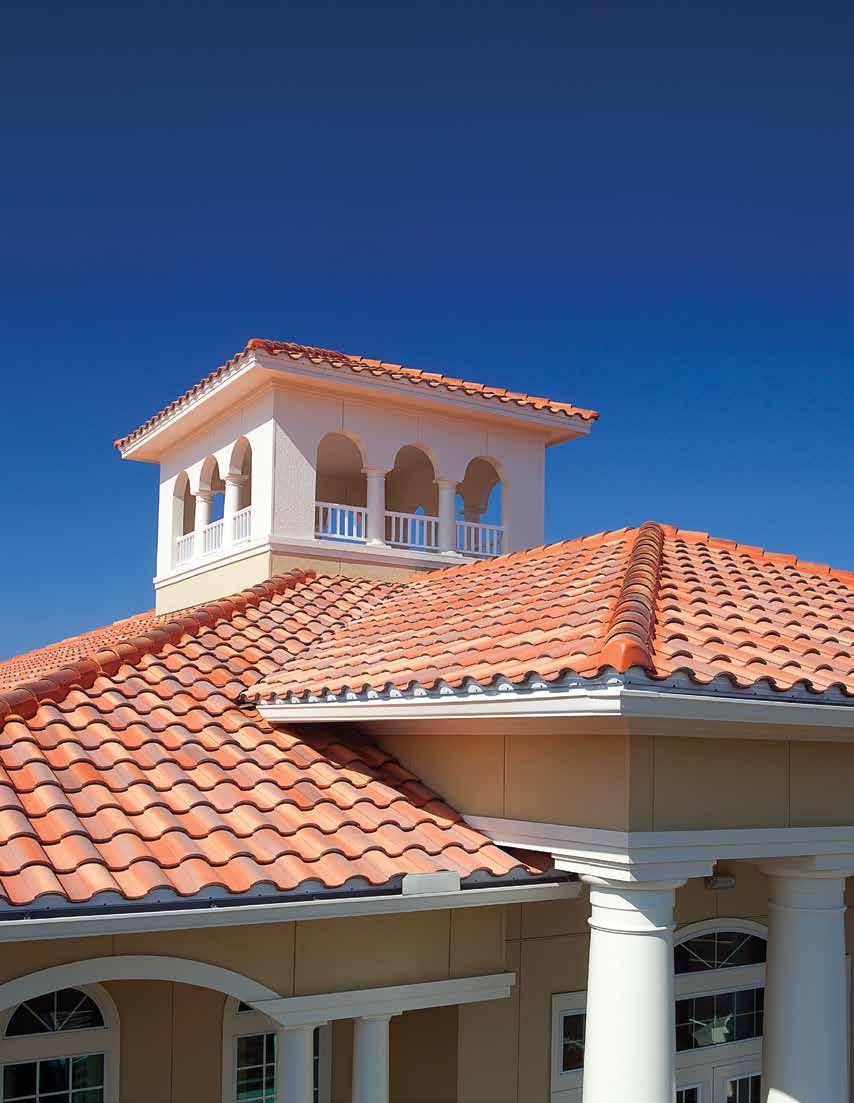
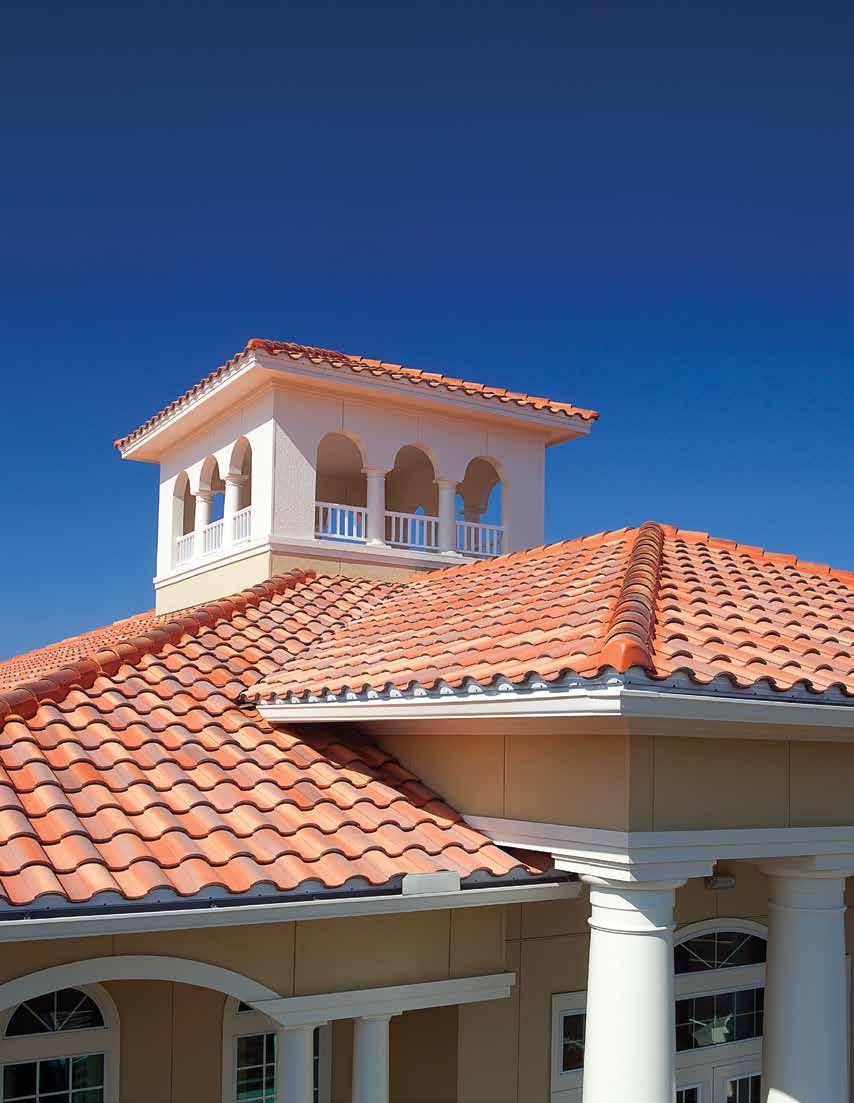
ROOFING Florida
Roof Tile Issue
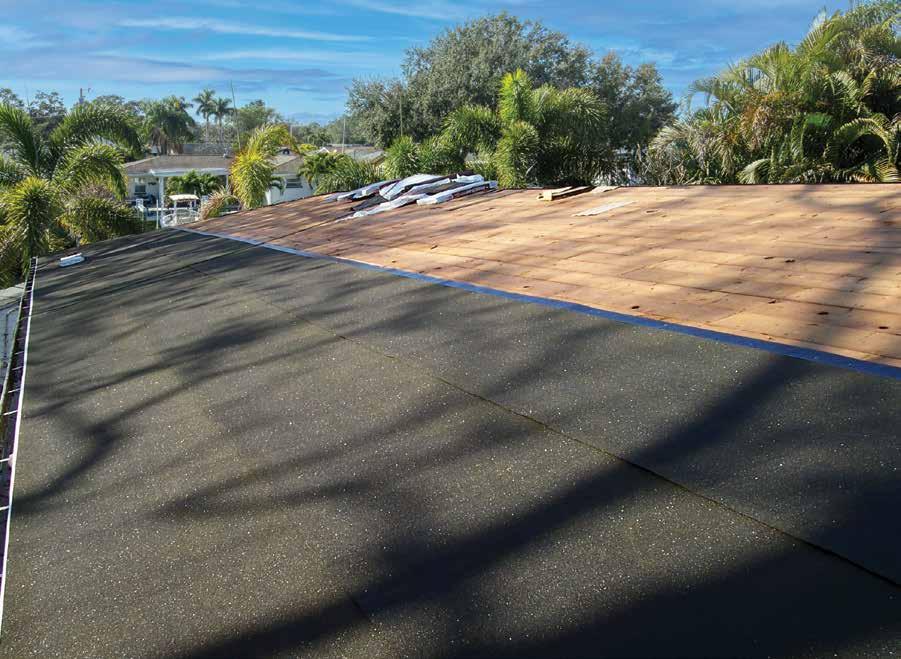
FORTIFIED ROOFING
NEW FOR 2023! MFM introduces IB-3™ StormStopper Plus, designed specifically for the Florida roofing market. Stop storm damage in its tracks and offer your customers a qualified FORTIFIED PROGRAM product for years of worry-free service. This 50-mil, self-adhering roofing underlayment features a granulated surface and a non-removable selvedge edge for a secure seal on overlaps for whole roof protection.
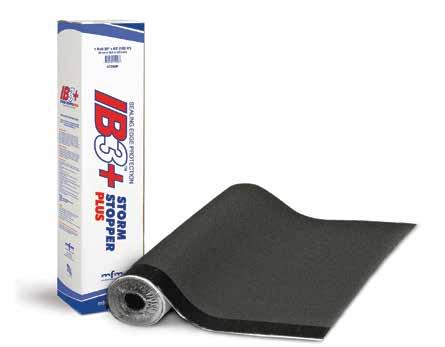
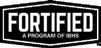





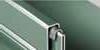

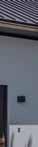





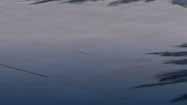




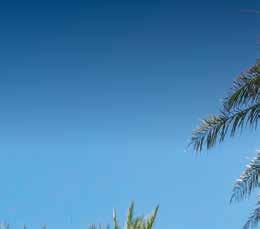
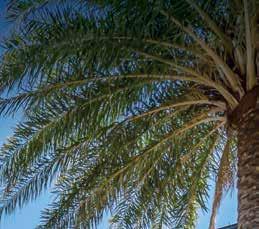

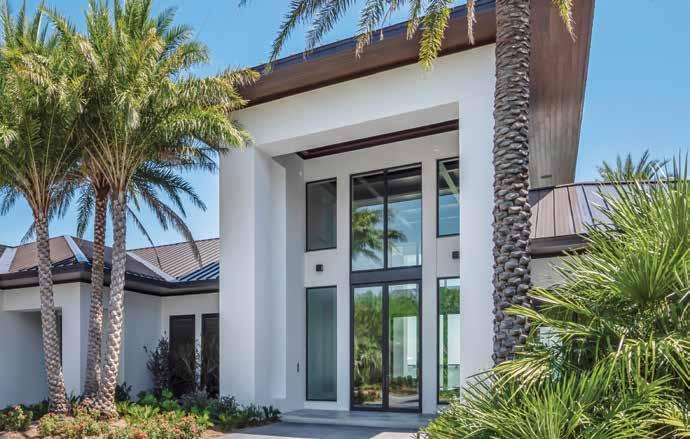

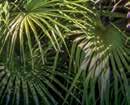
Equally strong and attractive , these metal roofing panels are available in Florida in our full line of PAC-CLAD painted steel, aluminum and Galvalume Plus coatings, ensuring that your roof will endure whatever comes its way. All panels are Miami-Dade County and Florida Building Code approved.

