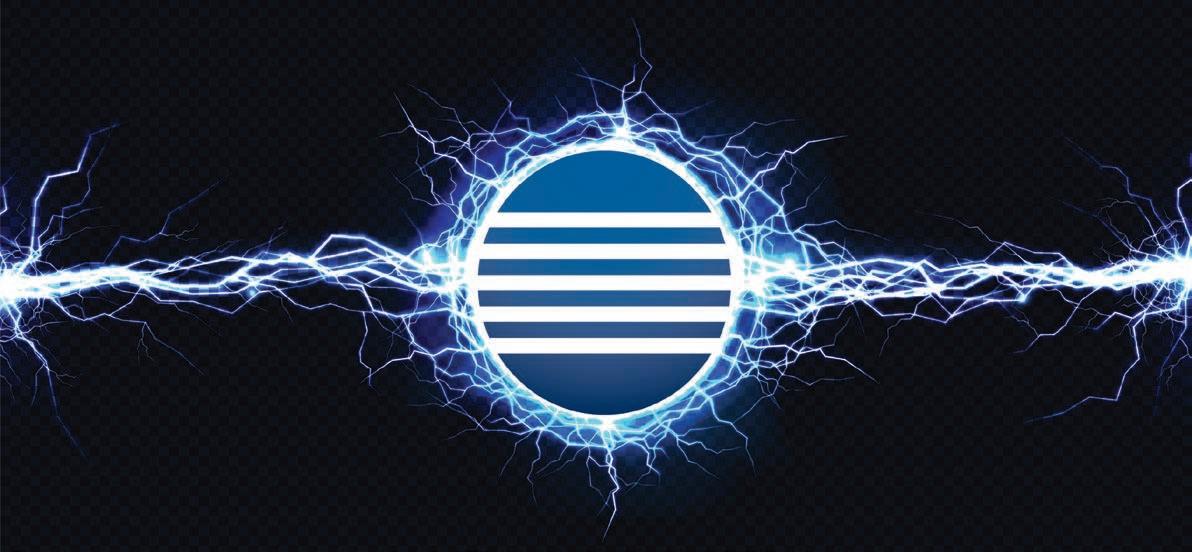
ELYSIS replaces the carbon anodes used in traditional aluminium smelting with inert, proprietary materials, to eliminate all greenhouse gas emissions from the smelting process, instead emitting pure oxygen. is new process can deliver an estimated 15 percent savings in production costs, as it eliminates traditional operating expenses associated with items such as calcinated coke, coal tar pitch, anode baking furnaces, and more. It also has the potential to increase production by 15 percent compared to traditional processes. Here’s the most exciting part: ELYSIS is already producing zero-carbon metal today at its Industrial Research and Development Center in Quebec, Canada. And that metal has already been used in commercial applications from companies ranging from Apple and Audi. e joint venture is on track to have a commercially available package for the broader aluminium industry from 2024. ELYSIS is a critical lever to decarbonise the industry, as smelting represents a majority of the emissions in the aluminium manufacturing process. However, it’s equally important to address carbon emissions in the alumina re ning process. Unveiled in 2021, our Re nery of the Future project aims to both reduce the capital cost of developing a re nery and enable decarbonisation of the alumina re ning process through a combination of processes and technologies, including mechanical vapor recompression (MVR) and electric calcination. With support from partners such as the Australian Renewable Energy Agency, Alcoa is adapting these proven technologies for use in alumina re ning. Together, these technologies have the potential to cut 98 percent of emissions from the re ning process and reduce fresh water use by up to 70 percent. With MVR, compressors powered by renewable energy turn waste vapor into steam that can be used to provide re nery process heat. Low-pressure steam is captured before it reaches liquid phase and re-compressed back to the high-pressure steam needed for digestion. is would avoid signi cant energy losses and save water. In fact, MVR alone has the potential to reduce an alumina re nery’s carbon footprint by 70 percent and eliminate up to 35 percent of freshwater usage. Electric calcination is a direct replacement of a traditional, direct- red calcination plant. Calcination is the nal stage in the re ning process. Currently, calciners are powered by fossil fuels, but with electric calcination renewable energy will drive the calciner, eliminating carbon emissions. e process also allows 100% of the steam generated by the calciners to be captured and reused, signi cantly reducing water use. Electric calcination also allows heat to be delivered via a thermal storage system, enabling the re nery to act like a battery to support activities to stabiliae the grid.We are proud that Australian governments are investing to assist in the testing and development of the technologies.
ELYSIS is a joint venture built around a zerocarbon smelting technology invented at Alcoa’s Technical Center near Pittsburgh. is technology represents the rst major smelting breakthrough in more than 100 years, reinventing the Hall-Héroult process rst developed by Alcoa’s founder in 1886.
Working with partners across the value chain, we are advancing a series of technologies that algin with our vision to reinvent. e industry is ready and eager for change. And so are we.
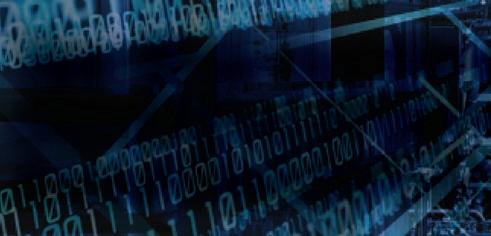
Standard aluminum ingot produced without any direct greenhouse gas emissions from Alcoa’s ELYSIS™ joint venture
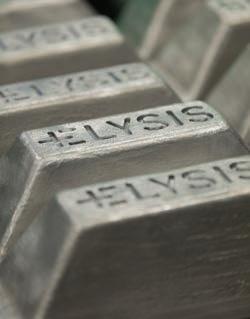
•• 8 Aluminium Show Newspaper www.aluminiumtoday.com
The time to reinvent the aluminium industry for a sustainable future is now
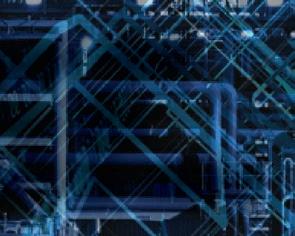
e aluminium industry has a critical role to play in the low carbon future. It can replace both heavier metals and plastics across a wide range of applications. Perhaps most importantly, it’s in nitely recyclable, and it’s no surprise that aluminium demand will continue to grow for decades to Accordingcome.tothe International Aluminium Institute (IAI), global demand for aluminium will increase by up to 80 percent by 2050. In order to ful ll its potential as a linchpin of the sustainable economy, however, the industry will need to rapidly to the IAI, the industry would need to reduce greenhouse gas emissions intensity for primary aluminium by more than 85 percent from a 2018 baseline to meet a Beyond 2 Degree Scenario de ned by the International Energy Agency. To achieve decarbonisation at scale will require breakthrough innovation that can fundamentally transform the energy requirements of our industry. Furthermore, reaching the 1.5 Degree Scenario requires a 97 percent reduction in greenhouse gas emissions intensity. Both scenarios include a 340 percent increase in post-consumer scrap utilisation. At Alcoa, we’re working on technologies that have the potential to decarbonise aluminium smelting and alumina re ning, as well as unlock new possibilities for post-consumer scrap recycling. ese projects align with our vision to reinvent the aluminium industry for a sustainable future and will help us achieve our net zero 2050 ambition for scope 1 and scope 2 emissions.
By BEN KAHRS Alcoa Executive Vice President and Chief Innovation Offi cer
On average, Alcoa’s global refining system has the world’s lowest average carbon dioxide emissions.
decarbonise.According
Alcoa’s Wagerup Refinery in Western Australia is one of the three refineries that Alcoa operates in Western Australia.
Unlocking new possibilities for postconsumer scrap recycling Research shows that the world’s increasing demand for aluminium will need to be met by an increase in recycling, and Alcoa is working to develop
Transforming the aluminium production process to decarbonise smelting and refining Our technology roadmap includes two initiatives that can fundamentally transform aluminium smelting and re ning – our ELYSIS joint venture and our Re nery of the Future project.
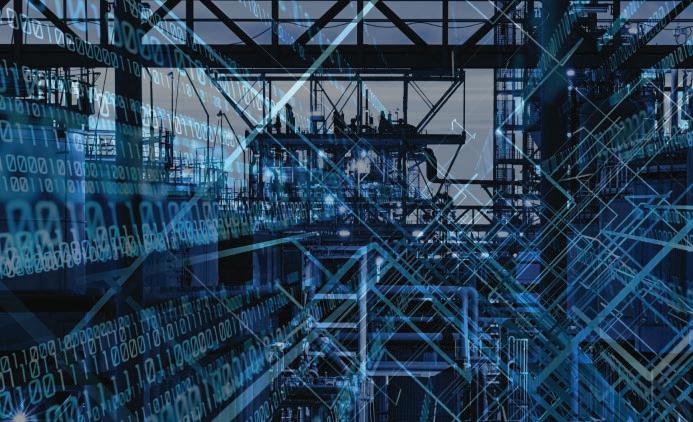
Aluminum rolling slab ingot is produced at Alcoa’s Mosjøen smelter in Norway.
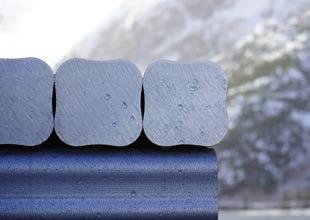
Molten aluminum metal is being poured at Alcoa’s Fjarðaál smelter in Iceland.
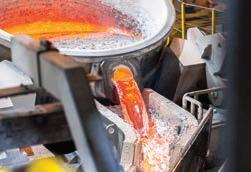
Ben Kahrs is Alcoa’s Executive Vice President and Chief Innovation Officer. He is responsible for Alcoa’s breakthrough Innovation and global Information Technology and Automated Solutions.
technology that can unlock more of our metal’s in nite recyclability. Our ASTRAEA metal puri cation process, the third major component of Alcoa’s technology roadmap, is designed around a new electrolytic process. It can take any post-consumer aluminium scrap, regardless of alloy combination, and bene ciate it up to high purity that exceeds the purity of primary aluminium produced at most smelters today. We are targeting the millions of tons of aluminium scrap contained in low-value automotive shredded scrap. is type of scrap is composed of impurities and alloys that contain other trace metals, making it di cult to recycle today. But our ASTRAEA process can change that, unleashing the potential of under-utilised aluminium.epuri ed metal created from low-grade scrap could then be usable for rigorous applications such as aerospace. Reinventing the industry for a sustainable future e work to decarbonise the aluminium industry is just beginning, but the path for Alcoa is clear.

GLAMAMaschinenbauGmbH Headquarters: Hornstraße19 D-45964Gladbeck/Germany Fon:+49(0)204397380 Fax:+49(0)2043973850 email:info@glama.de glama.de Costeffectiveheavyduty mobileequipment foraluminiumindustries... always thedurable solution GLAMAUSAInc. 60HelwigSt.,Berea,Ohio44017 Fon:+18774526266 Email:sales@glama-us.com
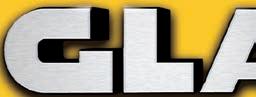



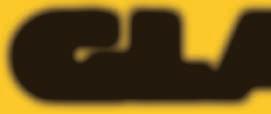
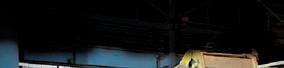

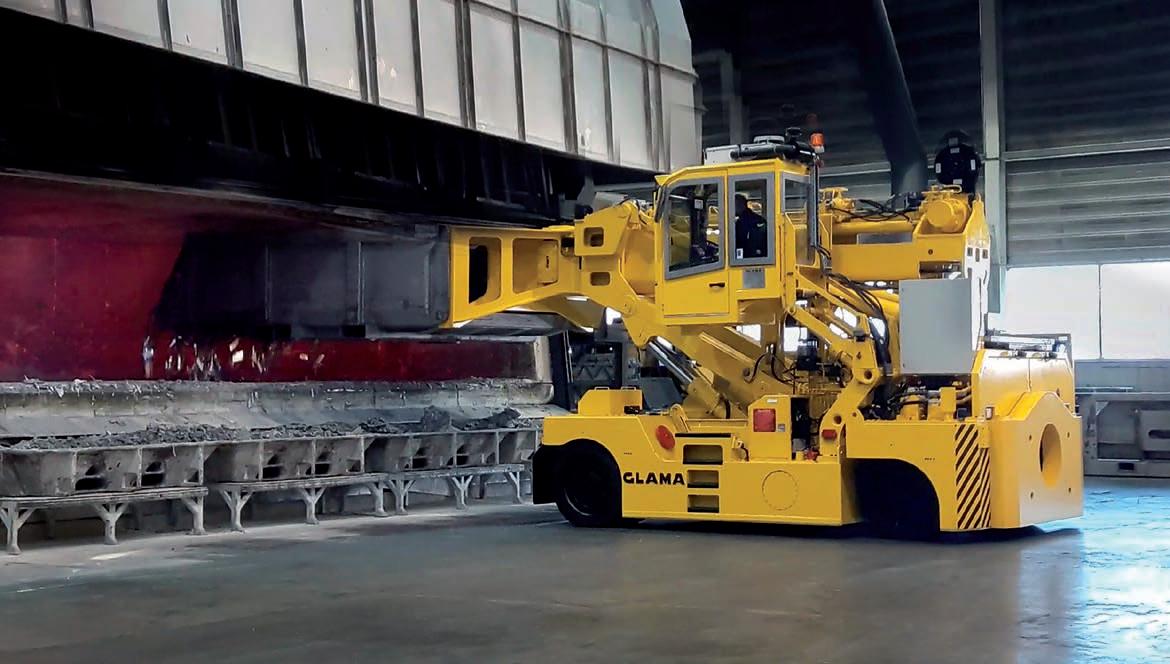
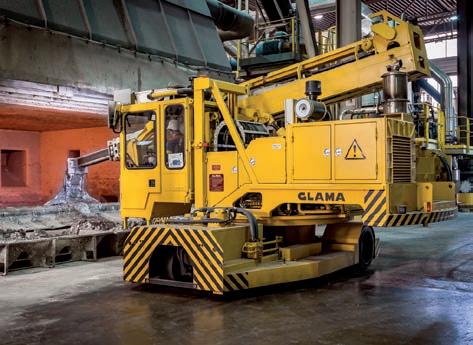

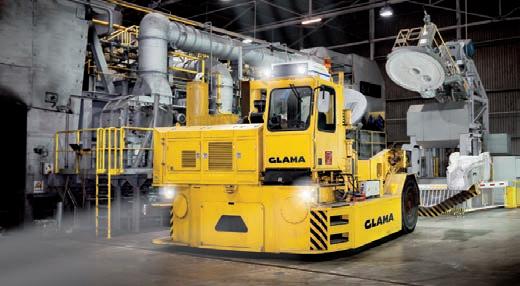
New materials handling solutions on Stand 3D10
Moving away from diesel – multiple benefits
•• 10 Aluminium Show Newspaper www.aluminiumtoday.com
The Combi-XLE model with a 5t lift capacity was launched in 2021. This multidirectional forklift combines emission-free operation with powerful performance for tough applications. It shares the same design features with its original IC-powered counterpart such as high ground clearance, large cushioned front and rear tyres, patented all-wheel traction and a spacious cab. These allow smooth operation on semi rough terrain whilst offering a high level of driver comfort. It also incorporates upto-the-minute technology such as the patented all-wheel traction that reduces tyre wear and load swing and enhances braking. Also included is a newly developed, patented EcoSteer System which provides a smaller turning radius and improved user experience. The Combi-MR4 is a multidirectional 4-wheel electric powered reach-truck, which incorporates Combilift’s new Dynamic 360° ™ steering. This provides rotation on each wheel, enabling seamless directional change of the truck while on the move and allows forward, sideward and crab steer mode, guaranteeing swift operation and excellent manoeuvrability. The wheel configuration of two drive wheels at the rear and two sets of smaller dual front wheels provides a platform height as low as 380mm, allowing otherwise redundant storage areas towards the floor to be used. The versatile Combi-MR4 can handle long loads as well as palletised goods with ease, and can load and offload from delivery trucks. Driver comfort and safety are also major considerations, and this new truck definitely delivers the goods from an ergonomic point of view: a high visibility operator cabin, multifunction control joystick, AC-electric power steering and joystick operated hydraulic mast functions all make for a smooth ride and straightforward operation. The articulated rear axle with two rear rubber drive wheels provides optimum traction for outdoor use, while still ensuring nimble and accurate truck placement. Sustainability begins at home Sustainability has always been an overriding priority for Combilift, and one which influenced the design and build of its new global HQ in Monaghan, which was officially opened in 2018. Construction of the 46,000 m2 facility began in 2015, and from the outset the aim was to incorporate the latest and most innovative and energy efficient manufacturing processes with a focus on sustainability and the well-being of the workforce. Starting with a clean sheet ensured that no compromises had to be made, and local suppliers were used wherever possible for raw materials such as the stone, cement and steel required for the initial build phase to minimise transport miles. A large proportion of Combilift’s annual procurement is still sourced within Ireland, which continues to support the local economy. Daylighting technology means that 30% of the roof space is covered in skylights, enabling staff to work in a natural daylight environment with 173% more white light exposure. Large floor to ceiling windows increase the overall natural light inside the building to 84%. When artificial lighting is required it is supplied by LED lights with PIR sensors allowing for daylight dimming and areas of the factory not in use to be switched off automatically.
A 1Mw biomass boiler is used to provide heating for paint spray ovens and assembly lines. The biomass is fuelled by supplier pallets, and 40 acres of willow have been planted on Combilift land by the factory to ensure sufficient ongoing supplies. Solar panels provide 185kW of energy which generate 10% of the daily electricity usage. A 110,000 litre rain harvest tank collects and stores rainwater which is used for jet washing and bathroom facilities.
Plugging in to greener power for sustainability
New electric models
•• www.combilift.com
The new Combi-XLE multidirectional forklift with 5t lift capacity – powerful performance for tough applications Combilift’s range of materials handling solutions continues to grow at a rapid pace

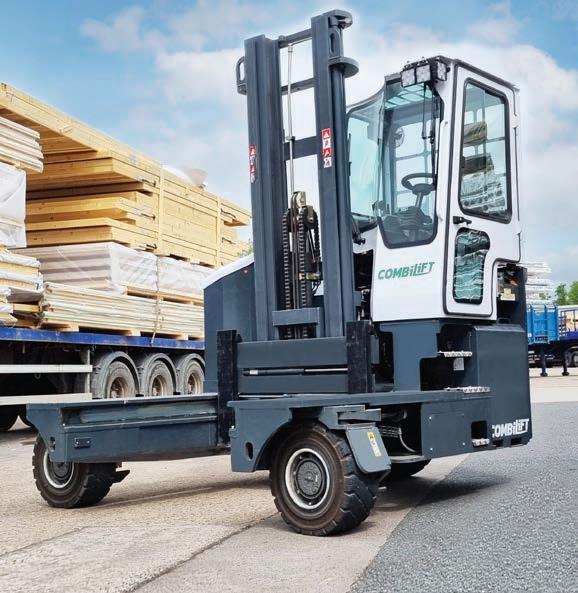
The Volatile Organic Compounds (VOCs) levels that are contained in solvent based paints have a detrimental effect on the environment and contribute significantly to air pollution. Combilift has switched to waterbased paints that were developed specifically for the company, and this technology has 74% fewer VOCs than regular solvent-based paints to keep levels as low as possible. And finally a few further statistics which dmonstrate the company’s commitment to recycling and reusing materials to conserve natural resources. 92% of all components used in the truck assembly are 100% recyclable; 90% of the electric trucks’ batteries are recycled; Combilift is on track to save over 473 tons of CO2 by using carbon neutral wood chip instead of gas for heating within the factory; parts are stocked locally by 300 dealers in over 85 countries, eliminating unnecessary airfreight. From a small corner of Monaghan, Ireland, Combilift is helping its customers in over 85 countries to do their bit for a sustainable future!
A major focus at ALUMINIUM 2022 is sustainability, the circular economy and the characteristics of aluminium itself as a future-proof material that can be easily and cost effectively recycled. Reducing emissions is also an issue that is becoming increasingly important for manufacturers of industrial equipment and vehicles and has led to an increase in the amount of electric powered options now available. This has been fuelled not just by more stringent legislation, but also by shifting public attitudes which has put pressure on companies in a wide variety of industry sectors to be more environmentally friendly. Combilift will be exhibiting and showing live demos of its new, electric powered materials handling solutions on stand 3D10.
When Combilift was established in 1998, diesel was universally acknowledged as the mainstream power source for heavy lifting equipment, but as is the case with the automotive industry, technology has advanced to offer more viable and greener alternatives. More than 60% of the trucks that come off the company’s production lines in Monaghan are now electric. Combilift is supporting its customers in their aims for more sustainable operation by expanding its electric range at a pace - in the last year alone it has added four new electric models to its portfolio. Combilift’s CEO and Co-Founder Martin McVicar: “The growing demand for electric power reflects the wishes of our customers, who are as committed to sustainability and a circular economy as we are.” Combilift further helps its customers achieve their environmental goals with its versatile multidirectional “3 forklifts in 1” models, which work inside and out, reducing fleet size and thereby their carbon footprint. A hallmark of all Combilift products is the ability to increase storage capacity without expanding the size of a facility – by working in narrower aisles and with taller pallet racking for example. This results in fewer new builds and lower energy consumption for heating and lightning, for a significant reduction in the physical and therefore carbon footprint.
Switching to an electric fleet from diesel is now a much more attractive option than it once was, and this is down to improved battery performance and technology, which enables ever increasing lift capacities, longer run times and much longer intervals between charging. So what is good for the planet can also be good for your Talkingbusiness.offinances: fuel costs are currently at an all-time high and this is even more of an issue as since April 1st this year it is no longer legal to use red diesel for non-road mobile machinery. The TOC (total cost of ownership) for electric powered trucks is therefore attractive. As electric powered trucks do not have traditional combustion engines or hydraulic transmissions, there is no longer any need to check and top up engine fluids or lubricants, resulting in fewer services and cost savings.Butit’s not all about money either. Just as on-street emissions from traffic has proved to be the cause of serious health problems, people need to be protected from pollution at their place of work. The British Safety Council has called for limits on the amount of exposure to diesel emissions, and an electric fleet obviously improves air quality and reduces the potential risks to employees and visitors on-site. Noise pollution caused by loud diesel engines can have a negative impact on the comfort and wellbeing of the workforce – and neighbouring wildlife - too.
combilift.com Safety Storage Efficiency To find out how Combilift can help you unlock every inch of your storage space and enhance the performance and safety of your operations. Contact Us Today Enhance the Safety, Storage & Efficiency of Your Aluminium Storage with Combilift Visit us 2022AluminiumatShow Stand 3D10 Combilift is the perfect fit for the Aluminium industry. Our versatile range of multidirectional forklifts and pedestrian forklift trucks are designed for narrow aisle operation, allowing you to maximise your storage, efficiency and safety.
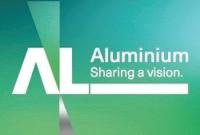




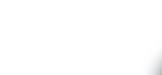
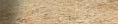
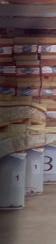



