AISTECH 2023 DETROIT FURNACES PERSPECTIVES SUSTAINABILITY
We preview the AISTech exhibition. Electric smelting furnaces past, present and future.
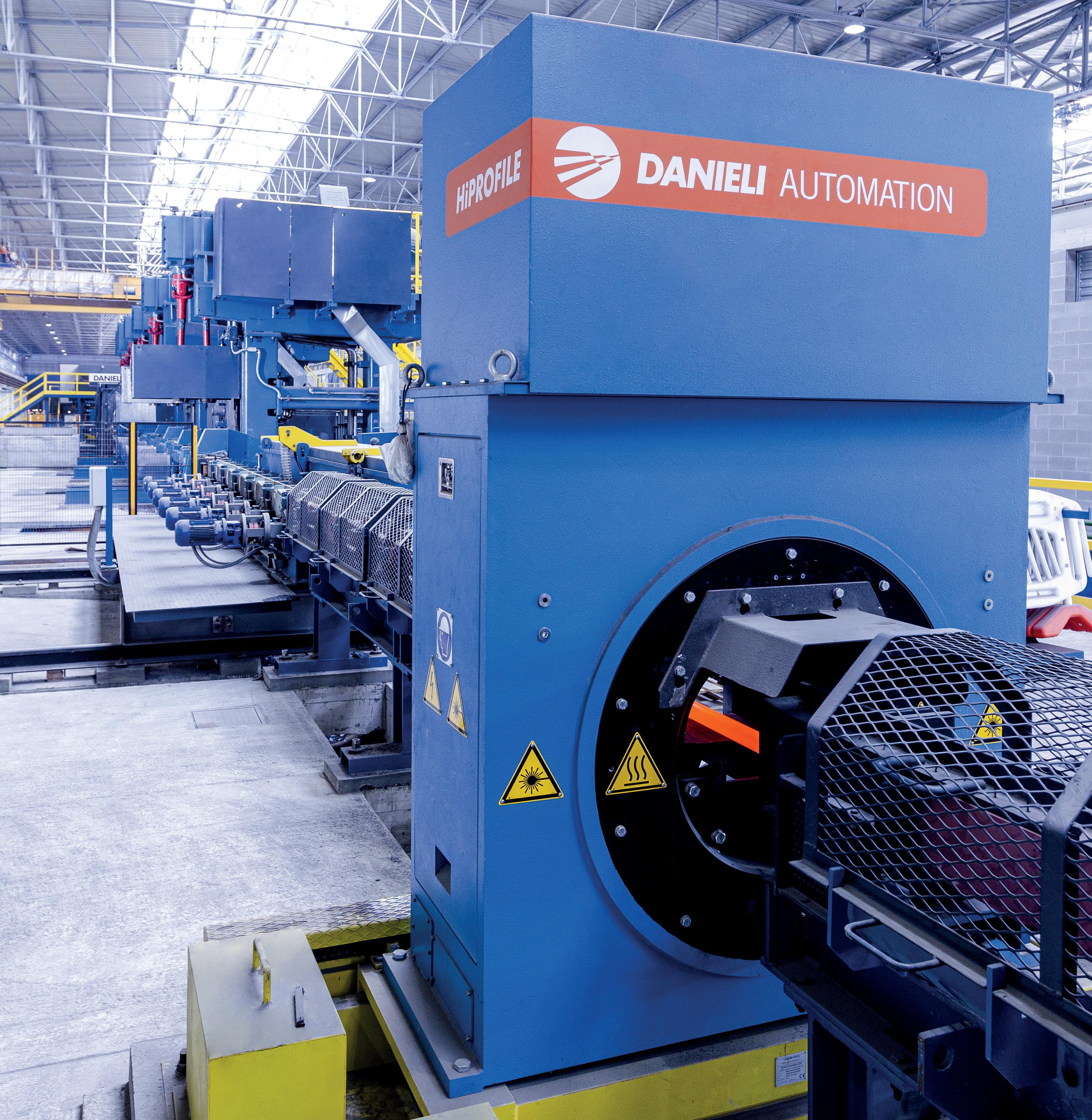
Liberty Steel discusses its decarbonization plans.
We talk to Quoc Pham, CTO of US-based Electra.
We preview the AISTech exhibition. Electric smelting furnaces past, present and future.
Liberty Steel discusses its decarbonization plans.
We talk to Quoc Pham, CTO of US-based Electra.
Software Excellence for Steel and Aluminium Producers
EDITORIAL
Editor Matthew Moggridge Tel: +44 (0) 1737 855151 matthewmoggridge@quartzltd.com
Editorial assistant
Catherine Hill
Tel:+44 (0) 1737855021
Consultant Editor
Dr. Tim Smith PhD, CEng, MIM
Production Editor
Annie Baker
Advertisement Production
Martin Lawrence
SALES
International Sales Manager
Paul Rossage paulrossage@quartzltd.com
Tel: +44 (0) 1737 855116
Sales Director
Ken Clark kenclark@quartzltd.com
Tel: +44 (0) 1737 855117
Managing Director
Tony Crinion tonycrinion@quartzltd.com
Tel: +44 (0) 1737 855164
Chief Executive Officer
Steve Diprose
SUBSCRIPTION
Jack Homewood Tel +44 (0) 1737 855028
Fax +44 (0) 1737 855034
Email subscriptions@quartzltd.com
matthewmoggridge@quartzltd.com
The Future Steel Forum 2023 is looking good. There are, however, a couple of changes that all potential visitors to the event need to be aware of. First, there’s the date, which is currently billed as 2122 September. That is now incorrect. The date has changed and is now 2021 September. Please bear this in mind. Second, the venue. The Forum is no longer hosted by the Hilton Vienna Danube. Instead, it will take place at the Hilton Vienna Garden. I have it on good authority – from somebody who lives in the city –that the new venue is a cut above the old one. In other words, all is good. So, just to summarise: Future Steel Forum 2023, 20-21 September, Hilton Vienna Garden. Please disregard previous information. It goes without saying that I look forward to seeing you in Vienna where we have some very interesting speakers on the programme, including representatives from POSCO, South Korea; Ternium of Argentina; Tata Steel India and JFE from Japan. Hopefully some other major global players from the world of steelmaking will be speaking too and I will, of course, keep you updated.
The Future Steel Forum is now in its
seventh successful year and has become a calendar event for the global steel industry. I like to think that the steel industry looks forward to the Future Steel Forum as much as I look forward to visiting the USA for the AISTech exposition and conference (8-11 May). This year it’s in the so-called Motor City, aka Detroit, home of Motown and Marshall Bruce Mathers lll (Eminem). I hope to see some of you there as the event is jam-packed with stuff of interest from the world of North American and global steelmaking. My personal favourite will always be the Town Hall Forum where senior-level executives from the world of North American steelmaking get together to thrash out some of the big issues affecting the industry. This year’s event features Traci L Forrester, executive vice president, environmental and sustainability, Cleveland Cliffs; Sushma Walker, president, Nucor Business Technology; Michael S Williams, president and CEO of Timken Steel; Richard L Fruehauf, senior vice president – chief strategy and sustainability officer, US Steel; and Barry T Schneider, president and chief operating officer, Steel Dynamics Inc. Sounds like another winner to me!
US steelmaker Cleveland-Cliffs Inc has announced that it will continue to address food insecurity as one of its key areas of social responsibility. The company held its third annual ‘Souper Bowl Food Drive’ across all of its operations earlier this year and collected 240,000 pounds of non-perishable food items. In conjunction with the food donations, ClevelandCliffs and The ClevelandCliffs Foundation have also made cash contributions totalling $500,000 to more than 48 food distribution organizations in the local communities where the company operates throughout the United States and Canada.
Source: Business Wire, 15 March 2023.
Severfield, a North Yorkshirebased steel fabrication firm, has bought a Dutch steel contractor as it seeks to expand its European operations. The firm spent €24m on the acquisition of Voortman Steel Construction Holding B.V., which is based in Rijssen, in the east of the Netherlands. The acquisition will give Severfield a manufacturing base in Europe and will ‘open up attractive opportunities’, including access to the electricity distribution sector, which according to Severfield, is ‘high growth’.
Source: Construction News, 15 March 2023
China plans to cut annual crude steel production in 2023, according to a report from Bloomberg, marking the third year in a row that the government has mandated reduced output in order to rein in carbon emissions. China is the world’s biggest producer and consumer of the alloy. Since output hit a record of 1.053 billion tons in 2020, it has declined each year to remain just above 1 billion tons. The sector accounts for about 15% of national emissions, second only to electricity generation. As part of the plan, the government will also ban new steelmaking capacity.
Source: CNBC, 15 March 2023
UK council chiefs have vetoed plans for a sign showing the former Redcar steelworks buildings as the location was deemed ‘too political’, it has been claimed. The sign, designed by schoolchildren, was earmarked for a roundabout in Dormanstown, but this would have put it next to Teesworks industrial estate which is housed on the defunct steelworks site. The blast furnace was demolished in November 2022, after dominating the Redcar skyline for 43 years. UK Labour party group leader Alec Brown said Redcar and Cleveland Council probably ‘did not want to upset Teesworks’.
Source: BBC, 17 March 2023
SSAB and Vestre have started a collaboration, whereby the Norwegian urban furniture producer will be the first company globally using fossilfree steel to make a piece of
furniture. Vestre will present the first collaboration project later this spring. Thomas Hörnfeldt, head of sustainable business at SSAB, said: ‘‘It is fantastic to start this sustainability journey with Vestre since they share our goal of reducing the carbon footprint throughout the value chain. At the same time, the collaboration also shows the breadth of uses for our fossilfree steel”. Source: Hydrogen Central, 18 March 2023.
Canada has adopted bans on the import of all primary Russian steel products, such as iron and non-alloy steel, and semi-finished and finished products such as tubes and pipes. These trade sanctions follow a package of Russia sanctions adopted alongside the other members of the G7 to mark the one-year anniversary of Russia’s actions
27 Indian steel companies have signed 57 memorandums of understanding with the Indian Ministry of Steel to produce coated/plated steel products, high-strength/wear-resistant steel, specialty rails, alloy steel products, steel wires and electrical steel. According to the Indian government, this will see an additional investment of Rs 30,000 crore in the domestic steel sector, leading to a capacity addition of 25Mt/yr and creating 55,000 new job opportunities.
Source: Zee Business, 19 March 2023
in Ukraine on 24 February.
Source: European Sanctions, 19 March 2023
As the metals industry transforms in pursuit of green steel, the future of sustainability demands pioneers and leaders with vision, courage, and a willingness to push the boundaries of innovation and eco-friendly metals production. Primetals Technologies is redefining sustainable metals production.
We’re making orange the new green.
Tata Steel, which operates two blast furnaces in Port Talbot, UK, has warned that it may shut down one of the furnaces unless the British government outlines longterm plans to support the industry by this summer. The Indian company has informed ministers that it needs details of support by July to justify a potential multi-billionpound investment in green steelmaking facilities at its South Wales site. Officials are in negotiations with Tata Steel and British Steel, the only other firm operating blast furnaces in the UK, to provide £300 million each to boost investment in green technology.
Source: Energy Live News, 20 March 2023.
US Steel has launched its first podcast series, ‘Steel Stories by US Steel’, a look at the ever-changing world of steel, featuring interviews with industry experts and leaders with insights on events and developments shaping the future of steel and the shifting landscape of American manufacturing. Hosted by David Kirkpatrick, technology and business journalist and founder of Techonomy Media, Steel Stories explores US Steel and the steel industry’s contributions to modern society and its journey toward decarbonization.
Source: Business Wire, 20 March 2023
Bhilai Steel Plant (BSP), an arm of state-run Steel Authority of India Limited (SAIL), has been given license to produce a full range of IS 7904 Grade steel wire rods, which are used in bridge cables and tyre reinforcement materials. “Developing customised grades of products with specifications and chemistry as desired by customers has always been a thrust area for SAIL-Bhilai Steel Plant. Not only do these new grades fulfill customer demands and find newer applications, development and supply of value-added grades also fetch higher net sales realisation,” a BSP spokesperson said.
Source: Business Standard, 20 March 2023
The namesake for the Carrie Furnace, a former blast furnace located along the Monongahela River in the Pittsburgh area industrial town of Swissvale, Pennsylvania, has been uncovered by non-profit organization Rivers of Steel’s director of historic resources and facilities, Ron Baraff, through researching an article from the Pittsburgh Daily Post. Caroline ‘Carrie’ Clark was the daughter of William Clark, one of the founders, owners, and the first president of the Carrie Furnace Company. When she was 21 years old, Carrie was the first to light the fires and christen the furnaces. Thus, they were named in her honour. Source: WESA, 21 March 2023
The Indian steel industry has asked India’s Federal Board of Revenue (FBR) to urgently introduce interim tax relief measures to ensure
availability of steel scrap until the ‘issue of letters of credit’ is resolved. Members of the industry have asked the FBR to temporarily reduce withholding tax to 0.25% on scrap supplies and increase sales tax by 1% on supply from non-registered scrap dealers until the issue is resolved by the State Bank of Pakistan.
Source: Business Recorder, 21 March 2023.
Steel production rose by 10kt in the Great Lakes, North America region in March, and is up by 37kt from February, according to the American Iron and Steel Institute. Locally, steel mills in the Great Lakes region, clustered mainly along the south shore of Lake Michigan in Northwest Indiana, made 557kt of metal in the week that ended 18 March, up from 547kt the
previous week.
Source: NWI.com, 21 March 2023.
EIT RawMaterials, a company within the EIT (European Institute of Innovation and Technology) committed to supporting Europe’s transition towards a green economy, has partnered with Anglo American, a leading global mining company, to initiate steel decarbonization. Speaking of the policy to tackle steel decarbonization, Bernd Schäfer, CEO of EIT RawMaterials, said: “It is the mandate of EIT RawMaterials to drive innovation and decarbonise the raw materials sector, from mining to recycling. However, it takes a global village and outstanding industry leadership and collaboration to look beyond their boundaries to solve solutions for the greater good – that is, to address the challenges of climate change.” Source: Innovation News Network, 21 March 2023.
At SMS group, we have made it our mission to create a carbon-neutral and sustainable metals industry. We supply the technology to produce and recycle all major metals. This gives us a key role in the transformation towards a green metals industry.
The collapse of banks has rattled both the construction sector and the steel industry, but with future demand in scrap steel forecast to grow, the long-term outlook is mostly positive, says Manik Mehta*
THE construction industry – and, with it, the steel industry which provides large volumes of steel for construction purposes – was ostensibly unnerved by the collapse of banks, notably the Silicon Valley Bank (SBV) and the Signature Bank. The latest information from the construction sector suggests that the banks’ collapse could be a wake-up call for the construction sector which will have to make a re-assessment of its needs in 2023.
Trepidations were also felt within the so-called affordable housing market in California’s Bay Area (a specialized construction industry and important steel consumer) amid concerns that the SVB collapse could affect mortgage lending. Given the severity of the short-term impact for the construction sector, the path to a long-term recovery appears arduous, with many crystal-ball gazing pundits suggesting that the SVB’s failure could have a stronger impact than presently assumed.
The timing of the SVB’s failure was also
very critical for the construction sector, which had only recently begun to stage a recovery following a turbulent 2022. However, while it does face challenges such as a growing shortage of workers coupled with high-interest rates, there is optimism within – and also outside – the construction industry that the long-term future outlook is good. Government sources have been suggesting that investments in the construction sector will gradually rise, particularly in infrastructure construction because of the massive government allocations for modernizing and developing infrastructure. The funding will sustain infrastructure construction for years to come. Nevertheless, it would be myopic to ignore the fact that the SVB’s collapse will not ‘just pass away’ without causing setbacks to private and affordable housing, particularly on the west coast.
One dark cloud that continues to hover over the US economy – and the steel industry – is the fear of a recession, a word
*US correspondent, Steel Times International
that is being uttered more often now than before. Jean Bolvin, the head of the BlackRock Investment Institute, observed recently during a press briefing at the New York Foreign Press Centre, that central banks would not intervene. “…That’s the kind of regime phase that we’ve been [in] since last year, where the message from central banks has been all about bringing inflation [down] to 2%. I think we’re still in that regime, and I think from the central banking community it’s really about the cost of losing control of inflation, [which] is way higher than creating a recession, and while they would like to avoid a recession and they speak as if they hope it’s going to happen, they’re going to be more comfortable with having a recession than being held responsible for having created a big inflation problem.”
Notwithstanding the optimistic longterm outlook for construction projects, which will benefit from the infrastructure investment of some $225 billion under the
Infrastructure Investment and Jobs Act, the industry faces other short-term problems beyond the SVB fiasco and the highinterest rates. The recession that experts are predicting, will not just envelope the US but will also affect the world; this, in turn, is very likely to affect the construction professionals, particularly those involved in the logistics and sourcing of materials from around the world.
This being said, steel prices are influenced by several factors. Prices can surge following breakdowns in supply of raw materials, which has happened following the Ukraine war, and the resulting rawmaterial shortages that have sent prices spiraling. As the year 2023 started, US service centres had low levels of inventories, driven by the fear of accumulating highpriced inventory.
But things seemed to have changed with many looking for additional steel as supplies remain tight resulting from lower utilization levels at steel mills. The lower inventories with service centres suggest that buyers have less quantity available to buy from; indeed, many have been operating without certain types of steel products in their inventories. As a result, steel mills such as Steel Dynamics or Nucor’s Gallatin mill in Kentucky have been operating below the expected levels, though both corporations expect to improve their performance in the second quarter. Steel mill outages are also limiting the US market and are expected to last until May.
The bottlenecks in steel supply have been exacerbated by declining steel imports, thus eliminating a supply source that helped bridge the short supply from domestic production by sourcing foreign steel which
offers the consolation of costing less than domestically produced steel. Indeed, the February data from the US Commerce Department suggests that the country recorded the ninth consecutive month of declining imports.
Meanwhile, steel producer US Steel has resumed operation of its blast furnace no. 8 at its Gary steel mill. It had idled both the no.3 blast furnace at Mon Valley Works in Pennsylvania and the no. 8 furnace in Gary in 2022 after steel prices had plummeted from the high levels of 2021 as fears spread of an impending recession. The steel producer resumed operation of both blast furnaces, and the outlook for steel has resultantly improved. US steel producers have benefited from the increased production levels of car manufacturers who had earlier adopted a cautious approach because of recent shortages in semiconductor chips and other materials.
US Steel confirmed in a press release that the flat-rolled segment’s order book ‘reflects broad improvements across most end-markets’.
The No. 8 blast furnace at Gary Works can produce up to 1.5Mt of iron annually.
It was originally idled for a planned maintenance project last year and was supposed to be restarted in August after three months of construction, but then market conditions deteriorated and US Steel opted to idle it until demand returned.
In positive news, analysts expect scrap demand to rise, as market conditions suggest impressive growth in the coming years. According to the latest industry report by Fact.MR, a provider of market research and competitive intelligence, the global steel scrap market is projected to grow at a CAGR (Compound Annual Growth Rate) of 4.9% and reach a total volume of 1.05Mt by 2033.
Steel is one of the most recycled materials in the world; one of the main components used to make steel is recycled steel. Steel is simple to separate from the waste stream and be recycled due to the metal’s high magnetic characteristics. Steel recycling also aligns well with the global call for decarbonization; besides contributing to a significant decline in CO2 emissions, it reduces consumption of iron ore, and contributes to huge energy savings. Scrap is anticipated to make up a sizeable amount of metal production in the future as deposits across the world become scarce and the costs of obtaining ore keep rising.
