Since 1866
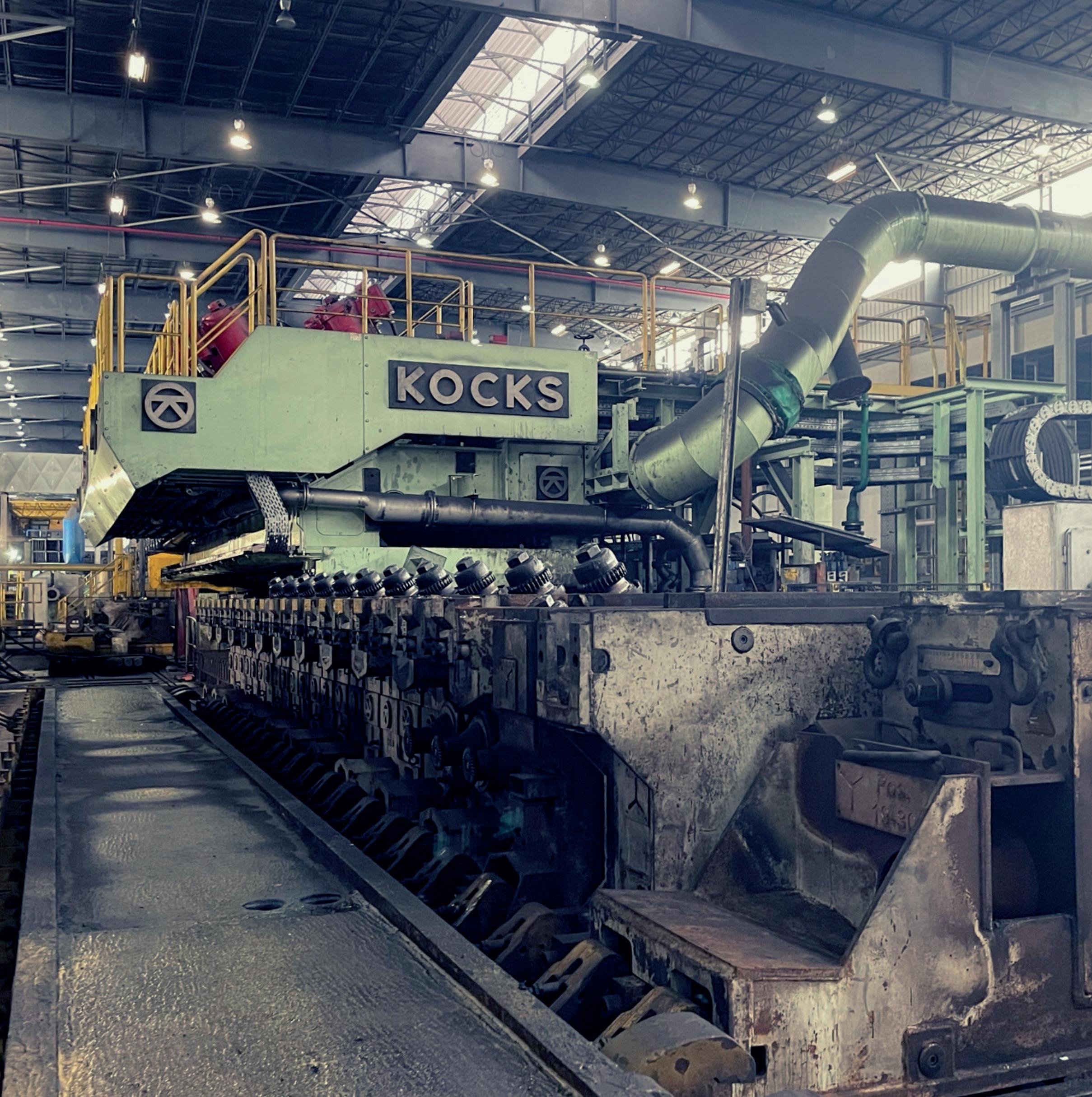
Since 1866
The rst continuous monitor of strip cleanliness providing real-time data with unprecedented precision that distinguishes between oil and iron nes contamination.
The only system to differentiate between Oil and Iron Fines
Real-time cleanliness monitor for strip processing lines
Utilising Laser Induced Breakdown Spectroscopy (LIBS)
sales@sarclad.com
sales@sarcladna.com
sarclad.com
sales.china@sarclad.com
sarclad.india@sarclad.com
Non-contact sampling
20Hz sample rate
Eliminates need for ‘tape test’
EDITORIAL
Editor
Matthew Moggridge
Tel: +44 (0) 1737 855151
matthewmoggridge@quartzltd.com
Assistant Editor
Catherine Hill
Tel:+44 (0) 1737855021
Consultant Editor Dr. Tim Smith PhD, CEng, MIM
Production Editor
Annie Baker
Advertisement Production
Carol Baird
SALES
International Sales Manager
Paul Rossage paulrossage@quartzltd.com
Tel: +44 (0) 1737 855116
Sales Director
Ken Clark
kenclark@quartzltd.com
Tel: +44 (0) 1737 855117
Managing Director
Tony Crinion tonycrinion@quartzltd.com
Tel: +44 (0) 1737 855164
Chief Executive Officer
Steve Diprose
SUBSCRIPTION
Jack Homewood
subscriptions@quartzltd.com
Tel +44 (0) 1737 855028
Fax +44 (0) 1737 855034
Steel
2 Leader by Catherine Hill.
4 News round-up
Two pages of global steel news.
6 Innovations
New products and contracts.
17 USA update
The saga continues: Nippon’s bid for US Steel.
21
Latin America update Brazilian and Mexican electrical steel markets.
25
India update
India aims for self-reliance.
28
China
China’s hydrogen strategy: national versus regional plans.
32
Hydrogen reduction
Hydrogen unleashed: opportunities and challenges.
38
Green hydrogen
Green hydrogen for the steel industry – requirements for success.
42
Sustainability leaders
GravitHy: dragging emissions down.
48
North American markets
‘Hydrogen is the future’
52 Perspectives Q&A: Kanthal Heating steel, cooling the planet.
54 History
Coalport Bridge – a later cousin to Iron Bridge.
42
In 1671, the Irish scientist Robert Boyle discovered and described the reaction between iron filings and dilute acids, which results in the production of hydrogen gas; ‘’So inflammable it was, that upon the approach of a lighted candle to it, it would readily enough take fire, and burn with a blewish flame with little light, yet with more strength than one would easily suspect.’’
Hydrogen, part of a planetary makeup that sustains stars and planets, is instilled in public imagination in its many forms; a complex sustainability saviour for heavy industries, galactic swirlings captured in the sky, flames licking the Hindenburg as it collapsed over New Jersey in 1937. The mythos that surrounds hydrogen is much what Boyle appeared to predict; a chemical with the capacity to overspill, and to set alight. In the three centuries that have passed since Boyle’s discovery, scientific advances have wrought an alternative, and nuanced language to understand the periodic table. Hydrogen’s capacity to produce the intense heat required for industrial production has led it to become somewhat of a paraded
new technology in the context of steel decarbonization; the movement away from carbon-rich fossil fuels into a clean industrial feedstock which powers furnaces, without the planet-killing smoke. That’s not to say that the adoption of hydrogen technology will be an easy feat; alongside its touted high performance as a fuel source are logistical challenges, such as its storage, transportation, and its fickleness, or tendency to explode. Such are the complexities of working with an element that contains ‘more strength’ than expected; the expectation belies its faculty to perform and adhere to no will other than its chemical potential. As Soroush Basirat states on p.32, ‘green hydrogen comes at a high cost’, yet projects like Nel Hydrogen’s electrolysis plant at Ovako’s steel facility in Sweden (p.38) are shedding light on its inherent sustainable capabilities. As said by Roald Dahl; ‘‘My candle burns at both ends/it will not last the night/but ah my friends and oh my foes/ it gives a lovely light”. The industry cannot solely rely on hydrogen as an omnipotent saviour, but what is burned, will burn bright.
Scientists at the Max-PlanckInstitut für Eisenforschung, a centre for iron research, have shown how green steel can be produced from aluminium production waste. In an electric arc furnace similar to those used in the steel industry for decades, they convert the iron oxide contained in the red mud into iron using hydrogen plasma. With this process, almost 700Mt of CO2-free steel could be produced from the 4 billion tons of red mud that have accumulated worldwide to date – which corresponds to around a third of annual steel production worldwide.
Source: Phys Org, 4 February 2024
Tata Steel's Kalinganagar and Meramandali plants in Odisha have received the Responsible Steel certification, a company statement said. Responsible Steel is a global multi-stakeholder standard and certification initiative that works with
South Korea's POSCO Group and the United Arab Emirates' Abu Dhabi National Oil Company (ADNOC) will collaborate on blue hydrogen production facilities in Gwangyang to supply steelmaking, according to a report by Kallanish. The two companies signed a strategic collaboration agreement this month at ADNOC's headquarters in Abu Dhabi. Under the agreement, they will build blue hydrogen production facilities at POSCO’s liquefied natural gas terminal in Gwangyang.
Source: Kallanish, 6 February 2024
steel producers, consumers, and intermediaries towards building a sustainable steel industry by addressing challenges including climate change, diversity, and human rights. Tata Steel CEO and MD TV Narendran said, "The Responsible Steel certification for our sites is a testament to Tata Steel's unwavering commitment to sustainability. It reflects our proactive approach towards addressing the evolving challenges of the steel industry and shaping a better tomorrow.’’
Source: The Economic Times, 11 February 2024
ArcelorMittal has indicated to investors that additional capital expenditure projects in the United States could be on its near-term agenda. In a presentation accompanying its 2023 year-end and fourth quarter results, the Luxembourg-based company indicated that its 1.5Mt/yr electric arc furnace (EAF) mill under construction in Calvert, Alabama, is expected to be complete in the second half of this year. Additionally, ArcelorMittal says it is studying an option to add a second 1.5Mt EAF at a lower capex intensity.
Source: Recycling Today, 8 February 2024
Tata Steel has said that it has taken a significant step towards promoting inclusivity by inviting applications from transgender candidates for various positions across multiple locations. "Transgender candidates with any of the following qualifications can apply:
The UK government’s anti-dumping body has recommended that measures limiting the import of certain steel products be lifted after the decision to close the blast furnaces at Port Talbot. The Trade Remedies Authority, which is charged with protecting UK industry from dumped or subsidised imports, said its preliminary view was to advise the UK government’s business secretary, Kemi Badenoch, to suspend safeguarding measures on imports of hotrolled flat and coil steel for a temporary period of nine months.
Source: The Guardian, 9 February 2024
Matriculation in English or ITI or graduation in any discipline or diploma in engineering in any discipline from any institute recognized by AICTE or UGC or Degree in B.E./B. Tech in any discipline from any institute, recognized by AICTE or UGC," the company stated in its job listings.
Source: Outlook India, 13 February 2024
UK-based British Steel has submitted a planning application to the North Lincolnshire Council for its proposed electric arc furnace (EAF) mill in Scunthorpe, which is in the East Midlands region of the UK. The application follows an earlier one submitted to the Redcar and Cleveland Borough Council in northern England in December 2023 to build an EAF at the company’s steel beam mill in that jurisdiction.
Source: Recycling Today, 13 February 2024
Artom Steel
is investing over €6 million to modernize production processes and significantly reduce carbon emissions and fuel consumption. The company is collaborating with metallurgical suppliers, such
Celsa, Spain’s largest private industrial group, is considering the sale of its steel plants in Poland, Norway and the UK. The total market value of the assets reaches €1.3 billion. Celsa’s Polish unit Huta Ostrowiec is likely to attract the most interest from potential buyers and could be worth up to €800 million. The Norwegian plant can be valued at around €300 million, while the British Celsa Steel UK is estimated at around €200 million.
According to the report, Celsa is working with Citi to analyze the triple deal with its foreign subsidiaries.
Source: GMK Center, 14 February 2024
as SMS Spa and Badische Stahl Engineering, to upgrade its facilities in Romania. With around 2,350 people employed at the Resita steelworks, the move towards greener production processes will not only secure jobs but ensure a healthier planet for future generations, the company claims.
Source: BNN Breaking, 15 February 2024
signed a memorandum of understanding (MOU) with Port Pirie Regional Council, a local government area in South Australia, to develop Port Pirie into a future hub for green iron production. This initiative aligns with the global steel industry’s shift towards decarbonization and the anticipated ‘Green Iron & Steel Strategy’ by the South Australian government. The MOU outlines a collaborative effort to engage with state and federal governments, plan for green iron production, and involve the community and First Nations in the process.
