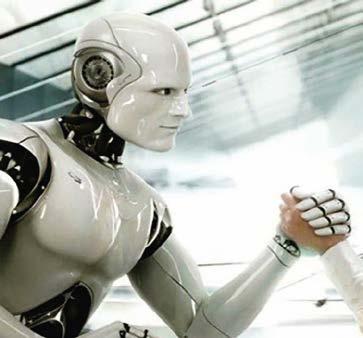
29 minute read
I robot ? Creano crescita e
Viene dagli Stati Uniti l’ultimo studio che prova a rispondere alla domanda che accompagna lo sviluppo e la crescita dell’industria 4.0: i robot stanno “rubando” il lavoro all’uomo?
I ROBOT? CREANO CRESCITA E OCCUPAZIONE, MA SOLO NELLE AZIENDE CHE LI ACQUISTANO
Analizzando il mercato francese,
Atre economisti – Daron Acemoglu (MIT), Claire LeLarge (Université Paris-Sud) e Pascual Restrepo (Boston University) – hanno osservato come nelle aziende che acquistano robot aumenti il valore aggiunto, la produttività e l’occupazione, portando grandi benefici in termini di competitività. Un processo virtuoso che però avviene a discapito del livello di occupazione nel mercato di riferimento, in quanto tale parametro diminuisce nelle aziende concorrenti a un livello superiore rispetto alla forza lavoro introdotta nelle aziende dotate di robot. Si instaurerebbe insomma un gioco a due fattori il cui saldo netto sarebbe – questa la conclusione dello studio – un complessivo calo occupazionale nel mercato di riferimento. Se da un lato la maggiore produttività introdotta in azienda dall’utilizzo di robot tende a far crescere la domanda di lavoro, lo spostamento di produttività dal lavoratore al robot garantirebbe effetti positivi sul singolo ma anche una diminuzione dell’occupazione e dei salari a livello complessivo.
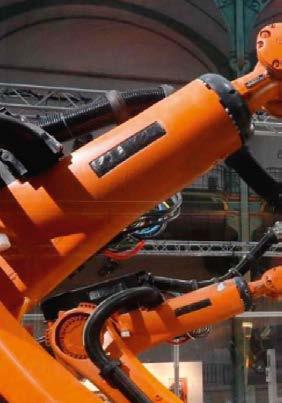
La ricerca
A fornire questa nuova analisi, dicevamo, sono l’economista francese Claire LeLarge e Daron Acemoglu e Pascual Restrepo, due professori che già nel 2017 avevano già affrontato l’impatto dei robot sull’industria (allora con riferimento al mercato statunitense),
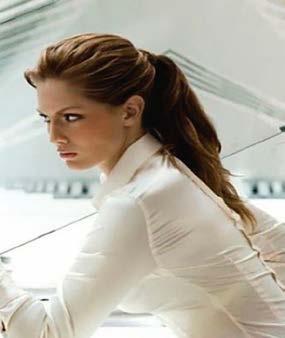
mostrando alcuni dati secondo i quali questo processo avrebbe provocato un calo di occupazione e salari. Ora l’attenzione degli studiosi si concentra per la prima volta su un paese europeo – la Francia – molto più vicino al nostro per cultura e tipologia del mercato del lavoro, descrivendo una situazione più complessa. Su un campione di 55.390 imprese francesi attive tra il 2010 e il 2015 nel settore manifatturiero, gli economisti si concentrano sulle 598 che nel periodo in considerazione hanno acquistato robot industriali. Un gruppo di aziende che, sebbene rappresenti numericamente poco più dell’1% del campione, impiega da solo il 20% della forza lavoro e produce il 20% del valore aggiunto complessivo.
Chi compra robot cresce
La ricerca mostra proprio come queste aziende abbiano registrato tra il 2010 e il 2015 una crescita del 20% in termini di valore aggiunto, ma nello stesso tempo il contributo apportato dal fattore lavoro è diminuito del 4,3%. La riduzione del contributo del fattore lavoro al valore aggiunto però non ha comportato una riduzione in termini assoluti dell’occupazione, anzi: in queste aziende sono cresciuti sia il numero di ore di lavoro totali (+10,9%) che il salario orario dei dipendenti (+0,9%). Una delle spiegazioni possibili che fornisce lo studio alla crescita in termini occupazionali delle imprese che impiegano robot, è che solo le aziende con un grosso potenziale di crescita possano essere inclini a introdurli, creando una sorta di circolo vizioso. Ma l’effetto positivo in realtà potrebbe anche essere una conseguenza della redistribuzione dei beni e della forza lavoro dovuta alla riduzione dei costi rispetto ai competitor. Il concorrente che non introduce i robot, infatti, registra una significativa perdita di valore aggiunto e occupazione.

L’occupazione generale scende
Le imprese che adottano robot, riducendo i costi, guadagnano quindi quote di mercato a scapito dei concorrenti. Di conseguenza, la crescita occupazionale in queste aziende può andare di pari passo con la perdita di posti di lavoro nelle altre. Lo studio infatti mostra che se un’azienda incrementa del 10% l’utilizzo di robot, i suoi competitor registrano un calo occupazionale del 2,5%, e un calo del valore aggiunto del 2,1%, mentre il fattore lavoro non subisce variazioni sostanziali. Ma qual è il saldo complessivo? Sommando tutti i fattori – aumento dell’occupazione nelle aziende che adottano tecnologie robotiche e riduzione dell’occupazione nelle altre – emerge che a fronte di un aumento del 20% dei robot in un determinato settore si genera un calo del 3,2% del livello complessivo di occupazione in quel settore.
INDUSTRY 4.0 D E S IG N MAGAZINE
FABBRICHE A CORRENTE CONTINUA, PIÙ CHE UN’IPOTESI?