Future demand for steel scrap is anticipated to rise in tandem with an increase in the demand for raw materials used in the manufacturing process from emerging economies such as China, India, and Brazil. Steel has been able to meet the challenge provided by competitor materials due to the development of new lightweight goods, bake-hardened grades, and highstrength steels. �
Technologies offering enhanced product performance and a more environmentally sustainable production process.
John Cockerill Industry’s ARPs come with smart plant control systems, provide waste energy recovery and drastically reduce pickling process plants’ fresh acid demands and waste streams in general. What is more, they are providing the lowest emissions in the market.
Our E-Qual® equipment and processing lines are designed for the production of strong, ultrathin, lightweight, and high-quality Non-Grain Oriented (NGO) steel grades essential for the future of e-mobility.
8 - 11 May | Détroit, Mich., USA
BOOTH #2165
johncockerill.com/industry
JVD (Jet Vapor Deposition) offering the lowest ‘global warming potential’ according to life-cycle assessment measures
A world first and a technological breakthrough in steel coating, this unique technology providing multiple advantages, was developed for steel giant, ArcelorMittal with the help of our experts.
Today John Cockerill Industry is in charge of commercializing this unique technology worldwide.
In the second part of an ongoing feature, Germano Mendes de Paula* discusses the restructurings of Mannesmann Brazil; including its transformation into a whole subsidiary, its technological developments, and the opening of a new greenfield mill.
ALONG the first decade of this century, Mannesmann Brazil experienced two important corporate restructurings; the first regarding its parent company, with the second being its transformation into a whole subsidiary.
In fact, 2000 was decisive year for Mannesmann group, as it was the target of a hostile take-over by the British telecoms company Vodafone. To comprehend this transaction, it is necessary to consider the previous process of productive diversification undertaken by Mannesmann. In 1970, the company’s original tubes and trade division still represented 77% of total sales, with this figure falling to 54% in 1980 and even to 8% in 1999. Meanwhile, the share of the capital goods and automotive divisions in the revenues increased from 16% in 1970 to 44% in 1980, reverting partially to 41% in 1999. The telecommunications division, which was set up in the 1990s, came to represent 39% of total sales in 1999. It is estimated that roughly about two thirds of Mannesmann’s investments in the 1990-1999 period were
directed to the telecoms sector. For this reason, Mannesmann became a target of Vodafone in 2000.
After the takeover, the German steelmaker Salzgitter acquired a majority interest in Mannesmannröhren-Werke (MRW), which had made heavy losses, for the symbolic price of one Deutschmark. However, since 1997, Mannesmann’s tube operations were under the umbrella of Vallourec & Mannesmann Tubes (V&M Tubes), a joint-venture between the French tubemaker Vallourec (55%) and MRW (45%). In addition, MRW controlled 21% of Vallourec.
In July 2000, MRW sold its 76% stake in the Brazilian subsidiary to V&M Tubes, which can be understood as an intra-group ownership restructuring. The Brazilian firm was renamed as V&M do Brasil. Moreover, it promoted a share purchase offering, aiming to acquire all the shares held by minority shareholders. V&M Tubes improved its participation to 93% of the Brazilian subsidiary, which was delisted from São Paulo Stock Exchange as of September 2000.
In 2005, Vallourec gained full control of V&M Tubes by purchasing MRW’s 45% stake in the company. In the following year, Salzgitter sold its remaining 17% participation in Vallourec. Consequently, for the Brazilian subsidiary, its original parent company was Mannesmann, then V&M Tubes, and then Vallourec during the period 1997-2005.
Graph 1 shows the evolution of the Brazilian subsidiary, in its Barreiro mill, during the years 2000-2010. Underpinned by technological improvements developed in the previous decade, the company was able to obtain a good productive performance, before the global financial crisis of 2008-2009. Pig iron production increased from 512kt in 2000 to 610kt in 2007, whereas the crude steel output was respectively 519kt and 686kt. The fabrication of seamless tubes also rose from 423kt to 603kt during the aforementioned period. However, not surprisingly, all operations were severely impacted by the global financial turmoil from 2008 onwards.
* Professor in Economics, Federal University of Uberlândia, Brazil. E-mail: germano@ufu.br
In 2005, Tubos Soldados Atlântico (TSA) was established, as a joint-venture between Europipe (70%), V&M do Brasil (25%), and trading company Interoil (5%). It startedup its 90kt/yr large diameter welded tubes operation, at a cost of $65M, in 2007. The new plant is located in Serra, in the State of Espírito Santo, close to the ArcelorMittal Tubarão steelworks, which supplies hotrolled coils. In 2012, V&M increased its stake from 25% to 96% in TSA. In 2020, the plant was renamed as Vallourec
Tubular Solutions (VTS) – Serra, reflecting Vallourec’s full ownership.
More importantly, the negotiations between Vallourec and the Japanese steelmaker Sumitomo Metals (SMI) regarding the construction of a large greenfield project to produce seamless tubes in Jeceaba, in the State of Minas Gerais, began in 2006. In the following year, Vallourec & Sumitomo Tubos do Brasil (VSB), a joint-venture between Vallourec (56%), SMI (40%) and Sumitomo Corp. (4%), was established.
Jeceaba’s project consisted of a 1.5Mt/yr pelletising plant, a 300kt/yr blast furnace, a 1Mt/yr EAF-base steel shop and a 600kt/ yr rolling mill, for tubes with a diameter between 168-406mm. Concerning round bars output, approximately 70% would be consumed at the same site, whereas the rest would be used in the Barreiro mill and exported. The new mill would be primarily dedicated to the manufacturing of tubular petroleum products. The start-up was scheduled for 2010, while the total investment was estimated at approximately $1.6bn. The increase in supply was much higher than the projected domestic demand growth, so that 80% of the production of the new plant would be exported.
Jeceaba was chosen because of the following reasons: a) it is just 100km away from the Barreiro mill, so they can coordinate their operations; b) it is only 70km from the Pau Branco mine, which is the captive source of iron ore; c) it is 500km from Sepetiba and Rio Janeiro harbours; d)it has good rail access to the mentioned ports and Barreiro mill; e) it has a good supply of electricity and gas; f) there is room for future expansion.
Jeceaba’s construction commenced in 2008, while the foundation for rolling mill building occurred in 2009, followed by the start-up of the blast furnace in 2010. The mill was officially started-up in September 2011, one year after its original planning. This is a small delay, considering that the global steel industry was shaken by the collapse of Lehman Brothers in 2008.
It is interesting to note that Jeceaba has implemented a 0.96Mt/yr Consteel®, facility which was the first and only piece of equipment to pre-heat scrap in Brazil so far. It came on stream, jointly with other equipment in the melt shop, in August 2011. Nevertheless, the blast furnace had its assembly completed as was ready to start operations at the end of 2011. However, the retraction of the steel market led to the beginning of the operation being delayed to July 2014. While it can operate with both coke and charcoal, it has been consuming the latter since its start-up. Jeceaba’s original plans included another blast furnace of the same size, but the company is still waiting for market conditions to improve before completing its assembly. The evolution of Barreiro and Jeceaba’s productive performance from 2011 onwards will be discussed in the next part of the article.�
World leading technology for applying texture to rolling mill rolls using state of the art Electro Discharge Texturing techniques.
The latest technology in non-contact surface & sub-surface inspection of hot and cold rolling mill rolls with Eddy Current, Compression Wave and Creep Wave capabilities.
Bespoke In-Chain and off-line strand condition monitoring systems for continuous casting.
Sarclad UK sales@sarclad.com
Sarclad North America sales@sarcladna.com
Sarclad China sales.china@sarclad.com
sarclad.com
Sarclad India sarclad.india@sarclad.com
CARBON emission reduction has been at the forefront of every global discussion since the United Nations’ 26th Cooperation of Partnership (COP26) meeting held in Glasgow in 2021. All UN members voluntarily declared their ‘net zero’ plans. Following them, India also announced plans to become carbon neutral by 2070. With this declaration, the government of India took several measures to reduce CO2 emissions through various means. Industries were asked to allocate funds and upgrade their plant and machinery, as consumer markets across the world started focusing on low-carbon products. In order to remain competitive in the world market and continue business unabated, the Indian steel industry also advanced its facilities with next-generation plants and machinery and started producing low-carbon products without compromising on quality.
India’s steel sector accounts for 12% of total CO2 emissions with an intensity of 2.55 tonnes CO2/TCS as against the global average emission intensity of 1.85 tonnes CO2/TCS. This clearly indicates that India needs to adopt more industry-friendly initiatives to reduce emissions and achieve the world average. To reduce carbon emissions, India’s Ministry of Steel has been continuously engaging with stakeholders in the environment, renewable energy, mines, and other such ministries for the past several months. With this, the government focused on carbon emissions reduction technologies such as green hydrogen in steel making, carbon capture, storage, and utilization (CCUS), and the best available technologies on energy efficiency as well as
transitioning to renewable energy.
In the Ministry of Environment, Forest and Climate Change’s (MOEF&CC) biennial update report to the United Nations’ Framework Convention on Climate Change (UNFCCC), its estimation of India’s total release of CO2 in 2016 was 135.42Mt. But, with the expansion plans as per the National Steel Policy presently underway, India’s overall CO2 emissions are all set to increase substantially as a result of the steel industry.
India’s steel industry plays a pivotal role in crucial sectors including construction, infrastructure, automotive, engineering, and defence. It has witnessed phenomenal growth over the last few years, and is now the second largest producer in the world, beaten only by China.
Both production and consumption of steel have increased significantly in the last few years. Data compiled by the Joint Plant Committee (JPC) under India’s Steel Ministry showed crude steel production at a record 103.18Mt between April 2022 and January 2023 period as against 99.03Mt reported for the previous full financial year (i.e. April
2021-March 2022). Similarly, finished steel production during April 2022-January 2023 stood at a high of 98.26Mt compared to 93.41Mt in the previous full financial year. Further, India’s finished steel consumption was reported at 96.38Mt between April 2022 and January 2023 in comparison with 86.97Mt in the last financial year (April 2021-March 2022).
From the steel industry’s point of view, the government has divided the entire 2070 plan into three broad categories. Focusing on the short term – until 2030 – the Indian government has decided to promote energy efficiency in the steel industry and encourage steel producers to emphasize resource efficiency and renewable energy for a sustainable future. For the medium term – between 2030 and 2047 – the focus area could be green hydrogen and carbon capture, utilization, and storage. For the long-term perspective – between 2047 and 2070 – disruptive alternative technological innovations are the primary focus that can help achieve the transition to net zero.
To promote healthy growth in the steel industry with its focus on low-carbon and
best-quality products, India has introduced the Steel Scrap Recycling Policy which enhances the availability of domestically generated scrap to reduce the consumption of coal in steel making. Also, the Ministry of New and Renewable Energy (MNRE) has announced the Green Hydrogen Mission for the production and consumption of green hydrogen as a fuel and replacing fossil fuels like coal. Additionally, India introduced the Motor Vehicles Recycling Rule under which old vehicles were scrapped and sent for recycling. The hope is to eventually increase the availability of steel scrap in the country. A national solar mission was also launched to promote solar energy and help the steel sector to reduce overall CO2 emissions. Also, a Perform, Achieve,
and Trade (PAT) scheme was introduced to incentivize the steel industry to reduce energy consumption.
According to the World Steel Association, scrap plays a key role in suppressing industry emissions and resource consumption. Every tonne of scrap used for steel production avoids the emission of 1.5 tonnes of CO2 and the consumption of 1.4 tonnes of iron ore, 740 kg of coal, and 120 kg of limestone.
India’s Steel Policy estimates the country’s crude steel production will reach 300Mt by the financial year 2030-31, by expanding capacity through both greenfield and brownfield projects.
The government has emphasized the lower use of power in existing steel production factories. To achieve this goal, however, the government has encouraged steel producers to cut down on their use of iron ore and coking coal as raw materials to manufacture the best quality products for application in infrastructure and construction projects. Barring specific applications where iron ore is required to be
used as raw materials, the government has encouraged producers to use ferrous scrap to produce steel products, especially for rural consumption.
The government plans for secondary steelmaking using ferrous scrap as raw material to account for 40% of India’s total steel production. Presently, India imports a huge quantity of ferrous scrap to meet the raw material demand for producing secondary steel. Production of secondary steel by using scrap is estimated to utilize 74% less energy than the production of steel from iron ore.
The International Energy Agency (IEA) has called upon local government and the steel industry to adopt ways and means to reduce carbon emissions at least by 50% by 2050 and continue to bring down the release of greenhouse gas to make the world’s climate goals successful. Overall, green steel production and consumption in India has started gaining momentum as steel companies make efforts to reduce their carbon footprint, but the transition is very costly. �
Solar Turbines offers solutions for unsteady flows of wide composition fuel gases such as high H2, CO, CO2 and HCs. Transform what you thought was waste gas into valuable power and heat.
2023
The Future Steel Forum, now in its SEVENTH successful year, is heading for Vienna this September to examine the important relationship between digital manufacturing and the decarbonization of the steelmaking process. Come and listen to experts from the two most important areas of global steelmaking at present. This is a must-attend conference for anybody with an interest in the fast-developing world of Industry 4.0 technologies and those responsible for sustainable steel manufacturing.
CONFIRMED SPEAKERS FOR FUTURE STEEL FORUM IN VIENNA INCLUDE:
AISTech 2023, held 8-11 May in Detroit, USA, promises an array of new products, systems, and solutions from its vast list of exhibitors. See below for what not to miss at North America’s largest iron and steel technology conference and exposition.
AMI Automation, an international automation and control solutions company, will be exhibiting a range of new products at AISTech 2023. The SmartFurnace, which is an artificial intelligence expert system, is designed to dynamically select the best operating points for electrical and chemical energy input based on the actual heat conditions adapting to every aspect of the furnace operation. The Off Gas Module, says AMI, will interact with the SmartFurnace Oxygen Module to control the carbon injection and oxygen, reducing the emissions of CO, increasing the CO2 produced during the combustion of carbon and oxygen, and optimizing the chemical energy input in the furnace. Another product to be showcased at the event is AMI’s Infrared Off Gas Sensor system, which has the capability of measuring CO, CO2, H2O, temperature, velocity and flow. The modular design allows these gases to be measured as required, says AMI, with the main advantages being the extremely easy installation and tested reliability.
Other products to be exhibited include the IoConveyor, for controlled scrap feeding, the IoTrode, for optimizing electrode consumption and controlling the rate of watercooling sprays, and the SmartKnB – a graphical programming platform to develop complex solutions in which process engineers and customers can build, test and validate models to improve EAF operation.
AMI Automation will be exhibiting at booth #2257
Global technology provider Sarclad will be launching its Multi-Servo Array EDT, which the company claims is targeting applications that require the highest possible texture quality and consistency. Sarclad’s EDT MSA has a single or double texture station design, which then traverses the full width of the roll barrel, combining individual servo control for each electrode, with
an innovative formed array. The control system employs a novel closed-loop power delivery design, which ensures that the energy delivered by each spark is precisely controlled,
Primetals Technologies, a leader in plant solutions, will be showcasing its Arvedi Endless Strip Production, which provides flat steel producers with a means of producing thick 25mm to ultra-thin gauges of just 0.6mm in an endless casting and rolling arrangement that is both compact and energy efficient. Compared to the conventional casting and rolling process, says Primetals, Arvedi ESP combines the slab casting, cooling, storage, reheating, hot strip mill, and rolling processes into one effective process. The range of steel grades produced using an Arvedi ESP includes advanced steels such as HSLA, pipe grades – e.g., up to API X80 –, silicon steel, HSS and AHSS grades, DP, and multi-phase steel grades. One of the qualities of the strip made with Arvedi ESP is the fact that it can be regarded as a ‘cold-rolled substitute,’ meaning that it fulfils the quality criteria normally only achieved through additional cold rolling. Arvedi ESP produces gauges from 0.8mm to 1mm, e.g., 1mm thick steel with yield limits up to 315 MPa, 1.2 mm thick steel with yield limits up to 420 MPa, 1.4mm for DP 600, and 2mm thick HSS with yield limits up to 700/800 MPa. Checkered plates with 1.5 to 3.5mm thicknesses were also recently produced on an Arvedi ESP line.
Primetals will also be exhibiting its electric steelmaking portfolio, which includes the EAF Ultimate and EAF Quantum, designed to deliver high-quality results with advanced technologies. The EAF Ultimate provides a comparable tapping weight to converter steelmaking routes, and the EAF Quantum features scrap-preheating via waste heat recovery, decreasing energy consumption to 280 kWh/t, resulting in overall savings. Key features of all electric arc furnaces from Primetals Technologies include reliability, low energy consumption, and a rapid return on investment.
ensuring greater consistency of the surface texture. The texturing process is closely monitored in real-time by an advanced digital control system, designed to provide the highest levels of process control, while simultaneously communicating detailed feedback to the control system and machine operator. Each texture head can be equipped with a range of custom options from 12 to 36 electrodes per station, with a double station machine providing a
maximum capacity of 72 electrodes, for those seeking a roll texturing capacity in excess of 10,000 rolls per year.
Speaking on the launch of the new application, Grant McBain, head of sales and marketing at Sarclad commented: “The MSA can be applied and tailored to each customer’s own specific set of requirements. Providing roll shops with the ability and versatility to provide textures specific to their own needs and applications is paramount and that is what the Sarclad EDT Multi Servo Array concept delivers.’’
Sarclad will be exhibiting at booth #1786
Thermal processing equipment supplier Inductotherm Heating & Welding will be showcasing its recent award: the Silver Ecovadis Sustainability Rating. This new accolade follows on from Inductotherm Heating & Welding’s triple BSI - ISO accreditation awarded in June 2022, which included ISO9001 for Quality, ISO45001 for Occupational Health & Safety and ISO14001 for the Environment.
Inductotherm Heating & Welding is undertaking a process of developing and improving its environmental and sustainability practices to ensure it is ‘sensitive and responsible to the local and wider environment’. Via implementing a wide range of changes in all areas of the business, from adopting renewable energy to changing to eco-friendly supplies and engaging with suppliers, the company hopes to commit further to sustainability.
In addition to its commitment of social and environmental responsibility, the company hopes that these accolades provide its customer base with the reassurance that they are engaging with a forward-thinking and ethical company committed to providing its customers with the environmentally sound and continually improving service. Achieving the Silver rating has allowed Inductotherm Heating and Welding to attain ‘Preferred Supplier Status’ with existing Tier 1 customers who highly value sustainability across all areas of their business.
INDUCTOTHERM will be exhibiting at booth #2463
AMETEK Land and AMETEK Surface Vision have joined forces to present their solutions for temperature measurements and surface inspection in steel manufacturing to visitors at the AISTech 2023 exhibition hall.
AMETEK Land is an experienced supplier of non-contact temperature measurement solutions to the steel industry, with dedicated solutions and flexible instrumentation that can be customised for specific processes. These solutions include the SPOT family of fully featured, high-performance pyrometers for fixed non-contact infrared spot temperature measurements. These are available in a variety of operating wavelengths and temperature ranges to meet different process requirements. The advanced SPOT GS model is specifically designed for continuous, accurate measurement of coated steel strip temperature during galvanizing and galvannealing.
Also on display will be the Cyclops L portable pyrometer range of highly accurate hand-held instruments. Ergonomically designed for singlehanded use, these non-contact thermometers provide easy, accurate point-and-measure temperature
readings. The Cyclops 055L model will be of particular interest to iron and steel manufacturers, with a measurement range of 1000 to 2000 °C (1832 to 3632 °F) and Meltmaster measurement mode designed for molten metal and foundry applications. At AISTech, the company will demonstrate its SmartView and SmartAdvisor solutions for a wide range of surface inspection applications. These flexible, modular systems are used throughout the steelmaking process to assure the highest level of quality, says AMETEK.
