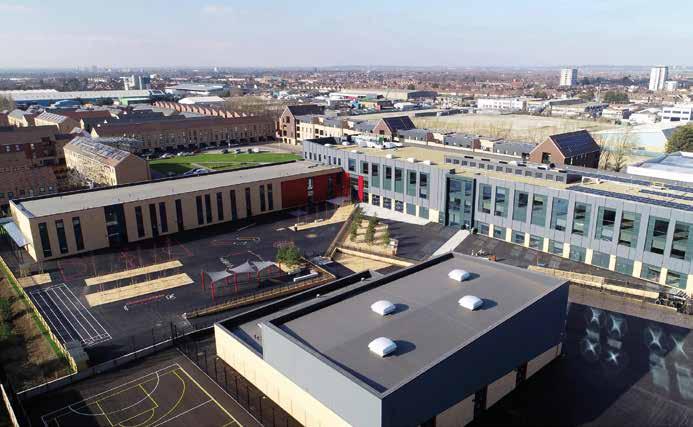
4 minute read
Educational Construction
Lymington Fields School campus complements an adjacent housing scheme and forms part of a regeneration plan that is designed to accommodate 45 nursery pupils, 630 primary school pupils and 900 secondary school pupils.
Architects Bond Bryan have used a variety of offsite solutions for several other school projects and were confident in its ability to meet both the client’s budget and technical requirements. On completion, the campus will form the largest secondary school in Europe. The use of offsite construction enabled the delivery of this project using a componentled approach where the design was broken down into the minimum number of repeatable components. For Lymington Fields School the same 16 components were used to deliver approx. 90% of the school. This repetitive use reduced both manufacturing and installation cost due to speed and efficiency. The reduction in programme resulting from this design approach saved around £3million of prelim costs. The standardisation of design included taking the original structural design and rationalising 40 column types down to two precast columns – saved both time and cost. The architects were confident in its ability to meet both the client’s budget and technical requirements. The use of offsite also reduced the impact on local neighbours. The school is in a residential area and offsite meant not only fewer people on site and less noise, but also a shorter construction period and fewer deliveries and increased traffic. Sustainability and high levels of health and safety were considered to be a critical driving force from both Bond Bryan and the contractor Mid Group – this meant that this entire project was delivered without a single tonne of waste being sent to landfill. One of the key drivers to reducing cost was to reduce the programme durations. The frame was complete and watertight in only 18 weeks as three different construction solutions were used, allowing three different teams to be on-site at the same time.
Wrapping the concrete frame in SIPs allowed the earlier start of the MEP team, delivering further savings and allowed almost all rooms in the building to be occupied for fit out at a
1
comparatively early stage in the works. The approach was not only more efficient for the contractor, but also enabled sub-contractors to work more efficiently, with trades able to work onsite for longer durations. This reduced the cost to suppliers and further reduced costs to the Client.
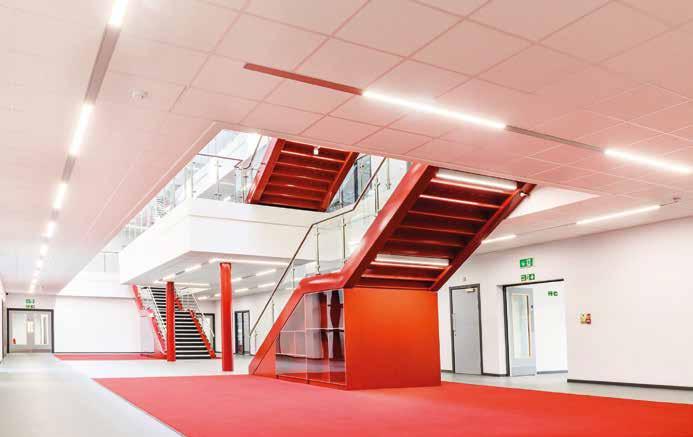
“It was important that the building looked like a 'traditional' building both in terms of look and feel. This was very easy with SIP wall panels, enabling flexibility in the design and form, making sure the design worked for the end-user for today and tomorrow but would also keep its robustness. The envelope was free of constraints as the SIP allows for a wide variety of claddings and bricks. It was decided to use a Brick slip system (another offsite element) and rainscreen cladding.”
The envelope was free of constraints as the SIP allows for a wide variety of claddings and bricks. It was decided to use a Brick slip system (another offsite element) and rainscreen cladding. The building met the brief and all the end-user requirements without any compromises, with a few additions from the standard DfE approach. First in terms of architecture the cost efficiency of the project allowed the contractor to add a large atrium, large glazed screens and landscaping. But also from a services view, the design completely challenged the standard approach in schools and reduced the provision for heating of the building (due to the high performance of the envelope) but added some cooling systems in every rooms. The enduser is delighted with that redefined strategy from a wellbeing point of view, but also regarding performance and sustainability, the school achieved a BREEAM Very Good rating. Furthermore, the primary energy usage of 60kWh/m2/yr is by far more financially efficient against the 75kWh/m2/yr target of the DfE and equates to a financial saving of circa £50k per annum for the school. The entire design team worked on a BIM approach. The designers could easily resolve clashes and co-ordination prior to offsite manufacturing. Due to this approach the design and co-ordination needs to be resolved very early on, and there is very little room for changes on-site and co-ordination issues (as elements are built offsite).
The Lymington Fields project has been used as an example of longterm value – it was already severely delayed during the initial strategy and procurement stages – the use of offsite was essential in order to meet the Local Authorities plan to open the school on time, and the school was completed and handed over to the client only 15 months from the start date. The end user, in this case the school was invited to visit a number of our buildings already built using offsite solutions to give them an understanding of what it was and how robust the solutions were. Seeing actual buildings with added benefits of being robust and thermallyefficient and without having to make compromises really convinced the school that it was the way forward.
2
For more information visit:
www.bondbryan.co.uk www.mid-group.co.uk
Images:
01-02. On completion Lymington Fields School campus will form the largest secondary school in Europe. Courtesy Bond Bryan Architects