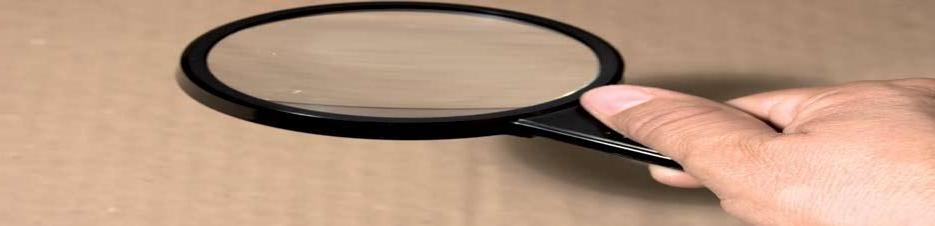
13 minute read
Qué medir en el proceso de corrugado?
20 ¿Qué medir en el proceso de Corrugado?
Por el Ing. Fernando Solera Gerente de Calidad y Servicio Técnico Corrugados Altavista Guácimo, Limón – Costa Rica
Este artículo está dirigido a todas aquellas personas que se están iniciando en el proceso de fabricación de cajas de cartón. El objetivo de este trabajo es colaborar en el aprendizaje de las principales variables que deben ser medidas para asegurar un cartón de calidad, pues al principio de mis labores en este sector muy pocas veces encontré información que me aclarara con detalles lo que necesitaba medir y las tolerancias recomendadas. Es así que basado en mi experiencia y en la recopilación de diferentes fuentes presento este manual.
He dividido el manual en cuatro secciones: (1) Mediciones a través del proceso de corrugado, (2) Medición de las características de calidad del cartón, 3) Cuidados durante el proceso de fabricación de cartón agrícola, y 4) Pruebas finales para la caja terminada.
Si tenemos un proceso confiable, nuestro cartón será de calidad confiable, y como decía mi primer jefe: Lo que no se mide no se puede mejorar.
A. Mediciones del Proceso de Corrugado
1. Desgaste de masas corrugadoras El desgaste de las masas corrugadoras es producto de la abrasividad del papel médium durante la formación de la flauta. Este desgaste provoca de forma paulatina una pérdida de calibre en el cartón corrugado, la cual ocasiona a su vez una pérdida de resistencia en la caja terminada; por lo tanto, se recomienda medir la profundidad de la flauta con precisión y de manera periódica.
Recordemos que el calibre se relaciona con la resistencia, ya que fue determinado mediante experimentación en la fórmula de McKee, la que establece lo siguiente:
BCT= k x ECT x PxC
Donde C es el calibre del cartón, P el perímetro y k una constante.
de Corrugado?
Existen calibradores tipo “carga por resorte”, cuyo estándar Tappi es de 8 lb/ft. El instrumento debe tener una precisión de ± 0.0005 plg.
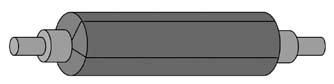
Los valores mínimos de profundidad de flauta son de 139 mils plg en flauta C y 91 mils plg en flauta B. Para hacer la medición, el rodillo debe dividirse en cuadrantes y al menos realizar 5 mediciones en cada uno de ellos. Se recomienda realizar esta medición al menos una vez al mes y colocar el resultado en una gráfica de control de manera que se vaya observando la evolución del desgaste.
2. Paralelismo de los rodillos corrugadores El paralelismo en los rodillos corrugadores debe evaluarse a fin de evitar los siguientes problemas: fracturas o cortes sobre los lados de las estrías, corrugaciones inclinadas, desgaste anormal del rodillo, y de hecho en el uso de presión inútil.