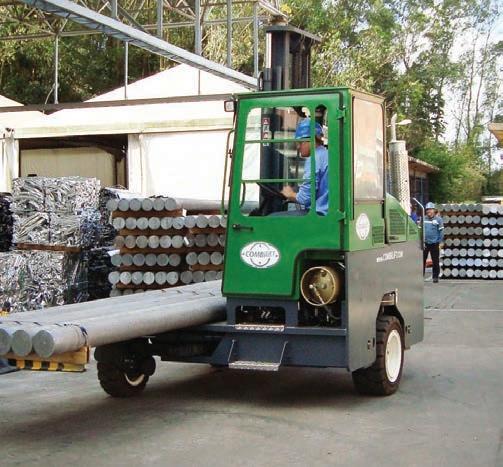

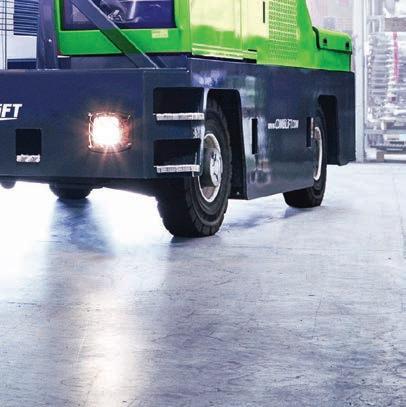

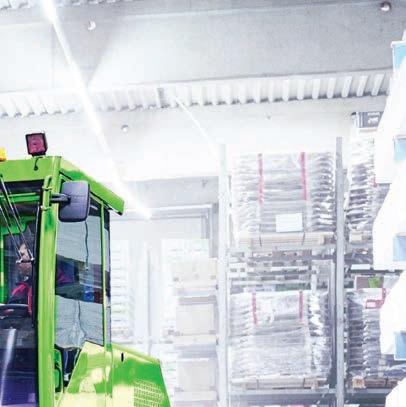
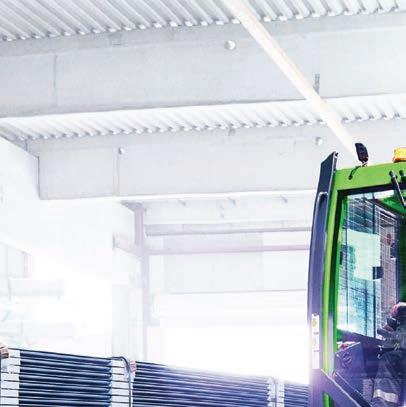

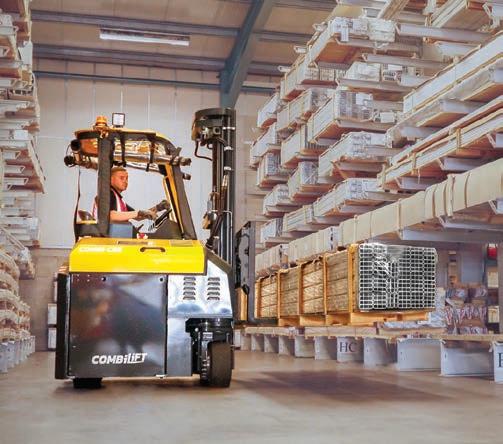
Mr. Kook-Heon Ahn CEO, KNF

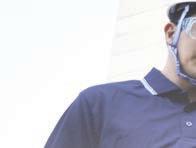
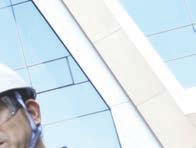
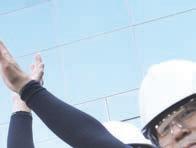
Top Notch, No.1 Asia Aluminium Supplier KNF maintains strong partnerships with world leading Aluminium mills especially with Arconic(Alcoa), Novelis(Aleris), Fusina and Lamial etc. This is why KNF supplies high quality Aluminium with competitive unit price to customers.
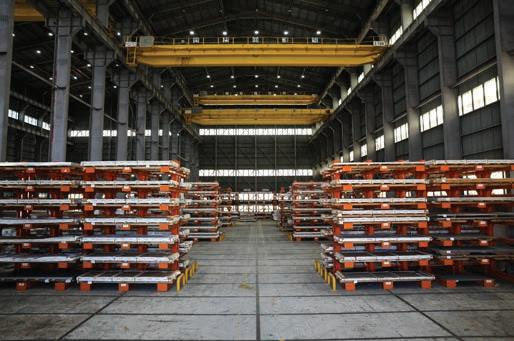

Celebrating its 35th Company Anniversary
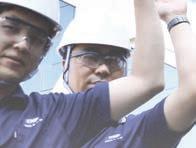
In order to follow the growing concern about the ethical impact and sustainability, KNF is also striving to become an ‘ESG management’ company.
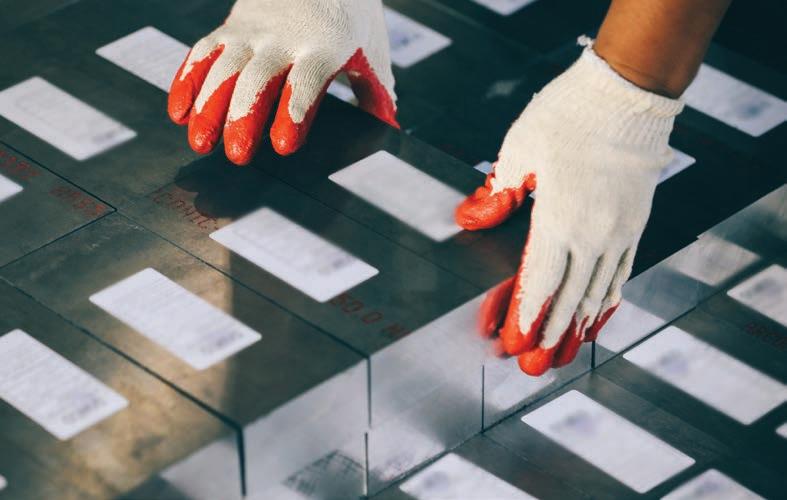
•• 12 Aluminium Show Newspaper www.aluminiumtoday.com
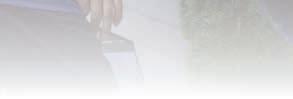
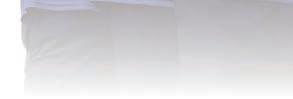
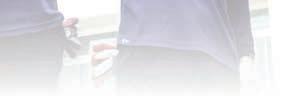
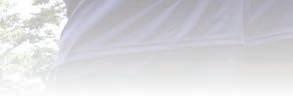
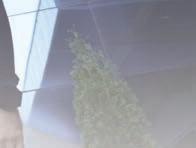
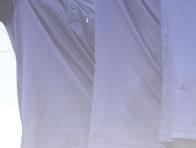
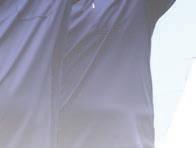
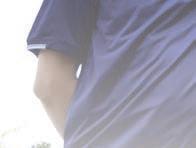
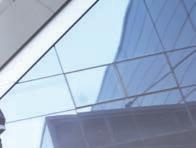
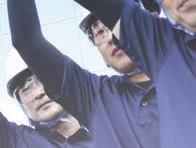


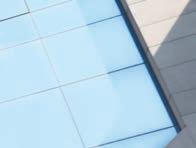

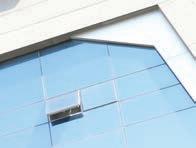
Recently ourourcontinuetheKNFpricequality,materialsourprosperityKNFdueextremeexperiencingmaterialssupplyingisvolatilitytotheCOVID-19.hasvisionandtosupplyAluminiumwithhighcompetitiveonschedule.willkeeppassionandtoincreaseefforttoachievegoals.
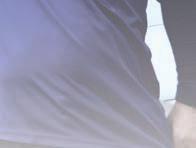
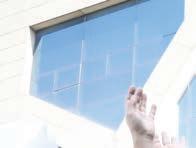
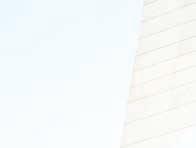
Technology Investments for the High Quality KNF continuously determines the compliance and effectiveness of the quality system. It achieved Aerospace Standard AS9120, ISO9001 quality management certification, the environment certification of ISO14001 and ISO45001 occupational health and safety management systems as they value the safety most. To meet their value, KNF constantly invested to high technology machines like Automatic Aluminium precision cutting machine and vacuum lifters. This new step shows that the company is committing more innovative and smart ways. This is how the company provides high-quality Aluminium products for each customer’s satisfaction.
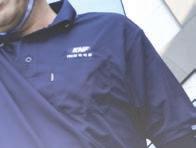
KNF (Korea Non-Ferrous Metals) is an Aluminium total service provider since 1987.The company (also called as Hanbee in locally) provides metal processing, warehousing and becomes one of the most comprehensive metal service centers in Asia. It supplies the world leading Aluminium plates, sheets, extrusions for various industries such as Aerospace & Defense, Semiconductor & Display, Marine & Silo and Automotive. KNF was honorably selected as a Korea’s Ministry of Labour Enterprises of 2021 and 2022 Hidden Champion Company by South Korean government.
Leading Company As the company develops and the demands in the Aerospace & Defense industry increase, KNF is now planning to expand the facilities in Sacheon Branch which is the Aerospace & Defense material center.
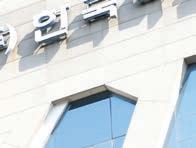
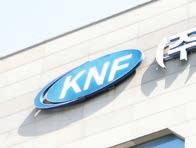

Power precisionmeets

























































Introducing the next generation X-TRACT™ for aluminum sorting With even higher throughput and sorting speeds up to 3.8 m/s, the next generation X-TRACT™ delivers unrivaled performance in separating aluminum from heavy metals. Get factsthe
































































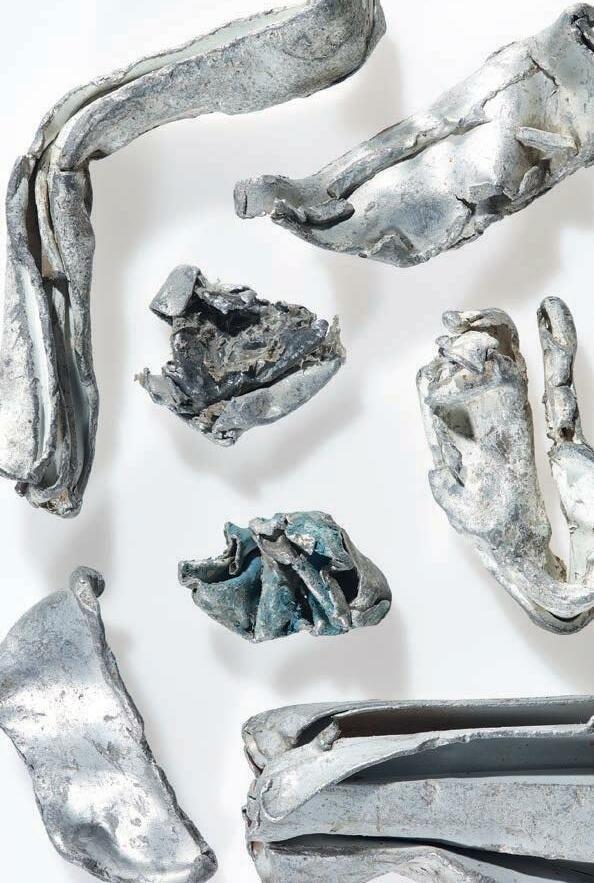
•• 14 Aluminium Show Newspaper www.aluminiumtoday.com
One of the major reasons behind the 2021 merger of Mecfor Inc. and Advanced Dynamics to form EPIQ Machinery was our future ability to provide a wider range of innovative, sturdy, and high-performance equipment.EPIQMachinery adopts a global solution approach that integrates fixed and mobile equipment in overall solutions/systems to reach better operational efficiencies and optimum levels of automation. This allows us to live our mission and design the best solutions to suit our clients’ needs. We understand that our customers are facing multiple challenges simultaneously. While safety, low emissions and energy savings are at the core of decision-making processes, Primary Aluminium Smelters are investigating ways to increase capacity through amperage creep while Secondary Smelters are investigating ways to improve the management of various recycled waste. Everyone also needs to find ways to cope with a shortage of personnel and ongoing supply chain issues. Therefore, doing business with a versatile and diversified equipment supplier such as EPIQ helps provide a global vision to streamline the progress of expansion and performance improvement projects.EPIQMachinery cumulates years of expertise with brands that are recognised in the industry: AD, MECFOR, BROCHOT and more recently AGV. Aluminium production is a batch process with multiple stages; at EPIQ we have the ambition to connect all stages of a smelter to maximise the process flow through fully automated Heavy Duty Global Material Handling Systems integrating both fixed and mobile equipment. Our passion for challenges drives our team to explore alternatives in regards to layouts and available technologies in order to maximise the level of automation, that with the objective of having the best production rate at the lowest operational costs possible.
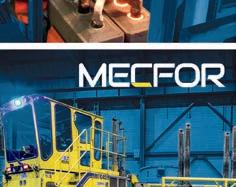
Another example demonstrating our integration capabilities is our anode management system which coordinates communications between the various carbon plant processes and manages the anode storageManagingfacilities.anode quality, integrity and output can be challenging. Trust our Anode Slot Cutting Machine (ASCM) to help reducing the number of rejected anodes and to assure a constant quality of anode density.
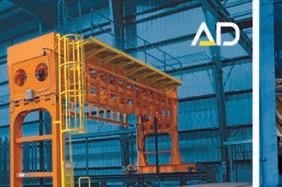
By: Yannick Beaulé, Chief Revenue Office, EPIQ Machinery*
When the current flows: potroom Not only can we work in improving anode yield; but we can also work on the quality of the pot rebuilds using our world leading BROCHOT Pot Ramming Machine. Still today, the unique design favors an optimal compaction making sure that all joints are sealed properly. EPIQ ‘plug-n-play’ approach makes it quicker for the on-site installation, minimising impact on production. You can rely on perfectly reproducible compacting pattern by setting parameters.
Conclusion Moving Forward, our main objective is our customers’ satisfaction both in terms of health and safety and in terms of performance of our equipment. With our Mobile Solutions and our ability to better automate handling equipment, we are confident that we offer a right balance between efficiency, costs, and technology. EPIQ is structured to be able to take on large scale turn-key projects while at the same time has the flexibility and agility to design and implement made to order (custom) solutions for specific customer needs. EPIQ blurs the lines between being a technology company and a heavy machinery manufacturer, by continuously supplying new and innovative technologies. These integrations and innovations open new opportunities for reduced environmental impacts, increased efficiency and productivity and improved operator safety for the aluminium smelter of the future.
All shapes and sizes: Ingots, slabs, sows, billets: finished product sector Between the BROCHOT and AD brands, EPIQ Machinery can work from casting lines up to finished goods handling. As a FANUC robot integrator, EPIQ can add more automation in the process, especially for the casting line.


Cleaned cuts facilitate the gas evacuation and promotes a better electrolytic process. Once the anode is ready to leave the rodding shop, EPIQ MECFOR hauling solutions come into play. Either the client seeks for conventional haulers, electric or AGV; we can work all types of mobile hauling equipment.Weareincreasingly invited upon to carry out engineering mandates during which we address an overview of the client’s process, identify bottlenecks, and consider updates by integrating new technologies, by adding new equipment in the process line or rework the layout. Each situation is unique and deserves to be analysed properly.

There is more to EPIQ than meets the eye
Once the molten aluminium is tapped out of the pots and transferred into ladles; it is time to haul it to the casthouse using MECFOR Molten Metal Haulers. Over the years, MECFOR brand has also designed Crucible Tilting Haulers, Molten Metal Transfer by Pressurisation technology and Bath Tapping Vehicles. Haulers can be narrow or wide. One tractor is coupled to specialised trailers and loaded with technologies (sensors, 360-degree camera, ID card, telemetry features, and more).
Starting point: carbon plant At EPIQ, we have an open and collaborative approach with our customers. It always starts by listening to our customers’ needs and where they are at in their evolution. All operation assisted technologies that can relieve burden for our customers are studied and challenged as part of our R&D product improvement. We work with the customer to develop the best technical solution: our customers know their processes and we know how to tie them together for optimised efficiency. Our knowledge of equipment designing combined to industry requirements gathered over time allows us to add value to our customer’s operations. Under the BROCHOT brand, EPIQ can deliver a complete Rodding Shop of all modern pre-bake anode technology. Combined with the advanced expertise of the AD line of products, producers have access to world leading Anode Handling and Cleaning Systems. In aluminium smelters, all of the anode production processes are connected through a highly automated system. Numbers of new Industry 4.0 technologies are ready now for integration to improve product quality, reduce energy consumption, increase operator safety and ergonomics. For example, EPIQ designed a quality inspection station with a vision technology using 2 cameras and our own vision software based on proven artificial intelligence and learning machine algorithms.
The infinite malleability of gray metal: casthouse Aluminium is omnipresent in our life. Its uses have multiplied in several new hightech sectors. Some require speciality alloyed aluminium prepared in the foundry sector. Whether you are looking for a dedicated rail bound charging machine or Smart Casthouse solution, EPIQ can help make furnace charging, tending and cleaning operations more efficient. We offer Operator’s assistance technology and Furnace Protection System (FPS); all to bring greater efficiency and better control over operations. At EPIQ Machinery, we are improving our Smart Casthouse solution by introducing a new vehicle called EPIQ MECFOR Furnace Vehicle (MFV) and by increasing embedded technologies onto our equipment. Our Smart Casthouse solution helps facilities understand the equipment usage, schedule maintenance time, tool usage and consumption rates, and added personnel safety in and out of the equipment. In the coming months, EPIQ is to jointly to present with Dynamic Concept an innovative, energy-efficient robot to automate furnace skimming, stirring and cleaning with programmed and flexible operation. Through its geometry and its ability to produce different patterns, the Automated Robotic Furnace Tending (ARFT) will improve the quality of furnace tending. It will cover the entire surface without omitting an area in less time. In addition, precise force control will help to prevent refractory breakage. Battery-powered, ARFT will offer great adaptability to any environment and will have flexibility, thanks to the integration of an artificial vision system. These are just a few of the benefits our customers are seeing, and this helps generate more profitability to the end user.
EPIQ AD has state-of-the-art billet homogenisation system integrating volumetric inspection station, inline centerline crack inspection, billet sawing, laser marking and stacking robot. What else to expect MECFOR, the mobile equipment line of products has evolved over the past few years. Our cast house solution has become much more attractive to clients thanks to the series of smart tools that ‘talk’ to the vehicle and that enables the equipment to adjust its speed, movement, limits height and acceleration depending on the type of tool (e.g.: stirring blade versus charging box) and on the vehicle position (in front of the furnace or driving around the plant). The vehicle ‘thinks’ for the operator and allows for a safer and better operation. Electrification and robotisation; new technologies that will help aluminium producers reduce their carbon footprint is another area where we are investing time and effort. EPIQ Machinery is actively working on its fully electric line of vehicles and looking into broadening its Automated Guided Vehicle (AGV) offer. On the other hand, material handling is sometimes an afterthought, especially after expansions or increase in demand. With the AD brand, EPIQ Machinery is helping our customers increase casthouse automation in existing plants and is active in assisting our customers design and build the casthouse of the future for greenfield smelters and re-melters. EPIQ Machinery works with customers in a collaborative effort to assure today’s demands and needs are met and that designs and processes are upgradeable for future requirements.
* ABOUT THE AUTHOR Since the merge between Advanced Dynamics and MECFOR back in August 2021, Yannick Beaulé fills the Chief of Revenue Officer (CRO) position at EPIQ Machinery. Everyday, he works to define the growth plan and oversees its implementation through out all commercial spheres of the company. He participates in mergers and acquisitions as well as partnerships. Among other things, he is responsible for creating, together with the Sales, Aftermarket and Spare parts teams, an efficient and dynamic network of partners, agents, and distributors. His passion for challenge translates into a close to EPIQ’s client’s approach for each step of the client’s journey.
Newspaper
ST. LOUIS, MISSOURI, USA 800 325 7075 | www.gillespiepowers.com | 314 423 9460 ✓SINGLE CHAMBER / MULTI CHAMBER FURNACES ✓SCRAP DECOATING SYSTEMS ✓TILTING ROTARY MELTING FURNACES ✓SCRAP CHARGING MACHINES ✓LAUNDER SYSTEMS ✓CASTING / HOLDING FURNACES ✓HOMOGENIZING OVENS ✓COOLERS ✓SOW PRE HEATERS ✓REPAIR & ALTERATIONS
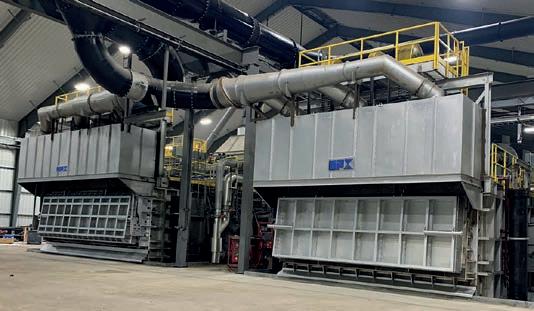
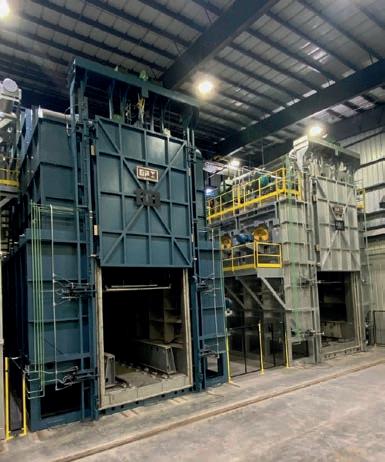

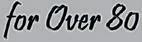

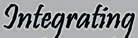
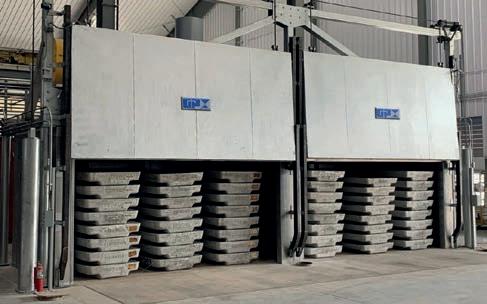















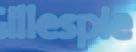
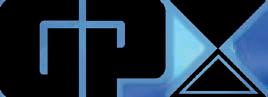
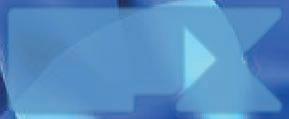
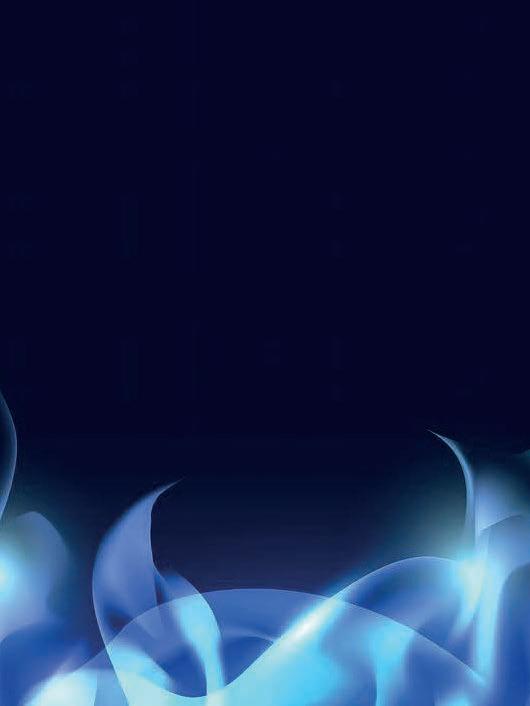
Roll Texturing for the Aluminium Industry
Microscopic image of a 1.2Ra EDT texture - the typical roughness for the aluminium industry demonstrating the above texturing characteristics
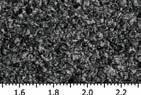
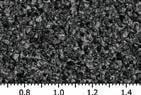
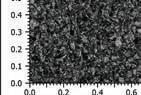

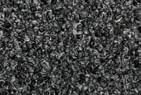
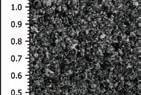
••
The Sarclad Rolltex ECO provides textures that are both stochastic (i.e. random, without lateral pattern) and isotropic (i.e. not varying in magnitude when measured in different directions). These characteristics are inherent in Sarclad EDT texturing, nut not
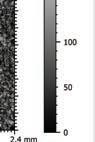
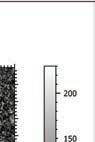
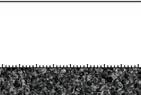
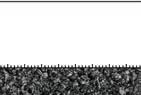
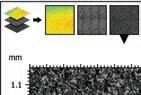
Umut Başaran, Sales and Marketing Manager of VIG Metal, aligns the companies Global Goals for Sustainable Development with company policies such as environment, quality, HR and OHS; “This year, our motto is “Sustainable Vision, Sustainable World” and “Our Biggest Investment is World”. Based on these values, we created the VALU brand for the aluminum segment. Behind the work we do, we strive to leave a better planet for the future, because we believe that a sustainable world is possible with a sustainable company vision.” He says “In order to create ‘value’ and ‘trust’, we aim to be a preferred supplier by offering our customers the right combination of quality, innovation and operational excellence, and costing. We are also mobilising all our resources to create a high-tech, modern and safe working environment where our employees will be proud to be members of our family.“ VIG Metal will meet with its partners and visitors at its stand in Hall 4A24 in ALUMINIUM 2022.
The benefits of the Sarclad Rolltex Eco variant: Strip surface preparation for coating Removes minor strip defects or Offimperfectionsersbetterstrip surface “keying”, aiding better bonding of surface coatings
VIG Metal is located in Kütahya Industrial Zone with an open area of 57.000 m2 and a closed area of 27.000 m2. 70% of the aluminium lines they use in production are designed and developed by the group company VIG Makina.
VIG Metal, one of Turkey’s largest aluminium sheet and coil producer, has been increasing its capacity day by day since 2012.

