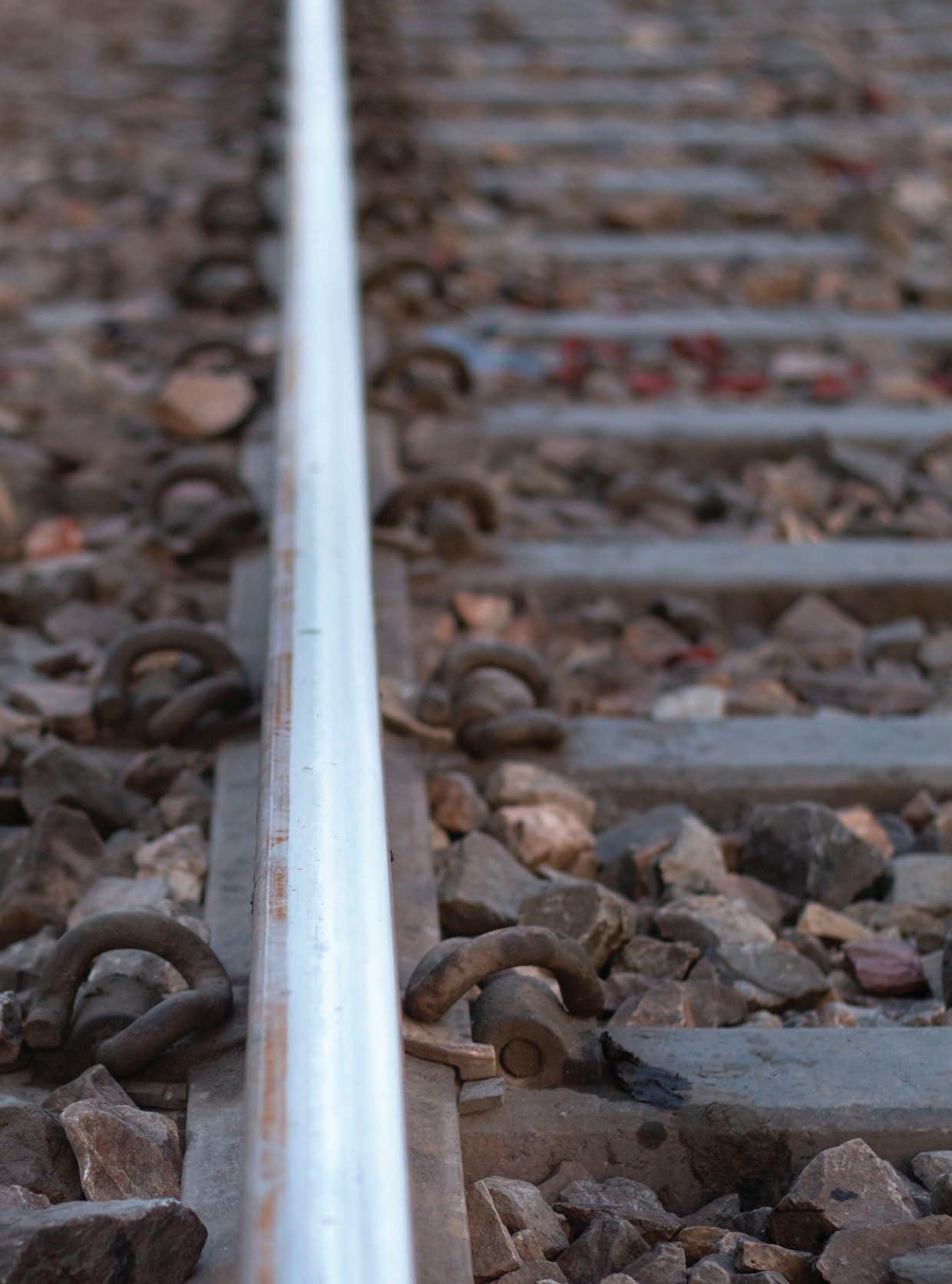
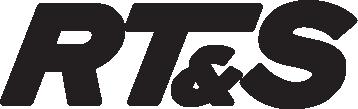
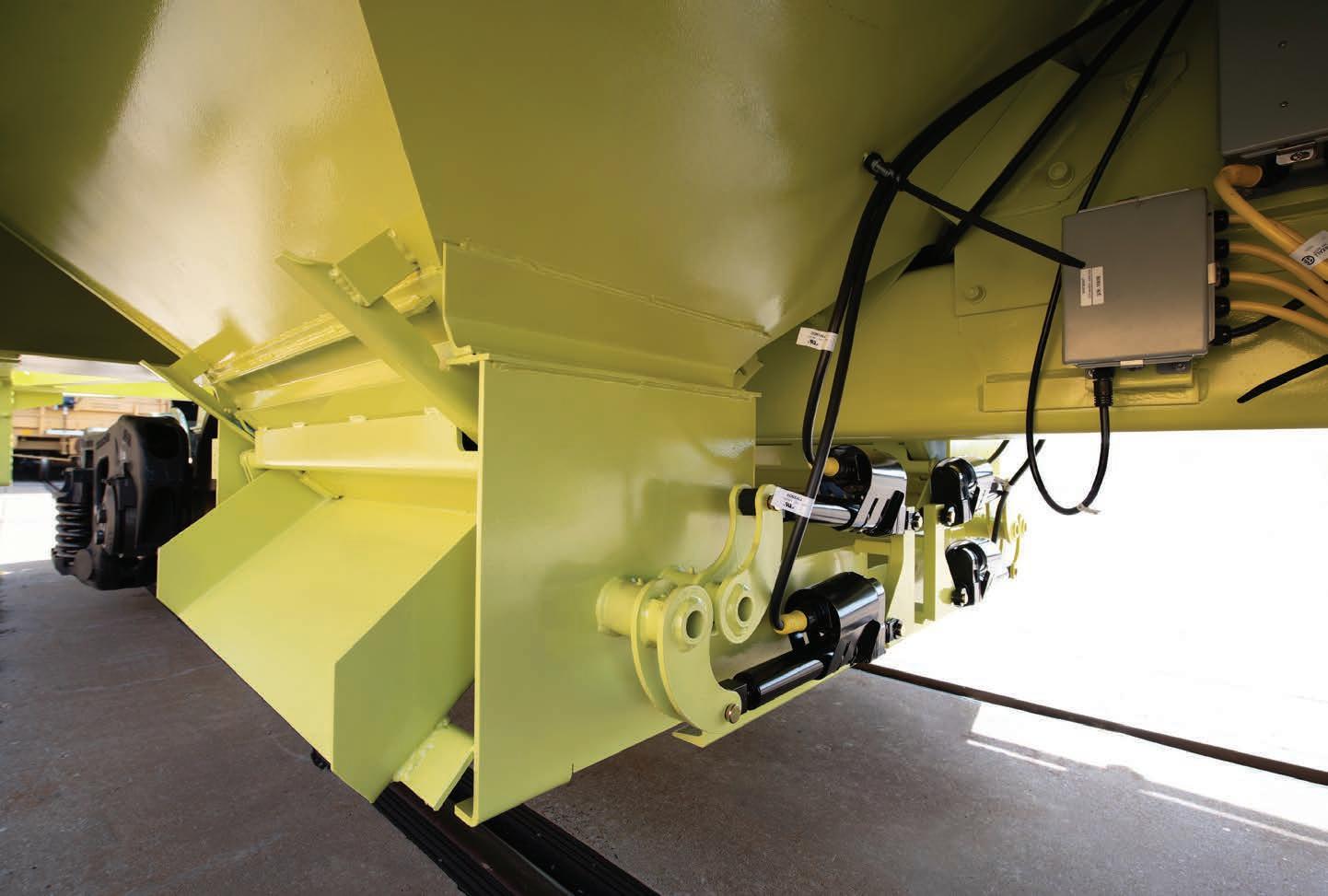
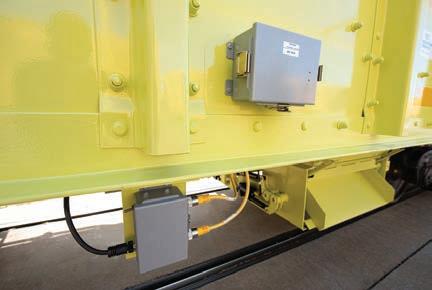
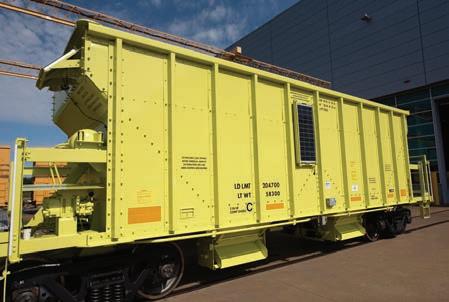
With 25,000+ ballast gates sold worldwide, Miner AggreGate® sets the standard, delivering proven reliability and innovative flexibility. Our new Stand-Alone Solar Powered Electric AggreGate—complete with its own car-mounted work lights for night ballasting—enables independent operation of individual cars anywhere within the ballast train. This boosts MOW agility and efficiency by eliminating the need for grouping manual and automatic cars. An optional remote wireless control system allows for specific car and gate selection for up to 1000 cars. Standard electric, air-powered and manual models are also available.
LEFT: Accessible gate controllers and battery banks ensure smooth operations and efficient maintenance.
MIDDLE: Car-mounted solar panels keep the battery banks charged and ready for stand-alone ballast operations.
RIGHT: Miner’s stand-alone LED lighting system enables safer night operations.
Vol. 121, No. 3
Print ISSN # 0033-9016, Digital ISSN # 2160-2514
EDITORIAL OFFICES
1025 Rose Creek Drive Suite 620-121 Woodstock, GA 30189
Telephone (470) 865-0933 Website www.rtands.com
DAVID C. LESTER Editor-in-Chief dlester@sbpub.com
JENNIFER M c LAWHORN Managing Editor jmclawhorn@sbpub.com
EDITORIAL BOARD
David Clarke, University of Tennessee
Brad Kerchof, formerly Norfolk Southern Jerry Specht, CPKC/AREMA
Scott Sandoval, Genesee & Wyoming
Robert Tuzik, Talus Associates
Gary Wolf, Wolf Railway Consulting
CORPORATE OFFICES
1809 Capitol Avenue Omaha, NE 68102
Telephone (212) 620-7200 Fax (212) 633-1165
ARTHUR J. MCGINNIS, JR. President and Chairman
JONATHAN CHALON Publisher
MARY CONYERS Production Director
NICOLE D’ANTONA Art Director
HILLARY COLEMAN Graphic Designer
JO ANN BINZ Circulation Director
MICHELLE ZOLKOS Conference Director
CUSTOMER SERVICE: 847-559-7372
Reprints: PARS International Corp.
