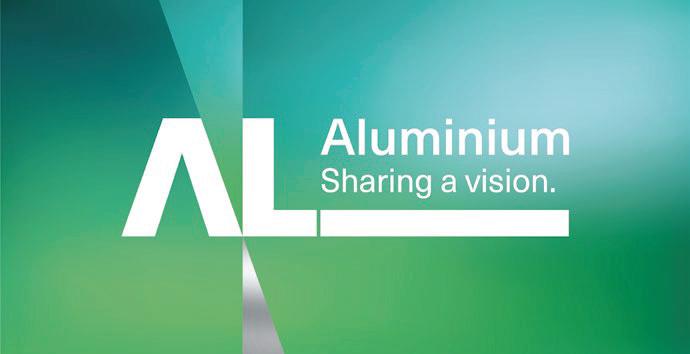
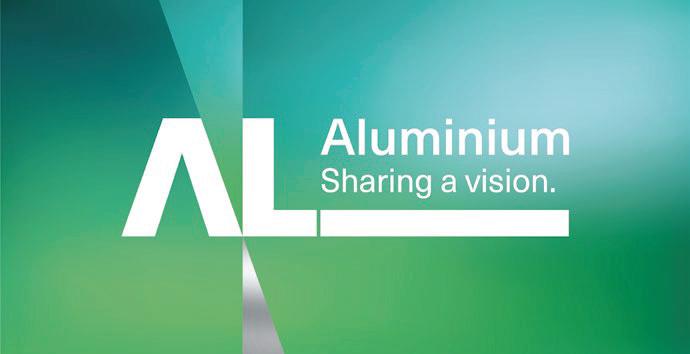
ALUMINIUM 2024 – Bringing the Material to Life Newspaper
The ALUMINIUM show will open its doors as a networking platform soon and promises to once again be a major meeting place for the whole aluminium industry, offering unique opportunities to discover and discuss the latest developments and innovations in the sector. We can’t wait to welcome everyone in the exhibition centre in Düsseldorf again, our event brings together experts from the whole value chain, producers, processors and customers, as well as science and technology, to present their latest research findings and technical developments. When big international players and the most exciting young companies and SMEs meet, when the whole sector, from special experts to aluminium enthusiasts, veterans and newcomers, unites, the material will come to life. And this year again the show offers numerous lectures, panel discussions and workshops that provide deeper insights into the current challenges and opportunities in the industry.
Now, with ALUMINIUM 2024 just around the corner, the anticipation is palpable. This event is set to be a landmark gathering, providing the much-needed exchange as a platform. As the product manager of the show, I am excited to see the industry come together to share a vision of a sustainable, innovative, and prosperous future.
Sharing a Vision
Under the motto “Sharing a Vision”, we set the task of establishing aluminium as a sustainable and future-proof material, making it clear that the material is a must in terms of climate change, resource conservation and transformation. This year’s show aims to be a testament to the material’s potential, bringing together the brightest minds and the most innovative companies to explore new possibilities and set the course for the future. As a networking platform, we bring together industry leaders, researchers, innovators and young talents from around the world, who share the same vision for aluminium and who will share their unique insights and experiences, driving the industry forward, fostering a culture of continuous improvement and innovation. By sharing best practices and solutions, we can collectively work towards a greener future.
Among more than 700 exhibitors there are well-known German pioneers such as TRIMET and the SMS group, but also leading companies from Austria such as AMAG, HAI and IMA Schelling. International industry giants such as Norsk Hydro from Norway, Rio Tinto from Spain, Gränges from Sweden, ElvalHalcor from Greece and Alcoa from the USA will also be represented. Equally wellknown companies in the industry that are regularly represented at ALUMINIUM are Speira and Constellium, but there are also many newcomers this year, such as SIMVIC Recycling and KAPPA Filter Systems.
The presence of companies from emerging markets such as Turkey, represented by exhibitors like Assan Alüminyum, and the United Arab Emirates, with companies like Emirates Global Aluminium, is also impressive. Ma’aden from Saudi Arabia

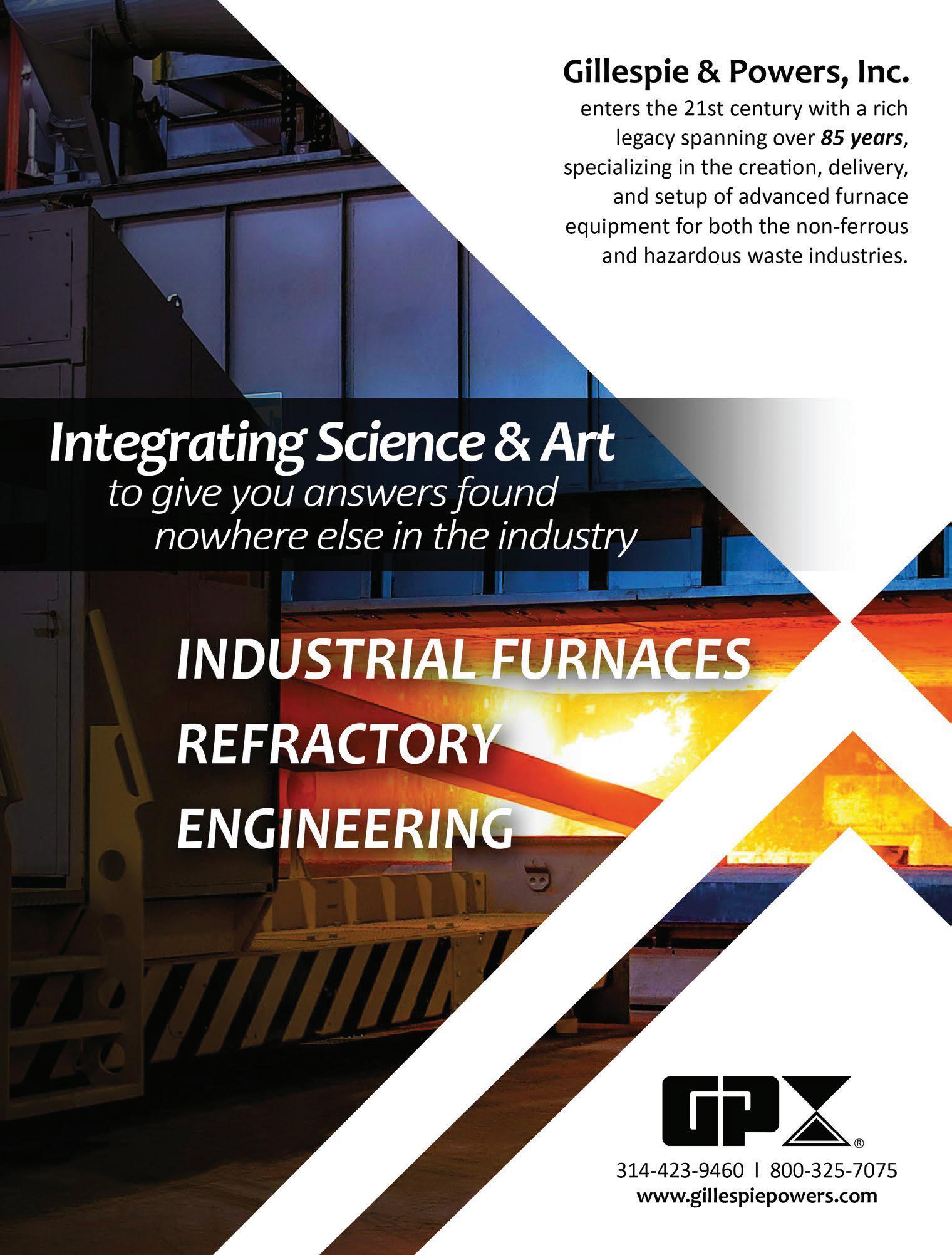
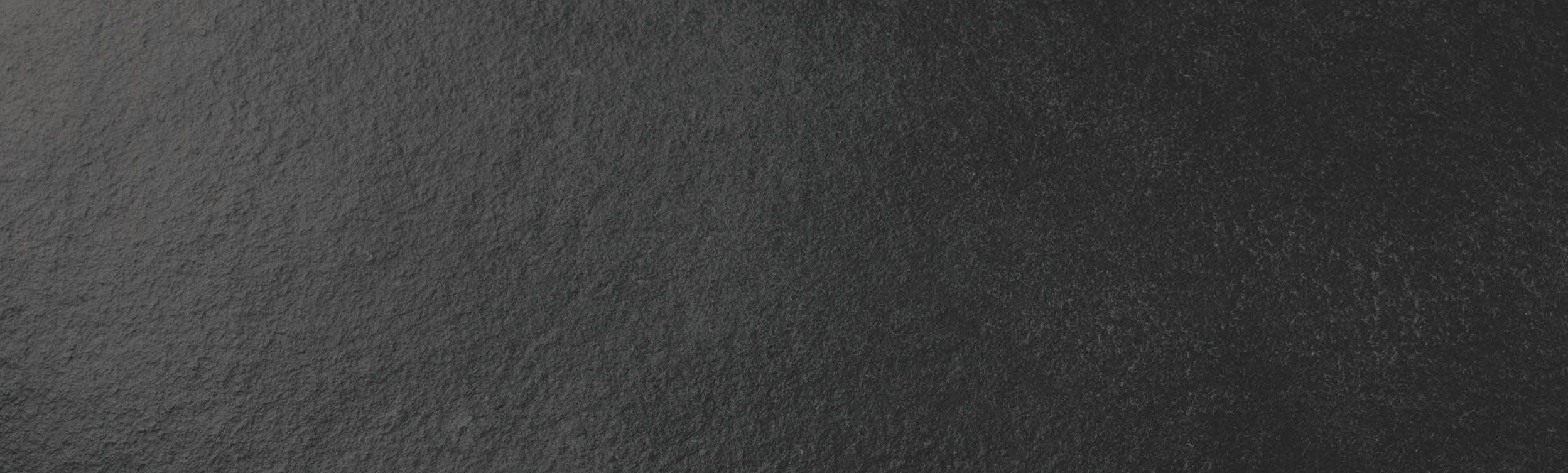
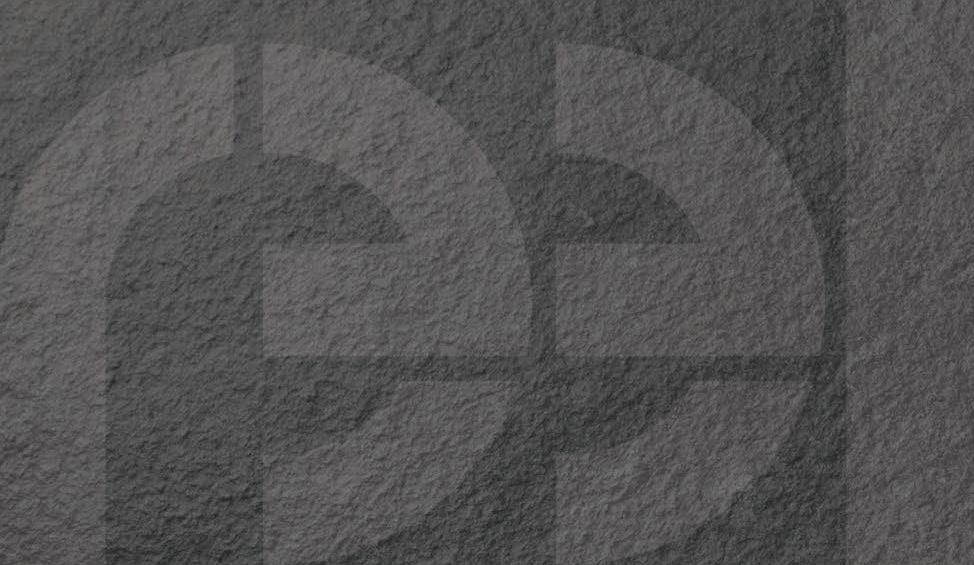
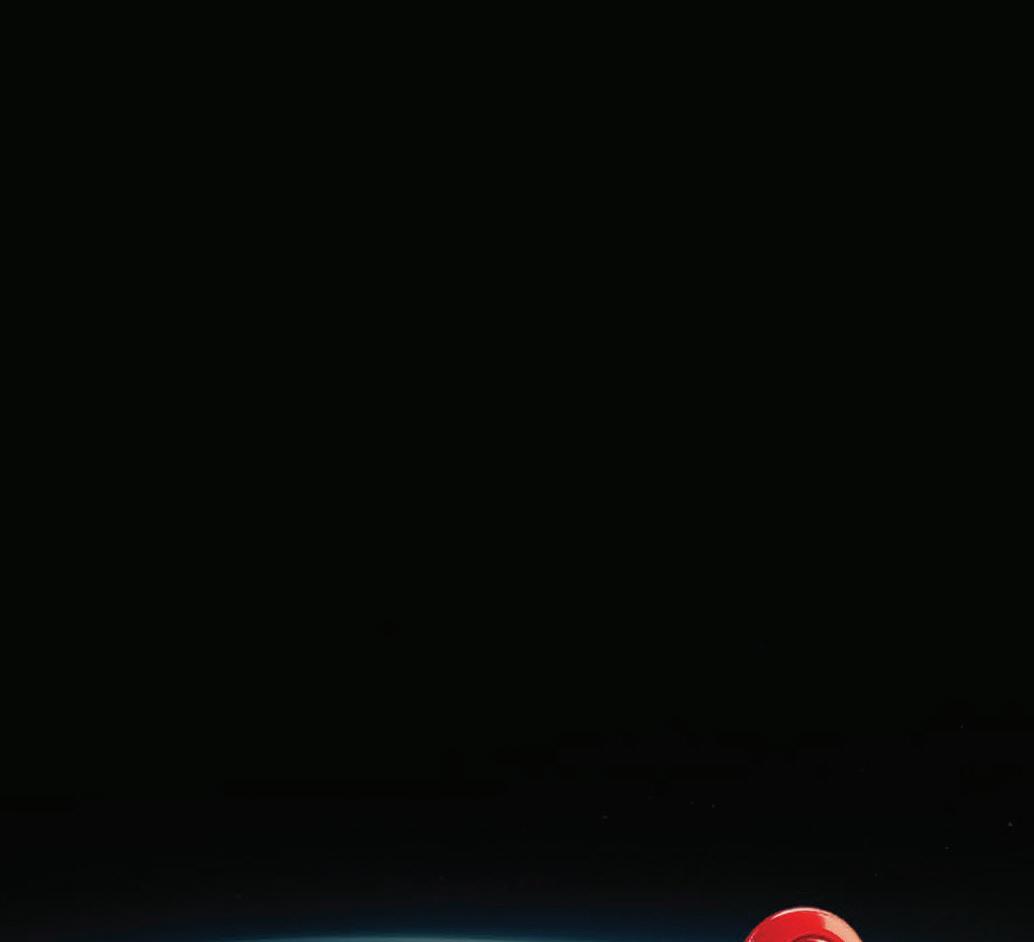




TOGETHER TOWARDS PERFORMANCE
GLOBAL REACH INNOVATION,
EFFICIENCY, SUPPORT.
Experience our global network of Support and Technology Centres.
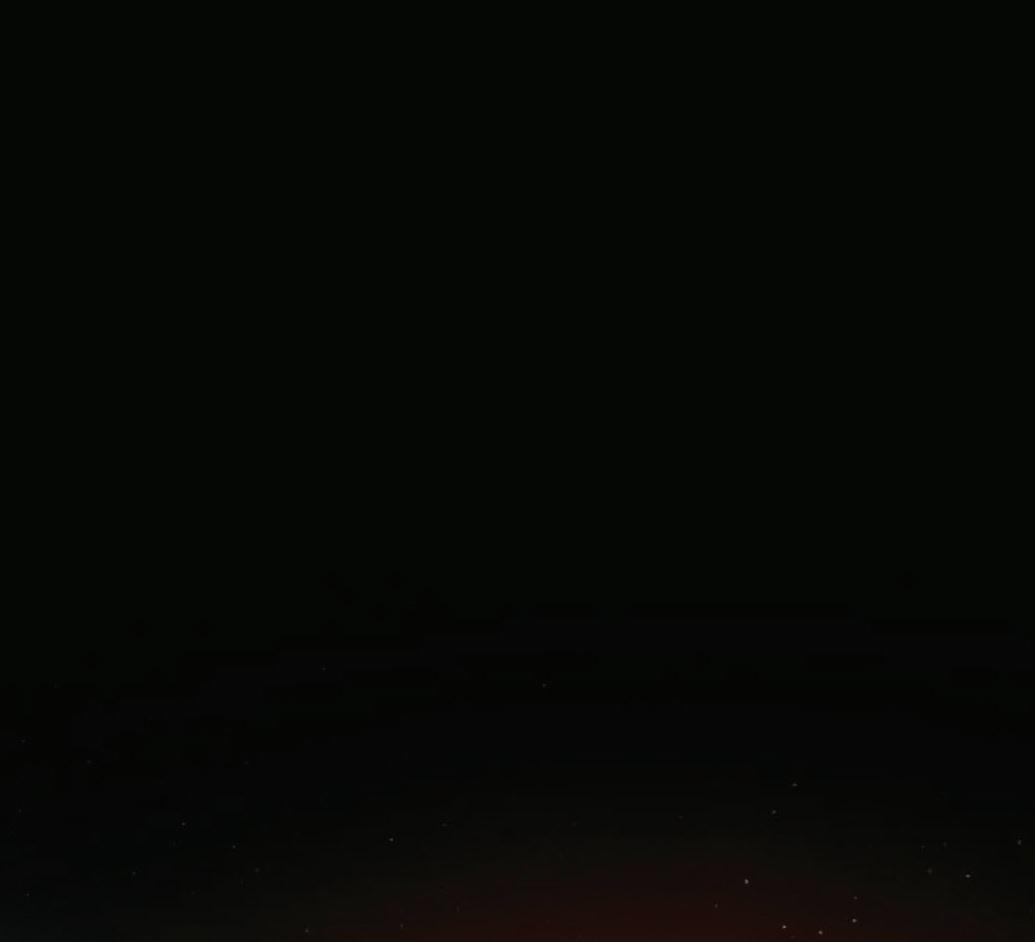
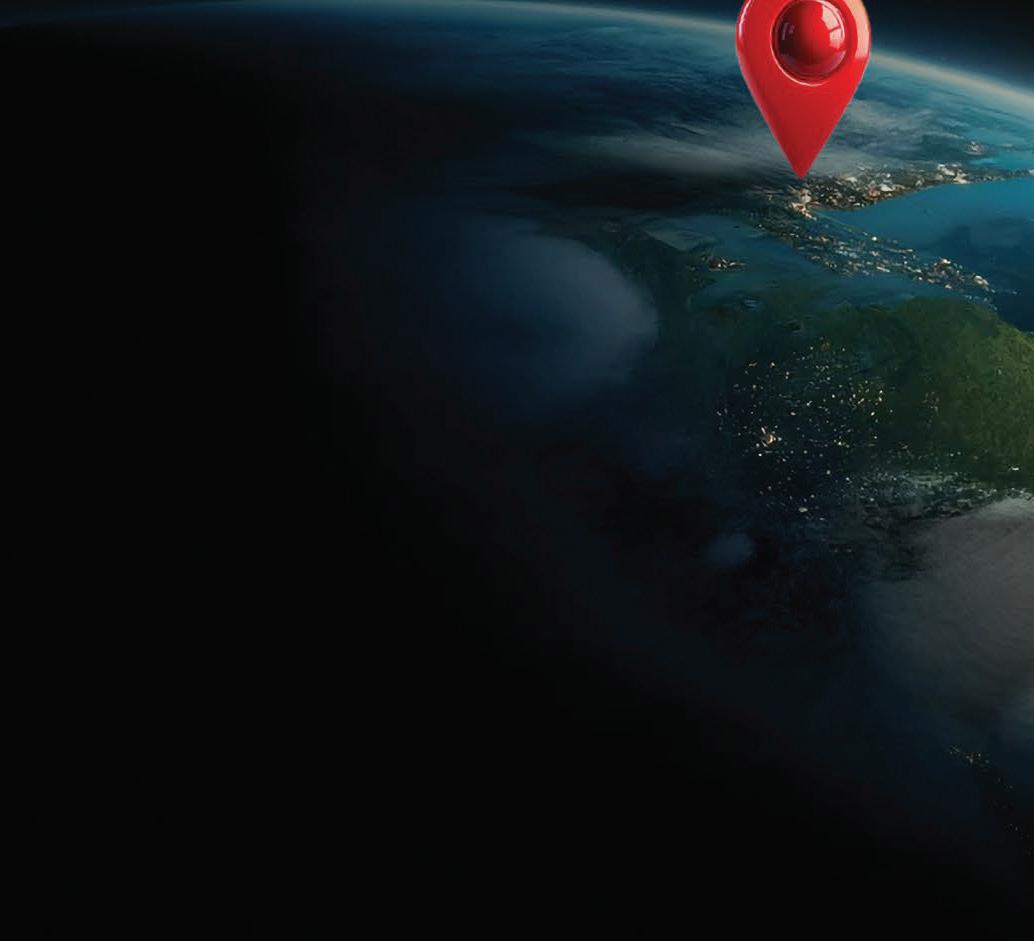
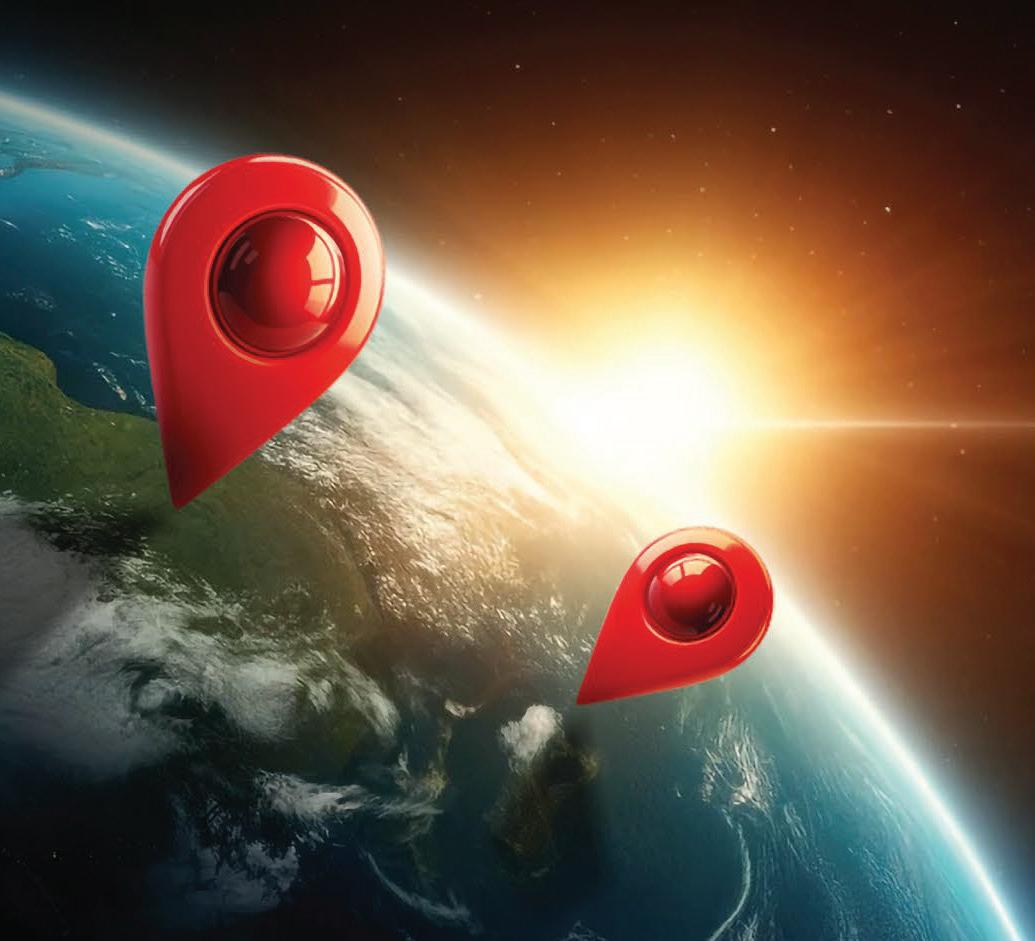

Our Global Support and Technology Centres, are dedicated to the development, support and promotion of efficiency, technology and innovation within the Aluminium industry. Our Technology Centres serve as focal points for research, development and customer service, bringing our support structures closer to our customers worldwide. REEL Aluminium is also committed to green innovation and sustainability which translates into REEL’s commitment to contribute towards a net-zero aluminium industry.
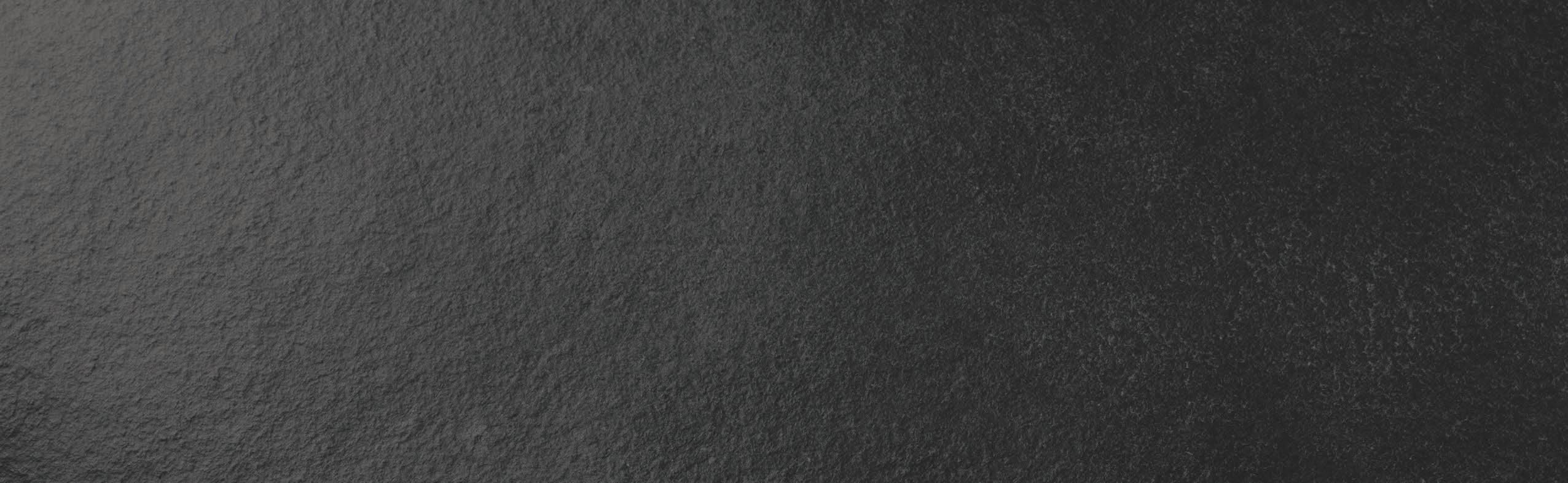
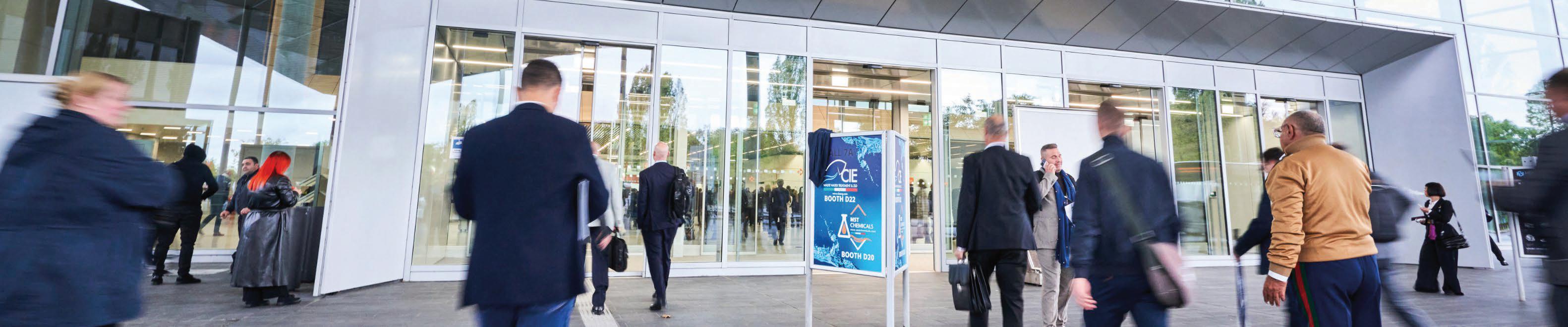
WELCOME TO ALUMINIUM 2024
Dear Exhibitors and Visitors of ALUMINIUM 2024
As you hold this special edition of Aluminium International Today, you are part of an event that many have eagerly anticipated – including us as organisers. Over the next few days, ALUMINIUM will focus on one of the most important materials of our time; a material more promising, more exciting, and more essential for the future than many other. A material, that was also recognized as a strategic raw material by the EU in its Critical Raw Materials Act. A material, that provides numerous opportunities, but also challenges.
Throughout the years, the aluminium industry has fostered a genuine community, unified by a shared passion for aluminium and a collective vision for a better future. This spirit of collaboration and mutual communication is perfectly encapsulated in our motto for ALUMINIUM 2024: “Sharing a Vision.”
As organisers, we are proud to be a part – and to form a platform – of this vibrant community, to shape its future together and build businesses for our clients.
The success of an event like ALUMINIUM 2024 relies on the cooperation and trust of many partners. I would like to extend my heartfelt thanks to all exhibitors, visitors, and partners, including associations, leading scientific institutes, and trade media like Aluminium International Today. Their contributions have been instrumental in the continuous evolution and success of ALUMINIUM.
A special note of gratitude goes to our key partners who have helped us create a content program of unparalleled quality and depth. These include Aluminium Deutschland, whose conference is once again an integral part of the event, European Aluminium, our strong advisor in Brussels, the CRU Group, whose renowned experts shape the program of the Speakers Corner Sustainability & Recycling, and Quartz Business Media, the force behind the very publication you are reading now.
I would like to welcome you to ALUMINIUM 2024 and wish you an exceptional experience and, above all, great success.
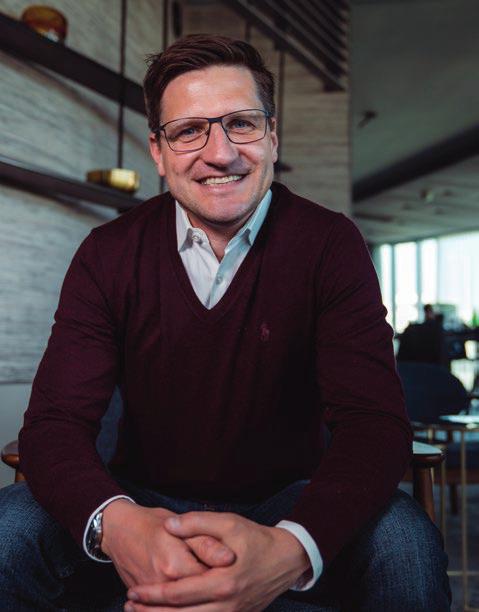
Michael Köhler Managing Director
ALUMINIUM 2024 – Bringing the Material to Life
Women With Metal Awards
IAI Sustainability: Past, Present and Future
European Aluminium: Green ambitions
Alufoil: Half- Century of Innovation
TALSAD: Turkish Aluminium
ALFED: 2024 in Review
Casting vs. Additive Manufacturing
From Today to Tomorrow
What Needs to Change
Engineering, Manufacturing and Commissioning
Driving Innovation and Efficiency in Manufacturing
Cast House Safety and Productivity
The Latest Hot Rolling Emulsion Technology
Meeting the Needs of the Industry
100 Years of Innovation
Industry Leading Mounted Charging Machines
Pioneering Removal of Alkaline Metals
Leading the Sustainable Industry of the Future 1 6 8 10 12 14 16 18
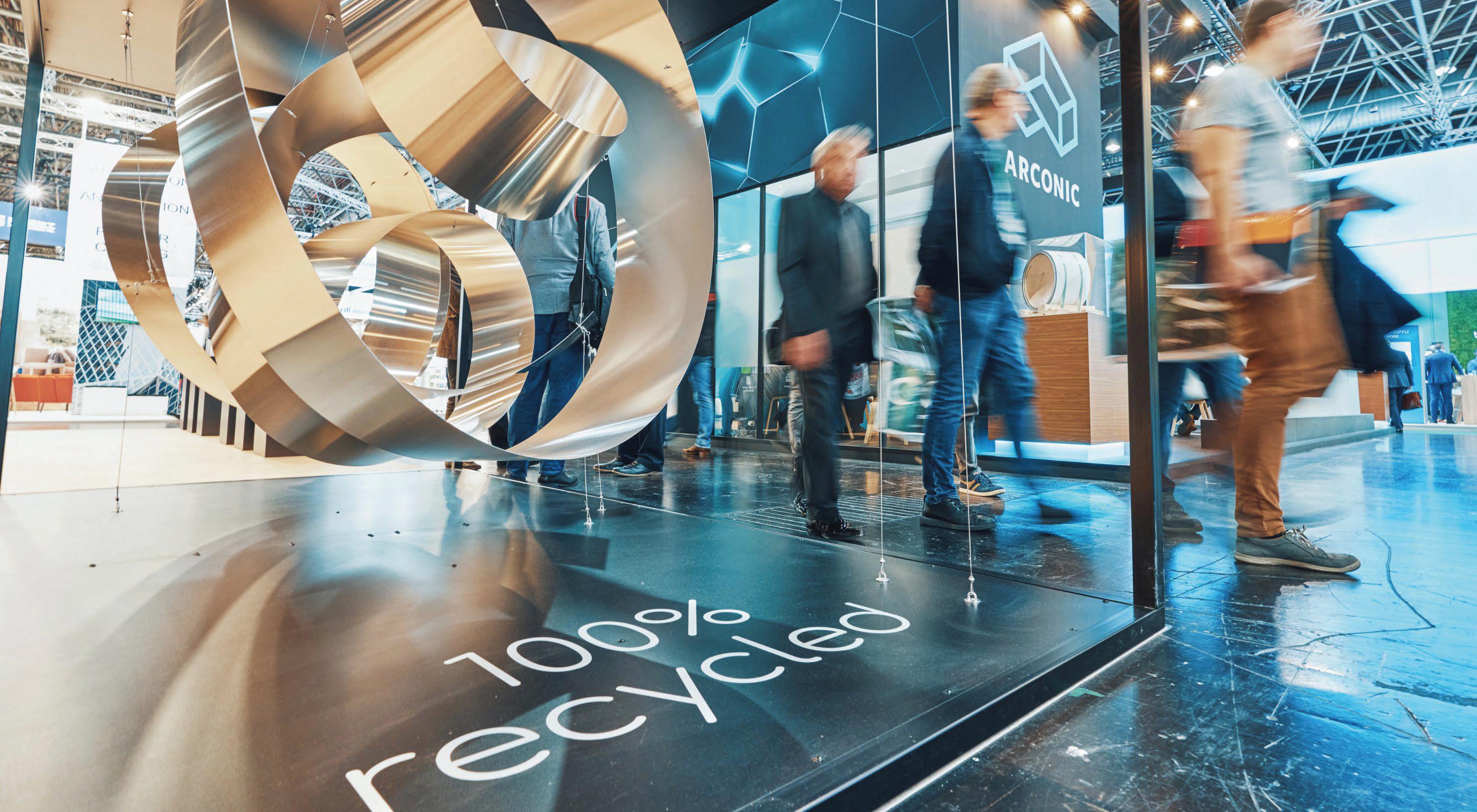
is celebrating a premiere this year, which underlines the increasing internationalisation of the ALUMINIUM world’s leading trade fair.
Transformation of the aluminium industry
The aluminium industry is currently in the midst of an exciting transformation process. Decarbonisation, digitalisation, demographics and the energy transition are key topics that are affecting the industry worldwide. Digitalisation is slowly progressing across all industries, companies are under pressure to move forward and are faced with the challenge of making their processes more efficient, shortening decision-making paths and optimising collaboration with suppliers, for example. In this respect, ALUMINIUM is becoming a showcase for the latest developments and trends that are shaping the future of the industry – from advanced production processes to new applications, the trade fair is the ideal place to find out about the latest innovations.
Particularly in view of demographic developments, digitalisation and automation represent a great opportunity, but also a major challenge for society. ALUMINIUM presents solutions on how companies can organise their complex business processes more efficiently and develop digital business models.
Three days, five halls, a full programme
As a guide for the industry, ALUMINIUM 2024 will not only provide answers to the questions and challenges of our time on the exhibitor side, visitors can also look forward to a comprehensive programme with conference presentations and discussion panels on all three days of the trade fair. The programme as well as the different themed pavilions match the different key topics of the halls.
While Halls 1 and 4 focus on semifinished products, Hall 5 is all about furnace construction, metal working and processing, joining technologies and automation. Hall 3 focusses on surface treatment and rolling technology and is home to the Surface Pavilion including the Surface & Design Lounge.
Hall 6 concentrates on casting and heat treatment, furnace construction, primary production and recycling. In addition to the Primary and Foundry Pavilion, visitors will also find the Foundry Community Café as an
ideal place to network and exchange ideas. At the Innovation Plaza Sustainability & Recycling, experts will come together for the Speakers Corner to discuss challenges and solutions.
The halls, programme, pavilions, special shows and special days form an overall concept that addresses all the challenges facing the industry – the Career Day, for example, will also support the search for skilled workers: On the third day of the trade fair, together with Aluminium Deutschland, we are inviting students and young professionals to have a look behind the scenes of the aluminium industry.
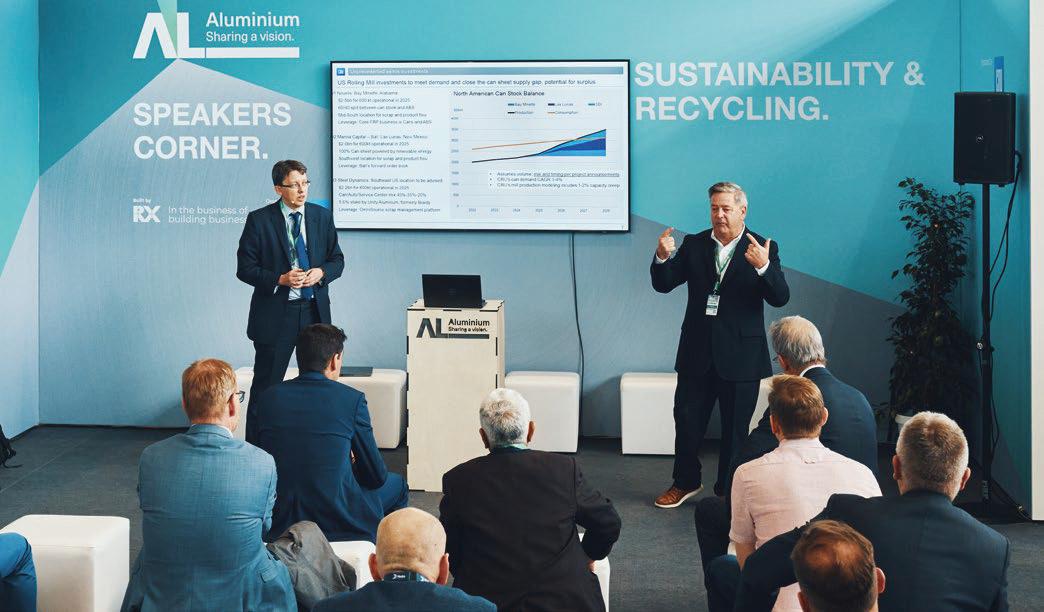

Yasmin Ouiriemmi, Product Manager ALUMINIUM, RX Deutschland GmbH
a commitment to diversity of thought and open dialogue. We welcome dissenting voices, encouraging spirited debates and constructive criticism. By embracing differing viewpoints, we aim to challenge assumptions, stimulate innovation, and chart a collective path forward for the aluminium industry.
Shaping a greener future at the Speakers Corner Sustainability & Recycling
Embracing the diversity of thought at the ALUMINIUM Conference
This year’s ALUMINIUM Conference organised by Aluminium Deutschland will once again provide a stage for top-class experts from industry, science and politics to inform and debate the most exciting developments and trends in the aluminium industry. From leading figures in the aluminium industry, startups and think tanks to executives representing automotive, construction, and packaging sectors, the lineup of speakers ensures a comprehensive exploration of aluminium’s role in affecting the future of multiple industries. They will address the top themes currently resonating within our and our customers’ industries, as well as society at large.
Wolf Ketter, Chaired Professor of Information Systems for a Sustainable Society at the University of Cologne, for example, will talk about how the aluminium industry can harness the power of artificial intelligence to become more commercially, economically, and environmentally sustainable. Isabelle Kraft, Engagement Manager at Ducker Carlisle is focussing on the impact of electrification, large and mega castings to automotive aluminium.
This year’s ALUMINIUM Conference concept is designed to foster insightful discussions and collaborative initiatives that have an impact on the trajectory of the aluminium industry and on diverse further sectors. At the heart of the conference lies
Next to the conference and the various themed pavilions, we’ll once again also have the Innovation Plaza “Sustainability & Recycling” with its own Speakers Corner for expert presentations and discussion panels. The Innovation Plaza is dedicated to the sustainable transformation of the aluminium industry across the entire value chain –matching the topics at the Speakers Corner organised by CRU, where experts and industry leaders will be discussing their latest views on the green transitions for sustainable growth along with developments in the aluminium recycling industry.
The programme comprehensively addresses all facets of sustainability and circular economy, providing a holistic view of the industry’s future. Next to lectures focussing on the latest recycling technologies, sorting and shredding systems or the energy crisis, Christian Koulic, Global Market Executive Metals – OneB2B Solutions, TotalEnergies, for example, will address the challenge of clean firm power, whereas Alexandre Torbay, Co-founder of Keewe and Chief of carbon services will share insights on the new European Union CBAM regulation. In her keynote, Cristina Acedo, Senior Product Developer at Henkel, focuses on Henkel’s commitment to “Respect the Planet, Rethink Design & Processes” by highlighting the company’s efforts to reduce the environmental impact of aluminium metal pretreatment across various industries. In collaboration with customers, they keep innovating designs and processes, focusing on energy and water consumption, raw materials, productivity, quality, and traceability.
“Women can do aluminium, too” Brand new this year: The ‘Women With Metal - the ALUMINIUM Awards’, which we launched in collaboration with Women With Metal, the UK Aluminium Federation (ALFED) and Aluminium International Today. Women continue to be under-represented in many industries, including the metals and therefore aluminium industry, and receive less visibility, support or even recognition. Under the motto ‘Women can do aluminium, too’, the ALUMINIUM Awards are not only intended to honour women in the aluminium industry, but also to encourage other women to become active in the industry and to position themselves with confidence – a goal that our partners and exhibitors are also increasingly pursuing, as the high response to the awards illustrates: With over 60 nominations, our judges will have a tough decision to make. The eight members of the jury also include strong women from the industry, for example Duygu Saymen, Secretary General at TALSAD, or Fiona Solomon, CEO of ASI.
The awards ceremony will take place on the second day of the fair, 9 October, on the ALUMINIUM Conference stage in Hall 3.
Let’s shape the future of aluminium together
After all, both new projects and wellestablished show formats will make ALUMINIUM 2024 a comprehensive experience for all aspects of the material. The trade fair will continue to serve as an important platform for much-needed dialogue and networking within the industry. With a broad spectrum of exhibitors, innovative ideas and exciting discussions, ALUMINIUM 2024 remains an unmissable event for the entire industry and all interested parties.
Join us in Düsseldorf from October 8 to 10, 2024, to be part of this extraordinary event. Whether you are an industry veteran or a newcomer, ALUMINIUM 2024 offers unparalleled opportunities to learn, network, and grow. Let’s shape the future of aluminium together.
SCAN HERE TO FIND OUT MORE

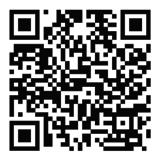

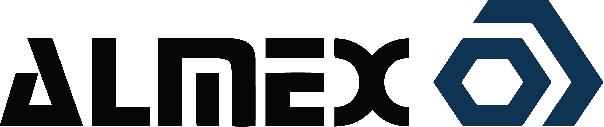
Women With Metal to Highlight Trailblazers
This initiative, spearheaded by Kirsty DaviesChinnock, Managing Director of Professional Polishing Services Ltd, and supported by the Women With Metal organisation, underscores a broader movement towards gender equity and diversity in a traditionally male-dominated field.
A Visionary Initiative for Inclusivity and Representation
The Women With Metal project was conceived during an informal conversation that highlighted the lack of inclusive events specifically tailored for women in the metal industry. What began as a small networking event has blossomed into a vibrant community and a registered company, now hosting regional workshops and the annual conference. The inaugural Women With Metal conference, held in October 2023, was a resounding success, laying the groundwork for what promises to be an even more impactful gathering this year.
Kirsty Davies-Chinnock emphasised the need for visible leadership roles for women, noting, “I want to encourage more women to go into more visible leadership roles, without detracting from the men in those roles.” The upcoming conference will not only celebrate women’s achievements but also provide valuable networking opportunities and skillbuilding workshops aimed at fostering a more inclusive workplace.
Held in Birmingham, UK, the conference will take place on Tuesday 29th October and plans to welcome more than 150 attendees.
The Women With Metal Awards: A Milestone in Recognition
The Women With Metal Awards, set to be a highlight of the ALUMINIUM 2024 Show, will
recognise women who have made significant contributions to the aluminium sector. Dr. Fiona Solomon, an awards judge and the Chief Executive Officer of the Aluminium Stewardship Initiative, commented on the importance of these awards: “Even though the metals industry tends to be male dominated, there are many remarkable applicants to these awards. They are all to be commended on their passion, leadership, tenacity, and contributions to the aluminium sector, across a range of disciplines and seniority.”
Dr. Solomon’s remarks highlight the awards’ role in acknowledging the diverse talents and achievements of women in the industry, inspiring both women and men to support diversity and inclusion initiatives.
Looking Ahead: Expanding Impact and Opportunities
The future of Women With Metal looks bright, with plans to expand the conference into a two-day event and to develop continuous professional development courses. These initiatives aim to equip participants with the skills and knowledge needed to excel in the industry and to foster a culture of collaboration and inclusivity.
Kirsty Davies-Chinnock also highlighted the potential role of technology, including artificial intelligence, in shaping the future of the metal sector. By integrating these advancements into the conference’s agenda, Women With Metal aims to prepare attendees for the evolving landscape of the industry.
The Women With Metal Awards and the broader conference represent a significant step forward in promoting gender diversity and inclusion within the metal sector. As the industry continues to evolve, initiatives like
AWARD CATEGORIES
○ Role Model – the ultimate archetype
She always leads by example, shines with professionalism and expertise, contributes creative and innovative ideas, shows commitment and full support for her colleagues and also stands up for the things that are important to her at work but also outside of work. Her professional career can certainly boast some very special honours, but she is still down-to-earth, honest and authentic. This woman is the best example of what women can achieve in the industry, and she has a radiance that inspires the entire sector – a real role model!
○ Young Leader – the dynamic power women
She is young, dynamic and full of energy: this woman is extremely committed and proves to be a particularly active force in the company. What she does, she does with passion and ambition, full of drive she pursues a vision and has ambitious goals with her team. She likes to pursue or develop unusual ideas and creative approaches, has outstanding communication skills and an inspiring innovative spirit. She is courageous, open and flexible, she is not afraid to break new ground and take risks – and she is full of power!
○ Sustainable & Innovative Leader – the strong pioneer
She is characterised by particularly outstanding achievements and exceptional success: Throughout her career, this strong pioneer has overcome every hurdle and always shone with creative and innovative impact. Sustainability and innovation go
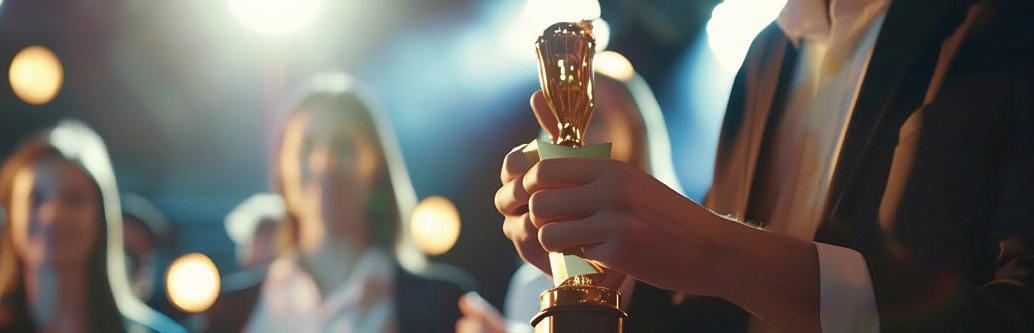
•• www.aluminium-exhibition.com/en-gb/visitors/WomenAward.html#/sessions
these will be crucial in ensuring that all voices are heard and valued.
Awards Programme at ALUMINIUM 2024
The ALUMINIUM Show is not just a platform for the entire aluminium industry, it is a place for the world and a place for everyone: We include, we don’t exclude, which is why we also want to provide more support and visibility for women in the industry and thus created the ‘Women With Metal – ALUMINIUM Awards’ together with our partners,“ proudly announces Yasmin Ouiriemmi, Product Manager of ALUMINIUM at the organiser RX.
Women can do aluminium, too! Women are still underrepresented in the aluminium industry and often receive less visibility, support or even recognition. Under the motto “Women can do aluminium, too”, the awards are meant to help promote equality and diversity in the
aluminium industry, recognise outstanding achievements by women and to strengthen their position in the sector. But they will also recognise the commitment of male colleagues who have been proven as strong allies by providing extraordinary support to their female colleagues.
The Awards will celebrate nominees and winners across categories including: ‘Unsung Shero’, ‘Role Model’, ‘Sustainable & Innovative Leader’, ‘Young Leader’ and ‘Male Ally’, highlighting the diverse aspects of the achievements and commitment of women and their supporters in the aluminium industry.
SCAN HERE TO FIND OUT MORE

hand in hand for this woman, especially when it comes to establishing aluminium as the material of the future and thus driving forward the transformation of the entire industry. Sustainability is a particular concern of hers, which she is actively committed to – she is a courageous metal master!
○ Unsung Shero – the hidden champion
She is a hero of everyday life and a hero of the industry: a woman who has a solution ready for every challenge, who always keeps a cool head in a crisis, who always has a sympathetic ear and is on hand with help and advice, a woman who shows total commitment and motivates the entire team. She is the woman for all cases, she knows everything and knows everyone, she is the one who is always there when questions arise and always knows the right answer – she is the unsung hero of the aluminium industry, a real “alloy angel”!
○ Male Ally – the committed companion
He is always a solid anchor who supports his female colleagues when it’s getting tough. He is the ally who supports, drives, encourages, motivates and celebrates the women in the industry. He is there when he is needed, shows sensitivity and empathy, has already enabled his female colleagues to make further progress, to achieve their goals and he actively promotes change, more equality and the recognition of women in the industry – he’s a true ally!
Metal Awards Trailblazers THE JURY
VOICES FROM THE PARTNERS
“Women With Metal is incredibly proud to be working with RX for The Aluminium Awards in 2024 to celebrate women working within the aluminium sector and encourage more to join us. Aluminium is a sustainable and innovative material and increased diversity in the sector can only enhance this. With thirty-five years working within the metals sector I know what a rewarding career this is and I am delighted to be able to shine a spotlight on some wonderful women and allies who are achieving great things. I am very excited to visit Dusseldorf and create the first Aluminium Edition of Women with Metal for The ALUMINIUM Awards.”
KIRSTY DAVIES-CHINNOCK, CEO and Founder of Women with Metal and Managing Director of Professional Polishing Services
“After following the Women With Metal endeavour from the beginning and seeing the positive impact it is already generating across the aluminium sector, I am very honoured to be supporting this special Aluminium Edition on the judging panel! This exciting opportunity presents a continuation of sharing and development with other women and builds on the important topics and issues for nearly 50% of the metals industry workforce today. It will also highlight the huge achievements being made in our sector, champion growth, amplify voices, and pave the way for a more inclusive and thriving professional landscape. Investing in and showcasing the advancement of women within this sector isn’t just a commitment to diversity; it’s an investment in innovation, excellence, and the future of our industry. I can’t wait to see the nominations and be part of such a game-changing event.”
NADINE BLOXSOME
CEO, Aluminium Federation
KIRSTY DAVIES-CHINNOCK
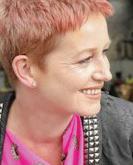
CEO and Founder of Women with Metal and Managing Director of Professional Polishing Services. Kirsty has worked in the metal sector for 35 years and is an expert in surface finishing of aluminium, stainless steel and other non-ferrous metals for sectors including Nuclear, Pharmaceutical and Architectural. An experienced NED she is also a Director and past Chair of the British Stainless Steel Association and CIC ART Business Loans.
In 2023 Kirsty launched the Women in Industry Podcast to shine a light on women working in traditionally male dominated industries no matter what stage of their career. Kirsty is also a frequent media contributor for the BBC, SKY News and for print media both industry based and broadsheet.
NADINE BLOXSOME
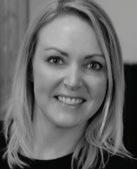
Nadine brings over a decade of industry knowledge to the role of Chief Executive Officer at ALFED, honed through her tenure as Editor at Aluminium International Today magazine and in the past has been responsible for launching market leading events and conferences. Alongside other ALFED colleagues and member companies, Nadine plays a pivotal role in advancing the interests of the UK aluminium industry and driving initiatives that promote economic prosperity, environmental stewardship, and technological innovation. Presented with a unique opportunity to lead and shape the future of a critical sector within the UK economy, Nadine is responsible for influencing policies and fostering collaboration to ensure long-term sustainability and success.
YASMIN OUIRIEMMI
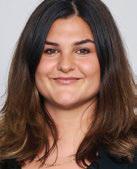
Yasmin Ouiriemmi has been responsible for the project management of ALUMINIUM World Trade Fair organised by RX Deutschland GmbH, since 2022. After the graduation in Business Administration she gathered first experiences in organising congresses at the Center for Wind Power Drives at RWTH Aachen University and in agencies for analogue, digital and hybrid events. As Event Manager, Yasmin had already been in charge of various events in the materials trade fair
This year’s ALUMINIUM Show will be marked by a groundbreaking event: the Women With Metal Awards, designed to celebrate the significant contributions of women in the metal industry.
portfolio of RX since 2019 until she took over the co-design of the supporting programme and the coordination of partnerships for ALUMINIUM in 2020, with the promotion to Product Manager following.
DUYGU SAYMEN
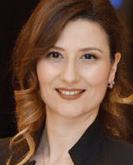
Duygu Saymen was appointed Secretary General of The Turkish Aluminium Industrialist Association having previously held the role of Deputy Secretary General. As the leading representative of the Turkish Aluminium Industry, TALSAD works for sustainable growth and development of the aluminium industry in local and regional markets, development and implementation of new and advanced technologies, implementation of good practices in health, safety and environment and works to develop strong local and international partnerships.
DR FIONA SOLOMON
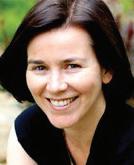
Fiona is the CEO of the Aluminium Stewardship Initiative (ASI), which she joined in March 2015 with the responsibility for leading the development and implementation of ASI. In 2023, ASI has more than 320 members and has issued more than 300 Certifications for performance and chain of custody in the aluminium value chain.
Her career has specialised in building new and innovative initiatives in mineral supply chains over 25 years. She was previously Director – Standards Development at the Responsible Jewellery Council from 2007 to 2015, where she developed a certification program for gold, diamonds and platinum group metals which was adopted by more than 1000 companies across the supply chain from mine to retail. She has served as a Board Member of the ISEAL Alliance and a founding member of the OECD’s Multi-Stakeholder Steering Group for responsible mineral supply chains. From 1997, Fiona worked for 10 years at Australia’s CSIRO, leading research into mining and sustainability, and was also seconded to WWF to manage a multi-stakeholder project on the feasibility of mine-site certification.
She has a Bachelor’s degree (Hons 1) in mechanical engineering and a PhD in philosophy of technology, both from the University of Queensland, and is a Graduate of the Australian Institute of Company Directors.
MARIUS BAADER
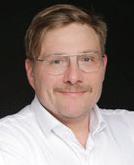
Marius Baader is the Managing Director of Aluminium Deutschland. As a representative of the aluminium industry, AD strives to engage in an open dialogue with the public in order to increase transparency and understanding of the material aluminium and its members’ products among customers and consumers. To this end, there is a constant exchange of experiences and ideas within the association; it is the prerequisite for effective representation of the interests of all member companies, including externally.
PAUL VOSS
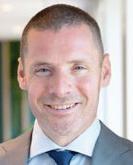
Paul Voss is Director General at European Aluminium, the industry voice of the aluminium value chain in Europe. Paul is a long-term public affairs and governmental relations expert with 20 years of experience in the Brussels and energy sector. Prior to joining the aluminium industry, Paul Voss served as Managing Director at Euroheat & Power, the association for the European district energy sector, and as Head of Public and Industrial Affairs at energy solutions provider Danfoss District Energy.
A British-Belgian national, Paul is married with three children and holds degrees in Political Science and European Public Administration from Universities in Canada, France and Belgium.
ZAHRA AWAN
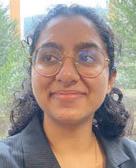
Zahra Awan is the current Assistant Editor of Aluminium International Today. Before starting her role, she completed a degree in English. She started the role in 2021 and has relied on the openness of the metals industry to teach her all there is to know. Learning, with the help of key industry players, researchers, universities, and the shop floor, and moving away from classical texts to economic and industry data, she has discovered satisfaction in numbers and the achievements of innovative discoveries. She is most appreciative of the work that the industry does to decarbonise, and attributes its hard work to the reason for her own personal awareness of the importance of sustainability in her everyday life.
Sustainability: past,
By Pernelle Nunez, International Aluminium Institute
In 1972, when the International Aluminium Institute was founded, sustainability was in its infancy. Aluminium producers were aware of the importance of managing key operational challenges such bauxite residue, process emissions and worker health and safety but progress on these issues was mostly limited to individual company efforts and collaboration at a global level was not a priority.
Significant changes have occurred over the last 50 years, demand for aluminium is almost ten times greater, aluminium production hubs have shifted location, the global industry has successfully collaborated on a host of issues, and the scope of the IAI’s activities have also significantly broadened. When the IAI was initially founded, one of the key priorities was for it to provide reliable and robust industry statistics and though that has remained a high priority, sustainability is now a major area for collaboration across the IAI’s member companies and the broader stakeholder groups with which it engages.
What gets measured gets managed
In the aluminium industry, data has often been seen to be critical to improving performance. The IAI’s work is underpinned by data, much of it originating from members directly, providing a reflection of the recent past, and summarised in key metrics such as production, energy consumption, power mix and emissions. These metrics, collected over time, offer insight into the industry’s evolution, historic baselines and emergent trends, providing much needed context to drive action and investment to improve overall performance across the sector.
An example of this is the industry’s work on climate change. Since the 1990s, climate change has been one of the most important issues for the aluminium industry. Historically, long-lived and potent greenhouse gases (GHGs) known as Perfluorocarbons (PFCs), were significant contributors to the industry’s emissions profile accounting for approximately 30-40% of the sector’s CO2e emissions in 1990. The IAI, having started to collect PFC emissions data [1] in 1990 alongside the commencement of an active work program in collaboration with member companies to better measure, report and manage these emissions, has seen significant reductions in average industry PFC emissions per tonne of aluminium from 5 tCO2e in 1990 to 0.75 tCO2e in 2021. These reductions were driven by a mix of investment in newer smelting technology, improved measurement practices and more sophisticated monitoring and process control systems across the industry.
The IAI has always had data at the heart of its work and the aluminium industry’s application of leading analysis methods including life cycle impact assessments [2] of materials and production, and material flow analysis[3] of aluminium stocks and flows, has laid the foundation for much subsequent work. In 2021, building on the IAI’s decades of data and analysis, a landmark report on Aluminium Industry GHG Pathways to 2050 [4] was launched. The report set out the current baseline of GHG emissions for the sector (approximately 1.1 billion tonnes of CO2e in 2018), outlined in detail the emissions
trajectories for the global aluminium industry under different climate-aligned scenarios, and proposed potential technological pathways to reach those end points; electricity decarbonisaton, direct emissions reduction and increased recycling and material efficiency.
The report has since acted as the foundation for many multistakeholder climate discussions, decarbonisation initiatives and reporting frameworks, indicating the continued importance that such data and analysis can have in creating an enabling environment for action. The stark findings that despite growing demand for aluminium, sector emissions need to be reduced from 1.1 billion tonnes in 2018 to just over 50 million tonnes by 2050 under a 1.5 degrees pathway, have provided the backdrop to many collaborative efforts. The analysis has also provided aluminium companies with a key reference to better understand their own contributions to sector emissions and support the development of specific corporate targets, pathways and emissions management plans.
Pushing for progress
There remain many unknowns around exactly how the industry will decarbonise including technology development, rollout and retrofit and financing. Despite this, the industry continues to push ahead with decisive climate action. The IAI has tracked the number of decarbonisation projects announced [5] in recent years aligned with its three pathways, and it has grown from a dozen projects in 2020 to over 50 in 2023. The diversity of activity across all major producing regions demonstrates that there is no single solution to decarbonising the aluminium industry and that efforts are needed on all fronts.
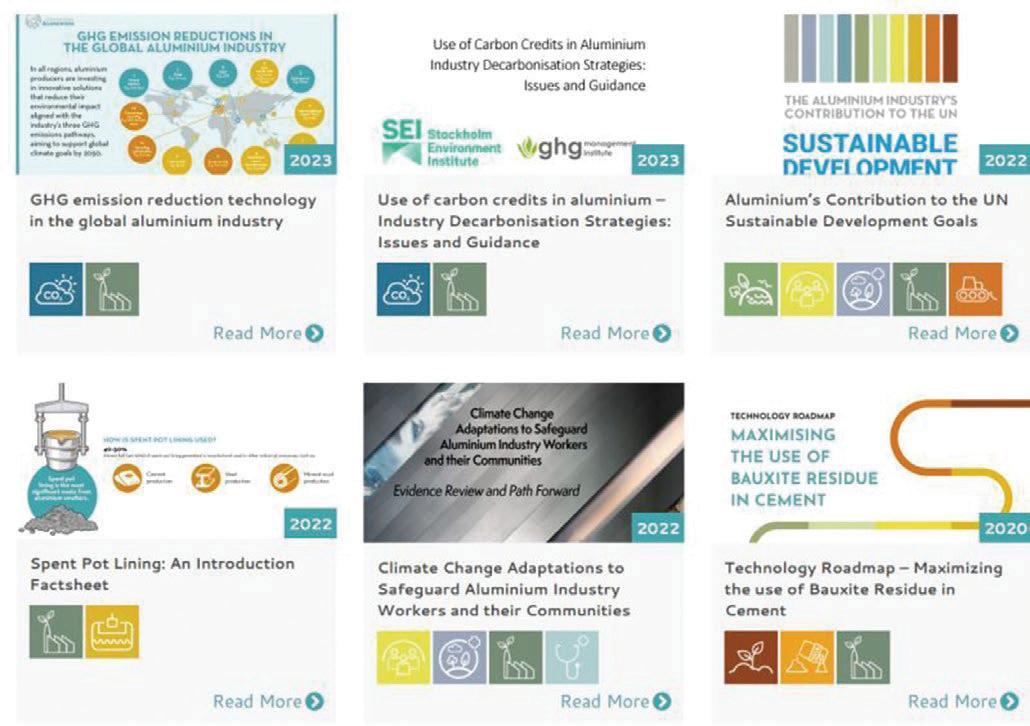
medium and long term and is supported by major aluminium producers accounting for over 250 million tonnes of CO2e emissions.
The collation and consolidation of key climate metrics for stakeholders including annual tracking of sector progress, fosters a new level of accountability. The credibility of the sector’s climate efforts hinge on continued reductions in absolute GHG emissions over the coming years – something it has just begun to demonstrate based on emissions data for 2022 [7] released earlier.
In addition to the outlined efforts on GHG disclosure, there is a broadening of