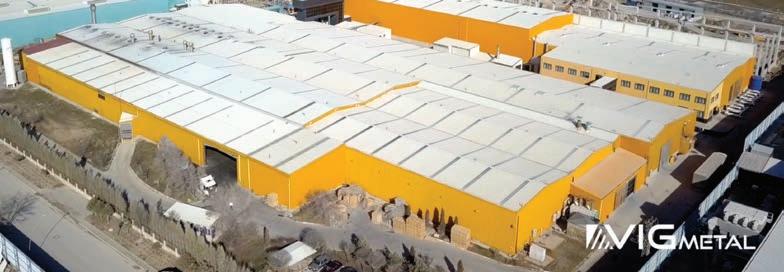
VIG Metal is also increasing its employment rate with its expanding production volume, supporting the development of employees and women’s employment with qualified trainings.
Rolltex ECO - The preferred industry solution for Aluminium mills.
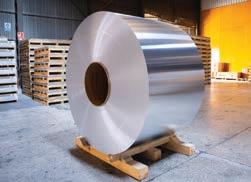

RolltexSarcladECO 10Celebratingyears
• Achieves the highest quality strip appearance (stochastic & isotropic) Strip formability improvements Retains even coating of lubricant for the Reducespress flow friction in the press Retains surface appearance after forming Further information available at: sales@sarclad.com | sarclad.com
VIG Metal, while producing with continuous casting and high-tech cold rolling machineries, adopts sustainable methods at every stage of the production process. Adopting reuse and recycling systems, the company focuses on reducing waste at its source and using energy and natural resources efficiently. Beyond the savings measures used in the factory, it tries to reduce its carbon footprint with solar energy systems investments, renewable resource investments and digital transformation systems. Celebrating its 10th anniversary in 2022, VIG Metal reached a volume of 40.000 tons with new investments such as annealing furnaces, casting line with a width of 1500mm production capable and new high-tech cut-to-length line with a width of 2000mm production capable. Comparing its first year in production with a capacity of 12.000 tons in 2012, to its export volume which reached 77% this year with the special products made for the leading companies in the global market, VIG Metal grew more than 300% within 10 years.
Total Aluminium content history & forecast, lbs / vehicle laser texturing and are critical in ensuring consistency of body panel appearance through the stamping process.
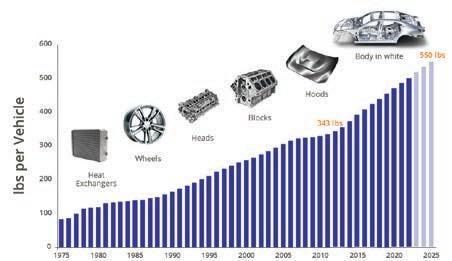
For surface critical applications such as Automotive external panels and white goods, Sarclad’s Electro Discharge Texturing (EDT) technology ensures the optimum textured finish is transferred on the strip from the rolls. The Rolltex ECO (12 electrode texture head) has been specifically designed for the aluminium industry, providing precision texturing for up to 1,000 rolls per year.With aluminium consumption in automotive body in white applications increasing year on year, it is imperative that the rolls are optimally textured to imprint the required roughness and peek count onto the aluminium strip. These textured rolls are critical in the production of aluminium strip for body in white automotive panels, where the texture is ‘imprinted’ to provide lubrication for forming and an aesthetic appearance suitable for the highest surface critical applications.
•• 16 Aluminium Show Newspaper www.aluminiumtoday.com Newspaper



VIG Metal while exporting aluminium to many different European countries such as Germany, Italy, Poland, Austria and Netherlands and to different business units such as construction, automotive, white goods, energy, distributor market, is ranked as the 10th Fastest Rising Company in the Top 1000 Exporter Companies list of 2021 announced by the Turkish Exporters Assembly (TIM).
•
Sarclad UK sales@sarclad.com sarclad.com World leading technology solutions for Aluminium rolling mills Roll inspection Roll texturingsurface World leader in EDT texturing of rolls for strip supply into the highest grades of exposed automotive and white goods Surfaceapplications.andcoreroll defect detection for aluminium and steel rolling mills, utilising eddy current, compression and creep wave technologies. Sarclad North America sales@sarcladna.com Sarclad China sales.china@sarclad.com Sarclad India sarclad.india@sarclad.com










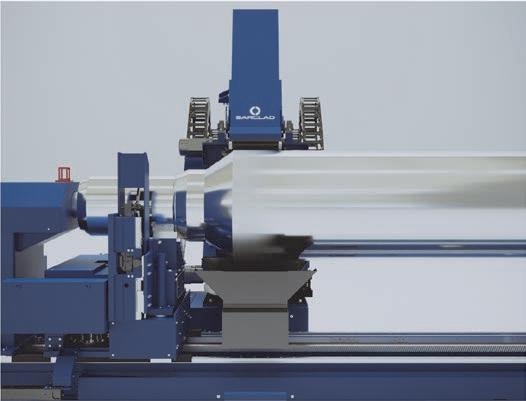
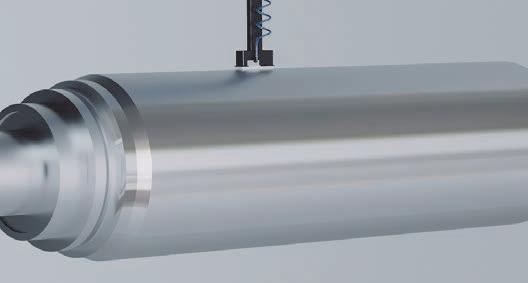
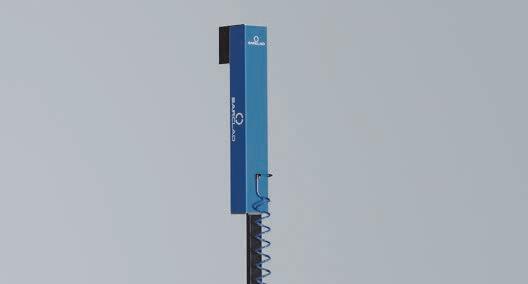
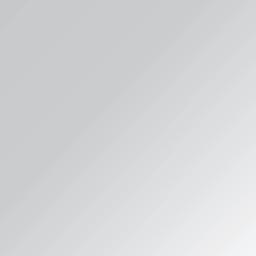
Constantly Innovating For 30 years, Alouette’s efforts to continuously innovate have allowed them to improve work methods, boost know-how and establish themselves as one of the most efficient aluminum smelters in the world. Over 30 years of operations, Alouette has successfully completed two major expansion phases—which included creating the largest private construction site in Quebec at the time—in order to increase its production capability and to upgrade to modern, highperformance equipment. With this same drive for innovation, the company began its ambitious transformation into a “4.0 plant” by leveraging innovative technologies and practices in automation, data analysis, and artificial intelligence. Alouette is one of the few aluminum smelters to use skimming robots to recover waste metal directly from the crucible, which can then be recycled. A company with close ties to the community As a driving force for the economic and social development of Sept-Îles and the surrounding area, Alouette is fully committed to contributing to a rich local ecosystem by giving back to the community. Since its inception, Alouette has invested over half a million dollars annually to support local causes, including furthering the next generation of workers, encouraging academic perseverance, facilitating equitable access to food for young people, promoting sports activities, and highlighting the richness of the Innu culture.
Alouette celebrates its 30th anniversary In 2022, Aluminerie Alouette is celebrating an important milestone: its 30th anniversary! In 1992, the community of Sept-Îles (Quebec, Canada) joined forces with Alouette to produce the highest quality aluminum in the entire world. Alouette is also one of the largest aluminum smelters in the Americas and a world leader in the production of responsible aluminum. Throughout its evolution, one thing has remained constant: the company’s close ties to the community. With a renewed vision and commitment, Alouette is now paving the way for the next generation of aluminum production.
Claude Gosselin, President and CEO of Alouette
Role: Primary aluminum producer
Over the years, more than 200 community, cultural, environmental, educational, and sports organizations have benefited from Alouette’sEmployingsupport.nearly 900 people in various trades, Alouette is the largest private employer in the city of Sept-Îles and a major offreserve indigenous employer for the Uashat mak Maniutenam community. Alouette’s commitment to the future is clear: to continue being an employer of choice with strong ties to itsAtcommunity.Alouette,a whole new generation is taking shape for a promising future.
•• 18 Aluminium Show Newspaper www.aluminiumtoday.com






















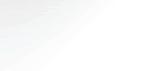
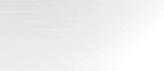
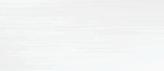
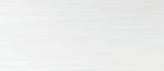
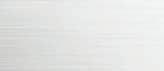
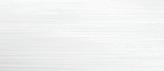
The company now recycles or recovers more than 80% of its residual operational materials (wood, water, aluminum, etc.) and plans to reach 100% over the next 10 years. Due to this exemplary management of residual operational materials, in April 2021, Alouette obtained the highest recognition level of RECYC-Quebec’s ICI on recyclce + program, becoming the first aluminum smelter in Quebec to receive such an honour. “We are now more than ever aware of the importance of respecting the environment. This is key to ensuring the sustainability not only of our commercial operations, but of community and our collective future as well,” stated Claude Gosselin, President and CEO of Alouette.Already a world leader in the production of green aluminum, Alouette continues its quest for innovation by applying the most environmentally friendly measures to its operations. The decarbonization of aluminum production will be one of the greatest challenges of the next few years and Alouette is constantly on the lookout for innovations that will enable them to achieve carbon neutrality by 2050.
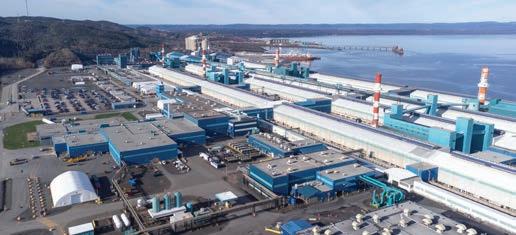
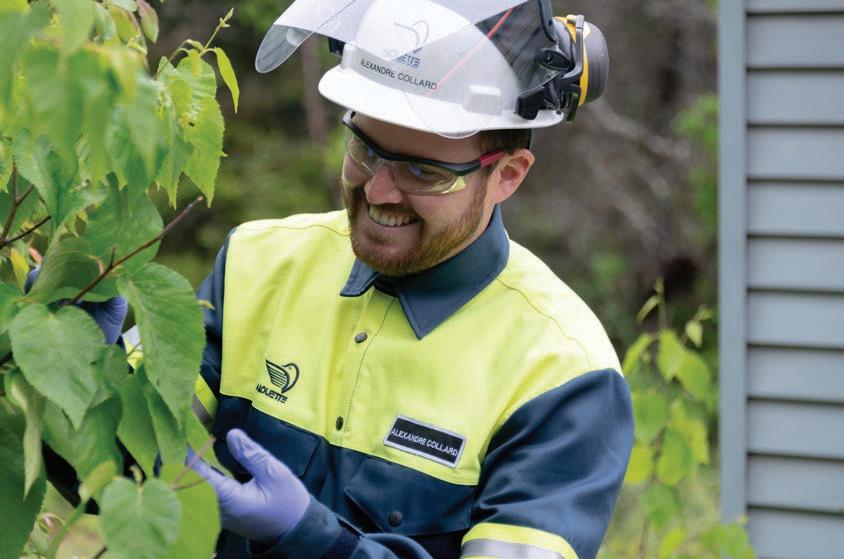
ALOUETTE IN A NUTSHELL

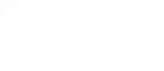
President and CEO: Claude Gosselin Inception: 1992 Number of employees: 900 Partners: AMAG - Austria Metall AG (Austria, 20%); Hydro Aluminium (Norway, 20%); Investissement Québec (Canada, 6.67%); Marubeni Metals & Minerals (Japan, 13.33%); Rio Tinto (Canada, 40%).
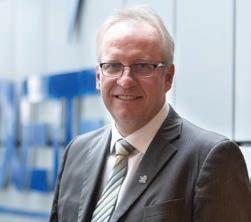
30 years already, and a new generation takes flight
Producing the Greenest aluminum in the world Protecting the environment has always been a priority at Alouette. Over the past 30 years, Alouette’s greenhouse gas emissions have decreased by 40%, thanks to ongoing efforts to significantly reduce their environmental footprint by meeting or exceeding the most stringent industry standards. “Our environmental ambition is simple: to produce more while consuming less energy,” explained Sébastien Scherrer, Director of Strategic Development and Improvement. Thanks to committed experts, responsible environmental management and rigorous monitoring, Alouette has made significant environmental progress in recent years.



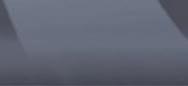

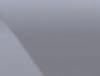
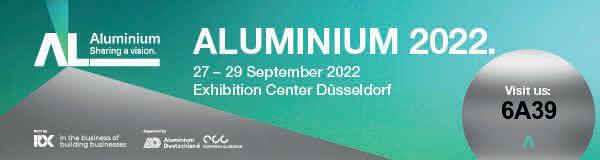
Sorting Aluminium: Separating the brilliant from the good
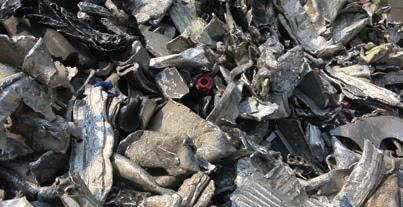
TimCONTACT:Blosze – Marketing STEINERT WiddersdorferGmbH,Str. 329-331 50933 Tim.Blosze@steinert.deGermanyCologne
When it comes to sorting aluminium alloys, STEINERT sets the quality benchmark and will be showcasing its solutions at the “Aluminium” trade fair in Düsseldorf, Germany.
X-ray transmission (also known as “XRT”) separates heavy metals from light metals Returning aluminium to recycling circuits requires pure fractions which processors can only manufacture on a step-by-step basis. The recycling process initially involves the separation of ferrous and non-ferrous metals – both of which are possible with STEINERT’s magnetic separation technology. In the following process step, key technology comes into play: X-ray transmission separates heavy metals from light metals. This produces clean, defined aluminium mixtures. The STEINERT XSS
T EVO 5.0 is at the forefront of technology, world-wide. As confirmed by Stemin S.p.A., the Italian aluminium recycling specialist that has relied on STEINERT’s sorting machines for many years: “We have opted to buy from Steinert because of its ongoing research and development in the field of metal recycling, the fact that the quality that its machines achieve, when sorting, is improving all the time and because its ever-more efficient sorting machines help us to produce the quality levels we need. This was absolutely the right decision for us,” said Olivo Foglieni, chair of the holding company FECS to which Stemin belongs.
•• 20 Aluminium Show Newspaper www.aluminiumtoday.com Newspaper
STEINERT LSS with LIBS technology sorts aluminium by alloy type at AMAG Austria Metall AG. (inset) Clean wrought aluminium: coarse fraction from STEINERT XSS® T EVO 5.0
STEINERT XSS® T EVO 5.0: Olivo Foglieni, Chair of the FECS holding, to which Stemin belongs, is once again turning to STEINERT XRT sorting technology.
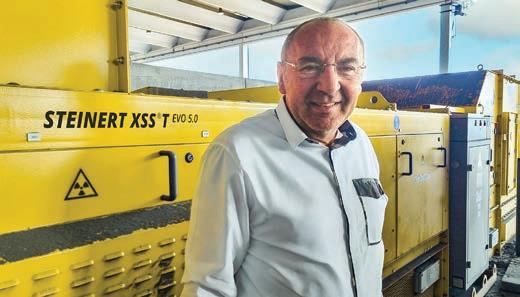
The STEINERT LSS (Line Sorting System) enables the customer to separate multiple alloys in just one detection run by the LIBS sensor. LIBS – short for laser-induced breakdown spectroscopy – is a technology used for elemental analysis. By default, the calibration methods stored in the measuring device analyse the concentrations of the alloy elements Cu, Fe, Mg, Mn, Si, Zn and Cr. The sorting of alloys involves first separating the shredded material mixture in such a way that the material is fed past the laser, so that the laser pulses hit the surface of the material. This causes tiny particles of material to evaporate. The emitted energy spectrum is recorded and analysed simultaneously to detect the alloy itself and the individual alloy components of each individual object. Up to seven different materials are detected in the first part of the machine. Compressed air nozzles then shoot these materials into different bunkers in the second part of the machine, depending on their elemental composition.Ifyouwould like more information on this topic, visit us at Stand 6F01, Hall 6, at the Aluminium 2022 trade fair in Düsseldorf, Germany, from 27th to 29th October 2022.
As always, purity is the primary objective when it comes to recovering secondary raw materials. Exporting materials of low-value and quality is a thing of the past. Today, achieving the very highest purity levels is essential. STEINERT has set further milestones in the sorting of aluminium scrap by introducing the first LIBS sorting plant in Europe, bridging crucial gaps for its customer, and enabling even more secondary scrap to be returned to resource cycles.
ABOUT STEINERT STEINERT can look back on a 130-year history: founded in 1889 in Cologne, this family-run business is one of the world’s leading companies in magnetic separation and sensor sorting. With 400 employees, STEINERT generates an annual turnover of around EUR 100 million. In addition to 50 sales partnerships and joint ventures around the globe, the company also has subsidiaries in Germany, Australia, the USA, and Brazil.
STEINERT LSS | LIBS sorting system separates aluminium by alloy This sorting machine for aluminium recyclers, which processes pre-sorted aluminium by alloy type, has been in operation at AMAG Austria Metall AG since 2018, and will be implemented by other companies in 2022.
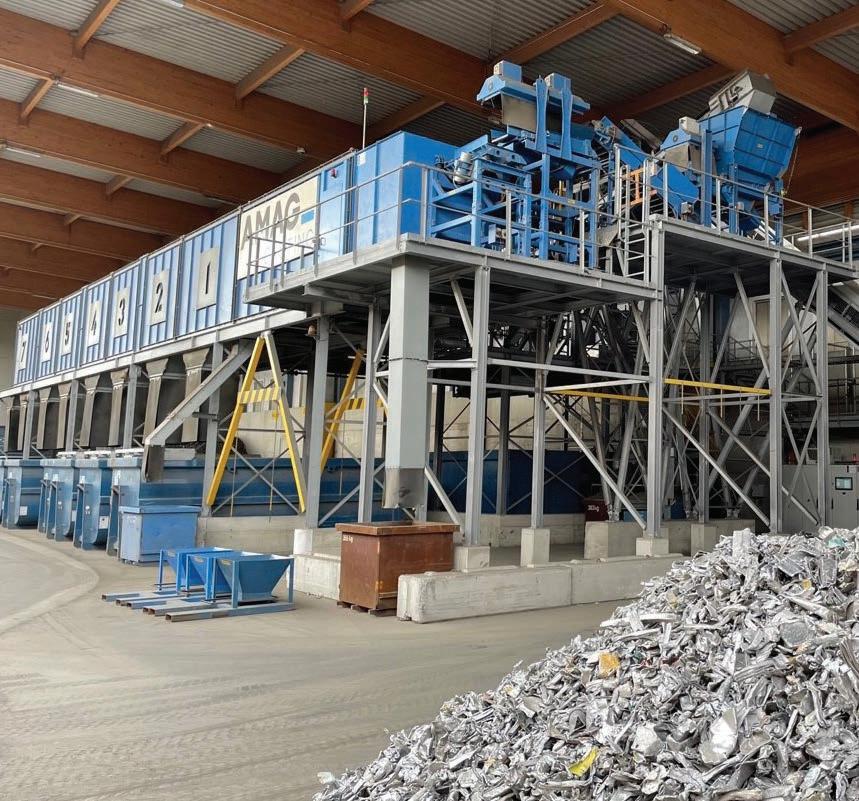

•• 22 Aluminium Show Newspaper www.aluminiumtoday.com Future Aluminium Forum 2023: Meeting the Demand With global aluminium demand projected to increase 40 per cent by 2030, the aluminium sector will need to produce an additional 33.3 Mt – a reality only possible through the inception of streamlined technologies, digital manufacturing and sustainable solutions across the supply chain. Join us at the Future Aluminium Forum to meet manufacturers rising to the challenge, focus on the opportunities that growth will bring, and prioritize time for your own learning and networking. In 2023, the Forum will return in a live format to Québec City, a region where the aluminium industry has existed for more than a century and is now seeing rapid change and collaboration between manufacturers, processors, suppliers and OEMs. Register your interest at www.FutureAluminiumForum.com @Alu_Forum To find out more about speaking contact: Nadine Bloxsome, Conference Director nadinebloxsome@quartzltd.com | +44 1737 855115 To find out more about stand and sponsorship opportunities contact: Nathan Jupp, Sales nathanjupp@quartzltd.comManager|+44 1737 855027 MAY 2023 Québec City, Canada O cial media partners: Supported by: FAF_23_HalfPageAd_185x128mm.ind.indd 1 24/08/2022 11:13 Newspaper