253 West 35th Street 7th Floor New York, NY 10001
212-221-9595; fax 212-221-9195 curt.ciesinski@parsintl.com
By David C. Lester, Editor-in-Chief
Amajor focus for Railway Track & Structures is education. Recent efforts focused on this include our partnership with the WheelRail Interaction Heavy Haul conference as the Presenting Sponsor and our monthly article based on a presentation at one of the recent seminars. We also have work from currently practicing railway engineers on specific topics targeting young engineers at the beginning of their careers, along with senior engineers who continue to work for a railroad or who have begun a rail engineering consulting practice. With reports of more people retiring from than joining the railroad, education is more important than ever.
This year’s WRI Heavy Haul conference will be held on June 10-12, 2025 at the Westin Kansas City Hotel at Crown Center in Kansas City, Mo. The three-day conference begins on June 10 with the Principles course, for which NURail Center of Excellence, is the Presenting Sponsor. NURail is a consortium of university engineering departments led by the engineering department at the University of Illinois at Urbana-Champaign, and focuses on the basic principles of Heavy Haul wheel-rail interaction. Other university engineering departments participating in the consortium are the University of Illinois Chicago, University of Delaware, Kansas State University, Michigan Technological University, Morgan State University, Rutgers University, University of Texas at Austin, and Tuskegee University.
We are excited to see NURail Center of
Excellence partnering with WRI. This organization focuses on research along with education and outreach. NURail’s Executive Director, Christopher P.L. Barkan, said “These faculty, from a small group of colleges and universities around the nation, began working together in the mid-2000s, first supporting one another’s development of rail programs and then, reaching out to faculty at other colleges and universities to support their efforts to expand or reintroduce rail into research and educational programs at their schools.”
From an educational standpoint, Barkan points out that practical application is just as important as more theoretical research.
“Furthermore, most of the NURail PIs (Principal Investigators) have substantial experience with the rail industry or public sector rail organizations. This is critically important because while understanding what is technically possible is necessary, it is not sufficient in developing an effective program of transportation research and education. Faculty and their students must understand the context and institutional constraints in which their results will be applied if their work is to have an impact.”
WRI 2025 information and registration links can be found at https://wri2025hh. wheel-rail-seminars.com.
DAVID C. LESTER Editor-in-Chief
Rafael Maldonado, Deputy Division Manager, ENSCO, Inc., Charlottesville, VA
Ivan Aragona, Data Management and Digital Solutions Director, ENSCO, Inc., Tampa, FL
The Transportation Technology Center (TTC), operated by ENSCO, is a hub for testing and developing cutting-edge railway maintenance solutions. In an industry facing increasing demands for higher speeds, greater tonnage, and enhanced safety, data-driven asset management has become essential for maintaining infrastructure reliability.
Traditionally, track maintenance relied on manual inspections, consolidating information into spreadsheets, and following pre-planned maintenance schedules. Decisions were often based on experience and routine rather than real-time data. With the integration of predictive analytics, advanced track inspection systems, and machine learning, railroads are shifting toward condition-based and predictive maintenance models. This transition enables more targeted maintenance, extends asset life by addressing issues before they become critical, and reduces costs through optimized capital planning.
Track Asset Management System
The ability to maximize the value of track inspection systems and implement a predictive, condition-based maintenance strategy hinges on the development of a well-defined asset register. A comprehensive asset register serves as the foundation for effective track infrastructure management, enabling railroads to integrate real-time condition data into
decision-making processes.
Historically, asset registers are primarily cataloged physical track infrastructure and operational conditions in track charts, including point assets (e.g., turnouts, culverts, bridges), linear assets (mainline track, sidings, yard tracks) and operational criteria such as gradient, curvature, and track class/speed limits. As railroads transitioned toward data-driven maintenance strategies, these registers expanded to include component-level details such as tie type, fasteners, and rail type. Geographic Information Systems (GIS) and track chart overlays have further improved data completeness, ensuring a more accurate representation of assets across extensive rail networks.
At a minimum, a modern track asset register
consists of several key attributes that collectively support effective track infrastructure management. These include linear and point assets, such as track, turnouts, bridges, and culverts, as well as linear location references, like mile markers, foot markers, and chainage measurements. Geospatial positioning, using GPS coordinates from inspection systems, synchronizes with asset linear locations to improve accuracy.
Additionally, the register includes track design characteristics, such as gradient, tangent, spiral, and curved sections, and track components, including rail type, tie type (wood, concrete, etc.), and fastener type. Operational characteristics, such as track classification and tonnage, further refine the data necessary for decision-making.
At first glance, capturing such a detailed asset register may seem excessive. However, as railroads continue shifting toward data driven maintenance strategies, these detailed records become invaluable for conducting analysis of premature failures and long-term asset performance studies by integrating with track inspection systems condition data.
Railroads now have access to a wide array of inspection technologies capable of monitoring track conditions at scale with unprecedented accuracy. These systems enhance manual inspections, enabling track inspectors and maintainers to focus on high-priority areas with greater precision. From track geometry measurements to high-resolution imaging, today’s inspection solutions are deployed across a variety of platforms, including dedicated manned inspection vehicles, autonomous in-service rail-bound vehicles, and drones.
• Track Geometry Measurement Systems (TGMS) play a fundamental role in assessing rail infrastructure health by measuring gage, crosslevel, alignment, profile, warp, and twist.
• Rail flaw detection, once dependent on manual inspections, has greatly improved with Ultrasonic Testing (UT) and Eddy Current Testing (ET), which identify internal rail defects and surface cracks before they become critical.
• Vehicle/Track Interaction (V/TI) monitoring provides insight into track
conditions under real-world operations, capturing data such as carbody accelerations, truck lateral movements, axle impact loads, and mid-chord offset variations.
• Machine vision inspection, using highresolution cameras and artificial intelligence, automates defect detection for ties, fasteners, ballast conditions, and joint bars.
Other key technologies include Gauge Restraint Measurement Systems (GRMS), which assess track stability under simulated loads, crucial for preventing derailments, especially in heavy-haul operations, and
LIDAR-based 3D mapping, which provides detailed models of track corridors for vegetation management, clearance assessments, and track bed analysis.
These inspection technologies, when integrated into multi-system platforms, allow for comprehensive data collection in a single survey pass. The Federal Railroad Administration’s (FRA) Automated Track Inspection Program (ATIP) exemplifies this approach, incorporating multiple inspection technologies within a single vehicle to maximize efficiency. Additionally, DOTX 225, now part of the Transportation Technology Center’s (TTC)
inventory following its transfer from the FRA, continues to play a role in track assessment and monitoring at the facility.
Transforming Data into Decisions
The true value of track condition data lies in its ability to inform maintenance decisions. Raw measurement data must be aggregated, processed, and analyzed to determine which assets require intervention. This process involves several key steps:
1. Location Determination: Aligning track inspections data with an asset register ensures consistency across multiple surveys.
2. Data Quality Filtering: Predictive systems rely on high-quality inputs; filtering out poor data—such as correcting sunlight interference in optical based systems or replacing invalid readings using historical trends—improves accuracy.
3. Data Alignment and Fine Tuning: Highprecision alignment, whether manual or automated, is required to enable reliable degradation predictions.
4. Track Segmentation: Converting linear railway infrastructure elements into discrete, analyzable segments ensures consistent comparisons across a network.
5. Prediction Models: Once data has been aligned, predictive models assess future track conditions. Some preventative maintenance activities have well documented effects, allowing for accurate short-term forecasting and long-term planning.
6. Maintenance Rules (Performance Indicators & TQI): Performance indicators and Track Quality Indices (TQIs) are
metrics used to assess the overall condition of track segments based on data. While a single defect may trigger an alert, TQIs analyze multiple parameters, enabling strategic, data-driven maintenance recommendations.
Case Study: Condition-Based Maintenance Planning
A condition-based Maintenance of Way (MOW) algorithm was developed to assess track segment health and provide a data-driven approach to maintenance planning. The TQI, derived from this algorithm, serves as a key performance indicator:
TQI = WA × σALG + WP × σPRF + WW × σWRP + WX × σXLVL
where,
σ = Standard deviation of track geometry measurement,
ALG = Alignment (average of the left and right rail measurements), PRF = Profile (average of the left and right rail), WRP = Warp, XLVL = Crosslevel, W? = Weighting Factor for each parameter
Analyzing TQI data over an 18-month period allowed railroads to identify track segments in need of resurfacing. Figure 3 provides a comprehensive view of the rail linear infrastructure, maintenance segments, and the Surfacing TQI for each segment over time. During a 12-month period, the thematic analysis confirmed poor surfacing conditions, which significantly improved following the surfacing
program’s completion. While some areas remained red on the thematic map, further examination revealed that most corresponded to road crossings, where surfacing is typically limited. By using visualization tools, railroads can differentiate between spot surfacing treatments, which raises isolated low spots to prevent deterioration—and out-of-surfacing, which involves raising the entire track to a new uniform height after reballasting.
The FRA’s Transportation Technology Center (TTC), operated by ENSCO, provides a scalable environment for validating and improving track geometry forecasting models without impacting revenue service operations. The High Tonnage Loop (HTL) at TTC allows researchers to study track deterioration under accelerated conditions, simulating the impact of heavy freight traffic with daily accumulations of one million gross tons (MGT) of traffic. This unique setting also enables controlled experiments on moisture conditions and their effects on track geometry.
To enhance track maintenance logistics, TTC will soon implement ENSCO’s Automated Maintenance Advisor (AMA). While Class I railroads and transit systems operate on a much larger scale, the fundamental goal remains the same which is identifying potential issues early to prevent failures and extend asset life. By leveraging AI-driven maintenance recommendations, AMA will assist in planning timely interventions, preventing further degradation before conditions become critical.
With TTC’s key tracks in continuous use, minimizing downtime is essential. The integration of AI and automation enables more efficient maintenance planning while ensuring safe, uninterrupted operations—advancing both the science and practice of railway asset management.
For more information on how TTC supports research, testing, and development for the rail industry, visit ttc-ensco.com
JOE DALOISIO Chairman, National Railroad Construction and Maintenance Association (NRC)
January 23, 2025, marked some noteworthy firsts. I had the privilege of testifying for the first time before Members of Congress in a congressional hearing. It also was the first time in the NRC’s history that a chairman or any NRC official has testified before Congress.
