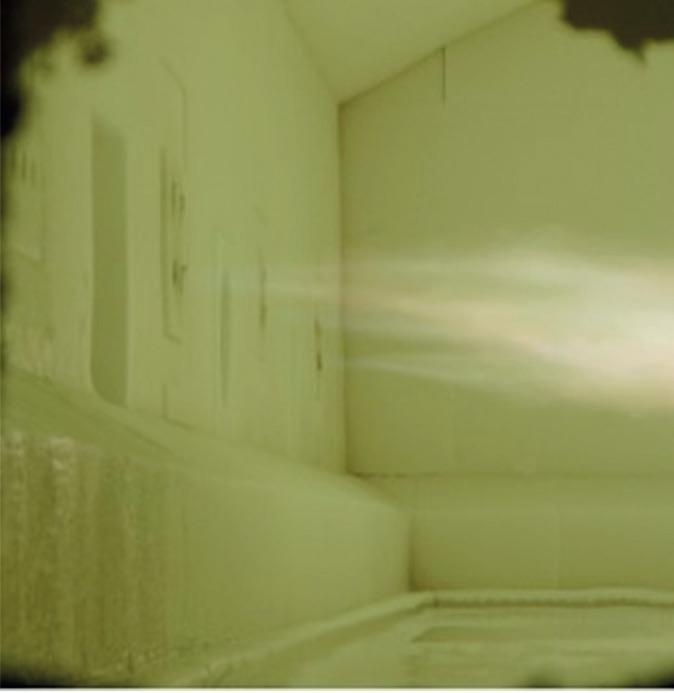
9 minute read
Descarbonización
Descarbonizar la industria del vidrio: el papel de las soluciones refractarias
El doctor Michel Gaubil* y Mélanie Allen-Larut** comentan cómo la alta calidad de los materiales refractarios puede ayudar a los fabricantes de vidrio a superar los retos de la neutralidad en carbono.
� Fig. 1. Superestructura que utiliza ER 1851 de baja ex. � Fig. 2. Tuckpro del ER 1195 RT. � Fig. 3. Corona de AZS electrofundidos, baja ex,del ER 1851
Además de los retos típicos de producir con sostenibilidad vidrio de alta calidad a costes óptimos, la industria del vidrio se enfrenta a nuevos retos de cambios de paradigma: neutralidad en emisiones de carbono y circularidad. El reto más importante de esta industria en los años venideros es lograr una producción de vidrio baja en carbono. Muchos gobiernos y muchas empresas anunciaron objetivos claros para alcanzar la neutralidad en las emisiones de carbono en las próximas décadas. La industria del vidrio debe cumplir con la parte que le corresponde.
La economía circular es su segundo reto clave. Además de un mayor uso del calcín, se debe tener en cuenta el ciclo de vida total del horno, lo que incluye el final de esta vida útil y el reciclado de los materiales refractarios. Las soluciones refractarias son fundamentales para los hornos de vidrio y su rendimiento. Por lo tanto, su papel clave es el de apoyar a los fabricantes de vidrio en estos nuevos retos.
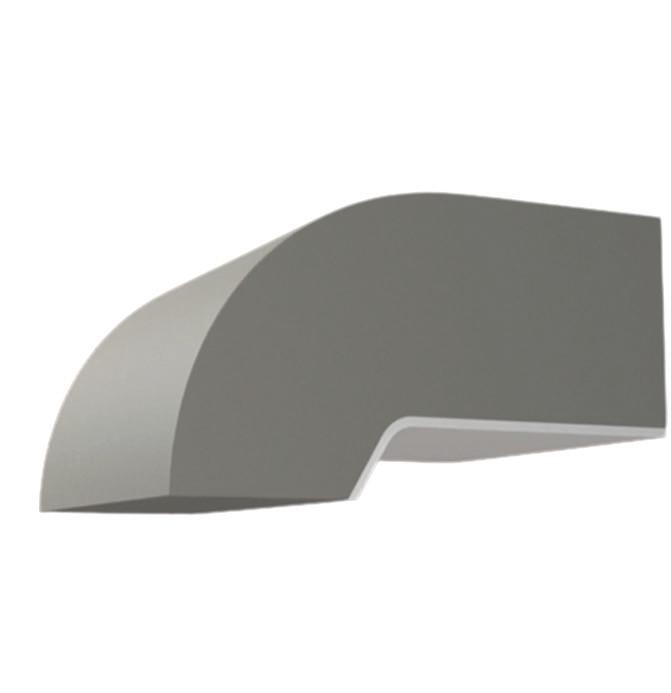
Servicios para apoyar el cambio hacia la neutralidad en las emisiones de carbono
En el camino de la producción industrial hacia un vidrio neutro en carbono hay aun muchos obstáculos. El más importante es el cambio hacia fuentes de energía renovables. La mayoría de los protagonistas de la industria están probando y desarrollando dos candidatos principales: la electricidad y el hidrógeno. También se están investigando otras opciones, como el biogás y los biocombustibles.
A pesar de la incertidumbre, sabemos que habrá un impacto al cambiar los combustibles de los materiales refractarios del horno de vidrio y que se necesitará más flexibilidad en la mezcla de energías, sobre todo en el período de transición.
Para mitigar los riesgos en la seguridad y la vida útil del horno, serán claves los servicios de simulación numérica en función de un conocimiento especializado en los materiales refractarios para anticipar y tomar las mejores decisiones refractarias. En los modelos de corrosión se analiza el impacto de los parámetros, como el perfil de temperatura del vidrio, el perfil de velocidad del vidrio, la composición refractaria y la eficiencia de enfriamiento de la vida útil de los materiales refractarios. Estos servicios de simulación numérica ayudan a elegir las mejores soluciones refractarias para las condiciones específicas del horno para vidrio.
Los cambios en las condiciones de funcionamiento, que no se habían visto a esta escala hasta ahora, también intensificarán la necesidad de supervisar los hornos en tiempo real. Los sensores que se pueden colocar en los refractarios para observar la evolución del desgaste del horno en tiempo real garantizarán las funciones del horno, activarán los ajustes necesarios de las condiciones de funcionamiento o, de ser necesario, avisarán sobre la necesidad de mantenimiento o reparaciones antes de que ocurra un accidente importante.
