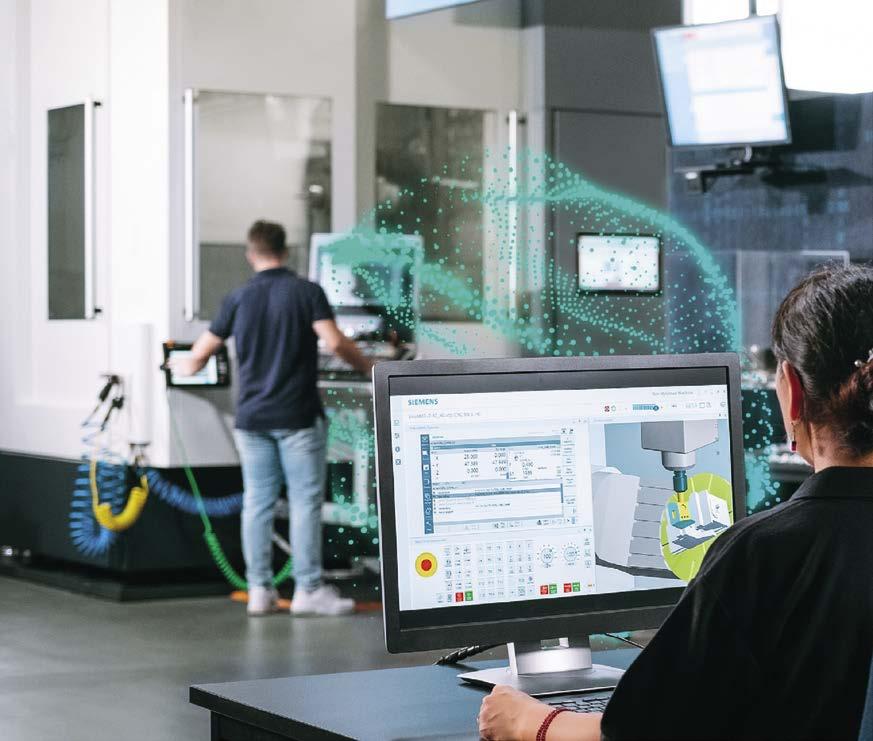
6 minute read
Siemens numero 1
SIEMENS
SIEMENS, NUMERO 1 NELLA SOSTENIBILITÀ
SIEMENS È LEADER NELLE CLASSIFICHE INTERNAZIONALI DI SOSTENIBILITÀ DA OLTRE 20 ANNI. NEL DOW JONES SUSTAINABILITY INDEX (DJSI) 2021, SI È CLASSIFICATA AL PRIMO POSTO TRA I SUOI COLLEGHI DI SETTORE
IIl DJSI è una classifica di sostenibilità stabilita a livello globale, preparata annualmente dalla società di investimento Standard & Poor’s per conto del fornitore di indici Dow Jones. Siemens è stata inclusa in questa classifica ogni anno dal 1999, quando il DJSI è stato pubblicato per la prima volta. Nell’attuale classifica, pubblicata a novembre 2021, Siemens ha conquistato il primo posto tra le 45 aziende incluse nella classifica del proprio comparto industriale, con una valutazione complessiva molto positiva, ottenendo 81 punti su 100 possibili. “Essere sostenibili significa essere in grado di conservare e sviluppare le risorse e gli elementi che consentono alla vita sulla terra di proliferare”, ha affermato Raffaella Ghizzoni, Sustainability Manager di Siemens, in occasione della Giornata Mondiale della Terra 2021. “Siemens, come grande multinazionale, si impegna molto concretamente per la sostenibilità e negli ultimi anni ha lavorato per associare il proprio brand a quello di una società sostenibile, definendo un programma che aveva come riferimento i 17 obiettivi che l’Organizzazione Mondiale delle Nazioni Unite ha definito nell’agenda 2030”.
Forte punto di partenza per l’ecodesign
In relazione agli obiettivi della progettazione ecocompatibile e dei materiali secondari – in altre parole, per lo sviluppo sostenibile dei prodotti e il riutilizzo delle materie prime nella produzione – Siemens ha già implementato in tutti i prodotti rilevanti dell’azienda il 26% degli standard di progettazione ecocompatibile, prendendo in considerazione aspetti come garantire la riciclabilità dei prodotti fin dalla fase di progettazione. Entro il 2030, l’azienda vuole sviluppare il 100% delle sue famiglie di prodotti rilevanti in modo sostenibile sulla base dei requisiti di progettazione ecocompatibile. Siemens intende intensificare l’acquisto di materiali riciclati – denominati “materiali secondari” – per metalli e resine e vuole attuare il principio di un’economia circolare. Inoltre, l’azienda intende avvicinarsi il più possibile all’azzeramento dei rifiuti non riutilizzabili (obiettivo: zero landfill waste) entro il 2030. Nell’anno fiscale 2021, il 38% dei metalli utilizzati da Siemens per fabbricare i suoi prodotti era già stato acquistato da fonti riciclate.