The industry also recognises that despite recent ramping up of activity, there is still much more to do keep global climate goals in reach. To better understand how much more, tracking progress will be essential. At COP28, the Aluminium Industry GHG Initiative was launched [6] to continue to bring much needed transparency and consistency to GHG disclosures. The initiative commits to tracking GHG ambitions, plans and progress over the
industry discussions to incorporate climate resilience & adaptation. Recent work has focused on climate change adaptations to safeguard aluminium industry workers and communities [8], highlighting the human health impacts of climate change will be most severe in many of the same regions where the industry is most active. The work explores adaptation measures for the private and public sectors to reduce human
health impacts on workers, communities, and businesses. During 2024, the work has continued with an expanded scope to consider physical and financial risks and approaches to resilience and adaptation planning across sector at present.
The broadening of the climate discussion highlights the importance of looking beyond mitigation for a comprehensive approach to climate change. It also serves as a reminder of the interlinked nature of many complex sustainability issues. Climate change (and actions to mitigate it) can have a material influence on nature, biodiversity, water and people. The industry is clear that whilst decarbonisation is essential, it should not lose focus on other issues and decarbonisation should not happen at any cost – a holistic approach is needed where solutions consider the impact on other sustainability issues and potential unintended consequences.
An increasingly competitive landscape
Industry associations must be cautious with competitive or commercial issues, but sustainability performance has become an increasingly competitive and commercial space over recent years. Carbon footprint metrics in particular are being used as key differentiators between producers and by consumers and specifiers in their decisionmaking about materials. Requests for information and data are becoming more detailed and complex and in many cases the dialogue is also no longer restricted to just carbon. Mirroring the industry’s commitment to a holistic sustainability approach, there is also a broader conversation around sustainability performance emerging with many downstream users and consumers interested in other environmental issues such as nature, water and waste management alongside social issues such as human rights, community impacts and modern slavery. Industry initiatives such as The Aluminium Stewardship Initiative [9] and the IAI’s Aluminium Forward 2030 Initiative [10] offer
present and future
fora for the value chain to engage in a variety of ways on these complex issues, identify good practice and drive positive impact. They bridge gaps between producer and consumer and offer aluminium a strong position to deliver on the needs and wants of customers whether it be through certification, data or dialogue.
Through the IAI’s Aluminium Forward 2030 Initiative, the industry has directly engaged with its customers - from automotive makers choosing between steel and aluminium to windows producers looking for sustainably produced materials and packaging producers interested in driving fully circular models towards 100% recycling rates. It is a model that has demonstrated value to both upstream and downstream aluminium actors, and with cooperation across the value chain needed to deliver on growing consumer sustainability expectations, it is one that is likely to keep evolving.

and more sustainable products. It is now time though to redirect the industry’s competitive energies and to look outwards, to capitalise on the strong position aluminium has over competing materials such as PET, glass [13], steel and cement, and to ensure aluminium’s sustainability credentials for end-use applications are showcased to key decisionmakers.
Looking Outward
Aluminium has properties that make it an ideal material for use across a variety of end-use sectors and as the global population grows, aluminium will continue to have a vital role to play in transport, aviation, packaging, infrastructure, and energy. It’s also becoming increasingly appealing for sustainability-focused consumers with its ability to be infinitely recycled enhancing options for circular models, its durability prolonging product lifetimes and lightweight nature reducing fuel consumption or extending driving ranges. Demonstrating these qualities with credible data and studies alongside comprehensive reporting on sustainable production should now be a focus. This would continue to strengthen aluminium’s position as a material of choice in the future and provide potential opportunities for material substitution and even stronger demand growth.
and perhaps more importantly, encourage closer collaboration beyond the industry. The step changes necessary to meet community, customer and other stakeholder expectations will require action from many outside of the aluminium industry and so it is important to continue to look outward, respond to external pressures and ensure that the information needed to support aluminium’s position as a material of the future is clear, credible and coherent.
A people-centric future
Sustainability has a strong forward-looking element to it and as the industry continues to map out what it could look like in the coming decades, it is important to not only think of aluminium as a material for the future but to ensure the aluminium industry itself is in a strong position for the future. To do this, the industry will have to embrace new technologies, adapt and innovate but it should also keep in mind the central role that people play in defining its future. In 1987, 15 years
after the establishment of the IAI, the United Nations Brundtland Commission defined sustainability as “meeting the needs of the present without compromising the ability of future generations to meet their own needs”, placing people very much at the centre of sustainable development discussions.
The IAI has continued to expand its work program to reflect the important role that people play in influencing our approach to sustainability with the establishment of a new Social Working Group exploring diversity, equity and inclusion, expansion of the climate change workstream to consider impacts on communities and workers, and through the closer collaboration with external stakeholders who are key partners to accelerating the industry’s sustainability journey. Producing sustainable aluminium and having a sustainable aluminium industry is about recognising that sustainability is about much more than just having the lowest emissions, it is about a secure future, meeting society’s needs and delivering for people.
Despite the IAI’s caution around competitive issues, some of the recent competition within the aluminium industry around carbon footprint and sustainability has in many ways been a positive. It has been instrumental in driving corporate ambition, pushing for the establishment of clear industry calculation methodologies[11], guidance and tools [12], and creating a competitive landscape where producers strive for better performance, lower emissions
The industry must also engage with other stakeholders such as policymakers and the financial community as the policy and investment landscape continues to rapidly. Environmental, Social and Governance (ESG) disclosure and reporting will continue to play an important role in communicating to external parties about the performance and sustainability efforts happening across the sector. Green procurement and demand stimulation policies and sustainable financing and offtake frameworks have the potential to shape the future of the sector, incentivising and supporting positive change. The sector should take notice of these opportunities and be active participants.
The IAI has played a key role in bringing together representatives of the industry to collaborate and push for continued improvements in the production, use and recycling of aluminium. Over the coming years, it will continue to progress key sustainability issues both within the industry

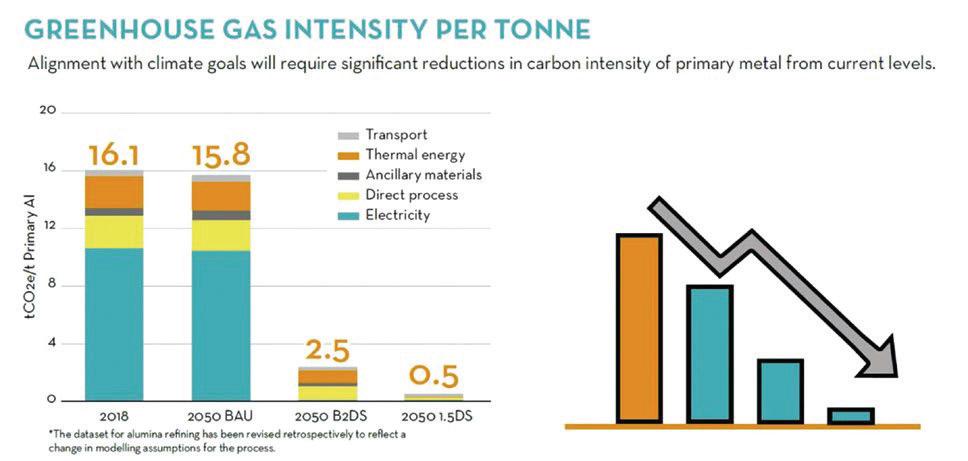
REFERENCES:
[1] https://international-aluminium.org/statistics/ perfluorocarbon-pfc-emissions/ [2] https://international-aluminium.org/ resource/2019-life-cycle-inventory-lci-data-andenvironmental-metrics/ [3] https://alucycle.international-aluminium.org/ [4] https://international-aluminium.org/resource/ aluminium-sector-greenhouse-gas-pathwaysto-2050-2021/
[5] https://international-aluminium.org/ innovations-in-the-aluminium-industry/ [6] https://international-aluminium.org/ aluminium-industry-backs-new-greenhousegas-initiative/
[7] https://international-aluminium.org/ resource/greenhouse-gas-emissions-decline-inaluminium-industry/ [8] https://international-aluminium.org/resource/ health-risks-and-adaptation-in-a-changingclimate/
[9] https://aluminium-stewardship.org/ [10] https://international-aluminium.org/aluminiumforward-2030/ [11] https://international-aluminium.org/resource/ aluminium-carbon-footprint-methodology/ [12] https://international-aluminium.org/resource/ iai-scope3-calcuation-tool-and-guidance/ [13] https://international-aluminium.org/wpcontent/uploads/2022/02/Aluminium-vs-glass-andplastic-FINAL-Information-Sheet-1.pdf
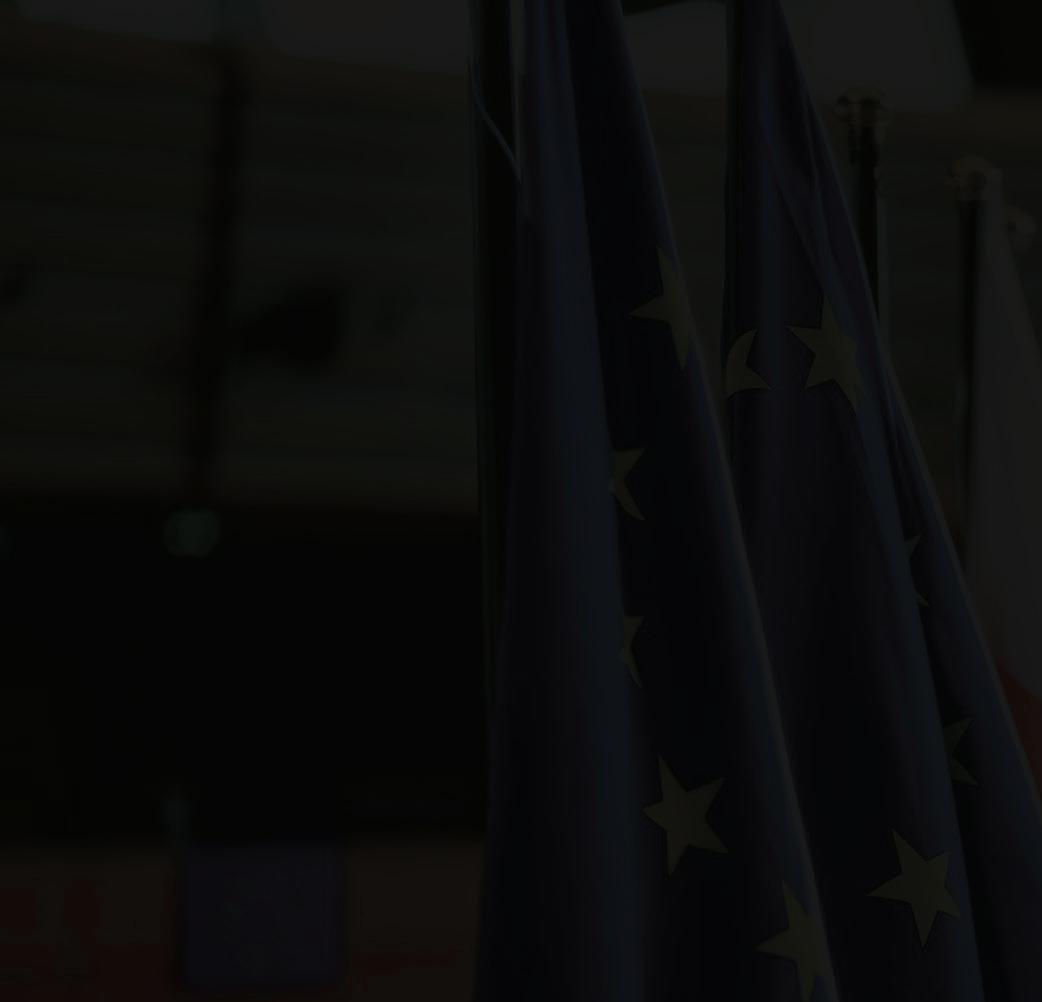
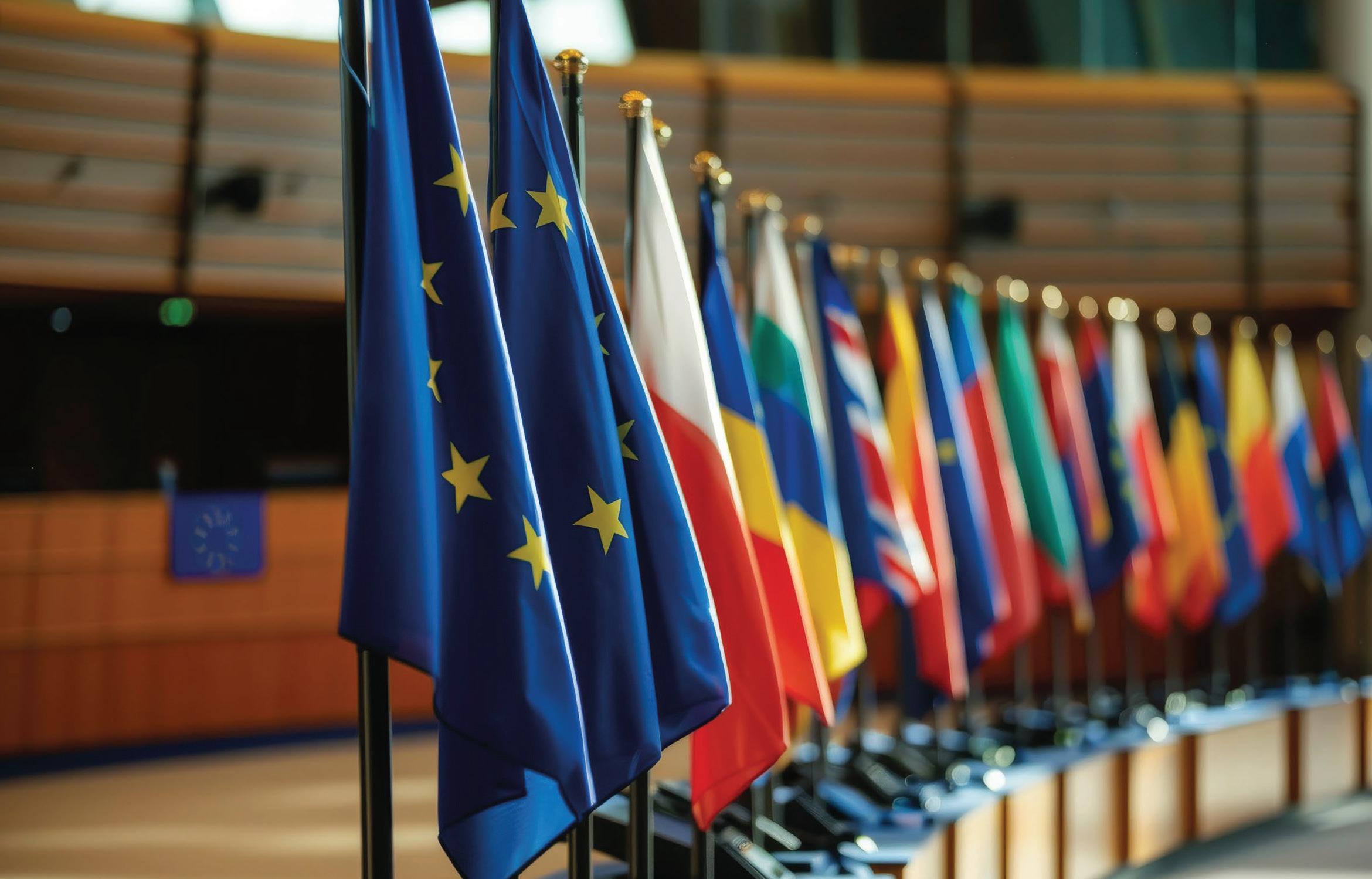
Green Ambitions
Meet Industrial Needs: Our Call to EU Policy Makers
By Paul Voss, Director General, European Aluminium
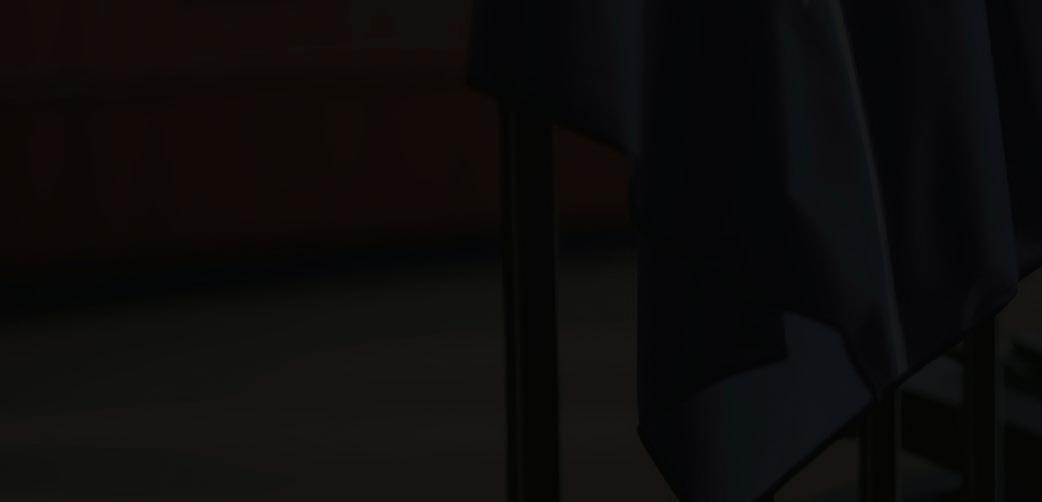
As the EU kicks off a new legislative cycle (2024 to 2029), the mood in Brussels is shifting, and industry is taking centre stage. The Antwerp Declaration [1], which began in February, has been a real game-changer. It’s brought together a diverse group of voices—trade unions, NGOs, think tanks, policymakers, and industry leaders—to chart a new course for our industrial future. From the discussions with over 25 sectors, one thing is clear: we can’t choose between staying competitive and decarbonising— they must go hand in hand.
As Ursula von der Leyen kicks off her second term as President of the European Commission, her guidelines for 20242029 emphasise this dual imperative. Streamlining regulations, ensuring green energy access, and supporting industrial decarbonisation are now top priorities. We’re also looking forward to the proposal for a New European Competitiveness Deal, which is expected by the end of the year. While this is a step forward, this political momentum must be translated into tangible, impactful measures if it’s going to mean anything.
To get started, Europe needs a clear and ambitious industrial strategy that ensures we have reliable access to the resources we need, boosts the development of new capacity, and brings back what we’ve lost over the past few years. With the increase in clean technologies, the demand for materials like aluminium is set to rise by 30% by 2040. But if Europe doesn’t make it attractive to produce these technologies and raw materials here, we’ll end up importing more and missing out on economic opportunities. It’s high time we take inspiration from the US Inflation Reduction Act (IRA) and push for a comprehensive action plan that elevates competitiveness as a strategic priority. Europe must provide the clarity, predictability, and confidence needed to make the business case stronger. We hope the upcoming Competitiveness Deal will do just that.
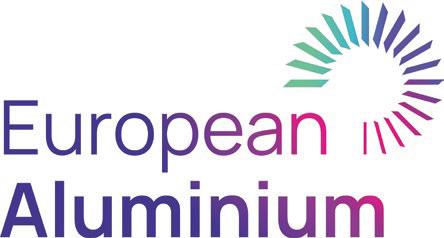
We also need to focus on improving circularity and recycling. Connecting the dots between raw materials, clean technologies, and European-made products will build on the momentum of the EU’s Green Deal Industrial Plan. This includes key initiatives like the Critical Raw Materials and Net-Zero Industry Acts.
Reaching net zero by 2050 is a must, but for the aluminium industry—where much of the emissions come from energy use—this goal relies heavily on cleaning up our energy system. We need to make clean energy both affordable and accessible. This means speeding up the adoption of Power Purchase Agreements (PPAs), boosting public support for these agreements, and increasing the share of renewables in our grid. Revising State Aid Guidelines to support clean electricity and gases is also crucial to keeping energy costs competitive.
In parallel, protection for European manufacturers against the real threat of carbon leakage must be maintained and even strengthened. The EU’s Carbon Border Adjustment Mechanism (CBAM), ostensibly designed to prevent carbon leakage by taxing imports based on their carbon footprint, could ironically end up doing the precise opposite if we don’t get the details right. For aluminium, CBAM should only include direct emissions and keep the current CO2 cost compensation system intact in order not to further undermine the competitiveness of our producers.
Additionally, the Emissions Trading System (ETS) needs to be reformed to better support aluminium production and recycling. Setting clear benchmarks that reflect and reward our efforts to cut CO 2
emissions will help align our environmental and economic goals.
Fair competition is crucial. The EU must take a stronger stand against imports from non-market economies that use unfair trade practices. Effective trade defence and preventing the circumvention of trade measures are essential. We should also work on a strong EU-US Global Arrangement on Sustainable Aluminium, based on fair production costs, to address global emissions and market distortions. Building alliances with like-minded countries to form a “climate club” dedicated to sustainable practices will further strengthen our position.
Lastly, updating REACH—the EU regulation on chemicals—is key to balancing effective regulation with with the need to maintain competitiveness, a principle which should underpin all policy development in the coming years.. We need better monitoring of imports to ensure they meet Europe’s high safety and environmental standards, creating a fair and competitive market environment.
The next five years will define Europe’s industrial destiny. Will we champion innovation and clean manufacturing, or sleepwalk towards industrial decline, outsourcing everything for quick economic gains? Now is the time for everyone to step up—policymakers, industry leaders, and stakeholders need to come together like never before. I’m incredibly proud of our team in Brussels—a group of immensely dedicated and skilled professionals who tirelessly champion the industry’s interests with passion and expertise. However, real progress will only come from united action. Let’s engage with policy makers and push for the changes we need. The future of our industry and Europe’s industrial fabric depends on it.
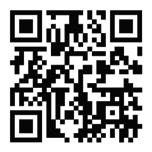
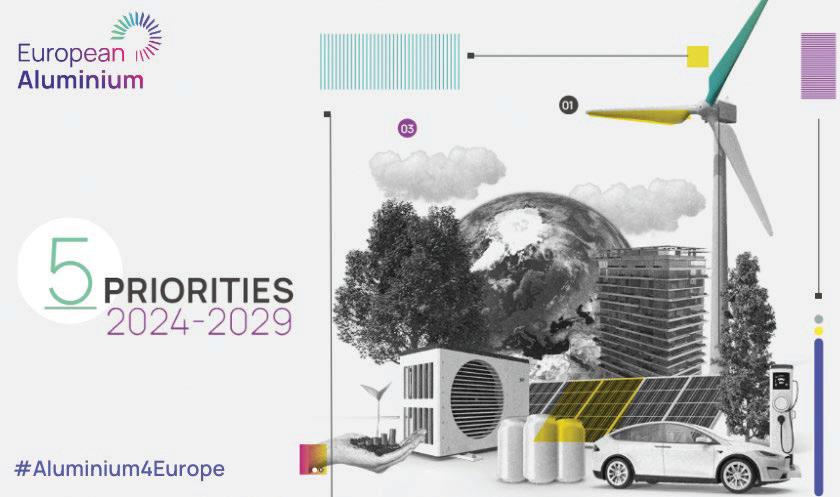
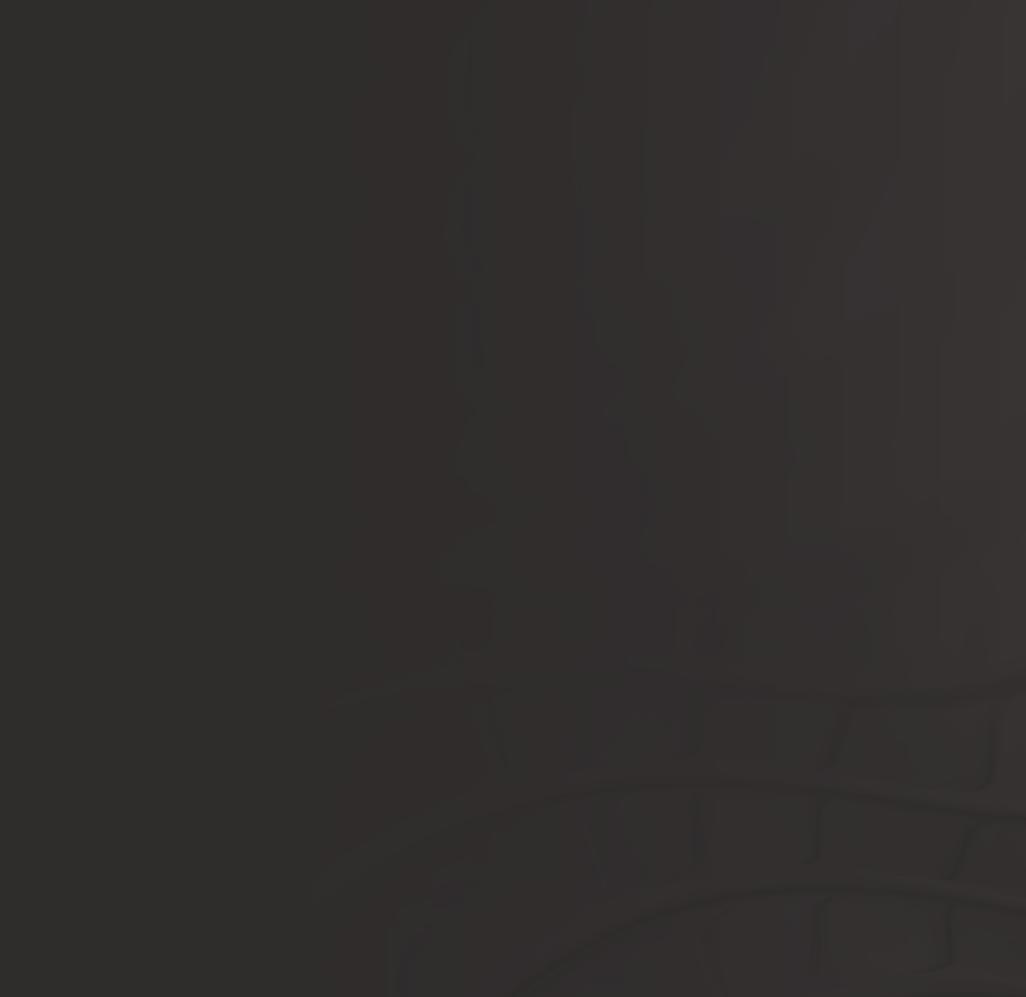
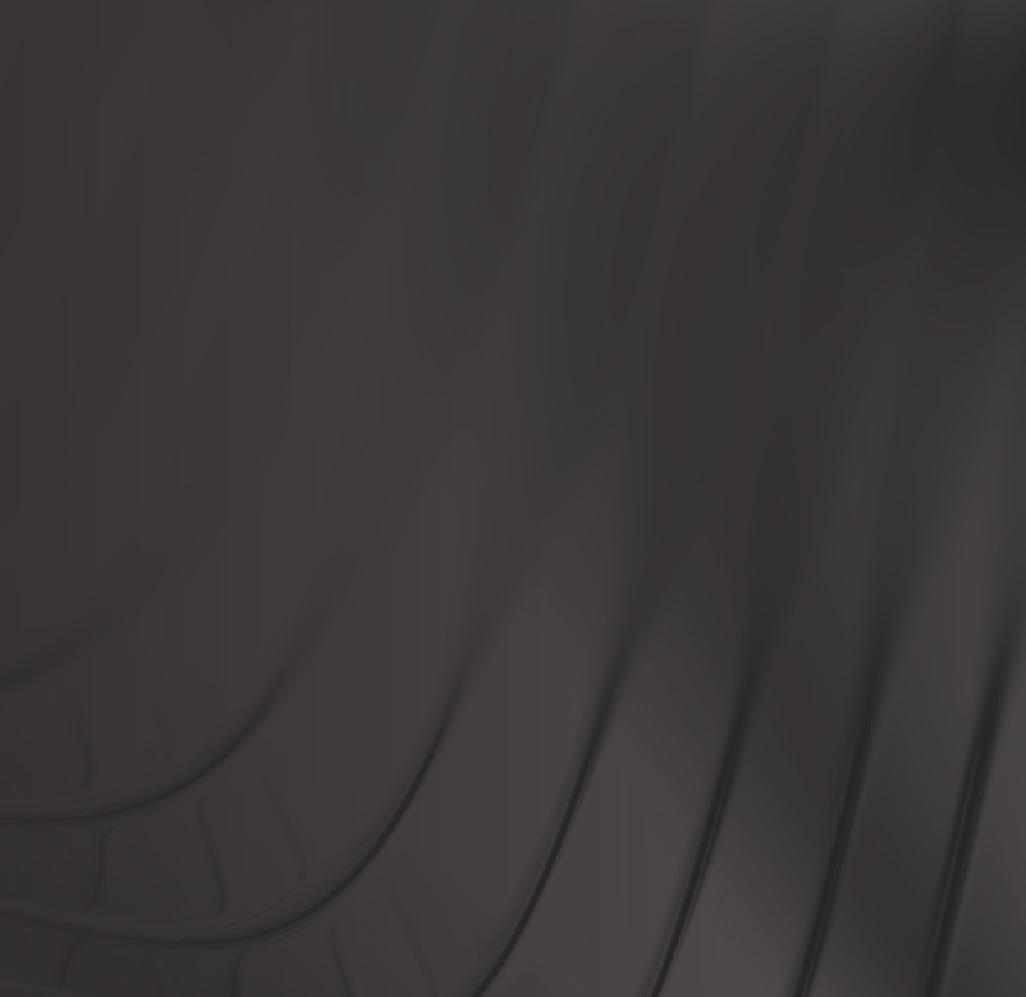
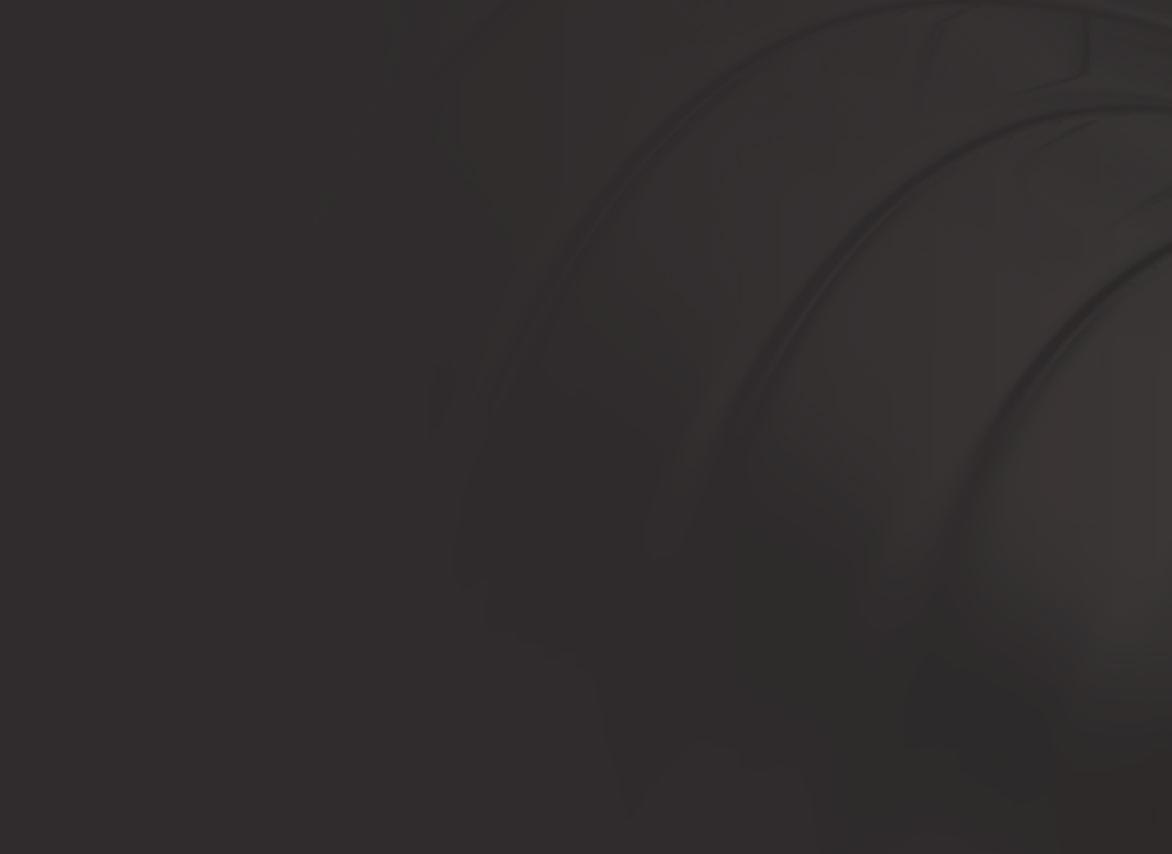

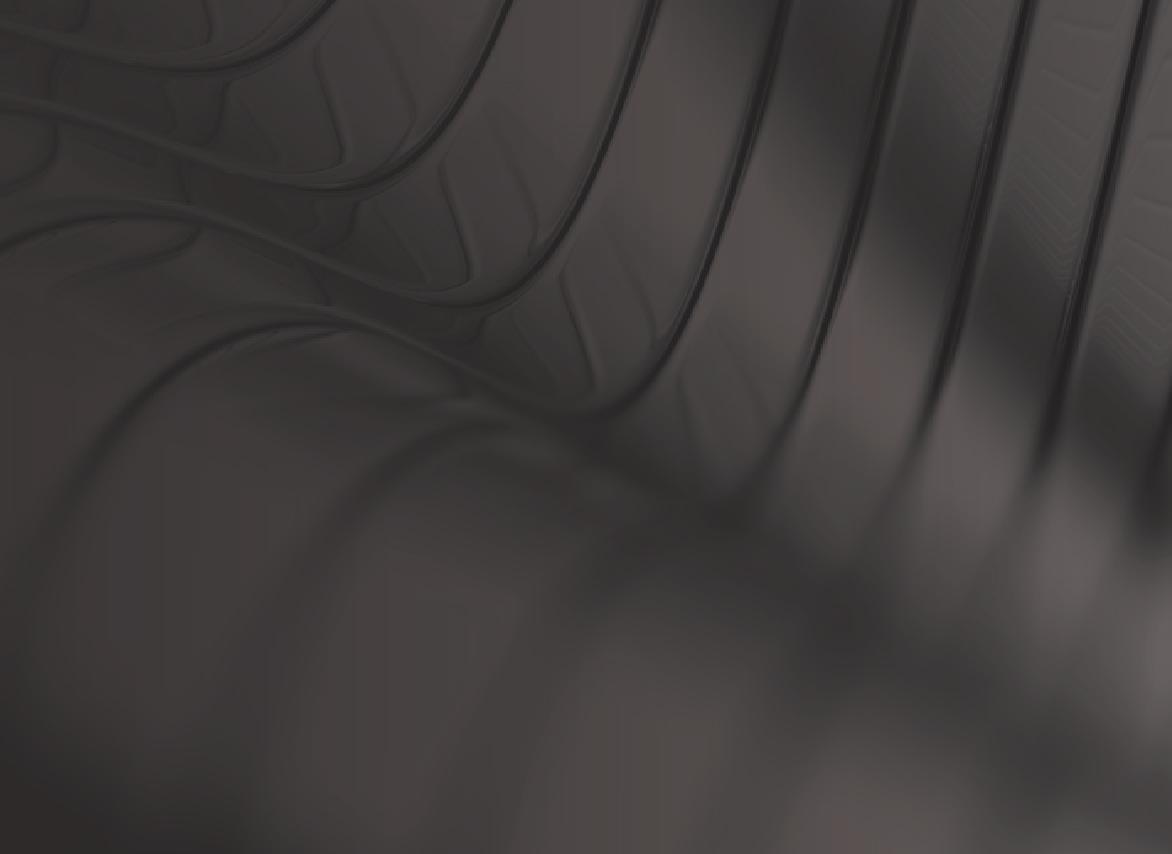

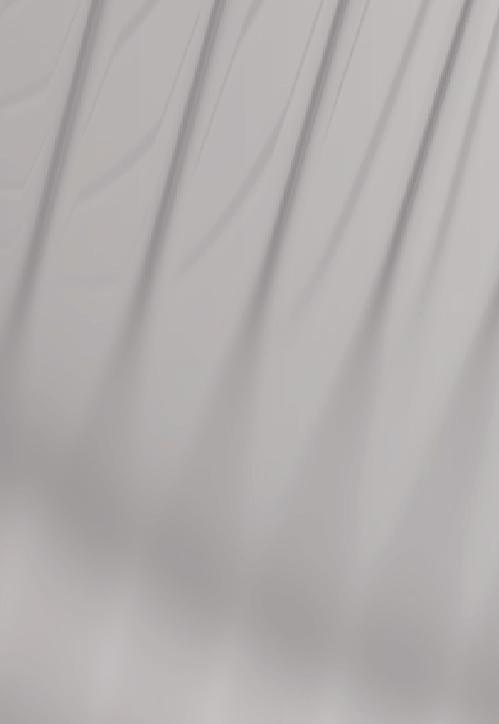
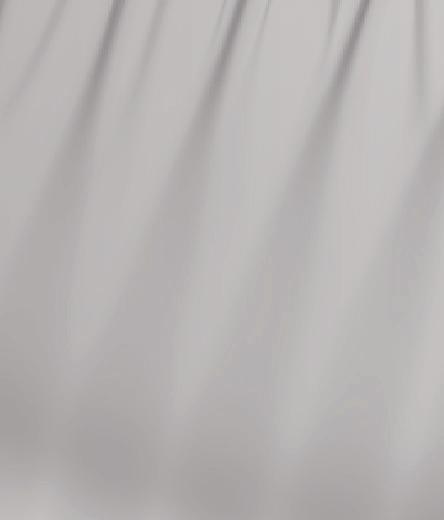

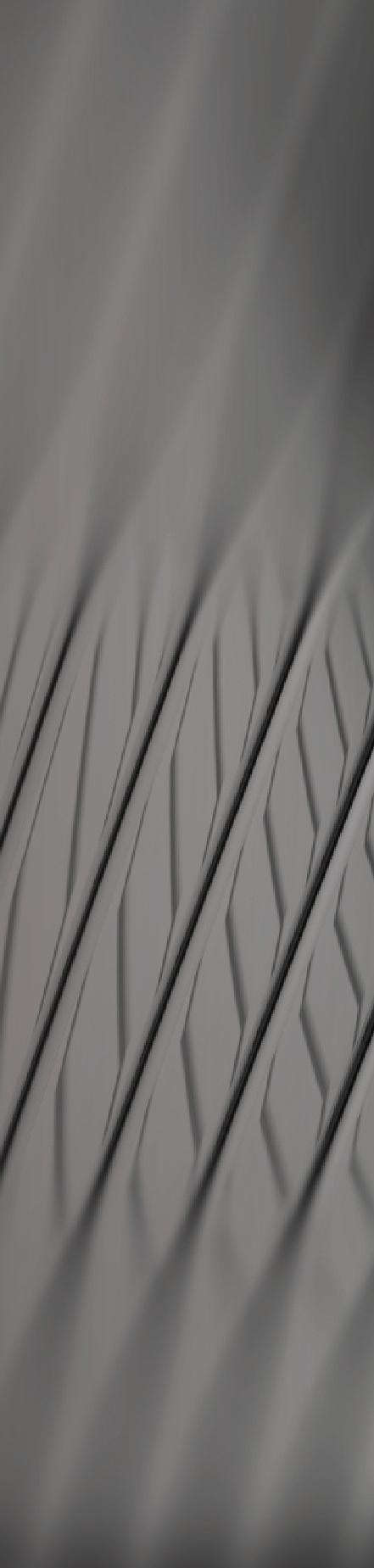
At Air Products we’re helping customers transition to low-carbon fuels such as hydrogen, generating a cleaner future for us all.
We’re also reducing emissions by improving the efficiency of existing aluminium production plants.
Our Smart Process Advisor system is playing a key role in decarbonising the industry, ensuring furnaces are operating at peak performance. Visit us at Aluminium 2024, Hall 6, Stand M70 to find out more.
Or contact us to see how these innovative new technologies can help you achieve your most critical KPIs.
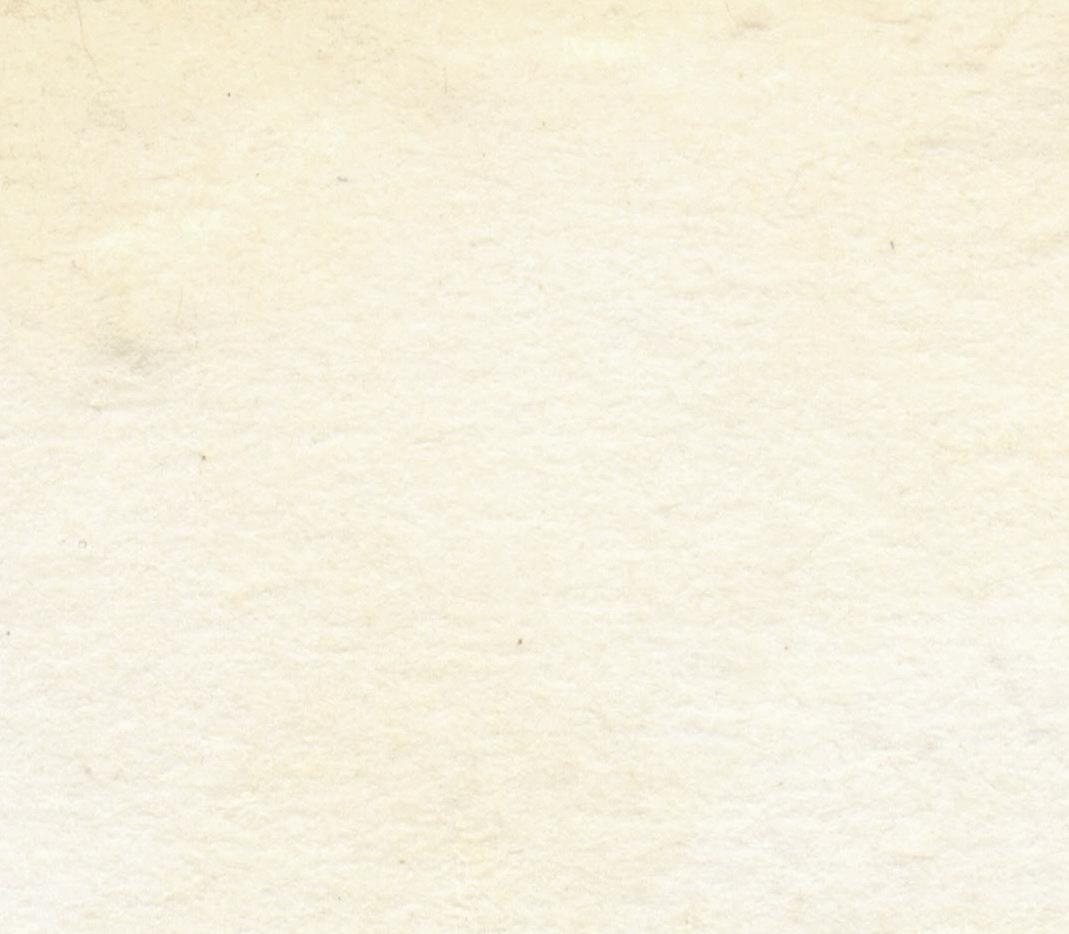
The European Aluminium Foil Association (EAFA) stands as the premier organisation in Europe representing companies in the aluminium foil industry. With over 40 members engaged in the manufacture, processing and marketing of aluminium foil, the EAFA has been a cornerstone of the industry since its foundation 50 years ago. Throughout its history, the EAFA has championed the interests of its members, fostering innovation and promoting sustainable practices within the sector. This article will delve into the EAFA’s history, achievements, current projects, and the challenges that lie ahead.
A Brief History of Aluminium Foil

The story of aluminium foil began in 1910 when Robert Victor Neher filed a patent for the continuous rolling process and established the first aluminium rolling mill in Kreuzlingen, Switzerland. By 1911, the Bernese company Tobler started using aluminium foil to wrap its chocolate bars, including the iconic Toblerone. In 1912, Maggi followed suit, employing aluminium foil for packaging soups and bouillon cubes. The exceptional barrier properties of aluminium foil against light, moisture, and aromas quickly made it indispensable in various industries. Over the years, aluminium foil has found applications in food and beverages, pharmaceuticals and beyond. Today, its uses include aseptic drink cartons, pouches, lids, wraps, blister and strip packs, foil containers and much more.
The Founding of EAFA
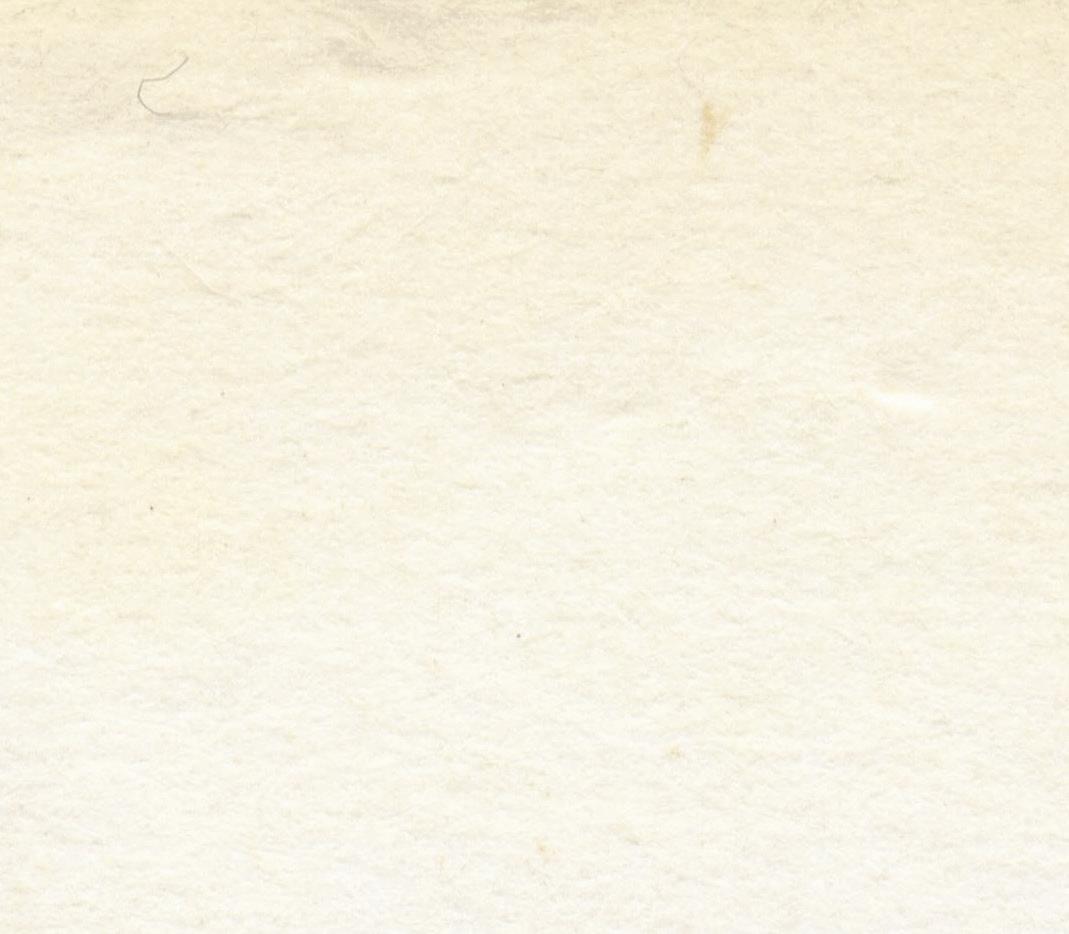
A Half-Century of Innovation
50 Years of the European Aluminium
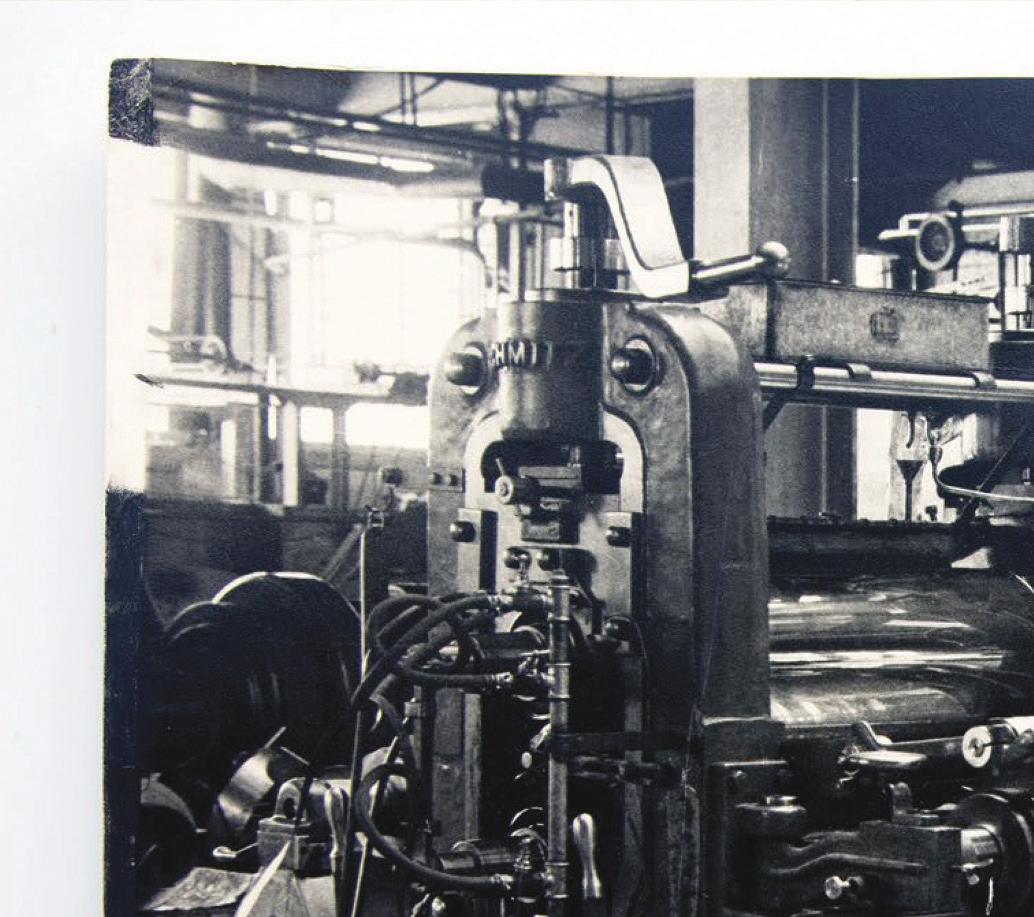
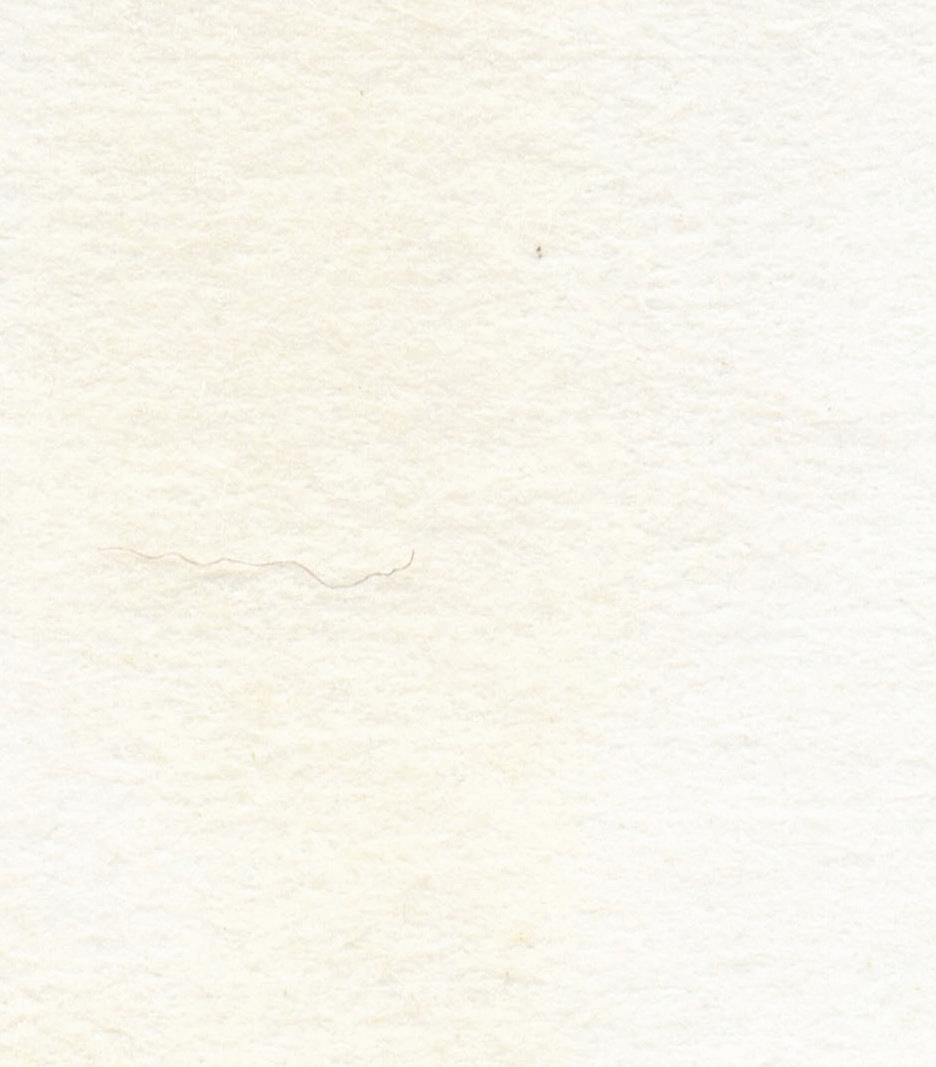
In 1974, the EAFA was officially established to represent and promote the interests of European aluminium foil manufacturers. This year, the association proudly celebrate its 50th anniversary – a half-century of significant milestones and substantial contributions to the industry. The roots of the aluminium foil sector, however, stretch back much further. As early as the 1920s, initial organisations emerged to promote and regulate the industry.
One of the early milestones was the formation of the AFCO in 1955, which enabled the first collaboration among aluminium foil companies in Europe. This facilitated the exchange of production data and statistics, and the establishment of uniform values and best practices.
These formative years laid the groundwork for the creation of EAFA, an organisation dedicated to unifying the industry and driving it forward. The first divisions within EAFA were the Roller Group and the Converter Group. Until the late 1990s, the association was organised into national groups, each with its own secretariat. It was only after member companies became more international that a central Secretariat was established in Düsseldorf, streamlining operations and fostering greater collaboration.
Development and Achievements Over the Years


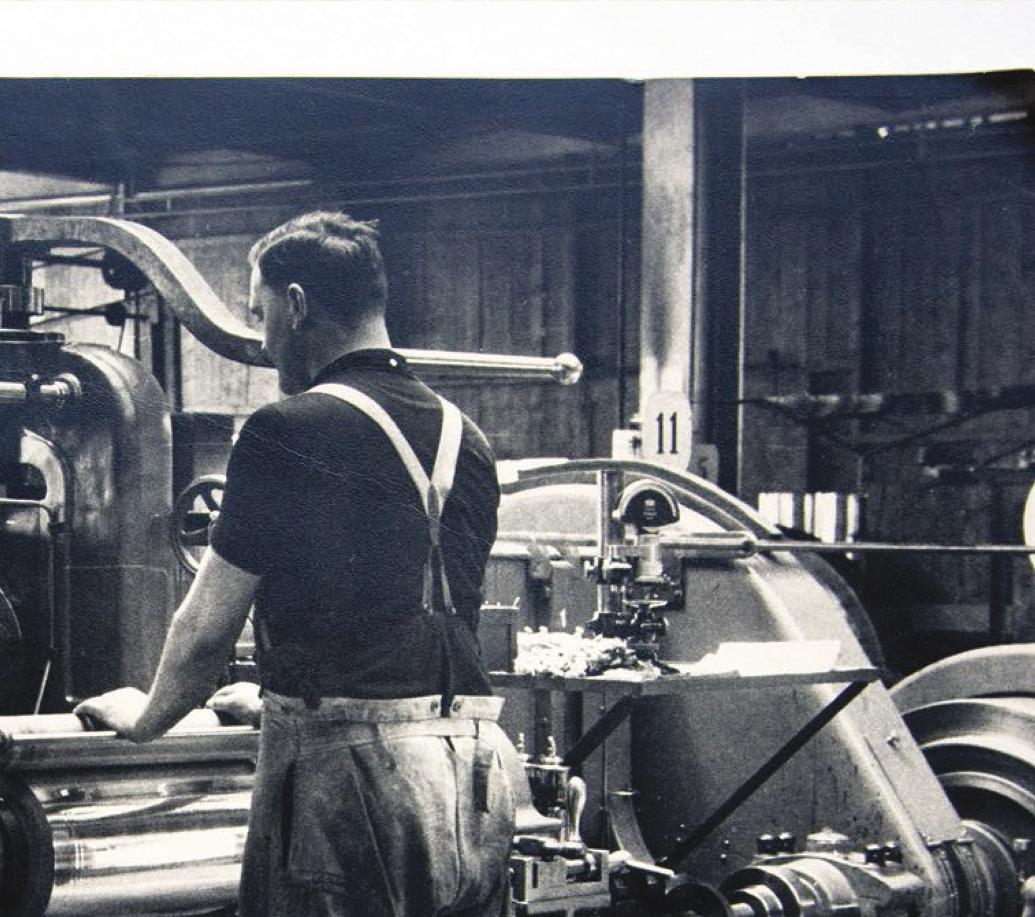

and early collaborations of the 1950s and 1960s, EAFA continued to drive progress and innovation in the industry.
During the 1980s, EAFA placed a strong emphasis on innovation and sustainability.
The introduction of the Alufoil Trophy was a pivotal moment, recognising outstanding achievements across various segments: brand owners, retailers, packaging manufacturers, consumer groups and several others. This award has become a prestigious accolade, celebrating excellence and inspiring ongoing advancements in the field.
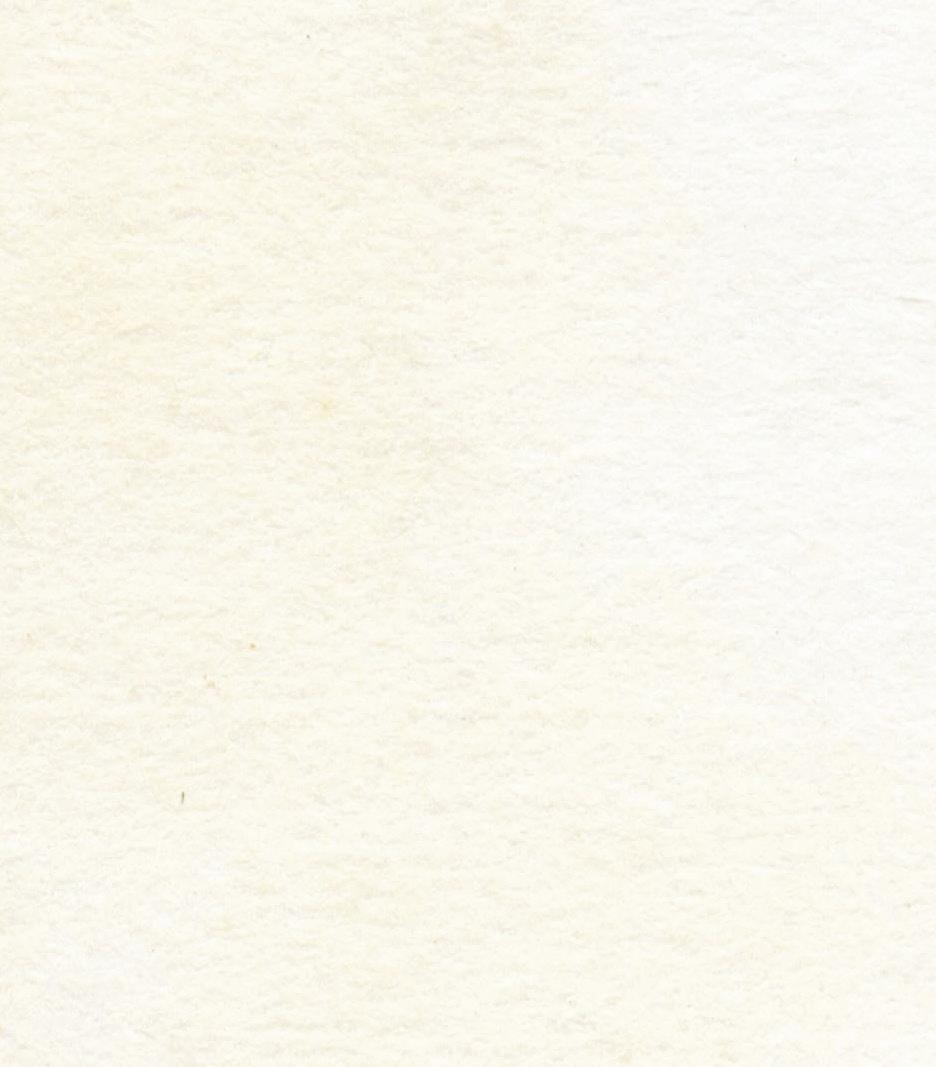
EAFA has achieved numerous successes and made substantial contributions to the aluminium foil industry over the past five decades. Building on the foundational efforts
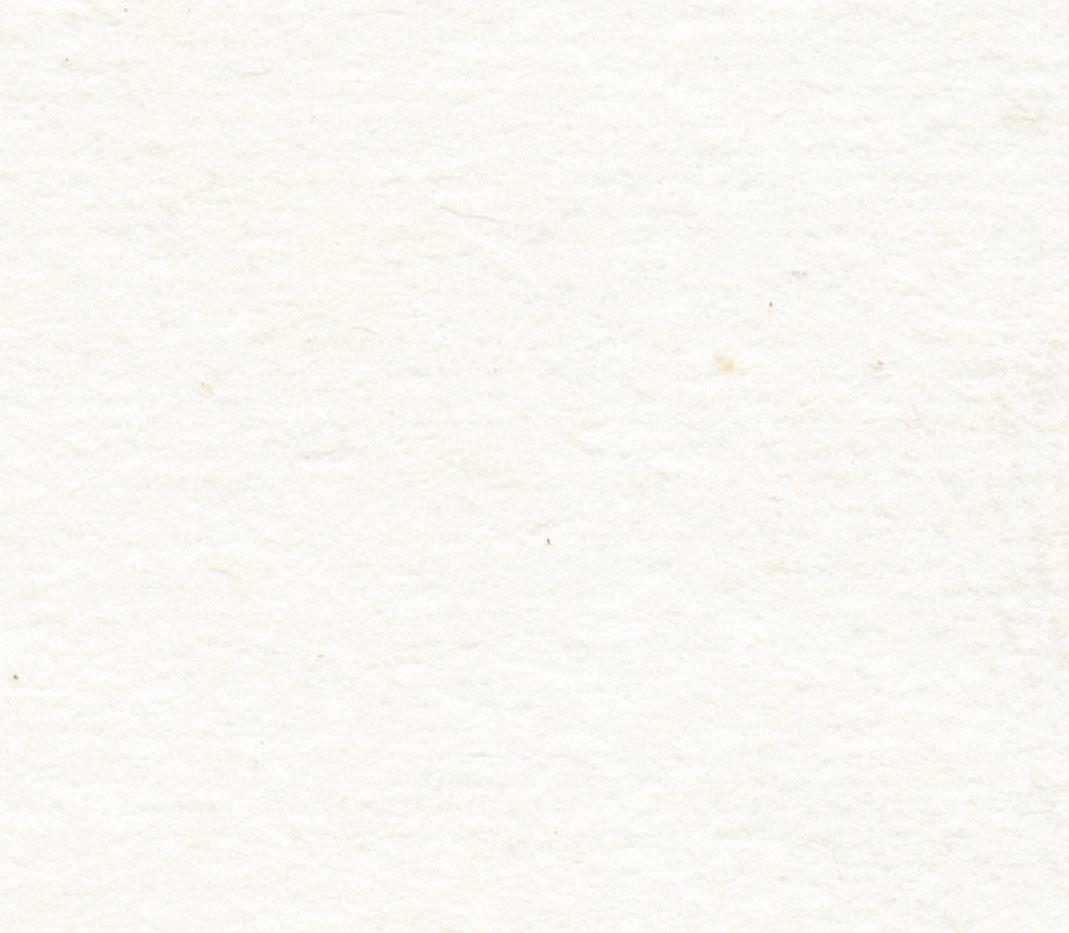
EAFA was also an early advocate for holistic life cycle assessments (LCAs) of products packed in aluminium foil, an effort even acknowledged by the United Nations Environment Programme (UNEP). These assessments demonstrated the environmental benefits of aluminium foil packaging, highlighting its minimal ecological footprint and its contribution to resource conservation.
In response to evolving industry needs, EAFA established the Container Group (for semi-rigid alufoil containers and trays) in 1993 and the Rewinder Group (for household foil) in 2004. These groups allowed the EAFA to address specific challenges and opportunities within these segments more effectively covering now the rolling and further processing steps of aluminium foil.
The formation of the Aluminium Closures Group in 2013 marked another significant expansion, cate ring to the growing demand for aluminium closures and providing new business opportunities for their members.
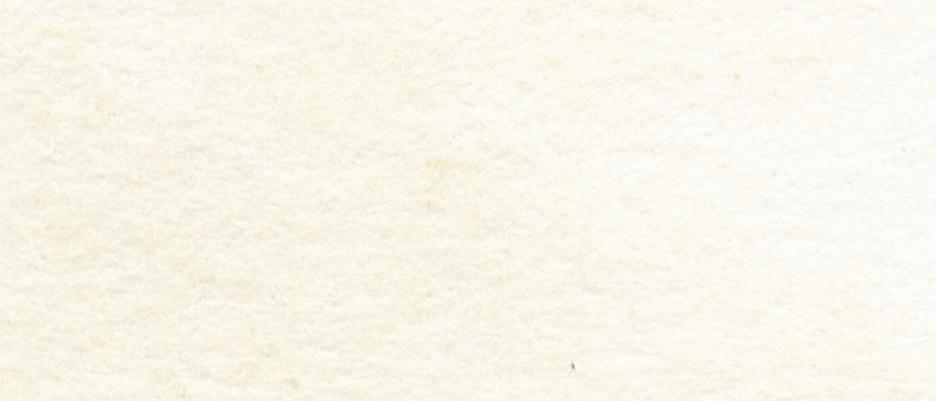
EAFA’s Converter Group, through its merger with Flexible Packaging Europe (FPE), remains a material-neutral organisation
under its own branding, maintaining its status as a sister organisation next to EAFA. This structure enables the association to adapt flexibly to the changing demands of the industry, while effectively representing the interests of the members and leveraging synergies to advance sustainable solutions and innovations collectively.
As co-initiator of the Global Aluminium Foil Roller Initiative (GLAFRI), the first global foil association representing over half of the world’s foil rollers, EAFA operates the secretariat for GLAFRI and plays a pivotal role in organising the biannual global conference GLAFCO. GLAFRI is dedicated to coordinating actions on sustainability to support market growth and promote innovative development in the foil industry. GLAFRI members, comprising foil rollers and suppliers, are responsible for a significant portion of global foil production, working together to advance sustainability practices and drive the industry’s future.