OUR WORK CONTINUES ON MAY 7 WHEN WE TAKE OUR CASE TO WASHINGTON FOR THE NEXT RAILROAD DAY ON THE HILL. YOUR VOICE IS VITALLY IMPORTANT.
It was truly an honor and one of the most memorable experiences of my life. I delivered a five-minute statement and answered questions from Members throughout the hearing before the Railroads, Pipelines, and Hazardous Materials Subcommittee of the House Transportation & Infrastructure (T&I) Committee. The hearing – entitled “America Builds: Examining America’s Freight and Passenger Rail Network” – featured testimony from four rail industry stakeholders about their priorities for the new Congress and current and potential transportation legislation.
I’ve been to Capitol Hill and met with Members of Congress before as part of Railroad Day on the Hill and our NRC fly-ins, but this was an entirely different experience that was humbling, a bit intimidating, and exciting. The other witnesses sat at a desk facing subcommittee members in stadium-like, tiered seating looking down at us, surrounded by CSPAN cameras, microphones and photographers, and staff scurrying around added to the experience.
I took the responsibility of representing the opinions and experiences of NRC member contractors and suppliers very seriously. Despite my lack of experience in this situation and limited time, the voice of NRC members took center stage.
Safety is always our top concern, so I made a case for allowing railroads, rail contractors and suppliers the ability to innovate and deploy new safety technologies. “We urge Congress to use data-driven solutions that would effectively increase the safety of the rail network and avoid policy changes that would place unnecessary or excessive mandates on the rail industry that would not enhance rail safety.”
I urged lawmakers to improve the efficiency of CRISI and other grant programs. “The speed at which grant agreements have been executed has been way too slow. By the time the construction phase begins, a number of variables, most notably the increase in costs, jeopardizes the successful
execution of these important projects. We encourage Congress and the new Administration to deliver grant funding in a responsible but more expedient manner.”
I also stressed the importance of a competitive bidding process in rail construction and maintenance contracts to get the best return on these investments. “The NRC strongly supports increased opportunities for contracting out and competition within these programs to stretch federal funds further. Increased flexibility for railroads and commuter rail agencies to contract out work will benefit the industry. This is not an attempt to take work from in-house labor forces, rather it is intended to help the industry as a whole perform more work more efficiently.”
NRC members are always striving to find the most innovative ideas and methods to deliver projects at less cost without compromising safety. “Our member companies are both specialized in and incentivized to accomplish this on a daily basis. Therefore, we would like to strongly urge that all rail construction and maintenance work performed with federal assistance be competitively bid out to the independent railroad construction industry, to the fullest extent possible, to ensure the most efficient use of taxpayer dollars.”
This opportunity to testify before Congress came as a result of years of work and persistence by NRC staff and our own members. I am particularly grateful to Matt Ginsberg, who leads the NRC’s government relations. Matt’s ongoing relationships on the Hill, along with those by NRC President Ashley Wieland, positioned the NRC as a credible resource for realworld perspectives on rail-related legislation. Their efforts were bolstered by scores of NRC members who participated in Railroad Day on the Hill and held grassroots events at their facilities and jobsites over the years.
Our work continues on May 7 when we take our case to Washington for the next Railroad Day on the Hill. Your voice is vitally important. Please join us and help us take advantage of every opportunity to get our seat at the table.
“We aren’t just in this industry. We are this industry!”
By Jennifer McLawhorn, Managing Editor
As we make our way into spring 2025 and turn our attention to rail projects in a future issue, we decided to take a look at engineering firms that play a role in the early formation of such projects. Railway Track & Structures asked what various engineering firms believe the future of the industry holds. Highlighting the emergence of “megaprojects,” navigating generational and technological gaps, and investing in people were some of the outlooks provided. What follows is a special report on the future of rail engineering from leaders of top engineering firms in North America.
By Bill Hjelholt, Global Freight Rail Director, Senior Vice President, HDR
When you serve the railroads, everything starts with safety.
The industry’s safety culture and reduction of incident rates tells a great story of self-directed safety improvement. As railroads invest more every year in safety technology that goes far beyond regulatory requirements, there’s an opportunity for rulemaking and policy to incorporate the benefits of new technologies and innovation, such as autonomous inspection. At HDR, we developed our own FRA-approved Roadway Worker Protection training so that we can safely and quickly mobilize any of our specialists when called upon to help a railroad client. The industrywide focus on enhancing service and market share is prompting reflection on the limits of operating ratio as the key performance metric. There is a priority on enhancing reliability and interconnectivity to better serve shippers. It’s encouraging to see the Surface Transportation Board’s recent support to streamline smaller acquisitions that improve connectivity and service. As the industry continues to refine itself to meet market demands, we see cases where Class Is are selling track segments to short lines to improve agility in handling local traffic. In other scenarios, Class Is are acquiring short lines, so the national rail network benefits with
improved rail connections across regions. The historically bipartisan support of U.S. federal grant programs, such as CRISI and RCE, is a key driver for continued safety and efficiency across the rail network. HDR will continue to partner with communities, railroads and shippers, as we assist regulatory approvals from the STB and identify and plan railroad projects that provide socioeconomic benefits and garner FRA support. To be successful in the everaccelerating speed-to-market race in which consumers seek to optimize delivery from the supply chain network, railroads are prioritizing service reliability with each movement across their network. There’s a tremendous opportunity for railroads to capitalize on their inherent advantages to grow market share with intermodal traffic. A single intermodal train removes over 300 trucks from congested roadways and reduces fossil fuel consumption by up to 75% in the process. HDR is helping railroads capitalize on these advantages with permitting strategies that reduce approval timelines in the complex regulatory environment. While railroads must focus on their daily mission of safe and efficient freight movement, they are also finding time for focus on long-term strategies. Industry leaders are proving that when sustainability is properly executed, it reduces the total cost of infrastructure ownership. It is just good
business. Railroad’s carbon emissions per ton-mile are also the lowest among all surface transport modes, but this is not stopping them from investing in alternative fuels, batteryelectric locomotives, and yard equipment. HDR’s Regenerative Rail program is advising the industry and its regulators on the opportunities and challenges of alternative fuels and electrification as they seek to further decarbonize operations. In the immediate future, navigating a reset of international trade with a minimum of supply chain disruption will be a shared interest between railroads, shippers, and suppliers. We feel confident that worthy projects will see continued investment, from the private sector and federal and state governments. This sentiment is embodied in the ASLRRA’s advocacy efforts for its 600-member railroads and continued emphasis to modernize the 45G tax credit. In this dynamic environment, we believe railroad industry decisions will be guided in large part by return on invested capital. HDR sees a bright future for the industry as we continue to make investments in our people and new technologies. These will enable us to help railroads reduce net investments by teaming with funding partners, reduce the total cost of ownership with smart designs, and enhance revenue streams by accelerating project delivery.
By Mark Fialkowski, President of Infrastructure North America, Parsons
The rail industry has always been an exciting ride; at Parsons, we continuously evolve alongside it. As procurement models change, the delivery partner model has gained particular traction, reshaping how large-scale rail projects are conceived and executed. This shift is evident in our work on major infrastructure projects covering a wide range of rail systems.
In February 2024, Parsons was selected as part of a joint venture to serve as the delivery partner for the $16 billion Hudson Tunnel Project, the most urgent infrastructure project in the U.S. today. This marks our first major delivery partnership in the country, and we’re thrilled to contribute to such a high-profile endeavor. Just before the New Year, we were also selected as part of a team working on the $7 billion Austin Light Rail project, further solidifying our role as a leader in alternative delivery models.
These projects represent a growing trend: the emergence of “megaprojects” in the U.S., similar to those we’ve delivered in the Middle East. These massive undertakings require significant coordination between multiple stakeholders, including agencies, contractors, and designers, to complete them successfully. Whether we are the lead program manager or engineer of record on these and other complex projects, we remain committed to ensuring smooth collaboration and reducing risks. Our focus on minimizing change orders, improving scheduling, and providing greater cost certainty is critical in delivering successful outcomes in today’s dynamic rail environment.
As the rail sector evolves, so does the technology that drives it. One of our key contributions to the industry has been in the area of train control. We’ve come a long way since the introduction of communications-based train control (CBTC) in the late 1990s, a system in which Parsons has played a pivotal role. Today, CBTC is widely recognized as a best practice in train control, and we continue to assist agencies in implementing and upgrading their systems to optimize operational efficiency and safety. Our expertise in this area ensures that agencies stay at the forefront of technological advancements
while improving the passenger experience and reducing operational costs.
Looking ahead, Parsons is poised to play an integral role in the next wave of transformative rail projects. We are leveraging our global experience to help bring highspeed rail to the U.S., tapping into decades of experience in delivering cutting-edge infrastructure. With our background in cybersecurity for the U.S. Federal Government, we are uniquely positioned to help safeguard critical rail infrastructure against
evolving cyber threats. We remain focused on one overarching goal: delivering exceptional value to our clients and stakeholders, no matter the scale or complexity of the project. From rail electrification and advanced signaling to the latest in datadriven solutions, we are committed to shaping the future of rail by providing innovative, reliable, and sustainable solutions. At Parsons, we don’t just deliver rail systems; we are driving the future of transportation forward.
By Kendall Koff, President & Chief Executive Officer, RailPros
Alook at the rail industry today can easily lead us back to the timeless goals of efficiency, safety, and growth that one hears about at every industry event and from every railroad CEO. As a life-long rail professional, I agree with the focus and the passion for achievement in these areas. However, my thoughts also turn to how to find the success we seek
in a changing environment. I would like to share a perspective on what we at RailPros describe as a person-centric culture. This brings together everything we do, however, for this article, I will focus on two key items: generations in the workforce and technology.
It begins with people. The generations in the workforce today create a remarkable opportunity for success:
1. Generational diversity in the workforce – In 2025, there are four generations represented in the workforce: Baby Boomers, Generation X, Millennials, and Gen Z. Some of us have straddled the divide between analog and digital, learning new technological tools as they come into existence. But for others, smart devices and the internet have always been the norm. Companies can leverage the experience of the most tenured team members and capitalize on the younger generations’ new, fresh ideas and perspectives to longstanding challenges. Learning how to best communicate across generational lines and balancing the new with the old is an essential item for all companies in our industry.
