
23 minute read
Future-proofing Newbuild Homes
Offsite construction is transforming the built environment and nowhere is that felt most in the housing sector, with volumetric modular methods providing huge opportunities for change. Andrew Shepherd, Managing Director at TopHat, talked to us about market developments.
1
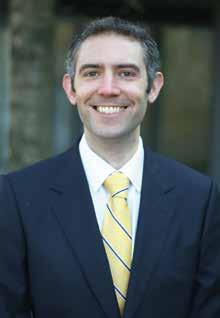
Central to the successful implementation of innovative offsite construction methods is the adoption of technology and ‘automated manufacturing’ to deliver the UK’s oftquoted requirement of 300,000 new homes annually? But how big are the opportunities for volumetric modular construction in addressing some of these numbers?
“There is no one-stop-shop solution to the housing crisis and modular housing certainly isn’t the solution all by itself – the last time we delivered over 300,000 was back in 1953,” says Andrew. “However, what it can offer is additionality and speed, helping the market grow, without impacting on the existing homes that we deliver. By manufacturing offsite along production lines, companies such as TopHat can bring homes to the market twice as fast as traditional methods, helping to speed up the delivery of much-needed housing across the UK to get closer to the 300,000 new homes-a-year target as well as increasing productivity from a restricted workforce.”
The volumetric modular market has grown significantly in the last 3-5 years, with huge amounts of investment entering offsite manufacturing to fund new factories and innovative products. TopHat received a £75million investment from Goldman Sachs to help expand and scale the business – what are they doing differently and offering new compared to others operating in the marketplace? “TopHat’s patented technology means our products can be tailored so they can meet the local design requirements of a particular place,” says Andrew. “Much like the automotive and aviation sectors – or with the wardrobes you may buy in IKEA – the fundamental parts can be produced en-masse with high levels of quality assurance. Yet TopHat’s technology allows such parts to be customised, meaning it maintains quality and speed of delivery without having identical towns up and down the country. This is unique to TopHat and is a key point for our clients, as this means they can ask us to adjust our products to meet the requirements of local authorities and planning committees. TopHat also has a high level of automation in our manufacturing processes, which help deliver the high levels of tolerance and quality.” Reshaping design perceptions of what modular homes look like and feel like to live in are important, with notions of temporary post-WW2 prefabs now long gone. Pressure now surrounds producing low carbon, sustainable homes ‘at quality but at low cost’, something that is not easy. The Government’s English Housing
2
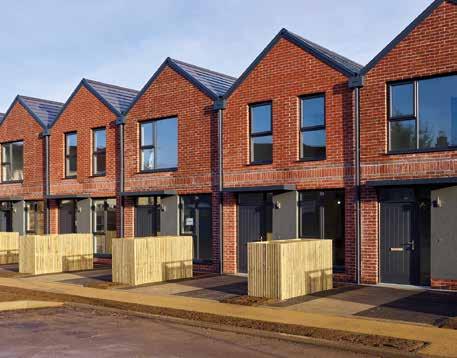
Survey recently revealed that there is an urgent need to improve the quality and energy efficiency of England’s homes. “Through the use of timber technology, we can significantly reduce the carbon footprint of our buildings,” says Andrew. “Such that one traditional masonry home has the same embedded carbon of 27 TopHat homes. We can also deliver zerocarbon homes, meaning they emit no carbon from utilities such as heating, water and electricity. This is done by utilising low-carbon technologies such as air source heat pumps and solar panels. “By integrating technology into our design processes, which allow the company to model the energy performance of a home by collecting and collating empirical data points, we typically deliver homes that are a third more energy-efficient than those traditionally built and achieve a high EPC rating. This helps save consumers hundreds of pound on energy bills each year. These energy-efficiencies also mean that TopHat’s homes exceed current and newly proposed building regulations – like the Future Homes Standard – avoiding costly retrofitting programmes in the future. None of this is done at the expense of good quality design. Large windows, high ceilings and ergonomic design are key elements to delivering good homes, none of these are compromised through the adoption of offsite.” “TopHat’s homes can be powered for as little as 90p a day. The efficiency of our homes means that occupiers are better able to afford to heat their homes. The benefits also extend to the local community, where our projects result in a substantial reduction in transport to and from site, especially when compared to a traditional construction approach. Furthermore, residential property is an increasingly popular asset class for institutional investors, who as a rule are increasingly focused heavily on the ESG agenda. Similarly, housing associations and councils also have to meet strict environmental criteria. Delivering homes more sustainably will play a key part in helping both these parties meet green targets, which are only likely to become even more important over time.” TopHat recently completing the delivery of 20 affordable homes for Medway Development Company, Medway Council’s development arm in Chatham, Kent. All 20 of the homes, which were delivered on an infill site will be made available for affordable rent and operated by the mhs homes housing association. Low-carbon technologies, such as solar panels, have been integrated into the design of the homes and will provide residents with clean, lowcost electricity. Due to high levels of airtightness, the homes will achieve at least a ‘B’ Energy Performance Certificate rating – making them more energy-efficient than 92% of newbuilds in the UK. What else is TopHat hoping to achieve in 2021 and where is the modular housing market heading over the next 18 months?