Industry Updates
Gulf Coast Supply Promotes Senior Leadership
Gulf Coast Supply & Manufacturing, the trusted name for metal roofing for over 25 years, announced the promotion of three company executives.
Shawn Kirk, who has served as Vice President of Operations and played a pivotal role in the company’s operations since June 2018, has been promoted to Executive Vice President of Operations. His deep understanding of the manufacturing processes will continue to drive efficiency and innovation across its operations.
Craig Mohr, who has served as Director of Sales and Marketing, has been promoted to Vice President of Sales and Marketing. His strategic vision and leadership have been key factors in the company’s sales growth since he joined in January 2021.
Jordan Graham, who has served as Manager of Accounting and Finance since July 2021, has been promoted to Vice President of Finance. His financial acumen and leadership have been vital to improving the company’s financial processes and performance.
“We are thrilled to announce these well-deserved promotions within our company,” said Gulf Coast Supply President Harry Yeatman. “Each have demonstrated exceptional leadership and dedication to our company. I look forward to their continued contributions to Gulf Coast’s success.”
Eagle Roofing Products Celebrates 35 Years
From humble beginnings to becoming the largest privately held USA-Made, USA-Owned concrete roof tile manufacturer in the U.S., Eagle Roofing Products has been the company of choice for its customers and partners for over three decades. Founded in 1989 in Rialto, Ca., it is a well-known and trusted leader in concrete roof tile manufacturing, offering resilient and sustainable solutions to the residential, institutional and commercial building construction sectors. A family-owned and operated company, it has expanded its roots from coast to coast with four manufacturing plants, two stocking yards and nine design centers since its genesis to provide products and services throughout the U.S. and Canada.
What started with a single high-pressure concrete tile extrusion machine and five employees has grown into a corporation with over 500 employees and a reputable product offering. With over 150 tile color options, seven profile options and dozens of roofing components, Eagle has created a portfolio of versatile, elegant and energy-efficient products with every type of new construction build and reroof project in mind.
“Over the years, Eagle has stood firm in our resolve to do right by our people and the best interest of our customers and the roofing industry in general. When
issues arise in society, business or the economy, we remain loyal to our mission of providing quality products no matter what,” stated Vice President of Sales and Marketing, John Campbell. “The future may seem uncertain but with the right resources and our steadfast commitment of team members, we are confident in the new heights we will reach.”
Its plans for Eagle's future include expanding their roof tile and components offerings, as well as creating a robust internal learning initiative designed to strengthen employee skills. “We have a ton of new internal and external projects in the works. We recently launched an online reservation system, Time Is Money, to better help our customers with reduced truck turnaround times and now we are rolling out Order Eagle 2.0, a new and improved ordering platform to benefit distributors, roofers and dispatchers. We are also creating meaningful roof tile systems with our products and updated components that help our roofing partners simplify the selling process. There is a lot in the works and our goal is to help our customers in every way we can,” Campbell stated.
Eagle attributes its success to its unwavering commitment to stellar customer service. Regardless of role or status, the company has firmly developed a company culture that prioritizes transparency, reliability and quality to ensure that each customer’s needs are met. “We wouldn’t have gotten this far without our team members and it is because of them that we’ll celebrate another 35 years and more,” Campbell noted.
NRCA Announces New Slate of Officers
Doug Duncan, President of Nations Roof, Villa Park, Ill., was elected Chairman of the Board and Alex Hernandez, President of Clark Roofing Company, Broadview, Ill., was elected Chairman of the Board-elect. Chad Collins, President of Bone Dry Roofing Co., Bogart, Ga., David Hesse, Vice President of Kalkreuth Roofing and Sheet Metal Inc., Wheeling, W. Va. and Tim Stephens, Vice President of Operations for Architectural Sheet Metal Inc., Orlando, Fla., were elected Vice Chairmen for two-year terms. Tupac de la Cruz, Founder of Roofing Solutions LLC, Prairieville, La., was elected Vice Chairman for a one-year term.
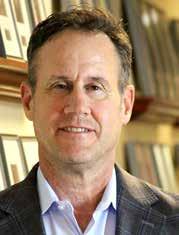
NEW PRODUCTSROOFING Florida
East Lake Metals
When your metal roof needs to stand strong against some of the toughest environmental elements, East Lake Metals has the solution for you. Armored Coast roofing offers metal coated with ZAM, the best corrosion-resistant steel made of zinc, aluminum and magnesium. The reliability of Armored Coast metal roofing is exemplified by its substrate warranty, which extends over 300 feet from the coast and its 35-year paint finish warranty. This makes it an ideal choice for properties located on canals and brackish water bodies. Available in 22 colors, Armored Coast is perfect for any pre-painted steel materials used along the 95,000 miles of coastline surrounding the U.S. For more information, visit www.eastlakemetals.com.

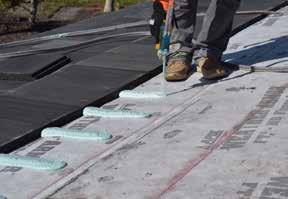
ICP Group
APOC Polyset Roof Tile Adhesives are specifically designed to bond clay roof tiles to approved underlayments on new construction, reroofs and tile repair projects while being approved for use in the most stringent high-wind regions of the world. These products are available in the form of low-pressure one- and two-component polyurethane foam adhesives in disposable and refillable packaging. ICP offers free jobsite and office training and “qualified applicator” cards for the APOC Polyset Roof Tile Adhesive products. Reach out to schedule your next training. For more information, visit www.apoc.com.
PAC-CLAD | Petersen New Paint Pen
PAC-CLAD touch-up paint quickly returns a building’s architectural metal facade to its intended appearance. These easy-to-use paint pens are available in all standard PAC-CLAD colors and have a shelf life of one year. Apply felt tip lightly to any scratched, nicked or worn area. If needed, gently wipe the area with a soft cloth to remove excess paint. Allow the paint to dry and set. Contact your rep or visit www.pac-clad.com for more information and full usage instructions.


MFM IB-3 StormStopper Plus
MFM's IB-3 StormStopper Plus is a new self-adhering, 50-mil, granulated surfaced roofing underlayment. The underlayment features a non-removable selvage edge for a secure seal on overlaps for whole roof protection. IB-3 StormStopper Plus does not require priming of the roof deck due to an enhanced adhesive system for aggressive adhesion. IB-3 StormStopper Plus meets ASTM D 1970 and has Florida Building Code Product Approval FL 41919.1. For more information or to request a free sample, please visit www.mfmbp.com.
Nu-Ceil by Nusens USA
Nusens USA is proud to present Nu-Ceil, the future of interior protection for construction and re-roofing projects. Our patent pending Ceiling Containment System, Nu-Ceil, has drastically reduced the cost of interior protection – now everyone can afford it!
■ Catches overhead dirt, dust, debris and even water
■ Certified for installation below sprinklers
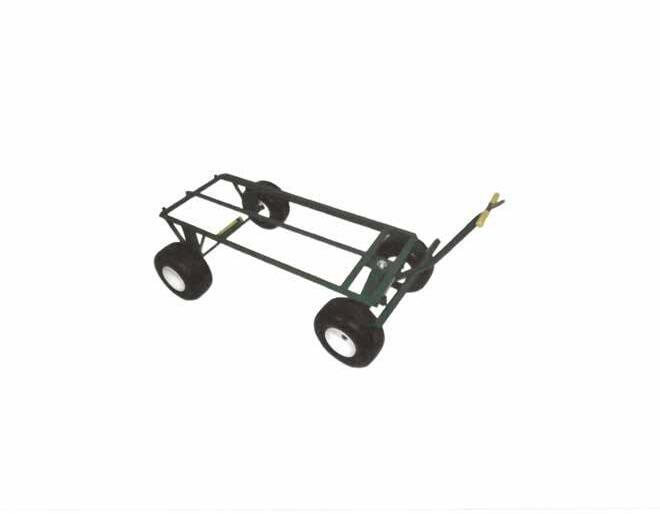
and ship quickly to Florida and all Southeast locations. Please visit www.roofcarts.com or call toll-free 877-869-0200 for more information.
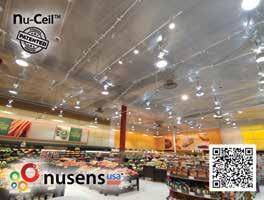
The Winston Group
Talon 5000 is a new thermoplastic automatic welder that is 100% Made in the USA. It has extremely “user friendly” controls and includes an LED work light to illuminate the work area. For more information, visit www.winstongroup.com or contact sales@winstongroup.com.
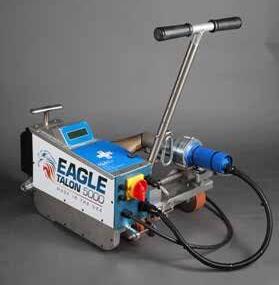
The Impact of Worker Misclassification in the Construction Industry
For years, employers in a myriad of industries have grappled with the requirements related to worker classification. Misclassification occurs when employers designate workers as independent contractors when they actually should be considered employees. As presidential administrations have changed, so have the related laws and, along the way, some states have adopted stricter guidelines.
Recent studies show that in addition to drivers in gig industries such as Uber and Lyft, construction laborers are among the most severely impacted workers in the nation. In addition to affecting those workers, misclassification has far-reaching implications.
Worker Classification Guidelines
As you likely know, workers hired to do a job on a regular basis and at a set location are often categorized as employees. They receive benefits that may include medical insurance and paid leave. Their employers
provide unemployment and workers’ compensation insurance and their Social Security contributions are taken directly from their paychecks. In contrast, independent contractors are not tied to one employer. They work on a number of different projects, usually for a set fee or hourly rate. They are generally not eligible for benefits.
It is important to realize, however, that classification requirements have changed over the years, at times becoming more restrictive or less so. The new rule introduced by the U.S. Department of Labor (DOL) in January 2024