Source: Mining Technology, 14 February 2024
Brazilian steel producer Gerdau and local renewable power producer and trader Newave Energia have broken ground on a 420-MWp solar park project in Brazil’s Minas Gerais state. The Arinos Solar
Liberty Galati, a Romanian steel plant that is part of the GFG Alliance group of companies owned by metal magnate Sanjeev Gupta, has announced the restarting of blast furnace No. 5 after it was suspended in January this year.
The company is currently increasing the furnace’s capacity. After reaching the planned capacity of the unit, Liberty plans to resume the operation of rolling lines, including at plants in the Czech Republic and Hungary.
Source: GMK Center, 15 February 2024
Park, as it is named, will require an investment of $302 million, Gerdau said. Arinos' construction is scheduled to be completed by the end of the year. Once the solar farm is up and running, 30% of the output will be used to feed Gerdau's steel manufacturing. The asset's full capacity is equivalent to 7% of Gerdau's total energy consumption in Brazil.
Source: Renewables Now, 16 February 2024
Engineering company Fluor Corporation has been selected by H2 Green Steel to lead the construction of the world's inaugural renewable hydrogen-based 'green steel' mill in Boden, Sweden. Fluor's engagement in the project will involve engineering, procurement, and construction management services for the plant. The plant will feature a melt shop, casting, rolling, and finishing facilities, all designed to operate with renewable hydrogen.
Source: BNN Breaking, 16 February 2024
Jari A. Koskinen, sales manager, Konecranes Industrial Service & Equipment,
modernization of the two ageing cranes
“We leveraged advanced technologies such as our Crane Reliability Study and RailQ to assess
“The heritage protection status of our facility meant there were significant restrictions on how to carry out the project. Konecranes played an
active role in planning the modernization so the historical integrity of the power plant was preserved,” said Petra Väisänen, project manager, Fortum Power & Heat.
Konecranes used a variety of advanced Consultation Services, such as a Crane Reliability Study and RailQ, coupled with a steel structure analysis to take a deeper look at the crane and its components. This analysis formed the basis
for the modernization plan, addressing specific challenges posed by the ageing cranes. The modernization includes the installation of two 87-ton hoists (SMT1925) and two 10-ton (CXT6022) auxiliary hoists, along with the replacement of electrical cubicles, cables and wiring.
A strong focus on customers and commitment to business growth and continuous improvement make Konecranes a lifting industry leader. This is
underpinned by investments in digitalization and technology, plus the company’s work to make material flows more efficient with solutions that decarbonize the economy and advance circularity and safety.
For further information, log on to www.konecranes.com
Primetals Technologies operates three service workshops in China, and recently, the facility located in Changxing, Huzhou City, Zhejiang Province, entered Phase 2 in a strategically planned extension that the supplier says will further enhance the capabilities of Primetals Technologies’ Metallurgical Services organization.
On 29 November, Primetals held a ceremony to celebrate the expansion of the Changxing workshop. Guests from the Changxing government, customer representatives, and members of Primetals’ global executive management team participated in the opening festivities.
“Thanks to the start-up of the Phase 2 facilities, Primetals Technologies will further expand its local service competences,” said Tomislav Koledic, CEO of Primetals Technologies China. “We are now able to provide a wider range of services to meet the ever-changing customer and market requirements, including manufacturing of core equipment, repair, and long-term maintenance work. The range of these services covers the complete production chain, including steelmaking, casting, ESP plants, long rolling, flat rolling, and processing.”
“As an OEM, Primetals Technologies is in a unique position,” said Karl Purkarthofer, global
head of metallurgical services at Primetals. “With the combination of our expertise in processes, technology, electrics and automation and maintenance, as well as upgrading and revamping, we are not only able to improve maintenance results, but also support our customers in their ambition to improve overall plant performance. All this goes hand-in-hand with our motto ‘Next level services now’.”
Established in 2019, the Changxing branch measures close to 13,000 square metres including the approximate 5,900 square metres added in phase 2. The scope of services now includes long rolling and flat rolling mills, continuous casters, the EAF Quantum, and Arvedi ESP lines. Additionally, the workshop now also acts as a platform for advanced condition monitoring and predictive maintenance services.
Thanks to the expanded facilities, Primetals Technologies now aims to expand its Metallurgical Services business across China, with a focus on further developing top-class services for upstream technologies.
New equipment and wider range of competencies allow Primetals Technologies to extend the range of services at the workshop in Changxing. The facility now offers services for
Refurbishment and key component manufacturing for long rolling and flat rolling mills are also part of the scope of services at the Changxing workshop. Morgoil oil-film bearings, which have an excellent reputation in China for their high quality and long lifetime, are an example of rolling equipment being refurbished at the workshop. Equipment from Arvedi ESP lines is regularly maintained at the Changxing location.
For further information, log on to www.primetals.com
the growing numbers of EAF Quantum plants in China – for example, the location executes maintenance work for key components in Primetals Technologies’ scrap preheating system, as well as the EAF Quantum lance tip, an important part of the oxygen blowing and carbon injection processes. This part of the electric steelmaking plant is welded using different materials, which ensures high temperature resistance.
The Changxing service workshop is characterized by lean operations, the concept of smart manufacturing, and the implementation of energy-saving measures. Photovoltaic cells are installed on the roof and will provide 60% of the power required to run the facility.
use on an electric arc furnace (EAF) at the SeAH Changwon
The plant produces 1.2Mt of steel and 1Mt of steel products annually, putting SeAH in the global top 10 of special steel manufacturers. Its
stainless-steel rods and wires made from special steel have end-uses with customers in the automotive, energy and shipbuilding industries.
ABB ArcSave will be installed on an EAF that produces carbon and stainless steel and has a steelmaking capacity of 100 tons. The technology is expected to improve furnace efficiency, reduce energy consumption and overall operating costs on the continuously operated EAF at Changwon. Steelmakers have typically reported yield improvements of up to 1%, productivity increases of 5-7%, and electrical energy savings of 3-5% when deploying the equipment.
The customer will be able to improve metallurgical conditions in the EAF melt using the ABB technology. The stirring solution has optimized the operation of some of the world’s largest arc furnaces and can help reduce the carbon footprint at both existing steelmaking lines and greenfield projects.
“We have experienced the benefits of the ABB
ArcSave first-hand and look forward to further improving the efficiency of our electric arc furnace steelmaking operations with a second installation,” said Eung-Sou Lee, director, production division, SeAH Changwon Special Steel.
“We are very pleased that SeAH Changwon Special Steel has once again chosen ABB to provide this unique technology,” said Zaeim Mehraban, global head of sales, ABB Metallurgy. “It underlines the positive effect that ABB ArcSave has for high-alloy steel producers, including overcoming the challenge of bottom skull formation which can impact steel yield, furnace volume capacity, maintenance costs and downtime.”
The new order, which will be commissioned in late 2024, is the second from SeAH Steel and follows the installation of an ABB ArcSave electromagnetic stirrer on an EAF with a 70-tons production capacity in 2018. By introducing electromagnetic stirring and replacing an existing bottom gas stirring installation, SeAH was able
The installation of IMS’ radar width measuring at steelmaker Salzgitter’s roughing stand has led to a more stable rolling process despite the harsh conditions with high occurrence of splashing water, steam and scale, the company claims.
The radar width measuring system enables stable width measurement at the roughing stand, fulfilling a key prerequisite for improving width performance
The harsh conditions that prevail in the area of the roughing stand, including the high occurrence of splashing water, steam and scale, make it difficult to use optical measuring systems. Optical measuring methods require complex cooling and suction devices as well as extensive maintenance to be able to reliably measure the width through the view of the camera. These are factors that make the use of this method during operation and maintenance very costly. A radar-based measuring method offers a technically and economically attractive alternative.
Several years ago, IMS Messsysteme GmbH, together with Fraunhofer FHR and Salzgitter Flachstahl GmbH, developed a measurement system based on radar technology which for the first time enabled stable, precise width measurement at the roughing stand.
The final installation of the radar width measuring system took place at Salzgitter Flachstahl GmbH between the upsetting press and the blooming train, immediately before the roughing stand – a position that allowed the complete measurement of the width along the entire slab length before each upsetting pass. SMS group GmbH then integrated the radar width measuring system into the automation system. The measuring results obtained during real operations made it clear just how much potential the radar width measuring system has for the optimisation of width performance.
The use of the radar-based width measurement system reliably solved several problems at once, contributing to a considerable improvement in the width of the pre-strip and thereby
to reduce bottom skull thickness from up to 1,000mm to less than 200mm. EAF productivity was improved by between 5-7%, scrap handling costs were reduced by 70-80%, electrical energy savings were at between 3-4%, and there were 40% savings on furnace refractory repairs. Other improvements included easier scrap bucket charging and better melt bath level control and tap weight hit ratio.
Requiring no physical contact with the bottom of the EAF, ABB ArcSave enhances metallurgical performance during the melting of large scrap items, reducing stratification via forced convection. This improves EAF operation by homogenizing temperature distribution and chemical composition, while speeding up scrap and ferroalloy melting compared with natural convection alone.
For further information, log on to https://global.abb/group/en
also the finished strip.
‘‘After we increased the availability of the radar width measurement system together with IMS and SZFG and then integrated it in our automation system as a measuring device, we have been able to achieve significant improvements in process stability. This was only possible thanks to the high reliability of the radar width measurement, even in the harsh conditions in the entry of the blooming train,‘‘said Dr Olaf Jepsen, head of research and development at SMS group GmbH.
The radar width measuring system was commissioned at Salzgitter Flachstahl GmbH back in 2017. Before the newly developed system was commissioned, its measuring accuracy and stability was first verified at the exit of the roughing stand by comparing the results with an optical width measurement system. Once it was moved to its final position right at the entry of the roughing stand, it was ultimately possible to achieve 99% availability of the radar width measuring system despite the challenging conditions there. The maintenance requirements are primarily limited to the cleaning of the measurement window in the scope of regular maintenance downtime. Readjustment and calibration is only rarely necessary, for instance after retrofitting or conversion work in the measurement area.
‘‘Various measuring methods have already been investigated in this challenging environment. However, they all required so much maintenance and had such a high rate of error that permanent availability could not be ensured. Only radar width measuring offers excellent availability alongside minimal maintenance effort,’’said Ingo Leckel, production measuring technology employee for wide-strip hot mills at Salzgitter Flachstahl GmbH, confirming the benefits of the radar width measuring system.
For further information, log on to www.ims-gmbh.de
MIDA–QLP
are the winning Danieli direct-rolling technologies for the most competitive production of long and flat green-steel products.
They are the result of the research and continuous improvement profused over 20 years, along with multi-million dollars of investment.
Their unmatched performances have fueled their success worldwide, thanks to lower resource consumption and carbon emissions, unbeaten OpEx, and outstanding product quality.
So, top technology becomes copied technology, the shortest route for competitors that, abandoning their solutions, now try to imitate MIDA–QLP and QSP–DUE Equipment and layout may be copied, but experts know that details make the difference.
Automation and process solutions are not easy to copy, and this will be the experience of anyone trusting in those imitations.
The competitive advantage for our customers, obtained by field results, is the best defense for our technology – more than court rulings protecting our patents.
Danieli offers the best guarantees for speedy learning curves, steady performances, and now Digital Plants with no men on the floor. Buy the Original.
GIANPIETRO BENEDETTI CHAIRMAN OF THE BOARD OF DIRECTORSArvedi AST (Acciai Speciali Terni), a European stainless steelmaker, has chosen plant supplier Fives to take a digital step forward to transform its production management.
Eyeron®, an intelligent quality management system developed by Fives, was installed across the entire integrated plant of Arvedi AST with the aim of streamlining the production process and taking quality management to a higher level.
“We had, on one hand, a huge amount of process data handled by different systems across several steel manufacturing workshops, and, on the other hand, demanding requirements regarding coil quality from individual customers. Therefore, our primary goal was to find a digital solution that would allow us to consolidate process and quality-related information on a single device, increasing efficiency and significantly
improving quality control,” said Gian Piero Ruello, coil intelligent processing project manager at Arvedi AST.
“Eyeron® fundamentally transformed our company’s work philosophy, enabling proactive quality control and production issue prevention. Fives played a key role in this process, demonstrating a high level of professionalism and expertise throughout the entire journey, offering customized solutions and constant assistance and guidance,” added Gian Piero Ruello.
The project consisted of several key stages, including data collection, rule enforcement, and dashboard customization. Each stage had its challenges that pushed the joint project team to find appropriate solutions.
The first milestone – data collection – was the most crucial as it required an upgrade of the
internal system and infrastructure to handle the massive data that Eyeron® required.