“Our focus this year is going to be refining and improving our product,” adds Andrew. “We’ve recently hired Airbus’s former vice president of digital transformation, Matthew Evans, to be our Chief Technology Officer – a role which will see him integrating new technology into our manufacturing process to deliver well-designed, energy-efficient housing for private developers, housing associations and local councils. My prediction for the next 18 months for the market as a whole is that modular housing will become an increasingly mainstream choice for housing delivery, and TopHat will be at the forefront of this.”
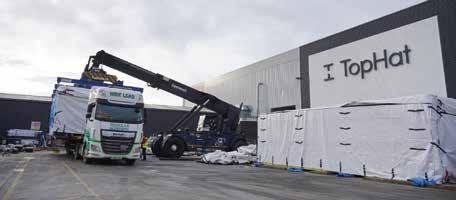
3
4
For more information visit:
www.tophat.io
Images:
01. Andrew Shepherd, Managing Director, TopHat 02-03. Factory production produces high-tech, quality, low carbon homes that can be delivered quickly and efficiently 04. White Road, Medway
PROVIDING AN AGILE SOLUTION
Jackie Maginnis, Chief Executive, Modular and Portable Building Association (MPBA) discusses how offsite construction can respond to help provide a solution to the many recent events that have resulted in the construction industry coming under unprecedented scrutiny.
The pressure of operating COVID-19 secure construction environments combined with tough schedules and difficult specification decisions are all taking a toll on developers – particularly those operating in the public sector. As we strive to recover, it has forced a rethink of the way buildings are designed and built. When we eventually return to the ‘new normal’ – it is a given, at least in the short term, that social distancing measures are here to stay. There is now widespread agreement that in order to operate effectively and safely developers need to reduce their reliance on labourintensive traditional construction and look to new methods.
Taking the majority of the build process offsite into well-managed factory environments requires much less manual labour, making volumetric modular methods inherently easier to implement safer social distancing measures and enhanced hygiene regimes. Factories also offer health and safety benefits because they are controlled settings where procedures and process take priority. Another significant aspect is the supply chain simplicity offered via modular approaches – taking many of the complexities of specification issues off the critical construction timeline. The pandemic combined with the Brexit transition has the potential to create serious challenges, with an established supply chain predominately in the UK, using volumetric modular technology can help avoid disruption. The potential for a faster and more streamlined build process was highlighted by the UK Commission for Employment and Skills Council which estimated that if 25% of the construction sector transitioned to offsite approaches, a 3.6% increase in productivity would be readily achievable.
Modular technology reduces build times by an impressive 50-60% when compared to traditional processes. This quick turnaround time is key for helping the construction industry offset delays in project timelines. As has been clearly demonstrated during this time of crisis, factories can keep rolling and where there is an urgent need – increase shifts up to 24 hours a day. Many of our members made gargantuan efforts to help support the construction of additional healthcare and education facilities over the last few months, achieving unprecedented delivery schedules of a few weeks rather than many months or even years. There is quite rightly a renewed focus on the quality of materials and the processes involved in creating buildings. Again, this is where modular construction can offer some muchneeded assurances, as the supply chains and testing regimes are much more connected. Not only does this ensure smooth delivery within a tight timeframe, but it also limits the opportunities for materials to be ‘engineered’ out and allows for a high level of accountability throughout the build process. The climate emergency remains a key concern. Compared to traditionally built projects – up to 67% less energy is required to produce a modular build. Offsite construction also has a positive impact on the carbon footprint of the building as it allows for a reduction in the total number of deliveries to sites by up to 90%. In addition, not only is the actual construction process ‘greener’, but the airtightness achieved in using volumetric modular approaches enhances in use energy efficiency and reduces carbon omissions for the lifetime of the building. Modules can now also be factory fitted with sustainable technology such as solar panels and energy-efficient glass. Some developers have remained entrenched in outmoded methods, however we are now seeing a shift in attitude when it comes to modular technology, largely driven by increased awareness of the time and cost-saving benefits. This in turn is leading to an increase in adoption. According to Forbes, 7.5% of the homes built in the UK in 2017/18 were modular, and increased growth was forecast for 2020 even prior to the pandemic. The government are trying to address multiple issues, but housing still remains a priority. Back in October, Housing Minister Secretary Robert Jenrick said the government will listen to views on where new homes should be built but will not cut its target to build 300,000 homes a year. It has been a matter of great debate if the target will be met but the need for new, affordable homes is not going away and modular construction offers a solution.