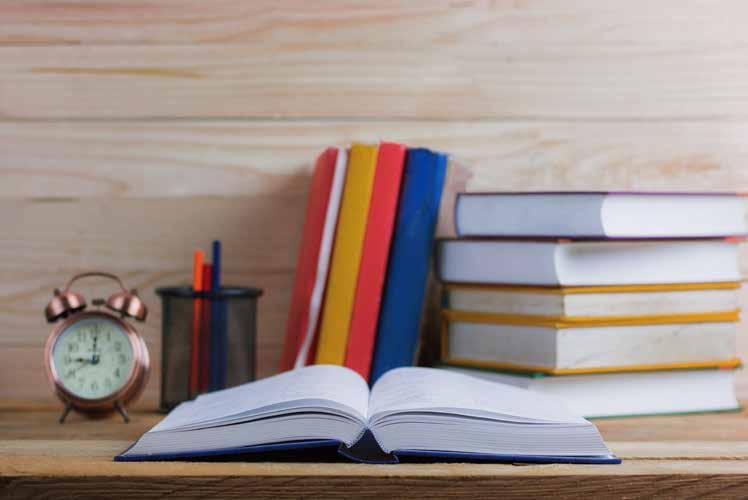


requires a six-factor analysis to determine the proper classification.
■ Whether the worker has the opportunity for either profit or loss. For example, does the worker choose the tasks to perform and set the rate of pay? Does the worker use marketing to seek more work?
■ What investments the employer and worker have made: Who owns the equipment being used?
■ Whether the working relationship is permanent: Is the work occasional or erratic? Or is it regular and ongoing?
■ What the nature of the work is and who has control: Does the employer supervise the worker and set the hours?
■ If the work is integral to the employer’s business: Is the work essential to the company’s success?
■ If the work relies on the worker’s skill and initiative: Does the worker bring specialized skills? Or is the worker trained by the employer?
Before classifying workers, employers must carefully and comprehensively consider these factors. In roofing, this directly impacts subcontractor labor and 1099 salespeople.
Misclassification Practices
Even with these guidelines in place, many employers still misclassify their workers. Such practices may occur when employers lose track of the most recent requirements or do not fully understand them. However, some employers intentionally misclassify their workers as independent contractors as a way to save money. After all, paying for medical coverage, as well as unemployment and workers’ compensation insurance, can be expensive.
The Issue Specific to Roofing
Although many trades are affected by worker misclassification, the construction industry appears to be among the most problematic. A recent report found that more than one million – and perhaps as many as two million – construction workers either are misclassified or receive off-the-books payments. In fact, for many contractors, this misclassification may be fundamental to their business model.
Around the country, there are stories of roofing workers being hired via labor brokers. Many of these brokers operate offsite and pay workers in cash each week. These brokers often target low-paid undocumented workers who have few other options for work. Fearful of being deported, these workers will seldom report unfair labor practices and will take whatever jobs they can get.
However, this cash-only, off-the-books arrangement provides workers with few protections. If they
are injured on the job, they may have no insurance. In addition, if their broker does not pay them, they have no recourse. Workers in skilled trades, such as roofing, appear to be the most widely affected.
Regional Trends
There is no doubt that worker misclassification is a national issue but it may be worse in various areas of the country. For example, according to some surveys, more than 30 percent of construction workers are misclassified in the South, with a nearly 40 percent rate in the state of Texas. In reality, I anticipate that these percentages are much higher.
With the new independent contractor rule that went into effect in March, recognize that if you use subcontractor roofing labor or independent salespeople, you may be at risk of a misclassification case. There are ways to mitigate the risk such as making sure you have sound agreements with your 1099s and that, operationally, you are focused on the independence of non-employees.
We anticipate that there will be additional regulation and legal opinions better defining misclassification in the months to come so stay tuned for additional legal updates.
FRM
The information contained in this article is for general educational information only. This information does not constitute legal advice, is not intended to constitute legal advice, nor should it be relied upon as legal advice for your specific factual pattern or situation.
Trent Cotney is a partner and Construction Practice Group Leader at the law firm of Adams and Reese LLP and FRSA General Counsel. You can contact him at 813-227-5501 or trent.cotney@arlaw.com.
Free Legal Helpline for FRSA Members
Adams and Reese LLP is a full-service law firm dedicated to serving the roofing industry. FRSA members can contact Trent Cotney to discuss and identify legal issues and to ask general questions through access to specialized counsel. They offer free advice (up to 15 minutes) for members. If additional legal work is required, members will receive discounted rates. This is a pro bono benefit provided to FRSA members only. Contact Trent at 813-227-5501.
FRSA Notches Major Victories in 2024 Legislative Session
The Florida Legislature adjourned, sine die, from its 2024 regular session on Friday, March 8 at 2:25pm. Over the course of 60 days, legislators considered over 2,000 pieces of legislation, with 325 proposals ultimately passing both chambers of the Legislature. Among the bills that passed, FRSA enjoyed remarkable success on several of its top priorities. Let’s take a look back at a tremendous 2024 session for the roofing industry.
Green Light for Roof Inspections
Over the last several years, the Legislature has taken landmark steps to shore up the state’s ailing residential property insurance market and to enact key consumer protections for insureds. Among the consumer-friendly measures, FRSA was a key supporter of language to ensure that residential property insurance policies could not be cancelled solely for the age of an existing roof exceeding 15 years. Thus, under s. 627.7011, Florida Statutes, an insured is afforded an opportunity to have a roof exceeding 15 years of age inspected for a determination of remaining useful life. Unfortunately, roofing contractors were inadvertently omitted from the list of “authorized inspectors” permitted to perform such services. This omission was successfully resolved during the 2024 legislative session. HB 1611 Insurance by Rep. Cindi Stevenson (R – St. Augustine) and Sen. Jay Trumbull (R – Panama City) amends state law to include licensed roofing contractors in the list of “authorized inspectors” under s. 627.7011, Florida Statutes. The bill passed the Legislature on March 7 and now awaits action from Governor DeSantis.
Keeping Trail Lawyers Out of the Building Code Process
Legislation was filed early in the 2024 session that would have awarded prevailing party attorneys' fees for successful petitioners seeking interpretations from the Florida Building Commission. The bill, HB 481 Building Construction Regulations and System Warranties by Rep. Randy Maggard (R – Zephyrhills) and Sen. Ed Hooper (R – Clearwater), was well-intentioned but the idea of prevailing party attorney’s fees as an attraction to draw trial attorneys into the building code interpretation process was of great concern to the construction industry. FRSA engaged with industry sponsors, including the Florida
Homebuilders Association (FHBA) and the Associated Builders and Contractors of Florida (ABC) and the bill sponsors to have the attorney fee language struck. HB 481 ultimately passed the Legislature on March 4. It awaits further action from Governor DeSantis.
It’s Tool Time! (Again)
FRSA was a key contributor to efforts in 2022 to establish a state sales tax holiday recognizing Florida’s skilled workforce and students seeking a career in building construction and the trades. That year, the “Tool Time” Sales Tax Holiday was created in partnership with Rep. Bobby Payne (R – Palatka) who chose the week of Labor Day as a time for sales tax free shopping on key items such as hand tools, power tools, work attire, safety equipment and related products. Tool Time was renewed in 2023 by the Legislature as part of the largest tax cut package in the state’s history. This year, despite fewer dollars for tax cuts, the Legislature again renewed the Tool Time Sales Tax Holiday for 2024 under the direction of Rep. Stan McClain (R – Ocala) and Sen. Blaise Ingoglia (R – Spring Hill). For the third year in a row, the sales tax holiday will be enjoyed during the week of Labor Day. Tool Time saves Florida taxpayers nearly $20 million per year and ceremonially recognizes the ongoing accomplishments of our skilled workers. The tax package, HB 7073 Taxation, passed the Legislature on March 8 and awaits signature from Governor DeSantis.

