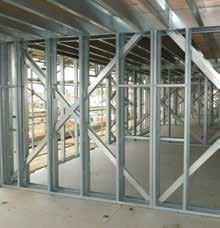
16 minute read
Fire Resistance of Light Steel Framing
Mark Lawson and Andrew Way of the Steel Construction Institute (SCI) discuss issues related to fire resistance of buildings and introduce upcoming new SCI guidance on the fire resistance of light steel framing.
Since the Grenfell fire disaster, the question of the fire safety of medium and high-rise residential buildings has been heightened. Clients and checking authorities are understandably concerned about fire safety, particularly for buildings that exceed 18m in height, and Regulations have been introduced to prevent the use of combustible materials in external walls. SCI has been working with members of the Light Steel Forum and other industry experts to update design guidance on the fire resistance of light steel framing which is well established as a construction system for medium-rise residential and mixeduse buildings. Steel has well-known properties at elevated temperatures and comprehensive design data is presented in BS EN 1993-1-2 and formerly in BS 5950-8 (dating from 1990). BS 5950-8 was the first fire engineering code worldwide and it influenced Eurocode developments. The critical temperature of structural steel beams and columns is taken as 550°C for the design of the fire protection to these members and this critical temperature increases as the proportionate loading (known as the load ratio) on the member reduces. Structural engineers are familiar with the design approach for structural steel but the application of methods for cold formed steel is the subject of the recent work by SCI. Light steel framing has gained a market share because one of its benefits is that it is non-combustible and does not add to the fire load of the building, which are in addition to its other benefits. It may be used with joisted floors or increasingly, with composite floor slabs that are supported by the light steel loadbearing walls.
Strength Retention of Cold Formed Steel
Cold formed steel has slightly reduced strength retention properties at elevated temperatures compared to structural steel H sections and hollow sections because of the influence of local buckling of its thin profile. Nevertheless, the strength reduction factor (SRF) for Class 4 sections at 500°C is still 0.53 of the nominal yield strength. This means that a light steel section can support the reduced loads at the fire limit state up to this slightly lower critical temperature. Light steel framing differs from structural steel in that it is a planar construction system. The 2D walls and floors are protected by layers of Type F or similar fire rated plasterboards. In the last three years, an unprecedented number of loaded fire tests have been performed by light steel framing and plasterboard suppliers to satisfy 60, 90 and 120-minutes fire resistance requirements for loaded walls and floors.
A fire test on a loaded wall is generally performed using the thinnest steel section in a range with the highest sensible load that can be applied by the test house. Temperatures are measured on the flanges and web on the C sections at a number of positions, so that the critical temperatures can be related directly to the load that is applied for the particular wall build-up. This is the socalled ‘load ratio’ method.

With this test information, the design of a C section with thicker steel or with another wall height from that tested can be calculated using the method developed by SCI. The only issue that affects the design solution is then the effect of non-uniform heating
1 2
through the C section for fire on one side, which has two opposing effects: it causes some thermal bowing which adds to bending effects (or P- effects); but on the beneficial side, the centre of resistance of the C section moves towards the cooler unexposed flange. Generally the two effects can cancel each other for the normal range of wall lengths but the loss in buckling resistance due to thermal bowing is taken into account.
Design Methodology for Loaded Walls
The formula that links the design resistance of a loaded C section in a planar wall at the fire limit state to its buckling resistance in normal conditions is given by:
Nb,Rd,fi =k1 Nb,Rd SRF(θref)
b,Rd,fiN is the axial load that may be supported in fire. severe than a fully developed fire within a compartment in a building. The approaches that have been proposed for an external fire are:
b,RdN is the buckling resistance of the C section in normal conditions taking • A fully developed ISO fire curve, but account of the effective length for with a cut-off temperature of 680°C buckling. as permitted by BS EN 1363-2 for external walls. With this, the fire SRF(θref) is the strength reduction endurance will be increased relative factor for Class 4 cold formed steel to an equivalent internal wall, but section. this tests is rarely performed (θref) is the reference steel temperature for a non-uniformly heated section that • A fully developed ISO fire curve, but with compliance for an external wall takes account of non-uniform heating. taken as a notional fire resistance of 60 minutes or as a maximum k1 is a coefficient that takes account of thermal bowing effects and is typically of 30 minutes less than for the internal structure. This is a simple 0.8 for walls supporting joisted floors way of recognising that a natural or 0.9 for walls supporting composite fire occurring outside a building (concrete) floors due to the greater or emanating from windows and restraint provided by the stiffer floor. radiating back