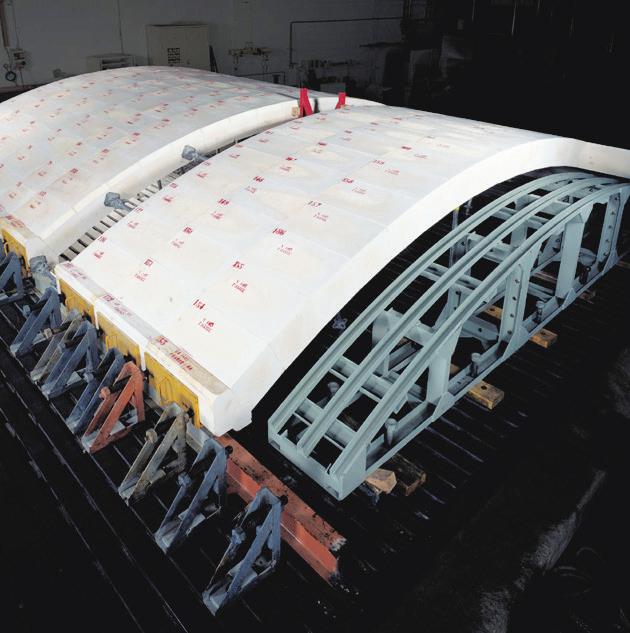
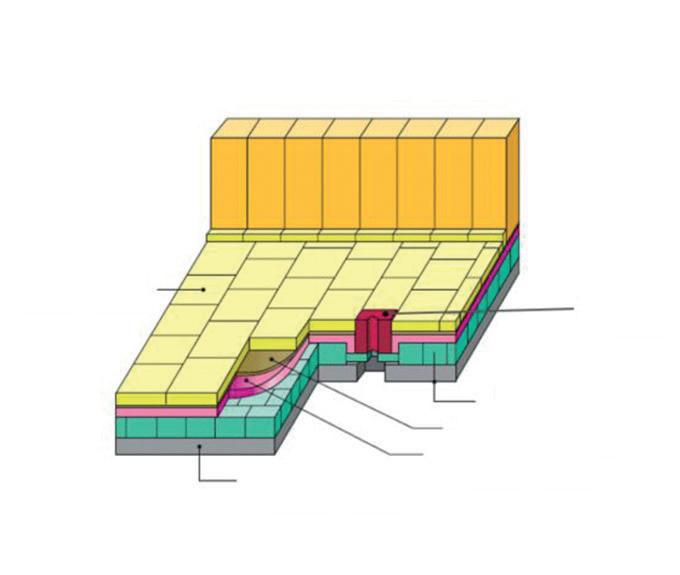
Soluciones refractarias de alto rendimiento
Las tecnologías y las medidas que permiten el cambio hacia la neutralidad de carbono, como el boosting eléctrico, más aislamiento en ambos lados de contacto con el vidrio y la tecnología de la superestructura y la combustión de hidrógeno, exigen un rendimiento refractario mayor.
En la aplicación de la superestructura, el uso de tecnología de oxicombustión y más aislamiento térmico dan como resultado un aumento de la exudación y la corrosión.
Muchos productos de alta calidad en la cartera refractaria cumplen con estos requisitos. Se demostró que el uso de AZS electrofundido de baja exudación junto con los materiales electrofundidos con alto contenido de alúmina o circonio son adecuados para lidiar con condiciones del horno más urgentes (Fig. 1).
Utilización de alto contenido de circonio para aplicación de tuckstone
Las superestructuras y los tuckstones en especial estarán en atmósferas más corrosivas. Los tuckstones con alto contenido de circonio garantizan la alta resistencia necesaria para la corrosión, pero, por lo general, son más vulnerables a la tensión termomecánica. Combinar una protección de cerámica compuesta (con alta resistencia de compresión y baja conductividad térmica) con un tuckstone con alto contenido de circonio lo protegerán del riesgo de fi suras por estas tensiones. Por ello, el tuckstone aislante podrá cumplir con su papel de evitar pérdidas térmicas. La estabilidad de la superestructura y la protección térmica de los bloques soldados que están debajo aumentan y contribuyen a una vida útil del horno más larga (Fig. 2).
La oxicombustión, si bien no es una tecnología nueva, vuelve a ser pertinente para los hornos híbridos y de hidrógeno. Con esta tecnología se provocan en comparación temperaturas altas de funcionamiento junto con mucho vapor de agua y concentración de alcalina en los vapores. Los materiales refractarios deben soportar estas nuevas condiciones, sobre todo en la corona.
La primera opción para las coronas en la oxicombustión son las soluciones de refractarios electrofundidos como los materiales AZS con baja exudación o con alto contenido de alúmina. Una unidad con especifi caciones muy precisas garantiza la corrosión necesaria y las propiedades de resistencia a la fl uencia en la corona del horno (Fig. 3).
El boosting eléctrico da como resultado directo temperaturas más altas en la base del horno para vidrio y un aumento en la tasa de fl ujo de convección de la fusión. La respuesta más conocida para estos retos es utilizar cerámicos electrofundidos. Sin embargo, esto ya no es sufi ciente: se debe tener en cuenta una solución refractaria completa para la base del horno.
El primer elemento de esta solución son los cerámicos electrofundidos sin vacíos. Además de mayor resistencia a la corrosión, los cerámicos deben garantizar el cierre de las juntas después del calentamiento para garantizar la seguridad de la base del horno (Fig. 4).
No se debe ignorar el rendimiento de los morteros. La dilatación armonizada de las distintas capas de los cerámicos y de los morteros es fundamental para evitar fi ltraciones de vidrio inesperadas.
Para los hornos con mucha energía eléctrica, se debe tener en cuenta usar soluciones adicionales de refractarios electrofundidos con alta resistencia eléctrica, como el Xilec 9, diseñadas especialmente para esas condiciones extremas. Estos materiales son la mejor opción, y la más segura, para las condiciones de funcionamiento más duras, gracias a su alta densidad de corriente (Fig. 5).