21
Se aconseja realizar la medida de paralelismo durante la instalación y al menos una vez al mes. Una manera de hacer las mediciones es con papel NCR, en cada extremo y al centro del rodillo. Las indicaciones del papel deben ser iguales en espesor y localización. 3. Paralelismo del rodillo engomador vs. rodillo doctor El paralelismo entre el rodillo engomador y el rodillo doctor es de primordial importancia para evitar problemas de combado en el cartón, ya que una abertura desigual provocará mayor paso de adhesivo, lo que viene a generar la famosa “curvatura en S”. Con el uso de galgas debe medirse el paralelismo al menos una vez al mes. 4. Indicador de redondez (TIR) La medición de la redondez es importante para evitar problemas de vibración en los rodillos corrugadores y formación de altos y bajos. Debe realizarse al momento de instalar y al menos dos veces al año. Si los rodillos se levantan más de 0.015 plg, los rodamientos deben cambiarse. Problemas potenciales de insuficiente temperatura generan altos y bajos, ampollas y corrugaciones sueltas. La medición debe realizarse durante la operación con pirómetro de superficie. Si existiera una diferencia de 8 grados o más entre los extremos del rodillo, es probable que el tubo sifón esté quebrado o mal colocado. La temperatura de operación depende de la presión de vapor disponible; la temperatura de la superficie de los rodillos debe exceder ciertos mínimos dependiendo de la velocidad de operación y por consiguiente de la presión de vapor. La temperatura de vapor teórica es como se expresa en las tablas de vapor
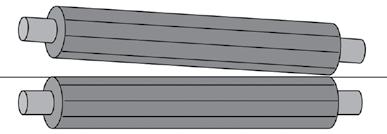
22
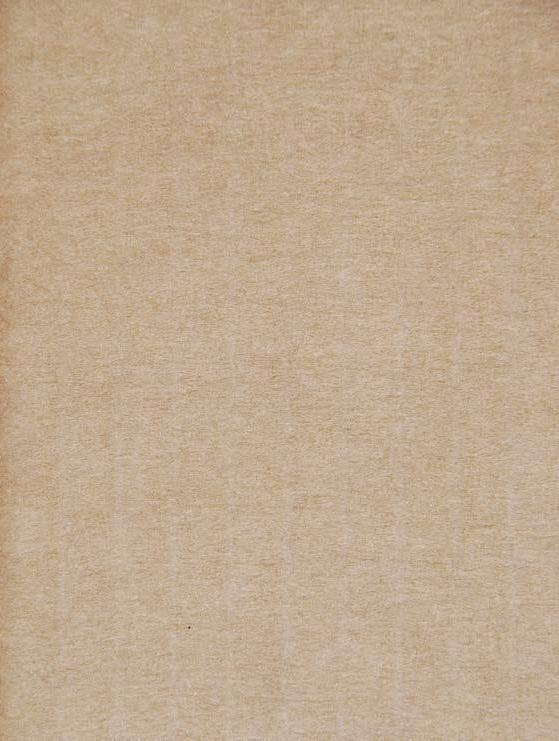
5. Temperaturas de rodillos y planchas calientes
frente a la presión de vapor indicada: La siguiente es la gama de temperaturas de operación preferidas para superficies de rodillos calentados:
Durante la operatividad de la máquina es importante controlar la temperatura en la superficie del papel, pues un exceso de calor provocado por el arropamiento en el rodillo precalentador puede generar un problema de pegado ya que la goma gelatiniza antes de tiempo.
Las siguientes son temperaturas recomendadas para los papeles:
6. Paralelismo del rodillo de presión La presencia de “impresiones” visibles a lo largo de las líneas de goma del cartón de cara sencilla determina si el rodillo de presión está paralelo con el rodillo corrugador. Esta marca deberá ser uniforme a lo largo de su longitud o a través del ancho de la lámina.
Debe revisarse el diámetro del rodillo de presión por un deterioro excesivo. El rodillo debe tener una corona para permitir una carga uniforme durante la operación.
1. Pruebas de Calidad para el Cartón Corrugado a. Calibre
Es una de las propiedades más importantes del cartón corrugado. El bajo calibre provoca pérdida de resistencia en la caja.
El calibre teórico se determina con la siguiente fórmula: CL1 + CL2 + CM + 0.9 x AF
Donde CL1 y CL2 son el calibre de los liners, CM es el calibre del médium, y AF es la altura de la flauta.
