
10 minute read
Perfi l de la empresa
Leerdam Crisal Glass (antes Libbey EMEA) ya obtuvo enormes logros de sostenibilidad desde que introdujo la tecnología Optimelt en sus plantas de fabricación hace cuatro años, pero ese no fue el final de la historia. Ya transformó una de sus plantas de gas en eléctrica y quiere ser libre de carbono mucho antes de la fecha límite climática del 2050. Greg Morris habló con Antoine Jordans* y Marco van Valburg**.
Las operaciones en Europa de Leerdam Crisal Glass ya van bien encaminadas a encontrar soluciones sostenibles. Mientras las empresas de otras industrias pueden estar recién empezando su camino hacia la descarbonización, hace varios años que la sostenibilidad y la neutralidad de carbono son temas centrales entre los fabricantes de vajilla de vidrio de Europa.
La empresa, antes Libbey EMEA, fue comprada hace poco por el fondo de inversiones neerlandés Anders Invest. Tiene plantas de producción en Leerdam, en los Países Bajos, y en Marinha Grande, en Portugal, y una de sus fábricas ya funciona con energía eléctrica 100 % ecológica. Además, sus oficinas van camino a dejar de utilizar papel y plástico y a utilizar iluminación con ledes; también se instalarán paneles solares. Ahora, la empresa tiene como objetivo descarbonizar por completo sus fábricas de producción antes de la fecha límite del 2050 que estableció el Acuerdo de París.
Como comenta Marco van Valburg, Director de programas estratégicos en Leerdam Crisal Glass: «cómo llegar a ser libres de carbono para el 2050 es un tema muy importante para nosotros, para la industria y para mí personalmente. Somos parte de las industrias pesadas y sabemos que tenemos que reducir el gas, debatir qué hacer con la reducción de CO2 y, relacionado con esto, utilizar la electrificación y el hidrógeno».
Sostenibilidad
El señor van Valburg y su colega Antoine Jordans, Gerente general de Leerdam Crisal Glass, suman entre los dos más de 66 años de experiencia en la fabricación de vidrio en la empresa. Ambos ocuparon varios puestos dentro de la empresa, en la planta y en sus oficinas corporativas, y conocen muy bien el proceso de fabricación del vidrio. Ambos están orgullosos del progreso alcanzado por la empresa en sus esfuerzos de sostenibilidad.
El señor Jordans comentó que: «el objetivo es producir vidrio libre de carbono idealmente antes del 2050. Ya estamos encaminados y buscamos nuevas tecnologías de hornos y otras tecnologías que puedan ayudarnos a descarbonizar la fusión y las máquinas, tales como el recocido, que utiliza grandes cantidades de energía».
Si bien el proceso de fusión representa aproximadamente un 70 % de toda la energía que se utiliza en la fabricación de envases de vidrio, las estadísticas son diferentes cuando hablamos de vajilla. Tanto el proceso de recocido como el requemado del producto utilizan una cantidad importante de gas natural.
El señor Jordans también comentó que: «cuando miramos en general y nos preguntamos ¿dónde podemos electrificar y utilizar una fuente diferente al gas natural? Hay soluciones simples, pero para algunas todavía falta inventar la tecnología y, en otros casos, tenemos que ver qué efectos tiene, por ejemplo, quemar hidrógeno en los materiales refractarios.
«Además, nos preguntamos si hay suficiente energía eléctrica en la red para pasar los hornos a electricidad. Porque muchas veces no hay suficiente energía».
Los dos reconocen que la infraestructura en su país natal tendrá que ser actualizada para cumplir con los requisitos de capacidad si se quiere descarbonizar a todas las industrias pesadas.
� Antoine Jordans (arriba) y Marco van Valburg. � Planta de Crisal.