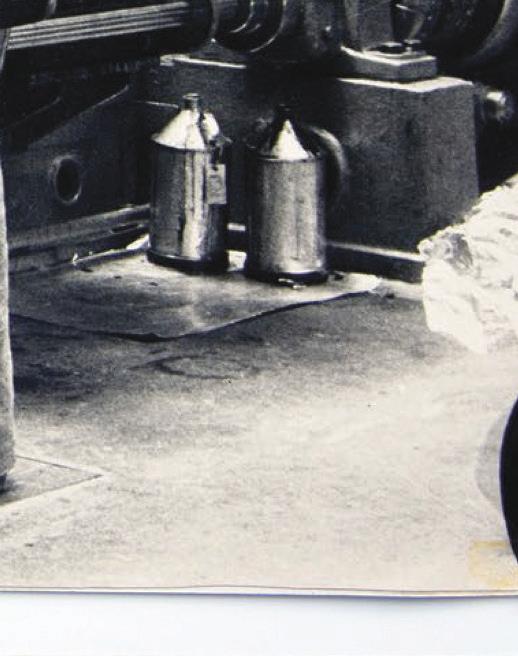
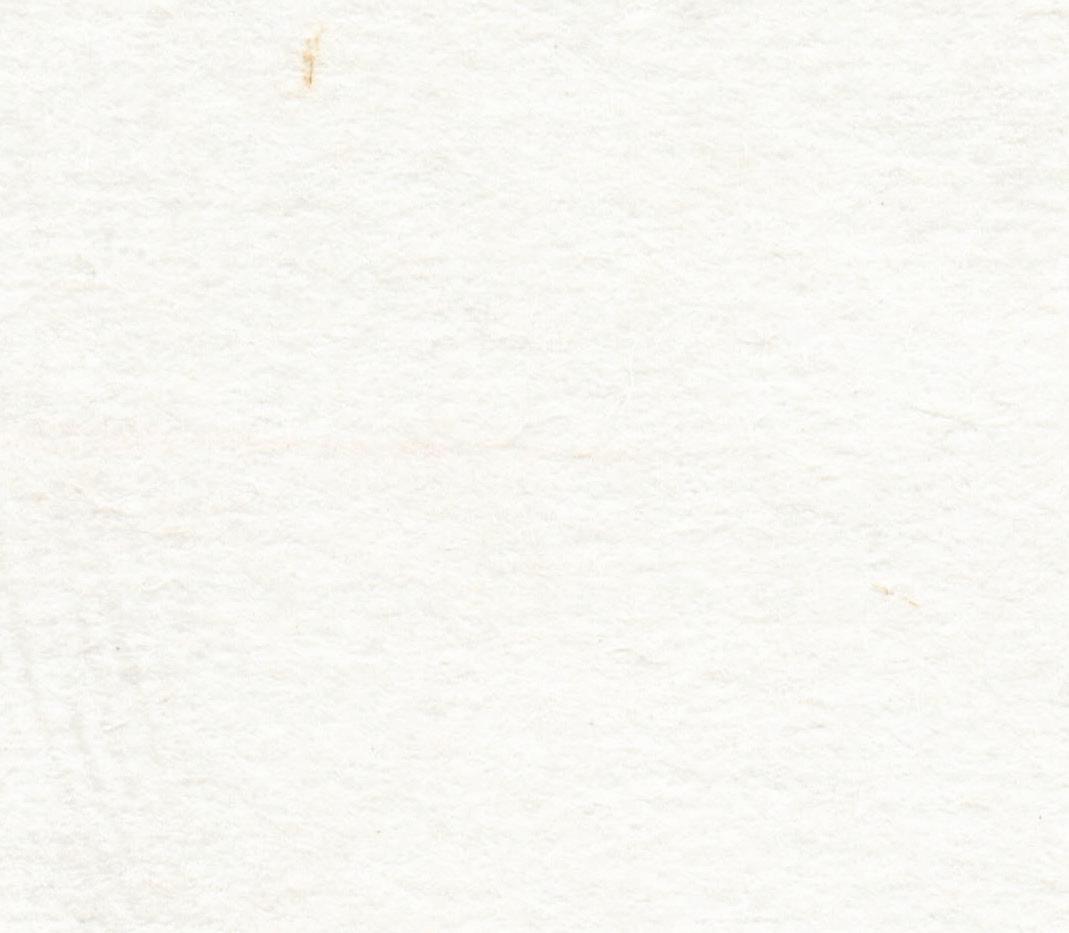
In 2023, the EAFA and its sister organisations took a strategic step by opening an office in Brussels. This move enhances its ability to advocate for the members’ interests at the European level, placing it closer to policymakers and enabling more effective engagement on critical issues.
Current Status
Today, EAFA is a dynamic organisation that continuously adapts to the evolving needs of its members. The aluminium foil industry continues to grow, making remarkable technological advancements. The industry representation remains a vital advocate for its members, addressing the challenges of a rapidly changing environment and ensuring
their interests are well-represented.
The organisation facilitates the exchange of knowledge and best practices through regular conferences, workshops, and seminars. These events provide its members with opportunities to stay informed about the latest industry developments and to network with peers.
In addition, the association compiles and provides more than 30 industry statistics supported by member data for various applications and product groups delivering important industry benchmarks and detailed market information. This key service is accompanied by economic data, trade statistics on global, regional and national level, end consumption statistics and trend analyses. Access to various external databases enables current updates and customised analysis whenever required by member companies.
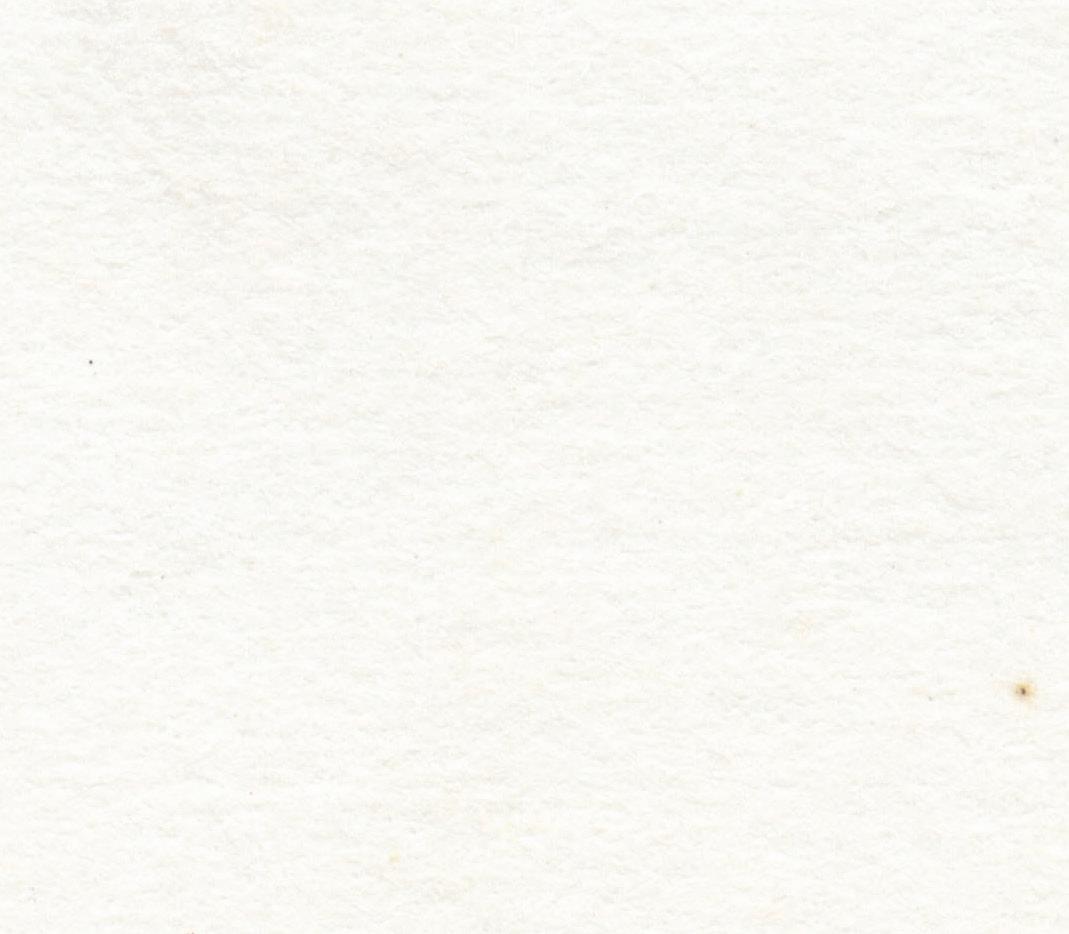
The regular, transatlantic exchange with counterparts such as the Aluminium Foil Container Manufacturers Association (AFCMA) from North America allows the organisation to share global knowledge and best practices, working together to develop solutions for the industry.
Current Projects & Activities
The EAFA is currently involved in several pioneering projects that will shape the future of the aluminium foil industry:
○ Sustainability and Recycling: EAFA promotes essential recycling processes to make packaging lighter and more sustainable. Life cycle assessments of foodstuffs show that aluminium foil packaging has a low ecological footprint and helps to conserve resources. Various

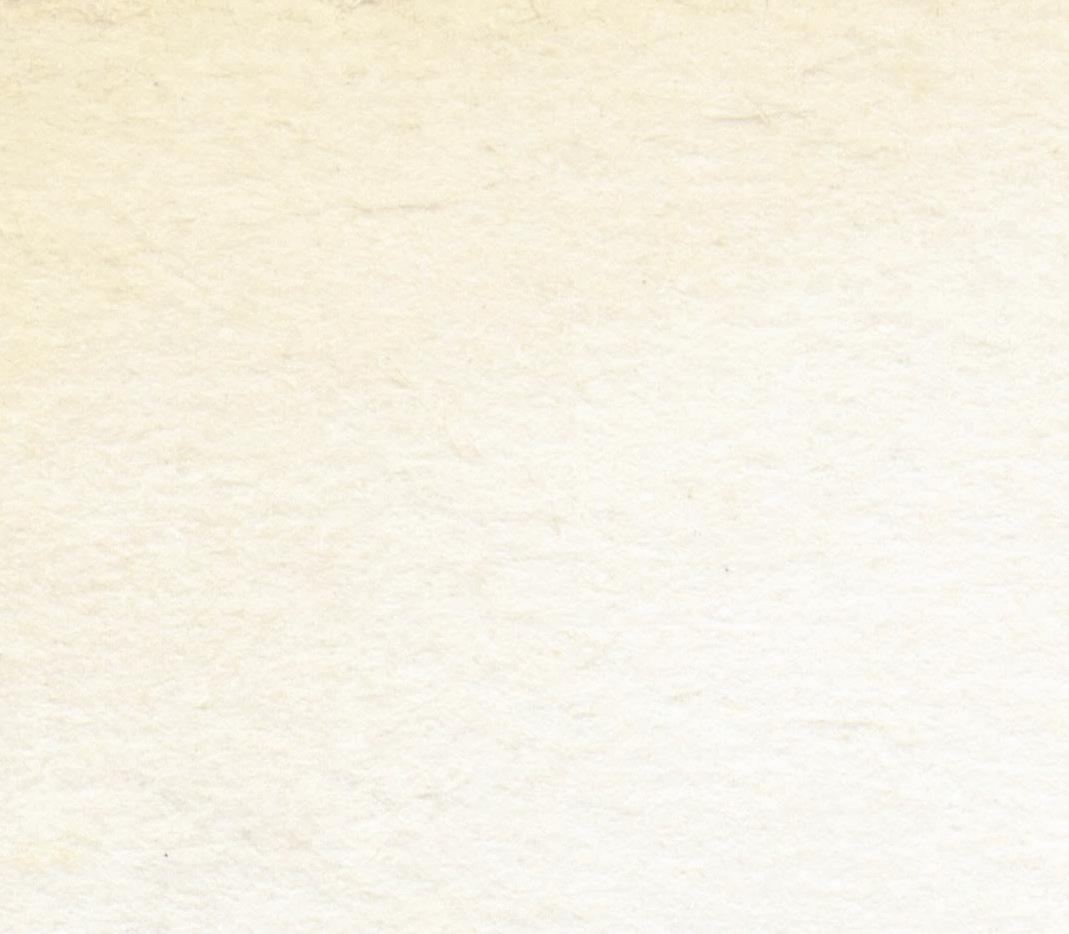
studies have shown that aluminium foil in food packaging has a positive impact on the environment. To better understand the environmental impact of aluminium foil in different packaging applications, EAFA has commissioned a series of full LCA studies from independent institutes specialising in LCA. These can be found on the homepage for further reading: https://www.alufoil. org/food-lifecycle-studies
○ PPWR: EAFA is actively engaged in the legislative process of the Packaging and Packaging Waste Regulation (PPWR), aiming to minimise waste and enhance the recyclability of packaging. This includes not only the recyclability of packaging materials but also the real recycling at scale in the future.
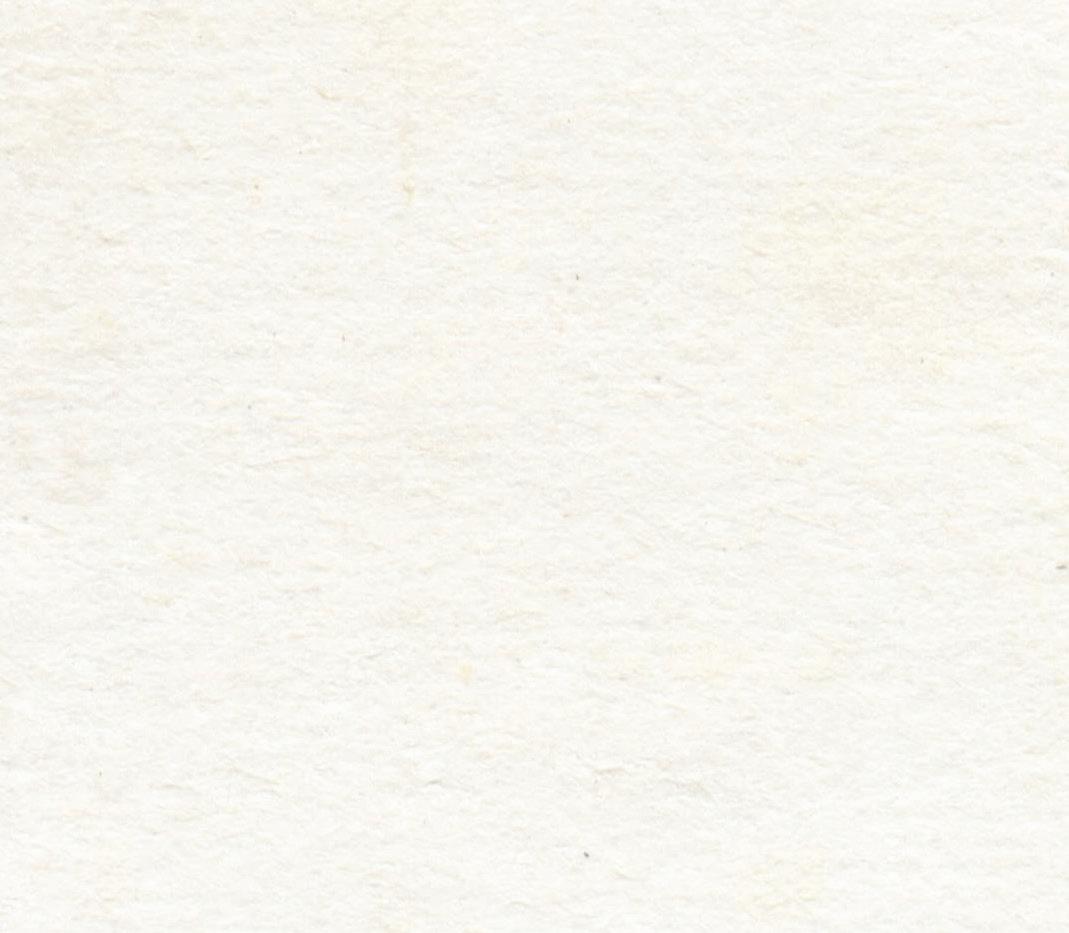
○ Aluminium and Health: Ensuring the safety of products in contact with food is a top priority. EAFA advocate for the industry’s interests through rigorous studies and realistic analyses, ensuring that aluminium foil remains a safe and reliable choice for applications in contact with food. In this context, for example, EAFA has supported a study which shows that exposure to aluminium through food contact materials containing aluminium is completely reversible. The study by the Institute and Polyclinic for Occupational, Social and Environmental Medicine at the University of Erlangen-Nuremberg investigated whether a diet with high exposure to aluminium food contact materials leads to increased systemic aluminium exposure. It was found that an increase in aluminium exposure could be measured in humans through subacute exposure to Al-FCM under real conditions, but that this was completely reversible.
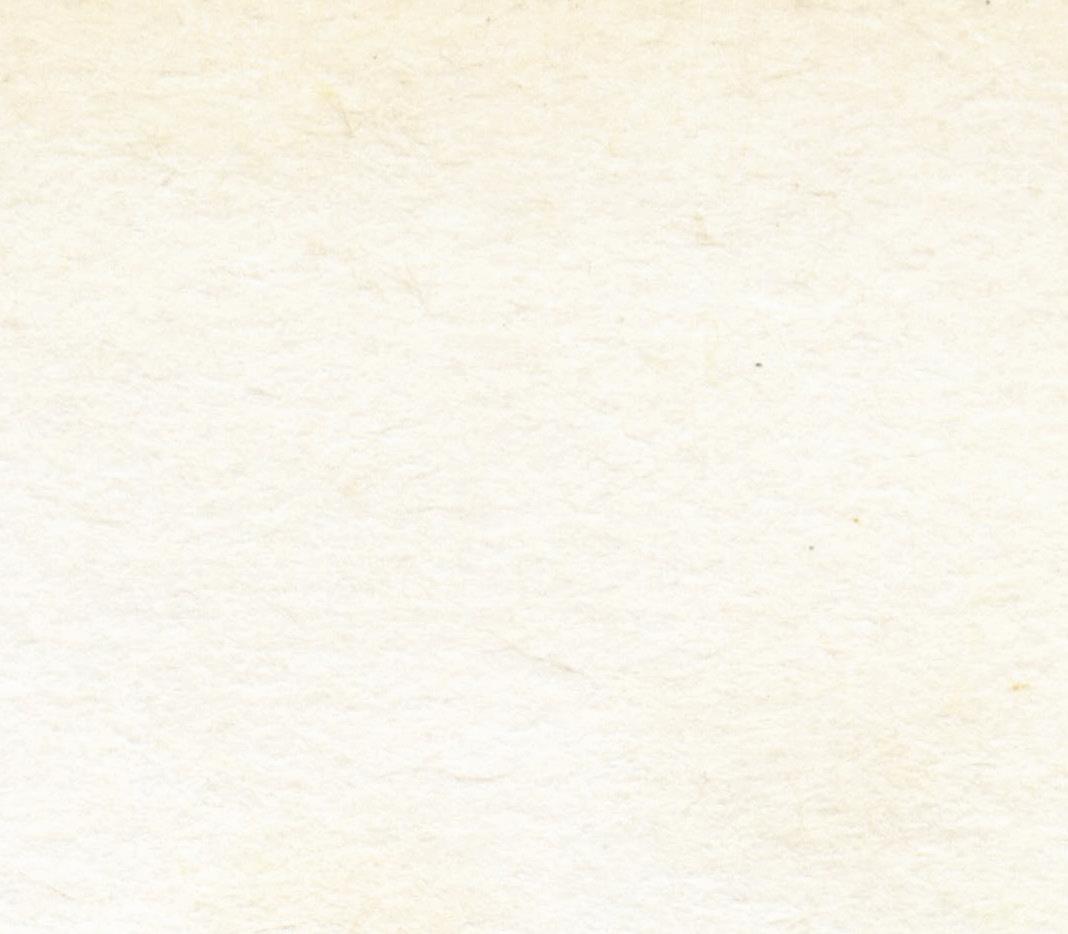
Innovation and Commitment: Aluminium Foil Association

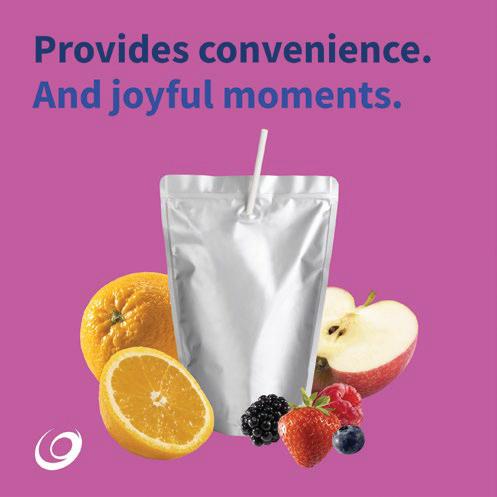
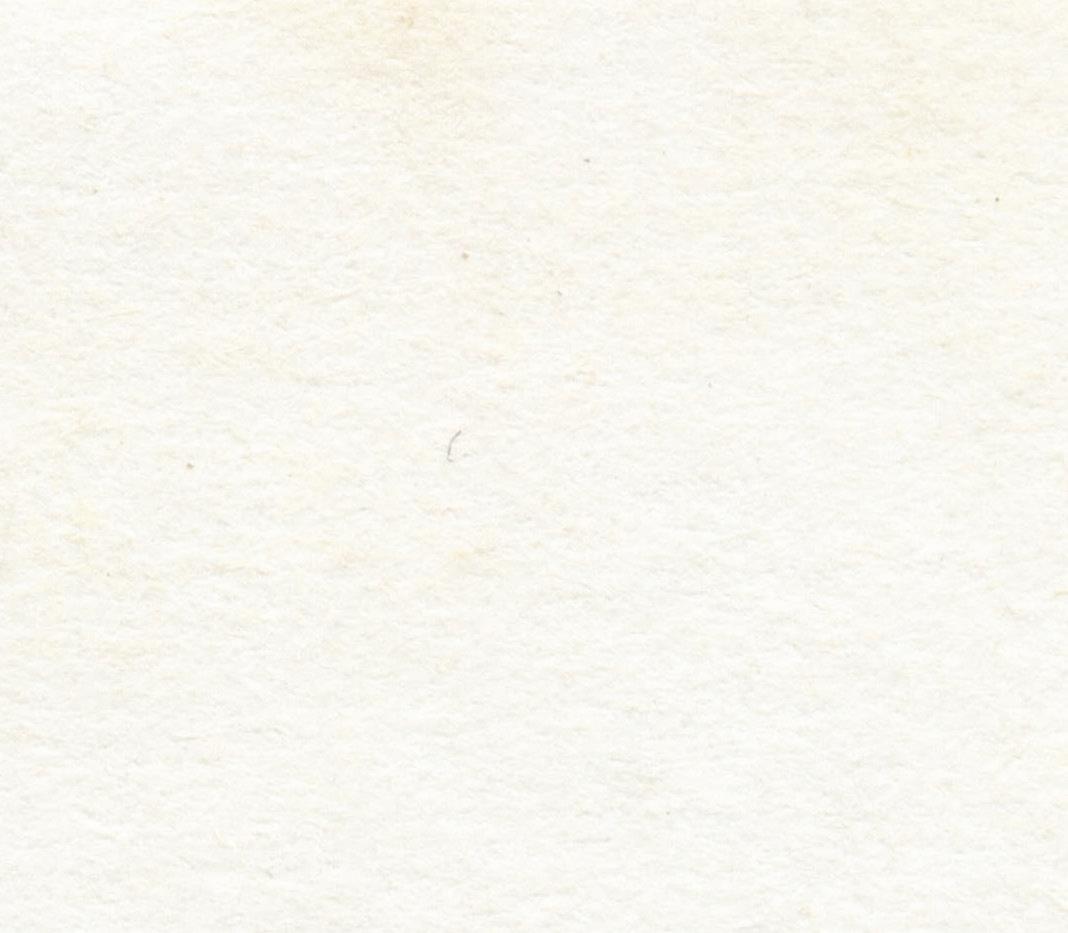
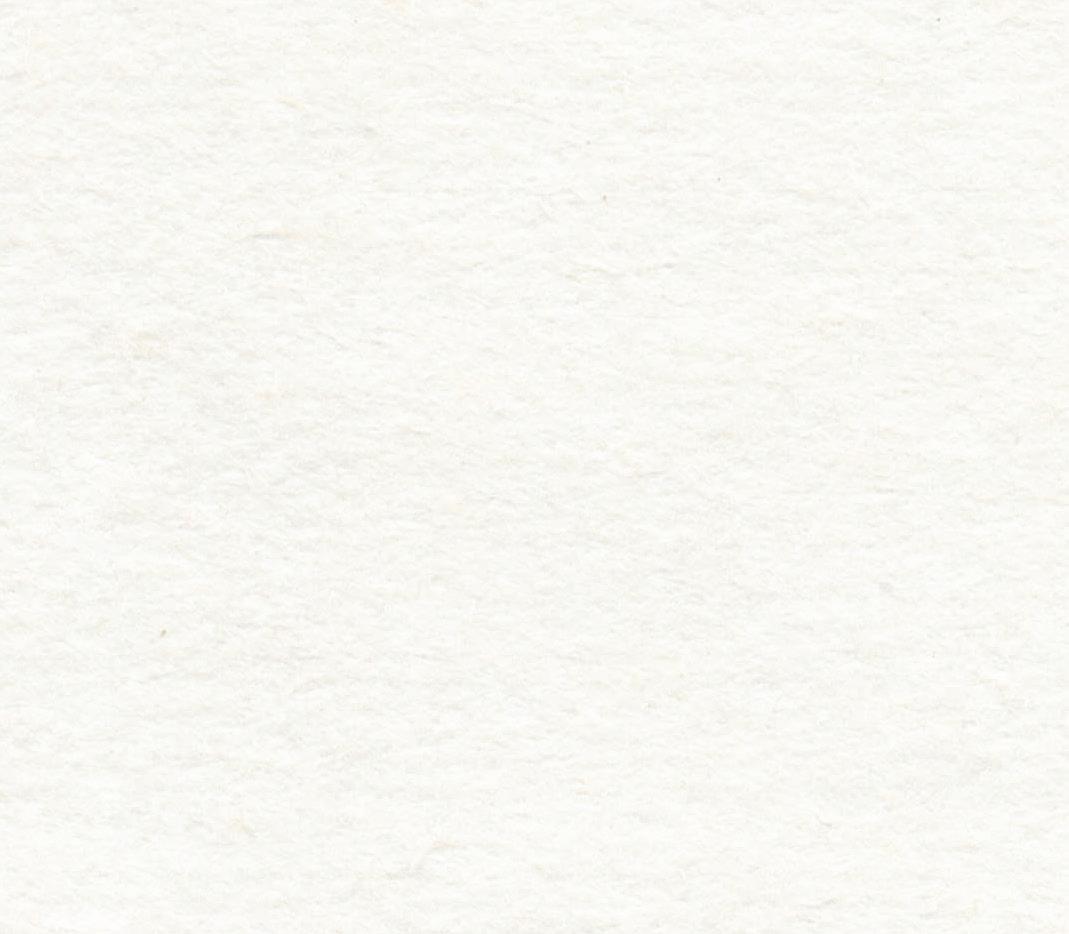
“Protect What We Love” Campaign: For the past 2.5 years, this successful campaign has aimed to highlight the versatility and sustainability of aluminium foil, raising awareness of its benefits. Through regular PR activities in the press and on social media, the campaign has significantly strengthened the image of aluminium foil.
Outlook
The aluminium foil industry faces numerous challenges, including evolving regulatory requirements and increasing demands for sustainability and recycling. EAFA will continue to work closely with its members and the entire value chain to address these challenges and advance the industry.
aluminium foil can greatly contribute to environmental goals. Through concerted efforts in communication and collaboration, EAFA aims to highlight the extensive benefits of aluminium foil, ensuring it remains a preferred material in various industries.
Aluminium foil is an indispensable material in numerous applications, from food packaging to industrial uses and emerging sectors such as e-mobility.
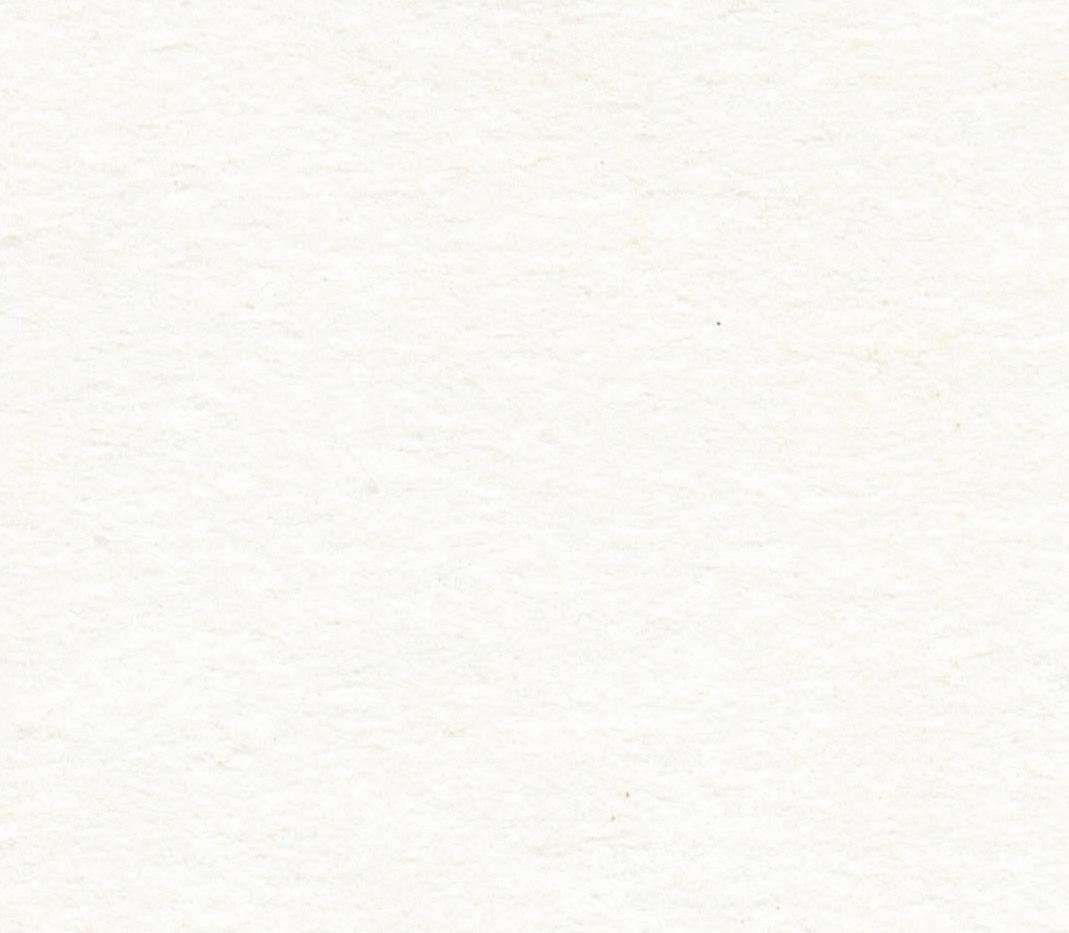
One of EAFA’s primary goals is to further promote the circular economy and develop innovative solutions for a sustainable packaging industry. This includes improving recycling processes and developing new, eco-friendly materials and technologies. Although still increasing, 8% of primary aluminium is already used for the production of aluminium foil.
Moreover, the EAFA will intensify its efforts to educate the public about the benefits of aluminium foil and raise awareness of its contribution to a sustainable future. This will be achieved through targeted PR campaigns, public relations initiatives and collaboration with other organisations and stakeholders. Public awareness and education are critical, as the versatility and sustainability of

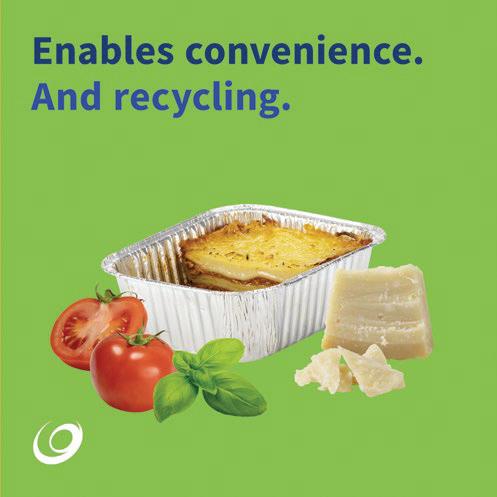
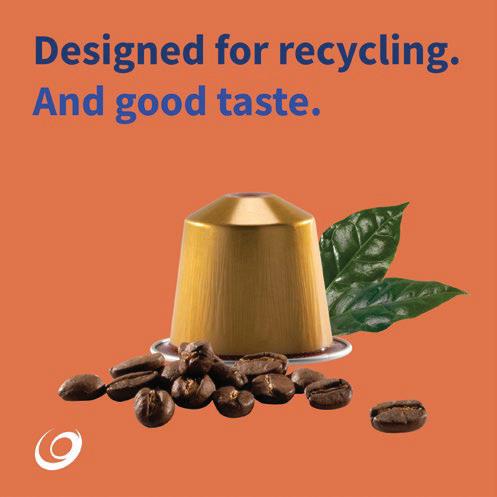
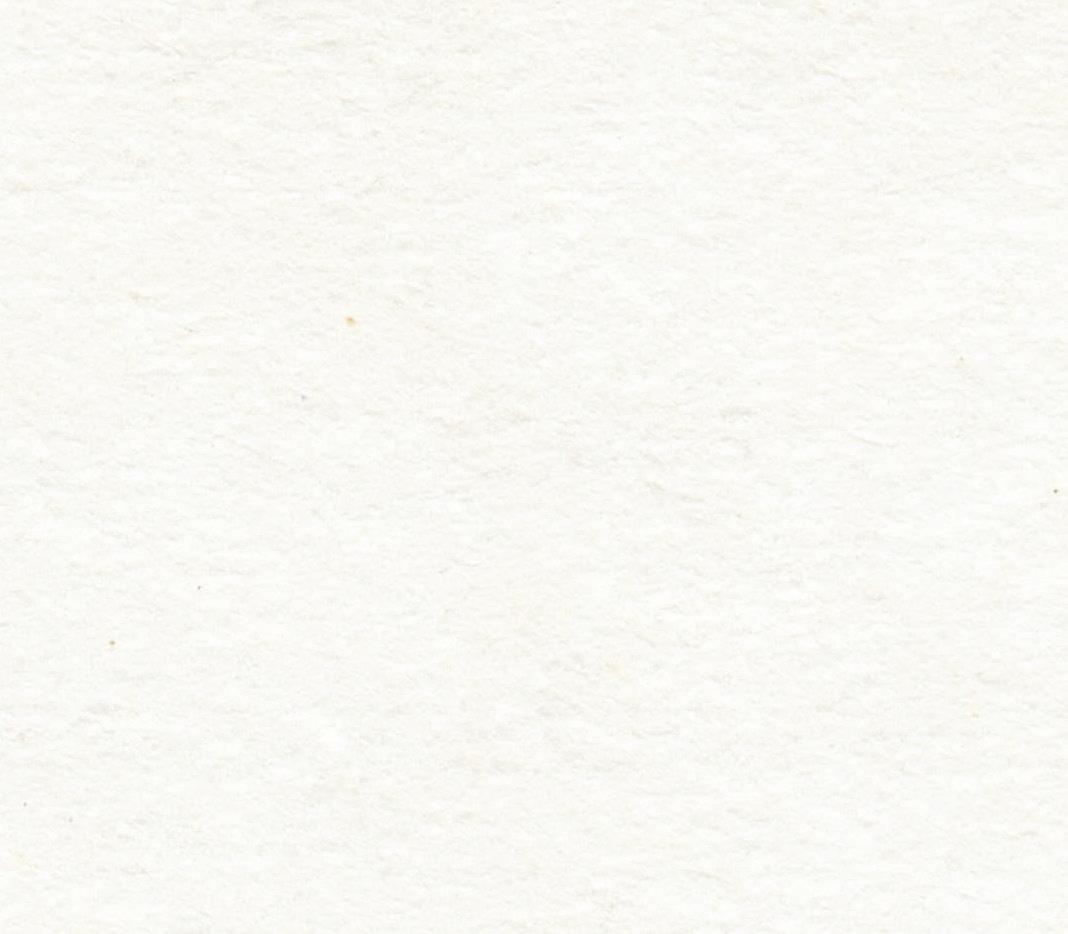
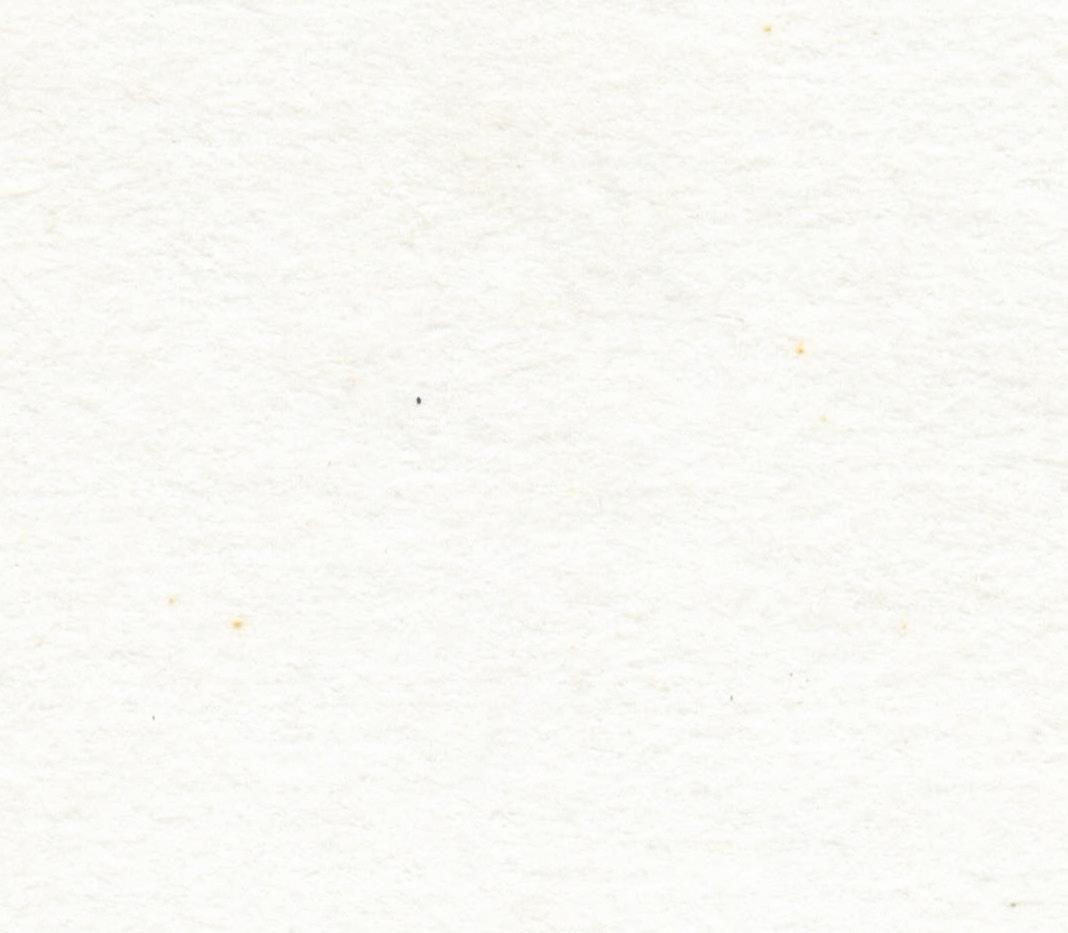
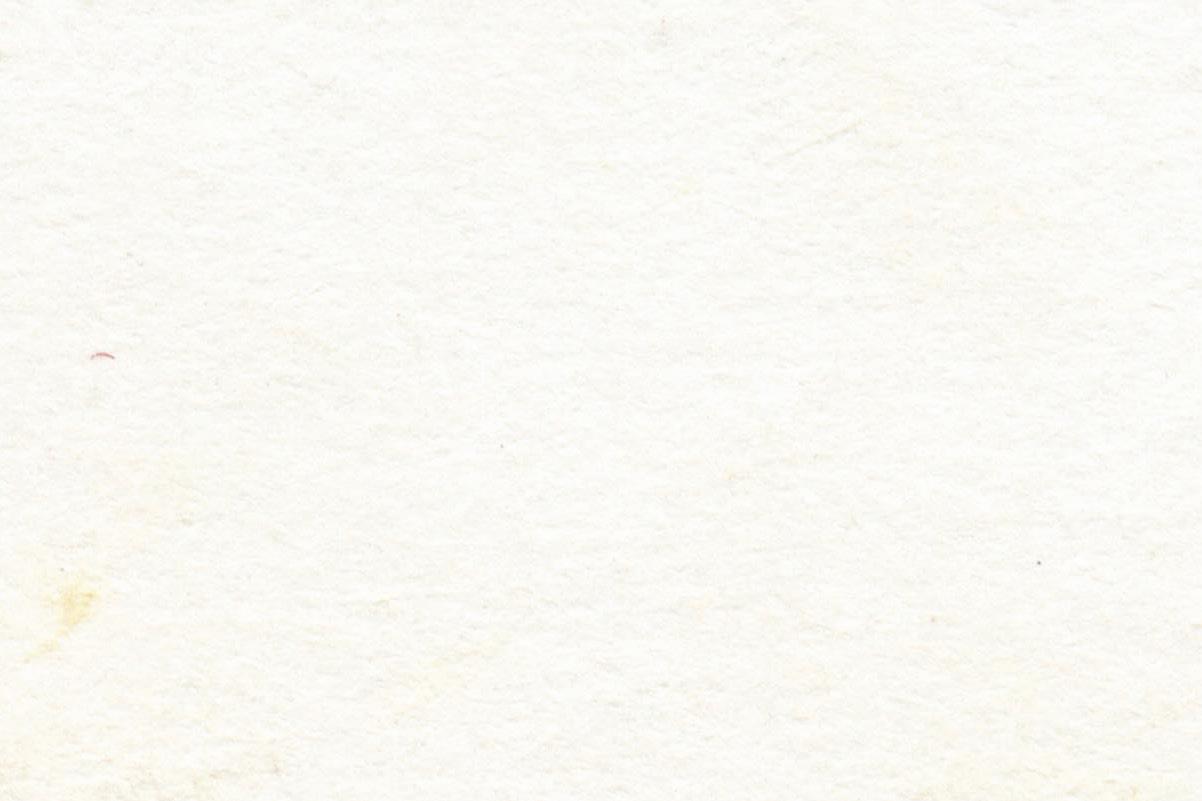
EAFA is proud to have been part of this vital industry for 50 years, successfully supporting its members as sparring partners and guides. This milestone is a testament to the association’s commitment to fostering a collaborative environment where industry players can thrive. By leveraging collective expertise and shared resources, EAFA has continually advanced the aluminium foil industry’s standards and practices, promoting growth and innovation.
The ALUMINIUM trade fair plays a crucial role for EAFA and its members. It provides an important platform to showcase the latest innovations and developments in the aluminium foil industry and to network with other industry players. It will present its achievements and projects to a broader audience, representing the members, and being present for personal exchange and the expansion of EAFA´s shared network.
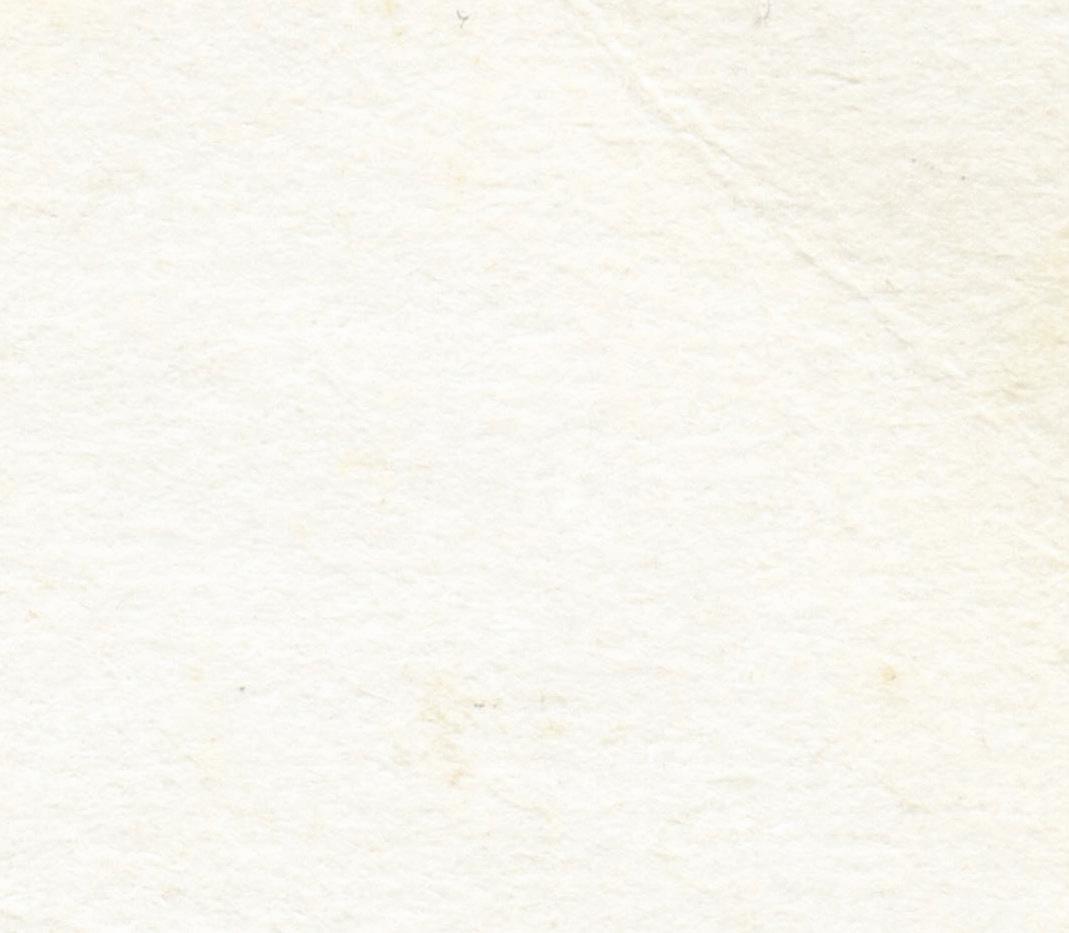
It offers excellent barrier properties, is lightweight yet robust, and, most importantly, is fully recyclable. The remarkable attributes of aluminium foil make it a cornerstone of modern packaging solutions, enhancing product shelf life and reducing food waste. Additionally, its role in industrial applications continues to expand, driving innovations in sectors that demand reliable and sustainable materials.
In conclusion, the association is grateful for the long-standing collaboration and support of the entire aluminium foil industry. EAFA’s success over the past 50 years would not have been possible without the dedication and cooperation of its members and partners. The path ahead is filled with opportunities to enhance sustainability, drive technological advancements, and meet the evolving needs of consumers and industries worldwide. EAFA remains committed to leading these efforts, ensuring that aluminium foil continues to be an essential and forwardlooking component of modern life.
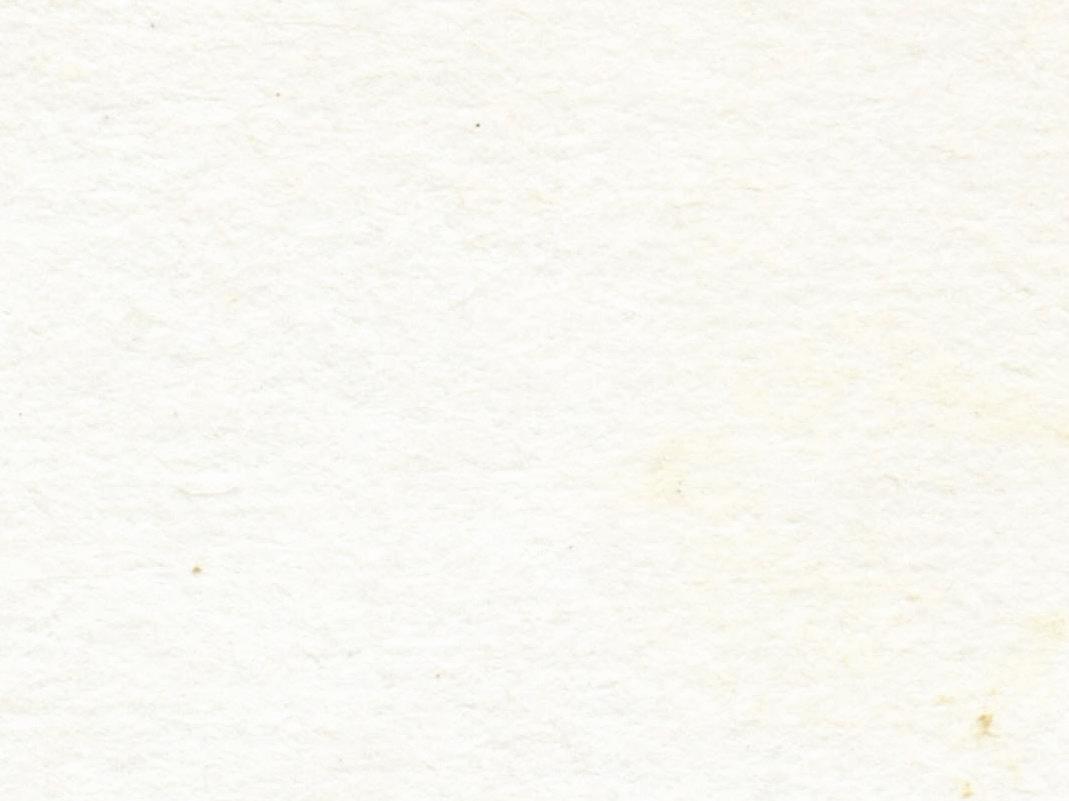
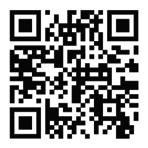
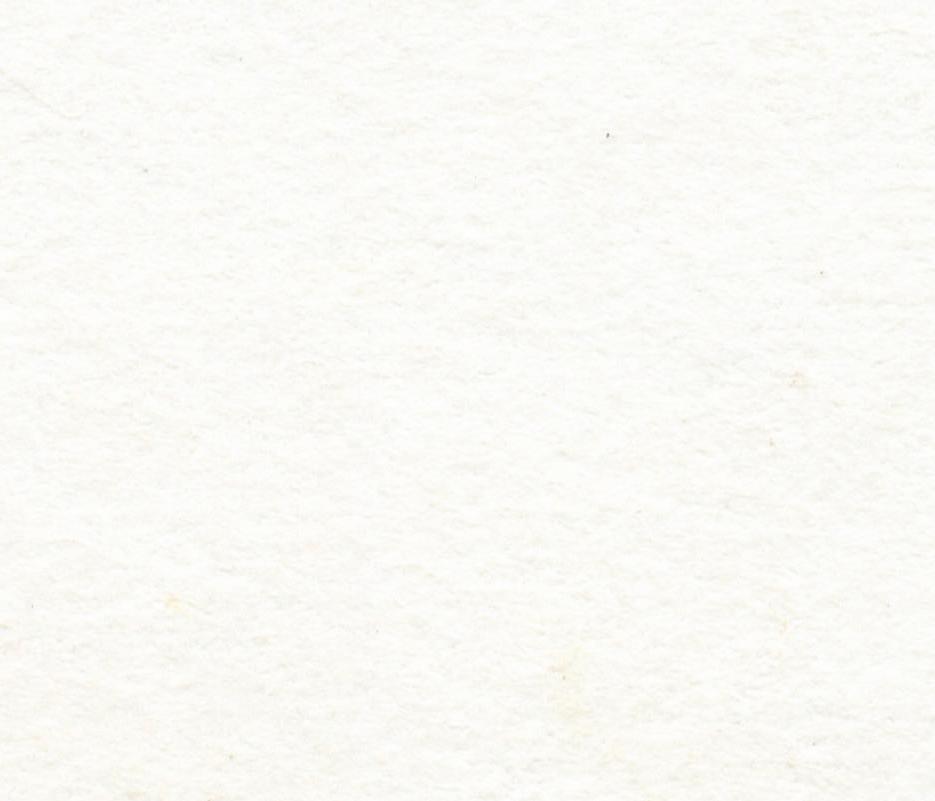