The second phase concerned the management of quality rules to effectively manage the collected data: the quality rules applied by the quality managers were first rationalized before being implemented in Eyeron® thanks to its user-friendly rule editor.
The final stage encompassed dynamic scheduling with product reallocation module and a machine learning algorithms application for process control improvement. This last phase also provided an opportunity to adapt dashboards and reports to the needs of each user.
For further information, log on to www.fives.com
Tenova LOI Thermprocess, part of Tenova and one of the leading companies supplying industrial furnace systems for the heat treatment of metals, has once again proven that CO2-neutral heat treatment can go together with low nitrogen oxide (NOx) emissions in a project with thyssenkrupp Hohenlimburg GmbH.
In a campaign involving several annealing cycles, a further step has been taken towards decarbonizing steel production as part of the joint project. In production trials, the fuel gas supply for the heat treatment of hot-rolled narrow strip was gradually converted from natural gas to up to 100% hydrogen. For the first time in the world, 70 tons of steel strip were heat-treated in a bell-type annealing plant with Tenova LOI’s HPH®-flameless technology in a CO2 neutral
process, the company claims.
For the flexible delivery of natural gas/H2 mixtures, a specially developed mobile natural gas/hydrogen mixing station was used during the annealing process in order to assess the influence of increased hydrogen admixtures on the overall system. The increased hydrogen requirements for the annealing cycles due to the approximately one-third lower calorific value were supplied by a special trailer and fed directly into the pipework systems of the bell-type annealing plant.
“The project is part of thyssenkrupp Steel Europe’s long-term decarbonisation strategy and includes the goal of achieving climate neutrality in all downstream production processes by 2045 at the latest, in addition to iron and steel production,” said Jan Bernhofen, team co-ordi-
nator, processing, at thyssenkrupp Hohenlimburg GmbH.
“The combustion of hydrogen is technically more complex than the direct use of electricity or the combustion of natural gas. This project has provided us with further insights into the decarbonization of the bell-type annealing process and is helping us on our joint path towards the transformation to climate-neutral steel production. Tenova LOI Thermprocess supplies the suitable technologies for a wide variety of plant types,” commented Dr. Gökhan Gula, project manager and process engineer at Tenova LOI Thermprocess.
For more information, visit www.loi.tenova.com
Technologies turning steelmakers’ decarbonization goals into reality.
Jet
The JVD line introduces a technological breakthrough in the steel coating of advanced high resistant steel grades difficult to galvanize by hot dipping. This genuine alternative to Electro-Galvanizing and Hot-Dip-Galvanizing considerably reduces the cost of galvanized steel and provides multiple advantages when it comes to quality, speed and OPEX. Developed for ArcelorMittal with the help of our experts, John Cockerill is in charge of commercializing this unique technology worldwide.
Electrical
Our E-SiTM equipment and processing lines are designed for the production of strong, ultrathin, lightweight, and highquality Non-Grain Oriented (NGO) steel grades essential for the future of e-mobility.
Other developments & technologies aiming at decarbonizing the steel industry:
VolteronTM: CO2-free Steel Production Process
Furnace Electrification
Carbon Capture Heat Recovery
Plants
High-performance
John Cockerill Industry’s ARPs come with smart plant control systems, provide waste energy recovery and drastically reduce pickling process plants’ fresh acid demands and waste streams in general. What is more, they are providing the lowest emissions in the market.
Steelworkers oppose while politicians question Nippon’s takeover bid, but the Japanese steelmaker remains confident that it will complete the purchase. By
WHILE the initial hullabaloo over Nippon Steel’s takeover of US Steel has diminished, the takeover saga seems to continue with new twists and turns.
Firstly, there is the reaction of the steelworkers who are rattled by the opaqueness surrounding the deal and, secondly, there are also murmurs of opposition from politicians who are unsure about a ‘prized jewel’ of the American steel landscape slipping into foreign hands, even though Japan is a staunch US ally.
Steelworkers, banded under the trade union United Steelworkers (USW), have filed what they describe as ‘grievances’ against the deal, claiming that proper information
Manik Mehta*about the sale was not provided, nor was the union ‘consulted, nor reassured, that its collective bargaining agreement would be honoured’, according to various media reports.
However, US Steel denied the allegation and said that it had already met its obligation under the basic labour agreement (BLA), and was looking to ‘quickly and favourably’ resolve the union’s grievance. The company stated that it was hoping to finalize the nearly $15 billion acquisition in the second or third quarters of this this year.
The acquisition was largely ‘sprung’ on the union, the USW contended, saying that
*US correspondent, Steel Times International
its support was for a bid from rival steel producer Cleveland-Cliffs, Inc. whose July purchase offer at $7.3 billion for US Steel was rejected; thereafter, US Steel received offers from other companies.
In its letter to US Steel ‘s CEO David Burritt, the USW referred to the BLA provisions which, the union contends, were violated during the review process, and called for resolving the dispute. The violations, the USW said, included the company’s failure to provide the union with any information about the sale process that its board of directors had started in August, including important deadlines or timetables, and the bids it had received; the
USW said it was entitled to the information under the BLA, when US Steel agreed with Nippon’s Houston-based holding company on the acquisition.
The USW referred to certain sections of the BLA with US Steel which has a validity until September 2026.
The USW also emphasized the successorship factor to ensure that whoever takes over US Steel will be bound by the labour agreements between the USW and the company.
The USW said it was not consulted nor taken into confidence that its collective bargaining agreements would be respected.
Both US Steel and Nippon Steel stated that ‘represented members’ would continue to receive their paychecks, profit-sharing and benefits from US Steel which, after the takeover, would retain its name. However, the USW did not seem to be convinced, telling its members that ‘talk is cheap, coming from greedy corporations’ and this was the reason why it insisted on including successorship rights in the BLA to protect the workers’ contracts and their interests.
To reassure its workers, US Steel emphasized, in a posting on its website, that Nippon Steel had the ‘financial wherewithal and desire’ to honour all the agreements existing with the USW.
However, the USW said, after its meeting with Hiroshi Ono, Nippon Steel North America’s president at the union’s headquarters, that ‘simply saying Nippon Steel North America (the US office of Japan’s Nippon Steel) will accept our labour agreements’ did not satisfy the BLA
conditions.
The USW also cast doubts on the question of profit sharing which it considers as an employee benefit under the BLA, and said in a statement that it was prepared to continue the grievance process right till the end, contending that it held the management accountable for trying to cash in by selling out American steelworkers and ignoring the contracts and the dedicated workers.
While the USW/US Steel wrangling is expected to continue until it is finally resolved, the acquisition deal is also subject to close scrutiny by the Committee on Foreign Investment in the US (CFIUS), under the treasury department, vested with powers to approve, block, or amend the deal on national security grounds and even forward the deal to the highest authority, the US president, for a decision.
supply chain reliability’.
Biden’s reaction – and also that of other leaders of the two parties – has, so far, been restrained, compared with the sharp criticism from lawmakers of the two parties. Indeed, former President Donald Trump, who is running again for the President’s office, has been silent so far.
Steel industry sources say that Nippon Steel/US Steel lawyers had held talks with treasury department officials on the deal’s announcement in December 2023, concentrating on the process for filing with the CFIUS.
President Joe Biden had expressed doubts on US Steel’s sale to Nippon Steel, apparently fearing that this could become an issue in an election year.
White House national economic adviser Lael Brainard noted that the president believed that the ‘purchase of this iconic American-owned company by a foreign entity – even one from a close ally – appears to deserve serious scrutiny in terms of its potential impact on national security and
Nippon Steel has been sounding confident about completing the US Steel deal, with the company’s president, Eiji Hashimoto recently telling reporters, after the Japan Iron and Steel Federation’s New Year party, that the deal posed ‘no harm to America’ as Nippon Steel would invest in line with the economic security strategies of the US and other Western countries. He added that Nippon Steel’s substantial investment and its advanced steel-manufacturing technology would be advantageous to the US, adding that the current labour agreement would be maintained, and that taking good care of the employees and labour union ‘is our specialty’. His company had anticipated challenges in the form of different opinions, objections, and government scrutiny.
Meanwhile, the American Iron and Steel Institute (AISI) reported a 0.1% increase in the nation’s weekly steel output to 1.699Mt and capacity utilization of 76.5% during the week ending January 13, 2024, compared with 1.697Mt and 75.9% capacity utilization in the year-earlier week and a steel output of 1.707Mt in the previous week.
The top steel-producing regions were the Southern region with 769kt, and the Great Lakes region with 553kt during the week. �
The PROFILEMASTER® SPS is a light section measuring device for measuring contours and dimensions on profiles of all kinds in cold and hot steel applications.
Benefits:
Maximum measuring accuracy thanks to temperature-stabilized measuring systems
Shape fault detection (SFD) thanks to high sampling rate
High-precision measurements
Detects process problems at an early stage
Fast maintenance and easy cleaning
While electrical steels are estimated to account for only 1% of the global steel market, its supply is being considered as an increasingly critical input to Original Equipment Manufacturers (OEMs)’ electrification plans as well as various energy transition initiatives. By Germano Mendes de Paula*
THE commercial electrical steel market is divided in two major categories: the non-grain oriented electrical steels (NOES) and grain-oriented electrical steels (GOES). NOES’ main applications are: hydroelectric plant generators, electric motors, fluorescent lamp ballasts, and hermetic compressors for refrigerators, freezers and air conditioning. Each electric vehicle motor requires around 68kg of NOES, according
to Cleveland Cliffs. GOES are used in the manufacturing of transformer cores, power reactors, hydro generators and turbo generators. As transformers are the only major consumer of GOES, the market is significantly smaller for that product rather than for NOES, at around one third of the demand. Cold Rolled Motor Lamination (CRML), which is known as semi-processed electrical steels because it requires
annealing after stamping and a product little seen outside of North America, is not examined in this article.
Unsurprisingly, during the age of energy transition, there are new projects dedicated to producing electrical steels (also known as silicon steels and magnetic steels). For instance, in 2022, ArcelorMittal announced investments of €300 million in Mardyck, France, for this purpose. It will have a
* Professor in Economics, Federal University of Uberlândia, Brazil. E-mail: germano@ufu.br
200kt/yr capacity and it is expected to startup in 2024.
US Steel commissioned the new 180kt/ yr NOES line at its Big River Steel mill in Osceola, Arkansas, in October 2023, at a cost of $450M. Cleveland Cliffs (formerly AK Steel) has also deployed $30M as capital expenditure into its Zanesville, Ohio, facility to enlarge production capacity of NOES by another 70kt annualized. Considering that electrical steels gained momentum worldwide, it seems interesting to compare the two largest Latin American markets: Brazil and Mexico.
Brazil is the only producer of electrical steels in the region. Aperam South America, formerly known as Acesita – a state-owned Enterprise (SOE) – began to produce NOES in 1979 and GOES in 1981. The company also initiated the fabrication of High Grain-oriented (HGO), a high-permeability product, which allows increased efficiency and reduced size of electrical generation and distribution transformers, as of 2017. HGO requires investments in modern equipment, which is supported by dedicated research and development efforts.
Aperam’s electrical steels are produced in its Timoteo steelworks, located in the state of Minas Gerais. Aperam’s NOES installed capacity reached 194kt/yr in 2022, while the GOES capacity achieved 56kt/yr. Taking data from the consultancy company Steel-Insights into consideration, they were equivalent respectively to 1.4% and 2.2% of global figures. Bearing both products combined in mind, the company’s capacity equals 250kt/yr (or 1.5% of the world).
Graph 1 shows that Brazilian electrical steel output plummeted from 188kt in
2012 to 143kt in 2017, largely due to a severe domestic macroeconomic crisis. It partially recovered to a plateau of 150kt/yr in 2018-2019 and then faced a temporary additional drop to 123kt in 2020, as a consequence of Covid-19. Since then, it has stabilized at around 160kt/yr.
The country’s exports were relatively low during the examined period. On average, it reached 10kt/yr. On the other side of the spectrum, imports diminished from 109kt in 2012 to 56kt in 2016, following the trajectory of domestic production. Afterwards, it was around 70kt/yr in 20172019 and 100kt/yr in 2020-2022. More importantly, imports as a proportion of domestic production increased from 58% in 2012 to 78% in 2022.
The Mexican experience was totally different from the Brazilian one, as the market is fully served by imports. During the 2012-2016 period, imports reached 200kt/yr. Since 2017, it has expanded, with imports more than doubling to 455kt in 2022. Despite
the fact that Mexico does not produce electric steels, it exported roughly 8kt/yr between 2012-2022.
