DIGITAL PRINTINGANDAUTOMATEDFINISHING
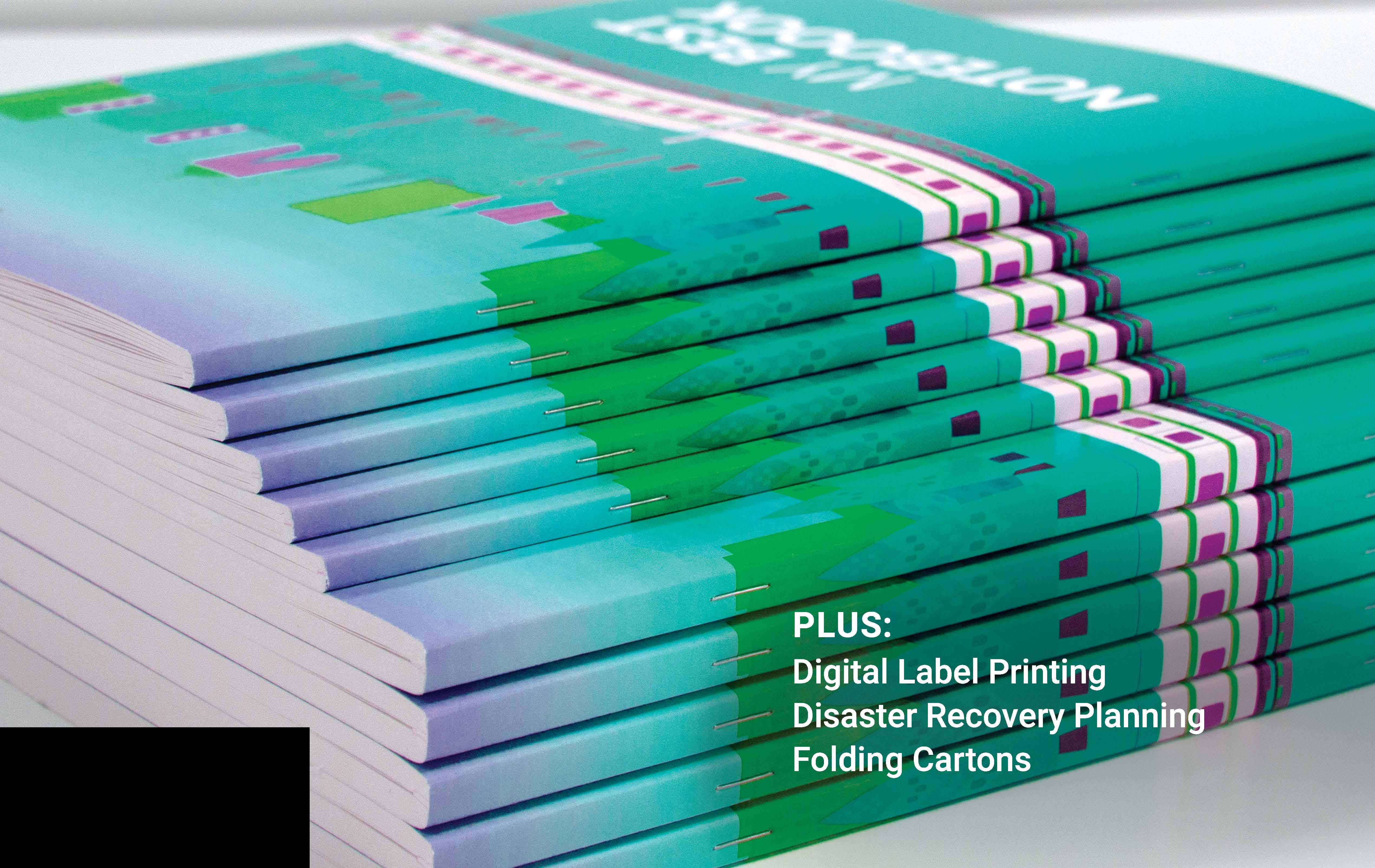
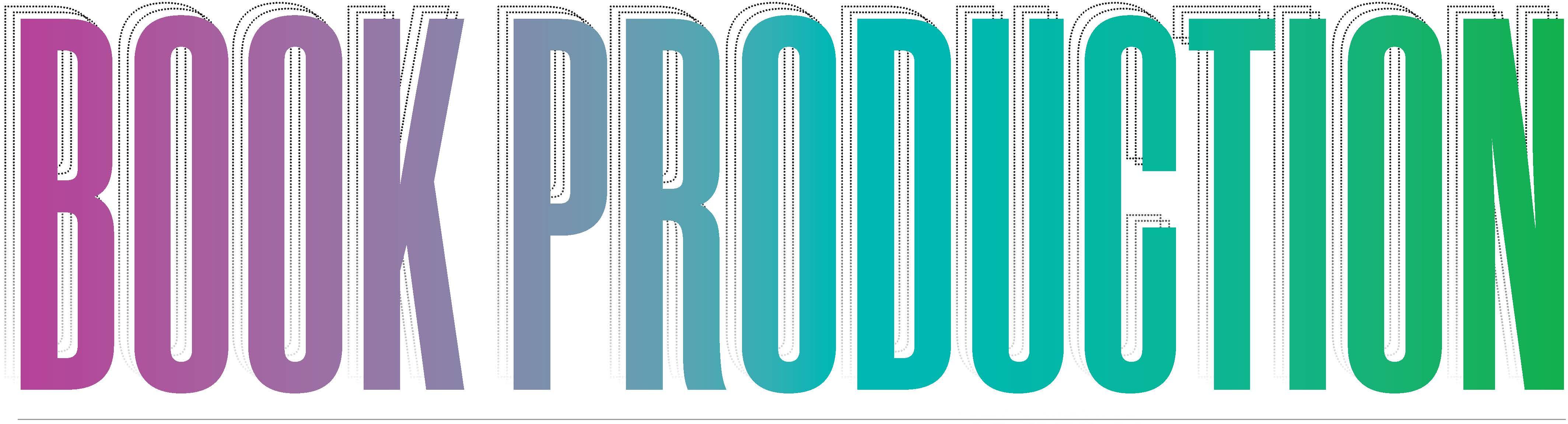
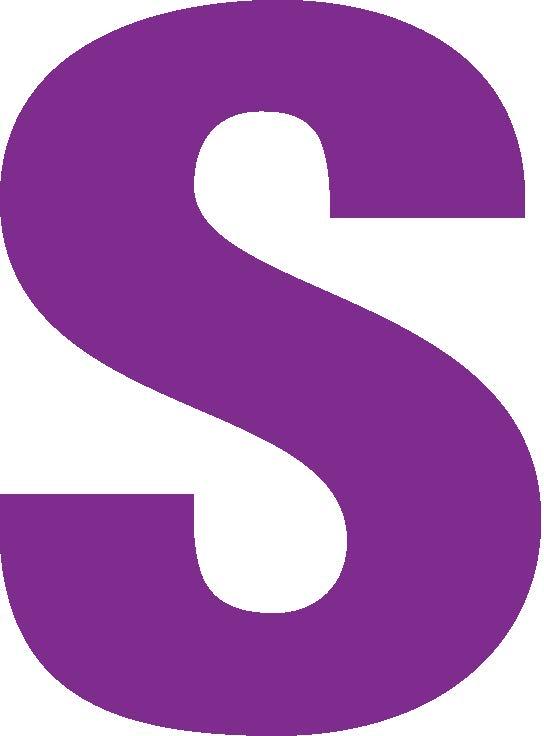
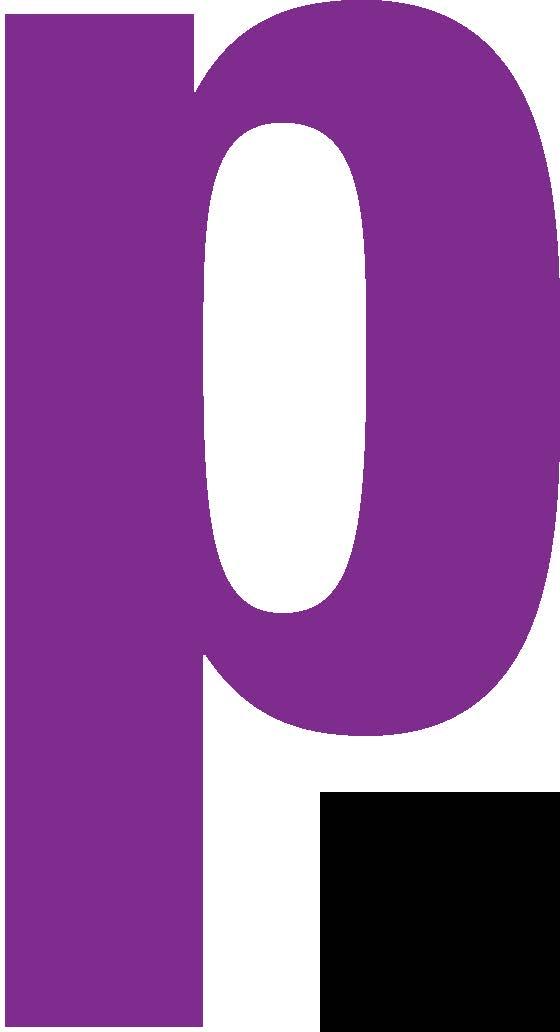

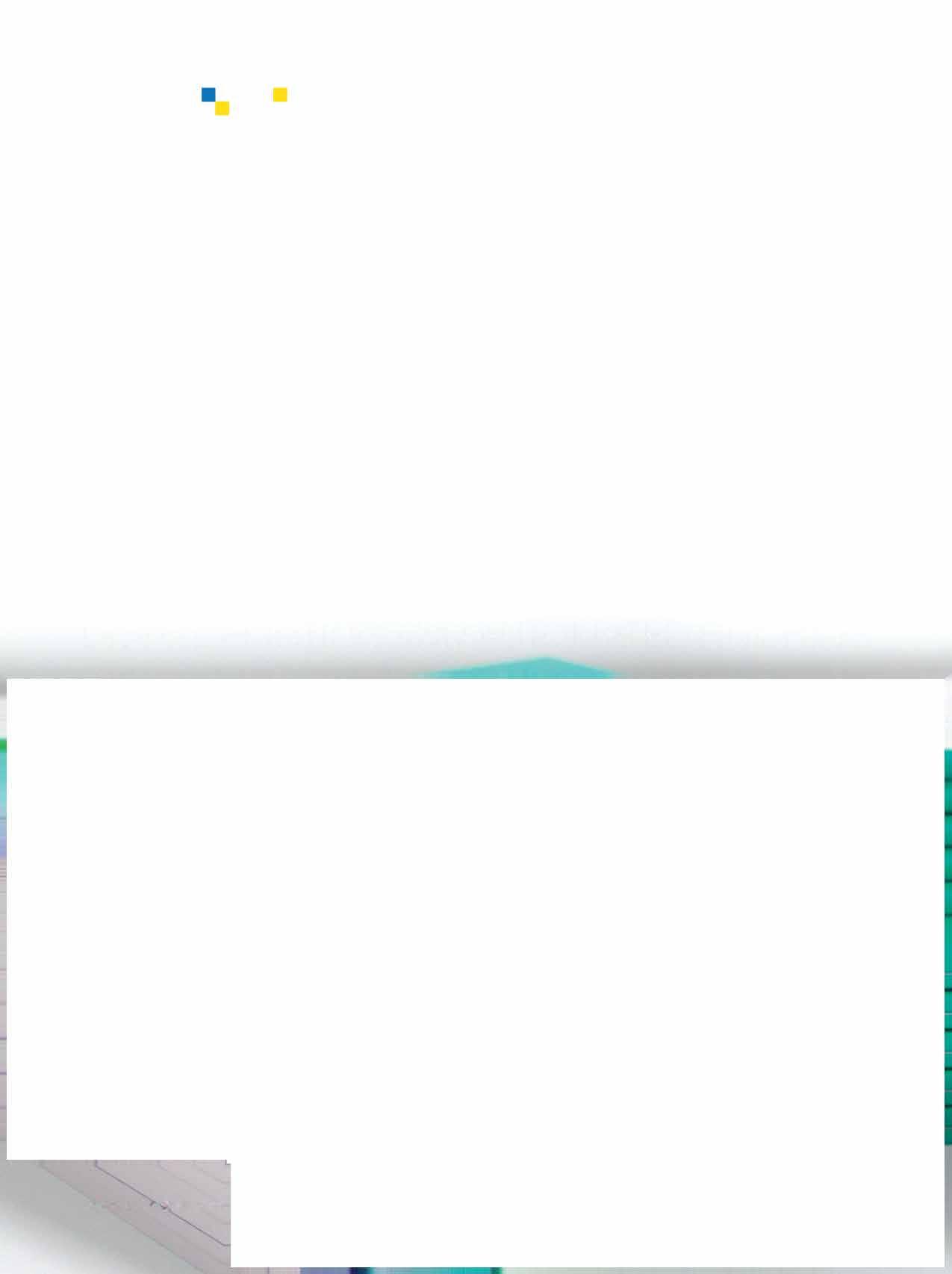
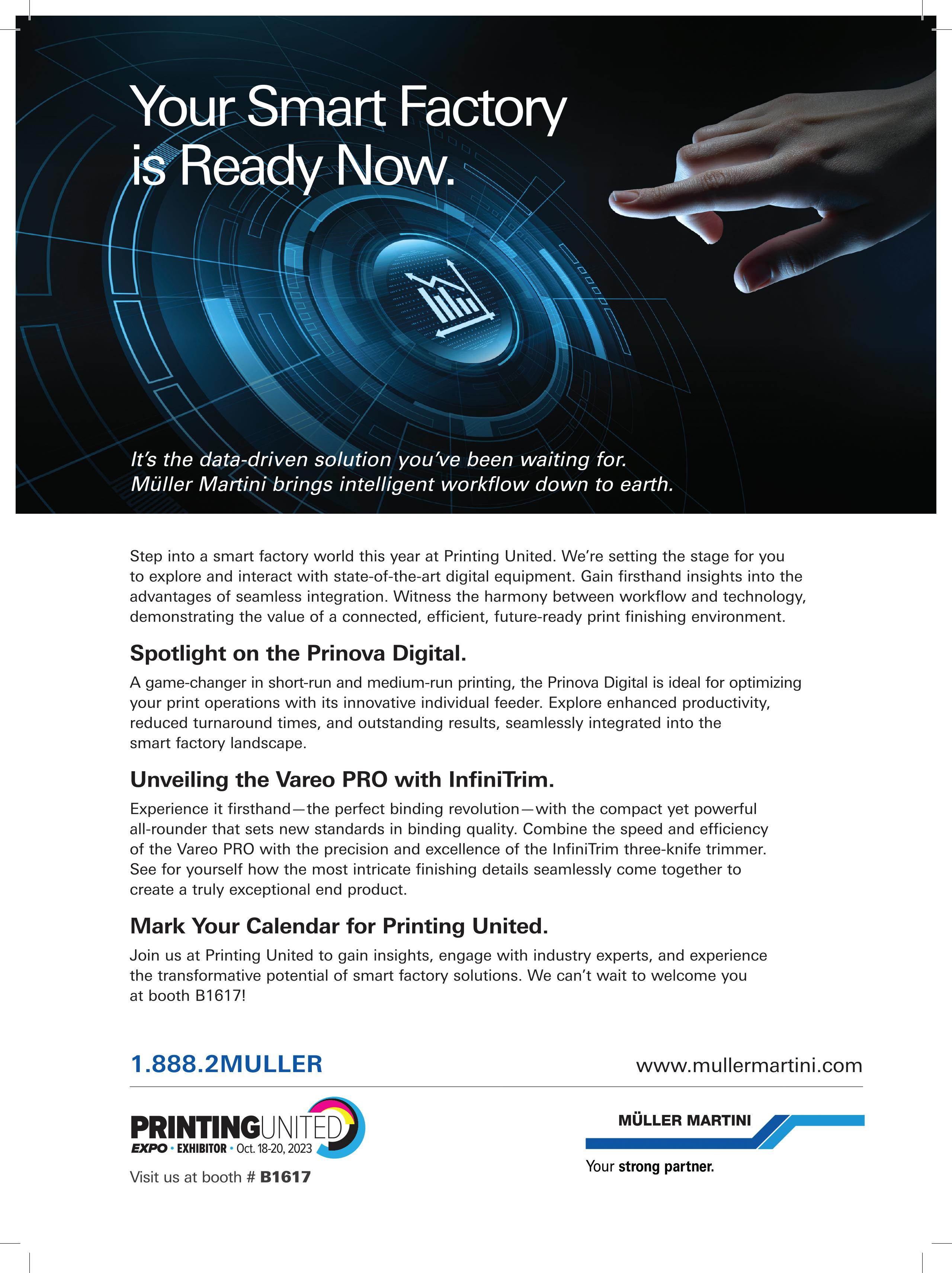
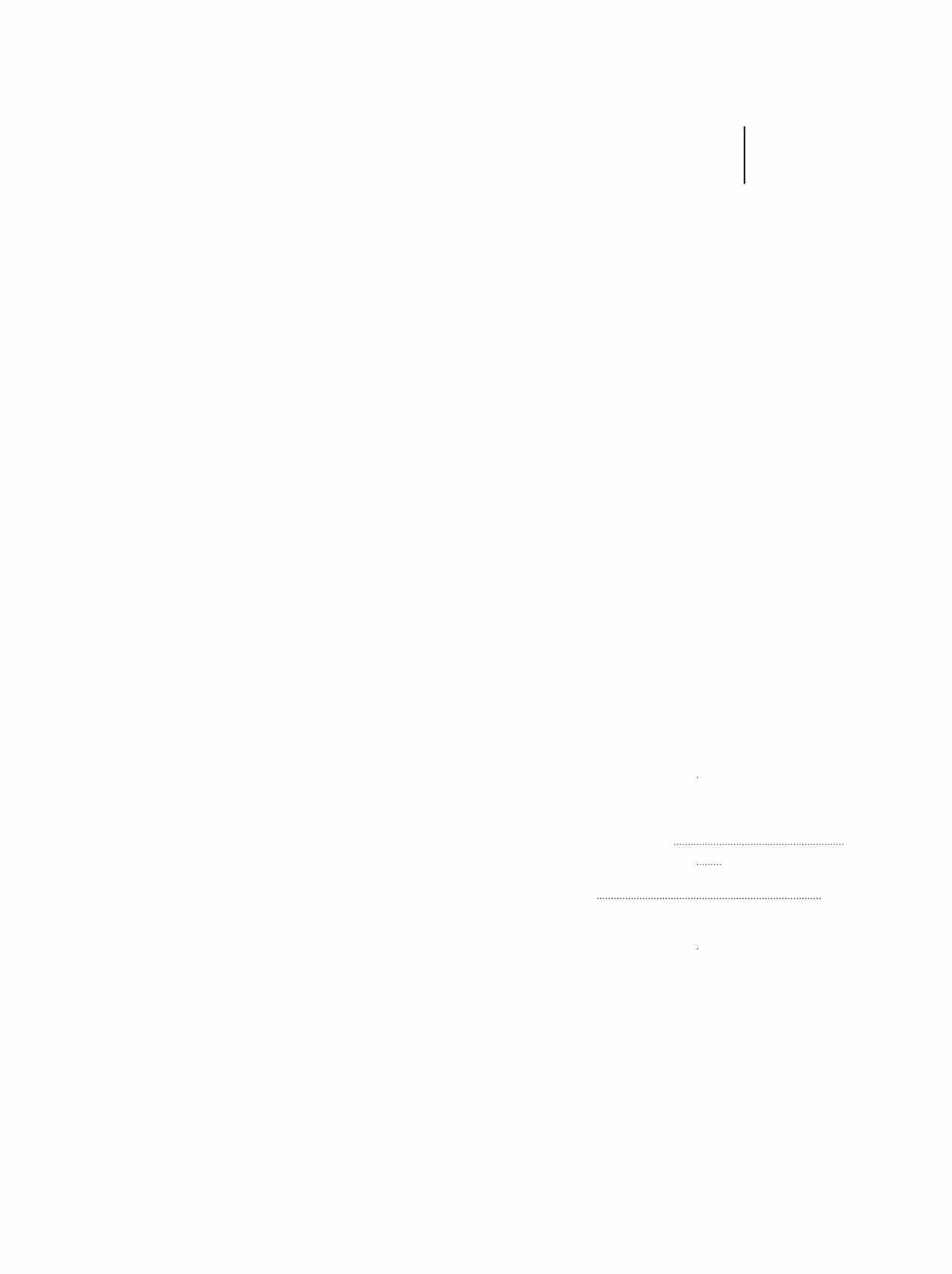
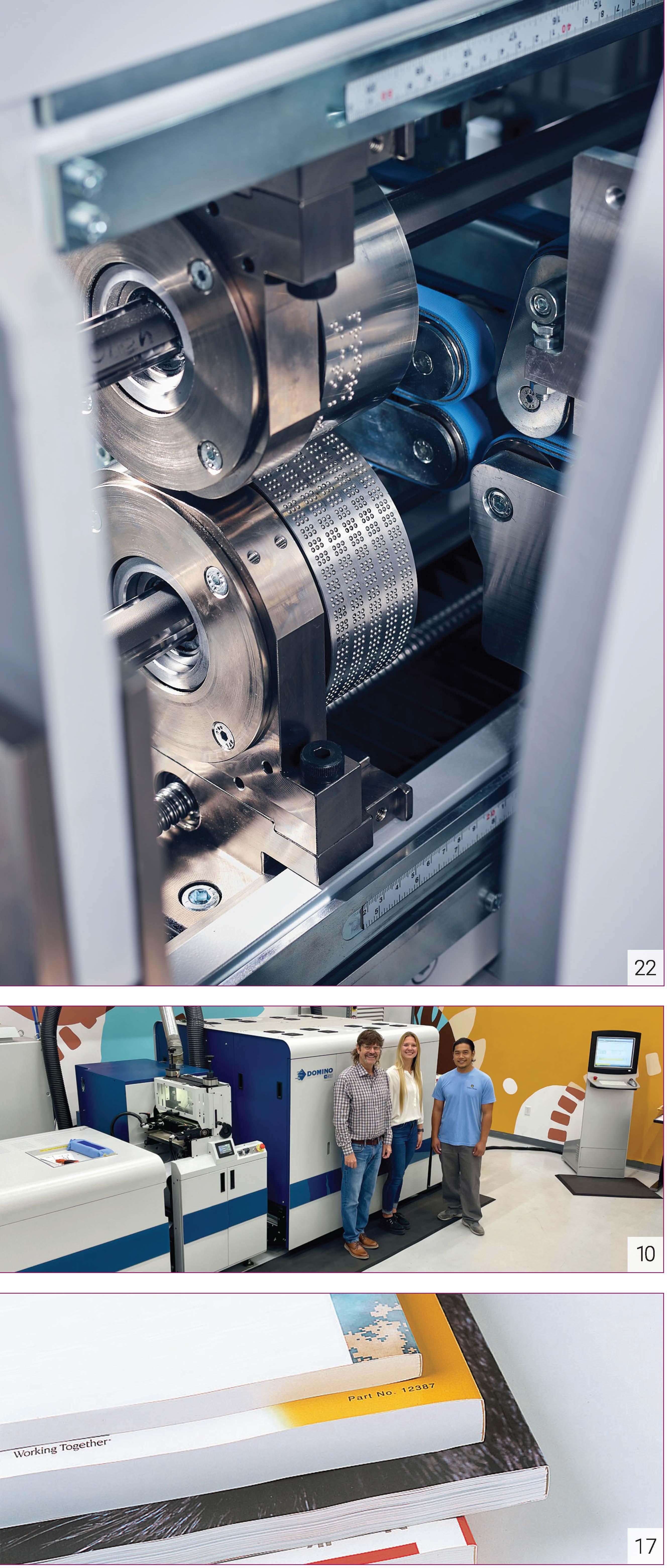
One area we have our eyes on is folding cartons. This paperbased packaging application is in demand as the need for sustainability and desire to eliminate plastic take front and center for brand owners. High-Quality, High-Value Packaging discusses ways in which the latest in digital printing and finishing technologies support short-run folding carton production.
dpsmagazine.com
Volume 25, Number 5 • ISSN: 1529-2320
EDITOR IN CHIEF
Thomas Tetreault 978-921-7850
EDITOR
Cassandra Balentine cbalentine@rockportpubs.com
ASSOCIATE EDITOR
Melissa Donovan mdonovan@rockportpubs.com
ART DIRECTOR
Sarah M. White swhite@rockportpubs.com
WEB EDITOR
Melissa Mueller
CONTRIBUTORS
Kemal Carr, Olivia Cahoon, Gina Ferrara, Mark Hanley
ADVERTISING SALES