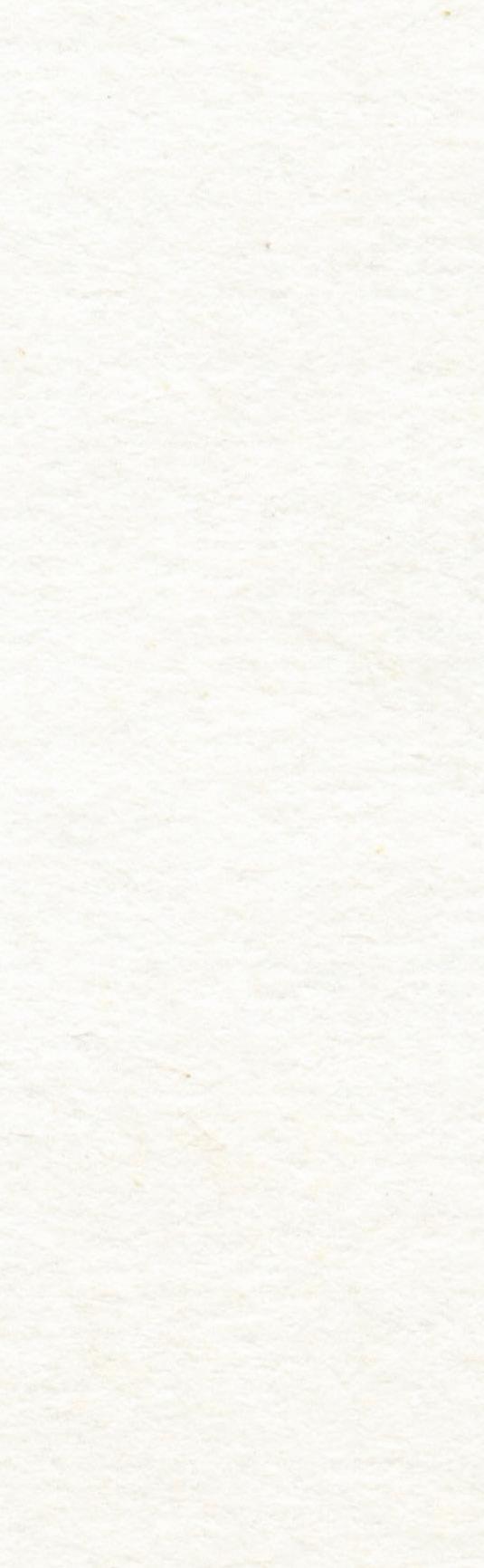


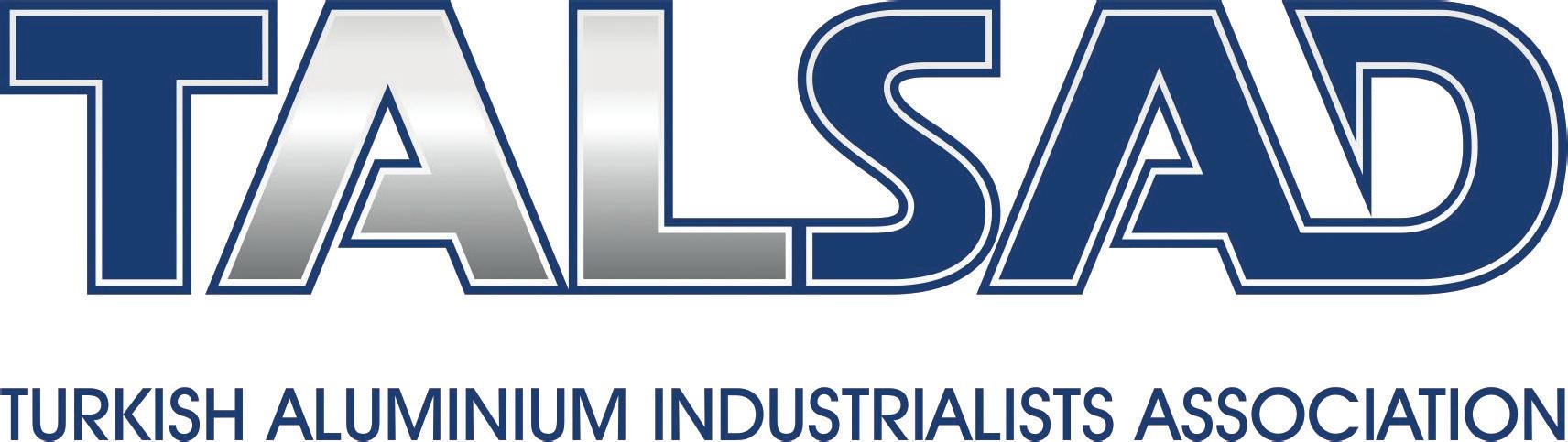
The Turkish Aluminium Industrialists Association (TALSAD) established on March 15, 1971 by leading Turkish aluminium industrialists to help and guide growth of national aluminium industry.
TALSAD works for sustainable growth and development of the aluminium industry in local and regional markets, development and implementation of new and advanced technologies, implementation of good practices in health, safety and environment and works to develop strong local and international partnerships. TALSAD now represents 77 aluminium manufacturing and processing member companies as one of the oldest industry organizations in Turkey and confidently promotes the Turkish aluminium industry to the global markets.
Turkish Aluminium Industry has been spread over a wide range of segments and industrial sectors including extrusion, rolling, casting, billet and ingot production, architectural and industrial applications including primary aluminium production.
Turkish Aluminium Industry has achieved sustainable high growth rate over the last decade and therefore has strengthen its place in the world markets.
TALSAD is:
○ The one of the oldest and deep-rooted association, working since 1971,
○ The leading industry organisation of the Turkish aluminium industry,
○ Working to expand the use of aluminium in Turkey and in our region,
○ Functioning to strengthen the link between our industrial sectors and our society,
○ Supporting new and advanced technology implementations of aluminium
○ Keen in guiding the development of aluminium industry through new industrial applications, research and development,
○ Working for a sustainable industry,
○ The platform to develop strong partnerships at national and international level.
TALSAD takes an important step in harmonising the Turkish aluminium industry to the future
Under the coordination TALSAD, Aluminium Industrialists Association, in partnership with ?DDM?B, Istanbul Ferrous and Non-Ferrous Metal Exporters’ Association and ALUTEAM, Aluminium Testing, Training and Research Centre, within the scope of Istanbul Development Agency’s Innovative Istanbul Financial Support Program for the Year 2021, the project named “Sustainability and Certification Centre for the Compliance of the Istanbul Aluminium Industry with the EU Green Deal Policies” was successfully completed in 2023.
The general aim of the project is to meet the needs of aluminium producers, which is a strategic industry and export sector for our country and Istanbul, in order to comply with the EU Green Deal, circular economy, Carbon Border Adjustment Mechanism, carbon footprint policies and regulations in a timely and effective manner by providing guidance, technical support and certification services on a business basis. One of the main focal points of the project is to adapt the aluminium producer companies to these new obligations, which have become an important element of global competition, with the steps to be taken within this framework. The project also aims to create a structure that will issue the EU Green Deal and circular economy convenience certificates required for aluminium by forming a Sustainability Certification Centre with its own financial cycle, as a part of international accreditation systems.
BEING PART OF RECYCLING WITH OVER HALF A CENTURY OF EXPERIENCE
In commemoration of the Turkish Aluminium Industrialists Association’s 50th anniversary in 2021, TALSAD has actively promoted aluminium recycling through a project competition themed “Be a Part of Recycling.” The aim is to enhance the contribution of aluminium, a fully recyclable material, to the national economy and foster widespread awareness and engagement in aluminium recycling. Following the success of the first competition, the second one took place in 2023. The project competition, supported by the Republic of Türkiye Ministry of Industry and Technology and the Çevko Foundation, awarded the top three projects at the 11th International Aluminium Symposium’s gala event.
TALSAD CONTINUES TO EXPAND ITS PORTFOLIO OF SUCCESSFUL INITIATIVES ON BOTH NATIONAL AND INTERNATIONAL PLATFORMS
The Meeting Point of Eurasian Geography; 12th International Aluminium Symposium Will Be Held On 2025 In Istanbul
The 12th International Aluminium Symposium (ALUS’12), organised every two years by TALSAD, TÜB?TAK (The Scientific and Technological Research Council of Turkey) and METEM (UCTEA Chamber of Metallurgical and Materials Engineers Training Centre), will be held at Istanbul Expo Centre in 2025. Since 2009, the Symposium has joined forces with ALUEXPO, International Aluminium Technology, Machinery and Products Trade Fair, which has been the meeting point of Europe, the Middle East and Eurasia, and has continued to be held simultaneously with the fair since then.
Future Aluminium Forum (FAF’24)
Took Place in Istanbul with Partnership of TALSAD
By bringing together the leading figures of the aluminium industry and offering the opportunity to make connections from a global perspective, the Future Aluminium Forum (FAF’24) was held on May 22-23, 2024, at the Crowne Plaza Florya Hotel in Istanbul, organised by the editors of Aluminium International Today magazine in partnership with TALSAD. The event began with opening speeches by Nadine Bloxsome, editor of Aluminium International Today magazine, and Duygu Saymen, Secretary General of TALSAD. It continued with a presentation titled “Market Update: Overview of the Turkish Aluminium Industry” by Erol Metin, Advisor to the Board of Directors of TALSAD, followed by sessions from other esteemed international participants.
After a day filled with esteemed speakers and presentations, the first day of the conference concluded with the Opening Cocktail Reception hosted by TALSAD. The Opening Cocktail and the conference sessions held over the two days were met with great interest by all participants.
Women’s Power in The Aluminium Industry: Aluminium Awards The Aluminium Awards, a prominent event of this year, is organised in collaboration with Women with Metal and RX Global to honour successful women in the aluminium industry. The award ceremony will take place at The Aluminium Düsseldorf 2024 Fair on October 9, 2024, aiming to highlight diversity and equality within the industry. This significant event features five distinct award categories, with TALSAD Secretary General Ms. Duygu Saymen serving as one of the jury members responsible for selecting the winners.
The jury members are selected from internationally respected institutions within the aluminium industry. These distinguished industry representatives advocate the importance of equality and diversity, supporting the motto “Women can do aluminium, too!”
THE ROLE OF TURKISH ALUMINIUM INDUSTRY IN EUROPEAN ALUMINIUM
In 2023, the Turkish aluminium industry faced significant challenges, marked by contractions in both exports and local consumption. This downturn reflects not only a reduction in Turkey’s export capacity but is also linked to market contractions in key target countries. From January to December 2023, exports decreased by 14,1% compared to the same period in 2022, amounting to 1.19 million tons. Export revenue saw a significant decrease of 20,7%, resulting in $5.3 billion.
Turkey is a significant importer of aluminium raw materials on a global scale. The Turkish aluminium sector relies on imports for 95% of its primary aluminium needs. In 2023, Turkey’s total aluminium imports reached 2.275.871 tons, with primary aluminium making up 74,3% of this total. The value of these imports amounted to $6.3 billion in 2023, reflecting a decrease in US Dollar terms compared to previous years, corresponding to a relative decline in London Metal Exchange (LME) prices. From January to May 2024, Turkey imported 815.000 tons of aluminium, with 71.1% being primary aluminium and a 15.7% decrease from the same period of previous year. Scrap/secondary aluminium imports also decreased by 8.6% to 74.000 tons.
Turkey’s exports of finished and semifinished aluminium products span a vast array of countries worldwide, reaching nearly every nation. Turkey’s largest market is formed by its exports to the EU market. Nearly 64% of Turkey’s exports of finished and semi-finished products are destined for EU countries. This highlights Turkey’s crucial role in the EU’s trade dynamics outside its own member states, showcasing strong bilateral trade relationships and economic interdependence. This noteworthy achievement influenced from the European Union’s decision on anti-dumping measures against China in aluminium extrusion products. The sector’s success stems from its established presence, with continuous growth over fifty years, bolstering production capacity and talent. These developments marked 2023 as a year of re-establishing market share and balancing export markets.
In 2023, Turkey ranks as the 4th largest exporter and the 5th largest importer for the EU in aluminium finished and semi-finished products trade beyond its own region. During this period, the significance of exports to the European Market remained, but Turkey’s exports to these countries decreased by 15% compared to the same period of the previous year.
In the first quarter of 2024, Turkey ranked 14th globally in the total export of all aluminium products and 13th in imports. The top five export destinations are developed economies in January – May 2024. An analysis of the export distribution over the past decade reveals that Turkey’s aluminium sector is progressively expanding its reach to a broader geographic area.
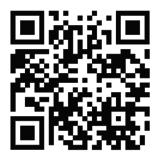
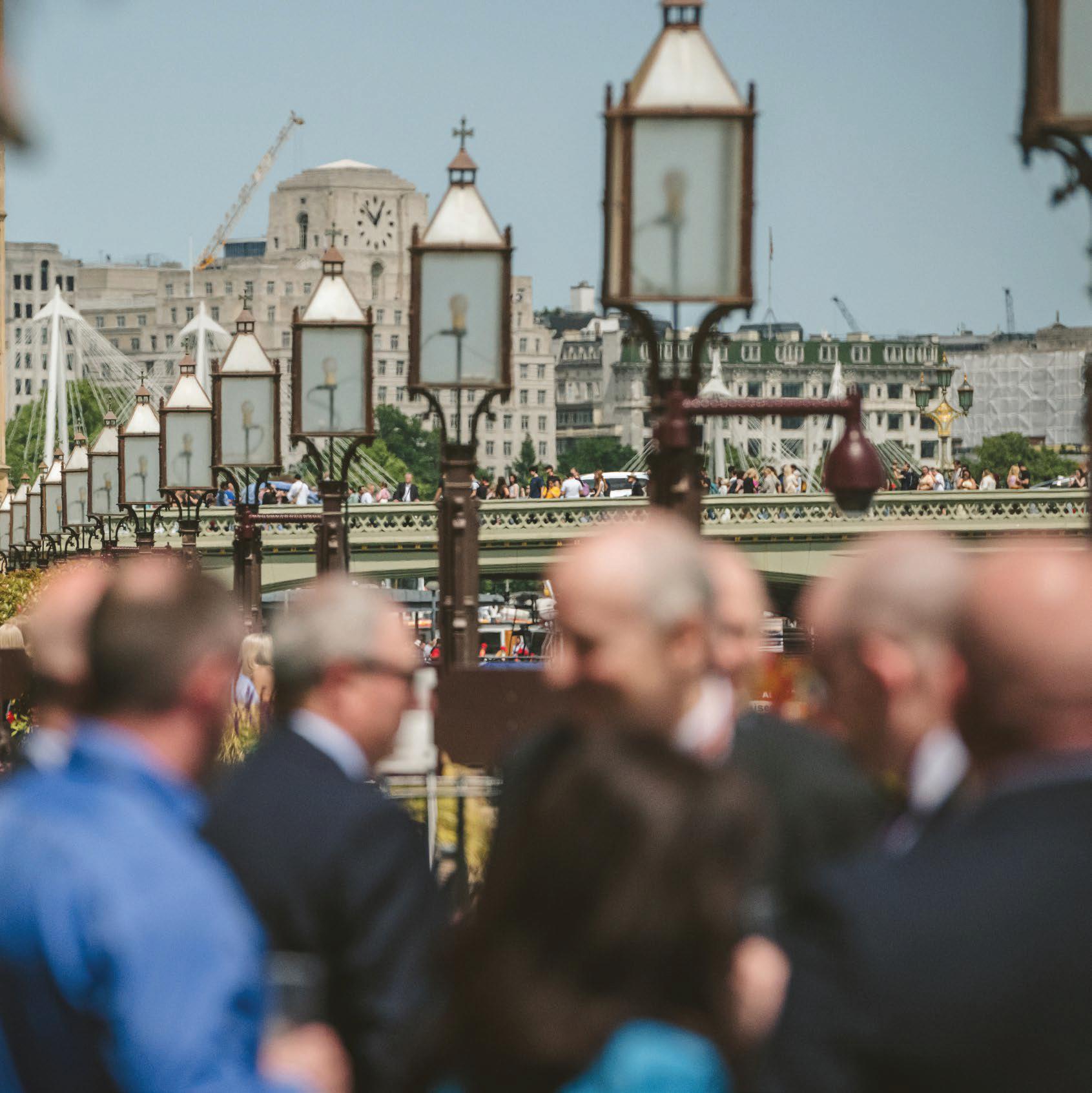
in Review for
UK Aluminium Federation (ALFED)
With more than 170 members across the entire UK aluminium supply chain, the Aluminium Federation (ALFED) represents businesses who process, trade, and work with aluminium. We foster innovation, promote best practice, develop skills, and champion member interests. As the voice of the UK industry, our mission is to expand the market for aluminium products by helping members solve problems, lobby government and boost their competitiveness. Whether it’s providing technical support, delivering market insight, informing trade policy or offering
networking opportunities – everything we do focuses on helping UK aluminium capitalise on opportunities.
Why Aluminium?
Aluminium is an affordable, highly recyclable material that supports a global circular economy. It is valued for it being so lightweight; its one-third of the density of steel, making it ideal for applications where weight reduction is crucial. Despite its lightness, aluminium also offers excellent strength and durability, and is corrosion resistant as it naturally forms a protective
oxide layer, making it resistant to corrosion. Aluminium is also an excellent conductor of heat and electricity, and is 100% recyclable without losing its properties, making it environmentally friendly; around 75% of aluminium ever produced is still in use today.
How are we helping to promote aluminium’s role as a critical material for a sustainable future?
This year, with the formation of the new Government, it’s more important than ever to showcase how aluminium is a key contributor to the UK economy. For instance,
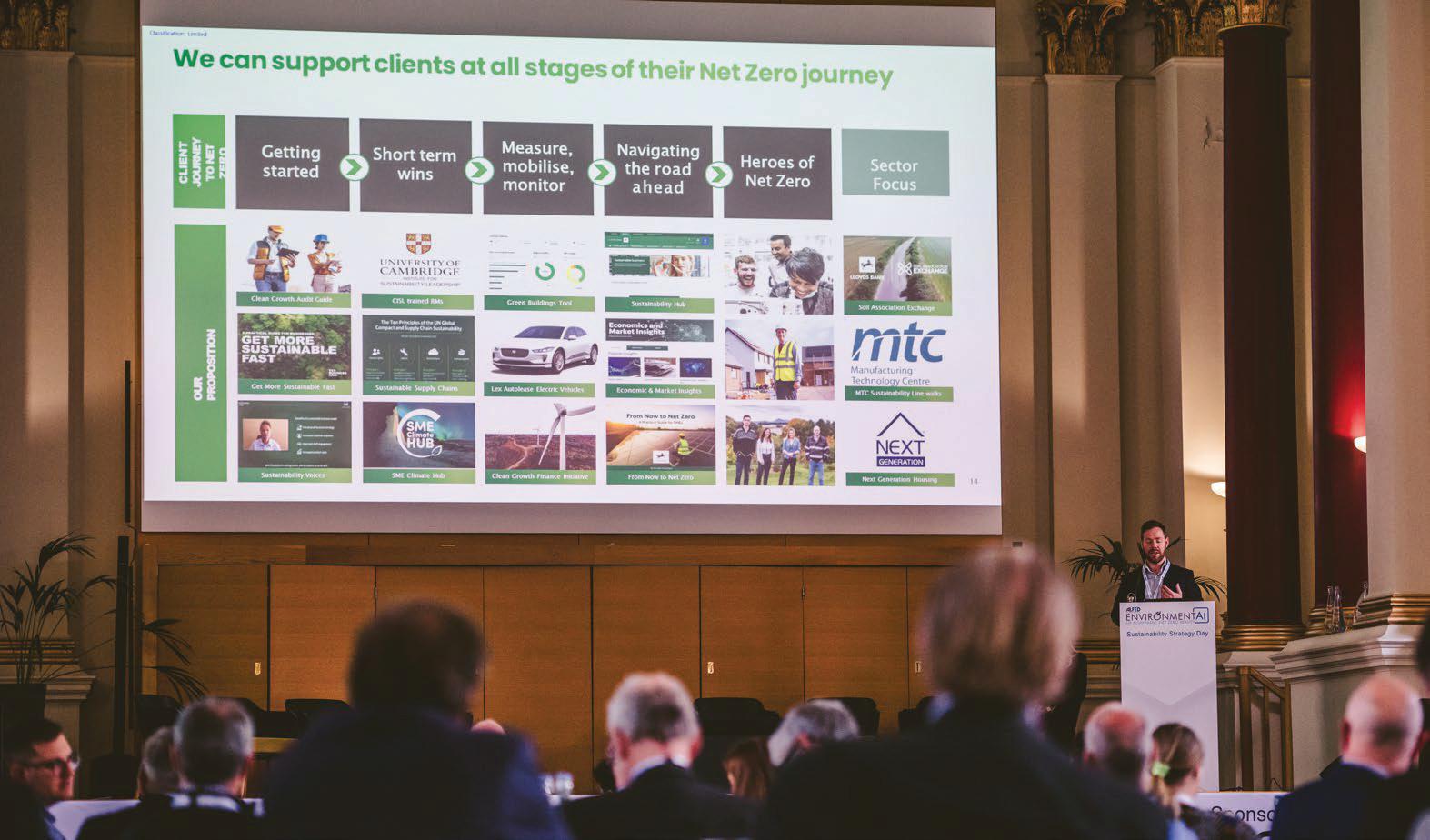
in a 2024 report we recently worked on with the Fraser of Allander Institute to provide an updated analysis of the UK aluminium industry, it was concluded that the aluminium industry has now surpassed precovid levels, directly contributing £1.5 billion to the country’s economy. As the voice of the UK industry, ALFED remains committed to working with sector and government representatives to champion for a long-term industrial strategy, and this mission has been proposed in the launch of our UK aluminium manifesto, showcased for the first time at our Annual House of Lords Lunch, which this year focussed on the theme of implementing a comprehensive industrial strategy for the UK aluminium sector.
The manifesto focuses on doubling down on policies for net zero, safeguarding energy security, and developing a clear industrial strategy to support sustainable aluminium production. Commenting on the launch of the UK Aluminium Manifesto, ALFED’s Nadine Bloxsome stated: “The aluminium industry plays a pivotal role in driving economic growth and innovation in the UK. The launch of the UK Aluminium Manifesto reaffirms our commitment to advocating for policies that support the growth and sustainability of the aluminium sector. By working together with policymakers and industry stakeholders, we can unlock the full potential of aluminium to drive economic prosperity and address the challenges of climate change.”
A lot of the points outlined in the UK Aluminium Manifesto were echoed in King Charles’ III’s recent speech in the House of Lords. Within His Majesty’s address, he highlighted not only that securing economic growth will be a key mission for the new Government, but also the plans for the establishment of an Industrial Strategy Council, pursuing sustainable growth by encouraging investment in industry, skills, and new technologies, and finally the commitment to a clean energy transition. Pinpointing the aluminium sectors role in these aims, the industry is not only a key contributor to the clean energy transition, but due to it’s recyclable and environmentally friendly nature, and being the ‘strategic metal’ of the future, it can also contribute to the pursuit of sustainable growth.
Looking Ahead to the ALUMINIUM Show 2024!
The ALUMINIUM Show is the world’s leading trade show and B2B platform for the aluminium industry and its main application industries – the show focuses on solutions for automotive, mechanical engineering, building and construction, aerospace, electronics, packaging and transportation.
As the industry’s most important platform, ALUMINIUM brings together producers, processors, end consumers and technology suppliers along the entire value chain from more than 100 countries.
ALFED Chief Executive Officer, Nadine Bloxsome will be in attendance at the show in Dusseldorf from the 8th-10th October 2024! Keep an eye out for her on the judging panel for the inaugural Women with Metal – The ALUMINIUM Awards; the award ceremony looking to celebrate the achievements of those recognised as being among the strongest, most influential women in the aluminium industry.

VISIT US AT ALUMINIUM 2024
Meet our Coil Coating Specialists Jakob Søndergaard and Ronnie Skov at Aluminium 2024 in Düsseldorf October 8 –10. You’ll find them in Hall 4, Stand 4F40.
Metalcolour proudly presents products from its Technical Coating area. Metalcolour Technical Coating is a highly specialized division offering customized solutions in coil coating of numerous metal substrates with own developed or customer specified primers, binders and coating. The solutions developed typically have
several purposes in a combination of technical requirements and high volume production. Main part of our clients utilizes Metalcolour to industrialize processes in order to take advantage of economies of scale in decreasing cost per unit. Great savings has been generated by solutions from Metalcolour Technical Coating.
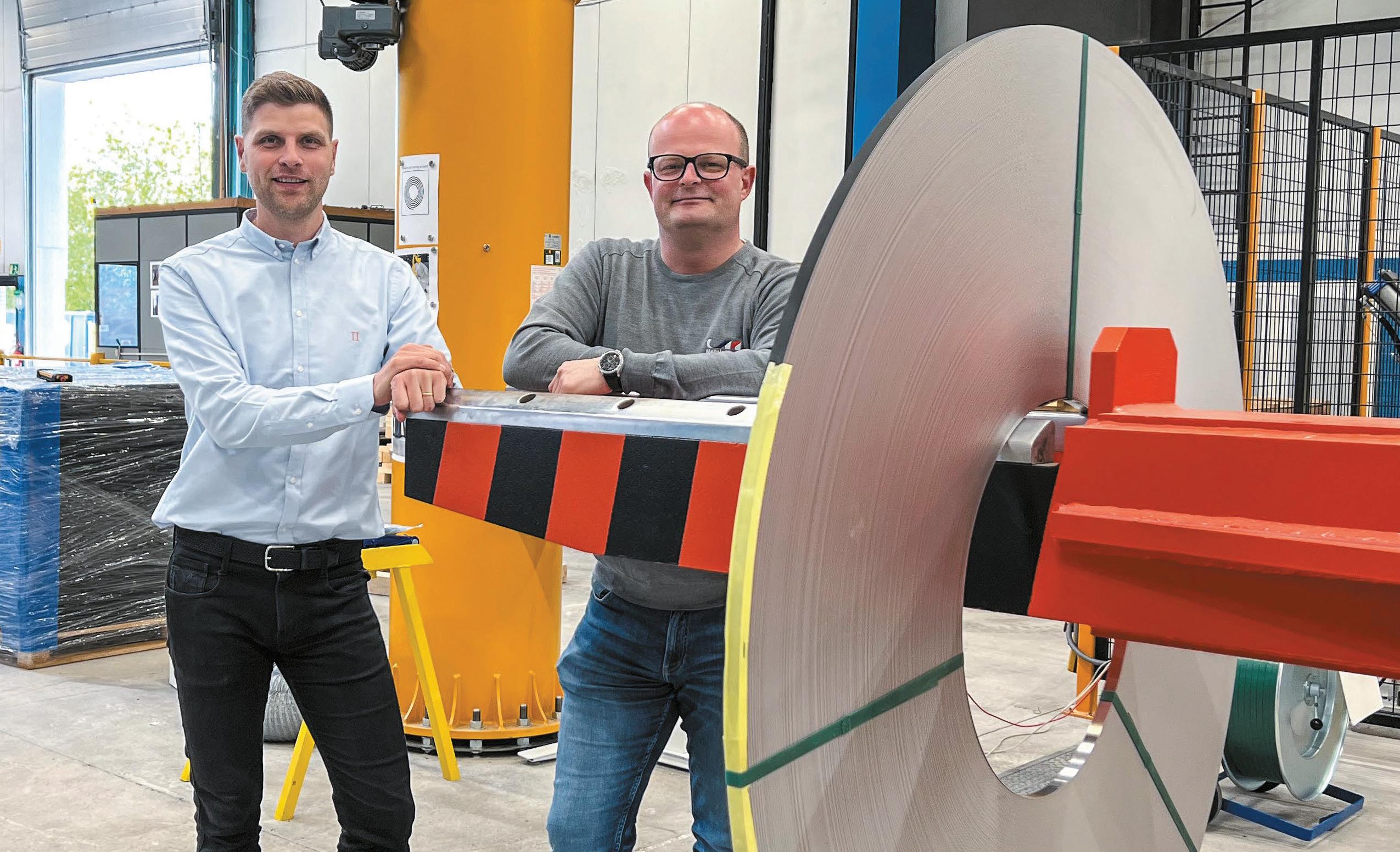
Do
a personal meeting? Scan
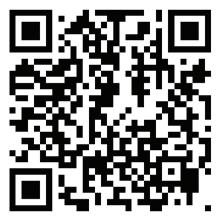
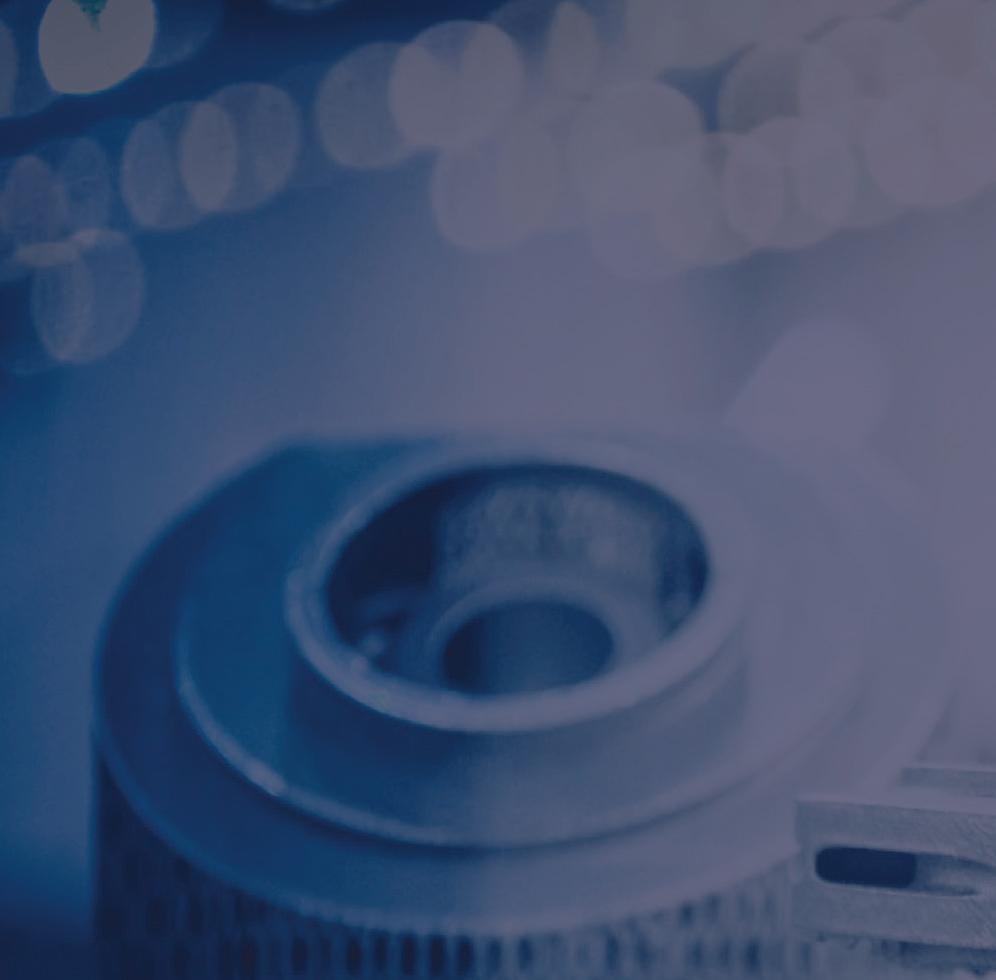
Casting vs. Additive Manufacturing with Aluminum
By Dr. Markus Seibold, CEO & Co-Founder of MakerVerse
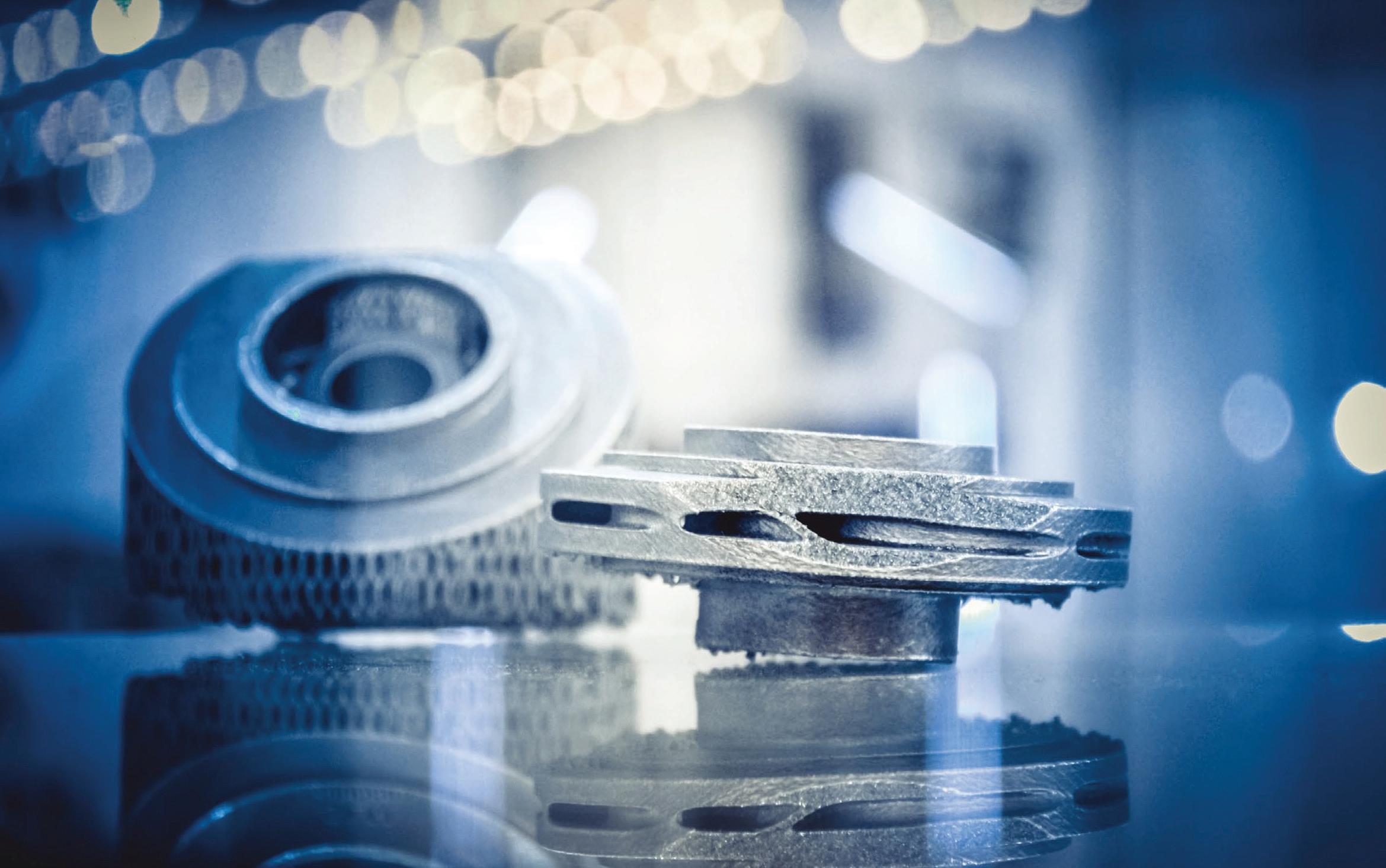

Additive manufacturing with aluminum has improved so much that it is now a superior method to casting in many cases.
I admit I might seem a little biased. For close to a decade, I led the Additive Manufacturing team at Siemens Energy. I pushed to adopt 3D printing and sought new applications. As the technology improved, finding valid applications became easier.
While I’m passionate about additive manufacturing, it’s not my personal bias that convinces me of the benefits. It’s the quantifiable research done on manufacturing with aluminum.
High Performance
According to a 2021 study, additive manufactured parts made from AlSi10Mg achieve better density, corrosion resistance, and fatigue resistance than their cast counterparts. [1]
Moreover, the study highlights AM’s unparalleled design flexibility and efficiency. Unlike casting, which requires extensive tooling and molds, AM allows for creating complex geometries and intricate internal features directly from digital designs.
Finer Microstructures
A 2019 study in the same journal offers further proof.[2]
Researchers found the AlSi10Mg alloy produced through Laser Powder Bed Fusion (also known as Selective Laser Melting/SLM) exhibits superior mechanical properties to its cast counterpart. The findings show that the additive manufacturing process produces significantly higher tensile strength, yield strength, and hardness.
This is attributed to the rapid cooling rates and finer microstructures,
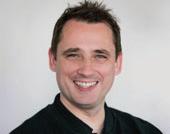
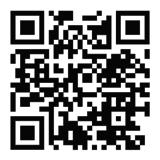
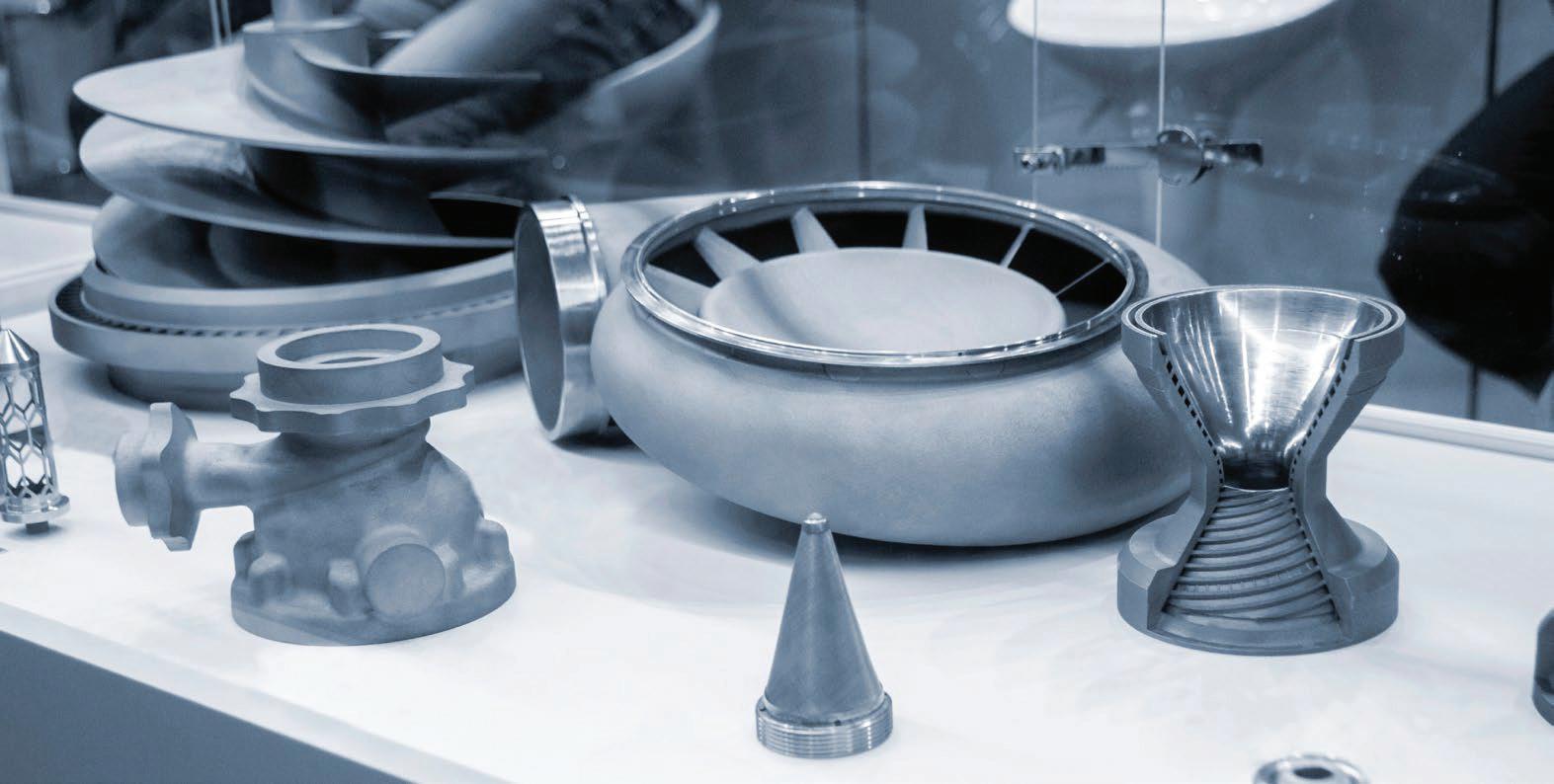
which enhance the alloy’s mechanical performance. In contrast, traditional casting methods often result in coarser microstructures and higher porosity, adversely affecting the material’s strength and durability.
Rigorous Testing
A 2021 study took an extremely detailed look at AlSi10Mg[DK1][DK2] components made with additive manufacturing and casting. [3] Using a robot-assisted technical system and 360 different experiments, researchers found that the AM parts showed a:
○ 10 percent higher yield strength on average
○ A 20 percent higher ultimate tensile strength
management, and fulfillment, MakerVerse helps with everything from initial prototypes to full-scale production.
Full Range of Manufacturing Methods
As additive manufacturing technology evolves, its adoption for high-performance aluminum components will increase.
However, “traditional” manufacturing methods such as casting will always be essential for specific applications. While tooling requires heavy upfront costs, cost per part in many high-volume serial production cases is lower. For exceptionally large parts, cost can be advantageous even for lower quantities.
Some manufacturing methods, such as rapid casting, combine additive manufacturing with traditional casting. With this emerging technology, a mold is 3D printed – typically out of sand. The mold is then used for one-off parts out of aluminum or other metals.
All this shows the importance of having access to and insights into the full range of manufacturing methods. Every job needs the right tool, and each technology’s purpose depends on the application.
References:
[1] Brock, Lisa & Ogunsanya, Ibrahim & Asgari, Hamed & Patel, Sagar & Vlasea, Mihaela. (2021). Relative Performance of Additively Manufactured and Cast Aluminum Alloys. Journal of Materials Engineering and Performance. 30. 10.1007/s11665-020-05403-7.
[2] Song, Bo & Yan, Qian & Shi, Yusheng. (2019). Comparative study of performance comparison of AlSi10Mg alloy prepared by selective laser melting and casting. Journal of Materials Science & Technology. 41. 10.1016/j.jmst.2019.08.049.
[3] Christian C. Roth, Thomas TancogneDejean, Dirk Mohr, Plasticity and fracture of cast and SLM AlSi10Mg: High-throughput testing and modeling (2021) Additive Manufacturing, Volume 43, 2021,101998, ISSN 2214-8604, https://doi.org/10.1016/j. addma.2021.101998.
sounds wrong to me from a grammar perspective[DK1] I guess the word look is missing[DK2R1]
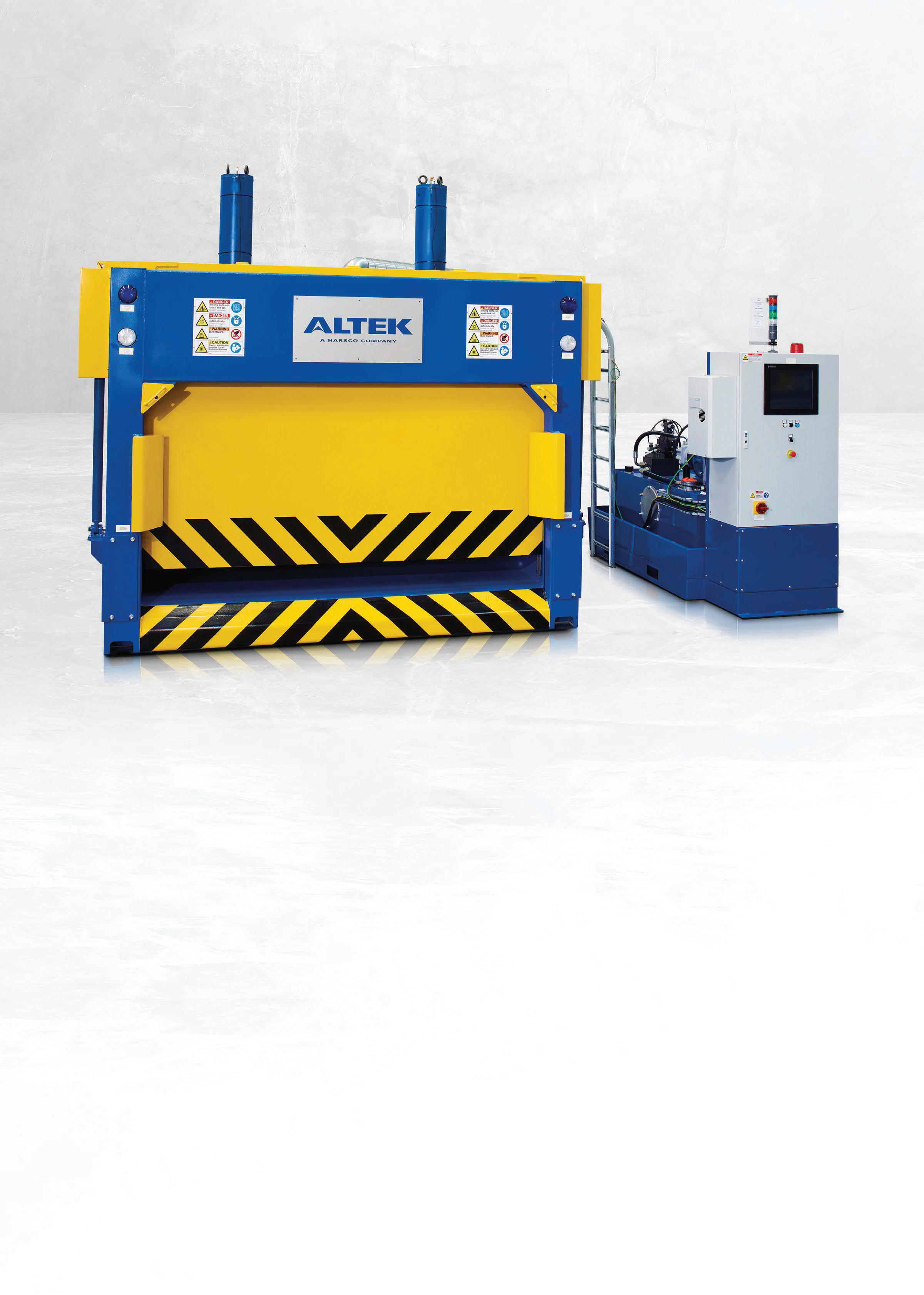
Industry-leading dross press technology
Maximising metal recovery from your dross
The Altek Tardis Gen III is the most advanced dross press in the market, utilising several key features to enhance in-house drain and ensure excellent secondary recovery benefits for the highest aluminium recovery potential from dross.
• 10x dross press model sizes
• Quick pressing cycles –typically 6 minutes
• 60+ dross pan designs: 50kg to 2,500kg capacity
• Clean working environment
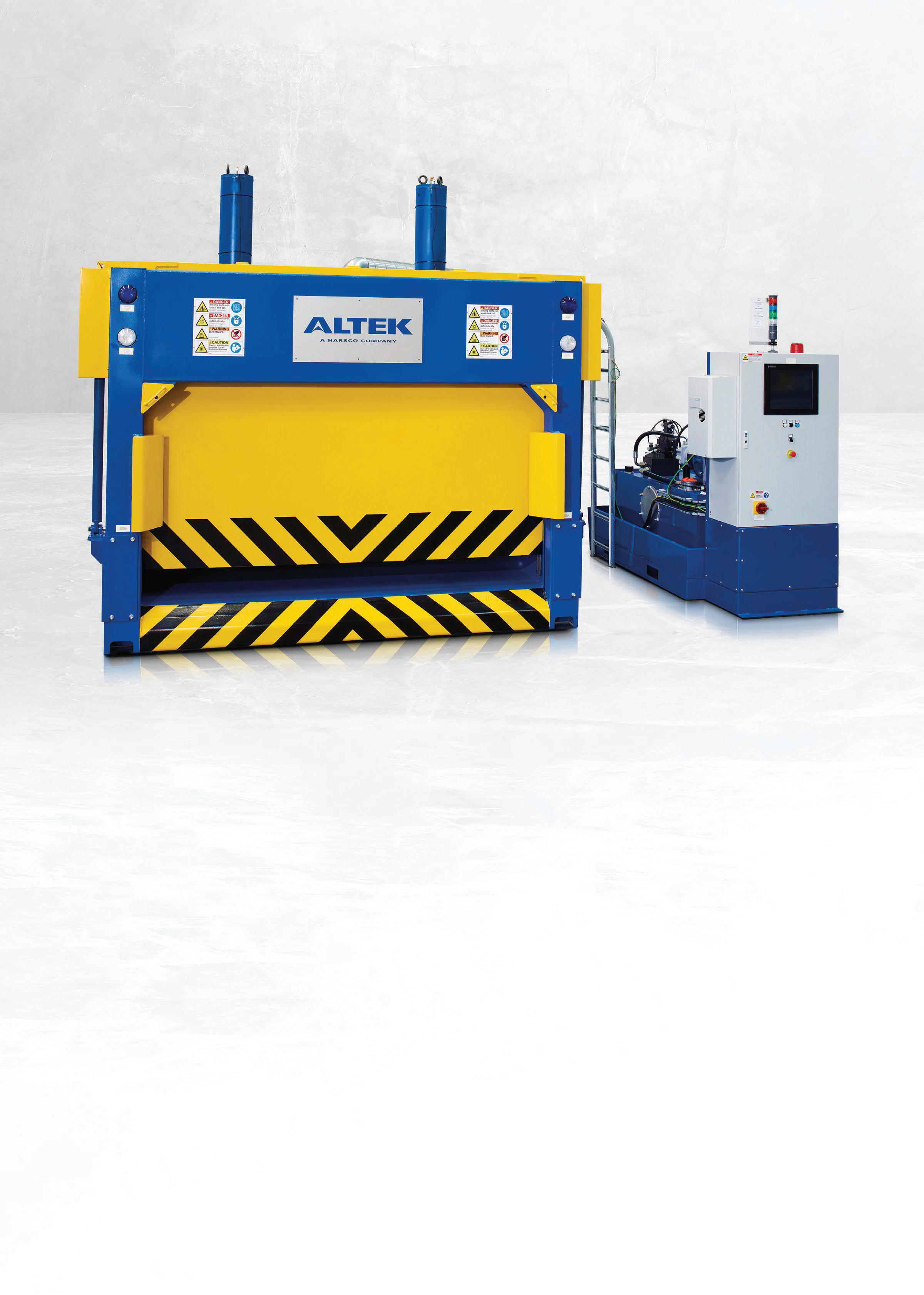
• 5% - 25% in-house drain
• Flexible, reliable and robust
• 40% - 70% secondary recovery
• Low operation and maintenance costs
EPIQ: From today to tomorrow
By Isabelle Gaudreau, Marketing and Communication Coordinator
Barely three years after the merger of Advance Dynamics and Mecfor, we can say that the face of EPIQ Machinery has already changed a lot. The company, anchored in its present with a sharp eye on its future, is seeing great transformation opportunities within the primary metals industry, including aluminium production.
In 2021, thanks to its expanded range of equipment solutions, the company has positioned itself as a supplier of choice. Now able to offer complete handling solutions, both fixed and mobile, integrating smart technologies, it pushes the innovative character and stands out among heavy machinery manufacturers.
Join forces. Consolidate. Move forward.
In recent years, EPIQ Machinery has increased its strategic alliances and partnerships. Under the precept that together, we go further, it demonstrates its vision that with truthful collaborations built on lasting relationships of trust, it is possible to increase each person’s potential tenfold. This is how a US-based material handling equipment supplier became the factoryauthorised distributor of MECFOR mobile equipment, products, and parts, for the entire US market. With Taylor Northeast (February 2022), customers get the local support they need. Then, the company entered into a partnership with a Quebec equipment manufacturer (August 2022).
In fact, Dynamic Concept and EPIQ Machinery joined forces to co-create a robot intended for maintenance operations in foundry furnaces for primary and secondary aluminium producers: the ARTF. This equipment represents a further step towards robotisation executing high-risk
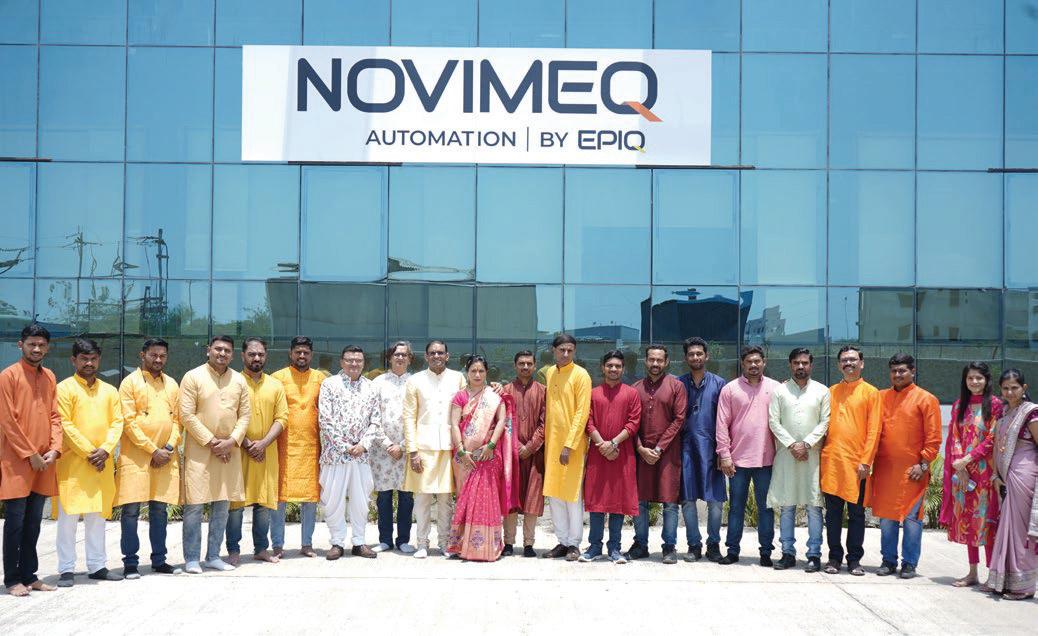
tasks by integrating automation, vision and auto guided vehicle technologies. With its innovative concept, the ARTF - Automated Furnace Tending Robot - is a major step to Industry 4.0.
Still in this spirit of innovation and automation, another partnership has emerged. This time with the Spanish company DTA The Smart move (September 2022). Under the EPIQ DTA brand, it is now able to offer a wide choice of electrical auto guided vehicles (AGV) on the global Aluminium market. The objective of this partnership is to make AGV/AMR technology accessible and in line with the specific needs of harsh and difficult operating environments.
In the aluminium industry, many heavy load travels are carried out between different sectors (molten metal ladles, anodes, billets, ingots, etc.). Each requiring a rigorous analysis of inputs to guarantee
safe movement in all conditions, indoors and outdoors, in all seasons. EPIQ Machinery thus acts as an integrator of solutions and provides after-sales technical support.
Check. Validate. Design.
Being EPIQ means being determined to develop innovative solutions that will bring greater operational efficiency and better financial performance to ensure the sustainability of our industrial ecosystem, for all our business partners.
To better meet these imperatives, in September 2023, the company acquired STYMER, a team of dedicated experts specialised in design engineering, finite element analysis (FEA) and computational fluid dynamics (CFD). This group offers cutting-edge support in engineering, product development and analysis.
In today’s competitive environment, efficient Engineering Design & Detailing is
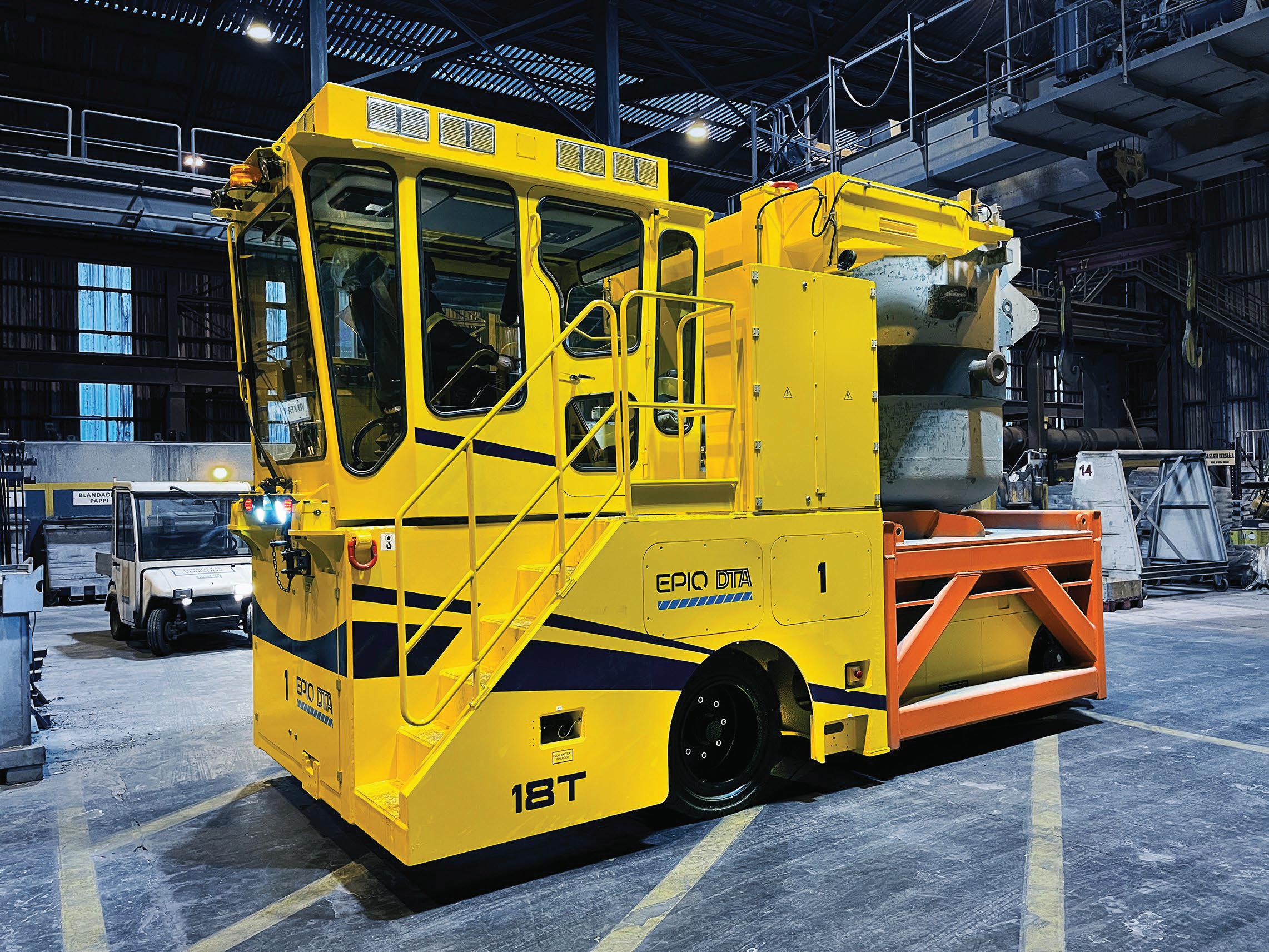
the cornerstone of success. STYMER helps converting innovative concepts into tangible results. The team transforms ideas into cutting-edge products.
Innovate. Achieve. Automate. Robotisation, automation and digitalisation will form the main axes of development. This trend will lead Aluminium smelters to meet the requirements of optimised production in an environment with access to fewer human resources and an omnipresent focus on decarbonisation.
Since its beginnings, EPIQ has embraced the principles of automation. Whether by adding robots to AD handling equipment systems or by integrating the MecforLink system on mobile equipment, EPIQ significantly increases the value of its solutions.
However, the future demands more. This is why EPIQ is positioning itself to offer data capture and advanced information management tools directly linked to the needs of each plant in order to be able to rely on artificial intelligence (AI) and increase its efficiency. From now on, the solution offered, without close technical support and in-depth field experience, is no longer sufficient.
Faced with this observation, EPIQ has created a new division specialised in the offer of automation services of all kinds. The NOVIMEQ Automation team (June 2024) is able of meeting the needs of design, programming, simulation, technical support on site, training and document management. The combination of these capabilities allows to provide complete industrial automation and digitalisation solutions, ensuring that control systems and processes reach new heights in terms of growth, reliability, sustainability, efficiency, quality and safety.
Transform. Reinvent. Build.
An electrification program of mobile solutions combined with the offer of autonomous vehicles (AGV) is a major step towards the decarbonisation needs of Aluminium plants. It also opens the door to greater automation of processes.
At the start of another industrial revolution oriented towards big data analysis and the integration of AI, EPIQ Machinery sees great opportunities for reshaping the Aluminium industry.
Ultimately, EPIQ wants to be a leading player in enabling Aluminium production plants, both primary and secondary, to move from pulled production to pushed production. With an increase in information available, in real-time, and specialised software capable of using this information to communicate production orders to the various handling solutions, together we will be able to reinvent the industry.
In short, the company, as a vector of change, pursues its ambition to design and manufacture equipment that will allow its customers to do what they have always done, but better, by providing them with tools for faster and more efficient decision-making. All this is EPIQ.
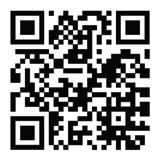
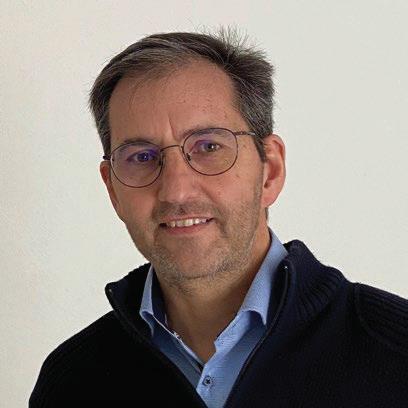
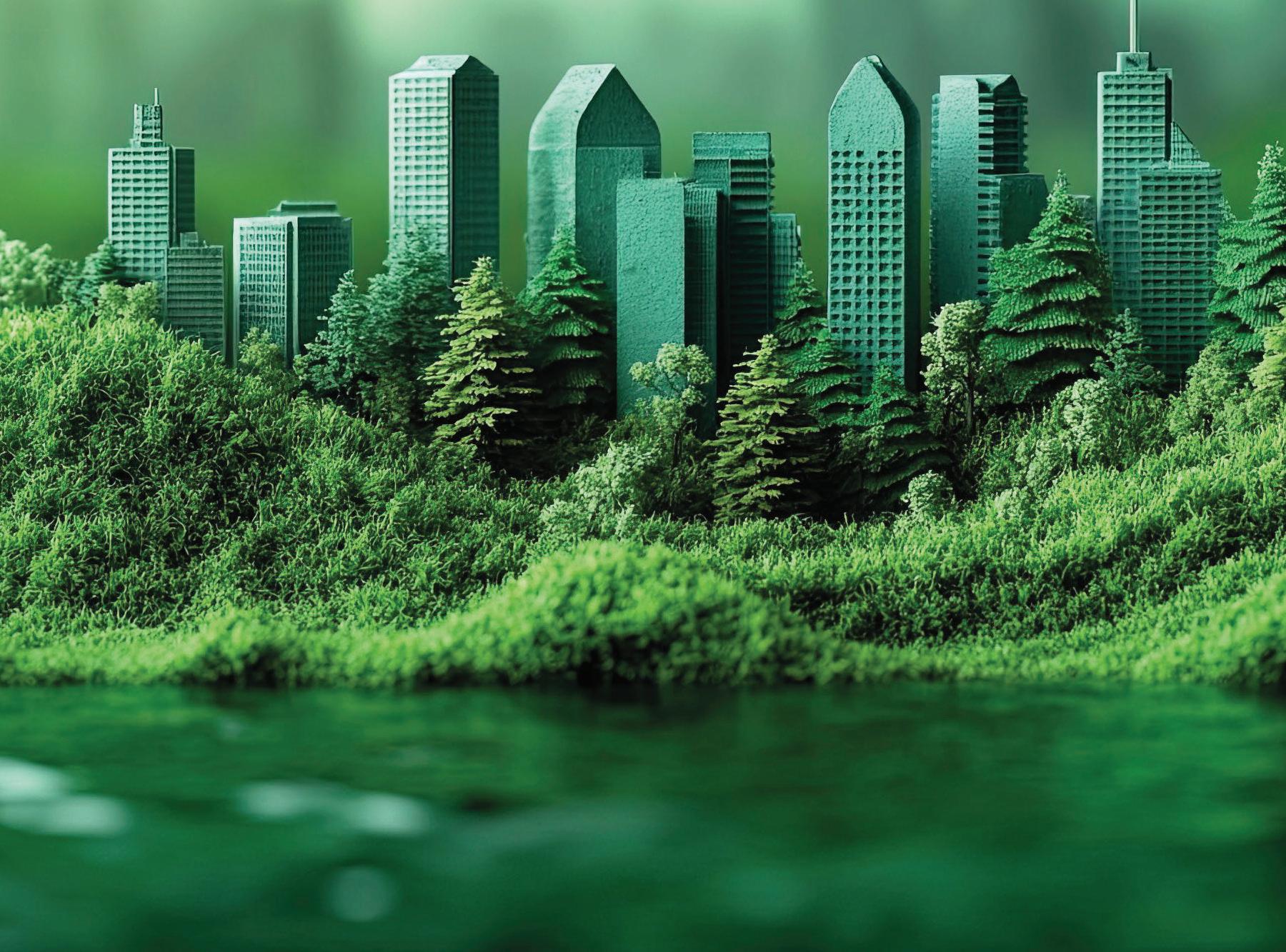
By Jerome Lucaes, CEO and Founder, Fast Forward Zero