Además del impacto en las losas del horno, las altas temperaturas en la base del horno para vidrio también tienen afectar la parte inferior de los bloques soldados. Se necesita un relleno reforzado en esta zona, donde la colada fi nal solía ser sufi ciente, con un cambio a los bloques soldados con una cavidad para la colada más reducida y bien controlada.
Extremo de la fusión
ER 2010 RIC TJ
Aislamiento XiLEC 9 RT
ERMOLD
Cemento ERSOL 06 ERSOL SL
� Fig. 4. Soluciones para las losas de la base: Losas de AZS dopadas con itrio, cerámicos ER 2010 RIC con capa de seguridad ERSOL SL
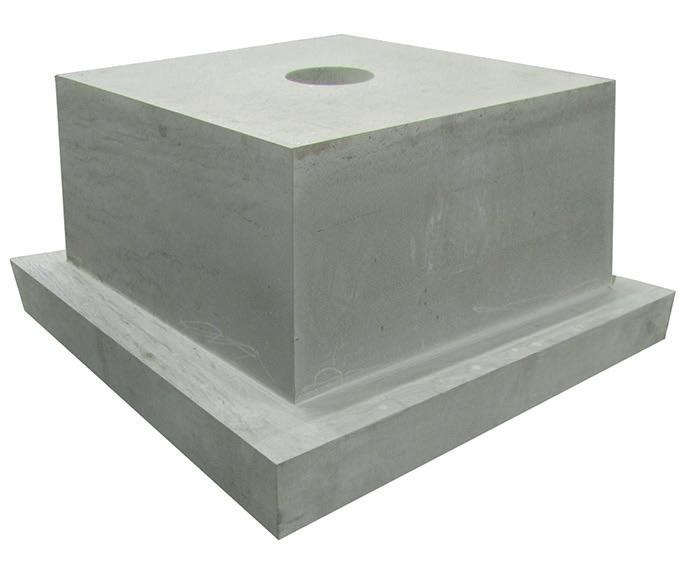