Without an even wider adoption of modular technology, it is going to be difficult to achieve the levels of agility, flexibility, responsiveness and the assurance the UK is going to need to both actively and safely achieve the scale of the public sector and housing targets.
For more information visit:
www.mpba.biz
PROMOTING A FULL RANGE OF MODULAR SOLUTIONS
Sika UK has grown steadily over the past few years, despite operating in challenging market conditions and have appointed Simon Griffiths as Head of Sales – Modular Construction, a role that will see him build on the continued growth of the company in the modular construction sector in the UK.
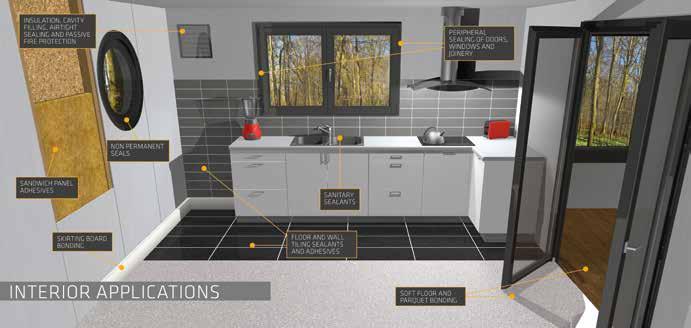
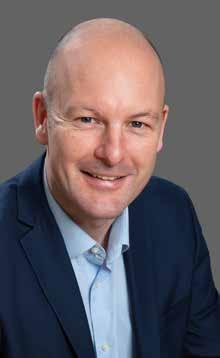
2
The new appointment will see Simon build on the already well-established Sika brand in the UK, with a clear focus around Sika’s offer to modular builders, and specifiers of modular build projects. Simon has many years of experience advising on suitable roofing systems within the modular market, coupled with experience of building envelope system selling. He has worked closely with main contractors and specifiers, and has a clear understanding of their needs, in order to deliver on expectations, and also has experience in delivering projects as part of Government Frameworks.
Simon joined Sika in 2007, initially as a Technical Advisor for the Sika Sarnafil roofing brand, a market leader in roofing membranes. A move into sales management for the roofing business unit, which included brands such as Sika-Trocal and Sika Liquid Plastics, meant a wider exposure to Sika’s other market leading brands in a huge market sector within construction.
“Sika has a wide portfolio of products ideal for the modular construction marketplace, but much more than this, we have a wealth of experience in many manufacturing applications, such as Automotive, Transportation, Marine, Appliances and Renewable Energy,” says Simon. “We go beyond the supply of materials and have the technical expertise to assist in the development, testing, and design, through to supporting implementation in production lines – often curating custom offerings. I’m here to help modular builders and specifiers, by being the go-to person at Sika for all their needs, and I am looking forward to ensuring our customers’ needs and expectations are properly met.”
1
Sika’s Offer for the Modular Construction Market
The past year has seen events that have re-shaped the world we live in. The world around us has seen generational shifts, with rapid transformations in IT and advances in technology. Modern methods of construction (MMC) continues to move towards the heart of our construction industry in the UK. We understand that, for the offsite constructor, finding ways to increase pre-manufactured value (PMV) for the client, but keeping the manufacturing process as efficient as possible, can be challenging. We believe that it is the responsibility of key suppliers to assist this process, in whichever way possible. At Sika, we have the technology to support all areas of manufacture.