What Needs to Change to Scale Up Decarbonisation in the Aluminium Sector?
Decarbonising the aluminium sector requires significant changes in several areas. Decarbonising electricity for smelting operations, transitioning to biofuels and hydrogen for thermal energy in alumina production, and scaling up new technologies like carbon capture, inert anodes, and carbo-chlorination will demand investments amounting to hundreds of billions of dollars globally.
Currently, the combination of mandatory carbon pricing and voluntary price differentials for low-carbon aluminium is insufficient to drive substantial investment towards achieving carbon neutrality. Despite this, we are seeing numerous net-zero plans, partnerships, emerging technologies, and pilot projects.
For example, Vedanta Aluminium has entered into long-term power delivery agreements to source over 1,335 MW of renewable energy, enough to produce 900 kt of green aluminium by 2030. ELYSIS is expected to begin the first demonstration of its inert anode 450kA cell in 2024.
Additionally, the International Aluminium Institute (IAI) has committed to transparently and publicly track the greenhouse gas reduction progress of all its member companies on an annual basis. Remarkably, for the first time in history, global greenhouse gas emissions from the aluminium sector declined in 2022, dropping from 1.13 gigatonnes CO2e to 1.11 gigatonnes CO2e, while aluminium production increased by 3.9% to 108.2 million tonnes. The greenhouse gas emissions intensity of primary aluminium production has been decreasing since 2019, with a 4.4% reduction in intensity observed in 2022, from 15.8 tonnes CO2e per tonne to 15.1 tonnes CO2e per tonne.
These achievements are commendable, and the aluminium industry is arguably ahead of any other hardto-abate sector. However, the impact achieved so far is too small, and the pace of action is far too slow to meet the decarbonisation trajectory required to align with the objectives of the Paris Agreement.
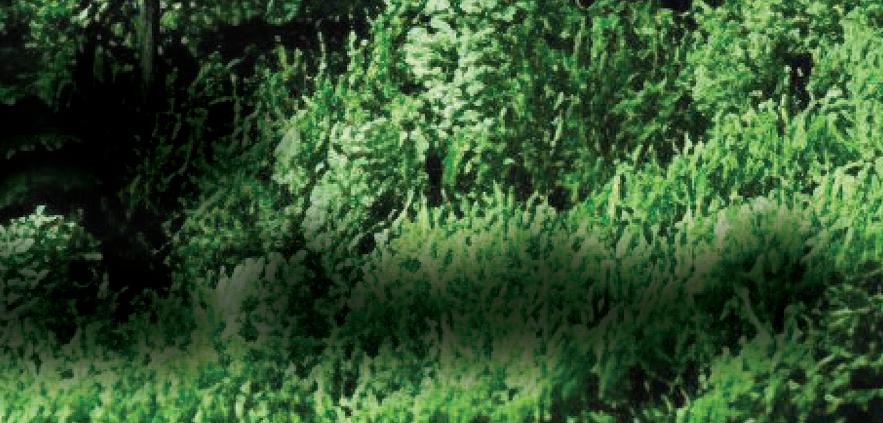
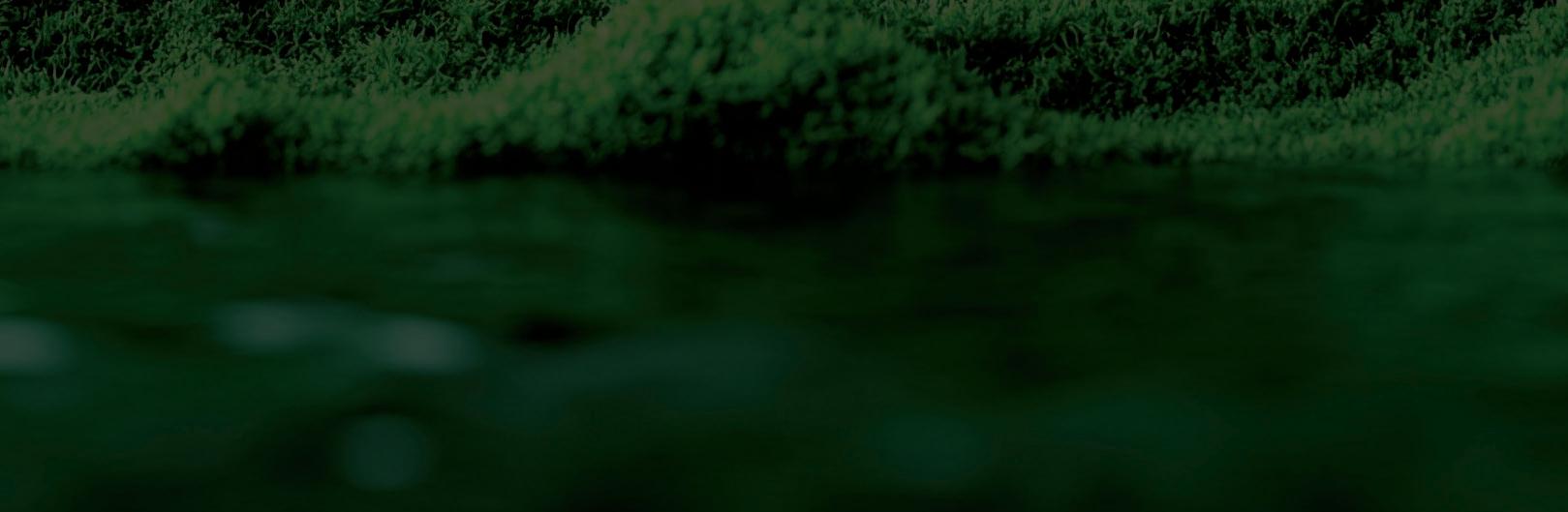
Most projects are either located in regions where carbon is taxed or where governments provide financial support. The current pricing differentials in the aluminium sector range between $30 to $50 per tonne of aluminium, which is less than 2% of the global price of aluminium. These premiums are nowhere near the level required to justify decarbonisation efforts without public financing. Furthermore, many end-use customers, such as automotive OEMs or beer companies, argue that they lack access to reliable data on the actual carbon footprint embedded in their products due to multiple transformation steps and complex value chains.
So, what needs to change to create the conditions for companies to make final investment decisions with real decarbonisation impact? If you’re interested in exploring this topic further, join me, Jerome Lucaes, at the Aluminium Expo in Düsseldorf on Tuesday, October 8th. I will be delivering a keynote speech at the Sustainability and Recycling Corner.
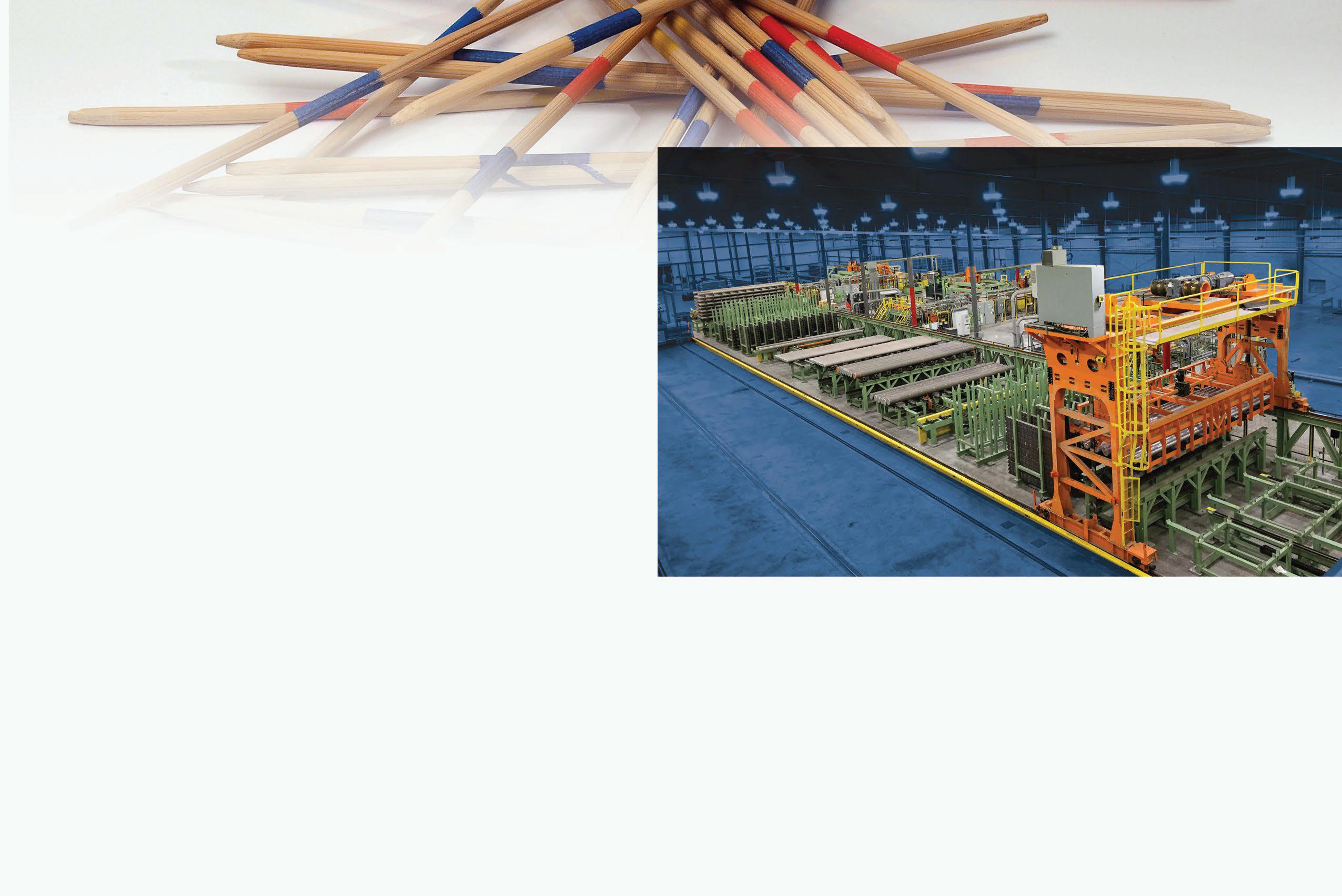
For an organized billet handling, trust branded EPIQ AD’s Billet batch homogenizing system that offers:
A touchless aluminium billets gantry system.
A fully automated homogenizing sequence on to sawing and batching operations.
Only linear motions for increased reliability and better positioning.
Engineering, Manufacturing and Commissioning
GLAMA Maschinenbau GmbH, founded in 1961, sells its know-how in engineering, manufacturing and commissioning of machines and equipment for customers of Steel Forging and Aluminium Industry on all continents of the world.
We deliver machines with a unique combination of advanced control, big data, artificial intelligence and rugged, reliable construction. GLAMA equipment withstands the heat, dust, vibration and battering of heavy industry, while delivering precise handling performance with lifetime expectations over 20 years.
A qualified and experienced team of German engineers work on optimised products on customers’ requirements to simplify operation methods at remarkable low operational cost. As a result, we are a loyal partner to a customer base of over 2000 machines at appr. 160 different customers.
Following equipment belongs to GLAMA’s product range:
Aluminium Industry:
○ Furnace Charging Machines
○ Furnace Tending Machines (Skimming/ Cleaning)
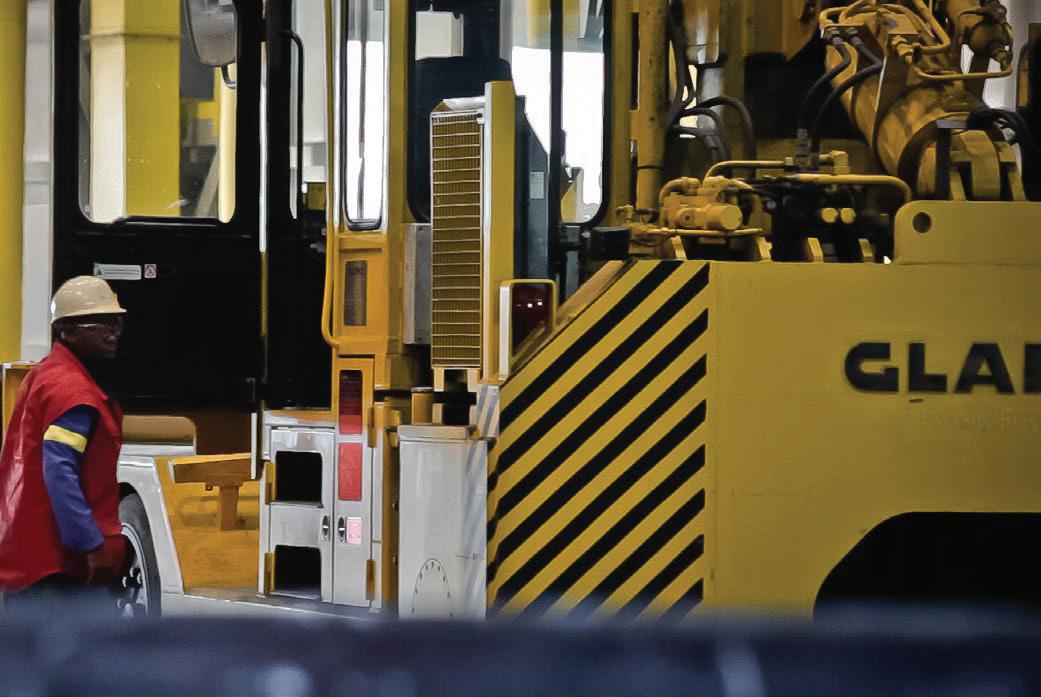
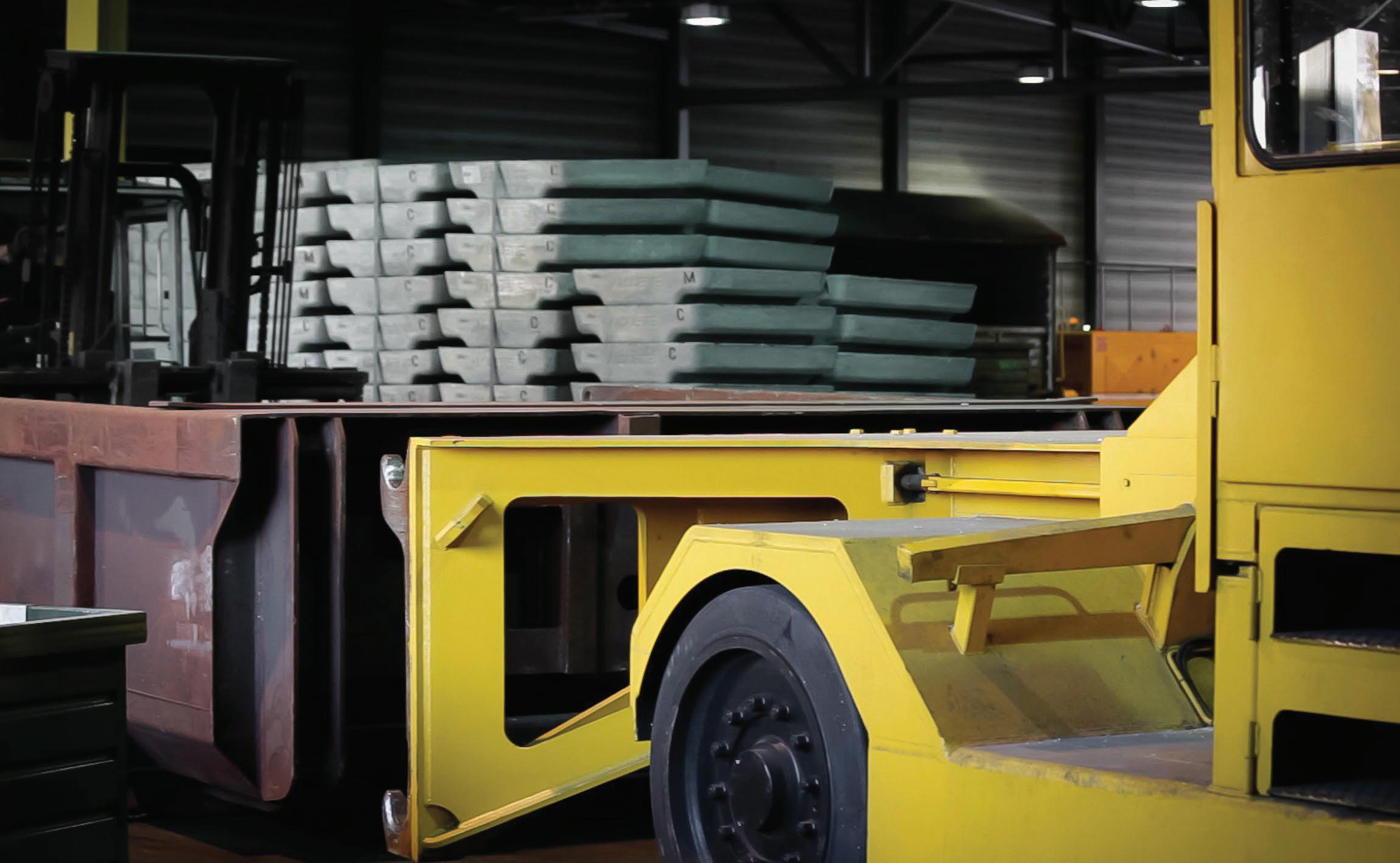
○ Ladle Charging Trucks
○ Anode Changing Vehicles
○ Hammer Crustbreakers
○ Tapping Trucks
○ Anode Pallet Transporters
○ Butt Cleaning Machines
○ Coil Lift Trucks
○ Molten Metal Carriers
Steel Forging Technology (Open Die, Closed
Die and Rolling):
○ Railbound Forging Manipulators
○ Mobile Forging Manipulators
○ Tool Manipulators
○ Ingot Cars with Turntable
○ Pop-Up Turntables
○ Tool Magazines
○ Charging Manipulators
○ Tong Charging Machines
○ Robots for manipulating, transporting, open-die forging and roll changing
Steel Smelting Industry:
○ Furnace Charging Machines
○ Ladle Tilters
○ Deslagging Machines
○ Plug Insert Machines
○ Tap Hole Repair Machines
#GLAMA - always the better solution
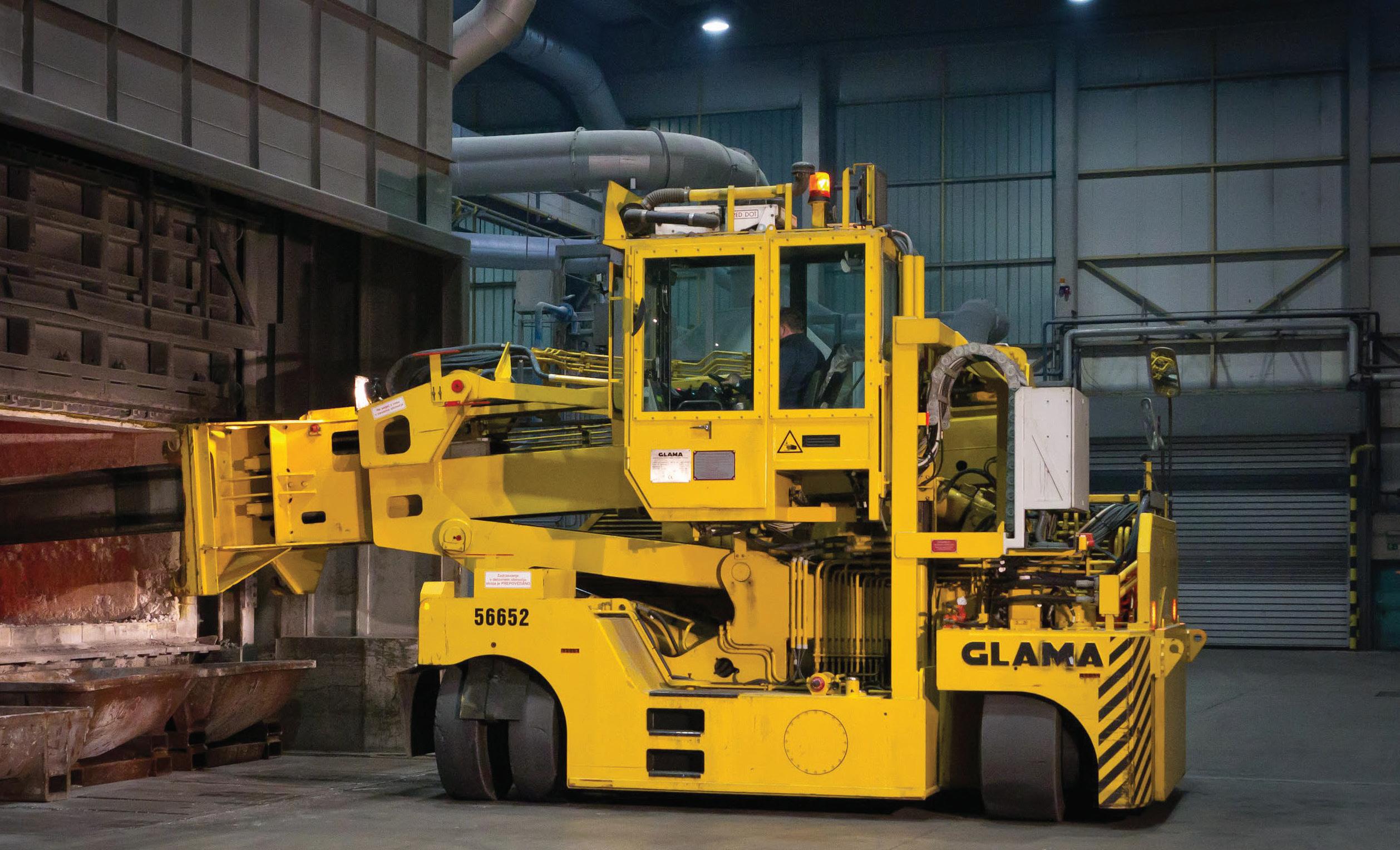
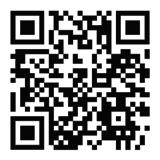
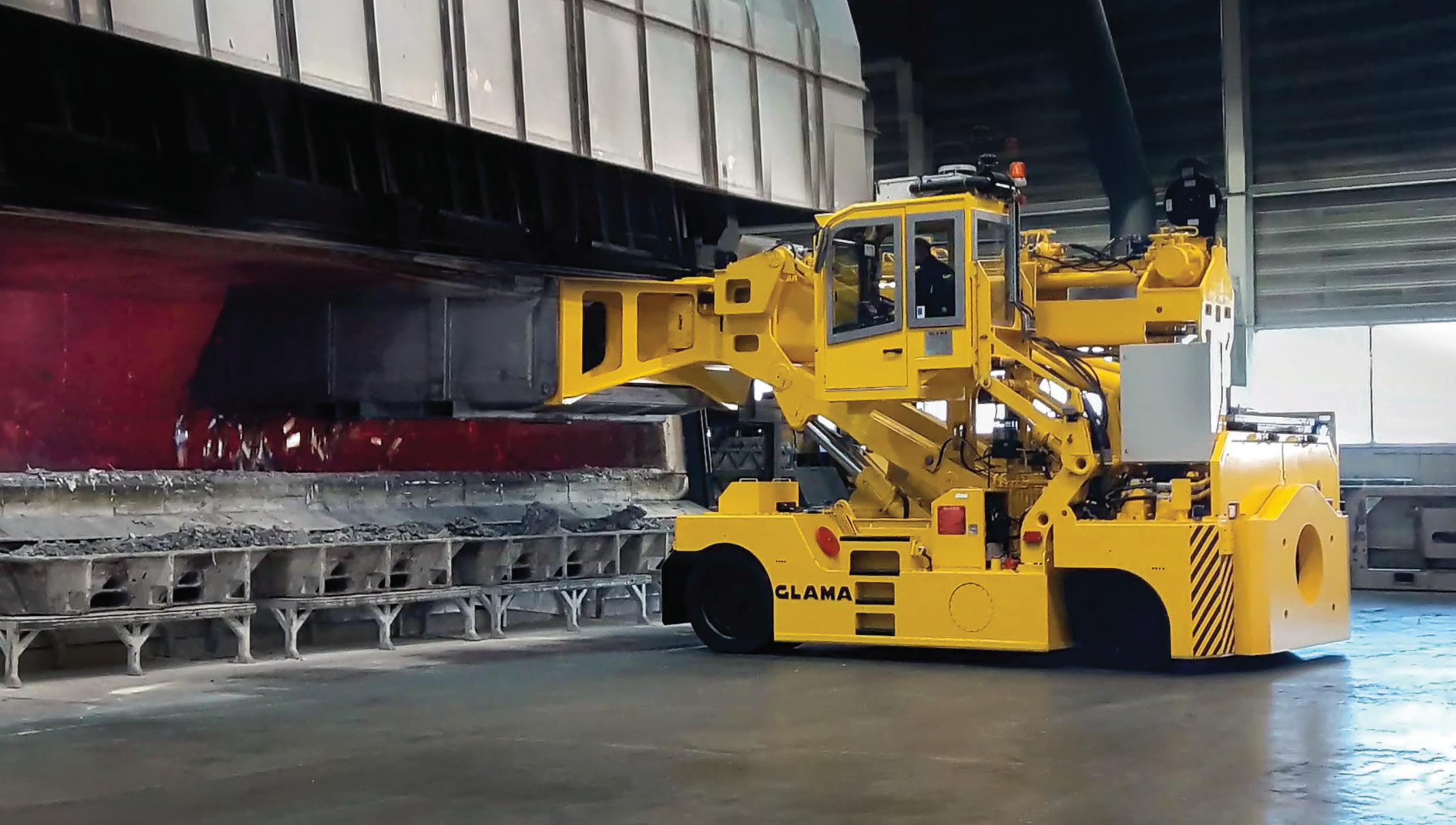
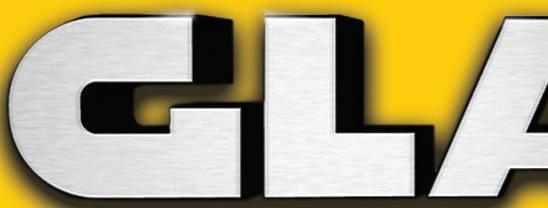




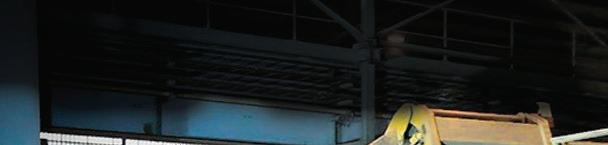
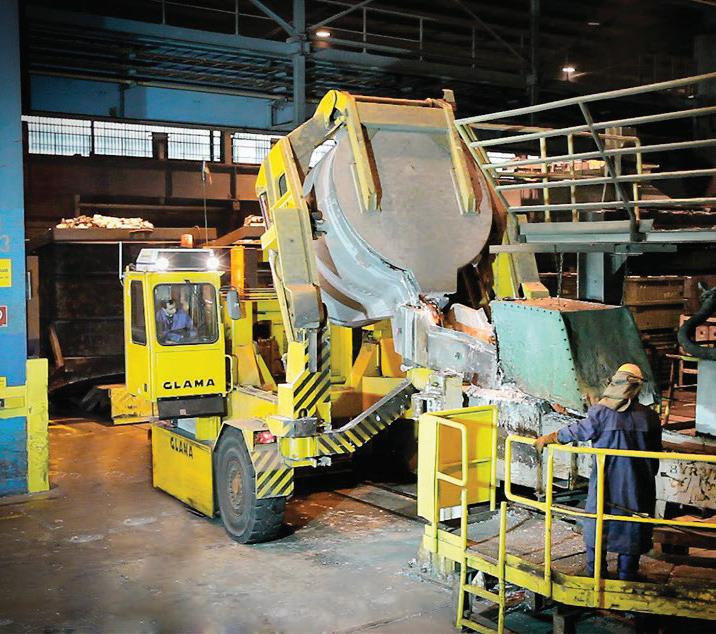
Costeffectiveheavyduty mobileequipment foraluminiumindustries...
GLAMAMaschinenbauGmbH
Headquarters: Hornstraße19
D-45964Gladbeck/Germany
Fon:+49(0)204397380
Fax:+49(0)2043973850
email:info@glama.de
GLAMAUSAInc.
60HelwigSt.,Berea,Ohio44017
Fon:+18774526266
Email:sales@glama-us.com


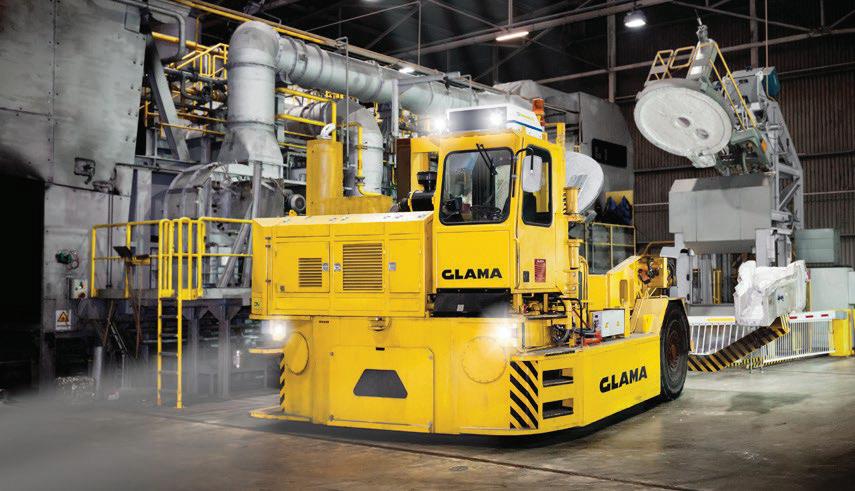
Driving Innovation and
Efficiency
in Manufacturing
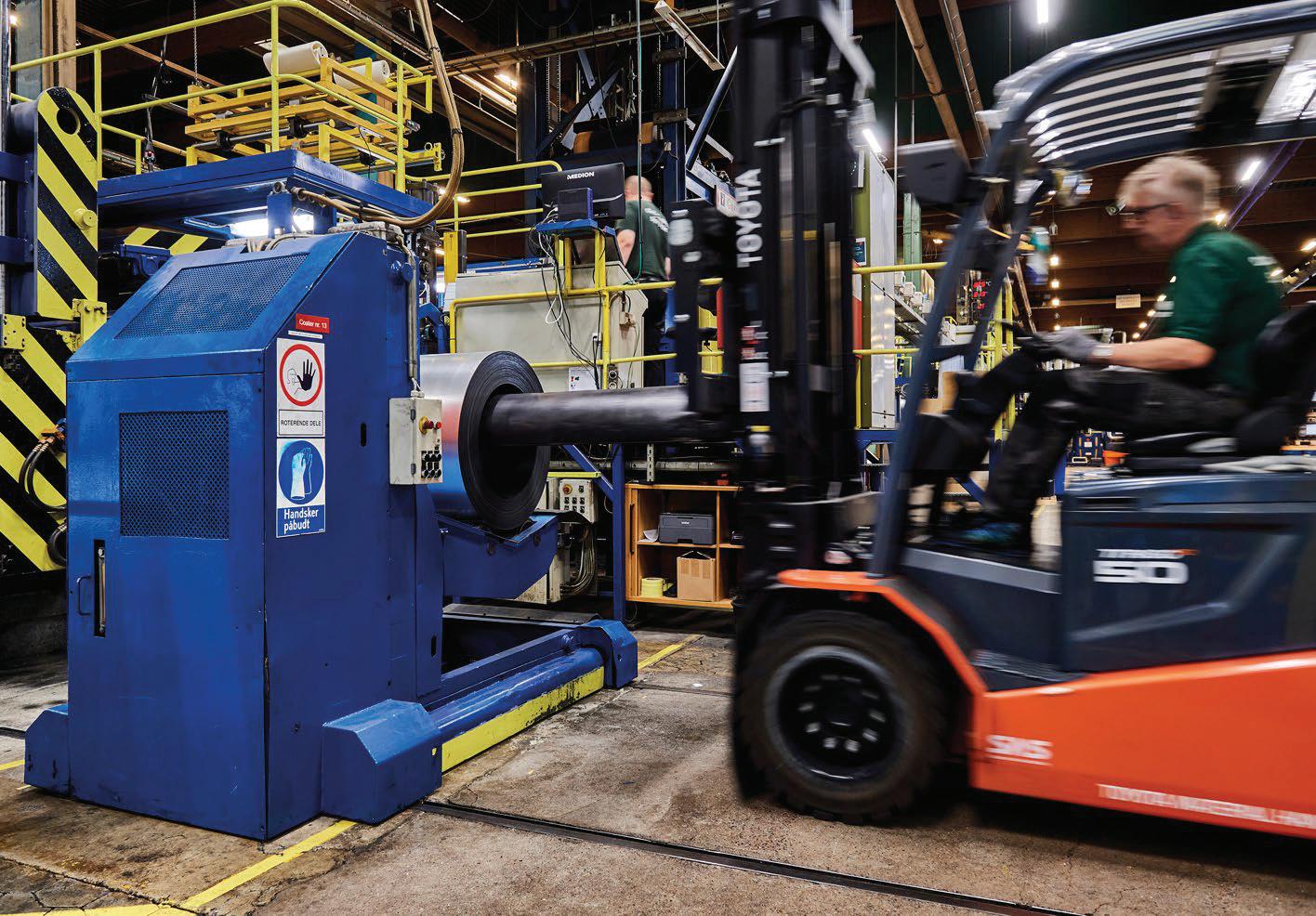
In the competitive landscape of manufacturing, the ability to adapt, innovate, and streamline processes is crucial for success. Metalcolour Technical Coating emerges as a key player in this narrative, offering bespoke solutions that revolutionise production efficiency and quality.
Metalcolour A/S in Denmark, the company’s success hinges on being a dependable supplier and an innovative partner. Transitioning to pre-coated raw materials has often proven to be a gamechanger for clients, resulting in fewer production steps, shorter lead times, and significant cost savings. Innovation is deeply ingrained in Metalcolour’s DNA, driving both customer-facing solutions and internal improvements that propel the company forward.
Earlier this year, we invested in a stateof-the-art precision slitting line. By adding this production process and upstreaming in the value chain we keep control over quality to meet higher demands from customers. Moreover, it gives flexibility from raw coil to shipment during the whole manufacturing process.
Metalcolour operates a cutting-edge Coil to Coil line, producing lacquered sheet metal and sheet metal with technical coatings. With a focus on continuous improvement, we constantly seek to enhance our processes by asking, “Can we do this better, and if so, how?” This commitment to innovation leads to collaborations with customers and subcontractors, facilitating the transition to pre-coated raw materials and fostering success for both parties.
The shift towards tighter collaboration with customers has led to deeper dialogues and enhanced understanding of product properties, resulting in optimised utilisation. This approach has empowered customers to insource
certain manufacturing processes, leading to newfound market opportunities and operational efficiencies.
Internal innovation is also a driving force at Metalcolour. With a highly committed team of coil coating specialists, we are contributing valuable ideas for enhancing production processes. Noteworthy examples include resolving machinerelated challenges and developing industry-
leading techniques that set new standards in the market.
Across borders, Metalcolour Sweden exemplifies a commitment to innovation by introducing groundbreaking solutions such as foil-laminated Aluminium for the marine sector and pioneering methods for measuring shine on embossed surfaces. Collaborations with suppliers have led to the development of heat-applied protective
foils, reducing material waste and enhancing product durability.
In conclusion, Metalcolour Technical Coating stands out as a catalyst for progress in the manufacturing industry. Through a combination of innovation, collaborative partnerships, and a relentless pursuit of excellence, we are reshaping the future of manufacturing by driving efficiency, quality, and sustainability.
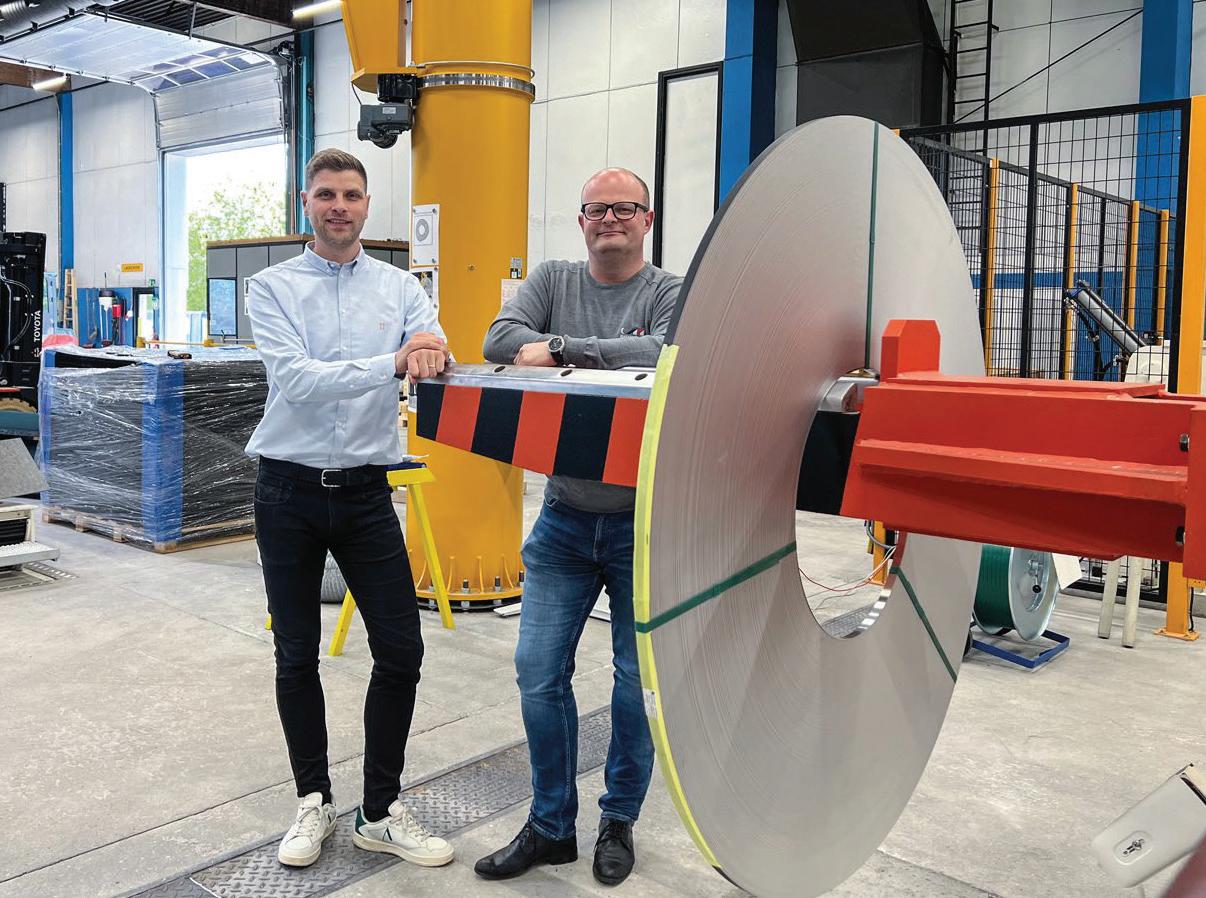
SCAN HERE TO FIND OUT MORE
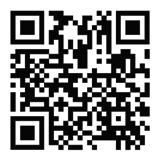
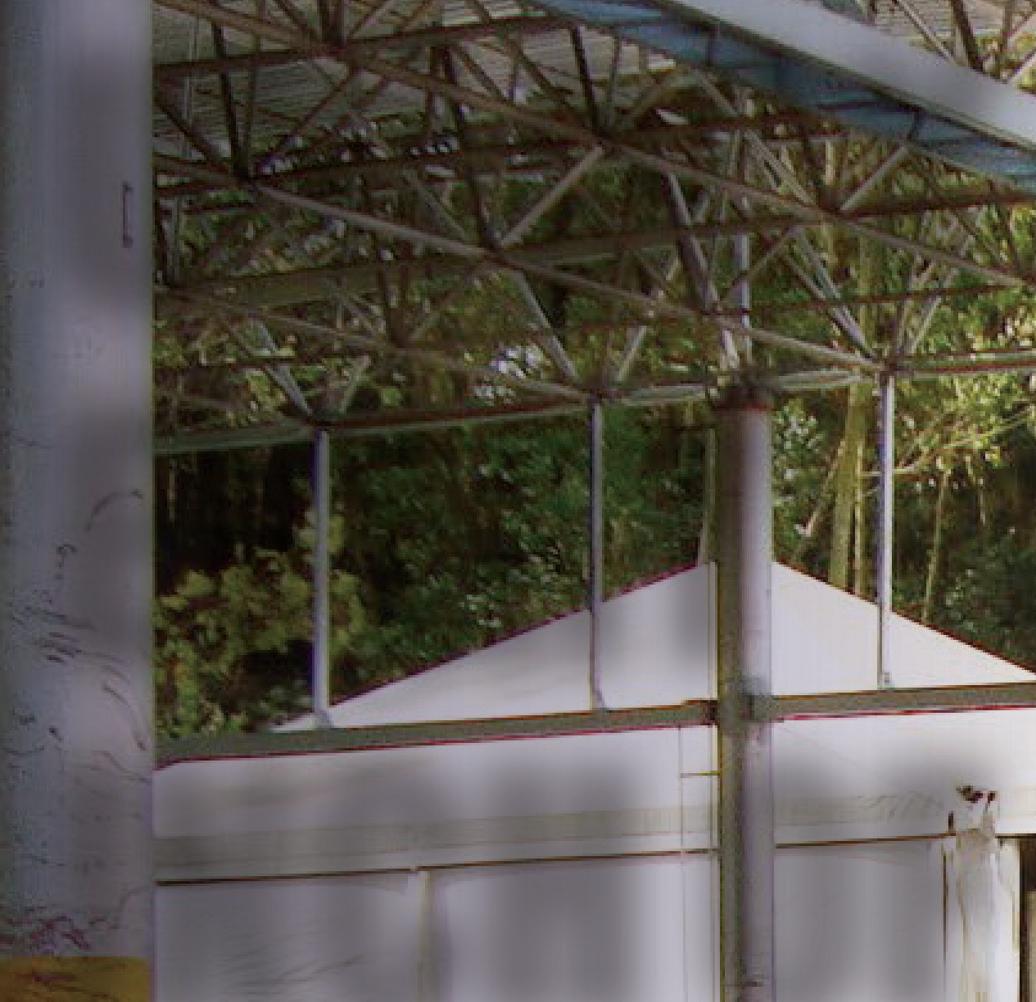
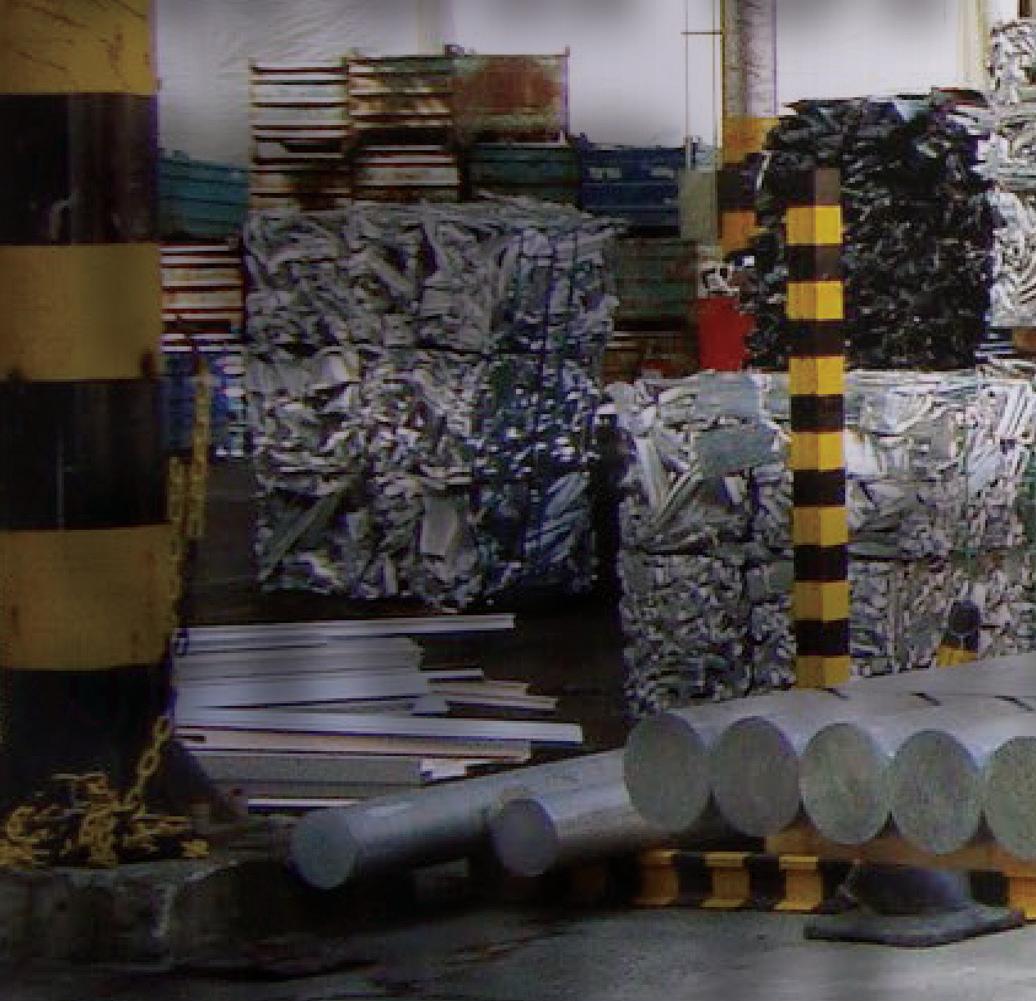

UNLOCK EVERY INCH OF YOUR STORAGE SPACE!

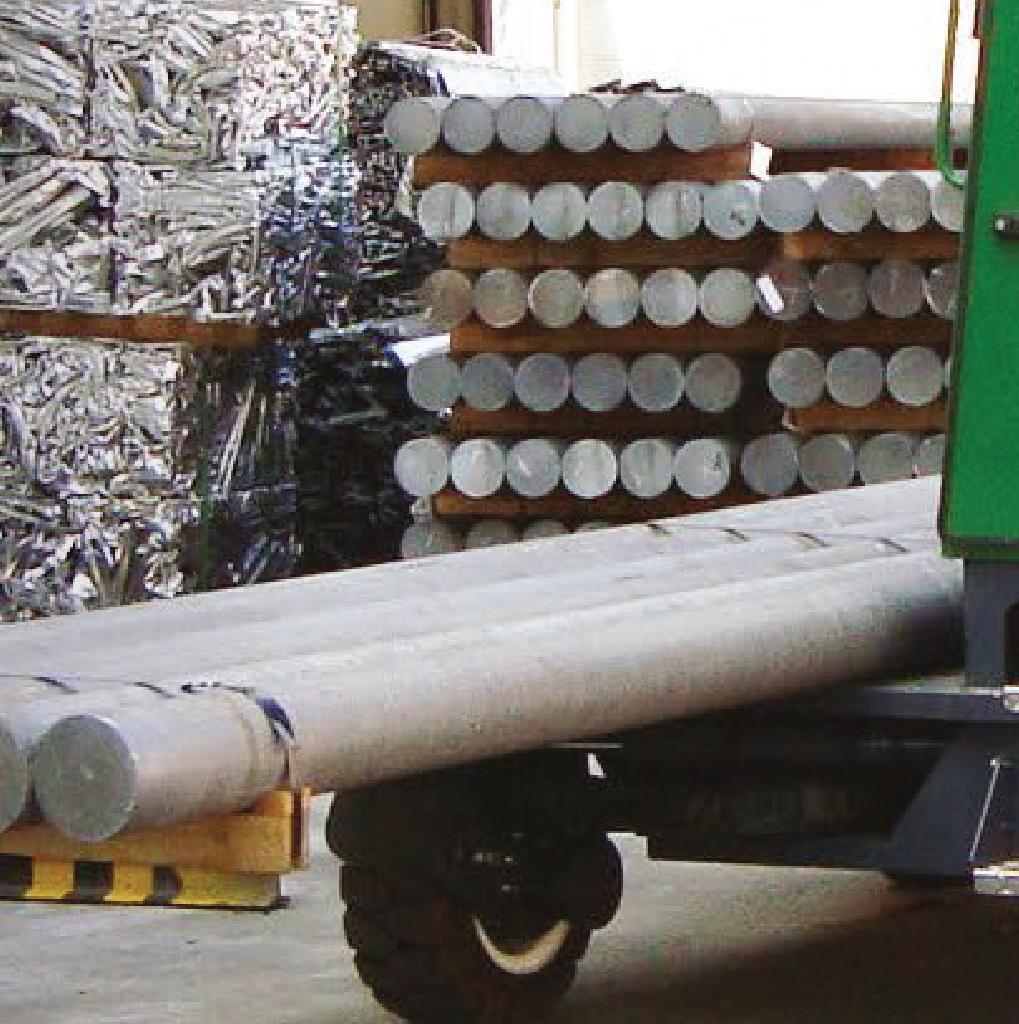



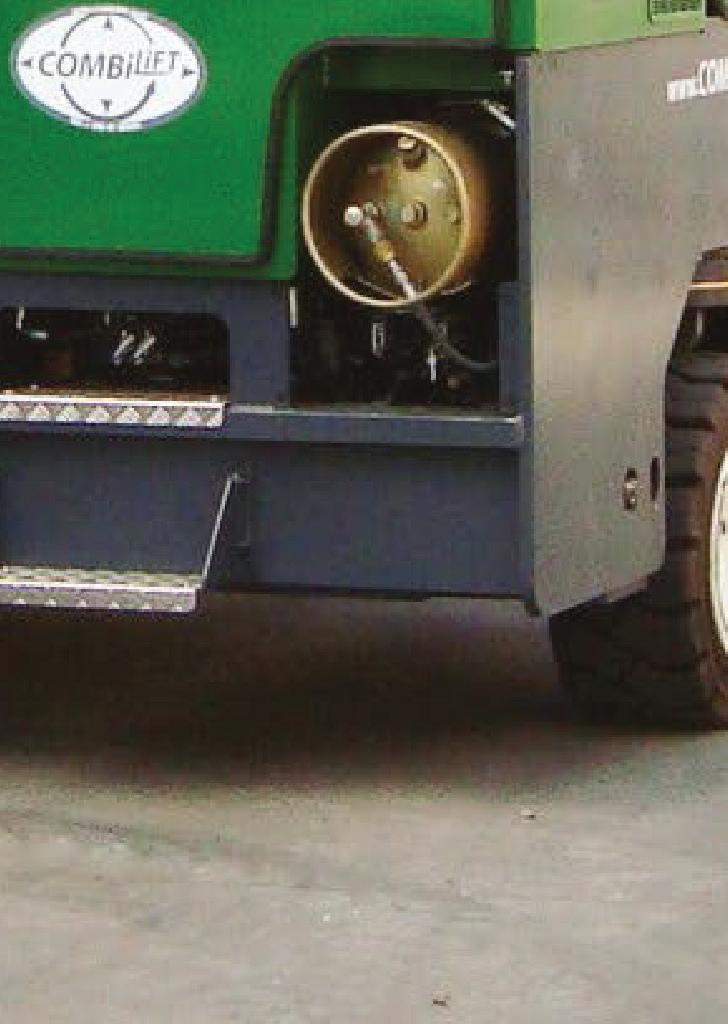
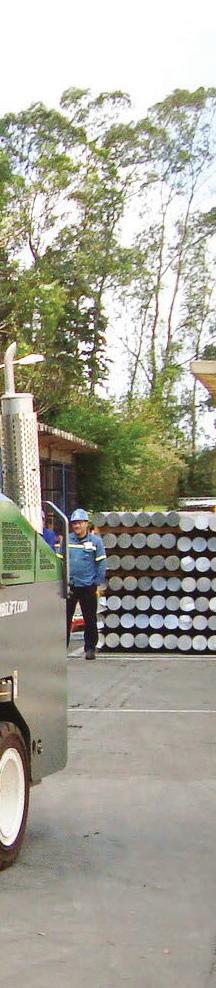
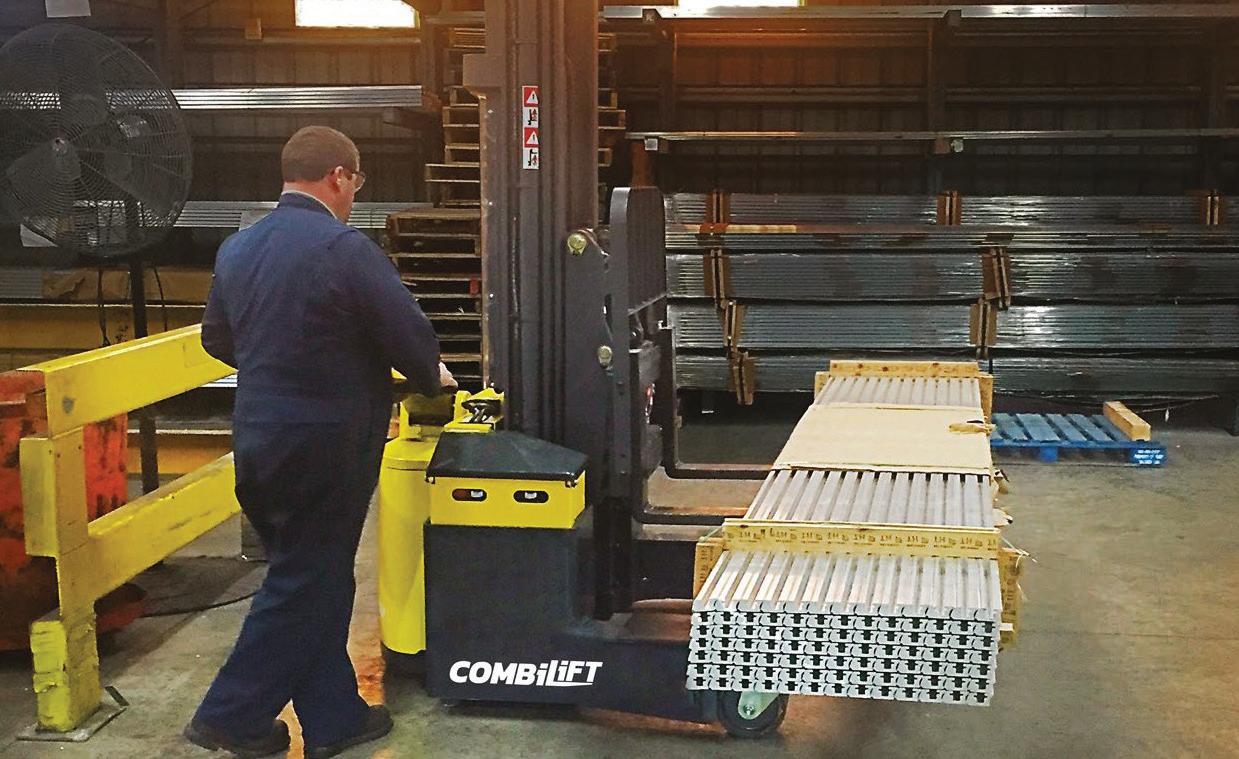
ENHANCE THE SAFETY, STORAGE & EFFICIENCY OF YOUR LOGISTICS WITH COMBILIFT
Our pioneering product range of multidirectional, articulated and pedestrian forklifts, straddle carriers and container loaders allows you to manoeuvre long loads safely, reduce aisle widths and increase the amount of space available for storage.
For 25 years, Combilift has been revolutionising the way companies handle and store goods. We help companies of all sizes and from every industry to maximise the capacity, safety and efficiency of their warehouse and storage facilities. CONTACT US TODAY
To find out how Combilift can help you unlock every inch of your storage space.
Increase Cast House Safety and Productivity with Fioscope’s In-Furnace Air-Cooled Smart Camera Technology
Fioscope GmbH are a global pioneer in high temperature camera applications, image processing, machine learning and process control. Through RiA Cast House Engineering GmbH, an exclusive partner for the Aluminium industry, Fioscope has been providing air-cooled In-Furnace camera systems to the Aluminium Cast Houses since 2014. Through this partnership, Fioscope has assisted in advancing safety and productivity levels in numerous Cast Houses worldwide. In typical operations, the melt cycle cannot be observed without opening the door and losing heat and energy, as well as the associated safety risk to the operators.
Fioscope’s air-cooled camera system – made In Germany – provides Cast House personnel with real time melt process feedback through a true colour, HD resolution video image capture (See figures 1 and 2). Giving Cast House personnel this feedback reduces the time and frequency of exposure to molten aluminium, a clear safety advantage. Reducing the amount of time the furnace door is open also provides extensive productivity benefits through keeping the furnace temperature higher, therefore melting material faster and increasing the throughput of the melting furnace. Reduced energy consumption is also possible through keeping the combustion
chamber of the melting furnace at higher temperatures by keeping the door closed, therefore reducing the time that energy sources are required to raise the temperature of the furnace to melting and casting temperatures.
All of the above benefits of increased safety and productivity levels can be further enhanced with the addition of storage and playback capabilities. Meaning, events that may occur in the furnace can be reviewed and preventative actions implemented to prevent them happening again. Similarly, over a weekend or a nightshift for example, Cast House management can review footage from within the furnace over the last 7 days on a FIFO system. Additionally, 1 frame per hour can be stored for 6 months, meaning long term changes in refractory can be monitored without having to look into the furnace making it easier to track and plan for maintenance stops for example.
Fioscope’s air-cooled camera systems have smart capabilities. Combining professional high resolution image acquisition with latest digital image processing technologies for accurate identification of process parameters. After an off-site training period on Fioscope’s neural network the software is able to detect the height of the scrap heap or recognise dross

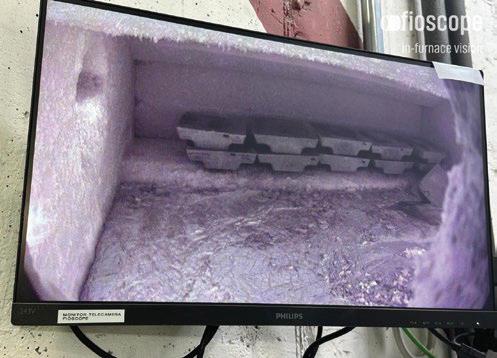
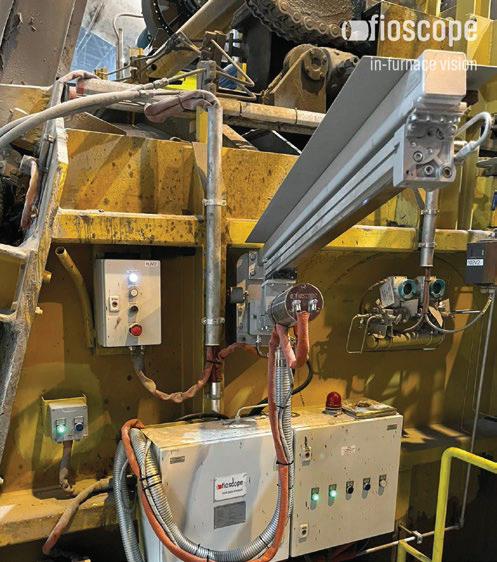
on the molten bath and produce a PLC signal to indicate a certain action to the Cast House operator, such as “Furnace Ready to Charge” or “Furnace Ready to Skim”. This leads to obvious productivity benefits as the furnace may have been ready to receive more material or to skim earlier, however the operators were unaware. All whilst maintaining a door closed operation, offering the safest environment to operators.
Fioscope are constantly developing new and innovative features with our smart camera technology, for example monitoring the burner flame for changes in shape, colour, size. Monitoring refractory for signs of damage and wear as well as monitoring the combustion chamber for anomalous and potentially dangerous conditions to alert operators.
Fioscope’s air-cooled cameras can easily be retrofit to existing furnaces as shown in Figure 3. Fioscope’s camera system consists
of a camera probe, air blower as well as a pneumatic and electrical control box which can all be mounted to the furnace itself. Simply requiring a power supply and a compressed air feed to keep the lens dust free and the image clear, the Fioscope system can be installed with minimal alterations to the furnace and in a short downtime period.
Visit our stand at Aluminium Dusseldorf to discuss how our air-cooled smart camera technology can increase the productivity of your Cast House whilst protecting your operators.
SCAN HERE TO FIND OUT MORE
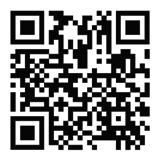
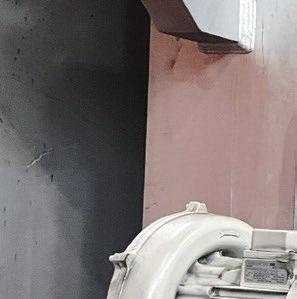
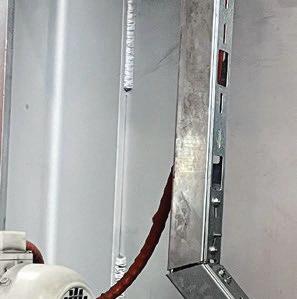
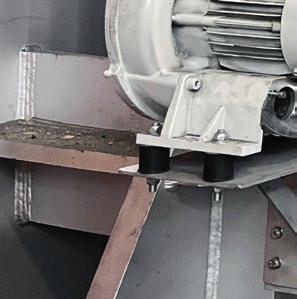
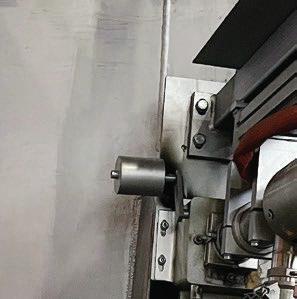
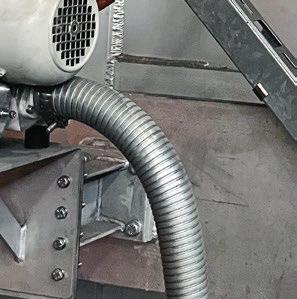
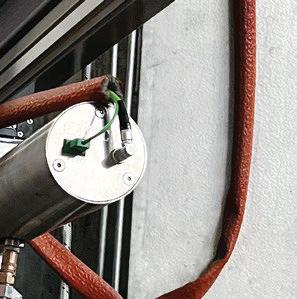
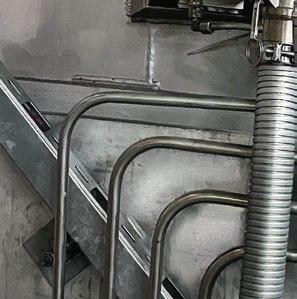
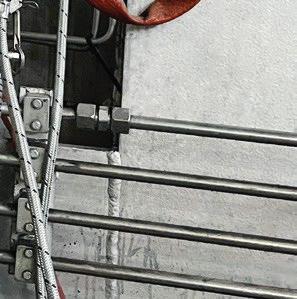
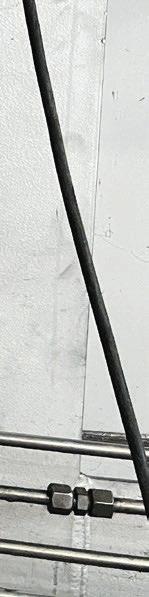
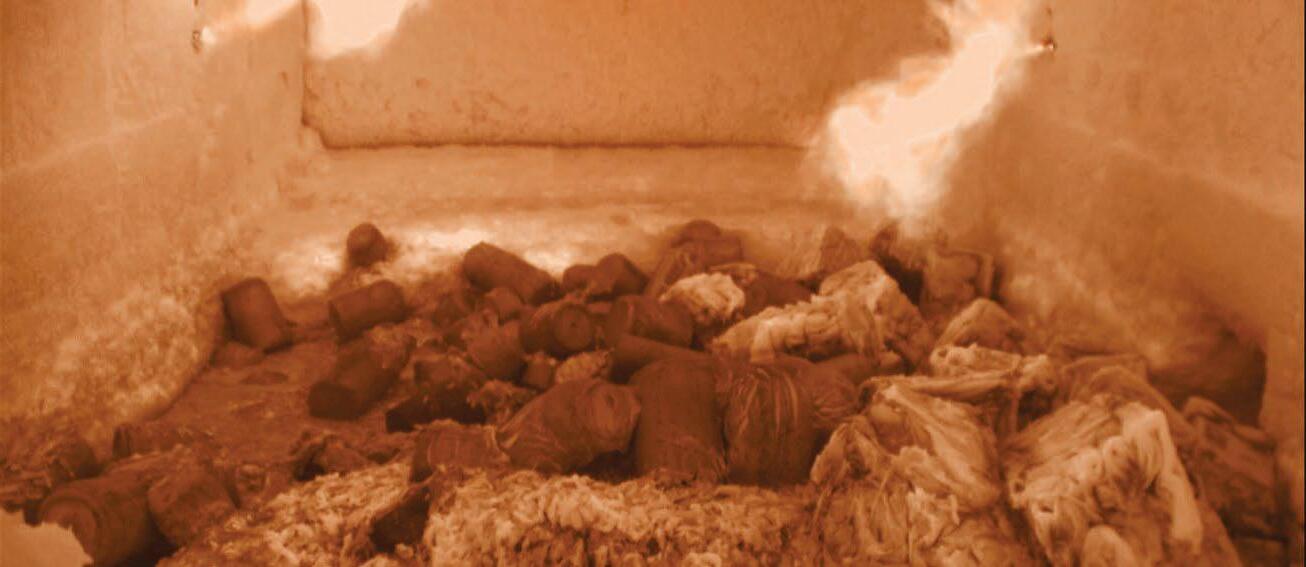
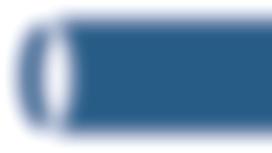
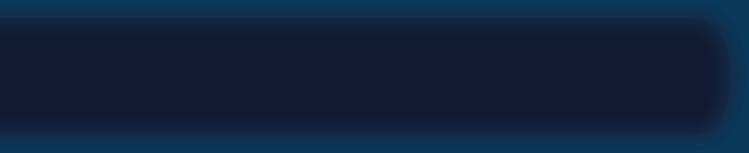
Advanced & Innovative Aluminum Solutions for the Automotive Industry
Cutting Edge Alloy Development
Continuous Ultrasonic Billet Testing Line
Lot Based Tracebility
High-Precision Fully Robotic CNC Machining & Welding Lines
NEXAL, low-carbon (≤ 4 tCO2e/tAl) aluminum billet
Production of both Interior and Structural Body Parts (Battery Casings, Crash Management Components, Safety Beams…)
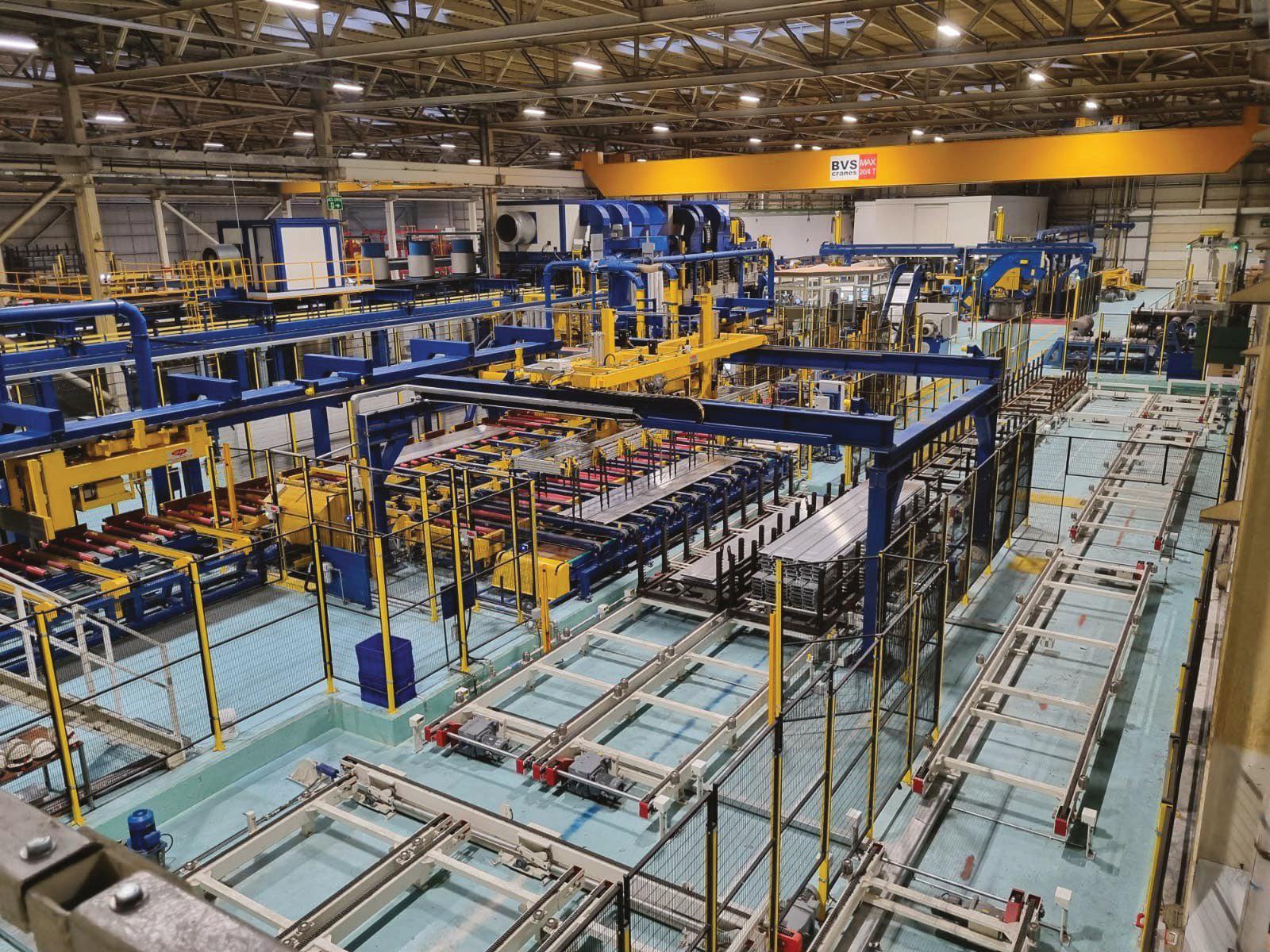