2. Technology – There is more computing power in your smartphone than NASA
had in the supercomputer that sent the Apollo missions to the moon. This means there are more ways to streamline, simplify, and automate pieces of the work we do than ever before. Technology can help us run scenarios, adjust the design, and predict outcomes in ways that are more efficient than calculating by hand. As exciting as it can be to become an “early adopter” for new software/programs/ platforms, our industry relies on safety first. Proper vetting, training, and testing must be done before utilizing something new.
At RailPros, we pair junior employees with more senior staff and encourage a two-way flow of information. This helps us to smooth out those generational gaps and align our teams, which, in turn, allows us to work more efficiently for our clients. We also have an IT steering committee that serves as our ‘checks and balances’ before we go live with the latest and greatest. This helps us ensure we’ve looked at a tool from all sides before we begin to use it for our own initiatives and eventually for those of our clients. In leveraging this multigenerational workforce and adopting relevant new technology, I am confident that the rail industry will continue to grow and thrive.
By Jerry Jannetti, PE, Senior Vice President and U.S. Transportation and Infrastructure Executive, WSP
Shortly after the New York Subway’s inaugural trip in 1904, Chief Engineer William Barclay Parsons and third rail co-inventor Henry Brinckerhoff partnered, forming a relationship that ultimately contributed to major transit and rail projects, including every New York Subway expansion. Third rail technology is still used in many systems worldwide. Their collaboration laid the foundation for WSP, a leading engineering, environment and professional services firm, that has designed and delivered rail systems, stations and terminals for over 120 years. Today, WSP is contributing to 346 transit and rail projects across the U.S., including:
• The Los Angeles County Metropolitan
Transportation Authority’s Southeast Gateway Line, a 14.5-mile, ninestation light rail transit line that will connect downtown Los Angeles to the City of Artesia. WSP is the lead environmental and design consultant.
• T he Purple Line Light Rail, a Maryland Department of Transportation/ Maryland Transit Administration 16-mile light rail transit project north of Washington, D.C. WSP provides program management as part of the Purple Line Transit Partners joint venture.
• T he Frederick Douglass Tunnel Program, a 1.4-mile Amtrak tunnel connecting Baltimore to Washington, D.C., replacing a frequently bottlenecked 150-year-old tunnel.
The WSP-Parsons Joint Venture is providing engineering and design services through final design.
• T he Hudson Tunnel project, centerpiece of the Gateway Program. Two new rail tunnels connecting New York and New Jersey will provide resilience during extreme flooding events. WSP is providing engineering support for the environmental impact statement and preliminary engineering design services. Project funding remains a hurdle. Where the U.S. has spent billions on rail initiatives in recent years, however, European nations have spent trillions. Keeping up requires U.S. agencies to secure creative revenue sources and continue pioneering industry advances. Forging partnerships with firms like WSP has helped clients secure more than $53.7 billion in transportation grants since 2009, including $30.5 billion from the Federal Transit Administration and $15 billion from the Federal Railroad Administration. In addition, WSP has
PRESENTING SPONSOR FOR PRINCIPLES COURSE
secured grants totaling $25.1 billion since 2022 through the Bipartisan Infrastructure Law.
The ever-increasing value of data may provide another source of revenue. Evaluating effective ways agencies can monetize cumulative data while ensuring individual privacy will be critical in coming years.
THE RAIL INDUSTRY IS RIPE FOR INNOVATION IT HASN’T SEEN SINCE THOSE EARLY NEW YORK SUBWAY DAYS.
Adopting new technology, such as generative artificial intelligence, and encouraging innovation can dramatically advance rail reliability, safety and operational efficiency. WSP prioritizes
AI and its potential to evaluate data, which will lead to safer, more efficient networks. Driverless train initiatives using autonomous vehicle systems has become a global trend. In partnership with tech organizations, WSP led a ground-breaking pilot of autonomous freight trains aiming to revolutionize short-distance transportation from industrial sites in Finland.
We work closely with industry trailblazers to develop energy-efficient fleets that incorporate biofuel, battery technology and hydrogen fuel-cell technology that reduce emissions and improve sustainability. When U.S. transportation leaders see innovation and progress on rail projects around the world, they wonder when these advances are coming to their local network. At a firm involved with many of those global projects, I tell them we can start right away. The rail industry is ripe for innovation it hasn’t seen since those early New York Subway days, and WSP has the talent ready to usher in those transformations.
The Educational Railroading Conference Leader Since 1994
The Principles of Wheel/Rail Interaction: Revitalized and reimagined with a tighter focus on practical application for 2025, The Principles of Wheel/Rail Interaction, is an intensive, full-day course covering the fundamental aspects of wheel/rail and vehicle/ track interaction.
The course will begin with a case study — an examination of an actual wheel/rail interaction-related derailment. Presenters will cover the primary aspects of track, vehicle suspension systems, wheel/rail contact, the dynamics of vehicle/track interaction, damage mechanisms, friction management, and vehicle and track measurements systems — all the topics we have traditionally covered — but will also connect the dots between theory and what actually happens in the field. A wrap-up session will review the causes attributed to the case study derailment in light of the Principles examined throughout the course.
We will also look at approaches that can be taken to mitigate wheel/ rail- and vehicle/track-related derailments in the future.
Register at www.wheel-rail-seminars.com
Questions? Contact Brandon Koenig, Director of Operations
847-808-1818 or email at brandon@wheel-rail-seminars.com
PRESENTING SPONSOR FOR HEAVY HAUL
The Heavy Haul Seminar is devoted to examining wheel/rail, vehicle/track interaction on rail freight systems. The Seminar brings together track and mechanical users, researchers and suppliers in a positive, educational setting like no other in the industry. Information on where and how the latest technology is being used to improve wheel/rail interaction and overall performance on freight railways is presented through a combination of seminar sessions, dedicated Q&A periods, and technical “InfoZone” sessions.
Topics will include:
• Mitigating Derailment Risk at Switch Points and Guard Rails
• CPKC’s Track Geometry Program: Making the most of Automated Track Inspection Data
• Risk Management in Train Marshalling Through Real Data Analysis
• Technologies used to validate air brake, safety and maintenance exemptions at CPKC
• Assessing the Effect of Total Friction Management on Legacy KCS Rail Wear
By Tim Rock, President & Chief Operating Officer, Gannett Fleming TranSystems
For decades, rail has been the backbone of North America’s supply chain and urban mobility. But maintaining that position requires more than investment — it demands a smarter, more connected approach to infrastructure modernization, one that maximizes efficiency, minimizes risk, and builds for long-term resilience.
The challenges facing our industry today aren’t abstract — they are here, now, impacting our clients, our communities, and the future of transportation. Whether it’s the need to rehabilitate aging corridors, integrate new technology, or expand capacity to meet rising demand, the rail sector must find new ways to deliver projects faster, with greater precision, and with long-term
sustainability in mind. At Gannett Fleming TranSystems, we’re focused on doing exactly that.
The recent Gannett Fleming TranSystems merger was never about getting bigger. It’s about getting stronger, more agile, and more effective.
For decades, both firms have been recognized as leaders in rail, transit, and infrastructure solutions. Now, we’re building on that foundation by streamlining operations, improving technical collaboration, and enhancing project delivery. We’re not just a larger firm — we’re a smarter, more responsive partner to our clients.
Take rail network modernization. The
Racine Railroad Products’ cutting edge operator control interface and computerized automation not only increases production, it also improves safety while making our machines easier to operate and maintain the equipment. We offer a wide-range of innovative powered portable hand tools.
days of relying on fragmented data and siloed decision-making are behind us. Clients need a more connected, insightdriven approach to project delivery. That’s why we’re integrating building information modeling (BIM) and geographic information systems (GIS) into our workflows, creating a real-time, visualized understanding of complex rail corridors. These tools aren’t just about efficiency — they bring clarity to decision-making, minimize risk, and allow rail owners to anticipate challenges before they become costly issues.
The same principles apply to asset management and maintenance planning. Instead of traditional inspection cycles that rely on historical data, we’re helping clients adopt data-driven predictive maintenance strategies informed by digital twins and reality capture. This shift doesn’t just improve reliability — it maximizes infrastructure lifespan and ensures that capital investments are targeted where they’ll have the greatest long-term impact.
I’ve seen firsthand that success in this industry isn’t just about technical expertise — it’s about vision, integrity, and execution. These are foundational principles I believe in, and they guide how we operate every day:
1.
The strongest firms invest in their people. The best organizations don’t just attract top talent — they develop it. That’s why we emphasize mentorship, hands-on leadership, and career growth. When we invest in our teams, we invest in the future of rail.
Clients don’t need more talk; they need real solutions that work. Whether it’s a freight capacity expansion or a passenger rail upgrade, they trust us to deliver on time and on budget. That trust is built through reliability, transparency, and the highest standards of performance.
3. Leading by Doing
Leadership isn’t about words — it’s about action. If we want to see real progress in rail and transit, we have to step
up, drive innovation, and push for smart policies and infrastructure investments. That’s the kind of leadership I believe in, and it’s the approach we take as a firm.
Where We Go From Here
Every project we work on — whether a major rail expansion or a critical infrastructure upgrade— has lasting consequences. It shapes how people move, how goods flow, and how economies grow. That’s why we take a stakeholder-first approach, ensuring that today’s decisions create infrastructure that is adaptable, resilient, and built for the long haul.
At Gannett Fleming TranSystems, we’re not just preparing for the future of rail — we’re shaping it. Long-term success in this industry depends on more than technology and investment. It requires clear vision, decisive action, and a willingness to challenge the status quo. The firms that lead will be the ones that understand where the industry is headed and act with purpose —ensuring that the infrastructure we build today drives progress for decades to come.
by Jeff Tuzik
Corina Moore is an agent of change. A champion of embracing change, too. Her transformative tenure as Ontario Northland’s Chief Operating Officer (2010 – 2014) and President and CEO (2014 – 2022) saw the railway emerge from divestment, deep financial woes, and an uncertain future to a thriving commercially driven organization known for being data-driven, customercentric, and financially sustainable. In addition to refocusing the railway
on revenue growth and performance metrics, she attributes much of her success at Ontario Northland to fostering a culture of embracing change, of questioning the status quo, and one of diversity and inclusion.
In her keynote address at the 2024 Wheel Rail Interaction conference, Moore, who is currently Executive Vice President of Transportation and Infrastructure at WSP Canada, explained how she worked to transform the organizational culture of Ontario Northland
and how the changes she helped effect there can be implemented elsewhere in the industry.