Larry Smith, LAND director of sales – Americas, said: “AISTech is the number one industry event for iron and steel manufacturers, and we are looking forward to meeting old and new customers alike. Most of all, we’re excited to introduce them to our range of solutions that will help them to improve thermal efficiency, increase product quality and control emissions, and support industrial decarbonization.”
AMETEK Land and AMETEK Surface Vision will be exhibiting at booth #2023
Kelk, a leader of performance sensors and systems for the steel and aluminium industries, will be exhibiting its ACCUCAMB Camber Gage Model C885; an advanced solution for true bar shape measurement and strip steering applications. The ACCUCAMB C885 Camber Gage is a non-contact optoelectronic instrument, which measures the camber (curvature), strip angle, centreline and width of a transfer bar during the rough rolling process. In the True Bar Shape configuration, the gage will also determine the shape of an entire bar. The ACCUCAMB C885 Camber gage also measures the centreline deviation and width of a strip during the finish rolling process.
The sensor uses an area array camera to image a portion of the bar. The lines that best match the bar edges are extracted from the data and used to determine width, centreline deviation and bar angle. The image data is also analysed to estimate bar camber. Advanced algorithms provide accurate edge detection and allow for limited temperature gradients, scale and steam.
The scan rate is optimized for each application and held constant. The measurements are most accurate where the strip height above the roll table is predictable, and a standard MODBUS/ TCP communications protocol provides access to all process data and gage status information.
Kelk will be exhibiting at booth #2042
Our solutions for strip processing lines enable you to optimise your manufacturing processes and increase your production quality:
» EMG iTiM: Online thickness measurement
» EMG SOLID®: Online oil layer measurement for electrical steel
» EMG iCAM®: Online strip and slit strip width measurement & Edge crack and hole detection
» EMG SORM®: Online roughness measurement
» EMG EVK3: New optical sensor generation
emg.elexis.group
AIC, an Italian company specialized in industrial systems for the iron and steel sector, will showcase new updates on its all-electric patented mechatronics station, introduced on the market as TRIMBOT, combining mechatronics, industrial robotics and 3D vision systems with a high level of automation and artificial intelligence. The system is able to perform autonomous trimming and sampling of finished coiled products’ head and tail ends and operate within any type of coil handling area, whether vertical, horizontal, or a combination of both. The target of the system is to eliminate the actual manual trimming activities based on counting rings, performing the trimming process more than 600 times more accurately compared with the conventional manual trimming, or any other ring-counting trimming solution, according to AIC.
The company will also showcase its Ring Processing Turret; a circular guide with a shape that follows the natural circular shape of the coiled wire, that identifies, measures, cuts and separates the trimmed material from the rest of the coil. The Ring Processing Turret is mounted to a large diameter slewing ring which is bolted to the main trolley, and the rotation of the Ring Processing Turret is generated by a gear motor mounted on the main trolley.
AIC will be exhibiting in booth #1156
Falkonry, an AI software provider, will be presenting its industrial analytics application, Falkonry Insight, which can ingest and process large volumes of time series data to reveal both process and machine anomalies. According to Falkonry, the application allows operational users to review patterns that deviate from expected behaviour, compare signals, diagnose issues and generate reports. By utilizing patented AI technology that can process all available data, Insight is able to automatically surface related behaviour that could potentially lead to production problems.
The underlying approach of Insight is founded on encodings using an autoencoder that represents time series data based on a novel deep learning architecture, and a fully unsupervised approach to detect an anomaly. The application securely connects to existing automation control systems or data acquisition systems, such as iba, and ingests the time series data into the Falkonry AI platform. Within a few days, the self-supervised
learning starts surfacing the discovered anomalies automatically, which are then scored based on their severity and flagged for review. The maintenance and automation users then review these anomalies and diagnose the root causes, getting a view of the anomaly state across a process or a sub-process, and resultantly can compare the signal behaviours over different time periods to have a quantitative understanding.
Falkonry will be exhibiting at booth #2452
With the global steel industry looking to move toward direct reduced iron (DRI)-based production to reduce emissions, the Middle East and North Africa (MENA) region has the opportunity to capitalize on the switch.
THE global steel industry is eyeing a switch to direct reduced iron (DRI) using green hydrogen to reduce emissions.
Unlike the blast furnace-basic oxygen furnace (BF-BOF) process that uses coal to make iron, the direct reduced iron-electric arc furnace (DRI-EAF) route predominantly uses natural gas, which produces lower carbon emissions.
The Middle East and North Africa (MENA) region is potentially in a good position to begin producing carbon-neutral or green steel, as it has particular advantages over other areas in the world.
Its steel sector is already dominated by DRI with an established supply of DR-grade iron ore. Technical barriers may make it difficult to ramp up DR-grade iron ore production to supply other regions.
MENA’s transition to H2DRI-EAF could commence immediately due to the region having more DRI plants than anywhere else globally.
MENA has excellent solar resources to aid in the production of green hydrogen via renewable electricity. Access to such rich solar energy resources will allow for production of green hydrogen at a competitive price. If it acts fast, MENA has the potential to lead the world in green steel production.
In 2021, MENA accounted for nearly half of the world’s DRI production. The region produced only 3% of global crude steel output, of which about 95% was based on EAF production, predominantly from DRI-
EAF1. This is explained by the abundance of natural gas in the region as well as the lack of high-quality coking coal reserves.
Fig 1 illustrates DRI production around the world. With more than 55Mt, MENA was highest followed by Asia and Oceania
World Steel Association and Midrex*
Note: At the time of writing, 2021 crude steel production figures for Bahrain, Libya and Qatar were not published and 2020 figures were applied. Table excludes countries in the region that produce steel from scrap-EAF: Morocco, Tunisia, Kuwait, Jordan and Israel.
(including India) with about 39Mt2. India is the world’s largest producer of DRI utilising gasified thermal coal, a more carbonintensive process compared to gas-based technology3. Mexico, Russia and the US are other significant producers.
Iran, Saudi Arabia and Egypt are the leading steel players in the MENA region, producing more than 80% of the region
total. Table 1 shows MENA’s production of crude steel and DRI in 2021.
In 2021, the Middle East produced more than 45Mt of crude steel, with 94% produced from the EAF route and the rest from the BF-BOF route. Iran is the only country in the area that used BF-BOF with just 2.8Mt produced via this technology in 20214. For North Africa, the proportions are almost similar.
The International Energy Agency (IEA) modelled in its 2021 Net Zero Emissions scenario that H2DRI-EAF’s share of global primary steel production would reach 29% by 20505. Under its own net zero by 2050 scenario, BloombergNEF models suggest
that 56% of primary steel production would come from H2DRI-EAF by 2050, equivalent to 840Mt/yr6
The current global share of the DRI-EAF route is less than 5%, yet the future appears bright for this technology and MENA is likely to be one of the leading players due to the region’s competitive advantages.
In 2020, steelmaking capacity in the Middle East increased by 7.2Mt. It will rise further in the coming decades mainly due to the expansion of Iran’s steel sector.
MENA’s steel industry is relatively low carbon compared to the rest of the world, where steel production is dominated by blast furnaces using coal, both as a source
of energy and iron ore reduction. According to the IEA, direct and indirect carbon emissions of BF-BOF is 2.2 tonnes per tonne (t/t) of crude steel while the DRI-EAF emits 1.4 t/t7
As the cost of renewable energy has fallen dramatically in the past 10 years, solar photovoltaic (PV) and onshore wind could now compete with fossil-based electricity (generated from coal or natural gas) in most regions8
As with the region’s steel industry, electricity production in MENA predominantly relies on gas-fired power plants. MENA’s share of renewable energy is currently much lower than the global average, although the region has high potential for solar energy9
In fact, MENA has the highest PV power potential globally10, according to the World Bank (Fig 2).
Renewable investment has been gaining momentum in MENA predominantly due to the dramatic reduction in the cost of solar PV projects. The global levelized cost
of solar electricity (or LCOE) has fallen from $0.381/kWh in 2010 to $0.057 in 2020 – that is, an 85% reduction in 10 years. In 2020, the bids for solar PV recorded some new low prices in the Middle East from $0.0157/kWh in Qatar to $0.0135 in the United Arab Emirates (UAE) and even $0.0104 in Saudi Arabia. The International Renewable Energy Agency (IRENA) assessed that producing solar PV electricity in the Middle East at $0.01/kWh is possible11
Major projects are under construction in Saudi Arabia, Morocco, UAE, Israel and Egypt. The IEA estimates that MENA’s renewable energy capacity growth will double over the 2021–2026 period compared to the previous five years and reach 32GW, up from 15GW12
New renewable capacities will change the power mix in MENA by 2050. IHS Markit forecasts that 83GW of wind and 334GW of solar capacities will be added by 2050, which will increase the respective shares of wind and solar from 1% and 2% to 9% and 24%13
Green hydrogen is produced from water electrolysis, by splitting the bond between
hydrogen and oxygen in water molecules. Producing green hydrogen requires the use of renewable electricity and it has yet to reach global price competitiveness.
With the global energy transition accelerating, green hydrogen has become one of the most important investment options in the energy sector. The IEA predicts that by 2030, the installed global capacity of electrolysers will reach 54GW and the Middle East with 3GW will sit below Europe, Australia and Latin America14
Having access to cheap solar energy is a regional competitive advantage for MENA countries in the future hydrogen economy. Scaling up solar power capacities to produce green hydrogen is a big challenge although the MENA region has two main advantages: land availability and solar radiation.
Table 2 illustrates the difference between a European and North African country in terms of needed capacities and cost of production to change technology in a steel plant with an annual capacity of 4Mt from BF-BOF to H2DRI-EAF using green hydrogen. Based on calculations by Hydrogen Europe, Tunisia requires 31% lower PV solar capacity and consequently lower electrolyser capacity15
The cost of hydrogen production via electrolysis is currently lower than blue hydrogen in Middle Eastern countries. In July 2022, the cost of alkaline electrolysis in Qatar was $2.59/kg, Saudi Arabia $3.20, Oman $3.55 and UAE $5.14.
The cost of polymer electrolyte membrane (PEM) electrolysis is generally around $1/kg higher than alkaline technology. The price of blue hydrogen, produced by the combination of steam methane reforming (SMR) and carbon capture and storage (CCS), is about $7/kg in the Middle East16
The IEA foresees the Middle East as an area with scope for the lowest cost of green hydrogen production.
The IEA reported that by 2030 the cost of hydrogen production in the Middle East powered by solar PV could be less than $1.5/kg based on capital expenditure of $320/kW and electricity at $17/MWh. By 2050, the hydrogen price could fall further to $1/kg as capex and electricity costs decrease to $250/kW and $12/MWh17
BloombergNEF suggests that with delivered green hydrogen priced below $1.5/kg, H2DRI-EAF technology could be
cost competitive by 205018
As MENA could produce hydrogen domestically, the cost of transportation to steel producers could be lower than other areas. Based on the hydrogen carrier and the distance, the transportation price varies. MENA has good infrastructure and pipelines that could facilitate cheaper transportation domestically.
DR-grade pellet supply
DRI-EAF technology currently needs a different feedstock to meet rigid specifications for quality and physical properties. The DR-grade pellet must contain at least 67% of iron, requiring further processing of iron ore. Some steelmakers are investigating new technology combinations that could allow use of lower-grade iron ore in DRI process19
MENA’s steel and mining sector has already invested in the upstream value chain and can supply the high-quality pellets to feed steel companies.
Headwinds
In addition to the technical barriers of using hydrogen for DRI production on a commercial scale, other headwinds include the supply of DR-grade pellet for further expansion projects, scaling up the renewables and green hydrogen value chain and the fact that MENA is a water-stressed region.
Although MENA has access to DR-grade pellet for the current capacity of DR plants, any further development and capacity increase must be planned simultaneously with the aim of balancing the whole value chain based on H2DRI-EAF.
The solar PV and electrolysers also occupy hectares of land. A 1GW PV installation covers more than 6,000–8,000 acres20, a matter of lesser importance in the MENA area given the expanse of uninhabited lands with ample sunlight to allocate to this
purpose. Twelve out of 17 countries with extremely high baseline water stress are in the MENA21region. Locating in such an arid areas is a challenge for any industry.
To produce 1kg of green hydrogen via solar PV and wind requires on average about 32kg and 22kg of water, respectively. Despite hydrogen’s small global share in total water demand, it could be difficult to supply water as a feedstock reliably in MENA due to scarcity.
The IEA suggests that added energy input
breakthrough, though MENA could be a global leader of steel decarbonization if the region shifts promptly towards green hydrogen and renewables.
There is no single solution for rapid steel decarbonization. Tailored solutions are required for each country’s capabilities and competitive economic advantage.
As well as producing green hydrogen for export, the MENA region could also use more domestically to produce low-carbon steel for export.
Providing green electricity, a big challenge for steel producers in some parts of the world, is less of a barrier in MENA.
With ample renewable energy potential, MENA could become a leader in hardto-abate and carbon-intensive industries, specifically steel.
Compared to other regions, MENA has in situ capacity of DRI-EAF, which means no extra investment is needed to replace the base technology.
All new investment could be focused on producing green hydrogen and expanding renewables.
MENA could possibly replace 30% of its natural gas with hydrogen in the existing fleet of DR plants without major modification of the equipment, then move towards 100% green hydrogen in a second phase.
via desalination could increase the total cost of hydrogen production by only $0.01–0.02/kg. As such, water is not included as a main cost driver22. In another study, IRENA found using desalination plants in water-scarce regions will increase the cost of hydrogen production by $0.05/kg, which is negligible23
Developed nations including Australia, Germany, the US and China have been the first movers in the green hydrogen
1. World Steel Association. 2022 World Steel in Figures. 2022. 2.
to
14 February 2022.
Many mining companies face the challenges of iron ore quality and the production of DR-grade pellets. The former is not an issue in MENA, though finding reliable resources for future expansion could be a challenge for steel producers in this region.
MENA’s knowledge of this specific steel technology is an invaluable asset. Among the most important steel decarbonization pillars, this production knowledge, coupled with further work on iron ore beneficiation, pelletising and DR plants, will greatly assist MENA’s green transition. �
2022. 3.
6. BloombergNEF. Decarbonising Steel. A Net-Zero Pathway. 1 December 2021. 7. IEA. Iron and Steel Technology Roadmap. October 2020. 8. IRENA. Renewable Power Generation Costs in 2020. June 2021. 9. World Bank. Global Solar Atlas. Solargis. 2022. 10. World Bank. Global Photovoltaic Power Potential by Country. June 2020. 11. IRENA. Renewable Power Generation Costs in 2020. June 2021. 12. IEA. Renewables 2021. December 2021.
13. IHS Markit. Middle East and North Africa Power and Renewables Market Briefing. April 2022. 14. IEA. Global Hydrogen Review 2021. October 2021, p. 117. 15. Ibid. 16. S&PGlobal. Platts hydrogen price wall. July 2022. 17. IEA. Global Hydrogen Review 2021. October 2021. 18. BloombergNEF. Decarbonising Steel Technologies and Costs. 25 August 2021. 19. IEEFA. Solving iron ore quality issues for low-carbon steel. 9 August 2022. 20. Green Coast. Solar Farm Land Requirements: Top 7 Tips for Farmers, Ranchers, and Landowners. 5 December 2021. 21. World Resource Institute. 17 Countries, Home to One-Quarter of the World’s Population, Face Extremely High Water Stress. 6 August 2019. 22. IEA. Global Hydrogen review 2021. October 2021. 23. IRENA. Global Hydrogen Trade to Meet the 1.5°C Climate Goal: Green Hydrogen Cost and Potential. May 2022.
Midrex. 2021 World Direct Reduction Statistics.
IEEFA. India’s technology path key
global steel decarbonisation.
4. World Steel Association. 2022 World Steel in Figures. 2022. 5. IEA. Net Zero by 2050 Scenario. May 2021.
Scarabaeus pelletizing discs provided by HAVER & BOECKER NIAGARA are used for sustainable and efficient production of iron ore pellets. The unit’s design minimizes circulation, increasing productivity and profitability. The pelletizing discs used for agglomerating iron ore concentrates into pellets are remarkable for their very narrow particle size distribution with a target size of 10 to 14 mm, important for DR-Processes.
The Scarabaeus process creates higher quality pellets, which can be sold at better prices due to significantly tighter particle size distribution spread and a higher iron ore content.
The Scarabaeus process generates higher tonnages by minimizing the material return rates and avoids double processing of over or undersized pellets due to automatic machine parameter adjustments, which can also adapt to varying material property fluctuations in the feed material.
The Scarabaeus process creates pellets so high in quality that they can be utilized for the direct reduction process. This in return can create e normous CO2 emission savings, thus minimizing the mine’s impact on the environment.
This article covers the work being done at LIBERTY Steel to transform assets, as well as crucial policy requirements for the steel industry in Europe to remain competitive while continuing to lead on decarbonization.
THE advent of the Inflation Reduction Act (IRA) in the United States has kicked off what some market commentators have termed a ‘Subsidy Arms Race’ with the EU Green Deal Industrial Plan announced in February this year. The Industrial Plan has seen mixed responses, with EU member states questioning the feasibility of incentives funded in very different fiscal contexts, the relaxation of state aid regulations, and businesses highlighting its complexity and lack of focus.
Policy is a hugely important lever for decarbonization; implementing supportive policies and incentives, alongside tax and protection mechanisms is key to delivering decarbonization goals and respective technology. Without this, we are unlikely to unlock the pools of capital needed to fund the long-term transition to lower carbon production in industry.
The EU steel industry context
It’s a complex story: the aftermath of
COVID, the disruption from the war in Ukraine and fears over energy security are underpinning worldwide trends towards economic nationalism. The European steel industry is having to react to these significant short-term market changes, while at the same time progressing its
decarbonization plans.
LIBERTY has significant investment planned in Europe to meet our ambition to be carbon neutral by 2030, reflecting the global imperative to halve emissions this decade and reach net zero emissions by 2050. We believe decarbonization is the route to creating a more sustainable and economically resilient industry while supporting the EU’s Green Deal goals. Goals that are not just important in Europe, but that carry weight and significance in the global efforts to decarbonize.
Europe is a huge market and will continue to be an attractive destination for investors provided it remains competitive as a low carbon advanced manufacturing economy. Europe already benefits from a high skills base and supportive conditions for technology development and decarbonization. But we’re in a global race and other countries are catching up and, in some cases, overtaking, as demonstrated in the USA with its IRA.
Bit by bit, we’re seeing decarbonization moving from a moral principle to having a pragmatic competitive edge, and in some cases even business as usual.
The challenge, as many readers will recognise, is decarbonizing an energyintensive industry and doing so while remaining internationally competitive.
Currently, both primary production of steel from iron, and secondary production in an electric arc furnace, rely on huge amounts of fossil fuels – and, therefore, carbon emissions – to produce steel.
The good news is that technology is advancing solutions to decarbonize. But, support is required to further develop and scale these solutions in order to be competitive and rapidly replace legacy processes.
The main available and proven technology route is to maximise Electric Arc Furnace (EAF) production, as these furnaces emit a fraction of the direct emissions compared with the blast furnace route.
Modern so-called ‘hybrid-EAFs’ can run on renewable energy which nearly eliminates scope 1 & 2 emissions from the process. Hybrid EAFs also have the advantage of being able to process a range of materials – hot metal, DRI and scrap – making them a very flexible technology and ideal for transitioning away from blast furnaces.