En el cabezal corrugador, el calibre puede alterarse también por varios factores:
1) insuficiente calor y vapor del médium 2) deficiente formación de flauta 3) mucha presión en el rodillo de presión 4) aplastamiento de las puntas de la flauta en el rodillo guía. En la mesa de secado también existe peligro de pérdida de calibre al estar las planchas pandeadas o desalineadas. Cualquier área levantada ocasionará que el cartón se deforme y tuerzan las flautas con pérdida de calibre.
Las planchas deben ser limpiadas periódicamente, porque además la suciedad impide la transferencia de calor. Así mismo, las bandas o fieltros deben limpiarse periódicamente.
En la guillotina también puede darse la pérdida de calibre, específicamente en los rodillos alimentadores y en el nicho de los rodillos transportadores.
El calibre debe medirse periódicamente durante el proceso y actuar de manera inmediata cuando se detecta una pérdida. Se recomienda medir cada vez que se cambia el gramaje de un papel y en diferentes posiciones de máquina: lado operador, lado centro y lado transmisión.
b. Resistencia al aplastamiento horizontal (Flat Crush) El flat crush evalúa la resistencia de las flautas en el cartón corrugado a una fuerza aplicada perpendicularmente a la superficie de este, lo que a su vez afecta en
Fuerza de aplastamiento sobre la muestra horizontal del cartón
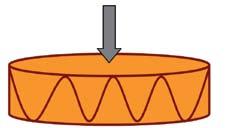
gran manera a la resistencia final a la compresión de la caja de cartón corrugado, por ejemplo durante la transformación del cartón en los procesos de impresión y troquelado.
Esta prueba da una idea de la calidad del corrugado medio o de algún posible daño hecho a las flautas recién formadas.
c. Mullen (Test de estallido) La prueba se efectúa de la misma forma que para una muestra de papel. El corrugado medio no influye en nada para la resistencia al estallido del cartón corrugado.
Este análisis sirve para definir los grados del cartón en las nor-
23
mas de transporte en EE. UU. (se le conoce como la Regla 41); es relativamente insensible a las variaciones en el contenido de humedad como sí sucede con el ECT, se considera una buena medición del comportamiento general en cuanto a resistencia y capacidad de la caja durante el transporte, principalmente en pruebas de caída. Durante el ensayo, se estira una región de forma circular de 1 plg de cartón corrugado mediante una membrana de hule que va formando una ampolla hasta que finalmente revienta el cartón. La presión de reventamiento viene a ser el valor del Mullen. El ECT se define como la fuerza de compresión máxima que una pieza de ensayo soportará sin que se produzca ningún fallo (colapso) en ella. La prueba se aplica sobre una muestra de 2x2 plg, la cual es sujetada por un dispositivo, luego se aplica una carga a velocidad constante hasta que la muestra colapse. El valor obtenido en este ensayo nos ayuda a estimar la resistencia de la caja.
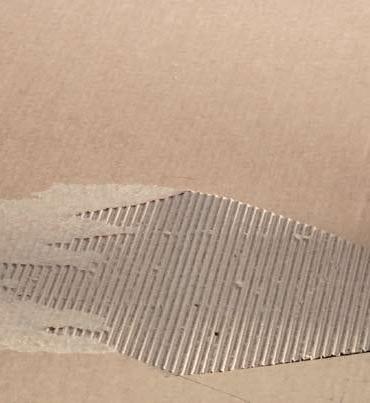
24
d. Resistencia a la com- presión vertical (ECT)
e. Adhesión de pines Esta prueba determina la fuerza necesaria para separar las capas de papel.
En la primera etapa se corta una muestra de 6x2 plg y se inserta un juego de pines entre las flautas. Para flauta B, la muestra debe ser de 4 x ¼ plg.
En la segunda etapa, la estructura formada es sometida a una fuerza de aplastamiento hasta que los pines se separan. La fuerza aplica-
da mide la resistencia de la unión entre los papeles liner y médium.
Los resultados mínimos esperados en esta prueba son de 55 lbf/ft en flauta C y de 65 lbf/ft en flauta B.