It’s a story she’d told in part at WRI 2018, where she had a room full of railway engineering types nodding their heads in acquiescence to her approach to proactively changing the culture in an industry that is not known for its ability to change. Her efforts in transforming, revitalizing, and expanding Ontario Northland earned her respect and acclaim throughout the Canadian
and North American railroad industry. Also in 2018, she was the first woman appointed to the Railway Association of Canada’s Board of Directors in its 100-year history. The League of Railway Women named her North America’s Outstanding Woman of the Year. Identified by Railway Age in 2017 as one of 10 visionary women in the North American rail industry, she was the first woman to appear on the cover of Railway Age since its inception in 1856. Industry consensus is that she knows what she’s talking about.
Moore acknowledges that change can be hard. New technologies and processes — especially those that have the potential to disrupt the status quo — are much easier to talk about than they are to implement. As a result, many innovations simply stall and go un- or underused due to structural and cultural barriers in the organization, she said.
“The railroad industry is known for being resistant to change,” she said. This gradual calcification stands in stark contrast to the origins of North
America’s great railways. When these organizations were young, they were at the forefront of a changing world. They were innovative, creative, and they were on the cutting edge of technological advances, she said. Over time this spirit faded; “until recently, processes and technologies stagnated.” Before Moore’s transformation of Ontario Northland, there were systems and processes that had been in place, unchanged, for five generations of employees – more than 100 years.
The common mantra: “we’ve always done it this way” is often used to justify outdated and inefficient practices, but it’s also a trap that prevents progress, Moore said; “this is why it’s so important to cultivate a culture of continuous improvement, of challenging the status quo.”
How is the culture of an organization defined? How is it experienced? First, it includes the outwardly facing aspects like policies and procedures, mission and vision statements, dress and protocol, and the nominal ways in which things are done. “These are the company statements about respect and empowerment that hang on the wall.” Moore said, “They don’t tell the full story. They aren’t what drives the success or failure of the business.”
The important part of the culture, the true culture, is largely invisible to the outsider. It includes attitude and emotion, values and beliefs, unwritten rules and traditions, and the way things are actually done and what is genuinely
valued. “These are the things that matter; the things that affect every process and person in the organization, every day,” she said. Despite improvements in recent years, she said, the culture within the railroad industry still lags behind industry contemporaries.
In her time at Ontario Northland and WSP, Moore has developed both a theoretical and a practical understanding of how to bring about cultural change in an industry often resistant to it — it’s not a hands-off process; it’s one that has to be implemented, she said. It starts with leadership fostering an ecosystem that’s conducive to, and inspires, a mindset of change and innovation. The right culture also instills the importance of caring about employees and listening to their input. There are three components in this ecosystem:
• People: Who’s doing it?
• P rocess: How it’s being done.
• Technology: What it’s done with. Stagnation in any one of these can kill an organization, she said. If this is the
top-down view, the individual viewpoint is one of constantly questioning, adjusting, and improving the processes they interact with on a daily basis. “Ontario Northland wasn’t transformed by a single big idea; it was thousands of conversations, suggestions, and tweaks that combined to make the organization stronger both culturally and financially.”
This is atypical of the leadership style often encountered in the railroad industry. Until recently, these organizations tended to fall under a commandand-control style of leadership where influence and authority are entirely dependent on position on the organizational chart, Moore said. Stagnation sets in because this type of leadership misses the fact that ideas that inspire change — process improvements and efficiency gains — can come from anywhere and anyone in the organization; “leadership isn’t about title, it’s about influence,” she said. Effective leadership provides a vision that connects the “how” and the “why” of processes and strategies so
that the people involved in each step feel both engaged and integral.
When people within an organization feel heard and valued, they are more likely to be creative and innovative when they encounter limitations or inefficiencies. And when they see evidence of their influence in organizational processes, they feel empowered to go above and beyond. This, in turn, inspires others to do the same — a positive feedback loop for the organization and everybody in it.
Fostering a sense of community and engagement within the true culture of an organization also means, from a practical standpoint, that leadership can’t be a separate silo, either structurally or culturally. “This means going out to the track, the shop floor, the environment where the work is done, and having real conversations about how the work is done; what works, what doesn’t work,” Moore said. This kind of regular interaction keeps channels of communication open and reinforces a process of iterative
improvement. The practical experience of people on the front line is critical to help define and implement the kinds of systemic and process changes that affect the entire organization, she said.
Another part of true culture, one often overlooked, Moore said, is the demographic makeup of the organization itself. “Too often, we [as an industry] think of diversity as just an HR policy or box to check-off, and we forget the inclusion part — which means that people feel heard and a sense of belonging,” she said. Gender balance and diversity are not mere buzzwords but rather intrinsic components of an innovative and creative culture. “People who are “different” (gender, age, race, experience, etc.) bring different perspectives to the table; perspectives that lead to enhanced customer service, engineering designs that have improved constructability and usability, and forward-thinking ideas that were inspired by diverse viewpoints. Organizations that have diversity and
inclusion as a cornerstone of their culture have a competitive advantage.”
Moore recounted an event that occurred shortly after she became CEO of Ontario Northland in which a coworker remarked that employees would now have to talk about “their emotions” on account of the CEO being a woman. “I took this as an opportunity though,” Moore said. “Emotions are a huge part of the culture; they’re a huge part of the business. When we talk about ‘emotion,’ we’re talking about morale, motivation, productivity.” Regardless of an individual’s place on the org chart, fostering a culture of caring and support in addition to accountability among their peers will make the organization stronger, “and you’ll see the results on the bottom line,” she said.
There are also tangible, demonstrable benefits to making diversity and inclusion part of the culture — an issue that Moore previously raised at WRI 2018 and remains relevant. The railway industry skews largely male. When Moore
joined Ontario Northland, only 8% of the workforce was female — a figure in keeping with the industry at the time, she said. By the time she left, 23% of the workforce was female and 50% at the executive level; productivity and morale were up. “We saw it at Ontario Northland, and we see it across the industry; there’s more revenue, more profit, better safety stats, and better service when we have a more diverse and inclusive workforce.”
This applies to attracting the talent and perspective of a younger demographic as well. This is a talent pool that is facile with the latest technologies, that has new perspectives on how transportation can work, Moore said. These qualities can be a valuable complement to the institutional knowledge and experience that industry veterans bring to the table. This can be a particularly difficult barrier to breach. Traditionalism and the status quo are powerful forces that often
lead to gatekeeping and rigidity, creating a culture in which new approaches (and people) are met with entrenched resistance, even hostility. A big part of why changing this culture is critical to the health of the industry, Moore said, is that new generations of (potential) employees largely hold the keys to technologies that will carry the industry into the future. This talent is lost if they bounce off the organizational culture.
Moore recalled one time at Ontario Northland in which a 35-year veteran shop technician worked with a recent college graduate to automate a process that hadn’t otherwise changed since the railroad’s inception.
This atmosphere of collaboration didn’t happen organically, however; it took a great deal of effort to create an environment in which disparate, traditionally siloed groups were comfortable working together, she said. “In the past, this kind of thing didn’t happen. There was no trust. We’d end up butting
heads with the union who would dig in and resist any change.” But when these groups came together, young/old, union/ non-union, and communicated with honesty, the organization saw tangible benefits. “We were collaborating with the common goal of making the organization stronger and more sustainable.”
At WSP, Moore continues to champion a culture of continuous improvement and innovation. The strategies and behaviors necessary to drive this culture require constant focus and a clarity of objectives, she said; “It is a journey, but one that is critical to the long-term success of the organization.”
Jeff Tuzik is Managing Editor of Interface Journal
https://interfacejournal.com/
This article is based on a presentation made at the Wheel Rail Interaction 2024 Heavy Haul conference.
https://wheel-rail-seminars.com/
By Brad Kerchof
Hi-rail and walking inspections and automated track geometry testing — the traditional means of track inspection — provide a wealth of actionable information. But another less-emphasized method of inspection — riding trains and conversing with train crews — can also provide valuable insights.
That was certainly the case for me in 2004 when I rode the head end of a double-stack train from Sheffield, AL to Memphis on Norfolk Southern’s “A” Line. It was late afternoon, well after
quitting time of the local track supervisor and his maintenance gang, when we rolled through Grand Junction, TN, the headquarters town of the Grand Junction subdivision. Standing on the top step of the locomotive’s center stairwell, my face pressed against the windshield, I looked over the short hood and down at the track. At 40 mph, I had a bit more than a second to evaluate a no. 10 turnout, from switch point to frog. In that brief moment I didn’t notice anything unusual. But after the locomotive had passed the frog, an image appeared in my mind: a joint
bar laying face up in the gage of the track, next to the toe block of the spring frog. Did I really see that?, I asked myself. I questioned if a dislodged bar was even possible, given that the joint was secured by five bolts, the line was inspected twice a week, and the turnout was literally 100 feet from the track supervisor’s office. Nah, not possible, I concluded. It was just my imagination, and certainly not worth placing a 10-mph slow order and calling the supervisor.
I stuck with my plan to spend the night at a Memphis motel and report to the
Spring frogs are used in main-track turnouts where the diverging side sees light traffic and slow speeds (typically 10-15 mph). The advantage of a spring frog is that it does not have a flangeway opening on the main line side, which greatly reduces wheel impact (and thus frog maintenance).
Grand Junction headquarters the next morning. Upon arriving, and under the guise of stretching my legs prior to the track gang’s safety meeting, I walked over to the turnout to confirm that the spring frog’s toe block was indeed fully intact. But there it was — the main-line side joint bar laying face up in the gage of the track. After a few “holy s*!#s,” I contacted the dispatcher to place that 10-mph slow order and enlisted the track gang’s help to reassemble the joint. Through the previous night, a half dozen trains had run over this turnout.
Fortunately, the construction of the joint — a tie plate that spanned multiple ties, a toe block that remained in place, and fasteners on adjacent ties still doing their job — had kept the rail ends aligned enough to allow safe passage of those trains and their several thousand wheels.
A learning experience? You bet. And, no, the lesson was not that a joint bar is an optional piece of track material. Rather, I realized that I needed to trust my eyes (as well as the images subsequently displayed in my mind), and to absolutely investigate further.
This lesson squared very well with what I came to understand later in my career. While failures — both material and human — are common, catastrophes resulting from those failures are not inevitable. Just as often as not, infrastructure, equipment, and people will give a hint of a developing problem. We just need to be out on the property, paying attention, to see it.
Brad Kerchof was Division Engineer of NS’s Alabama Division through the 2000s and retired as NS’s Director Research & Tests in Roanoke, VA in 2019.