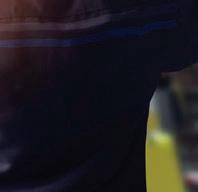

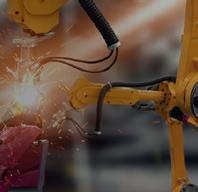
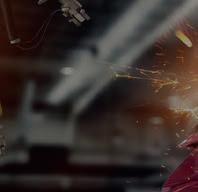
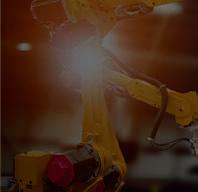

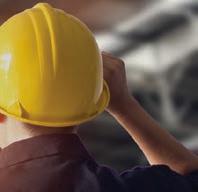

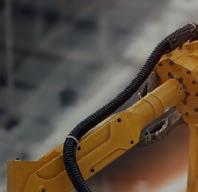
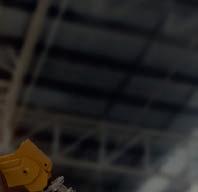
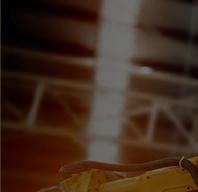
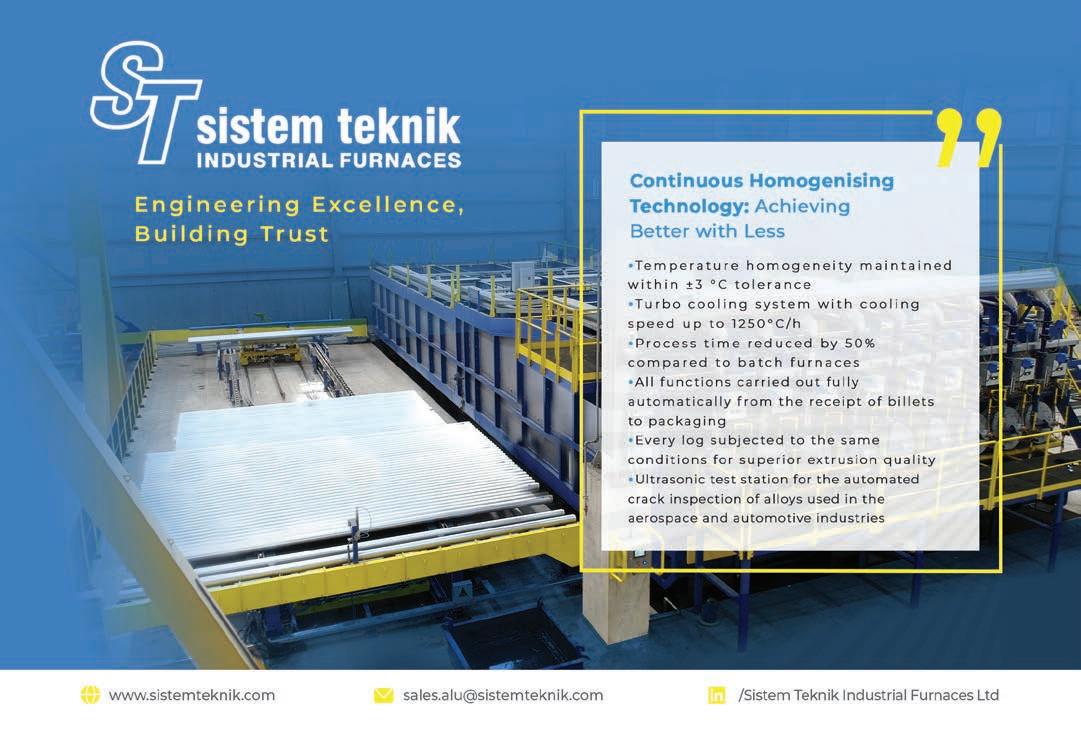
The new EVY Compact Vacuum Cleaner FRESH SMARTTHINKING,CLEANING www.hencon.com The cleanest • Filters even the finest dust: 2 - 0,2 micron • Cleans without dust clouds • Sustainable: better for men & machine The leanest • Compact, highly manoeuvrable model • Reduces your Total Cost of Ownership • Single out of stock model The meanest • Fully continuity-adjusted • Collects all dust, ready to re-use & re-market • It’s all about Serving Progress! For more information about EVY: www.hencon.com/evy
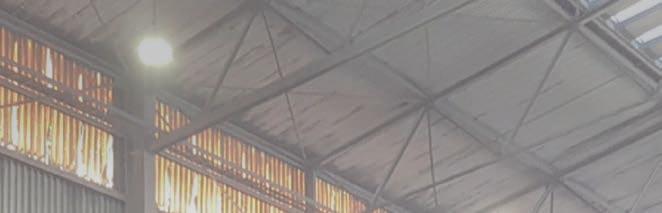

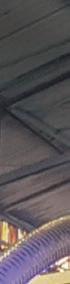
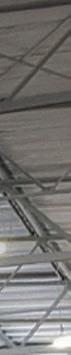

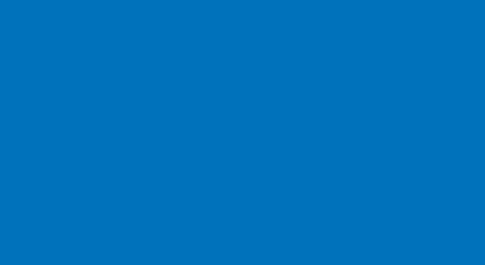
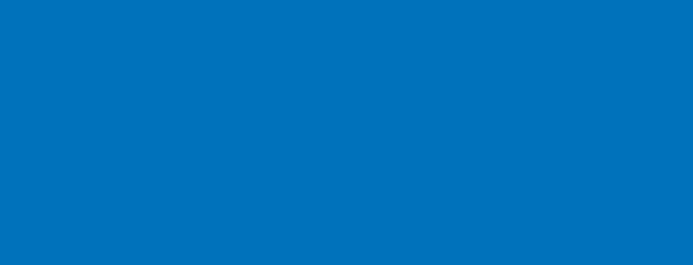

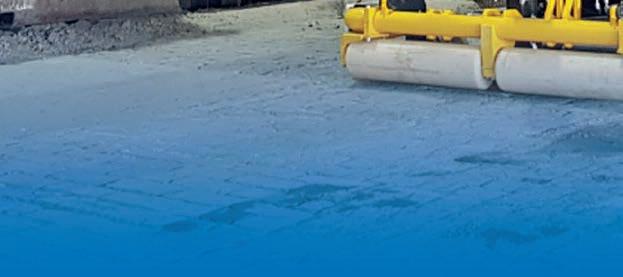
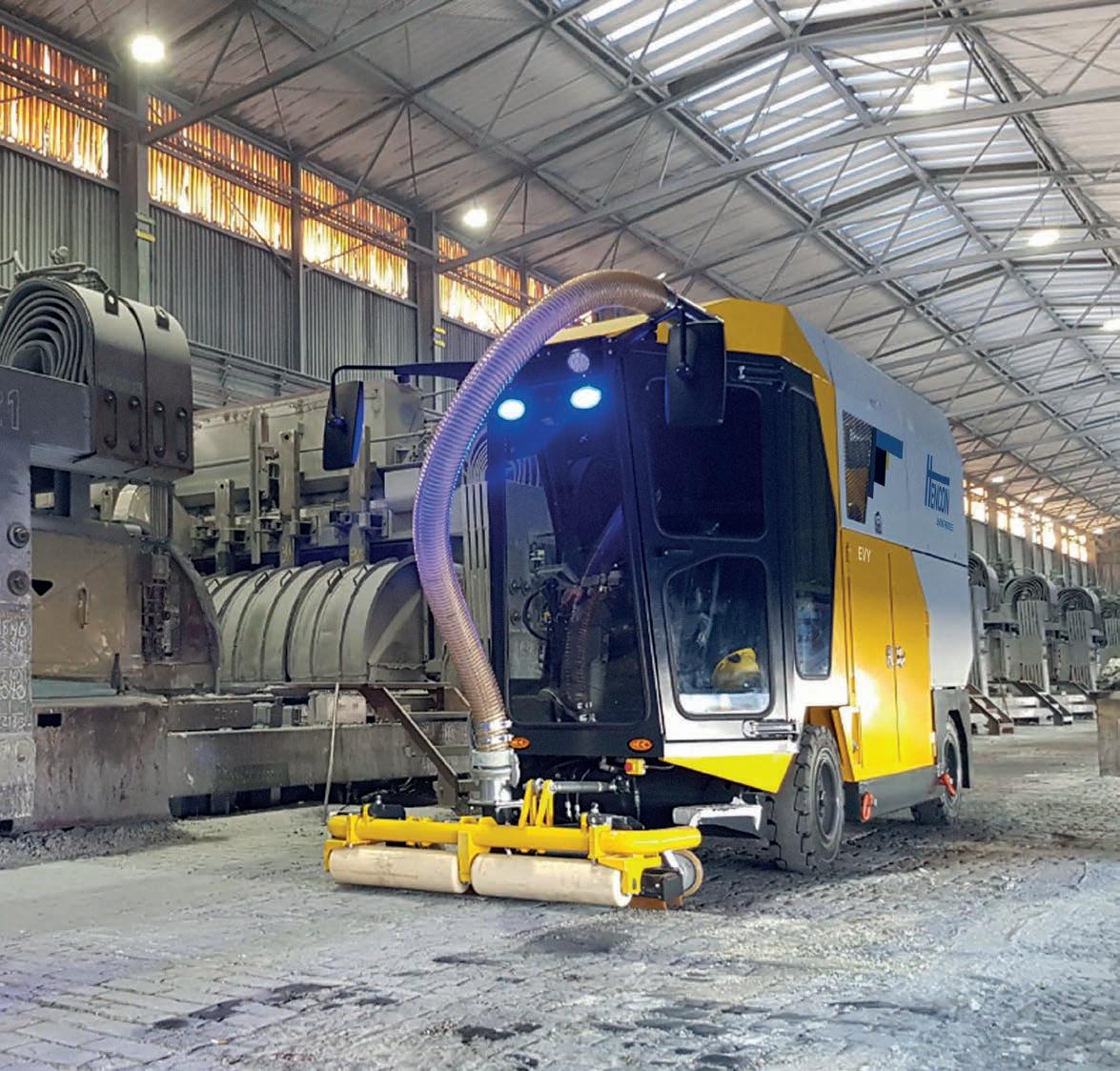
PhoenixTM GmbH GermanyLtd UK



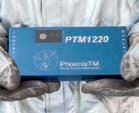














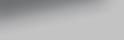















































































• Reduction in inner furnace clearance creating possible product impingement issues and blockages To prevent such problems, regular scheduled inspection and clean out of the furnace is necessary. This is not a pleasant, quick operation, and requires chipping away flux debris with pneumatic tools. Often requiring a furnace down time of 1 to 2 days, this task is only performed when essential. Leaving the clean-up operation too long though can be catastrophic causing dramatic deterioration in product quality or risk of mid production run stoppages. Until now there has been no easy way to see how your product travels through the furnace under normal operation conditions or means by which the need for furnace repair or clean down can be confirmed. A new technology called Optical Profiling changes all this and for the first time gives you the means to see what your product sees in production; a true products eye view!
Learning what is truly happening to the product inside the black box, that is your furnace, is important and shapes the success of your operation and customer satisfaction.
sales@phoenixtm.com ... where experience counts ! PhoenixTM LLC USA info@phoenixtm.com www.phoenixtm.com

Root Cause Analysis – Process Profiling Help The temperature profile of any thermal process is invaluable to get a better understanding how the furnace is working and is a critical tool in fault finding when things go wrong, because they do, and they will! Root cause analysis is a standard tool used in industry to identify the root cause of product or process problems without jumping to conclusions or making knee jerk reactions. In root cause analysis it is important to distinguish between symptoms and problems and drive to find, in the mist of many potential causes, the true root cause.

•• 24 Aluminium Show Newspaper www.aluminiumtoday.com Temperature Profiling and Surveying Solutions in the Aluminium Industry Process Monitoring solutions for • Homogenizing • Solution Heat Treatment T5/T6 • Ageing • Brazing (CAB & Vacuum) • Powder Coating …...and many more Comprehensive Passes through furnace with the product. • Complete product temperature profile • Measurement at up to 20 points • Live 2 way radio communication option Safe No Trailing thermocouples so quick, safe, system installation without production delays. Easy Fully compliant AMS2750 or CQI-9 TUS reports with only a single Click!
Applying ‘thru-process’ optical profiling to fully understand, what is happening in your aluminium CAB furnace...a product's eye view! Newspaper continued on page 26 •• PhoenixTM
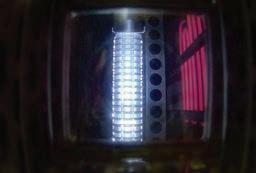
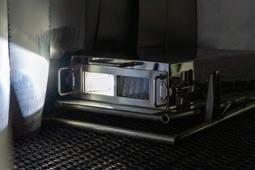

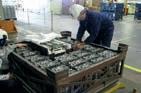







info@phoenixtm.de PhoenixTM
As shown in Figure 2 below, a temperature profile of a continuous aluminium brazing (CAB) furnace process shows the detailed critical phases of the heat treatment process each contributing to the quality of the final product.
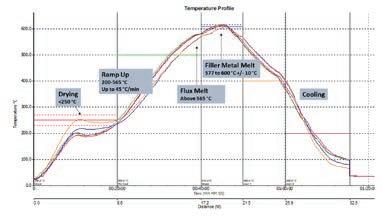
To fully understand the operational characteristics of the heat-treat process an essential technique is that of thru-process temperature profiling where the environment and product temperature is continuously measured as the product travels through the process. Such technique provides what is referred to as a ‘temperature profile’ which is basically a thermal fingerprint for that product in that particular process. This thermal finger print will be unique and allow understanding, control, optimisation and validation of the heat treat process.

happens in your

Taking an example of the Aluminium CAB brazing process, the temperature profile trace may show that the cause of a quality issue is due to the product braze temperature in a particular zone of the furnace being too low. This, although identifying a cause does not necessarily explain the root cause. A low Optical profiling system being used in a conveyorized aluminium brazing furnace

In the global Industrial heat-treating market tens of thousands of products are sent through conveyorised ovens or furnaces each and every day. The thermal processing of these products whether heat treating the core material or even curing a surface coating is often critical to the quality or performance of the finished product. Whether aluminium brazing a radiator or curing paint on a car body, achieving the correct process times and temperatures is essential.
product temperature in a particular furnace zone may be due to many possible different root causes – faulty control thermocouple, burner, recirculating fan or even damage to furnace structure / insulation. The low product temperature may in some circumstances not be detected by onboard furnace controls and will require a deeper dive investigation. Identifying the root cause will require inspection at the source of the problem. This action is referred to commonly as “Going to Gemba” a Japanese word which means ‘the real place’. In this situation going to Gemba means investigating what is actually happening in the furnace in a particular zone, at the point of occurrence.
Figure 2: Typical temperature profile of continuous aluminium brazing furnace (CAB) showing the critical temperature transitions.
Root Cause Analysis – Continuous Aluminium Brazing (CAB) Example –Automotive Radiator Line SYMPTOM | High number of radiator rejects identified in QA PROBLEM | Poor product quality due to weak braze joints CAUSE | From temperature profiles product braze temperature identified to be too low in Zone 4 ROOT CAUSE | Recirculating fan fault in zone 4 resulting in poor non uniform heat transfer to GoingradiatorstoGemba is not always the easiest of tasks especially when considering identifying the root cause of furnace problems. Any task involving the internal inspection of a furnace generally requires that the furnace is switched off, allowed to cool and then dismantled to allow access by operatives. Taking our aluminium brazing (CAB) example, internal inspection of the furnace is not a quick and easy task. Operating at 550 °C the cool down period is significant to allow engineers safe access for inspection and corrective action and then further delay to get the furnace back up to a stable operating temperature. Such maintenance action may mean one or two days lost production, from that line, which is obviously detrimental to productivity, meeting production schedules, satisfying key customers and your bottom line. In addition to process temperature problems there are many other production issues that can be faced relating to the furnace operation and safe reliable transfer of the product through the furnace or oven itself. In the CAB process a day to day hazard of the process is the build up of flux debris. Flux materials used to remove oxides from the metal surface and allow successful brazing can accumulate within the internal void of the furnace. These materials are most problematic at the back end of the muffle section of the furnace where due to the drop in temperature, entering the cooling zone, materials condense out. Flux build up can create many different process issues including; • Physical damage to the conveyor belt or support structure requiring expensive replacement
Introduction truly furnace?
• Reduction in belt lubricity creating jerky movement and causing unwanted product vibration • Lifting of the belt mesh creating an uneven transfer of products causing possible excessive product movement, clumping or clashing.
– Do you know what

Metal is the backbone of our society. It’s in the structures we ride, work and live on every day. That’s why you’ve trusted the detection technology inside every ARL iSpark for over 80 years to ensure every piece of steel and metal you produce is safe. With so much riding on that, why would you choose anything else?
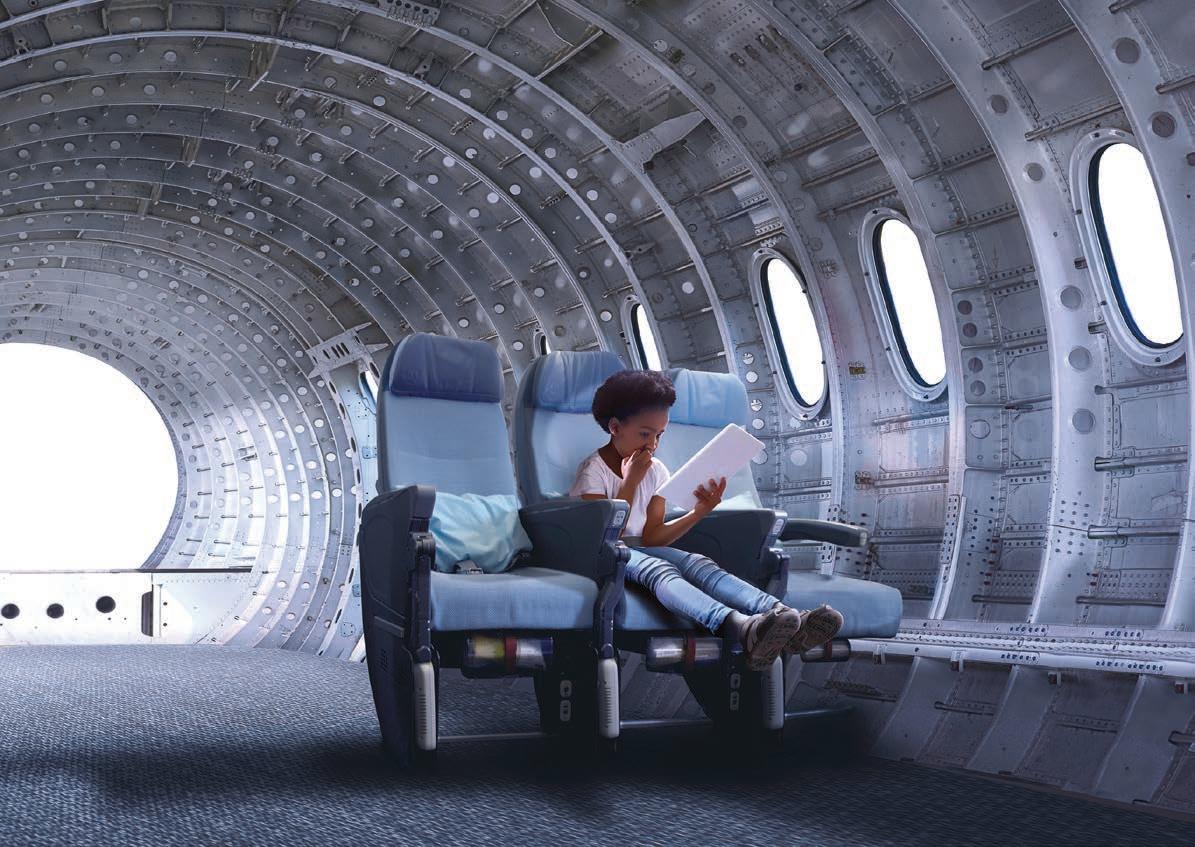
©2021 Thermo Fisher Scientific Inc. All rights reserved. All trademarks are the property of Thermo Fisher Scientific and its subsidiaries unless otherwise specified. AD41409 0821
Find out more at thermofisher.com/ispark
*Based on a data comparison, completed by Thermo Fisher Scientific in 2021, of detection limits for OES systems using data published in specifications and applications notes for ARL iSpark and competitors.
When you need to know it’s safe * ARL iSpark. The trusted standard.
Aluminium Show Newspaper www.aluminiumtoday.com
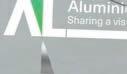
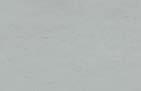
INTRALOGISTICS

1 29.07.2022

Check that key furnace features are working correctly and not damaged • Fans, Ducting, Control thermocouples, Gas Feed pipes, Zone separation curtains/ brushes
‘Thru-process’ optical profiling is a new revolutionary technique for visually inspecting the condition of and also transfer of product through a continuous furnace. Combining such information with a product temperature profile, process engineers can work with maintenance teams to not only Understand, Control, Optimize and Validate the heat treat process but also Maintain the furnace to protect productivity and quality. Employing the optical profile information preventative maintenance or furnace clean down can be scheduled with confidence, and when problems occur, rapid fault finding is possible. Furnace inspection as part of the production flow at temperature eliminates, days of furnace downtime, lost production and an interrupted product supply chain. PhoenixTM your CAB process to Find, Fix and Forget your furnace problems!
Check that the product travels safely and smoothly through the process without conflict or obstruction
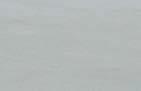
• Conveyor belts run flat and product orientation is kept constant – No belt damage or distortion



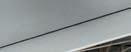
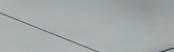



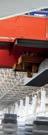



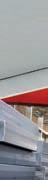
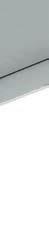


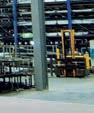


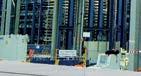
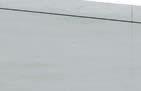
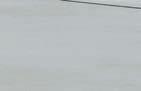


• No product vibration of excessive movement which may cause damage to product or affect processing step eg: brazing • Check that product is able to pass through without clashing with furnace furniture or product clumping
Condition & Operation of Key Furnace Features



•• For more information contact: Dr Steve Offley, Product Marketing Manager, PhoenixTM Ltd UK; tel: +44(0)1353223100; e-mail: Steve.Offley@phoenixtm.com
•• 26
Vortex is a solution selected by an increasing number of companies looking for alternative and more efficient systems for annealing aluminium coil and foil. What makes the technology attractive is the proven and excellent quality of the final product, and a significant reduction of cycle time by up to 30%. Solutions with the prefix ‘eco’, in other words, economical –ensuring higher production profit – and environmentally friendly as well as fuel efficient are the current trend in the world of heat treatment,” states Piotr Skarbi?ski, Vice President Aluminium Process Business Segment at SECO/WARWICK.The solution is directed to all aluminium manufacturers of flat-rolled products, and therefore aluminium rolling mills, regardless of the manufactured alloys and industries for which they are intended Vortex® is the best Vortex technology combines the advantages of nozzle systems while still achieving very high heating uniformity and temperature control precision. The required process profile requirement is achieved, and the processing time is reduced to a minimum. The important element of the SECO/ WARWICK’s solution is an advanced control system that enables users to obtain the required precision annealing temperature in the shortest possible time. Another important element is heating uniformity throughout the coil.
• Correct alignment adjustment of ducting to allow correct air flow / convective heat transfer • Identify ignition events or other safety related issues within the furnace Product Transfer
Thermal Process Observation