This transformation is underway across all three of our major steel making sites in the EU; at Czestochowa in Poland, at Ostrava in the Czech Republic, and at Galati in
Romania. Each site has a role to play in our carbon reduction plan that will drastically reduce the 5Mt of carbon they currently emit annually.
In Galati and Ostrava, we’re dedicating up to €2 billion in green steel transformation investment to reduce carbon emissions by up to 90%. Last year in Ostrava, with our technical partner Danieli, we announced the first project in Europe that will entirely replace its blast furnaces with hybrid EAFs, which will reduce carbon emissions by 80% by 2027.
In Galati we are making similar investments in electric melting furnaces and solar energy, while in Czestochowa we’re focused on installing 3 MW of renewable energy capacity to further decarbonize its existing EAF operations.
The second decarbonization route we’re focused on is removing coking coal from primary steel production. It works by replacing coal first with natural gas as the reducing agent for iron ore and eventually with green hydrogen produced by renewable power.
Using natural gas through Direct Reduced Iron (DRI) furnaces can reduce carbon emissions from primary steel production by half and using green hydrogen will get us down to low-digit carbon emissions.
Today, this route is only truly viable in certain locations across the world where conditions are just right.
Our plant in Whyalla in South Australia is perhaps the best example globally. There we have vast high quality magnetite reserves, fantastic solar and wind resources, a deep-water port, a well-connected rail
network, and a super-skilled workforce.
This rich mix in Whyalla makes it among the best locations in the world to decarbonize primary steel making, and is made even more appealing by the South Australian government’s commitment to invest AUD$593m in a hydrogen power plant in Whyalla to support the industrial production of the green hydrogen required.
In either technology route, the key to speeding up the transition to green steel is contingent on access to large-scale competitive clean power, access to critical raw materials such as steel scrap and iron ore, investment incentives and protection from unfair competition from markets that do not produce to the same standards as Europe.
There are specific key enabling factors that are vital to the transition to clean steel production.
First, the EU needs effective long-term industrial and trade policies. Policies that support European industry overall, protect its steel industry against imports of cheap, carbon-intensive steel from third countries, and help the industry to invest in innovation and decarbonization. What’s required here is for the EU to mobilise incentive mechanisms that are tailored to high impact sectors like steel.
Second, ensure the Carbon Border Adjustment Mechanism is effective. We have already seen outstanding work done in reaching an agreement on the CBAM and ETS. The next step is a concrete and effective solution for exports and ensuring
that plants emitting less carbon – such as those using hybrid EAFs – are appropriately recognised.
Third, tackle the energy crisis. The EU needs to ensure the supply of abundant, secure and affordable low-carbon energy as a transition to EAF production will require a four-fold increase in the industry’s electricity usage.
The outcome of the review of the Electricity Market Design will be key for the steel industry and we are hopeful that the commission will adopt measures that support and prioritise energy-intensive industries.
Fourth – and particularly important for the long-term – support the industrial deployment of hydrogen. The upcoming revised European legislation on hydrogen and gas decarbonization is a strategic tool that can clearly prioritise the use and supply of hydrogen to those sectors, such as steel, where its use can deliver huge carbon emissions reductions, as Whyalla will show.
Fifth, start treating steel scrap as a critical raw material. Europe currently exports more than 20Mt/yr of scrap, much of it to third countries who use it to produce steel to import back into Europe. However, as steel manufacturers switch to EAF technology, our demand for this material is likely to more than triple. The upcoming EU Waste Shipment Regulation trialogue will be instrumental in making sure that shipment
outside the EU is subject to stronger monitoring systems and anti-circumvention measures. Scrap is a critical raw material and as such it should be included in the Critical Raw Materials Act.
Sixth – and finally – human capital is vital. If we are to successfully transition to sustainable production, this relies on the industry finding and attracting good, qualified people to help transform the steel industry. As an industry, we should rise to the challenge of revitalising the image of the sector as a force for good and a place where young steelmakers can make a difference. EU stakeholders will need to collaborate to ensure that the right training and academic opportunities are put in place to ensure the EU has the right talent and avoid ‘expertise leakage’.
To advance this aim, last year we launched the GREENSTEEL Academy and the GFG Foundation in Czechia and Romania to help upskill our current employees and build interest in the sector among younger generations.
The transition to sustainable industry in Europe (and elsewhere) will have to be a team effort where manufacturers, investors, customers and governments come together to transform processes, share knowledge and protect our strategic and business futures. We will continue to be at the heart of that debate as we continue to transform our businesses for that low carbon future. �
In the past decade or so, ‘sustainability’ has become one of those buzz words used often by business people throughout the world, including leaders within the steel industry. But one of the key things to consider when discussing ‘sustainability’ in the steel industry is what does that word mean exactly?
By Richard McDonough*TO different entities, ‘sustainability’ means different things: a focus on the raw ingredients used to produce steel in some cases. In others, the focus is on the longterm viability of a business or the industry overall in terms of investments to assure job opportunities in the future. For others, it refers to the input supplies utilised in the steel making process. Still others focus on the emissions produced and the utilisation of products left over from manufacturing steel.
“We look at sustainability broadly,” stated Kevin Dempsey, president and chief executive officer of the American Iron and Steel Institute (AISI). “Most of our focus is on the environment – carbon emissions and water usage, for example. Other pillars include social aspects, economic aspects, and job creation. All are important.”
Members of the AISI include firms that have steel production facilities in the United States (US). The organisation describes its mission as one “…to influence public policy, educate and shape public opinion in support of a strong, sustainable American steel industry committed to manufacturing products that meet society’s needs.”
“We’re working towards net zero or near zero carbon emissions,” said Mr. Dempsey. He indicated that there are several processes and techniques being utilised today in the American steel industry that provide a strong foundation for long-term
sustainability.
Among those processes and techniques he cited are the high percentage of steel produced by electric arc furnaces (EAFs), the high level of recycling scrap steel products, the increased use of natural gas in place of coal, and the increased use of renewable energy sources – wind and solar, in particular – in steel production in the US.
Together, Mr. Dempsey explained, these efforts have helped to lower carbon emissions emitted per tonne of steel produced in the US today; these processes and techniques are also anticipated to be part of the plans for the continued decline in carbon emissions per tonne of steel produced in the future.
“Electric arc furnaces produce less than half of a tonne of carbon per tonne of steel produced,” he explained. “As compared to most of the rest of the world, American steel producers have a higher share of production through the use of electric arc furnaces.”
The circular economy is one of the critical
aspects helping steel manufacturers reduce carbon emissions for each tonne of steel produced. Several sources confirm that steel is the number one recycled product in the US.
“Our members are pushing on all fronts with investments to recycle scrap steel as well as to create new steel,” Mr. Dempsey said. He noted that marketplace competition among a number of businesses had helped to lead to innovations in steel recycling: “Each firm is competing with each other to better separate components in the recycling processes.”
To reduce carbon emissions even further, Mr. Dempsey indicated that improvements in the supply chain and the use of alternative fuels – alternatives to coal – will continue to help reduce carbon emissions by steel producers and enhance the sustainability of the industry.
“The steel industry in the US is shifting away from the use of coal,” he stated.
Mr. Dempsey said that one alternative to coal is iron pellets.
“With iron pellets, steel producers use natural gas as fuel rather than coal,” Mr. Dempsey said. “Down the road in the future, hydrogen will be an option for steel producers.”
He noted that several steel manufacturers – as well as businesses and organisations in other industries – are in discussions with the US Department of Energy on ways to utilise hydrogen energy for operations.
In addition, Mr. Dempsey stated that
in the US involve a range of locales and industries – not just steel manufacturers and the communities where they are located. Several large-scale carbon capture and storage facilities are being planned and constructed in the Midwest and Northern Plains of the US. Among those industries initially being targeted to utilise carbon capture and storage facilities are businesses active in agricultural pursuits.
sustainability in a context of businesses investing in their operations so that there is a future for skilled workers.
“The USW views capital expenditures that go beyond routine maintenance and repair at represented facilities as investments in the sustainability of our plants,” according to a statement from a spokesperson for the USW. “Sustainable employers also invest in training workers and modernizing plants, showing a long-term commitment to our communities. We often bargain capital expenditures and investment commitments into our contracts because it directly impacts the long-term security and sustainability of our jobs.”
The USW describes itself as “…North America’s largest industrial union. We’re 1.2 million members and retirees strong in the United States, Canada and the Caribbean. We proudly represent men and women who work in nearly every industry there is.”
Big River Steel – United States Steel Corporation
United States Steel Corporation (US Steel) is one of the major steel producers with facilities throughout the US and beyond.
steel companies are also looking at carbon capture and storage options. These options use a process where carbon emissions are collected and transported typically by pipelines for eventual deposit in deep recesses of the Earth.
Carbon capture and storage options
Labour unions in the US have encouraged sustainability programmes in the steel industry and within other heavy industries.
The United Steelworkers (USW), the major American union with members working in the US steel industry, views
The company noted that today, one of its operations, Big River Steel, “…has annual raw steel capacity of approximately 3.3Mt with an electric arc furnace (EAF), ladle metallurgy furnace (LMF), Ruhrstahl Heraeus (RH) degasser, and thin slab caster/ hot rolling mill. Finishing facilities include a pickle line/tandem cold mill, batch annealing furnaces, a skin pass/temper mill, and continuous galvanizing line. Principal
products include hot-rolled, cold-rolled, coated, and electrical sheets.”
US Steel is in the process of a major expansion of its operations at Big River Steel in Osceola, Arkansas. This community is in the central part of the nation. Transportation is available at this site through rail service, nearby interstate highways, and the Mississippi River.
According to a recent statement from US Steel, “The steel produced at Big River Steel provides our customers in the appliance and automotive sectors with some of the most sustainably produced steel in North America, and this capacity will increase when the expansion of Big River Steel is complete. US Steel’s accomplishments at Big River Steel mark a step toward achieving our 2050 net-zero greenhouse gas (GHG) emissions goal (Scope 1 and Scope 2 emissions).”
Scope 1 emissions, noted US Steel, “…are primarily derived from the manufacturing of our products at all of our facilities, [while] Scope 2 emissions are primarily derived from purchased electricity for our sites.”
“US Steel is working to mitigate supply chain challenges by becoming increasingly self-sufficient,” the recent statement from US Steel continued. “We have invested
construction on the NGO [Non-grain Oriented] line at Big River Steel is progressing as planned with completion expected later this year. This project supports several aspects of US Steel’s Best for All strategy, which is focused on delivering profitable, sustainable steel solutions that are best for people and planet.”
In its 2022 Sustainability Report, Commercial Metals Company (CMC) stated that it had kept more than 19 billion pounds of recycled metal from landfills; had a rate of 88.4% water recycling and reuse rate; had a 7.4% increase in waste recycled since 2021; and had a 127% increase in electricity secured from renewable sources since 2019.
CMC describes itself as a manufacturer, recycler, and fabricator of steel and metal products and provides related materials and services through a network of multiple facilities, including electric arc furnace mini mills, among other facilities in the United States. The company also has operating facilities in Poland.
According to its sustainability report, “every tonne of CMC steel avoids the
from filtered air off our furnaces, [was sent] to recyclers who extract zinc and other valuable metals for use in the production of paints, tyre rubber, fertilisers, animal feed, and more.”
One of the sustainability efforts cited by Mr. Dempsey of the AISI is found at the Cleveland-Cliffs HBI Plant in Toledo, Ohio. According to a statement from this company, “Cleveland-Cliffs’ Toledo Direct Reduction plant, completed in 2020, is the first and the only producer of HBI in the Great Lakes region. This natural-gas-based plant supplies high-quality hot-briquetted iron (HBI), a low-carbon iron feedstock used in our blast furnaces, BOFs [Basic Oxygen Furnaces] and EAFs.”
“Producing and using HBI contributes to the company’s greenhouse gas reduction initiative,” the statement continued.
“Given the facility’s low-cost production, the industry focus on decarbonisation, the increasing scarcity of domestic prime scrap, and the growing EAF capacity in the US, the Toledo direct reduction plant is expected to generate significant value for the company going forward.”
On 15 September 2022, Cleveland-Cliffs
millions of dollars in a new pig iron production facility located at our Gary Works plant in Gary, Indiana. The pig iron produced at Gary Works will provide an essential fuel for our growing fleet of electric arc furnaces at Big River Steel.”
The company explained that the “…
mining and usage of 2,500 pounds of iron ore, 1,400 pounds of coal, and 120 pounds of limestone. Using our co-products from steelmaking, 100% of slag [is] re-used and 99% of baghouse dust [is] recycled.”
As an example, the company explained that the “...EAF baghouse dust, collected
Leaders of the Administration of US President Joseph Biden visited the direct reduction plant of Cleveland-Cliffs in Toledo. From left are:
Robin Carnahan, administrator of the US General Services Administration (GSA);
Pete Buttigieg, US Secretary of Transportation (DOT); and Ali Zaidi, assistant to the President of the US and national climate advisor.
(Image courtesy of the US Department of Transportation through a video on Twitter, 15 September 2022.)
and the United Steelworkers worked together to welcome leaders from the Federal government to the Toledo Direct Reduction Plant. Among those attending were Pete Buttigieg, US Secretary of Transportation (DOT); Robin Carnahan, administrator of the US General Services Administration (GSA); and Ali Zaidi, assistant to the President of the US and national climate advisor. According to Ms. Carnahan, the GSA is the largest landlord in the US and has 230,000 motor vehicles in its fleet for use by Federal employees.
“Secretary Buttigieg recognised Cleveland-Cliffs’ leadership in the steel industry for its transformative investments in carbon-efficient steelmaking,” noted the firm in a news statement issued on the day of the visit. “The company is using the hot-briquetted iron produced in Toledo across all of its integrated blast furnace/basic oxygen furnace steel mills and electric arc furnace steel mills to significantly reduce GHG emissions.”
“At the Cleveland-Cliffs steel facility in Toledo, we’re seeing what creating jobs in the fight against climate change looks like,” said Secretary Buttigieg during his visit to Ohio. “The Administration’s Federal Buy Clean Initiative is a clear win for all of us: good for union jobs, good for the environment, and good for taxpayers.”
In a video posted to Twitter, the three officials of the Federal government spoke about how sustainability efforts in the steel industry are helping the nation and the world in striving for long-term growth that takes into account ways to reduce carbon emissions.
Here is part of their discussion: Secretary Buttigieg: “Hey, Secretary Pete here. We are in East Toledo, Ohio. I’m with White House Climate Advisor Ali Zaidi and GSA Administrator Robin Carnahan. So exciting to see how new industrial processes are creating great jobs and helping with America’s fight against climate change.”
Ms. Carnahan: “You know, at GSA, we manage a lot of buildings and a lot of cars, and it turns out that supply chain emissions are more than twice what we get from buildings and cars. So, if we can start here at the beginning of the supply chain and make cleaner steel, concrete, asphalt, glass, we can have a huge [impact]...”
Mr. Zaidi: “For the longest time, we’ve talked about the industrial sector as hard
to decarbonise. What the steel workers here in Ohio are proving is we do hard things here in America. And when we build those wind turbines, one megawatt requiring 500 tonnes of steel, not only are those wind turbines going to produce clean electricity, they’re going to use clean steel made in America.”
Secretary Buttigieg: “So exciting to see what creating jobs in the fight against climate change looks like on the ground. Great to see it here in the Midwest, and there…[are] great things like this happening across the country right now.”
Ms. Carnahan: “And let me just say, I think it’s a triple win. It’s good for jobs, union jobs, it’s good for the environment, the future of our kids, and it’s great for taxpayers.”
Secretary Buttigieg: “Absolutely.”
Other steel producers active in sustainability efforts in the US include Nucor Corporation, SSAB Americas, and Steel Dynamics, among others. Highbar LLC is a new company planning major steel operations that are designed to be sustainable in a number of ways. The Ferrum Chronicles will detail the efforts by Highbar in an upcoming edition of Steel Times International. �
NORTH American steelmakers appear to be going full steam ahead with their plans to add a massive amount of new electric arc furnace (EAF)-based production capacity over the next several years despite growing concerns about the potential for an economic downturn. In fact, industry observers are not ruling out the possibility that the mills could announce yet more flat roll and long product investments in the coming months.
“What we are seeing is the modernization, decarbonization and electrification of the domestic steel industry,” Philip Bell, president of the Steel Manufacturers Association (SMA), said, with mills being committed to investing in good times and bad in order to meet their customers’ expectations, expand their product offerings and help decarbonize the American steel industry. He noted that already a variety of EAF steelmaking projects existed – both greenfield mills and expansions of existing production capacity – and that between now and 2025 it is expected that another 20 million short tons (Mst) of annual production capacity coming
from a variety of product lines, including sheet, rebar and other bar products and plate, are expected to come online.
Josh Spoores, a principal steel analyst for CRU, noted that the initial investment push came in 2018-19 when North American steelmakers announced plans to add about 7.2Mt of sheet capacity and 1.1Mt of plate capacity. He observed that due to some well-known, well documented delays, much of the sheet mill capacity, which was initially expected to come online and ramp up in 2021, is still in the process of ramping up.
But on the other hand, a new greenfield Brandenburg, Ky., plate mill is on its expected timeline. In fact, Al Behr, Nucor’s executive vice president of plate and structural products, stated during the steelmaker’s fourth quarter earning conference call that the mill has started shipping product to customers and is now going through its final commissioning stage. It is expected to ramp up its largely discrete plate production throughout this year, going from 10-20kt in the first quarter, to 100kt in the second quarter, and about 200kt in the third and fourth
quarters of this year.
Additionally, Kevin Dempsey, president and chief executive officer of the American Iron and Steel Institute (AISI), noted that American steelmakers have announced plans to build an additional 7.6Mt of steelmaking capacity over the next two to five years. He said that these investments –including projects that are either currently under construction or will be in the near future – will have a very favourable impact, noting, “They will not only create new jobs, but they will help American steelmakers to take share back from foreign producers –many of whom are government owned or subsidized.’’
All that capacity, as well as other US steelmaking capacity that is either currently under construction or that has been announced, is EAF based, which Alexander Kershaw, a senior steel analyst with Fastmarkets, said isn’t surprising. In fact, he said that due to environmental concerns, he doesn’t believe that any additional blast furnaces will ever be built in the US or Canada, and that, instead, additional blast furnaces could be closed down.
Blast furnaces could also be repurposed to produce pig iron to adapt to market influences, Philip Gibbs, a senior metals equity analyst for KeyBanc Capital Markets, said. “That is why US Steel recently added a 500kt pig iron module at its Gary Works in Indiana,” enabling it to sell some of the pig iron it produces there to other mills, either domestically or abroad, he explained, similar to what Stelco did in Canada in 2021 and is reportedly considering doing in Missouri. CRU’s Spoores pointed out that US Steel has also recently inked an agreement with SunCoke Energy, which will supply the steelmaker’s Big River Steel with pig iron from blast furnaces it purchased in Granite City, Ill.
This fits with US Steel’s other moves to transform its business model. During its fourth quarter earnings conference call in February, David Burritt, the steelmaker’s president and chief executive officer, stated that the path for the company’s Best for All strategy, which is focused on value creation, ESG transformation and disruptive innovation through its transition to mini-mill steelmaking and a differentiated metallic strategy, is becoming a reality. That, he said, serves as a catalyst to generate increased and resilient free cash flow and best-in-class finishing capabilities that are crucial to sustainable steel solutions. He said one example of this is its second 3Mt/yr Big River Steel mill, which will include two EAFs, an endless casting and rolling line and advanced finishing capacity. Burritt said that mill, which broke ground in February 2022 and is expected to come online in 2024, will enable US Steel to
produce advanced steel grades with up to 80% fewer greenhouse gas emissions.