By David C. Lester, Editor-in-Chief
Just about any ballast maintenance seminar one attends stresses that the key functions of ballast are drainage, drainage, and drainage. This is because water, particularly trapped water, is the enemy of a stable ballast layer. While water drainage is a function of ballast and promotes track stability, it’s also important to remember that drainage is important to maintain the quality of the ballast. This effort enables ballast to serve its other major functions of dispersing wheel loads to the subgrade below and to keep ties in place.
The placement of new ballast used to be a somewhat subjective process, based primarily on visual observations of a track inspector. Today, however, ballast can be automatically placed in the proper location remotely using a system of GPS mapping that has the coordinates of where the ballast should be dropped. Since ballast must be placed in the proper quantity and in the right location, this system has vastly improved the workflow and results of laying new ballast.
There are many aspects of good ballast maintenance that RT&S will address in future articles preceding our semiannual ballast maintenance vendor spotlights. This month, however, two railroads share some
details of their ballast maintenance program.
Genesee & Wyoming, for example, owns multiple railroads of varying traffic loads and lengths around the United States. Since the company acquires new properties periodically, Jeff Watson, Vice President of Engineering says that “a significant challenge at G&W is restoring [ballast that’s been subjected to years of less-than-ideal maintenance] inherited from predecessor owners. We see a wide range of ballast conditions across our properties, ranging from ties buried in fouled ballast that might consist of limestone, slag, and cinders or whatever was locally available [at the time of installation or the last resurfacing] to fully restored or newly constructed granite ballast sections meeting our CWR [continuous welded rail] requirements and accommodating drainage and surfacing required for high tonnage and Class 4 track speed [freight: 60 mph and passenger: 80 mph].”
Watson adds that ballast renewal activities can be done independently or during tie renewal projects. “As we work to establish tie-cycles, we ensure all components within the work limits meet our current standards when the project is complete. This often includes grade crossing renewals, turnout
upgrades, various OTM [other track material] and significant attention to installing a quality ballast section. Major ballast projects often include roadbed repair, production undercutting or shoulder ballast cleaning.”
Nick Lucero, Assistant Director Roadway Planning at BNSF, tells RT&S that “to monitor [ballast] conditions, BNSF employs a combination of track geometry, LiDAR (Light Detection and Ranging), and Ground Penetrating Radar (GPR) technology. Track geometry provides a snapshot of where issues may currently exist and where ballast maintenance may need to be carried out. LiDAR technology offers high-resolution, three-dimensional mapping which allows for precise measurement of the ballast profile and potential impacts to the structure’s drainage capacity.”
Lucero adds that “GPR is used to assess the subsurface condition of the ballast, detecting issues such as fouling or degradation that may not be visible from the surface. Empirical and mechanistic models use data from these technologies to identify areas of concern based on condition and risk to the structure. These models are continually refined and verified through field inspection, which ensures accuracy and reliability.”
By Jennifer McLawhorn, Managing Editor
One of the largest vendor spotlights we focus on at RT&S, ballast maintenance solutions are necessary for ensuring the stability and safety of railway tracks. Over time, ballast can become compacted or contaminated with dirt and other debris, which affects its ability to perform its intended function. Regular maintenance includes cleaning, tamping, and replacement to ensure the track remains properly aligned and supported to prevent track deformation and maintain smooth operations.
Ballast Tools Equipment (BTE) says it “offers a full line of custom-engineered excavators and backhoes, each perfected for hi-rail applications, along with a comprehensive catalog of innovative, specialized work attachments. BTE works directly with Class 1 railroads, short lines, and railroad contractors to assess and address the industry’s most aggressive challenges, from heavy vegetation management to system-wide production tie programs. Those collaborations inform BTE’s innovations—hi-rail solutions that, by design, make difficult maintenance of way work simpler, safer, and more productive. Benefits that MOW crews can only find with BTE include the proprietary Automatic Attachment Recognition system, which makes optimizing machines for multiple attachments seamless and immediate, and BTE Priority Hydraulics, which direct 30% more flow to attachments, maximizing power and control exactly where and when it’s needed.”
Brandt understands that “ballast maintenance is no easy task—it takes power, precision, and the right equipment to keep tracks solid and trains moving. That’s where the Brandt RTB100 & RTB115 Hi-Rail Backhoes come in. Built for the rail, these machines switch from road to track in under three minutes, so you spend less time setting up and more time getting the job done. Their high-flow hydraulics power through ballast work with ease, while a 26’ reach and heavy-duty lift capacity make short work of even the toughest tasks. With automated pressure regulation, durable suspension, and AAR-compliant hi-rail gear, you get rock-solid stability and safety to operate with confidence. When it’s time to move ballast, clear debris, or keep the track in top shape, trust Brandt Hi-Rail Backhoes to work as hard as you do.”
Custom Truck One Source’s “rotary dump body is a game-changer for ballast and material transport on the rail, built with the reliability and innovation the industry demands. The Load King 14 ft, 12-14 Cu Yd elliptical dump body features proportional hydraulics, joystick control, a hinged drop
ladder (street side), along with manual or hydraulic rail dogs. Its integrated rail gear includes hydraulic actuation, front brakes, front rail sweeps, slotted rear links, a heavyduty rear bracket, and manual pins. Every unit undergoes track testing and FRA annual rail gear inspection to ensure top-tier performance. At Custom Truck, we take control of lead times with in-house manufacturing, ensuring faster delivery and unmatched quality. From hi-rail pickups to tandem axle material handlers, our railroad division designs and builds to your exact needs. With over 300 years of industry expertise, Custom Truck is a trusted name for rail solutions—on and off the track.”
For Miner Enterprises, John Arends told RT&S that “stand-alone solar powered AggreGate® outlet gates manufactured by Miner Enterprises enable independent operation of individual railcars anywhere within the ballast train. This eliminates the need for grouping manual and automatic cars, boosting agility and efficiency in MOW operations. Optional remote wireless control systems enable specific car and gate selections for up to 1000 cars. AggreGate outlet gates feature large guillotine door openings designed to stop ballast flow with minimum effort. Single- and double-door controls provide precise ballast shutoff capabilities at switches, crossovers, and bridges. The AggreGate can effectively dump ballast inside, outside, or on both sides of a rail simultaneously. Standard electric, air-powered and manual gate
models, suitable for retrofit and new car builds, are also available. Solar-powered AggreGate systems also include car-mounted work lights for added safety in low visibility and nighttime ballasting. The Miner Lighting System includes four energy efficient LED lights mounted on the railcar’s under-carriage.”
RELAM (Railway Equipment Leasing and Maintenance) has “strategically positioned repair facilities across North America and a wide selection of on-track machinery and hi-rail vehicles. This network enhances your access to affordable, late-model equipment while significantly reducing transportation costs to and from your job sites. RELAM provides Knox Kershaw, Kershaw and Nordco ballast regulators that can also serve as snow fighters, ensuring tracks remain clear in any weather conditions. Current inventory includes the Knox Kershaw regulator series 860, 925, and 940, Kershaw 46-2 and 4600 regulators, along with the Nordco M7 available year-round. Additionally, RELAM offers new, rebuilt, remanufactured, and late-model Harsco 6700 and Mark IV Production Tampers, along with Harsco TS-30 HD and Plasser PTS 90C Track Stabilizers.”
The Knox Kershaw Inc. KBR925 is “engineered for ballast work on all track types. Its integrated plow and wing system transfers ballast from shoulder to shoulder in a single pass, leaving one shoulder perfectly profiled. Equipped with a standard reversing valve, it
can easily clear ballast from switches and grade crossings. The upgraded KBR925 provides a 130-gallon hydraulic tank relocated to the front for improved weight distribution. Its sloped fuel tanks with integrated steps enhance cab access, while the ballast wing is designed to use a consistent grader blade throughout for superior efficiency. The KBR925 offers the optional Plus+1® System, which automates key functions for more seamless operations and features a touch screen for monitoring system functions. This system is also available as an option on the KSF 940 and is standard on the KKA1050, KTC1250, and KPB200 models.”
Loram states it “provides a full range of products to ensure effective ballast management. From ballast delivery, to specialty excavation and shoulder ballast cleaning, to complete ballast renewal, Loram has the equipment necessary to support all aspects of ballast maintenance. When high volume ballast delivery is required, Loram’s Dump Train and Dump Train for Curves can deliver 1500 tons of ballast per hour. These machines are designed to efficiently place ballast up to 50 feet from the track centerline in support of washout repairs, track construction, or for stockpiling ahead of planned maintenance. When two machines are paired together, 3000 tons of ballast can be quickly delivered in a single track occupancy window. For improving drainage around specialty trackwork, in tunnels and on bridges, the LRV Excavator is the preferred equipment. Using a combination of up to 500 HP of vacuum power and 5,000 pounds of nozzle force, the LRV excavator can excavate anywhere up to 15 feet from track centerline down to 5 feet below top of rail. The LRV Excavator is one of the most versatile machines in the fleet, and railroads continue to find new uses for its combination of excavating power and nozzle flexibility. For tracks needing preventative maintenance, Loram’s fleet of Shoulder Ballast Cleaners (SBC) can excavate the complete shoulder section, screen the ballast, and return the good ballast in a single pass. Trains can operate at track speed immediately after shoulder ballast cleaning. The SBC can excavate and screen up to 1500 cubic yards of fouled ballast per hour. In severely fouled locations, these machines can be operated as “waste only” and will bypass the screens and discharge the ballast excavated into a towed material handling car or the right of way.”