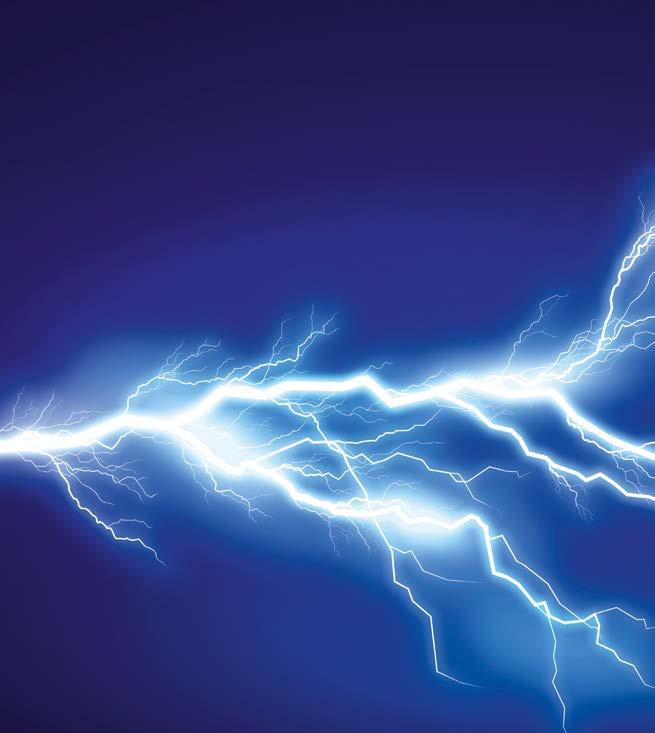
Un convegno sponsorizzato da LAPP Italia pone all’attenzione degli addetti ai lavori i vantaggi che si avrebbero distribuendo la corrente elettrica in forma continua invece che alternata. In Germania da un paio d’anni è attiva un’iniziativa in tal senso. Ma ci sono anche svantaggi.
LLe reti di distribuzione dell’elettricità portano nelle nostre case e nelle nostre fabbriche corrente alternata, ma è innegabile che gran parte degli apparecchi che alimentiamo usano al loro interno la corrente continua. E allora non avrebbe più senso distribuire direttamente corrente continua, riducendo la complessità della sincronizzazione e gli sprechi del processo di conversione AC/DC? Questo, in sintesi, l’interrogativo che si sono posti i relatori dell’evento “Rivoluzione Energetica: il futuro dell’industria è in corrente continua?” tenutosi al Palazzo dei Giureconsulti a Milano e sponsorizzato da LAPP Italia, filiale locale del Gruppo LAPP specializzato nei cavi, connettori e accessori per l’automazione.
L’evento, aperto dal managing director di LAPP Roberto Pomari, ha visto intervenire, fra gli altri, Marco Vecchio, Segretario di ANIE Auto
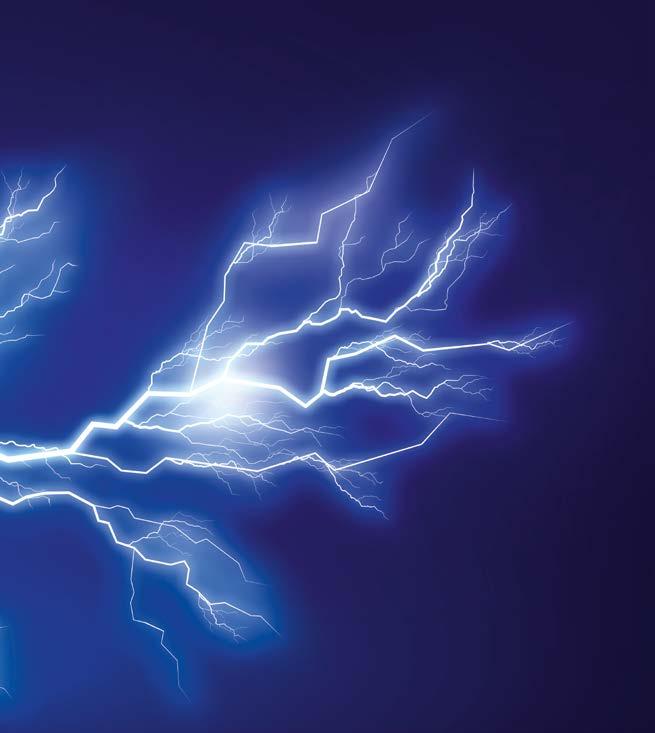
mazione, Giambattista Gruosso, Professore Associato del DEIB – Politecnico di Milano, Georg Stawowy, CTO di LAPP Holding, e Gaetano Grasso, Head of Product Management and Marketing di LAPP.
Il problema
Se le nostre reti trasportano l’elettricità sotto forma di corrente alternata, è a causa di una vera e propria guerra commerciale e di brevetti che vide protagonisti, negli ultimi anni del 1800, Thomas Edison (schierato per la corrente continua) e George Westinghouse, che aveva scommesso sulla corrente alternata, insieme al geniale Nikola Tesla, artefice (anche con Galileo Ferraris) di gran parte delle scoperte e invenzioni che avevano permesso di trasformare l’elettricità da fenomeno da laboratorio a fonte di energia ad ampio spettro. Vinse Westinghouse, grazie appunto all’apporto di Tesla e a un problema insormontabile che affliggeva la corrente continua: il trasporto su lunga distanza a quei tempi non era possibile, pena la perdita della maggior parte dell’energia sotto forma di calore, a causa
INDUSTRY 4.0 D E S IG N MAGAZINE
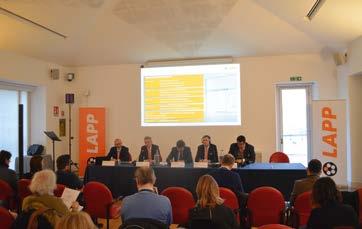
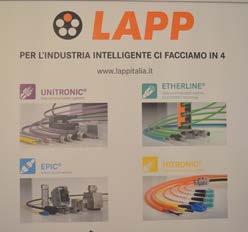
del bassissimo voltaggio generato dalle dinamo dell’epoca. Da allora viviamo in un mondo percorso da cavi che portano corrente alternata. Ma, soprattutto a partire dal dopoguerra, con l’arrivo dell’elettronica di potenza, il numero di apparecchi capaci a funzionare con corrente continua è costantemente aumentato. Qualsiasi dispositivo alimentato a batteria di fatto lavora in corrente continua, ma anche molti apparecchi che alimentiamo in alternata, al loro interno hanno un trasformatore e un ponte rettificatore (o più recentemente un circuito di alimentazione “switching”) che serve a trasformare l’alternata in continua, per alimentare i circuiti. Il caricabatteria del vostro cellulare fa proprio questo: trasforma l’alternata a 220V in corrente continua a 5V.