On the other side of the coin, we’ve been charting the evolution of book publishing since the start of DPS magazine. Continued advancements in technology as well as shifts in cultural preferences enable just-in-time production of many varieties of books. We address this in Read On.
One of the best ways to highlight the power of digital is through a customer success story. This issue’s Spotlight section highlights San Diego, CA-based Label King. The label provider expanded its operations to incorporate digital printing with not only an investment in technology, staff, and workflow, but footprint as well.
Whatever type of print operation you manage, we’re continuously reminded of the importance of contingency plans. That’s why we dial in on disaster recovery in our Document Strategies column.
The issue wraps up with highlights from Standard Finishing 360’s event and Canon Solutions America’s annual thINK Ahead 2023 conference.
October is coming in hot! In a few weeks you can expect our October issue—just in time for Fall events. Stay tuned for coverage on the latest announcements and trends!
Best
PUBLISHER
Thomas Tetreault 100 Cummings Center, STE 321E Beverly, Massachusetts 01915
Ph 978-921-7850 x110 • Fx 978-921-7870 edit@rockportpubs.com
SALES
Amanda Doyon
Ph 978-921-7850 x170 • Fx 978-921-7870 adoyon@rockportpubs.com
Nicole Pizzi-Cerundolo
Ph 978-921-7850 x160 • Fx 978-921-7870 npcerundolo@rockportpubs.com
Subscribe online at dpsmagazine.com
CORPORATE & PUBLISHING OFFICE 100 Cummings Center, STE 321E Beverly, Massachusetts 01915
ROCKPORT CUSTOM PUBLISHING, LLC
CHAIRMAN
Jeffrey Jensen
PRESIDENT & CEO
Thomas Tetreault
CONTROLLER
Missy Tyler
Digital Publishing Solutions is published by Rockport Custom Publishing, LLC. Please send change of address forms to: 100 Cummings Center, STE 321E, Beverly, MA 01915. © Rockport Custom Publishing, LLC 2023. Reproduction by any means of the whole or part of Digital Publishing Solutions without written permission from the publisher is prohibited. Views expressed in the editorial pages do not imply our endorsement.
Subscription Rates: U.S. $41.65 per year, seven issues; single copies: $5.95, Canada and Mexico: $52.22 (U.S.D.), Other international subscriptions: $71.05 (U.S.D.)