SOLUTIONS FOR THE ALUMINIUM INDUSTRY HALL 3, BOOTH D72

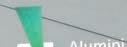

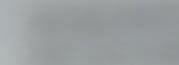

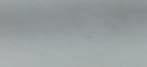

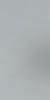






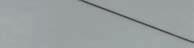



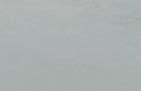

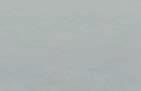
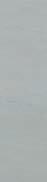
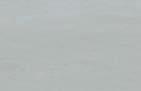
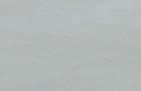

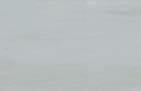
Check that the process is being performed correctly where heat treatment action is physically visible • Brazing – Melt and Flow of filler metal Summary

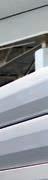
Vortex® implementations Over 30 furnaces based on the Vortex system design have been implemented. They operate mainly in Europe, but also in Asia, North and South America. Our customers are among the aluminium industry leaders. These customers have continued to cooperate with us for years by ordering subsequent equipment based on satisfying results from earlierAssanprojects.ALÜMINYUM is a world leader in the production of aluminium products using the continuous casting method, operating dozens of SECO/WARWICK solutions. In order to increase production capacity, the company has once again decided to purchase SECO/WARWICK’s Vortex® technology, equipped with an innovative nozzle heating system for annealing aluminium rolled strips.
SINCE 1925.
Newspaper Optical Profiling Optical profiling is a new complementary technique to that of ‘thru-process’ temperature profiling. The new technology allows for the first-time process engineers to view the inner workings of the furnace under normal production conditions. Travelling through the furnace, with the products being processed, the Optic system gives a product’s eye view of the entire heat treatment journey. Employing similar thermal protection technology ‘thermal barrier’ used in temperature profiling, in place of the temperature data logger a compact video camera and torch are used to record a video of what a product would see travelling through the furnace. The principle is just like your car’s dash cam, the only difference being that your journey is being performed in a furnace at up to 550 °C. The resulting video “Optical Furnace Profile” shows process engineers so much about how their process is operating without any need to stop, cool and dismantle the furnace. This allows safe routine furnace inspection without any of the problems of costly lost production and days of furnace downBenefitime.tsof applying the Optical Profiling principle in conveyorized furnace processes:
the
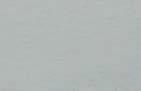
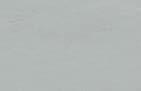
Vortex® technology: frequently chosen by industry

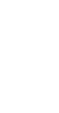


When realising high-efficient processes in the aluminium industry, customers worldwide trust on know-how and the leading intralogistics concepts from worldwide expert Vollert. vollert.de 10-2022.indd 14:09:33


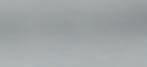


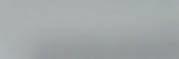

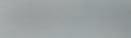
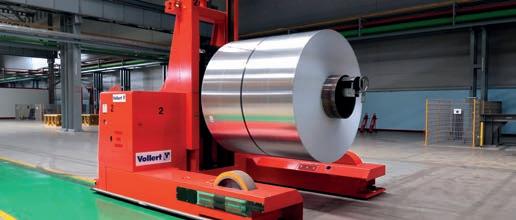

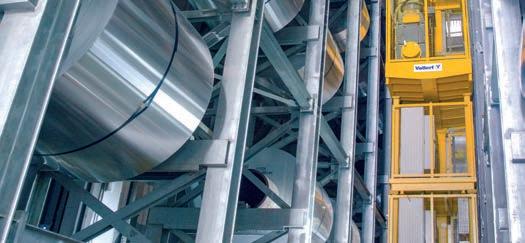
Furnace Condition Check the condition of the internal walls of the furnace to ensure they are fit for purpose • Damaged or Distorted panels / Sealing gaps / Corrosion • Build-up of dirt/flux/condensate or general processing debris – Contamination risk –identify need for critical cleaning action
Anzeige ALUMINIUM Newspaper
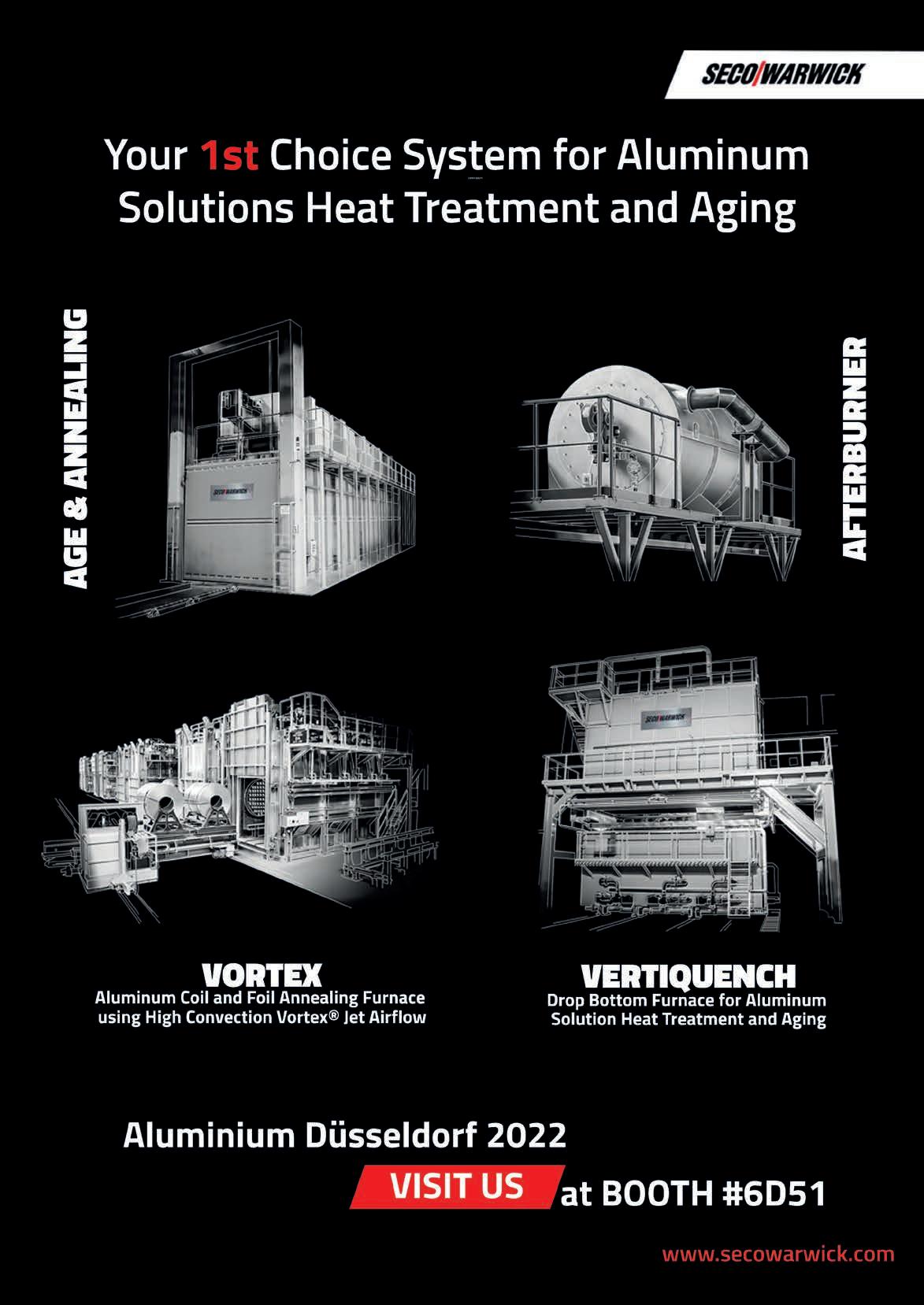
The next area to reduce CO2 emissions is from the production of Alumina (1.3 mt of CO2 for every 1 mt of aluminium) by replacing fossil fuels in the process by using green hydrogen. This is possible by upgrading certain production equipment in an Alumina refinery but will require CAPX investment. A lot of work is being done on this by the major Alumina producers but it will take time to implement and will also be subject to the ability to competitively source green hydrogen. Reducing CO2 emissions from freight is the next area of focus (.6 mt of CO2 for every 1 mt of aluminium production).
AlofmtperCO2 24201612840 Renewable PowerNatural GasWorld AverageCoal AlofmtperCO2 43210 carbonZEROOtherfreightGreenaluminaGreenCarbonanodeRenewablepowersmelter Smelter Carbon footprint by Power Source Path to ZERO Carbon journeyAluminium’sto ZERO Carbon
In closing going “Green” will not be easy and require sacrifice no matter what industry you are in. We need to challenge the norm and take on the mindset “The only easy day was yesterday”!
•• 28 Aluminium Show Newspaper www.aluminiumtoday.com
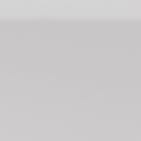
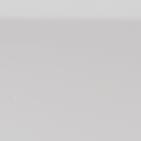

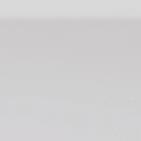
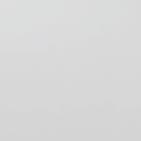
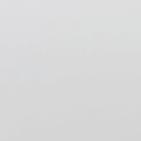



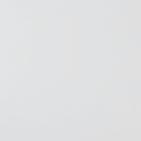
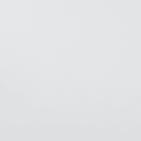
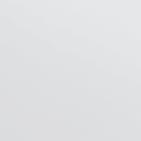
As a result of the electrolysis process the aluminium reduces to the bottom of the pot (hence the term Reduction Lines) and the remaining oxygen eats away the Carbon Anode in the pot. This is a continuous process which runs 365 days a year 24 hours a day and you need to replace the Carbon Anode every 27 days. Ok, I know this was way too much technical talk but hopefully you understand why a Carbon Anode is important. It is possible to replace the Carbon Anode with what is called an Inert Anode, a technology developed by Alcoa many years ago. However, this technology has never been fully scaled for commercial production. The Inert Anode is made of specialty alloyed steel bars thereby replacing the need for the Carbon Anode in the process. I know this sounds simple and you may ask why are we not doing this?
The last area of CO2 emission reduction I have labeled as “Other” (.3 mt of CO2 for every 1 mt of aluminium production). This is primarily related to the use of vehicles within a smelter which are powered by diesel as well as gas powered furnaces primarily used in the Casthouse area. In both of these areas there are solutions to have an electric option. However, this would be for new purchases whereas to replace existing equipment will be cost prohibitive.
The simple answer it is not so easy! But there is a company called Elysis (located in Canada) which is a joint venture between Alcoa, Rio Tinto and the Canadian government focused on having this technology commercially demonstrated by the end of 2023.
You may ask how is it possible to eliminate freight as smelters need raw materials? Well there are a couple of things that can be done to eliminate roughly 50% of the CO2 emissions. The first thing companies can do is optimise shipments to have more larger cargoes which lowers the total number of shipments and also saves money. You may ask why companies are not already doing this if it saves money? Again the answer it is not so easy to manage complex supply chains and the recent issues from the COVID pandemic have made it even worse. However as the world returns to normal there is a big opportunity to better optimise shipping sizes which will reduce CO2 and save money.Thesecond thing companies can do is focus on using cargo ships which have the ability to do backhaul shipments. Today once a ship delivers its cargo it usually brings back the ship empty. If companies are able to carry a backhaul cargo, they fully utilise their ship and avoid another ship making that journey. Torvald Klaveness out of Norway is a good example of a company utilising this strategy with their custom built Cabu ships. As example they bring Alumina from Australia to the smelters in the Middle East and then return bring back caustic soda from the Middle East to be used in Australia Alumina refineries. This again is another example of reducing CO2 emissions and saving money.
As a world we need to accept that going “Green” may require investment where there is not a financial payback.

Fortunately for the world aluminium is the second most abundant element on the planet however the process to produce primary aluminium generates large amounts of CO2 emissions. The process of smelting aluminium from the processed bauxite (i.e. Alumina) is power intensive process resulting in the generation of CO2 emissions especially when using energy from fossil fuels. Today the world produces approximately 68 million metric tons (mt) of primary aluminium annually with an average CO2 footprint of 17 mt for every 1 mt of aluminium produced (yes you read that correctly!). So this equates to 1.2 billon mt of CO2 generated from the production of primary aluminium each year. The average CO2 footprint for a smelter varies drastically depending upon the power source used, for example aluminium produced from coal-based electricity generates around 20 mt of CO2 whereas the if it is from renewable power (e.g. Hydro or Wind) then there is only 4 mt of CO2 The vast majority of the 68 million mt tons of primary aluminium is produced using coal fired power stations, typically in China and India. In terms of aluminium produced from renewable power there is approximately 15 million mt produced annually (or only 22% of the total). So we have a long way to go to shift to all renewable power. Even if a smelter has renewable power there is still 4 mt of CO2 produced. Obviously, the ability of an existing smelter to change their power source is not really an option. So how can we address the 4 mt which is not related to power generation? The below chart breaks down the elements which make up the remaining 4 mt of CO2 from aluminium production. The biggest area of CO2 emission reduction relates to the use of the Carbon Anode in the aluminium electrolysis process (accounts for 1.8 mt of CO2 for every 1 mt of aluminium production). I will do my best to explain the aluminium electrolysis process in simple terms. In order produce aluminium you need to split the aluminium from the oxygen in Alumina. This is done in a reduction cell (commonly called a pot) where Alumina (which looks like sand) is continuously fed into molten liquid bath in which a Carbon Anode is submerged then hit with large amounts of electricity to complete the process (on average 15 megawatts of power is needed to produce 1 mt of aluminium).
There needs to be a balance between what companies (and the end consumer) are willing to pay and what are companies willing to do invest even without a clear financial payback. In addition, the industry needs to more calculated risks in embracing new technologies.
Today sustainability and going “Green” have become of paramount importance to the world. This has challenged all companies review their business models and, in many cases, reinvent themselves. Nowhere is this more evident than in the large industrial industries such as aluminium. Being the former CEO of Aluminium Bahrain I can tell you aluminium is an amazing material that is used in almost everything we touch, whether it be your i-phone a soda can or the car you drive. In addition, we cannot forget the critical role aluminium will play in the Electric Vehicle (EV) revolution given its lightweight properties, conductivity and ability to be infinitely recycled.
•• Author: Tim Murray, CEO of Cardinal Virtues Consulting (former CEO of Aluminium Bahrain).
I know some people may say why do we need smelters and why can’t we just do more recycling to support market demand. Personally, I think all the new recycling initiatives are wonderful and we as a world should do our very best to maximise recycling but unfortunately it is not enough. It is not a mutually exclusive solution; the answer is we need both.
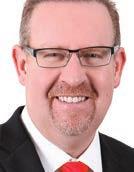



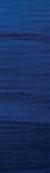
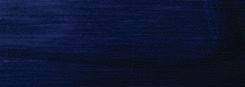

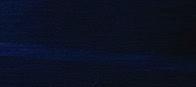
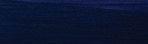

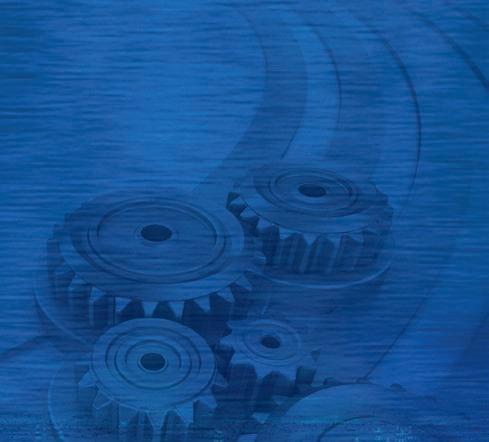

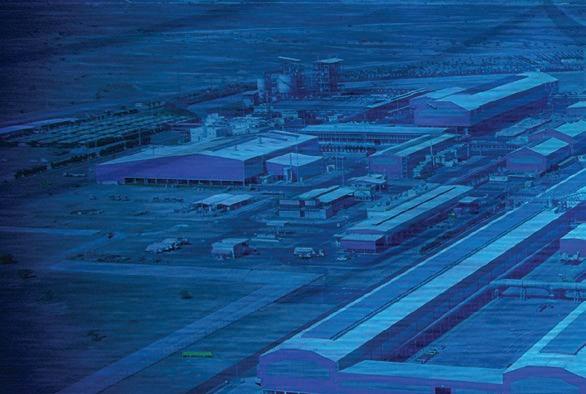
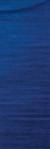




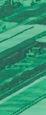






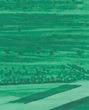




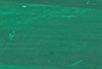







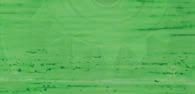























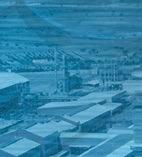



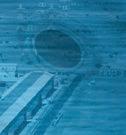































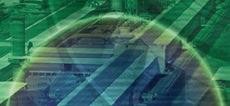






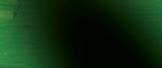



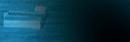
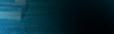




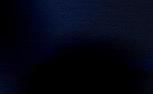
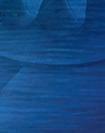









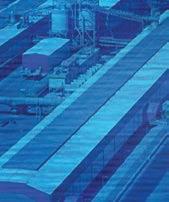











































































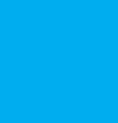



















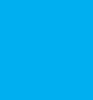



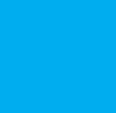

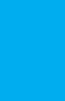



























•• 30 Aluminium Show Newspaper www.aluminiumtoday.com
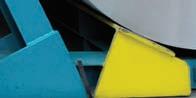
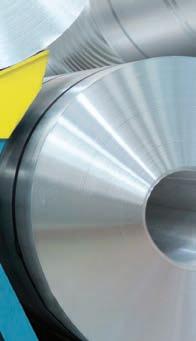
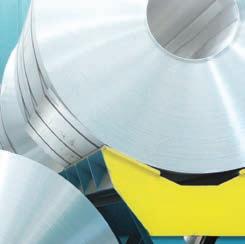


As one of the leading manufacturers of the flat rolled aluminium industry and a subsidiary of Kibar Holding, Assan Alüminyum continues to invest in improving sustainability. Assan Alüminyum is able to fully offset its scope 2 emissions with its renewable energy production and processes the 100 percent and infinitely recyclable aluminium in its integrated recycling facility. As of the beginning of 2022, Assan Alüminyum achieved full performance standard certification from ASI (Aluminium Stewardship Initiative), the global initiative setting the sustainability principles for the aluminium industry worldwide, with the environmental, social and economic sustainability-focused criteria.Assan Alüminyum, a subsidiary of Kibar Holding, produces coil & sheet, foil and pre-painted aluminium products with an annual production capacity reaching up to 360 thousand tons at its production facilities. With its core values of reliability, flexibility, innovation and sustainability, Assan Alüminyum serves many different sectors such as automotive, packaging, construction, HVAC and consumer durables, exporting 75 percent of its sales, to more than 70 countries in four continents, mainly to North America and West Europe.
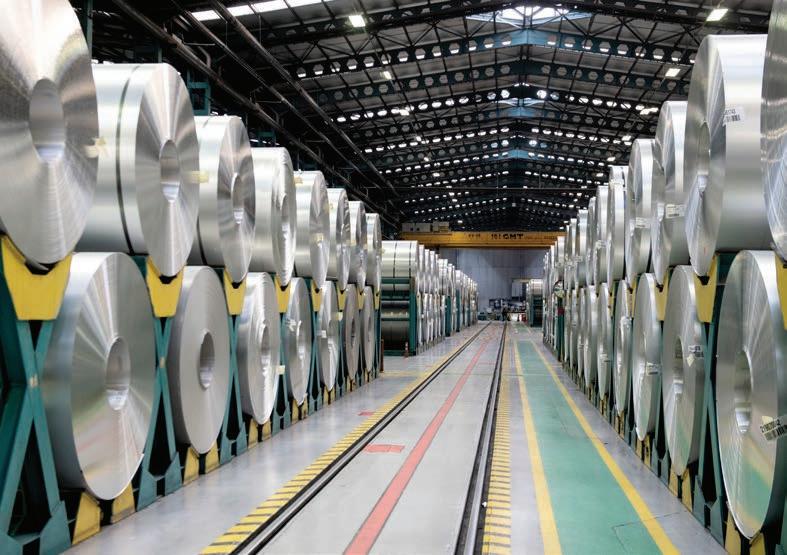
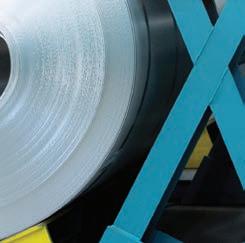

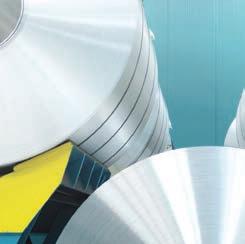
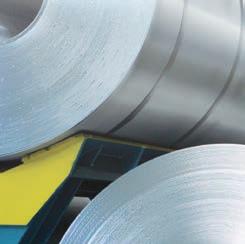
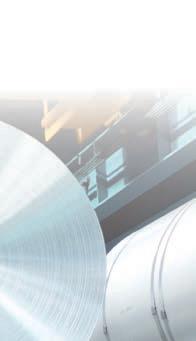
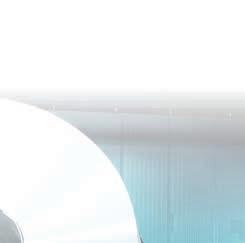
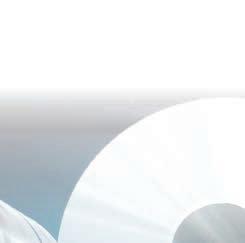
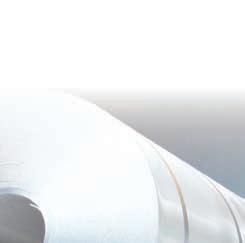
Assan Alüminyum Continues to Invest in Sustainability