L’opportunità
Durante il suo intervento, il professor Gruosso ha fatto notare che al centro del piano Industria 4.0 (ora Transizione 4.0) non ci sono, come molti credono, IioT e AI, non è che Industria 4.0 sia equivalente a fabbrica più cloud più Wi-fi: il tema fondamentale del progetto 4.0 è l’innovazione. E fra i molti modi di fare innovazione, uno particolarmente importante è la riduzione dei consumi, l’efficientamento energetico dei macchinari. Ora, fra le possibilità concrete per migliorare l’efficienza e l’ecosostenibilità c’è proprio quella di creare microgrid in corrente continua da fonti rinnovabili – per esempio, i pannelli fotovoltaici. La Germania ha avviato da un paio d’anni un’iniziativa in tal senso, chiamata Industry DC (per Direct Current), alla quale partecipano molte delle più grandi aziende. Ma quali sono in concreto i vantaggi dell’uso della corrente continua in un’architettura microgrid? Per prima cosa, è possibile l’integrazione diretta nella rete di forme di immagazzinamento dell’energia – batterie, in altre parole. Poi ci sono miglioramenti dell’efficienza dovuti a vari fattori. Per
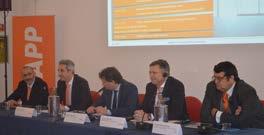
esempio il recupero dell’energia in frenata per i robot, l’eliminazione delle perdite da conversione AC/DC, la facile integrazione con fonti rinnovabili come il fotovoltaico o l’eolico. Infine, si semplifica l’installazione di cablaggi e apparecchi: meno cavi (non ci sono più tre fasi da gestire), nessuna problematica di sincronizzazione della frequenza portante di 50 Hz, riduzione della componentistica. Un esempio a questo proposito: è vero che la maggior parte dei motori industriali funziona in alternata, ma non certo con quella a 50 Hz. Per questo hanno bisogno di un “drive” che prenda l’alternata in ingresso, la converta in continua, e poi la riconverta nel tipo di alternata che serve per muovere il rotore. Con l’alimentazione in continua, il primo stadio di ciascun drive, responsabile di parte delle perdite da conversione, verrebbe completamente eliminato. Discorsi simili si possono fare per altri settori nei quali la corrente continua sta già riscontrando una notevole diffusione. Basti pensare ai data center, dove la continua ha iniziato a diffondersi dalle sezioni dedicate alle apparecchiature “telco” e oggi si avvia a diventare la tecnologia prevalente. O ai cavi sottomarini, dove la continua è già mainstream.
Prospettive e tendenze
Marco Vecchio ha mostrato durante l’incontro una slide di Electrify Italy, densa di informazioni: a sinistra sull’impiego crescente dell’elettricità, a destra sulle conseguenze positive. Fra i dati che emergono, la previsione che nel 2050 il 46% del fabbisogno di energia in Italia sarà coperto dall’elettricità (ora siamo sotto il 19%). Solo per il trasporto (auto elettriche), la quota passerà al 41% dall’attuale 3% e spiccioli. Inoltre, l’85% dell’energia sarà prodotta da rinnovabili, molte delle quali sono intrinsecamente in corrente continua. In conseguenza del maggiore impiego di elettricità al posto di altre fonti, si prevedono un calo delle emissioni di CO2 del 68%, risparmi sulla sanità (dovuti alla migliore qualità dell’aria) per quasi 700 miliardi di euro, un risparmio sulla bolletta energetica delle famiglie intorno al 17%, e un calo del consumo primario (grazie alla maggiore efficienza energetica) fino al 42%. Una serie di possibili scenari sono stati mostrati da Georg Stawowy, che ha mostrato come una rete impostata sulla continua (anche
Diversi scenari di rete con le relative efficienze complessive
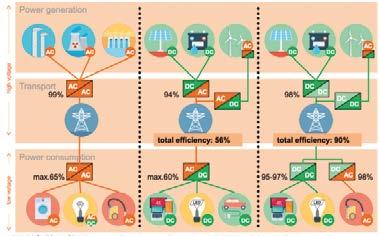
per la trasmissione a lunga distanza/alto voltaggio) abbia un’efficienza totale maggiore di quella di una rete tradizionale in alternata e anche di una rete con generazione in parte continua, trasporto in alternata e utilizzo in continua dopo conversione. “L’Italia consuma oggi circa 321 Twh – ha dichiarato Stawowy. - se riuscissimo a migliorare l’efficienza del 10%, potremmo emettere 34,4 milioni di tonnellate di CO2 in meno ogni anno, e 23,6 milioni di tonnellate di NOx. La riduzione di consumi permetterebbe di spegnere un paio di grandi centrali, tipo la Federico II di Brindisi e la Torrevaldalica Nord a Civitavecchia”. E a riprova di questo, ha osservato che il progetto DC-Industrie2 (seconda fase del già citato DC-Industrie) è oggi uno dei più grandi progetti di ricerca in Germania, con la Mercedes impegnata nel progetto con la “Factory 56” di Sindelfingen, una smart
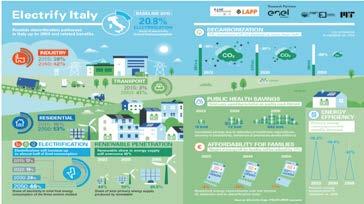
Le previsioni di elettrificazione, a destra i vantaggi previsti
factory 4.0 alimentata da una grid in continua, mentre Bmw e Audi hanno in cantiere progetti similari.