Recorriendo un camino sostenible en vajilla
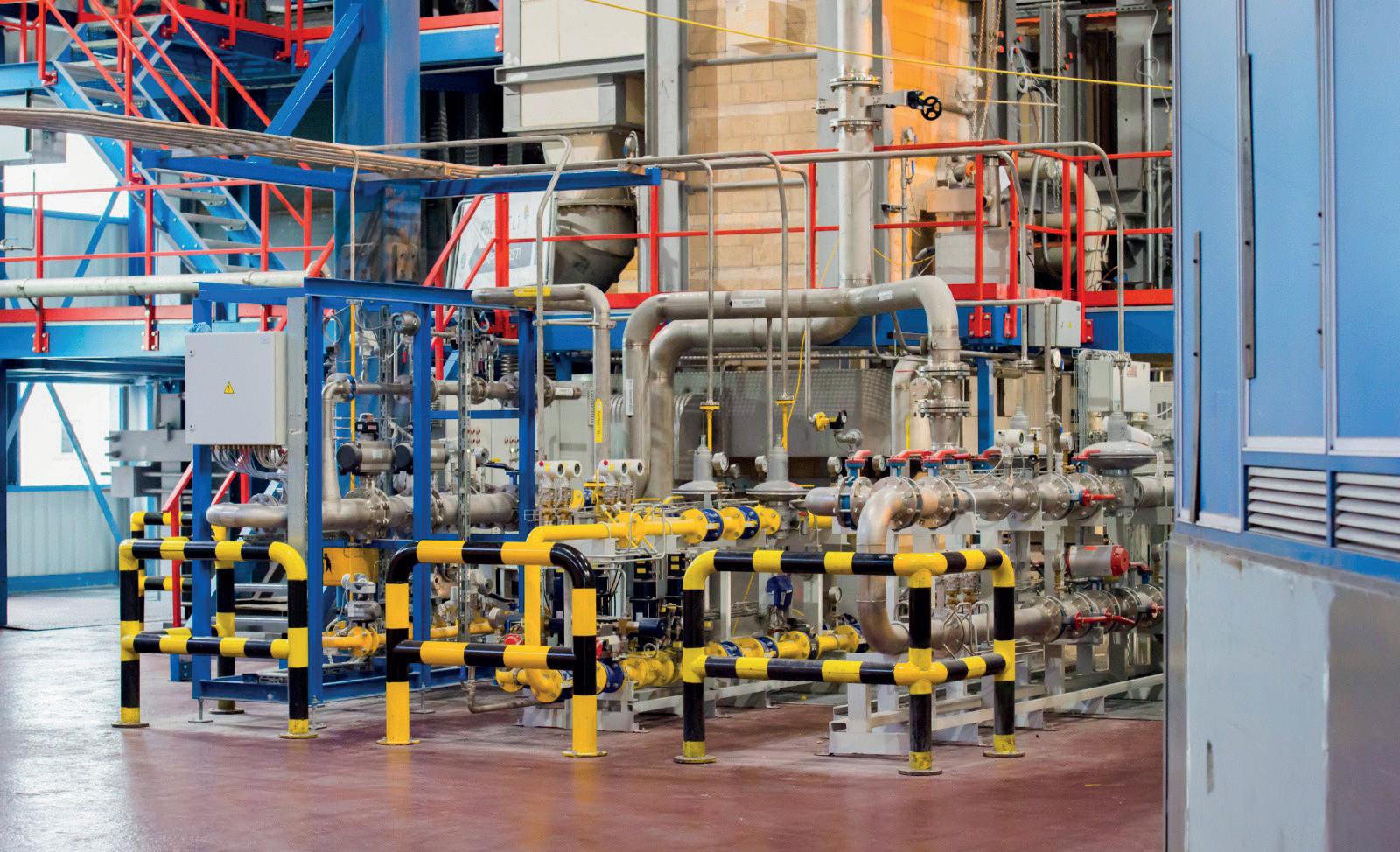
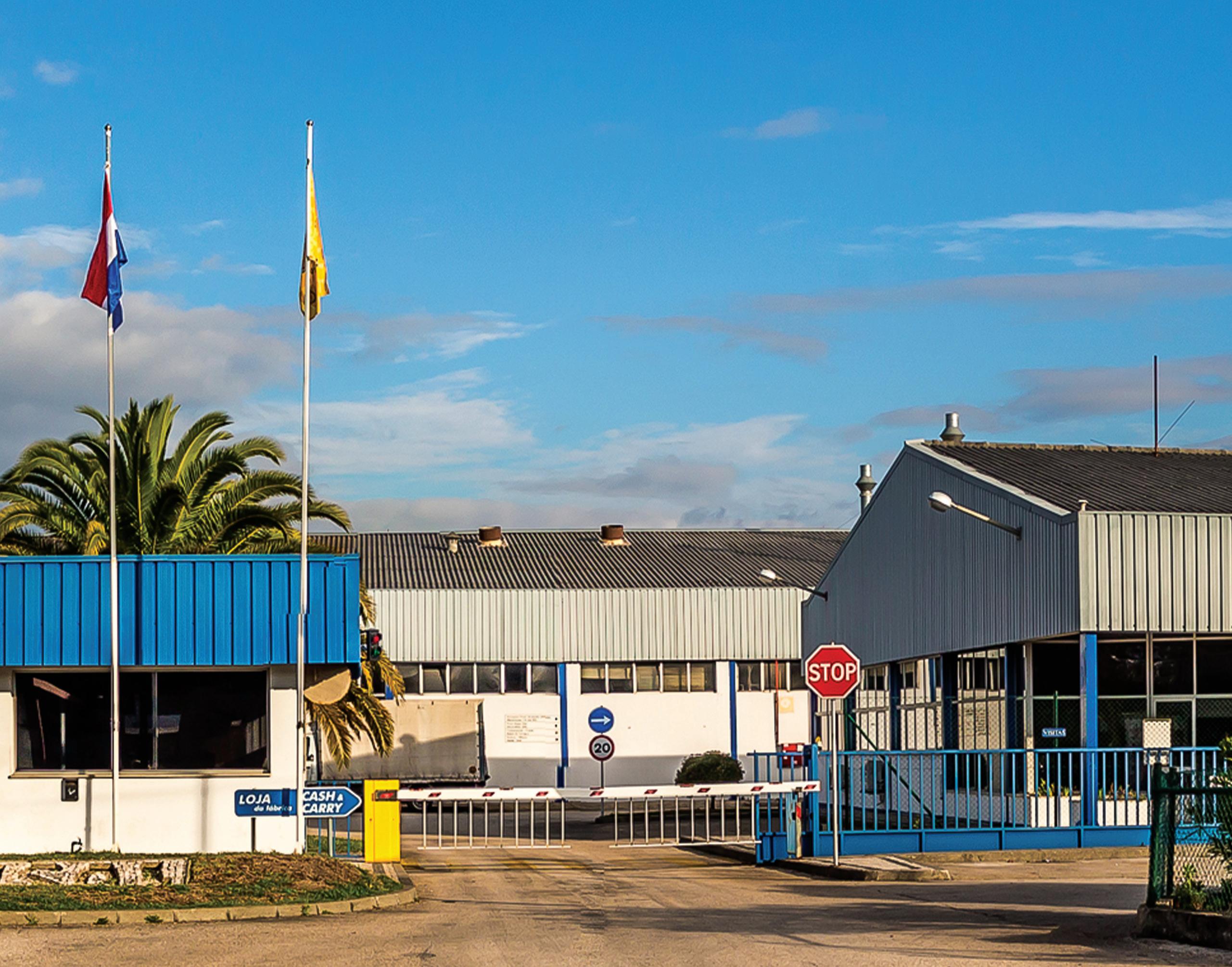
Éxito
Si bien saben que llegar a la neutralidad de carbono no es un camino fácil, señalan el éxito reciente de la empresa con la tecnología Optimelt como indicador de lo que se puede lograr. El señor van Valburg trabajó en el proyecto y vio en primera persona los beneficios de sostenibilidad que la nueva tecnología le trajo a la empresa.