The German distributor Klöckner acquired National Material of Mexico (NMM) in August 2023, a service centre and materials supplier serving automotive end markets, with 10 facilities throughout Mexico. NMM operates a service centre model, as opposed to a purely distributory model. The acquisition allows Klöckner to enter the Mexican electrical steel market. Mexican steelmakers have also announced various investment projects recently, to some extent motivated by nearshoring, but no new line of electrical steels have been added so far. Electrical steels remain a niche market. There is a quite reduced number of producing countries, headed by China and other Asian players. Indeed, Steel-Insight estimates that Asian nations control 90% of NOES capacity and 67% of GOES capacity in 2022. Latin America has played a minor role regarding production, but Mexican demand has been showing a remarkable trend in the last six years. �
GLAMA Maschinenbau GmbH
Headquarters:
Hornstraße 19 D-45964 Gladbeck / Germany
Fon: +49 (0) 2043 9738 0
Fax: +49 (0) 2043 9738 50
Email: info@glama.de
GLAMA USA Inc.
60 Helwig St., Berea, Ohio 44017
Fon: +1 877 452 6266
Liquiline CM44 and CPS11E:
Versatile transmitter and Memosens pH sensors ensure reliable measurement
FieldPort SWA50:
Intelligent Bluetooth or WirelessHART adapter for the easy connection of all HART field devices to the Netilion Cloud via Edge Devices.
Cerabar PMC71B:
Absolute and gauge pressure transmitter combining measurement accuracy with IIoT functionalities.
With the introduction of the ‘Production-Linked Incentive booster 2.0’, India’s speciality steel sector is hoping to go from strength to strength. By
Dilip Kumar Jha*INDIA aims to achieve self-reliance in speciality steel production and become a net exporter following the successful implementation of the second round of the Production-Linked Incentive (PLI) booster.
Currently under consideration, the second PLI booster is expected to prompt steel mills to establish at least 25Mt of additional production capacity by the end of the proposed three-year tenure of the scheme.
India presently imports between 5-6Mt/yr of specialised steel mainly from China, Japan, and South Korea, among other countries, to bridge the supply-demand deficit.
Speciality steel is a value-added product where normal finished steel undergoes processes such as coating, plating or heat treatment, making it suitable for applications that require specific properties such as defence, space, power, automotive, and specialized capital goods. Additional production of speciality steel is required for the domestic steel sector to scale up to the global value chain. Key features of the scheme include three incentives; participation limited to companies registered in India, commitment to investment thresholds, and incremental
*India correspondent, Steel Times International
production as outlined in the scheme guidelines.
Restricted to the premium steelmaking sector across high-value categories, the second PLI scheme is expected to have a capital outlay of INR 40 billion (~$480 million), nearly double the total disbursement made under the original programme. Segments to be covered under the PLI 2.0 scheme include coated and plated steel, speciality rails, high-strength and wear-resistant offerings, and alloys such as electrical steel, and wires and tubes, among others. The government is currently
Source: Ministry of Steel, Government of India; FY = Financial Year (April-March)
A= Incremental sales in current year with reference to previous year or the base year whichever is higher
B= Weighted Average sale price (net of taxes) in current year
C= Weighted Average sales price (net of taxes) in the base year (2019-20)
Source: Ministry of Steel, Government of India; FY = Financial Year (April-March); INR=Indian rupee
recommendations made by concerned stakeholders for the smooth transition of PLI 2.0, which aims to promote high-end steel or speciality steel manufacturing, thereby reducing India’s dependence on imports. The draft guidelines indicate that the usage of coated plated steel across user industries requires an investment of INR 5 billion (~$60 million) towards capacity addition. Eligible products are widely used in the automotive industry. Furthermore, the speciality rails segment, mostly used in head-hardened rails, is likely to draw an investment of INR 2 billion (~$24 million), alloy steel (wires and tubes in segments like tool and die, valve steel and automotive power tool) to the tune of INR1 billion (~$12 million), and tyre beads and metallic coated wires may attract an investment of INR 800 million (~$10 million). Products such as zinc/aluminium/copper-coated wires, carbon steel, high-strength rebars, and CRGOs would also be eligible for PLI 2.0. Faggan Singh Kulaste, India’s minister of state for steel, indicated the government’s overall outlay for PLI 2.0 at INR 40 billion (~$480 million).
PLI 1.0
Since 2018, India has emerged as the world’s second-largest crude steel producer and the second-largest consumer of finished steel since 2019. However, the country has remained import-dependent for value-added steels in specialised applications. With an objective of making India self-reliant in speciality steel, the government approved a PLI scheme for this sector with a financial outlay of INR 63.22 billion (~$759 million) on 22 July, 2021. The present specialized steel production capacity in India is estimated at 25Mt/yr.
finalizing the draft in consultation with the major consuming sectors of specialized steel such as roads, the Department of Atomic Research, commerce, defence, and others, to assess its impact on various industries, and plans to launch the scheme soon.
T V Narendran, managing director of Tata Steel Ltd, one of India’s the largest integrated primary steel producers, highlighted the need for massive
investment in the speciality steel sector to counter increasing imports from China.
Speaking on the company’s New Year plan at its factory in Jamshedpur, Jharkhand, Narendran expressed optimism about the government’s increasing focus on infrastructure development, which he believes will be the key driver for the industry’s growth in the future .
The government is current reviewing
The first version of the PLI scheme (PLI 1.0) attracted a total investment of INR290 billion (~$3.48 billion) with a guarantee to install 25Mt/yr of additional capacity additions. The application window for PLI 1.0 closed on 15 September 2022, with the government receiving 79 applications from 35 companies.
Companies participating in the PLI 1.0 scheme have committed to downstream capacity additions of 24.78Mt/yr. Some of the categories covered by that PLI 1.0 include coated steel in the non-alloyed category, wires, water and weatherresistant steel, asymmetric rails with forgings, metallic, coated wires, among others. �
due to a lack of media attention, China’s ‘substantial market size’ and extensive electrolyser capacity foreshadows its future influence and leadership in the hydrogen sector.
By Anne-Sophie Corbeau*media focuses largely on low-carbon hydrogen developments in the US and Europe. However, China is also the country with the largest installed electrolyser capacity and the largest electrolyser manufacturer capacity. The country’s substantial market size and extensive industrial infrastructure not only facilitate fast technological advancements in the hydrogen space, but also offer the potential to achieve economies of scale which could
significantly influence the global hydrogen landscape.
To realize China’s potential as a clean hydrogen leader, it is crucial to understand its hydrogen strategy. Indeed, China’s strategies are plural given the multiplicity of hydrogen strategies at the provincial level. These give a very different perspective than the national hydrogen strategy, with a more bullish view on renewable hydrogen development. It appears that provincial strategies may, in fact, give a more accurate view of China’s potential than the national one.
*
An overview of China’s hydrogen landscape
China represents roughly one-third of global hydrogen output at around 33Mt (2020). This production heavily relies on fossil fuels (79%), while about 21% of it originates as industrial by-product. Meanwhile, the contribution of renewable hydrogen remains marginal, accounting for less than 0.1% of production.
Hydrogen production and consumption in China are concentrated in the northwest and northeast, with the highest outputs in the Autonomous Region of Inner Mongolia (‘Inner Mongolia’) and Shandong, each of which exceeded 4Mt in 2020, followed
by Xinjiang, Shaanxi, and Shanxi with over 3Mt. These regions’ coal abundance fuels hydrogen production, mainly serving local petrochemical and chemical industries. The northwest, rich in renewable energy resources (wind and solar), is also positioned to become a renewable hydrogen hub.
However, anticipated surging demand in eastern and southeastern China highlights a growing supply-demand geographic mismatch. With only 400 km of existing hydrogen pipelines, China lacks the infrastructure to transport hydrogen from distant renewable-rich regions to emerging consumption hubs. Recent initiatives to develop infrastructure such as shortdistance hydrogen pipelines, hydrogen refueling stations, and liquid hydrogen storage facilities are primarily concentrated in four major industrial clusters: the Beijing-Tianjin-Hebei Region, the Yangtze River Delta, the Pearl River Delta, and the Ningdong Energy and Chemical Industry Base. Consequently, they may not be able to connect renewable hydrogen supplies with primary demand centres.
China’s national and regional hydrogen development strategies compared
A notable feature of China’s hydrogen strategy is that it is not, in fact, singular, but instead is comprised of a national strategy and a multitude of regional strategies. China released its medium and long-term strategy for the development of the hydrogen energy industry (2021–2035) (‘the National Plan’) in March 2022. It strategically positions hydrogen as
(1) an important part of China’s future energy system; (2) an important carrier for achieving China’s low-carbon energy transition; and (3) a key emerging industry and development direction of future industries in China. The National Plan aims to establish a hydrogen supply system using both industrial by-product hydrogen and renewable hydrogen. However, its targets for renewable hydrogen production may appear relatively conservative with a range of 100-200kt/yr by 2025 (or 0.3 to 0.6% of current Chinese hydrogen consumption).
By contrast, provinces, cities, and municipalities across China have introduced their own hydrogen development plans that establish far more ambitious renewable hydrogen goals. Out of the 34 regions that make up mainland China, 18 have
independently introduced their hydrogen industry’s 14th Five-Year Plan, while the others have incorporated hydrogen into broader industrial strategies. These local strategies are setting targets far beyond those of the National Plan. The regions’ cumulative targets for renewable hydrogen amount to 1.1 to 1.2 Mt by 2025, or five to 12 times the conservative national target. For instance, Inner Mongolia has an ambitious objective of 480kt of renewable hydrogen by 2025, more than twice the national target.
Localized hydrogen strategies are tailored to leverage regional advantages and infrastructure, leading to varied approaches across provinces. Regions with abundant renewable resources, such as Sichuan with its hydropower potential, prioritize renewable hydrogen production. In contrast, coal-rich regions, such as Shanxi, primarily focus on industrial by-product hydrogen from coal-chemical production. Regions with an abundance of both renewable and coal resources, such as Inner Mongolia, adopt a diversified approach.
Regions also prioritize different applications according to their unique needs. Inner Mongolia, Shanxi, and Shaanxi aim to deploy hydrogen fuel cell forklifts and trucks for mining operations. Zhejiang focuses on leveraging hydrogen for combined power and heating as well as fuel cell electric vehicles (FCEVs). In fact, all regions emphasize establishing hydrogen refueling stations and deploying FCEVs, with some having identified targets, aligning with China’s longstanding policy support in these areas. Some regional plans state the adoption of renewable hydrogen for industrial decarbonization without explicit targets, with the exception of Jilin’s 250-350kt capacity goal for green chemicals and refining.
Still, these strategies underscore the vital role of local governments in the initial phase of China’s hydrogen development, acting as a testing ground for the central government. Local officials and leaders of state-owned enterprises are collaborating with central ministries to implement hydrogen policies, motivated by the prospect of career advancement to align with the national development objectives Table 1.
Inner Mongolia’s hydrogen leadership
Inner Mongolia’s 14th Five-Year Plan on hydrogen development, announced in
Note: Highlighted cell indicates the plan mentions the target/application without a quantified target. Industrial usage covers steel, refining, chemicals; highlights do not imply all applications are covered. Some plans offer post-2025 visions/targets, but this table only shows 2025 targets. Abbreviations: Guangxi – Guangxi Zhuang Autonomous Region; Tibet – Tibet Autonomous
Ningxia
2022, sets the most ambitious renewable hydrogen production target by far at 480kt/ yr by 2025. The region has undergone rapid expansion in terms of installed renewable hydrogen production capacity, often developed by major state-owned enterprises (SOEs), and will host one of the world’s largest renewable hydrogen projects, currently under construction.
Several factors contribute to Inner Mongolia’s ability to assume a leadership role in hydrogen development in China. The region:
• possesses substantial solar and wind
potential, with technically exploitable wind and solar energy resources of around 57% and 21% of China’s potential, respectively.
• has a pre-existing local hydrogen demand, such as ammonia production, and oil refining and future demand from steel manufacturing.
• benefits from its proximity to the eastern economic hub (Beijing-TianjinHebei region). The 400-km Ulanqab-Beijing pipeline is China’s first long-distance hydrogen pipeline. It has an initial capacity of 0.1Mt/yr and the potential to expand to 0.5Mt/yr.
To determine whether local renewable hydrogen targets are a better benchmark than the national target, it is crucial to estimate whether Inner Mongolia could potentially achieve its 2025 target.
Based on publicly available statistics, Inner Mongolia hosts 50 renewable hydrogen projects, of which three, yielding a combined 10.884kt/yr hydrogen production capacity, are operational. Moreover, 21 projects with a cumulative capacity of over 300kt/yr are under construction and are expected to be online by 2025. This represents 63% of the province’s goal. Another 26 projects with an aggregate production potential of 1Mt/yr are planned, with around 460kt expected to be online by 2025.
