We must move urgently to decarbonize steelmaking. Producing DRI at scale needs the right process equipment.
US politicians oppose Nippon acquisition of US Steel.
The aerodynamic aspects of blast furnace performance.
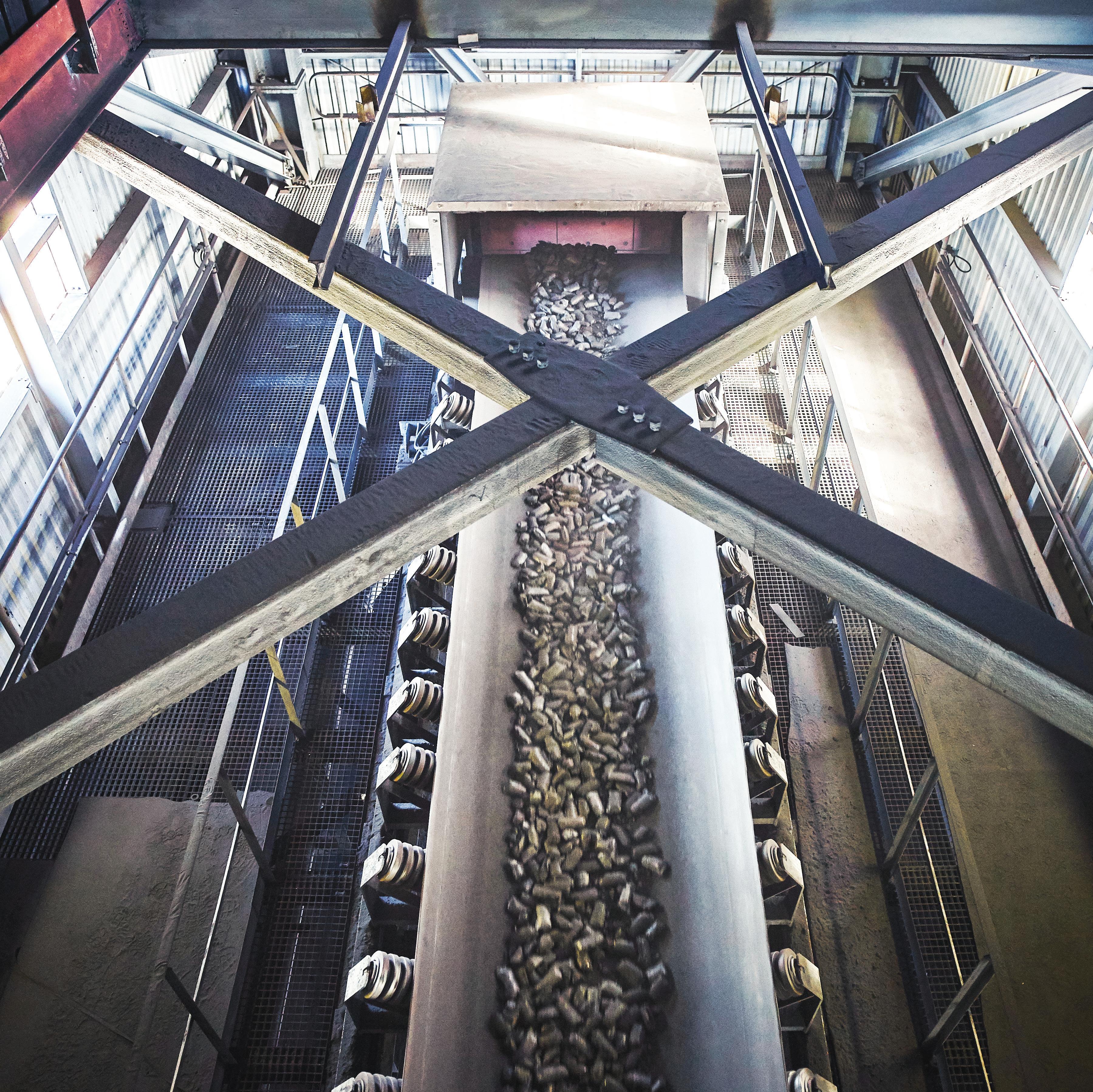
We must move urgently to decarbonize steelmaking. Producing DRI at scale needs the right process equipment.
US politicians oppose Nippon acquisition of US Steel.
The aerodynamic aspects of blast furnace performance.
Technologies turning steelmakers’ decarbonization goals into reality.
John Cockerill Industry is committed to help its steelmaking clients enhance product performance and effectively reduce emissions, all while preparing for the needs of tomorrow’s steels.
The JVD line is a genuine alternative to Electro- and Hot-Dip Galvanizing considerably reducing the cost of galvanized steel and providing multiple advantages when it comes to quality, speed and OPEX. Developed for ArcelorMittal with the help of our experts, John Cockerill is in charge of commercializing this unique technology worldwide.
High-performance Acid Regeneration supporting responsible steel making and the circular economy
John Cockerill Industry’s ARPs are providing the lowest emissions in the market. They come with smart plant control systems, provide waste energy recovery and drastically reduce pickling process plants’ fresh acid demands and waste streams in general.
Our E-SiTM equipment and processing lines are designed for the production of strong, ultrathin, lightweight, and high-quality Non-Grain Oriented (NGO) steel grades essential for the future of e-mobility.
matthewmoggridge@quartzltd.com
Things are never quite what they seem, ask Philip K Dick – although that’s impossible as he’s been dead since 1982. He did, however, write a lot about alternative universes. In The Man in the High Castle, for example, he imagined a world where Hitler had won the war, and there are many other examples in the many strange and thought-provoking novels written by the great man. You might have noticed of late that steel magazines and conferences have focused heavily on decarbonization. All the talk about hydrogen steelmaking and the importance of scrap and DRI and renewable energy might intimate that lots is being done and it won’t be long before the global steel industry is as green as the grass courts at Wimbledon. Well, a lot is being done – a hell of a lot – and there are many companies busy working on ultracutting-edge tech that will most certainly lead to fossil-free steelmaking, most notably SSAB with its HYBRIT initiative and H2 Green Steel’s planned hydrogen steelmaking facility in Boden, Northern Sweden. Stuff is happening elsewhere too, but Sweden is where it’s at and that’s why this year’s Future Steel Forum will be held in Stockholm (17-19 June).
In fact, you really should register and check out the programme, which is now online at https://www.futuresteelforum. com, but getting back to those alternative universes, this month’s Steel Times International carries a thought-provoking article by Global Steel Monitor, which is a real eye opener. While it is heartening to hear all the good news coming out of Sweden – and elsewhere in the world – it’s important to remember that while we’re all talking the talk about getting rid of blast furnaces and installing EAFs, we have many mountains still to climb. Dates like 2030 and 2050 are all very well, but of late 2060 (for when China’s steel industry might become fossil-free) and 2070 when India could make the grade, have entered the textual output of magazines like this one. In short, blast furnaces are still being relined and rebuilt and millions of dollars are being spent on them. The BF will be around for much longer than we all anticipated and in so many ways, their extended stay needs to be shortened. I’m beginning to think that 2080 or even 2090 might soon find their way on to the pages of this magazine as dates when we might expect our industry to be fossil-free.
The reliability of an entire production line or individual production areas can be increased by integrating our X-Pact ® Battery Storage units into the production facilities’ power supply.
Using either new batteries or second-life batteries with very large storage capacities, they provide emergency power or reactive power, offer an autonomous energy supply, support area networks, and optimize the supply using self-generated electricity.
Learn more about stationary battery e-storage as an integral part of your operational infrastructure. Find out more at www.sms-group.com/services/x-pact-battery-storage
Jindal Stainless has commenced the maiden usage of green hydrogen in its stainless-steel plant in Hisar, India. The fully automated plant utilizes an alkaline bipolar electrolyser, which has a capacity of 350 Nm3/ hr, guaranteeing an aroundthe-clock supply of green hydrogen using dedicated solar energy and storage. The facility aims at abating around 54kt of CO2 emissions over 20 years and is based on a longterm off-take agreement.
Source: Hydrogen Central, 5 March 2024.
Outokumpu, the sustainable stainless steelmaker, has been certified by Fair Pay Workplace (FPW) for its efforts to create sustainable fair pay across the company, which employs 8,500 people in almost 30 countries. Outokumpu is the first in the stainless steel
A deal supported by the UK government’s export credit agency has landed a £4.5 million export contract for structural steel firm Severfield. Headquartered in York, Severfield has five manufacturing sites in the UK and two in mainland Europe. Since securing the contract, Severfield has fabricated steel for this project at its Dalton site in North Yorkshire. The company has now shipped 1.9kt of structural steel to Guyana where it will be used by VAMED Engineering GmbH as it builds the new hospital in the capital, Georgetown.
Source: Gov.uk, 8 March 2024
industry – and one of the very few companies in Europe – to receive the official verification by FPW. “We have invested in pay equity for many years and have worked with FPW to review and independently verify the impact of our efforts to achieve true equal pay between genders,’’ said Johann Steiner, executive vice president for sustainability, people and communications at Outokumpu.
Source: Cision, 8 March 2024.
US-based Boston Metal has opened the first phase of its metals plant in Brazil's Minas Gerais state. “This first commercial deployment represents a beacon of progress in advancing sustainable metals production,” CEO Tadeu Carneiro said in a statement.“Our high-value metals business will expand rapidly and will support us as we scale our MOE [molten oxide electrolysis] platform to meet the growing global demand for green steel.”
Source: BN Americas, 8 March 2024
South Yorkshire steel firm Sheffield Forgemasters is taking on 14 apprentices to work in defence and civil nuclear manufacturing. The firm was bought by the UK Ministry of Defence (MoD) in 2021, and plays a key
ArcelorMittal Kryvyi Rih plans to increase the utilization of its iron and steel divisions by improving maritime logistics, as stated by the company’s CEO Mauro Longobardo in an interview with Delo.ua, a news-based website. ‘‘In 2024, we plan to increase production as we have good news about the opening of maritime logistics. I won’t go into details, but the Black Sea ports are available for our type of products – iron ore concentrate, pig iron and rolled metal,’’ he said. The company plans to maximize the capacity of its mining division and launch two BFs in the second quarter of this year, in April, to start the steel division.
Source: GMK Center, 8 March 2024
role in the national nuclear submarine supply chain. It said apprentices would work in one of the ‘most advanced engineering facilities of its kind’, gaining a qualification while getting paid.
The company said it wanted ‘the most capable and committed individuals’.
Source: BBC, 9 March 2024
Czech steelmaker Liberty Ostrava will cut costs by $218.4 million and reduce production by more than half in a restructuring plan aimed at restarting its idled blast furnace, according to local media reports. A regional court spokesman said that the company had pledged to deliver a completed restructuring plan to creditors by early March, after the court upheld a moratorium on debt it owed.
Source: Nasdaq, 11 March 2024
In the realm of metallurgy, there are no compromises. And neither are our transport solutions. No matter the challenge, we deliver the optimal solution. Our products showcase their full strength even under the toughest conditions, ensuring your production runs around the clock. www.tii-kamag.com
A towering steel monolith has appeared on a hill in Wales' Hay-on-Wye region, with its origins remaining unknown. Similar structures discovered in Utah and California in 2020 were later revealed to be the handiwork of an artist group named 'The Most Famous Artist', hailing from New Mexico. The global monolith phenomenon also reached Romania and Ukraine in late 2020, with other UK sightings closer to Wales, such as the Isle of Wight and the Merry Maidens stone circle in Cornwall, England.
Source: Money Control, 12 March 2024.
Swedish steelmaker SSAB has confirmed that it is in discussions with Tata Steel
India’s JSW Steel is set to launch a new blast furnace at its Dolvi steel plant in Maharashtra with a production capacity of 4.5Mt/ yr in 2026. Construction of the blast furnace is expected to be completed in March 2026. The steelmaker’s steel production capacity is currently 10Mt/ yr, with a blast furnace and an electric arc furnace in operation. The new unit will increase production by 45%.
Source: GMK Center, 13 March 2024.
concerning a potential acquisition of Tata Steel Europe’s IJmuiden steel mill and related downstream assets. SSAB has participated in several different discussions concerning consolidations in the European steel industry. The discussions with Tata are on-going but no decisions have yet been made.
Source: Army Technology, 16 March 2024
Sustainable energy developer Orsted will be offered the first batch of lower-emission steel from Dillinger, subject to availability and commercial terms and conditions. The metal plates form a part of the offshore wind monopile foundations and are intended to be used for future projects. The reduction of the processrelated carbon emissions from production is expected to be around 55-60 % compared to conventional heavy plate steel manufacture, Orsted said.
Source: ReNews, 13 March 2024.
Tata Steel Netherlands has scrapped its plan to cut 800 jobs, the trade union FNV stated, after meeting with the company. All employees at risk of layoffs will hear from the company that they will remain employed by Tata Steel. Some may have to move to a different job within the company, the union said. The company previously announced in November that it was going to cut 800 office jobs in the human resources, finance, and purchasing departments and outsource office work.
Source: NL Times, 14 March 2024.
Steelmaker Thyssenkrupp and research organization Fraunhofer have partnered to develop solid oxide electrolyzer cell (SOEC) technology for large-scale
hydrogen production.
According to reports, the high energy efficiency of SOEC technology will primarily benefit industries where industrial waste heat is generated during production as its use significantly reduces electricity consumption. Waste heat is generated in the production of green steel, ammonia, methanol, fertilizers and energy storage, among other things.
Source: Energy Central, 15 March 2024
ArcelorMittal Kryvyi Rih has received approval from the Environmental Protection and Natural Resources of Ukraine (MEPR) for a new tailings dump. The planned activity envisages the construction of a tailings storage facility due to the fact that the existing facilities have reached ‘the limits of economic feasibility and physical possibility of their expansion.’
Source: GMK Center, 15 March 2024
Spain has officially launched the construction of a pilot hydrogen production plant for industrial needs as part of the public-private project Hydrogen Hub Asturias (H2Asturias) led by global steelmaker ArcelorMittal. The facility, called GasLab, will be built on the site of the ArcelorMittal plant in Gijon. The unit will process all types of industrial gases, which expands the range of research that will be conducted on hydrogen recovery processes.
Source: GMK Center, 18 March 2024.
Apologies to Amir Badiee of the University of Lincoln's School of Engineering in the UK. Mr. Badiee's name was spelt incorrectly in the introduction to an article titled Challenges and strategies which appeared in the March 2024 edition of Steel Times International.
Italian plant builder Tenova has secured a contract to furnish an experimental direct reduction plant commissioned by Nippon Steel Corporation.
Source: ChemAnalyst News, 20 March 2024.
Brazil’s industry ministry has launched a number of investigations into the alleged dumping of industrial products by China. At the request of industry bodies, the ministry has in the past six months opened at least half a dozen probes on products ranging from metal sheets and pre-painted steel to chemicals and tyres. Developed markets have started taking extensive measures against imports from China, with the EU launching an anti-subsidy probe into Chinese EVs and the Biden administration recently raising security concerns over China’s market growth.
Source: The Financial Times, 16 March 2024.
ArcelorMittal has patented a hot-rolled plate or forging of an austenitic steel resistant to relaxation cracking. The composition includes specific percentages of elements including copper, manganese, and silicon, ensuring high performance and durability
Gerdau, Brazil’s largest steel producer, has announced the sale of its operations in Colombia and the Dominican Republic with the aim of focusing on an asset optimization strategy and long-term growth. Gerdau will invest in projects designed to increase the competitiveness of its operations in other, more relevant markets and expand its presence in long, flat, and special steel in the Americas, sharing value with its clients, investors, and other stakeholders, it said in a public statement.
Source: American Recycler, 19 March 2024.