Vendors: We welcome your product news. Include prices, slides, photos, and digital files with your press release. Please forward product samples and media kits to Reviews Editor, DPS Magazine, 100 Cummings Center, STE. 321E Beverly, MA 01915. We cannot be responsible for unsolicited product samples.
Continued advancements in technology as well as shifts in cultural preferences enable just-in-time production of many varieties of books.
regards, Cassandra Balentine, editor cbalentine@rockportpubs.com
Standard Finishing Systems recently held its annual Finishing 360 event on June 21 and 22, 2023. The open house took place at its National Demonstration and Training Center in Andover, MA.
More than 150 of the company’s customers and partners from across the U.S. attended the event to see its port-
solutions in action, learn more about the technology, and catch up with Standard representatives.
Standard’s Finishing 360 is designed to bring print service providers (PSPs) to its facility to present a comprehensive lineup of the latest Horizon and Hunkeler solutions.
Over the course of the two-day event, attendees had access to hands-on, personalized equipment demonstrations as well as high-level tours that provide an overview of its complete finishing line.
Its latest finishing technologies were displayed, including robot-assisted feeding, fully automated variable production, and cloud-based performance data and diagnostic tools.
Of note, systems and solutions on hand included the Hunkeler/Horizon Roll-to-Saddlestitch line featuring Hunkeler’s Generation 8 Unwinder and Cutter and Horizon’s iCE StitchLiner Mark V Saddlestitcher, as well as Horizon’s BQ-500 Perfect Binder with case binding accessories.
Visitors also learned about Standard’s pre-owned equipment program and the company’s trade-in and buyback programs. The Standard service team was also available to discuss the company’s service support options including service contracts, parts, preventative maintenance, and on-site or remote technical support. dps
The conference drew a total of 395 live attendees, 52 percent of which were customers and prospects, and the rest were made up of press, analysts, partners, speakers, and Canon staff.
The thINK association and by extension the annual thINK Ahead 2023 event aims at connecting Canon inkjet customers with peers and companies that will help level up their print business, and solve individual challenges.
“The goal of thINK is and has always been to accelerate the success of all Canon Solutions America production inkjet customers. We do that in two ways, one of which is to provide deep dive educational sessions, tools, training, and resources—not only at the annual thINK Ahead conference but also
365 days a year on thINKForum.com,” shares Eric Hawkinson, executive director, thINK Forum. “The other is to build community, to facilitate the coming together of Canon Solutions America production inkjet customers, print industry experts, and partners to enable them to network and learn from one another, to share best practices and mentor those in their community.”
The event presented many networking and educational opportunities.
A variety of vendors were on hand to answer questions throughout the event in the Partner Pavillion, including Canon Solutions America, the event’s executive sponsor. Partners from finishing to media and workflow included BCC Software, Billerud, Contiweb, C.P.
Bourg, Crawford Technologies, Crown Van Gelder NV, Domtar, Digital Substrate Solutions, DirectMail2.0, EF Cooling, EMT International, Finch Paper, GPA, Kelly Spicers, Magnum Digital Solution, Inc., MBO America, part of the Komori Group, Merlin, Midland Paper, Mintel/Comperemedia, Muller Martini, Neenah, One Vision, Pixelle, Plockmatic Group, Quadient, Racami, Rochester Software Associates, Roll2Mail, Solimar Systems, Standard Finishing, Sylvamo, TEC Lighting, Inc., Tecnau, Trekk, Ultimate TechnoGraphics, Videk, VITS International, and WestRock.
Additionally, the thINK Ahead 2023 event offered a variety of educational sessions designed to address the challenges industry leaders face today, including response optimization, workforce development and retention, postal regulations
and opportunities, Wayfair tax compliance, sustainability, and direct mail trends.
Rob Tynan, VP of operations, OneTouchPoint, a Canon inkjet customer, is always looking for new ways to improve its business and processes, and notes that a few key sessions stood out as a way to meet these goals—Employee Loyalty and Retention, Create Career Pathways, and Leading Your Business to Success.
From these sessions, Tynan learned that the way each generation thinks about the work industry is drastically different, and it’s important to understand each group’s perspective to create a positive work environment. “Coming into the office and ‘just’ working 9 to 5, giving eight solid hours, and following strict guidelines to get the job done no longer provides job satisfaction to everyone. Organizations and leaders need to adapt to change to accommodate our replacements. This will require the brain to rewire paths of mental thinking that have been programmed into us over the decades,” he shares.
This knowledge helped Tynan consider these differences and his company’s approach to management. “I have a staff of all ages and want to ensure that both I and the organization meet their needs,” he offers. “A week after returning from the thINK event, I formed a company ‘employee morale team’ to strengthen communication between our management team and associates.”
thINK Ahead 2023 concluded with two closing keynote presentations. Attendees first heard from Louis DeJoy, the 75th Postmaster General of the U.S., who delivered remarks centered around the Delivering for America plan, a blueprint for putting the United States Postal Service
on a positive trajectory. This was followed by a presentation by Dusty May, Florida Atlantic University (FAU) Basketball Head Coach, who led the 2022 to 2023 men’s FAU basketball team to its greatest season in the school’s history, advancing to the Final Four. He shared insights on leadership, teamwork, and motivation styles that foster winning teams.
This year’s thINK event focused on education, networking, and of course— some fun. While the industry is facing tough challenges, staying ahead of the trends and making connections that matter make a world of difference.
“Print is evolving. It sounds simple, but the complexities of the products printed today are rewarding their users with such an amazing impact. We know retention rates from educational material are better when delivered via print. Personalization, variable information, and ultra-customized products are easily produced in exceptionally low volumes. Our users and their clients inspire the industry and motivate all of us to be more creative and deliver fully featured automated tools to propel the future of print,” comments James Tressler, VP, sales and service, C.P. Bourg Inc.
“The state of our community is strong and growing. The simple fact is that Canon is producing world-class
production inkjet equipment and our membership is continuing to increase due to the ongoing marketshare success they have driven. These members bring new energy that fuel the content and conversation delivered at thINK Ahead,” adds Hawkinson.
Mark Hunt, director of strategic alliances, Standard Finishing Systems, felt the thINK community was brimming with optimism and enthusiasm about the industry. “There was a real sense of community both in terms of putting heads together to analyze some of the challenges facing the industry and in the sense of building relationships and enjoying the time spent together.”
Overall, Gerald Wilson, manager director, ef cooling US, Inc., found thINK Ahead 2023 to be a well-done event, worth its time participating. “thINK has done a great job creating an open, collaborative community that is interested in new ideas and better ways of doing things,” he concludes.
While the 2023 thINK Ahead forum is over, the resources are still building. Canon inkjet customers and prospects are invited to check out thinkforum.com for a range of tools separate from the annual event. Mark your calendars as thINK Ahead returns to The Boca Raton July 15 to 17, 2024. dps
Labels are an exciting segment of print. They are essential for communicating important information as well as generating attention. As digital print technologies continue to improve, the opportunity in labels also expands.
Located in San Diego, CA, Label King specializes in flexographic and digital printing, as well as direct thermal, thermal transfer, and barcode label printing technologies. Established in 2002 with one machine in a small suite, the business has transformed into a well-run label manufacturer with a 9,300 square footfacility.
ten years he realized he needed to pivot in order to change his life trajectory. He saw an opportunity in labels after recognizing the application's popularity and room for improvement. After doing his due diligence researching existing label operations and taking classes on running a label press, the stars aligned whenhewasreadytomakehismove.
to sell its assets-including a Webtron 650labelpressandasmallbookofbusiness; as wellas a press operator willing toworkundernewmanagement.
Therestishistoryandtodaythelabel business is thriving with 23 employees offering a mix of flexographic and digitallyprintedlabels.
Parker's three top requirements for Expanding into Digital extension of its customers' businesses. opening a label business included a
Thecompanypridesitselfinbeingan
There are a lot ofpeople whocan make labels. But we want to give customers an excellent experience
Parker began his career selling packaging and after about
- Robert Parker, owner/president, Label King
modernizethe business. It was a strategicdecisionthatitwantedto doright,whichmeantinvestingin notonlya press, butinthe space andtalentaswell.
Keepingawatchfuleyeonindustrytrends, "There arealotof people whocanmake press to run labels, cutting dies, and a Label King realized the growing imporlabels. Butwewanttogivecustomersan skilled operator. He soon found cutting tanceofdigitalprintcapabilitiesanddeterexcellent experience, giving them what dies; an existing label business looking minedthatitwasimportanttoexpandand they want, when they want it, how they want it, and ultimately helping to make their product evenbettersotheysellmore-it's awin-win,"sharesRobertParker, owner/president, LabelKing.
Parker had his sights set on incorporating digital label printing technology for several years. He admits the process took a long time to come to fruition, but this was by choice. “I had constraints, like how to do it and where to do it.”
Prior to its digital expansion, the Label King shop floor was 8,300 feet, which housed a lot of equipment and processed a lot of orders, day in and day out. “We were running three shifts and using the space,” he offers. To Parker, it didn’t make sense to disrupt the operation with a move.
