

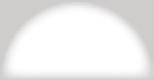
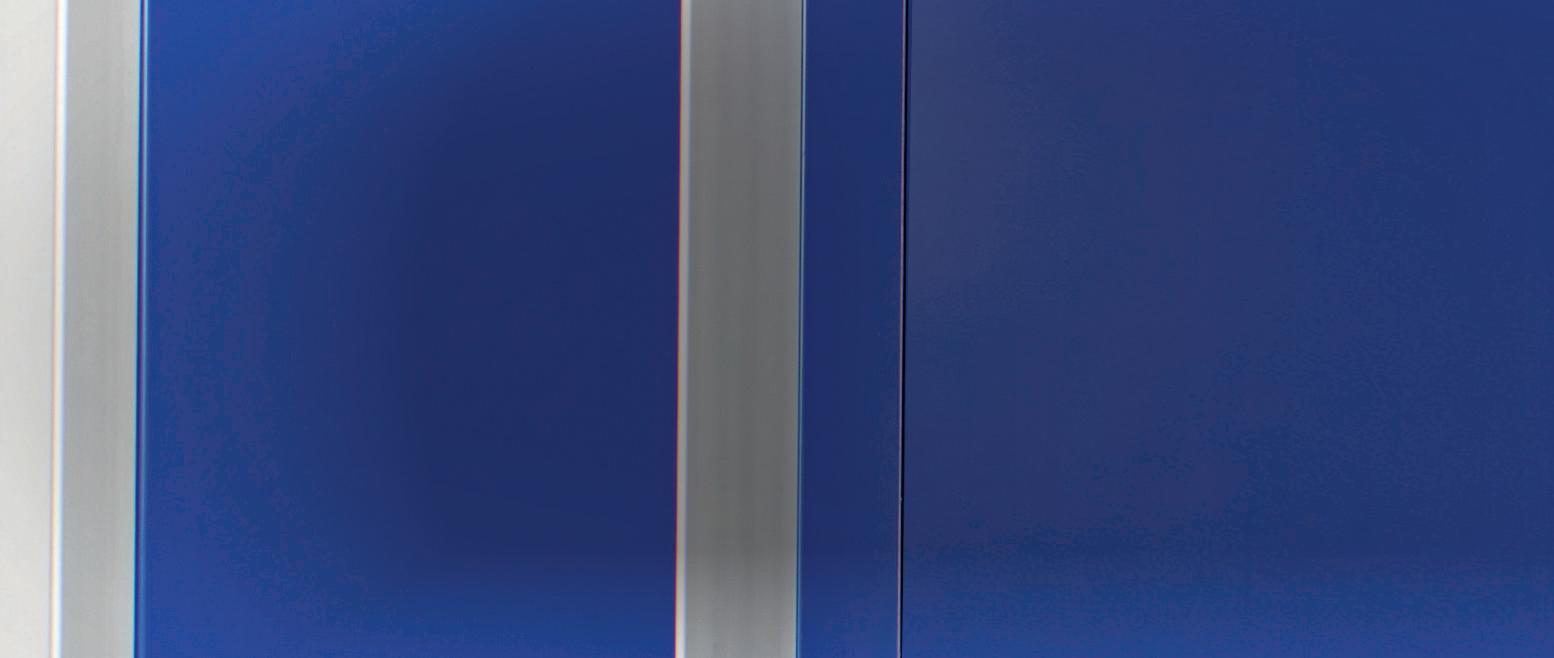
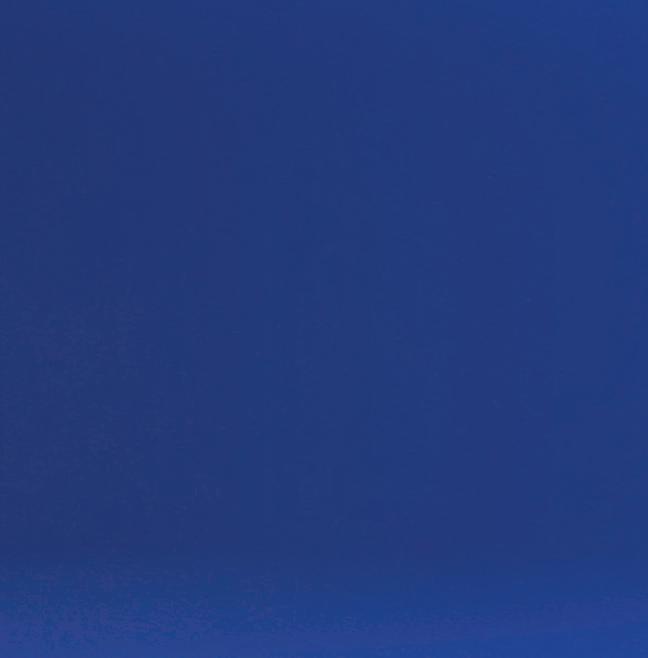

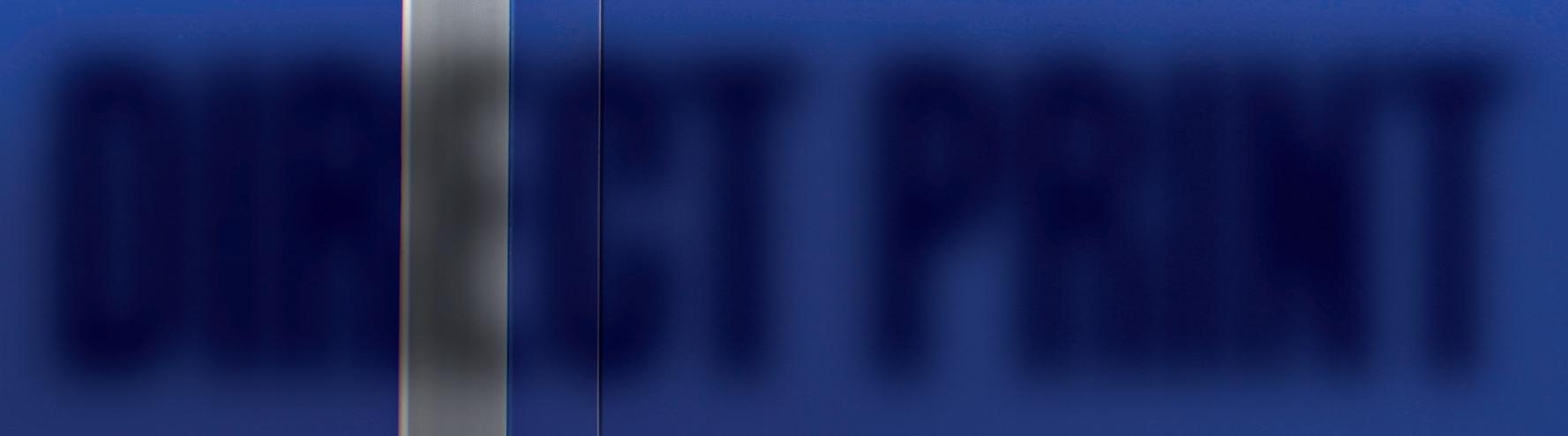

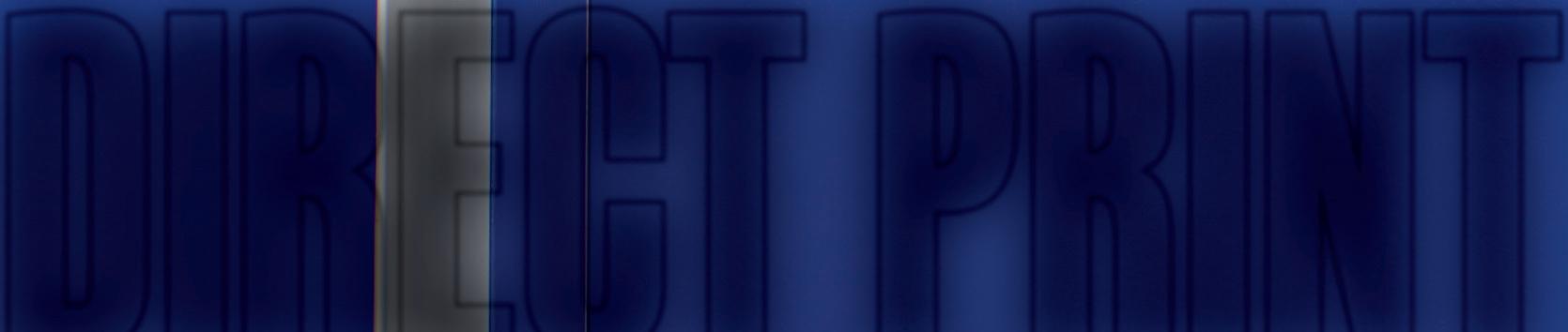
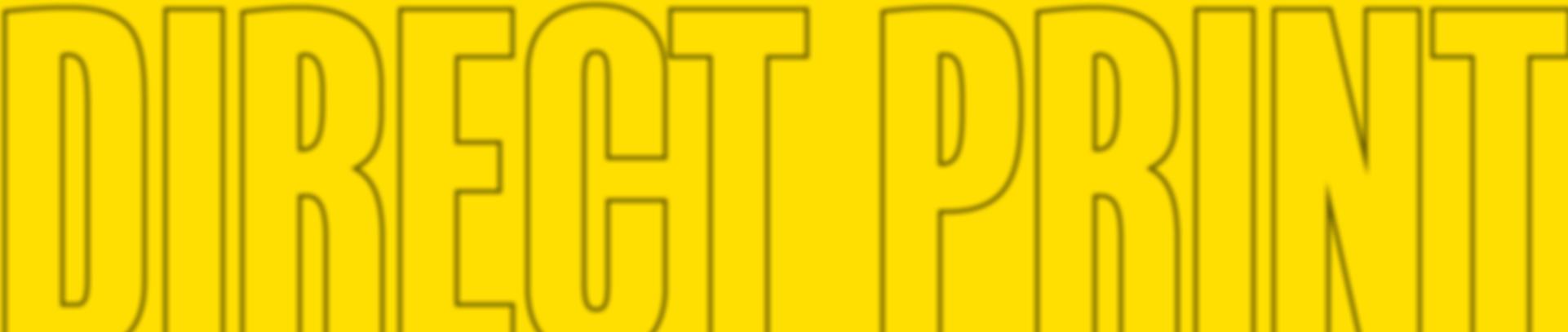





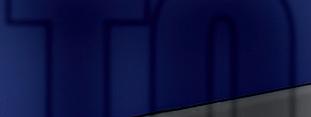
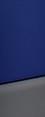


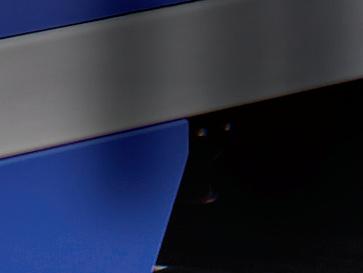
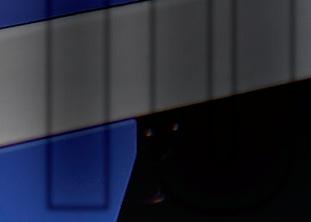





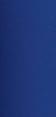



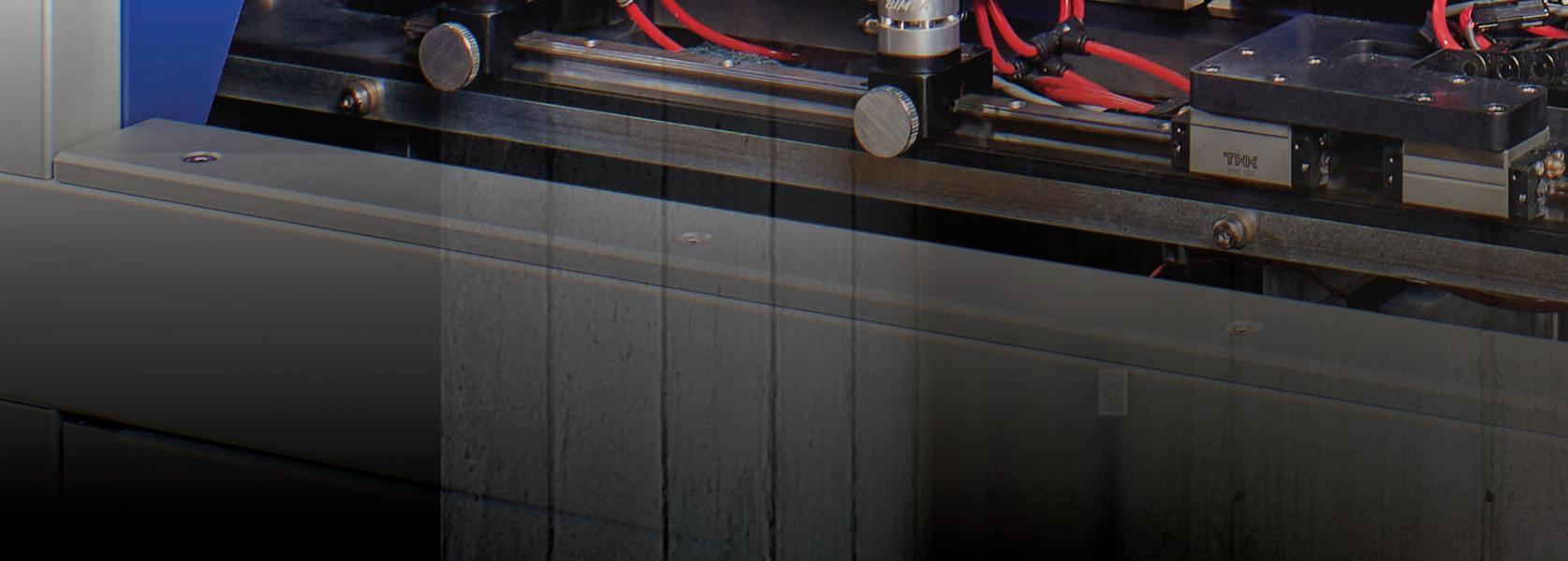

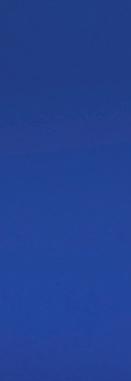
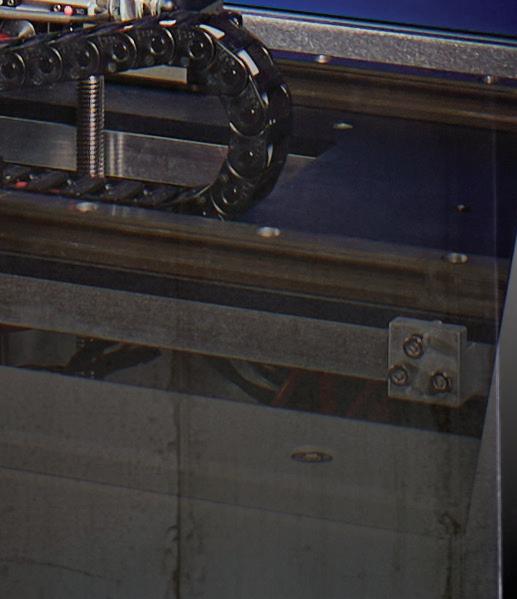
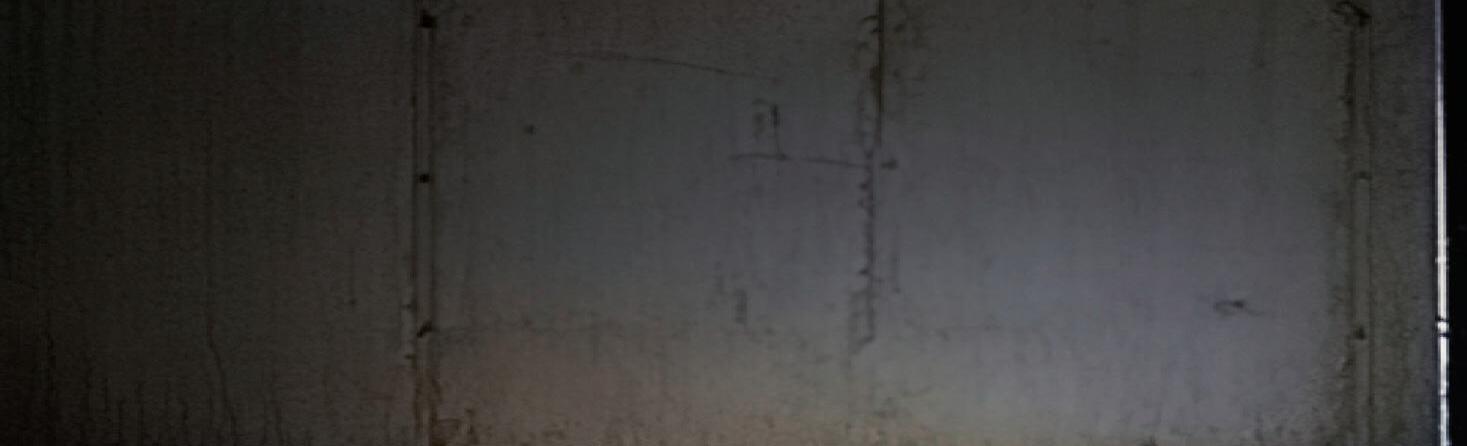
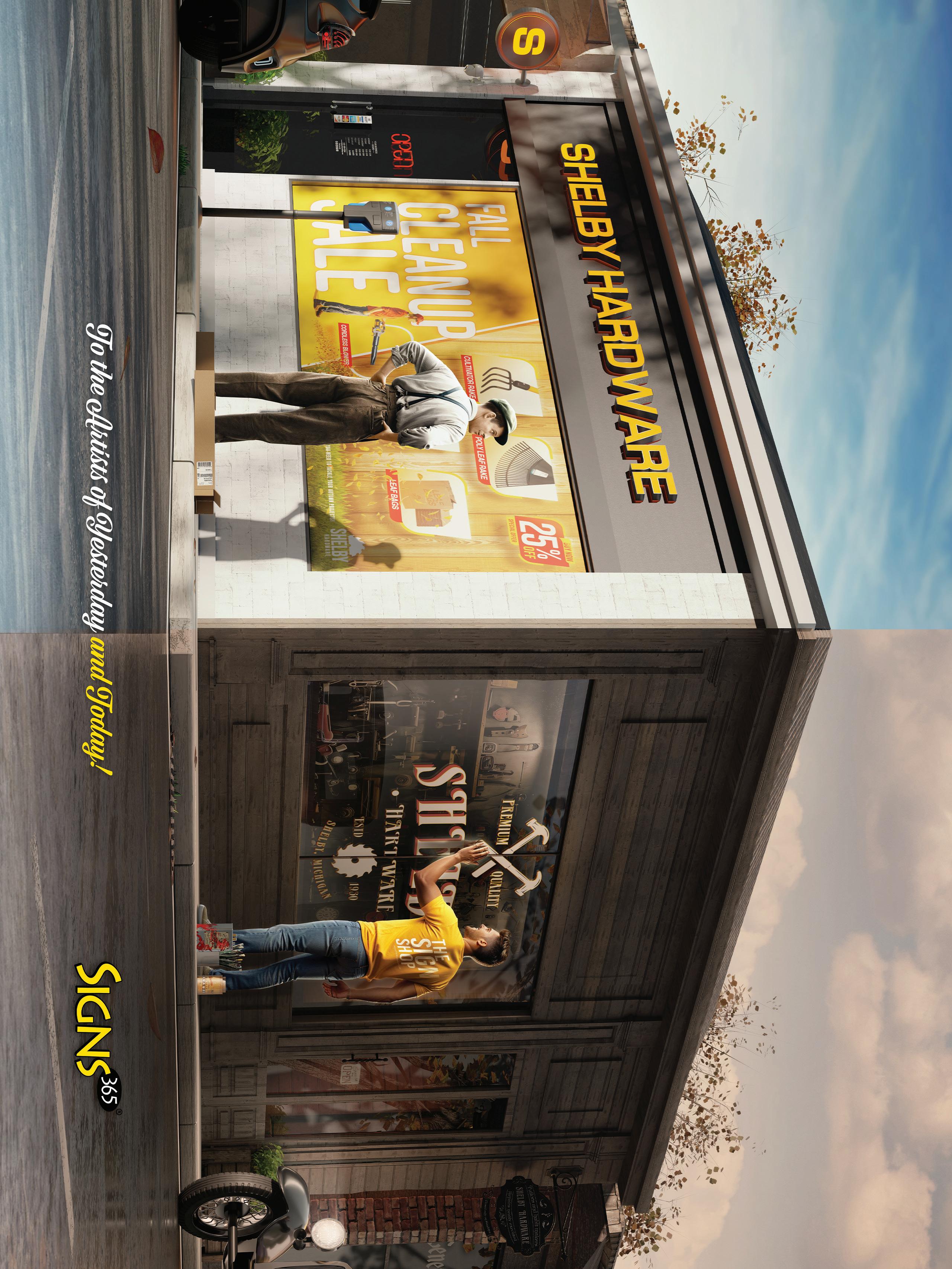
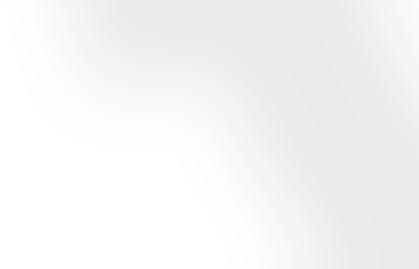
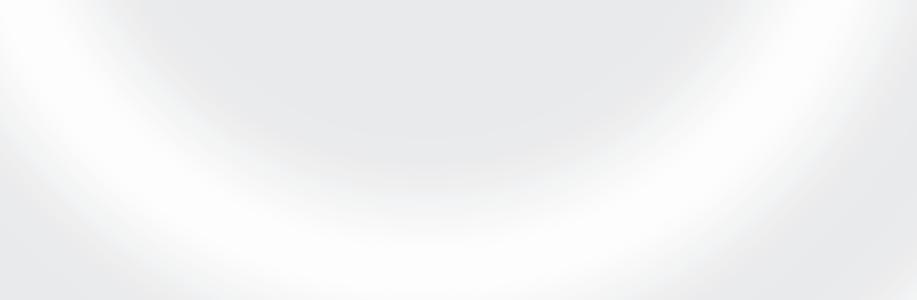
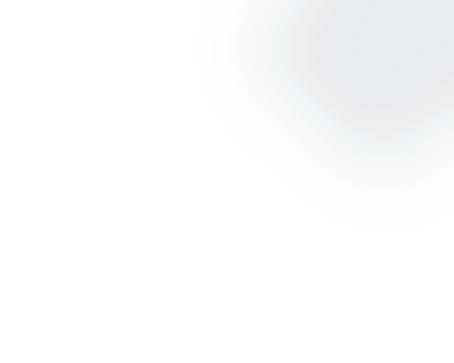