FRM
Chris Dawson is an Attorney and professional Lobbyist for GrayRobinson’s Orlando office and is licensed to practice law in both Florida and Alabama. He primarily focuses on lobbying and government relations for public and private sector clients at the executive and legislative levels of state government. He is credentialed as a Designated Professional Lobbyist by the Florida Association of Professional Lobbyists. Chris also holds two degrees in Civil Engineering and has experience in construction litigation and design professional malpractice defense.
RCASF’s Educational Training Day
Focused on Educating Workers
Lisa Pate, FRSA Executive DirectorAt the end of February, the Roofing Contractors Association of South Florida (RCASF) held their second annual educational training day at SOPREMA’s Pompano Beach training facility. There were 339 attendees, which included company owners, supervisors, foremen and workers. Attendees broke up into groups and rotated through various training stations. You could feel the positive energy in the classrooms and hands-on demonstration areas as topics included: roof coatings clarifications, adhesive applications, hotair welding, safety and fall protection harnesses, fire rescue prevention and first aid, networking, helping property owners after the storm, sales calls, permitting updates and company culture.
In addition to training sessions, there were tabletop displays from vendors, including FRSA. This gave us an opportunity to support the RCASF Affiliate and to meet members and perspective members while sharing benefits and program information. Interesting facts shared by RCASF included:
■ Office track trainers – 5
■ Field track trainers – 19
■ Translators – 5
■ Volunteers – 21
■ Chefs – 4

■ Pastries – 903
■ Sponsors – 9
■ Table sponsors – 12
■ Raffle prizes – 15
Congratulations to the RCASF Board of Directors and Committee members on another successful event!

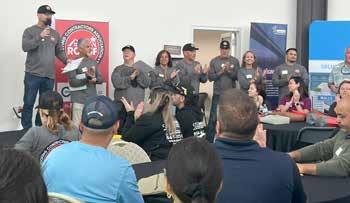
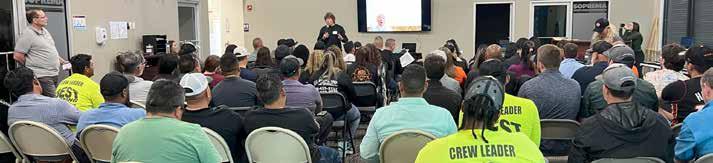
Proactive Risk Planning for Roofing Professionals – Part One
Roofing projects are inherently distinct and frequently embody significant complexities. These endeavors often span considerable durations and require the mobilization of diverse resources such as personnel, materials, machinery and financial backing. Typically, these projects are driven by specific goals or desired outcomes, offering all participants a clear directive and framework.
Exploring Project Risk Management
The essence of project risk management lies in its ability to diminish the likelihood of not meeting project aims while seizing potential opportunities. It enables project managers to effectively prioritize, allocate resources and adopt measures that mitigate the risk of project shortfalls. This strategic approach enhances business and project performance and bolsters decision-making with greater insight and confidence. It underscores informed decisions in project planning and execution phases to circumvent or mitigate risks, capitalizes on opportunities and ensures adept contingency planning and resource distribution aligned with risk assessments and budgetary considerations. Collectively, these efforts lead to increased certainty and diminished overall risk exposure.
The benefits of rigorous risk management, including enhanced opportunity identification and minimized risk exposure, affirm the value of a contractor’s engagement in the process. Superior insights become pivotal at the managerial level, fostering
Florida
5,000 Industry Professionals
517,345
sound decision-making. Furthermore, risk management introduces a structured framework that precludes surprises and advocates for prudent risk mitigation strategies.
Notably, risk management is not exclusive to large or high-risk roofing projects. Institutionalizing this process makes it applicable across projects of all sizes and at every stage from initial strategic assessment and planning to procurement, execution and project completion. Its applications are diverse, spanning budget evaluation for business plans and managing project cost overruns and delays, thereby promoting better accountability and justifying decision-making through a consistent and robust process.
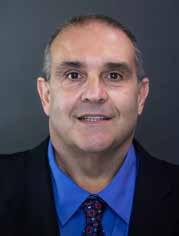
Understanding Risk in Project Management
Risk management is crucial for effective management, achieving superior business and project results and efficient material procurement. Many managers and business owners practice risk management in various forms, albeit without explicitly referring to it as “risk management.” The concept of risk, however, is central to their efforts towards more successful project outcomes.
Integrating risk management activities within an organization’s management framework significantly contributes to the success of roofing projects. Conversely, inadequate risk management can adversely affect the achievement of organizational goals. It is crucial to engage in risk management from the project’s inception and maintain this focus throughout its duration.
Effective project risk management hinges on three primary actions:
■ Prompt and continuous identification, analysis and assessment of risks, coupled with developing strategic plans for management.
■ Allocate risk management responsibilities to individuals best equipped to address them, potentially implementing new practices, procedures or systems. Print
■ Ensure that the investment in risk reduction is proportionate to the project’s significance and the associated risks.
A comprehensive risk management approach should cover risks related to overall business strategies, the design and execution of the roofing project and financial considerations. Business risks encompass those that could impact the entire company’s operations, while project risks pertain to factors affecting the project’s cost, timeline or quality. Financial risks include variables like fluctuating material costs, inaccurate estimations, payment delays or undertaking projects that exceed a contractor’s financial acumen.
Developing a risk assessment matrix is advisable when preparing for an upcoming roofing project. This tool facilitates the identification and prioritization of risks by evaluating their likelihood and potential impact. The process begins with asking, “What could go wrong?” Then followed by:
■ Identifying hazards: Recognizing all potential risks to the project.
■ Analyzing risks: Carefully evaluating identified risks.
■ Assessing risk probability: Rating the likelihood of risks occurring throughout the project’s lifecycle on a scale from one (rare) to five (almost certain).
■ Determining risk severity: Grading the potential impact of risks from one (insignificant) to five (major).
■ Risk rating: Grading the overall project impact of identified risks from one (negligible) to five (extreme).
Above are an illustration of a Risk Rating Key and a hypothetical Roofing Project Risk Analysis Sheet. It’s important to regularly review your risk assessment matrix to identify any new or evolving risks.
Risk Ownership
Identifying and prioritizing risks culminate in establishing a risk owner role – individuals tasked with ensuring effective risk management. The risk owner coordinates all necessary actions to manage each identified risk. In roofing, stakeholders and project teams should
strive for risk mitigation. Designating a risk owner is crucial as it guarantees the development, upkeep and timely execution of a risk response plan.
Stay tuned for next month’s conclusion in this series, where we will delve deeper into the strategic responses to risks identified in roofing projects. Part Two will explore the various risk management strategies, including avoidance, transfer, mitigation and acceptance. We’ll also discuss the crucial process of ongoing risk monitoring and introduce the quantitative aspects of risk management. Whether you want to enhance your project outcomes, improve operational efficiency or safeguard your financial stability, Part Two will provide valuable insights and practical tips for roofing professionals looking to elevate their risk management approach. FRM
John Kenney, CPRC has over 50 years of experience in the roofing industry. He started his career by working as a roofing apprentice at a family business in the Northeast and worked his way up to operating multiple Top 100 Roofing Contractors. As CEO, John is intimately familiar with all aspects of roofing production, estimating and operations. During his tenure in the industry, John ran business units associated with delivering excellent workmanship and unparalleled customer service while ensuring his company’s strong net profits before joining Cotney Consulting Group. If you would like any further information on this or another subject, you can contact John at jkenney@cotneyconsulting.com.
Hip, Ridge and Rake Tile Installation Using the FRSA-TRI Manual
Mike Silvers, CPRC, Owner Silvers Systems Inc. and FRSA Director of Technical ServicesHip and ridge conditions have proven to be the weak point observed post hurricane in all roof covering types. The occurrence of these failures on tile roof systems have been reduced significantly since the FRSA-TRI Florida High Wind Concrete and Clay Tile Installation Manual (the manual) became effective in August of 2005 as the 4th Edition. This and subsequent editions have been revised to significantly improve the performance of tile hip and ridge. When the installation techniques described in the manual are followed, hip and ridge, as well as other portions of tile roofs, perform admirably, often with no observed failures. The failures of tile hip and ridge can almost always be traced back to applications that were not in compliance with the manual or the HVHZ roofing application standards (RAS), which can be be used in lieu of the manual. The purpose of this article is to help clarify what is required in the manual as well as addressing proper roofing practices.
The hip and ridge table below outlines the different parameters for hip and ridge attachment options and is where our understanding of proper applications begins. Start in the first column to choose the method you will use to install the field tile. If using a structural member, choose which type in the second column, follow the installation guidelines in the appropriate row or the manufacturer’s recommendations. We will address the use of mortar as a structural support later. First, let’s review each of the structural member options. Metal Member – Set member in plastic cement or compatible sealant. Fasten 6” on center on each side
of the metal flange with minimum 1-1/4” ring shank roofing nails. If mechanical attachment of the member is not used, install the member with foam per the manufacturer’s instructions. The member should be cantilevered to provide a base for the adhesive for the starter tile. Review the following drawings that demonstrate why cantilevering is important and several different options when doing so.
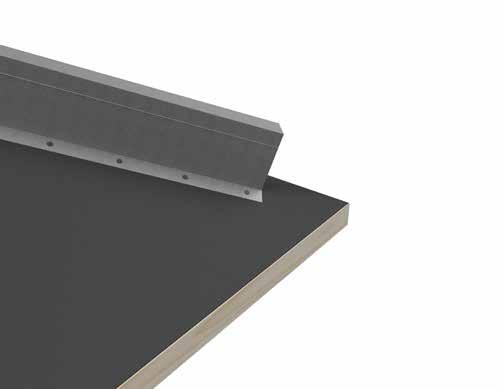
The lower part of the metal is five to six inches from the outer edge without a cantilever.
Important: the above installation is one typically found in the field, however, it does not allow the adhesive to make continuous contact with both the ridge cap and support on the first tile.
HIP AND RIDGE ATTACHMENT TABLE
The following drawings are structural hip and ridge support options that allow adhesive to make continuous contact with both the bottom of the tile and the structural support.
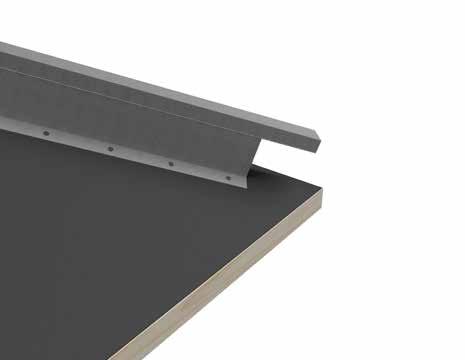
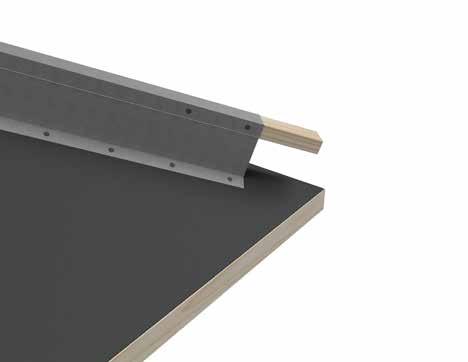
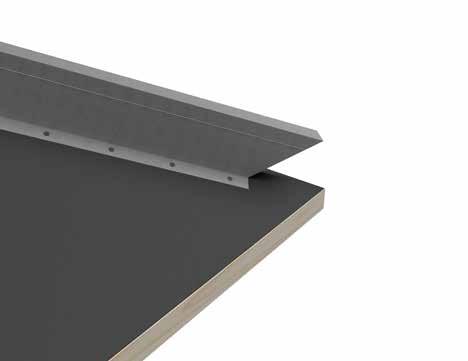
FRSA members have access to codes and technical support from FRSA staff.
Not a member? Call Kelly Sealander at 800-767-3772 ext. 142 for more information.
www.floridaroof.com/membership
One inch from the lower edge of the hip.
The lower part of the metal is five to six inches from the outer edge of the hip.
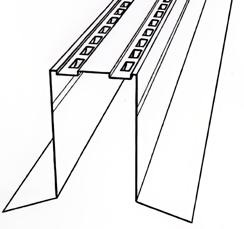
Metal member with perforations for improved foam adhesion.
Metal hip and ridge support frame installed per the manutacturer's product approval.
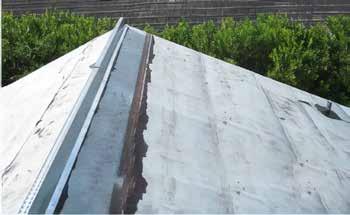
Seal all nail penetrations with compatible roof cement unless the underlayment meets ASTM D1970 sec. 7.9.
Metal member installed at ridge with sealant.
Wood Member – Fasten 18” on center with four #8 screws per metal strap or H-bracket. Each attachment point shall have two fasteners on each side of the wood member. The fasteners shall be spaced evenly on the metal strap or H-bracket with the attachment holes parallel to the hip or ridge. The straps and H-brackets shall be a minimum of 26 gauge. All materials must be compatible with each other. If mechanical attachment of the wood member is not used, install the member with foam adhesive per the manufacturer’s instructions. Member must be pressure treated and must be of sufficient height to maintain an even plane of trim tiles.
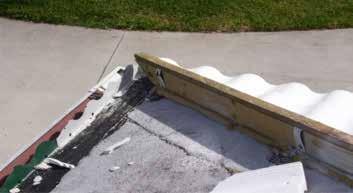
Adjusting the height of wood member note: Stacking nailer boards may be used to adjust height. Maximum thickness of 2” per additional nailer board.