Eventually the Label King decided to do a bump out in its existing space adding an 1,000-foot climate-controlled space to house a new digital operation.
After the space situation was sorted, it needed to get a proper workflow in place. “Talking to people in the industry
we quickly figured out that being prepared was the most important step. You can have the best machine, but you need to feed it, and digital prepress is different than the flexographic processes we were used to.”
Parker hired Turi Fiske in August of 2020 as a digital production and marketing manager and started a search for the machine that would kickstart the digital phase of Label King.
“Fiske came in knowing what she was doing. She established the front end for us. She took the bull by the horns and ran with it. It’s all about people doing the right things,” states Parker.
Before installing a Domino N610i in early 2022, the company vetted multiple press options.
Parker explains that Label King needed a press it could easily transition
flexographic work to. The print provider wanted some speed, gamut, reliability, and support. “Anyone can be great before you get the press. What happens after you get the press?” he asks.
The first step of its search was obtaining print samples. Parker and Fiske estimate they sent about 15 files out to a short list of six or seven digital label press manufacturers. When they received the prints back, they wrote the name of the press on the back of the sample and did a blind test, ranking them all by color accuracy, print quality of text, and overall image sharpness. This got them to the top three options.
The label provider then took the time to visit each of those manufacturing sites for in-person demonstrations on a multitude of jobs using various substrates on demand, without advance preparation.
Parker and Fiske agree that Domino made it easy; there was no hesitation from the demonstration room regarding the samples or materials. The vendor hit the colors perfectly the first time and the staff showed great teamwork and camaraderie.
The Domino N610i is a digital UV inkjet label press, capable of running up to 246 feet per minute at 600 dpi. This N-Series printer is able to produce over 90 percent of the Pantone color range and features the brightest whites with an opacity over 70 percent ensuring the finest printing depth. It is also capable of rendering small print type, 2D codes, and image detail on several different types of substrates.
The Domino N610i digital UV inkjet label press was installed and started running in May of 2022.
“We started at zero and began ramping up. By our fourth month of production, our revenue from that press was over $100,000. Having the Domino enables us to increase capacity, keep existing business that we would have otherwise lost, as well as gain new business,” comments Parker.
He offers one example of a brand owner in the food sector that wanted to run a large number of SKUs that wouldn’t be appropriate for flexographic. It was, however, a great candidate for digital. They needed 16 labels for a big presentation for a major retailer.
Label King received the art on a Monday, produced the labels in the same day on the Domino, and in the client’s hands for a presentation the next day. “We would not have been able to do this test run on our flexographic press. From what started with 16 labels, the potential is millions,” adds Parker.
Aside from opening the doors for new and existing customers, the efficiency in
production is unparalleled. Fiske recalls multiple instances where the team will get an order and get it out the same day. “Once the file is ready, we can get a rerun order printed within 15 minutes as long as the right materials are ready to go.”
Digital printing also provides flexibility, especially in terms of color gamut. “We do a lot of spot colors on flexographic and the Domino allows us to hit a huge amount of these colors. The ink is vibrant, which is an important feature. Labels have to stand out on a shelf and having that vibrancy is definitely helpful,” comments Fiske.
An additional benefit Label King realized with digital is reduced waste, which is essential from a cost and environmental standpoint.
Compared with its flexographic jobs; Fiske says there is no question less material is used with digital. One example, prior to digital a shop rule was if there was 500 feet or less of material remaining on a roll, it would generally be discarded because a flexographic job wouldn’t print to it. Now, a 300-foot job is printed with what would-be-thrown-out material. “We have a pile of those small rolls so now we are able to maximize our material usage. It not only saves material, but it also saves time.”
Label King now offers its established customers a digital option for work that makes sense. While the move to digital took Parker a little longer than he would have liked, the investment was done right the first time. Today the company gets more done with fewer people and shifts. The company is also able to meet customer demands for shorter run work while simultaneously reducing waste and maintaining its reputation for excellent customer service. dps
In 2011, Leiman Chan set out to transform his family's business, Los Angeles, CA-based Nonstop Printing, into a print manufacturing dynamo. After over a decade at the helm, Chan's vision has now been realized, thanks to the enormous untapped efficiencies of customized workflow automation. With a staff of ten, Chan's digital printing business specializes in short-run, high-quality art books as well as event printing and signage. His clients include some of Hollywood's biggest celebrities and entertainment firms-so personalized service, accuracy, attention to detail, and exceptional print quality are essential.
After ten years, Chan was still struggling with manychallenges faced by other small printing companies-including profitability, talent acquisition, and staff burnout. In particular, he had difficulty retaining staff in his busy prepress department. "I was desperate for a breakthrough and realized that it was no longer sustainable to keep replacing staff," he recalls.
Seeking a breakthrough, Chan came across Tilia Labs and learned that smaller printers were reducing imposition times from a few minutes to a few seconds. Realizing the potential for efficiency gains, Chan invested in Phoenix, which dramatically reduced imposition times and processed small orders more
efficiently. Automation also eliminated stressful manual touchpoints that were burning out employees.
The CEO sought advice on how to take these efficiencies to the next level, and was introduced to Marc Raad, CEO, Significans Automation. After a thorough analysis, Raad and his team determined that the best path forward was to deploy the Enfocus Switch workflow automation tool. "So, we did the groundwork and we also taught Leiman advanced programming and scripting," shares Raad. "He loved every minute of it!"
Chan's vision was finally becoming a reality. "Significans Automation showed
me how to create these incredible workflows and time-saving automation," he says. With his unique insight into every department at Nonstop, Chan was able to integrate and automate all critical aspects of his workflow-including proofing, file delivery, finishing, and bindery.
Prior to automation, it took 15 to 60 minutes to proof a book. With automation, that's now down to three to five minutes.
Significans Automation also deployed GMG Color software to improve workflow and color management. This cut press downtime over ten percent due to reduced operator intervention to adjust color using curves. Rework due to proofing errors or miscommunication was cut by 15 percent, and prepress staff was eventually reduced by 50 percent.
Today, Chan estimates that he could add over $1 million in new businesswithout hiring new employees or buying new equipment. "Significans Automation helped revolutionize our business through automation even more than I had envisioned. I hope my success story gives hope to other small printers," he adds.
For a review of your specific workflow automation needs call Significans Automation at 877-463-4465 or visit significans.com. dps
Disaster recovery (DR) plans provide assurance to print-related business that they can meet service level agreements (SLAs), even in the case of unexpected events.
Thelifebloodoftheprintandmail industry istheSLA andfailing tomeetadeadline because managers did not consider the impact of potential contingencies can cost far more than an apology or penalty on a contract, which Steve Berman, director of risk and compliance, DATAMATX, says could cost the confidence ofone or many customers.
natural disaster, you and your client may be open to fines, penalties, and legal action," agrees Ernie Crawford, president and CEO, Crawford Technologies.
Moreover, steep fines are levied for noncompliance ifregulations are not met or a SLA is missed," shares Brian Murphy, director, operations, Mail-Gard, IWCO.
''As we learned from the pandemic, print and mail operations are deemed critical business functions. Transactional printers deliver bills, checks, and other business-critical information to customers. Not having a DR solution would be as negligent as not
DRsolutionscanmeanthedifference betweenbusiness as usual and insolvency. "Historically, print-to-mail operations are the last thing that a business looks at during their overall DR planning. Digital data usually recovers fairly quickly, however, print-to-mail operations take weeks, months, or even years to fully recover. Without the proper planning an organization can lose millions ofdollars, directly affecting its bottom line.
Disaster recovery is insurance to deliver your services in the event of a disruption.
tionwillmitigateyourriskwhena disruptionoccurs."
Print providers should take a proactive approach to DR "DR is insurance to deliver your services in the event ofa disruption;' stressesCrawford. Itiscriticalto protectyouroperationandclientdata, but toalsoensureyoucanquicklyrecoverand resume operations with minimal disruptions. "It demonstrates your commitment tomaintainingthetrustofyourclientsand reputation. IfyouhaveaSLAtocreateand mail or deliver informationwithin a specified timeframe, then a DR soluhaving a data center disaster recovery plan," says Kemal Carr, president, Madison Advisors.
"If your organization experiences a disruption due to a system failure, data breach, or
- Ernie Crawford, president and CEO, Crawford Technologies
Berman stresses that DR isn't just cleaning up from a leaky roof or filing an insurance claim. "It could involve anything
from equipment failure or supply chain disruption to a natural disaster or cyber incident. Business consumers of print services become more sophisticated and many require print providers to show evidence of a serious, professional commitment to disaster recovery,” he offers.
Failing to deliver on business promises can lead to irrefutable harm towards a print business’ reputation.
Carr feels that while all production operations should consider establishing a robust DR plan, those operating under specific SLAs and state or federal regulations or those that produce documents exposing the organization to risk, such as policy cancellations, new account activations, and checks, rely most on the DR plan to minimize business losses and penalties.
Mary Ann Rowan, CXO, Solimar Systems, points out that print businesses often store critical data and customer information that could be lost or compromised in a disaster. “Transactional and direct mail printers are often at the top of the list regarding types of businesses that should be most concerned. These printers typically handle large volumes of data and require efficient failover recovery solutions to ensure they can continue operating without interruption.”