Inner Mongolia may still fall short of its ambitious 2025 target since there is uncertainty about whether planned projects will actually materialize. The region’s ability to reach its ambitious target depends on projects currently under construction as well as additional planned projects that are supposed to begin construction soon. Based solely on projects operational and under construction, Inner Mongolia’s anticipated annual hydrogen output would surpass the national target of 100–200kt/ yr. With planned projects included, Inner Mongolia’s potential annual renewable hydrogen production capacity could reach 1.4Mt, exceeding the aggregated renewable hydrogen production targets announced across all regions. Most projects are located within the industrial zone adjacent to the petrochemical plants in which they could replace gray hydrogen. These projects also reflect the heavy statedriven involvement of China’s hydrogen market–32 of the 50 existing projects are spearheaded by SOEs, and an additional six involve collaborative efforts between SOEs and private enterprises.
Similarly to other parts of the world, there might be questions about whether the hydrogen produced from these electrolysers will truly be ‘renewable’. In 2021, the China Hydrogen Alliance proposed the Standard and Evaluation of Low-Carbon Hydrogen, Clean Hydrogen, and Renewable Hydrogen. However, this framework sets a relatively unambitious threshold of 14.51 kgCO2e/ kgH2 for low-carbon hydrogen (which is above the current carbon intensity of hydrogen from steam methane reforming)
and 4.9 kgCO2e/kgH2 for renewable hydrogen (above the EU’s threshold of 3.38 kgCO2e/kgH2).
Moreover, the differentiation between hydrogen produced from renewable sources and other variants remains ambiguously addressed in official Chinese government documents. Both the central government and local governments refer to ‘hydrogen’ and ‘green hydrogen’ without providing explicit definitions. Even the PRC Energy Law (Draft) does not differentiate between various hydrogen production approaches. Consequently, China’s current hydrogen policy lacks mechanisms to regulate the sources and carbon intensity of hydrogen (e.g., by requiring that ‘renewable
hydrogen’ be produced exclusively from renewable electricity).
This lack of a precise definition is not so surprising given that many regions and countries are still in the process of considering how to precisely define renewable hydrogen. The EU approved a definition in a Delegated Act only in June 2023, while the US finally published the hydrogen tax credit guidance in late 2023. However, on the provincial level in China, there does seem to be an attempt to articulate a definition for renewable hydrogen. In 2023, Inner Mongolia, and several other provinces, began to distinguish between grid-connected and off-grid hydrogen production projects (relying solely on wind and solar plants).
One notice published by the Inner Mongolia Bureau of Energy states that ‘grid-connected projects, in principle, should not purchase electricity from the grid.’ ‘In principle’ is a unique Chinese term that indicates the clause has room for manoeuvre based on regulations, which implies this rule might not be strictly enforced. However, if ‘grid-connected’ projects do not use grid electricity, these
projects would satisfy the European definition of ‘temporal correlation’ which emphasizes that hydrogen producers must ensure that renewable electricity generation and hydrogen production coincide temporally. This rule in Inner Mongolia indicates an attempt to produce electrolytic hydrogen solely from renewable energy.
Local policy and industry developments on renewable hydrogen in China are already exceeding the national strategy and its conservative targets, making them a better indicator of China’s ambitions. In particular, Inner Mongolia’s renewable hydrogen production target is more than twice the national target and seems potentially within reach based on projects currently under construction.
China’s hydrogen strategy, unlike the
EU and US, leans more towards economic growth than immediate climate action, as evidenced by the limited emphasis placed on measuring hydrogen’s carbon intensity. Despite several regions having suggested restrictions on fossil-based hydrogen, national policies still lack a strong push against it. Still, climate mitigation does exert influence: hydrogen is integral to China’s low-carbon transition, while provinces promote renewable hydrogen to replace gray hydrogen. China’s hydrogen development landscape presents a complex mix of challenges and opportunities. As the global community navigates the intricacies of the hydrogen economy, understanding China’s unique approach, characterized by a blend of centralized directives and regional initiatives, is paramount, providing insights into the future trajectory of the world’s largest hydrogen market. �
The H2-DRI-EAF process shows significant promise in decarbonizing the steel sector, but challenges must be addressed to achieve genuinely green steel through hydrogen reduction. By Soroush Basirat*
GREEN hydrogen is set to transform the steel industry. Hydrogen-based direct reduction (DR) technology is already leaving behind other decarbonization solutions for primary steelmaking such as carbon capture and storage (CCS).
H2-DRI-EAF involves the use of hydrogen (H2) to produce direct reduced iron (DRI), which is then processed in an electric arc furnace (EAF) to produce steel. In the BloombergNEF net-zero outlook, 64% of the total primary steel production projected for 2050 is associated with H2-DRI-EAF, followed at 25% by DRI-EAF equipped with CCS technology. The remaining share is allocated to blast furnace-basic oxygen furnace (BF-BOF) steelmaking and other technologies.
In its revised net-zero roadmap 2023, the International Energy Agency (IEA) envisions that 44% of iron production will be derived from hydrogen-based processes by 2050, followed by other technologies including CCS and direct iron ore electrolysis.
While hydrogen use in ironmaking based on the DR process makes sense to produce low-emissions steel, there are specific hurdles that must be overcome to facilitate this shift. The foremost challenges include ensuring an adequate supply of DR-grade iron ore, and establishing a sustainable green hydrogen value chain for steel production.
The iron ore mining industry has been a major sector with established corporate entities for many years. To
*Energy finance analyst – global steel, IEEFA
cater to emerging demand for green iron, companies are adopting diverse strategies, including opening new iron ore mines with high-grade ores such as Iron Bridge, Australia, and Simandou, Guinea. Furthermore, inventive methods are being explored such as microwave and biocarbon technologies for producing low-emission pure iron, along with the use of smelting reduction with lower-grade ores.
Compared to the iron ore sector, green hydrogen is relatively new. However, it will play a pivotal role in effectively decarbonizing the steel industry, which demands closer examination.
The challenge of creating a green hydrogen value chain for steel
The decarbonization of the steel sector will necessitate additional and more dedicated gigaWatt-scale green hydrogen projects. Green hydrogen is still in its early stages of development, and increased investment is crucial for its integration into the steel industry. In the H2-DRI-EAF process, one tonne of steel requires nearly 300 megaWatts (MW) of electrolyser capacity operating around the clock.
Currently, among the commercial-scale green steel projects, only H2 Green Steel has outlined a comprehensive plan, proposing an electrolyser capacity above 700MW for steel production and aiming to transition directly to hydrogen instead of gas as an alternative reducing gas. Thyssenkrupp is exploring the possibility of outsourcing hydrogen supply for its plant in Duisburg, Germany, opting not to invest directly in
the hydrogen value chain. This will entail considering long-term supply contracts for both green and ‘blue’ hydrogen from domestic and international sources.
The hydrogen economy faces constraints such as limited electrolyser manufacturing capacity, and entails significant electricity consumption, posing challenges for renewable energy supply.
To sustain the operation of largescale green hydrogen-based DR plant, a consistent supply of renewable electricity must be guaranteed throughout the year. The variability of renewable energy sources, such as solar and wind, necessitates oversizing of capacity and the implementation of energy storage solutions to ensure a continuous energy supply. This necessity contributes to an escalation in the initial investment costs for renewables that can dwarf the CAPEX needed for the steelmaking facilities.
As per the US government’s updated Inflation Reduction Act (IRA), tax credits are available exclusively for hydrogen projects meeting specific criteria covering three key factors. First, the project must involve dedicated renewables constructed no more than 36 months before the commencement of electrolyser production (Additionality). Second, the renewables and electrolysers should operate within the same grid (Grid Access). Third, the project must align precisely with renewable power generation in terms of production time (Time Matching). The new requirements push developers to build their hydrogen plants with dedicated renewables nearby.
As of December 2023, the Hydrogen Council reported that despite a substantial number of projects announced, amounting to 305 gigaWatts (GW) in total pipeline capacity, the combined electrolyser capacity for green hydrogen has only surpassed 1GW. This capacity is sufficient to decarbonize just one steel mill with a capacity close to 3Mt/yr. The hydrogen development sector is also grappling with challenges such as cost inflation and rising financing expenses that push up the price of the hydrogen. The estimated levelised cost of producing renewable hydrogen (LCOH) is about USD4.5/kg to USD6.5/kg if built today. It is expected to decline to USD2.5/kg to USD4.0/kg towards 2030. Chinese electrolysers present an opportunity as they are two to five times more cost-effective than their Western counterparts; however, their performance
lags behind that of Western models.
Owing to inflation and uncertainty regarding government support, some projects are deferring their final investment decisions (FIDs). Lenders are anticipating support from off-takers for green hydrogen projects, but the price gap between production costs and off-takers’ desired rate remains substantial. End users are hopeful for more supportive regulations to facilitate a smoother transition, potentially resulting in an uptick in project finance approvals in 2024.
With all of these challenges facing green hydrogen production, it is crucial to prioritise the available capacities for sectors that can yield a substantial reduction in carbon emissions, such as the steel industry.
German think tank Agora Industry has underscored that steel stands out as the sector with the greatest potential for carbon reduction among various hydrogen applications. Interestingly, even in sectors where direct electrification is not feasible, shifting from coal to hydrogen – as seen in the steel sector – yields more benefits compared with transitioning from other fossil fuels, including oil and gas, to hydrogen.
In addition to distributing valuable green hydrogen across various sectors according to priority and carbon reduction potential, developers should reconsider exporting hydrogen for long distances. Particularly for projects under development in regions like MENA, hydrogen transportation is not an optimal solution, with inefficiencies and energy losses that add costs to the hydrogen value chain. Instead, using hydrogen domestically for producing hydrogen-reduced iron is strongly recommended as a preferable approach.
As an alternative, some steelmakers are opting to shift the ironmaking process to locations with access to more affordable and reliable energy sources, importing pure iron as a feedstock in the form of hot briquetted iron (HBI). The concept that is emerging sees a decoupling of ironmaking from steelmaking processes.
To bring this into reality, some steel producers are focusing their efforts on Australia, Brazil, the Middle East and Africa, all of which are positioned to establish themselves as green hubs for steel raw materials. POSCO is in the process of outlining a USD12 billion investment for green HBI in Australia. Plans for the development of 2Mt/yr of HBI and 0.7Mt/
#itsmorethanjustamachine
3-ROLL TECHNOLOGY FOR SBQ SIZING.
A Reducing & Sizing Block for long products keeping its promises.
Achieve your goals with KOCKS RSB®
up to 160mm
finishing size in round or hexagonal dimensions
up to 20%
increase in production
up to 10% energy savings in the mill line
yr of iron ore pellets were submitted for environmental approval in October 2023
Gas is only an intermediary solution The growth of the green hydrogen value chain is a process that will extend over several years. This is reflected in the basic design of numerous newly announced green iron and steel projects, which are strategically planned to be hydrogen-ready. Most of these projects are set to commence operations initially utilising natural gas (NG) – the exception being the Nordic countries. Continuous access to affordable renewable energy derived from hydro power frees the Nordic nations from any reliance on gas at the outset.
Midrex, the largest manufacturer of DR
plants, offers flexibility in its process, which can function with varying hydrogen ratios in the reducing gas mix. This allows for a gradual transition from gas to hydrogen whenever green hydrogen production becomes cost-competitive.
Tenova and Danieli, the joint developers of the Energiron DR technology, claim that all Energiron DRI plants are hydrogen-ready by design and can start using hydrogen as reduction gas without equipment modifications.
Experiments such as elevating the hydrogen share to 60%, in a trial conducted by HBIS, validate the potential of utilising a gas mixture in Energiron shafts to decrease carbon emissions in the ironmaking process. In May 2022, ArcelorMittal Long Products
Canada, equipped with two Midrex shafts, successfully conducted tests replacing gas with hydrogen partially. Table 1
The concluding remarks of COP28 highlighted the imperative to shift away from fossil fuels in energy systems, signalling the commencement of a pivotal phase. This underscores the collective responsibility of all nations to swiftly phase out fossil-based industrial operations, ensuring alignment with the goals of the Paris Agreement.
Despite the current high price of hydrogen, it is anticipated that the cost will become increasingly economical as electrolyser technology matures in the near future, prompting a shift towards hydrogen. Conversely, as the energy system moves away from fossil fuels, a global glut of gas supply is expected by the end of this decade. Investing in new capacity development is likely to result in stranded assets.