� Fig. 5. Bloque de electrodos XILEC 9.
Circularidad
El primer paso hacia una economía circular es reducir la cantidad de los materiales necesarios para alcanzar un rendimiento similar. Prolongar la vida útil del horno y maximizar el uso de los activos refractarios con materiales refractarios de alta calidad y con operaciones de servicios de reparación específi cos pueden ayudar a alcanzar este objetivo.
Al fi nal del ciclo de vida de la producción, todos los hornos de vidrio tienen el mismo problema: un producto de alta calidad se convierte en residuos, y, en algunos casos, en residuos peligrosos.
La mayoría de los proveedores consolidados del mercado ofrecen servicios de demolición y de evacuación de residuos. Algunos ofrecen la revalorización de los residuos y los transforman en materias primas nuevas o los reciclan.
La responsabilidad de la industria del vidrio por la «otra vida» de sus materiales procesados se vuelve más evidente cuando los materiales refractarios se clasifi can como residuos peligrosos al momento en el que el horno se apaga, como los materiales que contienen óxido de cromo.
La exposición consciente con la pregunta ¿qué pasa con esos materiales? no se acaba cuando los evacuan y retiran de la fábrica. En muchas tablas de sostenibilidad se incluye el tratamiento de los residuos y se hace aún más responsable a quienes fabrican vidrio.
Esa pregunta es más delicada en los países en los que la legislación responsabiliza a quienes tienen hornos aun después de la evacuación de los residuos. En esas zonas es muy importante encontrar proveedores de servicios que garanticen una utilización aprobada.
Quienes proveen materiales refractarios son parte del Alcance 3 de los fabricantes

de vidrio. Elegir proveedores de materiales refractarios que puedan garantizar una alta utilización de materias primas secundarias y una mezcla de energía baja en carbono será un factor competitivo clave en los próximos años para quienes fabrican vidrio.