“You may think only providers that process transactional communications would need to be concerned about DR, but, in fact, all print providers should be concerned,” stresses Crawford. While transactional communications are timesensitive with legal and financial implications and, therefore, have stringent SLA requirements with contracts that require DR, direct mail and marketing communications are just as critical to generating sales and acquiring new customers. “They both require handling large volumes of data and rely on complex systems and equipment. Any disruption due to a natural disaster or data
breach can lead to significant financial losses, customer dissatisfaction, and damage to client relationships with both types of mail.”
DR plans along with robust solutions ensure a quick recovery of systems, customer data, and operations. They help ensure continuity by allowing print providers to maintain commitments to clients while preserving their business reputation, states Crawford.
All printers should at least take the first step of measuring impact, comments Berman. “Measuring potential business impact of a system disruption is beneficial to even the smallest of print shops. However, transactional mailers have an added responsibility of processing data and producing product in a defined timeline in order for bills, legal notices, and statements to be delivered as part of the customer’s cash flow. Therefore, the computer systems, business processes, and information security of transactional printers is at least as critical to the business as the machines that put ink or toner on paper.”
A typical DR plan is multilayered and well-documented, covering all elements of the operation, including supply chains, utilities, labor, and the physical plant.
DR solutions typically include several key features,
says Rowan, including data backup and restoration, system replication, failover capabilities, and automatic failback. She explains that data backup and restoration services are essential for ensuring that critical documents can be quickly recovered in the event of a disaster. System replication and failover capabilities allow businesses to dynamically switch to a backup production system in case of a failure or outage. Automatic failback enables businesses to automatically switch back to their primary system once it is restored.
DR should cover anything from creating the communications to proofing and verification, printing, finishing, and distribution. “In many instances with compliance communications, printing departments and organizations are allowed to use B&W instead of color or default to a standard envelope, this is all dependent on your contracts and agreements,” shares Crawford.
COVID-19 drastically changed disaster recovery (DR) strategies for all organizations.
“I do not think many organizations and print providers thought their staff would be isolated for two weeks and not be able to return to work. Many printers and mailers had entire departments that could not come to the office,” recalls Ernie Crawford, president and CEO, Crawford Technologies.
He points out that organizations have realized that staffing and critical knowledge are just as important to business continuity and quick recovery as equipment and systems.
“If you still rely on your staff to set up printers, inserters, and production machines based on job number, then you are going to fail your DR testing if those people are not available. This demonstrates that normalized print workflows can be instrumental in shifting workloads to another site.”
Many operations adapted to seamlessly continuing operations by implementing new health and safety protocols and extending relationships with current suppliers during and following COVID-19. “For some operations, the pandemic exposed weaknesses in their DR plans, while for others it highlighted the complete lack of a plan altogether. Operations without cross-trained employees found themselves limited in their ability to process work when key employees were unavailable,” comments Kemal Carr, president, Madison Advisors.
The pandemic also highlighted the need for robust and adaptable DR strategies. Brian Murphy, director, operations, Mail-Gard, IWCO, says DR plans now must include remote work scenarios that ensure secure access to critical systems and data. “While we may never see COVID-19 again, every organization needs to ensure that they have flexible solutions and adaptable processes to ensure business continuity when the unexpected happens. Your processes and staff need to be agile to quickly accommodate unexpected events, such as supply chain disruptions or the need to shift to create their communications in another location.”
“As an organization, you do not need to have extra equipment sitting in a warehouse for a test every 90 days or once a year. DR may just direct your output to a print vendor or partner on the other side of the country. DR can be simple or complex depending on your requirements, timeframes, and agreements,” comments Crawford.
Carr suggests starting with crosstraining employees to form the basis of a
business continuance strategy, enabling others within the organization to take on roles as needed.
Additionally, load balancing or contracting with an operation located in a separate geographic region reduces exposure to natural disasters, adds Carr.
Berman recommends management signal its commitment to the DR process by understanding the standards associated with business continuity
See page 21 for more information.
and disaster recovery (BCDR) planning. “There are two main standards that many IT-based businesses use to build a DR framework. NIST Special Publication 800-34 details contingency planning for federal information systems and the international standard ISO 22301 deals with security as well as resilience and business continuity management systems requirements.”
He says the proper steps to a successful BCDR or contingency plan for both standards include a commitment from leadership; identifying the scope, resources, risks, and business impacts of various kinds of outages and threats; determining preventative controls to ensure continuous operations for critical systems; creating contingency plans and roles for recovery during and after a disruption; training key personnel in their roles and activities; testing the plan and conducting exercises regularly; and evaluating and maintaining the plan as changes occur.
“Implementation of these plans frequently requires an investment in additional equipment, software, services, or outside expertise, which is why management’s commitment to the process is key. A written plan that is only dusted off to change the review date is not very useful when the procedures and roles in it have been adjusted by events and neglect,” offers Berman.
“We consider it essential for every client to test on a regular basis, as critical communications workflows change over time and your recovery plan needs to keep up with those changes,” comments Murphy.
Print and mail providers are essential businesses that must have a contingency plan in place for unexpected events. DR plans help to ensure business continuity by allowing print providers to maintain commitments to clients while preserving their business reputation. dps
technology continues to transform book manufacturing by offering print providers and publishers new options to improve efficiency and profitability. While book printers have been producing books on digital presses for some time, innovations intechnologyare moving more work from offset to digital, improving productivity, and offering new opportunities for products and services;' shares Tonya Powers, director of marketing, Canon Solutions America, Production PrintSolutions.
There are a number of ways to breakdown the various segments that fall under the book umbrella.
Bob Flinn, director of business development, Standard Finishing Systems, says that printers and book manufacturers in the U.S. usually group books based on the printed format, finishing system, and run length.
"Printed formats usually fall under two large umbrellas-hardcover and softcover/paperback. A majority of hardcover books fall in a size range of between 6x9 and 8.Sxl 1 inches while softcover/paperback books typically fall under four types-pocket, digest, trade, and board books," continues Flinn.
For run length, Ray Hillhouse, VP sales and marketing, Plockmatic Group Offline Business Unit, categorizes by short run or even run-of-one, citing vanity publishing and photo books as two examples. "Digital print offers the buyer great options for low quantities of book or booklet products."
Dividing by genre is another popular option. "There are some segments such
as adult trade publications, higher education, children's, K to 12, and religious, but these categories are broken into further segments, which makes it difficult to really define the book umbrella," admits Carlos Martins, solutions manager, Muller Martini North America.
"The books category can include a lot of application types, like books, manuals, catalogs, periodicals, journals, kids books, personalized books, textbooks, coffee table books, photo books, and yearbooks;' attests Powers.
Alternatively, Armen Snkhtchianm marketing manager, C.P. Bourg, believes it's important to consider the book industry in the broadest sense. Ask what can be considered a book today and which formats are standard. "The demand for publications is so diverse that it's difficult to cover all needs. On demand production of books, and publications of all kinds, is the safest and most competitive option today."
Out of all the segments, the consensus is adult trade fiction, particularly paperback is the healthiest category.
For example, Stephen Sanker, manager, digital printing, Koenig & Bauer North America, believes growth in softcover book demand comes from books on demand over the last couple/ few years and also an increase in trade paperbacks. He expects this to continue as a result of new consumer buyer trends and self publishing.
"For us, working at the low- to midrange style and quantity of publication, markets continue to expand and grow. Be it one-off photo books, vanity products, or volume publications of several thousand paperback books. There is every reason to imagine the short-run sector to almost continually expand, as costsper-copy seem to be forever tumbling due to print efficiencies," states Hillhouse.
1. Equipment such as the Morgana Systems BM4050 booklet maker, complete withVFX dual bin feeder, allow for copies to be wrapped in a cover, supplied via the second bin, prior to forming a SquareBack finish to give the perfect bound appearance with a stapled product.Martins notes that coming out of the COVID-19 pandemic, there was a big rise and subsequent demand for books in all segments—particularly educational and adult trade. During the pandemic, the personalization market for books, such as photo books and yearbooks, certainly struggled, but is now rebounding as more people travel and schools return back to normal.
Donna Covannon, director, marketing, Xeikon, shares Bookscan data provided by the Book Manufacturers Institute. “Adult fiction shows the most growth opportunity in terms of sales of printed books from 2019 to 2022. Young adult fiction and nonfiction show a slight to moderate year-over-year decline in unit sale of print books. January 2023 year-over-year publishing trends indicate that the largest year-over-year 2022 versus 2023 growth is in adult books; higher education course materials and university presses.”
Overall, “there continues to be a push-and-pull between eBooks and printed books, so we don’t expect positive growth in demand for printed books to continue at a certain level forever. But these past few years have shown us that the book manufacturing industry has a strong foothold and can withstand competition from alternative format,” explains Flinn.
Finishing tools from cutting and folding to binding advance to support digital inkjet for book production. This is seen in all book segments.