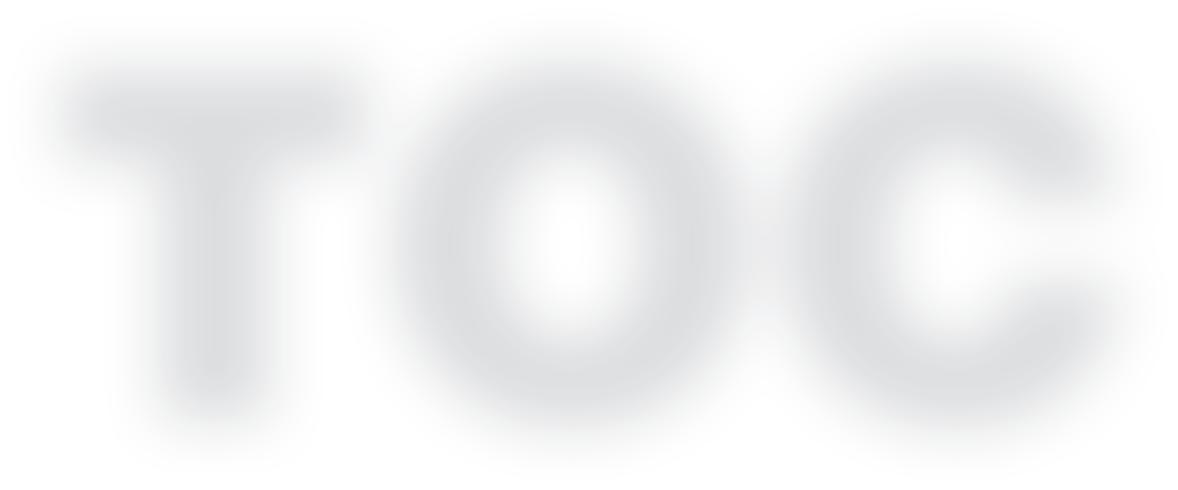
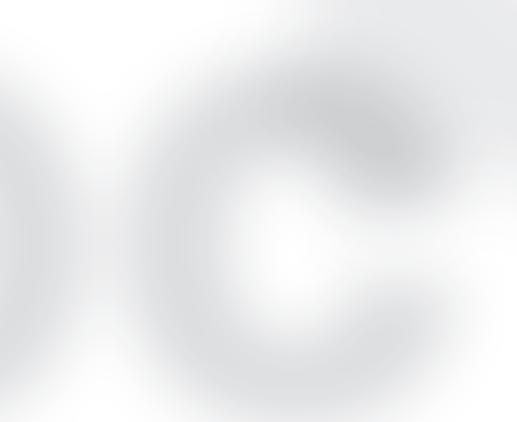
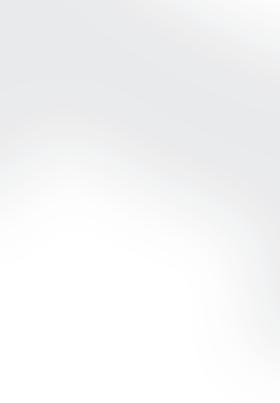
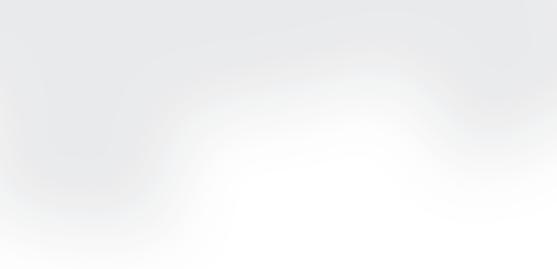



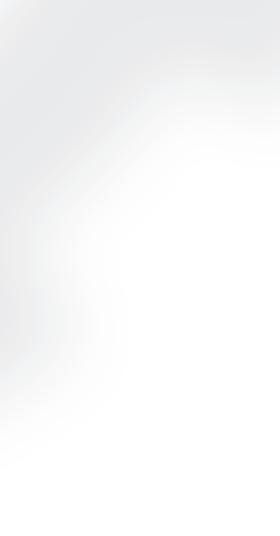
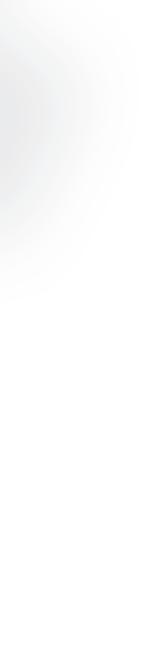
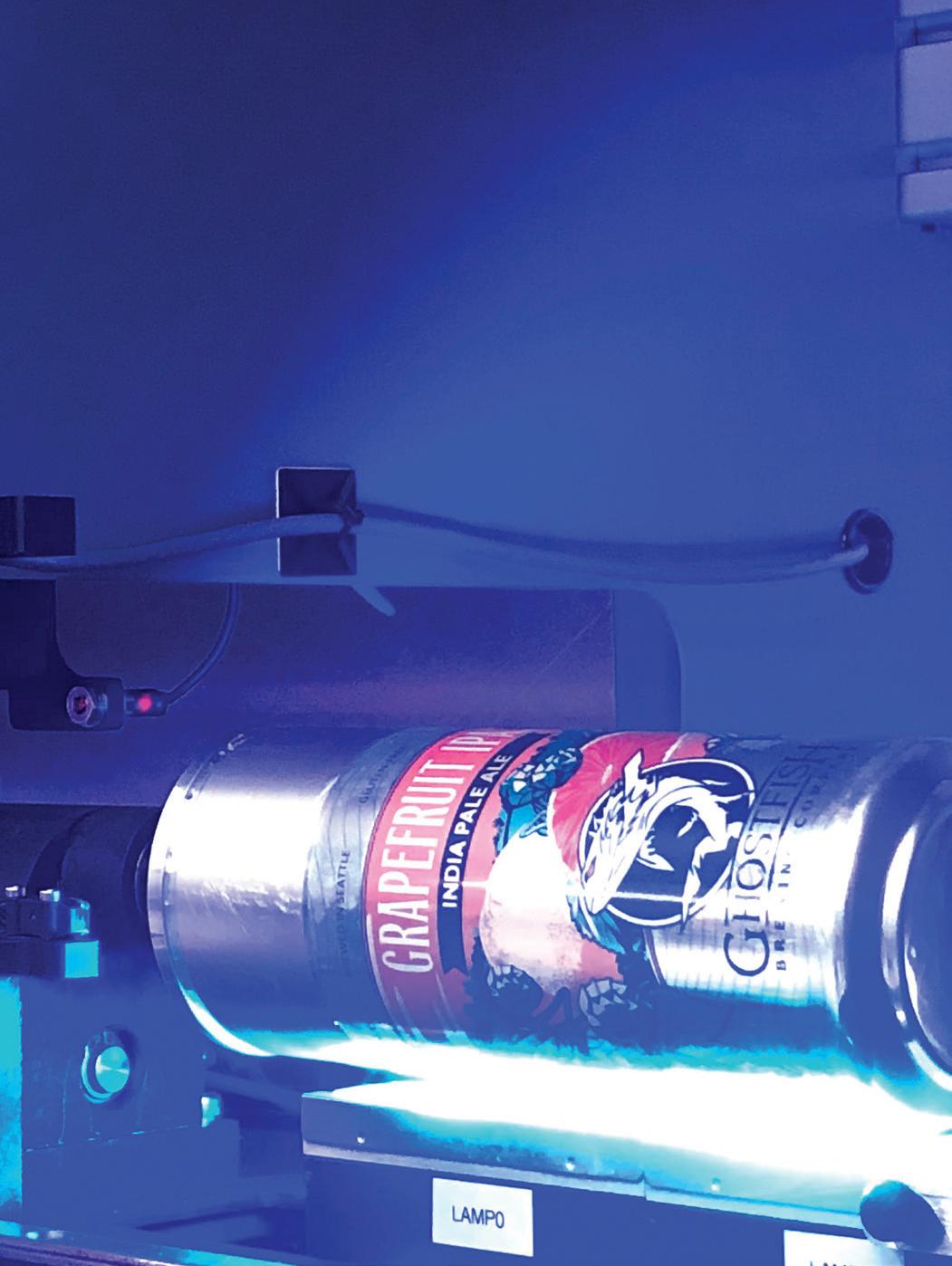
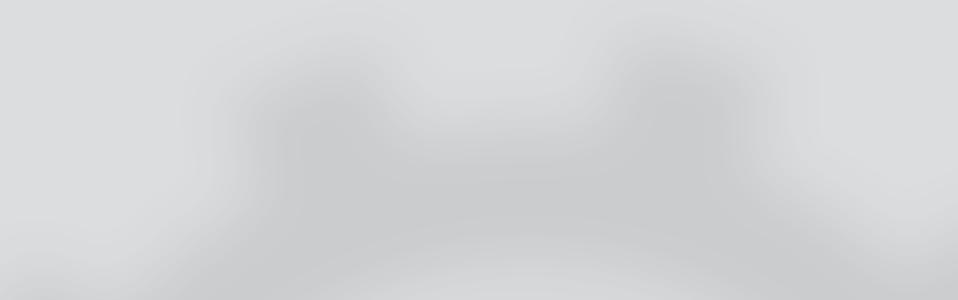

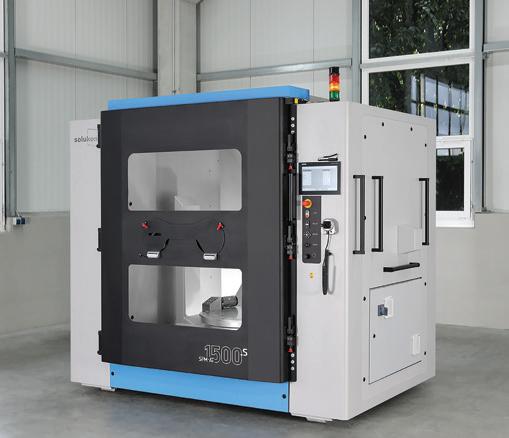



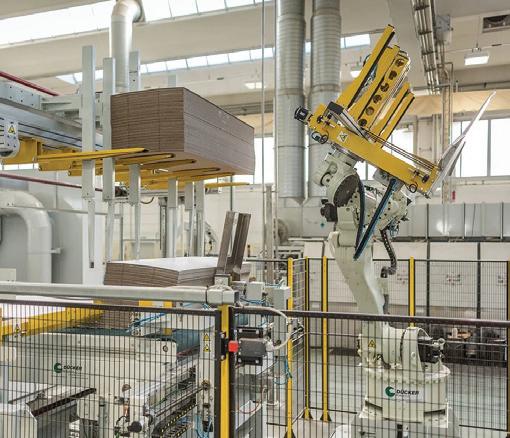

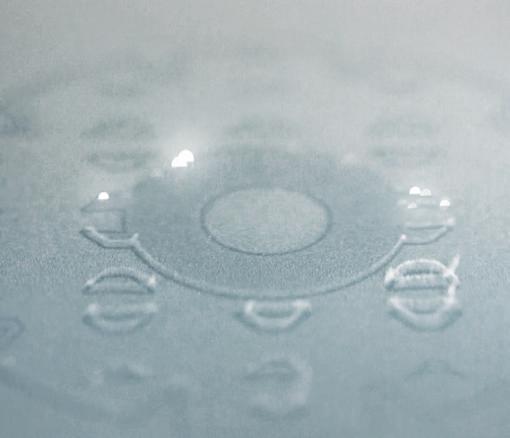

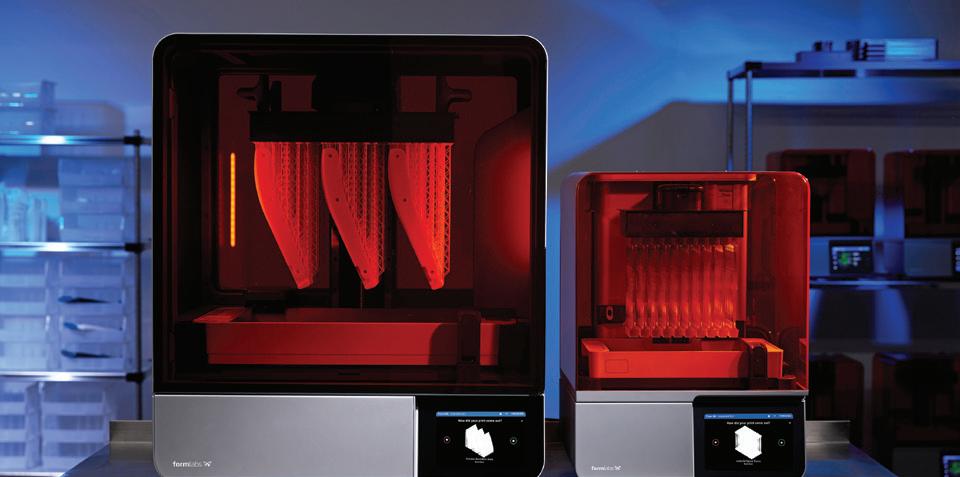

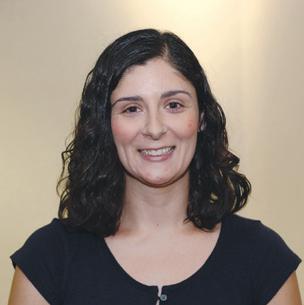
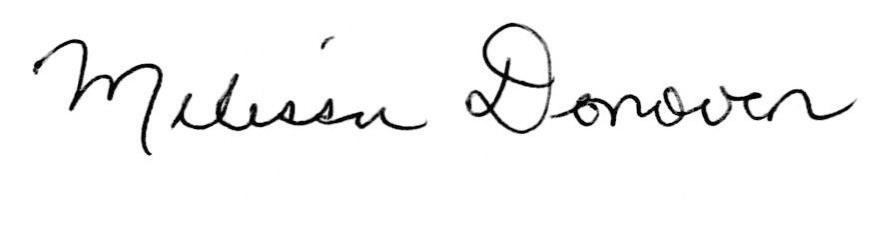



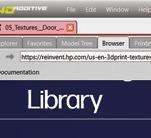
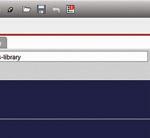
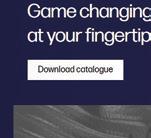
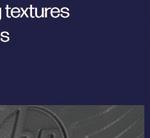
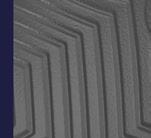
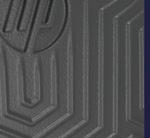
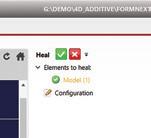

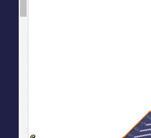
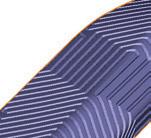

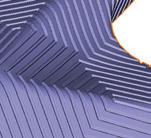
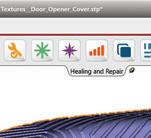
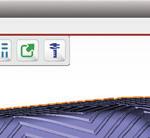
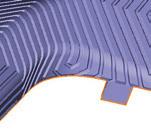
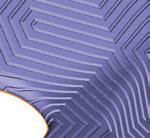
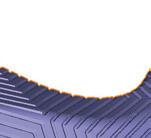
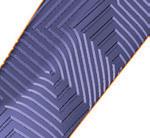
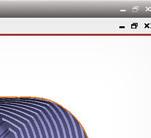
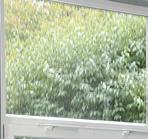
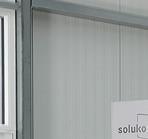
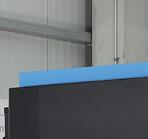


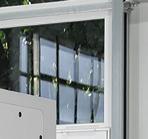
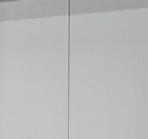
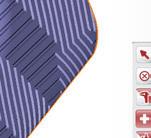
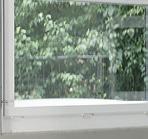
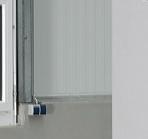