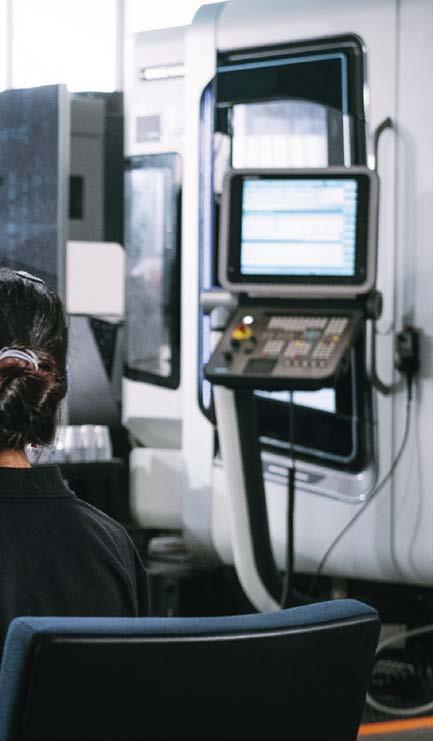
Focus sull’obiettivo di 1,5 gradi Celsius
Siemens ha anche compiuto notevoli progressi nei suoi sforzi per la protezione del clima. Negli ultimi due anni, l’azienda ha ridotto le emissioni di CO2 delle sue operazioni di un altro 36%. All’inizio del 2021, l’azienda si era prefissata nuovi obiettivi di riduzione che sono stati convalidati dalla Science Based Targets-Initiative (SBTi). In questo modo, l’azienda vuole dare il suo contributo per limitare il riscaldamento globale a 1,5 gradi Celsius. Sulla base del
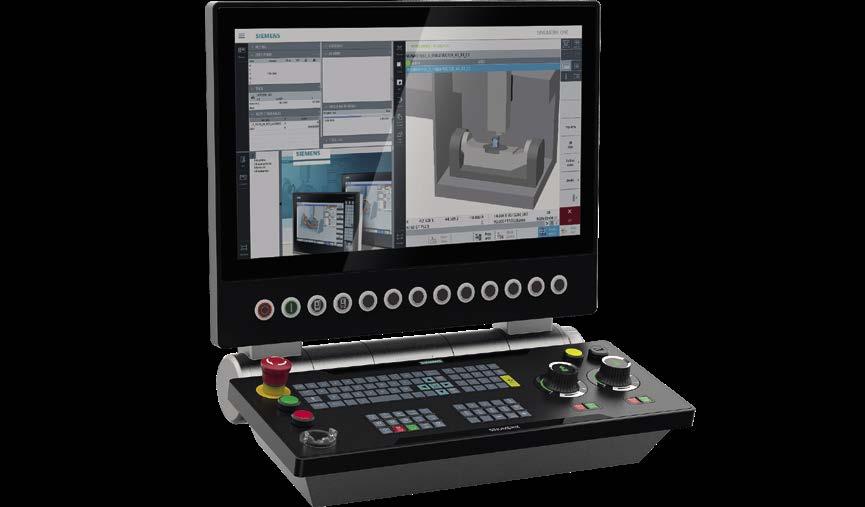
percorso di riduzione SBTi, Siemens vuole diventare carbon neutral nelle sue operazioni commerciali entro il 2030. Entro quell’anno, l’obiettivo è di ridurre le emissioni lungo l’intera catena del valore del 15% rispetto al 2019.
Partner tecnologico affidabile per la Transizione 4.0
Nell’anno fiscale 2021, Siemens non solo ha ridotto ulteriormente le emissioni nelle proprie operazioni, ma ha anche aiutato i suoi clienti a fare lo stesso: le tecnologie del portafoglio ambientale di Siemens hanno consentito ai clienti dell’azienda di abbattere 88 milioni di tonnellate di CO2, il dieci percento in più rispetto all’anno fiscale 2020. Più in generale, l’azienda si pone come partner sempre più affidabile per la trasformazione digitale delle industrie italiane, in un’ottica sempre più sostenibile. Di fronte ad un mercato volatile, instabile, in cui aumenta la richiesta di personalizzazione, di velocità di reazione e di attenzione alla sostenibilità, è importante saper ottimizzare anche i propri processi interni di progettazione, attraverso una organizzazione del lavoro più snella e flessibile, approcci di vendita più efficaci e una gestione ottimizzata della Supply chain; il tutto per poter garantire la competitività quindi il futuro della propria azienda.
Sinumerik ONE è il primo CNC nativo digitale, concepito e sviluppato per essere il fulcro della piattaforma digitale Siemens nel mondo della macchina utensile, che permette di esprimere il massimo potenziale della digitalizzazione, di innovare più velocemente, in modo sostenibile e più sicuro, di massimizzare la produttività e di sperimentare un nuovo modo di progettare, vendere e utilizzare le macchine utensili in un mondo in cui la digitalizzazione sta ormai pervadendo non solo ogni ambito della nostra vita quotidiana ma anche della filiera della macchina utensile.