“Each book market segment is facing the same market pressure—demand for short runs and book-of-one from established publishers and self-publishers alike. This demand has pushed book manufacturers to incorporate digital inkjet into their workflows for more cost-effective production and has forced manufacturers on the finishing side to develop solutions to keep up,” explains Flinn.
Automated finishing solutions like page integrity, cover book block matching, job tracking, and fulfillment increase efficiency, according to Flinn. Automated setup and changeovers onthe-fly allow a shop to process more jobs with varying page counts and size
formats. This is all achieved with fewer touch points and operators.
These intelligent systems, as Martins refers to them, rely less and less on human intervention. They combine processes, allowing data to be shared, which is used to make informed decisions in an instant.
Advancements in inkjet quality continue to push forward and influence where and what can utilize the technology. For book manufacturing, one segment of interest is highend books like coffee table and photo books.
“A subset of adult books, luxury books are often overlooked—and sometimes not even recognized—as a literary genre, coffee table books have been around for more than a century. Even in today’s screen-obsessed world, consumers find themselves mesmerized by the allure of the coffee table book,” shares Donna Covannon, director, marketing, Xeikon.
Tonya Powers, director of marketing, Canon Solutions America, Production Print Solutions, says “demand for custom printed photo books shows that people want to reconnect and remember moments with a tangible asset. These are great for marking occasions like weddings, births, holidays, or vacations, as well as school and association yearbooks.”
Bob Flinn, director of business development, Standard Finishing Systems, believes that advancements in inkjet technology have come to point where it can now be utilized for high-end books. “There have been significant advancements in color inkjet print technology ranging from better color quality and more accurate color controls to expanded paper options and embellishments such as spot coating, high gloss or matte finishes, and dimensional coating.”
Carlos Martins, solutions manager, Muller Martini North America, agrees that the quality of inkjet allows for high-end books to take advantage of the technology. Some high-end books that are typically sewn are now being printed on inkjet presses based on his experience.
“We see an increase for high-quality color, accent color, photos, and coverage overall when it comes to digital production,” reveals Stephen Sanker, manager, digital printing, Koenig & Bauer North America.
Powers says more print service providers are offering high-margin products like photo specialty books and producing them on production inkjet presses. “Image quality improvements in inkjet presses make them an attractive and cost-effective option for photo books.”
“A good, reliable operator requires years of training before reaching an adequate level of performance, and what’s more, needs continuous training as
production technology evolves too. Add to this the human error factor, and publication production automation is essential today if we are to be
competitive and guaranteed not to be left behind by technological progress,” suggests Snkhtchianm.
According to Hillhouse a good example of Finishing 4.0 in action is photo book production. Mainly produced in runs of one or two copies, these shorter run lengths make a touchless workflow essential. “The production system needs to be capable of setting itself up automatically for each new product, based on digital job data, and launching production with the absolute minimum of manual intervention. Any changes to the process need to be detected and managed. The aim is to coordinate these three components, ideally enabling a touchless workflow while keeping production costs low, despite shorter runs and an increase in product variety.”
Vision and inspection tools also play a role. “Vision systems are critical to the process and today’s smart factory would not work without them. These intelligent license plates are what drives the automation in finishing equipment,” notes Martins.
“Verification and integrity software can perform sheet, signature, and book block-level tracking as well as cover-tobook block matching. Depending upon the configuration, these systems can reject incomplete book blocks or book blocks with the pages out of order, alerting the operator or even generating a reprint file,” shares Flinn.
Systems driven by barcodes are also used. In the instance of finishing, a barcode can provide instructions for equipment to follow, sending a digitally printed job to the correct unit, which leads to greater efficiencies, notes Hillhouse.
“For the increases we see along with the new trends toward reducing labor and increasing automation, fully finished books via digital press production are getting attention. Our focus is to provide this type of fully integrated solution via a digital inkjet web printing machine. With this solution we are able to fully
integrate with finishing systems to produce a finished book," shares Sanker.
Despite advancements in the overall book manufacturing process, there are still areas that could improve. Tools are being developed to target these issues.
As a whole, the top challenges-as with any other part of the print industrycontinue to be "labor; paper/supply chain related; sustainability; inflation; and general economic uncertainty," shares Covannon. Automation addresses all of this, reducing labor and supply chain issues.
"Communicating and integrating solutions from different manufacturers remains a real challenge in the industry. While we increasingly emphasize flexibility and automation in publication production, it is crucial to offer customers a clear evolution path, enabling them to integrate machines from different producers into their solution," shares Snkhtchianm.
Flinn notes one area with room for improvement is streamlining hardcover-case bound-book production. "The casing-in process has traditionally been an entirely separate step in book pro-
to combine content so it can be finished more efficiently," says Martins.
In terms of softcover books, Martins believes there are no challenges that need to be addressed. "Standardization on format size and using intelligent finishing equipment to finish and trim to size already exists and works well. Producing book-of-one with intelligent workflow to manage cover print and sequencing is easily managed. Many successful production lines are running from blank roll of paper to a finished, one-off book."
handle the paper shortage as demand increases. It will be interesting to see how the industry adapts going forward," notes Flinn.
Of course, there is no reason to think the industry as whole won't succeed in moving pastthesechallenges. "Bookprinters were early adopters of digital printing and production inkjet. Much of the early growth in production inkjet volume was in the printing of monochrome book blocks. Thenext phase for digital book production is sheetfed inkjet presses that can affordably produce high-quality monochrome and color work on a variety of substrates;' foresees Powers. dps
duction, and while greater automation While digital inkjet techhas improved the casing-in process for longer production runs, short-run and book-of-one have remained manual processes. Fortunately, there are new solutions arriving on the market that can streamline the process and reduce the costs associated with short-run hardcover book binding."
Other inefficiencies in hardcover book production revolve around "the complexity of producing covers with embellishments and then matching the content to the required text block to produce book-of-one. However, smart systems are being developed with smart sortation devices and robotics
4. Muller Martini embraces Industry 4.0 or Finishing 4.0. It is designed around four main pillars-automation, connectivity, variability, and touchless work/low. dpsmagazine.com
nology and finishing solutions manage to keep pace and react to the demands of consumers, there are other external factors at play.
"The industry as a whole is moving in a positive direction, but there are still ongoing concerns about paper and labor shortages. Digital workflows and higher degrees of automation have relieved some of the burden of the labor shortage, but book manufacturers need to get creative to
I) advertiser index & companies mentioned
gamut, a high degree of repeatability, the elimination of plates, and reduced makeready waste.
“The first sheet from the press is good, meaning testing for new customers is a completely different model because the real product can be printed on the actual production sheet from the actual production device,” he states.
As the customer’s needs grow, Martin points out that the same production process can competitively run their needed production typically up through a few thousand sheets. If the volume grows and versioning becomes high, then the inkjet process could remain the process of choice. “If the volume gets higher still, the producer can choose to stay with digital or move the job to offset where the larger volumes could be produced more economically,” he shares.
Overall, Martin doesn’t view inkjet as a standalone process for folding carton production, but more of a complimentary process to traditional methods.
An example of a segment that utilizes the benefits of inkjet printing is cannabis. “New products are brought to market requiring on boarding and development, easily done in an inkjet environment. Some of these products tend to be more regionally impactful, keeping volumes down and allowing inkjet production to be very competitive,” he notes.
Folding carton printing requires the ability to handle the substrate at various weights and thicknesses, fidelity in color reproduction, as well as the ability to hit spot colors that are outside of the CMYK space.
In addition to UV inkjet, another printing concept ideal for folding cartons is nanography technology, which hits all of the above requirements and more.
Amir Shalev, market development director, Landa, points out that Landa’s presses offer full compatibility to mainstream folding carton production
thanks to B1 print sheet size and ability to work on any paper and board without pre-treatment—including recycled and uncoated materials. “Integration to inline finishing at B1/41 inches is critical for converters looking to expand beyond very short prototype runs,” he stresses.
“We are seeing folding carton production across the board in our customer base. We have mainstream converters from the largest global packaging companies who use our presses exclusively for folding carton production,” comments Shalev. “We also find that commercial printers are using the presses’ versatility to expand into folding cartons as a growth area quite successfully.”
Many folding carton trends are apparent, according to Shalev, including reshoring and destocking.
For pharmaceutical, personalized medication and SKU proliferation combined with spot color usage creates a high push for efficient production of packaging and an explicit need for flexible production.
Small- and medium- sized brands in the food and beverage market as well as the personal care segment look to digital technologies to create a variety of offerings for their client base.
“They believe in experimenting with the market through quick interactions in social media and subsequent product releases. Our solutions are well
suited to take their multiple versions from market testing and into full production,” says Shalev.
In terms of future features, Shalev adds that variable data printing is an exceptional capability that is still not widely used, but holds promise for adding with things like security features and unique consumer engagement and tracking.
Electrophotography—specifically liquid electrophotography (LEP) as offered by HP—is well known for its capabilities in digital folding carton production.
The HP Indigo 35K Digital Press is a second-generation press based on eight years of experience to serve the growing digital folding carton market. “HP Indigo’s LEP technology delivers the highest print quality in digital folding cartons. It offers an offset look and feel on a digital press and the most advanced color management system on the market,” says
Shahar Lev-Ari, product marketing manager, HP.