Plastic Member – Install the member with foam per the manufacturer’s instructions. (Coastal)


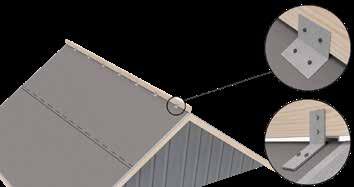
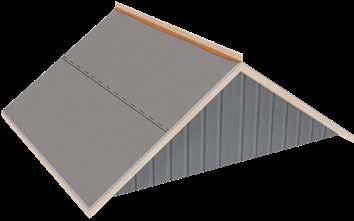
Metal (with approval), wood and plastic hip and ridge members may be set in adhesive per the manufacturer’s instructions.
Field Tile Cuts at Hip or Ridge – All cut field tiles adjacent to a hip or ridge shall be attached to the cap sheet and/or the adjacent tile with an approved adhesive, mortar or mechanical fasteners and adhesive.
All field cut tiles (two tiles on each side of hip) and the top course of ridge tiles must be attached to the substrate with code-approved adhesive, code-approved mortar or mechanical fasteners and adhesive.
In situations where the ridge course of tile has been cut, the field cut tile and the full tile course below the cut tile must be attached to the substrate as well. This
requirement is designed to minimize any dynamic movement of the field cut tiles, at the most stringent zones of the roof, which may occur during a high-wind event such as a hurricane.

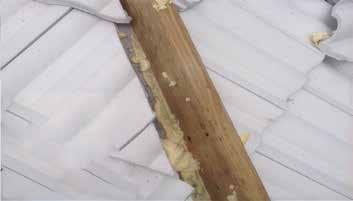
Cut tiles without nail holes may be drilled, notched and nailed or affixed with tile adhesive, wire or cut tile clips (approved adhesive is the most commonly used method of attaching cut pieces).
Installing Hip and Ridge Tile
Mortar for Attachment – When using foam or mortar field tile attachment, mortar can be used as a structural attachment. Place a full bed of pre-bagged mortar under the entire tile. Each tile must be fully embedded into the mortar. The field tile secured to the underlayment along with mortar on each trim tile creates the structural bond. Install hip and ridge tile in a continuous bed of FBC-approved pre-bagged mortar as structural support and weather blocking. The entire cavity under the trim tile should be filled with approved mortar. Miter or point-up the hip starter tile to match the intersecting eaves.
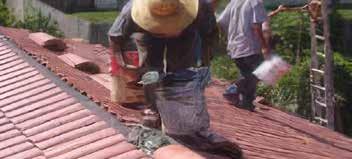
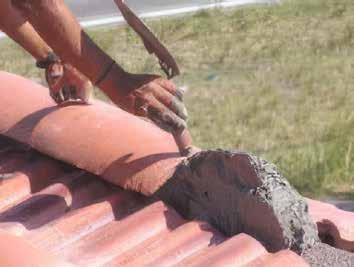
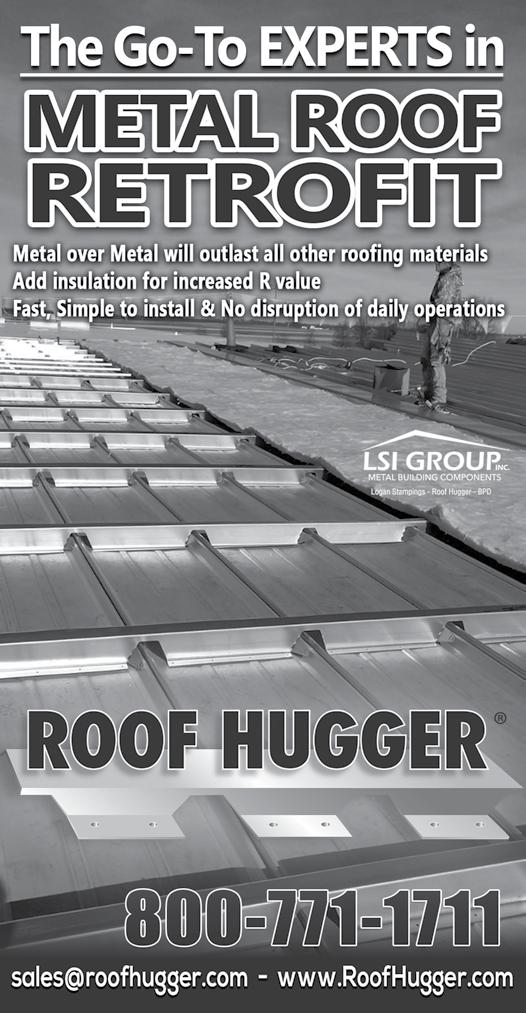
Starter Tiles – All starter tiles must be secured at both ends of the tile either with mechanical fasteners, mortar and/or adhesive. When the field tile is installed with foam or mortar, the starter tile may be installed with an approved mortar and/or adhesive. The starter tile must make continuous contact with the adhesive. See manufacturer’s recommendations or the specific installation techniques for different type support members below.
After the Starter Tile – Install the next tile, centering over the structural support and/or the starter tile. Continue in the same manner working from the lowest point toward the highest point of the roof. At intersecting junctions (e.g. hip/ridge, ridge/gable, ridge/ valley), cut tile to form a solid fit and ensure the first and the last hip/ridge tile is securely fastened. Any exposed fasteners shall be sealed with a UV-resistant sealant. The minimum head lap when installing the hip and ridge tiles is 2”, as stated in the FRSA-TRI manual. It may be necessary to increase the head lap to cover exposed hip/ridge tile fastening holes or adhesive. Cover exposed fasteners with a UV-resistant sealant. Note: Hip and ridge tile can’t make contact with field tile before it contacts adhesive and the member.
On Metal Member – Place foam under starter tile per manufacturer’s recommendations or secure the head of the tile with one #8 screw and apply adhesive in the gap between the structural support and the tile. The member may need to be cantilevered to provide a base for the adhesive.
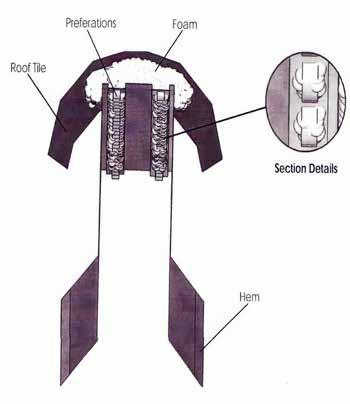

On Wood Member – Place foam under starter tile per manufacturer’s recommendations or drill a hole in the lower third of the starter tile and secure with a mechanical fastener into the wood member a minimum of 1”. Seal the head of the fastener with a UV-resistant sealant. Adhesive may be used in lieu of a fastener as long as the wood member has been cantilevered to provide a base for the adhesive. The gap between the structural support and the tile must make contact with the adhesive. See manufacturer’s recommendations.