Even in regions with access to gas reserves, like Western Australia (WA), where projects such as POSCO’s new HBI plant have been announced, securing gas is challenging due to the extremely tight supply, as most gas produced in WA is exported as liquefied natural gas (LNG). Conversely, regions such as the Middle East boast plentiful and affordable gas resources that have historically been employed in iron production.
The first wave of green steel initiatives is emerging in Europe. Following the Ukraine war, Europe aims to replace Russian pipeline gas partially with increased LNG imports, mainly from the US. Introducing new gas demand from steelmakers could strain the overall supply, necessitating reconsideration in studies for transitioning to the NG-DRI pathway even as a bridging solution to true green steel. It’s crucial to note that utilising LNG as a feedstock may raise the final steel cost, given the additional expenses incurred during liquefaction, transportation and regasification processes for LNG compared with delivering gas via pipeline.
Europe is decreasing its reliance on gas, as renewable sources are claiming a larger share of the energy mix on the continent. The EU aims to fulfill 42.5% of its energy demand from renewable sources by 2030.
Given the transformations in the energy sector, the concept of utilising ‘blue’ hydrogen – made using gas, with the emissions captured with CCS – in steelmaking is irrational. CCS remains an
unproven technology with a track record of underperformance and low capture rates.
According to a report from the US Department of Energy (DOE), the majority of blue hydrogen projects are not deemed clean due to their high upstream emissions and do not qualify for tax credits. The EU also does not provide extensive subsidies for blue hydrogen. Moreover, in line with the EU’s revised Renewable Energy Directive (RED III), industries such as steel are mandated to have at least 42% of their hydrogen use sourced from renewable energy by 2030, with a further increase to 60% by 2035. This updated directive effectively excludes the possibility of blue hydrogen development for steelmaking in the EU. The utilisation of gas-based DRI is not a definitive solution for achieving steel decarbonization due to its significant carbon emissions. Green steel producers should have a clear strategy to transition towards green hydrogen or, at the very least, plan to incrementally incorporate hydrogen to curtail their reliance on gas.
H2-DRI-EAF represents a narrative of allocating limited resources to create
valuable products. Currently, green hydrogen comes at a high cost, and there is a scarcity of DR-grade iron ore. By judiciously allocating these two resources to
green steel facilities, and with the backing of supportive yet rigorous regulations, the transition to green steel can continue to gain momentum in 2024. �
THE
GROUP GROUP
Global Sponsors
Slowly but surely, momentum is building to upscale H2 production via electrolysis, with goals to increase renewable energy sources, and reduce costs.
By Lynn Gorman*THE steel industry is realigning future investment from the legacy steelmaking technologies of the BF and the BOF to the current preferred technology of the EAF. As such, steelmaking is on track to become significantly greener, and the plants will become smaller, cleaner, and consume less energy. Today, the steel industry releases 7% of the world’s CO2. According to a report by Wood Mackenzie, the steel industry’s carbon emissions are expected to fall by 30% by 2050 compared to 2021 levels. The European steel industry has already cut its CO2 emissions and energy use by half since 1960, and aims to achieve further cuts of 80-95% by 2050 compared to 1990 levels. Because of the enormous installed equipment base and the long life of steel production plants, the evolution to a greener steel industry may be a slower one compared to some other industries such as power generation, semiconductor, and
automotive. However, the steel industry is indeed positioning itself for a cleaner future and has demonstrated notable efforts on the decarbonization journey.
The iron and steel industry knows where
*Freelance writer
the technology gaps are, what the market realities are, and what the cost inhibitors are, enabling stakeholders to turn the stumbling blocks into practical solutions. There are pilot projects well underway
worldwide, and demonstration facilities in northern Europe that serve as teaching models for the optimal systems to employ, strategic partnerships to nurture, and are providing the data the steel industry has been seeking.
Steel is the most recycled manufactured
product in the world. EAF steel plants primarily use scrap steel to make new steel, yet they must add additional iron molecules to the process, such as DRI (direct reduced iron), sponge iron, or HBI (hot briquetted iron), to augment recycled steel in EAF production. EAF iron
feedstock produced in a shaft furnace to complement scrap steel made from ore is using a CO (carbon monoxide)-hydrogen blend currently made from natural gas or coal. The near-term solution for a greener steel industry is replacing natural gas and/ or coal used for producing iron units with zero carbon hydrogen as the reducing gas for EAF feedstock preparation. Clean steelmaking may ultimately use hydrogenderived DRI and hydrogen-enhanced electric arc furnaces with near-zero CO2 emissions per ton of steel. However, to reach that level requires massive production of green hydrogen at a cost that’s acceptable to steelmakers.
David Wolff, director of industrial product sales at Nel Hydrogen, cited several requirements for green hydrogen to contribute to the steel industry successfully.
“The volume of hydrogen that the steel industry could use – both in iron production as a reducing gas and in steelmaking as a heating fuel source – exceeds the current capacity of electrolytic hydrogen generation by orders of magnitude,” said Wolff. “There simply aren’t enough electrolysers right now, however new electrolyser equipment manufacturing plants will be coming online by 2025, and likely just in time for the steel industry to benefit.”
Competitive market realities will also affect the steel industry’s transition to green hydrogen. Other market sectors, for example sustainable aviation fuel, green ammonia, and hydrogen fueling, are moving more quickly, and making larger investments in hydrogen electrolysis for their needs than the steel industry. As such, these ‘first movers’ are first in line to procure electrolysers.
These more active market sectors are creating enough demand so that new electrolyser manufacturing plants are being built, which will aid the steel industry as its evolution continues and its demand for electrolysers increases. For instance, Nel is building a new electrolyser equipment manufacturing plant near Detroit, Michigan, USA. When fully developed, the Michigan plant alone will have a production capacity of up to 4GW of alkaline and proton exchange membrane (PEM) electrolysers.
Alkaline electrolysis and PEM electrolysis are the two types of electrolysis systems that are generally considered commercially mature right now. There are other types in development which also show promise.
Alkaline technology has historically been used for large capacity hydrogen plants. Alkaline cell stacks cost fewer capital dollars on a per kW basis because they do not use precious metals as catalysts as PEM does, and alkaline equipment has reduced in cost to a great extent, having been commercially deployed for almost a century. Alkaline electrolysis is being used at green steel projects in Sweden such as Ovako (see article about this project in Steel Times International September 2023 issue); HYBRIT, a joint venture between SSAB, LKAB, Vattenfall; and H2 Green Steel.
Conversely, PEM electrolysers are compact, and can ramp up quickly to cope with variable energy sources or changing hydrogen demand. They can be supplied to make a range of hydrogen production from pounds per day to hundreds of tons per day. PEM electrolysers have been working in the field commercially for about 50 years. According to Wolff, PEM is well suited to small footprint applications and offers simple, straightforward equipment that does not require downstream compression or gas purification.
Electrolysis begins with the electrolyser’s cell stack. That’s the core of the electrolyser, akin to the chip in a computer or the engine in a truck. Each cell stack is made up of many electrolytic cells, each of which is an electrochemical reactor. Add water, an electrolyte and DC power, and the cell stack creates hydrogen and byproduct oxygen. Cell stacks can be arrayed to increase production in a number of different configurations.
Ironmaking and steelmaking sites are typically large; most of them are expected to accommodate multiple electrolyser ‘trains’ to accommodate generation in the 100MW to 500MW range that might be required at full scale. There’s also the concept being explored to establish separate green hydrogen generation plants – complete with co-located offgrid renewables, companion storage facilities, and transport fleets to deliver the green hydrogen to various nearby iron and steel locations. For example, the Hy Stor Mississippi Clean Hydrogen Hub project features underground salt caverns for storage. Hy Stor’s goal is to develop a green hydrogen generation, storage, and transportation hub in the USA. The first phase of the project is expected to be commissioned in 2025.
Another stumbling block to a green
steel industry is, of course, cost. Water electrolysis runs on electricity, and electricity is the largest contributor of hydrogen cost when deploying water electrolysis on a large scale.
“Both CAPEX and OPEX must decline,” said Wolff. “Progress is being made on that front as we scale up electrolysis and clean energy plants, but it takes time to make that progress and there are few shortcuts.”
Wolff used the analogy of the electric vehicle market, citing that it has taken about 10 years for EV costs to come down to the point where mainstream consumers are buying them.
Many markets right now need steady, predictable, high-quality electricity. One potential scenario for green hydrogen electrolysis in the steel industry is to closecouple the electrolysis plant with a solar array or with a wind farm – meaning the electrolysers operate directly off of those renewables with no costly grid in between. This may speed short-term progress toward cost-effective green hydrogen. Longer term, according to Wolff, it makes more sense for electrolysis to be a valuable grid participant, enabling enhanced energy usage and lower costs for all.
Green steel is a premium product. When the private sector users of steel demand
At Ovako’s facility in Hofors, Sweden, steel can be heated prior to rolling with hydrogen produced through water electrolysis and green electricity to reduce the facility’s carbon emissions
greener steel, such as the automakers, and the public sector incentivizes it – as the Inflation Reduction Act in the US will do once the guidelines are known – the investment in green hydrogen generation equipment is expected to grow to serve the steel industry.
Certain regions are using carrot and stick approaches to inspire innovation. Carbon pricing is a powerful incentive for lower carbon steel in Europe but has not been used to strongly influence behaviour elsewhere.
“Having to pay a tax for every pound of CO2 released could go a long way to incentivizing the investment into these new clean technologies for the steel industry,” said Wolff. “That, combined with earning a premium price for greener steel, for example in a car, will help pay for the steel company’s investment.”
Wolff suggests that we in the steel industry should be striving to take on the projects today that specifically revolve around using hydrogen as the reducing gas in ironmaking and replacing the gray hydrogen in steelmaking with green. This will give the industry experience of operating electrolysis plants and will make a measurable difference in the carbon intensity of the steel. �
José Noldin, CEO of GravitHy*, and a self proclaimed ‘CO2 killer’, sits down with Catherine Hill* for a closer look into a consortium that is on track to build, own, and operate the first low carbon iron production plant in France.
Well, I always knew that I wanted to be an engineer. Attending a technical high school led me to pursue a degree in mechanical engineering. When I got my engineering diploma my initial ambition was to embark on a career in the automotive industry, but there was a plot twist. Due to a family connection with Dr. Marcos Contrucci – a living legend and inventor of the Tecnored ironmaking process – I had the opportunity to join the early stages of the development of Tecnored (today owned by iron ore giant Vale). Initially my job was to be the focal point for the development of the data control system when I found myself captivated by the complexities and nuances of ironmaking. Since then, I did my MSc and PhD in metallurgical engineering with Prof. Jose Carlos D’Abreu (the pope of selfreduction ironmaking) and have dedicated my professional life to this remarkable sector, and I have never looked back.
Since day one on my professional journey! I can say that I work in sustainability and decarbonization even before these concepts were widely recognized by those names.
For example, Tecnored’s ground-breaking approach aimed to replace the conventional, high-temperature, and capital-intensive methods involving sintering, coke ovens, and blast furnace with a more efficient alternative, i.e., cold-bonded self-reducing agglomerates smelted in a compact shaft furnace. Less capex, less opex, less energy requirements and the use of biomass and other challenging raw materials.
Back in the early 2000s, I was already advocating for technology changes in steel, to redesign the value chain, replace coke, and decouple iron from steelmaking. Similar messages that we convey now with GravitHy, this time with much stronger support due to the need of steel industry to transition towards a low CO2 future. So, it’s a lifelong quest to decarbonize steel production while making it more efficient and sustainable.
As a leader and decarbonization champion I must keep my eyes on the end game, but we need to celebrate small victories along the way. Still lots to be done but, after starting alone, looking around and seeing our great team of CO2 killers at GravitHy, who share the same values and commitment to get it done, is an enduring pride for me. On a personal note, when my daughters said they finally understood what I did at work, it was a very special moment.
GravitHy is an industrial start-up created under the leadership of EIT INNOENERGY (largest sustainable energy innovation ecosystem) via its EGHAC (European Green Hydrogen Acceleration Centre) that identified the need and opportunity to decarbonize steel production by building, owning and operating H2-based DRI facilities. To materialize the company, EIT INNOENERGY followed a value chain approach, gathering other industrials with relevant expertise: IDEC Group (real estate), ENGIE (energy), Plug Power (H2), Primetals Technologies (equipment builder) and FORVIA (Tier 1 supplier for the automotive industry). I was then hired by the founding shareholders to develop the company throughout its journey.
An industrial start-up like GravitHy has five successive phases: ideation, activation, execution, operations and replication. The founding shareholders did an excellent job in the ideation phase and I’m committed to continue building and leading the team that will deliver throughout all other phases. Setting up the company, embarking and aligning the various stakeholders for a groundbreaking value proposition in a capital-intensive and hard-to-abate industry, carried out by a disruptor like GravitHy, posed significant challenges. My consortium partners say that finding the right CEO was also a major challenge, so I must agree as well.