Spoores noted that among the new US steelmaking capacity that is already online is Steel Dynamics’ 3Mt/yr greenfield flatrolled steel mill in Sinton, Texas; a 1.5Mt/ yr expansion at Nucor’s Gallatin mill in Ghent, Ky.; and North Star Bluescope’s 950kt expansion of its Delta, Ohio, mill. Earlier this year, Steel Dynamics estimated that its Sinton plant, after a trying startup in 2022, would achieve about 80% capacity utilization this year with two additional coating lines expected to be ramped up during the third quarter. Mark Millet, the steelmaker’s president and chief executive officer, said that Sinton’s hot strip mill design, including its thermal mechanical rolling capabilities, allows the mill to produce higher strength steel grades with lower alloy content, therefore at a lower associated alloy cost. Also, while occurring about six months later than expected, Nucor’s president and chief executive officer, Leon Topalian, said that Nucor expects to fully ramp up its Gallatin expansion in the second quarter of this year.
Meanwhile, Spoores pointed out that there is currently about 2.9Mt of long product production capacity and about 6.9Mt of sheet steel capacity currently under construction. For example, when it comes to long products, Gibbs noted that Commercial Metals’ second 500kt Mesa, Arizona, rebar and merchant bar micro-mill, which it dubs AZ2, is expected to come online this spring. Barbara Smith, its president and chief executive officer,
said during the company’s earnings call that CMC is also planning to build another 500kt rebar mill in Berkeley County, West Virginia. In addition, Nucor is constructing a new 430kt rebar micro-mill and adding a new melt shop at its Kingman, Arizona., bar mill. Also, SMA’s Bell pointed out that Highbar LLC, is not only building a 600kt rebar micro-mill in Osceola, Arkansas, but that it will be building another – possibly two more -- micro-mills as well, and that Pacific Steel Group plans to build a 380kt rebar micro-mill in California that is expected to come online in 2025.
Nucor is also building a 3Mt greenfield sheet mill in Mason County, West Virginia., which Topalian said will expand the company’s ability to provide its customers with cleaner, higher quality steel products for demanding automotive and construction applications when it comes online in two or three years. ArcelorMittal and Nippon Steel are putting in a 1.5Mt EAF at their AM/NS Calvert joint venture mill later this year, although Spoores said it really won’t add new steelmaking capacity, but rather will allow the mill to produce its own slabs rather than importing them.
Actually, SMA’s Bell said that these investments shouldn’t just be seen as moves to add capacity, but rather an algebraic equation with some capacity
Only available with our previously introduced TapHole Manipulator (THM) for Clearing and Cleaning
being added, and other capacity coming offline simultaneously, particularly blast furnace capacity, with companies evaluating their portfolios and determining what they are going to use their furnaces for. It is also expected that this new capacity will be displacing some imports, although he said the amount of such displacement will remain very speculative until the new production capacity actually comes online.
“We haven’t seen much displacement of imports quite yet,” Spoores said, noting while steel imports are down, that is more a function of market requirements than additional domestic production. “But once the new EAFs really start ramping up we could see some of that displacement.”
Another question is what impacts new capacity will have upon raw material availability. That, Fastmarkets’ Kershaw said, is one reason why he is bullish about US scrap prices. “The new mills will particularly need more prime scrap, and already there hasn’t been enough prime scrap – and to a lesser extend shredded scrap, to meet current demand,” he said, adding that given that you can’t increase the supply of
prime scrap very easily or quickly the mills will have to adjust the use of other raw materials.
There are, however, varying views about how tight steelmaking raw materials are and will be once this new capacity comes online. For example, Steel Dynamics’ Millett called such ‘angst’ unwarranted, noting that the US remains a net exporter of scrap, exporting 15-22Mt/yr. AISI’s Dempsey said that to meet the demand of a changing market and the nation’s changing needs, American steelmakers have also made investments to increase their use of direct reduced iron (DRI) and hot briquetted iron (HBI), which he said could lower emissions for both integrated blast furnace-basic oxygen furnace mills and EAF mills.
Gibbs said that domestic mills have been making such investments for a while, with Cleveland-Cliffs, Nucor and voestalpine adding about 15Mt of capacity in the US over the past 15 years. He also noted that given the tightness of prime scrap supply, US mills have been finding ways to use more shredded scrap, helped by new separation technologies to raise the quality
of that scrap by removing the copper and other undesired residuals found in shredded scrap.
To date the mills’ changes in their raw materials mix have been limited, Bell said, other than using about 50% less pig iron compared with a year ago. But, Spoores said, there could be more of a push to have high quality iron units, and that will likely result in a new wave of investments in new US iron metallics facilities. Spoores added that it makes sense for those facilities to be domestically based given that the US has both high quality iron ore and low-cost natural gas.
As far as steelmaking capacity itself goes, it is uncertain how many new investments will be added to the pipeline, Kershaw said, noting that it will depend upon the mills’ perceptions of future downstream steel demand. But, while the US economy could slow somewhat over the next year or two, he said that an extended downturn isn’t expected. Therefore, Spoores said he believes there is a very good market case for additional EAF steelmaking capacity to be announced and built. �
Using the cheapest input materials while complying with crude metal quality requirements are important goals of EAF plant operators. To support them, we developed the Metallics Optimizer (MO) application that calculates the cheapest commodity mix by integrating machine learning techniques into physical process models. By Dr.
RECENT years have seen a steady increase in the use of the electric arc furnace (EAF) process for producing crude steel. It is expected that more than 50% of crude steel will be produced in scrap-based EAFs by the year 2100. Using scrap instead of virgin materials such as hot briquetted iron (HBI) or pig iron reduces carbon emissions during steelmaking by about 1.67 metric tons per ton of scrap and can thus help to reduce the carbon footprint of steel production. However, some types of low-quality scrap have higher amounts of impurities and come with greater uncertainty in terms of the concentration of these impurities than is the case with high-quality scrap or virgin materials. These impurities can jeopardize product quality. Copper in particular is detrimental to product quality. Hence, many operators try to avoid using too much low-quality scrap in their charge mixes and prefer to charge the more expensive highquality scrap and virgin materials, especially if the charge mixes are calculated manually without the help of modern machine learning techniques.
In this article, we describe the Metallics Optimizer (MO) application. By performing a machine learning-based estimation of the copper content in the raw materials, the degree of uncertainty concerning
the copper concentration is lower. A more accurate copper concentration is subsequently used in the charge-mix optimization. Consequently, more low-cost scrap types can be used, which reduces production costs.
The Metallics Optimizer (MO) tackles this problem with a two-step approach. In the first step, the copper concentration
of raw materials is estimated by the Materials Identifier (MI) using machine learning algorithms. These dynamic values are subsequently used in a second step, the charge-mix optimization (CMO). The dynamic copper concentrations are more accurate than static values, as these do not represent fluctuations in the scrap quality over time due to the market availability of scrap, uncertainties in the scrap supply chain, or changing suppliers. The CMO
takes into consideration current market prices for raw materials, their availability in the scrap yard, and other constraints related to the production environment. Through a better understanding of the scrap chemistry, it is possible to produce closer to the maximum allowed chemistry targets. As a result, more low-cost and high-copper scrap types can be used, which in turn reduces production costs.
The MO application is cloud-based. All necessary data is stored in the application database, which accesses the customer data sources. Physical properties of the raw materials are loaded from level 2 systems. Data for historic and scheduled heats is pulled from level 3. The ERP system provides the available inventory and price information for raw materials and additives.
The copper concentrations are periodically estimated by the MI for every scrap type. The frequency can be set by the user. The estimations are sent to a user interface (UI) for inspection by the operators. If required, the concentration values of all elements can be overwritten manually in the UI. Additionally, the estimates are sent to the
CMO, where they are used to calculate the charge mixes. The optimized charge mixes are also displayed in the UI together with the raw material and energy costs. The operator can also manually adjust the charge mixes or configure the process constraints in the UI. Fig 1
The Materials Identifier (MI) estimates the copper concentrations in the different commodities. Fig 2 illustrates the architecture of the data sources. The MI uses the historical charge-mix recipes, the steel analysis and yield, and the hot heel weight as inputs. This data is already available in most melt shops. If the hot heel weight is not tracked, it can be imputed from other data. This information is then used to calculate the target element concentrations (in this case copper) in the commodities.
New estimates can be generated at userdefined intervals (e.g. every day or every hour). The historical heat data is taken from a period before the actual predicted date. The length of this period is an important hyperparameter for the model and is set for every customer and EAF.
Fig 3 shows the results of the copper estimate for two different scrap types. To provide a better illustration, the copper estimates are non-dimensional and show the static copper value for the customer. Here, the static copper value is 1. A value
higher than 1 means that the actual copper content of that particular type of scrap, as estimated with the MI, is higher than the static value. Hence, using the static value in charge-mix calculations could lead to an underestimation of the actual copper content in the steel and potentially have a detrimental effect on the final product. This is the case with the mixed scrap seen in Fig 3 for the period 2020-09 onwards. A value below 1 means that the actual copper concentration as estimated by the MI is below the static value used by the customer. Hence, more of this scrap type could be used in the charge mixes without jeopardizing the quality of the final product. If this scrap type is low in cost, significant savings could be achieved. In Fig 3, home scrap has an estimated copper content that is only about half as high as assumed by the static value. If available, more of this scrap type could be used than previously assumed, even for steel grades with lower copper limits.
To better understand the advantages of the MI on the final steel quality, a comparison of historic charge mixes is made. The static and the estimated copper values of the MI are both used in a mass balance to calculate the copper content of the final product. This calculated copper content can then be compared to the measured copper content of the final product. This
comparison is depicted in Fig 4. The blue and yellow lines represent the ratio of the calculated copper content to the actual measured copper content. A value of 1
overestimates the copper content in the steel.
The charge-mix optimizer (CMO) calculates
costs. It also takes business and technical constraints into account. This may include the availability of a certain scrap type in the scrap yard, the minimum or maximum amount of a single scrap type allowed in the charge mix, the minimum or maximum concentration of any element in the final product, or the desired tap weight. Custom constraints relating to a specific furnace can also be added. The CMO returns the cheapest calculated charge mix under those constraints. It also returns the overall costs and the costs for raw materials and energy (or any other costs that are considered in the optimization).
For every chemical element, a safety margin can be applied in the charge-mix calculation. The safety margin reduces the maximum concentration allowed for that element in the final product during optimization. Hence, even if the element content in the scrap is underestimated, the quality of the product is not at risk.
would signify a perfect match between the calculated and measured copper values. A value greater than 1 would mean that the calculated copper content is higher than the measured copper content, therefore the copper concentration in the scrap is overestimated. A value below 1 would mean that the copper concentration in the scrap is underestimated and the calculated copper content of the final product is below the measured copper content. This poses a risk for the final product quality.
As shown in Fig 4, the use of the MI brings the ratio of calculated to measured copper content closer to 1, which is the ideal value. The static copper characterization generally
the cheapest charge mix for any given steel grade. It can take into consideration any costs, such as raw material or energy
The charge-mix optimization is sequencebased. In every heat sequence, the overall costs of the sequence are minimized. This has the advantage that transition zones between heats are taken into consideration. This is especially important for furnaces with large hot heels, as the hot heel of a previous heat influences the next heat. The hot heel with its chemical analysis is an input for the next heat, in the same way as the charged scrap mix. That is why going from a heat with a high copper content to a heat with a low copper content can be challenging, sometimes even impossible, even if scrap types with very low copper concentrations are charged.
Fig 5 shows copper concentrations in the final product. The solid green
line represents the copper target. The dotted blue line represents the charge mix produced by the customer with the traditional recipe. With some heats, there is a large gap between the green and blue lines. This means that more scrap types with a low copper content are used than necessary. As those scrap types are usually more expensive, there is potential to save money by using scrap types with higher copper content, which are usually less expensive. Consequently, the area between the green and blue lines represents the potential savings that can be made.
The dashed yellow line represents the charge mix calculated by the CMO. In this case, no safety margin was applied during optimization. With most heats, the copper content of the optimizer is equal to the copper target.
This means that the maximum permissible copper content has been attained, which corresponds to the cheapest possible charge mix. The first three heats of the sequence have a copper concentration below the target value. Heats 4 to 5
undergo a transition from a heat with a high copper target to a heat with a low copper target. As the CMO is sequencebased, it takes the copper target for the whole sequence into consideration. It starts with a lower copper concentration in heats 1 to 3 and reduces the copper content in heat 4 already, because a gradual reduction is cheaper than the large step between heats 4 and 5. Depending on the hot heel size, such a large reduction might not even be technically feasible.
In heats 11 to 14, there is a transition zone in which small changes in the copper concentration occur. These changes in the copper concentration (higher or lower) can be achieved in one step. The last 5 heats see a change of the copper target from a low value to a high value. This transition also takes place in two steps. The highest copper target value is not attained. This may be due to the fact that the cheapest available scrap types result in a lower copper concentration in the mix than the target.
The Metallics Optimizer calculates the cheapest possible charge mix for the EAF. It consists of the Materials Identifier, which estimates the element concentrations for every raw material charged in the EAF, and the Charge-Mix Optimizer, which minimizes production costs for a sequence of heats.
The Materials Identifier reduces any uncertainty regarding each elements’ concentration in the relevant raw materials. This reduced uncertainty is then beneficial for the charge-mix calculation. Raw materials with a higher copper content can be used to a greater extent as a much lower safety margin can be applied.
These high copper content raw materials are usually less expensive than those with low copper concentrations. The CMO is sequence-based and, therefore, also accounts for transition zones between heats by considering the hot heel as an input stream to the heat. This ensures that feasible charge mixes are created, which can be used directly in the production process. �
WHEN it comes to electric furnaces in the iron and steel industry, the electric arc furnace (EAF) is usually the first that comes to mind. These tilting, swivel-roofed, batch melting furnaces have been widely used for over a century in scrap-based steelmaking. With the need for decarbonization becoming ever more pressing and novel iron and steelmaking flowsheets emerging, another type of electrically-powered
metallurgical furnace – the electric smelting furnace (ESF) – is gaining attention. These stationary, sealed, fixed-roof, continuous operation furnaces are commonly used in the non-ferrous and ferroalloy industries and are the key to various viable decarbonization pathways, including replacing the blast furnace and enabling direct, continuous steelmaking from DRI.
Much like the EAF, the ESF consists of a
molten metal-resistant refractory crucible. It uses electrical power, supplied from electrodes vertically inserted through an enclosed roof, to achieve heating, melting, and the required smelting reactions. That is where the similarities end as the EAF and ESFs differ drastically in their design and operation. Although it replaces coal-based fuels with electricity, in many ways the ESF operates more like a blast furnace (BF) than
As the global push for decarbonization intensifies, the steel industry will need to develop more sustainable ways to manufacture steel. Electric smelting furnaces will be a key innovation in creating a more sustainable future, says Yale Zhang*, with their ability to process high-gangue ore and increase the degree of electrification being a critical part in the industry’s strategy to decarbonize.
an EAF, as summarized below:
The past
The EAF and ESF share the same roots dating back to the 19th century, when William Siemens demonstrated the first electric furnace for scrap melting at the Paris Expo in 1879. Paul Héroult developed this idea into the EAF steelmaking process, leading to a patent and commercial plant in 1907. Early development of the ESF started earlier, with a focus on phosphorus and
calcium carbide production, commercialized in 1889 and 1894, respectively. The invention of Soderberg electrodes in 1919 was revolutionary for continuous electric smelting and became the standard feature of metallurgical ESFs ever since.
The development of the rotary-kiln and electric smelting furnace (frequently referred to as RKEF) process for ferronickel in the 1950s, electric melting of DRI to produce pig iron in the 1960s, and non-ferrous slag cleaning processes saw the increasing
application of ESFs. Thanks to its ability to handle large slag volumes, accommodate higher temperatures, as well as its versatility in furnace customization, the ESF is now the dominant technology used to produce FeNi, FeCr, FeSi, silicon metal, and PGMs (Platinum Group Metals). Despite that, it is limited to niche ore processing when it comes to ironmaking. This includes the processing of vanadium titaniferous ores at New Zealand Steel and the now defunct Highveld Steel to produce pig iron and
TiO2-rich slag. ESFs are also used extensively to process titanium-bearing ilmenite (FeTiO3) ores, at operations by Rio Tinto Fer et Titane (RTFT) and Rio Tinto Richard’s Bay Minerals (RBM), to name a few. Several DRI-ESF ironmaking processes have also been developed over the past decades, including Kobe’s FASTMELT process and Inco’s Inmetco process. Currently, the rotary hearth furnace RHF-ESF process used by Iron Dynamics is the only active commercial ESF-based ironmaking operation to produce hot metal using a conventional ferrous slag system.
The recent rise in the interest of applying ESF technology to iron and steel production follows the realization that the existing direct-reduced iron DRI-EAF processes –the foremost candidate to replace blast furnaces and basic oxygen steelmaking as a lower-emission alternative – is heavily constrained by pelletizing capacity and raw material supply, namely the limited availability of low-gangue iron ore. If high gangue iron ores are used directly in the DRI-EAF process, all gangue material from the ore is rejected at the EAF as steelmaking slag, which is inefficient due to the high volume and iron content of the slag. To produce pellets more suitable for EAF steelmaking, the iron ore must undergo a gangue rejection step prior to the DRI-EAF route. The losses from the ore beneficiation step are recovered through increased selling prices when using low-gangue, DR-grade iron ores. When applied to higher gangue, BF-grade iron ores, this leads to unacceptable levels of energy and yield losses that cannot be recovered through an increased selling price.
To support the world’s growing appetite for low-emission green steel through the DRI-EAF pathway, much of the highgangue iron ore used in BFs today needs to be converted to low-gangue iron
ore. Unfortunately, the capital cost and implementation timeline required for such a pursuit is prohibitive and introduces other risks, such as water availability and logistical issues regarding tailings storage and handling. For many lower grade ores, iron yield loss is significant during beneficiation, especially to produce what is considered DR-grade pellet feed. Significant decarbonization can only be achieved if proposed lower-emission steelmaking processes are suitable for most of the world’s ore supply, which is higher gangue, BF-grade iron ores.
This is where the ESF comes in. Wellproven in the non-ferrous and ferroalloy world where it is accustomed to dealing with much higher slag volume, the ESF is an ideal process to melt low-to-high gangue containing DRI using electrical energy. The resulting carbon-containing hot metal
produced from the ESF can be transferred for subsequent oxygen and/or electrical steelmaking while gangue is removed in the form of low-Fe containing slag. This slag is comparable to blast furnace slag and can be valorized as a clinker substitute for the cement industry where this in-turn reduces the cement industry’s carbon emissions.
Besides effective gangue rejection and the possibility of using more cost-effective, BF-grade iron ore in a lower emission flowsheet, there are other benefits to the steelmaking processes from having an ESF upstream. The ability to turn DRI into hot metal opens the possibility for the BOF to be coupled with the lower-emission ironmaking process. This is a significant advantage, as it enables the production of steel grades that are otherwise difficult to produce with the DRI-EAF route (e.g., low nitrogen steel), as well as hot metal pre-
treatment processes before steelmaking. In addition, in many cases this allows the continued use of existing and highly optimized steelmaking assets. This is the current decarbonization transition pathway being pursued by several major European steelmakers to replace their blast furnaces, with minimal impact to their existing ore supply, steelmaking assets and product mix. Notable steelmakers committed to this pathway include Tata Steel Netherlands and Germany’s thyssenkrupp.