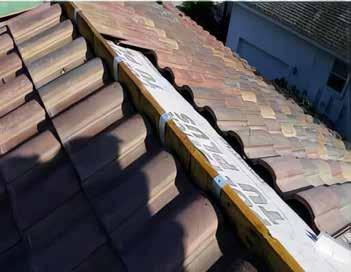
The use of mechanical attachment to wood member
tile foam adhesive or other approved tile adhesive placed at hip or ridge overlap is an acceptable application.
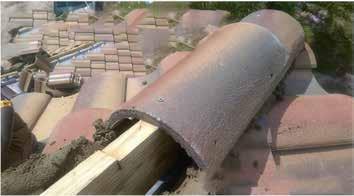
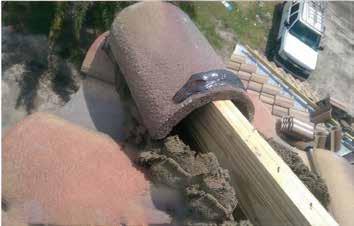
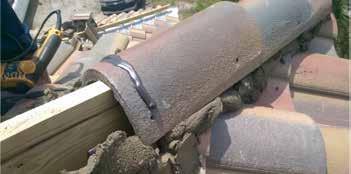
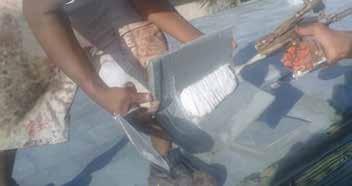

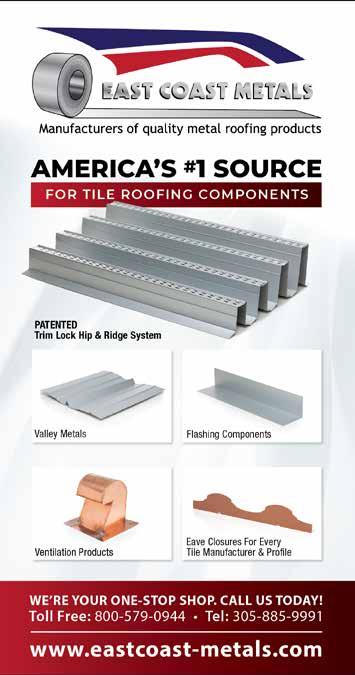
Weather Blocking – Hip and ridge tiles need to have weather blocking, it is mandatory in Florida for all profiles. It protects the underlayment and flashings. It also provides hip and ridge with finished appearance while increasing the overall life and performance of the roofing system. Mortar, mastic, pressure-sensitive roll adhesives or polyurethane foam can be used. Choose one of the following:
1. Mortar – Pre-bagged or jobsite mix is used to weather block the longitudinal edges of the hip and ridge tiles and provide aesthetics. A full bed of mortar is placed along the longitudinal edges of the hip and ridge tile either during the application of the hip and ridge tiles or may be packed in after the hip and ridge tiles are installed and the adhesive has cured. Install mortar to seal all voids between the field tile and the hip/ridge tile. Care should be taken to ensure enough mortar is used. The mortar should create a wedge to keep it from dislodging from under the hip/ridge and the field tile junction. Ensure areas are sealed to prevent water entry. After the mortar is packed into place, then apply point-up mortar to the desired finish.
2. Foam – Is used to weather block the entire cavity of the adjoining planes of field tile to the sides of the structural support. This system uses foam as the weather blocking. There is no mortar placed along the longitudinal edges of the hip and ridge tile. Foam is placed where the field tile abuts the structural support. A bead of foam is placed parallel to the hip and/or ridge and the structural support to tile junction to act as a weather block and is applied prior to the attachment of the hip and ridge tile. Install foam to seal all voids between the field tile and the structural support. Care should be taken to ensure all areas are sealed with adhesive to prevent water entry. Apply a polyurethane compatible coating to protect the foam from UV exposure.
3. Pressure-sensitive Roll Adhesives – This system can be used with a wood structural support. The flexible self-adhered membrane is applied in a continuous or step fashion, sealing to both sides of the adjoining field tile a minimum of 2” prior to the mechanical attachment of the trim tile to the wood structural support. The flexible flashing may be visible but should not extend onto the field tile beyond the outside edges of trim tile.
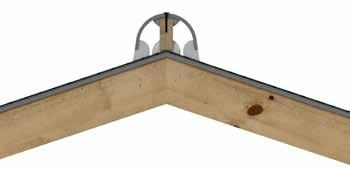
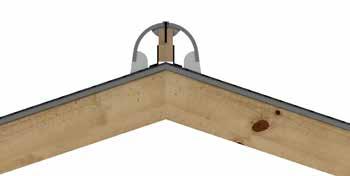
Mechanically attached wood hip and ridge boards using metal brackets. Use mortar or foam adhesive as weather blocking.
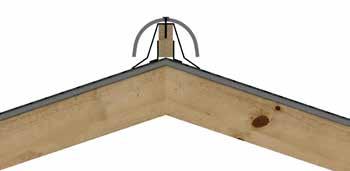
Mechanically attached wood hip and ridge boards using metal brackets. Cover with self-adhered weather blocking.
Adequate amounts of pre-bagged or job mix mortar should be used to insure a proper finish of the weather blocking point-up. Mortar should match the tile finish color.
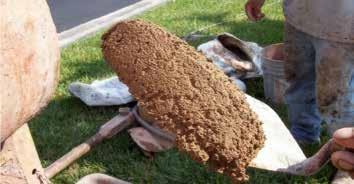
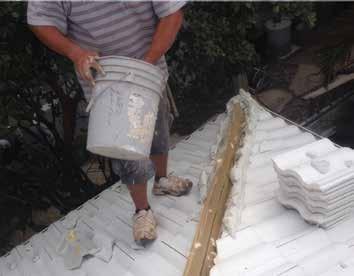
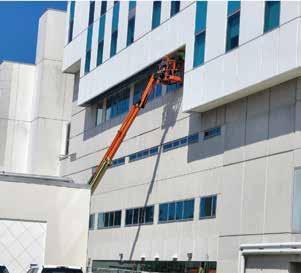
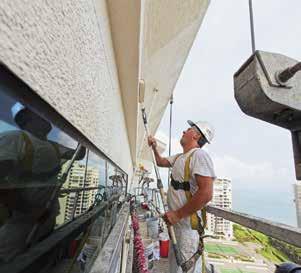
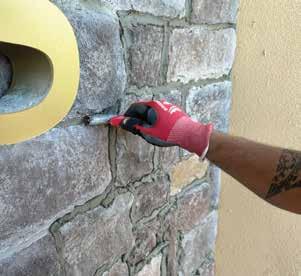

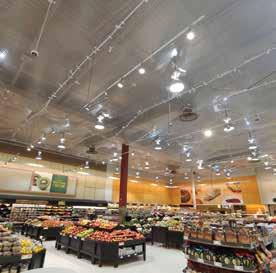

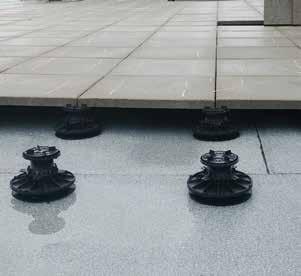
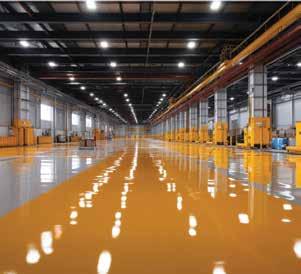


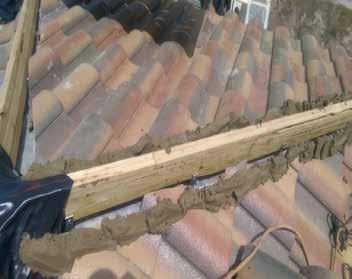
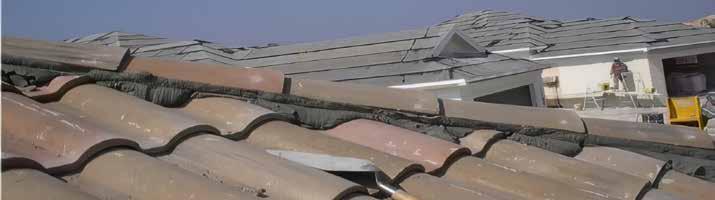
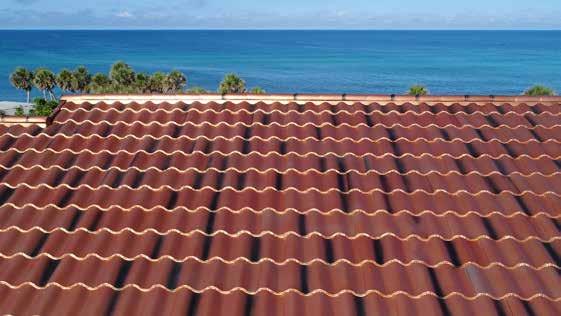
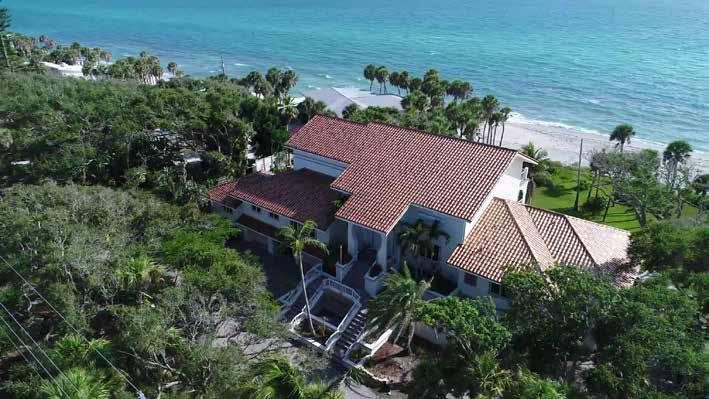
Abut each succeeding rake tile to nose of the field tile above and maintain a constant headlap.
Cut and install first rake tile the exposed length of first eave tile with factory finish of rake tile towards the eave.
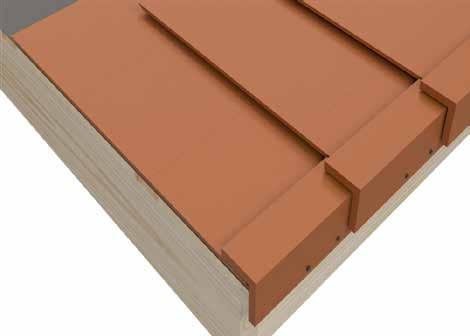
Fasten rake tile with a minimum of two 10d nails and/or #8 screws. Fasteners to be of sufficient length to penetrate the frame a minimum of 3/4”.
Gable/Rake
Choose one of the following:
Rake Tile – Cut and install first rake tile with the exposed length of first course of field tile with factory finish of rake tile towards the eave. Fasten rake tile with a minimum of two 10d nails of sufficient length to penetrate the framing a minimum of 3/4”. Butt each succeeding rake tile to the nose of the field tile above and maintain a constant headlap.
Mortar Finish – Place mortar bed along roof edge. Point smooth to a straight edge finish.