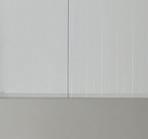


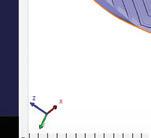
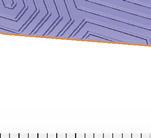
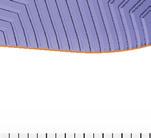
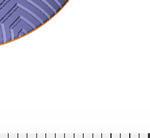


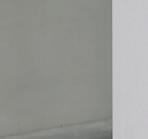

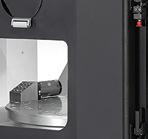
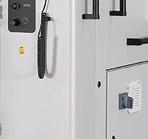
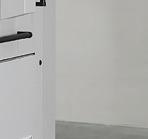
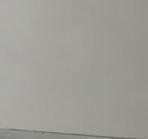
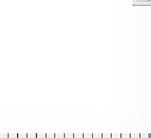
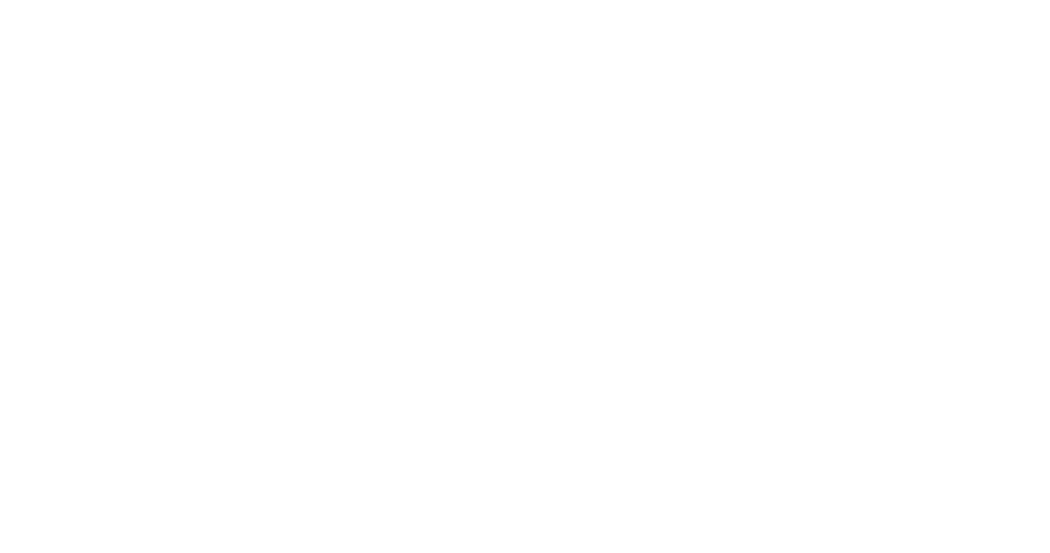
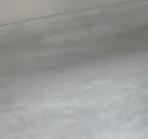
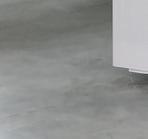
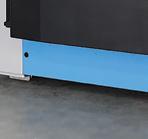
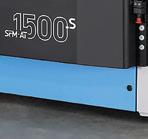
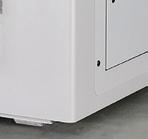
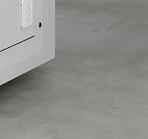
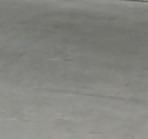
METEOR INKJET LAUNCHES METVISION
Meteor Inkjet Ltd expands its offerings with the launch of MetVision, software for machine vision aided nozzle status detection and correction; and streamlined printer configuration and calibration.
The ability to accurately detect misfiring nozzles in inkjet systems is of crucial importance to OEM print system builders. Poorly performing nozzles can result in print quality issues, printer downtime, and product waste. These difficulties can be especially problematic and costly in industrial environments. Meteor’s MetVision software not only paves the way for machine vision solutions to these problems, it offers streamlined system configuration and calibration capabilities.
MetVision software facilitates the creation, detection, and analysis of test patterns. Designed for production environments, MetVision works with Meteor’s complete suite including MetPrint, MetScan, and MetIndustrial. #154
DENTAL 3D PRINTER FROM PRODWAYS
Prodways announces its latest three-dimensional (3D) printer range the DENTAL PRO Series. Designed specifically to meet the evolving needs of modern dental laboratories, this new range of 3D printers using Prodways’ patented MOVINGLight top-down digital light processing technology offers enhanced productivity, precision, and versatility for a range of dental applications. Capable of producing up to 72 denture bases or 55 aligner models in a single print run, this printer’s modular build platform up to 300x445 millimeters guarantees optimal production output.
The dental industry is constantly evolving, and dental laboratories require solutions that can keep pace with growing demands for speed, accuracy, and high-quality results. The DENTAL PRO 3D Printer delivers on all fronts, offering cutting-edge technology that simplifies workflows while ensuring superior accuracy for even the most complex dental models. #155
FORMNEXT CHICAGO POSTPONED
The organizations behind Formnext Chicago formally announce the postponement of the show, which was due to launch April 8 to 10, 2025, at Chicago, IL’s McCormick Place.
“In light of the current market conditions, the structural dynamics of additive manufacturing (AM), and scheduling conflicts with another AM show, it became increasingly difficult for us to host a successful and impactful event,” says Douglas K. Woods, president, The Association For Manufacturing Technology, which organized the show with Mesago Messe Frankfurt and Gardner Business Media. “After careful consideration, we believe that postponement of Formnext Chicago is the most responsible decision under current circumstances.”
The objective of Formnext Chicago is to bring together the entire AM and industrial production ecosystem in North America, expanding the success of Formnext in Germany. #156
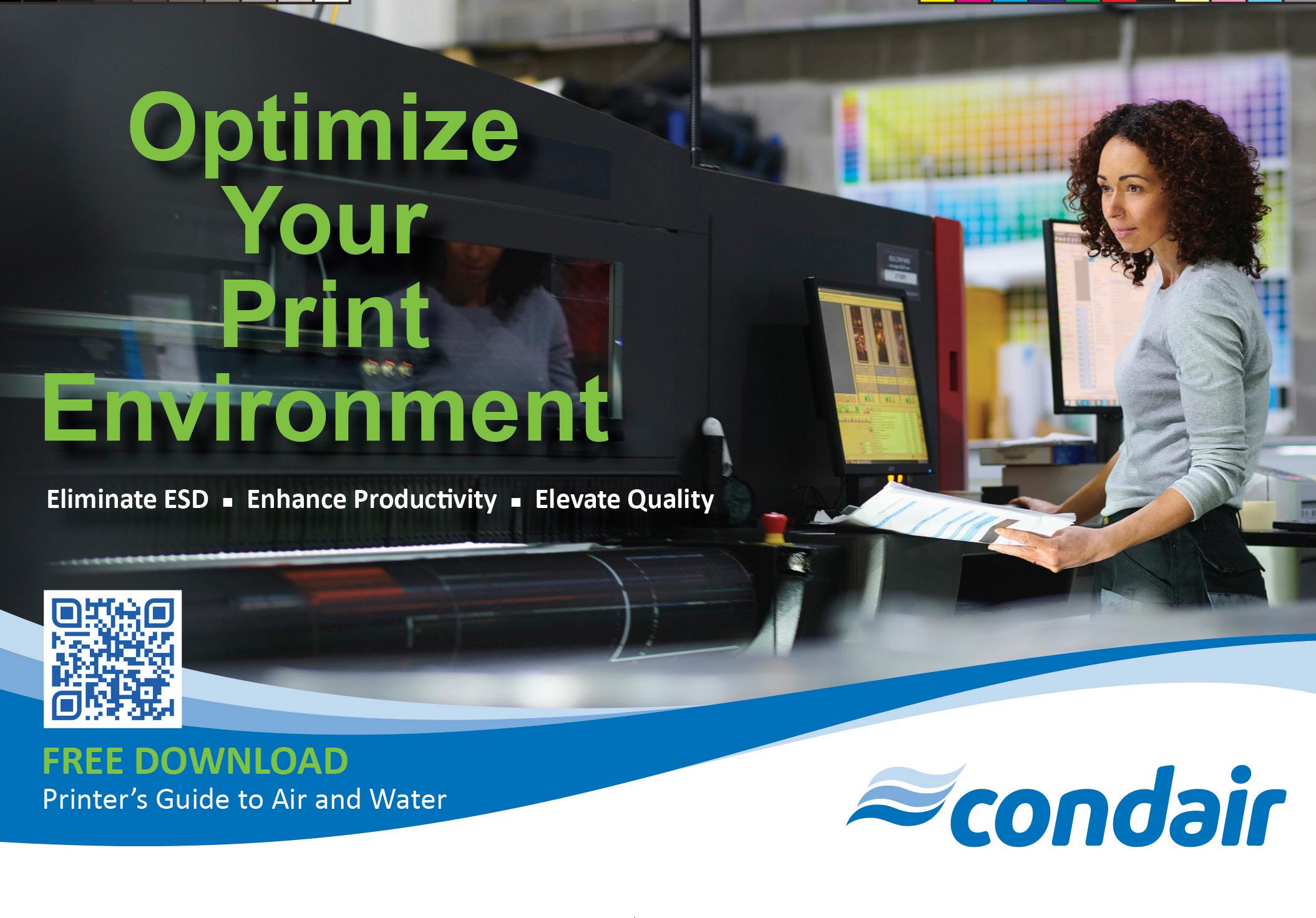
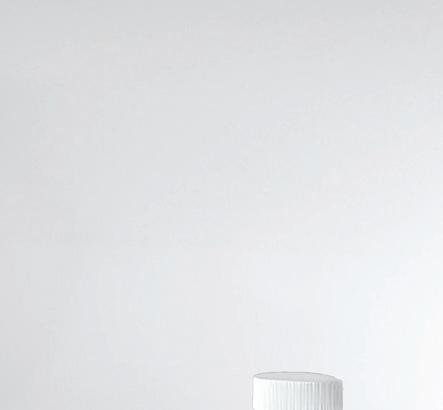


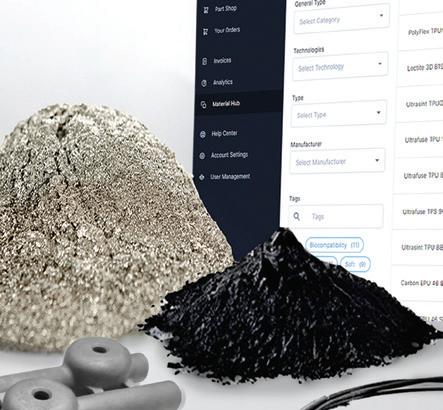


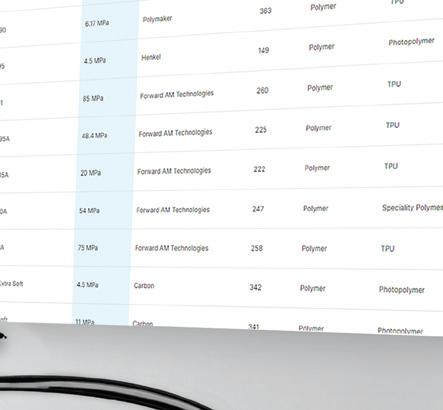
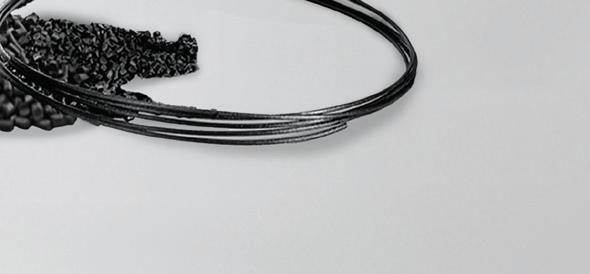

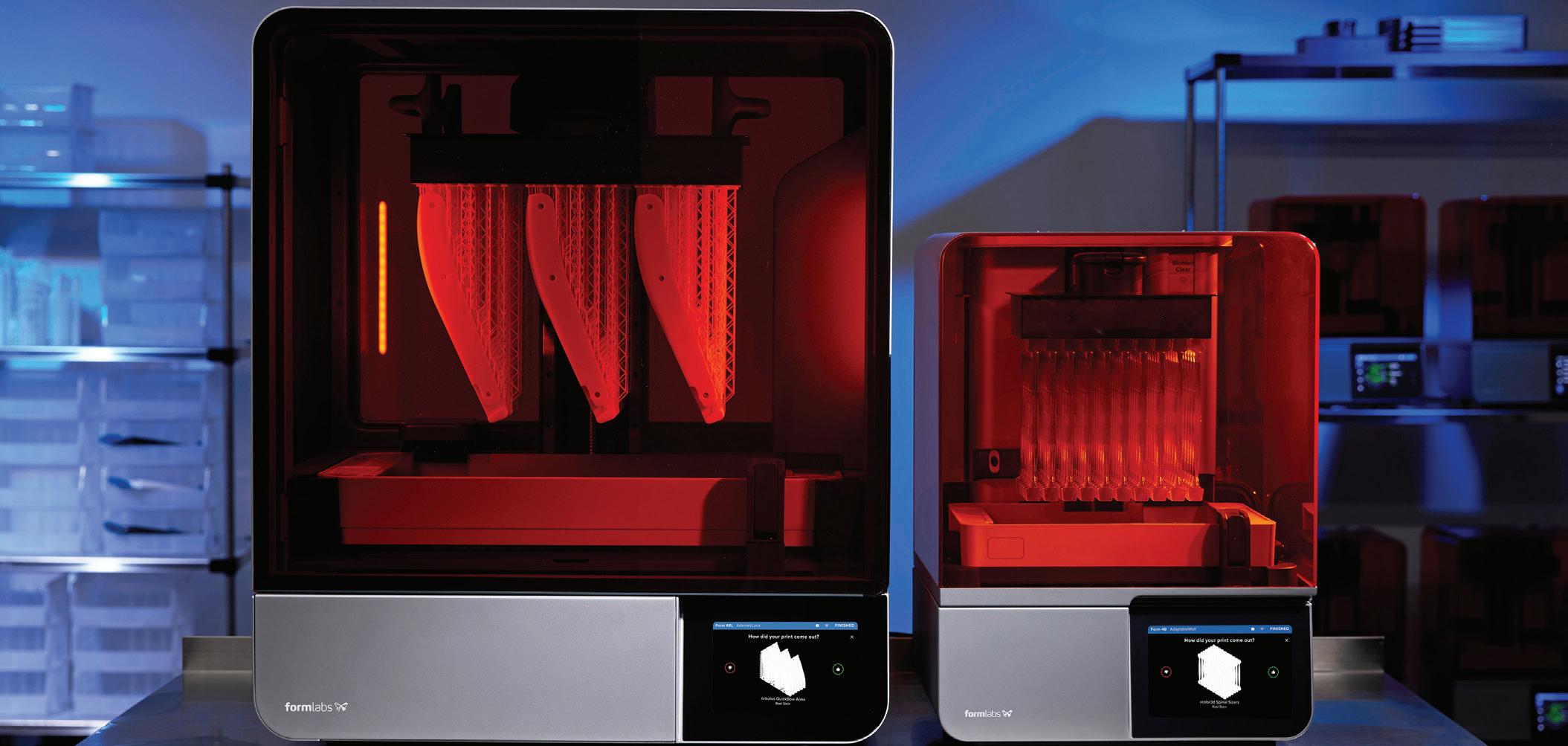

Cubicure GmbH, hall 11.1, booth E38, represents hot lithography technology with its Caligma 3D printing system, which quickly and precisely produces prototypes and small series made from polymers without the need for tools. Recent innovations include ThermoBlast, a 3D printing material that can withstand ambient conditions up to 300 degrees Celsius. INFO# 138
Formlabs, hall 11.1, booth C68, showcases Form 4L and the biocompatible version, Form 4BL, the company’s newest large format stereolithography (SLA) printers. When it was released earlier this year, Form 4 redefined professional SLA 3D printing, unlocking new levels of productivity with a 99 percent print success rate and five times faster speeds to deliver most parts in under two hours. With a five times larger build volume while maintaining Form 4’s fast speeds and reliability, Form 4L expands the possibilities of in-house manufacturing for large-scale flexible prototyping as
2. Formlabs, hall 11.1, booth C68, showcases Form 4L and the biocompatible version, Form 4BL. 3. Artec 3D, hall 12.1, booth G21, demonstrates the Artec Spider II 3D scanner. 4. Solukon, hall 12.0, booth D71, launches the SFM-AT1500-S.
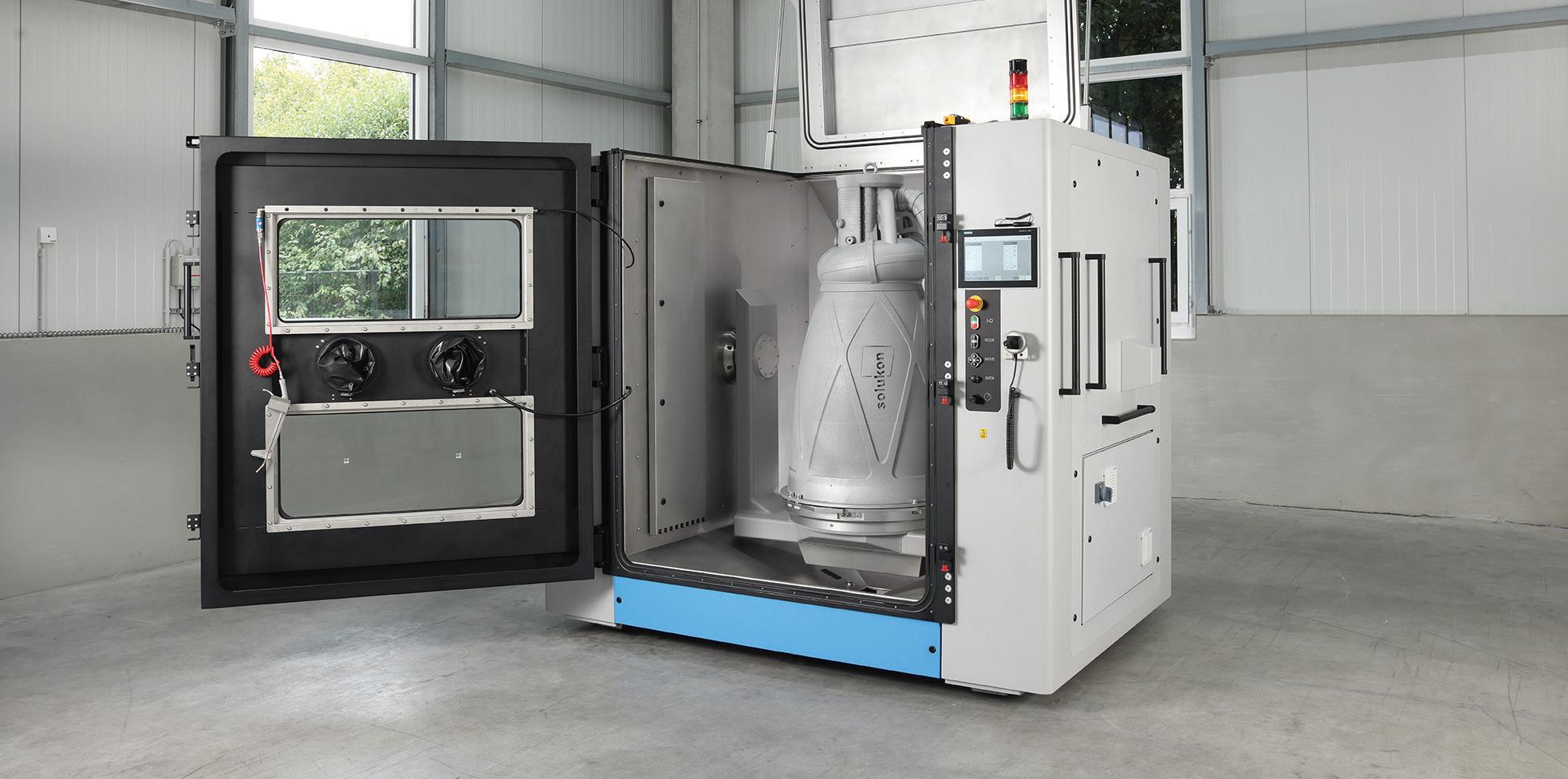
well as high-volume production. Formnext attendees can see both Form 4 and Form 4L in action with live printing and product demonstrations. Plus, Formlabs shows off its full lineup of materials, including new Nylon 12 White Powder and Nylon 12 Tough Powder. INFO# 139
Materialise, hall 12.1, booth C139, introduces upgrades to its software, which is designed to empower users with enhanced controls and customizations within its solutions. These updates allow users to leverage Materialise products in a way that best supports their applications and goals. With Magics, Materialise’s software for data and build preparation, the software development kit creates fully customized workflows to optimize for quality and printing time. It also introduces a feature that compares multiple part orientations pre-build to help users meet cost and quality needs. Additionally, Materialise announces a partnership to protect the intellectual property of printed parts in maintenance, repair, and overhaul. Finally, the company expands a collaboration that enables users to print high-performance geometries from massive design files as
well as offer booth tours centered on use cases that showcase AM’s capabilities in series production and certified manufacturing. INFO# 140
MMP Technology/BINC Industries, hall 12.0, booth D18, offers solutions for surface treatment. The deburring/
polishing method—known as Micro Machining Process (MMP)—technology, is a mechanical-physical-catalyst surface treatment applied to items placed inside a treatment tank. An innovative deburring and polishing process, MMP technology’s selective removal of






