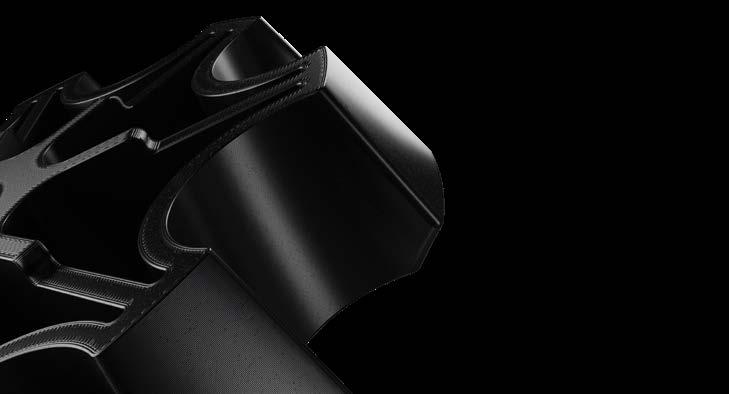
4 minute read
UN PORTFOLIO SEMPRE PIÙ AMPIO PER LA STAMPA 3D GRAZIE ALLA NUOVA TECNOLOGIA FDR DI EOS E AI NUOVI TECNOPOLIMERI DI ROBOZE
AAmpliare le soluzioni di stampa 3D: questo l’obiettivo delle partnership che CELADA ha istituito con EOS, ai vertici globali nella fornitura di tecnologie nel campo della stampa industriale 3D di metalli e polimeri e ROBOZE, eccellenza nel campo dell’additive manufacturing, specializzata nella produzione di stampanti 3D ad alte performance per tecno polimeri. La mission del Gruppo CELADA è infatti la ricerca quotidiana della tecnologia più adatta al cliente, in grado di assicurare alte performance e vantaggi competitivi. Clienti, innovazione e attitudine ad intuire nuovi scenari, sono i valori fondanti della cultura aziendale del Gruppo.
Grazie all’accordo con EOS, CELADA Group completa la sua già vasta offerta di macchinari per la produzione industriale con le soluzioni EOS nel campo della stampa 3D, considerate strategiche non soltanto per i prodotti all’avanguardia ma anche per l’utilizzo di materiali metallici e polimerici avanzati, in grado di fornire nuovo impulso alla crescita dell’intero settore del manufacturing nel nostro fini e pareti sottili sono fondamentali, FDR è la soluzione ideale. A differenza delle altre opzioni del portafoglio EOS, utilizza un laser CO2 con una potenza di 55 watt. Il laser produce un fascio molto sottile con un diametro di messa a fuoco due volte più piccolo rispetto alle tecnologie SLS esistenti.
Paese. In particolare, CELADA porta sul mercato la nuova tecnologia FDR per la serie P110 FORMIGA, prodotto già noto ed apprezzato per le sue caratteristiche di qualità nella gestione del processo SLS, che ora si evolve nella versione Fine Detail Resolution.
Convinta che la produzione additiva sia di fondamentale importanza soprattutto per il comparto manifatturiero italiano ad alto valore aggiunto, grazie all’ampliamento del proprio portfolio con le soluzioni di stampa 3D ROBOZE specializzate nella manifattura additiva con super polimeri e materiali compositi, CELADA aggiunge alla già ampia scelta di materiali nuovi tecnopolimeri finalizzati alla bio-sostenibilità ed alle prestazioni. In questo modo il Gruppo completa l’offerta aumentando i campi di applicazione per i propri clienti con una resa industriale, precisa, ripetibile e ad alte performance.
La tecnologia consente di ottenere superfici estremamente sottili, nonché parti delicate ma stabili con una elevata qualità superficiale. Ciò apre nuovi campi di applicazione per la produzione in serie ed incrementa le possibilità di utilizzo per l’industria della stampa 3D per le materie plastiche nelle applicazioni in cui “sia necessaria la precisione”.
La capacità del processo FDR di processare pareti con spessori fino a 0,22 mm determina che la nuova tecnologia combina il meglio di due mondi: l’alta risoluzione dei dettagli della stereolitografia (SLA) e la durata e la qualità della stampa 3D industriale a base di polvere (SLS).
