
7 minute read
New Dimensions in Roofing
Room-in-roof systems provide invaluable benefits to housebuilders looking to create space and energy efficient design – this is reflected in a new system from Ultrapanel Building Technologies that is set to combine offsite techniques and advanced manufacturing.
The Ultrapanel room-in-roof system has been developed by Ultraframe, a long-time leader in the UK’s home improvement sector and precision engineered at Ultraframe’s 500,000sq ft facility in Lancashire. Essentially the Ultrapanel system is a hybrid roofing system, geared towards meeting the demands of volume housing developers looking for a high-performance, flexible and quality assured roofing solution. “At Ultraframe we’ve always designed products that are easy to handle, quick to assemble by relatively unskilled labor and products that can add light and space to a home’” says Andrew Thomson, Design and Development Director, Ultraframe UK. “With Ultrapanel we’re bringing those benefits to the housebuilding sector, designing a flat packed room-in-roof system that can easily be incorporated into any house design.” With factory production only taking two weeks, Ultrapanel’s short lead time provides flexibility to housebuilders managing complex and demanding schedules, and like all offsite technologies reduces on-site frustrations such as poor weather and labour shortages. The system is both lightweight and easy to manoeuvre with use of a telehandler, reducing the cost and complexity of expensive lifting equipment and on-site cranage. The Ultrapanel system can be installed by a team of three in just one day to achieve a rapid weathertight building envelope. The flexible system can see a roof installed in a single day and creates approx. 50-60% more usable space than traditional attic trusses. Importantly, windows and dormers can be placed anywhere in the roof with no ‘dead zones’. This means that the layout of the top floor room can be maximised as windows can be placed exactly where they are needed – even above staircases to bring natural light into the floors below. As Ultrapanel has no traditional roof trusses or purlins, the ceiling can be vaulted allowing space for a mezzanine floor in some roof designs. “The complete Ultrapanel system is the only room-in-roof system with BBA certification and NHBC Accepts,” says Andrew. “This provides assurance to housebuilders that the structural, thermal, condensation risk and fire risk have all been independently verified. The design has a structural eaves section which distributes the load into the supporting wall so the support
1
traditionally required either side of a roof opening does not need aligning with the wall below. The absence of internal structure means maximum flexibility to utilise the space.” The Ultrapanel system is precision engineered in one ‘unitised hybrid panelised solution’ to maximise the material properties of the structural steel and timber elements, integrated with a high-performance insulation core. The Ultrapanel system is delivered to site as a complete room-in-roof kit of parts including all components and fixings at a pre-agreed assured price. Reducing the costs and risks surrounding on-site storage, this means the system is more sustainable and eliminates much on-site waste and associated disposal costs. “To make the system both lightweight and thermally efficient the structure is a composite I-beam with steel cords and a hardboard web using a patented joining method,” adds Andrew. “This utilises the best characteristics of each of these materials – the steel is both strong and formable, to create easy clip features, the hardboard creates the thermal break. Together they support the insulation to make a panel which is less than 6kg/sq m, so a 5m roof panel only weighs 18kg. There are also structural beams using both steel and OSB which are fully insulated so there are no cold spots in the system.” A dedicated Ultrapanel team will be offering continuous support – from the first enquiry to the installation – through its dedicated customer care and site teams. With installer training for in-house operatives, the Ultrapanel team will also be offering guidance throughout the design, specification, manufacturing and installation process. “We have been developing the system over the past four years alongside major housebuilders to ensure we get off to a quick start, says Andrew. “We have developed a version of the panel using non-combustible materials which we use for the party wall structure and we will continue to extend applications of this new material.”
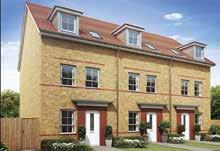
2
To see the system in more detail a special virtual live build event will take place on 30 March where Andrew Thomson will talk through the process.