onto the external wall has a lower effect than a fully The procedure uses measured developed fire internally assuming temperatures in a test and so it is adequate fire stopping around important that this data is obtained as windows etc temperature versus time in order to be able to back analyse the test. It is a pre-requisite that a valid test result is • A fully developed ISO fire curve without any reduction. obtained for the particular wall buildup for use of the calculation method. The complete design guidance will be presented in a new SCI publication P424, and its accompanying Annexes giving the full design methodologies for light steel loaded walls and floors. The external sheathing boards that are used are very robust structurally but do not necessarily possess the inherent insulation characteristics of gypsum-based plasterboard. Furthermore, for buildings more than 18m high (currently for England), nonExternal Fires on Loaded Walls The same approach may be applied to combustible insulation and sheathing boards are required. external walls but here the question is what is the fire severity of an external fire? At present, there is no agreement on this as logically it should be less
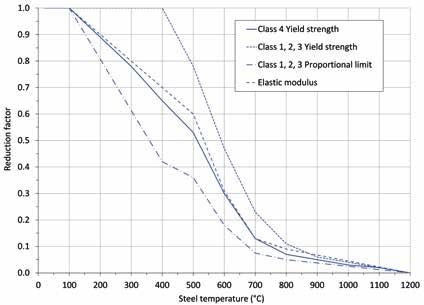
3
Composite Floor Slabs
Composite floor slabs can provide up to 120 minutes fire resistance without requiring a fire protected ceiling by virtue of the embedded reinforcing bars in the deck ribs. Guidance on the fire resistance of composite slabs is given in BS EN 1994-1-2 and in the former BS 5950-8, and SCI publication P375 - Fire Resistance Design of Steel Framed Buildings.
Design Methodology for Loaded Floors
Loaded floors differ from loaded walls in that the effects of thermal bowing do not add to the applied moments and the critical temperature is taken as the bottom flange temperature. Also, for floors, the plasterboard ceilings can become detached as they weaken in fire. The design approach for loaded floors is based on a similar approach to walls but a constant coefficient of 0.6 is used and the buckling resistance can take account of the restraint offered by the floor boarding, as follows:
N
c,Rd,fi =0.6 Nb,Rd SRF(θexposed)
However, most joisted floors are designed for serviceability limits of deflection and so their load ratio will be less than 0.3, so that their critical temperature will be similar to that of loaded walls.
For more information visit:
www.steel-sci.com www.lightsteelforum.co.uk
Images:
01. Light steel frame construction with metal decking for composite floors 02. Typical application of light steel loaded walls supporting a joisted floor 03. Strength and stiffness reduction factors for steel at elevated temperature
LSFA: NEW GUIDE TO SPECIFICATION
Utilising light steel frame as the principle structural component in a building creates many design opportunities. To help understand this better, the Light Steel Frame Association (LSFA) has launched a new Specification & Engineering Guide for Light Steel Frame.
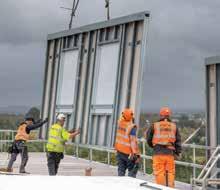
1 2
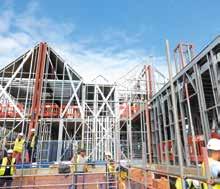
Established to support the overall objectives and growth of the sector, the LSFA formed a working group with some of its members including EOS, DACS, Evolusion Innovation, Fusion Building Systems, Sigmat, Siderise, Ayrshire Metals, Cogent Consulting and the Steel Construction Institute, to develop a Specification and Engineering Guide to ensure that construction professionals gain maximum benefits from specifying light steel framing systems. Engaging the manufacturer’s design team early ensures that their knowledge and expertise in the use of the system permeates through the design process. Many crucial factors that can transform design, engineering and specification decisions not only streamline the construction process but can also save a vast amount of time and money.
“There is often a misconception within design circles that the use of offsite construction limits architectural flare and leads to uninspiring box-like structures. This is far from the case as can be seen from the wide range of structures in differing architectural forms which members of the LSFA have produced.”
Freely available to download, the guide outlines design opportunities, fire safety, performance in construction and in-use together with the different types of systems, applications, and interfaces of light steel frame. Most importantly, the Specification and Engineering Guide outlines the sustainability benefits of steel that are not widely understood. Steel construction provides highly sustainable and economic buildings, representing an efficient use of resources. This longevity combined with the inherent value of an asset that can be recycled or reused at end of life means that steel is not a cost but can be a valuable investment.
The LSFA collaborate with the SCI – a trusted, independent source of information and engineering expertise globally for over 30 years – and a leading, independent provider of technical expertise and disseminator of best practice to the steel construction sector. Throughout the Guide there are links through to useful documents published by the SCI and other leading industry organisations. As the construction industry looks to raise the bar to meet new Building Regulations and sensitivities surrounding of combustible materials, the light steel frame industry is witnessing unparalleled demand for panelised and volumetric modular systems, together with ‘through wall’ solutions which are delivered to site complete with wall linings and sheathing boards.