EAF steelmaking fed by hot metal from an ESF also benefits from lower gangue input in addition to the latent and sensible heat of the molten hot metal, as it reduces yield loss and boosts productivity – much like many hot metal-based EAF operations today. The use of hot metal gives EAF operators an additional source of highquality ore-based metallics (OBM) made from more cost-effective high gangue iron ore sources to fill the growing demand for merchant pig irons/hot-briquetted iron (HBI) – a situation that is likely to worsen with the continued deterioration of scrap quality and related impurities. The possibility of adding a hot metal pretreatment step (e.g., dephosphorization and carburization) before adding it to the EAF has the potential of unlocking more lucrative steel grades as well.
DRI technology is evolving from using natural gas or syngas, to hydrogenbased reduction, to further reduce carbon emissions. One consequence of this transition is a rise in the production of low-carbon or even carbon-free DRI. Modern EAFs rely heavily on carbon in DRI for chemical energy, slag foaming, and yield improvement, with operators often preferring higher carbon content in the DRI. Without this carbon, EAF steelmaking can become less efficient, resulting from lower yields and increased energy consumption. This poses a challenge for the industry’s transition to low-carbon or carbon-free DRI.
Rather than feeding DRI to an EAF directly, an ESF has the flexibility of being able to process low-carbon or carbon-free DRI. Inside the ESF, carburization reactions occur that impart carbon into the molten metal. The key to this carburization is the ESF’s ability to maintain a strong reducing atmosphere within the crucible, unlike an EAF which experiences significant ingress of air. This lessens the reliance of an ESF on
carbon chemically bound within the DRI, as it can better utilize carbon sources that are added to the furnace, such as anthracite. Furthermore, steelmakers have shown interest in potentially replacing coal-based reductants like anthracite for biomass – an emission-free carbon source to further drive emission reductions. If ESFs act as the bridge between low carbon DRI to EAF steelmaking, many of the challenges of transitioning to hydrogen-based DRI can be addressed.
Even more remarkable is the prospect of transforming an ironmaking/DRI-melting ESF into a direct steelmaking process, potentially replacing the traditional EAF altogether. To achieve this, Hatch developed the patented Continuous Reduced Iron Steelmaking Process (CRISP) to create the next generation of integrated steel mills. This can be either new construction, or Hatch can convert ironmaking CRISP+ furnaces into steelmaking CRISP furnaces to eliminate either oxygen steelmaking or electrical steelmaking. The concept involves altering the physical and thermochemical condition inside the ESF to achieve decarburization of the hot metal instead of reduction. The stationary fixed-roof furnace design also allows for many of the operational advantages described for an electric smelting furnace in ironmaking service to evolve into a direct steelmaking operation.
The CRISP direct steelmaking process is an established concept, and a successful pilot was carried out in Sweden between 2008 and 2009. The pilot demonstrated the ability to produce low-nitrogen liquid steel comparable to BOF-made liquid steel while achieving improved yield, and low emissions. Additionally, this technology relies on solid waste oxides for decarburization, eliminating the need for oxygen injection, which reduces utility costs and boosts iron yield. Replacing the ESFEAF pathway with one step, results in an innovative, efficient continuous steelmaking process that requires lower total energy with a higher degree of electrification.
As the global push for decarbonization intensifies, the steel industry will need to develop more innovative and sustainable ways to manufacture steel. While there are several new technologies in development that will help achieve this goal, the advancements of ESFs will be a key innovation in creating a more sustainable future.
The ability of ESFs to process highgangue ore and increase the degree of electrification of traditional iron and steelmaking will be critical in meeting the industry’s emission reduction targets; and the ESF’s effectiveness and versatility in performing different process functions makes it an instrumental piece of the green iron and steel value chain of the future. �
Charles Dickens was a remarkable man who experienced hardship in his early years when his father was put in prison due to insolvency. Charles had to quit school to work but resumed his studies some years later and became a fantastic writer and observer of mankind. His novella A Christmas Carol was published 180 years ago and is the inspiration for this article on the endeavour of decarbonizing the steel industry by 2050.
With the introduction of the Bessemer, Thomas and Siemens-Martin processes in the second half of the 19th century, it became possible to decarburize blast furnace iron in liquid form. The amount of manual work decreased, the economies of scale increased and thus productivity and profitability. For small ironworks in Sweden, it was a disaster and entire communities disappeared. Many probably swore by Henry Bessemer, but the few companies that had enough capital and opportunity, invested in the new technology and grew. The death of mills did not go unnoticed by the politicians and legislation was demanded to prevent the transformation of the industry from taking place. That did not happen and it took until the energy crisis at the end of the 1970s before a similar crisis appeared.
This time the politicians were more active and gave extensive support to investments in the steel industry to secure jobs. Blast furnaces were shut down and replaced by electric arc furnaces and certainly jobs were created, first when the new plants were built and again when they were dismantled
to be shipped to where they could be operated at a profit. A complete waste of money. Now that the steel industry is once again facing great stress and demands for change, do we have anything to learn from this story?
As cruel as it may sound, the first lesson should be that there is a time for everything and when the conditions that made a place a successful industrial location disappear, in the long run the industry will also disappear. Trade secrets, skilled employees and niche products may be sufficient conditions for survival and prosperity, but new technology alone will not help if it can be applied with greater success elsewhere. Furthermore, it is interesting to note that when investment in new steelmaking processes took off, they had reached what we call today a top technical readiness level (TRL). Sir Henry Bessemer may have invented the Bessemer process, but it was after long trials that it finally succeeded when Göransson, who was manager at Högbo mill north of Sandviken, could take it into operation. The Thomas and SiemensMartin processes had similar stories: they were developed in England, Germany and
France and were introduced on a wide scale in Sweden where they were first proven. Another lesson is that process development takes time. Bessemer’s ideas to use oxygen instead of air in steelmaking and to replace ingot casting with continuous casting took until the mid-20th century to be implemented for steel. To continue, the energy crisis led to extensive development programmes worldwide to replace the blast furnace with processes that did not need agglomerated raw materials. After 50 years, there are few implementations of new reduction technology, and the blast furnace is still the dominant reduction process. A successful story is, however, the natural gas-based direct reduction process that has gone from moderate sizes of 100 kt/yr to the mega modules we see today of 2.5 Mt. It is impressive, but has taken more than 50 years to scale up.
Today, more than half of the world’s production of steel is made in China, and India has announced that it will increase
For 50 years, Köppern briquetting machines have played a key role throughout the world in the production of HBI for DRI processes.
And HBI is still in demand, as demonstrated by the new HBI plants equipped with Köppern roller presses at LEBGOK (Russia), ArcelorMittal (USA), CLIFFS (USA) and upcoming installations, reducing the CO2 footprint of the steel industry.
» State of the art technology
» Experts in process technology
» High plant availability
» Long-lasting equipment
Köppern – Quality made in Germany. www.koeppern.com
production drastically. The blast furnace is the dominant reduction process for iron ore followed by natural gas-based direct reduction. Scrap is the other ferrous raw material and the amount available for steelmaking is greater in industrialized countries than elsewhere although the amount of available scrap is continuously increasing. When it comes to greenhouse gas emissions the relation between the three processes can, for the sake of discussion, be set as roughly 2kg, 1kg and 0.5 kg CO2-eq/kg steel.
Just a few years ago, the issue of greenhouse gas emissions was only mentioned in passing in the steel industry. Projects like EU-funded ULCOS, aimed in the first decade of this millennium to develop low greenhouse gas emission alternatives to ironmaking processes; their most successful project was the oxygen blast furnace with top gas recirculation and carbon capture
and storage (CCS) which was tested with good results on a pilot scale. Then, many of us experienced that the lid was put on. Instead, projects with direct reduction using hydrogen were introduced and were funded by the EU. These projects are now reaching demonstration level in the one million ton scale but are reported not to be profitable with present hydrogen prices.
Today, the debate about the development of the steel industry, at least in the Western world, is dominated by the issue of reducing greenhouse gases, and those who bring it to the agenda are mainly politicians, financiers, customers and the steel companies themselves. Organizations such as the UN, IEA, WTO, WEF, OECD, worldsteel and the G7 are committed to developing systems to drive development towards low emissions steelmaking. Organizations of investors and customers as well as steel makers and non-profit
organizations are also engaged in developing calculation systems, roadmaps, threshold values or different types of labels. Today, it is almost a full-time job to follow this development and to understand the effect different systems or programmes can have on the market and on the steel production companies.
A dilemma suddenly arises here. It’s quite simple. If we are to reduce emissions to 0 by 2050, we should look at what is emitted when producing each ton of steel and report this. If it is below a certain value, it can be considered close to 0. If you as a producer want to sell steel that is close to 0, you must invest in processes that do not emit greenhouse gases. Supply blast furnaces and direct reduction plants with carbon capture and usage or storage, CCUS, or switch to hydrogen or biogenic syngas as a reducing agent. It will, however, take time since the fossil-free processes are probably not ready for the market in full scale yet. Much can be done to reduce emissions to some extent, but few if any can reach close to 0 immediately, and politicians and customers must understand that.
The final question is: are we right to assume that all companies must survive the transition to close to 0 steel? It was not like that in earlier crises and if we twist the labeling systems so it becomes easier for a company with higher emissions to get the same label as a company with lower emissions, are we then working for decarbonization? Finally, when governments subsidize investment in new technology to save jobs, are we sure the plants can be run with a profit in the long run and the jobs will stay or is it just a waste of money?
In A Christmas Carol, Ebenezer Scrooge is, after confrontation with the ghosts of past and present Christmases, given the opportunity by “The ghost of Christmases yet to come” to – in a dystopic way – see into the future in order to make what we can call life-changing decisions. Let’s think about what we might experience if we were visited by “The ghost of steelmaking yet to come” and escorted to the “Greenish Steel Conference 2050” just in time for the inauguration speech:
“Dear delegates, as we gather here today, we can state that we have put a successful year behind us. After extensive negotiations,
the number of definitions of greenish steel has now been reduced to 300, which is three less than last year. Since both steel manufacturers and steel customers are involved in the design of each of the programmes, a greenish steel label that satisfies consumers can be guaranteed.
“The number of research projects for fossil-free steelmaking has now reached 2000 and the number of pilot installations of the five leading alternative processes for pig iron and DRI in operation has reached five i.e., one of each. Additional plants are planned when it is judged that it is possible to compete with traditional plants producing greenish steel.
“Projects to relocate steel facilities to areas with conditions for them to be operated without heavy losses are happily underway among many of our members. They represent great manufacturing potential for greenish steel once they are in the right place.
“Scrap exports have now completely ceased from the USA and the EU as they closed their ore-based works, which is why the countries that previously used this scrap
raw material have switched to sponge iron production in rotary kilns. Admittedly, this results in higher emissions of greenhouse gases than the previous ore-based production in the EU and the USA, but through a new calculation formula, this DRI can also be assessed as greenish.
The question of who should pay for the capture and storage of carbon dioxide as well as the extra cost for hydrogen production has now entered a decisive phase. Since all products are greenish even without CCS or hydrogen, there is no possibility of passing this cost on to the consumer. We expect to be able to have a conference on this and come to a decision around 2060-2070.
“This concludes my introductory remarks. Unfortunately, greenhouse gas emissions increased last year, so today we are 30% above the 2020 level, but in 2051 we expect the rate of increase to decrease.”
A Christmas Carol by Charles Dickens ends happily with Scrooge realizing that there are values other than money. In the business
world, unfortunately, it’s just a beautiful thought. A company’s task is to increase capital for its shareholders. Nothing else. However, laws and regulations, other stakeholders such as employees, public opinion, and, of course, customer requirements are considered, all of which affect the company’s profitability and longterm survival. It is natural for management to wish for regulations that favour their existing plants and way of production regardless of the impact on the climate.
Earlier crises have forced companies to rethink their supply chains and their business ideas, and some have been forced to close. Cash injections from governments in the wrong projects have only prolonged the pain since the laws of business economy are what they are. If we really want to meet the goals of the Paris agreement, we must brace ourselves and realize that the transition to near zero steel making will hurt, but not having a transition will hurt even more. Then, maybe even this carol can have a happy ending. �
Combilift is the perfect fit for the steel industry. Our multidirectional forklifts, straddle carriers and mobile gantry cranes are perfect for handling long product, allowing you to maximise your storage, efficiency and safety.
• Safer product handling
• Optimised production space
• Improved storage capacity
• Increased productivity & output
• Enhanced profits
Danieli’s Digimelter has allowed a technological breakthrough in electric steelmaking, with lower power and electrode consumption thanks to the Q-One power feeder, for zero impact on the power grid and the possibility to use renewable energies.
OVER THE LAST 50 years, electric furnace technology has continuously evolved (see Fig.1) towards increased efficiency, with electric energy consumption halved, tap-totap time reduced fourfold, and electrode consumption reduced by more than five times. These results have been achieved thanks to a combination of chemical packages (oxygen blowing, burners), design improvement (water-cooled walls, EBT, lances, bottom stirring) and enhanced process controls.
Another important trend has been the increase in average power for individual furnaces, which has led to the development of ultra-high-power EAFs capable of producing in excess of 360 tons of steel per hour.
Electric arc furnaces have a powerful impact on power grids: the more powerful the EAF, the more severe the effects, with consequences like flicker, a phenomenon characterized by quick voltage variations that are visible in bulbs (flickering) and this can negatively affect power electronics, such as inverters in a rolling mill or similar processes. The arc furnace also impacts harmonic distortion and power factors with possible significant voltage drops, again impacting all plant auxiliaries, and in the worst case,s causing machine stoppages.
Many solutions have been developed over the years to dynamically compensate for such disturbances, namely SVCs (Static Var Compensators) and VSCs (Voltage Source Converters). These are high-power electronic systems designed to superimpose controlled reactive power to mitigate the impact of furnace disturbances.
The possible solutions for electric power transfer to the arc were the AC furnace and DC furnace. While AC furnaces are the most common technology applied – where arc voltage and current are controlled thanks to the positioning of electrodes – DC furnaces
use rectifiers to impose the current of the arc, but with some significant implications for equipment design and related maintenance.
DC furnace technology reduces flicker generation and improves furnace control, but requires a different and more expensive mechanical and electrical design. DC furnaces, therefore, are more maintenanceintensive and the bottom shell refractories require much more attention.
The Danieli Digimelter® for scrap/DRI Digimelter® is Danieli’s solution for modern, clean, competitive, sustainable green steelmaking, recognized by the market as the new benchmark technology for electric steelmaking to melt scrap/DRI.
It is a Danieli-patented technology with a combination of power, intelligence, and environmentally-friendly equipment for achieving 15,000 heats per year with minimal OpEx, the lowest environmental impacts, and high flexibility for raw materials.
• The Q-ONE electrical feeder provides the highest power factor and very low network flicker due to real-time arc control. It achieves high-power transfer thanks to independent control of arc current, voltage, and frequency, for each electrode.
• The Q-Melt intelligent controller runs EAF melting processes automatically by making use of the Q-Reg+ electrode regulator, Lindarc laser off-gas analyzer, and Melt-Model self-learning optimizer.
• The Zero-bucket concept is accomplished by the ECS continuous scrap charging and preheating system as well as continuous hot DRI feeding from the roof, for reduced environmental impact and enhanced energy saving.
• The Eco-Pro airtight design reduces pollutants to a minimum. Compared to a conventional EAF with the same charge mix, Digimelter® Eco-Pro reduces CO2 direct emissions (Scope 1) by more than 50% and overall CO2 emissions (Scope 2) by 25%.
Q-One is Danieli Automation’s patented, key technology and the basis of the Digimelter® concept.
In 2016 Danieli Automation installed the first Q-One, the first industrialized application of power electronics to control electric arc current and voltage in the EAF. In other words, using the conventional furnace design, this solution can impose arc current, with consequent benefits in process stability as well as a drastic reduction of impacts on the connecting electric network.
In fact, Q-One operates with a power factor at a medium voltage above 0.96, generating a very low flicker, and also avoiding the use of compensation systems because the harmonic generation is well below IEEE limits.
The system is modular by design: not only can the power required by the process be adjusted by selecting the number of modules, but also the solution can be designed for progressive growth in stages, meaning that initial power can be increased just by adding modules in a second stage. This modularity improves reliability and plant availability, considering the possibility to keep melting at reduced power (disabling one module) or even with two phases instead of three.
High availability is a must, and that’s why modules have also been designed with the same components and inverters, which minimize the quantity and value of spare parts. Digital control allows for remote monitoring and troubleshooting.
The working points are no longer discrete, dictated by the taps on a transformer, but can be chosen freely according to process needs.
One additional degree of freedom is given by the change of frequency, possible only in arc furnaces adopting Q-One technology. A frequency higher than network nominal improves arc stability and, therefore, is used during the boring stage, while a frequency below nominal, down to 20Hz – today used daily by our customers – is ideal for reducing energy consumption in the refining stage and for deeper penetration of the arc in the molten bath,
as well as to induce a beneficial stirring effect on the molten steel.
Lower frequency means a lower inductive reactance and consequently a lower consumption. Results from the field prove that up to 10% extra energy savings come from the low-frequency operation.
The control of arc current implies a much more stable operation of the furnace, visible during melting, due to the absence of cooled-cables swaying and electrodes oscillating. The outcome is reduced electrode consumption, up to 15%, and at least a 20% longer refractory life.
The unique, reliable, and flexible green power solution of Q-One also benefits from
Artificial Intelligence (AI) applications and advanced control solutions. Danieli Q-Melt advanced process control offers dynamic and automatic optimization of the melting profile. The system has been designed with Danieli’s Intelligent Plant architecture for continuous learning and improvement of the process.
In addition, Q-Melt furnace automation is fully integrated upstream with an automatic scrap-yard management system in order to optimize melting process control for accurate and consistent working points set-up and quality assignment. To conclude, the control pulpit is ergonomically designed to integrate human expertise and machine precision to achieve unique performances and superior quality with the best cost strategy.
Most importantly, these results are achieved with a no-man-on-the-floor philosophy, powered by advanced automation and the adoption of robots in the field to perform dangerous and repetitive operations and, therefore, achieve safe operation in steelmaking.
Danieli Zerobucket EAF is the most environmentally friendly melting technology with the lowest CO2 footprint.
Characterized by high flexibility in raw materials, low energy consumption, high reliability and utilization factor, lowest noise and pollution emissions, the Danieli Digimelter® Zerobucket with ECS horizontal continuous charging system might provide a solution to the latest needs of steelmakers.
A stable and smooth process allows operators to introduce the system to optimized operating conditions, reducing
risks of delays and providing a fast learning curve.
The Hytemp pneumatic transport is the most efficient way to deliver hot DRI to the EAF at > 600 °C with no dust losses. It has been in operation since 1998 at four reference installations (Ternium, Emirates Steel #1, Emirates Steel #2 and Suez Steel), and about 40Mt of DRI has been transported up to now. It offers outstanding reliability and availability close to 100%, with very low maintenance requirements.
Hytemp is fully integrated with the DRP and Q-Melt™ furnace control systems, and matches the highest safety standards thanks to the inert carrier gas and completely sealed design.
The Digimelter® Eco-Pro airtight design is conceived to minimize the emission of pollutants and their CO2 equivalent. Every detail of the Digimelter® has been carefully optimized in order to minimize air inlet to
the melting area.
The furnace is always kept sealed, thanks to the Thor 3K automatic slag door and improved sealing between the furnace and the ECS conveyor.