Swedish state-owned utility Vattenfall faces accusations of breaking contracts and the law with its decision not to allocate a 500MW grid connection in the Luleå area to H2 Green Steel and its flagship Boden project – a move that could halve its expected production capacity scheduled for this decade. H2 Green Steel had in 2021 reserved 2.6GW of new power from Vattenfall, with 1.75GW already allocated to the project since then. However, in January, Vattenfall reportedly opted to allocate 500MW of power in Luleå to the Hybrit green steel project–of which it is a member of the development consortium–rather than H2 Green Steel.
Source: Hydrogen Insight, 19 March 2024
in industrial applications. The patent covers reactor vessels, forgings, or pipelines made from the hot-rolled plate or forging as described in the claims.
Source: Mining Technology, 19 March 2024.
Pakistan's steel producers have sounded the alarm on the resurgence of large-scale smuggling, mis-declaration, and under-invoicing of steel primarily from Iran. In a letter addressed to the federal finance minister, the Pakistan Association of Large Steel Producers (PALSP) has highlighted how illicit activities are ‘systematically crippling the local steel sector.’ “Our steel industry is in a fight for survival amidst significant challenges such as currency depreciation, soaring financial costs, and escalating input expenses,” PALSP stated.
Source: Pakistan Today, 20 March 2024.
We understand how it is important to efficiently extract and process precious metals and minerals.
You save valuable resources while keeping your employees and the environment safe.
Improve your processes with our comprehensive portfolio of measuring instruments, solutions and services:
Liquiline CM44 and CPS11E:
Versatile transmitter and Memosens
pH sensors ensure reliable measurement and safe calibration in the lab.
FieldPort SWA50:
Intelligent Bluetooth or WirelessHART adapter for the easy connection of all HART field devices to the Netilion Cloud via Edge Devices.
Do you want to learn more?
www.de.endress.com/primaries-metal
Cerabar PMC71B:
Absolute and gauge pressure transmitter combining measurement accuracy with IIoT functionalities.
Tenova, solutions provider for the metals and the mining industries, thanks to the project SafeForPorts, has won a call for proposals issued by the Istituto Italiano di Tecnologia (IIT) under the banner of RAISE (Robotics and AI for Socio-economic Empowerment), implemented under the National Recovery and Resilience Plan, Mission 4, funded by the European Union – NextGenerationEU.
SafeForPorts is a new project tasked with creating smart and sustainable ports by implementing key Industry 4.0 technologies. It aims to revolutionize the safety of machine operators improving the efficiency of port operations by offering an innovative solution that integrates training on one side and assisted maintenance on the other to address critical needs in port areas.
Through the use of a Virtual Reality simulator, the project will develop a comprehensive solution for the remote training of operators and on-field assistance for the operation and maintenance of bucket ship unloaders (a rail-mounted mobile unit typically installed on port docks). The VR simulator will be accessible to operators via headsets, while remote assistance will be enhanced through the processing of structured photographic material using Computer Vision algorithms.
Designed and developed in Tenova’s virtual laboratory in Genoa, the VR prototype will include a workstation cabin with handheld controls simulating the 3D operational environment of the machine. The final system will advance the labo-
ratory model by developing interactive elements and refining operational logic to achieve full virtual operational capability.
The project falls within RAISE’s activities, which include the implementation of robotics and AI systems for the management of port traffic, contributing to the advancement of intelligent solutions in the maritime industry. It is being developed in partnership with Prosoft Intesys and InformAmuse as technology providers.
Silvio Leoni, executive vice-president of Tenova’s material handling business unit commented: “SafeForPorts holds strategic significance for
Together with Shougang Zhixin Electromagnetic, a Chinese steelmaker, Fives, an international engineering group, produced the first electrical steel product for electric vehicle motors at its Zhixin plant. The project, claims Fives, demonstrates its commitment to provide dedicated solutions for demanding steel production.
Shougang built a new annealing and pickling line (APL) to produce high-grade, non-grain oriented (NGO) electrical steel for the booming e-vehicle market. The new line required thermal technology that could keep up with its high capacity of 650kt/yr.
Fives designed and supplied an annealing furnace that featured advanced heating technology and a flexible cooling system to meet the challenging thermal requirements for electrical steel. The furnace included dedicated models specifically designed for electrical steel to achieve metallurgical control, oxygen control, high temperature thermal technology, and an emission reduction system.
The engineering and manufacturing of the main equipment were provided from China, while the burners, automation, and process instrumentation were delivered from France.
“We had a very challenging schedule, but we managed to produce the first commercial coil on 1 February 2024, just 16 months after the contract enforcement,” said Benoit Crunelle, project manager at Fives Stein Metallurgical Technology, Shanghai, a Fives subsidiary in China. “This success is due to our rigorous planning, well in advance of manufacture and delivery, regular and transparent communication with the client and the good working relationship between both teams,” he added.
For further details, log on to www.fives.com
Tenova, not just in terms of business, but also for actively contributing to the development of new technologies and the design of increasingly intelligent, optimized processes for smart and sustainable ports. This project testifies our commitment to prioritizing and enhancing a core value at Tenova: safety. As we embark on this initiative, we recognize it as a catalyst for innovation and a cornerstone toward shaping the future with new possibilities and perspectives.”
For further details, log on to www.tenova.com
Haver & Boecker Niagara has opened a new service and support facility, Haver & Boecker Andina Sucursal Peruana, located in Arequipa, Peru. The company hopes the facility will amplify its serviceability to mining operations by
Industrial machinery company Metso’s crushing and screening offering is expanding with a new software application named Metso Remote IC. The new Metso Remote IC is used for remote control and monitoring of the crushing and screening process, and it connects wirelessly all the Lokotrack® crushers and screens at the site.
With the Metso Remote IC app, the operator can view all the Lokotrack train machines and their main process parameters using a single dashboard. The feeder and crusher settings can be adjusted from the excavator cabin, and the overall visibility of the process allows the operator to adjust the feeding for an optimal production level, says Metso. In problem situations, the Remote IC automatically stops the feeder, thus preventing overloading. It also instantly alerts and provides a reason for the stoppage, which the company claims makes it quicker and easier to get back to operation. With a lower overflow risk, the process can be run closer to maximum capacity.
“One of the key features of the Remote IC is that there is no need for the operator to exit the excavator cabin to adjust the crushers or to stop the feeder in an overflow situation,” com-
increasing access to supply parts and equipment service. The facility provides service and support for mining operations throughout the region through diagnostics, equipment refurbishment, parts stocking and more. In addition to servicing existing equipment and supplying new parts, Haver & Boecker Niagara will both produce and repair exciters here, with a dedicated service shop
mented Toni Peltomäki, director, automation, at Metso’s Aggregates business area. “The ability to control and monitor the crushing and screening process from a single application has a significant impact on safety and eventually process productivity, since unnecessary process stops can be avoided.”
“We are constantly developing our products and digital tools to help our customers improve their productivity. Remote IC not only increases the productivity and safety of the plant, but it can also positively impact the employees’ experience and help attract a new skilled workforce,” said Renaud Lapointe, senior vice president at Metso’s Aggregates business area.
The Metso Remote IC app can be used on an Android tablet or mobile phone. It is available for all new Lokotrack models and can also be installed as a retrofit to all models that have the latest Metso Metrics installed. Metso Metrics is a cloud-based service for real-time performance information, maintenance planning and fleet management that works as a remote monitoring tool off-site.
For further details, log on to www.metso.com
specifically for exciters.
“Haver & Boecker Niagara opened its first South American subsidiary more than 50 years ago in response to the country’s booming aggregates and mining industry,” said Roberto Montiglio, managing director of Haver & Boecker Niagara’s Andean Region. “We have only seen the industry continue to thrive, which is why we are offering dedicated service and support facilities throughout the country, including the Arequipa operation. This allows us to better serve our customers, all while continuing to provide new and innovative solutions to the market.”
“At Haver & Boecker Niagara, we pride ourselves in the unmatched quality service and support we offer to our customers – no matter their brand of equipment,” Montiglio said. “We make an effort not just to provide a service but be a partner to our customers by offering the service and the support they need to increase production and equipment longevity. With the addition of the Arequipa facility in the heart of Peru’s mining region, we can do just that – provide easier access to on-site support for our customers.”
For further details, log on to www.haverniagara.com
In late 2023, Chiquita Guatemala (Chiquita) received the first two of three Konecranes reach stackers for their Terminal Ferroviaria in Puerto Barrios. With one more scheduled for delivery in 2024, all three will help raise Chiquita’s banana business to the next level, claims Konecranes.
Chiquita bananas are famous worldwide, and Puerto Barrios is an important regional distribution hub. With high volumes and tight time constraints to ensure freshness, Chiquita needs modern, reliable container handling that can operate almost 24/7.
“We are leaders in the tropical fruit market. To maintain our position, we need the best quayside equipment available. Konecranes offered us reach stackers that are already improving our efficiency, simplifying our processes, and lowering our costs. Once all three are on-site, their high performance and advanced systems will further streamline our operations,” said Ramses Lobo Ortiz, regional manager logistics, Chiquita.
“These reach stackers represent a new stage in our partnership with Chiquita as they employ the latest in lifting technology. State-of-the-art digital features will help Chiquita maintain their strong position in a highly competitive industry,” commented Paco Pruden, product support manager Americas, Lift Trucks, Konecranes.
The first two reach stackers, a Konecranes SMV 4632 TC5 and a Konecranes SMV 4632 TC6H are already on-site. The third one, currently on its way, is a Konecranes Liftace 4532 TCE5. All three vehicles are Smart Connected Lift Trucks on which TRUCONNECT® Remote Monitoring collects usage and functional diagnostics to improve safety, optimize performance and maintenance, and reduce environmental impact. Tyre Pressure Monitoring provides alerts for pressure changes, and the SOLAS-compliant Konecranes Static Weighing System eliminates the need for a separate scale. All measurement data is transmitted directly from the reach stackers to the yourKONECRANES customer portal.
For further details, log on to www.konecranes.com
Italy, Germany, Sweden, Austria, France, The Netherlands, UK, Spain, Turkey, USA, Brazil, Thailand, India, China, Japan
Danieli Headquarters in Buttrio, Udine, Italy
www.danieli.com
MIDA–QLP and QSP–DUE are the winning Danieli direct-rolling technologies for the most competitive production of long and flat green-steel products.
They are the result of the research and continuous improvement profused over 20 years, along with multi-million dollars of investment.
Their unmatched performances have fueled their success worldwide, thanks to lower resource consumption and carbon emissions, unbeaten OpEx, and outstanding product quality.
So, top technology becomes copied technology, the shortest route for competitors that, abandoning their solutions, now try to imitate MIDA–QLP and QSP–DUE Equipment and layout may be copied, but experts know that details make the difference.
Automation and process solutions are not easy to copy, and this will be the experience of anyone trusting in those imitations.
The competitive advantage for our customers, obtained by field results, is the best defense for our technology – more than court rulings protecting our patents.
Danieli offers the best guarantees for speedy learning curves, steady performances, and now Digital Plants with no men on the floor. Buy the Original.
BENEDETTI CHAIRMAN OF THE BOARD OF DIRECTORSThis year’s AISTech promises the usual line-up of optimizing technologies, innovative systems, and automation solutions in the exhibition hall, but all with an edge of sustainability, and digitalization. As is apt for the so-named ‘Discovery City’, read below for more details on what to encounter this May.
KOCKS, a supplier of solutions for long products rolling mills, has partnered with laser measurement provider LAP to develop the 4D Eagle S Measuring Gauge, which combines profile measurement capabilities with surface inspection in one system. The gauge uses advanced laser light sectioning technology to measure the complete profile of the long products and accurately detect and classify various rolling defects.
The associated SMART CORE X software encompasses all the necessary features to meet requirements, including easy-toaccess profile data, 3D imaging of defects, detection of periodic defects, export capabilities, and individual statistics over a user-friendly surface. OPC-UA allows access to all relevant data through a modern interface. Data-driven insights can be gained from this, which can ultimately be used to tap into a wide range of potential in everyday rolling mill operations. The team in the rolling mill benefits from transparency and the opportunity to optimize process and product quality sustainably.
Two 4D EAGLE S systems have been successfully implemented in the mill lines of a German steel producer, enabling quality assurance for round long products in a wide diameter range.
KOCKS will be exhibiting at booth #2816
Global technology leader ABB will be presenting safer and smarter solutions and innovative products and services for more efficient operations across the metals industry
One recent solution that the company will highlight at its booth is ABB Ability™ Smart Melt Shop, which combines real-time crane and ladle tracking, automatic and optimized crane scheduling, and heat loss prediction. Proven benefits from projects over the last year
include raising casting speeds by 4-5%, 5°C less arcing per heat, reduced delays, less material rejection and increased human safety.
ABB and metals industry supplier Tenova will also receive the 2024 AIST Charles W. Briggs Award for the collaborative work entitled ‘Tenova Large Electric Arc Furnace Equipped with ABB Electromagnetic Stirrer as a Model for the Efficient and Reliable Transition of the Steel Industry’. This comes as ABB’s ArcSave® electromagnetic stirrer (EMS) can be deployed in the melt shop to create equilibrium in the melt, which the company claims enables more steel to be made, using fewer resources.
ABB will be exhibiting at booth #1527
Polytec, an Italian company that has been developing automation systems and robotics for critical industrial processes for over 30 years, will be showcasing its cooling bed sampling robot, PolyTEST. PolyTEST is a fully automated robot with an artificial vision system for the complete cutting of steel samples from bars (and other products) positioned on a cooling bed. The main components of the system include a six-axis industrial robotic arm with a custom-designed tool to perform the sample cutting and moving, and an artificial vision system, which determines the best position to collect the sample and communicates it to the robot that executes the movement. Highlights, claims Polytec, are improved system reliability, quality increase, and productivity improvement.
Polytec will be exhibiting at booth #2415
Tenova, a leading company specialized in sustainable solutions for the metals and mining industries, will be featuring its recent contract with steelmaker Ternium, for the delivery of sustainable technology for the steelmaker’s new state-of-the-art steel mill in Pesquería, Mexico.
Tenova’s scope of work includes a direct reduction (DR) plant with integrated material handling system (MH) complete with a stockyard/train unloading system, an electric arc furnace (EAF) equipped with Consteel® and electromagnetic stirrer Consteerrer®, two ladle furnaces (LF), and a fume treatment plant that guarantees a total production capacity of 2.6Mt of steel for the automotive sector.
The MH system will be designed to
feed the DR plant with the specified flow and quality of iron ore and will also provide handling and storage for DRI production. It will also ensure safe and reliable operations, claims Tenova, including advanced dedusting equipment specifically designed to minimize pollution and drastically reduce impact on the environment.
The DR plant, based on the cutting-edge ENERGIRON® Direct Reduction technology jointly developed by Tenova and Danieli, will directly charge the Consteel® EAF with hot DRI, thanks to the Hytemp® pneumatic transport system.
Tenova will be exhibiting at booth #1929
Multi energy company TotalEnergies will present its ROLKLEEN range, a lubricant engineered to elevate the cold rolling process.
Products from the ROLKLEEN range can be used with reverse osmosis and deionizing water. According to TotalEnergies, its multiple benefits extend from energy savings to production levels while delivering superior strip quality. ROLKLEEN products utilize an
oxidation-resistant lubricant, minimizing the formation of sticky by-products and ensuring a clean surface. The ROLKLEEN range includes rust protection, which ensures no residue is left after degreasing, and protects against corrosion while matching environmental standards.