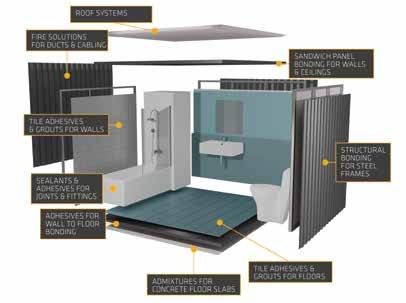
Sika can support the advancement of PMV, by providing unique and high-performing solutions. We can demonstrate high levels of technical knowledge, and support in many applications, from the floor, through to roof – these being interior and exterior applications for volumetric, panelised or pod manufacture. Our approach is to define ways to reduce build-time, simplify bill of materials, and increase quality as well as life expectancy, whether it be timber or steel framed construction.

Interior Applications
In the context of interiors, we can support with clever materials for cementitious bases through floor coatings, to luxury vinyl tile (LVT) adhesives and good solutions for wood floor bonding, as well as traditional floor tile adhesive systems. We can also support with joint sealants, whether it be sanitary or aesthetic. Our passive fire protection range can assist in making units safer. Our reduced dust, low emission wall levelling compound meets all the latest EHS requirements and gives class-leading finishing characteristics. Our high green strength adhesive can be used to reduce the requirement for mechanical fixings, which can create noise, vibration and harshness (NVH) issues. Pretty much, we can help you look at applications in new ways.
Exterior Applications
We understand the need for watertightness and with our weatherproofing solutions for roofing, walls and windows. We aim to assist you to deliver units, with minimal retro repair, and reduced zip-up costs. Our robust solutions will reduce transit damage of volumetric units, and our ideas to reduce weight will lower CO2 from transportation requirements. Our innovations to improve structural rigidity of units can mitigate flex in transit, and the subsequent repairs. Our membrane systems can assist with keeping the weather out, whilst the units wait to be slotted into the final building. Whichever exterior wall finish is used, Sika can support our customers. From renders to adhesives for brick slip bonding, to wood adhesives and bonded panelised systems.
Pod Manufacture
Our solutions for bathroom pods and wet rooms can reduce waiting time for curing. Whether it be for the concrete base or ETAG022 systems for wet room walls and floors, for tile bonding with automated solutions, or fast curing stiffener bar attachment, we are able to help. Sika has leveraged its huge product range to come up with some great solutions, to improve rigidity, reduce noise transfer, improve fire performance, reduce cycle time, lower costs, enhance sustainability, boost quality and provide a one-stop-shop from basement to roof.
3
4
For more information visit:
https://bit.ly/3ssM7fu
Simon Griffiths Mobile: +44 7803 667225 griffiths.simon@uk.sika.com
Images:
01. Interior Applications 02. Simon Griffiths, Head of Sales – Modular Construction 03-04. Many applications are available for modular delivery
CASE STUDY
SPECIAL BUILD FOR SPECIAL SCHOOL
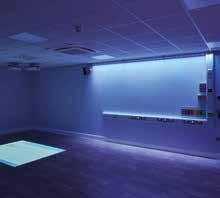
1 2

It’s sometimes easy to overlook the importance of a simple classroom block. The latest addition to Ty Gwyn Special School may look like a normal school building, but it is packed with interesting features and was delivered using offsite methods.
As the name suggests, Ty Gwyn Special School is no ordinary school, and t his is no ordinary classroom block. Ty Gwyn is wholly focussed on supporting pupils who have profound or complex needs. Rated as ‘Excellent’ by Estyn, the education and training inspectorate for Wales, the school will educate children from three years to nineteen years old who might present severe or challenging behaviour. The school needed a new block urgently to cater for a rise in pupil numbers – with less than ten pupils per class, classroom space is vitally important for the school. To procure the new block, Cardiff Council ran a mini competition via the SEWSCAP framework, which was subsequently won by Wernick Buildings. The building is constructed using 18 individual modules which were manufactured in Wernick’s dedicated factory in Port Talbot, less than an hour away from the site. These were transported to site by lorry, then craned into position and bolted together to form the core of the building. The brick cladding and trussed roof were then added to the core to give a traditional construction appearance. Manufacturing the building in a factory environment gave the project several advantages. Firstly, the building could be constructed at the same time as the foundations were being prepared, dramatically reducing programme length, particularly on-site. Manufacture was also not affected by site conditions like the weather, making the programme even more reliable. This was vitally important for the school, who would need the building in time for the start of the new term.
The reliability of modular building was further tested by the outbreak of COVID-19. However, as a large part of the fit-out had already been completed in the factory, Wernick were able to minimise the operatives needed on-site at any one time. Combined with careful site management, this allowed Wernick to continue work during the first lockdown, and ultimately the building was delivered ahead of schedule.