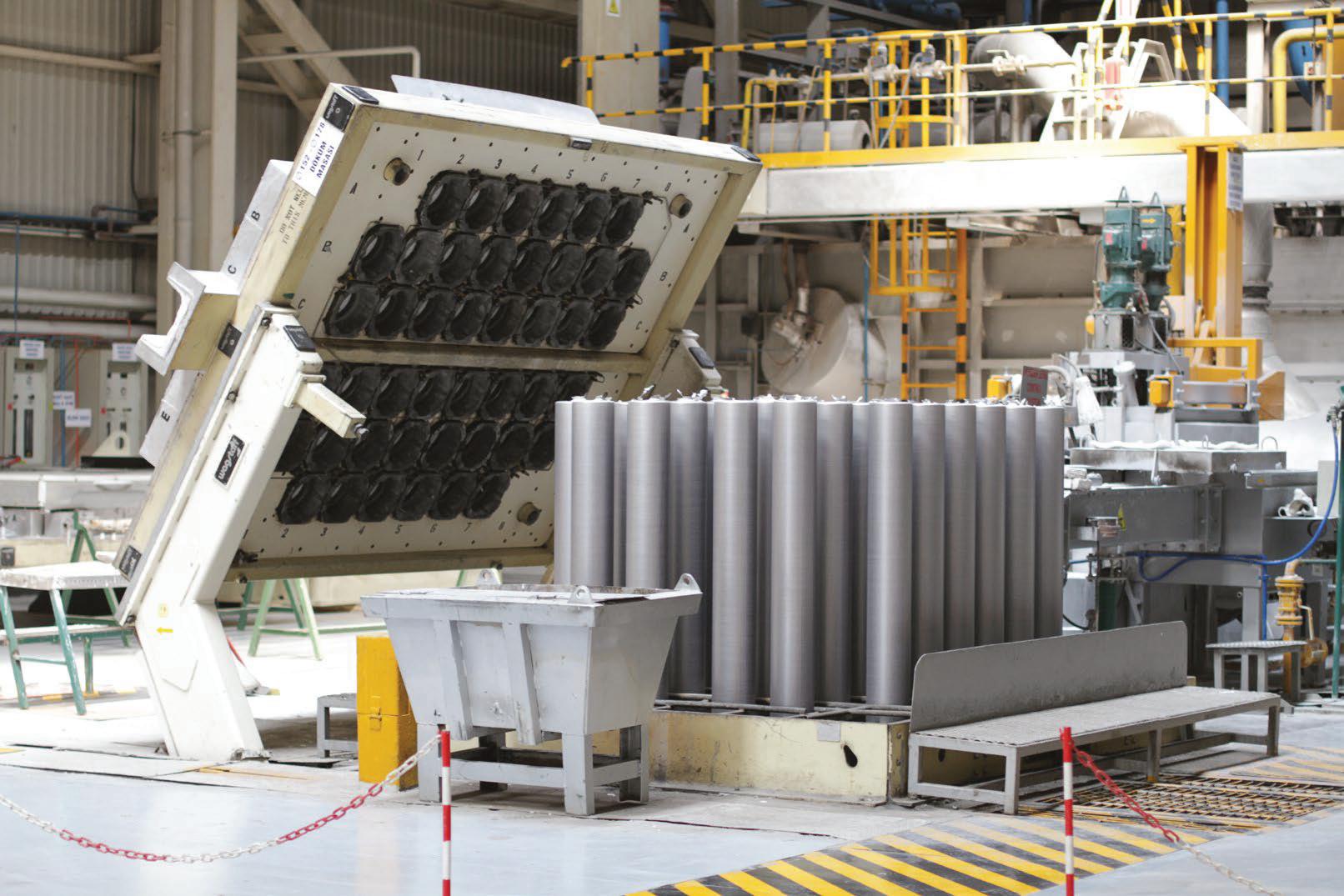
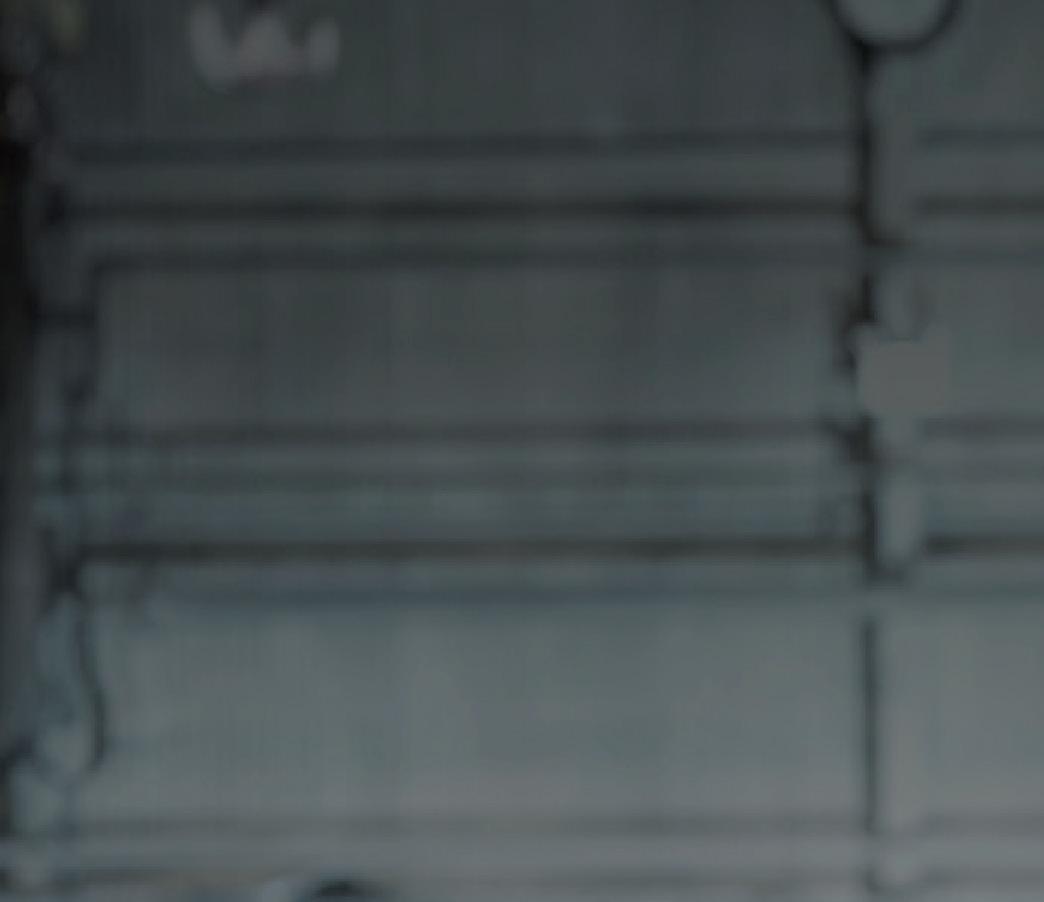
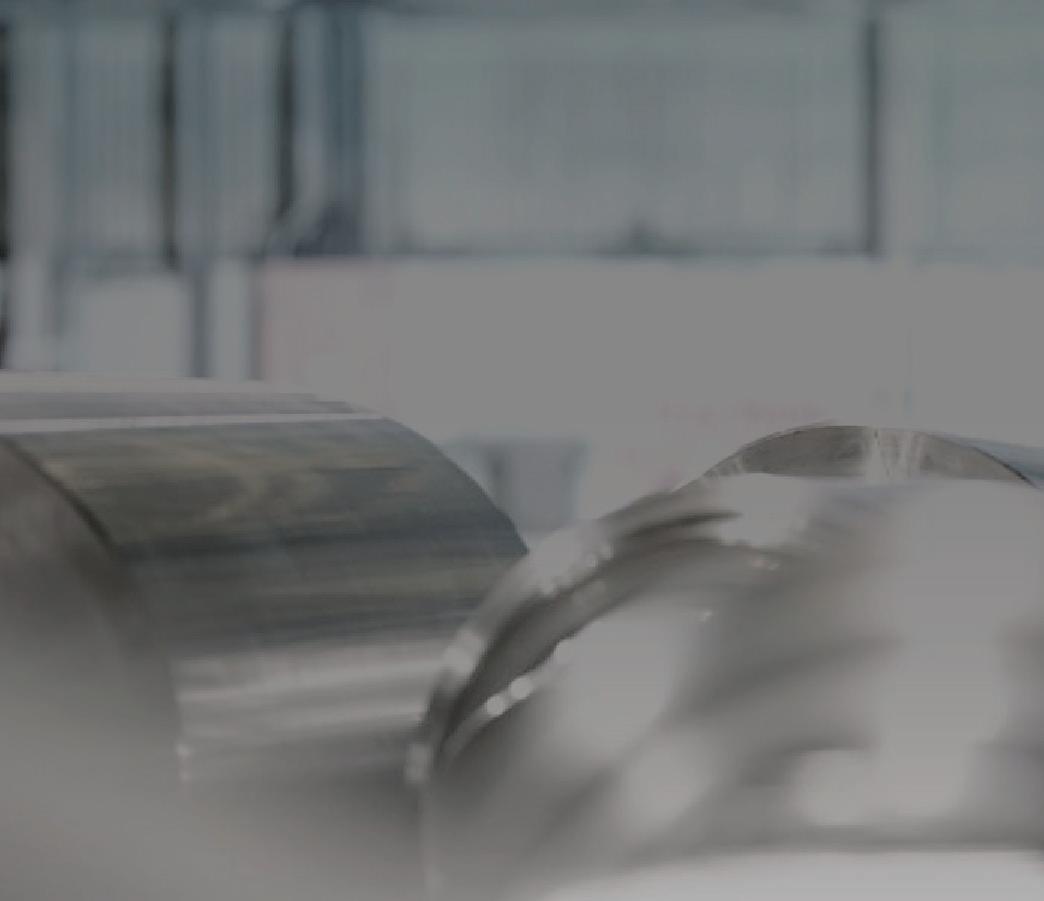
AN INSIDE VIEW: The Latest Hot Rolling Emulsion Technology from Quaker Houghton
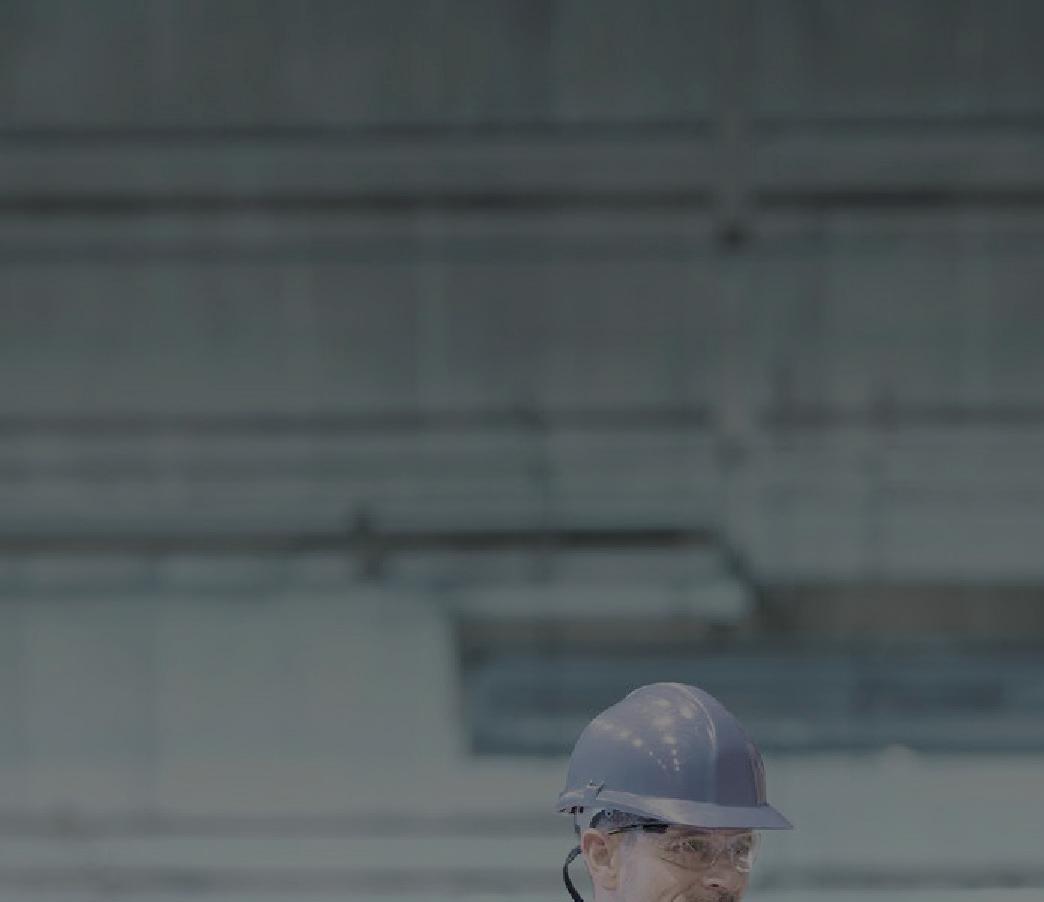
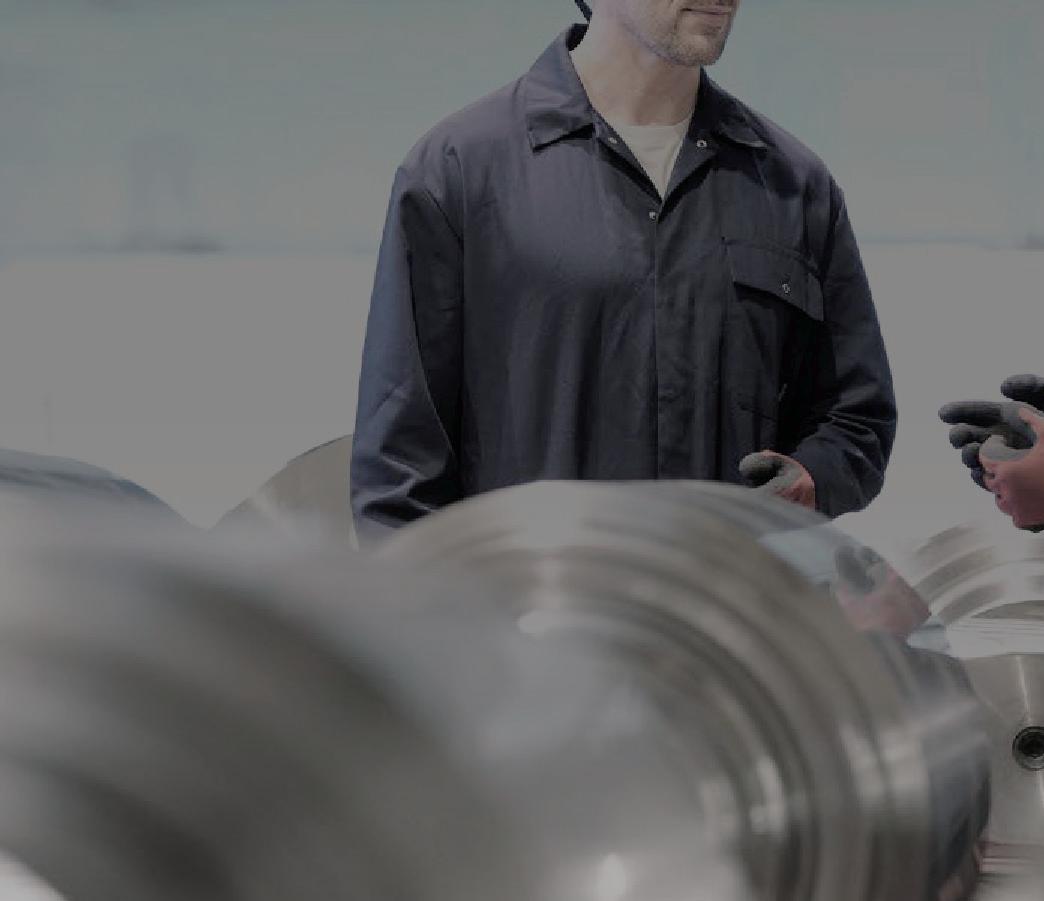

Quaker Houghton is the global leader in industrial process fluids, with over 75 years’ experience developing and supplying process fluids for metal production. Today the company serves over 100 aluminium hot rolling mills globally. We sat down with René Liedtke, segment leader for non-ferrous in Europe at Quaker Houghton, to discuss how the business is using its position as an industry leader to develop new products that support the evolving aluminium industry.
What’s the current state of play for the aluminium industry?
It’s a dynamic time for the aluminium industry. Sustainability is a huge driving force for change across many industries today, and for aluminium production this applies on two fronts – with the race to net zero both necessitating operational improvements and fuelling demand. Lightweighting of transportation components, battery foil used in e-Mobility, as well as plastic-alternative packaging all offer strong growth potential for aluminium mills.
But adapting to increased market demand isn’t always straightforward. For example, the production of battery foil involves very strict cleanliness requirements, and aluminium for automotive lightweighting needs careful control of metallurgical properties to achieve its high strength. Even upscaling production for established product such as beverage can stock isn’t without challenge, considering the stringent surface quality levels involved. Combined with the ubiquitous pressure on mills to improve productivity, reduce waste, and bring down the total cost of operation, these challenges can be a real barrier to success.
Our role is to enable our customers to embrace new market opportunities
René
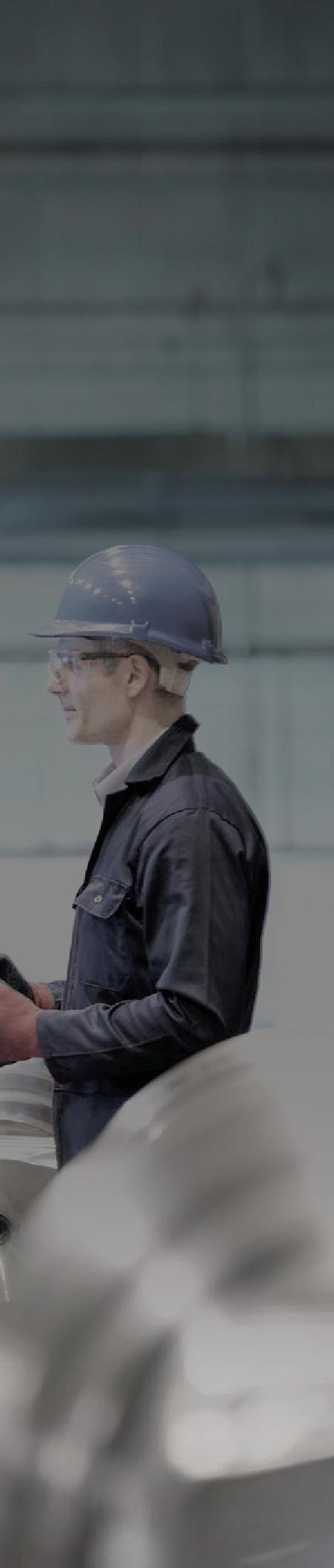
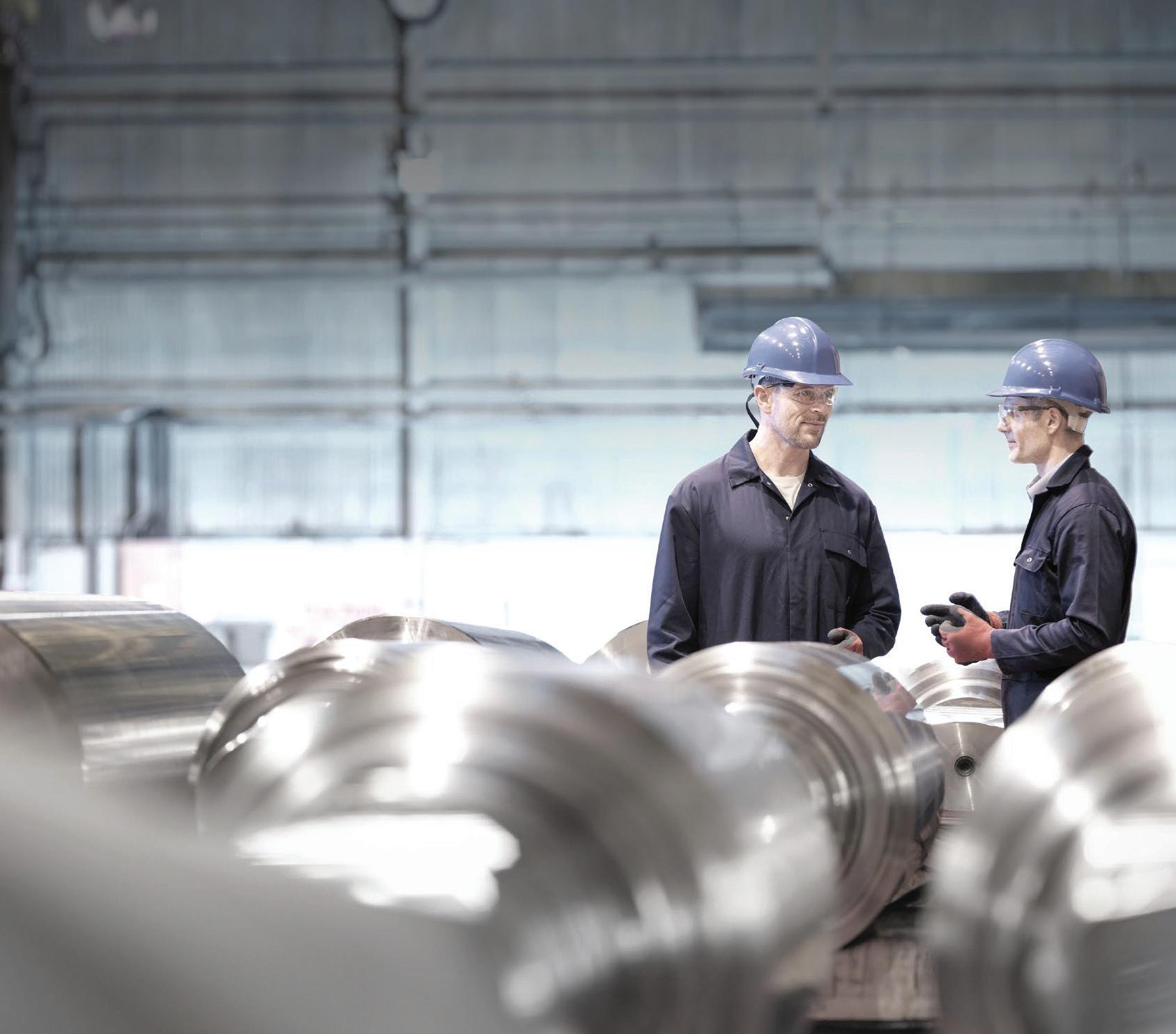
and ensure stable process conditions for established manufacturing routes. Through continual development and innovation of fluid technologies, and by applying our process expertise, we help achieve long term, competitive production in line with our customers’ sustainability and operational goals.
What does innovation mean to Quaker Houghton and how do you approach it?
Innovation is critical for progress. We continually improve our products and optimise them for specific customer needs, but it’s important to approach development from a broader angle too. We’re in a unique position as global industry leader to observe the latest trends and challenges of rolled aluminium manufacturers around the world. Plus, we work closely and collaboratively with our customers, so we see and hear first-hand the needs of production managers, process engineers and laboratory managers. Assimilating this information with our process knowledge and lubrication expertise enables ideation of new concepts.
But new fluid technologies need to be proven, as well as innovative. For this, we take a unique and rigorous approach to development. Firstly, we look closely at the specific process needs, and screen raw materials from our database using computer modelling to arrive at a formulation. Next, we take it to the lab, using custom-designed equipment that simulates the rolling process, which provides us with proof of concept.
From there Quaker Houghton has a unique capability: our 4-high pilot mill in Qingpu, China, where we evaluate rolling fluid behaviour in real-world conditions.
We refine new products along the way,
5000, is a non-soap technology that delivers superior mill cleanliness and requires minimal fluid maintenance. Key to its performance is the ability to keep aluminium fines dispersed in the fluid, allowing easy removal by filtration to prevent deposition and sludge formation. In operation, we’ve seen excellent mill and emulsion cleanliness with very low skimming volumes that will ultimately help reduce waste at the mill. Another important benefit is that the fluid is suitable for the full range of aluminium alloys to help support customer expansion into new markets.
Tell us about the industrial trial - did the product perform as expected in the field?
Speira Holmestrand was the first customer to trial the new technology, having much experience working with both soap-based and soap-free emulsion technologies on its breakdown and tandem mills. In the run-up to the field trial, we worked closely with the mill team on the preparations and a full manual clean out took place during the winter shut down before the system was refilled with 120,000 litres of the new emulsion. With a
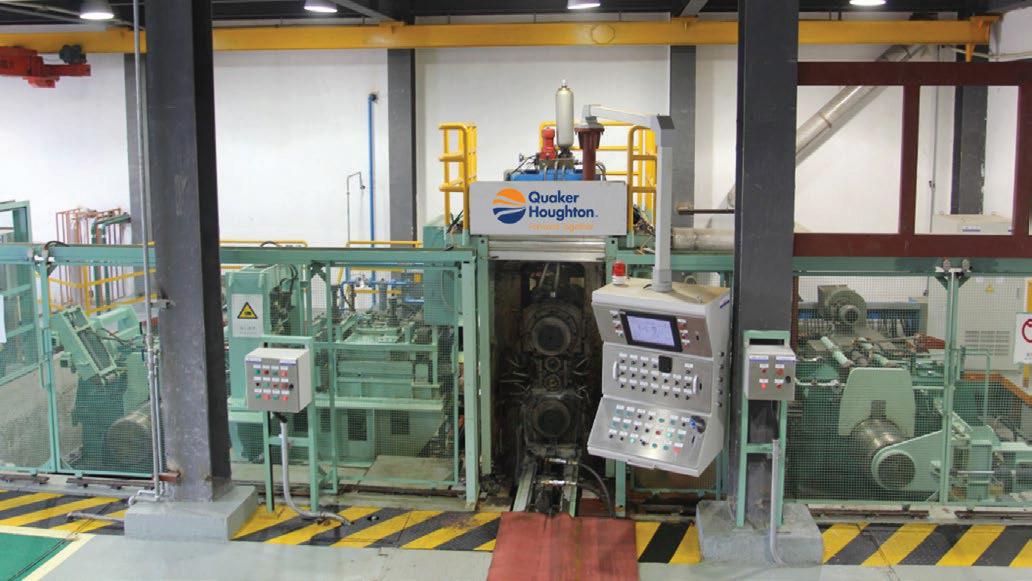
and once we’ve had a successful trial on the pilot mill, we already have proof of performance so customers can have great confidence in running an industrial trial – as we demonstrated with our latest emulsion technology QH EVEROLL™ A 5000. By developing hot mill protocols to mimic customer rolling conditions for the pilot mill as well as for our lab set-up, we can fine-tune our product for its intended application. This approach to innovation not only accelerates the development process but also de-risks the adoption of new technologies, helping our customers stay ahead in a changing world.
What can you tell us about this latest rolling fluid technology? What benefits does it bring to hot mill operations?
Two interlinked concerns for many of our customers are mill cleanliness and fluid maintenance. Despite being excellent lubricants, traditional soap-based chemistries produce metallic soaps in operation, which build up over time and change the lubrication properties if not carefully managed. Soapfree chemistries are often favoured for their reduced maintenance needs and lower product consumption, but are known to underperform in fines dispersal, resulting in heavy metallic sludge deposits in the tanks and on the mill equipment.
We set out to create an emulsion for hot rolling mills that would bring together the benefits of both traditional soap-based and existing soap-free technologies – while minimising the disadvantages. Our new hot rolling emulsion series, QH EVEROLL™ A
full production schedule in January there was little room for error – and that’s where we saw the full benefit of our development approach: thanks to the tailored product optimisation at the pilot mill, the trial was seamless.
We sent test equipment to Holmestrand and carried out fluid analysis daily for two weeks. But because of the high consistency of the emulsion parameters, the testing was decreased to twice weekly measurements, reducing the necessary manpower for onsite laboratory work. Besides a single ester addition during the very early stages of the product introduction, no additional tankside additives were used during the first five months of full operation. This proves the robustness of the new chemistry.
Overall, there’s been a 30% reduction in oil consumption compared with the previous soap-based technology. Excellent surface quality has been observed across all alloys and good dispersal of aluminium fines has resulted in superior cleanliness of the mill environment, in particular resolving issues with dirt buildup on the work roll chocks and adjacent mill equipment.
With this trial, QH EVEROLL™ A 5000 has demonstrated tangible benefits for hot rolling mills and we have verified our unique approach to development and innovation. We’re looking forward to the next trial!
SCAN HERE TO FIND OUT MORE
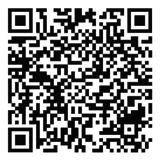
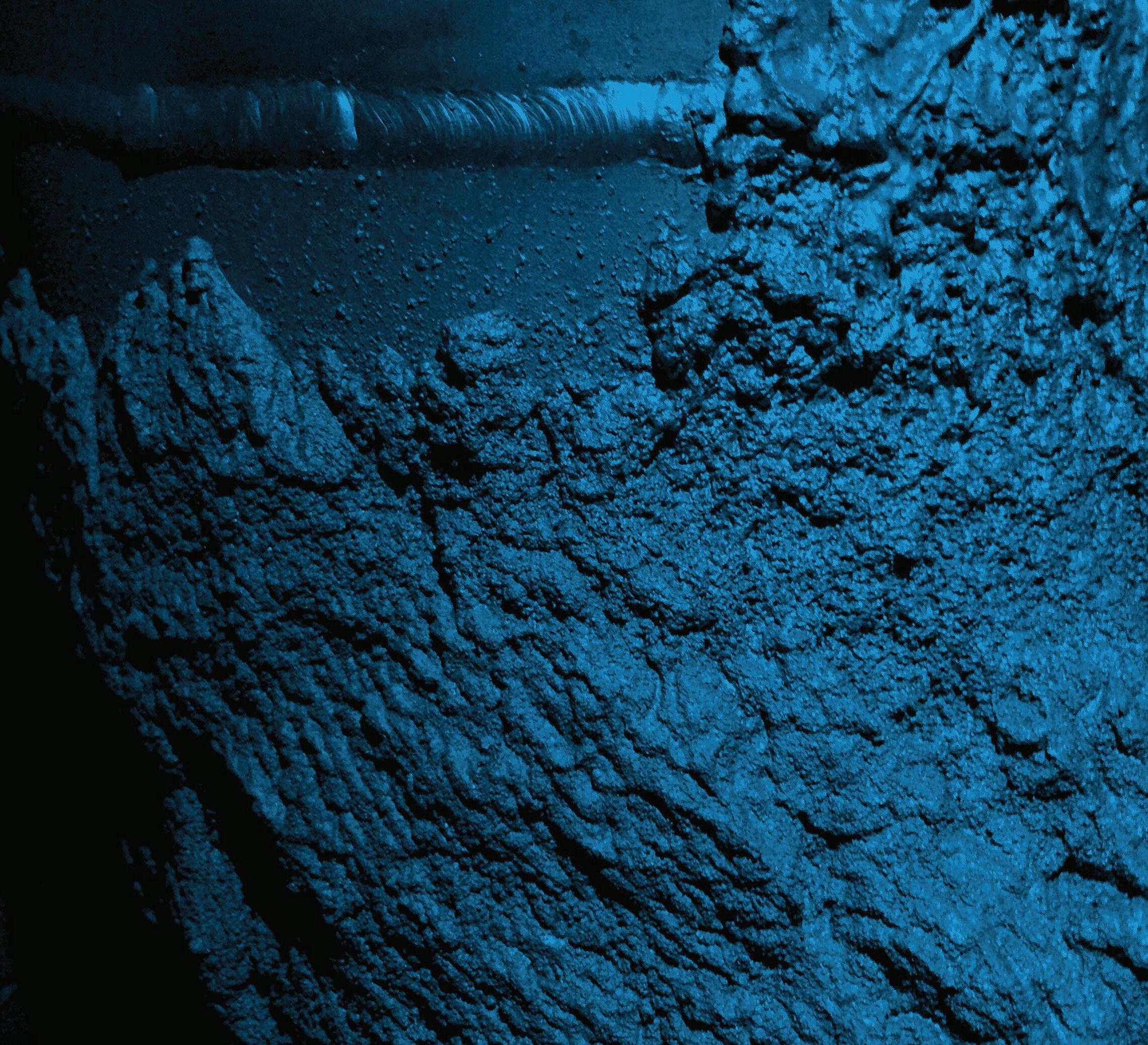
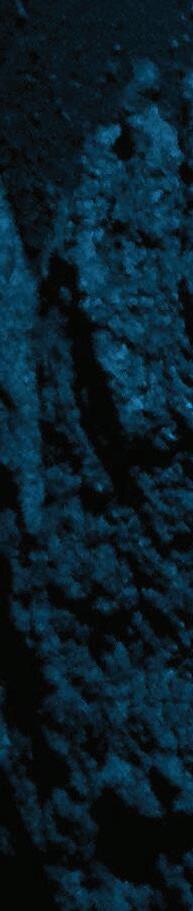
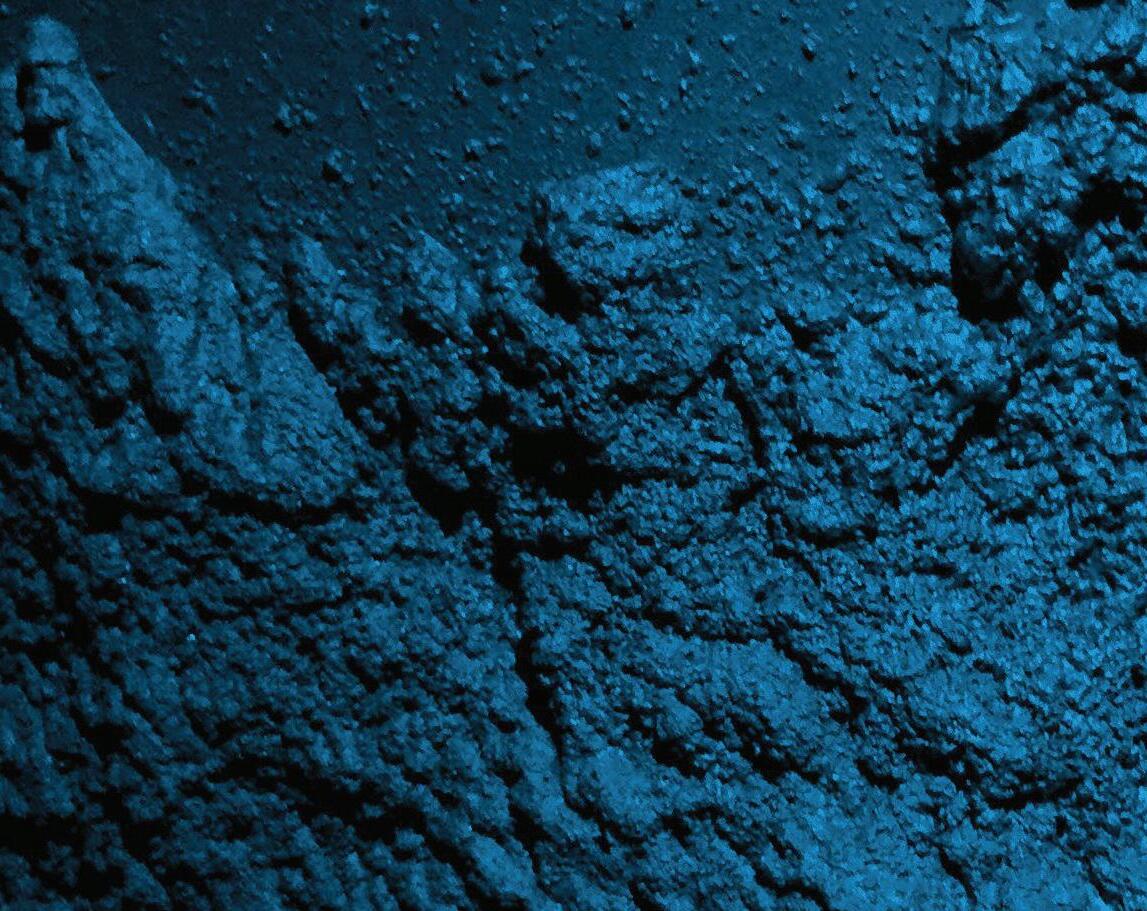


Meeting the diverse needs of the aluminium industry
Leveraging its extensive technical expertise, exemplary safety standards, robust aftersales service, and global reach, along with strategic proximity to key aluminium production hubs, REEL Aluminium has established itself as a leading supplier and a vital strategic partner for major smelter projects and companies worldwide. The company’s comprehensive portfolio encompasses a wide range of advanced solutions and services, positioning it as a key player in the industry. This comprehensive approach ensures that REEL Aluminium can meet the diverse needs of the aluminium industry, offering a level of service and expertise that is unmatched by competitors.
Today, REEL Aluminium offers a comprehensive suite of products and services, including Electrolysis and Carbon Cranes, Alumina Material Handling Systems, Vacuum Ship-unloaders/loaders, Port Material Handling and Storage solutions, Environmental Control Systems, Anode Rodding Shops, Green Anode Plants, Carbon Recycling Plants, and Bath Treatment Plants. These offerings provide a significant competitive advantage, enabling the company to meet the diverse needs of the aluminium industry efficiently and effectively. Moreover, the division is deeply committed to delivering cost-effective, engineered solutions designed to enhance operational KPIs and facilitate the upgrade and modernisation of existing plants. This commitment to innovation and efficiency is a hallmark of REEL Aluminium’s approach, ensuring that its clients can achieve optimal performance and sustainability in their operations.
REEL ALESA, a prominent Technology Center within the REEL Aluminium Division, headquartered in Zurich, Switzerland, specialises in the design, supply, installation, and commissioning of a variety of solutions specifically tailored to the aluminium industry. Its comprehensive range of offerings includes Alumina Material Handling Systems, Pot Feeding Systems, Vacuum Ship-unloaders/loaders, Port Material Handling and Storage solutions, and advanced Environmental Control Systems. REEL ALESA ensures optimal performance by focusing on equipping plants to handle raw materials efficiently from ports to pots, ensuring seamless integration and operation.
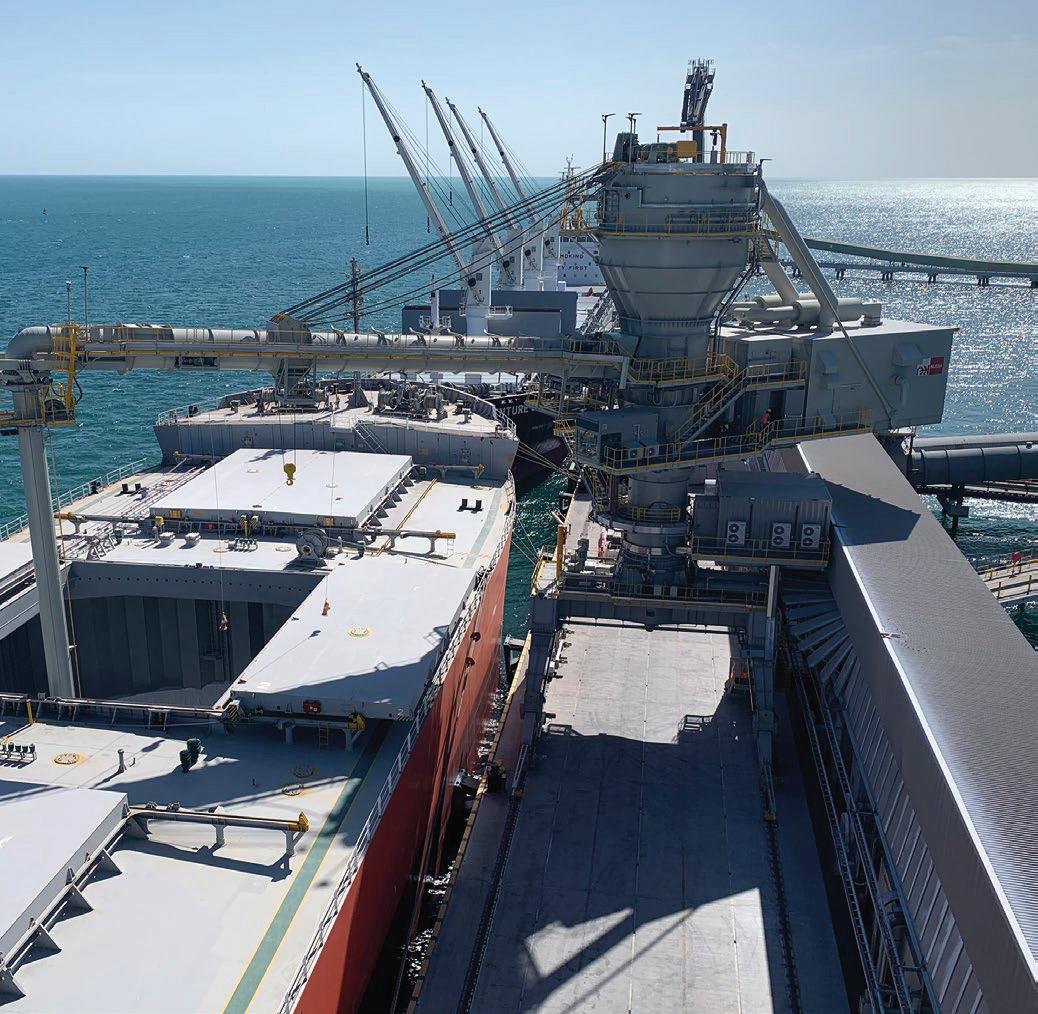
Its expertise in Environmental Control extends to exploring innovative Carbon Capture, Utilisation, and Storage options, while its high-capacity Vacuum Shipunloaders significantly reduce demurrage costs for clients, further enhancing operational efficiency. The Technology Center’s focus on research and development is critical to staying ahead of industry trends and challenges, enabling REEL ALESA to offer cutting-edge solutions that address the evolving needs of its clients.
Tailoring its solutions to meet the specific needs and challenges of aluminium smelting plants, REEL ALESA addresses critical factors such as safety, production requirements, and the necessity for minimal shutdowns. This tailored approach ensures that the solutions provided not only meet but exceed industry standards and client expectations. REEL ALESA’s commitment to customisation and client satisfaction is evident in its meticulous planning and execution processes, which are designed
to deliver maximum value and efficiency. By understanding the unique challenges faced by each client, REEL ALESA can develop solutions that are precisely aligned with their operational goals and constraints, ensuring long-term success and sustainability.
REEL Aluminium’s unwavering commitment to innovation and sustainability is evident in its provision of state-of-the-art solutions and equipment aimed at enhancing energy efficiency and implementing stringent environmental control measures. Various Technology Centres and Global Support Centres within the division are actively engaged in developing cutting-edge technologies designed to reduce energy consumption and greenhouse gas emissions, contributing to a more sustainable and environmentally friendly industry. This focus on sustainability is not just a response to regulatory requirements but a core value that drives the company’s mission to create
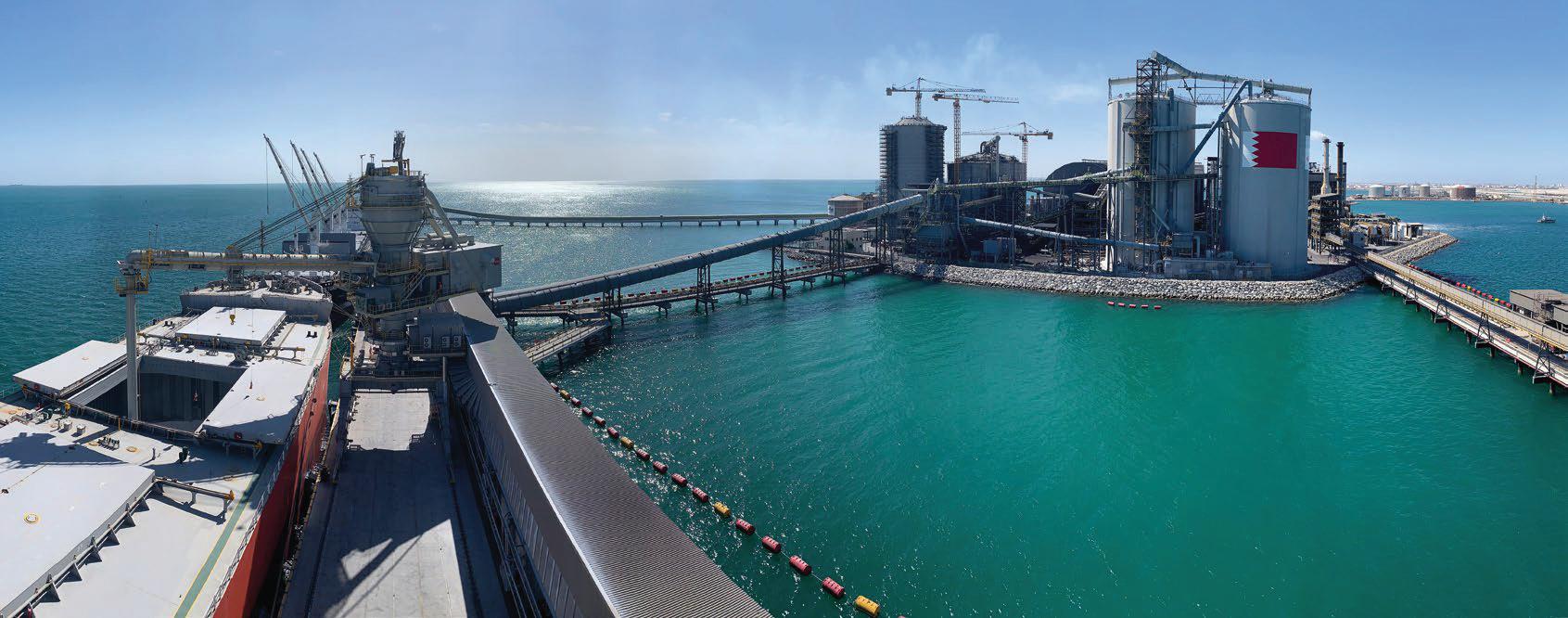
a positive impact on the environment. REEL Aluminium’s efforts in this area include the development of energy-efficient machinery, the integration of renewable energy sources, and the implementation of advanced waste management systems, all of which contribute to reducing the carbon footprint of its operations and those of its clients. Through its comprehensive solutions, REEL Aluminium adeptly addresses key challenges faced by modern aluminium smelters, such as controlling fluoride and sulphur dioxide emissions and managing hazardous wastes. The company’s recent technological advancements have significantly minimised environmental impact, including the development of sophisticated gas treatment systems and solutions for capturing and utilising wasted heat energy, thus promoting sustainability. These innovations not only help smelters comply with stringent environmental regulations but also offer significant cost savings by improving efficiency and reducing waste. REEL Aluminium’s commitment to continuous improvement and innovation ensures that its clients are always equipped with the most advanced and effective tools to meet their environmental and operational challenges.
In response to evolving industry trends, REEL focuses on both “Greenfield” and “Brownfield” smelter projects. While new “Greenfield” projects may not be anticipated for 2024, existing smelters are actively undertaking “Brownfield” projects aimed at increasing production capacity and ensuring compliance with stringent environmental regulations. The REEL Aluminium Division collaborates closely with smelters worldwide, providing state-of-the-art solutions designed to enhance production capacity and reduce emissions, ensuring sustainable growth. This proactive approach allows REEL Aluminium to stay ahead of the curve, anticipating future industry needs and positioning itself as a leader in the aluminium sector.
Amidst challenges such as rising raw material and labour costs, REEL Aluminium supports aluminium producers’ costreduction strategies through various initiatives. Internal efforts to manufacture project components locally, near smelters, aim to reduce logistics costs and enhance efficiency. By offering a diverse range of solutions, REEL meets smelters’ expectations, supporting their costreduction efforts and ensuring the delivery of high-quality products and services. The company’s focus on local production not only reduces costs but also strengthens relationships with local communities and suppliers, further enhancing its reputation as a responsible and reliable partner in the industry. Through its comprehensive approach to innovation, sustainability, and customer satisfaction, REEL Aluminium continues to set the standard for excellence in the aluminium industry.
SCAN HERE TO FIND OUT MORE


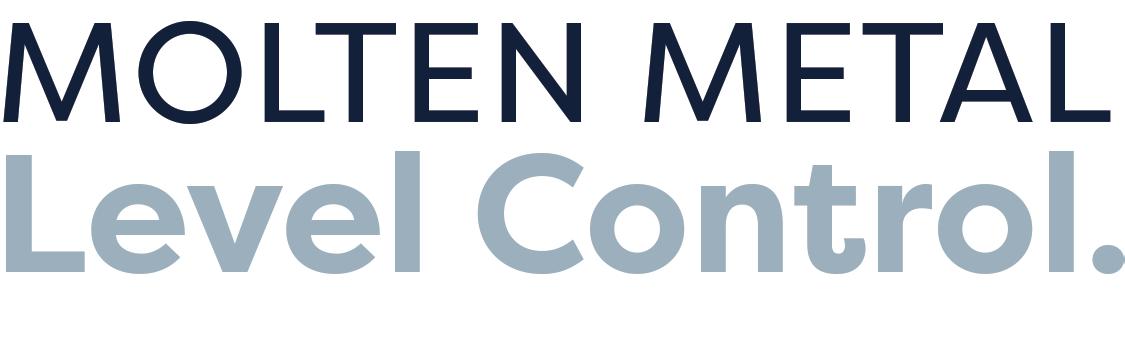

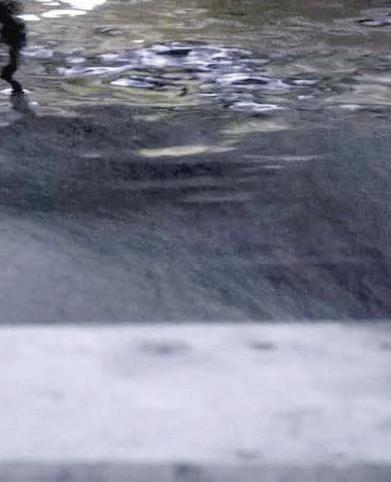
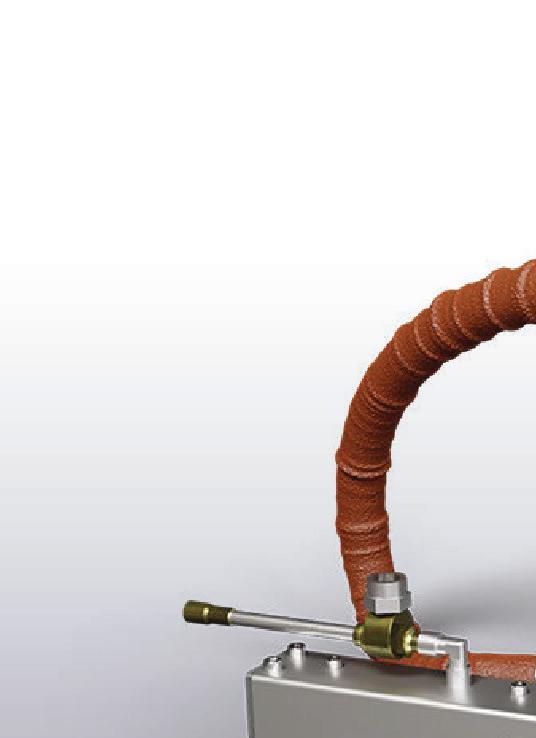
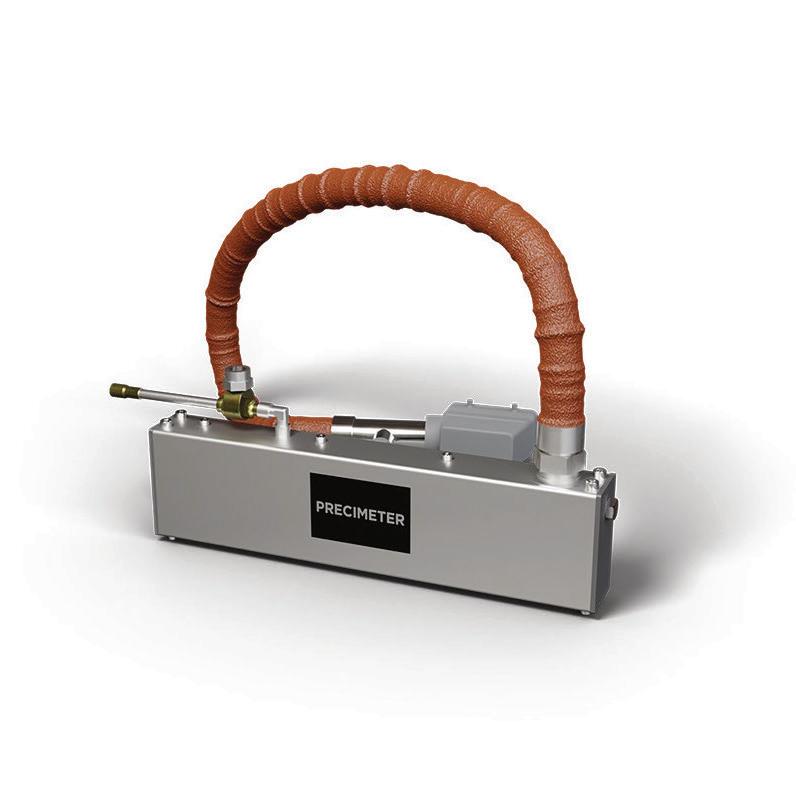

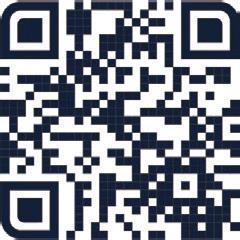

OTTO JUNKER GmbH
100 years of innovation
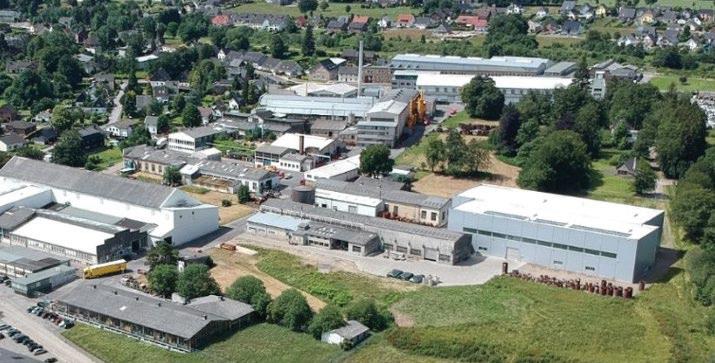
Deeply rooted by tradition, well prepared for the future: A manufacturer of industrial furnaces and equipment for melting and heat treatment of metals and for recycling of scrap and Li-Ion batteries as well as of “Power to Heat” energy storage systems.
Since its foundation in 1924, OTTO JUNKER GmbH has made a name for itself as a pioneer in building equipment for foundries as well as for rolling mills and pressworks and plays a leading international role as a furnace manufacturer and system supplier for metallurgical processes and the refining of metals.
This year, the company celebrates its 100 year anniversary and looks back at a time full of technological and entrepreneurial milestones, including major contributions to a sustainable industry. Several thousand industrial furnaces made by OTTO JUNKER are in operation all over the world. These are required wherever there is a demand for high-quality castings and forgings as well as
semifinished products such as slabs, plates, sheets, strips, foils, billets, rods, profiles, wires and tubes of all kinds of metal.
Commitment to research and progress
OTTO JUNKER plants are used for melting, pouring and heat treatment of metallic materials. Over the years, the company has not only maintained its position as technological market leader but even expanded it.
100 years ago, Dr.-Ing. E.h. Otto Junker founded his company in Lammersdorf in the Eifel region and specialised in metal processing. His aim was the marketing of the water-cooled mould for the production of brass rolling plates, an invention by his father, Andreas Junker. The committed company founder worked hard for the expansion of the company and the development of new machines and equipment. In doing so, he built up a close relationship with the Technical University of Aachen, which was and still is founded upon the principle that a continuous technical development is indispensable for the success of a company.
Since 1982, after the death of Otto Junker, OTTO JUNKER GmbH has been owned by the Otto Junker foundation which supports the education of young engineers and promotes research projects at the Technical University of Aachen. The cooperation has
A CENTURY OF INNOVATION GREEN FURNACE TECHNOLOGY
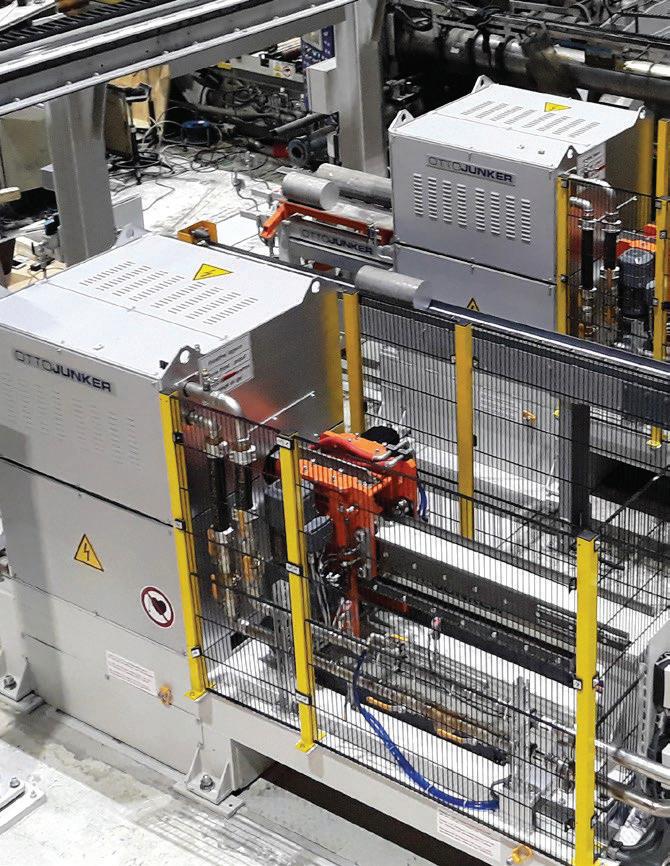
led to numerous technological breakthroughs and has helped to maintain the technological leadership of the company.
Technological innovative strength
The challenges to industrial furnace building have evolved. Apart from meeting exactly specified process parameters and the ongoing increase in capacity and reliability, today’s main focus is on questions of energy efficiency. This has become an integral part of everyday work and continuously pushes on the innovative spirit of the entire OTTO JUNKER group of companies.
“The capability to adapt to market requirements continuously and quickly - both from a technical and organisational point of view - remains an important success factor for us. This is guaranteed by the technical competence and flexibility of our employees, which is what characterises our company”, says Erik Mí?ek, CEO of OTTO JUNKER GmbH.
From the early days with electric melting furnaces for the foundry industry for all kinds of metal to state-of-the-art induction and convection systems for the aluminium, copper and steel industry, OTTO JUNKER has continued to enhance the market with groundbreaking technologies. Over the years, the company has developed from a small machine shop to a globally renowned manufacturer of high quality induction
melting and thermoprocessing plants whose products are used in more than 80 countries all over the world.
“Our focus is not only on dealing with the challenges faced by our customers, but also on contributing to an environmentally friendly industry in a pro-active manner,” Erik Mí?ek continues. “The next 100 years will be characterised by our pursuit to continuously redefine the boundaries of what is technically possible”.
The pronounced innovative strength of OTTO JUNKER has led to OTTO JUNKER also offering competent solutions with regard to sustainability outside of the metal industry. In cooperation with the Technical University of Aachen, industrial partners and with support from the German government, innovative energy storage and recovery technologies have been developed. These plants make a significant contribution to increasing the share of cost-effective, regenerative energy for providing industrial process heat and decoupling the processes from the volatility of regenerative power generation by wind and solar energy.
SCAN HERE TO FIND OUT MORE
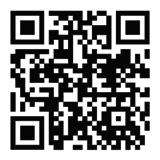
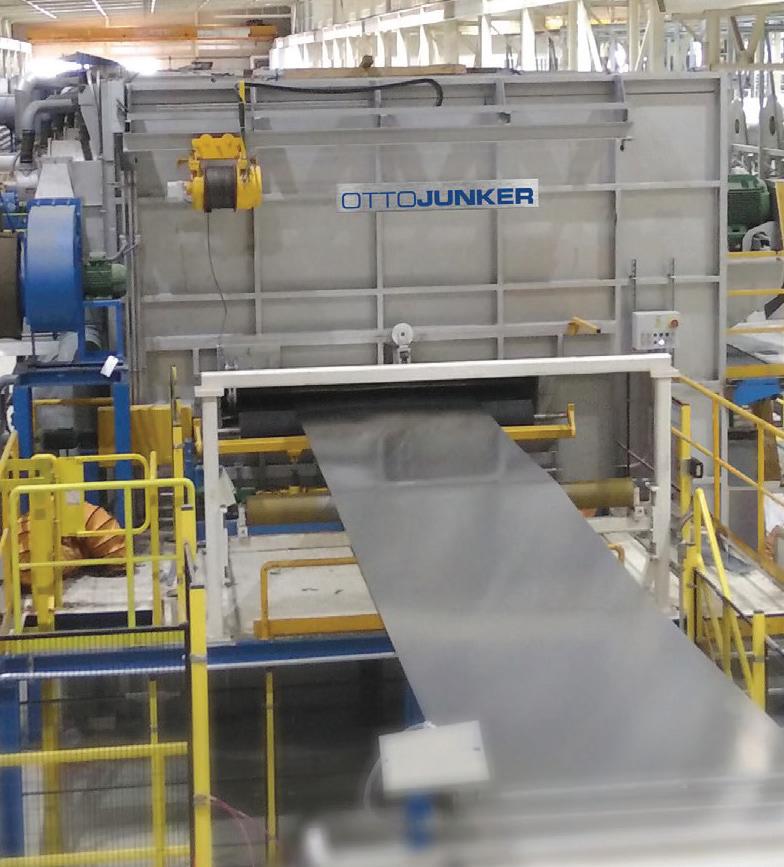
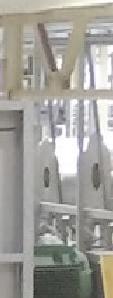
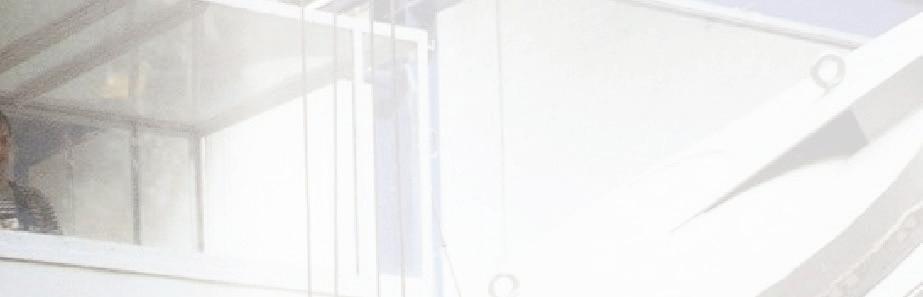
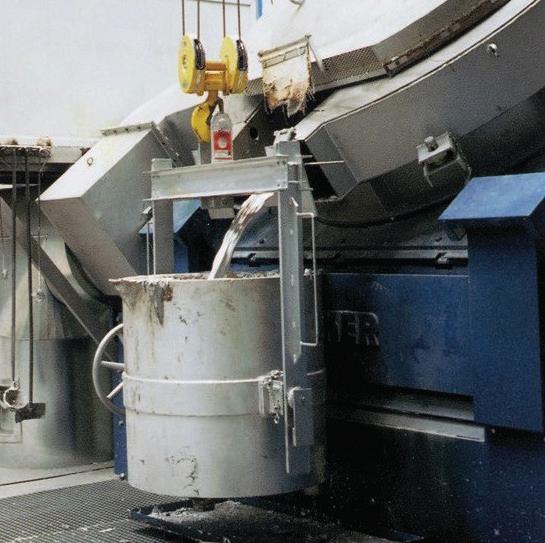
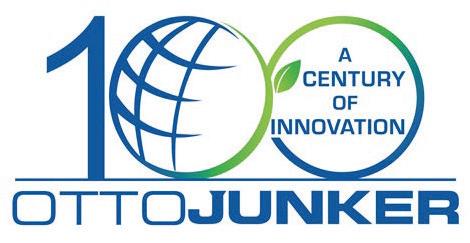
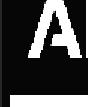

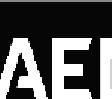

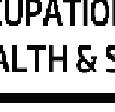

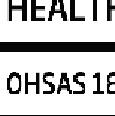
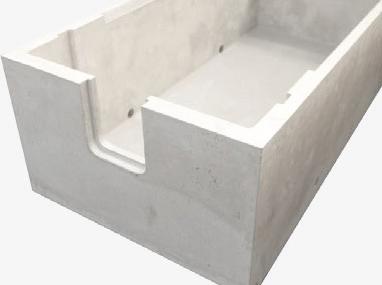

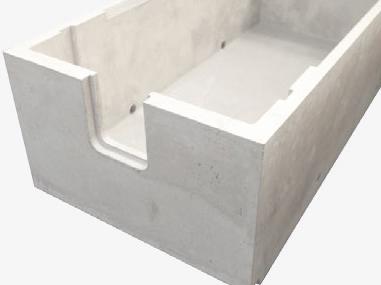
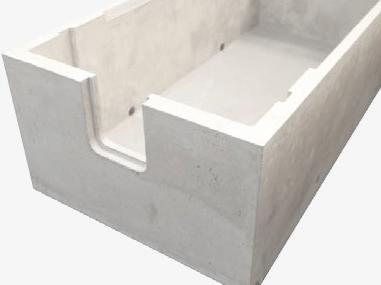
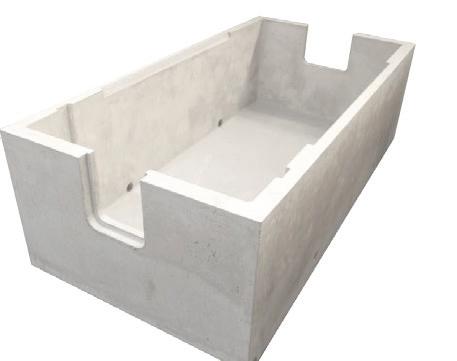
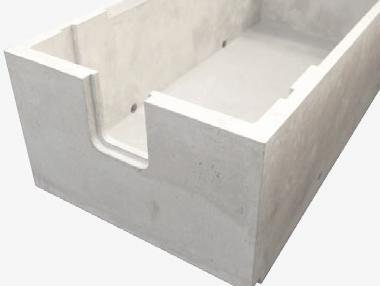

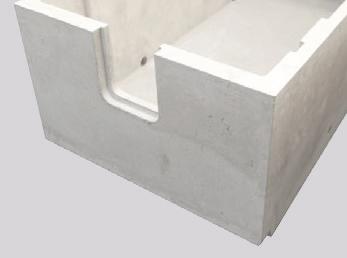
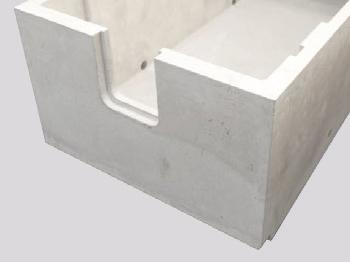




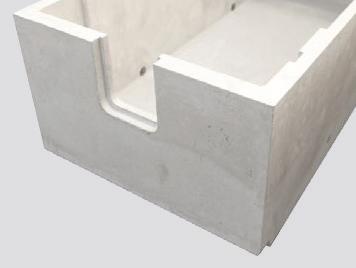
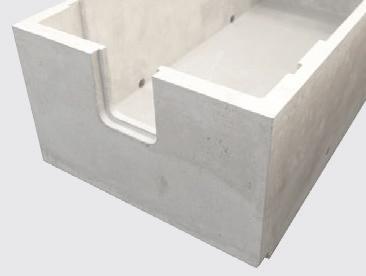
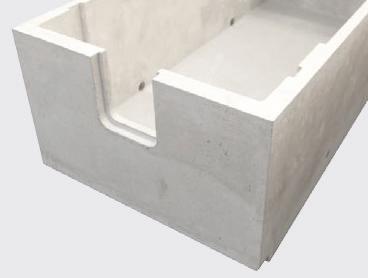
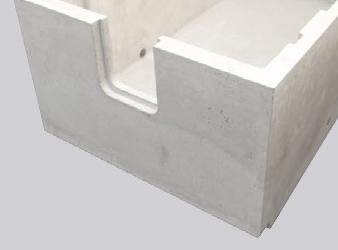

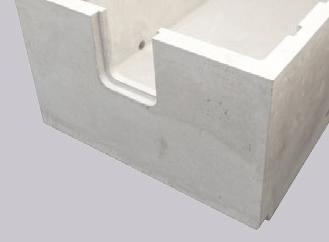
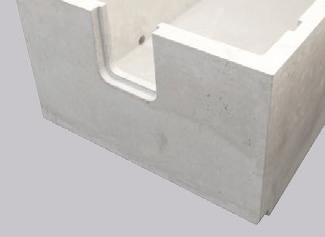
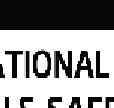
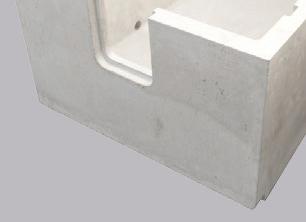
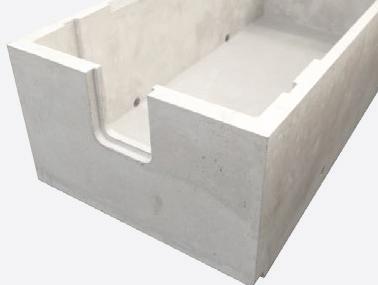

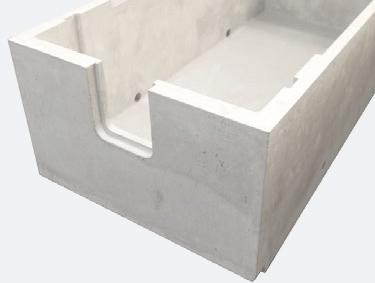
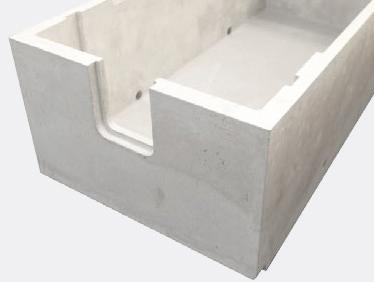

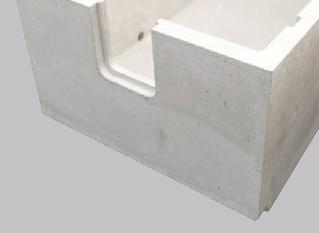


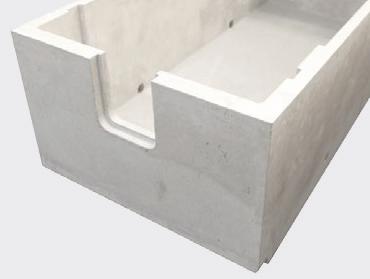
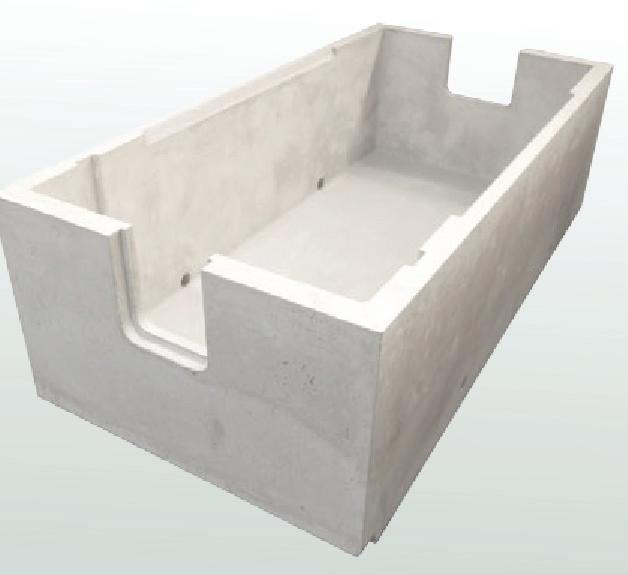
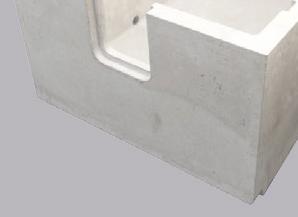
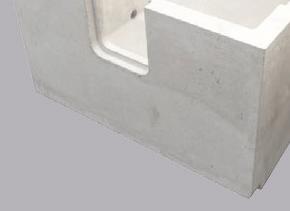
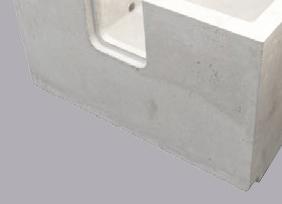