Images:
01. Gardiner Place in development. Courtesy EOS 02. Light steel frame components can be used across many different building types. Courtesy
Sigmat
www.lsf-association.co.uk
SPECIFICATION & ENGINEERING GUIDE
For Light Steel Frame Construction
LSF systems provide significant sustainability credentials including:
Thermal efficiency
Embodied carbon reduction
Reduced materials – load to weight ratio
Productivity/speed of build reduced, having a positive environmental impact Reduced transportation
Reduced waste
Compatibility with renewable energy technologies
Easily adapted/dismantled for re-use Steel is the most recycled product on earth after water
End of life recyclability
Hadley Group
For further information on LSF and sustainability go to: www.lsf-association.co.uk/library/lsfa-specification-and-engineering-guide/sustainability-and-lsf USEFUL DOCUMENTS Steel for Life and BCSA Supplement: Steel Construction Carbon CredentialsSCI Technical Information Sheet: ED020 – Sustainability of Light Steel Construction Hadley Group www.lsf-association.co.uk VERSION 1 - DEC 2020 12
9
Specification & Engineering Guide
RESIDENTIAL Sigmat - Byron House Apartments HEALTHCARE EOS - Sarah Swift Building, Uni of Lincoln COMMERCIAL Kier - Reading Gateway
COMMERCIAL Fusion Building Systems - Bleinham Care London EDUCATION Fusion Building Systems - University of Sussex LSFA is the representative body for light steel frame manufacturers, fabricators, structural building contractors and supply chain members including erectors, installers, designers, structural engineers and consultants. The Association works with members to raise awareness of the performance, productivity and sustainability benefits of steel.
To download your free copy of the Specification & Engineering Guide for Light Steel Frame visit: http://bit.ly/3cng7o4 For more information on LSFA members visit: www.lsf-association.co.uk
SHOWING THE WAY FORWARD
Geoff Pearce, Deputy Chief Executive at Swan Housing, told us about a busy 2021 ahead as its second factory gets ready to transform production of both its cross laminated timber (CLT) and steel frame-based homes.
1
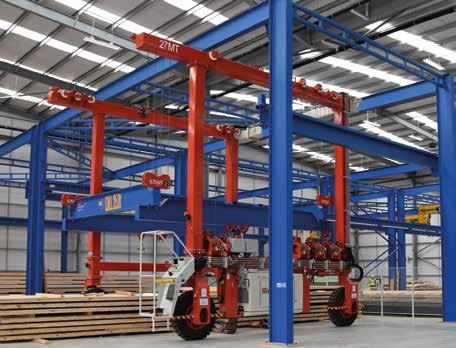
Swan Housing was an early champion of offsite construction and one of the first housing associations to adopt these methods in order to create more high-quality, sustainable homes and thriving communities for those who need it most. “We are on an exciting journey with modular and offsite construction that offers an innovative solution to providing more high-quality homes in the UK,” says Geoff. “Since the opening of our own modular factory in 2017, we have welcomed over a thousand visitors to our factory (pre COVID-19) and in 2019 we launched a modular design guide to share knowledge, experiences and challenges that we faced developing our modular approach. Our factory is able to save 50% on time using the modular construction process, whilst saving 10% on cost. The factory is now able to complete the modules for a three bedroom home in around nine days.” In October 2020, Swan announced the acquisition of a 15-year lease of Basildon 117, a newly built 116,841sq ft industrial unit, opposite their existing modular housing factory in Essex, to manufacture light gauge steel modular housing and operate alongside Swan’s existing cross laminated timber (CLT) volumetric system delivered in its current factory. The second factory was a key strategic move,” says Geoff. “It gives us additional capacity to build at height using a steel framed approach, while continuing to build houses in our existing CLT modular housing factory. The increased manufacturing space allows us to drive up quality and increase efficiencies by giving us more opportunity to use pre-manufacturing and componentisation. “With the support of the Getting Building funding – which is accelerating the fit-out of our second factory – we will be able to support the wider UK efforts to ‘build back better’ for the communities in Essex and East London in which we operate, by creating over 120 jobs by the time the factory is in full production. Furthermore, we will be providing additional apprenticeships in the Basildon factories in order to allow more young people to learn modern construction methods within the manufacturing industry and help address the growing skills shortage.” ‘Factory 2’ will allow Swan to increase its production to up to 1,000 homes a year. This level of production will allow them to use additional capacity to supply offsite homes to London Boroughs and other registered provider partners who share Swan’s social purpose. “We see it as our role to help those like us,” says Geoff. “Those with a clear social purpose around affordable homes, in order
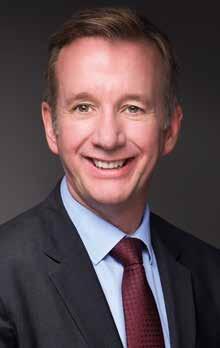
2
to deliver on the requirements of the future affordable housing programmes from both Homes England and the Greater London Authority (GLA) requiring delivery of MMC housing from partners. Factory 2 will utilise a steel framed, fully volumetric approach, allowing us to produce modules which are fully-accredited and mortgageable for higher rise apartments in addition to our existing CLT homes. “
With a huge emphasis on net zero carbon targets and affordable low carbon homes, offsite manufacture is a key way to streamline the construction process, reduce site inefficiencies and reduce waste. Swan’s experience of using offsite has shown that the manufacturing process is highly efficient, achieving: “90% reductions in waste and 70% levels of productivity (as opposed to circa 25% productivity on a traditional building site).” There is also a significant reduction in carbon by minimising on-site activity, particularly around deliveries, with research showing that this can deliver 40% fewer emissions.