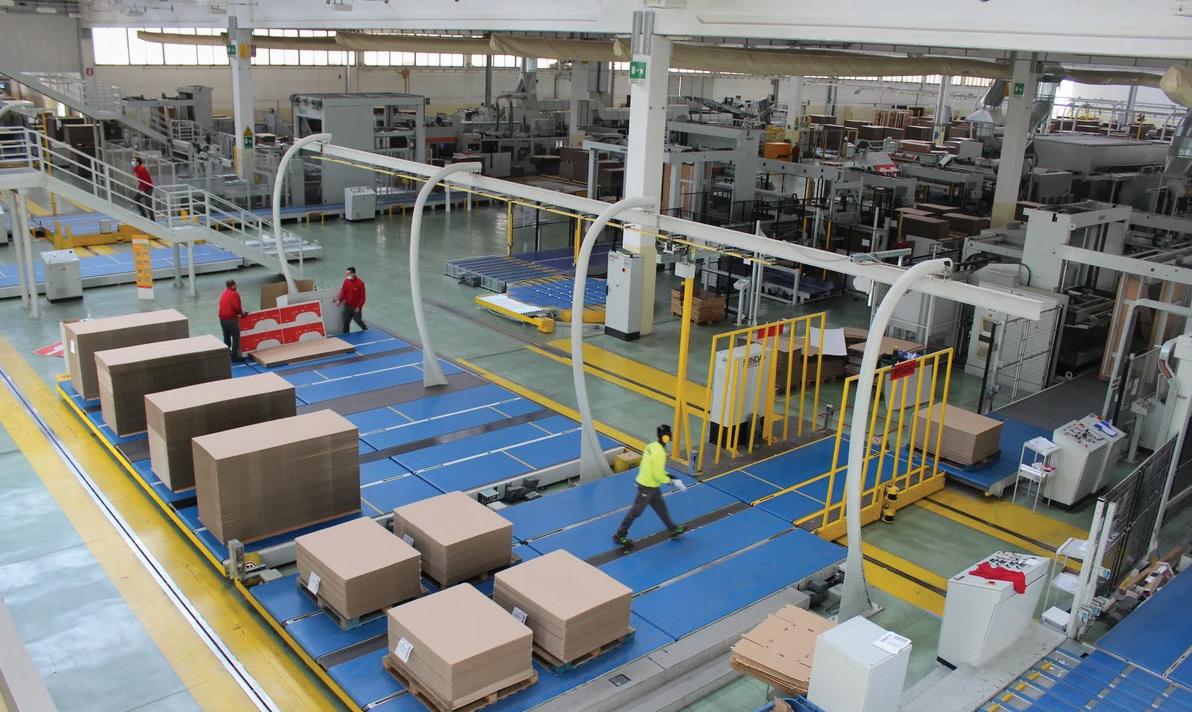
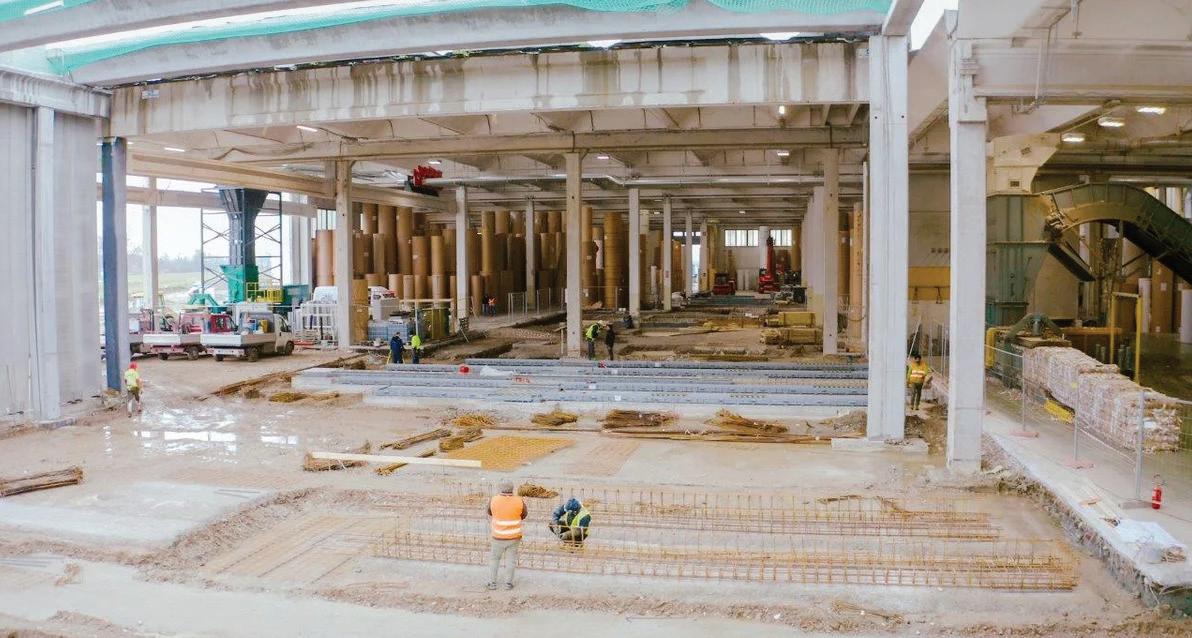




















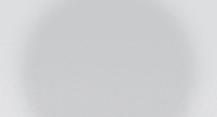

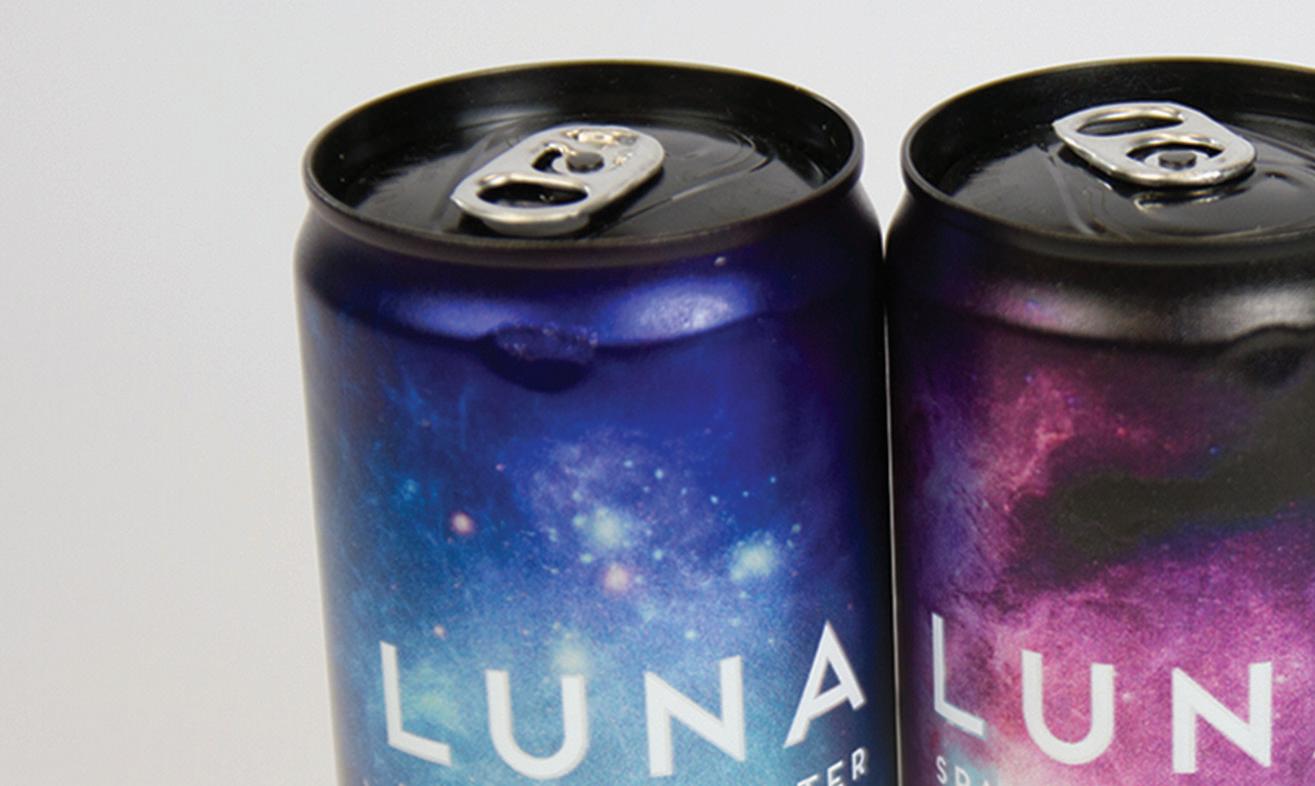









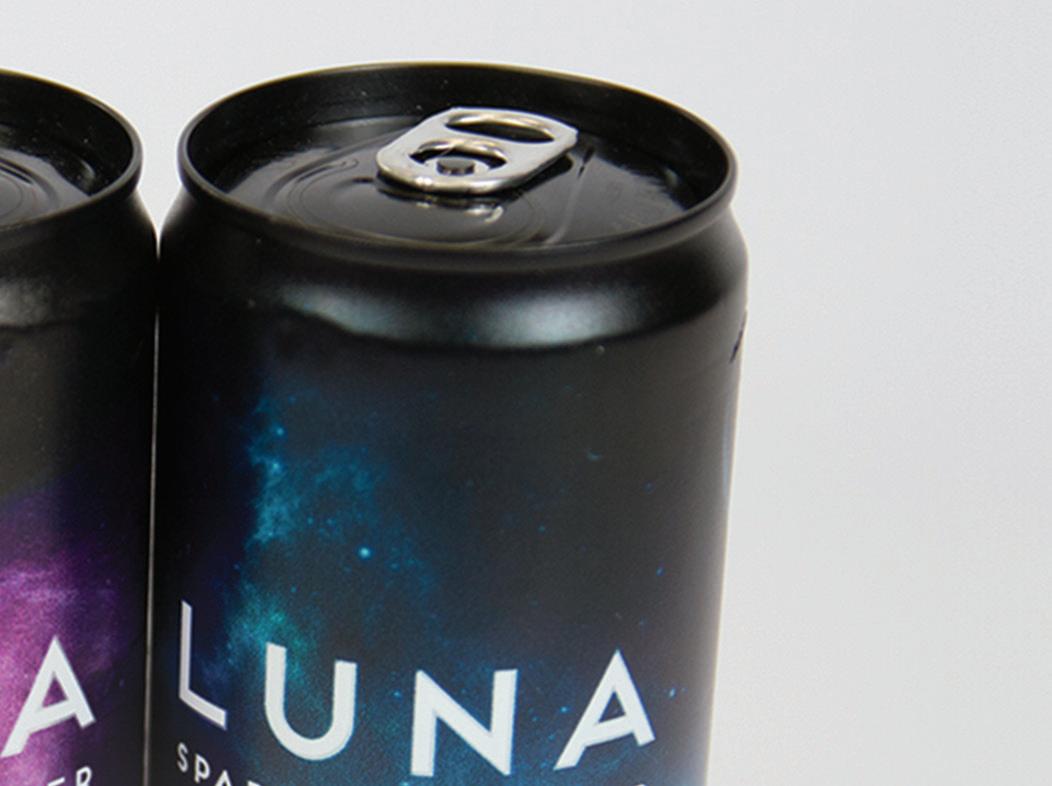





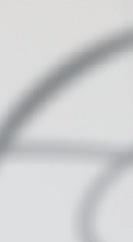
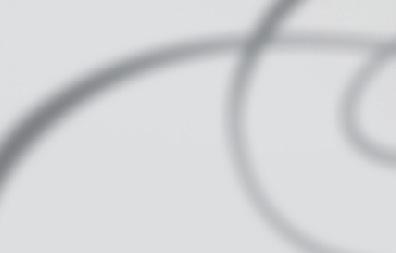

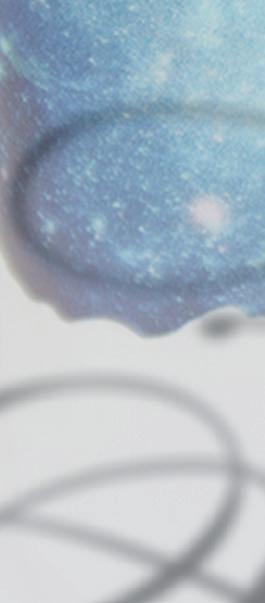













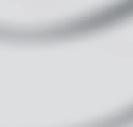





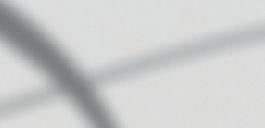
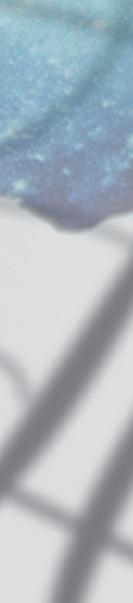

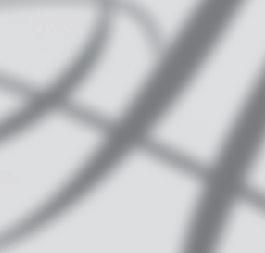




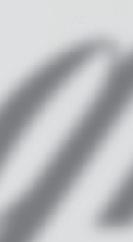
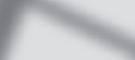
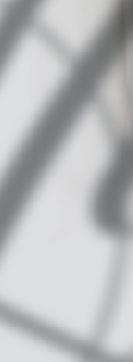



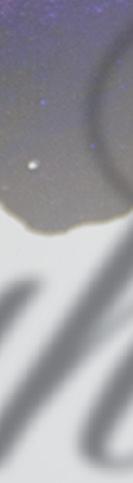
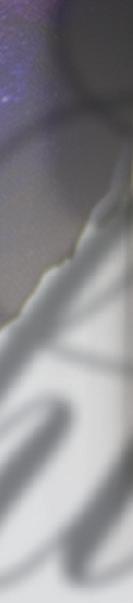


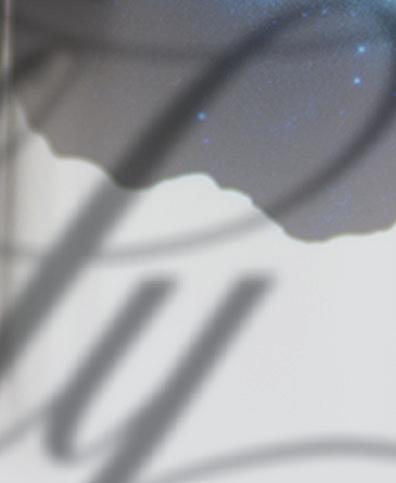

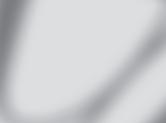










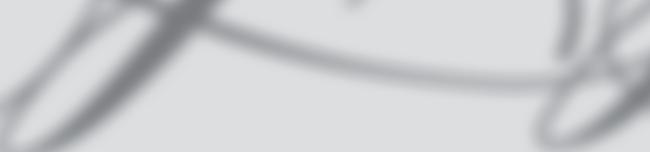



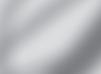

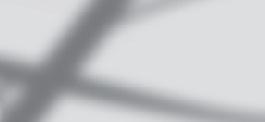


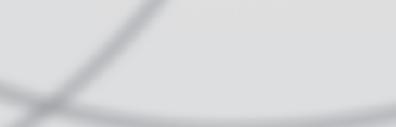
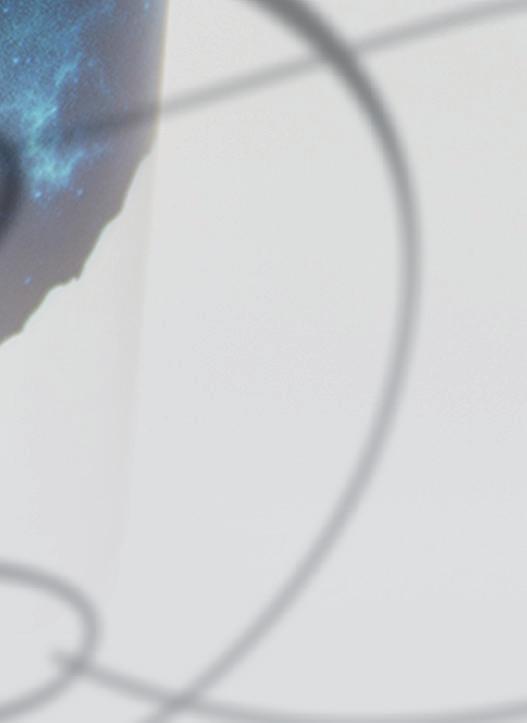
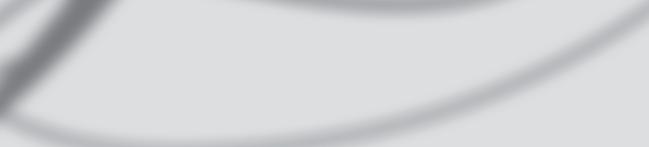



available, specifically UV printers, offer fast curing, no outgassing, and excellent ink adhesion. In most instances post-treatment processes aren’t required, further accelerating usage.
“Think limited editions, seamless wraps, variable text or names, texture
prints that you can feel, gloss or matte finish—these are all viable applications or effects when using a UV rotary printer, for example, to decorate cans. The possibilites are endless,” notes Michael Perrelli, sales director, Innovative Digital Systems.