Para el proyecto L1 se instaló un sistema con regenerador termoquímico (TCR, por su sigla en inglés) Optimelt para reducir el consumo de gas natural y las emisiones de dióxido de carbono de los gases de combustión en un 20 %. En este proyecto también se redujeron de manera considerable las emisiones de NOx y Sox así como el polvo en la fábrica.
El señor van Valburg comentó que: «fue un sueño hecho realidad para nosotros ver lo que ahorramos en energía y emisiones. Estoy orgulloso de lo que logramos, tuvimos las agallas de ir por el L1 y la tecnología Optimelt como la primera en el mundo en esta industria, y estamos muy satisfechos con los resultados que hemos conseguido hasta ahora».
Los señores Jordans y van Valburg comentan que la alianza con su socio de suministro Praxair (ahora Linde) junto con el ayuda económica de la UE contribuyeron al éxito del proyecto.
Desean buscar colaboraciones similares con socios en el futuro para su intento de descarbonizar.
El señor Jordans comentó que: «siempre estamos mirando al futuro a nuevas tecnologías para los hornos. Es un gran reto crear la hoja de ruta adecuada y tomar las decisiones correctas. Faltan
Optimelt en Leerdam.�
casi 30 años para el 2050, pero eso son solo dos vidas útiles de un horno, por lo que cualquier decisión con respecto a los hornos debe ser la correcta».
«Esperamos que algunos países de la UE apoyen a la industria en general porque hacer la transición es costoso y habrá demandas de otros sectores, como el del acero y el del cemento».
«Vaya como ejemplo el reciente proyecto Horno del Futuro que no obtuvo fondos de la UE porque otros proyectos industriales ahorraban más CO2».
«Es importante obtener este tipo de subvenciones porque es un gran paso y se trata de una tecnología nueva. Es una gran inversión y se asume un riesgo enorme. Pero si estamos dispuestos a asumir riesgos, estoy 100 % seguro de que encontraremos la manera de mejorar», comentó el señor Jordans.
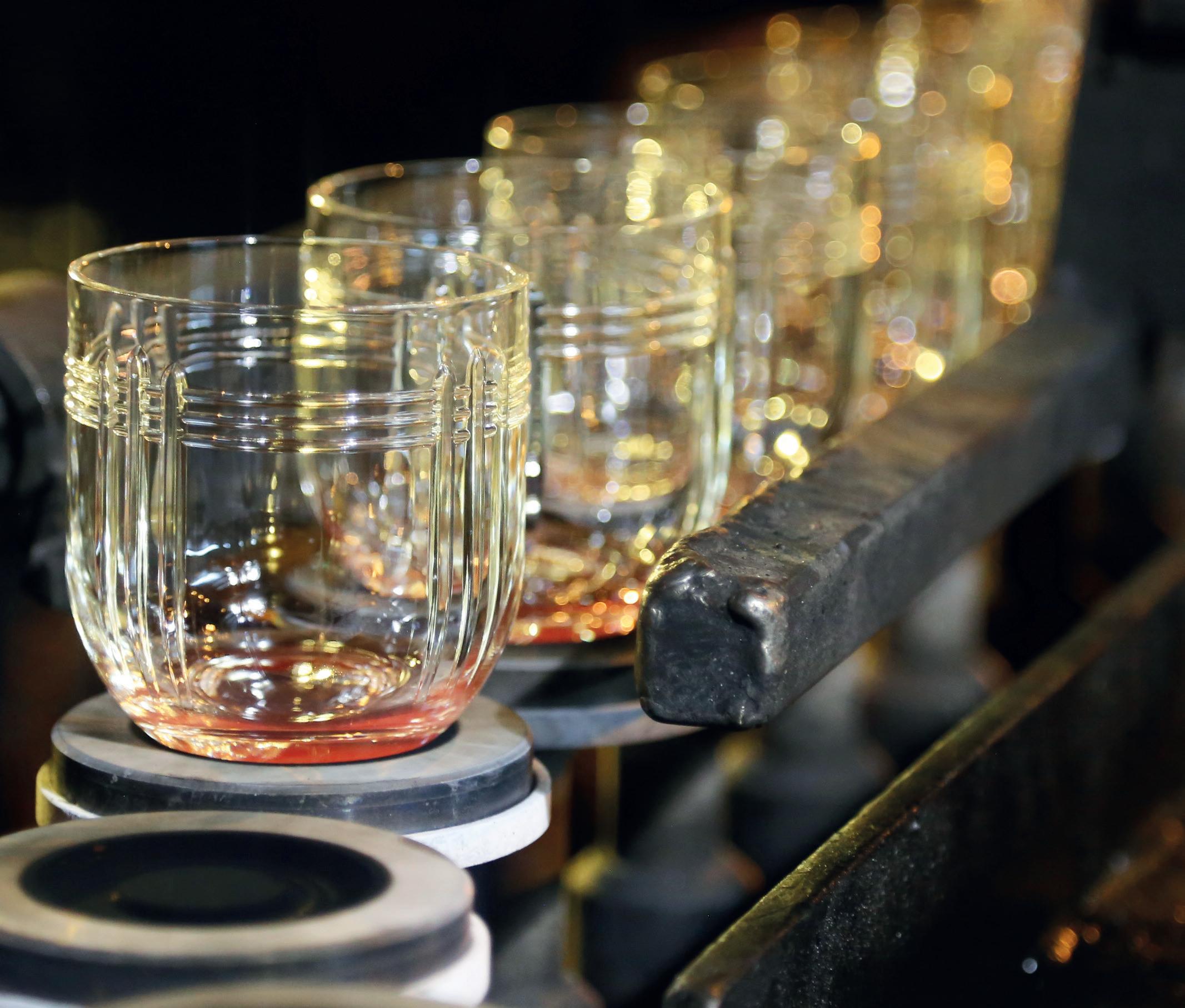
Optimismo
Poco después de nuestra entrevista, los Países Bajos informaron que el 50% de su energía total se generaba con energía «verde», como, por ejemplo, la energía solar y el biogás.