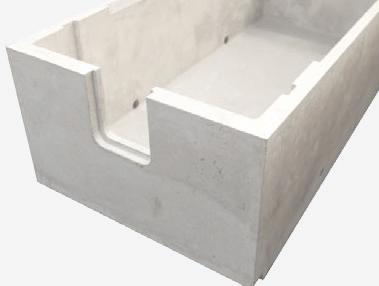
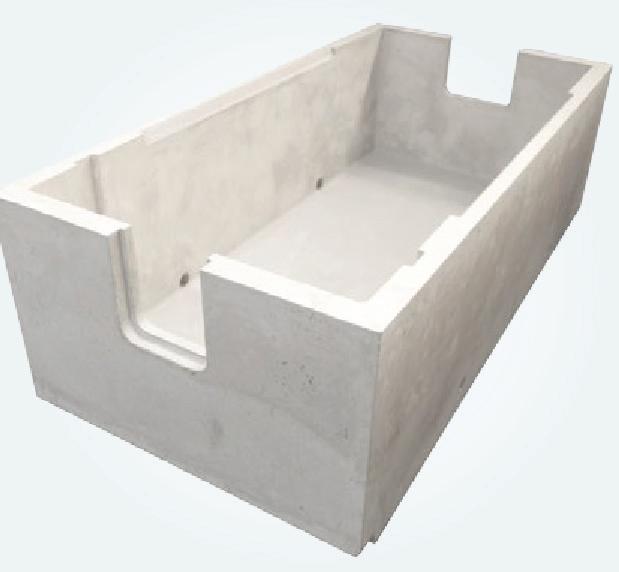
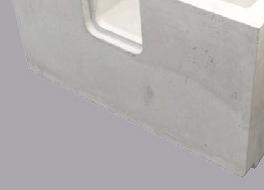
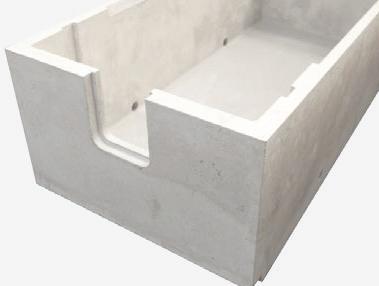
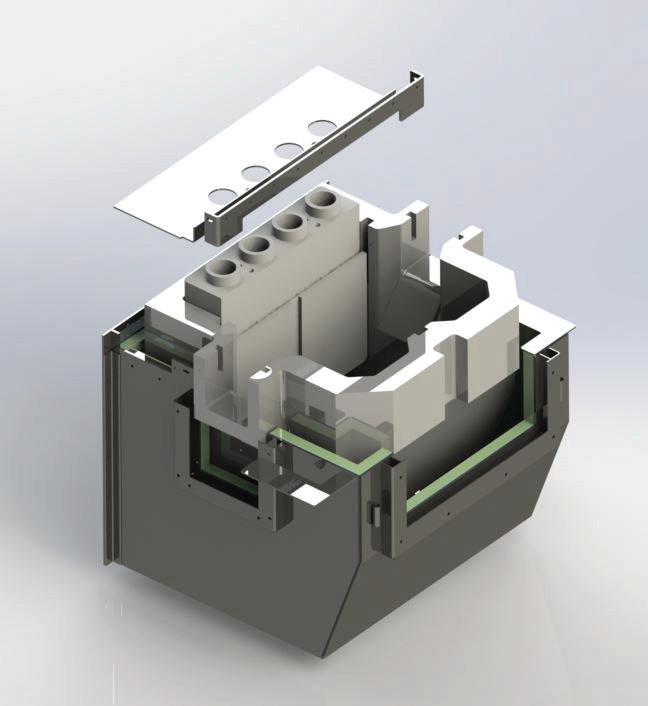
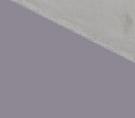
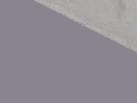
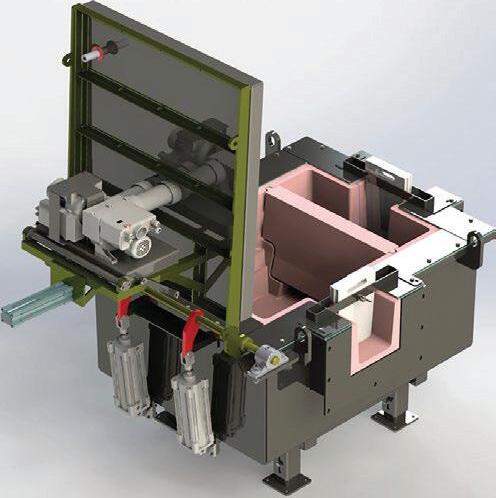




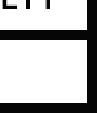
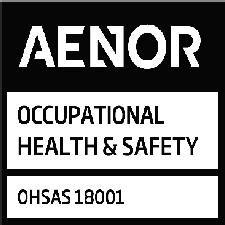


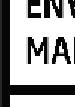
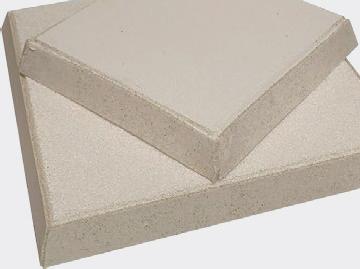
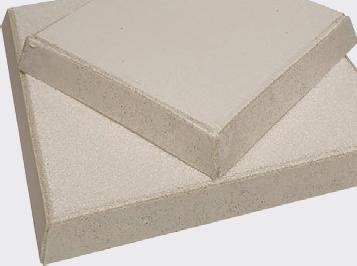

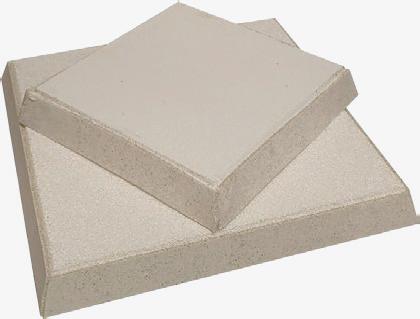
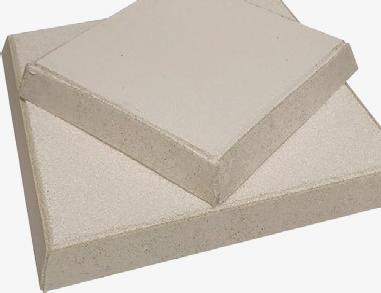
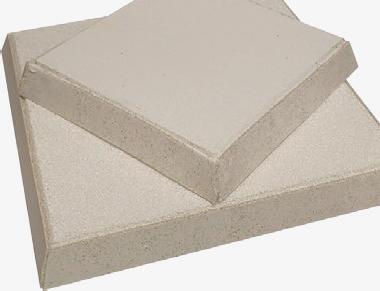
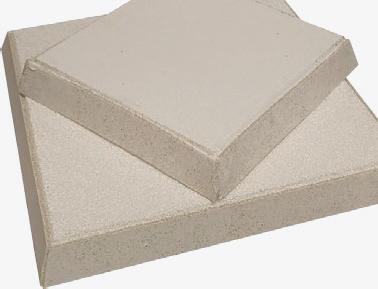


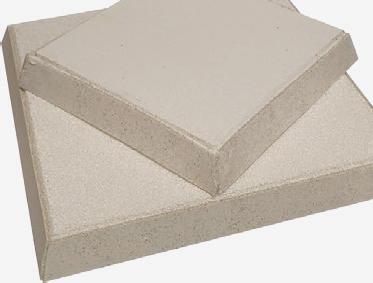
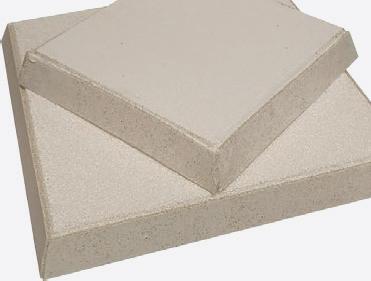
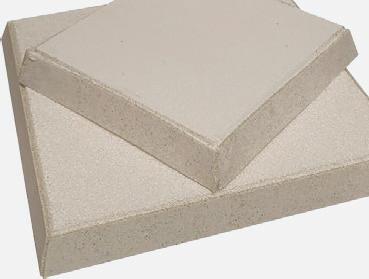
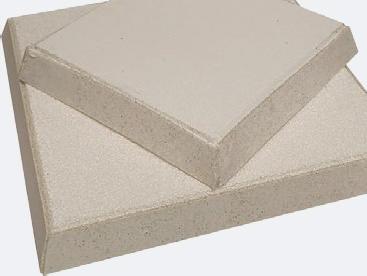
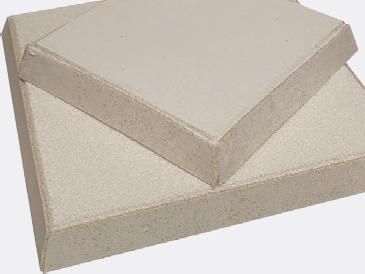
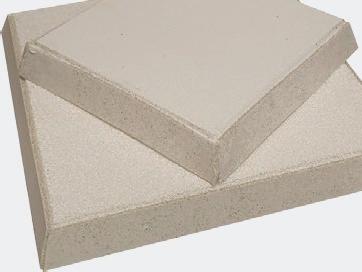

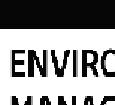



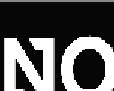
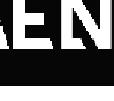

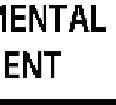

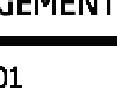

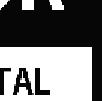

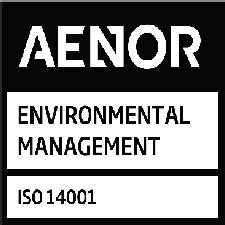

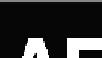

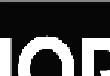
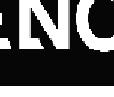
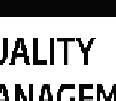


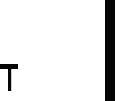
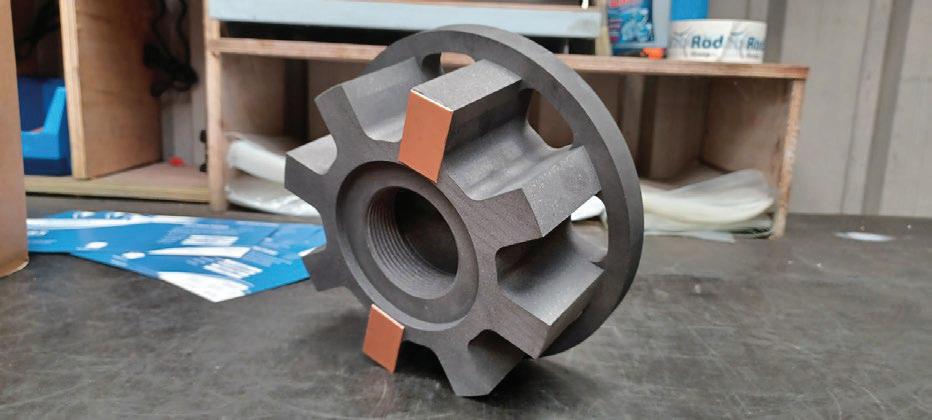
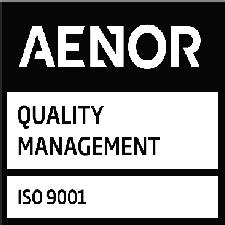



Industry leading RiA Rail Mounted Charging Machines for Multiple Melting Furnace Applications
RIA Cast House Engineering provide railmounted Cast House proven Charging and Skimming equipment for Aluminium Cast Houses worldwide. The design and development of all RiA Machines take reliability, durability, maintenance and occupational safety into account. RiA has supplied over eighty Furnace Charging and Skimming Machines, all rail-mounted and capable of Charging up to 30 Metric Tonnes in less than 90 seconds or Skimming a Furnace faster than a traditional Forklift Truck or wheeled Furnace Tending Vehicle, but with more repeatable results and without damaging the refractory lining. Key customers include Hydro, Constellium, Matalco, and many others. Several clients have multiple Machines in the same Cast House or across multiple sites and territories. One client alone has implemented more than thirty RiA Machines in ten different countries.
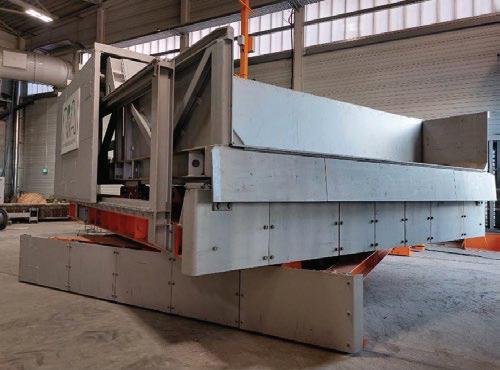
RiA installed their first rail mounted Charging and Skimming Machine pair in 2001, both of which are still in operation today after 23 years of continuous operation. Since this installation, the furnaces supplied to the aluminium remelting market have transformed to satisfy the growing demand for aluminium scrap recycling and the increased recycling of contaminated scrap. RiA’s product offering has grown with the changing landscape of aluminium remelting furnaces and today RiA offer robust and reliable rail mounted Charging and Skimming Machines to serve a varied range of furnace types that includes Multi-Chamber and Tilt Rotary Furnace applications that are now common features of Cast Houses around the world.
RiA Charging Machine for MultiChamber Furnace Applications
RiA rail mounted furnace Charging Machines for Multi Chamber Furnaces typically operate differently to a standard Charging Machine serving a single chamber reverberatory furnace. Smaller volumes of scrap are charged within each charging cycle, however the pushes are more frequent and continuous.
Multi-Chamber Furnaces typically operate with a clean chamber and a dirty chamber which includes a hearth that scrap is charged onto. RiA’s rail mounted Furnace Charging Machine regularly deposits material on to the scrap hearth, pushing the material at the end of the hearth into the bath, therefore creating room on the hearth for the next charge. With such regular charges required when running this type of operation, an efficient and reliable Charging Machine is essential to a productive and efficient operation to ensure cycle times are as fast as possible and

down time is kept to a minimum to allow for a constant feed of input material into the furnace.
Each RiA rail mounted Furnace Charging machine is engineered to serve the furnace(s) they tend, and RiA’s Multi Chamber Furnace Charging Machine is no exception. Our Charging Machine container fills the width and height of the charging door, and the stroke of the container is configured based on the furnace operation and the length of the hearth. Scrap material is then distributed evenly distributed across the length and breadth of the hearth to allow the combustion system access to the material for preheat and removal of contaminants.
The RiA Multi-Chamber Furnace Charing Machine pictured in Figure 1, recently commissioned, swivels 90 degrees, in front of the Furnace. A fume hood connects with the Furnace giving more opportunity to the furnace fume hood to capture any off gases that may leave the furnace when the door opens, can be seen in figure 2. Typically the Charging cycle, the process of adding more material onto the hearth of the furnace is less than 90 seconds, minimising the door opening time and conserving energy.
Although this RiA Charging Machine is serving a Multi-Chamber furnace, the core RiA philosophy remains as the machine is fully automated, without an Operator Cabin, nor Operator onboard. The Charge cycle is initiated from a single push button on a remote Operator Desk in a safe location. Therefore, maximising the safety for operators and ensuring a safe and efficient charge, every time.
RiA Charging Machine for Tilt Rotary Furnace Applications
Building on the knowledge and expertise acquired from RiA’s extensive Charging Machine reference list, in 2023, RiA commissioned their first rail mounted pusher type Charging Machine to serve a Tilt Rotary Furnace. The design and development of all RiA Machines take reliability, durability, maintenance and occupational safety into account. RiA’s pusher type TRF Charging Machine is no different, as you can see in Figure 3.
The machine pictured in figure 3 is designed and engineered to charge up to 10 metric tonnes of material in under 60
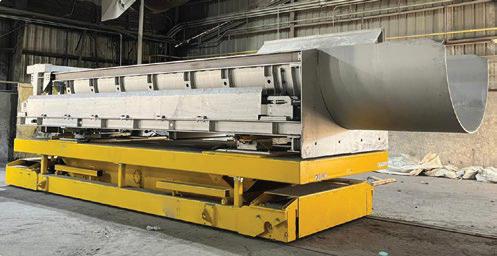
seconds. Conventional methods often consist of charging Tilt Rotary Furnaces with a wheel loader or a vibratory feeder. Wheel loaders are limited by the size of the bucket, typically charging 1 or 2 metric tonnes of material, meaning the charging process takes longer which limits the productivity of the tilt rotary furnace. Using wheel loaders to charge a Tilt Rotary Furnace also requires the operator to be near and in front of the furnace during the charging process whereas with a RiA Tilt Rotary Furnace Charging Machine there is no operator cabin on the machine. Once loaded with the charge material, from the push of a single button the machine will move to the furnace, send a signal to the furnace PLC to open the door, charge the furnace and then move back to the loading position. To avoid any risk loading the machine at height, this machine is equipped with a scissor lift to allow for the machine to be loaded at a safe height.
Above each wheel block the Charging Machine is equipped with load cells, the charge weight is then displayed on a screen nearby the loading position enabling Cast House operators to monitor the scrap weight per charge. This ensures the furnace is being charged with the correct charge weight and ensures it is simple to monitor material flows through the Cast House.
RiA have engineered the adjustable pusher plate of the Charging Machine to fit closely to the inner walls of the charge container and Charging Machine nose to ensure it is possible to charge fine material and even salt using the Charging Machine.
RiA’s electrically driven pusher-type design ensures the highest levels of reliability because it does not use a vibratory method to feed material into the furnace.
RiA provide a remote desk where an operator can view the machines operation from a safe location through a camera mounted on a mast at the rear of the machine. Joysticks are also integrated within the desk to allow for manual movement of the machine if required in maintenance mode for example, however in typical operation the machine operates from the push of a button with no other operator interaction required.
Each RiA rail mounted Furnace Charging machine is engineered to serve the furnace they tend, and the new Pusher Type Tilt Rotary Charging Machines are no exception. The diameter of the furnace door is used to calculate the diameter of the nose of the Charging Machine. With laser positioning, the refractory around the door of the furnace is protected from accidental collisions which can occur when charging dross and scrap with a wheel loader. An operator charging a furnace with a wheeled vehicle does not have the same limits, control and repeatability that a laser positioned rail mounted Charging Machine does. When Charging large pieces of scrap and dross skulls for example, it is inevitable that charging them inside the furnace door on a very frequent basis is going to cause rapid wear of the refractory around the door, potentially impacting the door sealing and therefore furnace performance whilst also leading to regular downtime and expensive repairs.
With Tilt Rotary Furnaces in the market now exceeding 60 metric tonnes in capacity, it Is more important than ever to charge the material in the quickest, safest and most energy efficient way possible.
RiA Charging Machine for Reverberatory Furnace Applications
Parallel to engineering new, efficient and robust Charging Machine solutions for varied furnace applications, RiA have continued to improve and enhance their Charging Machine solutions for single chamber reverberatory furnaces. It is now 25 years since RiA’s first Charging Machine installations, and those machines are still in operation today.
Through continuous development, the machines looks vastly different today and they have the ability to operate autonomously, not only not having an operator on board but utilising In-Furnace smart cameras to monitor the height of the scrap pile within the furnace and signalling to the Charging Machine to charge the furnace at the earliest and safest time, every time. Ensuring maximum throughput of material into the furnace whilst safeguarding operators.
RiA have now successfully designed and installed Charging Machines with a capacity of 30 metric tonnes of scap material that can be charged into a furnace in less than 90 seconds. The machine pictured in Figure 4 charges 20 metric tonnes in less than 90 seconds, considerably faster than if that volume of material was to be loaded with a fork lift truck or wheel loader, all without an operator needing to be on the machine or exposed to the potential hazards that charging a furnace can pose.
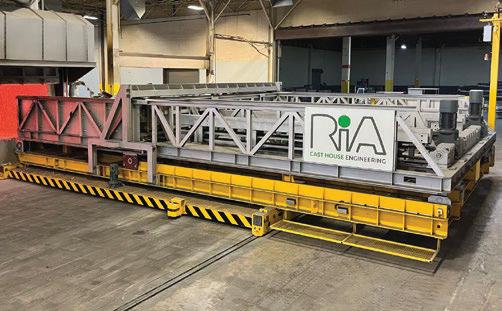
Whilst furnace configurations have changed in recent years, so have the size of furnaces, and RiA now supply Charging Machines that are serving furnaces in excess of 120 metric tonnes. Furnaces of this size have wide doors and deep hearths so it is vital that the Charging Machine serving the furnace has sufficient stroke to penetrate deep into the furnace to deliver the charge evenly from the very back, right to the front, to ensure a shallower scrap pile with a larger surface area to achieve the fastest melt rates. The growth of RiA Charging Machines has been simultaneous with the growth of melting furnaces as end users and furnace suppliers understand the need to have efficient and safe furnace charging practices when charging increased amounts of scrap into larger furnaces.
Come and see us at our stand to discuss how our rail mounted Charging and Skimming Machines can benefit your Cast House operation at ALUMINIUM Dusseldorf.
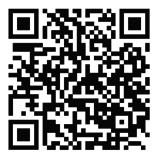

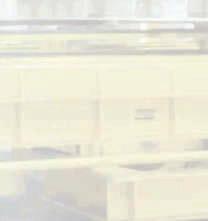
AUTONOMOUS
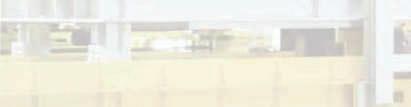
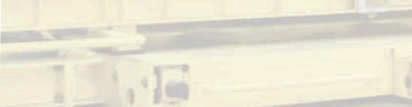
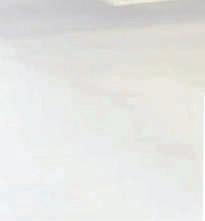
CHARGING & SKIMMING MACHINES
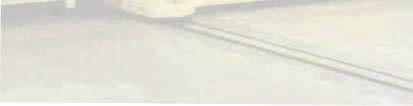
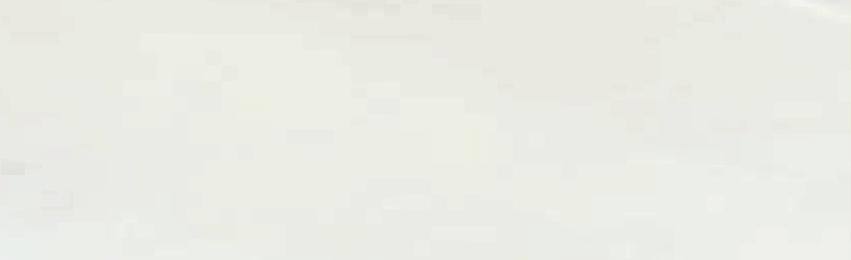
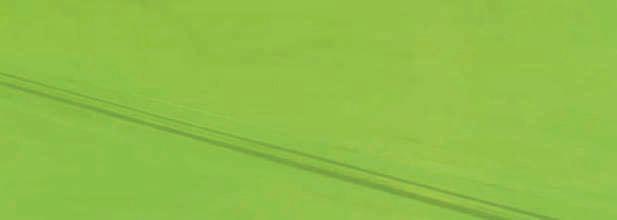
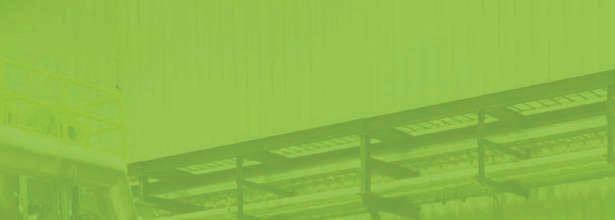


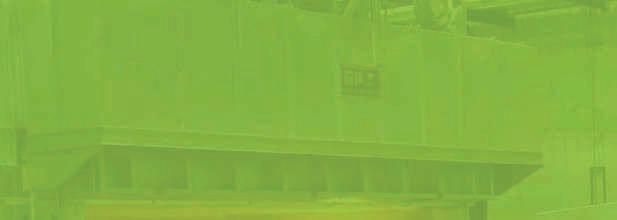


Storvik ICON: Pioneering Removal of Alkaline Metals in Primary Aluminium Production
As we prepare for ALUMINIUM 2024 in Düsseldorf, we are excited to share the groundbreaking progress of the Storvik ICON system—a new sustainable method to remove alkaline metals from primary aluminium while simultaneously reducing the transfer time from primary metal to the casthouse.
In developing this patented technology, Storvik collaborated closely with Enova and Hydro Aluminium to fine-tune the equipment and demonstrate the process to potential clients. This ecosystem, comprising funding, client partnerships, and our R&D team in Sunndalsøra, has been instrumental in refining the technology to an industrial-ready stage for a global launch. Early client involvement and Enova’s support have been crucial in keeping Storvik at the forefront of sustainable innovations and solutions. We believe this collaborative approach will continue to be pivotal in achieving our sustainability goals and helping the aluminium industry reach net-zero emissions by 2050.
Now, what sets ICON apart and positions it as an innovative replacement for traditional alkaline removal stations, such as RAM or TAC stations commonly found in modern primary smelters?
The Challenge:
In aluminium production, alkaline metals such as sodium (Na) and calcium (Ca) pose significant challenges. Traditional removal systems, typically standalone stations or furnaceadded fluxes, , conducting the removal process inside the crucible or furnace, are proven technologies but have limitations. These limitations include high environmental impact, significant investment costs, and high-risk operations requiring meticulous health, safety, and environmental (HSE) planning. If not conducted correctly it can result in cracks in aluminium billets or slabs, beyond operational control. Cracks can cause sever issues during the rolling and extrusion process.
The Storvik ICON Solution:
So why do we need new systems to remove alkaline metals from primary metal? Traditional systems are relatively inefficient in fluorine usage, resulting in high operational costs and a larger environmental footprint. Traditional systems are also very maintenance intensive and introduces HSE hazards, creating potentially dangerous working conditions. Consequently, the overall cost of traditional systems puts pressure on the aluminium price.
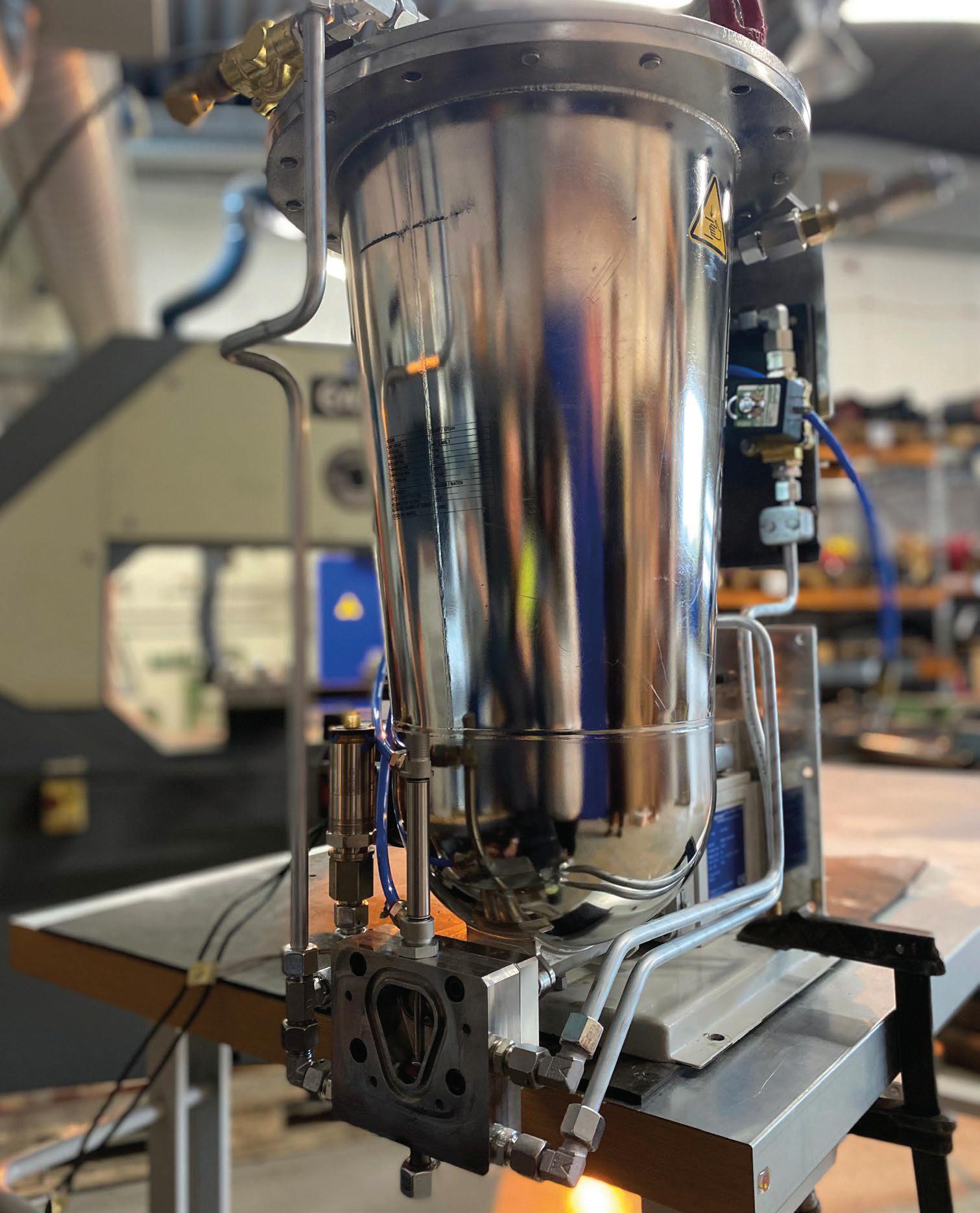
Storvik’s ICON system is a game-changer. Unlike traditional systems, ICON integrates into a tapping device, initiating the removal of alkalines during the hot metal tapping process and not at a later stge in the process. Since pilot testing began in 2021, ICON has shown promising metallurgical results, matching or outperforming state-of-the-art equipment. Despite initial challenges and an extended prototype development period, by the end of 2023, we achieved consistent results under predictable conditions, marking a significant milestone taking the prototype out of its development stage and into a new area of industrialisation and industrial testing over the next months.
Innovative Technology:
The core innovation of ICON lies in its use of inert gas mixed with aluminium fluoride, introduced into the liquid aluminium during tapping. This process initiates a significantly improved chemical reaction, effectively removing alkalines and reducing the risk of cracks. Operating during the tapping process represents a significant advancement in aluminium production technology, with positive impacts on HSE, material efficiency, and the reuse of collected material in the electrolysis process.
Sustainability and Efficiency:
ICON is not just a technological breakthrough; it is a step towards a more sustainable future. The closed system design significantly reduces heat loss and energy consumption. By limiting exposure to the outside environment, ICON minimises potential contamination, enhancing the quality of aluminium produced. This closed system also improves operator health and safety by reducing exposure to harmful elements. Furthermore, the improved chemical reaction during the tapping process delivers high-quality aluminium with a lower environmental footprint.
Storvik’s Legacy and Global Expansion:
Storvik has a long-standing history of excellence and innovation in the aluminium industry. Founded in 1913, Storvik has grown from a local enterprise to a global leader. Our strategic locations next to partners and clients in Norway, Eastern Europe, Iceland, and North America have fostered a robust network, enabling close collaboration on developing and testing new solutions. Over the years, Storvik has expanded its global presence, providing top-ofthe-range solutions for green anode production, rodding shops, electrolysis, and casthouses to clients worldwide. Our commitment to innovation and quality has driven us to continually push the boundaries of aluminium production processes. This dedication has positioned Storvik as a trusted partner in the industry, known for delivering reliable and efficient solutions.
Showcasing at ALUMINIUM 2024:
At ALUMINIUM 2024, Storvik will showcase its groundbreaking products for primary and recycled aluminium production, emphasising our continuous R&D efforts and commitment to reducing our environmental footprint. The ICON system will be a highlight, demonstrating our dedication to advancing technology and sustainability in aluminium production. We will also present a selection of products from our cast products department and new technologies for crucible cleaning, green anode production, and efficient rodding line solutions. As Storvik continues to push the boundaries of innovation in aluminium production, the ICON system stands as a testament to our commitment to quality, sustainability, and technological advancement.
We invite you to visit our stand at ALUMINIUM 2024 in Düsseldorf to learn more about ICON and our other pioneering projects. Our team will be available for in-depth discussions and presentations, showcasing why Storvik is a valued partner to clients worldwide.
SCAN HERE TO FIND OUT MORE

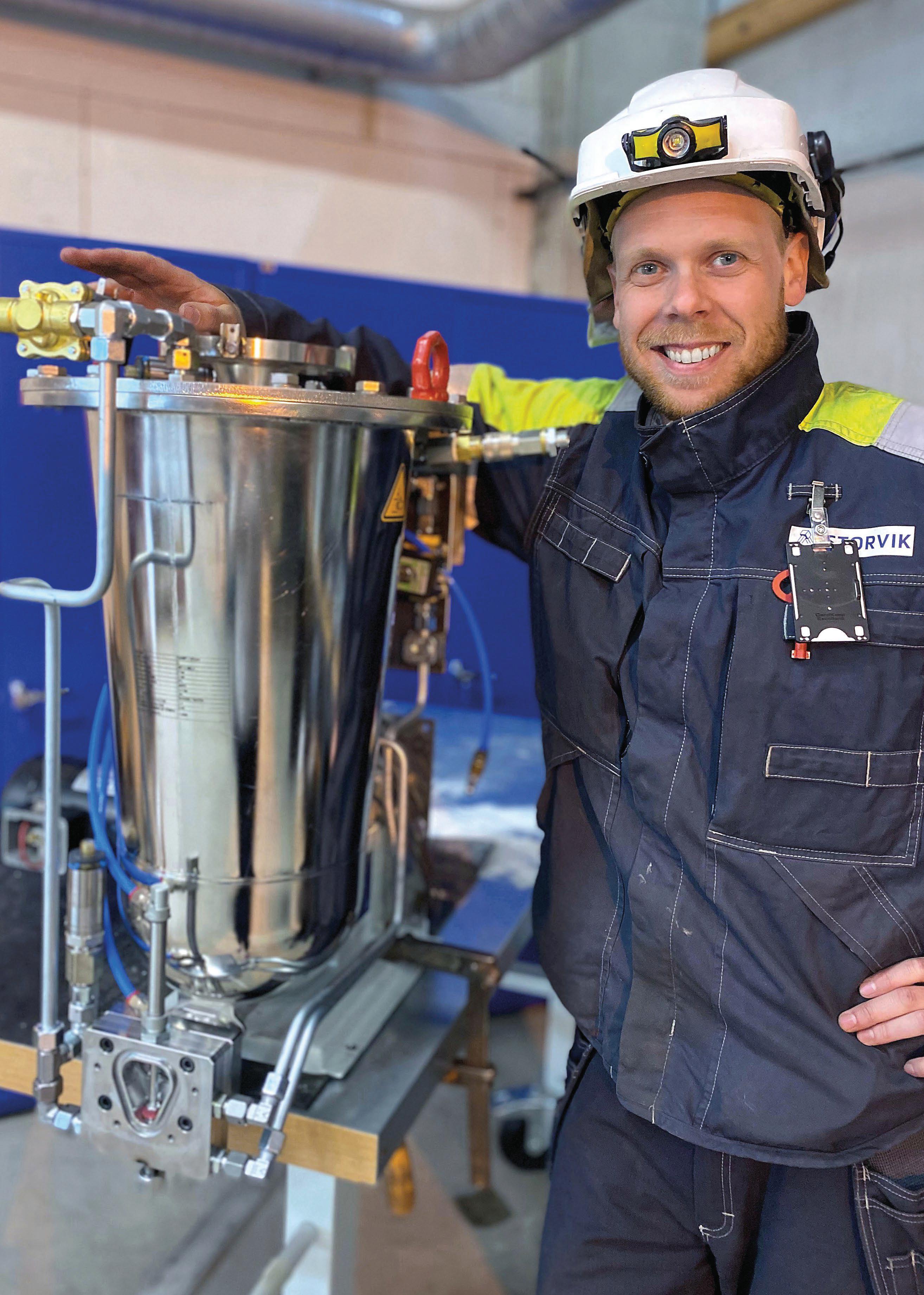


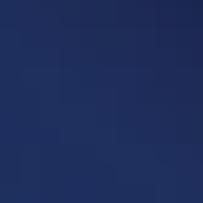
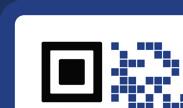

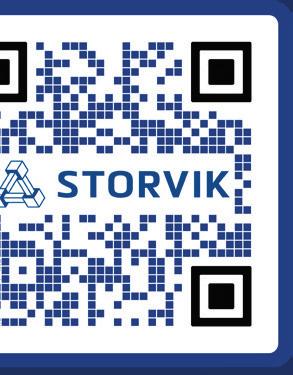
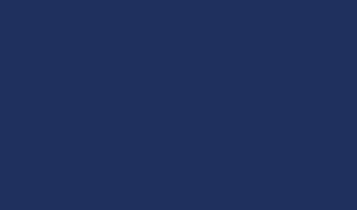
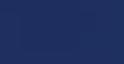

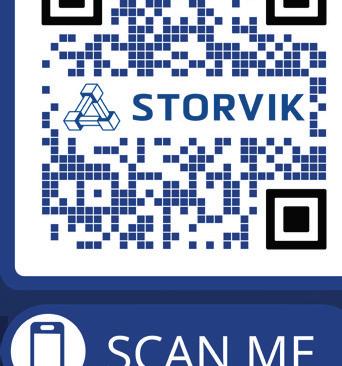




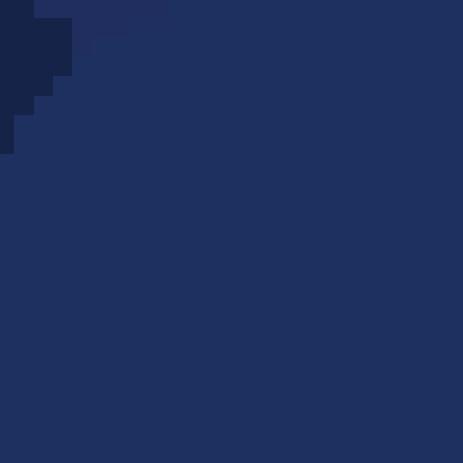

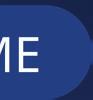

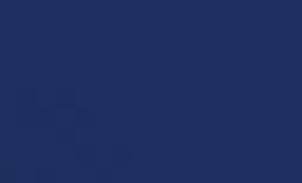
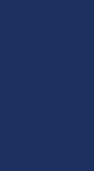
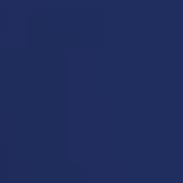
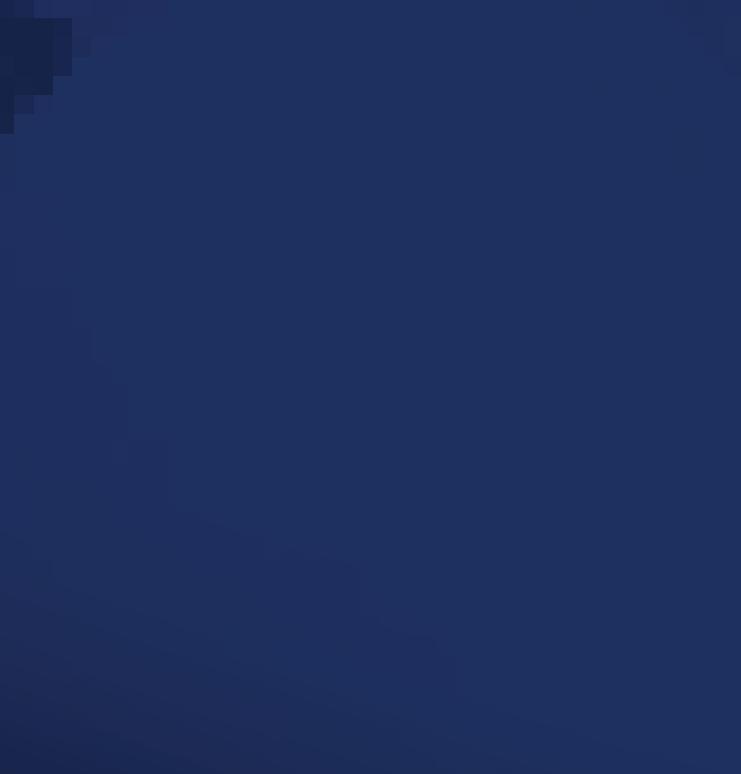



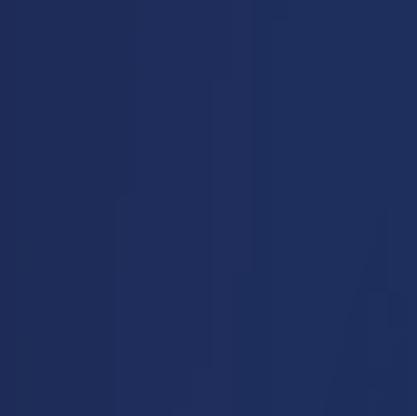
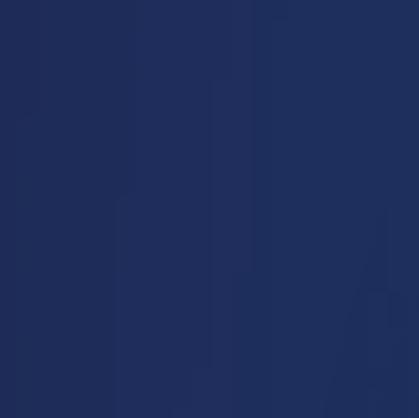
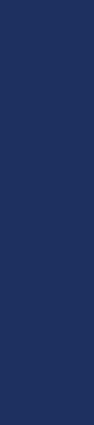
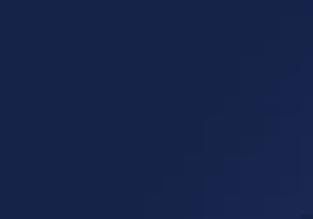
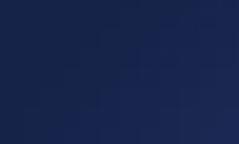
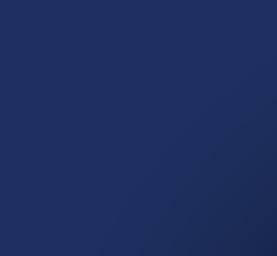

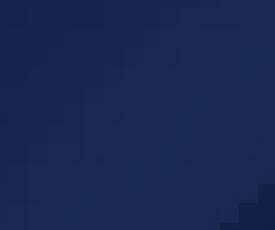

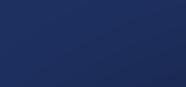
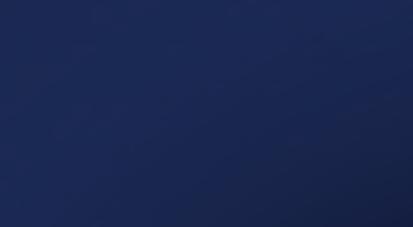

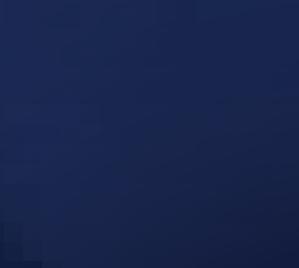
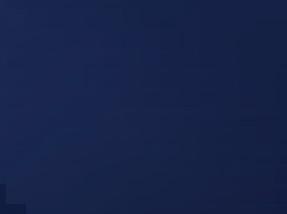

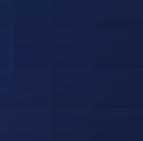
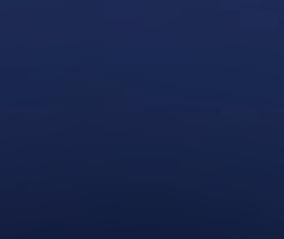
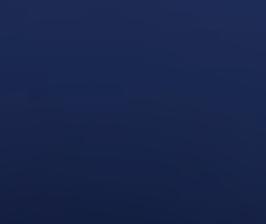



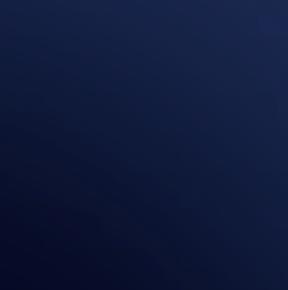
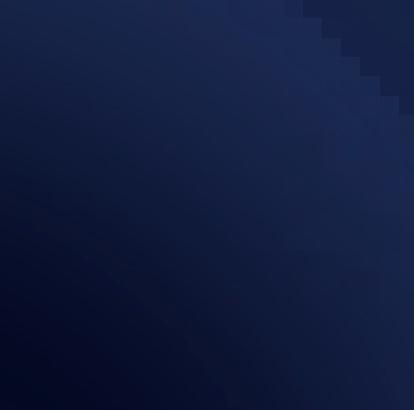
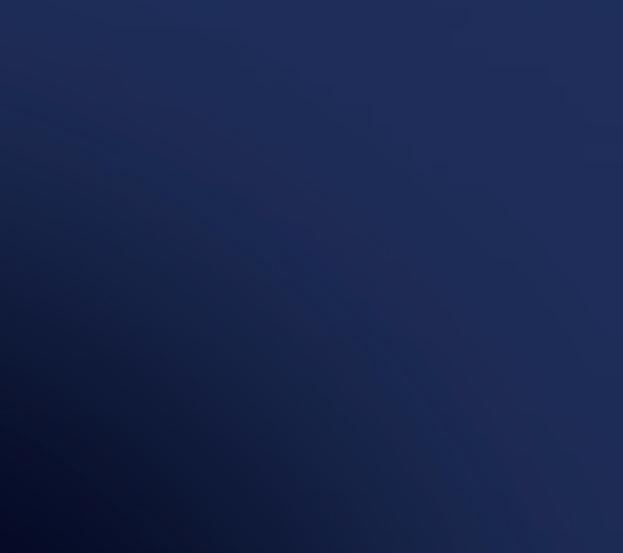
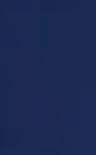
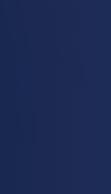

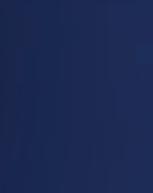

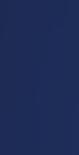
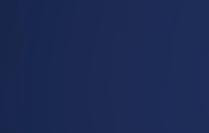

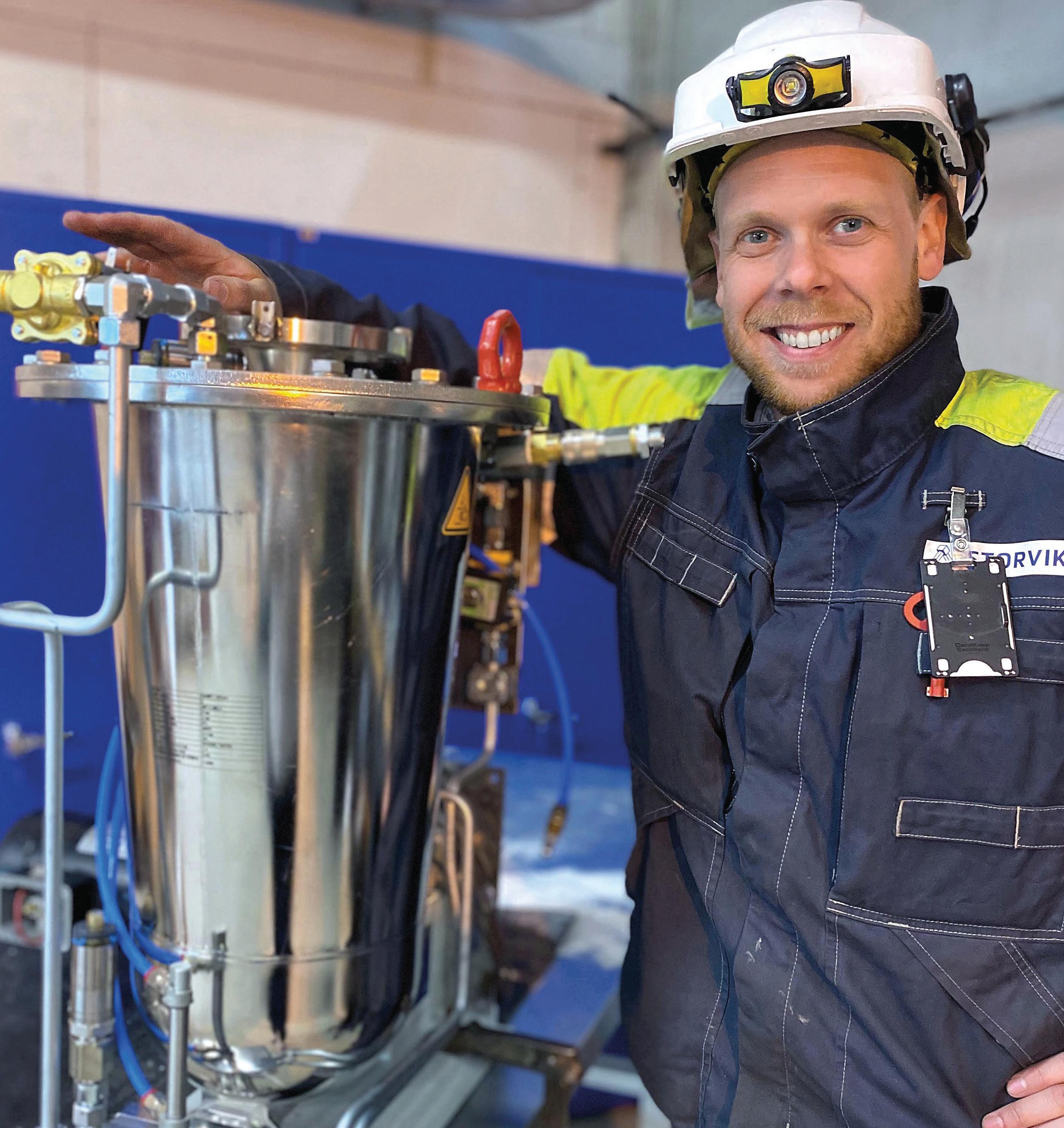

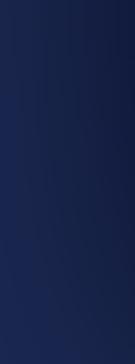


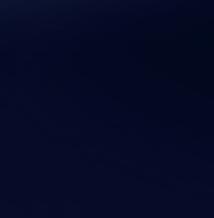
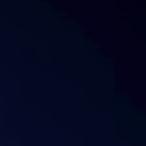
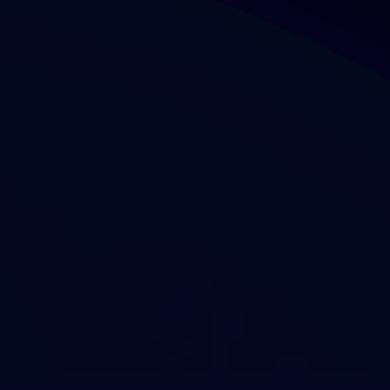
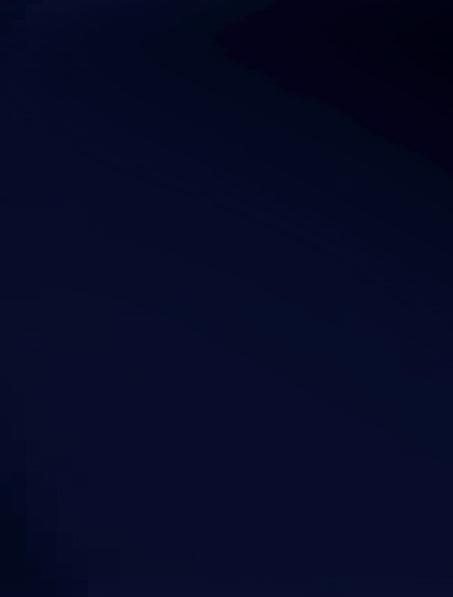


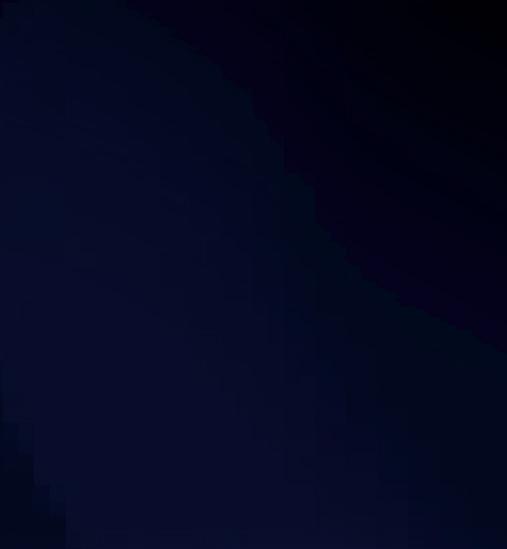
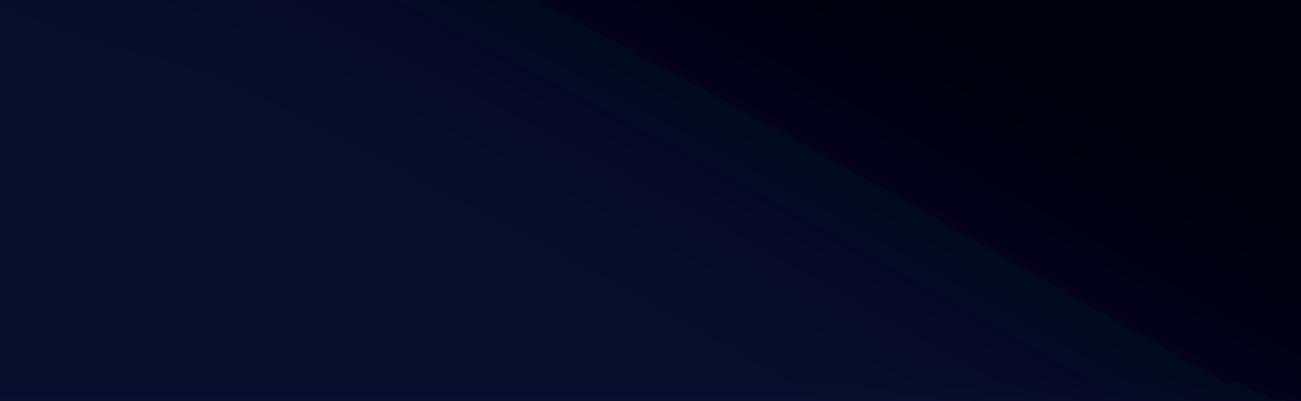
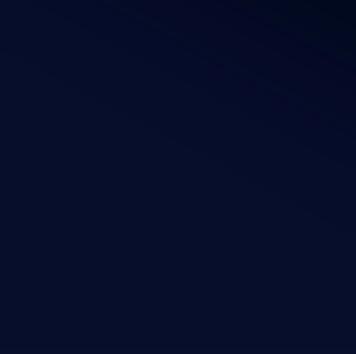
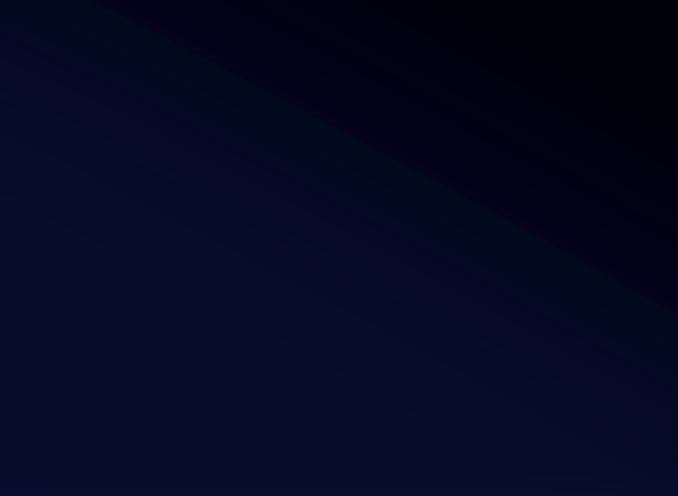
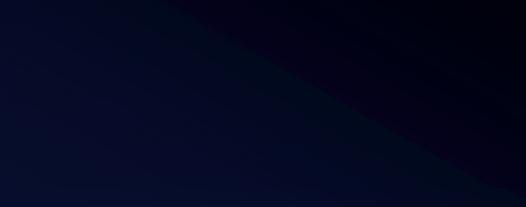

SUSTAINABLE SOLUTIONS SINCE 1913
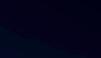
VIG Metal: Leading the Sustainable Industry of the Future