Plasser American’s “fleet of machines work together to improve track conditions and heighten efficiency during both regular operation and while performing regular maintenance. Everything from ballast bed cleaning, ballast distribution, shoulder cleaning,
The Pl as ser h e avy-duty, high speed, continuous action switch and pro duc tion track ta mping machine 0 9 - 2 X D Y N A C AT is capable of ta mping one or t wo ties at a time wi t h an integrated dynamic track stabi lize r Ta mping and lifting units are mounted on a separate satellite fra me attached to the main frame. While the satellite indexes two ties duri ng the act ua l work p roc ess (lif tin g , l inin g , cross-leveling, and tamping), the machine ’s main frame with stabilizer system move s s moothly and continuously. Equipped with AGGS, ATLAS, PLC CAN bus control sys te m, and its unique design and construction allows the 09-2 X D YNAC AT to achieve production rates of up to 4,200 feet per hou r.
stabilization, and tamping, Plasser American has the machine to get the job done safely, efficiently, and quickly. Ballast cleaning machines with different performances fulfill the individual requirements in North America. Smaller Ballast Cleaning Machines, such as the RM80, are designed for plain track and turnouts with one excavating chain and one screening unit. The RM80’s 50 mph travel speed and short set-up and knock-down times allow maximum utilization of available track time. The RM802,
the biggest undercutter in the U.S., is a highproduction Ballast Undercutting/Cleaning Machine especially designed to work on track with pre-dumped ballast. Production rates of up to 2,000 feet per hour are achievable. Shoulder Cleaning Machines like the FRM85F and FRM802 complement the portfolio, keeping the ballast shoulder free from ballast breakdown, ensuring drainage, and stretching maintenance cycles. Both shoulder and ballast cleaning machines are equipped with one of
two self-levelling shaker boxes that are able to recover a high amount of ballast in tough conditions and offer unbeatable performance. The BDS100/200 Ballast Distribution System is the ideal machine to accompany high-speed surfacing gangs or used alone to reposition existing ballast. The machines are equipped with a hopper unit for ballast storage, conveyors to distribute ballast and a fully adjustable x-type ballast plow, and unique shoulder plows to profile the ballast. The BDS100/200 opens new possibilities to distribute the existing ballast in the network and saves money and important resources. The Plasser 09-2X DYNACAT is a heavy-duty, high-speed, and continuous action switch and production track-tamping machine with an integrated dynamic track stabilizer. While the satellite tamps and indexes two ties at a time during the actual work process, the machine’s main frame, with stabilizer system, moves smoothly and continuously at a speed determined by the operator. This ensures consistent quality throughout the whole tamping section. These machines, coupled with Plasser American’s decades-long proven track record of exemplary
Track Safety Standards Subparts A-F
Track Safety Standards, contains the Track Safety Standards, Subparts A-F, for Classes of track 1-5. The standards cover general information, Roadbed, Track Geometry, Track Structure, Track Appliances and Track-Related Devices, and Inspection. Includes Defect Codes. Updated December 28, 2023
BKTSSAF Track Safety Standards, Subparts A-F $13.95 Only $12.50 for orders of 50 or more!
FRA Part 237 establishes Federal safety requirements for railroad bridges. This rule requires track owners to implement bridge management programs, which include annual inspections of railroad bridges, and to audit the programs. Part 237 also requires track owners to know the safe load capacity of bridges and to conduct special inspections if the weather or other conditions warrant such inspections. Updated December 28, 2023
BKBRIDGE Bridge Safety Standards $14.00 Only $12.60 for orders of 50 or more!
reprint includes the FRA's Railroad Workplace Safety Standards addressing roadway workers and their work environments. These laws cover such things as: personal protective equipment, fall protection, and scaffolding for bridgeworkers; and training issues. Also includes safety standards for on-track roadway vehicles. Updated December 28, 2023.
BKWRK Railroad Workplace Safety $13.95 Only $12.50 for orders of 50 or more!
The Track Safety Standards Calculator is a must for anyone who works on track. This slide rule type calculator contains many of the details for Classes of track 1- 5. Deviation from uniform profile and from zero cross level. Difference in cross level. Compliant with part 213.
BKTCAL Track Calculator $12.50 Only $11.25 for orders of 50 or more!
contracting services, provide the ultimate solution to ballast bed cleaning and track maintenance and are available for purchase and contracting services.”
Rhomberg Sersa Rail Group (RSRG) offers “public and private railroads new and innovative solutions to ballast and trackbed management. RSRG continues to advance its ballast and trackbed maintenance capabilities through innovation in autonomous GPR inspection which supports track safety and maintenance planning in ballast and subgrade maintenance activities and the setting and verification in work quality and overall effectiveness of maintenance activities. As a leader in maintenance services, the company continues to push the boundaries and set new standards for improved utilization of information used to optimize our end-to-end maintenance process and on track delivery, which includes equipment selection, material utilization that delivers improvements in product quality, productivity and the return on investment for our clients.” CCO North America Steve Atherton states, “RSNA’s role is to provide the best in class engineered solution which is measurable by improved track performance, reduced maintenance cycles and the extended overall life of the asset.”
BILL RIEHL AREMA President 2024-2025
In case you missed it, the Railroad Bridge Symposium was held in February at the Dallas/Fort Worth Marriott® Hotel & Golf Club at Champions Circle. The event was designed to provide content on both the technical and practical sides of railway structures management. Thanks to the enthusiastic support of the Sponsors, Planning Team, and Presenters, it really delivered! As previously reported, the event kicked off with a Dallas Area Rapid Transit (DART) field trip and then rolled into two days of intense presentations in two parallel tracks. Of course, the Wednesday evening social was a packed event where everyone could network and share stories of challenges and successes.
What I hadn’t shared in my December article was the combined Structures Functional Group Technical Committee Meetings that were held concurrently with the Symposium. Committees 7 – Timber Structures, 9 – Seismic Design for Railway Structures, 10 – Structures Maintenance & Construction and 15 – Steel Structures met throughout the week. This is the second time the Structures Functional Group got together for concurrent meetings in conjunction with a Symposium. The synergies are obvious when you get the entire functional group together at the same time. From cross-specialty collaboration to reduced travel for members who may be on two committees; the combined meeting provided great value both personally and professionally.
There was another benefit that these committees shared: Complimentary meeting space. Committee 15, in particular, is a large committee that is challenged in finding a large enough venue to host the meeting and
have the necessary breakout space at a reasonable cost. Usually, the attending members have to chip in to help cover meeting costs. By combining their meeting with an event AREMA was already building, their needs were able to be included in the event planning. The key to this success was early communication of needs and frequent updates as the planning continued.
If we measure this combined Symposium and Committee Meetings against the AREMA Strategic Plan, I think the Symposium Planning Team led by Walt Bleser, PE, AREMA Structures Functional Group Vice President, President & CEO with ARE Corporation and Ron Berry, PE, P.Eng., former AREMA Functional Group Director, General Director Structures, BNSF Railway, delivered a clear win. With respect to Knowledge Development, the Symposium delivered excellent content on both the technical engineering and practical execution sides of structures management. Technical Expertise was advanced through the synergies of the combined technical committee meetings. Of course, the Industry Networking opportunities speak for themselves. In the end, this combined Symposium and Committee Meeting exceeded attendance expectations with a record setting 319 Symposium attendees. The bar is now set for the Communication, Signals & Information Technology Functional Group as they start to plan their 2026 Symposium.
One final note I’d like to mention about the Symposium is the Keynote Address: Building Bridges to Better Lives. While not directly railroad bridge related, the address touched on many of the same challenges we have regarding design, budgeting, funding, material procurement, constructability, site access, and execution. Bridges to Prosperity is focused on reducing rural isolation through construction of mainly trail bridges to provide resilient lines of communication between communities. Their focus area is East Africa due to the mix of millions of people living in rural isolation due to impassable rivers, interest from national governments to make investments, and the region’s track record of safety and stability of leadership. An upcoming episode of the AREMA Podcast, Platform Chats, will build upon these topics and explore them further within our industry.
Looking ahead, the next event on the AREMA calendar is the Annual Conference
& Expo in Indianapolis, 14-17 September. You spoke through your survey responses, and we listened, so there will be several changes to the Conference lineup. First, we will move the Keynote address back from Wednesday to Monday’s General Session. Second, we agree that the time allotted for the Emerging Technologies Panel Discussion (Monday) and Tony Hatch’s State of the Industry (Wednesday) required more time and audience participation, and both will be extended to a full hour.
These changes to Monday’s schedule make for a very full schedule. So, for the upcoming Conference, in order to make room for the Keynote Address and the Emerging Technologies Panel, hosted by Walt Bleser (Podcast Host and Structures Functional Group Vice President), we will move to a concurrent session format for the Monday Technical Presentations. These time slots will be one hour instead of the usual 30 minutes in order to provide a deeper dive into these topics, with a combination of longer presentation and greater Q&A time.
As always, all sessions are recorded and as part of the full conference registration, access is provided complimentary On Demand in the Education Portal following the Annual Conference & Expo. By providing On Demand access, participants won’t miss any education and will have more access to all educational content.
The final news I’d like to share is the continuation of the work of the 2024 Sustainability and Resiliency Symposium. That event was a great success, and immediately following the closing remarks, the questions started as to when the next one would be held. Unfortunately, the Engineering Service Functional Group’s next opportunity in the Symposium schedule is 2029, and many would say this is too long to wait given the current interest in the topic. As an interim solution, Committee 13 - Environmental and the University of Illinois Urbana-Champaign (UIUC) proposed a joint event where AREMA joins the 27th Railroad Environmental Conference with a Sustainability and Resiliency Day. This will be held 11-13 November 2025 at UIUC. The call for abstracts is currently open. See https://rrec.railtec.illinois.edu/ call-for-abstracts/ if you are interested in presenting. Registration for the conference will open in the summer.
We appreciate your understanding while working behind the scenes to improve our website with updates to help us serve you better in the future. Thank you for your patience!
Secure your recognition with a booth and sponsorship at the AREMA 2025 Annual Conference & Expo in Indianapolis, IN, September 14-17. Registration will open in the spring. For details and to reserve your spot, visit conference.arema.org.
Is your Library up to date? The 2025 Communications & Signals Manual has over 109 new, revised, reaffirmed, or extended manual
APRIL 17
Committee 12 - Rail Transit Virtual Meeting
APRIL 27-29
Committee 11 - Commuter & Intercity Rail Systems Seattle, WA
APRIL 27-29
Committee 17 - High Speed Rail Systems Seattle, WA
APRIL 29
Committee 30 - Ties and Fasteners Pueblo, CO
APRIL/MAY
Committee 14 - Yards & Terminals Philadelphia, PA
MAY 5-7
Committee 5 - Track Seattle, WA
MAY 13-14
Committee 15 - Steel Structures Lafayette, IN
MAY 15
Committee 12 - Rail Transit Virtual Meeting
parts, so it’s the perfect time to get your copy of the 2025 Manual. Order online now at www.arema.org.
Download the AREMA 365 App for essential rail resources and networking opportunities. Easy access to news, events, and educational materials lets you stay informed and connected to the industry. Download it today by searching for AREMA in your phone’s app store.
If you’re looking for a podcast to binge, listen to AREMA’s Platform Chats . It features guests from every aspect of the railway industry.
Catch up on all four seasons available on all your favorite listening services today.