Out with the Old, In with the New Traditional methods of labeling aluminum cans present increased setup times in addition to limited design flexibility. DTO digital printing shortens production time in many stages of the process while presenting endless design possibilities.
Mike Pecorini, sales manager - Midwest, West, South, Koenig & Bauer Kammann US, lists traditional methods of labeling as lithography, shrink sleeving, pressure-sensitive labels, and screen printing.
For long runs, “traditional decorators are offset printers, which apply spot colors at multiple stations at
1. Small to medium cylindrical inkjet printers such as the Inkcups Revolution can print up to 600 units per hour depending on image size. 2. Roland offers a variety of UV devices with rotary accessories that can print on aluminum cans and circular objects. 3. INX developed the CP800 digital proofing can printer. This system is designed for use by decorators or design houses to provide a digital proof for approval by customers or brands.
speeds of up to 2,200 cans per minute. They shine with limited changeovers and high volumes, thus minimizing cost,” explains James Bullington, CTO, LSINC Corporation.
“The traditional decoration process involves large production machines that form the actual can and an offset CMYK printing plate press to get the artwork on the cans. While this process is fast, it requires a significant amount of space, equipment, and money to operate and maintain,” admits Philip Chu, product manager, Roland DGA Corporation.
Moving away from higher volumes, pressure-sensitive or self-adhesive labels applied to aluminum cans are ideal for shorter runs. “The print quality and color graphics can be very good,
and you can apply features to labels such as metallic look, gloss, and matte to be able to customize the label. However, there are some disadvantages. The label can only be applied to some part of the can and does not produce a full coverage effect,” shares Paul Edwards, VP of the digital division, INX International Ink Co.
“A more recent trend is to utilize shrink sleeve label technology to apply the decoration. This has the benefit of applying full coverage where the can is not flat but is fully wrapped around, which gives it a higher quality look more akin to a standard decorated can. As with the self-adhesive label, good print quality can be achieved and features added in terms of the look,” continues Edwards.
Shrink sleeving also addresses the demand of shorter print volumes, but “with bans and restrictions issued in Canada and the EU on disposable plastics, such as shrink sleeves, an opportunity opened up for DTO digital printing,” shares Bullington.
DTO digital printing eliminates consumables like plates and screens, the production line footprints are smaller, and it is an economical process. “DTO digital printing offers high-resolution, full-color printing directly on cans without the need for plates or screens. It allows for quick design changes, customization, and reduced waste, making it ideal for both large and small production runs. This results in fast, more flexible, and sustainable production,” states Pecorini.
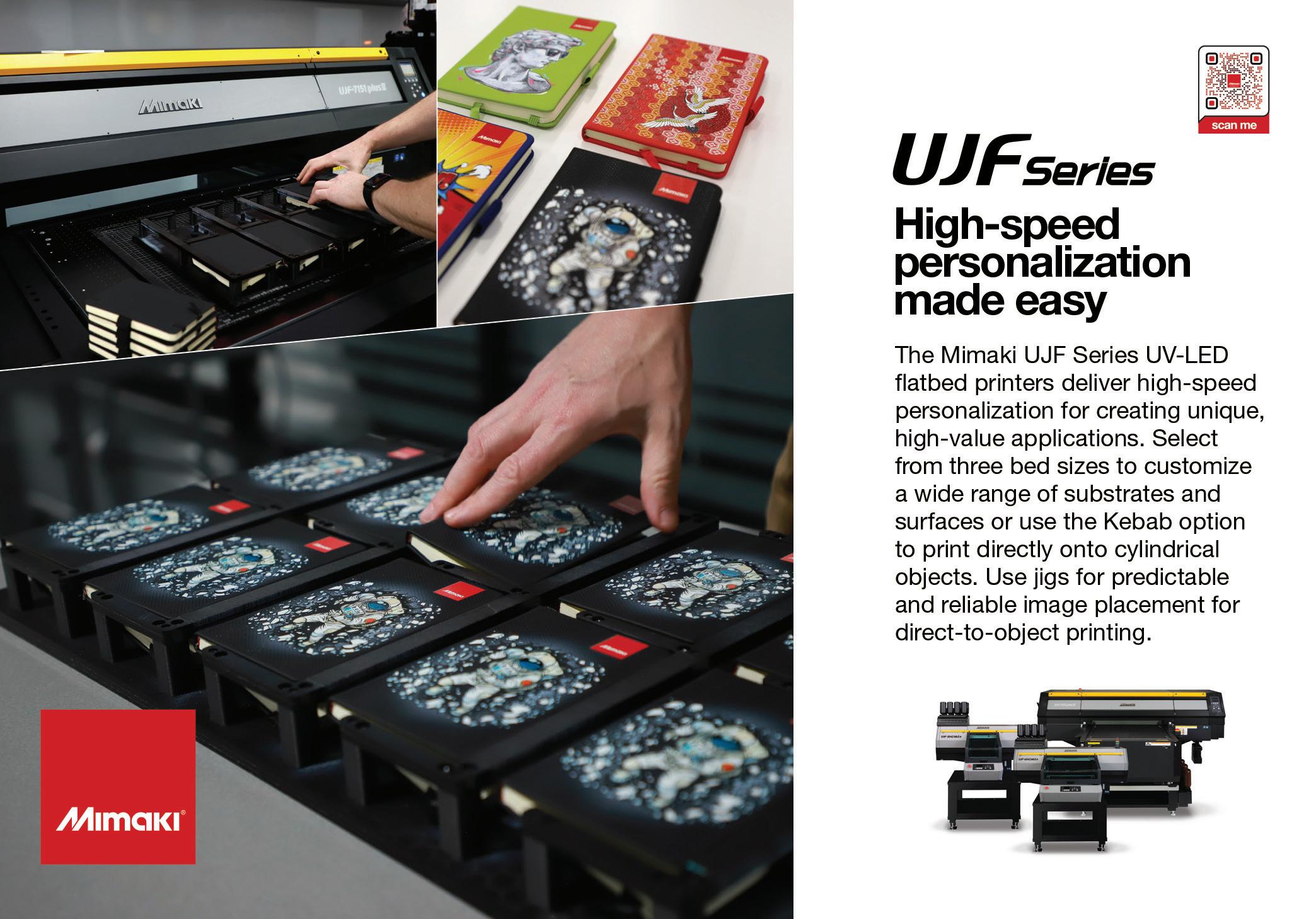
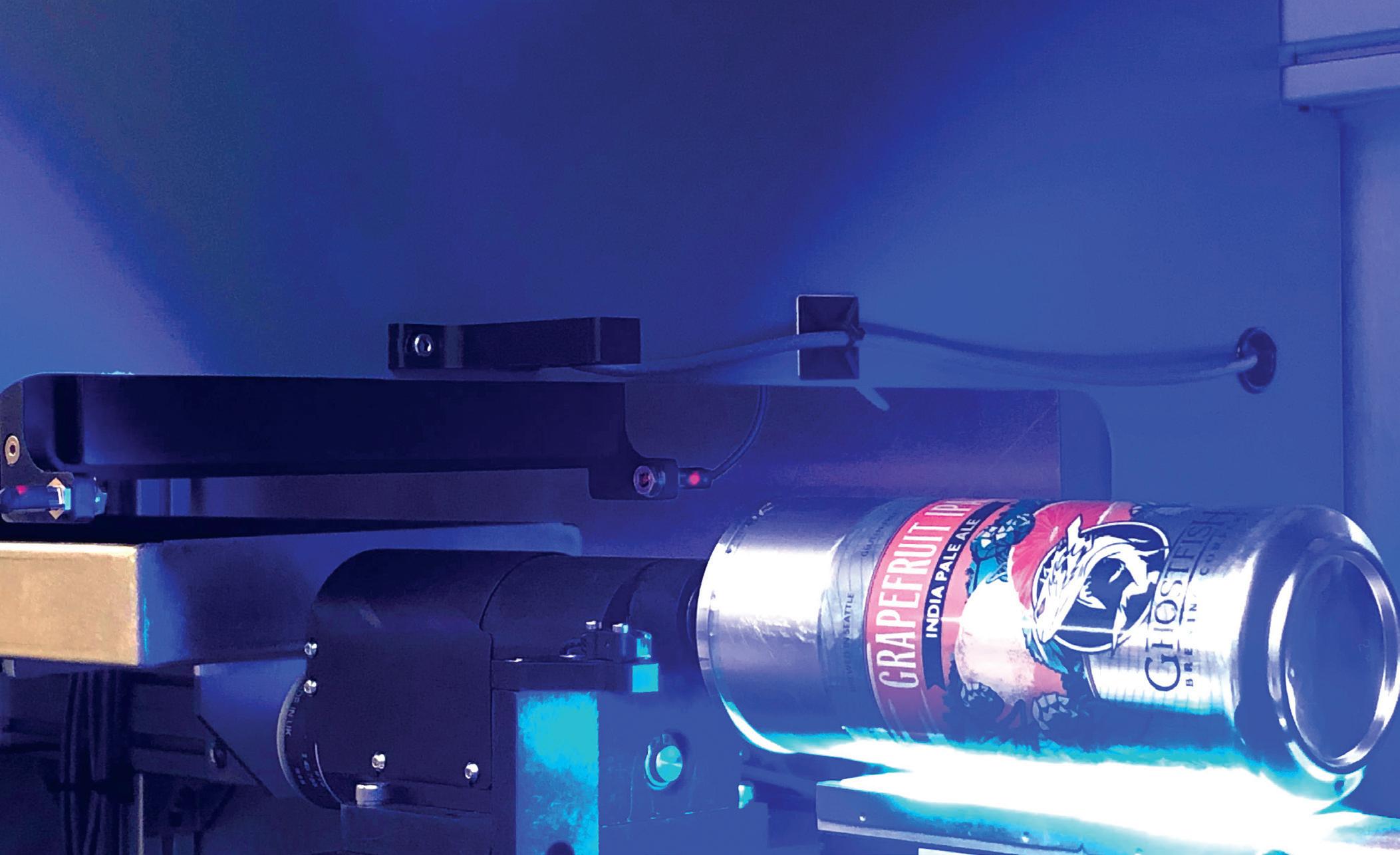
With DTO digital printing, users “can print a custom design with rich, bold colors and add unique textural and dimensional effects. The end result is an eye-catching product that can’t be done using the traditional/factory process,” admits Chu.
“Clearly, there are multiple digital label presses available today that can create short-run labels with a high level of personalization. However, you must consider the complexity of post print and the process for applying the labels after they have been printed
onto rolls. DTO can effectively print all cans with some form of variation if required,” says Edwards.
Another benefit of DTO printing is in the form of sustainability. “Given the strong recyclability credentials of aluminum cans, this is likely to become a strong selling point as both consumers and regulators look for packaging to become more sustainable. With supply chain sustainability also becoming more intensely scrutinized, lean inhouse packaging production options may now also be more appealing for
small- and medium-size manufacturers,” shares Gabriel Vallellanes, technical project manager, Inkcups.
Highest Usage
Beverage and craft brewers, reusable bottle manufacturers, personal care, and specialty food products all currently utilize DTO digital printing for aluminum cans.
According to Pecorini, beverage and craft brewing industries are the biggest adopters so far. “These sectors prioritize unique and eye-catching designs to stand out in a crowded market. DTO’s ability to offer high-quality customizable prints with quick turnaround times is a perfect match for the frequent product launches and limited edition runs commonly found in industries such as these.”
“The craft brewing industry today is taking full advantage of the ability to highly decorate cans to market their


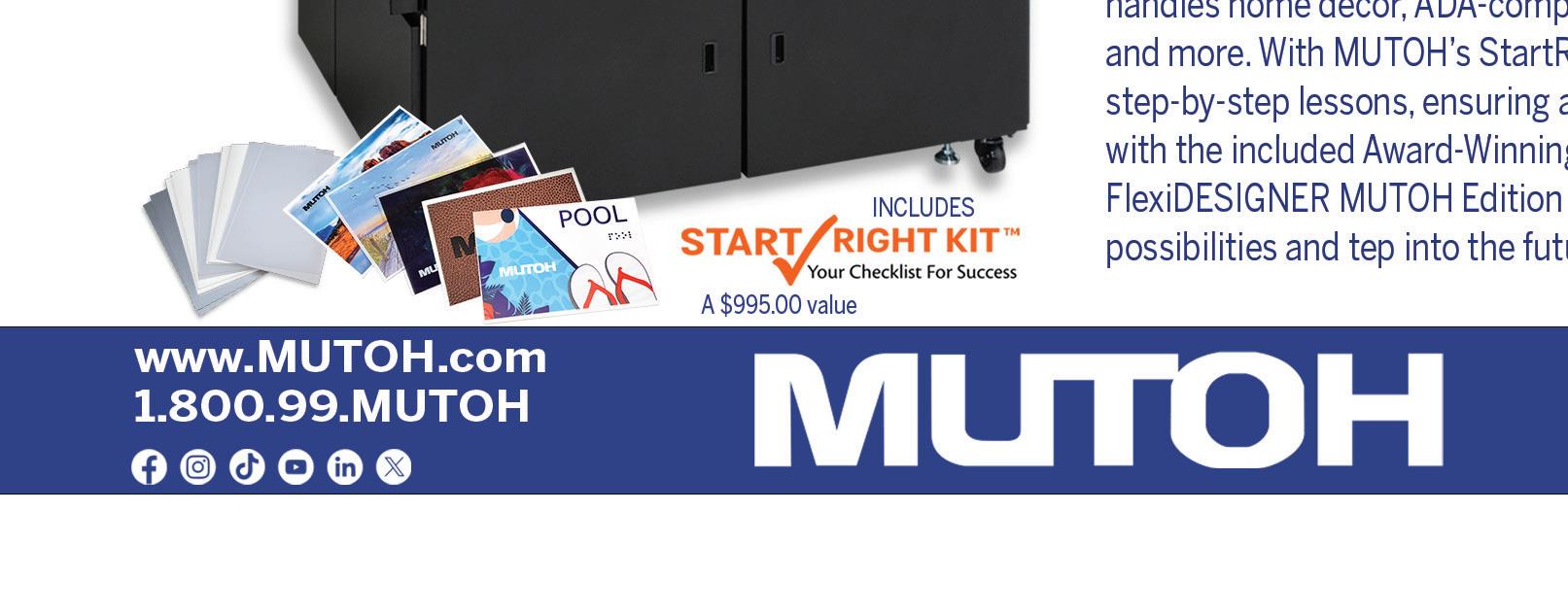
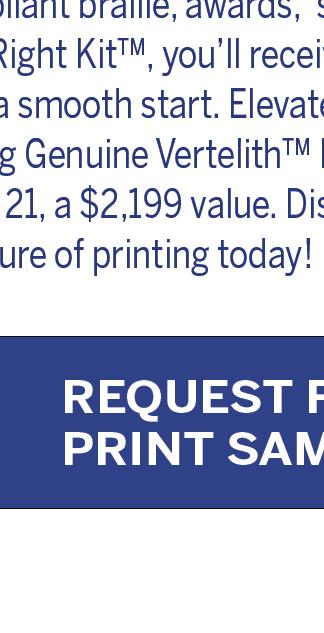
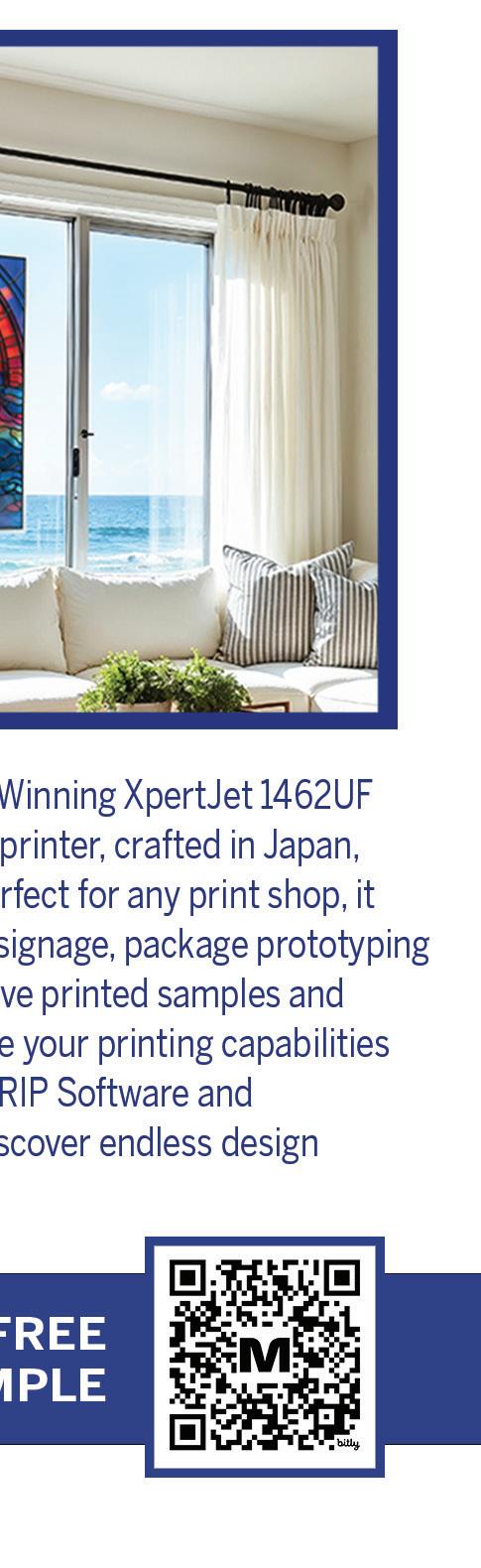
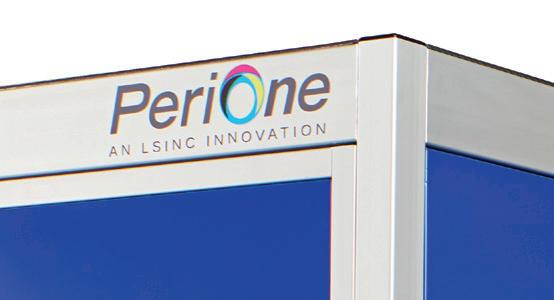
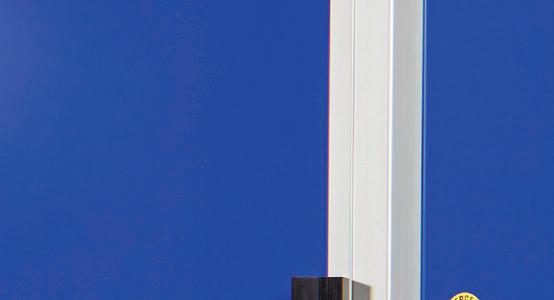
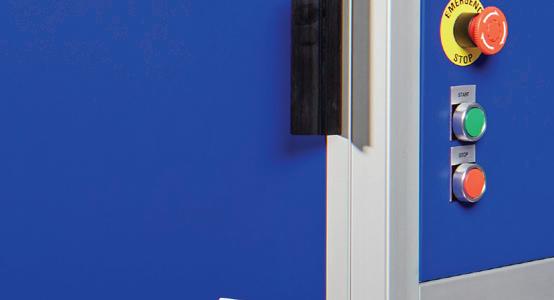