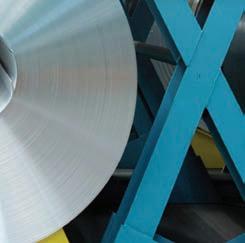
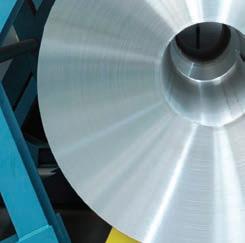
Foil production As one of the two largest aluminium foil manufacturers in Europe, the company’s annual foil production is reaching up to 130 thousand tons. The company has a renewable energy production facility in Manavgat. This facility produces clean energy at an equivalent rate to Assan Alüminyum’s annual electrical energy consumption. In addition, the integrated recycling facility, where aluminium is recycled infinitely also allows the company to reduce its carbon footprint.
Oriented Activities
Sustainability is Top Priority Assan Alüminyum aims to create value for future generations by making positive contributions to sustainability. The
wspaper
www.aluminiumtoday.com Aluminium Show Newspaper 31•• Newspaper company, as one of the pioneers of the global flat rolled aluminium industry, adopts global sustainability targets as business principles, not as obligations. On this matter, Göksal Güngör, the General Manager of Assan Alüminyum Energy efficiency Assan Alüminyum regularly implements various energy efficiency projects every year. These projects reduce natural gas and electricity consumption resulting in reduced scope 1 and 2 emissions. The projects implemented in the last 7 years created an equivalent impact to the planting of 2,5 million trees. Through the company’s renewable energy production, which is equivalent to the annual energy consumption of 50 thousand households, the company obtains I-RECs (International Renewable Energy Certificates) through which scope 2 emissions are fully offset. •• Visit us on stand 6A23
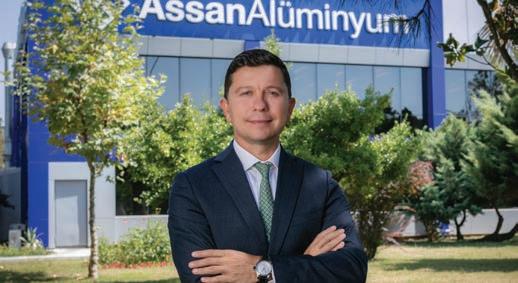
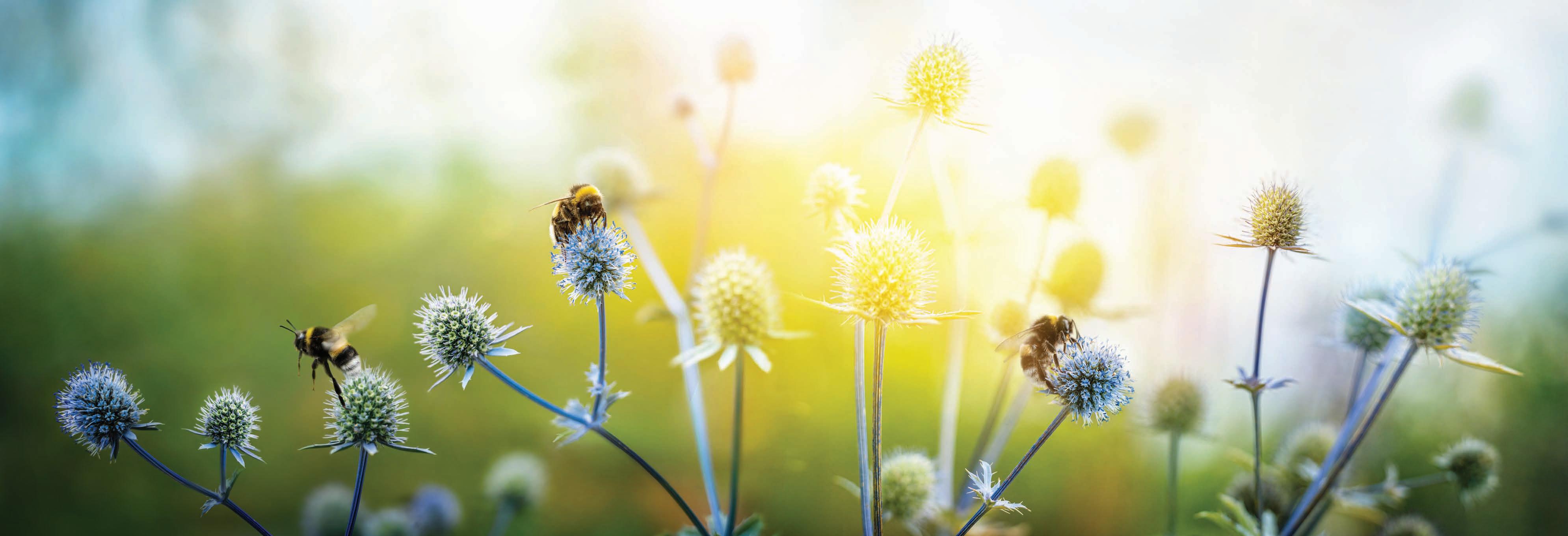
A key aspect of the success of this on-going pilot project is the excellent collaboration between the Fives and Qatalum teams. Qatalum has diligently tested and commented on the tool functionalities, proving excellent feedback in line with their continuous improvement culture. This pilot SMARTVibro project also beneficiates from the support of Fives ECL with its experience acquired during the implementation of SMARTCrane in other smelters.
Currently and throughout 2022, bi-monthly exchanges are planned with Qatalum to collect data for analysis, to provide ongoing configuration refinement and specific recommendations for improving system use and value. The SMARTVibro tool already brought up promising results and is expected to be fully operational by the end of this summer.
The implementation of Fives’ SMARTVibro solution in Green Anode Plants
•• 32 Aluminium Show Newspaper www.aluminiumtoday.com Newspaper Thanks to more than 65 years of experience as an OEM in various sectors of an aluminium smelter, Fives is in good position to understand the cross-links between the different processes. Fives has demonstrated an interest for the digitisation (industry 4.0) of the aluminium industry for several years by now. For instance: - Fives ECL has been proposing to train pot room crane operators on simulators for more than 20 years, - Fives Solios introduced self-adapting algorithms in the Green Anode Plant process 10 years ago As shown in the figure below, during the very last years, Fives accelerated the realisation of new digital products, covering the entire process chain and which are now ready for
Finally, at the beginning of December 2021, the installation and start-up of the solution took place, and the personnel was trained to the use of the tool.
Fives’ Key findings for successful digital implementation are as follows: • Aluminium producers’ stakeholders must have faith and trust in data value Target first, achievable results, accept imperfection or limited scope, then improve or complete the solution Various disciplines must be involved from the project launching:△OT/ITexperts△Operationpeople and Process experts
In a GAP, the vibro-compactor is the most complex and critical equipment and often the bottleneck in production. Its monitoring is therefore essential to maintain and increase the GAP overall performance. This is why SMARTVibro is the first “Smart” tool developed by Fives Solios. SMARTVibro monitors the operation of the Fives’ Xelios vibrocompacting machine, reports “smart alarms” to operation and assists customer maintenance team in its preventive maintenance. With more than 60 vibro-compacting machines in operation, this solution has great potential for deployment.
With Fives, smart data drives plant performance and contributes to “faire aimer l’industrie”. By Christophe Bouché , Carbon Product Director at Fives Solios
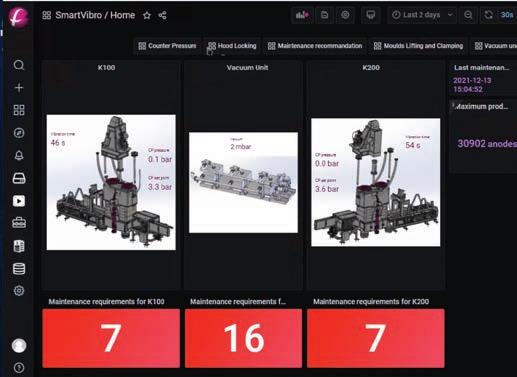
△ Maintenance people △ From both the managing and the floor teams
understanding of the process and the key equipment functioning allow Fives to design solutions fitted for smelter people. Thus, such digital solutions aim at better controlling of both process and operations, allowing « factual data checks», with less conflictual discussions between smelter departments to improve global performance faster. Digital solutions are not only a question of complex OT/ IT tools for gathering data, but also algorithms developed to propose meaningful information, for all involved people, from the floor up to the top management. Fives’ solutions are built on standard modules or technology bricks, nevertheless, they are adapted to each customer needs through an AGILE finalisation phase. The customer stays the owner of the data and if cybersecurity analysis and counter-measures are carefully applied, the generated databases may be safely accessible for any further analysis evenTherefore,remotely.the concept of Industry 4.0 which was still considered as a “nice to have” few years ago, is now considered by our customers as a true solution to improve the performance of existing facilities.
As mentioned, Fives is able to offer a wide range of digital tools dedicated either to process optimisation like the AMELIOS Suite or to equipment health monitoring like the SMART Suite. The SMART Suite started with the SMARTCrane product developed by Fives ECL. It closely monitors the operations in the potroom by analysing all the signals associated to the pot tendingFollowingmachines.thesuccess of SMARTCrane that is now running or under deployment on several reduction lines, Fives decided to develop the same concept to core pieces of equipment in the green anode plant (GAP).
The SmartVibro project started in 2020 with the support of Fives CortX, a subsidiary of Fives group dedicated to Industry 4.0. The first phase consisted of identifying all possible failure scenarios, resulting in the creation of 120 potential smart alarms. The technology based on a gateway box and data analysis software, is relatively simple, although additional new decision support functionalities will be added later to take full benefit of the all data collected and propose predictive maintenance capabilities.
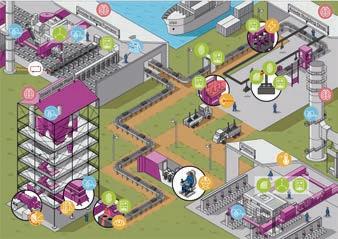
Fives approached Qatalum who had a first successful experience with equipment advanced condition monitoring in the paste plant in 2018 and who was keen on such technology.Fivesproposed a cooperation agreement to install SMARTVibro in Qatalum with remote access to allow Fives to obtain real-time performance data. After constructive discussions on contractual and cybersecurity issues, the final solution was validated by both parties.
Theimplementation.comprehensive
Demands and expectations are then very high. The first benefits have already been demonstrated: they deal with material consumption, improved OEE, environmental impact, valorised product quality as presented in several aluminium conferences in 2021 such as TMS, ICSOBA or FAF.
SMARTVibro continuously sends information to Fives’ experts, who analyse them more easily and feed the continuous improvement loop of this product line. This information is then helping Fives’ service teams to communicate more effectively with customers by better identifying and qualifying their pains and thus better targeting the interventions.
Process TrackingAdvancedEquipmentoptimisationhealthmonitoringcontrol&sensorssystem
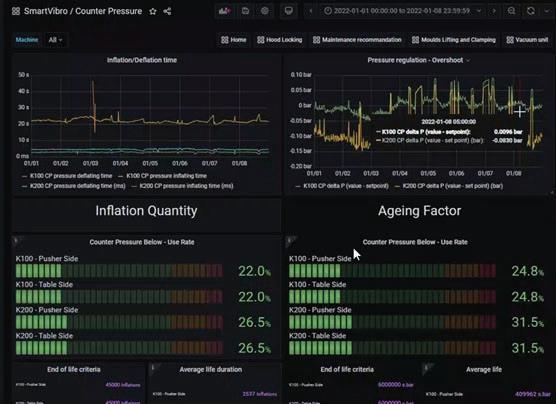
For Qatalum, this project addresses the following objectives:Improving maintenance monitoring through online critical event-based equipment condition and operating data, for better planning of interventions Monitoring machine performance in terms of overall equipment efficiency, Early warning detection • Remote monitoring to machine performance with a range of diagnostic and analytic reports
At the beginning of 2021, Fives was looking for an industrial partner to deploy the first release of SMARTVibro.
marketthealuminiumHigh-qualityforconsumer www.fivesgroup.com ALUMINIUM For you, industry brings innovation to life. Behind lightweight and recyclable cans, is an industry that produces the finest quality of aluminium, using high performance manufacturing Fromtechnologies.designing process equipment to supplying complete installations and services, Fives is one of the world’s leading aluminium industry suppliers, improving performance, the environmental footprint and quality of its customers’ products. Each day, Fives demonstrates that Industry can do it.

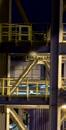

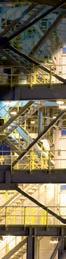




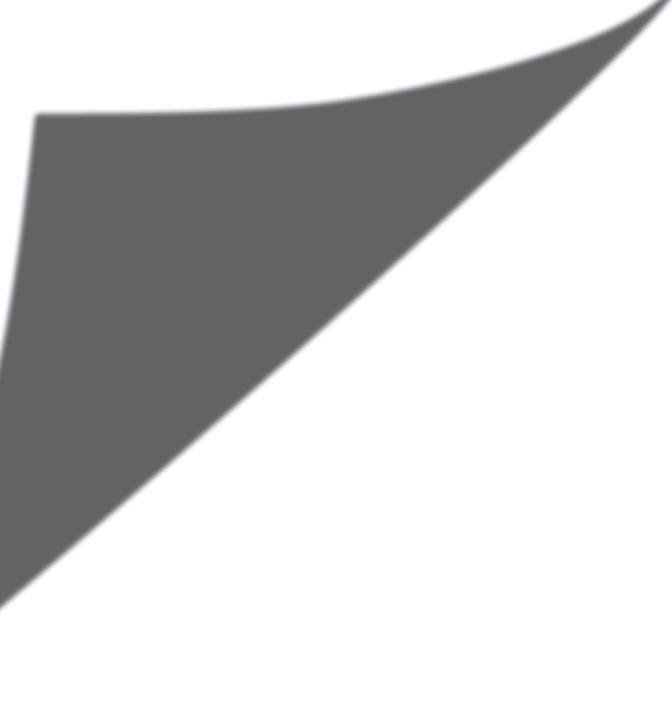


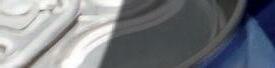


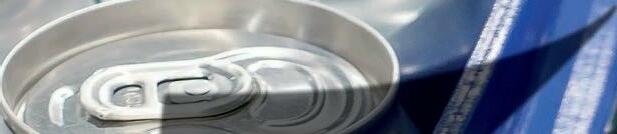

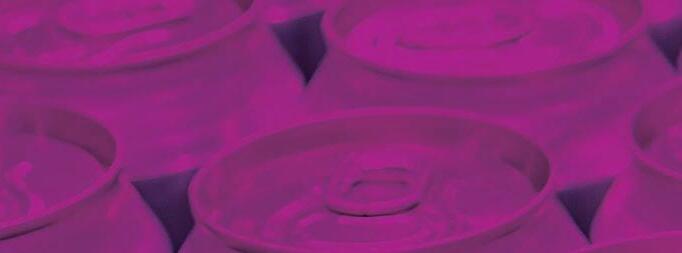


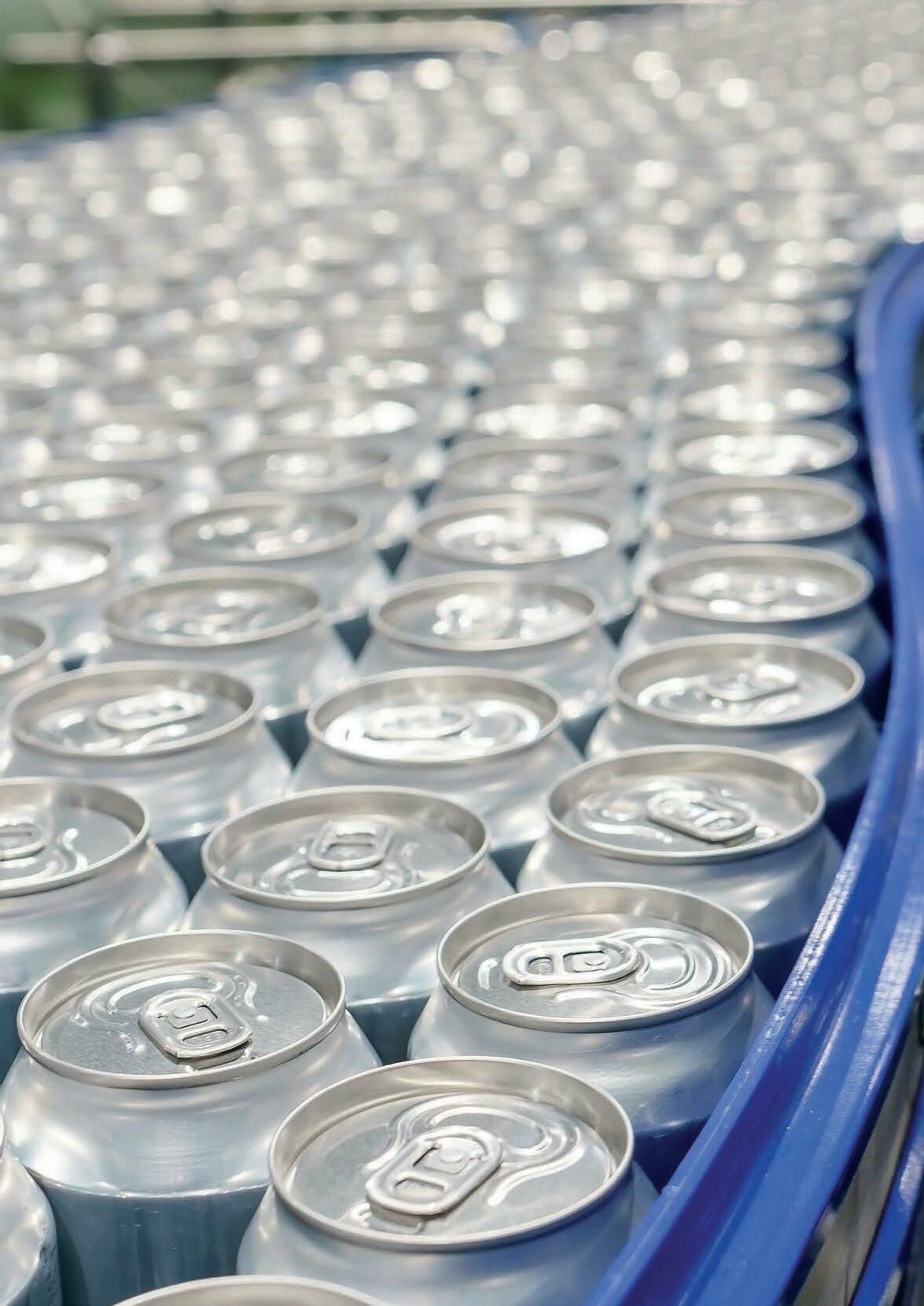
Maximise Productivity of your Cast House with RiA: Charge at the earliest and safest time, every time
RIA Cast House Engineering provides precision rail-mounted Cast House proven Charging and Skimming equipment for Aluminium Cast Houses worldwide. The design and development of all RiA Machines take reliability, durability, maintenance and occupational safety into account. RiA has supplied over seventy Furnace Charging and Skimming Machines, all rail-mounted and capable of Charging up to 30 Metric Tonnes in less than 90 seconds or Skimming a Furnace faster than a traditional Forklift Truck or wheeled Furnace Tending Vehicle, but with more repeatable results and without damaging the refractory lining.
Fig 2: RiA’s On-Board Camera monitoring the Furnace Charging cycle, relaying the footage to operators who can be situated in the safety of the operator pulpit.
Several clients have multiple Machines in the same Cast House or across multiple sites and territories. One client alone has implemented more than thirty RiA Machines in ten different countries. In recent years, in conjunction with our exclusive partner Fioscope GmbH, RiA added the innovative capability of AI Smart Camera based decision making to our Machines to offer fully Autonomous operation and therefore removing the requirement to have operators on or near our Machines. RiA’s Managing Director, Michael Rockstroh also became Managing Director of Fioscope GmbH in February 2022, helping to drive the continuous development of RiA’s AI enabled Autonomous Machines and assuring our growing customer base that RiA equipment is not only suitable for today, but also tomorrow and beyond.
•• 34 Aluminium Show Newspaper www.aluminiumtoday.com Newspaper
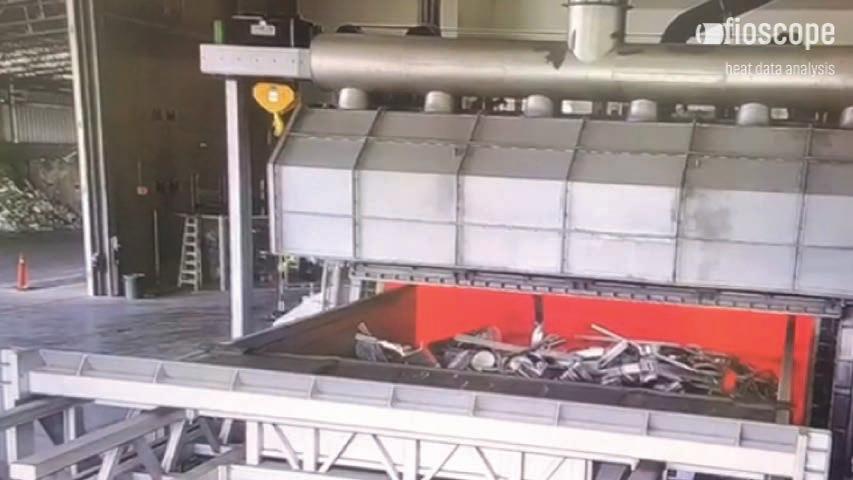
Fig 1: Screenshots of RiA’s Intelligent Cameras relaying real time information of melt progress to the Cast House.