TotalEnergies will be exhibiting at booth #3203
Sarclad will be launching the Contamination Monitoring System (CMS) for strip coating lines, which the company claims will revolutionise capability in the field. The CMS utilises Laser Induced Breakdown Spectroscopy (LIBS) to provide strip producers and line manufacturers with an
Nel Hydrogen, a global, dedicated hydrogen company, delivering optimal solutions to produce, store, and distribute hydrogen from renewable energy, will be showcasing the PSM; a proton exchange membrane (PEM)-based water electrolyser module that integrates eight 1.25 MW cell stacks to generate hydrogen from deionized (DI) water and four DC electrical power inputs. The PSM includes the PEM cell stacks, associated piping, DC power connections, and related critical monitoring instrumentation.
The PSM employs a modular approach to hydrogen production designed to offer guaranteed, repeatable performance per module to provide a cost-effective solution for hydrogen production at all scales.
automated, non-contact, online measure of very low levels of iron fines and carbon contamination on coils after the cleaning section on the galvanising line.
It is the first continuous monitor of strip cleanliness providing real time data with unprecedented precision that distinguishes
between oil and iron fines contamination, says Sarclad. Introduced under licence from CRM, the CMS is designed to be positioned post cleaning and pre-furnace. The system has been designed in a compact format to ensure that it can be fitted to any line, either new build or retrofit to existing lines. The sensor can be fitted to an automated and integrated traverse to allow measurement at various points across the width of the strip.
Sarclad will be exhibiting at booth #1855
Dassault Systèmes provides businesses and people with collaborative 3D virtual environments to imagine sustainable innovations. A solution that Dassault Systèmes will be exhibiting is DELMIA, which delivers solutions to address the most challenging situations metals manufacturers experience today. It connects the virtual
and real worlds to empower customers worldwide to collaborate, model, optimize, and execute supply chains, manufacturing, logistics, and service to achieve strategic business results.
Dassault Systèmes will be exhibiting at booth #1422
Nel Hydrogen will be exhibiting at booth #1729
For more than 60 years FrigorTec has been manufacturing crane air conditioning for metal production, container terminals, coking plants, mining, oil and gas, paper production, chemical plants, cement plants, offshore applications, and power plants. This May, the company will be exhibiting its CRANEFRIGOR™ Crane air conditioning units, (heating - cooling - dehumidifying), electronic rooms, and control cabinets for safe and optimal working conditions. In
addition, further details on FrigorTec’s filter systems will be available – which ensure the oxygen supply and reduce the dust load in the conditioned room. The units, which have been tested worldwide, are available in many installation variants and performance levels.
FrigorTec will be exhibiting at booth #2825
The Systems Group’s mission is to provide engineered solutions for a safer, more productive steel industry, with divisions including Systems Plant Services, Systems Contracting, Systems Spray-Cooled, Systems Fab & Machine, Systems Engineering, and Systems Clean Air. The company will be showcasing its latest product offering, Systems Big Ass Strainers (BASS), which is designed to optimize water filtration. With a maximum flow rate of 5600 GPM, the Systems Group’s BASS aims to ensure optimal protection for mill process equipment. Its design incorporates two quad seal rings, providing four heavyduty seal points to guarantee against secure filters from being displaced by reverse water flow through the outlet. The BASS is also equipped with an electric davit crane for assisted cover opening and closing. With a pressure rating of 150 PSI and manufactured in the USA, it integrates into any process water filtration system.
The Systems Group will be exhibiting at booth #2329
EMG, supplier of automation and control systems, will be featuring five of its solutions at its booth this May. The technologies include iTiM strip thickness measurement with X-ray, isotope, and laser technology, which incorporates X-ray, isotope, and laser technologies, and the iCAM® for strip and slit strip width measurement, which caters to a wide range of widths, from narrow to wide strips, and is particularly adept at measuring slit strips post-slitting process. EMG will also highlight its new EMG SORM® system,
which the company claims introduces a new era in online roughness measurement. Utilizing a confocal chromatic measuring principle, it measures surface micro profiles at production speed without mechanical contact, offering real-time data on roughness parameters. This innovation, says EMG, allows for early detection and correction of roughness deviations, enhancing the efficiency and quality of the manufacturing process.
EMG will be exhibiting at booth #2161
AIC Group is a global system integrator that designs, manufactures, and commissions plants worldwide, providing advanced and tailored automation plus mechatronics solutions for the metals industry. This May, AIC’s Robotics department will present tailor-made solutions for the metals industry to ensure an advanced process in the processing line, improving the oftenharsh conditions customers operate in. AIC’s robots can be floor-mounted or ceiling-mounted and can be integrated
into new layouts or in existing ones. An anthropomorphic AIC robot typically has six degrees of freedom and a wrist load of up to 40 kg.
AIC offers anthropomorphic robots, AI and 3D vision systems, control units and safety PLC, tags, QR readers and marking tools, metal support and welding machines, and all tools required for mechatronic applications.
AIC will be exhibiting at booth #2215
Political scrutiny continues from both sides in the US, as Nippon Steel’s acquisition of US Steel enters into the clearance stage.
By Manik Mehta*THE United Steelworkers (USW) union’s opposition against the Nippon Steel takeover bid of Pittsburgh-based US Steel is now followed by politicians opposing Nippon Steel’s move; Nippon Steel has quoted a purchase price of $14.9 billion which is roughly twice the offer made by US rival steelmaker Cleveland-Cliffs.
“It’s not just Nippon’s attractive price offer. Remember, this is an election year and both president Joe Biden and his potential rival Donald Trump (he has, as of writing this update, not yet been officially nominated though he is leading over the other Republican candidates), are reacting to Nippon’s takeover of US Steel,” explained Joseph Marciano, a New York-based analyst. “Then there is the national security element … and no candidate would like to appear less nationalistic when it comes to protecting American interests.”
In an otherwise free economy, inherent with opportunities for foreign companies investing in the US corporate sector, nationalism is today on a high pitch, and politicians seem to be outdoing each other in opposing a takeover by a foreign company, although Nippon Steel is based in
an allied country.
JD Vance, a Republican senator, argued that it was ‘not just this transaction I’m worried about, but that this could be a precedent’, fearing that US Steel would be less responsible to US national security needs and that this would allow Nippon Steel to avoid US tariffs on imported steel through the purchase. He has called for a blanket ban on any foreign buyer of a US company that benefitted from the tariffs. Foreign companies, keen to access the US market, should engage in greenfield investments.
Former president Donald Trump has vowed to block Nippon Steel’s acquisition of US Steel if he becomes president.
“I would block it instantaneously. Absolutely,” Trump said after meeting the president of the Teamsters labour union, which represents workers in the transportation industry. “We saved the steel industry. Now, US Steel is being bought by Japan. So terrible.”
Biden’s election strategists face pressure with the growing number of Republicans opposing the Nippon Steel acquisition. Biden has in the past underlined the
importance of US alliances and has welcomed foreign investment; nevertheless, he knows Nippon’s acquisition would anger the USW which had endorsed Biden’s 2020 candidacy and wields a constituency of over a million members, with many thousands in swing states Ohio, Pennsylvania, Michigan, Wisconsin, etc.
While foreign investments for new US factories were welcomed months back, Nippon Steel’s venture has rung alarm bells among politicians over security issues. Foreign investors can generally benefit from the administration’s massive infrastructure allocations of roughly $3.5 trillion, combined with subsidies.
Experts argue that tariffs on imported steel would draw foreign companies to invest in production in the US, reminding that Japanese carmakers invested in the US in the past; former president Trump in 2018 imposed 25% tariffs on imported steel and Biden continued with the tariffs, though he reached agreement with the EU replacing tariffs on European products with quotas, extending the arrangement until 2025. US Steel’s chief executive David Burritt had also remarked that his company benefitted
Reduced carbon footprint using hydrogen or carbon neutral fuels and equipment upgrades.
Emissions reduction solutions to help customers achieve near-zero methane targets.
Energy optimization to minimize lifecycle costs.
SoLoNOx™ combustion system to reduce NOx emissions.
For more information, visit us at www.solarturbines.com, call +1-619-544-5352 or email infocorp@solarturbines.com
from ‘accelerating de-globalization’; other countries also reviewed their risks of growing interdependence.
Meanwhile, both Nippon Steel and US Steel, trying to allay the doubts in the US, said that they would submit their agreement to the Committee on Foreign Investment in the US (COFIUS) which is chaired by treasury secretary Janet L. Yellen, to examine if the deal would affect any national security interest.
However, the COFIUS scrutiny, guarded and discussed by responsible members of the agency, is a protracted process and the wheels move slowly.
Some critics object to national interests being put in jeopardy but others argue that the US military uses roughly 3% of total domestic steel production. According to Pentagon data, modern fighter systems today consume less steel than in the past, using instead more materials such as titanium and aluminium.
Besides, the Defense Department does not directly purchase any materials from US Steel, though the latter has said that some customers, with defense and commercial businesses, may use the company’s raw steel for defense hardware.
COFIUS has taken controversial stands on deals with Chinese companies though Japan is considered a US ally. Also, Nippon Steel is known to have some stakes in eight US steel companies.
Nippon Steel representatives have been
talking to US lawmakers to allay their concerns, promising that US Steel would remain in Pittsburgh, with its name intact, and they would honour the steelworkers’ collective bargaining agreement. Nippon Steel, operating 11 blast furnaces, is expected to improve the efficiency of US Steel’s furnaces and also reduce the carbon footprint.
US Steel had spurned the nearly $8 billion offer made by Cleveland-Cliffs which, as details now emerge, had come close to winning over US Steel.
Nippon Steel, which eventually won the bid, was not, apparently, interested in other plants in the region but in US Steel’s minimills in Arkansas and the latter’s iron-ore
mining operations in Minnesota.
Nippon originally estimated the value of US Steel’s modern electric arc-furnace plants and the mines at $9.2 billion, according to regulatory filings; in late September, it indicated that it had bid at $9.5 billion. Its nearly $15 billion offer, made two months later, was finally accepted. But US Steel had some concerns about Nippon Steel; CEO David Burritt had called, two days before the deal’s finalization, Nippon’s executive vice president Takahiro Mori, to get assurance that Nippon would work with COFIUS. Nippon finally agreed on ‘all actions required’ to obtain COFIUS’ clearance, if it did not hurt its business.
Indeed, both companies sought the COFIUS review even before the Biden administration called for a ‘serious scrutiny’ of the deal and the opposition by lawmakers of both parties.
Meanwhile, US steel imports totalled 2.08Mt (net tons) in December 2023, including 1.61Mt (net tons) of finished steel (+ 2.6% and 7.7 respectively) over November 2023. For the year 2023, total and finished steel imports were 28.15Mt and 21.6Mt (net tons), down 8.7% and 14.1% respectively over 2022, the American Iron and Steel Institute (AISI) reported.
Top 2023 suppliers were Canada, Mexico, Brazil, South Korea and Japan. �
Brazil’s high import rate of Chinese steel is set to increase further after China’s touted investments in Brazil-based production facilities. By Germano Mendes de Paula*
IN 2023, China produced 1.019 billion net tons of crude steel, slightly up from the 1.018 billion net tons registered the previous year, according to worldsteel. However, the country’s domestic steel consumption was deeply impacted by a property sector crisis. Indeed, investments in the property sector declined by 9% in 2023, after a 10% drop in 2022. As a result, Chinese companies aggressively amplified their steel product exports by 36.2% to 90.3Mt in 2023, in order to offset low local demand.
Chinese domestic steel consumption in 2023 was supported by the automotive, shipbuilding, and solar photovoltaic sectors, according to Reuters. In 2023, shipbuilding completions totalled 42.32M deadweight tonnage, almost 12% higher y-o-y, while new orders in the sector jumped by 56% to 71.2M deadweight tonnage, official statistics showed. The China Association of Automobile Manufacturers (CAAM) claimed that the country’s auto production surged by almost 12%, rising to 30.16M units. Meanwhile, Chinese auto exports skyrocketed 58% to 4.91M units in 2023
(Table 1), helped by soaring sales in Russia after numerous brands withdrew from this market due to the invasion of Ukraine. Thus, the expansion of steel consumption due to the automotive sector in China during 2023, resulted in substantial indirect steel exports.
According to MySteel, China produced 96 million refrigerators in 2023, implying a 14.5% y-o-y evolution, while corresponding exports amplified by 22.4% (Table 1). The respective figures for washing machines was 105 million, 19.3% and 39.8%, highlighting that export growth was equivalent to the doubling of output amplification. For televisions, the amount
reached 193 million, with exports growing 7.5% even with a 1.3% production drop. Air conditioners, with a figure of 245 million, can be considered an exception in this context, because exports grew lower (4.6%) rather lower than the output (13.5%). That said, in the general context of household appliances, they followed a similar trend as the automotive sector.
Primary steel international trade statistics are released fairly frequently and they are typically updated. This is not the case for downstream steel industry data, which is often published after a considerable lag. A good exception regarding the latter is that, for the Brazilian steel market, downstream
* Professor in Economics, Federal University of Uberlândia, Brazil. E-mail: germano@ufu.br
steel statistics are unveiled monthly by the Brazil Steel Institute, with a delay less than 25 days. Furthermore, the mentioned trade association employs the same methodology developed by worldsteel.
Brazil-China steel international trade Brazil increased its direct steel imports from China (1.8Mt in 2022) to 2.9Mt in 2023, showing a 62% jump. Consequently, the Chinese market share concerning Brazilian steel imports increased from 53.4% to 57.7%, respectively. In the interim, Brazil’s exports to China were almost insignificant, reaching 49kt in 2022 and 54kt in 2023, or equivalent to 0.4% and 0.5%, correspondingly.
Brazil imported 2.15Mt of steel contained in manufactured products (in particular related to the metal-mechanical value chain) from China in 2022, with a small increase to 2.16Mt in 2023. The respective Brazilian indirect steel exports to China achieved 15kt and 17kt, correspondingly.
When Brazilian direct and indirect steel imports are combined, the Chinese figures grow from 3.9Mt in 2022 to 5.1Mt in 2023. This is equivalent to 16.7% and 21.5% of the national steel apparent consumption, respectively. This explains why the country’s steelmakers pushed the government to increase the import tariff from the current 10.8% to 25% of selected steel products, with a goal to protect from the ‘import tsunami’ captained by China, following the initiative that many countries have already adopted.
Table 2 shows a disaggregated view of
the composition of Brazilian indirect steel imports from China. The most important item is machinery and equipment, which decreased from 1.2Mt in 2022 to 1.1Mt in 2023.
Concerning the automobile industry, auto parts rose from 213kt to 243kt in years 2022-2023, demonstrating an increase of its market share from 23% to 27%. In the meantime, the car and commercial vehicle market expanded from 122kt to 183kt (or from 20% to 25%). For instance, automotive company BYD did not sell (export) even 300 cars in Brazil in 2022. In just one year, this number jumped to 18k.
Metal wires hit a plateau during the aforementioned years, not only in volumes (both from the world and China), but also in terms of high Chinese dominance (with a 57%-58% relevance). A similar performance was observed by the ‘structure, furniture and packaging’ category, with China’s respective market share being even higher (61%-62%).
Regarding household appliances, Brazilian indirect steel imports from China rose from 86kt in 2022 to 122kt in 2023, allowing a marginal gain in Chinese market share from 90% to 91%, which is a significant dominance.
As a whole, almost half of Brazil’s indirect steel imports in 2022-2023 originated in China.
Nonetheless, it is reasonable to expect that this already large ratio might increase in the coming years, because Chinese automakers BYD and GWM are investing to produce locally in Brazil, which tends to foster the import of auto parts. �
ACCOUNTING for nearly two-thirds of India’s steel consumption, the infrastructure and construction sector has led the country’s steel sector growth since the industry’s deregulation in 1991. Barring the Covid-19 period between 2020 and 2021, India’s steel sector growth amplified during the rest of the period in the last 10 years, following the government’s extended focus on public welfare schemes such as ‘Housing for All, and ‘Nal se Jal’ (tap water supply), among others.