The HP Indigo 35K Digital Press is a full folding carton production line— equipped with an inline priming unit and utilizes the Tresu iCoat II to create an efficient handoff between processes.
The inline priming unit gives converters the flexibility to choose virtually any off-the-shelf special media, such as metalized, blackboard, or uncoated Kraft, which are trendy options especially in healthcare and cosmetics.
With HP Indigo’s LEP technology, Lev-Ari says converters reach color faster, with minimal makeready waste. “This is especially valuable for jobs where media costs upwards of $1 to $2 per page.”
He says HP Indigo customers use the digital folding carton presses primarily for high-value boxes common in personal care and healthcare, where high standards of print, many SKUs, and premium/limited-edition items are in demand.
Lev-Air also see customers who leverage the value of personalization to
a variety of products, such as cups with variable data publishing, trading cards with full control of randomization, and gift cards on cardboard or synthetics.
Feature sets that matter for digital print include very short makeready and automation. “Especially today, where the time from order to box decreases drastically, there is substantial value in a press that can support multi SKU orders, zero inventory, and just-in-time production. It allows our customers to be very competitive, even with one-day turnovers,” says Lev-Ari.
Across the board, trends towards more sustainable options—less plastic—are all the rage.
Therefore, Danny Mertens, corporate communication manager, Xeikon, is seeing large growth in the use of paper-based materials and mono-material solutions that are easier to recycle.
“To this end, Xeikon introduced TITON toner, a new technology specifically designed for paper-based flexible packaging. TITON offers a unique combination of highly resistant, food compliant, and recyclable digital print that no other technology can match. It provides converters with a more sustainable way forward in digital flexible packaging production,” says Mertens.
In addition to excellent materials handling and 1,200 dpi resolution printing, Xeikon presses use toner technology that stands out from the competition due to its guaranteed food safety, which meets FDA regulations. “This makes it suitable for cups for hot and cold drinks, ice cream, popcorn, candy, and other snacks. With short production and fast delivery times of low minimum order
quantities, personalized or branded cups become a possibility even for small brands, cinemas, theaters, shops, or local events.”
In fact, a very successful application is digitally printed paper cups. “Paper cups is a fully developed solution that is offered in cooperation with Xeikon’s network of Aura Partners covering all print media, software, consumables, and equipment,” adds Mertens.
A die cutter is one of the most important pieces of finishing equipment for those looking to add folding carton packaging. We dedicate an entire article to die cutting in October, but here we present some specific information as it pertains to digital folding carton production.
Juan Kim, CEO, Valloy Incorporation, points out that only five percent of the market has migrated to digital in packaging, a number quite low when compared to segments like signage and commercial print. “However skillful operators for analog printing and cutting are getting older and younger people do not want to learn those analog machines, so there’s no other way to move to digital solutions. Production costs are higher at the moment.”
Automation is the way of the future in finishing, and Valloy’s new DuoBlade FX features full automation and offers a special PERFECT CUT algorithm. “It is tracing the exact path of cutting for dragging knives by true simulation, not just simple offset compensation like others.”
The machine has two actuating heads, which means operators can put the same tools or different tools for each. “If you put cut knife tools for both heads, production time can be doubled for kiss cutting or full cutting. If you put different tools for each, you can do kiss cut and full cut at the same time.”
Kim points to pharmaceutical products as one of the prime industries moving to digitally produced packages now. To meet their rapidly varying amount
and contents of the package, variable data is key.
The MBO Group, which is part of Komori, provides a die-cutting solution that Martin says offers makeready, productivity, and waste characteristics that match the digital print market. The BSR550 fits the most common B2 sheet size and uses low-cost flexible magnetic plates to die cut, score, perforate, emboss, and texture the sheet in one pass. Makereadies are made in only a few minutes with no die test striking and shimming is required.
“Furthermore, internal and matrix scrap is stripped away automatically so it is ready for folding and gluing or any other final finishing step. The stripping process is nickless, which creates a very clean edge fitting the insert, point of purchase, and blister pack market well. For folding carton work, digitally printed sheets can be loaded into the die cutter feeder and in a single pass can be die cut, scored, perforated, textured, and blanked, ready to be finished,” says Martin.
The new market wants a fast turnaround on orders with low waste and consumables, contributing to a lower carbon footprint. “Because it is B2sheet size, many common products in the pharmaceutical, medical device, cosmetic, and electronics markets fit multiple-up on the sheet. Most products in this segment use 18 pt stock or less, which also fits the BSR 550 well, and covering about 85 percent or more of the market. And with the larger sheet size and up to 12,000 sheets per hour (sph) speed capability, the die cutter can follow the customer into longer runs as they grow. This system really is agnostic to the print process of the sheet and it works as well for analog technology as it does for digital technology,” he offers.
Rollem International also offers a die cutter. Corwin points out that folding carton work is ideal for its Insignia line, which has been adopted by many printers, specifically for the purpose of moving into packaging and gaining access to
that high-value market. “With the ability to perform not only creasing, but perforating, folding, and gluing, carton work is handled with ease on the Insignia.”
The Insignia Series of die cutters are production-geared machines that handle both shorter runs and larger quantity output up to hundreds of thousands, depending on the job. Insignia will die cut, kiss cut, crease, perforate, and emboss a virtually unlimited number of products. The folder/gluer unit operates either inline or near-line with Insignia to provide uninterrupted finishing—flat sheet in, finished, creased, cut products are produced, all in one pass, with one operator.
“The Insignia’s setup and changeover time is quicker than competitors, the register is perfectly repetitive
forever with zero maintenance or potentialtofail; othersarereliantonelectronic componentswhichovertimewillnothold true;'statesCorwin.
Shealsofeelstheneedforskilledoperatorsdifferentatesanaloganddigitalfolding carton finishing. "Most analog technologies such as windmills or platen die cuttersrequireaseasonedoperatorwith knowledgeofhandlingtheheavyironmachines.A digital die cutter as such does notrequireahighskillleveltooperatethe unit.Someexperiencewithmachineryis aplus,butmostoperatorscanbetrained withinafewdays.Mostskilledoperators are aging out of the industrywith no replacementsinsight;'saysCorwin.
She points to job changeovers and makeready timeframes as another important differentiator of modern die cutters. "Utilizing either single or sets of male/female flexible dies, these dies are relatively easy to adhere and remove from the magnetic cylinders.
A 20 to 30 minute set-up on the Insignia rotary die cutter eliminatesdowntimeandincreasesproduction."
Tooling is another consideration. "Creating flexiblediesforarotarydiecutterinvolves prepressAdobe InDesign knowledge with just a slight learning curve required.Theartworkissentouttoone ofmanydiemakerswhocanturnthe dies around within a few business days.Theentireprocessismuchfasterthanproducingsteel-ruledies."
Thesustainabilityfactorismoreprevalenttodaywithmovementtrendingaway fromplasticpackaging."Thedemandfor paper-basedcartonsacrossallsegments continues to increase even in the food category with the development of safety testedcoatedcartons,"offersCorwin.
Gettingahigh-qualityprintisonlyhalfof the battle when it comes to folding cartons.Automationplaysanessentialrole.
For digitally printed folding cartons, Sautersaysshortrunsneedautomation. "This is the credo for KAMA'.s finishing solutions and the guideline for further development. Having focused on shortrun finishing solutions as a machine manufacturerforwelloveracentury,we haveexperienceonalargescaleandare also well ahead in the field of automationforfinishingdigitalprints."
Sauter sees two distinct differences when comparing digitally printed folding cartons with analog. The first is
COMPAN ES MENTIONED d.di�JJl Seepage21 for more information.
maintaining accurate registration from printtocuttoensurecustomersatisfaction and brand integrity. "KAMA'.s AutoRegister AR3 on the ProCut 76 Foil ensuresthehighestprecisionof0.1 mm for digitally print sheets and is capable ofaligning even twistedsheets precisely with its skew adjust function. That is howwecanapplyhotfoilstamping and tactileeffectsin high-end qualityondigitalprints."
The second is the importance of quality control in digital printing because every sheet and every blank can be different. "The KAMA workflow solves the challenge with inspection and ejection of defects in the FlexFold 52i folder gluer with different inspection levels depending on the type of folding carton-highest level for pharmaceuticalpackaging."
KAMA offers a complete finishing workflow for short-run folding cartons after printing-from die cutting, creasing, stripping, and blanking-all on the ProCut 76 Foil Packaging Edition as well as folding and gluing on the automaticFlexFold52ifoldergluerwiththe shortestchangeovertimes.
Advancementsindigitalprintingtechnologies as well as the finishing equipment designed to support them in the area of foldingcartonproductionissuretomake animpactinthisspaceoverthenextfew years.Thedemand forhigh-value,shortrun solutions is ideal for testing new productsandmarkets,onshoringanddestocking, and often support environmentalinitiatives.
"Digital print offers brands the flexibilitytoreact quickly tothe market with highly customized jobs printed just-intime with multiple SKUs on standout, specialized media, with brand protection,"concludesLev-Ari.
For more on digital folding carton production,checkoutourwebinaronthe topic,dpsmagazine.com/webinars.dps