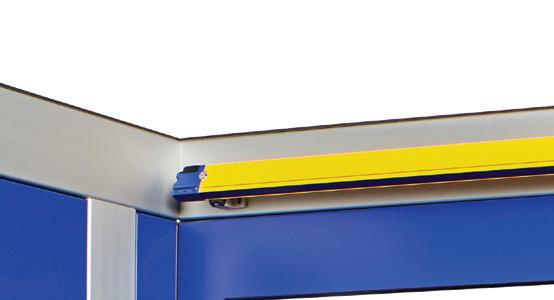
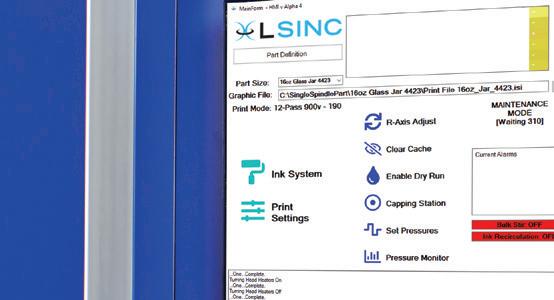
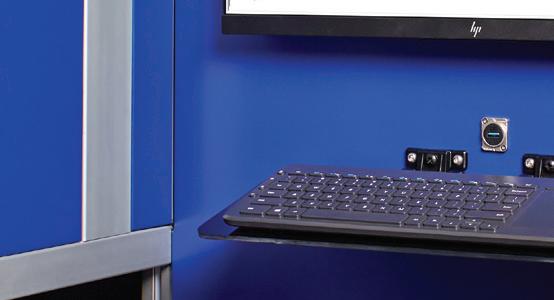
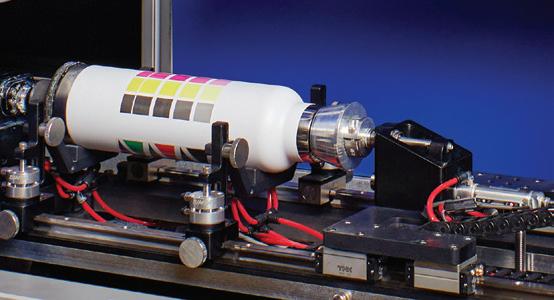

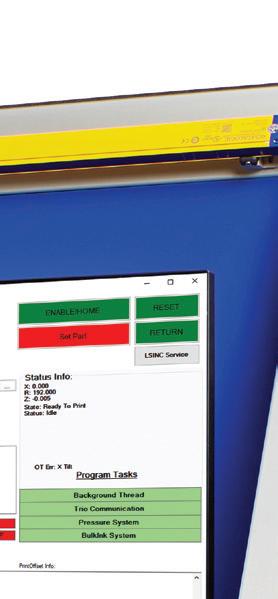

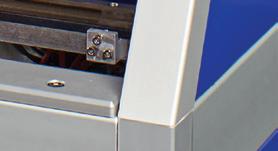
Inkjet is a non-contact technology and the spread of the ink on the can is important to its print quality. Also, the way in which the pretreatment interacts with the inks to enhance adhesion has benefits in some later processes, such as pasteurization,” says Edwards.
Depending on the ink technology used, post treatment may not be required, according to Pecorini. For example, UV-curable inks are fully cured when the can comes off of a Koenig & Bauer machine. This eliminates the need for additional curing steps and ensures the can is ready for immediate use.
Post treatment can be dictated by the user and their usage needs, thus rendering it optional. “When printing with UV devices and ink, I like to use a post cure—basically running the laps
across your printed surface to make sure the ink has had enough time to cure on the substrate. This helps with durability. By adding gloss you can cover your entire printed piece with a protectant layer that’s similar to that of an applied laminate,” suggests Chu.
“Post treatment can provide different visual quality effects than what are seen on the ink alone, as well as offer benefits in terms of post processing, such as with durability. Although not strictly necessary, it is beneficial to the final product,” says Edwards.
“While digital print has long been known for high image quality, continuity of tone, wide color gamut, and precise text, DTO inkjet printing facilitates the creation of tactile effects with spot varnish or by varying ink opacity.
As an example, tone-on-tone varnishing can be used to highlight a can’s sheen to create a ‘wet’ look. The only limit is the imagination of the designer,” attests Vallellanes.
Special Requirements
The surface and shape of an aluminum can presents other considerations in terms of printing.
The quality of the product is paramount and something to observe prior to the print process. Avoid cans with dents or other defects, advises Chu. “It’s important for the printing surface be as smooth and even as possible. The last thing you want to happen is to have something pop up and cause a printhead strike/crash.”
Pecorini recommends cans are in a basic formed shape—pre-necked and
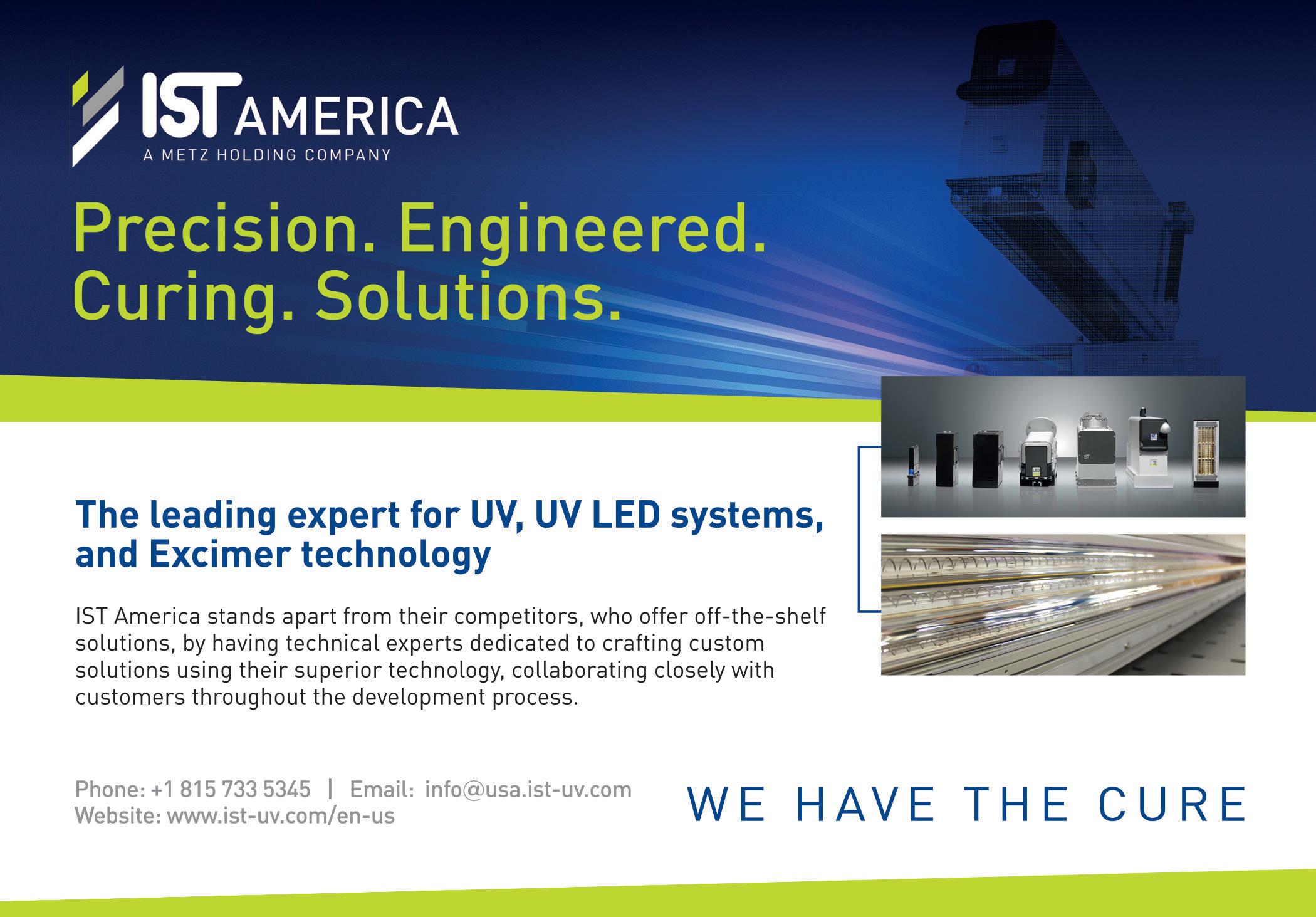

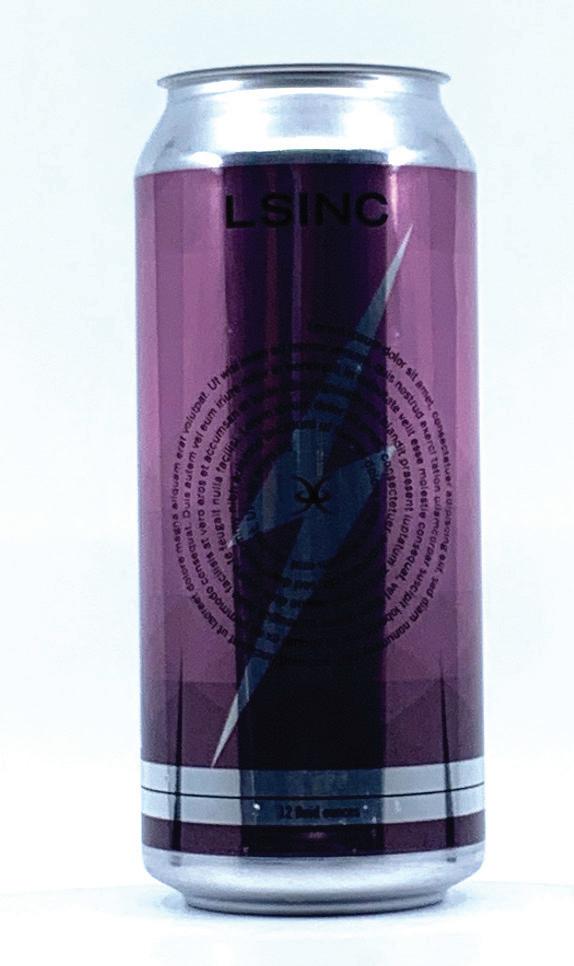
flanged—for easier loading on whichever printer.
Prior to printing, ensure the can has undergone proper surface preparation. “Clean the surface of the can with 91
percent isopropyl or denatured alcohol and then let it air dry. This will help ensure that the surface is as clean as possible before printing and further improve the graphic results,” suggests Chu. What the can experiences post print—out in the world—should be considered. “Inks and coatings applied to an aluminum beverage can must have resistance to abrasion during transportation, good adhesion before and after pasteurization, and acceptable resistance to fading under store light,” advises Alex Folloso, VP of R&D metal decorating technology, INX.
Bullington warns that ink printed too thick will flake when the can is crushed or dinged.
Other advantages to look into include software—maybe bundled with the digital printer—that optimizes ink application around the curved neck and bottom of the can. This enables full-height printing with both precision and consistency, explains Pecorini.
End to end, the print process benefits from automation, whether this is executed via software or some type of material handling. For example, Innovative Digital Systems offers a robotic loading system included on its various printers in addition to the ability to stack multiple cans in a single tool. “We have a full UV rotary printer line up that ranges from one- and two-up machines to a 2x2 shuttle system. All of them are capable of producing full color, seamless wraps, and various print effects on aluminum cans. With a printer for every need, speed, and budget, the Innovative Digital Systems line of UV rotary printers can meet the can printing needs of many companies,” says Perrelli.
Aluminum Cans
Between large brands considering shorter runs that promote limited edition beverages to smaller companies looking for minimal investment when it comes to branding and messaging, digital printing is poised to present opportunities. Highly decorative graphics with standout colors, and even specialty finishes like varnish, are sought out to differentiate products from the rest of the pack.
“As average run lengths for packaging come down and brands and retailers seek increasingly creative ways to achieve standing out on the shelf, DTO digital print is set to democratize packaging for small and medium beverage manufacturers,” notes Vallellanes.
DTO digital printers are designed to print to more than aluminum, but aluminum cans and bottles are prevalent items. Learn more in our recent free webinar on the topic, available at industrialprintmagazine.com.

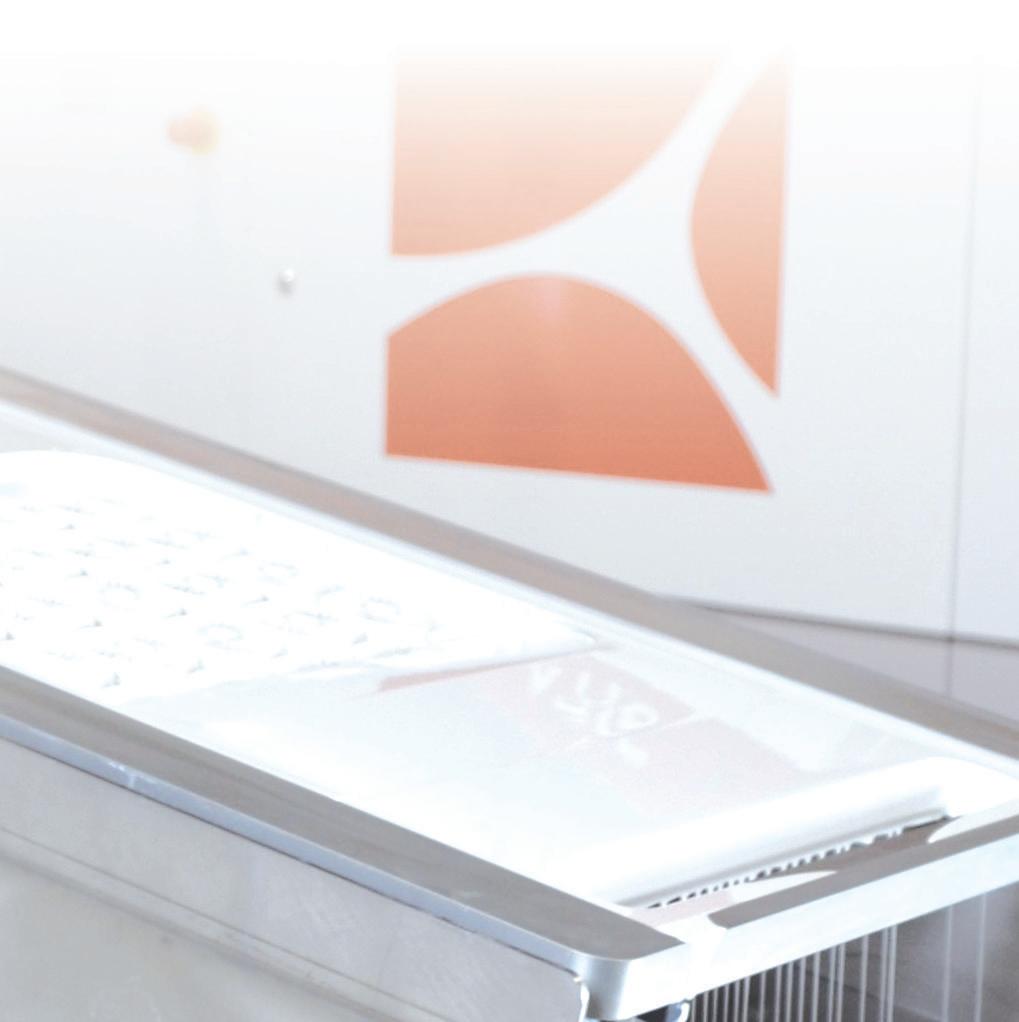


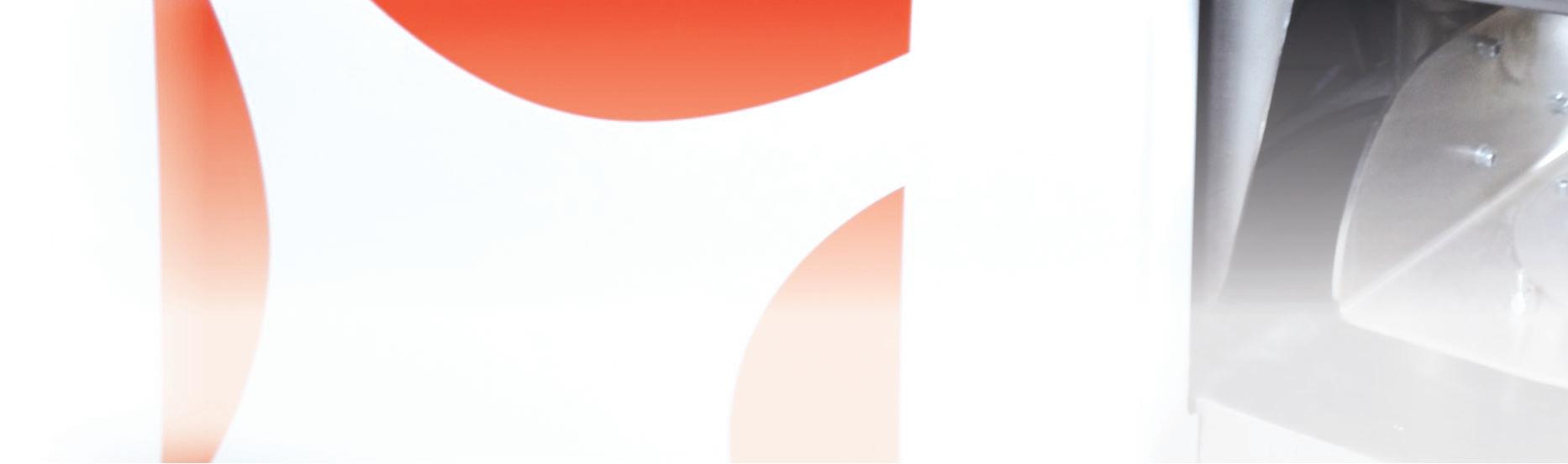
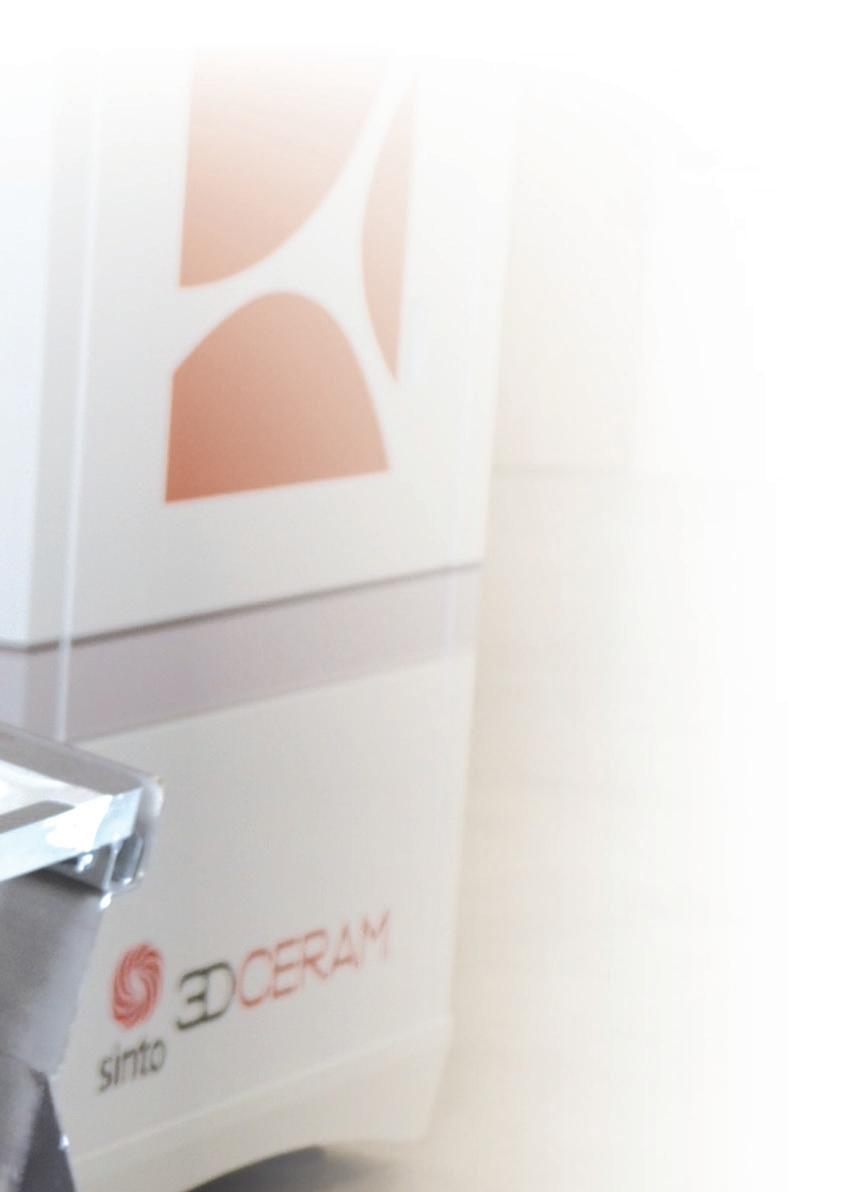