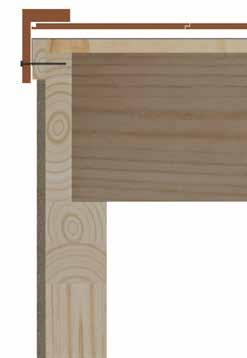
Installing Rake Tile
Two corrosion resistant fasteners shall be used on rake tile of sufficient length to penetrate the framing a minimum of 3/4”. For tile installations with a 3” head lap, cut the first rake tile to lay flush with the eave course tile. Abut the consecutive rake tiles to course above so that the factory finished butt ends are exposed. Place thick end of rake piece toward ridge.
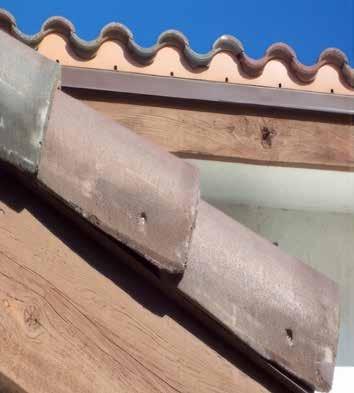
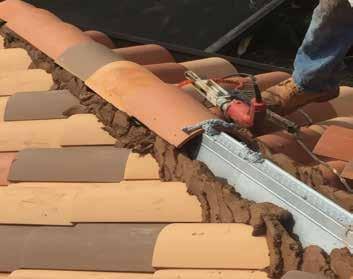
An example of an incorrect installation that leads to failures.
Had installers used these applications in the past and following them consistently since their implementation, we would not have observed the failures that occurred during recent storms (see failure examples below and to the right). The variables in material consistency associated with mortar itself is one concern. The inconsistency of the installation (placement and quantity of mortar) is the other. The addition of support members creates a more controllable and consistent installation method. This results in fewer failures by providing better uplift resistance.

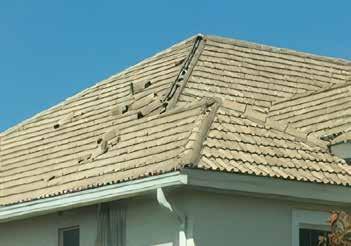
If installers become familiar with the methods described here and in the manual, we should be able to provide tile roof systems that can resist the uplift forces caused by design windspeed hurricanes. This in turn will help demonstrate how well tile roofs can perform.
FRM
Mike Silvers, CPRC, is owner of Silvers Systems Inc. and is consulting with FRSA as Director of Technical Services. Mike is an FRSA Past President, Life Member, and Campanella Award recipient and brings over 50 years of industry knowledge and experience to FRSA’s team.

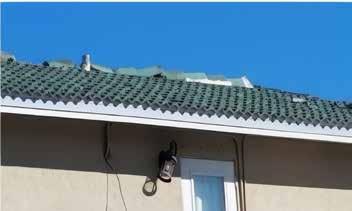
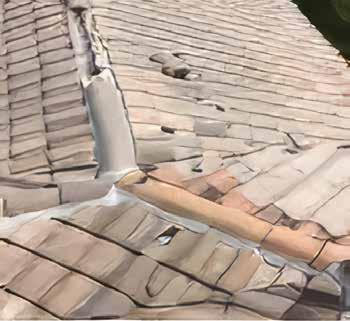
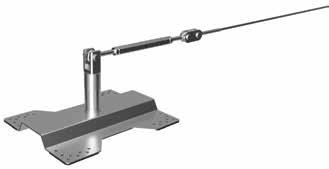
Tie Back Roof Anchors
•
•
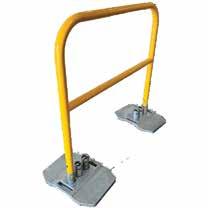
•
•
•
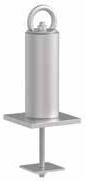

Technology and Roofing
Riku Ylipelkonen, Owner, Standard Building Advisors and FRSA Technical AdvisorTo most Florida residents, the roofing industry does not come to mind when thinking of careers at the forefront of technological advances and innovation. When perspective home buyers are asked, they speak about kitchens and bathrooms or huge windows for natural light. The roof is not usually mentioned. With advances in energy conservation, better wind uplift performance and innovative use of materials applied in new ways, the roofing industry is changing at a faster pace than the typical homeowner may be aware. While the materials used to construct the roof are changing, one must also look at how changing technology and innovation affect the means and methods of construction. Let’s look at what else is happening and how contractors can use these advances to their benefit.
Permitting is one of the first steps every project must undergo. The design on the roof, supporting approvals, testing and specifications all need to be gathered and submitted for plan review to gain the permit to perform the work. This process is easier if you have a tried-and-true system that sells and performs well. New system components and changes in building code requirements usually add complexity and the need to verify the paperwork and applicability of systems that have been reliable in the past. Some jurisdictions are implementing electronic permitting to simplify and speed up the process on these roof assemblies. If your municipalities don’t offer this, it is worth asking about. The permitting process is streamlined because the trip to the municipality’s office begins and ends at your keyboard. On the other side, the plans examiner now has an electronic filter that reduces the time needed to verify the validity of the permit.
Company phones have been a valuable tool to maintain contact with all the stakeholders within the roofing company. New applications are always being developed and may make the process of staying connected easier. The use of live video conference calls on mobile phones is being used to carry out inspections by some municipalities. Waiting onsite for an inspection is no longer the norm. What you need to have to get the inspection completed and passed is also changing. If your coverage jurisdictions do not offer this yet, it is coming. For the authority having jurisdiction (AHJ), this increases efficiency for an inspector who can sit at one location and receive calls from the entire municipality without the time and expense of traveling to each location. On the contractor’s side, this alleviates the time and expense of waiting for inspectors on location if scheduling is favorable. Having personnel onsite with a working mobile phone is fast becoming the preferred way to
perform inspections. This is a step up in the efficiency and effectiveness of our schedules. Make sure to gather photos, videos and any pertinent notes during the inspection and store them in a database with a file folder for the project. Documentation and recordkeeping make the difference in the long run.
The adaptation of business practices has accelerated in response to the COVID pandemic. Technology that was already in place is being utilized to streamline and improve the roofing project checklist. The next step is the application of artificial intelligence or AI for short. While the roof will continue to be designed, specified and constructed by real people, the supporting activities like permitting, inspections and other tasks will likely change further by the application of AI. How this develops is still evolving. An important part of AI implementation in the roofing industry will be saving time and expense in new ways. This is a much-needed change when resources and labor are in short supply.
Imagine a phone app where you input the building address. From there, software can perform a take-off, design the roofing system options and send an email message with the options in a contract to the customer. Any modifications can be done live with all changes tracked and agreed to within the app. Next, the app receives the signed contract and payment, fills out permitting online, orders the materials to ship to the location with timing that fits your crew schedule and reports progress to all interested parties automatically. From there, crews perform the work, inspections are scheduled automatically with the authority having jurisdiction and completion is documented and archived. While this example is missing a lot of content and context, it also shows the step to automated contracting that may be available in the near future.
Can the industry come together and agree that real people should answer and make phone calls though? FRM
Riku Ylipelkonen, Owner, Standard Building Advisors has been in the roofing industry for 15 years working for Polyfoam Products. When Polyfoam Products was acquired by 3M and the name changed to ICP Building Solutions Group. Riku worked at ICP as Technical Services Manager until March of 2023, when he left to begin his own company. Riku is an engineer and is working as a consultant with FRSA. He is a member on FRSA’s Codes Committee, Codes Subcommittee, Tile Committee and on the FRSA-TRI Manual Rewrite Committee. Riku is also a member of the American Society of Civil Engineers (ASCE).
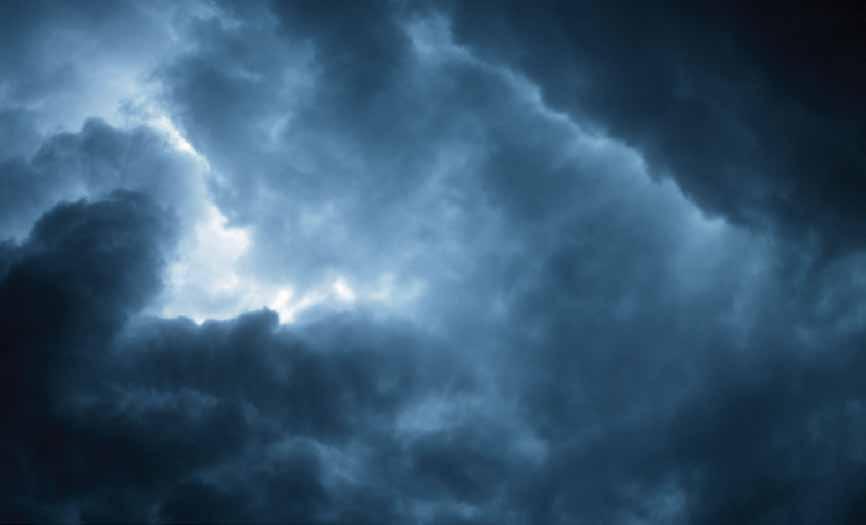
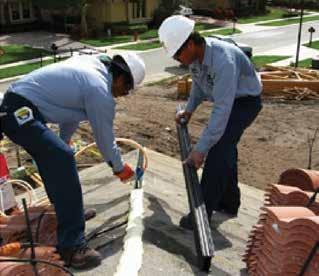
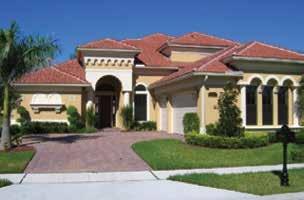
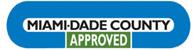
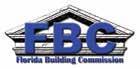
FRSA-TRI 7th Ed Tile Manual Offered
as
Advanced Seminar at Convention
Manny Oyola, Jr., Technical Manager Eastern Region FL, Eagle Roofing ProductsJust as some of us were getting ready to count down the last minutes of 2023 (while others were already asleep), the 8th Edition (2023) Florida Building Code (FBC) took effect. When it did, the FRSA-TRI 7th Edition Florida High Wind Concrete and Clay Tile Installation Manual (the tile manual) also went into effect. The tile manual is referenced by the FBC for tile roof installations throughout 65 of 67 counties in Florida; it may not be used in Miami-Dade and Broward Counties.
On each day of the Convention in June, I, along with Paul Oleksak from Westlake Royal Roofing Solutions, will be presenting a one-hour seminar for advanced (ADV) CILB CE credit: for scheduled times, take a look at the Convention brochure in the center of the magazine. The seminar will contrast changes between the previous 6th Edition and the current 7th Edition of the tile manual as well as provide an overview of how to use the manual for a tile roof installation. Here’s a sneak peek at what we will be looking at in June.
Changes in the 7th Edition Tile Manual
There were many updates to the tile manual. We will look at each of these in more detail. The following items represent several of the major changes:
■ Underlayment & Flashings Matrix
■ Elimination of Table 1A Enhanced Fastening of Two-Ply Hot Mop
■ ASCE 7-22 Roof Zones