With all these schemes in focus, the government is confident of achieving India’s steel production capacity of 300Mt by the financial year (FY) (April-March) 2030-31, up from 165Mt at present. Additionally, the metal’s per capita consumption in India is projected to rise to 160 kg by FY203031 from the existing 70 kg in FY2022-23. Dilip Oommen, president of the Indian Steel Association, stated, “The highest-ever investment of INR2,400 billion for railways will translate into robust domestic steel demand, thus spurring private investments and job creation. First-and-last-mile connectivity for sectors like steel, ports and coal, with an investment of INR750 billion, will improve logistics efficiency and help India’s steel sector growth.” Sajjan Jindal, chairman of the Jindal Group, echoed a similar response.
To improve steel consumption, the
government’s push for infrastructure development through the ‘Gati-Shakti Master Plan (a confluence of seven growth engines including railways, roads, ports, waterways, airports, mass transport, and logistics),’ ‘Make-in-India’ initiative for the manufacturing sector (focusing on Indiamade products to reduce dependence on imports), Pradhan Mantri Awas Yojna (PMAY) (Narendra Modi’s Housing Plan),
etc. is expected to stimulate demand and consumption of steel in the country. Further, the Ministry of Steel has also set up a Joint Working Group (JWG) with the Ministry of Housing & Urban Affairs (MoHUA), having members from the Bureau of Indian Standards (BIS), Central Public Works Department (CPWD), technical institutions, and industries for fostering steel usage in the housing and construction sector.
The only fully enclosed conveyor of its kind for HDRI transportation/charging
• High Dependability and Uptime Redundant patented mesh system
• Low Thermal Drop HDRI can be charged to the EAF at up to 700 °C (1,292 °F)
• Extremely Low Nitrogen Requirements Just one-third of conventional technologies
• Low Maintenance No chains, sprockets, hinges, or rails
• Challenging geometries up to 75 degrees Available as a pan plate or bucket conveyor
• Great flexibility Capable of transporting materials from fine-grained to lumpy
Number of
Delays in the completion of these projects and cost overruns, however, have raised concerns about the possibility of achieving these milestones. As of 1 January, 2024, a total of 1,820 such projects were under the surveillance of the Ministry of Statistics and Programme Implementation (MoSPI). Out of these, 848 projects, or 46.6% of the proposed ones, were delayed. This marks a significant improvement as at the end of March 2023 when the ratio of delayed projects to total projects was much higher, at 56.7%. This is still much higher than the pre-pandemic period, i.e., January 2020 when the ratio was just at 32.6%. On the positive side, a total of 618 projects are on schedule, and 56 are ahead of schedule so far. For the remaining 298 projects, data on the year of commissioning/gestation period remains unavailable. There are 198 projects showing delays beyond expectations.
A significant number of projects are also showing cost overruns. The cost of the 1,820 projects under monitoring stands at INR 30,700 billion which is approximately 18.7% above the original cost of INR 25,900 billion. Understandably, the cost overrun of India’s infrastructure projects has declined significantly from the level of 22% in March 2022. Surprisingly, 32% or 323 of the proposed projects are showing a delay of two-to-five years, driving the cost overruns. On the other hand, around 48% of projects have time overruns between one and 24 months. Also, 123 projects are experiencing a delay of more than five years. Thus, the average delay across 848 projects works out to three years.
Sector-wise projects, such as road transport and highways, remained the major sectors with the highest number of monitoring and delays at 1,021 projects and 450 projects, respectively. These sectors accounted for over 50% of the
total projects delayed. When compared with the pre-pandemic period (19.4% in January 2020), the cost overrun works out to be lower. Notably, the period just after the pandemic saw the highest cost overrun as the phase of reopening along with the Russia-Ukraine war, led to a sharp increase in input prices. With the correction seen in global commodity prices, the cost overrun is also trending lower.
In terms of major sectors, road transport, and highways, which have the highest number of projects under monitoring at
1,021, also recorded the highest number of delayed projects at 450. These accounted for over 50% of total projects delayed. Even as a percentage of total projects in the sector, the share of delayed projects is quite high at over 40%. Apart from this, the railway sector, which also has 250 projects under monitoring, recorded a delay of about 42%. For petroleum and coal, the share of delayed projects stood at 10.7% and 5.7%, respectively. In terms of the range of time overruns, which is defined as the difference between the anticipated date of commissioning and the original date of commissioning, railways and atomic energy seem to be lagging the most.
With the government laying a strong focus on capital expenditure by successively increasing the outlay, completing stalled projects on time will help boost current steel demand and also plan for new ones for the future. Meanwhile, the falling share of stalled projects in the last three months is an encouraging sign. �
CHAR Technologies is pledging itself as a sustainable gamechanger for heavy industries, with its proprietary technologies offsetting the use of high-emission fossil fuels, lowering costs as well as carbon fumes. Catherine Hill* spoke to Andrew White** on the company’s projects, processes, and journey from Master’s thesis to collaborating with the world’s second largest steelmaker, ArcelorMittal.
1. CHAR TECHNOLOGIES, AND MORE SPECIFICALLY PYROLYSIS, SEEMS TO BE A BIG POTENTIAL PLAYER IN INDUSTRIAL DECARBONIZATION. HOW DOES IT ALL WORK?
The technology is called high temperature pyrolysis. What that means is we’re heating stuff up. Pyrolysis means without oxygen, and the temperatures, as in the name, are high. Being in the steel industry, maybe it’s not as high as other processes, but within the world of pyrolysis, 800-900°c is what classifies high temperature pyrolysis. What we do is we take wood waste wood chips, or other organic residuals, and we put it through a high temperature
pyrolysis system. We then crack it apart to produce two valuable streams. The gas stream is called syngas, which can be used directly for its thermal benefits, if you put it through a burner or something similar. Alternatively, we can upgrade it to things like renewable green hydrogen or renewable natural gas. So that’s the gas stream. And then the carbon stream, because we can run at high temperatures without oxygen and we have a good level
of control over the process, we can create different biocarbons. The biocarbon we create can be well suited for PCI for blast furnace injection and the biocoal can be blended to make it a nut coke replacement. In addition, we can create carbons to go into electric arc furnaces, as well as biocarbon which allows for the offsetting of fossil fuel, and a lot of the steel making processes where that physical solid carbon is necessary.
2. COULD YOU SPEAK FURTHER ON THE USE OF SYNGAS AND HYDROGEN IN THE PROCESS, AS WELL AS AFTER?
If you could take a step back; what is wood made of? It’s cellulose, hemicellulose and lignin, which are basically carbon chains. You have carbons linked together with hydrogens connected to them, right? So, as we heat it up, what we’re after is fixed carbon – basically just carbon. When you look at an any coal or a biocoal that we make, it’s pushing 90% fixed carbon. It has almost no hydrogen, almost no oxygen. The biomass needs to go somewhere. Where it goes, is into a gas. And by operating at a high temperature, we can control a little bit of the make-
up of the gas. Our gas, as we make it directly out of the kiln, is on the order of 60+% hydrogen, and then some other components. We use that gas to run the plant by using some of it to create the heat we need. We self-consume somewhere around 15% of the gas we make, and we self-consume to heat it which is important. We’re not using fossil fuels to make biobased outputs. But then the rest of that gas, we can do a couple of things with it. We can use it directly. So that can go into burners. If we’re co-located with someone who needs a lot of heat, that
gas can just go directly through a burner and create heat. And through a separation process, we can pull the hydrogen out of the rest of the gas. With this process, we’ve then got this stream of marketable hydrogen – green hydrogen – and in the US, you would be able to qualify for these production tax credits of about $3 per kilogram of hydrogen – which is fantastic, because a kilogram of hydrogen goes for around a dollar, often less than a dollar. Alternatively, we can take that hydrogen and the rest of the gas we make, and we can convert it through catalysis into
3. HOW DID THE COMPANY START?
In 2010, I defended my thesis, which was on a related area to CHAR Tech’s current processes, and in 2013, after founding the company, CHAR Tech got its first round of funding. It was pretty small, like CA$100,000, but enough to do some testing and, and scale-up work. And then by 2018 we had commissioned our first pilot demonstration unit–and we’re still running that system.
4. CHAR HAS RECENTLY BEEN AWARDED $5M AS PART OF ARCELORMITTAL’S XCARB INNOVATION FUND. HOW DID THIS DEVELOP, AND WHAT DO YOU HOPE TO ACHIEVE AS PART OF THE INVESTMENT?
Around 2017 we started working with ArcelorMittal Dofasco, the plant based in Hamilton, Ontario. Initially, they were targeting PCI coal replacement, and then deploying an electric arc furnace to replace the blast furnaces. We’re now collaborating to manufacture our product, ‘CleanFyreTM’ biocoal, tailored for EAF purposes. Working closely with ArcelorMittal, we got a clear picture of what the biocoal needed to look like. Since 2017 we were sending them material, and they were testing it and giving us feedback. And then, this past July, we closed the investment from their XCarb Innovation fund, part of their low carbon green steel programme. Our long-standing
collaboration with Dofasco played a big role in this, providing solid technical validation. And then of course, getting the corporate investment was fantastic for us. Of all the companies they’ve made investments in, we’re the only ones in the biocoal space. If you look at [ArcelorMittal’s] climate action report, pyrolysis is one of the key elements of really being able to create green steel. And then, as part of that investment brand, we also received a fixed off-take agreement for the biocoal that we’re going to be producing at our commercial scale-up, which we’re in the process of building right now.
5. COULD YOU ELABORATE ON THE COMMERCIAL SCALE-UP FURTHER?
Our existing process plant can process about 500 kilos per hour of wood waste. So, we feed in 500 kilos per hour of wood waste to produce our output products. The commercial unit is going to consist of two larger processing lines. Each process line is capable of processing about three tons per hour of wood waste. So, we’ll be scaling up our input quite a bit. On the output side, we will also be scaling up to about 10kt/yr of biocarbon production. This came about
thanks to the US$14 million in government funding that we were fortunate to receive. The funding comes from funds and loans from the province of Ontario, and federally from the government of Canada. The facility will be making the biocoal and it’ll also be making renewable natural gas that we can inject into the gas pipeline here and sell for a premium because it’s renewable. So, it has huge environmental benefits.
6. HAS FEDERAL FUNDING ALWAYS BEEN A LARGE SOURCE OF FUNDING?
The programmes from the [Canadian] Province of Ontario, and the federal government, are a combination of grants and loans. They’re not taking an equity position. I think it is really important in the clean tech space because, ultimately, to scale up, especially the scale-up to the industrial demand that steel companies would need, there’s a really big jump from pilot to commercial scale. Sometimes that jump is challenging to get project level financing on its own, it can be hard to get offtake agreements for that first plant. These government programmes help in getting the first commercial project off the ground. I really like the programmes and I think the way the federal and provincial governments here roll them out, works really well. There’s a bit of a contrast, with the US being big fans of tax code, and they’ve gone down the tax code process with the Inflation Reduction Act, the IRA. There are some elements of that that I think would be good to see rolled out, particularly around the PTCs or production tax credits being a little bit more broadly applied. PTCs could provide growing companies like ours with more certainty around project finance, reducing contracting risks and attracting more project-level debt and equity partners.Both approaches have their merits, but these programmes are vital for getting that first commercial plant operational and to get the client using the product and then being able to expand from there.
renewable natural gas. And in North America and in Europe, there tends to be a good premium on renewable natural gas. So for us, a lot of the benefit and importance of the gas is that we’re really extracting the maximum value out of this biomass. We’re not just turning biomass into a solid carbon. We’re turning it into a solid carbon for steel making. We’re turning it into a gas that can go into steel making. It can go into the pipeline, it can go to other customers to really extract all the value out of that biomass stream.
woodings.com // smco.net
Superior Machine has joined the Woodings’ group creating the most capable hot metal equipment supplier group in North America. Offering the combined knowledge, engineering, manufacturing, and construction expertise for all your equipment needs.
Wherever hot metal is produced, you will find equipment from Woodings, Superior Machine, and
Munroe operating at the highest level in the most demanding conditions. Our products and professional installation services reduce downtime and extend campaign cycles.
We can provide you with more value than ever before from concept to installation, service to replacement, our size, scope, and experience gives us a unique ability to help you increase productivity and solve problems.
We are better together. Let us show you.
7. TOUCHING ON GREEN PREMIUMS, WHAT IS YOUR VIEW OF THE PLACE THEY HOLD IN THE MARKET, AND HOW DO YOU BELIEVE THEY WILL EVOLVE?
I think, generally because of the nature of steel making, green steel tends to lend itself a little bit better to a demand-driven pathway versus a regulatory pathway. I think that is particularly stark when you look at, say, Canadian production of steel, and then you look at what’s going on in Europe. If Canada implemented some sort of a carbon tariff to make green steel here competitive, and you know, especially when we talk about imports and then we look at our largest trading partner in the United States who doesn’t have it, it creates a real challenge for the production of steel.
I think there’s obviously a strong commitment to decarbonize steel making. But, because of the nature of the industry and the trade exposed nature of it, it’s
really a hard thing to come in on the sort of regulatory side of things. I’m not advocating against a carbon tariff because ultimately, I started the company to affect global change and try to reduce our impact on the climate. But I think as different procurement programmes are developed and demand for green steel starts to increase – whether its demand being from EV manufacturers who are looking to show that their entire vehicle is carbon neutral or from municipal or government contract – this is what should be driving the market for green steel. Having industries proactively ask for it is the best pathway to create a real marketplace for low carbon and carbon neutral steel. Because all the other trade issues can make this very complicated.
8. WHAT PROJECTS ARE CURRENTLY IN THE PIPELINE FOR CHAR?
We’ve got three additional projects that we’ve talked about publicly that are in the development cycle. One near Lake Nipigon, Ontario, one in Kirkland Lake, also Ontario, and one in St. Felicién, Québec. All of them were partnering with local feedstock suppliers, so local biomass. In the case of Lake Nipigon and Kirkland Lake, we are partnering with the local First Nation communities that are responsible for forestry operations. And then in, in St. Felicién, we’re partnering with the regional and municipal and city governments on
getting the biomass supported, as well as a biomass fired power plant to help with procurement of biomass. So, those are the three next projects. And really the intention is, how do we get to more meaningful biocarbon production numbers? How do we get to 100kt/yr, 500kt/yr? It’s really through this for us, that we’ll see development, through this rapid project deployment process. We are actively looking to build a couple of additional projects in the very near term.
9. WHAT DO YOU BELIEVE ARE THE BIGGEST CHALLENGES THE STEEL INDUSTRY IS CURRENTLY FACING?
Broadly speaking, the technology often uses a lot more carbon. The easy one to pick on is the difference between an EAF and a basic oxygen furnace process, because it’s just the amount of carbon that’s needed. But there’s actually some additional nuance there. From a challenge perspective, especially from our type of technology, it’s that biocarbon at its current stage of development can’t be a 100% coke replacement because of the strength properties of coke. We can replace PCI, we can replace nut coke, but replacing coke is a big challenge. That’s something that research organizations are working on. What I am really encouraged by is that in Canada, there’s the Canadian Carbonization Research Association that the main steel companies in Canada participate in. It’s supported through a government lab. In any regard, there’s the challenges that we’re facing on decarbonization, especially on the use of carbon. How do we get together and solve these problems? We can be competitors and we can have our own trade secrets and our abilities to try and be more competitive and create more margins than others. But some of these bigger challenges, I think, necessitate collaboration. The encouragement that I have is seeing this type of industry collaboration here in Canada. I imagine it exists in different ways and in different jurisdictions as well. But, industry collaboration on decarbonization is a great thing to see.