«Es una tendencia que continuará, pero hay que trabajar en forma conjunta con los gobiernos y, con suerte, también con la UE en nuestro caso, como lo hicimos con el L1, y se podrá conseguir un subsidio, y eso ayuda en verdad», comentó el señor Jordans.
Son optimistas de que la industria encontrará «Caminar por la fábrica y ver los hornos es como ver lava de un volcán, y después obtenemos un producto final cristalino. Es un proceso hermoso», concluye el señor Jordans.
soluciones antes del año 2050 y, en el caso de Leerdam Crisal Glass, creen que en el 2040 habrán cumplido entre el 80 y el 90 % de su objetivo. Ambos concuerdan en que la respuesta para la tecnología de los hornos será probablemente una combinación de electricidad y quizás hidrógeno. La electricidad permite procesos más eficientes, mientras que la llama se encendería con hidrógeno. Un horno para vajilla suele durar 15 años y los dos esperan que, durante el ciclo de vida útil de un horno, se encuentren las soluciones para el hidrógeno.
Mientras que las partes comerciales ya están ofreciendo la tecnología para los quemadores y las plataformas, lo que no se ha probado aún es el impacto de esta tecnología en la calidad del vidrio. El objeto de varios proyectos de instituciones como el de nuestros compatriotas de CelSian es encontrar la calidad del vidrio adecuada bajo diferentes condiciones de fusión y el impacto en los materiales refractarios y en la fusión.
Por si fuera poco, la inversión prevista en la red eléctrica nacional garantizará probablemente el suministro de energía.
«Si nos unimos, en cuatro o cinco años, sabremos mucho, encontraremos las soluciones», comentó el señor van Valburg.
COVID-19
Ambos fueron testigos y sobrevivieron a muchas crisis globales en los años que llevan en la industria. La actual crisis del precio de la energía llegó en el mismo momento en el que la industria repuntaba después de la pandemia por la COVID-19. Ambos reconocieron que estuvieron muy preocupados las primeras semanas de la pandemia, cuando se anunciaron los confinamientos en la primavera del 2020.