In today’s industrial and manufacturing landscape, sustainability, environmental impact, and economic efficiency have become the most critical factors determining businesses’ growth strategies. In this context, Vig Metal, a leading producer of sheets and coils from lightweight metals such as aluminium and magnesium, has taken its place among the pioneers of our sector through its investments and policies. With our high-quality aluminium production, environmental consciousness, and social responsibility, we stand out not only as a producer but also as an innovative force shaping the future. We increase our investments in a sustainable future every year and offer powerful solutions to our business partners with the industry’s most efficient management systems.
As Vig Metal, we play a significant role in aluminium production with our four casting lines, each with a capacity of 40,000 tons. During the production process, we use state-of-the-art casting lines and cold rolling systems, employing environmentally friendly methods to produce high-quality flat products while prioritising occupational safety. As we expand our production volume, we increase employment rates and support the development of our employees through quality training.
In this way, while producing at a scale that meets the demand in the aluminium sector, we also offer our customers various innovative and sustainable solutions. The machines used on our production lines are manufactured in-house and equipped with advanced automation systems. This minimises human error and aims to reduce work accidents to zero. With over 30 years of experience, we are moving forward confidently into the future with the strong relationships we have built with both our employees and our industry partners.
Renewable Energy Investments
As Vig Metal, a significant part of our environmental stance consists of our investments in renewable energy sources. By completing our solar farm project, we have created a structure that can meet 100% of our electricity consumption, thus preserving our commitment to sustainable energy. With the
installation of a 14 MW capacity solar panel facility, we have managed to significantly reduce our carbon footprint by decreasing our energy costs. This investment not only contributes to our company’s sustainable growth goals environmentally but also financially. Renewable energy usage has become a major competitive advantage for many companies today. With our investments in this area, Vig Metal is taking significant steps towards becoming an environmentally conscious company and aims to set an example for the sector.”
“Environmental Awareness and Certified Production
As Vig Metal, we produce according to international standards such as ISO, CE, REACH, and RoHS. We ensure that our processes comply with international certifications in various areas such as avoiding the use of prohibited or restricted products in our systems, producing in accordance with environmental management systems, and protecting occupational health and safety. At the same time, we are in the process of obtaining various certifications to maximise environmental awareness. We are conducting the necessary studies for LCA (Life Cycle Analysis) and EPD (Environmental Product Declaration) certificates. These certificates demonstrate that our company’s production processes minimise environmental impacts and that we have a sustainable production understanding, while also documenting that the materials we use are inspected and that we have taken the necessary measures regarding occupational safety. The processes implemented in this manner ensure that we act with an environmental responsibility perspective not only in terms of product quality but also in terms of production methods and waste management. As Vig Metal, we continue to demonstrate our environmental awareness by accelerating our efforts to obtain these certifications.”
Global Vision and Export Volume
In line with our growth targets, we attach great importance to exports. Our company holds a strong position in the international market with an export ratio reaching up to 85%. This not only strengthens our financial health but
also enhances our brand’s global impact. Our overseas investments and global partnerships form an integral part of our sustainable business approach. By successfully implementing our export strategies, we consider expanding markets and customer portfolios abroad, and diversify our products to suit these markets. In this way, we can more effectively meet the needs of customers in different countries and regions.
equality, protection of employee rights, and fair management, fulfilling our commitment to constantly updating our ethical policy.
As Vig Metal, we continue to pursue our growth goals by adhering to sustainability principles in a wide range of areas, from production to environmental awareness, from social responsibility to renewable energy usage. By following technological developments and environmental standards
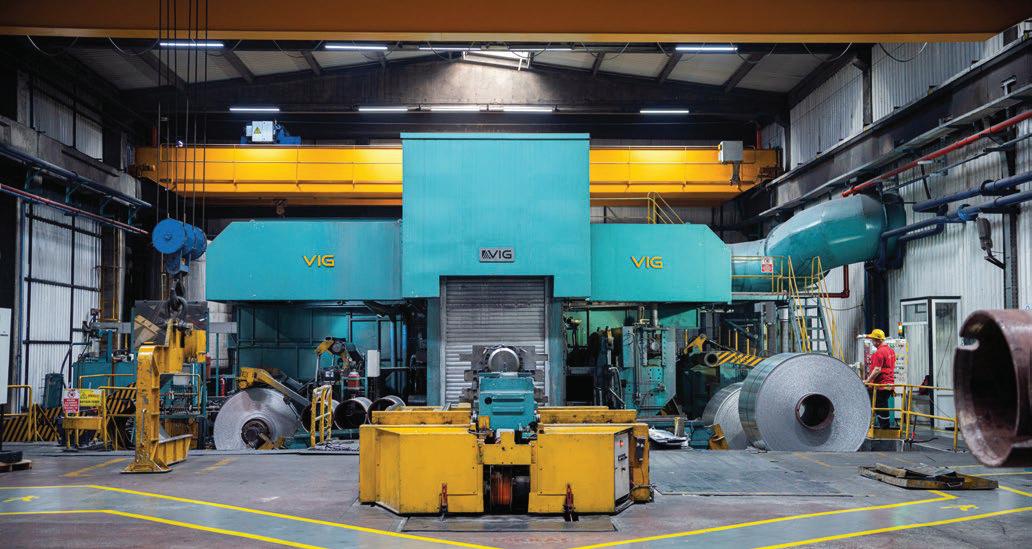
Social Responsibility and Ethical Policies
At Vig Metal, we not only prioritise environmental sustainability but also place great importance on our social responsibilities. The ethical policy guidelines we have established within our company aim to protect the rights of our employees, provide equal opportunities, and prevent discrimination. In this context, we continuously organise training and awareness programs to ensure fair treatment of all our employees. Moreover, we emphasise women’s employment and increase the number of our female employees every year.
This ethical policy demonstrates that our company is not just a workplace but also an organisation that acts with a sense of social responsibility. This policy creates a safe and supportive working environment for our employees, forming a crucial part of our strong commitment to occupational health and safety. We continuously increase the support we provide to our employees regarding social
in the sector, we act with a consciousness of protecting not only our own gains but also our natural and social environment.
With our goal of becoming a brand that can meet the needs of the future, we set an example for other companies in the sector with our steps in the field of sustainability and aim to leave a greener legacy for the future with environmentally friendly solutions.
Vig Metal’s success is shaped by both its environmentally friendly production approach and its sense of social responsibility. In this sense, our company is not just an aluminium producer but also a visionary working for a sustainable future. These steps taken for the future will serve as an example not only for the sector but also for the whole world.”
SCAN HERE TO FIND OUT MORE
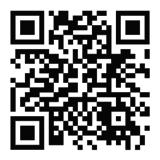
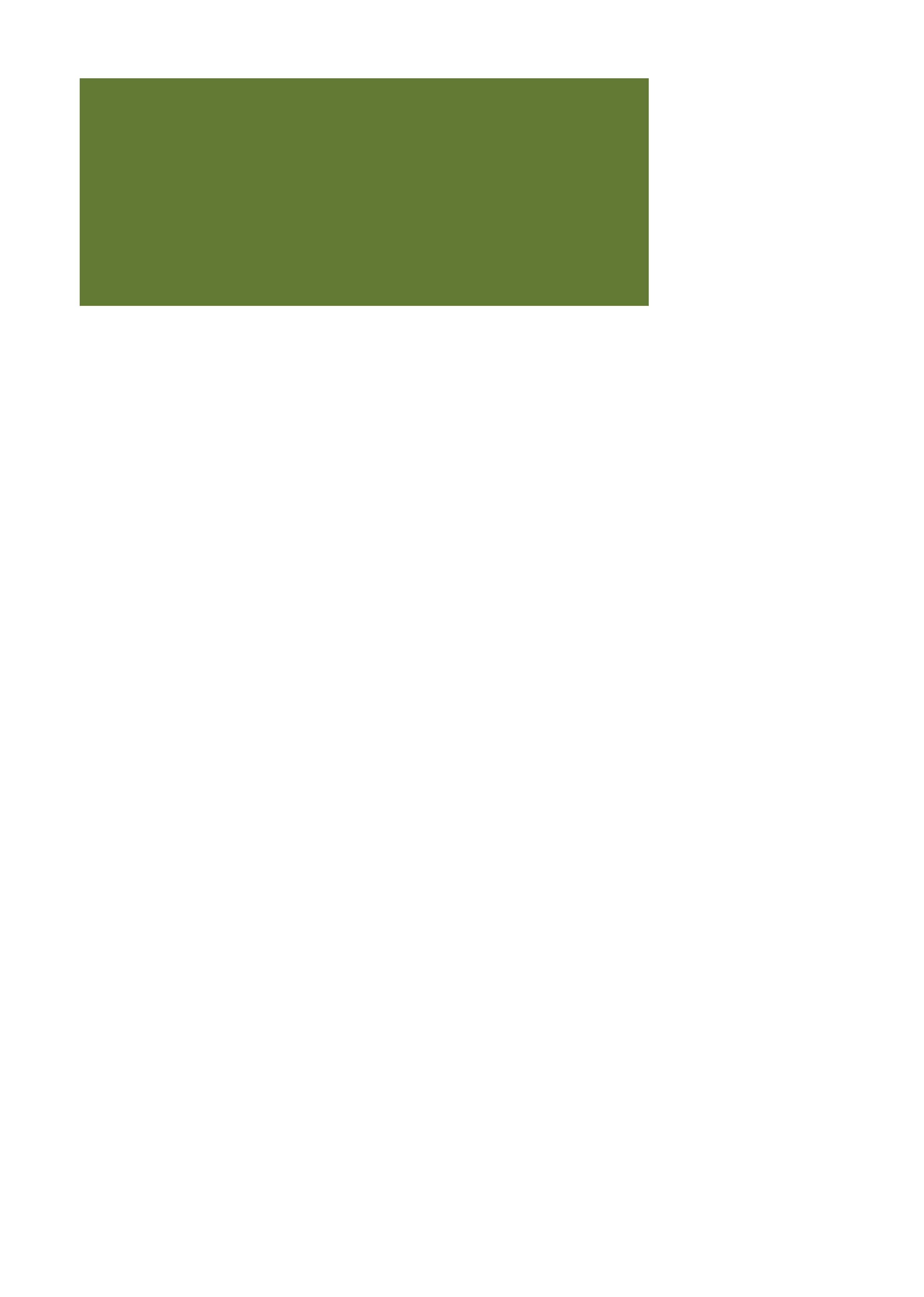
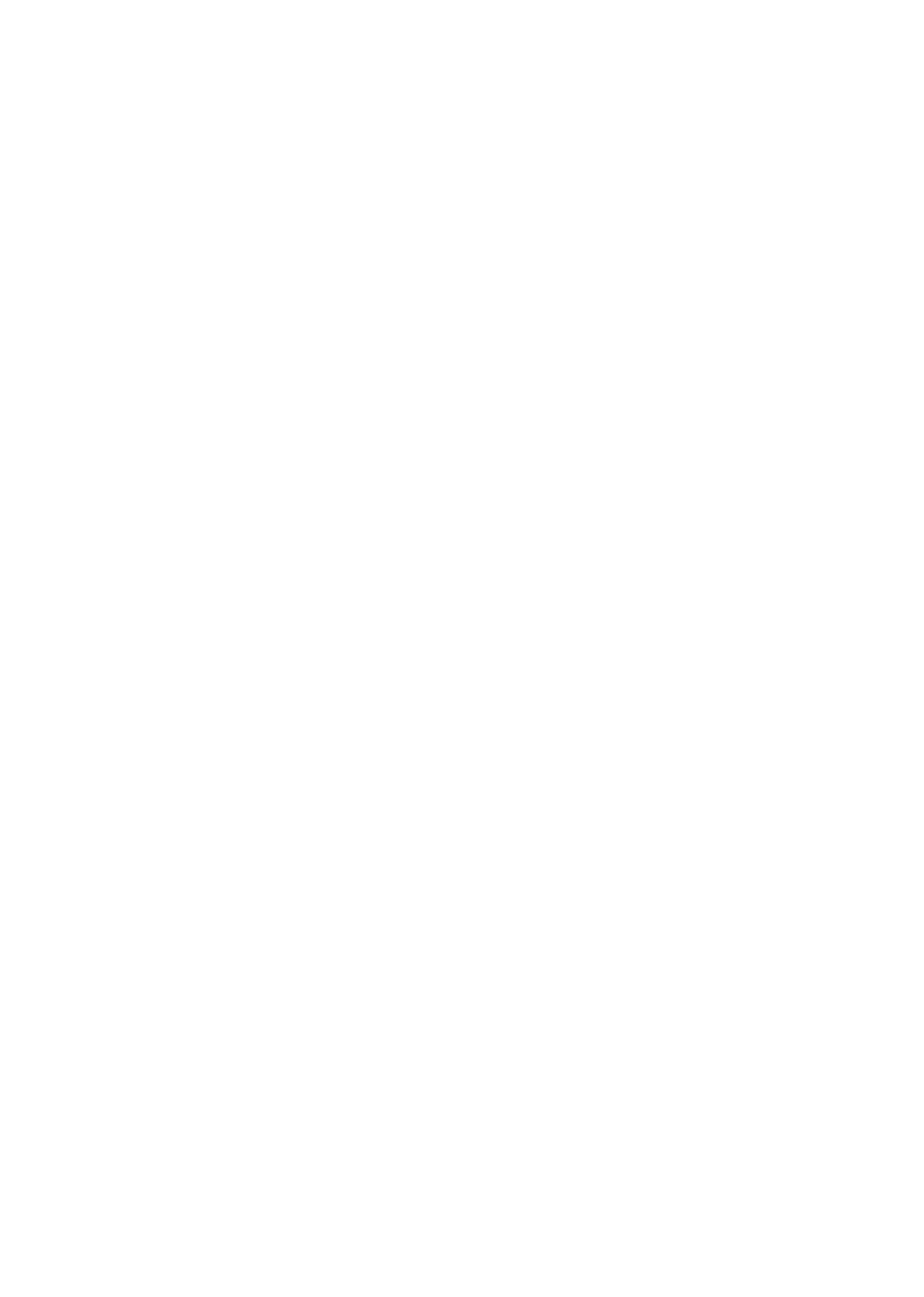
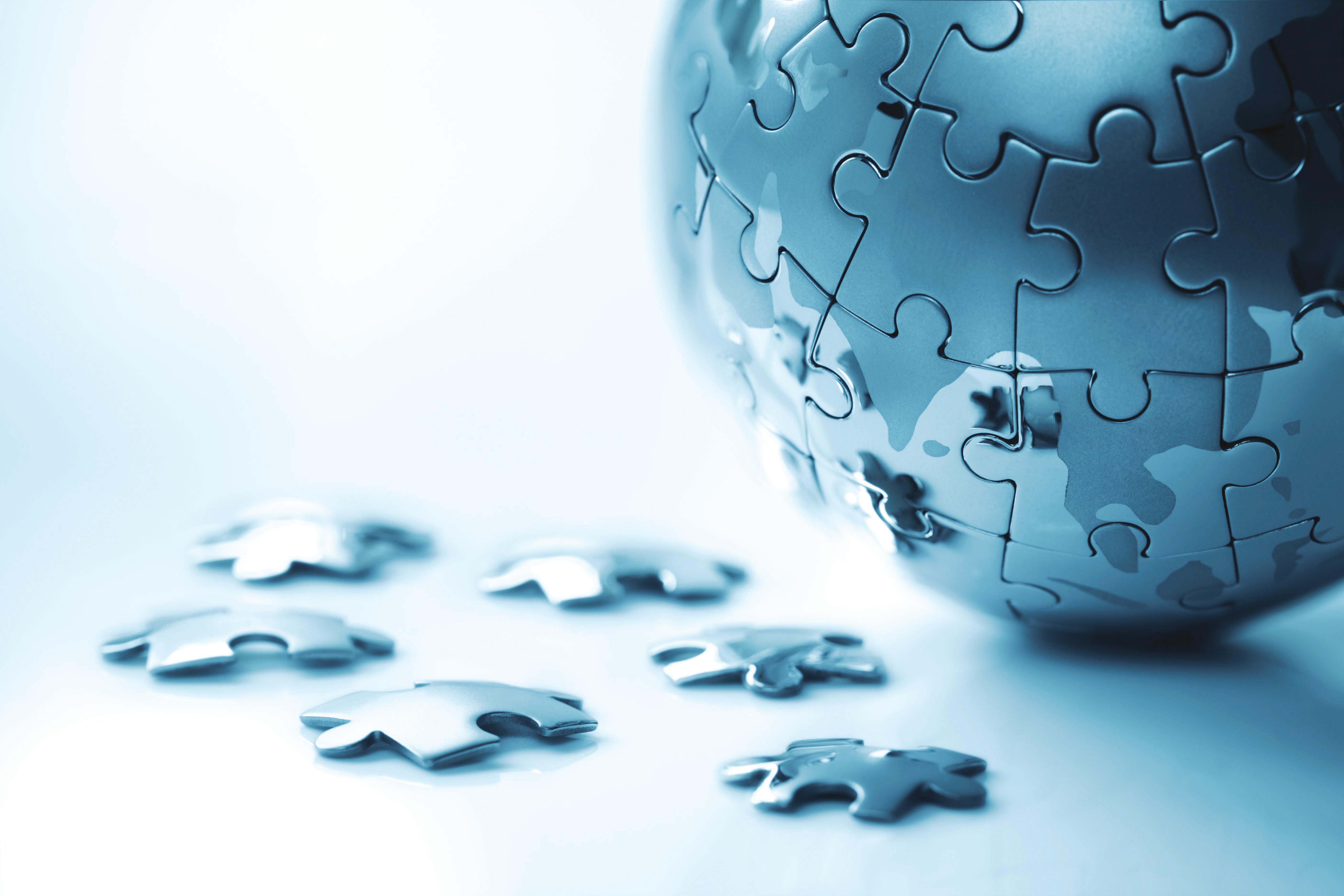
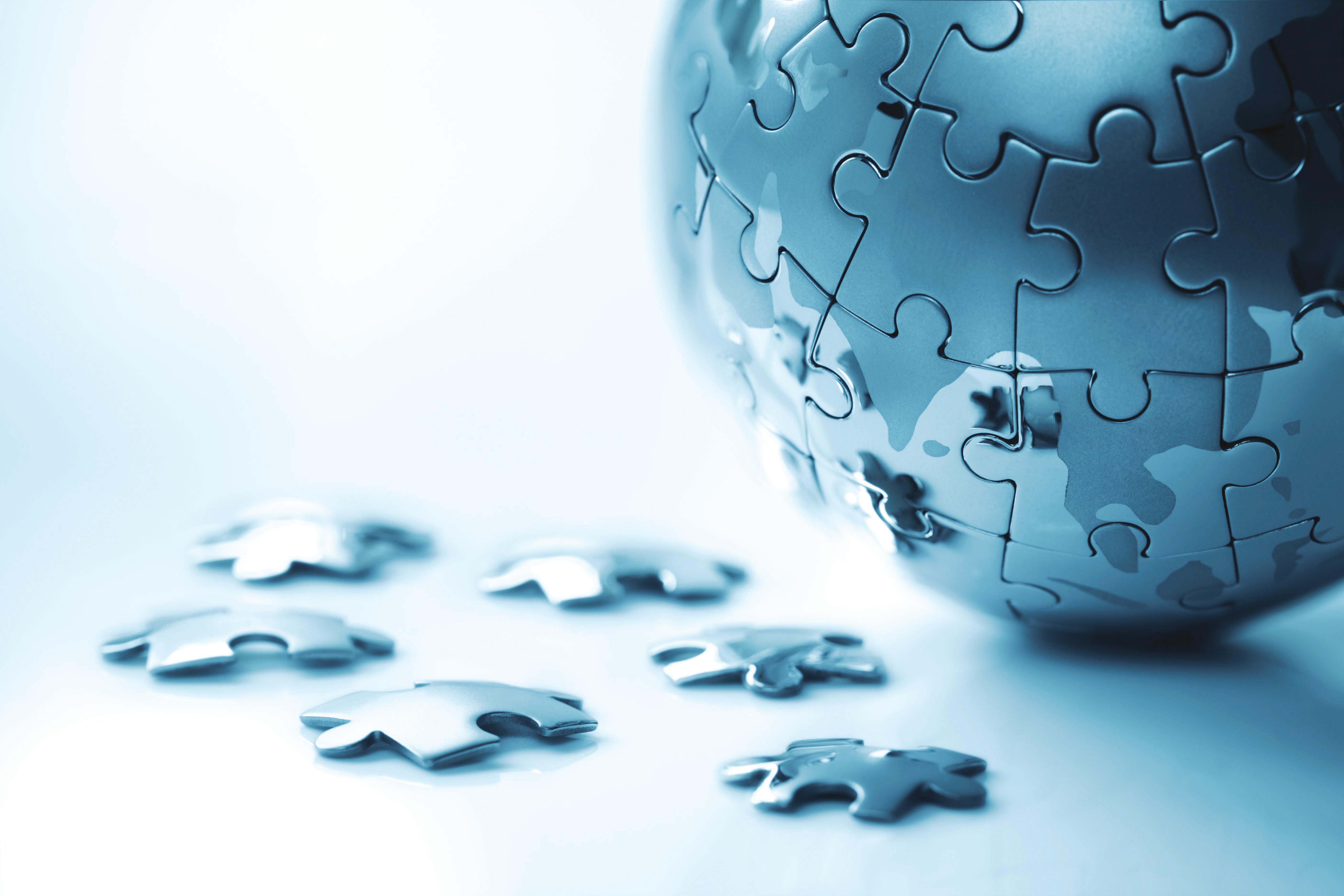
The Alutrends Report
Aluminium International Today proudly unveils the Alutrends Report 2024, a comprehensive exploration of the aluminium industry’s journey towards sustainability and innovation.
The report delves into the latest trends, technological advancements, and key sustainability initiatives shaping the aluminium sector. Featuring insights from industry leaders, its purpose is to delineate the crucial trends that will steer and transform the aluminium industry in the year ahead.
The report is poised to deliver in-depth insights into the forces that will shape our industry's trajectory in 2024 and focuses on pivotal areas such as challenges in recruitment and resources, technological advancements, and the imperative shift towards sustainability, and will spotlight the strategies businesses need to adopt to navigate
these evolving landscapes successfully.
"Aluminium’s role in the green energy transition takes centre stage," says Nadine Bloxsome, Editor of Aluminium International Today. "From wind turbines to electric vehicle chassis, aluminium’s properties are driving the shift towards a sustainable future."
The Alutrends Report 2024 is an essential resource for industry professionals seeking to stay ahead of the curve in sustainability and innovation.
In the dynamic landscape of commodities, where trends ebb and flow like currents in the market, sustainability stands out as an unwavering force, reshaping industries worldwide.
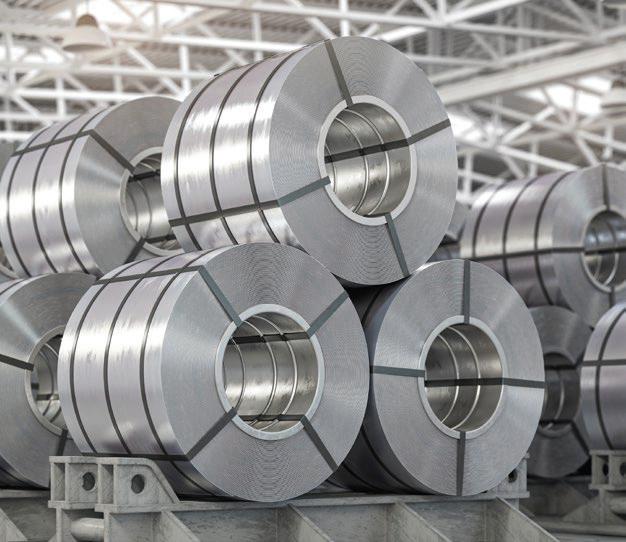
As the report explores the world of aluminium, it is apparent that sustainability isn’t merely a trend, but a pivotal driver steering its course in 2024 and beyond.
The 2024 report aims to navigate the currents of change within the global aluminium industry, with a keen focus on sustainability and the areas of the supply chain currently leading the way.
“Aluminium
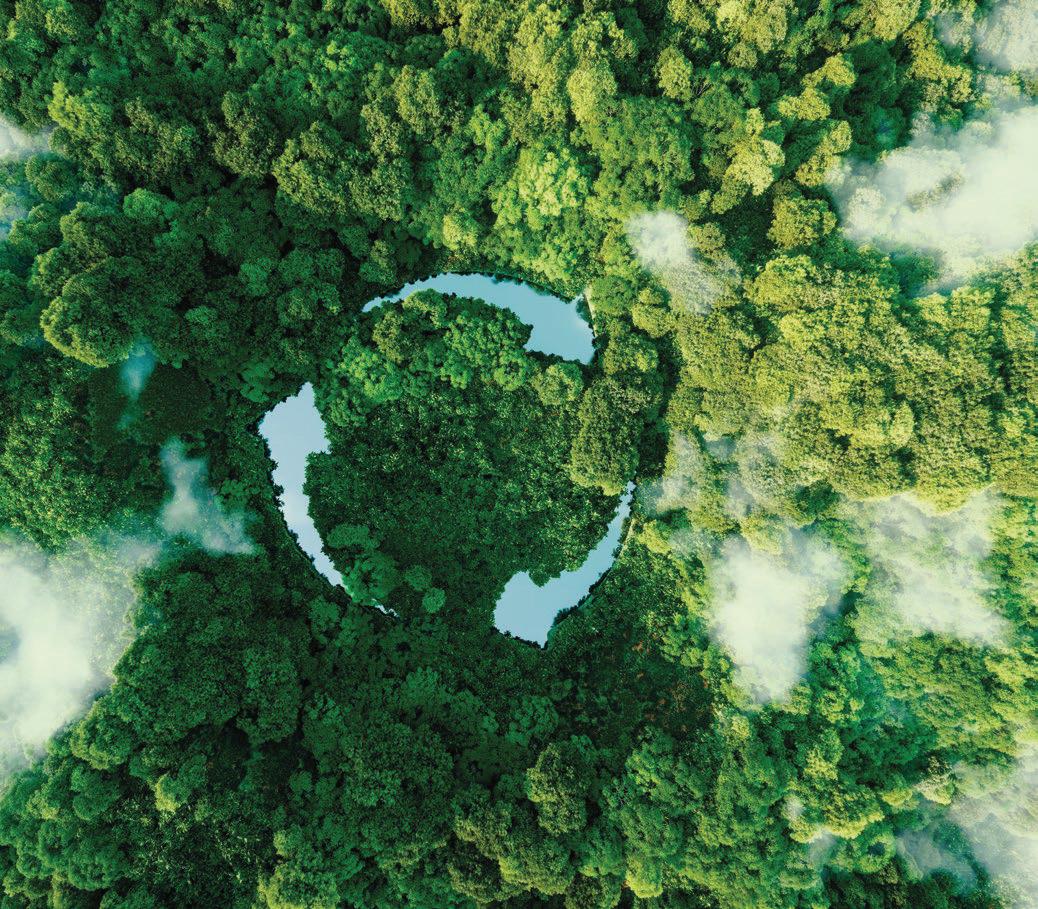
is critical to transitioning to greener and circular economies, given its use in electric vehicles, wind and solar power, electricity cables, and battery storage…” (Page 10)
Aluminium International Today presents the Alutrends Report 2024, an in-depth exploration of the aluminium industry's path to sustainability and innovation. This comprehensive report features insights from industry experts, covering the latest trends, technological advancements, and key sustainability initiatives shaping the future of aluminium production. Visit us at Stand
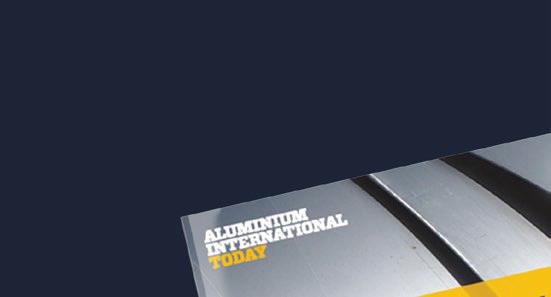
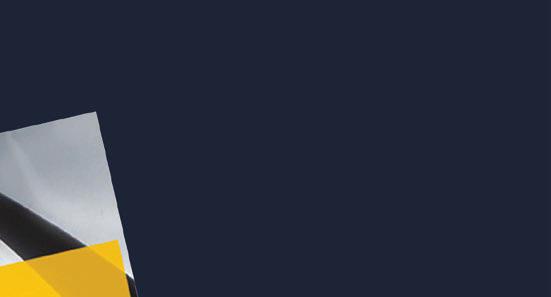
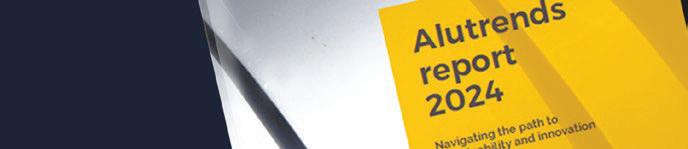

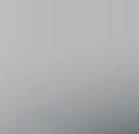

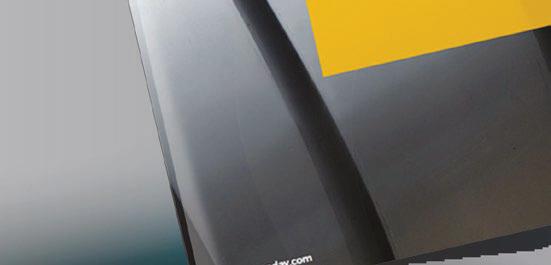

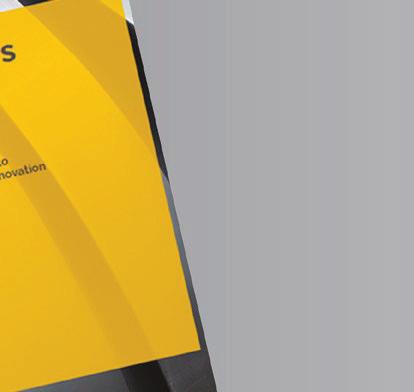
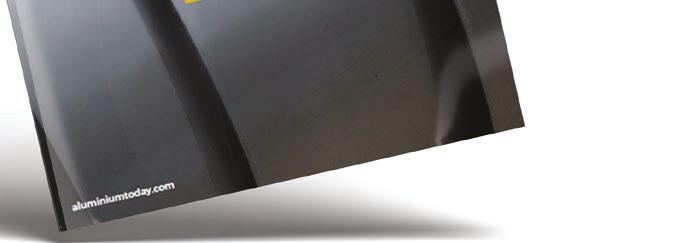
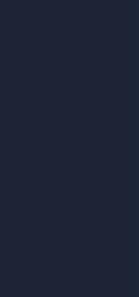
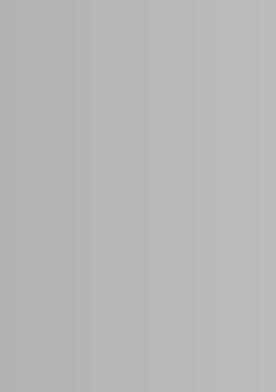
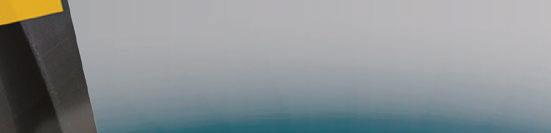
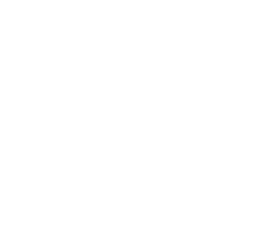

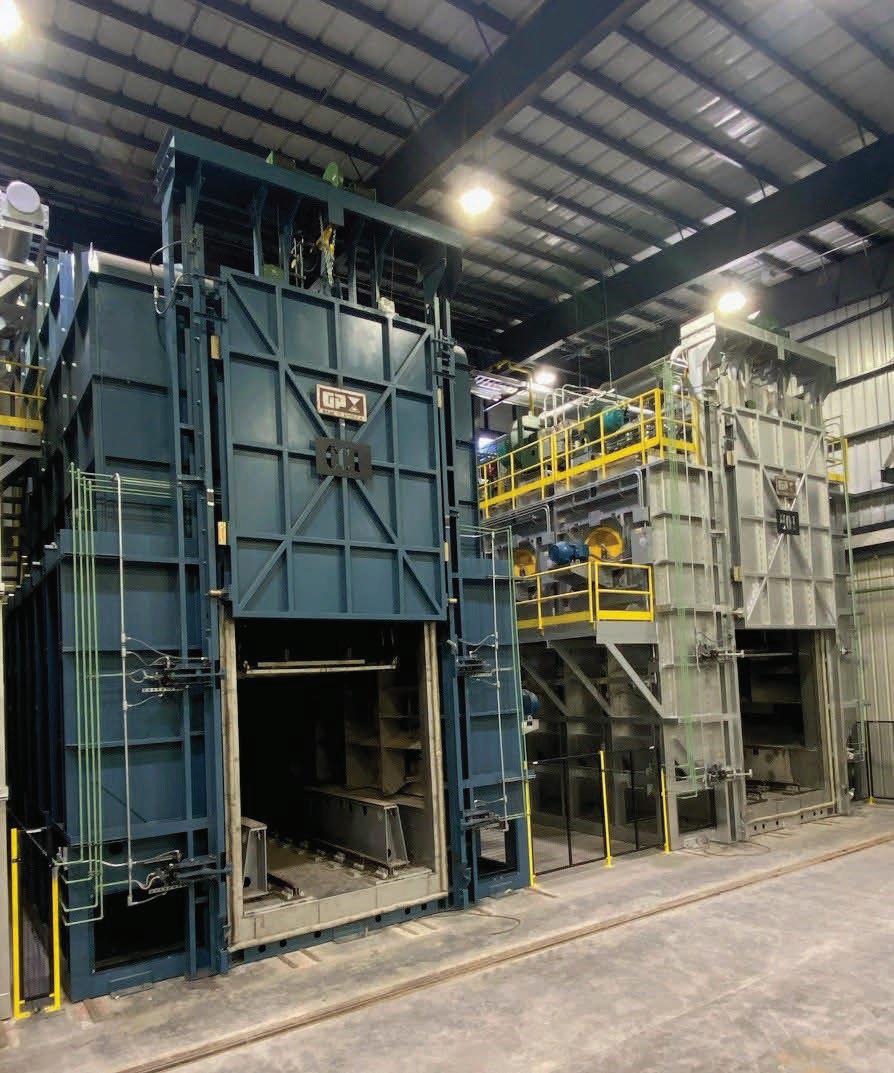
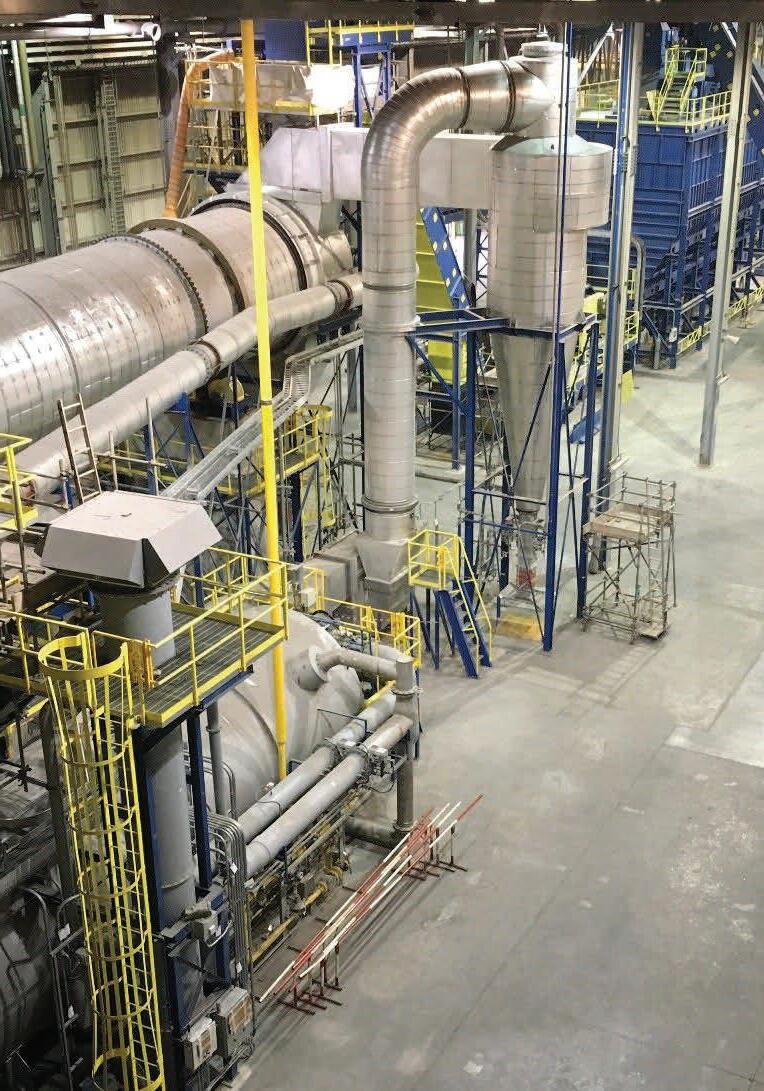
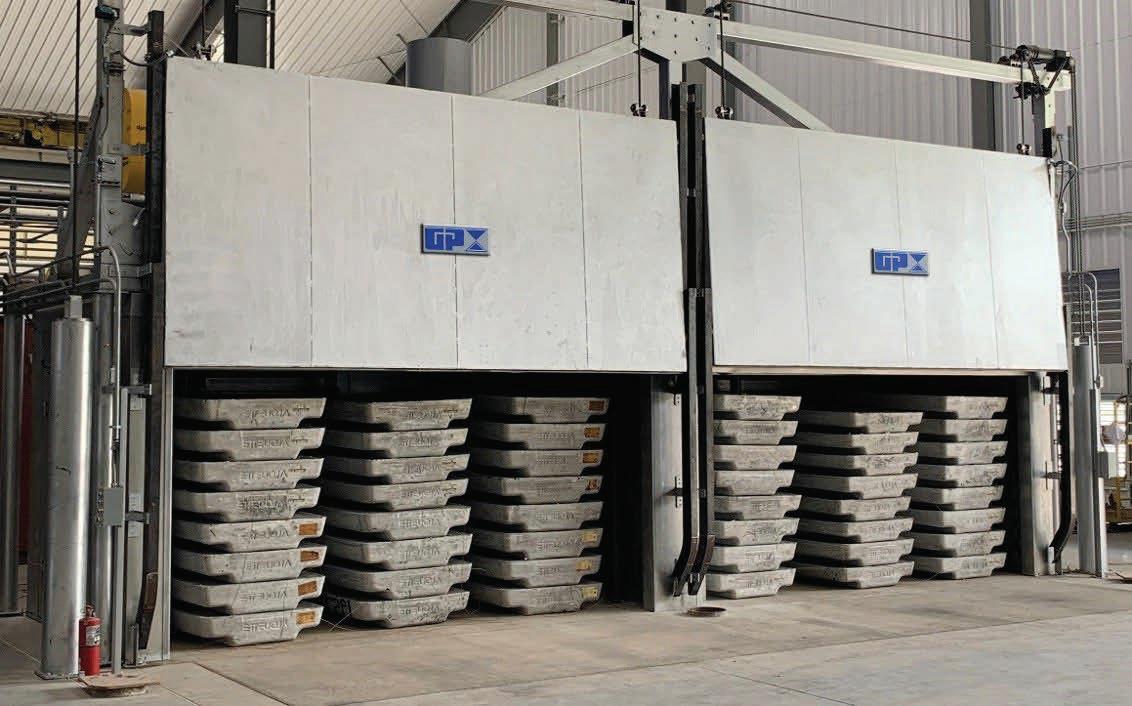
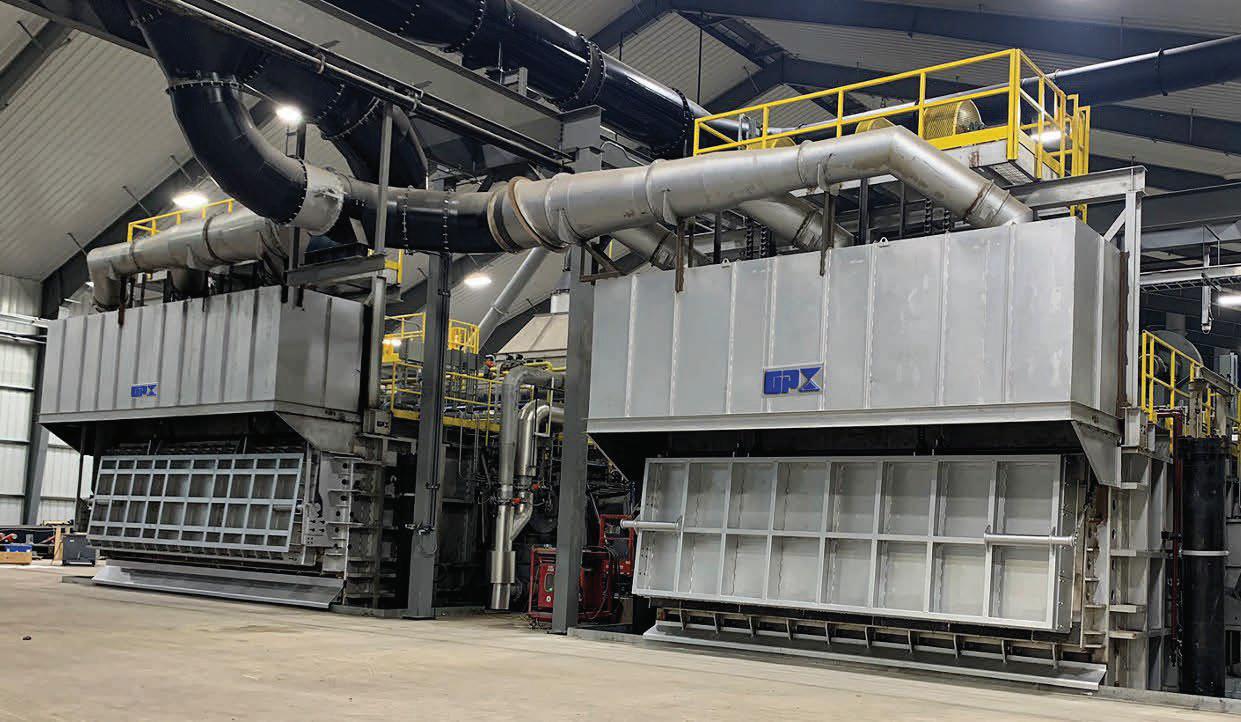
✓SINGLE CHAMBER / MULTI CHAMBER FURNACES
✓SCRAP DECOATING SYSTEMS
✓TILTING ROTARY MELTING FURNACES
✓SCRAP CHARGING MACHINES
✓LAUNDER SYSTEMS
✓CASTING / HOLDING FURNACES
✓HOMOGENIZING OVENS
✓COOLERS
✓SOW PRE-HEATERS
✓REPAIR & ALTERATIONS
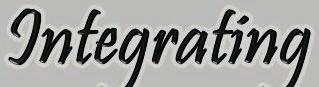
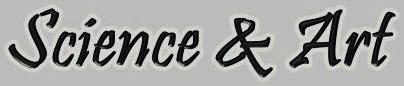
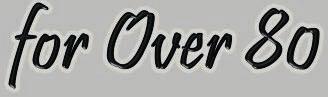
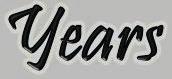






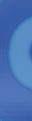
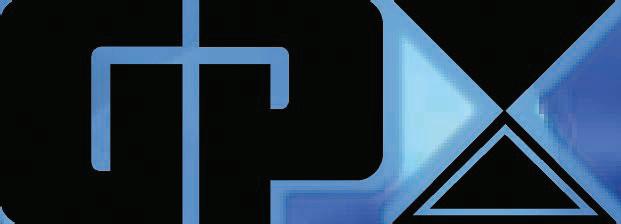
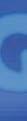


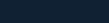
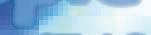








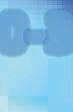




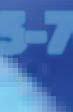



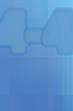


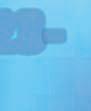
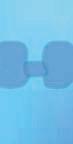




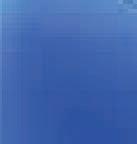
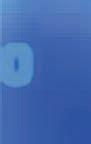


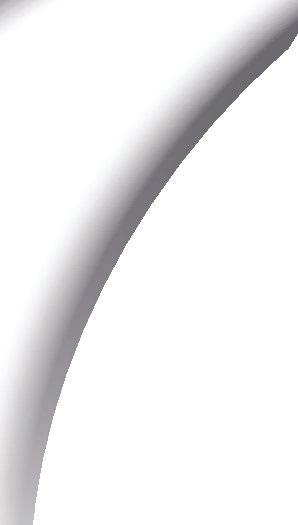

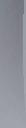

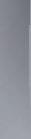

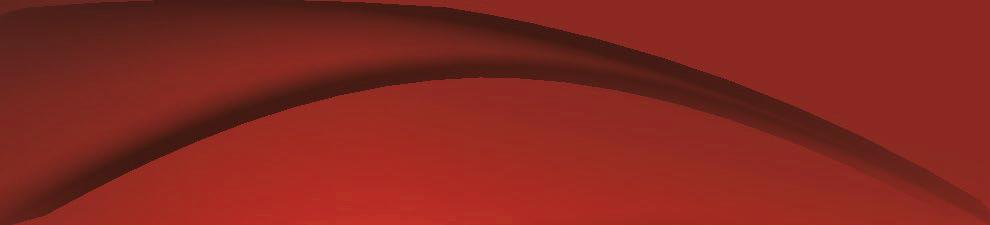
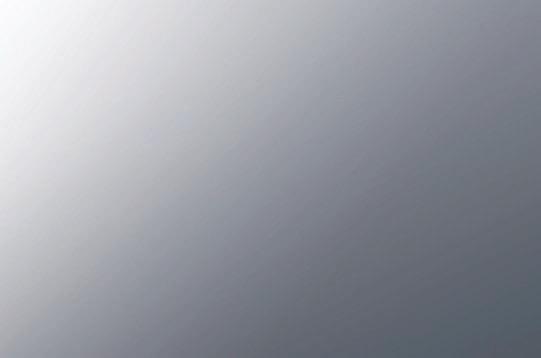

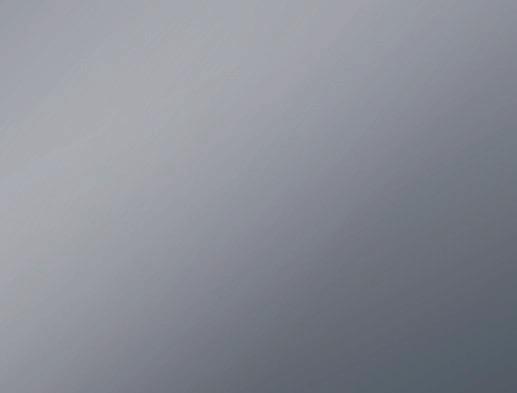
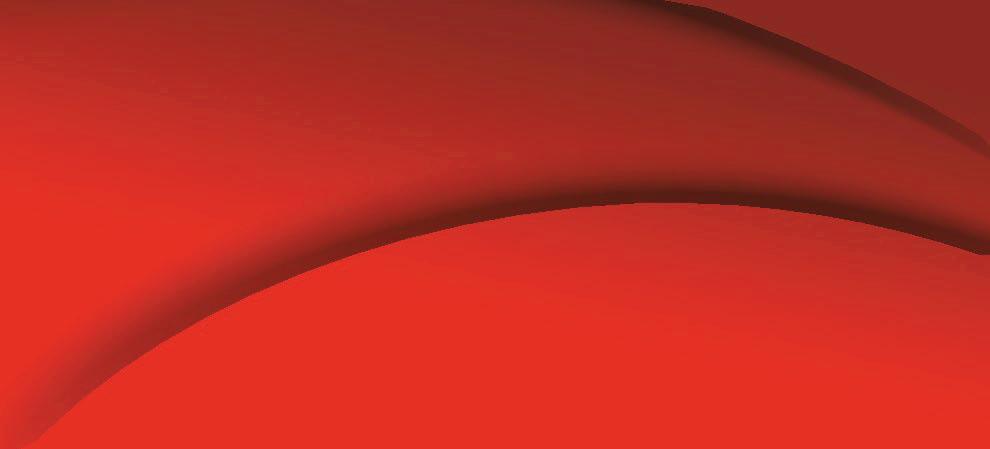

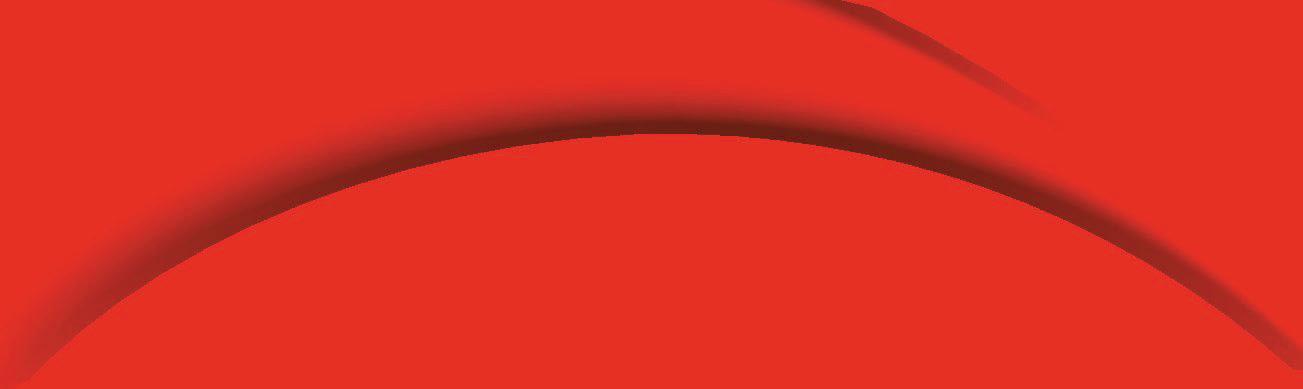

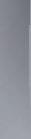




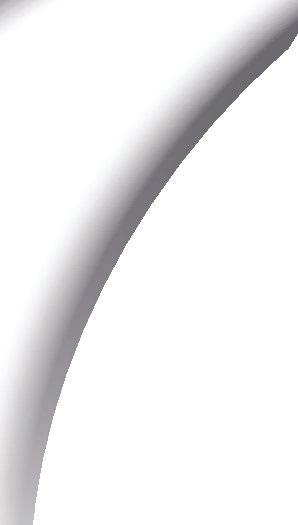
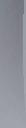

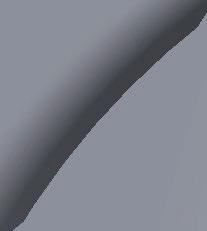
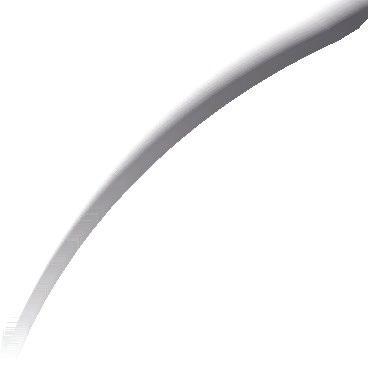
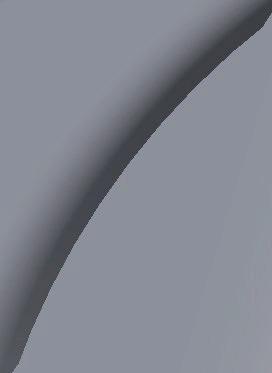




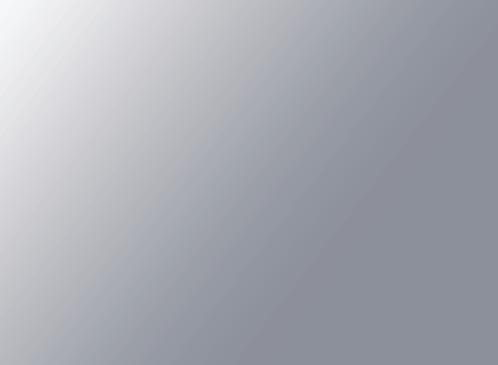
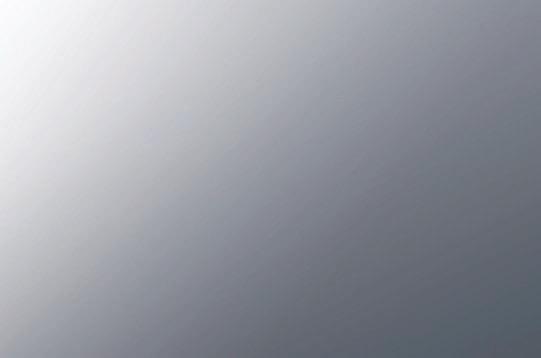
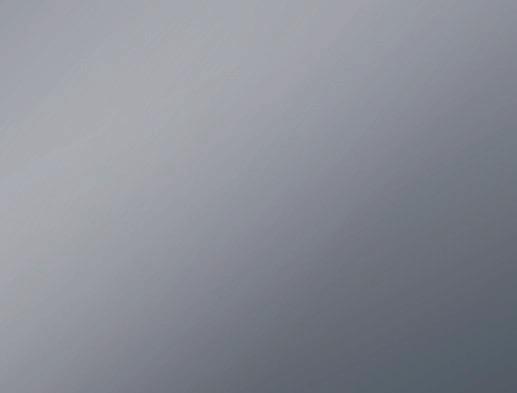
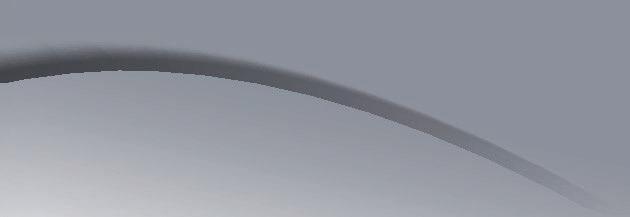
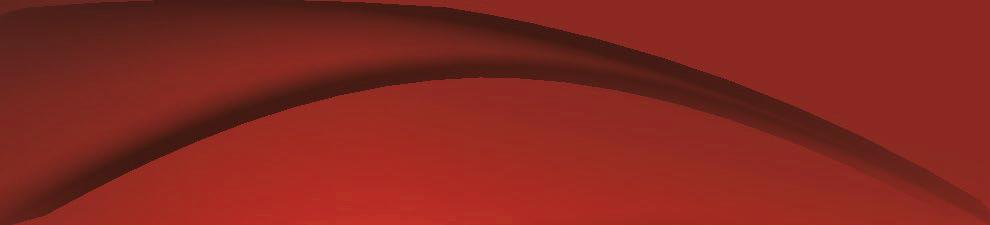
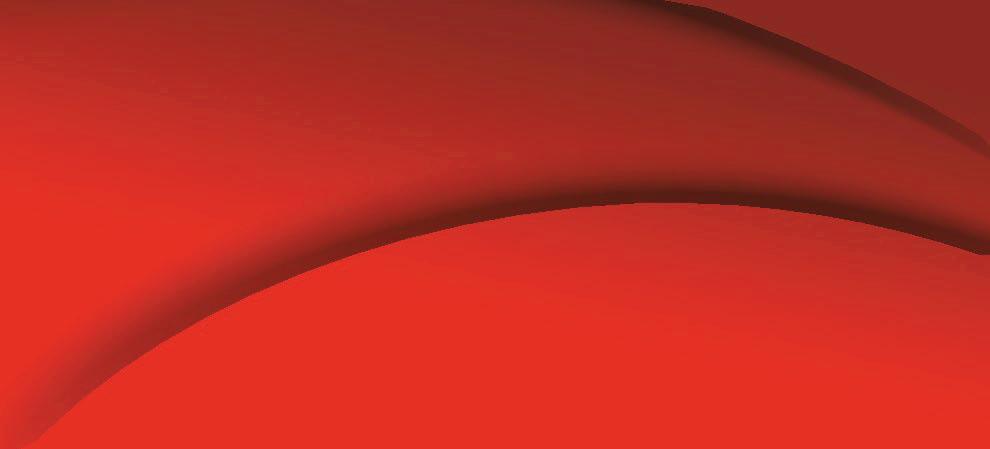


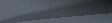
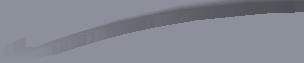


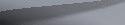

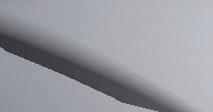

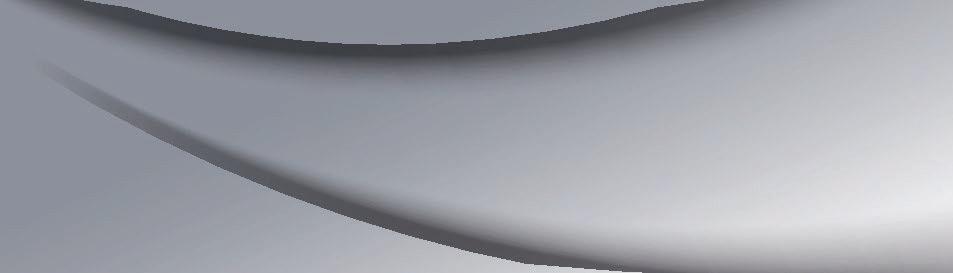
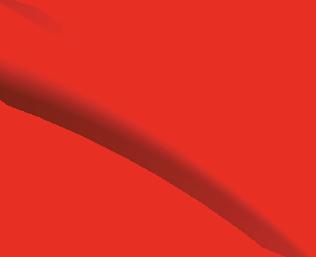
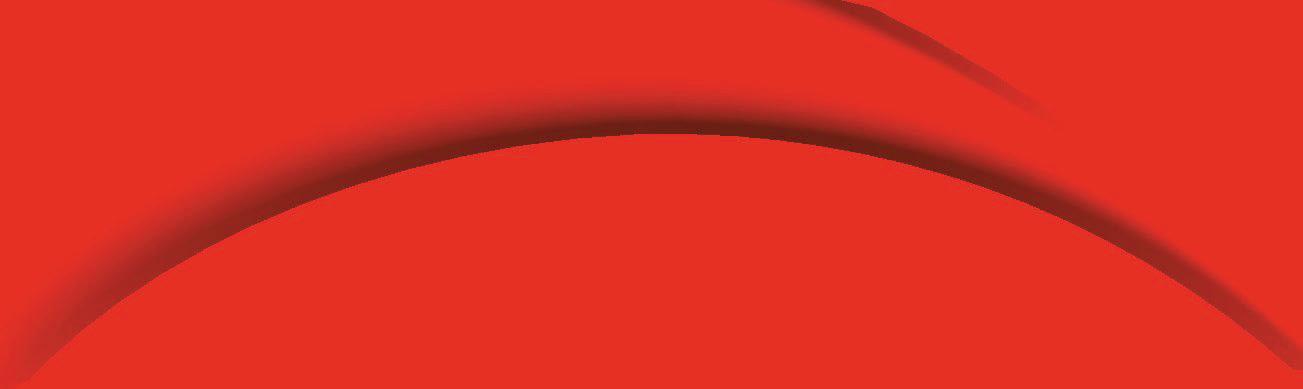
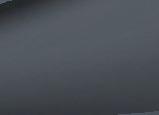
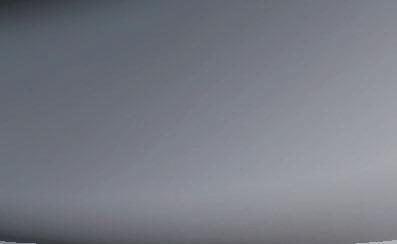
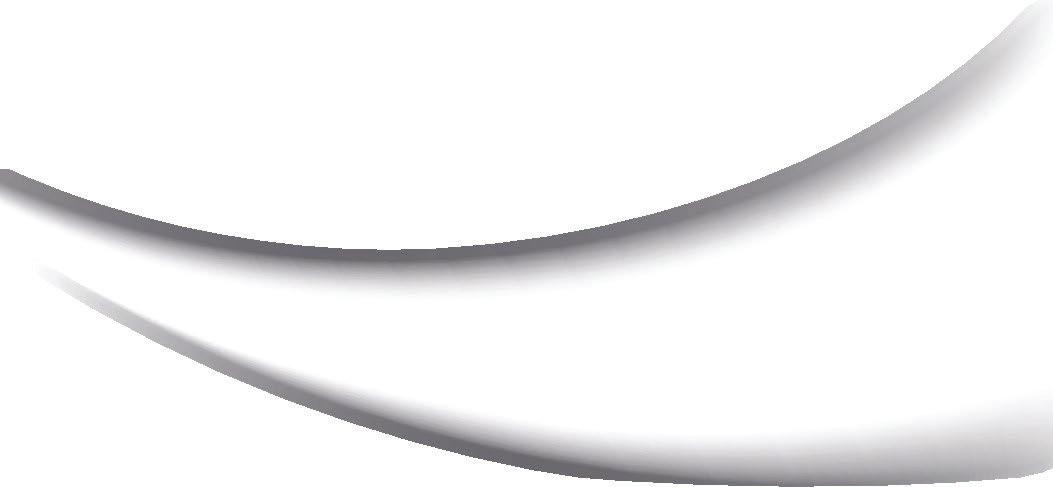

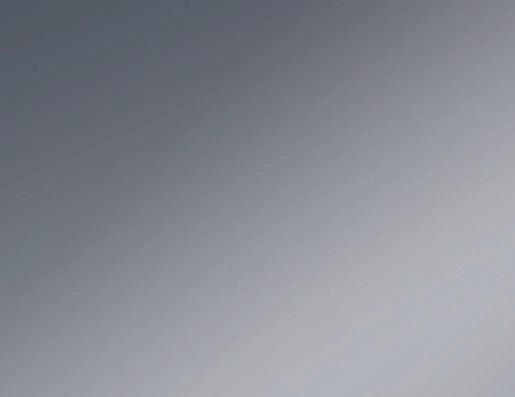

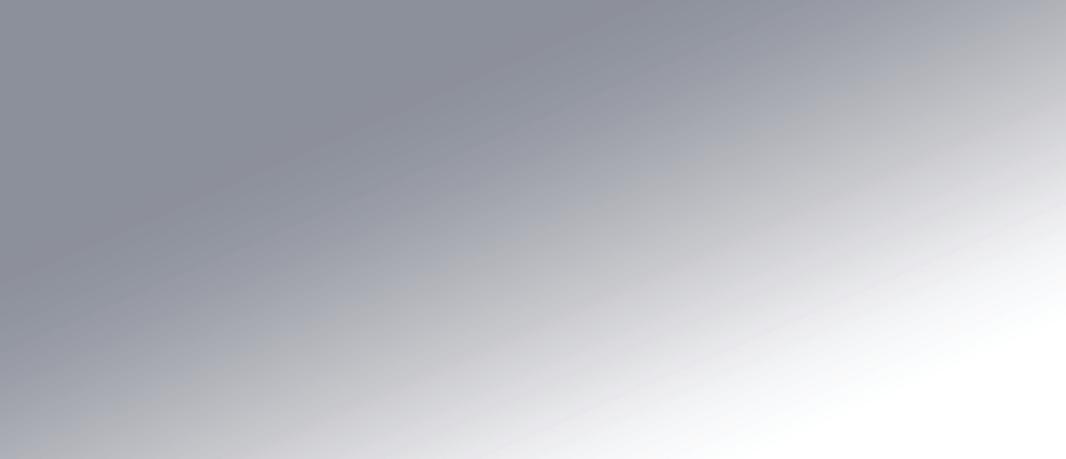

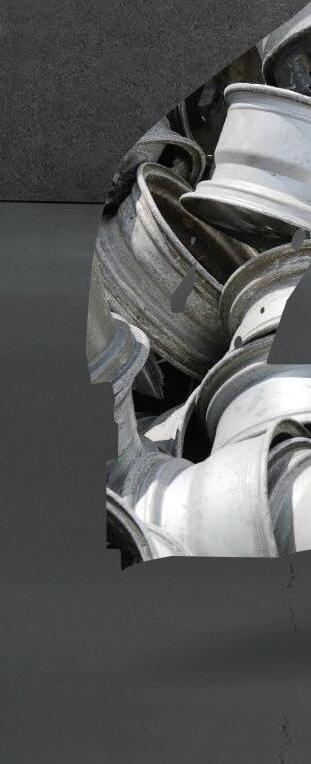
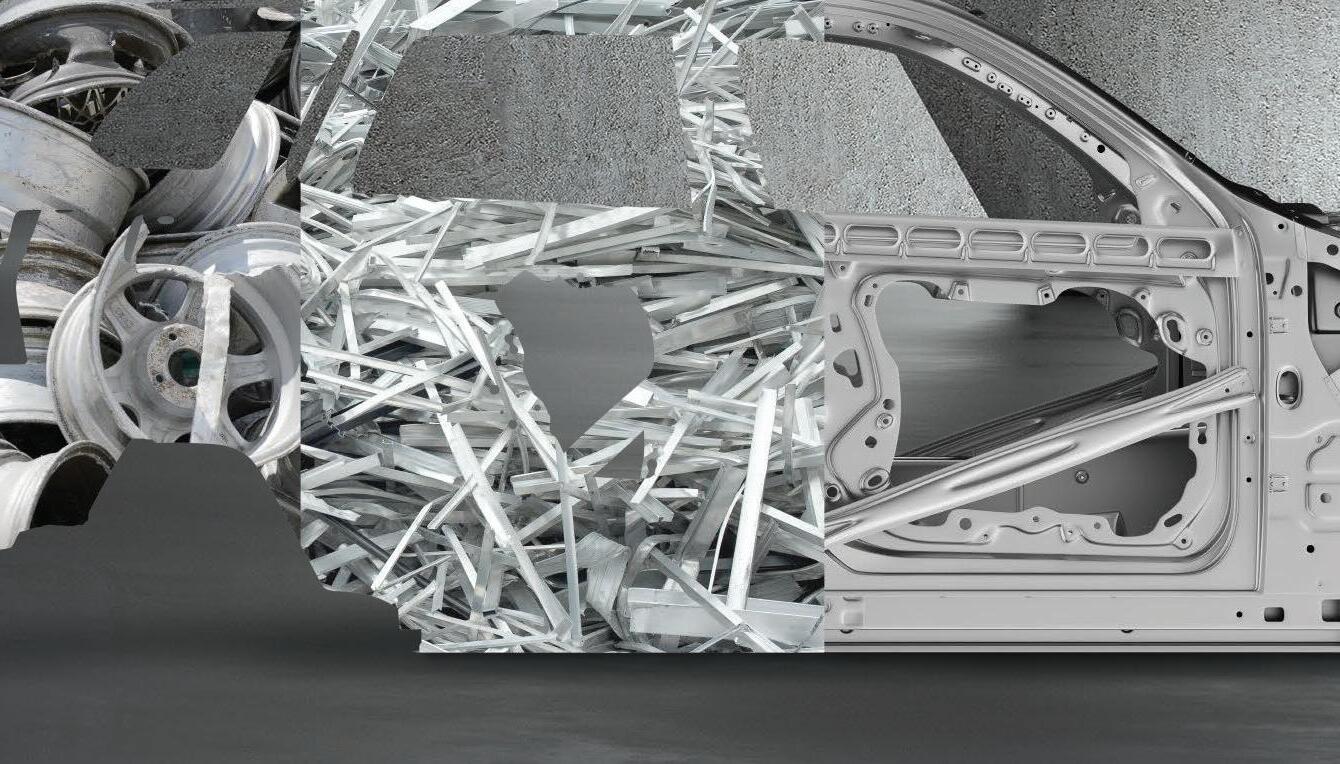
Every step matters on the path to zero
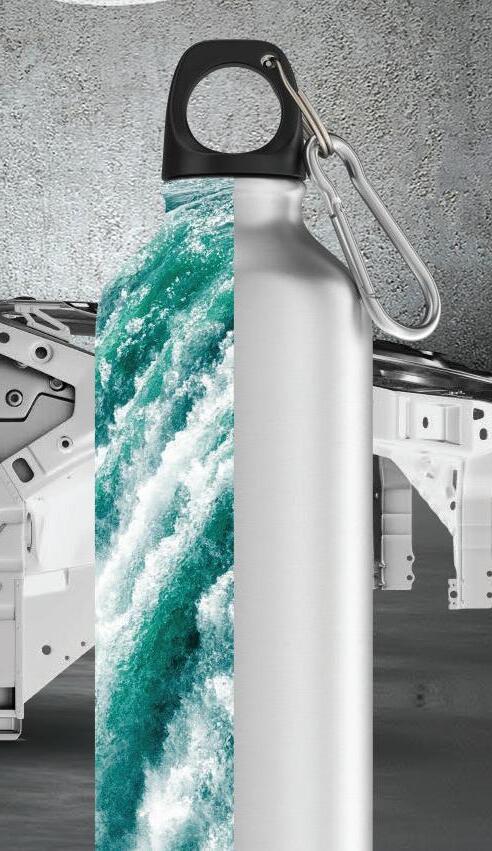
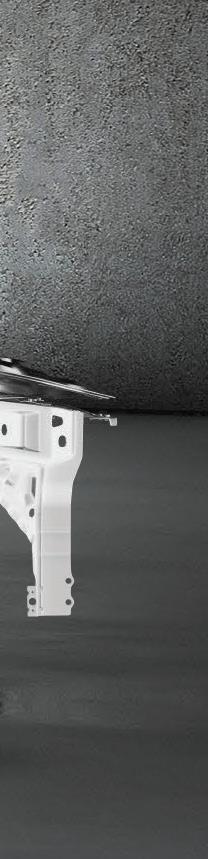
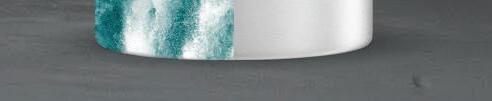
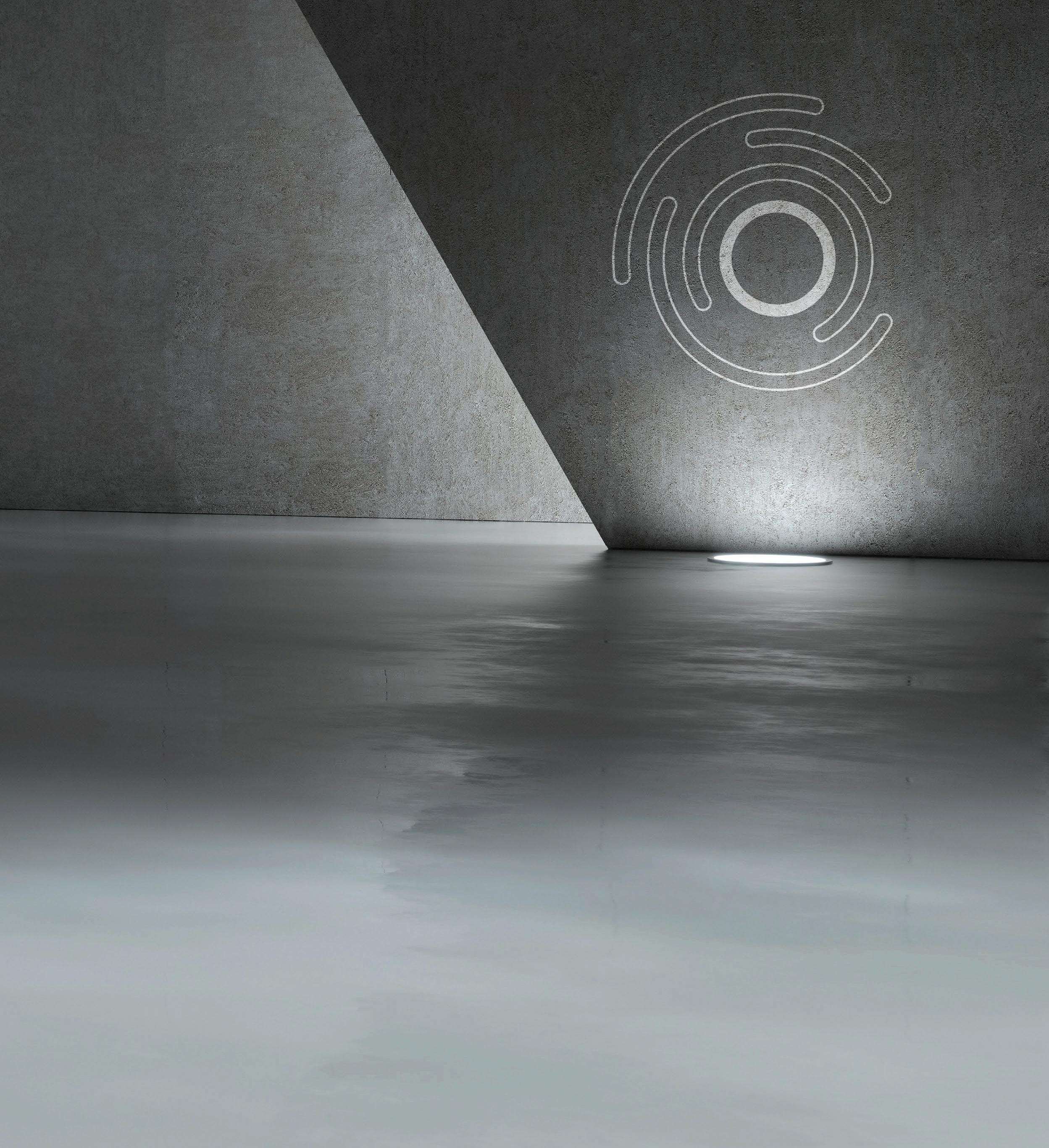
To continue developing modern society, we need more materials, and we need more from our materials, too. What we produce and consume must not only meet the surging demand, but also embody the principles of responsible sourcing, environmental consciousness, and recyclability.
Aluminium, with its infinite recyclability and corrosion-resistant longevity, is already a building block for a low-carbon, circular economy, but production comes with a footprint. Our recycled
and low-carbon aluminium products are one step closer to solving that problem, and one step closer on the path to zero.
Choose your materials with the future in mind. Visit hydro.com/path-to-zero to learn more.
Visit us at ALUMINIUM Exhibition 2024 Come to booth #4F57 in hall 4 and experience our sustainability ambitions at the stand, exploring our exhibits, seminars and workshops.