Vantaggi per la sostenibilità ed efficienza energetica
Con Sinumerik ONE, e le relative piattaforme di engineering e simulazione, cioè i digital twin, sia il CNC, che la macchina, che il processo produttivo possono essere simulati indipendentemente dalla presenza fisica della macchina e prima ancora che essa venga costruita e quindi possono essere realizzati e ottimizzati nativamente in ambiente digitale prima di essere disponibili nel mondo fisico. Grazie a Create My Virtual Machine e Run My Virtual Machine, sono disponibili 8 livelli di gemello digitale della macchina e della produzione che il costruttore di macchina e l’utilizzatore finale possono utilizzare in base alle proprie esigenze di simulazione, di progettazione o di ottimizzazione. Si apre così ad un nuovo modo di progettare,
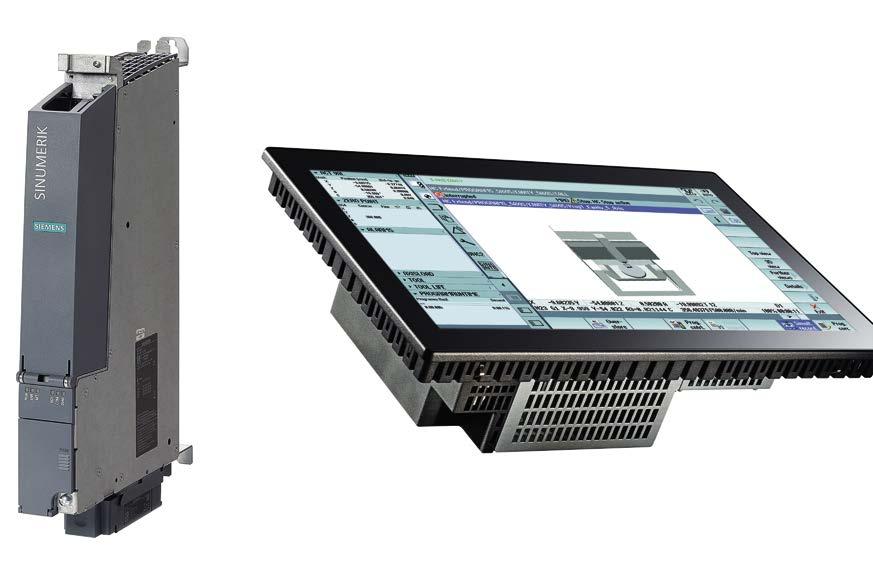
vendere e utilizzare le macchine utensili. Il digital twin non rappresenta più una semplice opzione della macchina venduta dal costruttore ma uno strumento efficace, e sostenibile, di competitività per lo stesso costruttore e utilizzatore.
Il costruttore di macchine, ad esempio, può offrire nuovi servizi agli utilizzatori finali, perché grazie alla disponibilità dei gemelli digitali di tutte le macchine installate può valutare possibili ottimizzazioni o risolvere, da remoto, possibili malfunzionamenti o anomalie sulla macchina senza necessariamente dover inviare tecnici sul campo. Inoltre, l‘utilizzatore finale può testare e ottimizzare i programmi sui gemelli digitali, incluso il controllo di collisione, senza dover impegnare fisicamente la macchina che può continuare la sua produzione; inoltre può mettere a disposizione di nuovi operatori neoassunti, in fase di training, il gemello digitale della macchina con tutte le sue funzionalità invece della macchina stessa evitando rischi di danni dovuti alla poca esperienza. Per l’utilizzatore finale significa quindi uno spostamento del lavoro di preparazione della lavorazione, dalla macchina all’ufficio, una riduzione dei tempi non produttivi, una riduzione dei rischi di uso improprio della macchina, quindi un incremento della produttività, una riduzione di numero di pezzi da scartare e infine un minor tempo per portare sul mercato nuovi manufatti.
Sinumerik ONE rappresenta una potente evoluzione della piattaforma SINUMERIK, che non solo mette a disposizione le elevate funzionalità già presenti sul predecessore Sinumerik 840D sl ma le amplia, e grazie a incrementate performance del PLC (10 volte più veloce), del CNC (fino al 50% più potente) e alla piattaforma modulare di gemelli digitali, consente un incremento della produttività della macchina che può arrivare al + 25%. I benefici di questo CNC innovativo riguardano l’intero ciclo di vita della macchina. Grazie all’utilizzo del digital twin i costruttori possono mappare virtualmente e ottimizzare l’intero sviluppo della macchina con una riduzione del Time-to-Market mediamente del 30%.
Attraverso potenti tool di ingegneria è possibile incrementare efficienza e flessibilità e ridurre i tempi di messa in servizio della macchina del 50%.
Con processi produttivi ottimizzati digitalmente, analisi dei dati e messa in funzione virtuale, e con tecnologie di azionamento innovative e integrate, i clienti possono risparmiare fino al 40% di energia e la corrispondente quantità di emissioni di CO2. Monitorando le prestazioni dei prodotti e dei processi, e riportando i dati nella progettazione del prodotto e nella pianificazione della produzione, il consumo di risorse e l’impronta ecologica dei prodotti sono costantemente ottimizzati durante l’intero ciclo di vita.