DELIVER IMPROVED YIELDS, HIGHER-QUALITY STEEL AND REDUCE COSTLY DOWNSTREAM
The high-resolution Slag Detection System (SDS) thermal imaging camera detects the transition between steel and slag and has been specifically designed to survive in harsh operating conditions, whilst utilising a particular wavelength to reduce obscuration caused by smoke and fumes.
Suitable for operators of secondary steel making vessels including stainless steel, SDS can also be used in other smelting operations such as copper and platinum. Its automatic operation ensures that only the predefined amount of slag is carried over before an alarm is triggered.
SDS is AMETEK Land’s definitive solution for monitoring and reducing slag carry-over in steel production facilities whilst saving money and improving operator safety.
Automatic detection and tracking accurately identifies the stream, reducing background interference
Accurate detection independent of charge weight
Fully automatic operation and clear alarm notifications
Improved connectivity through the use of Open Data Interface
The climate movement is finally beginning to shine a light on the iron and steel industry, which is responsible for 11% of global carbon dioxide emissions and 7–9% of global greenhouse gas emissions. The heightened focus on the iron and steel sector is evidenced by the incorporation of heavy industry decarbonization targets and technology investments at the national, international, and corporate levels in the past year.
By Caitlin Swalec* and Astrid Grigsby-Schulte**ONCE thought of as an industry without feasible decarbonization options (ie, ‘hardto-abate’), the steel industry now has a range of technologies and tools that can enable a meaningful shift to a low-emission sector. Still, as 2030 decarbonization targets and 2050 net zero targets draw near, the urgency of mitigating the carbon footprint of the global iron and steel industry grows even more quickly than the current ambition from governments and the private sector. The steel industry is currently not on track for net-zero scenarios, let alone 1.5 degree alignment.
The coal-based technologies prevalent in iron and steel production today are not sustainable in net-zero emissions scenarios. Blast furnace-basic oxygen furnace (BF-BOF) steelmaking needs to be phased out in favour of scrap and DRI-based electric arc furnace (EAF) production. EAF steelmaking
only produces 10–20% of the carbon dioxide emissions of BF-BOF steelmaking, depending on the input material (scrap, pig iron, direct reduced iron and so on). While scrap-based EAF steelmaking should be prioritized to lower industry emissions, scrap supplies are finite, and alternative iron production methods must be implemented to further eliminate emissions from the sector. New technologies such as green hydrogen-based direct reduced iron (DRI) hold promise for achieving net zerocompliant steel production if the necessary investments in development – including clean energy and hydrogen production –are made.
Society will continue to rely on steel for engineering, construction, medical, and energy applications as it builds new energy projects, replaces and develops infrastructure, and innovates for a bright future. As economies develop, the global demand for steel will continue increasing. The continued dominance of fossil fuels in steel production processes in operating and developing plants must be challenged and emissions reduced through a combination of strategies including material efficiency to lessen demand, increased reuse and recycling, and production decarbonization
through retrofits and advanced technology. The momentum to decarbonize the iron and steel industry must shift into high gear.
Current status of global iron and steel plant fleet
Global steelmaking capacity
The Global Steel Plant Tracker (GSPT) covers 2,271Mt/yr of operating crude steelmaking capacity, or 92% of global capacity according to OECD estimates. The GSPT also includes 1,486Mt/yr operating blast furnace capacity and 144Mt/yr operating DRI capacity, representing 93% and 99% of world capacities, respectively, or 93% of operating ironmaking capacity altogether. Additionally, the GSPT covers all crude iron and steel plants under development as of 1 March 2023, making this the most up-todate comprehensive tracker of changes in global steel capacity. Fig 1
According to the GSPT, 62% (1,397Mt/ yr) of global crude steel capacity currently uses the BOF route, 29% (665Mt/yr) uses EAF steelmaking, and <1% (<6Mt/yr) uses open hearth furnace (OHF) steelmaking. The remaining 9% (204Mt/yr) of capacity has not been distinguished between these routes. From the steelmaking capacity of known technologies, 68% is BF-BOF, 32% is
EAF, and <1% is OHF.
Over two-thirds of current steelmaking capacity is in Asia; China accounts for 49% (1112Mt/yr) of the operating capacity in the GSPT, followed by India at 5.3% (121Mt/yr) and Japan at 5.1% (115Mt/ yr). Outside of Asia, Europe has the most operating capacity at 13% (297Mt/yr) while the United States holds another 5.1% (115Mt/yr). When only BF-BOF steelmaking is considered, China accounts for 59% (819Mt/yr) of global capacity (Fig 2a).
Global ironmaking capacity
Asia also holds most of the world’s operating iron capacity with around threequarters of global ironmaking belonging to the region. China accounts for 55% (897Mt/yr, followed by India (122Mt/yr) and Japan (95Mt/yr). Europe, as in steelmaking, comes in second for regional ironmaking, representing 10% (158Mt/yr) of global operating capacity; Germany (33Mt/yr) and Ukraine (30Mt/yr), representing 2.0% and 1.8% of global capacity respectively, lead the region. Other notable countries include Russia (65Mt/yr), the United States (34Mt/ yr), and Brazil (34Mt/yr). Iran not only has a sizable operating ironmaking capacity overall (44Mt/yr), but also has the highest operating DRI capacity in the world (38Mt/ yr).
Per the GSPT, 91% (1,486Mt/yr) of global crude iron capacity currently uses BF technology and 9% (144Mt/yr) uses DRI technology, mainly a mix of natural gas-based and coal-based DRI. Less than 1% (9Mt/yr) of iron capacity in the GSPT has not been distinguished as BF or DRI technology.
Ironmaking units typically operate for
Fig 4. Current plans for steelmaking capacity development put shift towards EAF production behind decarbonization targets
Source: EAF capacity projection data from Global Steel Plant Tracker, Global Energy Monitor, March 2023. EAF capacity net-zero projection from 1.5C pathway in IEA Net Zero by 2050.
around 40 years, with lifetime-extending relinings every 15–20 years for BFs and every 20 or more years for DRIs. A typical BF relining costs approximately $200 million USD and represents 25–50% of the cost of a new blast furnace. Each of these cycles represents a chance for steelmakers to either double down on existing technology or else transition to cleaner production routes.
By 2030, 1090Mt of existing coal-based BF capacity (73% of the fleet) will reach the end of their working life, requiring decisions on refurbishment or shutdown. Two-thirds of these reinvestment decisions will arise in China. As each BF unit comes up against its reinvestment cycle, a plan must be made for switching the unit to low-emissions steel production technology, whether that means an immediate, full retirement or replacement of BF capacity, or a limited maintenance plan to prolong the lifetime of the asset by no more than 2–5 years until it can be fully retired or replaced by lowemissions processes. By 2025, no further reinvestments in BFs should be made, in order to minimize long-term carbon lock-in and additional stranded asset risk. Given that each BF reinvestment cycle decision plan takes time to develop (one to several years), these plans need to be created immediately to ensure that the 2025 target of no further reinvestments in BFs be met.
Fig 2a and Fig 2b
Steelmaking capacity under development
Still behind target on shift away from
Fig 5. Steelmaking capacity under development by technology type
Source: Global Steel Plant Tracker, Global Energy Monitor, March 2023.
Note: includes steel plants with capacity of at least 0.5Mt/yr.
coal-based BF-BOF steelmaking
According to the GSPT, approximately 731Mt/yr steelmaking capacity is under development worldwide, of which 52% (380Mt/yr) uses the BF-BOF route, 39% (286Mt/yr) uses EAF, and 9% (65Mt/yr) is unknown. Of these new developments with known production processes, 57% are BF-BOF and 43% EAF. While still primarily coal-based BF-BOF, the steel industry is beginning to face the reality of decarbonization: when the first Pedal to the Metal report was released in 2021, 68% of operating capacity used the BF-BOF process, 31% EAF, and less than 1% HF. Of projects that have commenced operation since then, 57% have been BF-BOF and 43% EAF. The higher percentage of deployed EAF steelmaking signals that some progress is being made in the shift away from BF-BOF and toward EAF.
Further breaking down the new capacity under development reinforces this observation. This includes both projects that have been announced with no concrete advancements and construction phase projects that have broken ground. Of new development capacity announced before 2021, 78% uses BF-BOF technology and 22% EAF, whereas those announced since 2021 are 48% BF-BOF and 52% EAF. Projects that have progressed to the ‘construction’ phase are 55% BF-BOF-based and 45% EAF. Fig 3
While these developments indicate a notable movement toward greener technology, this shift is nowhere near the scale of change needed to meet carbon
neutrality goals by 2050. The IEA’s Netzero by 2050 scenario puts the share of global EAF steelmaking capacity at 37% by 2030 and 53% by 2050. Given the heavy presence of BF-BOF steelmaking today (67%), even the shift toward EAF in new developments leaves the industry far from this timeline. To meet the IEA’s 53% EAF threshold by 2050 (while accounting for a projected 12% increase in global steel demand over this time period) approximately 347Mt of BF-BOF capacity would need to be retired or cancelled and 610Mt of EAF capacity would need to be added to the current fleet.
In this scenario, the share of planned steel capacity using EAF technology would need to reach 64% and BF-BOF reduced to 36% (and all equipped with CCUS). However, current development plans would add 380Mt of known BF-BOF capacity and only 286Mt of EAF (57% BF-BOF and 43% EAF), which would result in the percent of production using EAF technology remaining at 32% and BF-BOF at approximately 68% through 2050 (see Fig 4). Thus, significant action needs to be taken to change this trajectory by retiring existing BF-BOF capacity, cancelling BF-BOF capacity under development, and replacing BF-BOF plans with alternatives, mainly DRI-EAF.
Asia hotspot for new steel capacity
53 countries currently have new steelmaking capacity planned or underway. As with operating capacity, most (75% or 545Mt/yr) of this capacity comes from Asia, and a majority (55%) from just two
GLAMA Maschinenbau GmbH
Headquarters:
Hornstraße 19 D-45964 Gladbeck / Germany
Fon: +49 (0) 2043 9738 0
Fax: +49 (0) 2043 9738 50
countries – China and India (see Fig 5). However, the share of global development attributed to China and India is shrinking (down to 55% this year from 66% in 2021), with Chinese projects making up 28% (207Mt/yr) of global developments and Indian projects 27% (196Mt/yr).
India ramps up plans to add emissionsintensive BF-BOF steelmaking capacity India is now the world’s largest developer of new coal-based steel capacity, holding 40% (153Mt/yr) of BF-BOF steelmaking capacity under development. China, the previous frontrunner, is a close second with 39% (147Mt/yr), making the two countries responsible for over three-quarters of BF-BOF development globally. This is despite the fact that both countries have made pledges to achieve carbon neutrality, China by 2060 and India by 2070. Other countries with new BF-BOF capacity under development are Indonesia (24Mt/yr), Vietnam (22Mt/yr), Malaysia (12Mt/yr), the Philippines (10Mt/yr), Myanmar (4Mt/ yr), Cambodia (3Mt/yr), Iran (2Mt/yr), Bangladesh (2Mt/yr), and Nigeria (1Mt/yr), many of which have net zero commitments of their own (see Table 1). Fig 6
EAF steelmaking capacity expands as China’s share slows
Fig 6. China’s and India’s shares of global coal-based BF-BOF capacity
Source: Global Steel Plant Tracker, Global Energy Monitor, March 2023. Note: includes steel plants with capacity of at least 0.5Mt/yr.
Fig 7. Ironmaking capacity under development by technology type
Source: Global Steel Plant Tracker, Global Energy Monitor, March 2023. Note: includes iron plants with capacity of at least 0.5Mt/yr.
While BF-BOF developments are led by a few key actors, global distribution of new EAF capacity is expanding, with 286Mt/yr under development in 49 countries this year as opposed to 170Mt/yr in 32 countries the year before – a 68% worldwide increase. China accounts for 17% (49Mt/yr) of EAF developments, and although the country’s overall tonnage has remained largely unchanged from 2021, the global share this represents has decreased almost 12 points from 29% in 2021. This decline reflects the expanding distribution of EAF steelmaking. Other leading countries developing EAF capacity include Iran with 13% (38Mt/yr), India with 9.1% (26Mt/yr), Germany with 6.3% (18Mt/yr), and the Philippines with 4.9% (14Mt/yr).
While growth of EAF steelmaking capacity can be seen as a positive sign for the green steel transition, the source of electricity and EAF feedstock (scrap, pig iron, direct reduced iron, etc.) will determine the emissions intensity of the steel produced at these facilities.
Of known capacities for ironmaking projects under development, 71% (273Mt/yr) will use BF technology and 29% (114Mt/yr) will use the DRI process (Fig 6). Relative
to the current distribution of operating ironmaking capacity (91% BF, 9% DRI, <1% unspecified), ironmaking capacity is shifting towards a greater share being DRI production. Further, projects announced more recently (since 2021) have a higher proportion of DRI ironmaking (63% BF and 37% DRI) compared to projects announced before 2021 (84% BF and 16% DRI).
Overall, DRI is gaining a larger share of ironmaking globally.
However, the emissions intensity of steel produced from DRI varies significantly depending on the DRI process. Much of the DRI capacity under development is in India (18Mt/yr), where coal-based DRI production dominates the industry, resulting in the highest national average CO2 emissions intensity for EAF steel production. Moreover, while DRI is most often associated with the lower emissions EAF steel production route, DRI plants can also feed BFs or BOFs to make steel. This means that the development of DRI technology on its own does not indicate a full-scale shift away from coal-based steel production, but a significant reduction in emissions for one part of the iron and steelmaking process.
Fig 7
97% of global blast furnace capacity under development in Asia
While 13 countries have known plans to develop blast furnace capacity, 97% (265Mt/yr) of that capacity is located in Asia. The country with the largest global share is China with 56% (154Mt/ yr), followed by India with 25% (69Mt/ yr) and Vietnam with 8% (21Mt/yr). Blast furnace capacity is a critical metric in the steel industry’s decarbonization process; given that the blast furnace is the most carbon-intensive portion of steel production with limited, difficult, and high-cost decarbonization options, decisions about the refurbishment, retrofit, and retirement of existing blast furnace capacity and proposals and investments in new blast furnace plants versus direct reduced iron plants will determine whether the global steel sector aligns with the net-zero by 2050 pathway. For a more in-depth look at blast furnace capacities and developments, please see GEM’s new Global Blast Furnace Tracker.
DRI ironmaking capacity growing, but not quickly enough Capacity using the direct reduced iron (DRI)
process is more dispersed, with projects planned in 24 countries, though many smaller (<0.5Mt/yr capacity) DRI projects are noted. Countries with the largest DRI capacities under development are India with 16% (18Mt/yr), Iran with 10% (11Mt/ yr), and Germany with 9% (10Mt/yr). As indicated earlier, the share of DRI in total global ironmaking capacity is growing but is still far from where it needs to be.
Steel decarbonization strategies point out that DRI development should be strategically planned in countries with ample renewable electricity generation potential and iron ore availability exceeding domestic needs. The Net Zero Steel project identifies Australia, Brazil, Canada, South Africa, and Russia as good candidates for green hydrogen-based DRI production based on renewables potential and iron ore resources. An additional study that accounts for cost and worker wages, in addition to iron ore resources and renewable energy production, concludes that countries approximately 23.5 degrees
north and south of the equator (near the tropics of Capricorn and Cancer) are best suited for green hydrogen-based DRI production.
Stranded asset risk continues rising Stranded assets pose a significant economic risk to the iron and steel industry as more countries with major steel industries pledge to reach carbon neutrality but at the same time plan to build numerous large coalbased BF-BOF steel plants.
If all coal-based BF-BOF capacity proposed or under construction is fully developed, operated with unabated emissions, and historic overcapacity trends continue, the steel industry could face as much as $554 billion in stranded asset risk as countries work towards their carbon neutrality commitments (see Table 1).