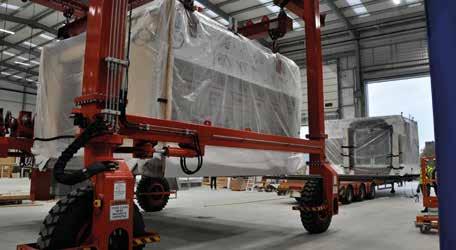
“The quality of the manufacturing process – to millimetre tolerances – delivers high levels of thermal, acoustic and airtightness,” adds Geoff. “Helping deliver homes that are efficient for householders to run. As a material, CLT offers significant sustainability benefits, so much so that our homes at Beechwood are carbon neutral for the first two years. We see our factory-made housing as critical to delivering our new corporate strategy aims around ‘Love the Planet’ and specifically delivering our first zero carbon housing development.” Having a secure development pipeline is essential to the success of any modular housing factory. This is needed to keep the factory team in production and deliver efficiencies of production and scale to cover the factory overheads. It is critical that efficiency and quality control is maximised, whilst reducing activity on-site. “We’ve learnt a lot over the past three years on how to operate most efficiently using our fully vertically integrated construction approach,” says Geoff. “From site acquisition to design, technical, construction, sales and marketing and after care – every step of the process is delivered by our teams. We’ve adapted how we work to best deliver modular – for example, adding a drawing office to our in-house team to ensure that architectural plans are optimised fully for production and enhancing the extent to which our modules are finished in the factory.” In many ways, factory-based manufacture has been able to deal with the impact of COVID-19 better than site-based methods and Swan have been meticulous with putting measures in place to deal with the complexities of the pandemic. “We have worked hard to keep both our traditional sites and modular housing factory operating during the COVID-19 response,” says Geoff. “In the factory and on-site a range of safe working practices have been implemented and adapted as the pandemic has evolved. These are kept constantly under review. We recognise the dedication and commitment of all the front line teams at Swan who have continued to provide services to our residents and constructing much needed new homes throughout the pandemic.” With key schemes in development and Factory 2 expected to move into production soon, Swan has a busy 2021 ahead. “Throughout 2021, we will continue to deliver on our landmark Beechwood regeneration scheme, whilst also developing our modular approach for Laindon Place, Basildon,” adds Geoff. “At Laindon Place we are replacing a tired 1960’s shopping centre creating 224 new homes including both CLT houses and steel framed apartments, as well as a new, vibrant high street and Swan Office. In Tower Hamlets, working in partnership with the Borough and the GLA we will be working towards delivering the next phase of our Blackwall Reach regeneration through our second modular housing factory. “It’s great to see positive recognition from the Government that MMC can help the UK build better and also respond to the climate emergency. We’ve directly benefited from the investment the Government has made through South East Local Enterprise Partnership (SELEP), providing £30million in funding for 14 projects in Essex, Southend and Thurrock from the Getting Building Fund (GBF), including £4.53million to accelerate the fit out of Factory 2. “It’s clear that this encouragement of adoption of MMC will continue through the affordable homes programme. Homes England have specified that developments funded by the Affordable Homes Programme 2021-26, must provide at least 25% of homes using offsite construction and the Mayor of London is looking for use of MMC in the GLA’s forthcoming programme. Although the next 18 months will likely provide challenges as the country continues to recover from the effects of COVID-19, Swan will continue to seek to support and engage with our key stakeholders and government advisers to focus on the many opportunities modular can bring – something the pandemic has ensured we all recognise is critical.”
3
For more information visit:
www.swan.org.uk
Images:
01. Geoff Pearce, Deputy Chief Executive, Swan Housing 02-03. Factory 2 will allow Swan to increase its production to around 1,000 homes a year