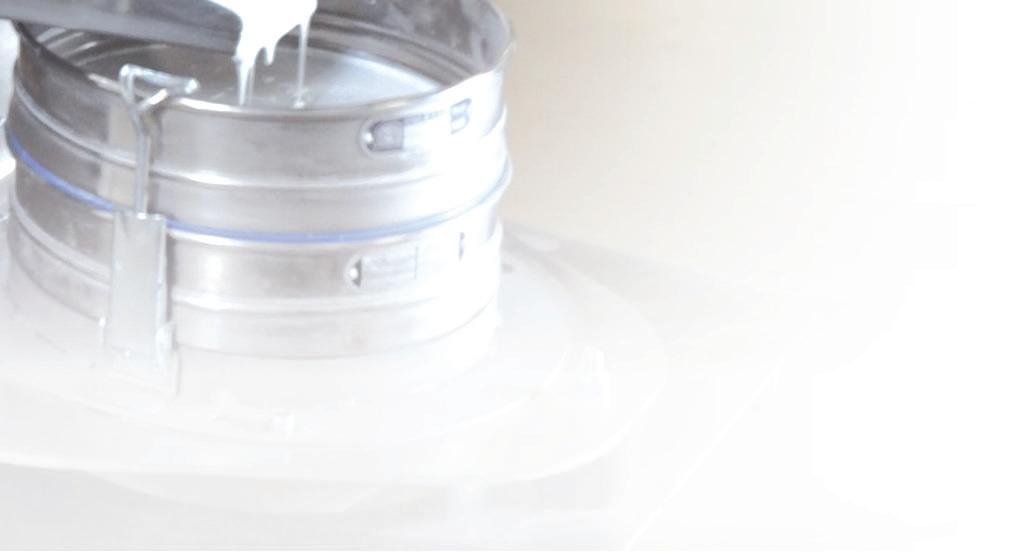

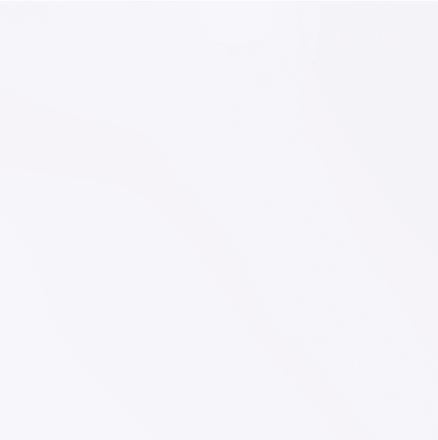



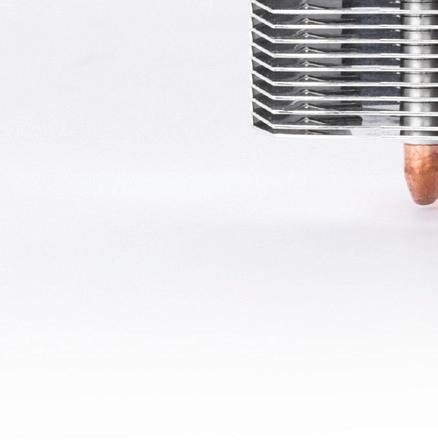
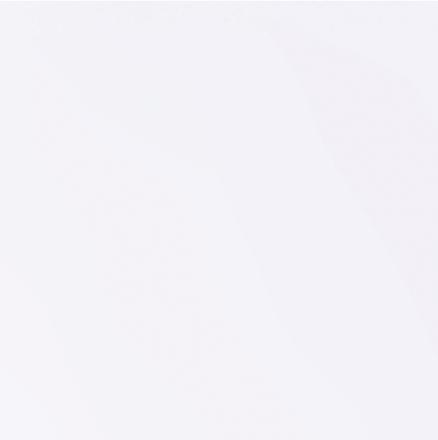


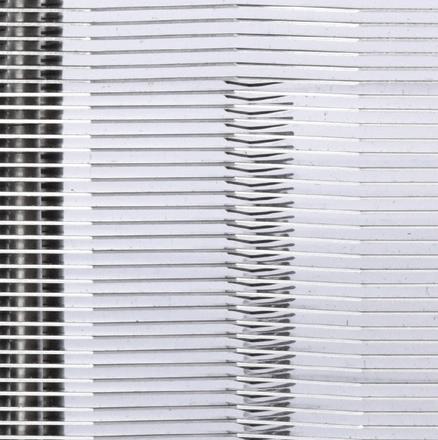

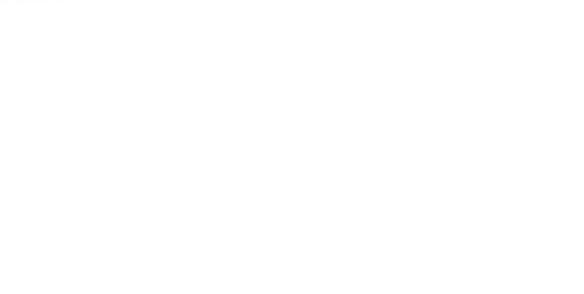


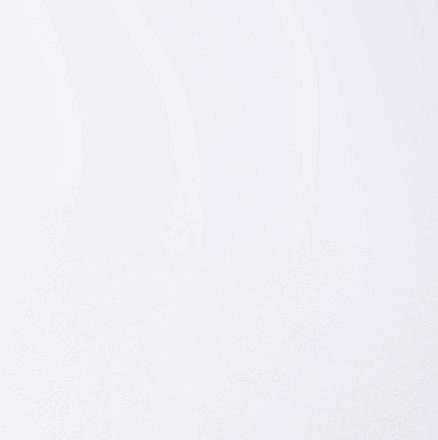
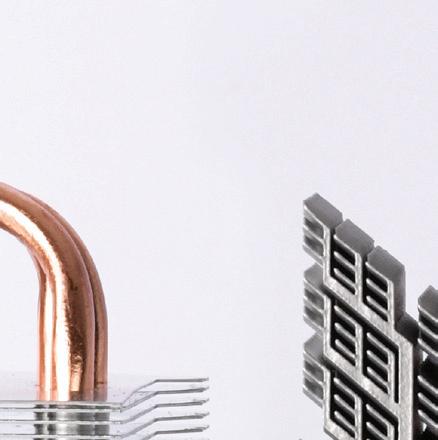
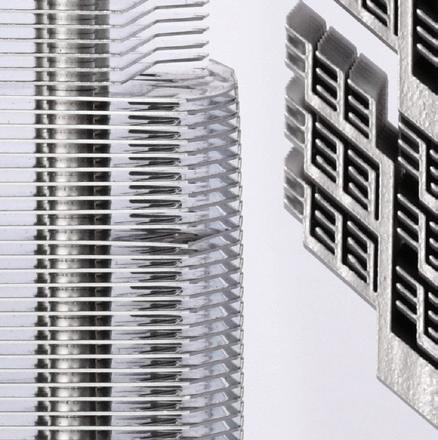
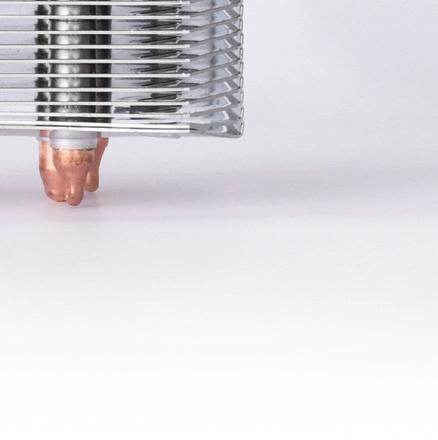
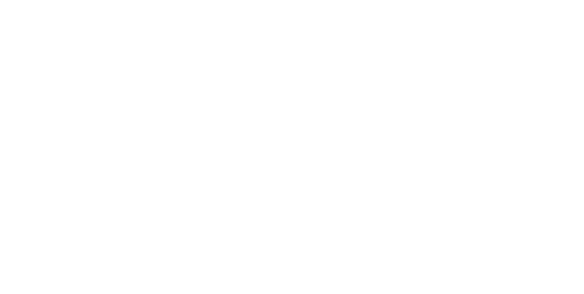
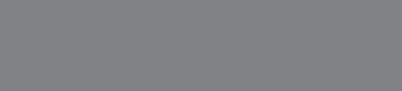
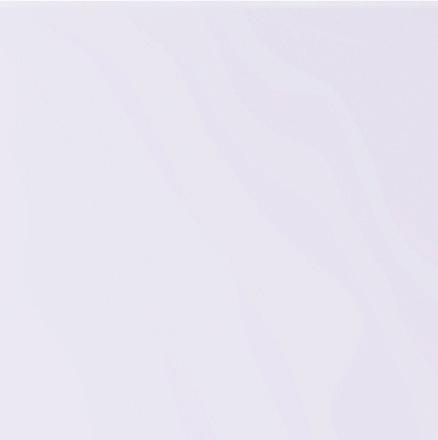
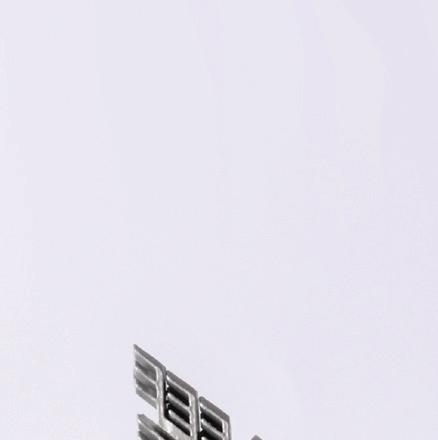



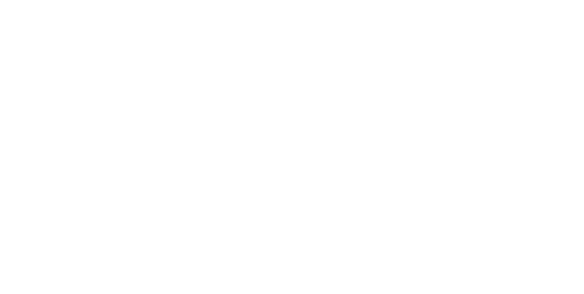


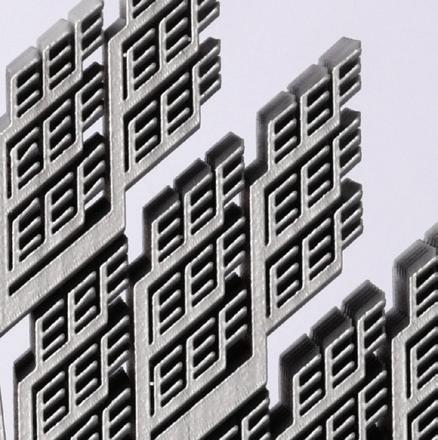

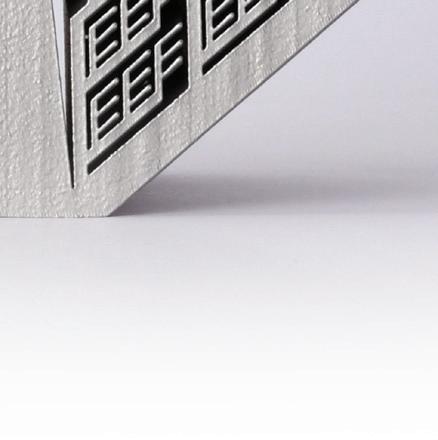

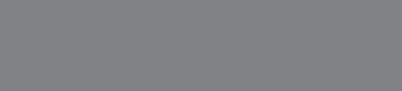

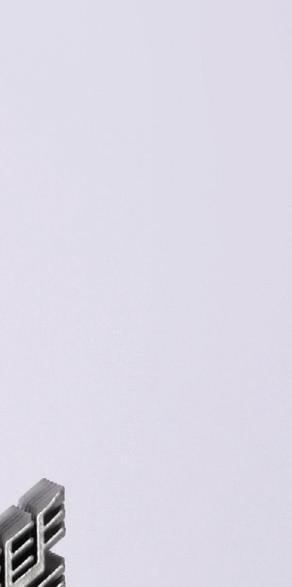
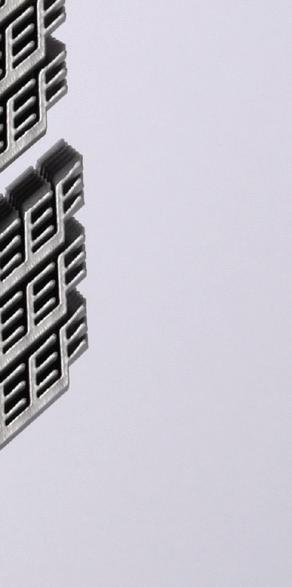
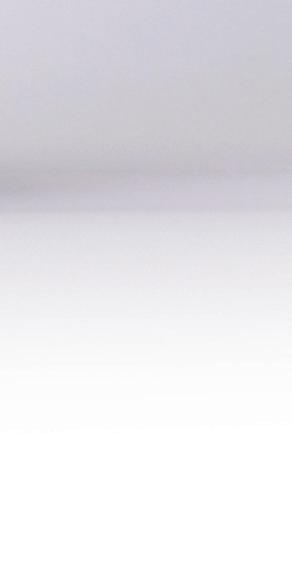

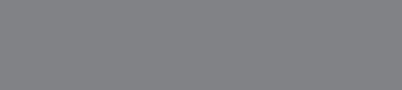

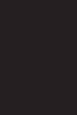

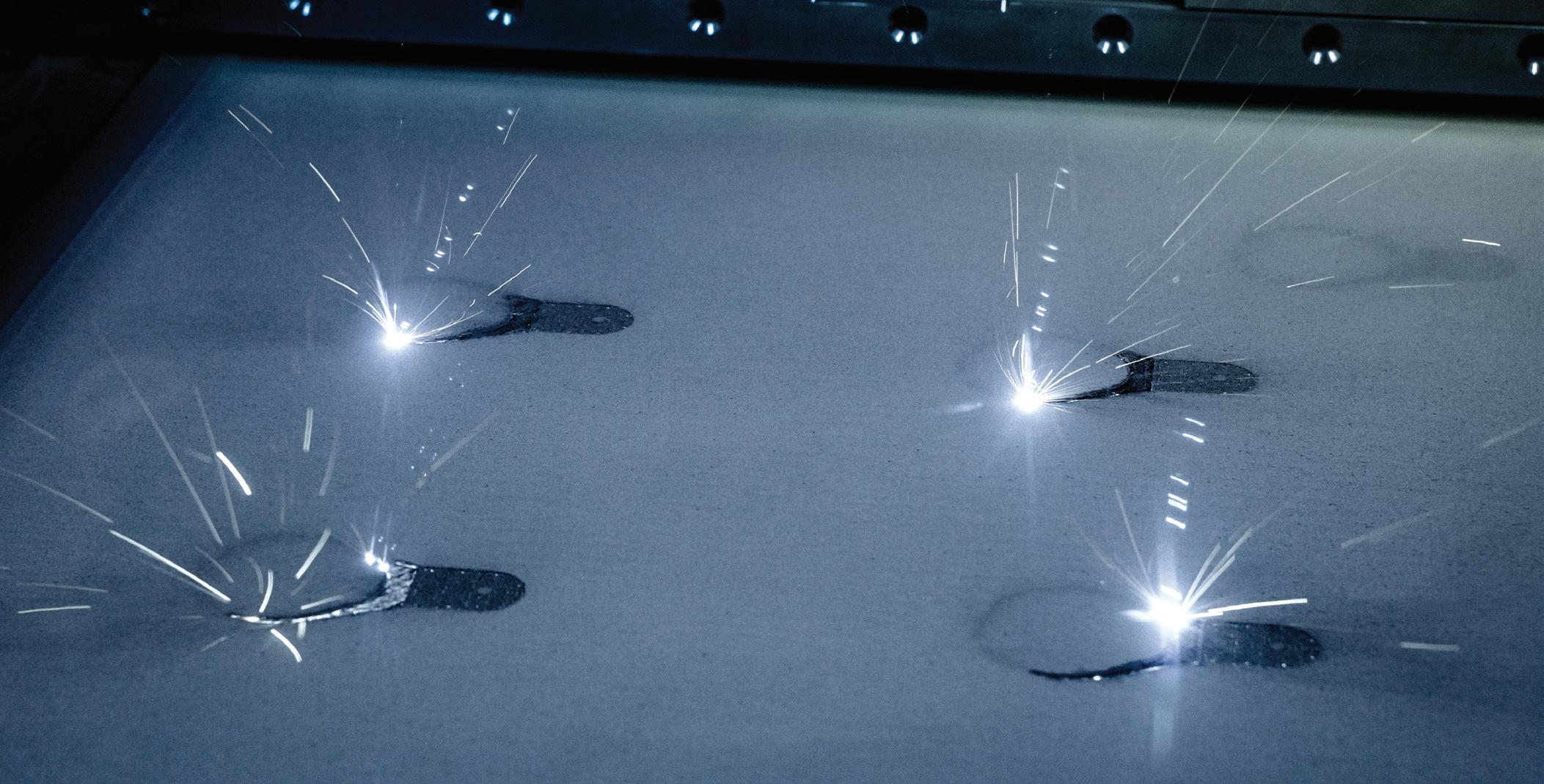
At a high level, Rangarajan says AI addresses the scalability and adoption challenges faced by the 3D printing industry. “From a design perspective, AI is both enhancing and simplifying the design process, empowering product designers and engineers to more easily design for AM by enabling faster simulation of product performance. This means that we can turn a group of 50,000 expert additive designers into millions of printable 3D design creators, lowering the barrier to entry for a traditionally technical and niche skillset.”
Rangarajan also sees an impact on total cost of ownership as AI-enabled predictive maintenance, real-time system monitoring, and improved process control reduce errors and variation in
2. 1000 Kelvin AMAIZE uses AI to simulate the metal AM process to increase the efficiency of engineers and avoid build failures. This image demonstrates the actual build process of metal using an EOS printer. 3. Materialise QPC uses AI to automate quality control by examining 2D images of the powder bed taken during the 3D printing process. By analyzing and correlating layer data from the 3D printing process, users identify defective parts before they are sent to post processing and quality inspection, which can account for 30 to 70 percent of a part’s total manufacturing cost.
printed products while flagging detected issues before they impact a production run, saving time, money, and increasing yield. “3D printing and AI will continue to advance and evolve in lockstep, uncovering new ways to advance both standard and AM processes in this new era of digitized production.”
Recognition of parts through AI helps in build preparation, supporting users and decreasing the learning curve when starting with AM. “Ultimately, these technologies enable greater efficiency and scalability within the AM workflow by providing insights on process improvements and automating digital processes such as the digital planning process of a printed medical implant or guide and digitally recognizing parts after building to assign correct post-processing classes to the parts,” says Verhoelst.
There is significant potential of AI automation in 3D manufacturing that allows for scaling. “One example of this benefit is the analysis of images during the build process to predict part defects. AM parts have hundreds of printed layers, and manually evaluating these in quality control is time consuming and
prone to human error. By leveraging AI to automate and monitor the printing process, users can avoid failed builds and hidden flaws in parts and optimize processes to avoid waste in materials and machine time,” shares Verhoelst.
“AM is typically a very complex process, melting thin layers of powder—between 30 to 200 microns—of metal or polymer powder with a laser, layer by layer by layer. A lot can happen over the course of thousands of layers, so the ability to simulate and predict anomalies is very interesting. Also, there are a lot of parameters that engineers have the ability to change in order to achieve a certain outcome. For example, laser power, speed, layer thickness, and gas flow. All of these parameters have various inter-depended outcomes leaving an engineer with endless opportunities. A prime use case for a digital assistant,” suggests Alefeld.
AI Challenges
With any emerging technology there are challenges to contend with.
“The main challenge today is that AM is still a comparable small industry. The required investment into AI tools is high,