Applicazioni industriali
A chiudere l’incontro è stata la presentazione di Gaetano Grasso, che ha mostrato alcuni esempi pratici della maggiore efficienza raggiungibile in azienda con l’utilizzo di griglie di alimentazione in corrente continua. Per esempio impiegando nuovi driver per CC, o bypassando il primo stadio di conversione di quelli attuali alimentandoli con corrente continua da 380V. Grasso ha anche parlato della necessità di standardizzazione della tecnologia CC, delle sfide che interesseranno i produttori di componenti (la mancanza di standard, la necessità di rendere facile l’uso, la possibilità di scollegare sotto carico, la prevenzione o estinzione di eventuali archi elettrici…) e in particolare chi fabbrica cavi – LAPP con i suoi OLFLEX ha sicuramente molto a cuore questo aspetto – con aspetti da considerare come vita utile, comportamento degli isolanti in presenza di CC, effetti delle scariche sugli isolanti eccetera. Tuttavia, i problemi tecnici sono risolvibili e le prospettive sono positive: riduzione delle perdite di conversione, integrazione delle energie rinnovabili, uso dell’energia di recupero e risparmi resi possibili da design più semplici e compatti sono fattori decisamente cospicui a favore della corrente continua. Non per niente LAPP ha già a catalogo soluzioni destinate alla applicazioni in corrente continua, per esempio nel fotovoltaico e nell’automotive. Parliamo dei cavi di ricarica CC E-Mobility, delle tecnologie per la connessione di pannelli solari OPV e del sistema di distribuzione dell’alimentazione OLFLEX Solar. In ogni caso, ci sembra difficile che nel prossimo futuro si assista a migrazioni di massa di impianti di distribuzione geografici dalla tecnologia in alternata a quella in continua. Invece, appare molto probabile che si cominceranno a vedere con maggiore frequenza delle microgrid impostate nativamente sulla continua. Pensiamo in particolare a impianti che servono grandi strutture, tipo centri commerciali o sedi di aziende, che utilizzano come sorgente principale di energia parchi fotovoltaici piazzati sui tetti o nei parcheggi. In una struttura di questo tipo, la continua rende più semplice (e più efficiente) lo stoccaggio in accumulatori, necessario a fornire corrente in modo continuativo assorbendo eventuali picchi, e non pone grossi problemi per il trasporto essendo le distanze limitate. L’interscambio con i sistemi ad alternata potrebbe a questo punto essere confinato al collegamento con la rete distributiva generale, normalmente mantenuto dalle microgrid per coprire i casi di emergenza (tipo esaurimento delle batterie in mancanza di energia fotovoltaica) o per vendere energia al gestore della rete generale.
La possibilità di guidare da remoto un tecnico per fare operazioni di manutenzione, anche complesse, attraverso la realtà aumentata, ma anche la realizzazione di digital twin nel campo della robotica collaborativa, dove poter simulare l’interazione tra uomo e macchina. Sono queste alcune delle applicazioni industriali della rete 5G che, con la release 16, che sarà rilasciata nel 2020, passa da una fase più dedicata al mercato consumer a quella industriale. IL 5G ALLA SFIDA DELL’INDUSTRIA, ECCO QUALI SONO LE NUOVE FRONTIERE
Sono stati questi alcuni dei temi al centro della giornata di studio, organizzata da ANIPLA, l’Associazione Nazionale Italiana per
SL’Automazione, dal titolo Il futuro della comunicazione industriale dal Time Sensitive Networking al 5G. Un’occasione per parlare del futuro dell’industrial networking che, grazie al 5G, potrà migliorare le attuali applicazioni che già sfruttano le reti 3G e 4G, ma anche consentire per la prima volta l’effettivo impiego di tecnologie senza fili in applicazioni di controllo industriale senza rinunce in termini di affidabilità e performance.
Le nuove sfide del 5G e la ricaduta sull’industria
Le reti 5G, quindi, superano nuove frontiere perché puntano non solo su parametri classici, come quelli della velocità, ma anche su altre prestazioni, che possono diventare punti di forza dell’industria. “Il 5G è diverso dalle generazioni precedenti perché non cerca di migliorare soltanto la velocità di trasferimento dell’informazione – spiega Antonio Capone, docente del dipartimento di Elettronica, Informazione e Bioingegneria del Politecnico di Milano – ma cerca di migliorare altri parametri prestazionali, come, per esempio, il consumo energetico, l’affidabilità e il ritardo dei servizi che utilizzano la rete. Questo è importante perché non è soltanto una novità dal punto di vista delle applicazioni che possono trovare appoggio nel 5G, ma soprattutto perché è una sfida di tipo tecnico per consentire al sistema di lavorare in punti che sono caratterizzati da parametri prestazionali differenti”. “La seconda novità importante del 5G – prosegue Capone – è che non è più soltanto un’infrastruttura che fornisce tubi attraverso cui far passare dei bit, come abbiamo sempre inteso la rete, ma è un qualcosa di nuovo, una piattaforma che consente a chi la utilizza di poggiarci anche applicazioni”.
Con il 5G una “seconda occasione” per l’economia locale
Le caratteristiche del 5G diventano anche una buona occasione di rilancio dell’economia perché questa tecnologia, grazie alle sue caratteristiche, può dare nuovo valore alle realtà locali. “Sappiamo che la grande internet ha portato grandissime trasformazioni nel mondo dell’economia e della vita sociale di ogni giorno – ricorda Capone – ma in realtà ha anche spostato gran parte del valore verso chi fornisce le applicazioni sulla rete, togliendolo dall’infrastruttura. Questo ha portato anche a una ridistribuzione in termini di possibilità di sviluppo economico rispetto alle grandi aree a livello globale. Il il 5G, quindi, è un’opportunità perché costringe, proprio per le caratteristiche di ottimizzazione che devono essere basate sul tipo di applicazione, a far lavorare gli operatori insieme alle industrie e ai settori verticali che lo utilizzano”. Una tecnologia che è molto più locale, più radicata sulla conoscenza del dominio applicativo e del modo con cui certi domini si applicano all’economia del territorio. “È una seconda occasione che ci viene fornita di evitare di far andare via il valore, magari oltreoceano – conclude – e tenerlo in Italia e in Europa. Però è un’opportunità che non è detto che venga colta, dipende molto dall’avvio di una collaborazione tra settori industriali diversi. Questa è una sfida che deve essere colta sia da chi gestisce le aziende, ma anche dal ma anche dal punto di vista delle regolamentazioni, delle politiche pubbliche, che devono favorire un modo diverso di creare valore”.