Leading is about driving and enabling people to deliver around a good strategy. At GravitHy we have a consortium of companies with different profiles, therefore, collaboration is essential, especially at board level.
In my professional life I had the chance to work with great leaders, Dr. Contrucci (Tecnored), Pedro Gutemberg (Vale), Baron Berghmans (Lhoist), Benjamin Steinbruch (CSN) and now Diego Pavia (EIT Innoenergy), among others. Everyone with a unique style that inspires me in different situations, from selling a pitch to crisis management. Therefore, rather than adapting, I’m challenged to use the entire leadership toolbox built over my career and inspired by many role models.
GravitHy’s Fos-sur-Mer plant is aiming to create over 3,000 new jobs directly and indirectly.
ARE THERE OTHER WAYS IN WHICH THE PLANT WILL CHANGE THE ECONOMIC AND SOCIAL LANDSCAPE OF THE AREA?
GravitHy will honour the metallurgical legacy of For-sur-Mer and ensure its competitiveness and sustainability in the long term. The city has a strong link with the port, which currently consists mostly of fossil fuel-based activities, that will evolve with the ongoing energy transition. One of our ambitions is to provide an alternative to carbon-intensive activities in order to sustain industrial jobs in the region and ensure a just transition. Being the largest H2 electrolyzer in France and a significant consumer of low-carbon electricity will create real opportunities for the development, attraction, and retention of young professionals and future generations. The whole value chain will benefit.
HYDROGEN IS A COSTLY AND LOGISTICALLY COMPLEX SOURCE OF ENERGY. HOW WILL YOU MANAGE AND/OR OFFSET ANY ISSUES ARISING FROM ITS PRICING AND/ OR STORAGE?
First and foremost, we need to understand the context. We are transitioning from coal which is a fossil energy that has been optimized over centuries. New energy sources naturally have challenges to outprice coal. I have one mantra which says ‘carbon pricing anywhere and everywhere’ and I believe that policies and legislations are moving in the right direction with the EU’s Carbon Border Adjustment Mechanism, Net Zero Industry Act, the US Inflation Reduction Act and so on, but their full impact will take time to materialize. Our strategy for hydrogen is to build and operate the full capacity to supply our needs on-site, thus simplifying transport and bringing a lot of flexibility and other technical and economical advantages. We will use a baseload supply of around 1GW of low carbon electricity from the French grid, avoiding the need for massive storage capacity. These are unique competitive advantages in our value proposition.
Definitively. Several companies are walking the talk in their pledges and realizing that green steel will be in short supply, therefore a premium needs to be paid to secure volumes. It’s already the case for players like H2GS, for example – and hats-off for their remarkable progress by the way.
Some enablers are needed though; for example, harmonisation of green standards, definitions, traceability and certification, which in my opinion should be technology agnostic and directly linked with the CO2 footprint, plain and simple.
But I must stress that the market only worries about premiums because CO2 emitters are not (yet) paying for their full emissions. In a not-too-distant future, with a further increase of CO2 prices and phase-out of free allowances, green steel will be the new standard and the market will stop talking about premiums, focusing instead on CO2 penalties for those not in compliance.
2017, José and a Bessemer converter
DELIVER IMPROVED YIELDS, HIGHER-QUALITY STEEL AND REDUCE COSTLY DOWNSTREAM PROCESSING ON THE BOF/EAF STEEL MAKING
The high-resolution Slag Detection System (SDS) thermal imaging camera detects the transition between steel and slag and has been specifically designed to survive in harsh operating conditions, whilst utilising a particular wavelength to reduce obscuration caused by smoke and fumes.
Suitable for operators of secondary steel making vessels including stainless steel, SDS can also be used in other smelting operations such as copper and platinum. Its automatic operation ensures that only the predefined amount of slag is carried over before an alarm is triggered.
GET THE BENEFITS:
Automatic detection and tracking accurately identifies the stream, reducing background interference
SDS is AMETEK Land’s definitive solution for monitoring and reducing slag carry-over in steel production facilities whilst saving money and improving operator safety.
Accurate detection independent of charge weight
Fully automatic operation and clear alarm notifications
Improved connectivity through the use of Open Data Interface
WHY FRANCE AS THE LOCATION FOR YOUR FIRST PLANT?
Several factors. For example, the fact that it is a good location with competitive logistics inbound and outbound, an availability of competences, and the ambition of the French government to put in place incentives to transform the country by reindustrializating, reshoring critical value chains and ensuring sovereignty. One other key aspect was certainly access to vast amounts of competitive and low carbon electricity. For many reasons, we are confident that our project in Fossur-Mer combines the right elements to produce low CO2 metallics that will be sold to frontrunners paying a premium, while ensuring a strong business case to everyone.
GOVERNMENTS IN EUROPE, ASIA, NORTH AND SOUTH AMERICA, AND AFRICA HAVE SHOWN A RANGE OF RESPONSES TO CLIMATE CHANGE, AND DECARBONIZATION TARGETS. WHAT EXAMPLES OF LEGISLATIONHAVE SHOWN THE MOST SUCCESS?
Everyone has been very vocal about IRA in the US which can be a game changer. Nevertheless, I remain confident that Europe is making concrete steps in the right direction. Green Deal was instrumental on the demand side and now initiatives like NZIA and the H2 Bank will foster a ‘made in Europe’ supply. All these responses to climate change are very welcome as they create a competitive environment to support companies in different regions. That being said, I really hope that the different policies enable the development of economies in low-income countries to minimize inequalities.
ARE THERE ANY OTHER AREAS OF THE WORLD THAT WOULD BE VIABLE FOR POTENTIAL EXPANSION?
Absolutely. Hard-to-abate industries will gradually electrify and move from coal, oil, and gas to green power. In the case of steel, it shall be especially so for ironmaking, therefore, besides our project in Fos-sur-Mer, we have a great opportunity in Finland and many other investigations ongoing.
WHAT ARE THE BIGGEST STUMBLING BLOCKS FOR THE STEEL INDUSTRY AT PRESENT?
We all agree that steel is an asset-heavy and capital-intensive industry. But it is also an enabler to fight climate change and, therefore, a must-have industry. Steel companies need to embrace change and avoid the trap of waiting too long.
Our industry has a great opportunity to modernize, reshape the value chain, do better. For this to happen we need strong policy formulation (again, carbon pricing anywhere and everywhere), improved infrastructure (electrical grid for example), access to capital (debt, equity and smart subsidies), aggregated demand, and more cross-sector collaboration to foster technological innovation.
Below: 2023, With Chris Barrington the global DRI and HBI guru.
WHAT WILL THE STEEL INDUSTRY LOOK LIKE IN 50 YEARS FROM NOW? WHAT KINDS OF TECHNOLOGIES AND PROCESSES WILL BE AT THE FOREFRONT?
First I predict that steel will remain the material of choice which makes me confident that we will continue having a very strong industry. Needless to say, steel quality will continue its absolutely remarkable evolution observed in the last decades, while steel in use and product design will be further improved. Technology wise, I tend to be pragmatic and recognize that we shall have a combination of solutions, with many EAFs supplied with H2-based DRI (hopefully from several GravitHy plants) as I also expect some remaining blast furnaces with carbon capture in specific locations where CCS/U can be acceptable and competitive with new technologies like molten electrolysis finally seeing the light. All-in-all, I believe in 50 years’ time steel will be greener and an enabler of the future we all want.
Steelmakers in North America are increasingly being drawn to hydrogen’s multiple advantages as a clean energy source, as infrastructure continues to adapt and accommodate its storage, transport, and deployment.
By Myra Pinkham*WHILE still in early stages, some steelmakers – particularly those with integrated mills –are starting to look at incorporating the use of hydrogen in their steelmaking processes.
“We could see hydrogen playing a more important role in the steel industry going forward, particularly to replace coal and natural gas in the iron ore reduction process, but to date its use has been rather limited due to hydrogen’s cost and availability,” Martin Pei, SSAB’s chief technology officer said.
Phil Gibbs, an equity researcher with KeyBanc Capital Markets, agreed, stating
that while hydrogen has been discussed for a very long time, it hasn’t been seen as commercially viable by steelmakers until very recently. In fact, he said that while conversations between steelmakers and hydrogen suppliers had begun somewhat sooner in Europe and some other areas of the world, he doesn’t believe that it was a major talking point in the United States until such legislation as the Inflation Reduction Act (IRA) and the IIJA bipartisan infrastructure bill were passed.
But now there seems to be some growing optimism. In fact, during his company’s
*North America correspondent, Steel Times International
third quarter earnings conference call, Lourenco Goncalves, Cleveland-Cliffs’ chairman, president, and chief executive officer, declared, ‘hydrogen is the future,’ as long as hydrogen is available and cost competitive. He said that is being made more possible by the clean hydrogen hubs that are being created as part of the IIJA.
This sentiment has not only been the case for the use of hydrogen by the steel industry but for the broader hydrogen market, Frank Wolak, chief executive officer of the Fuel Cell & Hydrogen Energy Association, admitted. He said that about 20 years ago
which is more efficient and is better able to tolerate variable flows of electricity, making it more compatible with the alternative energy resources needed to make cleaner, or greener, hydrogen.
“These are proven technologies,” Wolak said. “It is just a question of scaling them up.” He noted that while only about 10-11Mt of hydrogen is currently being produced in the US, that is expected to increase to 50-60Mt/yr.
One thing pushing that is the tax credits
For example, refineries use hydrogen to reduce the sulphur content in fuels, he noted. It is also used to increase the ammonia content in fertilizers and to produce methanol for the chemical industry.
He said that the global steel industry used about 5Mt of hydrogen in 2023. But SSAB’s Pei said that he could see hydrogen playing a much more important role in the global steel industry going forward for environmental reasons, noting that steel production currently accounts for about
there had been a push for hydrogen, largely driven by the desire to use hydrogen as a lower emissions vehicle fuel.
“But that push fell apart because it was too premature,” Wolak declared, explaining that the hydrogen production technology still needed to evolve, which he said it has since done in a major way. Technology for electrolyzers, compressors and fueling stations has significantly improved, while the renewable energy sector has witnessed growth, and the technology for making hydrogen from natural gas – and other new innovations such as potentially adding carbon capture and sequestration for the resultant carbon emissions – have been refined.
As far as advancements in hydrogenrelated electrolysis, Wolak noted that there has been a movement from using alkalinebased electrolyzers toward using proton exchange membrane (PEM) technology,
in the IRA. This includes a clean hydrogen production tax credit of up to $3 per kilogram and an investment tax credit of up to 30% for clean hydrogen projects that are due to begin construction by 2033. The level of these credits is based upon the carbon intensity of the hydrogen.
There are several different types of hydrogen with different carbon intensities. Wolak noted that ‘green or ‘clean’ hydrogen is produced used such renewable energy sources as wind, solar and hydropower, while ‘pink’ hydrogen is produced using nuclear energy, ‘gray’ hydrogen is produced using natural gas and ‘blue’ hydrogen is also produced from natural gas, but carbon capture and sequestration is also used to limit some of its carbon emissions.
Both globally (where hydrogen production has increased to about 98Mt by 2023 from 95Mt in 2022 and 90Mt at the beginning of decade) and in the US, very little hydrogen is being used as an energy source, Paul Butterworth, sustainability research manager for CRU pointed out. Instead, it is being used as a raw material.
7-8% of global carbon dioxide emissions.
Kevin Dempsey, president and chief executive officer of the American Iron and Steel Institute (AISI) pointed out that steel’s interest in hydrogen isn’t as an energy source, but rather to use it as an iron ore reduction agent to replace the use of coking coal, or coke, in a blast furnace and the use of natural gas in direct reduction facilities.
He explained that when coke is used as an iron ore reductant in a blast furnace it creates a pure, or close to pure, hot iron product. But doing so it emits carbon dioxide, which is a by-product of that process. However, if the steel mill uses hydrogen instead then the by-product is water vapour instead of carbon dioxide. “So, you go from producing a greenhouse gas to something that is generally considered to be harmless.”
Pei maintained that SSAB has led the drive for the use of hydrogen for steel production, when in 2016 SSAB invited LKAB and Vattenfall to jointly launch their HYBRIT initiative to develop a new fossilfree steelmaking technology that through
Cut-To-Length Lines
Crop Shears
Rotary Shears
Stretcher Levelers
Hydraulic Roller Levelers
Scrap Choppers
When it comes to building equipment to process ferrous and non-ferrous metals, nobody does it better than Butech Bliss.