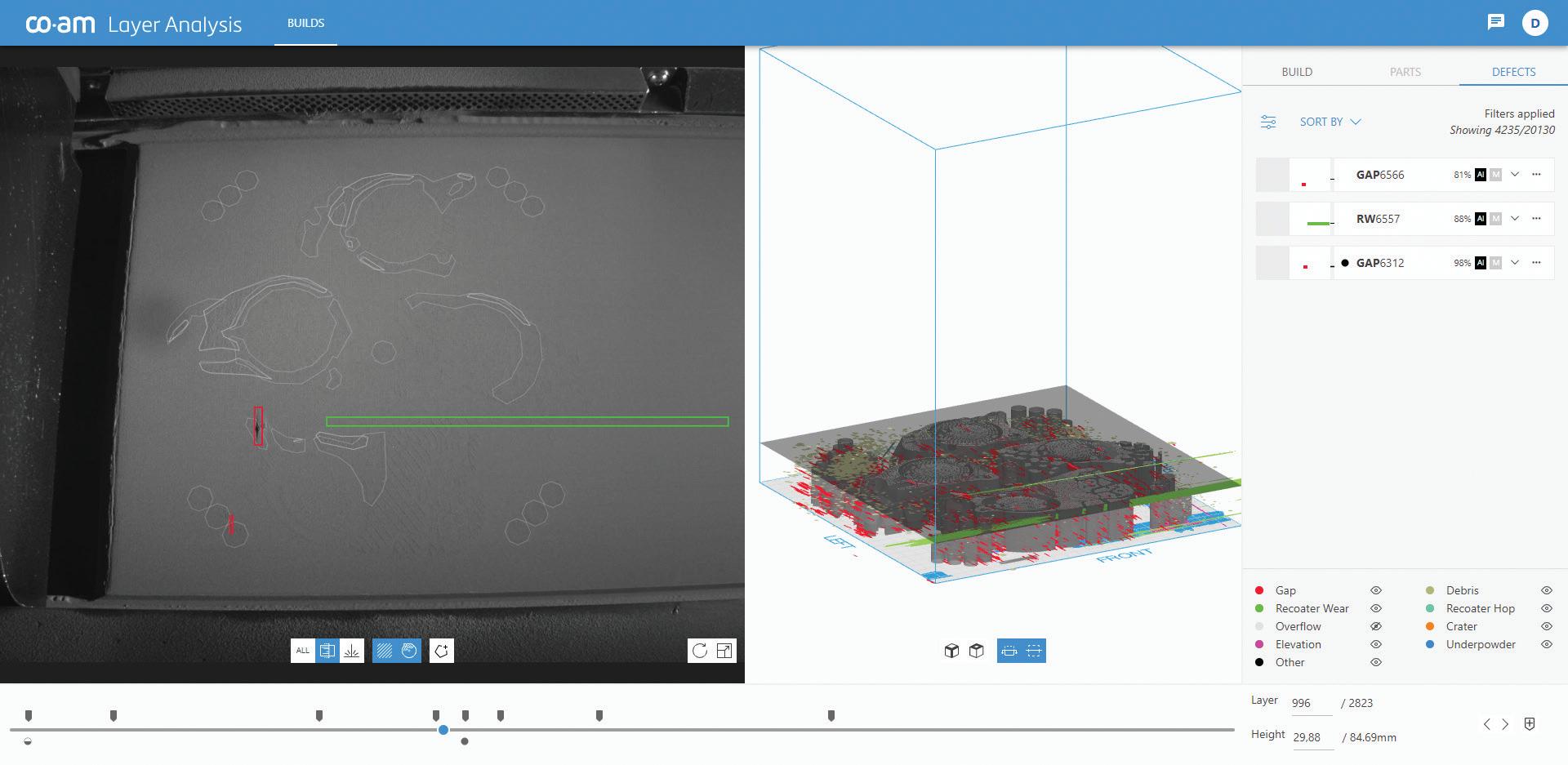

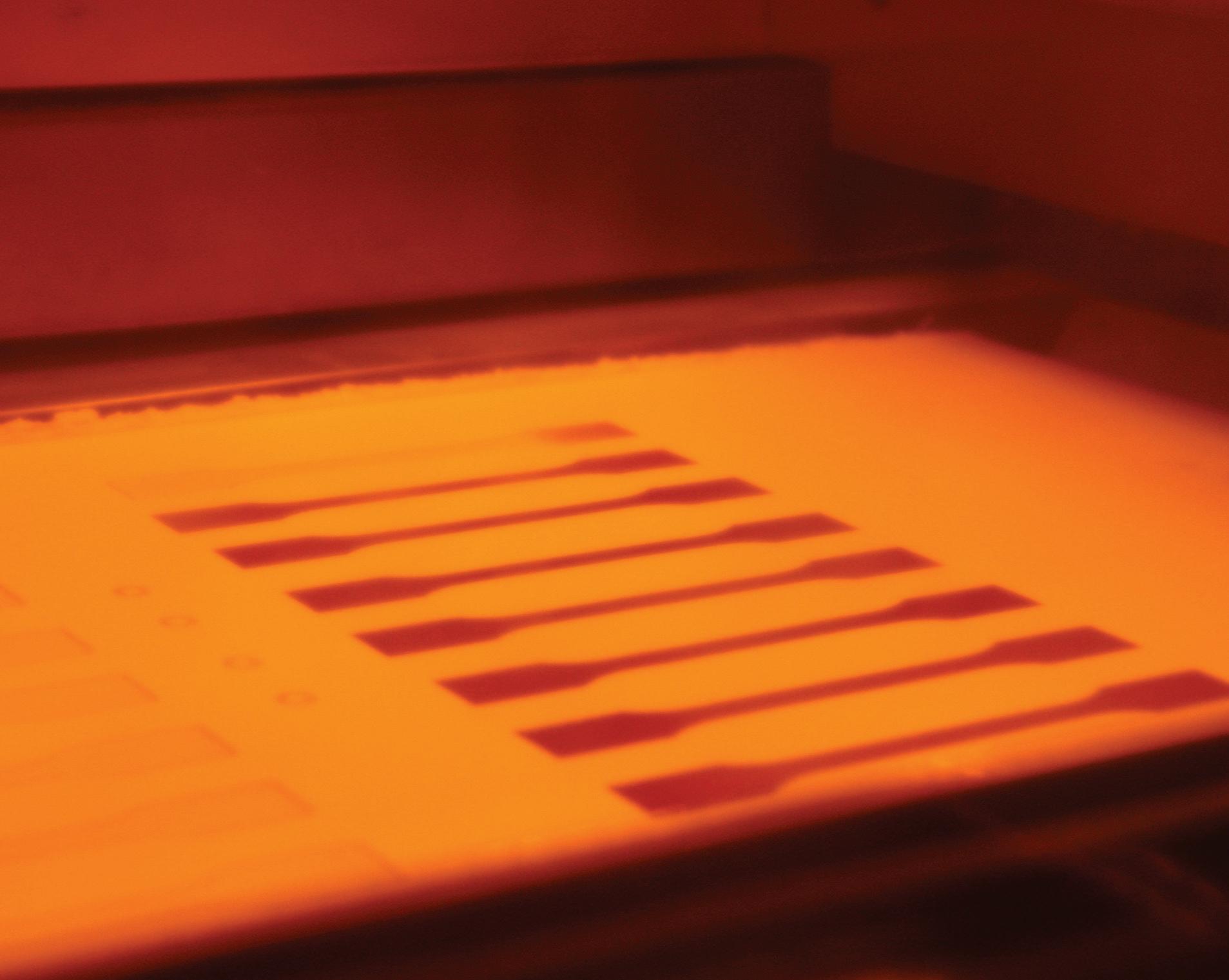
facilitate build preparation; and in automating quality control processes, such as error and defect classification. “In these tasks, we find that AI can provide higher accuracy and lower user involvement than traditional algorithms for more consistent and repeatable quality control in the printing process.”
Materialise’s software for 3D printer manufacturers includes the company’s AI-based Quality and Process Control (QPC) Layer Analysis offering. “This module uses AI to examine images of individual printed layers that are captured by cameras on 3D printers. In seconds, the tool scans the layer, identifies errors, and visualizes them to give
users a summary of defects in the build. This acts as an assistant to users, enabling them to identify errors that are not easily identifiable to the naked eye and to conduct root cause analysis to determine the impact of errors. This helps users more quickly determine if part quality meets standards and requirements in quality control,” explains Verhoelst.
Virtual Assistants
One of the primary uses for AI in 3D/AM settings is as a virtual assistant.
For example, 3DCeram developed CERIA for its CERAMAKER range of printers. CERIA is deployed in several modules, the first of which, CERIA Set, is a 3D printing assistant designed to check files, compose tanks, and produce optimized printing parameters.
Verhoelst adds that AI currently acts as a virtual assistant in AM quality control by identifying issues and errors within builds. “In the long term, there is potential for AI to assist in optimizing settings and processes for printing, based on previous builds and settings.”
Alefeld also sees this as a key use case for AI in 3D/AM. “AM requires some time to get to excellence as an operator or engineer. Leveraging digital assistants that can guide in the form of an ‘experienced advisor’ would allow us and our users to bring new applications to market faster, cheaper, and with newer talent.”
EOS partners with companies such as 1000 Kelvin, but also has a few projects in its pipeline. “I believe that AI will touch all process steps in the AM value chain, from design to data preparation to post processing. Some of the tools will be enhanced with AI by EOS, some will be provided by the many partners we work with,” notes Alefeld.
“Currently, we see AI virtual assistant solutions playing a significant role during the planning phases, particularly when integrated with third-party design or build preparation software. While these solutions will eventually be incorporated directly into the printers, the factory environment presents both opportunities and challenges. Opportunities include sensor integration, but challenges such as limited compute resources and, in many cases, lack of cloud connectivity, must be addressed,” says Rangarajan.
HP is evaluating virtual assistants that can help its customers to choose the best parameter sets to complement the HP 3D Printing Digital Production Suite and provide design recommendations.
AI in Manufacturing
AI is expected to play an increasing role in AM. Today, it is utilized in the form of virtual assistant technology to help automate and optimize complex 3D workflows. IPM
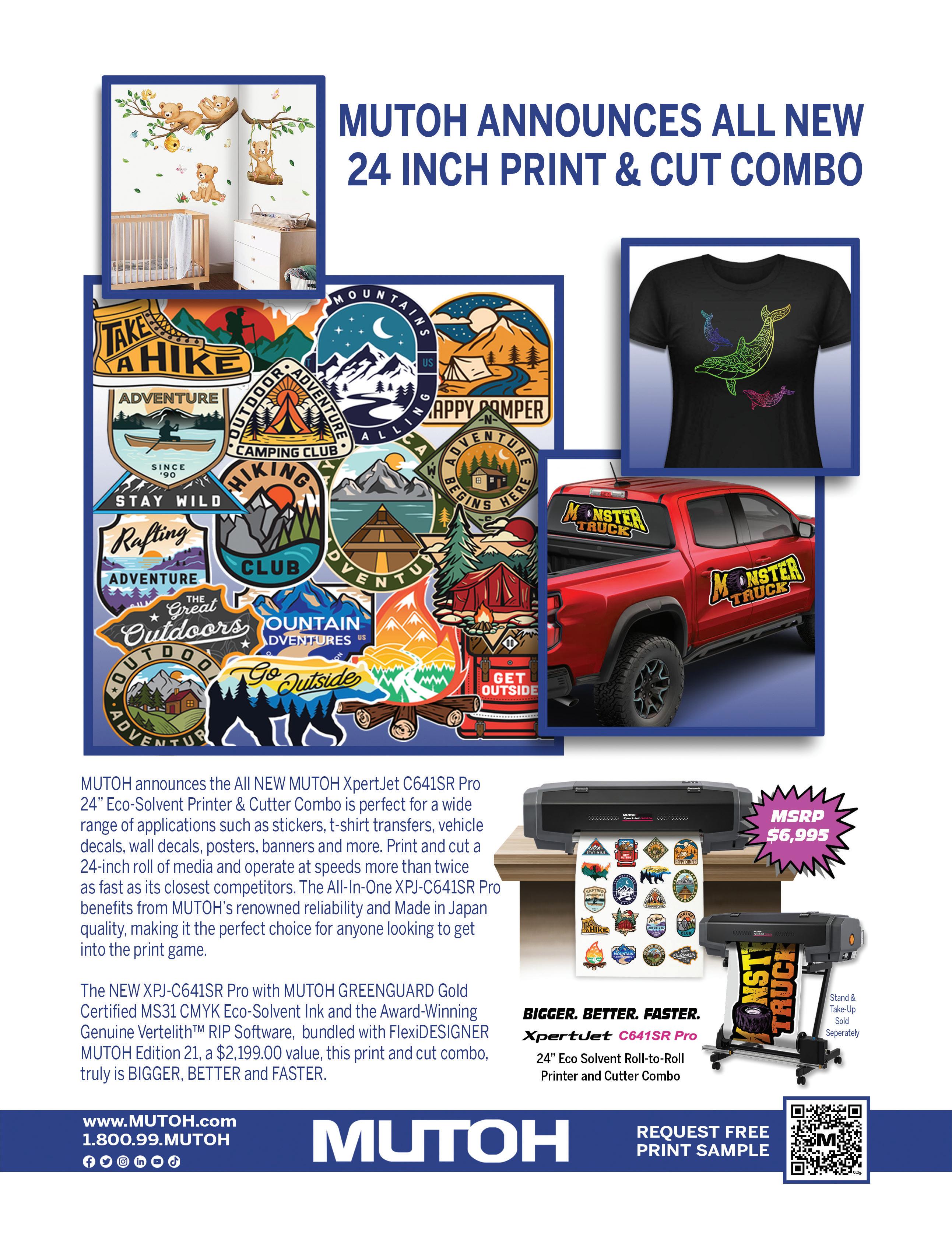
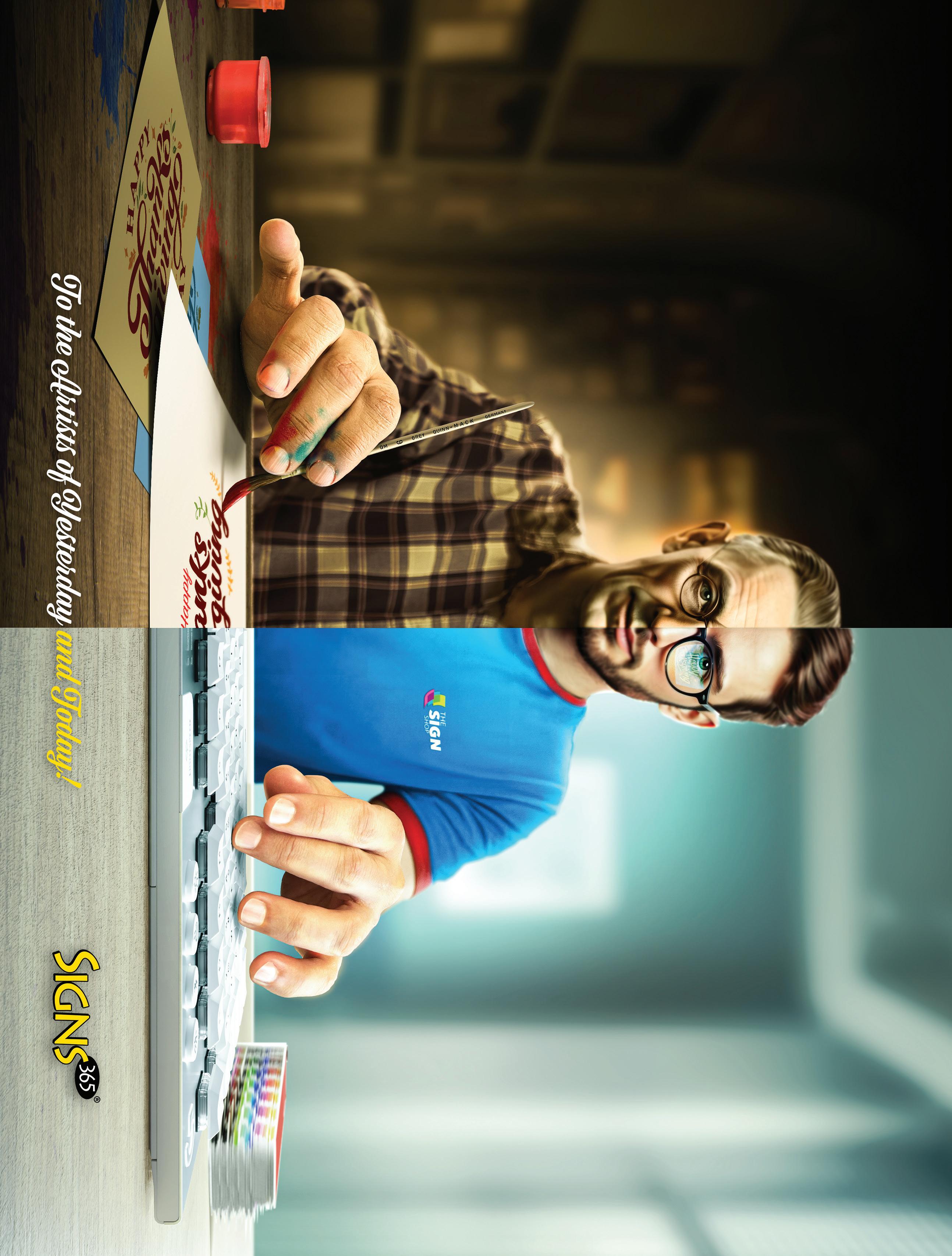