Pero una vez que el Gobierno neerlandés anunció que ayudaría a las industrias, y en cuanto los detallistas abrieron nuevamente, los pedidos de clientes aumentaron y las ventas crecieron bastante.
El señor Jordans comentó que: «sin contar los tres primeros meses en los que estuvimos muy preocupados, tuvimos dinero suficiente y establecimos un ritmo. Todos nuestros clientes nos pagaron, algunos detallistas más grandes incluso nos pagaron antes para ayudarnos, y eso fue muy amable de su parte».
Tendencias
A pesar de la elevadísima inflación actual en todo, desde el transporte hasta el embalaje, y también los altos precios de la energía, los libros de pedidos están completos. Se mantuvieron las tendencias de clientes sobre la diferenciación y la variedad en la vajilla de vidrio.
«A las personas les gusta ver una variedad de productos antes que ver más de lo mismo a precios aún más bajos».
«Las capacidades del producto que hay en las fábricas son más importantes que las máquinas que hacen la mejor calidad posible al menor coste posible». Vemos diferencias de contornos, de estructuras y formas, de colores y aplicaciones. El vidrio se utiliza, por ejemplo, para plantas, para la decoración, y para almacenar alimentos porque es mucho más seguro que el plástico».
La empresa cuenta con personal que se dedica a poner un pie afuera del negocio diario de la organización y en «leer el futuro» para detectar las futuras tendencias de los clientes. Esto no solo ayudó a la empresa a seguir siendo creativa e innovadora, sino que también la ayudó a estar siempre un paso adelante de la competencia, la mayoría, maestros en el arte de copiar.
Atraer y conservar jóvenes talentos sigue siendo la prioridad más importante de la empresa, en especial si hay competencia con otras industrias. Cree que su foco en la tecnología digital de fabricación de vidrio, junto con otros factores, es una manera posible de atraer milenials para trabajar en el negocio.
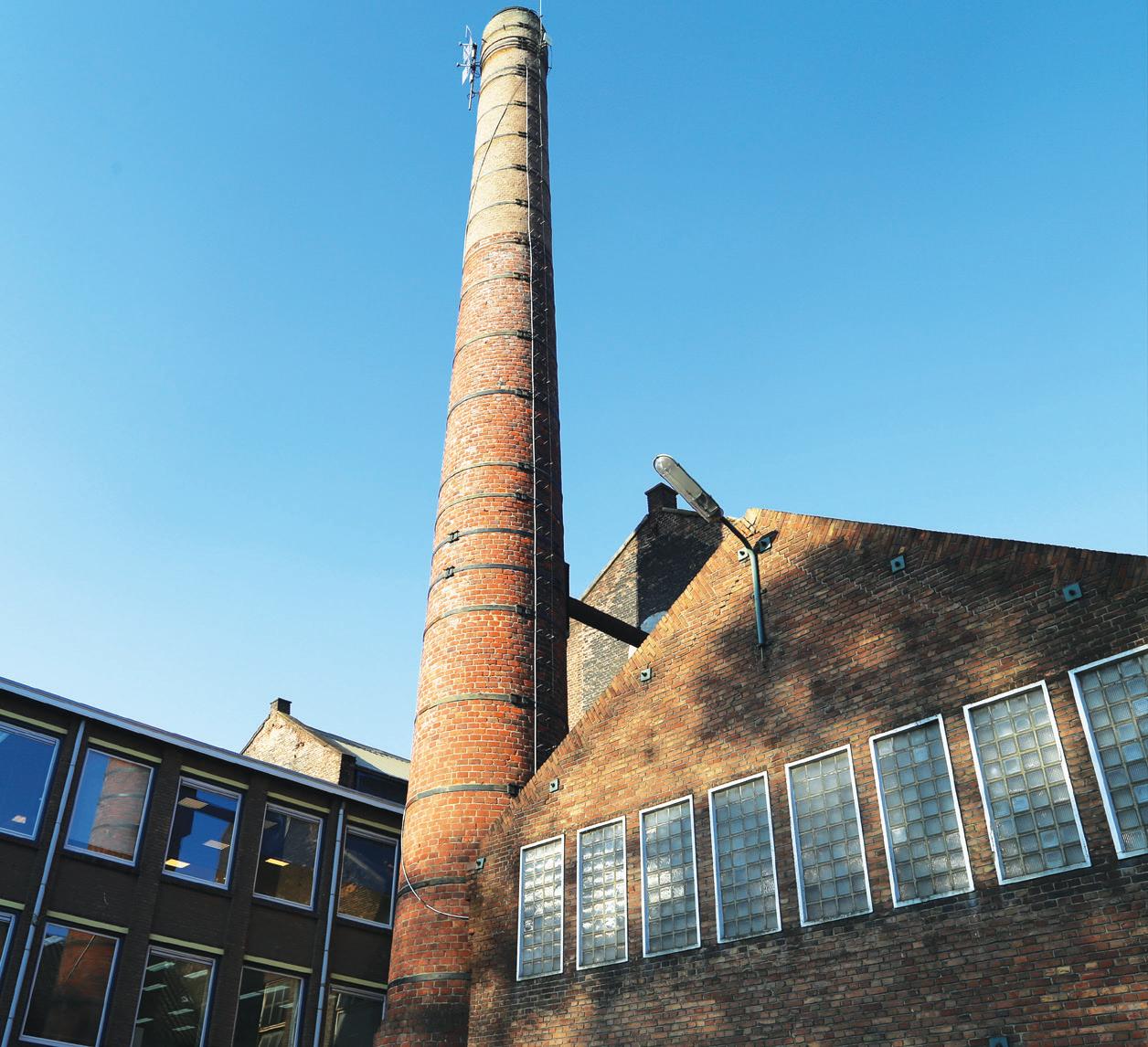
Digitalización
