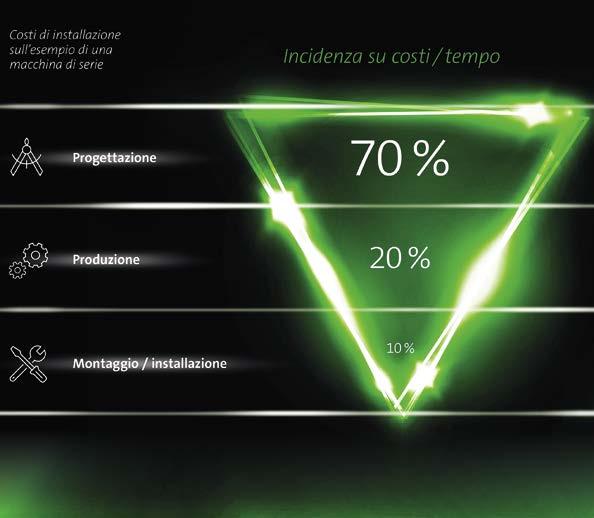
4 minute read
Come abbattere i costi di
I COSTI DI UN IMPIANTO INIZIANO A GENERARSI A PARTIRE DALLE PRIME FASI DI PROGETTAZIONE E NON È SEMPRE FACILE INDIVIDUARLI. LA LORO ELIMINAZIONE È POSSIBILE ADOTTANDO CONCETTI DI PROGETTAZIONE INTEGRATA DI SISTEMA, BASATI SULLA TECNOLOGIA DI AUTOMAZIONE DECENTRATA
A cura della redazione
Sin dalle prime fasi della progettazione, si prendono decisioni che determinano più dei due terzi dei costi totali di installazione. Una grande possibilità di risparmio nella realizzazione di macchine speciali
COME ABBATTERE I COSTI DI INSTALLAZIONE
Esistono vari scenari che determinano i metodi, o i concetti, che meglio si adattano ai bisogni individuali dei progettisti meccanici e, al contempo, puntano a un grado più elevato di standardizzazione ed efficienza delle installazioni elettriche. Questi approcci possono ridurre i costi di installazione fino al 30%. I tre scenari delineati di seguito evidenziano come la tecnologia di installazione elettrica debba occupare un posto centrale nella progettazione e nel computo generale dei costi e non essere un mero effetto collaterale. Fino a ieri, l’ingegneria meccanica era dominata da installazioni elettriche di tipo classico. L’intero sistema di controllo veniva collocato nell’armadio elettrico e una grande morsettiera collegava sensori e attuatori al bordo macchina. Molti singoli componenti, la cui compatibilità andava di pari passo con la suscettibilità agli errori del sistema, comportavano alti costi di installazione e commissioning. Ciò si ripeteva per ogni singola macchina. Le connessioni standardizzate erano una rarità e, ove presenti, dovevano essere assemblate manualmente con un grande spreco di tempo e risorse. La distribuzione di alimentazione e dati alla periferia dell’impianto avveniva tramite morsettiere separate. Il classico cablaggio in parallelo veniva semplicemente trasferito dall’armadio elettrico al bordo macchina. Se ciò semplificava, pur di poco, le procedure di cablaggio, aumentava tuttavia le possibili fonti di errore a causa del raddoppio dei punti di connessione. Gli errori di cablatura tra armadio elettrico e periferia erano frequenti e la loro risoluzione, in caso di cortocircuito e sovraccarico, era lunga e laboriosa, con conseguenti tempi di inattività e perdita di produzione.
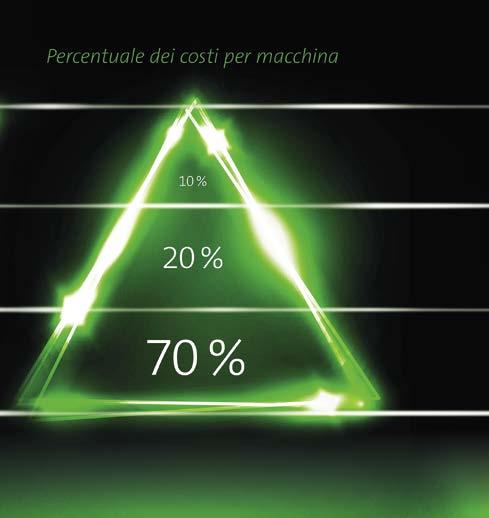
Oggi, il livello IO è posizionato accanto ai dispositivi, con una riduzione significativa delle dimensioni dell’armadio di controllo. I componenti di sistema a innesto dotati di connettori completamente testati, con grado di protezione IP67 e cavi di lunghezza variabile, beneficiano di una minore complessità elettrica e richiedono quindi tempi di installazione significativamente inferiori. L’eliminazione degli errori di cablaggio fa risparmiare tempo e fatica in fase di avviamento. E domani? Anche se si ha una visione a lungo termine, senza un approccio di sistema e una tecnologia di installazione mirata è improbabile riuscire a raggiungere un grado significativo di risparmio. Le soluzioni e i componenti di sistema personalizzati offerti da Murrelektronik non solo riducono i costi globali fino al 30%, ma innalzano anche il livello di tecnologia grazie a funzioni diagnostiche innovative: un valore aggiunto non trascurabile sia per costruttori che per operatori di macchine.
Connessione corretta, spesa evitata
All’interno di un’azienda, tutti i responsabili dei diversi centri di costo – dagli acquisti alla progettazione, dall’installazione elettrica al commissioning – contribuiscono a ridurre la spesa totale per i collegamenti elettrici di un impianto se adottano un approccio di sistema integrato e tecnologie di installazione dedicate. In ogni fase, la tecnologia di installazione può essere considerata l’elemento centrale per l’ottimizzazione dei costi, in grado, quindi, di rendere progettazione, design e produzione più flessibili, più semplici e più efficienti. È possibile razionalizzare la pianificazione dei progetti con l’utilizzo di installazioni modulari e decentralizzate IP67, invece di ricorrere a complesse morsettiere? Un minor numero di fornitori con componenti standardizzati e preassemblati permette una soluzione di sistema coordinata? I moduli I/O del PLC possono essere sostituiti da moduli I/O bus di campo decentralizzati? È possibile evitare l’utilizzo di fasci di cavi e di cablaggio con moduli di distribuzione vicino a sensori e attuatori? I cavi a innesto e pressofusi (che permettono assemblaggio, manutenzione e assistenza più rapidi e senza errori) possono essere installati al posto dei cavi a cablare? Che risultati ottiene l’operatore in termini di miglioramento della disponibilità del sistema grazie ad una diagnostica di facile comprensione?
(Inter)connettività: la tecnologia di rifermento per la riduzione dei costi
Una tecnologia di installazione efficiente e personalizzata, che si basa su una visione sistemistica, apre enormi opportunità di risparmio che possono influenzare il processo decisionale. Questi approcci rientrano nelle competenze degli ingegneri e degli specialisti coinvolti nella meccatronica, ma possono anche mostrare al management come evitare di dissipare risorse. Dal punto di vista di Murrelektronik, la progettazione di sistema offre opportunità e potenziali che non sono stati pienamente sfruttati. Identificare queste aree con il cliente e portarle in primo piano aumenta la disponibilità delle macchine e al contempo offre una tecnologia di installazione semplificata e una diagnostica intelligente. Solo implementando l’approccio sistemistico di Murrelektronik, è possibile comprendere come sia possibile ottenere fino al 30% di risparmio. L’adozione di queste metodologie, rispetto a quelle attuali, permetterà sicuramente di intraprendere il percorso verso l’ottimizzazione di tutti i processi.