Stranded assets are assets that have lost anticipated economic value as the result of changes in market conditions and regulations adopted as part of decarbonizing the global economy. Because
decarbonization options for BF-BOF steel plants are limited and largely unproven, BF-BOF steel plants will be vulnerable to stranded asset risk if the cost of carbon is realized through carbon pricing (ie, taxes) or emission standards, and a conventional steel plant may be unable to price competitively with low-carbon steel production plants. To avoid stranded asset potential, BF-BOF retrofits for low-carbon steelmaking would need to be developed and brought to market in a fraction of the time predicted in steel decarbonization roadmaps (see The risk of stranded assets.)
As this research continually expands its coverage of developing steel capacity and as countries further develop their decarbonization plans, a fuller picture of the increasing risk of stranded steel industry assets is available. As of June 2023, over 130 countries have announced net-zero goals and the amount of BF-BOF capacity in development continues to grow. From 2021 to 2022 there was an increase of approximately 7% (36Mt/yr) in BF-BOF assets under development in countries with net-zero carbon commitments, increasing the upper range of stranded asset risk estimations from US$518 billion to US$554 billion. Table 1
In addition to stranded asset risk from developing steel plants, a 2022 study of TransitionZero’s Global Steel Cost Tracker estimated that 132Mt/yr capacity at existing BF-BOF facilities will face stranded asset risk by 2030 and 514Mt/yr by 2050 if we are to achieve net zero emissions by 2050. Looking at stranded asset risk from existing plants and from plants under development together puts total capacity at risk at approximately 882Mt/ yr by 2050, equivalent to 36% of current
Table
commitments
Source: Global Steel Plant Tracker, Global Energy Monitor, March 2023. Note: includes steel plants with capacity of at least 0.5Mt/yr. Based on estimation that the capital cost of a new integrated BFBOF steelmaking facility is approximately $1-1.5 billion per Mts crude steel capacity.
global operating steel production capacity. It is thus increasingly clear that there are substantial financial risks associated with building new BF-BOF plants and extending the operational lifespan of existing BF-BOF plants.
While the majority of countries possessing significant steel production capacity have made explicit pledges towards achieving carbon neutrality, most of the top steel production companies are yet to demonstrate similar commitments.
According to the GSPT, out of the 20 companies that hold the largest shares of global steel production capacity (28.9% total), less than half (45%) have formulated concrete plans to reach net zero by 2050. Even among those with net zero 2050 goals, the average proportion of capacity reliant on the coal-based BF-BOF production route stands at 84%, while only 16% uses EAF.
This highlights the need for greater engagement in the private sphere as
well as the public, including widespread accountability mechanisms to incentivize corporate climate action.
• The last year was pivotal for heavy industry decarbonization. Steel has moved from inertia to progress. We saw the first set of blast furnace relining investment decisions made, and the pipeline of coalbased blast furnace-basic oxygen furnace production has somewhat changed for the positive. Coal-based steel production is on
the decline, but not quickly enough. Further challenges arise in ensuring that the steel transformation strives for fully decarbonized production routes, rather than other fossil fuel-based alternatives.
• The market is changing. Governments are handing out subsidies for green steel now, notably the European Union, United States, and Australia. Plans for new steel capacity reveal a small but distinct shift in steel production towards low-emissions steel production. The green steel transformation is becoming a race, and governments subsidizing uneconomic capacity using the coal-based blast furnacebasic oxygen furnace route will be left behind.
• South East Asia continues to lead in development of steel production capacity and is now emerging as a stranded assets hotspot. Capacity development plans in South East Asia need to be redesigned in alignment with net-zero plans, meaning no new coal-based blast furnace-basic oxygen furnace steelmaking developments and plans to retire and replace blast furnaces with fossil-fuel-free alternatives. �
The Future Steel Forum was launched to address the growing interest in digital manufacturing within the global steel industry, particularly the technologies associated with industry 4.0 such as Big Data, the Industrial Internet of Things, Artificial Intelligence and Machine Learning.Over the past five years, the event has attracted speakers from major steelmakers including ArcelorMittal, Tata Steel, Voestalpine, POSCO, Emirates Steel, US Steel, Big River Steel, Liberty Steel Group, TMK, Kobe Steel, Metinvest
Digital, Badische Stahl-Engineering, Buderus Stahl and many others. Future Steel Forum speakers tend to be involved in the development and/or use of systems that rely upon these technologies, and the event itself endeavors to attract a mixed audience of steelmakers and technologists. In a nutshell, the Forum is an event for forward-thinking steelmakers who embrace new high-tech production technologies that embody the essence of so-called “smart manufacturing”.
Visit our website to discover more about the event
Do you want to showcase or promote your products and services to over 200+ international steel professionals? Discover what opportunities we currently have available by contacting Paul Rossage on paulrossage@quartzltd.com
FOR LIMITED TIME, SECURE YOUR EARLY BIRD TICKET/S HERE, AND SAVE UP TO £200PP SPONSOR OR EXHIBIT
A model has been created to predict the shape of the cohesive zone in the blast furnace enabling the operating parameters of the furnace, in particular coal dust injection rate and oxygen enrichment of the blast, to be adjusted to create the desired inverted ‘V’ shape for maximum permeability of the burden, optimum heat flux ratio and proper drainage of the furnace at the tap hole. By R R Kumar1*, R K Singh1, Anindya Roy2, A K Mukherjee2, S Sudershan2 and M Roy1
CONSIDERATIONS regarding the effect of pressure loss in front of the tuyeres, distribution of the burden and gas flow in a large blast furnace (BF) are examined here with reference to the operating parameters of BF#5 (Kalyani) at IISCO steel plant, Burnpur, India. Laboratory investigations assessed the characteristic raw material qualities, determining the gas flow behaviour inside the furnace shaft. A formula was established to correlate the top gas temperature with the heat flux ratio of the furnace, and continuous measurement of the stack pressure was made under
different furnace operating conditions. A significant transient behaviour of the pressure drop was observed especially in the lower and middle zones of the shaft as a function of the accumulation of the liquid phase and the progress of smelting. The rate of burden descent between consecutive casts reflects the accumulation and drainage of the liquid products as a result of which heat transfer, reduction and aerodynamic processes assume a transient character. The analysis of gas temperature at the stock-line showed that variations are more pronounced in the
central and peripheral regions, while, in the intermediate regions, the conditions are relatively stable. The transient nature of the aerodynamic processes inside the furnace reveal the existence of an appreciable reserve capacity. Elimination of this transience was tested on the furnace at ISP which lead to improved operating parameters.
Blast furnace aerodynamics is concerned with defining the conditions for achieving maximum gas flow through the descending burden. Once the thermal and chemical requirements are met,
with four tap-holes, a high coal injection rate, a closed loop cooling system, waste heat recovery in the stoves, de-dusting in the cast house and a top recovery turbine for power generation, among others. The rated capacity of BF#5 is 2.70Mt/ yr. It is equipped with three stoves design for a 1200oC hot blast temperature. The designed campaign life is more than 20 years. So far, in its first campaign, commencing 30 November 2014, the furnace produced 16.76Mt by December 2022.
blast furnace performance.
Prediction of cohesive zone
maximum productivity is achieved with maximum gas flow rate. The factors which influence this, their inter-relationship and influence on the furnace operation have remained the subject of constant attention by investigators[1].The conditions are considerably complicated by changes in the character of burden as it descends to the tuyeres, and by unequal distribution of solids and gases in the stack. The rate at which reducing gas can be blown and the manner in which it is distributed directly affect the heat and mass transfer and the utilization of the reducing potential of the gas. Hence the rates of gas flow and gas distribution are directly related to thermochemical phenomena and ultimately affect the furnace efficiency and productivity.
The IISCO steel plant in India has a single blast furnace (BF#5) which is the largest furnace in SAIL. It has a volume of 4161m3 and a working volume of 3551m3. The furnace is equipped with many modern, state-of-the-art technologies including bell-less top charging, a twin cast-house
To achieve an average daily hot metal production of ~8000tpd with a fuel rate of ~540kg/thm, ideal gas dynamics are required by improving the furnace’s aerodynamic features. As BF#5 is the only furnace at ISP commissioned, consistent furnace operation to achieve the desired production rate and techno-economic parameters along with prolonging the campaign life is a major challenge for BF operators. BF aerodynamics has always been of fundamental importance and assumes a critical role as furnace size increases[1,2].The optimization of the smelting parameters is determined by the joint action of heat exchange, reduction and gas dynamics.
A qualitative and quantitative assessment of the flow and distribution of the gas within the burden column is the driving force for this investigation and development work, to improve the gas flow dynamics of the iron-making process and hence better
The shape of the cohesive zone can be used as a control guide for burden distribution. An estimation method has been developed based on the relationship between the shape of the cohesive zone and the vertical distribution of wall temperatures measured using thermocouples set in the stave coolers[3]. This method makes it possible to estimate the shape of the cohesive zone continuously, easily and at no expense. Three different types of cohesive zone shape, namely inverted V, L and W, are classified based on the stave wall temperatures. To quantify this relationship, a stave temperature index ‘S’ was derived using average temperatures TS and TB in the upper and lower part of blast furnace respectively.
Calculation of model
S = TB/TS
At (TS-Tav)*(TB-Tav) > 0
(1)
S= -TB/TS (2)
At (TS-Tav)*(TB-Tav) < 0
Where,
S: Stave temperature index
TS: Average temperature in upper shaft
TB: Average temperature in lower shaft
Tav: Average of all stave temperatures for a given period (say, 3 months historical data)
Boundary conditions
Boundary conditions were employed to
).
This index isolates the shapes of the cohesive zone among three broad categories having distinguished gas flow patterns. Application of this method to daily blast furnace data permits accurate estimates of the cohesive zone shape and allows instantaneous operation control.
Continuous tapping of the furnace creates conditions for stabilizing the up-thrust. Continuous tapping and controlling the flow of iron and slag may balance the amount of slag and hot metal falling into the hearth and the amount of slag and hot metal discharged to keep the liquid level in the hearth stable. The stability of the cokefree zone results in stability of the up-thrust resulting from the collection of liquid metal and slag.
A parameter, based on tapping time, can be introduced to measure the volatility of the liquid up-thrust (slag ratio) and is represented in (Table 2), where SF = 100*t2/∑t and t2: is the time of flowing of both metal and slag in minutes. ∑t is the overall tapping time in minutes.
Maximizing this value to over 90% should be aimed for at each tap-hole to regulate the tapping speed and hence stabilize the liquid interface[4]
The permeability of the deadman plays a vital role in draining the iron and slag from the hearth. The deadman is the region containing unburnt coke which sits on the hearth or floats just above it, the coke dissolving in the metal to near saturation. This is very important in controlling the gas dynamics in the lower zone. Information regarding the hearth permeability will help to improve drainage of hot metal and slag during casting. The capacity of the deadman can be quantified using the deadman cleanliness index (DCI) or deadman index (DMI). The DCI is based on the observation that, in case of poor
contact between the liquid products and coke, the carbon content of the hot metal deviates from the calculated equilibrium value. A spreadsheet based model has been developed based on the following empirical formula, taking into account hot metal temperature, composition and slag basicity: DCI = 2Thm – 121[Si] -128[P] – 156[S] +11[Mn] -389[C] – 190B -690 (3)
Where,
Thm: Hot Metal Temperature, oC [Si], [P], [S], [Mn], [C]: Mass % of these elements in the hot metal
B = Slag Basicity (CaO/SiO2)
For furnaces with volumes from 20004300m3, using auxiliary fuel injection (NG/ PCI) DCI varies within the range of 150-250 with the higher values resulting in better drainage capacity of the Dead-man[5]
One parameter affecting gas dynamics is the heat flux ratio which is defined as an index for controlling the gas flow rate, hence affecting the aerodynamic features of the blast furnace. Generally, the heat flux ratio (HFR) is expressed as the following equation:
HFR = (Heat capacity flux of solid)/(Heat capacity flux of gas) = Cps*Ws / Cpg*Wg = (Cpo*Wo + Cpc*Wc) / (Cpg*Wg) (4)
Where,
Cp = Heat capacity W = mass flux and suffixes s, g, o and c represent solid, gas, ore and coke respectively.
Each term in this equation varies with the temperature and the degree of reaction at a given position in the blast furnace.
A spreadsheet-based model has been developed to calculate the instantaneous value of HFR in a blast furnace. The empirical formula used for this purpose is:
See box for formulas at the bottom of this page.
Where
CR: Coke rate, kg/thm CO2:
Volume % in top gas
OR: Ore rate, kg/thm N2:
Volume % in top gas
PCR: Injected pulverised coal rate, kg/ thm H2:
Volume % in top gas
DR: Dust rate, kg/thm CO:
Volume % in top gas
[C]: Carbon concentration in coke,% [C]pig: Carbon concentration in pig iron, % [C]dust: Carbon concentration in dust, %
Using the heat flux ratio model, it is possible to record instantaneous data for this index which can be correlated with the top gas temperature at a particular pulverized coal injection rate and oxygen enrichment level.
The management band (eg 0.80+0.05) of this ratio can be identified as the optimized level of blowing and charging of the furnace.
Results and discussion
Cohesive zone shape and gas dynamics
Historical and instantaneous data of thermocouple readings in the lower shaft, B1, B2, and upper shaft, S1 and S2, were used to determine the shape of the cohesive zone. Once this was determined, the pattern of the gas flow up the furnace shaft was identified and accordingly corrections could be made to obtain the desired permeability of the charge in the furnace. Generally, to achieve the best driving rate in the furnace to produce around 8000thm/ day, an inverted V-shape cohesive zone was desired (Fig 1), whereas during a stiff furnace operating regime, the detrimental W-shape cohesive zone resulted requiring an adjustment of the burden distribution and blowing parameters to establish either the inverted V or L shape cohesive zone providing improved aerodynamics. Again correlating the permeability resistance index (K-factor) to the shape of the cohesive zone, the fluctuation in blast pressure seen in the case of L and inverted V shapes is lower than for the W shape. Therefore, it may be assessed that this method provides a useful tool for analysing the operational condition of a BF as well as indicating the effects that the properties of ore and coke have on the
operation of BF#5.
1. Cohesive zone shape prediction for BF#5, ISP
The gangue content in lump iron ore and sinter charged to BF#5 is 6-7% and 8-9% of these inputs respectively. This results in a higher slag volume (>380kg/thm) which makes the hearth activity more prominent. Continuous draining of the liquid products from the hearth becomes one of the priorities. The casting period has to be increased and the volatility of up-thrust in all four tap-holes must be maintained at more than 90%. Data analysis with respect to the casting pattern in all of the four tap-holes has been carried out to calculate the index SF (Volatility of up-thrust) to determine the drainage ability of the different tap-holes. The use of this index can be employed to obtain better casting practice as the difference in slag cutting time in some tap-holes may be identified by the SF value in the range of 80-90%.
During July-August 2021, a complete set of casting data was analysed and it was found that the behaviour of tap-
hole No 4 had a lower SF value than the other tap-holes. This has contributed to non-uniformity in the hot metal and slag compositions (Fig 2). Some preventive measures have been taken such as maintaining the clay quality, reducing the gap time, the size of the drill-bit and so on to arrest this type of uneven behaviour.
2. Volatility of up-thrust in tap-holes of BF#5 (Jul’21)
Cast-to-cast determination of the volatility of up-thrust index (SF) is a useful tool to assess the circumferential symmetry of the hearth which is important in maintaining the lower zone aerodynamics to acceptable limits indicated by a lower permeability resistance index (K value) in the desired range (~65% of total K value). Regular monitoring of this index may facilitate the elimination of dual hearth behaviour as well as consistency in hot metal and slag quality.