Dalla sperimentazione alle applicazioni
A dare un segnale di quello che potrà rappresentare il 5G per le imprese ci sono, ovviamente, gli operatori. Tra questi ha una grande importanza l’esperienza fatta da Vodafone che, in 18 mesi di sperimentazione, prima del lancio commerciale a giugno, ha coinvolto 38 partner per la realizzazione di più di 40 user case, nuove applicazioni che spaziano dalla sanità alla sicurezza alla mobilità fino all’entertainement e all’education. “In realtà c’è un cuore di soluzioni applicative che riguardano proprio la manifattura e l’Industry 4.0 – sottolinea Sabrina Baggioni di Vodafone – si tratta di 12 user case che insistono su quest’area, con l’obiettivo di tradurre una tecnologia innovativa in un beneficio sia da un punto di vista di maggiore
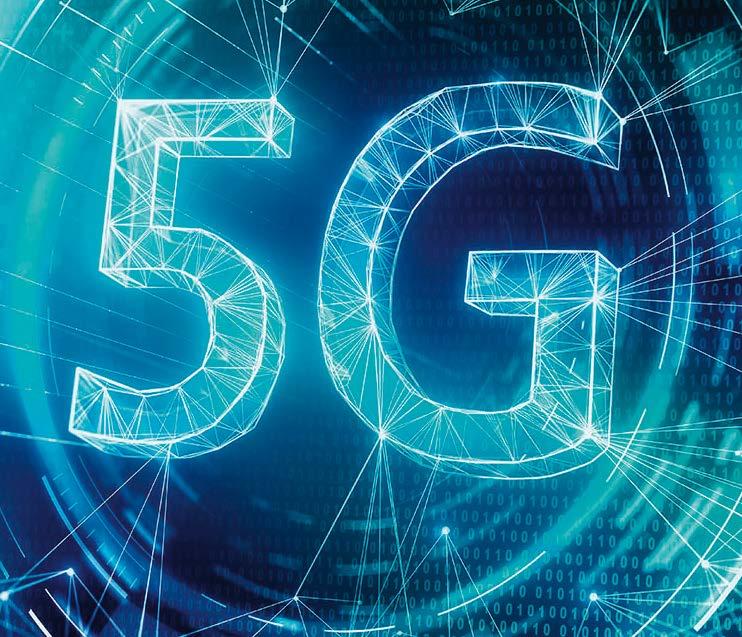
produttività e modularità dell’intervento sull’azienda, sia dal punto di vista della qualità dell’esperienza del consumatore finale o dei dipendenti dell’azienda”. “Uno di questi è una soluzione di realtà aumentata per la manutenzione assistita – prosegue – con un operatore che può intervenire grazie a occhiali smart che sovrappongono all’ambiente reale una serie di immagini grafiche e istruzioni ad altissima definizione. Il 5G permette una bassa latenza che consente alle immagini di muoversi seguendo il movimento dell’operatore, con istruzioni dinamiche. Nel caso in cui l’operatore, per qualche motivo, non riuscisse ad andare avanti l’elevata banda e, ancora una volta, la bassa latenza permettono la videoconferenza con un esperto che, da remoto, riesce a vedere quello che vede l’operatore sul luogo”. “Un altro caso, più specifico, riguarda gli impianti – continua – dove è importante fare un salto di qualità passando dalla sensoristica preesistente, che è cablata, a una sensoristica più evoluta. Con il 5G siano riusciti a portare un un impianto ad avere molti più sensori anche basati su immagini, quindi che sfruttano la banda del 5G senza interventi invasivi né sull’area di programmazione dell’impianto stesso né tantomeno di cablatura. Perché basta collegarlo a un modem e portare l’intelligenza e l’integrazione con il vecchio sistema sull’edge, che è un’altra delle caratteristiche molto importanti del 5G”.
Da Vodafone 10 milioni in 4 anni per le startup
Per sviluppare le competenze in questo comparto, quindi, Vodafone ha investito 10 milioni di euro su un programma quadriennale, arrivato alla terza edizione e rivolto al “tessuto più vivo è più innovativo”, quello delle startup e delle piccole medie imprese, che in Italia sono moltissime, e delle imprese sociali. Una “call” a presentare progetti che possono vedere un’evoluzione dei propri prototipi, grazie

al 5G, o per soluzioni che richiedano 5G per essere introdotti sul mercato. “Sulla base di un percorso di selezione ne identifichiamo ogni anno un certo numero – prosegue Baggioni – al quale diamo supporto e un investimento importante, per farli progredire nel loro percorso. Nella prima edizione, che risale ormai 2018, abbiamo identificato due vincitori uno proprio in ambito industriale con una soluzione molto simile a quella di manutenzione assistita tramite realtà virtuale e un altro in ambito entertainment, con una soluzione di realtà aumentata per lo sport. Su queste due startup abbiamo deciso di investire 1,6 milioni che, nel mondo degli investimenti startup, va considerata una cifra significativa”.
Qualcomm: a breve il lancio di prodotti industriali per il 5G
Tra le aziende di semiconduttori più attive sui temi della comunicazione e, in particolar modo sulla tecnologia 5G, c’è Qualcomm, che già da quest’anno, ha messo sul mercato chip dedicati. “Il 5G è stato lanciato già il 2019 per applicazioni che non sono ancora allineate con il mondo dell’automazione industriale – sottolinea Sebastiano Di Filippo di Qualcomm – però gli stessi building block, gli stessi elementi costitutivi, sono quelli utilizzati per applicazioni industriali. La mia azienda ha lanciato dei chip commerciali nel 2019, che sono nei telefoni che sono stati utilizzati per il lancio del 5G. L’evoluzione di questi chip renderà disponibili, nei prossimi mesi, anche prodotti per il lancio dei primi dispositivi di automazione industriale. Già nel 2020, vedremo il nascere di soluzioni per il mondo dell’Industrial Automation, dell’IoT, con il supporto del 5 G. Soprattutto per mercati, come quello tedesco, dove c’è già la disponibilità di spettro, per le private network e quindi è sicuramente uno dei punti di partenza per questo applicazioni”.