C. Controles de Calidad para Fabricación de Cajas Agrícolas
a. Aplicación de impermeabilizante Durante esta etapa es importante considerar el estado de la “rasqueta”; debe evaluarse periódicamente para evitar el paso de líquido por áreas desgastadas, lo que viene a representar un problema de curvatura al final del proceso.
Debe controlarse la mezcla aguaimpermeabilizante y evaluar la aplicación de esta para no caer en excesos, pues podría provocar problemas de pegado principalmente cuando el cliente utiliza adhesivo PVA para el cierre del empaque.
b. Cuidados en la aplica- ción del impermeabilizante
El tanque de dosificación debe permanecer tapado para evitar el ingreso de polvo.
Antes de mezclar el impermeabilizante con el agua, este debe batirse para prevenir el asentamiento de los sólidos.
Debe existir agitación constante en el tanque para evitar la formación de grumos.
c. Uso de la resina en la formulación del adhesivo La resina le confiere al adhesivo dos cualidades: 1) lo preserva de la presencia microbiana, ya que contiene formaldehído, y 2) ayuda a mantener los papeles unidos mientras la caja se mantiene en la cámara refrigerada.
Por esas características es importante asegurarse de que la resina está presente en el adhesivo cada vez que se corrugan cajas agrícolas. Una buena práctica consiste en identificar la presencia de resina y esto se logra con la aplicación de un colorante. Se acostumbra usar rojo 40 grado alimenticio, disolviendo previamente 100 gramos en 1 litro de agua. Este colorante le da al adhesivo un color rosado, siendo esto el indicativo de la presencia de resina.
d. Uso de parafina La parafina es usada en muchas corrugadoras para asegurar el desempeño de la caja en condiciones de alta humedad. La aplicación debe medirse al inicio del proceso y debe estar entre 5 y 7 g/m. Así mismo, debe controlarse la temperatura de la parafina y también el paralelismo del rodillo aplicador.
e. Pruebas de calidad para el cartón agrícola 1. La prueba de yodo Es una prueba de gran importancia y debe ser aplicada no solo para cartón agrícola. Ayuda a
25
26
determinar el grosor de la línea de goma y la continuidad de esta. Va de la mano con la prueba de adhesión de pines. Mediante el uso de una plantilla calibrada es posible medir el grosor de la línea.
Normalmente se trabaja con rangos de 60 a 70 mils plg para cartón normal y de 70 a 80 mils plg para cartón agrícola.
2. Prueba FEFCO 9 Esta prueba permite evaluar la calidad del pegado bajo condiciones extremas.
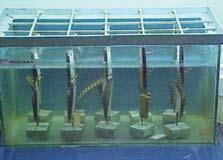
Se rasga una muestra de cartón a la cual se le coloca una pesa de 250 gramos. La muestra debe permanecer sumergida al menos 24 horas sin sufrir rotura. Esto es una garantía de que los papeles no se van a delaminar por efecto de la humedad en la cámara de refrigeración.
3. Prueba de Cobb La prueba de Cobb revela el grado de absorción de humedad del papel liner, tanto en la cara que lleva impermeabilizante como en aquella que no lo lleva.
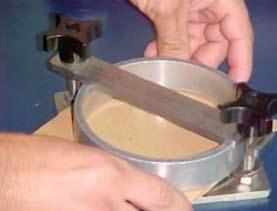
Se coloca una muestra de cartón previamente pesada sobre un dispositivo sujetador, se adicionan 100 ml de agua y se toma tiempo, este puede variar dependiendo de lo que se quiera medir, estos pueden ser de 2, 5 ó 30 minutos.
Al finalizar el tiempo, se elimina el agua y se seca el exceso de humedad, se vuelve a pesar y la diferencia de peso multiplicada x 100 viene a ser el número de Cobb.
Valores aceptables de Cobb para el lado impermeabilizado van de 24 a 28 g/m en un tiempo de 2 minutos. Este valor es bueno para cajas que cierran con adhesivo PVA.