L’unità P110 FORMIGA sarà inizialmente disponibile per processare il materiale PA 11 (successivamente lo saranno anche gli altri materiali più comuni per la tecnologia SLS) anche nella nuova versione PA 1101 ClimateNeutral, un materiale a base biologica che offre un’impronta carbonica inferiore rispetto ai polimeri a base di petrolio. Il materiale è stato sviluppato per supportare gli obiettivi di sostenibilità dei clienti EOS: gli utenti ricevono infatti un certificato che dimostra il calcolo e la compensazione corretti per le applicazioni.

La caratteristica FDR per P110 FORMIGA è anche l’occasione per completare l’aggiornamento del prodotto in ottica I4.0, con l’estensione all’uso di EOSPRINT 2 per la programmazione del job di stampa e la possibilità di includere l’unità in contesti di interconnessione mediante la piattaforma EOSCONNECT.
I nuovi polimeri per la stampa 3D FFF
I nuovi tecnopolimeri recentemente introdotti nel mercato da ROBOZE, a conferma del trend tecnologico intrapreso dalla creazione del laboratorio d’avanguardia dedicato alla ricerca e sviluppo di super materiali, sono processabili sulle stampanti della serie PRO ed ARGO. Si tratta di BIO-BASED PA, CARBON PA PRO e CARBON PEEK, super materiali in grado di sostituire i metalli, finalizzati alla bio-sostenibilità ed alle prestazioni.
BIO-BASED PA. È questo il nome del primo materiale biobased ad alte performance per la stampa 3D; già protagonista nel recente Formnext 2022, offre ottime prestazioni in termini di bassa igroscopicità, ottima ritenzione delle proprietà meccaniche dopo l’assorbimento dell’acqua ed eccellente stabilità dimensionale. Inoltre, le parti stampate esibiscono un eccellente aspetto superficiale di colore nero lucido.
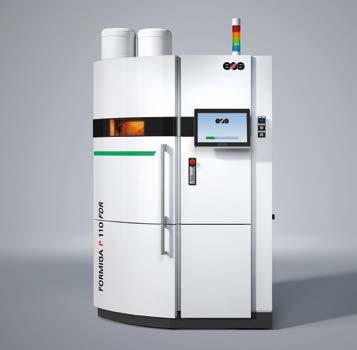
Con le stesse specifiche e prestazioni, ma con un’emissione di CO2 inferiore del 60% rispetto a una PA a base petrolio rinforzata con fibra di carbonio, questa nuova PA consentirà alle aziende manifatturiere di migliorare i propri obiettivi di sostenibilità nel pieno rispetto dell’ambiente.
CARBON PA PRO. Il materiale composito più resistente che ROBOZE abbia mai prodotto ha una maggiore concentrazione di fibre di carbonio che determina un aumento del 50% delle proprietà rispetto alla soluzione precedente.
Complessivamente, combinato con il processo di stampa 3D ROBOZE, Carbon PA PRO è 1,6 volte più resistente del suo predecessore ed è rigido più del doppio, quindi, può sopportare carichi meccanici molto più pesanti, rendendolo il materiale composito più resistente che ROBOZE abbia mai prodotto finora. Basti pensare che la sua resistenza a trazione (171 MPa) si attesta sullo stesso ordine di grandezza di leghe leggere di alluminio ma con una densità dimezzata.
CARBON PEEK. Il PEEK caricato con fibre di carbonio per parti con elevate caratteristiche strutturali presenta una maggiore concentrazione della stessa rispetto alla soluzione precedente, influendo positivamente su diverse proprietà. Tra queste si sottolinea una maggiore resistenza interstrato del 50% (la resistenza a trazione ZX è di 55 MPa), una maggiore elasticità e facilitazione di lavorazione, e una migliore finitura superficiale. Il risultato è che le parti sono più resistenti, esteticamente più gradevoli, si usurano più lentamente e possono essere consegnate più rapidamente all’utente finale. È utilizzato in un›ampia gamma di settori: dall’aerospazio e difesa all’automotive, dall’energy alla produzione industriale, al motorsport. La sua notevole durabilità lo rende una scelta comune per ambienti estremi. Grazie alle sue eccellenti proprietà, tra cui alta tenacità, temperatura di esercizio continuo e temperatura di transizione vetrosa molto elevate e alto punto di fusione, è il candidato perfetto per applicazioni di sostituzione dei metalli. Il tutto si traduce in notevoli risparmi in termini di peso, un fatto particolarmente rilevante nelle industrie quali l’aerospazio e la difesa.