The process itself is controlled automatically by the Q-Melt suite, leading to a minimization of oxygen and carbon injection, ensuring the most efficient melting with the lowest CO2 footprint. Compared to a conventional EAF with the same charge mix, Digimelter® Eco-Pro reduces direct CO2 emissions (Scope 1) by more than 50% and overall CO2 emissions (Scope 2) by 25%.
Hybrid-ready by design
Digimelter® fits in very well with the sustainable approach to steelmaking, thanks to the possibility of connecting the DC Link to renewable energy sources, such as photovoltaic, but also hydro or wind power, using the Q-One power feeder. With hybrid feeding, the OpEx of a furnace would be further improved, while the carbon footprint is also reduced. The Q3-Jenius software suite has been designed
to manage the different available sources, depending on their cost and availability, with consideration also paid to forecast energy consumption for specific products.
Having a very low impact on the grid, the Digimelter® represents an ideal solution for the decarbonization path, considering new arc furnaces melting scrap/DRI in place of blast furnaces. In fact, the electric network close to integrated plants typically was not designed to supply high volumes of electric power, required by arc melting, and the impact of traditional transformer EAF solutions on the electric grid is critical. With Q-One, even for high-power furnaces, in most cases there is no need for any additional compensation system to meet the electric authority requirements. Furthermore, the modularity of the Q-One system makes it suitable for the furnace evolution ‘in phases,’ where hot metal can be charged in high percentages in a first phase, while DRI and scrap will be mainly used, with higher power requirements, in a second stage.
The industrial transition from ironmaking to electric steelmaking started with Algoma Steel in December 2021. It was the world’s first steelmaker to convert fully from BF to EAF steelmaking, resulting in a 70% CO2 reduction. To be installed at Sault Ste. Marie, Ontario, Canada, and started by early 2024, the plant’s new, green steel shop will have a design capacity of 3.7 Mt/ yr of liquid steel.
Algoma Steel will operate two, 250t Danieli Digimelters®, powered by two Q-One digital power systems with a rated capacity in excess of 190 MVA each. The design provides for the bestin-class environmental performance with engineered enclosures for the two furnaces to minimize noise and emissions, while the Q-Melt automatic process control will deliver superior energy efficiency.
Two new, off-gas treatment plants, including baghouses and a dedicated recirculating water treatment plant, will combine to provide the best available technology for emission control and filtration, and water conservation.
Liberty Ostrava in Europe to make the step from ironmaking to electric steelmaking in August 2022. Two Danieli Digimelters® with a combined capacity of 3.2 Mt/yr will be installed at the Ostrava steelworks in the Czech Republic, and start operation in 2025. With a target emission reduction of 80%, this is the first step for Liberty towards carbon neutrality.
In the initial phase of the project, the two 200-t Digimelters® will replace Ostrava’s existing four tandem steelmaking furnaces (oxygen converters) and perform decarburization with flexible inputs of hot metal and scrap charges ranging from 8020% to 60-40%.
Starting from 2027, thanks to an enhanced electrical network, the furnaces will be able to melt HBI, DRI and scrap mixes, and up to 100% scrap, by fully exploiting the strengths of the Digimelter® Being powered by Q-One, Digimelter® ensures an almost negligible impact on the power network.
Digimelter® installations
Together with high-speed casting and Danieli Universal Direct Rolling, Digimelter® is one of the key technologies of Danieli MIDA minimills for long and flat products.
Due to the tangible advantages, the latest MIDA minimill orders, including those from CMC Steel, Bashundara, Pacific Steel, Nucor Steel, Tata Steel and Unitex, incorporate Digimelter® technology.
• CMC Steel Arizona 2 / USA
The first plant in the world to produce merchant bars in endless mode is CMC Steel Arizona 2/USA.
Operational in early 2023 in Arizona, CMC Steel Arizona 2 is home to the third Danieli MIDA QLP minimill for CMC Steel and will produce 0.5Mt/yr of rebar and small merchant sections. Hybrid-ready, it will melt local scrap using the Danieli Digimelter® (Q-One, Zerobucket, Q-Melt) and produce in endless casting and rolling mode. It will feature a patented layout specifically developed to fully match the needs of merchant products in terms of high plant uptime and excellent yield.
• Bashundhara / Bangladesh
Jumbo QLP® minimill to produce 1-Mt/yr bars and wirerod.
Danieli’s Jumbo QLP® will be installed in Chittagong and started up by mid2023. The Bashundhara minimill was designed with the latest, highly efficient
and environmentally friendly technologies. Danieli’s Digimelter® – which is ready for connection to renewable energies – will melt scrap continuously charged and preheated by Daniel’si ECS system. Straight rebar, and ribbed and smooth wirerod will be produced in endless casting and rolling mode through a single-strand, 150-t/ph Octocaster® featuring FCC® and octagonal section, starting from mid-2023.
• Pacific Steel Group/USA
A world first MIDA-QLP® hybrid minimill featuring Q-One® and Q-Jenius and making use of solar energy.
To be installed in Mojave, California. Operational by early 2025, the new MIDA Hybrid endless casting-rolling minimill will produce 380kt/yr (short tons) of straight
Nucor’s new MIDA-QLP will produce 410kt/yr (short tons) of quality rebars from recycled steel scrap. It will be installed in Lexington, North Carolina and will feature Danieli’s Digimelter® and LF powered by a Q-One® digital power feeder. The system is capable of using renewable energy. A single-strand, highproductivity Octocaster® will feed the rolling mill in full endless mode. Managed by Danieli Automation’s advanced process technologies and artificial intelligence, the minimill will incorporate Q3 pulpits to support operators in supervising a fully automated plant, making extensive use of big-data analysis. Robotized solutions will increase plant safety according to the ‘zeroman on the floor’ concept. Handled by a Q3-Met manufacturing execution system, production will start by summer 2024.
• Tata Steel / India
750kt of quality rebar produced in a sustainable way using a Digimelter® and endless casting-rolling technology.
Investment in a Danieli MIDA Hybrid QLP minimill for the production of long products is part of Tata Steel’s commitment to invest in a circular economy and to transition to low-carbon steelmaking through the steel recycling route.
The new MIDA QLP will be installed in the North of India, in Ludhiana, Punjab, and produce quality rebar, mainly 550 SD grade.
and spooled rebar in the most efficient and ecological way. Fed by a continuous charge system, the scrap will be processed through Digimelter® and LF digital melting and refining units, powered by the Q-One digital power feeder, which ensures the best power conditions at different frequencies. Hybrid by design, Q-One will make use of solar energy generated on-site, through Q-Jenius. This will be a fully automated plant, starting from automatic scrap management through final product tracking, featuring the Q3Met manufacturing execution system for production scheduling and tracking, for maximum plant efficiency.
• Nucor Steel / USA
This is the third order from Nucor Steel for a MIDA-QLP® endless casting-rolling minimill for rebar.
The minimill will feature the Danielipatented Digimelter® (Q-One hybrid power feeder + the Zerobucket scrap charge system + the Q-Melt advanced process control suite) and Octocaster® feeding an ultra-compact rolling mill. Operations will commence by the end of 2024.
• Unitex Steel / Bangladesh
1Mt/yr minimill for bars and light sections featuring the Digimelter® melting unit with continuous hot charge.
A complete minimill, including auxiliary plants for fumes and water treatment as well as the most advanced electrical and automation systems, to guarantee continuous and reliable production.
A highly efficient, 100-t Digimelter® featuring a Q-One digital power feeder and ECS continuous-scrap charging and preheating systems will competitively melt scrap. A four-strand, quality conticaster featuring FastCast Cube™ oscillator, EcoPower Mould™ and EMS, will feed a superflexible merchant rolling mill in hot-charge
mode. It will be installed in the Feni district of Chittagong, in the eastern region of Bangladesh. The minimill is scheduled to be started up in Q4 2024.
Q-One is very suitable for meltshop upgrades, including those that need renovation to boost productivity and performances.
It is applicable to both EAFs and LFs and provides increased power input and operation savings in terms of electric power and electrodes, along with zero impact on the power grid and other related benefits.
The first EAF upgrade dates back to 2016. Then, in 2019 at an 80-ton capacity furnace at ABS Sisak, Croatia, +10% productivity, -8% energy consumption and -15% electrodes consumption were achieved.
The latest order is from Cognor, Poland, for an upgrade of a 48-ton EAF.
The first ladle furnace upgraded to a Q-One power feeder has been in operation at Tokyo Steel since mid-2021, having a capacity of 125 tons, and that of CMC Steel
Arizona 1 at the Danieli MIDA minimill operating since early 2022, confirms the smooth and quick start-up already performed at Tokyo Steel.
Q-Melt interfaces with the Danieli Automation Q-SYM2 advanced, unmanned, upstream AI scrap-optimization and management system.
Q-SYM2 provides the furnace with the best classified raw material and scrap processing machine interaction according to the EAF/scrap bay’s needs.
Scrap is mapped from the moment it arrives at the steel plant right through to its use in the furnace, to ensure the quality and quantity of incoming material in line with the purchase order.
Real-time tracking allows for prompt, effective and simplified claim procedures when needed, thanks to artificial intelligence that makes possible automatic image acquisition and analysis.
Real-time scrap inventory is made continuously available, reducing human
errors and operational times. Scrap tracking handles scrap movement within the yard including loading and unloading bays.
A native integration within the overhead cranes improves yard management yield.
Accurate ‘crane mission-generation’ results in optimized crane utilization, with repetitive actions promptly executed based on scheduled and predetermined patterns.
The Danieli Digimelter®, powered by Q-One, represents the best available solution for the substitution of blast furnaces/BOFs with electric arc furnaces of 300 tons capacity or more.
Thanks to the unique power control on the arc, Q-One introduces a new approach to the melting process, with frequency control and freedom of choice on working points, minimal impact on the grid, achieving minimum OpEx for furnace operation, with hybrid feeding, intelligent process controls and safe operation.
Digimelter® is widely used in modern minimills and enables steelmakers to enjoy the benefits of melting efficiency, reduced energy and electrode consumption. �
Hydrogen-based steelmaking represents just one key production technology to replace the current integrated BF-BOF route with other production technologies, such as the extended use of scrapbased EAFs playing a major role. Novel H2-based technologies investigated in this paper include direct reduction to iron in shaft furnaces and using fluidised beds, suspension ironmaking, plasma direct steel production and electrolytic processing. The technical and economic viability of these at large-scale production is yet to be tested. By B Khalkho, S Sudershan, P Saravanan & S Srikanth*
DECARBONIZATION is essential to mitigate climate change to meet the goals of the Paris Agreement to prevent global warming to well below 2°C. Steel production, in terms of CO2 emissions, contributes about 7% of total global emissions (Pérez-Fortes et al 2014). A central challenge lies in finding pathways that allow the use of steel as an essential engineering material while avoiding its negative environmental impact. Primary steelmaking via the blast furnace –basic oxygen furnace (BF-BOF) route has an average emission intensity of 1860kg CO2/ tonne of liquid steel (tls). The majority of this comes from the BF (61%) and cokemaking plant (27%)[1]. Methods such as coke dry quenching and optimising pellet ratios, as well as BF equipment such as top gas recovery turbines, reduce but cannot eliminate these carbon emissions. Replacing coke with natural gas also significantly cuts CO2 in primary steelmaking, as can injecting hydrogen or ammonia into the BF. However, none can achieve carbon neutrality because they do not completely remove carbon from the steelmaking process.
Therefore a clear need for new technologies that can produce carbonneutral steel is required. The technoeconomic feasibility of three innovative steel
production technologies – blast furnace with carbon capture and storage (BF-CCS), iron ore electrolysis or electrowinning (EW) and hydrogen direct reduction of iron ore (H-DRI) – were evaluated by Fischedick, et al in 2014, based on the material and energy flows for the production of one tonne of crude steel[2]. In their analysis, they found H-DRI, as the most attractive
option, economically and environmentally. Integration of CCS in steelmaking is being explored under the ultra–low carbon dioxide (CO2) steelmaking (ULCOS) project. However, concerns over the safe transport and storage of captured CO2 make CCS options less attractive[3, 4]. Electrowinning or molten electrolysis of iron ore is a relatively new technology and is quite far from
Corresponding author khalkhobhawna@sail.in
reaching commercial feasibility. Some novel hydrogen steel technologies are discussed in detail.
Introducing hydrogen
Hydrogen, the lightest element in the periodic table, is a reducing agent. It can replace fossil fuels and also allows flexible and supply-oriented storage of renewable energies[5]. The use of green hydrogen – generated from renewable energy –can reduce emissions by 2.3GtCO2/yr[6] Hydrogen-based direct reduction of iron (DRI) uses hydrogen instead of natural gas or coal thereby eliminating CO2 emissions. Today, 5% of total global steel is produced by the DRI route[7] mainly using either the MIDREX process, Energiron from Tenova HYL or Circored technologies. These employ a mixture of carbon monoxide and hydrogen produced by steam reforming (SMR)[8, 9, 10, 11] of methane to heat and reduce the ore. Reduction reactions occur below 1535°C inside a shaft furnace. The reactions are:
Exothermic reduction of hematite by CO: Fe2O3(s) + 3CO(g) = 2Fe(s) + 3CO2(g) (1)
Endothermic reduction of hematite by H2: Fe2O3(s) + 3H2(g) = 2Fe(s) + 3H2O(g) (2)
The conversion of natural gas to a mixture of CO and H2 by steam methane reforming (SMR) is also endothermic and has a reaction enthalpy of 206kJmol[12] (equation 3):
CH4(g) + H2O(g) = CO(g) + 3H2(g) (3)
Novel hydrogen steelmaking
Five hydrogen steelmaking technologies are discussed below, each being considered for its merits and drawbacks.
In 2016, Luossavaara-Kiirunavaara Aktiebolag, Svenskt Stål AB and Vattenfall along with the Swedish Energy Agency started to build three pilot plants for direct reduction of iron ore using hydrogen. Known as the HYBRIT project[13], the concept uses optimally developed iron ore pellets for reduction by hydrogen gas in a direct reduction process shown in Fig 1
Reduction occurs in a solid state at a lower temperature than in the blast furnace and produces direct reduced sponge iron (DRI). H2 gas is produced by electrolyses using
renewable electricity, and oxygen is a byproduct. The reduction reactions are:
3Fe2O3(s) + H2(g) = 2Fe3O4(s) +H2O(g) (4) and
xFe3O4(s) + (4 x-3) H2(g) = 3FeO(s) + (4 x-3)H2O(g) (5) and
FexO(s) + H2(g) = xFe(s) + H2O(g) (6)
The University of Stavanger in Norway has investigated the chemical reaction occurring by adsorption of H2 gas on the iron oxide interface[14] (Fig 2). Studies have shown that the rate of iron ore reduction is higher
using pure H2 than when using Syngas (a mixture of CO and H2) at temperatures between 700–900°C[15]. It was also found that at temperatures higher than 900°C, the reaction rate decreases because of sintering and formation of a dense outer layer on the iron ore pellets[16]. The Activation Energy value for these reduction reactions vary from 11kJ mol-1 to 246kJ mol-1. There is a need for a more thorough investigation to evaluate the apparent activation energy required for the iron ore reduction reaction with pure H2
Advantages:
• High production flexibility
• Easy to start-stop
• Ability to feed DRI as HBI into a BFBOF system means existing conventional brownfield plants can be used while shaft furnace/EAF production is ramped up.
Disadvantages:
The process still requires iron ore pellets and producing them can cause significant emissions depending on the heat source of the pellet plant.
Pilot projects:
A HYBRIT pilot plant has been under development at the SSAB site in Oxelosund, Sweden and at Luleå, Sweden since 2018.
The Circored process (Fig 3) uses finely processed iron ore powders instead of pellets reducing iron ore fines directly without prior agglomeration. It operates at lower reduction temperatures than HYBRIT using pure H2 as the reducing gas. It is a three-stage process using fluidised beds at each stage. The first reduction stage is a circulating fluidised bed (CFB) to pre-heat the ore, the second is a partial reduction stage in a second fluidised bed (FB) reactor, and the third brings metallisation to 9395%.
The key steps in the Circored process are:
• Preheating of iron ore fines to approximately 850-900°C.
• Fast pre-reduction step in a further CFB at 630°C to achieve 65-75% metallisation.
• Final reduction in an FB at 650°C to 93-95% metallisation.
The advantages the Circored process are as follows:
• Circored-EAF route emits only about 50% of the CO2 emitted by the BF-BOF route.
• The use of ore fines over iron pellets removes pellet production, cutting costs and high CO2 emissions.
• Fluidised bed reactors have fewer internal sticking problems than shaft furnaces, achieving higher metallisation (approx. 95% to 90%).
Disadvantages:
• The process has the same H2 supply, electrolyser and operating cost problems as the shaft furnace method. Its electricity
supply must also be 100% green to achieve carbon neutrality.
• Higher investment than shaft furnaces for fluidised bed reactors.
Pilot project:
Outokumpu began production of an H2-DRI plant using the Circored process in Trinidad and Tobago in 1999 and reached 65t/h of HBI. However, today, the plant is owned by Arcelor Mittal and has been idle since 2015.
Fine iron ore or pellets are reduced using hydrogen plasma in a plasma steelmaking
reactor as illustrated in Fig 4. Carbon is added to the reactor to produce steel. Hydrogen plasma is H2 gas that has been heated or electrically charged to separate, or ionize it into its constituent hydrogen (H) atoms.
Advantages:
• The process removes the need for pre-processing iron ore and allows for lower reactor temperatures.
• This makes it commercially attractive.
Disadvantages:
The technology is at a very early stage of development, with an optimal process and full reactor design yet to be developed. Its commercial feasibility is yet to be proven.
Pilot project:
The Austrian steelmaker Voestalpine has built a small pilot hydrogen plasma reduction reactor at its Donawitz site.
There are two types of electrolytic processes: electrolysis and electrowinning[17] Electrolysis transforms iron ore at around 1550°C into liquid steel using electricity as a reductant as shown in Fig 5. In electrowinning, iron ore is ground into an ultrafine concentrate, leached and then the fluid reduced in an electrolyser at around 110°C. The resultant iron plates are melted in an EAF. ULCOLYSIS is the main electrolysis method, ULCOWIN the main electrowinning process.
Advantages:
Because these methods skip the upstream stages required in other production routes, such as producing coke or H2, as reducing agents, electrolytic processes have the potential to become the most energyefficient steelmaking methods, especially electrolysis.
Disadvantages:
Electrolysis of iron ore is still being tested in laboratories, suggesting a long and costly development phase. The process is also relatively inflexible compared to H2 direct reduced iron methods as it cannot be stopped easily.
Pilot project:
The EU’s ULCOS project, which involved many European steelmakers, including Arcelor Mittal, led to the development of
ULCOLYSIS and ULCOWIN. It demonstrated laboratory-scale high-temperature electrolysis for direct production of liquid steel.
5)
This process begins with the ultrafine grinding of low-grade iron ore to produce iron ore concentrate.
This is then reduced using hydrogen in a high-temperature ‘flash’ reactor which takes just a few seconds, directly producing steel, if carbon is added. The iron ore concentrate can also be pre-reduced at a lower temperature in a separate reactor before being added to the flash reactor as shown in Fig 6[17]
Advantages:
The direct reduction of iron ore to steel in one reactor, removing the need for ironmaking, sintering or palletisation, has significant cost and emission benefits. It also produces cleaner steel as the high
temperatures and fast reaction times ensure fewer impurities.
Disadvantages:
The technology is not well developed and is still at an experimental stage, with no largescale reactor tests yet conducted.
From a practical point of view, the iron ore must be ground to particles below 100 micrometres in diameter, requiring high energy intensity and increased plant maintenance.