Even if you do not yet operate RiA’s Charging and Skimming Machines, using our In-Furnace vision technology would allow you to safely recognise when it is the optimum time to charge your Furnace, knowing that you are doing it at the earliest and safest time, every time.
Introduction
Autonomous Operation Maximising Productivity In typical operations, the melt cycle cannot be observed without opening the door and losing heat and energy, as well as the associated safety risk to the operators. Therefore, valuable minutes can be lost if the Furnace is ready to receive the next charge, but the operators are unaware since the contents are not visible. For several years, RiA have integrated Smart Cameras onboard its Machines and in Furnaces to enable Autonomous operation. Significant advances in process control are then possible using air-cooled Smart Cameras. High-temperature resistant Cameras allow for real time observations of melt progress. They provide a safe and real-time process development benefit that was in the past impossible to even observe let alone monitor, without opening the Furnace door. RiA’s Intelligent Camera’s monitor the progress of the scrap pile, as it melts. The Camera’s determine the earliest possible moment in which the Charging Machine can deliver the next charge. Through this, Autonomous operation is possible. Figure 1 shows 3 still Images taken for the purpose of this article from the operator station at one of RiA’s fully Autonomous Charging Machine installations. Three different stages of the melt cycle are shown, following a charge. The first image shows the furnace with a scrap pile that has recently entered the furnace, using a ‘traffic light’ visual for the operators, the Intelligent Cameras not only relay the image but also highlight using the red light that the furnace is not ready to receive the next charge. A yellow signal on the second Image indicates that the Intelligent Cameras are detecting that the scrap pile has lowered in height and is therefore getting closer to the point in which RiA’s Charging Machine can enter the furnace without contacting the scrap pile. Operators are now alerted to the fact that within the next few minutes they must conclude loading the container to ensure RiA’s Charging Machine can deliver the next charge at the earliest possible moment, ensuring valuable production time is Finally,utilised.the third image and green light indicates that the Furnace is ready to receive the next charge. Previously, the Furnace door would need to be opened for the operators to confirm this information and make informed decisions, but in this case, RiA’s Intelligent Cameras detect the scrap pile is now low enough for the Charging Machine to enter, deposit the next load and retract from the Furnace without contacting the scrap already inside. Whilst ensuring maximum productivity through charging at the earliest appropriate time, there are also significant safety benefits as the requirement to open the furnace door is significantly reduced, combined with giving operators the assurance that they are not charging the next load into liquid aluminium. As operators are shown the time period they have to ensure the Charging Machine is loaded, this helps to ensure the Furnace contents will not be in a molten state, an important safety feature of high value to many of RiA’s customers. No time is lost during the charging phase of the melt cycle ensuring maximum productivity of your Cast House. Once the Charge Machine is loaded, operators can complete other tasks as RiA’s Intelligent Cameras trigger the cycle to begin, requiring no further operator interaction. Once the cycle is complete, the Machine moves back to the loading position to prepare for the next charge. As Figure 2 shows, the Furnace Charging cycle can be viewed safely from the monitor in the operator pulpit via another Camera mounted at the rear of the Machine.
Key customers include Hydro, Constellium, Kaiser, Matalco, Alumet and many others.
In summary, Smart Cameras reduce unnecessary door openings, shortening cycles and saving energy. These systems can increase safety and potentially avert accidents. Smart Cameras also allow the melt cycle to be optimised, ensuring charging can take place safely, at the first opportunity. Furnace Monitoring Systems allow playback, trouble shooting and diagnostics. It is believed that in the future all new Furnaces will incorporate In-Furnace Cameras. Contact RiA to find out how we can help optimise your operation.
AUTONOMOUSCHARGING&SKIMMINGMACHINES
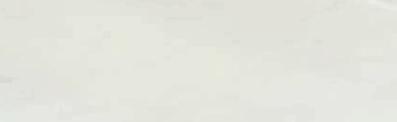
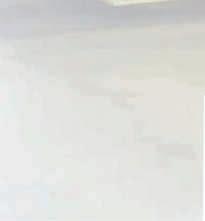
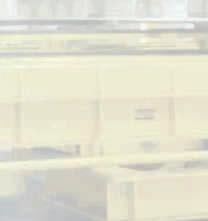

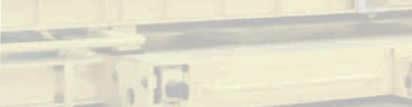

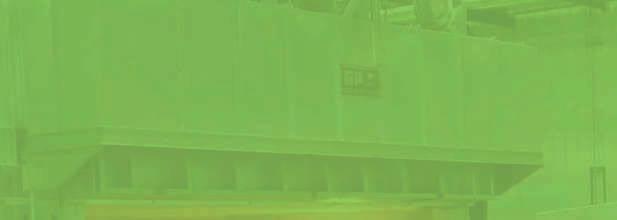

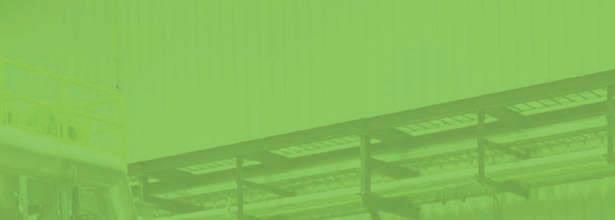





To find out more about smart solutions in the sense of a green, lean and digital future, visit the Achenbach stand (E 13 in Hall 3) at this year’s ALUMINIUM 2022. Here, visitors will also get a first impression of the new corporate design, also an expression of Achenbach’s further development into a provider of sustainable future concepts. 1: 3:
•• 36 Aluminium Show Newspaper www.aluminiumtoday.com
Ultimately, at Achenbach, the combination of innovative technologies, the perfect interaction of all machines and the optimal design are the key in terms of quality, performance, and sustainability. With Green.Lean.Digital, Achenbach has set out to sustainably increase the customer’s benefit and thus his competitiveness on the basis of future-oriented solutions.
Figure
Achenbach Smart Plant for battery foil production Smart Solutions for a green, lean, and digital future
The aluminium industry is facing major investments in sustainable production facilities that qualify the ‘magic metal’ aluminium with its versatile application options as an ideal material for the future. Whether for its 100 percent recyclable packaging solutions, battery foils for electric vehicles as well as electrical storage or highstrength aluminium alloys for automotive applications or as a part for innovative components - aluminium is in the fast lane due to its unique properties.
Only recently, a productivity increase of almost 30 percent was achieved in a study at a customer’s thin strip mill with the help of the OPTILINK platform, collecting and evaluating rolling data over a certain period and taking appropriate measures.

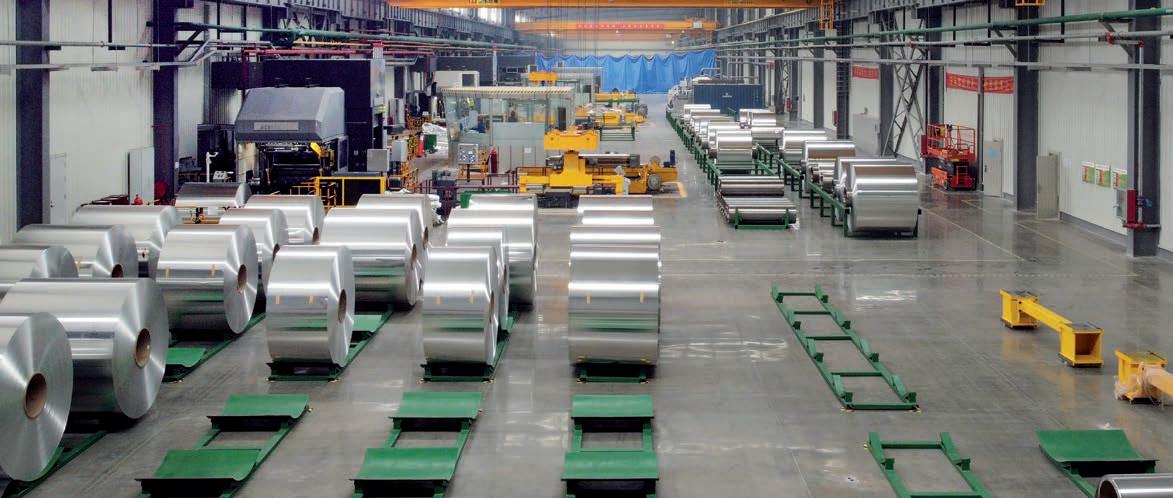
Achenbach UniTorque Direct Drive Technology Figure 2: Achenbach AIRPURE® Exhaust Air Purification Systems Figure
With the commitment Green.Lean.Digital Achenbach is setting clear signals towards future challenges to achieve a sustainable optimum for its customers, with innovative technologies demanding sustainability and profitability on the one hand and an integrative approach for optimised production supported by digitalisation on the other. With sophisticated technical knowledge, decades of experience and a high standard of perfection, Achenbach supplies its customers worldwide with first-class machinery. Well-targeted development work is the key to meeting future challenges and tapping the potential for success in tomorrow’s market. Specifically, Achenbach has recently developed numerous components in the rolling mill sector, which are increasingly being used by customers. They show that sustainability and productivity are no longer considered opposites, but rather increasingly mutually dependent. This is because sustainable machines consume less energy in production and especially in operation and are thus more productive because less must be used for the same output quantity. For example, a new technology to optimise flatness at the strip edges is the innovative Achenbach UniHeat Advanced Hot Edge System. Whereas heat dissipation beyond the strip could previously be delayed by targeted application of hot rolling oil, the heat is hereby inductively generated directly in the roll. This process is not only about 5 times faster but also requires significantly less energy. Thus –compared to a conventional hot edge system using hot oil – this new system of strip edge heating saves up to 90 percent of electrical energy. Replacing the conventional system with the inductive system guarantees a quick return of investment and moreover minimises the CO2 footprint of the production. Besides this, the new Achenbach UniTorque Direct Drive Technology (figure 1) also helps to reduce the carbon emission. This advanced technology, in which the motor is integrated directly into the coiler, convinces with excellent controllability in all power ranges, the absence of gears and clutches and with an overall efficiency of more than 95 percent due to lower friction with improved engine efficiency. Furthermore, it offers significant savings potential for the customer, resulting from less CAPEX due to reduced construction costs as well as less OPEX by minimised maintenance and reduced number of spare parts. Regarding the ecological and economic added value, it is above all the accompanying Achenbach OPTIPURE Media systems that convince numerous customers within the context of current orders for rolling mills. Always tailored to the specific application, Achenbach AIRPURE® Exhaust Air Purification Systems as well as Achenbach ROILPURE® Rectification Systems serve the energyoptimised separation, recovery, and regeneration of the rolling oil, so that it can be returned to the rolling process in as-good-as-new quality instead of buying new rolling oil. This is not only very sustainable due to the conservation of resources, but also extremely profitable due to substantial savings in consumption costs. For example, using an AIRPURE system cleaning the exhaust air from up to 7 rolling mills, enables the customer to recover an average of almost 100,000l of rolling oil per month (figure 2). With the goal of achieving a sustainable optimum for the customer, it is not enough to supply first-class stand-alone systems. The excellence of each individual machine along with a consistent link between the machines and systems themselves are the key to the highly productive and equally sustainable manufacturing of premium aluminium flat products. With its integrative approach, Achenbach is particularly qualified for complex foil plants including multiple production stages in the value-added chain. In this way, the entire production process from rolling to slitting to further processing can be perfected in its entirety. ‘Everything from a single source’ from Achenbach guarantees optimal material flow in the production process without interface losses and allows for economies of scope to the benefit of operators. With this in mind, new customers in particular are increasingly opting for the total solution from Buschhütten. On the Indian market alone, giving the increasing demand for aluminium foil and flexible packaging, Achenbach has received eight orders for new Achenbach Smart Plants with rolling and slitting technology since 2019. Especially for complex production plants in the battery foil sector, Achenbach’s integrative solution approach is perfectly suited to meet the highest quality demands of the end product as well as the requirements in terms of sustainability and productivity. Europe’s largest battery foil production in Hungary successfully went into operation at the beginning of this year and is a benchmark for comparable, demanding production plants. Two further Achenbach rolling lines especially for the production of battery foil in China started production last year (figure 3), another one has recently been ordered. However, the decisive factor regarding production optimisation is digitalisation making sustainable results possible in the first place. With the cloud-based analysis system Achenbach OPTILINK®, machine data from various sources can be systematically recorded across the entire process chain and valuable information on the entire production process can be extracted from it. As a result, the customer benefits not only from the most efficient production possible, but also from a relevant reduction in energy and resource consumption. “With OPTILINK Energy Monitoring, we can make a major contribution to greener aluminium by monitoring and optimising energy use in relation to a single coil,” says André E. Barten, CEO of Achenbach. Active monitoring and warning systems can detect problems in good time and intervene preventively to minimise waste and scrap, such as in the case of running aggregates despite machine downtime.
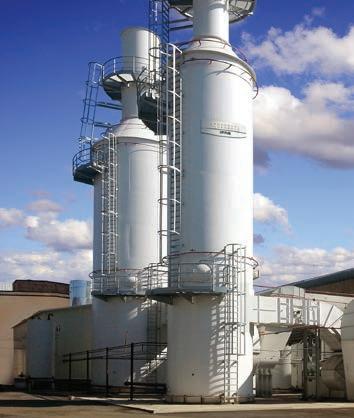
SINCE 1452 VISIT US HALL 3 E13 Achenbach Buschhütten GmbH & Co. KG · sales@achenbach.de WITH ACHENBACH INTO A GREEN, LEAN AND DIGITAL FUTURE ONESUSTAINABILITYSTEPAHEAD
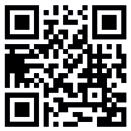
Higher efficiency and energy savings through high saw blade life and low chip waste. For the perfect production of aluminium blanks At the “Aluminium” trade fair in Düsseldorf from 27 to 29 September 2022, August Mössner GmbH + Co KG will be showing application examples of the wide range of its solutions for the aluminium industry. These include sawing, testing and handling of Mössneraluminium.offers a comprehensive portfolio of saws for processing T-bars, rolling ingots, plates, blocks and billets. The saws are unique in their solid steel construction, the precise cutting process and the long saw bladeMössnerlife. ingot saws are in operation worldwide. Adapted to different customer requirements, rolling ingots and T-bars are reliably cut to size. The sawing technology is used in primary and secondary aluminium production. “Planning, development, assembly and commissioning are carried out by our expert staff. The experience and know-how from 125 years of mechanical engineering flows into the development. Our customers worldwide appreciate the turnkey delivery of the plant technology “, explains Christian Kunz, Managing Director and Sales Manager at Mössner. Mössner’s ingot saws are available in various configuration levels. Depending on the customer’s needs, the ingots are imported, for example, by a downender. Heavy-duty shuttles then transport the ingots to the sawing area or, alternatively, stow them in the designated buffer area. Innovative handling systems and automated scrap, head and foot cut disposal allow for almost autonomous operation. After weighing and marking, the rolling or T-bars to be processed are ready for removal. If panels of different thicknesses are to be produced from one ingot, the Mössner horizontal saws are suitable for this.
•• 38 Aluminium Show Newspaper www.aluminiumtoday.com Proven energy saving from 15–60% Typical heat dross reduction abaut 20% Low NOx /reduced CO2 emissions High bath coverage Custom configuration Quadraflo© Sweep Aluminum Melting System ® Tel.: +41 (0)71 649 20 90 www.hotwork.agcontact@hotwork.ag

• Conductivity testing systems You can see Mössner’s systems “in action” at any time on Mössner’s YouTube channel. Mössner develops and builds special solutions in the fields of mechanical engineering, automation technology and robotics. With its 140 employees, Mössner is also able to handle larger projects without losing the necessary flexibility for special solutions. At its site in Eschach, Mössner develops, manufactures and assembles the systems and commissions them for its customers worldwide. In the field of aluminium technology, Mössner offers precise sawing and milling systems for primary and secondary aluminium production. These enable the processing of rolling ingots, T-bars, blanks, contours, circular blanks, samples, blocks and plates. August Mössner GmbH + Co KG, Hohenstaufenstraße 3, D-73569 Eschach, Phone +49 (0)7175 99806-0 | Phone +49 (0)7175 99806-35 | post@moessner-kg.de | www.moessner-kg.de
The horizontal saws are able to precisely produce blanks as panels in different sizes. This reduces the over-milling of the slab to a minimum and the customers receive more marketable material.
Mössner offers further innovative products for aluminium technology: Contour saws Vertical block saws with optional saw blade Circularrotationsawsfor the production of aluminium circles • Circular plate saws • Saws for the aerospace industry
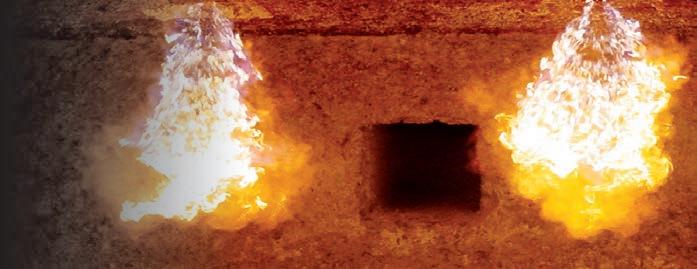
••
“With our turnkey, fully automated plate production, which also includes the process steps of milling, foiling and handling, our customers are always one step ahead,” explains Oliver Vogt, Product Manager in the Aluminium Division at Mössner.
Higher efficiency and energy savings through high saw blade life and low chip waste For the perfect production of aluminium blanks
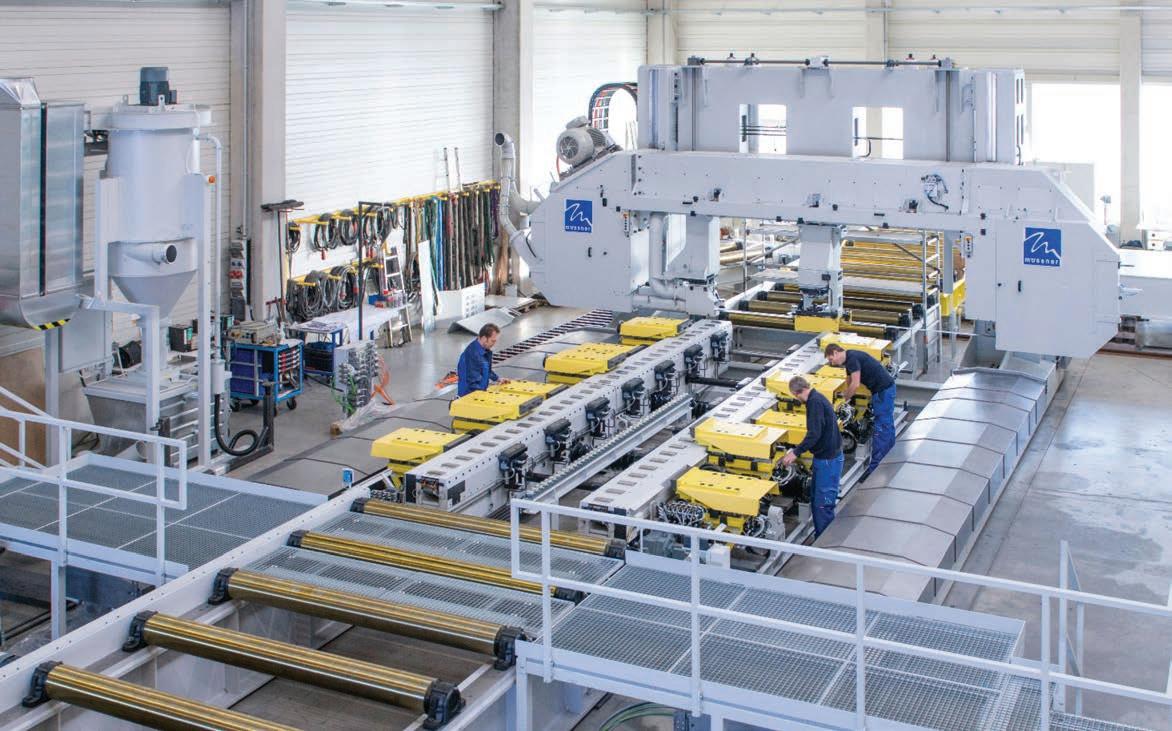
precimeter.com
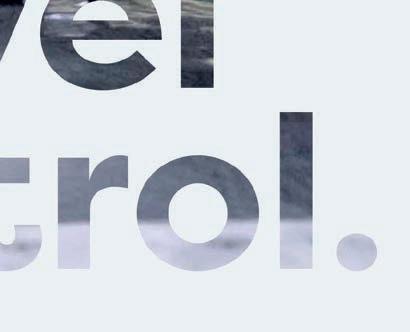
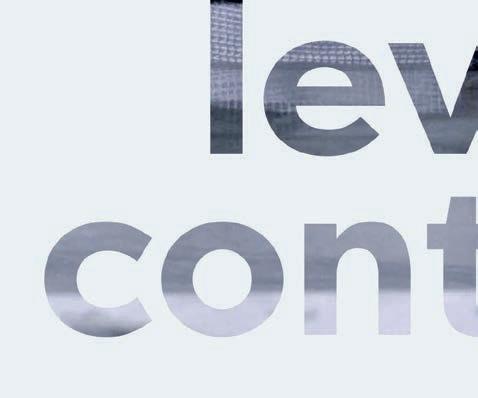

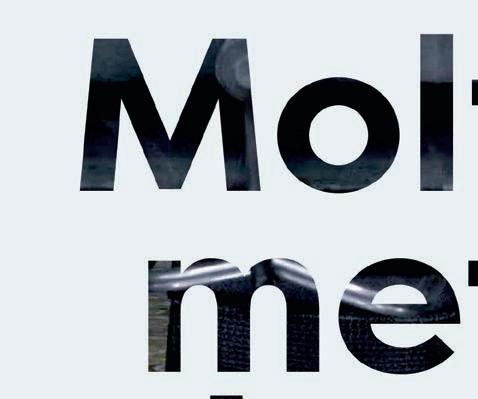
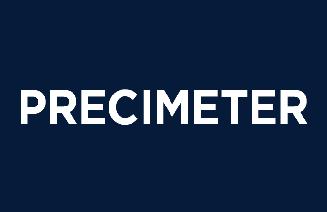