“Con la release 16 verranno prodotte nuove applicazioni e features per il mondo dell’Industrial Automation – prosegue Di Filippo – e quindi parliamo di bassa latenza, elevata releability per la comunicazione industriale, parliamo dell’integrazione del TSN, del supporto del positioning per applicazioni industriali. In particolare poi Qualcomm è coinvolta nello sviluppo di ulteriori caratteristiche permetteranno di aumentare le prestazioni, come ad esempio il Coordinated MultiPoint (CoMP), che è una funzionalità che noi supporteremo nel prossimo futuro. Il mercato industriale è diventato importantissimo – conclude – e pensiamo che sia il contesto nel quale si realizzerà, non solo a parole, la prossima rivoluzione, per cui vista nostra leadership sul 5G e visto l’importanza del mercato italiano europeo generale, stiamo investendo tanto per essere i primi ad avere soluzioni”.
I robot collaborativi parlano in 5G
Tra le applicazioni più interessanti nelle quali può integrarsi il 5G c’è sicuramente quella della robotica collaborativa che è al centro di un interessante esperimento che la integra con intelligenza artificiale e 5G. A spiegarla Andrea Zanchettin, docente del dipartimento di elettronica, informazione e bioingegneria del Politecnico di Milano e co-fondatore della startup Smart Robot. “La prima cosa che abbiamo provato a fare è stata l’eliminazione dei cavi – spiega – per avere la possibilità di utilizzare una connettività wireless. Poi abbiamo pensato di mettere in contatto il mondo dell’automazione industriale con quello dell’intelligenza artificiale. Abbiamo sviluppato, con Smart Robots, algoritmi che comunicano sul campo e danno istruzioni al robot per poter agevolare la collaborazione con l’essere umano”. A questo si unisce la sperimentazione di un sistema di visione che trasmette i dati in 5G al robot. Questo non è solo un sistema di visione, ma anche di intelligenza – sottolinea – con un progetto che abbiamo iniziato e che andrà avanti almeno fino a fine giugno 2020. Quello che vorremmo utilizzare un po’ di più è il dispositivo di edge computing, che è parte dell’infrastruttura 5G, sul
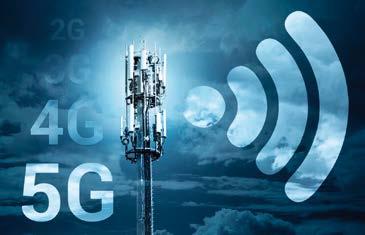
quale vorremmo portare un Digital Twin di tutta la stazione. In questo modo potremo ottimizzare più possibile quello che è il ciclo, facendo in modo di avere un modello non solo del robot ma anche della persona e dei suoi movimenti. Potremo, quindi, ottimizzare i movimenti robot da una parte di tempo ciclo, mentre dall’altra potremo minimizzare l’interferenza con la persona”. Un progetto che, per la parte relativa alla realtà aumentata, utilizza un dispositivo olografico, wearable e quindi, per sua natura, senza cavi. “La tecnologia 5 G è l’unica che si presta per poter operare con dei tempi di latenza certificati – prosegue – per dare istruzioni all’operatore rispetto a quelli che potrebbero essere nuovi cicli di lavoro. Un operatore non esperto, in questo momento, può solo fare affidamento a una documentazione scritta. Noi, integrando un dispositivo di realtà aumentato con un sensore che riconosce quello che fa la persona – conclude – siamo in grado di dare le istruzioni che servono al momento giusto. Nel momento in cui una persona prendo un determinato oggetto il dispositivo di realtà aumentata gli suggerisce quelle prossimo da prendere e come va assemblato con quello che ha preso in precedenza”.
Il 5G e la salute
Il convegno è stato anche l’occasione per sfatare una delle tante “leggende metropolitane”, ovvero quello della pericolosità del 5G per la salute. Antonio Capone, chiamato dal Parlamento per chiarire gli aspetti legati alle emissioni elettromagnetiche di queste nuove reti, spiega che la paura del 5G è infondata. “In realtà, rispetto all’impatto sul corpo delle onde elettromagnetiche – sottolinea Capone – la tecnologia in se è completamente irrilevante, l’unica cosa che conta sono le frequenze e la potenza emessa. Le frequenza del 5G non sono diverse da quelle per altri sistemi a cominciare da quelli radiomobili precedenti, e le potenze emesse sono in larga parte molto simili. Cambiano i sistemi di antenna ma, in realtà, cambiano in meglio perché riescono a evitare di disperdere energia dove non serve e quindi portano un miglioramento in termini di efficienza energetica”. “Da questo punto di vista – prosegue – dobbiamo stare tranquilli perché, tra l’altro, le emissioni 5G in termini stretti non si aggiungono a quelle degli altri sistemi. I limiti che sono stati stabiliti a livello internazionale, poi recepiti dai vari governi a livello locale, sono limiti che riguardano la somma di tutte quante le emissioni di tutti i sistemi, sia quelli di telefonia mobile che quelli di tipo diverso. Quindi in realtà il 5G non potrà superarli e costringerà gli operatori a stare comunque dentro questi limiti. In Italia, poi, per via di ragioni storiche, non completamente giustificate dal punto di vista scientifico – conclude Capone -, abbiamo dei limiti che sono 100 volte inferiori a quelli degli altri paesi europei e quindi in realtà possiamo stare ancora più tranquilli perché realmente i limiti di emissione italiani sono molto molto bassi”.
INDUSTRY 4.0 D E S IG N MAGAZINE
SEI MODI IN CUI IIOT
PUÒ TRASFORMARE IL TUO BUSINESS Il confronto sul tema “Industrial Internet of Things (IIoT)” è passato da “cos’è?” a “come si applica?” Martin Keenan, direttore tecnico di Avnet Abacus, identifica sei aree applicative fondamentali nell’ambito degli impianti di produzione dei prodotti elettronici.