The University of Utah (USA) has conducted proof-of-concept tests in laboratory reactors and is developing the process and reactor design for industrial use.
Three of the five processes described –suspension ironmaking, plasma direct steel production and electrolytic processing – are at an early stage of development. Their
technical and economic viability in largescale production is yet to be tested. Shaft furnace and fluidised bed reactors are at a more advanced stage of commercialisation.
Fig 7 compares the various approaches discussed.
European governments plan to invest 9 billion Euros to promote H2 production and the fund will focus on ‘green’ H2 [18]. This includes:
• Promotion of electrolysers,
• Promotion of the expanded use of hydrogen,
• Launching a ‘Hydrogen Technology 2030’ research offensive that includes the transport sector,
• Investment and operating grants for the production of hydrogen when switching to climate-friendly industrial processes,
• Strengthening infrastructure, and
• Expansion of international partnerships.
GLAMA Maschinenbau GmbH
Headquarters:
Hornstraße 19 D-45964 Gladbeck / Germany
Fon: +49 (0) 2043 9738 0
India’s hydrogen steelmaking India will need to start exploring deep decarbonization alternatives, including hydrogen, electrification and carbon capture, use and storage (CCUS). One of the major challenges is producing sufficient quantities of hydrogen at low enough cost. Fig 8 shows suitability of hydrogen production technologies for the future. In Fig 8, green represents a positive score, amber is mixed, and red is negative. Technology Readiness Levels (TRL), go from 1 (basic principles) to 9 (extensive implementation)[19]
The Indian Institute of Minerals and Materials Technology (IMMT) undertook a trial of hydrogen plasma technology during its previous round of research (2010–15), at a 5–10kg scale (IMMT, 2019). To achieve the next scale of trials (~100kg) would reportedly require around Rs 50 crore (US$ 6.17 M).
Tata Steel has trialled the HIsarna direct reduction process developed in Europe by Hoogovens, Corus and Tata Steel Europe. This uses powdered coal as the fuel and reductant. Ore fines are heated and partreduced to solid DRI in a cyclone converter furnace (CCF) located above a second vessel, the smelting reduction furnace (SRV). Powdered coal and oxygen are injected into the top vessel and the DRI produced falls into the SRV into which further coal and oxygen are injected to complete reduction to liquid iron and molten slag.
In 2018, Tata showed this technology could reduce ironmaking emissions versus the baseline conventional blast furnace by 60% from 2030. Figs 9 & 10 show the effects on emissions of adopting HIsarna.
Conclusion
Although hydrogen is one of the most abundant elements on earth, extracting from its compounds requires high energy. Currently, green hydrogen production costs are higher than traditional fossil fuel methods, and are dependent on the costs of renewable energy sources. These vary by region, and will fall as production capacity and subsidies for renewables and green hydrogen increase. H2 can be used as an alternative reductant to produce DRI that can be further processed into steel by melting in an EAF. It is important to note that a complete transition to a pure hydrogen-based steel production will not be needed to achieve the goal of a carbonneutral steel industry. �
References
[1] Sarkar, S.; Bhattacharya, R.; Roy, G.G.; Sen, P.K. Modelling MIDREX Based Process Configurations for Energy and Emission Analysis 2018. 89, 1700248. doi:10.1002/ srin.201700248.
[2] Fischedick, M.; Marzinkowski, J.;Winzer, P.;Weigel, M. Techno-economic evaluation of innovative steel production technologies. Journal of Cleaner Production 2014, 84, 563–58 doi:10.1016/j. jclepro.2014.05.063.
[3] Fuel Cells and Hydrogen Joint Undertaking. Hyrogen roadmap Europe. Technical report, Fuel Cells and Hydrogen Joint Undertaking, 2019. doi:10.2843/341510.
[4] The Future of Hydrogen. Technical Report June, International energy agency, 2019. doi:10.1787/1e0514c4-en.
[5] Julian Wettengel, “Thyssenkrupp tests use of hydrogen in steel production to bring down emissions”, Clean Energy Wire, Journalism for the Energy Transition, 12 Nov 2019.
direct reduction process through multiscale process modelling. Materials 2018, 11, 1–18. doi:10.3390/ma11071094.
[11] Alhumaizi, K.; Ajbar, A.; Soliman, M. Modelling the complex interactions between reformer and reduction furnace in a midrexbased iron plant. Canadian Journal of Chemical Engineering 2012, 90, 1120–1141. doi:10.1002/ cjce.20596.
[12] Keipi, T. Technology Development and Techno-Economic Analysis of Hydrogen Production by Thermal Decomposition of Methane Julkaisu 1519 • Publication 1519 Tampere 2017 Technology Development and Techno-Economic Analysis of Hydrogen Production by Thermal, 1519 ed.; Number 2017, Tampere University of technology, 2017; p. 127.
[13] Max Ahman, Olle Olsson, Valantin, Vogl, Bjorn Nyqvist, Aaron Maltias, Lars, J Nilsson, Lalle Hallding,, Kristina Scanberg, Mans Nilsson, Hydrogen steelmaking for a low-carbon economy, Stockholm Environment Institute.
[14] Teplov, O.A. Kinetics of the low-
[6] Philibert, C. Renewable Energy for Industry From Green Energy to Green Materials and Fuels; Technical report; International Energy Agency: Paris, France, 2017. Available online: https://webstore.iea.org/ search?q=renewable+energy+for (accessed on 5 January 2020).
[7] MIDREX. World direct reduction statistics. http://www.midrex.com/uploads/ documents/MDXSTATS20127-3-13Final.pdf, 2013. Accessed on 27.09.2019.
[8] Carlos and Martinis, A.D.P.E.; Jorge, B.; Lizcano. Energiron direct reduction ironmaking – Economical flexible, environmentally friendly. Steel Times International 2010, 34, 25–30.
[9] Anameric, B.; Kawatra, S.K. Properties and features of direct reduced iron. Mineral Processing and Extractive Metallurgy Review 2007, 28, 59–116. doi:10.1080/08827500600835576.
[10] Béchara, R.; Hamadeh, H.; Mirgaux, O.; Patisson, F. Optimization of the iron ore
temperature hydrogen reduction of magnetite concentrates. Russian Metall. (Metally) 2012, 2012, 8–21, doi:10.1134/S0036029512010132.
[15] Ranzani da Costa, A.; Wagner, D.; Patisson, F. Modelling a new, low CO2 emissions, hydrogen steelmaking process. J. Clean. Prod. 2013, 46, 27–35, doi:10.1016/J. JCLEPRO.2012.07.045.
[16] Chen, Z.; Dang, J.; Hu, X.; Yan, H. Reduction kinetics of hematite powder in hydrogen atmosphere at moderate temperatures. Metals 2018, 8, 751, doi:10.3390/met8100751
[17] Roland Berger, The future of steelmaking – How the European steel industry can achieve carbon neutrality.
[18] International Railway journal, Germany adopts € 9bn national Hydrogen Strategy.
[19] Will Hall, Thomas Spencer, Sachin Kumar, Towards a Low Carbon Steel SectorOverview of the Changing Market, Technology, and Policy Context for Indian Steel.
Although its technology is only in the early stages of development, Electra is passionate to go ‘above and beyond’ in the challenge to decarbonize, says Quoc Pham*, through its novel prototype of green iron; a feedstock to produce cleaner steel.
1. How are things going at ELECTRA? Is the steel industry keeping you busy?
We are in an exciting phase of our development at Electra as we scale from a lab prototype to a pilot plant that will be online by the end of the year. The steel industry does not keep us busy per se, as we are not selling any product yet, but our passion to urgently reduce steel carbon emissions and to improve the industry ESG in general is the main driver pushing us to go above and beyond.
2. What is your view on the current state of the global steel industry?
The industry is facing two main challenges/ opportunities: one is well publicized, that is the pressure to decarbonize, i.e. the green steel demand, and the other lesser-known one that is lurking in the background and that was brought to greater attention recently with the war in Ukraine, is the supply problem. The two challenges are working against each other as green steel tends to require higher grades of iron ore that are increasingly in shorter supply. Without an urgent solution, we could face a reckoning where steel could become much more expensive.
3. In which sector of the steel industry does ELECTRA conduct most of its business?
Electra is still in the early phases of developing technology to support new green steelmaking fed by Electra’s clean iron at 99.9% Fe content. Our presence and impacts will be in producing low-emissions ore-based metallics and in value creation from low-grade iron ores that are either not used today or are simply considered as waste.
4. Where in the world are you busiest at present?
We are busy scaling up our technology at
our facility in Boulder, Colorado. At the same time, we are exploring opportunities and feasibilities to build demonstration plants in various parts of the world where low-grade iron ores and/or ore wastes are available, especially in North America and in Australia.
especially in the expansion of the renewable energy infrastructure. Interestingly, both iron and aluminium are often found together in bauxite (alumina ore) and in iron ores.
7. What are your views on Industry 4.0 and steelmaking and how, if at all, is ELECTRA using it?
Industry 4.0 with its unprecedented speed and scale is a massive opportunity for improved efficiency, productivity and problem solving based on large-scale data and information. As a start-up that is not yet at scale, we keep a keen eye on scaleup and automation technologies and see Industry 4.0 as an important tool for us to build the steel industry of the future.
8. What were the greatest challenges in creating a green iron solution?
5. Can you discuss any major steel contracts you are currently working on?
We are exploring various opportunities with major steel consumers including Amazon and auto makers, as well as steelmakers such as Nucor; both Amazon and Nucor are investors in Electra.
6. Where does ELECTRA stand on the aluminium vs. steel argument? With the advances in electric vehicle commercialization, there is definitely a pressure to use lighter materials for vehicle construction to make room for the battery weight, which may favour aluminium. However, from a sustainability view, steel outperforms aluminium on cost, energy, carbon, and water usage. We see both metals as important to modern life,
Perhaps the greatest challenge we faced developing this new clean iron solution was the perception that it was not possible to dissolve iron ore in acidic solution, which is a prerequisite step prior to any attempt to perform low temperature iron electrowinning at 60°C. Electra has not only succeeded in this challenge by controlling the iron oxide phase, but also can remove deleterious impurities, such as phosphorus, which are damaging to steel quality.
9. In your dealings with steel producers, are you finding that they are looking to companies like ELECTRA to offer them solutions in terms of energy efficiency and sustainability? If so, what can you offer them?
For many steel producers, reducing scope 1, 2, and 3 GHG emissions and developing sustainable processes are key priorities. For those producers, Electra is not a potential competitor but a key enabler and partner, as it fills the supply gap that is widening while also enabling emissions reduction.
10. How quickly has the steel industry responded to ‘green politics’ in terms of making the production process more environmentally friendly and are they succeeding or fighting a losing battle?
Under pressure from public opinion, politics, and downstream stakeholders such as automotive companies, the steel industry has embraced the decarbonization challenge. Many companies have committed to reaching net-zero emissions by 2050. However, even though the goal may still be 30 years in the future, that is not much time for an industry that has assets with lifetimes exceeding 50 years and project planning horizons of 10-15 years. There is a reason why primary steel has been made pretty much the same way for the last 3,000 years.
11. Where does ELECTRA lead the field in terms of steel production technology?
We believe green steel is not just a matter of CO2 emissions, it is also about sustainability, and the two components go hand-in-hand. It is known that iron content in iron ores has decreased over the years and the high-grade ores will face severe supply challenges within less than 10 years. This is simply because we have used up all the lower cost, higher quality ores first. Hence a true green steel solution must also address the iron ore availability challenge. The unique advantage of Electra’s technology beside CO2 emissions is that sustainability component. Having the ability to deal with impurities, we are targeting the low-value ores that are not being used today, and lower grade ores currently considered waste that are abundantly available worldwide.
12. How do you view ELECTRA’s development over the short-tomedium term in relation to the global steel industry?
As a young start-up, our development is focused on scaling up while continuously de-risking and improving the technology. Our goal is to provide the steel industry with green and clean iron (or ore-based metallics) as a feedstock for making green steel to be evaluated in many markets that have a high appetite and high demand for green products such as electric vehicles.
13. China dominates global crude steel production and is accountable for almost half of what is produced. How should the industry react to this situation?
China has dominated global crude steel production when cost is the key driver and emissions are not a concern. However, acknowledging that climate change is a global problem that needs global solutions, many countries have started to implement the Carbon Border Adjustment Mechanism (CBAM) which not only prevents carbon leakage but also puts a price on emissions. This levels the playing field going forward. and provides a major incentive for lowemissions solutions.
14. Where do you see most innovation in terms of production technologies – primary, secondary, or more downstream?
We see innovation happening further upstream and further downstream than
Unlike coal that people can decide not to use, thereby making the entire industry obsolete, steel has very strong demand ahead because it is the backbone of a rapidly expanding green and sustainable economy. Hence, the demand is there, the challenge is whether we can supply it fast enough and with the right solution.
16. What exhibitions and conferences will ELECTRA be attending in over the next six months?
Electra is looking forward to attending CMU Energy Week; MIT Energy Summit, AISTech, Cleanpower 2023 and Ecosperity Week over the next six months.
17. Apart from strong coffee, what keeps you up at night?
Climate change is what keeps me up at night. Specifically, I have two worries:
First, how do we create a holistic solution that truly solves the decarbonization problem? Green steel can be made using hydrogen instead of coal, but where do we get the high-grade iron ore to do that? Beneficiating low-grade to high-grade ores consumes more energy and generates a lot of waste, which may cancel out sustainability gains from hydrogen. Second, how do we solve the transition to green steelmaking without wasting the potentially stranded assets estimated at $518Bn that also have large embodied-emissions? Manufacturing new green steel plants will inevitably generate more embodiedemissions even before we make any green steel.
18. If you possessed a superpower, how would you use it to improve the global steel industry?
primary and secondary steel manufacturing. Upstream innovation is driven by demand for clean iron, a key ingredient for making green steel from iron ores. Downstream innovation happens over a wide range of the value chain..
15. How optimistic are you for the steel industry going forward and what challenges face global producers in the short-to-medium term?
It is clear that we only have a small window of time to address the biggest challenge of mankind: climate change. It took us almost 200 years to optimize the blast furnace. We may have one tenth of that time to develop technology to address steel emissions. That is a daunting task because even if we had perfectly working technology today, scaling it will still take many decades. Just consider the roughly 7,000 terawatt-hours of renewable energy that is needed to fully electrify steelmaking. That is about twice the total annual electricity consumption of the entire US. If I could snap my fingers and make it so, I would create that renewable infrastructure to electrify steelmaking. �
Important: Appropriate Personal Protective Equipment (PPE) must be worn by anyone in proximity to molten metal.
IN the March issue of STI, I summarised the bloomery process to produce iron prior to the advent of the blast furnace. A solid mass of ‘spong’ iron – the bloom – is produced by heating iron ore in the presence of charcoal in a small shaft furnace built of clay. Sufficiently high temperatures are achieved for reduction by blowing air into the charge by means of bellows.
This labour-intensive means of producing just a few kilograms of iron at a time gave the product a high value, so finds of blooms during the excavation of ancient bloomery sites are very rare.
However, on the Weald of southern England, three such finds are recorded. The Cranbrook ‘bloom’ was discussed in the March 2023 issue of STI. We now look at two other finds, the Forewood bloom found near Crowhurst which, from the characteristics of the site, and the nearby find of a Roman coin, is believed to date from the early time of the Roman occupation (43AD to 410AD). The third
bloom, found at Nanny’s Croft, a site close to the Norman Castle of Arundel – built in 1070, may originate from Medieval times. Both blooms were examined by J A Smythe and are reported in The Transactions of the Newcomen Society of 1936 (17:1 pp197-203)*.
Unlike the previously described Cranbrook ‘bloom’ which had been forged to a billet, the Forewood bloom shows no evidence of consolidation by forging. The bloom weighs 1.24kg and is roundish in shape with a ‘knobbly’ surface. Composed largely of ferritic iron, it also contains considerable quantities of slag.
Metallographic examination shows the metallic part to be largely ferritic iron of hardness 100 VPN (Fig 1). Some areas have carburized to steel in which the iron carbide, cementite (Fe3C) is present in small quantities at ferrite grain boundaries, but more commonly precipitating as the interlamellar ferrite-carbide mixture,
pearlite. The quantity of pearlite in these areas indicates a carbon content of around 0.3w%, whereas analysis of the bulk sample indicates a carbon content of zero to 0.03w%. The iron is thus malleable and could be readily forged. In areas, the ferrite has nucleated on crystal planes forming a Widmanstatten structure, characteristic of a coarse-grained metal slowly cooled from a high temperature, but below the melting point (Fig 2).
The fact that this bloom was found among a large quantity of furnace slag suggests it was not deliberately discarded but rather lost when drawing out the furnace.
This smaller fragment of iron, weighing 305g, was reported as very hard to cut. VPN hardness results ranging from 770 to 480 suggest a quenched structure. Because of the high hardness, sections for examination could only be taken from surface regions and were cut using a
carbide wheel. Metallographic examination showed an inhomogeneous structure with highly carburised regions of carbon content rising to an estimated 1.6w%. Areas of free carbide (cementite) varied in close proximity to others of lower carbide content. Because all samples were taken from surface regions, they may not be representative of the core structure. The matrix material consisted of martensite, retained austenite and fine pearlite, indicating the iron had been quenched from the austenitic phase.
Some of the cementite had precipitated as thin plates in a Widmanstatten pattern (Fig 3). Sodium picrate was used to etch samples as this shows cementite as a dark phase, but is unable to reveal the needlelike structure of martensite in the matrix which is best revealed by etching with picric acid (Fig 4). Two distinct grain sizes are evident. Initially, a coarse-grained matrix, delineated by fragmented cementite, has arisen through holding at high temperature in the austenitic phase. Further cementite has precipitated within these grains (Fig 5). Subsequently, a much finer grained material has formed in which the grain boundaries
are again delineated by cementite, but as a continuous film this time. Small blocks of carbide are also seen within some grains (Fig 6).
The processing of the Nanny’s Croft bloom may be summarised as a high degree of carburisation taking place on the surface of the bloom during the smelting process, probably because of a prolonged hold in the furnace at an elevated temperature in excess of 1100°C. This would also lead to the formation of a coarse austenitic grain structure on which iron carbide nucleated at the grain boundaries and on crystal planes (Widmanstatten) during subsequent slow cooling within the furnace.
To account for the second generation of finer grains, the bloom must have been reheated again above 723°C, the ferrite –austenite transition temperature, where a fine-grained austenite was formed. Some cementite would also be taken back in solution, the quantity depending on the reheat temperature reached and the time at that temperature. On slow cooling once again, the cementite in solution precipitated out on the grain boundaries of the finer second-generation grains.
The presence of martensite in the final
structure indicates cooling must have been interrupted well before reaching the transition temperature of 723°C and the bloom quenched in water. This rapid cooling resulted in the formation of martensite and retained austenite in surface regions while the slower cooling rate in the core of the bloom would allow the formation of ferrite, pearlite and cementite, depending on the carbon composition of a particular region.
Whether this reheating took place in sequence within the same furnace or because of reheating a ‘hard’ bloom that could not be forged, cannot be determined. The continuous phase of cementite nucleated on the ferrite grain boundaries would render the steel extremely brittle and impossible to forge.
Whatever the process, recovery of the bloom to a malleable iron failed and the metal was discarded. �
*The micrographs are courtesy of The Transactions of the Newcomen Society of 1936 (17:1 pp197-203) Available for purchase on-line for £43.00 at https:// www.tandfonline.com/doi/abs/10.1179/ tns.1936.01