Using the deadman Cleanliness Index (DCI) model, the instantaneous determination of this index has been employed using the L-2 system data with respect to hot metal temperature and hot metal composition – including carbon and slag basicity. For BF#5, (Usable volume ~4161m3), the DCI value for better drainage behaviour is expected in the range of 180-250[6]
Using the model, it is estimated that the DCI value for BF#5 is being maintained at ~200 during the majority of casts available. Sometimes a deviation may occur which can be corrected by suitable adjustments. The higher the DCI value, the better is the Deadman permeability.
To create conditions for a good ratio of Deadman/hearth permeability, which will result in proper drainage and a long hearth life, the following are important:
� Good quality coke with respect to CSR and CRI values,
� Elimination of alkali build-up,
� Strong central working to reduce Deadman size and renewal of Deadman coke by central coke charging,
� High degree of indirect reduction to ensure good metal temperature and fluid slag,
� Proper slag regime control to have a fluid low melting slag,
� Maintaining optimum kinetic energy of blast to avoid coke degradation.
Interpreting heat fl ux ratio with coal injection
The descending velocity of the burden in the upper part of the blast furnace decreases as the consumption of coke by combustion at the raceway decreases with increased pulverized coal or coal dust injection (CDI) rate. The descending velocity of solids controls the absolute value of the heat flux ratio (HFR); and the distribution of gas velocity controls the heat flux ratio in a radial direction. It is important to control the lo/lc (ratio of layer thickness) near the furnace periphery to avoid creating a significant imbalance of the heat flux ratio in a radial direction.
Using the calculation model of heat flux ratio, the index HFR has been calculated for BF#5, ISP. It was found that with an increase of coal dust injection rate the heat flux ratio decreases in a linear manner with a best fit line of R2~70-80%. At the prevailing furnace operating conditions, HFR is calculated in the range of 0.75-0.80 (Fig 3). The index is sensitive with respect to the CDI rate and level of oxygen enrichment. It also influences the top gas temperature in a manner that for each increment in HFR of 0.01, the top gas temperature decreases by approximately 10oC[7]
3. Correlation between Heat Flux Ratio and CDI rate in BF#5
The study of this index gives an indication of the heat balance in the upper and lower part of the furnace. When CDI rate is increased, the heating rate of the burden in the upper part of the furnace increases resulting in a decrease of HFR and hence increase in top gas temperature. Maintaining the index in the range of 0.750.80, gives the operators a tool to fine-tune the blowing parameters through blast modification with respect to the CDI and oxygen enrichment ratio.
1. The use of a cohesive zone model helps in assessing the shape of the cohesive zone (inverted V, L or W type), through which the burden distribution as well as blast modifications may be optimized.
2. The use of the Deadman cleanliness index (DCI) and volatility of up-thrust (SF) indices help in devising the optimum casting strategy for proper drainage of slag and metal and also to maintain a healthy and active hearth.
3. An instantaneous record of the heat Flux Ratio (HFR) index in the range 0.750.80 facilitates achieving the desired heat balance in the lower and upper part of the furnace and enables a higher CDI rate while controlling the top gas temperature.
4. The percentage of prepared burden can be increased to the maximum (~90%) while maintaining consistency so as not to disturb the position and shape of the cohesive zone.
5. For proper drainage of the furnace, the deadman cleanliness index (DCI) should be maintained at >180 and volatility of liquid up-thrust in the tap-holes be maintained at >90%.
6. The Heat flux ratio index can be used to regulate a high coal dust injection (CDI) rate of (>130 kg/thm) along with higher oxygen enrichment (~5%) to control the top gas temperature.
The authors express their sincere gratitude and thanks to the management of ISP and RDCIS for their kind help and guidance to complete the research work.
References
1. V Narayanan, R Jaffrullah & R N Singh, TAP on BF Ironmaking (2002) Lecture-6
2. C R Shrinivasan, M N Thakur, R K Verma & S K Ojha, Iron Ore Processing & BF Ironmaking, p20
3. Y Omori, Editor, Blast Furnace Phenomena and Modelling, Elsevier Applied Science (1987), p24, 297
4. N Standish & L Colquhoun, Blast Furnace Aerodynamic Proceedings (1975), p915
5. Geerdes M etal; Modern Blast Furnace Iron-making (Third Edition, 2015) p55
6. Kobe Steel Technical Report, ISIJ International (1986) p841
7. K Ishii, Editor, Advanced PCI Technology & BF Ironmaking, Pergamon, ISIJ (2000), p143-145
The most technically advanced coil joining equipment available. Period.
Guild International can design and build the welding machinery you need to keep your coil processing lines up and running smoothly and profitably. We are the world leader in supplying highly-engineered coil processing equipment known for reliability and performance. Contact us today to begin designing the perfect coil joining equipment for your processing lines.
For more information, visit our website at www.guildint.com or call +1.440.232.5887 World Leader in Coil Processing Equipment for the Steel Processing, Tube Producing and Stamping Industries Since 1958
Direct reduced iron (DRI) is an increasingly popular raw material for green steel due to its sustainability benefits. But, producing it at scale depends on having the right process equipment, including motors and drives, explain Pasi Mannisto and Daniele Pedron*
THE global steel and iron industry is responsible for approximately 7% of total greenhouse gas emissions. To achieve the Paris Agreement’s objectives, the sector must cut its CO2 emissions – currently over 2.8 gigatons (Gt) annually – by over half before 2050.
Achieving this large-scale emission reduction will not be simple. It will involve a wide range of strategies.
These strategies encompass enhancements in energy efficiency, the incorporation of sustainable energy sources like wind and solar power, explorations into the viability of hydrogen or biogas as substitutes for coal in the initial stages of iron production, and amplified investments in digitalization to enhance safety, streamline processes, and extend the lifespan of machinery.
Another factor that will be essential to minimizing emissions is an increased use of direct reduced iron (DRI).
Effective DRI production, however, depends on the right choice of motors and variable speed drives (VSDs) to power various compressors, fans, and pumps throughout the process chain.
Steel production, today and in the future
Steel is produced today using either of the two main steelmaking routes. The most common one is the use of a blast furnace to produce liquid iron and a basic oxygen furnace to refine it into steel (BF/BOF). This approach accounts for 70% of global steel production and emits approximately 1.8 tons of CO2 for each ton of crude steel.
A more sustainable alternative is the direct reduction of iron ore using a shaft furnace. This process removes the oxygen from the ore while it remains solid (without melting, as it would in a blast furnace). Chemical reactions within the shaft furnace occur through the involvement of reducing agents, which include carbon monoxide, natural gas, hydrogen, or green hydrogen. Since this eliminates the use of coke (coal charcoal, which is nearly pure carbon), it produces significantly lower CO2 emissions. The resulting product, DRI, can then be used as feedstock in an electric arc furnace (EAF), to again refine it into crude steel.
The DRI-EAF process accounts for around 30% of global steel production and emits around one ton of CO2 for each ton of
*Global industry segment managers, ABB Motion
crude steel if natural gas is used. A further benefit of an EAF is that it can be rapidly started and stopped, enabling the mill to adjust production to suit demand. In an optimal scenario, hydrogen is employed in place of natural gas during DRI production. This brings the emissions of the entire DRIEAF process down to 0.2 tons of CO2 – or even zero, if the hydrogen is produced using renewable power – for each ton of crude steel.
The adoption of the different approaches varies significantly. China, for example, produces about 60% of the world’s steel and relies heavily on BOF (90% compared with 10% EAF). In Europe, the share of EAF is greater, at about 40%, and in the US it reaches about 75%.
The production of DRI demands substantial quantities of gas. The movement of this gas is managed through an array of motor-driven compressors and blowers. Each motor presents a chance to conserve electrical energy, thus contributing to emission reduction efforts. Variable speed
drives offer an additional advantage by allowing finer control over the motors that regulate gas flow. This heightened control enhances the overall quality of the endproduct. Moreover, these drives enable operations at optimal efficiency levels by ensuring that a motor only consumes the precise amount of electricity needed for the required gas flow.
Moreover, motors and drives need special construction procedures, tests, and certification to guarantee safe operation. Given that the gas within the compressors can lead to a potentially explosive environment, it’s imperative to use certified IEC Zone 2 motors or motors corresponding to Division 2 for NEC-CEC standards. Incorporating digitally connected motors and VSDs offers an additional advantage by providing operators with real-time data. This data empowers operators to make informed maintenance choices, enhancing the overall efficiency and reliability of the system.
Motors play a particularly crucial role in the operation of centrifugal process gas compressors (PGCs). For a direct reduced iron furnace with an annual capacity
of 2-2.5Mt, it’s typical to have two compressors. These compressors typically possess power capacities ranging from 8 to 15 megaWatts (MW). When combined with VSDs, these compressors offer enhanced process control and seamless start-up capabilities. In the absence of VSDs, gas flow regulation would rely on inlet guide vane (IGV) valves. However, this approach can introduce a host of process control challenges and complications in achieving smooth direct on-line (DOL) motor starting. Motors also power the centrifugal cooling gas compressor (CGC). Here, a single IEC Zone 2 motor ranging from 3 to 8 MW is suitable. Given the significance of controlled start-up in this application, drives come into play to facilitate a seamless process. These drives enable a gradual acceleration, bringing the motor up to full speed without causing electrical disturbances to the supply network or undue mechanical strain on the machinery. The implementation of VSDs brings about the advantage of precise control over speed, flow, and torque. This ensures a consistent output by adapting to evolving conditions, thereby maintaining operational stability.
The process gas (PG) heater relies on one or two fans – if this component fails, the entire plant has to stop, so high reliability is essential. A typical safe area fan motor has a power range from around 500 kW to a maximum power of 1 MW.
The gas humidifier, meanwhile, uses five or six centrifugal water pumps, each with a power range of 500 to 800 kW. In these applications, flow is often still regulated using control valves and direct on-line motors, but VSDs are increasingly popular since they enable better flow control.
The CO2 removal system (also called the carbon capture system) uses centrifugal or reciprocating compressors to reduce emissions. The captured CO2 can be stored or used by other businesses, such as those in the food and beverage or chemical sectors. If a DRI facility transitions to using hydrogen instead of natural gas, there is no longer a need for CO2 removal since the only by-product is water vapour.
The hot DRI – at over 600°C – is transported to the EAF using a pneumatic transport system (PTS) powered by a screw pneumatic transport compressor (PTC). The PTC typically uses a single 2 to 3 MW Zone
2 DOL motor. The PTS uses a non-reactive carrier gas, such as nitrogen, to maintain the quality of the hot DRI.
The heat from the hot DRI can be
sufficient network connection from the utility grid. As a result, it uses an on-site gas turbine to provide power. Six medium voltage (MV) motors, rated between
recovered in the melt shop, resulting in energy savings.
When the melt shop is unavailable, an external DRI cooler is used to store the product as cold DRI and subsequently as hot briquetted iron (HBI) using briquette machines driven by motors and drives.
An EAF is a type of furnace commonly used for melting scrap steel and DRI through the application of an electric arc, which may demand power levels reaching several hundred MVA. The supplementary components, such as de-dusting fans and water-cooling pumps, are all fitted with drives. These drives are designed to ensure that the motors function at their designated speeds throughout the smelting process. Additionally, they can be slowed down, conserving electricity, when a reduced speed is sufficient, such as during the furnace charging phase. This capability facilitates swift furnace start-ups and shutdowns, ultimately leading to increased productivity.
These are just a few of the largest powerconsuming applications involved in green steel production. In a real-life steel plant there are tens, if not hundreds, of different applications that can benefit from low and medium voltage motors paired with VSDs.
The Al-Tuwairqi steel mill complex in Karachi, Pakistan, struggled to secure
2000 and 6150 kW, play a vital role in DRI production, but bringing them online requires a huge amount of starting current, which can cause issues with on-site generator stability.
To overcome this issue, the operators selected a single ABB ACS5000 MV drive system to bring the motors online in sequence. The drive has increased the reliability of the plant’s network and means it does not need to upscale its turbine to enable motor start-up. It has also reduced maintenance costs for the plant and is expected to extend the lifetime of other electrical and mechanical equipment on the network.
Green steel is essential to our global goal of achieving net zero carbon emissions. Using DRI is a viable, effective way to produce green steel. This is evidenced not only by the existing operational plants across the globe but also by the growing count of newly announced and planned installations.
To ensure that the process is as efficient as possible, operators must consider not just the direct emissions, but the electricity used – and switching to highefficiency motors and VSDs is a clever solution. Adopting this technology is better for everyone: mills are safer and more productive, they emit less, and customers benefit from higher quality products. �
There is an almost universal recognition that hard-to-abate sectors, including steel, must move urgently to decarbonize both for their own survival and the good of the planet. By Marian D’Auria*
WE can’t do without steel. It’s the economic bedrock of almost everything that surrounds us today – infrastructure and energy, housing and transportation. And it will be at the heart of everything that enriches tomorrow – wind turbines and solar farms, electric cars and green cities.
Today, revenues from iron and steel are about $1.7 trillion. By 2050, as countries like India further urbanise and industrialise, that’s projected to pass $2.5 trillion – close to a 50% increase.
But we must do without its dark side: CO2. Steel already accounts for some 8% of global CO2 emissions. Allowing for the increased demand between now and 2050, there is no practical answer to achieving net zero, without sustainable steel production.
Our industry must make radical changes
For the new hydrogen economy to work, the ingredients must be right. LIBERTY has found that full set of very special ingredients in Whyalla, South Australia – a place where we can see the future of sustainable steel.
Whyalla’s first advantage is that the whole region at the head of the Spencer Gulf is a sun and wind trap. A natural
to combine steel recycling, renewable energy and breakthrough technologies such as hydrogen, to produce green iron and steel.
And at the same time, we must work to develop and attract the skills we will need to transition our workforce towards low carbon production techniques.
There is a huge opportunity here, but it requires collaboration across the value chain to bring it to fruition.
The Boston Consulting Group says eliminating emissions from the global steel industry could require investments of up to $3 trillion by 2050, including the energy infrastructure required to support the transition.
So there is a real opportunity here for asset owners looking to deploy capital in areas which will significantly accelerate decarbonization.
The most exciting opportunity, we believe, is hydrogen. It can take the steel industry from one of the highest polluters to among the cleanest and greenest. In return, steel can enable hydrogen to scale up and nurture whole new industries.
But there are two big blockers. First, producing hydrogen is extremely energy intensive. Second, hydrogen cannot yet be economically and environmentally shipped and that is why the coming hydrogen economy must prioritise locations with major renewable energy production potential. Hydrogen works better where it is produced.
battery, endlessly recharged by natural resources. A perfect source for production of green hydrogen.
A second major advantage is just as important: Whyalla is next to some of the highest-grade magnetite iron ore deposits anywhere on Earth. At present, LIBERTY has easy access to four billion tonnes of it, with billions more still beneath the surface.
(Pic 1)
* Global head of risk & sustainability
High-grade magnetite is key to green steel production since it requires so much less energy to turn it into Direct Reduced Iron (DRI) that can be easily stored and shipped. And then easily and safely transported to wherever it’s needed, to be turned into green steel – again with lower energy inputs.
And Whyalla has the rail and port infrastructure needed to move and ship
Steel Times International is the key publication for the steel market, reporting on iron and steel making issues from all corners of the globe.
The Steel Times International Directory is the essential guide to steel manufacturers, producers, suppliers of plant equipment and services to the steel industry. Order your print or digital copy priced from £105 or subscribers.
Packed with information on the steel industry and continually updated with news for steel professionals, www.steeltimesint.com features special articles and interviews with leading industry gures.