Conclusión
La industria del vidrio se enfrenta a los retos de cambios de paradigma de la neutralidad en las emisiones de carbono y la circularidad. En este recorrido se movilizarán todos los socios de la industria para trabajar en conjunto para alcanzar objetivos de gran alcance. Como parte de la industria del vidrio, los proveedores que se especializan en materiales y en servicios refractarios cumplen un papel clave y pueden ayudar en la transición a los fabricantes de vidrio al confi ar en la experiencia en materiales refractarios, en las capacidades de innovación y en su enfoque centrado en los clientes. �
* Director de Soluciones refractarias aplicadas, Gerente de marketing estratégico, SEFPRO, Francia www.sefpro.com



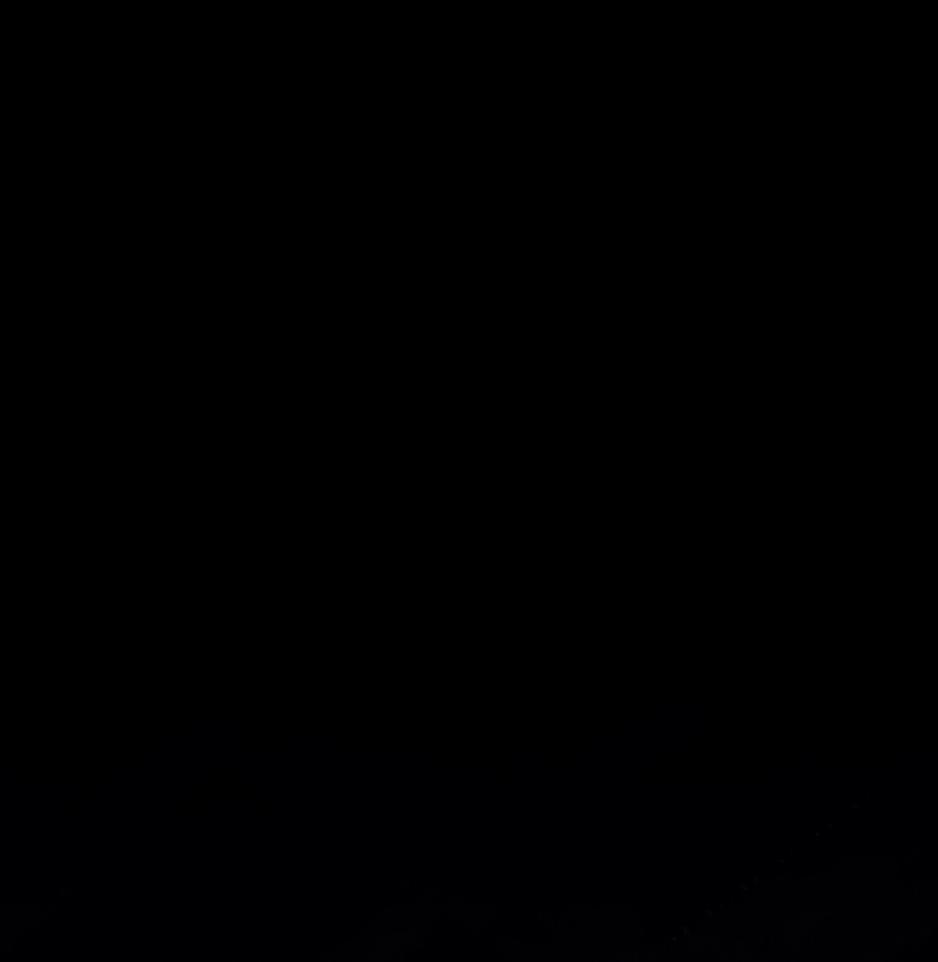
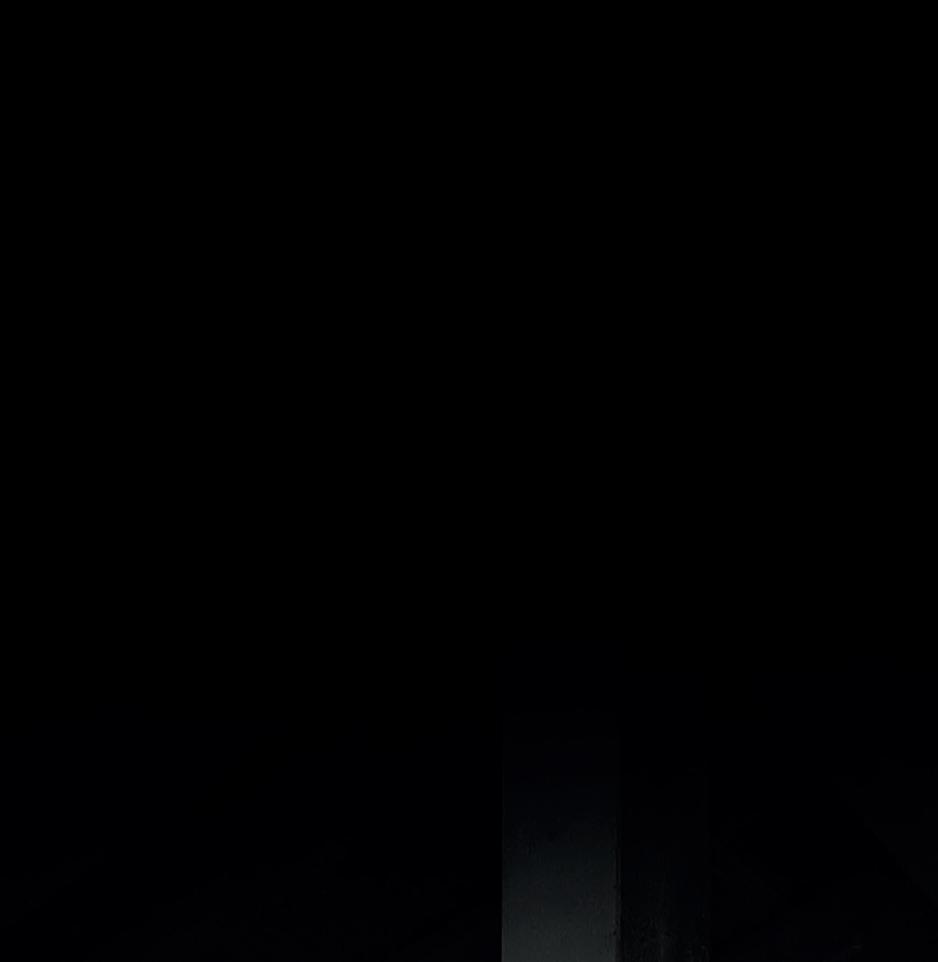
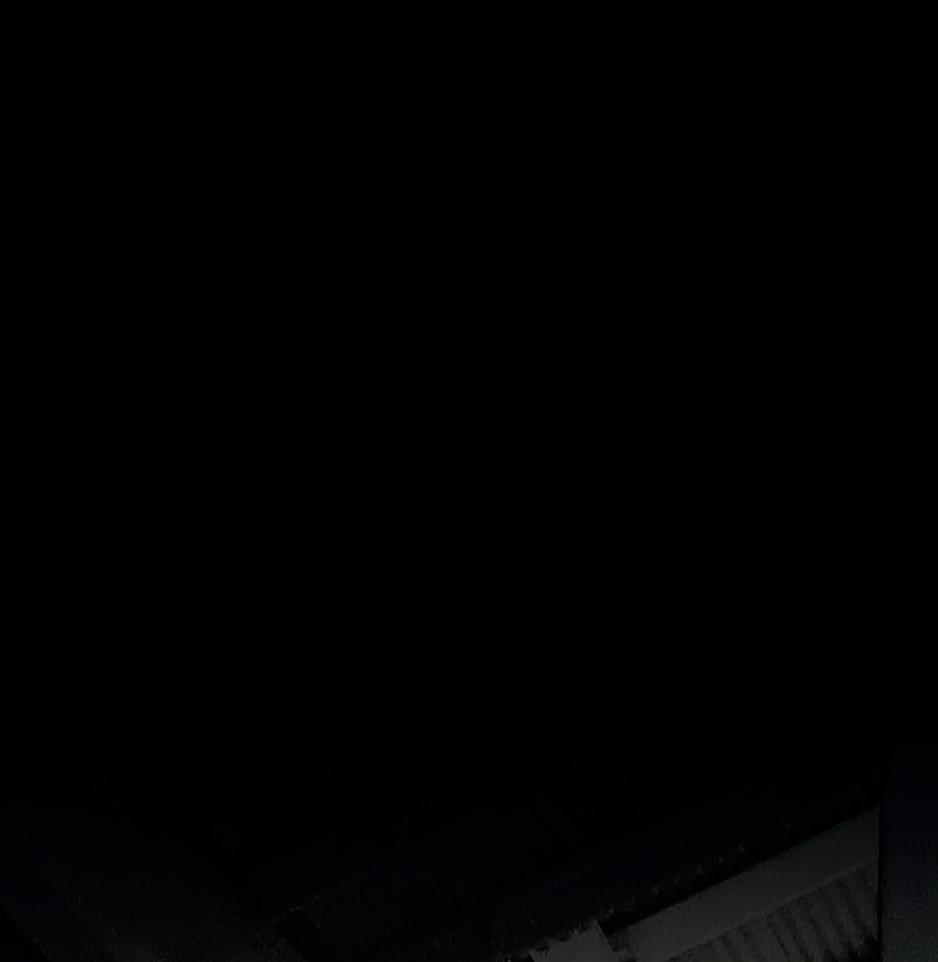
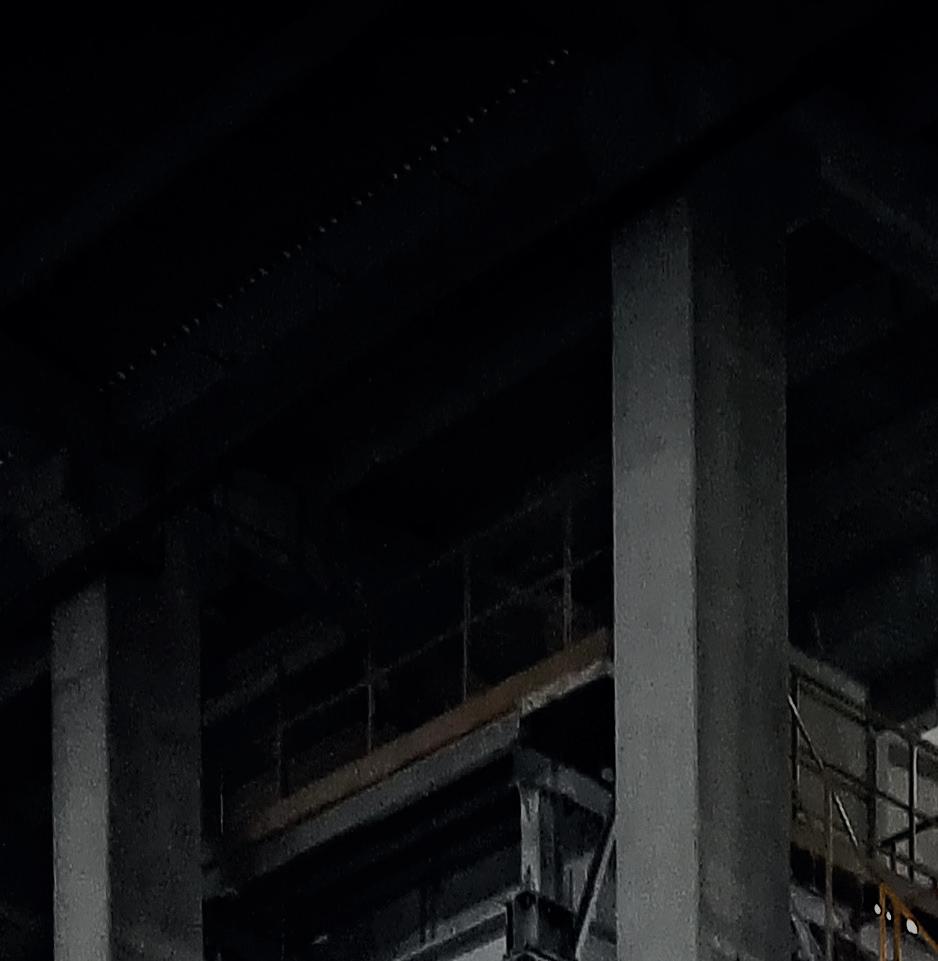

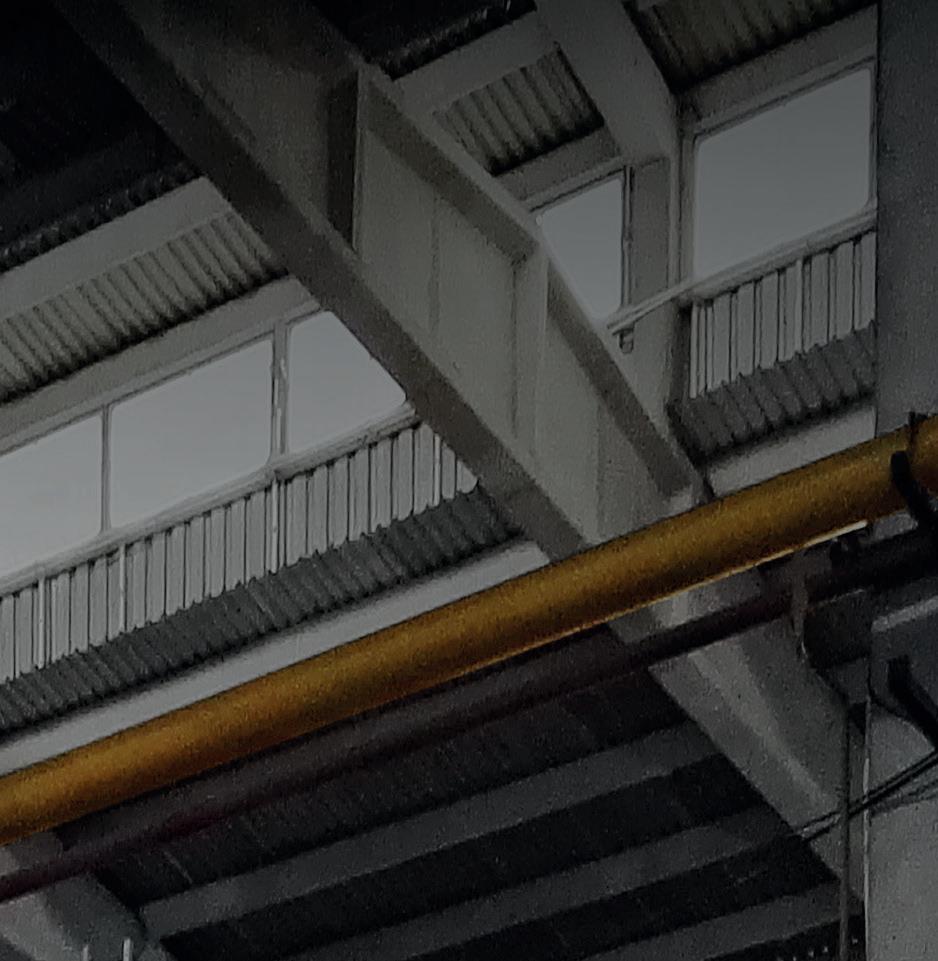
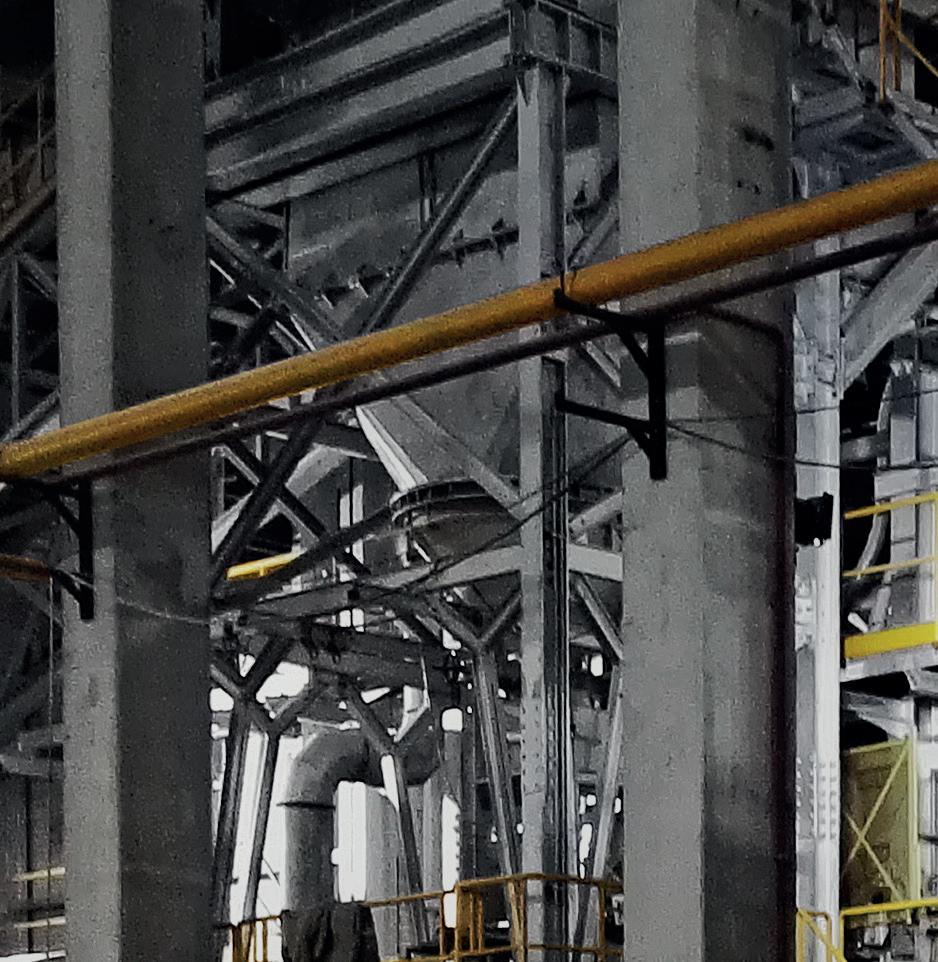
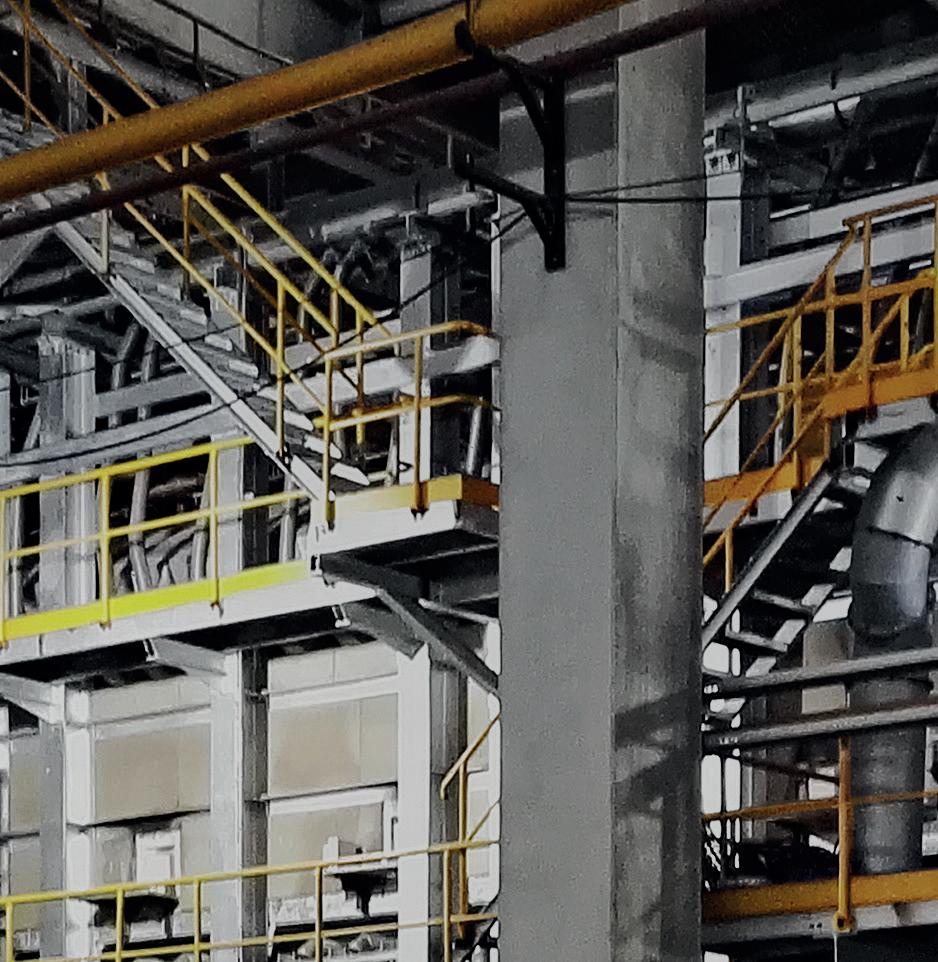
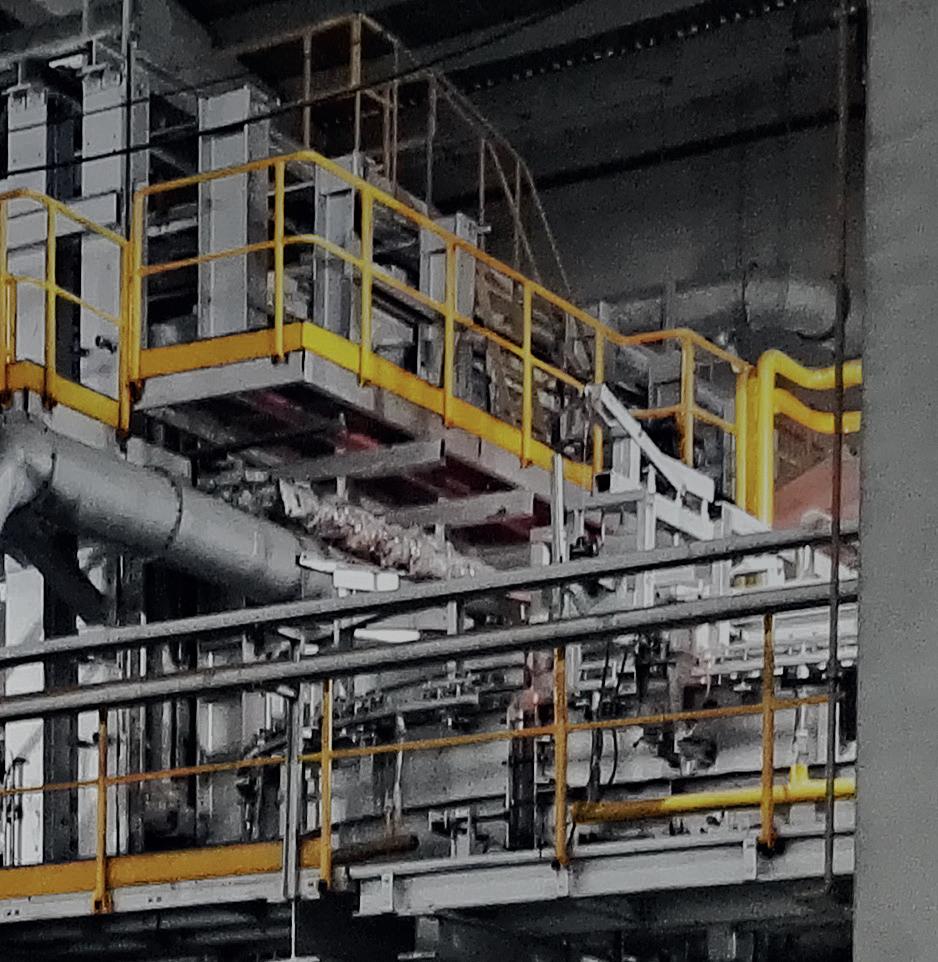
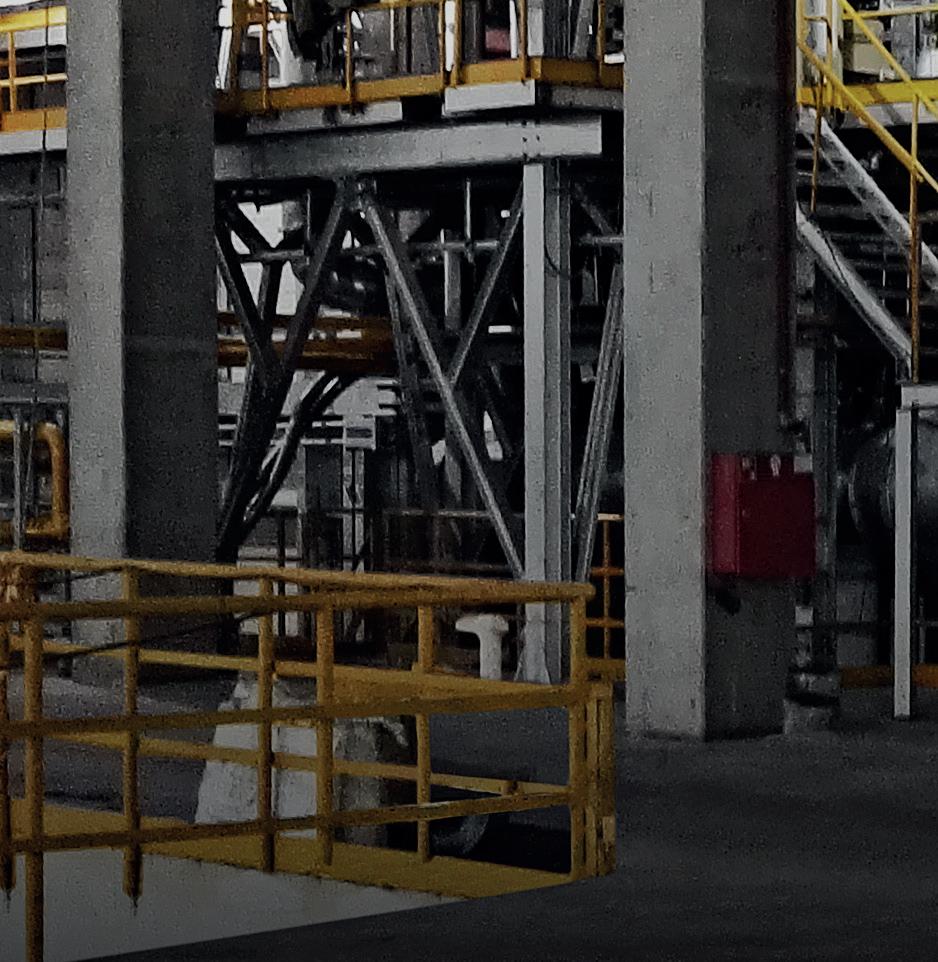
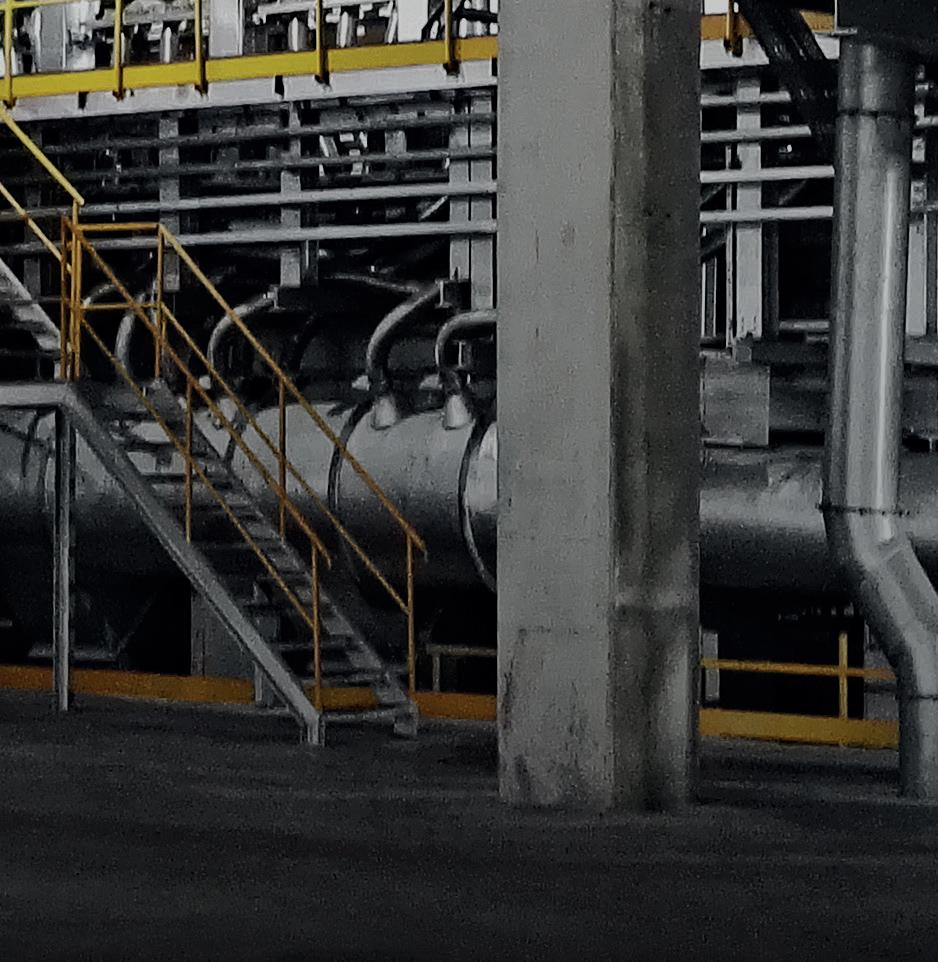
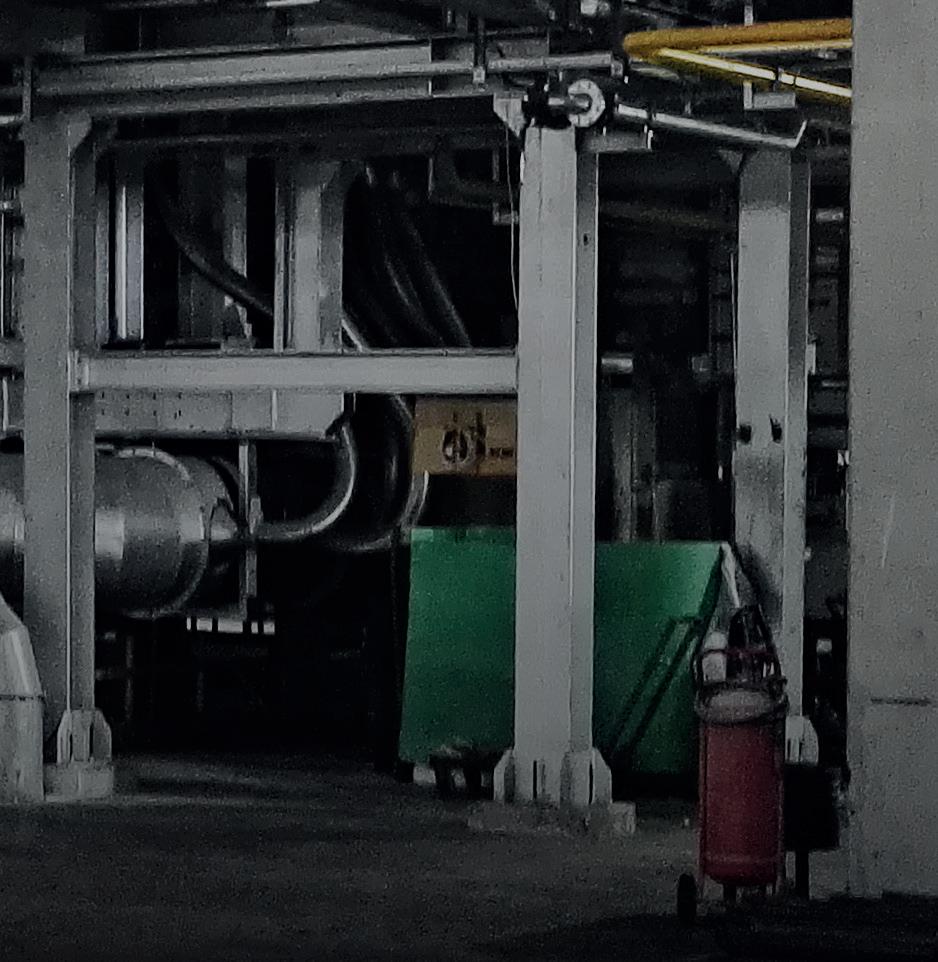