Providing a robust building which would be both a safe and calming environment for Ty Gwyn’s pupils was important. This was reflected in the enhanced specification required by the council which Wernick embraced fully, enhancing their standard modular system to meet the requirements. The painted internal walls were upgraded with impact-resistant plasterboard to better withstand the demanding classroom environment. The floor, apart from being fully non-combustible, was also enhanced to improve rigidity and acoustic performance. All the doors are also equipped with acoustic seals to reduce noise throughout the building and ALUMASC Safehinge anti-finger trap system to avoid any opportunity for entrapment. Acoustic performance was especially important for the withdrawal rooms off each classroom. These spaces can be used when a child needs a calming and safe environment. The walls and floor of these were padded to ensure child safety and were also equipped with an observation window and AV system, allowing teachers to play music for the children from the main classroom. A ducted heat recovery system was employed in the ventilation in these rooms, and comfort cooling is used throughout the building. Aside from the withdrawal rooms and interactive whiteboards in each class, there is also a dedicated sensory room with controllable coloured lighting and interactive projections on the floor and wall which pupils can engage with. All classrooms are also equipped with a DDA-compliant toilet and shower room, as well as a ‘nurse call’ system to help staff in emergencies. Glazing throughout the building was also enhanced to reduce U-values and improve security by meeting Secured by Design standards. As standard the windows had toughened glazing inner and laminate glazing outer. A spokesperson for Cardiff Council commented: “The Wernick team were excellent to work with from start to finish. Teamwork was at the heart of everything, and the team committed from the outset to deliver the project on time. Working relationships were excellent, and this facilitated first class communication and ultimately the delivery of a highly successful project.”
For more information visit: www.wernick.co.uk
Images:
01-02. Ty Gwyn Special School is packed with interesting features including a dedicated sensory room with controllable coloured lighting
OFFICE OF THE FUTURE
Our workplaces are facing a series of challenges in a rapidly changing future and the design and creation of new workplaces needs to be radically different from the past. Ed Hayden, Director at architects Scott Brownrigg, highlights some of many the challenges and solutions available.
1
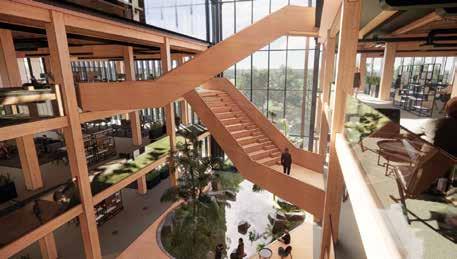
Some of the key challenges we face in new office design can be considered under three general headings: the pandemic impact and the transformation of our ways of working, responding to infection by creating healthy working environments and climate change and designing for net zero carbon. The way in which we work has changed nearly overnight, with the pandemic transforming large parts of the centralised office-based workforce to a dispersed homeworking society, and the effects of this are likely to last. What does this mean for the structure of companies, and what they require from offices in the future?
Technology offers autonomy, allowing anyone to work remotely anywhere, and the implementation of 5G technology will reinforce this. Individual ‘computer based’ focused working may well take place in the home setting, so we must consider what becomes of the traditional commercial office building. Whilst homeworking offers many benefits it also has some major disadvantages, dependent on your circumstances and if you have the space it can be great for focused tasks. You can work without interruption, surrounded by all the comforts of a home office tailored to your specific requirements. This shift to a homeworking lifestyle has been embraced by the majority of those who can do it, so what becomes of our offices and what do we need from them in the future?