«Estamos avanzando hacia la tecnología digital», comentó el señor van Valburg. «Es necesario avanzar para mejorar los procesos en la fábrica para hacer que los productos sean más eficientes. La tecnología digital puede ayudarnos a ser más astutos y fiables en cualquier proceso que tengamos: la producción, la gestión de los costes o las ventas. Necesitamos tener datos y analizarlos. Debemos predecir las tendencias que veremos y actuar de manera proactiva en consecuencia».
«Una respuesta que era aceptable hace 30 años, hoy es proactiva, y para ello, debemos estar más digitalizados. Entonces, debemos incorporar los sistemas adecuados y las personas adecuadas para analizar y procesar los datos. Esto es lo más importante y lo que impulsará la automatización. Así que nosotros estamos trabajando en este desarrollo». «Los datos son una forma de atraer jóvenes talentos a la empresa, pero también lo es hacer un producto e incorporar diferentes maneras de trabajo aquí o en el hogar para crear un equilibrio entre la vida personal y el trabajo, y nosotros estamos abiertos a ello».
«El producto que vendemos es atractivo, se vende bien en los bares y clubes de Europa. Siempre veréis nuestras copas de cóctel en los programas de entrevistas de la televisión neerlandesa. La combinación del producto que hacemos, el análisis de datos y la mercadotecnia hacen que la empresa sea atractiva».
A pesar de todos los retos y las crisis que enfrentaron en el pasado, la pasión de ambos por la fabricación de vidrio se mantiene intacta.
«El vidrio se fabrica hace miles de años y, para trabajar para la única empresa local que hace vidrio, tenemos mucha pasión. Muchas personas han trabajado en la fábrica por mucho tiempo, a veces generaciones, y eso es lo que me gusta».
«Caminar por la fábrica y ver los hornos es como ver lava de un volcán, y después obtenemos un producto final cristalino. Es un proceso hermoso», concluye el señor Jordans. �
* Director de programas estratégicos, ** Gerente general, Leerdam Crisal Glass, Leerdam, Países Bajos