For 135 years, steel producers and steel service centers have counted on Butech Bliss to deliver the design, engineering and technological advantages necessary to help them succeed. From entry to exit end we build it all. Our product lines include roller and stretch leveling technology, a full line of shears, material handling equipment and complete coil processing lines. We are more than a scrap chopper manufacturer.
Learn more about our world-renowned coil processing technology call +1 (330) 337-0000, visit ButechBliss.com or email sales@butech.com.
If our name is on the machine, it’s built better.
its use of hydrogen gas, emits water instead of carbon dioxide.
The companies have been jointly operating a pilot plant to produce hydrogen reduced sponge iron in northern Sweden since 2020 using renewable sources of power, and, given its positive results the companies plan to build a commercial scale facility, also in northern Sweden, which they hope to be commissioned by 2026.
Furthermore, SSAB is transforming its steel production in the Nordics by replacing current blast furnaces with electric arc furnaces in both Sweden and Finland.
“Given that we want our products to be fossil-free, we don’t want to use what is called blue or gray hydrogen, but hydrogen produced from fossil-free sources such as hydropower, wind and solar power,” Pei said.
“Our steelmaking peers have also started to move in this direction,” Pei said, predicting that in the coming decade or two a significant amount of steel production will move to the hydrogen route.
He said that while the most pressure to reduce emissions has been upon blast furnace-based steelmakers, some electric arc furnace (EAF) steelmakers have also started to look at using hydrogen given expectations that scrap will be in increasingly tight supply going forward, making DRI an even more important metallic input for all steelmakers.
While DRI is largely produced using natural gas, AISI’s Dempsey said that due to the way that modern DRI production facilities have been built, companies could substitute a lot of natural gas with hydrogen without making major modifications.
Also, KeyBanc’s Gibbs pointed out that Cleveland-Cliffs has already been making upgrades to its hot briquetted iron (HBI) facility, as well as one of its blast furnaces, to enable it to use hydrogen once it believes that hydrogen becomes commercially viable and scalable, and it believes it will help its steelmaking process.
Goncalves told investors that once cost competitive hydrogen becomes more available only minor additions are necessary, like the new pipeline and a couple of valves that Cliffs is currently installing at its Indiana Harbor plant – a capital investment of less than $9 million.
CRU’s Butterworth said that US companies that operate DRI plants, like
Cliffs and Nucor, could not only look to use hydrogen but to utilize carbon capture technologies at those plants. He said that would allow them to capture and store about 85% of their emissions.
Dempsey pointed out that in May, Cliffs had a successful trial injecting hydrogen directly into its No. 3 blast furnace at its Middletown Works as a partial substitute for coke. “It doesn’t have to be all or nothing,” he said, especially given that there could be a need to build new mills to use 100% hydrogen. “Cliffs’ test showed that companies can use hydrogen in an existing blast furnace to reduce carbon emissions.”
“Our decision to use hydrogen on our decarbonization path will set us apart from the crowd,” Goncalves said, stating that he believes that can be achieved in a costeffective, quality-driven manner.
Hydrogen use in the US is also expected to get a push from the seven hydrogen hubs that were formed last year as part of the IIJA bipartisan infrastructure bill, although Wolak said that it could be a year before the contracts for those hubs are finalized.
Dempsey said that it is the Midwest hydrogen hub in the Great Lakes region of the country that would have the biggest impact upon the US steel industry, as it is a critical location for Cleveland-Cliffs. In fact, Goncalves said it was Cliffs’ commitment to buy a large portion of the hydrogen output from the Midwest hub that helped to get that location selected by the Department of Energy.
He told investors that the very existence of the hub could attract other sectors to use hydrogen, giving the example that hydrogen fuelled vehicles could be a viable alternative to battery powered ones. Overall, while there is some increased optimism, it remains to be seen how much hydrogen production and its use by the steel industry takes off, KeyBanc’s Gibbs said. “It is being talked about, but like any other technology it must be proven over time. We are still early in that process.
Dempsey agreed, stating that a lot will depend upon how quickly hydrogen companies can ramp up their production and how quickly it is available at a more competitive price. But given the industry’s goals to achieve net zero emissions, Butterworth said it is possible that a significant amount of steel production will move to the hydrogen route over the next decade or two. �
Fossil-fuel reliant technology is out, and the electrification of heating solutions is in, says Dilip Chandrasekaran*. Kanthal, supplier of heating solutions, aims to manage the task of providing sustainable processes to allow steelmakers to decarbonize without compromising efficiency.
1. How are things going at Kanthal?
Is the steel industry keeping you busy?
Yes, very busy. We see a strong interest from the steel industry globally with a clear focus to electrify processes within steel processing.
2. What is your view on the current state of the global steel industry?
The need to minimize carbon emissions and enhance energy efficiency in numerous heavy industries has led to the growing shift from combustion-based heating solutions to electric heating.
For example, there is a strong drive within the steel sector to reduce emissions and increase efficiencies. The reduction of CO2 emissions is targeted in two ways: replacing carbon and coke with green hydrogen in the reduction of iron ore, and converting fossil-fired heating processes to electric. In both cases, electric heating solutions will be key in the heating of process gases or in various downstream processes within steel production.
3. In which sector of the steel industry does Kanthal mostly conduct its business?
Mainly in downstream steel processing such as heat treatment, annealing, reheating, roller hearth furnaces, where conversion from gas to electric is relatively straightforward.
4. Where in the world are you busiest at present?
In general, the strongest drive to reduce emissions and replace fossil-heating within the steel industry is in Europe, but steel companies in other regions are also driving projects and initiatives to reduce emissions.
5. Can you discuss any major steel contracts you are currently working on?
During the last quarter, we received a pilot order for electric process gas heaters for the upstream steel industry, to be used by a steel manufacturer in Asia to improve their existing blast furnace process. This generates both lower carbon emissions and improves the efficiency of the blast furnace process, resulting in a final product with a lower environmental impact compared with conventional technology.
6. Where does Kanthal stand on the aluminium versus steel argument? Kanthal develops and delivers heating solutions to both the steel and aluminium industries. The potential to reduce emissions by electrifying is much larger within steel, but the aluminium industry –with ready access to electric power – has become more active in replacing fossil heating with electric.
7. What are your views on Industry 4.0 and steelmaking?
The focus from the steel industry at present is more towards the reduction of carbon
emissions rather than driving Industry 4.0 within steelmaking. Electric heating (resistance heating) could potentially offer better control and digitalization opportunities compared to the existing heating technologies.
8. In your dealings with steel producers, are you finding that they are looking to companies like Kanthal to offer them solutions in terms of energy efficiency and sustainability? If so, what can you offer them?
There is a strong need from the steel industry to reduce emissions and increase efficiency. Kanthal can offer electrification solutions in heating processes to replace gas burners, offering both higher energy efficiencies, reduced costs and lower emissions, thereby enabling the steel industry to meet its sustainability goals.
9. How quickly has the steel industry responded to ‘green politics’ in terms of making the production process more environmentally friendly and are they succeeding or fighting a losing battle?
This varies globally due to differences in infrastructure, availability of energy/ electricity and government regulations. The global steel industry is responding to the challenge in reducing emissions, but the timeline to achieve this varies in different regions.
10. Where does Kanthal lead the field in terms of steel production technology?
Kanthal is a leader in offering a wide range of resistance heating solutions for various processing steps within the steel industry. The Kanthal product range covers the whole temperature spectrum required by the steel industry and can, therefore, offer the potential to convert a wide range of
downstream processing steps, from gas to fossil-free. Furthermore, Kanthal is one of the leaders in developing new innovative technologies for large-scale heating of gases that will be crucial in ironmaking (DRI and more efficient blast furnaces).
11. How do you view Kanthal’s development over the short-tomedium term in relation to the global steel industry?
In the short-to-medium term, Kanthal’s development will be focused on downstream steel processing where electric heating solutions already exist to a large extent. The focus will be on scaling up existing heating solutions and making them reliable and robust to fit the demands of the steel industry.
12. China dominates global crude steel production. How should the industry react to this situation?
To reduce emissions and become fossil-free globally, it is vital that the steel industry in China also reduces emissions and becomes fossil-free. It will be important to have carbon emission taxes globally to drive transformation of the steel industry also in China.
13. What is Kanthal’s experience of the Chinese steel industry?
Kanthal supplies premium products to the Chinese steel industry, but the competition from local Chinese suppliers is very tough.
14. Where do you see most innovation in terms of production technologies – primary, secondary, or more downstream?
There are ongoing projects and there will be a big need for innovative technology development within primary steelmaking, i.e replacing blast furnaces with DRIbased processes. Also, within downstream steelmaking, innovations will be needed within specific processing steps, like ladle and tundish heating, to replace existing gas burners with innovative fossil-free technology.
15. How optimistic are you for the global steel industry going forward and what challenges face global producers in the short-to-medium term?
We are very positive since most technical solutions are already available for many of the downstream steel heating processes. In the short-to-medium-term, the challenge is to scale up heating solutions for the steel industry to have robust and reliable solutions that can meet the challenges of the steel industry.
16. Kanthal is headquartered in Sweden; what’s happening steel-wise in the area?
The Swedish industry is very actively driving a transformation to a fossil-free steel industry, with an attractive electricity price and relatively good availability of fossil-free electric power supply. There are several large projects and investments being run in Northern Sweden to set up new sites for the production of fossil-free steel (Hybrit, H2 Green Steel). Most Swedish steel companies have clear roadmaps to become fossil-free in the coming 10-15 years.
17. Apart from strong coffee, what keeps you awake at night?
All the other obstacles besides heating technology that could potentially slow down or even hinder the transformation of the steel industry to become fossil free. Obstacles like access to fossil-free hydrogen, fossil-free electricity, electric power supply, to name a few.
18. If you possessed a superpower, how would you use it to improve the global steel industry?
I would use it to provide easy access to fossil-free electric power to the steel industry to enable conversion from gas heating and thereby reducing emissions. �
Coalport Bridge, a successor of England’s famous 18th Century Iron Bridge, is a showcase of innovation and design in its ability to carry vehicles over 200 years after its construction. By
THE Iron Bridge, in England’s West Midlands, is famous the world over for being the first substantial bridge to be built in cast iron. Completed by Abraham Derby III in 1779, the Iron Bridge spans the River Severn at Ironbridge Gorge. The single arched bridge has a span of 30.63m (110’
6”) rising 16.75m (55’) above mean water level. Five cast iron ribs support the bridge deck, and the 1,700 components that make up the bridge have a combined weight of 378 tons, the heaviest single component weighing 5.25 tons. Components are keyed together by joints reminiscent of carpentry
Tim Smith*joints, the bridge building technology of the day being of timber bridges. The bridge carried traffic until 1934, after which it was restricted to pedestrians.
Just two miles downstream of the Iron Bridge is another cast iron single span arched bridge, Coalport Bridge. Constructed
*Consulting editor, Steel Times International, and honourable secretary, Wealden Iron Research Group
in 1818, 39 years after completion of the Iron Bridge, this is of slimmer design and still carries vehicles today – all be it with a weight restriction.
The 1818 bridge was built as a replacement to earlier timber and timber and iron bridges. The first, an all-timber construction was started in 1777, two years before the Iron Bridge, and opened to traffic in 1780, seven months prior to the Iron Bridge opening to the public. It consisted of two 18.3m (60’) spans with a timber pillar in the middle of the river. It survived until 1795, just 15 years after opening, then being washed away in a winter storm, a storm survived by the Iron Bridge.
Following the success of the Iron Bridge, the replacement bridge at Coalport, designed by John Onions and John Guest, had a single span of three cast iron ribs, supporting a wooden deck. Constructed in 1799, this survived nearly 20 years until the central cast iron rib cracked.
The bridge was rebuilt by Onions in 1818, with the addition of two more ribs and cast iron deck plates. The buttresses were also increased in height. This is the bridge that survives today and is designated a Historic Monument. It still takes traffic across the river, all be it, with a weight restriction of two-tonnes and a speed limit of 10mph (16km/h), and a limit of only one vehicle on the bridge at any time.
Each of the five ribs has a helical twist, probably not a deliberate design feature as this requires each triangular spandrel, supporting the deck above the rib, to be of a unique design, but rather the result of distortion during cooling after the casting process.
The cast iron parapet proved an unstable addition as wrought iron wedges were used to secure each section. These corrode (more so than the cast iron) and swell, causing instability in sections of the parapet.
To warn drivers of heavier vehicles not to cross the bridge, today, an electronic weigh bridge monitors incoming traffic, warning drivers of overweight vehicles to stop and turn around. �