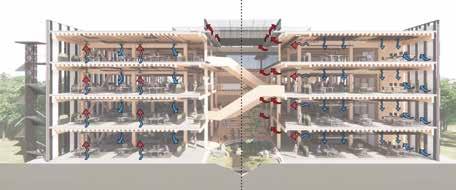
Collaboration, face-to-face contact and human social interaction are awkward and limited over the computer or phone screen. Fluid meetings where multiple items can be discussed in a freeform manner, splitting away from the primary topic and rejoining with new ideas, can be very difficult over networking software. Our buildings need to fulfil that role and become places for human co-operation and forums for creative collaboration. Responding to the challenges of the current (and future) pandemics the design of offices will need to limit the risk of infection spread. To rebuild acceptance of the ‘office’ we need to provide healthy environments, and to create these will require fundamental changes, which will be reflected in the offices we design for the future. The office of the future will need to mitigate against the spread of future contagious diseases and allow the office to continue running effectively through any future pandemics, this has a number of fundamental effects on office design. The prevalent use of air-conditioning has meant that in general 90% of the air in offices is recycled, and this is supplemented by 10% fresh air. This may no longer be acceptable given the perceived risk of airborne infection spread. We anticipate a reversal, with 90% of fresh air being a new
2
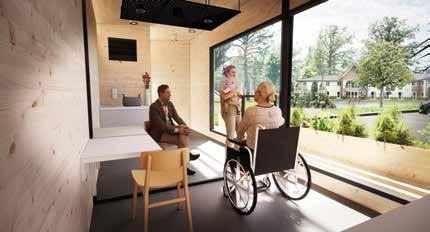
requirement, with possible changes to the design guidance such as the Well Building Standards and Building Regulations. Whether or not this risk has been proven there is still the issue of the building occupants’ perception – knowing that the air is recirculated and not filtered may well create anxiety and discourage occupants from using the space. A move to a natural or displacement ventilation solution with increased fresh air and avoidance of recycled air is a solution: the office of the future uses the atrium stack-effect to draw fresh air in through the façade and vent stale air out through the roof avoiding cross-contamination risks. During the winter, stale air is collected at the top of the atrium and used to preheat fresh air using a plate heat exchanger, again avoiding contamination. The heating and cooling of the space is implemented using radiant panels which can radiate heat (or cool) to adjust the internal temperature. Reduced occupation densities, carefully planned layouts, and limited contact with surfaces (such as door handles) are all matters that may become normal design considerations in the new generation of workplace design. Finally, the greater crisis that faces humanity is the effect of man-made climate change. We have a pressing need to address the amount of carbon dioxide that is released in the occupation and construction of our office spaces. 30% of the carbon is created during the construction phase, and in order to achieve ‘net zero carbon’ buildings must address this issue. Switching from carbon intensive materials such as concrete and steel to materials which ‘sequester’ carbon into the building fabric is fundamental in achieving these goals. The use of mass timber in the form of laminated veneer lumber (LVL), cross laminated timber (CLT) and glulam as the building structure is the solution. This is a ‘better than zero’ solution during the life of the building (and potentially beyond). The office of the future uses, pre-manufactured, zero waste timber construction systems with innovations such as LVL rib deck panels, CLT timber core walls and glulam columns and beams to create efficient attractive sustainable spaces. This combines perfectly with the other aims of a flexible collaborative working environment and a healthy naturally ventilated workspace. The new office concept combines all of these considerations, providing a healthy attractive environment which encourages collaboration and creativity without impacting on the health of the planet. We look forward with anticipation to a new era of workplace design which encompasses these goals, and we are already seeing a shift in the mindset of clients, occupiers and developers to be vanguards in the creation of the office of the future.
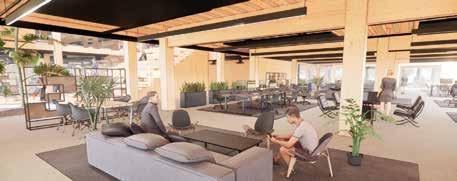
3
For more information visit: www.scottbrownrigg.com
Images:
01-03. The office of the future needs to promote health and wellbeing as well as excellent design 04. The Social Contact Pod
THE SOCIAL CONTACT POD
4
In response to COVID-19 Scott Brownriggs’ Design Research Unit has been working on a practical, rapidly assembled solution with CLT experts, Ramboll and M&E and sustainability specialists, Hoare Lea, ‘The Social Contact Pod’ allows families to spend valuable time with loved ones without the risk of contamination. Constructed from CLT panels (potentially surplus stock from house builds), it is lightweight, rapidly constructed and is easily transported on the back of a standard truck or pulled on a trailer. It can be installed at the entrance to a care home and/or dropped in a carpark or garden for immediate use.
Importantly it’s been designed to be fully sustainable so that pods can be repurposed or recycled with relative ease when they are, hopefully, no longer needed. Within the fully accessible design, a Perspex partition separates the two groups; an area of plastic membrane allows for human contact and hand holding. In terms of internal comfort the pod has high levels of air quality and natural daylight, along with a comfortable temperature, acoustics, and access to fresh air. Simplicity is key to the design, the pods are cost-effective to run, with the lowest carbon emissions possible, and feature simple controls for people to adjust their environment as needed.