LLa digitalizzazione sta alimentando un cambiamento significativo nel settore dell’ingegneria elettronica. La combinazione di sensori, software, connettività e analisi big data, definita Industrial Internet of Things (IIoT), sta trasformando gli aspetti fondamentali legati alla progettazione, alla costruzione e alla manutenzione dei prodotti.
Infatti, man mano che gli ingegneri sviluppano creatività e padronanza con il concetto IIoT, il suo ambito applicativo nel contesto della produzione di nuova generazione si amplia e favorisce l’affermazione delle fabbriche intelligenti del futuro. Il passaggio da “cos’è l’IIoT?” a “come può essere applicato?” ha portato allo sviluppo di una vasta gamma di progetti destinati ad offrire grandi vantaggi alle imprese, soprattutto a livello di fabbrica. In breve, sin dal momento in cui un prodotto viene concepito, l’IIoT può svolgere un ruolo di supporto e contribuire alla fase di realizzazione.
Per i principali fornitori di elettronica, come TE Connectivity, l’applicazione dell’IIoT sta già avendo un impatto concreto sul piano industriale. “Su questo tema la fase delle ipotesi è alle spalle: il paradigma IIoT sta già trasformando il modo in cui operano le fabbriche moderne, rendendole più snelle, più ecologiche e più redditizie”, ha affermato Ruud van den Brink, Product Manager Industrial Communications EMEA in TE. “Una ricerca di IDC dimostra che nel 2019 l’industria manifatturiera ha speso circa 197 miliardi di dollari in soluzioni IoT e che tale cifra è destinata ad aumentare esponenzialmente anno dopo anno. Quindi, l’Internet of Things Industriale è già una realtà e la sfida, per realtà quali i produttori di discreti, è di sfruttare al massimo i vantaggi che porta in dote”. Alla base di tutto vi è la connettività avanzata, che mette le apparecchiature industriali al centro dei sistemi integrati. I sensori sono sempre più piccoli, più economici e più efficaci, consentendo la raccolta dei dati praticamente da qualsiasi tipo di risorsa all’interno della fabbrica. Tali informazioni possono essere inviate in modo rapido ed efficiente al cloud e, una volta combinate con opportune tecniche di analisi, è possibile estrarne valori significativi. Con lo sviluppo di queste reti, la fab
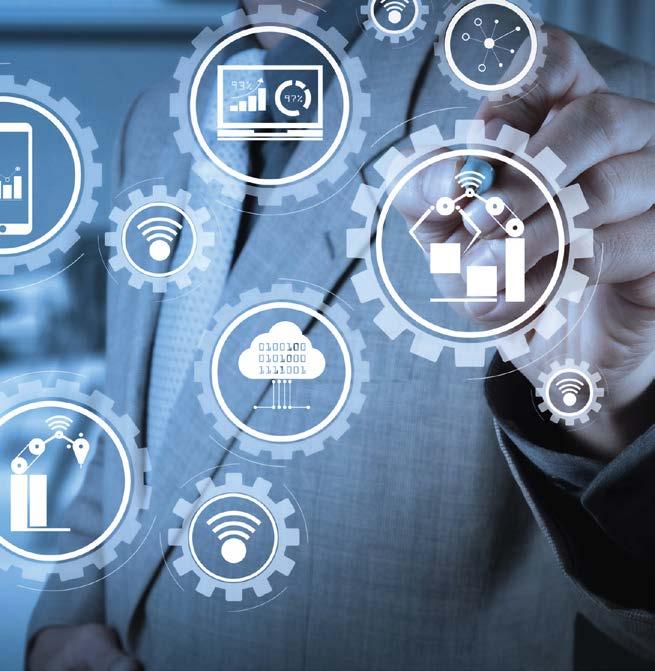
INDUSTRY 4.0 D E S IG N MAGAZINE
brica moderna può diventare un luogo più intelligente ed efficiente. Ma dove si concentrano esattamente i benefici? In questo articolo esaminiamo sei passaggi chiave della produzione che possono trarre vantaggio dall’IIoT, dalle prime fasi di gestione della catena di approvvigionamento fino al servizio post-vendita.
Fase uno: riflettori sulla creazione di una fabbrica più sostenibile
All’inizio del processo di produzione troviamo la fabbrica stessa. Qui, i sistemi di gestione automatizzata della produzione collegano sensori, attuatori, controller e altre apparecchiature attraverso una dorsale IP, consentendo il monitoraggio del consumo di energia legato a macchinari, illuminazione, impianti HVAC e rilevatori di sicurezza antincendio. Tali informazioni possono essere combinate con un set di dati più ampio, come le previsioni meteorologiche e i costi in tempo reale di elettricità e altre utenze. Il tutto permette di ottenere una visione più informata delle prestazioni della struttura. Questo tipo di sistema automatizzato di gestione è sempre più utilizzato negli stabilimenti di produzione elettronica in tutta Europa. Monitorando fattori come qualità dell’aria, temperatura e illuminazione, permette di sfruttare l’energia in modo più efficiente, riducendo così i costi.
Fase due: visibilità in tempo reale sulla supply chain
In termini di logistica legata alla catena di approvvigionamento, l’architettura IIoT si sta dimostrando un fattore chiave per migliorare l’efficacia operativa degli impianti di produzione, fornendo alle aziende visibilità e controllo su materiali e merci in arrivo. L’uso diffuso di tecnologie come tag e sensori RFID, combinati con reti cellulari 3G, LTE Cat-M1, LoRa WAN, Wi-Fi e Bluetooth, consente di tracciare container, pallet e roll-box prima della consegna, monitorando in tempo reale fattori come collocazione, temperatura o umidità. Una volta stivati all’interno del magazzino, la movimentazione automatizzata può garantire il prelievo e l’esatto posizionamento delle merci all’interno dell’impianto. Nel frattempo, le macchine in rete possono fornire un feedback in tempo reale sui tassi di produzione, creando un circuito ottimizzato per il reparto acquisti. Questo tipo di ottimizzazione della supply chain può favorire una produzione just-in-time e una maggiore flessibilità organizzativa, riducendo le merci in giacenza e i costi logistici.