A round-up of the top news stories is sent to more than 7,000 industry professionals each week. You can register online to receive the weekly newsletter and keep up-to-date with the latest news from across the steel manufacturing industry. www.steeltimesint.com/e-newsletter
large quantities of green iron. (Pic 2)
On top of these natural gifts, Whyalla has a workforce that literally grew up around iron and steel production. We have established a local workforce planning team and a training academy and transition centre within the community. These facilities are closely linked with the GREENSTEEL Academy and state and federal training institutions like the University of South Australia and the University of Adelaide. These initiatives meant we were able to redeploy every colleague affected by the closure of Whyalla’s coke ovens into other parts of our business. (Pic 3)
In Whyalla, we benefit from the forwardthinking, forward-acting Government. Australia’s Prime Minister Anthony Albanese and South Australia’s Premier Peter Malinauskas recently showed their support by attending the closure of Whyalla’s last coke-fired ovens after 55 years of service to make way for green technology. South Australia has just named the preferred contractors to build a hydrogen production
facility, hydrogen power plant and a hydrogen storage facility there.
Partnership across government and the supply chain can develop solutions that lower investment risk, enhance returns and
Pic 4
play to natural regional strengths. (Pic 4)
Many advanced economies and forwardlooking companies are looking for similar solutions, and we are starting to see other embryonic magnetite/hydrogen hubs in Brazil, the United Arab Emirates and Africa. To embrace these green hydrogen opportunities and make production
Pic 5
competitive, we will need evolving technologies and economies of scale.
Steel plants were traditionally situated near primary energy resources such as coal. As we move away from coal, the key lies in integrating renewable energy sources into the entire supply chain – sourcing, manufacturing, and logistics.
The essence of our model is to bring our magnetite resources to our sites and partner countries with abundant renewable power – such as Romania with its plentiful sun to power our solar farms, strong Black Sea winds and abundant natural gas. This will enable us and them to develop downstream hydrogen operations and supply chains – green iron production hubs, or ‘green valleys’ as the European Union is calling them. (Pic 5)
Our partners, whether government or corporate, will then be able to transform the green iron they offtake into steel production assets. These new hydrogen hubs will be able to exploit their natural advantages to develop a diversified, sustainable economy for future generations. (Pic 6)
We’re increasingly seeing governments across the world shape policy to support demand for sustainably produced steel - Europe’s Carbon Border Adjustment Mechanism, Contracts for Difference in Australia and Romania, and US hydrogen hubs for example. Pic 6
The private sector in industries that rely on steel is adapting too. In construction, the drive for building stock certifications is raising demand for sustainable building materials from companies like Australia’s Lendlease and Sweden’s Skanska. In the automotive sector, companies such as Volvo are driving green steel initiatives in the USA.
Just as important as getting the financial model right is meeting the challenge of workforce transition. GFG employs almost 30,000 people globally and our steel plants
have been at the heart of their communities for decades.
We must help existing colleagues reskill and retrain so they can deliver as much to our industry’s future as they have to its past. Failing to manage their transition properly will jeopardise the industry’s ability to move into the clean steel era.
We are committed to sustained engagement with employees, unions and communities on the challenges of transition. As we transition to clean steel we must explain decarbonization as a value driver and an opportunity rather than a
It is important for all stakeholders that we move towards action. We’ve already announced the first projects in Europe to transition away from BF to EAF technology in Czechia, Hungary and Romania. (Pic 8)
There is concrete evidence that, by being ready to adapt to change, embracing new partnerships and supply chain models, we can win market confidence and cut to a bright future for our industry and all who rely on it. �
The PROFILEMASTER® SPS is a light section measuring device for measuring contours and dimensions on profiles of all kinds in cold and hot steel applications.
Benefits:
Maximum measuring accuracy thanks to temperature-stabilized measuring systems
Shape fault detection (SFD) thanks to high sampling rate
High-precision measurements
Detects process problems at an early stage
Fast maintenance and easy cleaning
Post-2030, the steel industry is likely to undergo a profound transformation. Hydrogen will be the next big thing, but the utilization of all possible decarbonization paths will be necessary to make the transition successful, says Nils Naujok* and Holger Stamm*
1. How are things going at Oliver Wyman? Does the steel industry keep you busy?
We have been actively engaged in advising on the various aspects of the structural challenges the transformation has created – from supporting the transition to green steel to optimizing cost efficiency, organizational design, commercial excellence, and the production network. The decarbonization of steel has pushed us to address related challenges in other industries, such as energy. Our steel clients are looking for a smart, commercially viable energy strategy to power their green transition. Taking this kind of holistic approach has afforded us the opportunity to help the demands of not just the steel industry but several others struggling to develop viable green business models.
2. What are your views on the state of the global steel industry?
We’re bullish. Demand for green steel will see significant growth over the next five years and over the next decade. Evolving environmental regulations, technological advancements, new business models, and strategic partnerships are reshaping steel’s landscape with the goal of achieving a sustainable future.
3. Decarbonization is high on the agendas of steelmakers around the world. How will things pan out in terms of reaching climate goals by 2030? Are you optimistic?
While the goal of drastically reducing carbon emissions by 2030 is ambitious, the decarbonization of the steel industry is essential for the global economy to reach net zero. Steel is a building block of the economy, and one of the highest decarbonization levers available. The use of green hydrogen will be a gamechanger for the sector. And green steel can help decarbonize the auto and construction
industries All this makes us optimistic that progress will be made. The steel industry can be a frontrunner for decarbonization. If it misses its targets, it will be because of the lack of affordable green energy and resources and could lead to losing significant steelmaking capacities in Europe. to vanish from some locations, but other industries connected to the steel network will follow.
4. Are we likely to see a two-tier steel industry with some manufacturers producing ‘the gold standard’ – fossilfree steel – and others producing ‘less pure’ products?
In considering the trajectory toward fossil-free steelmaking, the development of a two-tier steel industry is a possibility. However, the growing divide between traditional steel production in some countries and innovative transformations to green steel in others will be the root challenge as the ramp-up of grey capacities is still ongoing in certain areas and will have a negative impact on global CO2 emissions. There is a need for a level playing field that balances grey and green volumes. On standardization, the only chance for the industry is that the product referred to as ‘the gold standard’ now becomes the usual standard and the green transformation in Europe acts as a blueprint for other regions. The key lies in fostering profitable and sustainable green markets in Europe.
5. It is often said that countries with renewable energy sources will change where steel is made. Thoughts? This is particularly relevant for the Middle East. We see the current role model of an integrated steel producer being reconsidered. Decoupling upstream and downstream production makes a lot of sense from an investment and capability point of view as the activities, especially in the Middle East, are accelerating. We see lots of new ventures in the fields of green hydrogen, green DRI, and green steel as well as projects from Chinese, Japanese, and Indian steel companies globally.
6. How do you envisage the decarbonization situation post 2030? Post-2030, the steel industry is likely to undergo a profound transformation. It is true that hydrogen will be the next big thing, but the utilization of all possible
decarbonization paths will be necessary to make the transition successful.
On one hand, the use of more circular, scrap-based steel production is advertised as the preferred method, using natural gas and/or hydrogen for DRI. Furthermore, new innovative technologies like direct electrolysis of iron ore are a promising route for CO2-reduced production processes. CCU and CCS give traditional steel producers the chance to show decarbonization progress. The fact that industrial carbon dioxide will be a crucial and scarce raw material when BFs disappear shows that the traditional route can still make a positive impact and offer new business opportunities.
7. There will always be a place for the blast furnace even though EAF steelmaking has become far more sophisticated. Do you agree?
Blast furnaces have been a foundational element of steel production for centuries and offer certain advantages, especially in terms of quality and production capacity. They are well-suited for largescale operations, and offer an economical solution when high volumes of steel need to be produced consistently.
However, there are green ways of production, such as combining DRI with a smelter instead of an electric arc furnace, that offer similar qualities to steel produced in the BF.
Additionally, the definition of new standards and grades for steel qualities in a green context is one of the questions that must be answered in collaboration with end user industries to ensure the fulfillment of customer satisfaction. There is no need for BFs in the future.
8. Is the USA’s journey toward fossilfree steelmaking shorter than that of the rest of the world?
The US has an advantage over Europe, no doubt, with its large number of electric-arc furnaces but whether it is shorter than the rest of the world is a nuanced question.
The USA has extensive access to renewable energy sources, particularly in the Midwest, where plenty wind and solar resources provide a stable foundation for green energy supply. The USA shows a high commitment to R&D by continuously exploring further possibilities of CO2reduced production processes.
It is important to emphasize that the
decarbonization of the steel industry is a global effort towards achieving climate goals.
9.The Swedes appear to have things sewn up where hydrogen steelmaking is concerned, but what other nations are worth watching?
Germany has been a frontrunner in implementing ambitious climate targets and actively investing in CO2-reduced technologies along with exploring options for hydrogen-based steelmaking. The transition in Germany has accelerated and is driven by a clear government strategy to support the ramp-up of green steel.
Additionally, the MEA region must be considered an emerging frontrunner in green steel production as it has abundant access to solar and wind energy and is strategically investing in renewable energy, which enables them to reduce their carbon footprint and position themselves as leaders in the global energy transition. The combination of renewable energy, supportive government policies, strategic investments and geographic proximity to key markets is bound to become a major player in green steel.
10. Is enough is being done to make steel a more sustainable product?
Steel is 100% recyclable, which makes it a sustainable material in itself. The steel industry is constantly looking for opportunities to foster circularity and build sustainable partnerships.
The urge and desire for sustainability and circularity is clearly noticeable throughout the whole value chain.
11. How optimistic are you for the global steel industry going forward? We must be optimistic so that we leave our children a world worth living in. And the lever of the global steel industry for global decarbonization is significant.
In Europe we can showcase the idea that it’s possible to combine environmental and economic interests and build lead markets that are profitable and green.
On this journey, we certainly face various challenges such as
• The availability and costs of renewable energy,
• The ramp-up of green hydrogen production, networks, and costs,
• The management of huge CAPEX projects to build the new, green assets,
• The availability of DRI-ready iron ore and the creation of green lead markets based on green-steel premiums.
12. What’s happened to those old chestnuts, Chinese overcapacity, countervailing duties, and tariffs?
They are very much alive and kicking, even if green production capacity can ramp-up while grey capacity is still growing. The problem is that there is a way to get around the Carbon Border Adjustment Mechanism (CBAM) by simply sending your green steel to Europe while sending the grey to regions with no carbon adjustment. This will not provide a level playing field for green steel globally and will stand in the way of development of a sustainable and profitable green business model. CBAMs and tools like them need to consider not only green volumes exported to Europe, but also grey volumes produced in parallel.
Global overcapacities are growing with investments in China and India and we see the danger that emissions-intensive over-production could displace green production. In 2030, the share of planned DRI capacities will be only 6% of global primary steel production.
13. How do you define green steel?
Green steel refers to steel production processes that aim to minimize or eliminate the environmental impact caused by steel manufacturing.
But a clear and standardized definition is still needed and wanted by many steel producers and users. It can get very complex to use different labeling systems when defining green steel.
For instance, we combine the share of scrap in steel along with specific scope 1, 2 and 3 emissions to define different grades up to “near-zero steel” as shown by the German Federal Ministry for Economic Affairs and Climate Protection and various stakeholders.
14. How important is scrap metal?
Scrap provides the opportunity to reduce the carbon footprint of steel production immediately, before DRI/HBI becomes available. That’s significant. From our perspective, one of the key success factors for future green steel companies is being able to balance DRI versus scrap. Thus, scrap should become a critical raw material for the European steel industry, the same way it is in the US. �
Scottish ironmaster David Mushet was the subject of an article published in Mechanics Magazine in 1825 in which the subject of carrying out antiquarian research to record blast furnaces in Sussex and Gloucestershire was discussed. Mushet was known for his inventions in the field of metallurgy and was an early advocate of animal rights and an opponent of vivisection...but not a vegetarian. By Tim
THE item below was published in ‘Mechanics Magazine’ Vol 3 published in London in 1825.
It is a report on a commentary or letter by David Mushet, a Scotsman who came to the Forest of Dean and set up an ironworks there – later to be run by his son Robert whose fame was to be his development of alloy steels and for showing Bessemer how to make sound steel by the addition of the high manganese iron alloy, Spiegeleisen to de-gas it. The report in the Mechanics
Magazine does not state if the comments were by David Mushet (1772-1847) or his son Robert, but since Robert (1811-1891) would have been only 14 at the time of publication, we can assume the comments came from the senior Mushet, David.
In the report David Mushet advocates the carrying out of ‘antiquarian research’ to record blast furnaces in Sussex and Gloucestershire (including the Forest of Dean) and elsewhere, fixing the date of the earliest blast furnace in England at about
*Secretary, Wealden Iron Research Group
Smith*1550, whereas the earliest documented record of a blast furnace in Great Britain was 1490 at Buxted in East Sussex.
The report reads:
Mr Mushet, one of the most scientific and ingenious of our iron masters, has, in some late inquiries into the history of the discovery and use of cast iron, appeared disposed to fix its date in England about the year 1550; before which time it appears that the art of casting iron was unknown, and he supposes it to have been an English
(1) In a footnote the Editor of Mechanics Magazine says: ‘We suspect this calculation has not been recently made. The amount of the manufacture for the present year is certainly much greater.’
8 print copies and a printed copy of the Steel Times International Directory
Digital copy of the magazine delivered to your inbox every month
Access to our digital archive of past issues and webinars
Weekly Steel Times International newsletter
PLUS access to all digital issues of Furnaces International
With a digital subscription you will receive all the benefits of the Print + Digital option, excluding print copies! Choose your subscription package...
Steel Times International is a leading publication serving the global steel industry and offering its readers a strong focus on all aspects of the production process embracing both basic oxygen and electric steelmaking. Contact us today
subscriptions@quartzltd.com to take advantage of our special subscription packages. WWW.STEELTIMESINT.COM DIGITAL ONLY SUBSCRIPTION
invention.
He continues:
There were in England and Wales, in the year 1720, fifty-three blast furnaces employed in making 17,350 tons yearly, or a little more than five-tons of pig iron each weekly. At that period fourteen of these furnaces existed in the two south-eastern counties of England, Kent and Sussex, where now (ie 1825) one, at most, survives near Battle.
Mr. Mushet suggests, as a curious matter of antiquarian research in Sussex and Gloucestershire (including the Forest of Dean), and several other counties, to ascertain the date and place of erection of the first tall blast-furnace in England for the making of cast or pig-iron. At present the size and number of these furnaces are so wonderfully increased in Britain as to manufacture nearly half a million tons of pig-iron annually(1), with a consumption of pit-coal, in all the attendant manipulations, equal, at least, to five million tons annually.
However, here Mushet was closer to reality with output of pig iron in Great Britain for 1825 being recorded as 578kt in
a list compiled by Staffordshire Ironmaster Francis Finch.
In reality, the first furnace to come to Britain used Walloon technology brought by immigrants from present-day Belgium. Built at Buxted in an area known as ‘Iron Plat’ documents record ‘iernefounders at Buxstede’ in December 1490 (Lambeth Palace Library, ED 1352). The furnace is also known as ‘Queenstock’ and is reputed to be the first place where guns were cast as whole units, ie with an integral breech,
around 1540.
William Hogge, an illiterate ironmaster, is credited with first doing this, although there is evidence that his former employer, the Rev William Levett, pioneered the casting of whole guns.
Regarding the end of the era in Southern Britain, the last furnace to close was in 1813 at Ashburnham, which, indeed, is just four miles from Battle, although its associated refining forge continued until 1827. �
Q-ONE reduces EAF overall OPEX with a shorter power-on time and very low network disturbances. It is a scalable system that can be implemented on new or existing AC EAFs, and it can be directly powered by renewable energy sources.