Leverage the power of your trusted association’s Railway Careers Network to tap into a talent pool of job candidates with the training and education needed for longterm success. Visit www.arema.org/ careers to post your job today.
NOT AN AREMA MEMBER? JOIN TODAY AT WWW.AREMA.ORG
CONNECT WITH AREMA ON SOCIAL MEDIA:
MAY 20
Committtee 9 - Seismic Design for Railway Structures Chicago, IL
MAY 20
Committee 28 - Clearances Fort Worth, TX
MAY 22-23
Committee 8 - Concrete Structures & Foundations Tucson, AZ
MAY 27 -28
Committee 2 - Track Measurement and Assessment Systems Calgary, Alberta, Canada
JUNE 19
Committee 12 - Rail Transit Virtual Meeting
JUNE 27-28
Committee 24 - Education & Professional Development West Point, NY
Join a technical committee
JULY 17
Committee 12 - Rail Transit Virtual Meeting
JULY 30-31
Committee 7 - Timber Structures Overland Park, KS
AUGUST 21
Committee 12 - Rail Transit Virtual Meeting
SEPTEMBER 14
Committee 14 - Yards & Terminals Indianapolis, IN
SEPTEMBER 17-18
Committee 39 - Positive Train Control Indianapolis, IN
NOVEMBER 12
Committee 28 - Clearances Virtual Meeting
Joining a technical committee is the starting point for involvement in the Association and an opportunity for lifelong growth in the industry. AREMA has 30 technical committees covering a broad spectrum of railway engineering specialties. Build your network of contacts, sharpen your leadership skills, learn from other members and maximize your membership investment. If you’re interested in joining a technical committee or sitting in on a meeting as a guest, please contact Alayne Bell at abell@arema.org.
For a complete list of all committee meetings, visit www.arema.org.
Chair: Eric J. Frostestad, PE, Senior Railroad Project Engineer, HDR
1. How did you get started in your career in railway engineering?
I’ve always had an interest in transportation infrastructure construction projects. When I was studying civil engineering at Iowa State University, it became apparent that I would like a career in designing and building transportation infrastructure projects. After college, I worked at an engineering firm designing street and highway projects, and I was contacted by a recruiter, asking me if I would be interested in railroad engineering. I did research and talked to the other firm and accepted the new opportunity. I’m grateful for the opportunity to have worked on many projects in my career from concept through construction.
2. How did you get involved in AREMA and your committee?
One of my mentors at the engineering firm encouraged me to sign up for AREMA and become active in a Committee. After I became an AREMA member, I read through the different Committee descriptions. I selected about four or five Committees that I was interested in and thought I might be able to contribute to. I decided to attend the next meeting of the first Committee on the list which was Committee 1 - Roadway & Ballast and that was as far on the list as I got. Even though I was a young railway engineer with little experience, the members were accepting, and I enjoyed the camaraderie. I could
tell it was a large group of friends. David Becker was the Committee Chair at the time and helped get me involved with one of the Subcommittees.
3. Outside of your job and the hard work you put into AREMA, what are your hobbies?
Traveling with my wife and family. Kathy and I enjoy hiking and exploring National Parks, mountains, and beaches. We’ve been to every US state.
Exercising and playing sports – I played in adult basketball, volleyball, and soccer leagues for several years. I now exercise by running, swimming, and weight training. I’ve participated in the Kansas City
Corporate Challenge almost every year since 1994.
Volunteering/Service – I’m active in my church as an adult youth group leader, attend two men’s groups, and act as support in an addiction recovery program.
I have volunteered at Micah Ministry (started by AREMA Past President Darrell Cantrell and his wife Sharon) by helping feed the homeless and food insecure for several years. I also help lead our church’s dinner which provides dinner and conversation for those less fortunate.
4. Tell us about your family!
My wife Kathy and I have been married for over 30 years. Kathy has enjoyed attending the AREMA Conference’s Spouse/Guest Program for many years. We have three grown children. Kristofer is a pharmacist. Ethan is a civil engineer and is married to Aly who is a physical therapist. Kalyn is a clinical laboratory scientist as is her fiancé Corbin.
5 . If you could share one interesting fact about yourself with the readers of RT&S , what would it be? I was a youth soccer coach for about 15
years as my kids were growing up.
6. What is your biggest achievement?
The opportunity to be the lead track and civil engineer for the Kansas City Junction or Argentine Flyover in Kansas City, Missouri. This project won the Dr. William W. Hay Award for Excellence in 2005. The Hay Award honors innovative railway engineering procedures, projects, and products and the individuals who have created and successfully applied them to the railroad industry. This amazing project touched almost every aspect of railway engineering.
7. What advice would you give to someone pursuing a career in the railway industry?
Become an AREMA member and be involved in a Committee. There is so much knowledge to be obtained by networking with fellow members and to develop friendships. Every railway engineering project is different, it is great to have a network of technical experts that you can call on.
Get PDHs at your Own Pace with AREMA’s On Demand Education
Access to important professional development content is just a few clicks away with AREMA Education. Our On Demand content spans many disciplines of PDH accredited courses that allow you to get your PDHs by learning from experts online without leaving your office.
1. LEARN MORE
Studies show that participants learn more while taking On Demand courses as you can skim through the material you understand and take more time in the more challenging areas.
2. GET INSTANT ACCESS
With AREMA On Demand courses, you don’t have to wait to learn and get your PDHs as they’re available instantly after purchase.
3. CONVENIENT AND FLEXIBLE
Above all things, On Demand education is meant to take at your own pace and on your time. Study from anywhere in the world, whether from your office or the convenience of your sofa.
4. COURSE VARIETY
AREMA On Demand education offers a wide variety of topics for all studies of the railway engineering community.
Register and Start Learning today at www.arema.org.
BECOME A MEMBER AND SAVE
Not an AREMA member? Join today at www.arema.org and get discounts on all AREMA Educational Offerings, from Virtual Conferences to our Webinars.
2400 Enterprise Dr., Independence, KS 67301
Call 620-485-4277 or visit precisionrwy.com for more details
Let Precision remanufacture your non-functional, outdated 6700 into a fully functional 6700 with the latest technology. If you have an old, worn-out 6700 ta m per, we have your solution.
Railway Equipment Company, LLC Re-Manufacturing • Upgrades • Unit Exchange • Leasing Want to see more of our work? Scan the QR code for our YouTube channel. Independence Works!
COMPANY
AREMA
DavRail
Herzog
Hougen Manufacturing, Inc.
Knox Kershaw Inc
Loram Maintenance of Way, Inc
Miner
MxV
Plasser American Corp
Racine Railroad Products, Inc.
Railway Educational Bureau
RELAM Inc
Wheel Rail Seminar
PHONE #
301-459-3200
817-201-0157
816-901-4038
866-245-3745
334-387-5669
763-478-2627
708-220-7137
719-671-8678
757-543-3526
262-637-9681
402-346-4300
770-335-9273
847-808-1818 E-MAIL
jalopez@davmarketing.com amcclain@hrsi.com info@trak-star.com knox@knoxkershaw.com alexis.b.nubbe@loram.com john.arends@arends-inc.com niki_toussaint@aar.com plasseramerican@plausa.com custserv@racinerailroad.com bbrundige@sb-reb.com jroberts@relaminc.com www.wheel-rail-seminars.com
Reader Referral Service
This section has been created solely for the convenience of our readers to facilitate immediate contact with the RAILWAY TRACK & STRUCTURES advertisers in this issue. The Advertisers Index is an editorial feature maintained for the convenience of readers. It is not part of the advertiser contract and RTS assumes no responsibility for the correctness.
MAIN OFFICE
JONATHAN CHALON Publisher (212) 620-7224 jchalon@sbpub.com
AL, KY, TN, CHINA
JONATHAN CHALON (212) 620-7224 jchalon@sbpub.com
CT, DE, DC, FL, GA, ME,MD, MA, NH, NJ, NY, NC, OH, PA,RI, SC, VT, VA, WV, CANADA: QUEBEC AND EAST, ONTARIO
JEROME MARULLO (212) 620-7260 jmarullo@sbpub.com
AR, AK, AZ, CA, CO, IA, ID, IL, IN, KS, LA, MI, MN, MO, MS, MT, NE, NM, ND, NV, OK, OR, SD, TX, UT, WA, WI, WY, CANADA: ALBERTA, BRITISH COLUMBIA, MANITOBA, SASKATCHEWAN HEATHER DISABATO (CHICAGO OFFICE) (312) 683-5026 hdisabato@sbpub.com
AMERICAS, EUROPE, ASIA, AFRICA, AUSTRAL ASIA NORTH AMERICA - CT, DE, DC, FL, GA, ME, MD, MA, NH, NJ, NY, NC, OH, PA, RI, SC, VT, VA, WV, AND EASTERN CANADA. EUROPE EXCEPT GERMANY, AUSTRIA, GERMAN SPEAKING SWITZERLAND, EASTERN EUROPE, ITALY, AND ITALIAN-SPEAKING SWITZERLAND. ASIA EXCEPT JAPAN AND CHINA. JEROME MARULLO (212) 620-7260 jmarullo@sbpub.com
GERMANY, AUSTRIA, GERMAN-SPEAKING SWITZERLAND, LATVIA, LITHUANIA, ESTONIA, POLAND, CZECH REPUBLIC, SLOVAKIA, HUNGARY, SLOVENIA, CROATIA AND SERBIA SIMONE AND SIMON FAHR
Breitenbergstr. 17 Füssen 87629
Germany Tel: +49 8362 5074996 sfahr@railjournal.com
ITALY, ITALIAN-SPEAKING SWITZERLAND
DR. FABIO POTESTA Media Point & Communications SRL Corte Lambruschini Corso Buenos Aires 8 V Piano, Genoa, Italy 16129 +39-10-570-4948
Fax: +39-10-553-0088 info@mediapointsrl.it
JAPAN
KATSUHIRO ISHII
Ace Media Service, Inc. 12-6 4-Chome, Nishiiko, Adachi-Ku Tokyo 121-0824
Japan
+81-3-5691-3335
Fax: +81-3-5691-3336 amkatsu@dream.com
IRJ PRO AND CLASSIFIED ADVERTISING SALES JEROME MARULLO (212) 620-7260 jmarullo@sbpub.com
Key Features and Benets for the Switch & Crossing Panel System:
• Safely removes, transports, and installs all types of switches and crossing panels efciently
• Fully loaded lifting system can turn in any direction while in motion
• Compact size & maneuverability
• Remote controlled
• Single line & multiple track adjustable width