For more information visit:
www.ultrapanel.co.uk
Images:
01. The Ultrapanel system is the only room-in-roof solution with BBA certification and NHBC Accepts 02. Courtesy Barratt
SCI Bookshop
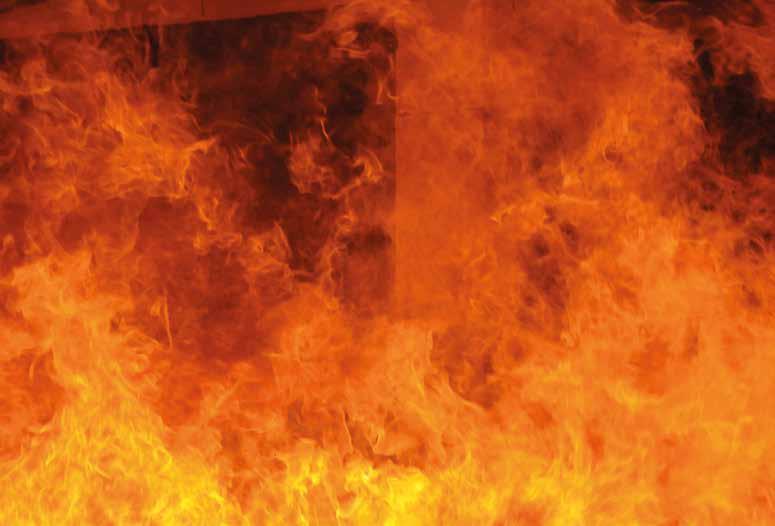
shopsales@steel-sci.com | + 44 01344 636525
NEW SCI Publication
Fire Resistance of Light Steel Framing (P424)
This new design guidance provides information on how light steel framed buildings should be designed and detailed to provide fire resistance in accordance with the Building Regulations.
The guidance includes:
Detailed design information on the application of the Building Regulation requirements to light steel framing, including requirements for fire testing.
Construction practice and detailing of light steel frames and their interfaces with other materials for fire resistance.
A set of typical generic construction details for light steel framing in terms of design for fire resistance is provided.
Calculation methods which may be used to extend the tested fire performance of a light steel wall or floor construction to a wider range of design parameters.
To purchase this new publication, go to the SCI Bookshop https://portal.steel-sci.com/shop.html
A NEW APPROACH TO BALCONY DESIGN
Sapphire Balconies are a leading manufacturer of balcony systems for residential applications and believe that modern methods of construction (MMC) and offsite manufacture are the future of construction.
Not only does MMC provide a range of benefits on-site, but it also tackles concerns including sustainability and helps establish a ‘golden thread’ of information as recommended in the Hackitt Report. Using MMC processes, Sapphire Balconies delivers balconies embodying quality craftsmanship and time-saving processes to construction sites around the world.

The Golden Thread
In her report, Dame Judith Hackitt identified the information gap between design and build and recommended what she called a ‘golden thread of information’. Using the COACH suite, a full suite of digital tools, Sapphire ensures every balcony has a fully traceable journey from design, to manufacture, to install. With the Passport app every balcony goes through a series of checks every step of the way and cannot continue until it meets high quality standards.
Benefits of Offsite Manufacture
In addition to the use of digital tools, Sapphire’s offsite construction methods benefits from consistency along the production line and controlled conditions reduce the opportunity for error. Factory environments also entail regular checks allowing faults to be found and remedied. Sapphire’s Glide-On™ Cassette® balconies are delivered fully-assembled, including balustrades. They are then simply craned into position and slide on to steel support arms for final attachment. Minimal further finishing is required, making this time-saving installation so fast that it is possible to fit more than 40 balconies in a single day.
Cutting Carbon
Key to Sapphire’s Glide-On™ Cassette® system is its lightweight, modular construction, which reduces forces on the anchors and connections that transfer the load of the balcony to the structure of the building. This is particularly important, for example, where structural elements are less rigid than reinforced concrete. Sapphire’s Glide-On™ Cassette® balconies are made of laser cut and mechanically fixed aluminium, making the balcony one third the weight of a comparable all-steel design. The smaller load may reduce the number of supports required, the number of façade penetrations and the risk of cold bridging or damp problems. This significantly cuts the environmental
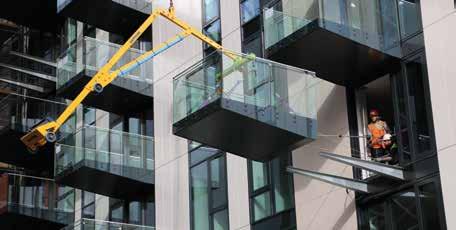
1 2
impact of the building by reducing occupational heat loss when compared to heavier balconies.
Design Flexibility
Sapphire Balconies has added its muscle to the modular revolution by giving architects wide scope in balcony design – combined with the reliability of modular construction. Sapphire has developed a lightweight cantilevered solution that makes a balcony as much at home on any virtually any MMC construction as it is on a traditional reinforced concrete structure. This gives architects the confidence to design balconies that balance all requirements – visual, practical and financial. This is true for a wide range of MMC materials and practices, such as cross laminated timber (CLT) frames, steel frames, thin concrete slabs and precast wall panels.
To find out more about Sapphire’s balcony solutions for MMC buildings visit: www.sapphire.eu.com/ knowledge/mmc-hub
Images:
01-02. Sapphire balconies are delivered fully assembled including balustrades and give architects wide scope in balcony design