Fase tre: monitoraggio remoto e manutenzione predittiva
Le linee di produzione sono costituite da impianti elettronici basati su complessi ecosistemi industriali com
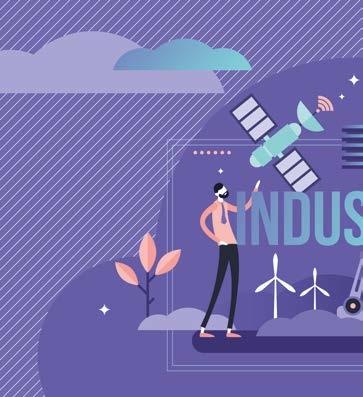
posti da centinaia o addirittura migliaia di elementi che lavorano senza soluzione di continuità al risultato finale. Se si aggiunge il fatto che la maggior parte degli impianti di produzione non è isolata - appartenendo probabilmente a una rete globale di strutture - è evidente l’importanza di avere una visibilità in tempo reale su tutti i processi operativi. Un’architettura IIoT basata su sensori offre informazioni accurate su una vasta gamma di beni industriali, per esempio motori e azionamenti, dislocati in qualsiasi parte del mondo. Gli ingegneri possono collegarsi ai sistemi di rete tramite tablet, laptop o cruscotti mobili per vagliare le prestazioni dei singoli elementi dell’impianto. Tale monitoraggio a distanza può essere utilizzato per identificare ed eliminare i colli di bottiglia e ridurre gli sprechi. Inoltre, un’architettura di questo tipo consente ai tecnici di valutare e prevedere le prestazioni dei macchinari a scopi di manutenzione, riducendo i tempi di fermo non programmati.
Fase quattro: il fattore umano - automazione intelligente in azione
I metodi di produzione stanno evolvendo rapidamente
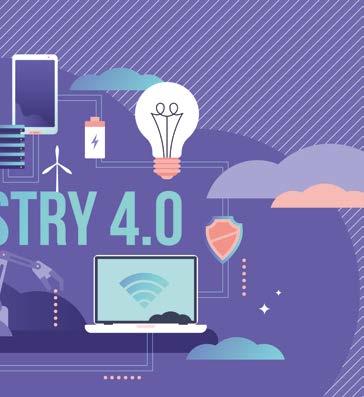
e l’automazione è al centro di queste tendenze mutevoli. Ad esempio, l’uso efficace di una nuova generazione di robot collaborativi (cobot) che affiancano i dipendenti può rivestire un ruolo importante nell’aumentare la produttività manifatturiera. Questi leggeri e compatti robot sono dotati di una serie di sofisticati sensori di movimento, di visione e di posizionamento che permettono loro di essere utilizzati a fianco delle persone senza la necessità di ricorrere a gabbie di sicurezza. Tale libertà offre livelli più elevati di flessibilità operativa all’interno di ambienti di fabbrica intelligenti, dove i cobot possono essere utilizzati per eseguire una serie di attività produttive, spesso noiose e ripetitive, permettendo ai dipendenti di aggiungere valore in altre aree. La flessibilità dei cobot è alla base anche del concetto di personalizzazione di massa, che consente di realizzare prodotti elettronici su misura per soddisfare la domanda dei clienti.
Fase cinque: Perfezionamento costante - aggiungere valore attraverso il design
Una volta che un prodotto è stato costruito, c’è spazio per sfruttare l’IIoT per assicurarne il costante perfezionamento. Sensori sempre più piccoli, più economici e più affidabili hanno cambiato il modo in cui i costruttori di prodotti elettronici lanciano le nuove idee sul mercato. Collegando i sensori ai prototipi e utilizzando i dati ottenuti dai test per avere una migliore panoramica sui possibili scenari operativi nella vita reale, i produttori possono sviluppare dispositivi con prestazioni superiori, più allineate alle esigenze dei loro clienti. Tuttavia, questo approccio, noto come data-driven design, non si ferma ai prototipi. I sensori installati nei prodotti già sul campo continuano a fornire informazioni operative, consentendo un ulteriore perfezionamento del progetto. In precedenza, i produttori erano costretti a sottoporre ogni iterazione progettuale al reparto di produzione o a esternalizzare il lavoro, causando notevoli ritardi. Oggi, viceversa, per accelerare ulteriormente il time-to-market dei prodotti design-driven possono essere utilizzate le stampanti 3D. Qui, l’ultima generazione di macchine per la produzione additiva permette addirittura di realizzare componenti polimerici e metallici in modo affidabile e ripetibile.
Fase sei: assistenza con un sorriso - implementare nuovi modelli di business
Affrontiamo ora il tema delle strategie di lancio sul mercato. La digitalizzazione incoraggia lo sviluppo di nuovi modelli di business basati sui servizi. In alcuni pacchetti di assistenza post-vendita, sensori, software e connettività consentono ai produttori di valutare le prestazioni dei loro prodotti in loco. Ciò può aiutare il cliente a evitare i tempi di fermo, prevedendo i problemi prima che si verifichino. Questa architettura abilitata IIoT sta portando inoltre alla definizione di nuovi modelli di business basati sulla “ servitisation”, dove l’utente finale noleggia un servizio o una soluzione anziché procedere all’acquisto della macchina, evitando così cospicui investimenti iniziali. Tale servizio si basa su KPI (parametri chiave) quali ad esempio i periodi di disponibilità, offrendo al produttore una visibilità più chiara in merito ai programmi di manutenzione. Il venditore del servizio, nel frattempo, può contare su ricavi a lungo termine più prevedibili.
Queste sei fasi dimostrano che l’IIoT può essere implementato sull’intero flusso di valore. Dalla logistica della supply chain alla produzione, manutenzione e servizio post-vendita, i costruttori stanno abbracciando i vantaggi della digitalizzazione per aumentare l’efficienza operativa e fornire prodotti con prestazioni migliori. Questa tendenza non mostra alcun segno di flessione: i sensori, infatti, diventano sempre più piccoli, più veloci e più economici, mentre connettività e analisi dei dati vengono largamente utilizzate per trasformare questi dati in vantaggi per l’azienda. In breve, l’IIoT è qui per restare - e la sua applicazione sempre più creativa continuerà a svolgere un ruolo cruciale nel potenziare le fabbriche intelligenti del futuro.