D. Prueba de Calidad para las Cajas Terminadas
1. Resistencia a la fuerza de compresión, BCT La fuerza de compresión de una caja de cartón corrugado es una medición directa de la resistencia al apilado de los embalajes de cartón corrugado.
El método BCT es un ensayo de carga de dirección superior a inferior, comprimiéndose entre placas planas paralelas a una velocidad constante. La fuerza de deformación queda registrada de forma continua hasta el momento en que se produce el fallo de compresión.
La fórmula de McKee establece una relación entre tres variables para determinar la resistencia a la fuerza de compresión. La fórmula establece lo siguiente:
BCT= 5.87 x ECT x PxC
caja y C es el calibre o grosor del cartón. El perímetro es igual a la suma de las longitudes del largo y ancho de la caja: 2 x (L+A).
Durante el transporte, la caja se verá sometida a vibraciones y cargas de choque, por ello existen otras pruebas para medir estos efectos.
2. Vibración Las cajas para embarque se colocan sobre una plataforma, la cual simula el motor de un camión cuando este es encendido. La vibración generada se transmite a las cajas, afectando su desempeño. 3. Pruebas para cargas de choque Existen dos pruebas: prueba de caída y prueba de impacto. Prueba de Impacto Se ensaya el embalaje sobre un plano inclinado de 10° y se hace chocar contra una plataforma. Luego se evalúa el daño del producto en las cajas internas.
Prueba de Caída
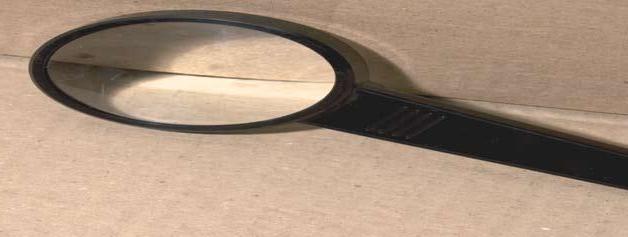
Es muy común que las cajas individuales se golpeen contra el suelo por un mal manejo.
En la prueba de caída se evalúa el daño que sufre el producto interno al

caer la caja en diferentes posiciones.
Fuentes consultadas
1. Hakan Markstrom. Métodos e instrumentos de prueba para el cartón corrugado. 2. Revista MARI Borrad Converting News, marzo-abril 1998 3. Alhu y CRC. Seminario de mantenimiento de rodillos corrugadotes. 4. Brandenburg and Lee. Fundamentals of Packaging Dynamics. 5. Henley y Rosen. Cálculo de balances de material y energía.
27
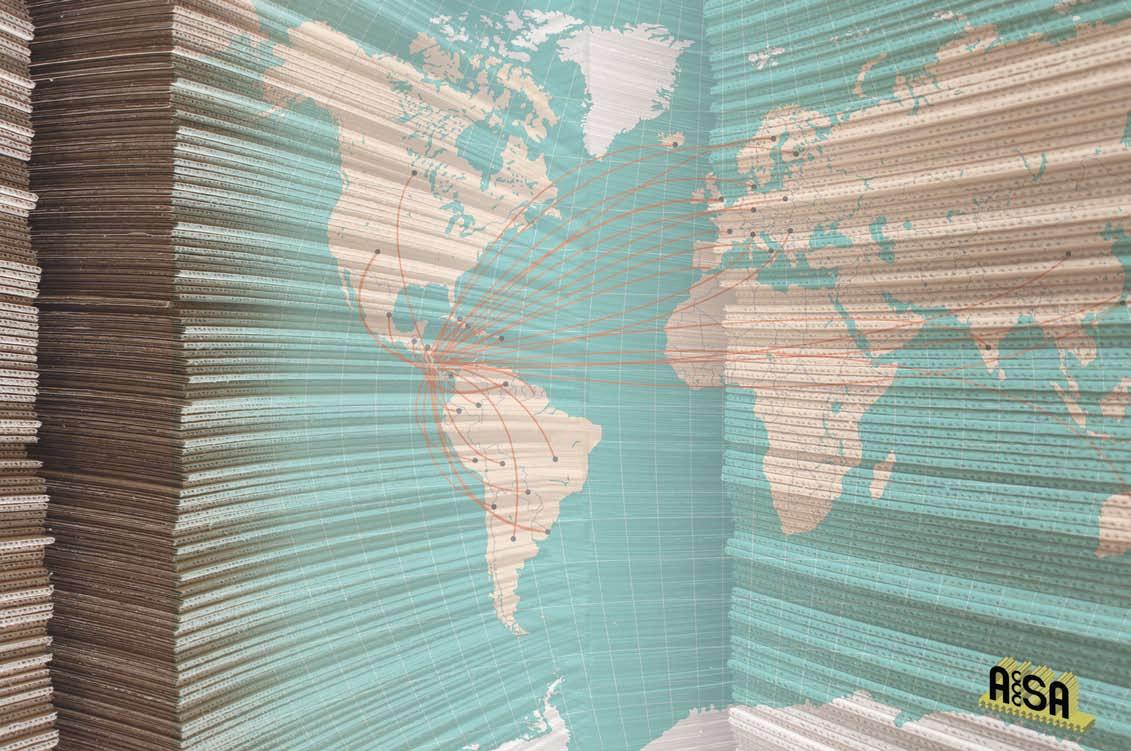
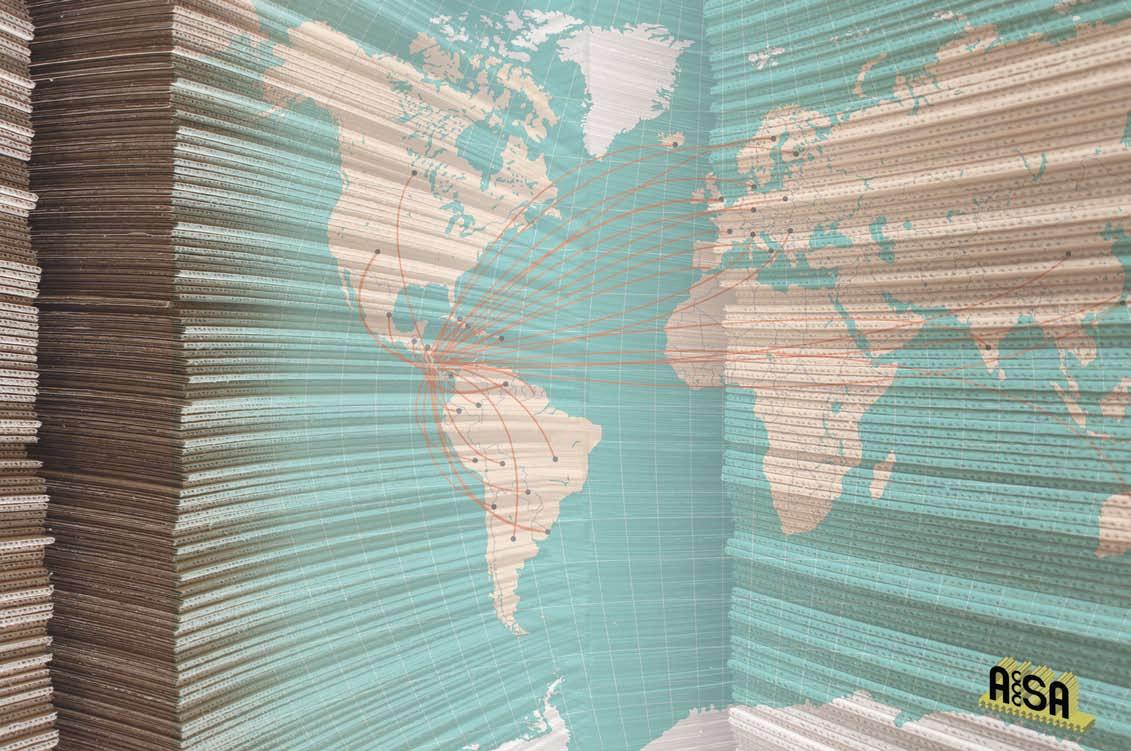