ALUMINIUM
Climate action and sustainability
•• 40 Aluminium Show Newspaper www.aluminiumtoday.com Newspaper
Rolling out novel technologies
GREENER SUMMIT 2022: Aluminium decarbonisation –from pathways to action
Near-zero electricity related emissions Aluminium production has always been an electricity-intensive process and under both the Beyond 2 Degrees Scenario and the 1.5 Degrees Scenario, it is the electricity-related emissions that require the greatest reduction to just 2% of 2018 levels. Whilst some moderate reductions in emissions could be made through further energy efficiency measures, the scale of the challenge – eliminating almost 700 million tonnes of CO2e emissions – should not be underestimated. In order for the sector to align with either decarbonisation scenario its overall power mix would need to be almost fully decarbonised via zero-carbon energy sources or through the installation of significant carbon capture and utilisation (CCUS) capacity. The required reductions in overall emissions translate into a reduction in carbon intensity from 16 tCO2e/t primary aluminium in 2018 to just 2.5 tCO2e/t (2 Degrees Scenario) and 0.5 tCO2e/t (1.5 Degrees Scenario) in 2050 (Figure 3). There is minimal commercial production currently at these Paris-aligned levels; even the lowest emissions operations today will need to reduce emissions further.
Pernelle Nunez, Deputy Secretary General, Director – Sustainability, International Aluminium Institute
To achieve such reductions, three pathways have been identified and focus on a suite of different technologies to address: 1. Electricity related emissions 2. Direct and thermal energy related emissions 3. Circularity and resource efficiency
use a combination of heat and electricity, and the cost of introducing less carbon-intensive technologies is high. In order to meet global climate goals, all industries are going to have to reduce emissions from current levels and the aluminium sector pathways demonstrate the deep reductions needed across the sector to meet the objectives of the Paris agreement. The IAI wanted to ensure its sector pathways analysis was rooted within an economy-wide context and a broader, systems-wide decarbonisation trajectory. With this in mind, two decarbonisation scenarios were developed which broadly align with the International Energy Agency’s Beyond 2 Degrees Warming Scenario1 and 1.5 Degree Warming Scenario2 which consider pathways for the global energy sector.
3. 1.5 Degrees – broadly aligned with IEA’s Net Zero Analysis from which a sector budget was calculated for the full sector Underscope.these scenarios, total sector emissions in 2050 varied significantly from about 1.6 billion tonnes CO2e under the Business-as-usual scenario to about 50 million tonnes under the 1.5 Degrees Scenario.
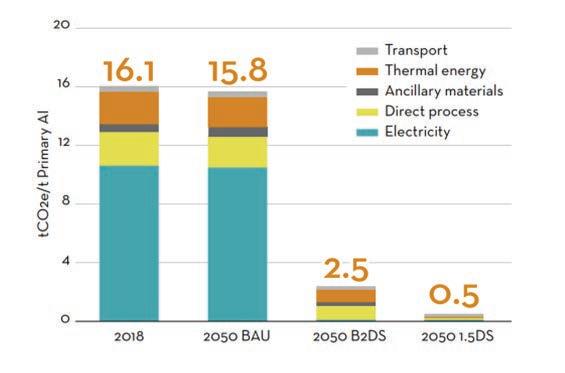
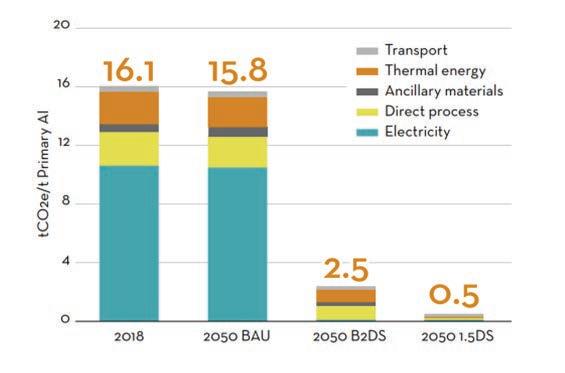
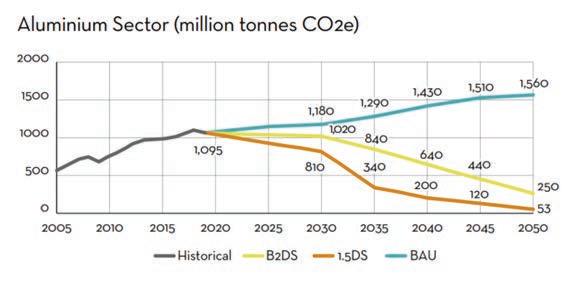
Establishing the sector baseline In developing the sector GHG pathways to 2050, establishing the baseline was an essential first step. In 2018, an ingot of primary aluminium had an average cradleto-gate (mine to casthouse) footprint of ~16 t CO2e/t Al based on the IAI’s life cycle work. Recycled aluminium was much less carbon intensive at 0.6 t CO2e/t Al. These figures give an emissions baseline for the sector for 2018 of 1.1 billion tonnes of CO2e – about 2% of total global annual GHG emissions3. Emissions associated with electricity constituted the largest share at approximately 700 million tonnes of CO2e, followed by process and thermal energy at 300 million tonnes of CO2e and ancillary materials production and transportation within the supply chain at 100 million tonnes (Figure 1).
Figure 1: Aluminium sector emissions by type (2018) Figure 2: Aluminium sector scenarios to 2050 continued on page 42 Figure 3: Primary aluminium emissions intensity 2018 and for the three 2050 scenarios Figure 4: Share of primary and recycled aluminium to 2050
Whilst the industry continues to grapple with the challenges of climate change, it has already taken decisive action where possible and is investing in low-carbon technologies. From inert anode scale-up and testing to increased solar, wind, nuclear and hydropower electricity generation – there have been a number of notable announcements from companies across all producing regions on projects to help reduce emissions as rapidly as possible.
Sector emissions in 2050 With the baseline established, three scenarios for the sector to 2050 were developed as part of the analysis (Figure 2):
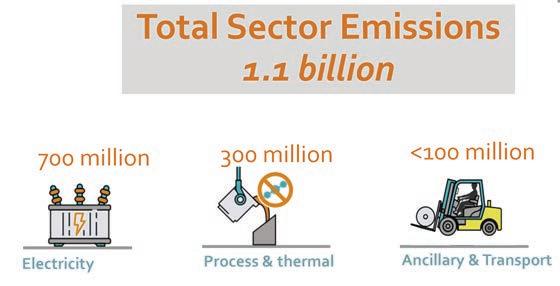
In recent years climate change has risen steadily up the business agenda; once relegated to side sessions at industry conferences, it is now an integral part of most keynote panels with climate challenges and emissions reduction plans regularly debated by executives of multinational aluminium companies. It is readily acknowledged as a major risk for organisations across many industries and the aluminium industry is no different. Climate change is by no means the only sustainability issue facing the sector, but it is widely recognised as one of the most pressing.Within this context, the International Aluminium Institute (IAI), the association for the global aluminium industry, set out to develop greenhouse gas pathways (GHG) for the sector to 2050 to understand what alignment with climate goals means for the sector in practice. In line with its 50year history as the go-to organisation for open-access industry data and analysis, the IAI adopted a data-driven approach, bringing together its long-standing life cycle and material flow modelling work to develop the first comprehensive aluminium sector pathways for the industry and other stakeholders. Pathways for a hard-to-abate sector Aluminium is often grouped with other industrial sectors that are significant emitters of greenhouse gas emissions, such as steel and cement. These are labelled as ‘hard-to-abate’ sectors because they are energy intensive,
1. Business-as-usual – assuming minimal changes from current operating practices and additional capacity coming on stream to fulfil growing demand for aluminium to 2050.
In some cases, these pathways require the adoption of existing technologies such as wind or solar generated electricity whilst others are dependent on the success of nascent technologies or those yet to be applied to aluminium production processes such as inert anodes, hydrogen, CCUS or mechanical vapour recompression. Many of these new technologies are currently at research and development or pilot scale and will require significant investment and collaboration to successfully roll out across the sector at the scale and pace required.
2. Beyond 2 Degrees – aligned with IEA’s Beyond 2 Degrees Analysis from which a sector budget was calculated for the full sector scope.
– MAY
PSImetals empowers sustainable operations for generations to come www.psimetals.com/ Software Excellence for Steel & Aluminium Producers
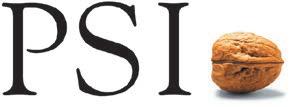
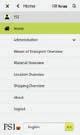
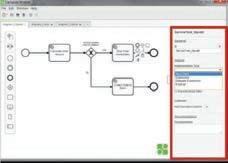
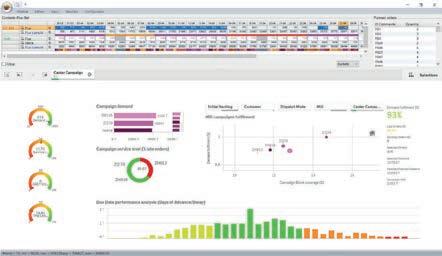

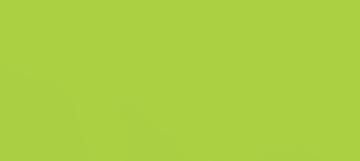

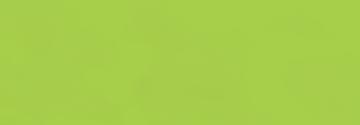
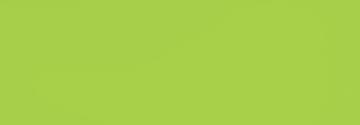
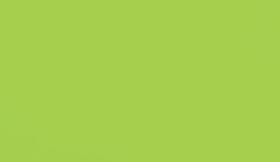
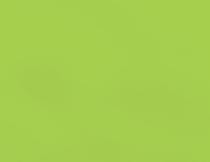
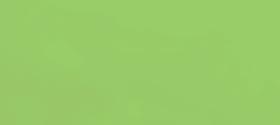
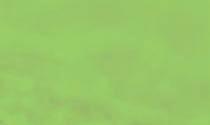
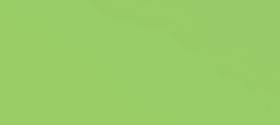
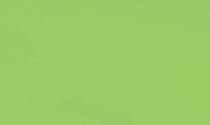
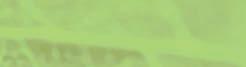
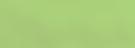
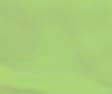

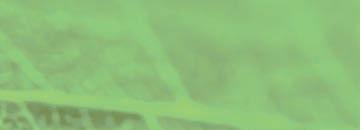
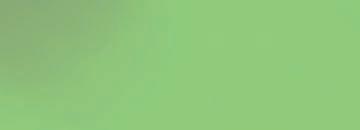
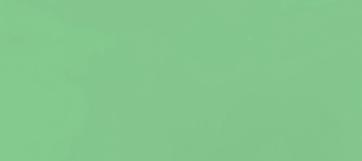

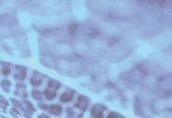
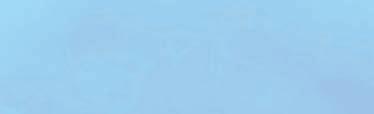
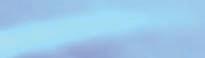
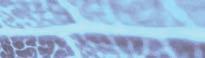

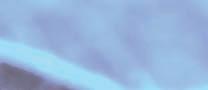
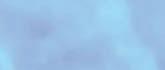

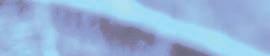


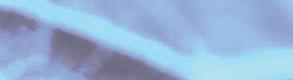
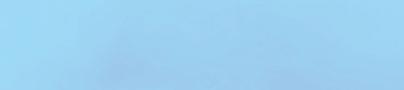
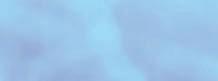


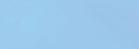
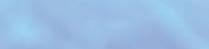
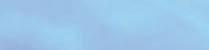
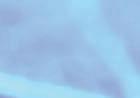
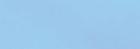



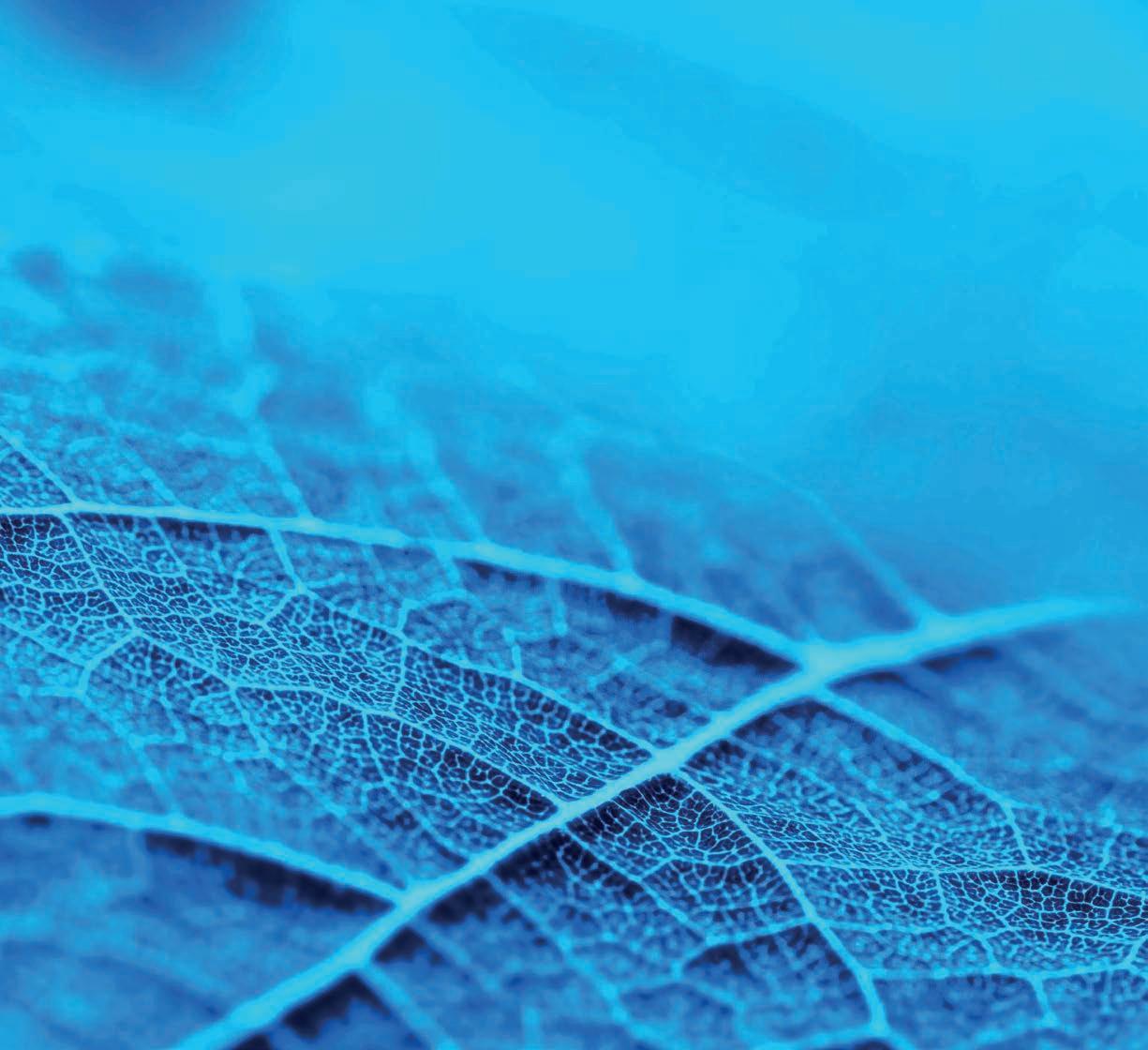
•• 42 Aluminium Show Newspaper www.aluminiumtoday.com Newspaper


Opportunities in a sustainable world Recyclability, along with its light weight and conductivity, mean that aluminium is a material valued in a number of growing end-use sectors including transportation, electrical infrastructure and packaging. Green policies provide significant opportunities for aluminium and the industry should look to maximise these, substituting where possible for other materials based on aluminium’s superior sustainability credentials. For example, in transportation, the shift towards electric vehicles is likely to increase aluminium demand by 12 million tonnes 2020-2030 as electric powered vehicles contain between 60 to 80 kg more aluminium than those powered by internal combustion engines. Similar opportunities exist in the packaging sector where both recyclability and light weight are in high demand and present potential for increased substitution of plastics and glass. In the electrical sector, aluminium’s importance in photovoltaic cells and power distribution provide further opportunities for the metal as a material of the future with increasing electrical infrastructure required as part of transitions to lower-carbon energy systems.Thereare significant opportunities for aluminium in societies that are aiming to become more sustainable. Aluminium has strong credentials as a material of the future, performing well compared to competing materials in a number of end-use sectors (Figure 5). The industry is well positioned with clear pathways, guidelines and standards to help deliver on the increasing transparency and data-driven approaches demanded by stakeholders. It is clear that aluminium is an essential material for a sustainable future, but in order to continue being a material of choice, it must itself be sustainable.
Author Bio: Pernelle Nunez is the Deputy Secretary General and Director of Sustainability at the International Aluminium Institute. She is responsible for the Institute’s broad sustainability work program and has worked on a range of collaborative industry projects including; life cycle impact assessment, environmental footprint analyses, sustainable waste management and GHG emissions accounting. Pernelle was a Lead Author for the Intergovernmental Panel on Climate Change’s (IPCC) 2019 Methodology Report Update to the 2006 National Greenhouse Gas Inventory Guidelines. She is also active in the IAI’s work on bauxite mining which encompasses issues such as biodiversity and community engagement. Pernelle holds a MSci Geology (Hons) from the Royal School of Mines, Imperial College London and a Postgraduate Certificate in Sustainable Value Chains from the University of Cambridge’s Institute for Sustainability Leadership.
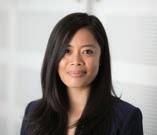
There have also been a number of collaborative initiatives at the R&D level which seek to build confidence and capacity in newer technologies, ultimately enabling further development and commercial deployment. Often such initiatives involve industrial partners working with research institutes cofunded by public and private sources. Such models are likely to be increasingly prevalent as corporate and national climate change strategies align over the coming years and climate-aligned finance begins to play a greaterWhilstrole.this climate action has been a priority for the industry, it is clear that the conversation has evolved over the past few years from being almost exclusively carbon-focused to one which accepts that decarbonisation cannot happen at any cost. Decarbonisation plans and technologies cannot be detrimental to the overall sustainability of operations. Similarly, it is increasingly acknowledged that climate change is not the only sustainability challenge that the industry must rise to and so efforts to address emissions need to be part of a broader sustainability plan and approach. To that end, we have seen companies adopt more sustainable practices in areas such as mining, water management, waste management and social impacts in parallel with their work on climate action. This integrated approach is likely to be increasingly important as stakeholder expectations around responsible production and sourcing grow. Recycling is only part of the solution The recyclability of aluminium is one of its key benefits and is crucial to the sector’s circularity and emissions challenges. Recycled metal has on average a much lower carbon footprint than primary metal and so through increased recycling, it is possible to reduce the overall sector footprint. Currently, recycling reduces the need for over 20 million tonnes of primary aluminium and so avoids approximately 300 million tonnes of associated emissions. Looking ahead to 2050, there are certainly savings to be made through more efficient use of aluminium, increased collection rates across all end-use sectors and the elimination of losses from the system, but it is important to remember that scrap is in itself a finite resource and is only a part of the sector’s decarbonisation pathways. With approximately 75% of all aluminium still in productive use – in cars, buildings and infrastructure – there will not be sufficient volumes available to completely replace primary aluminium. Recycled aluminium will increase its contribution to supply over the coming years as more scrap becomes available when products reach the end of their life and collection systems improve, but primary aluminium will continue to be needed to meet growing demand and so decarbonisation efforts across the sector must continue in parallel with initiatives to increase circularity and resource efficiency.
Aluminium performs well against competing materials in beverage container packaging4 Mössner develops and builds machines for cutting aluminium slabs, blocks and plates. Adapted to customer requirements, the special machines are individually equipped with a variety of components for an optimal solution to specific work processes. Visit us: Aluminium 2022, 27-29 September 2022 Düsseldorf, Hall 5 Booth 5C37 www.moessner-kg.de Quick and precise. Aluminium cutting machines from Mössner
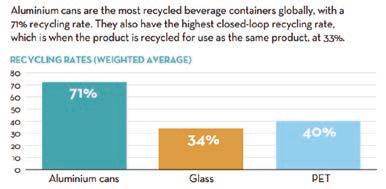
https://www.iea.org/reports/energy-technology-perspectives-2017 2 https://www.iea.org/reports/net-zero-by-2050 3 https://international-aluminium.org/resource/aluminium-sector-greenhouse-gas-pathways-to-2050-2021/ 4 https://international-aluminium.org/resource/aluminium-beverage-can-study/
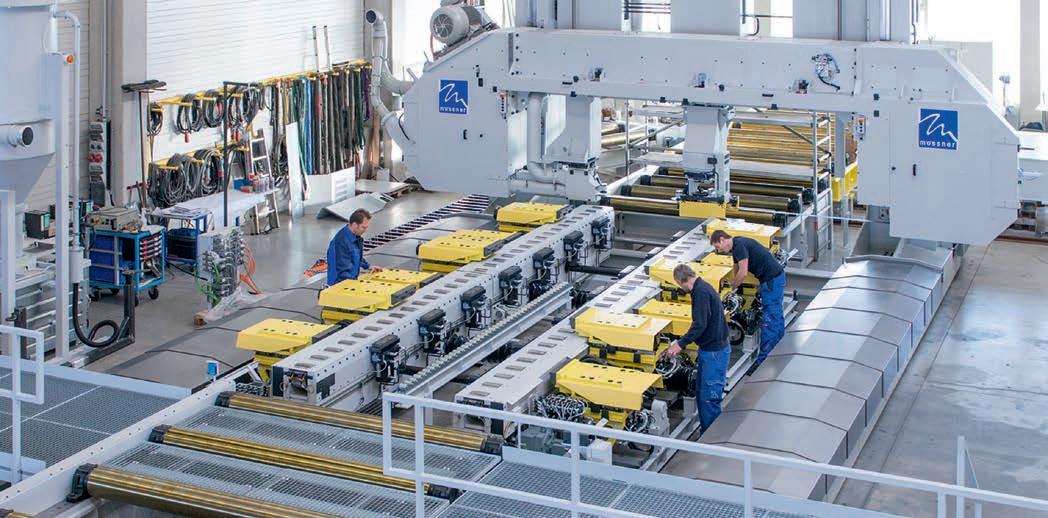
1
Figure 5:

THE NEXT DIMENSION IN GRAIN REFINEMENT Up to 85% less grain refiner needed for cost savings 120% relative efficiency compared to high efficiency refiners Reduced particle count consistently increases melt quality Made with low carbon aluminium +44 (0) 121 684 0175 | info@mqpltd.com | www.mqpltd.com


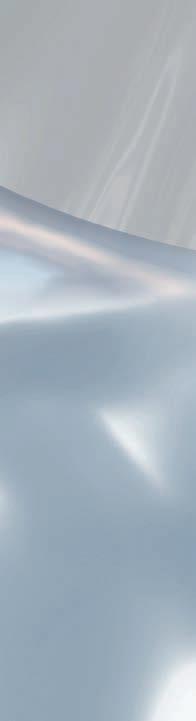


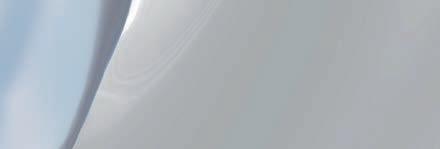

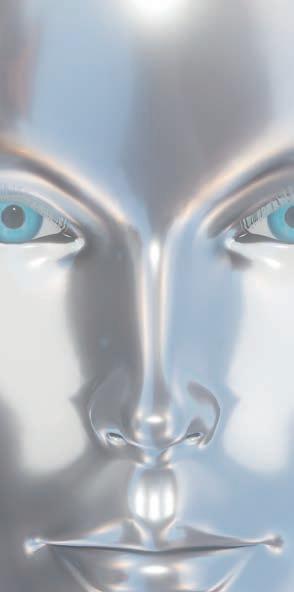
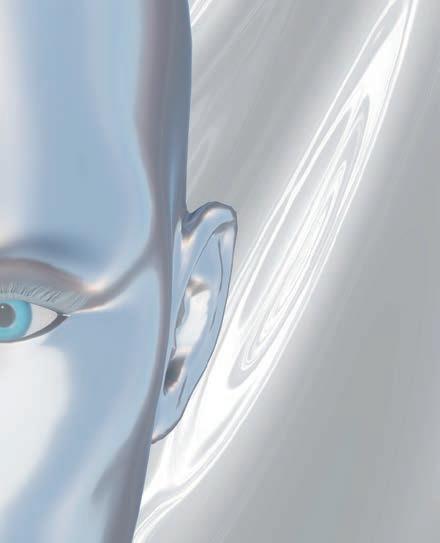
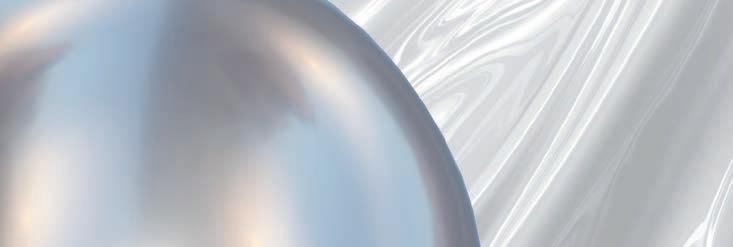

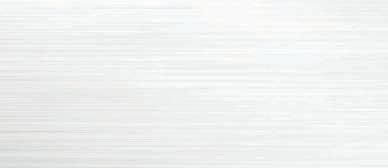


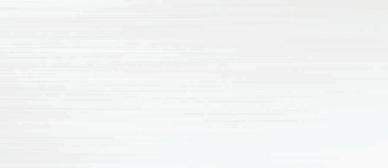
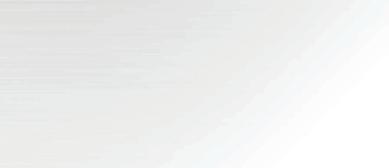
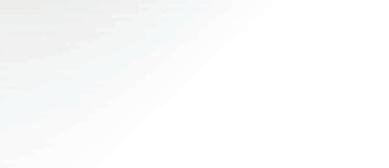
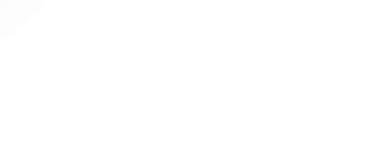
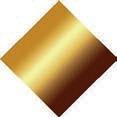


