■ ASCE 7-22 Values for Underlayment and Ridge Attachment
■ ASCE 7-22 Required Uplift of Field Tiles.
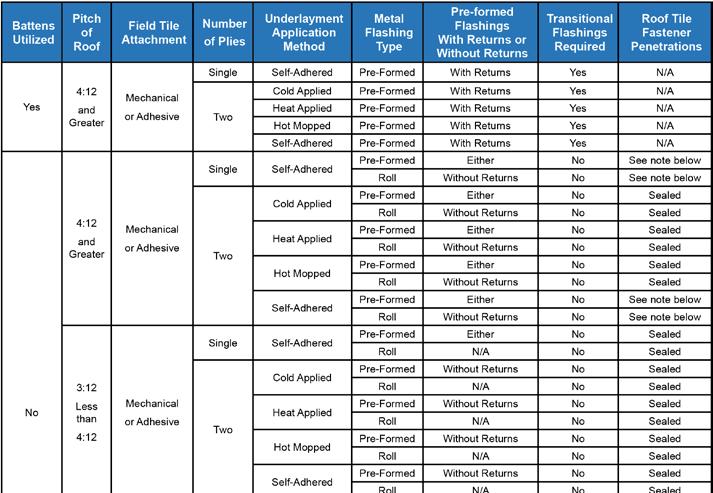
Underlayment & Flashings Matrix
The “Underlayment & Flashings Matrix,” which is shown in part on the previous page, is the starting point when using the tile manual. (I have shown only part of it because it is important to use the actual manual and not figures in this article or those seen in a presentation.) As an FRSA member, you are entitled to one free copy of the tile manual and can purchase additional copies at a discount.
As indicated with the red line, you start on the left side of the matrix and select the applicable characteristics for your installation. In this example it is for a roof with:
1. No battens
2. A roof pitch of 4:12 or greater
3. Field tile attached mechanically or with adhesive
4. Single-ply underlayment that is self-adhered
5. Pre-formed flashings with or without returns and
6. Does not require transitional flashings. When you are working on an installation with characteristics different than this example, you simply use the matrix to match the characteristics of the roof you are installing. The “See note below” listed under the “Roof Tile Fastener Penetrations” instructs you to “Refer to the underlayment manufacturer’s written installation instructions or Product Approval.” This will determine if sealant is required for fasteners that penetrate the underlayment or if the underlayment demonstrates fastener sealability. During the seminar, we will discuss the matrix in more detail.
Elimination of Table 1A
In order to update the tile manual, members of the FRSA-TRI Tile Manual Committee for Florida met over the period of many months to review the existing manual and develop changes that will not only improve the manual but to keep it compliant with the FBC. As committee members looked at the 6th Edition, Table 1A stood out as an item that needed to be removed. Table 1A provided prescriptive fastening values for two-ply hot mop underlayment. Members of the committee agreed, however, that this underlayment system should be required to meet wind uplift values through testing like all the other underlayment systems. As a result, the table was removed from the 7th Edition. Instead, when a two-ply hot mop system is installed, we use the same tables found in the tile manual that are used by the other systems to determine fastening requirements and use the manufacturer's product approval to determine the underlayment uplift resistance.
ASCE 7-22 Roof Zones
If you have been installing tile roof systems in Florida for more than a few years, you will remember that when the Florida Building Commission adopted ASCE 7-16 – over the objections of FRSA and other industry voices – it significantly complicated the layout of roof zones used to calculate fastener requirements to provide required wind uplift. Under ASCE 7-10 (used in the 5th Edition tile manual) there were three separate roof zones: the corner, the edge and the field. The corners experience the greatest wind uplift and so require the
highest amount of fastening resistance, then the edges and the field, which require the fewest number of fasteners relative to the other zones. As you can see by comparing the two diagrams for gable roof zones, under 7-16 there are six zones (1, 2r, 2n, 2e, 3r and 3e) while under 7-22 (as well as 7-10) there are only three zones (1, 2 and 3). The same differences hold true for hip roof zones. The reduction in the number of zones simplifies the fastener calculation process for contractors who want to decrease the number of fasteners used (helping to keep the price of the installation down) by calculating for each of the zones rather than calculating the attachments needed for the corners and then using the same number for the entire roof. The larger the roof size, the greater potential savings there can be from making the effort to calculate for each zone. However, for many contractors, the simplicity of using the highest pressure for the entire roof will be their standard approach.
The Roof Project Design Flow Chart and Design Value Tables
One of the main goals of the tile manual is to reduce the math involved in calculating the necessary mechanical or adhesive fastening requirements for a given roof tile system. That math can be quite involved as the note in Example 1 of the tile manual (page 20) indicates:
The ultimate design wind speeds, Vult, have been converted to nominal design wind speeds, Vasd, since roof tile attachments systems are based on test results.
Ke = Ground Elevation Factor = (ASCE 7-22 Chapter 26.9)
Ke = 1.0 up to 1,000 ft.
Kzt = Topographic Factor: Kzt = 1.0 (ASCE 7-22 Chapter 26.8.2)
Kh = Velocity Pressure Coefficient (ASCE-7-22 Table 26.10-2)
V = basic wind speed (mph) (ASCE 7-22 Fig. 26.5-1D) (170 mph)
Which provides us with the following equation:
qh=.00256*kh*Kzt*Ke*V2 = .00256 (1.04) (1.0) (1.0) (132 mph2) = 46.38 psf.
Instead of having to understand and find the values for each of the constants in the above equation, the tile manual allows installers to look up values in the appropriate table (based on the roof type and exposure category) and plug those numbers into the relatively simple roof project design flow chart to arrive at code-compliant fastening techniques for a given installation.
Attend FRSA Seminars in June
Tile Manual Diagram FHW-27 – Loading Guide Example
In addition to the quick overview of some of the items in the 7th Edition tile manual that we have covered here, the seminar will walk through using the Design Flow Chart in tandem with the Design Pressure Tables, review a ASCE 7-22 Wind Map for Florida and present the drawings and diagrams (like the tile loading guide diagram below) that make up the second half of the manual. Each attendee at the Advanced FRSA-TRI 7th Ed Tile Manual seminar will receive a copy of the 7th Edition tile manual that can be used in the field when installing tile roof systems in 65 counties throughout Florida. Perhaps most importantly, by attending this and other seminars at the FRSA Convention, you’ll have an opportunity to ask questions about related challenges you face during field installations. I look forward to seeing you there.
FRM
Manuel “Manny” Oyola, Jr., Eagle Roofing Products, holds a roofing contractor’s license and is an active member of the Tile Roofing Industry Alliance (TRI) and the Palm Beach County Roofing and Sheet Metal Contractors Association, the local FRSA Affiliate. He is also an active member of FRSA’s Codes Committee and Chairs the Codes Subcommittee, serves as President-Elect on FRSA’s Executive Committee and participates on the FRSA-TRI Manual Review Committee. Manny teaches roof tile courses for TRI and FRSA.
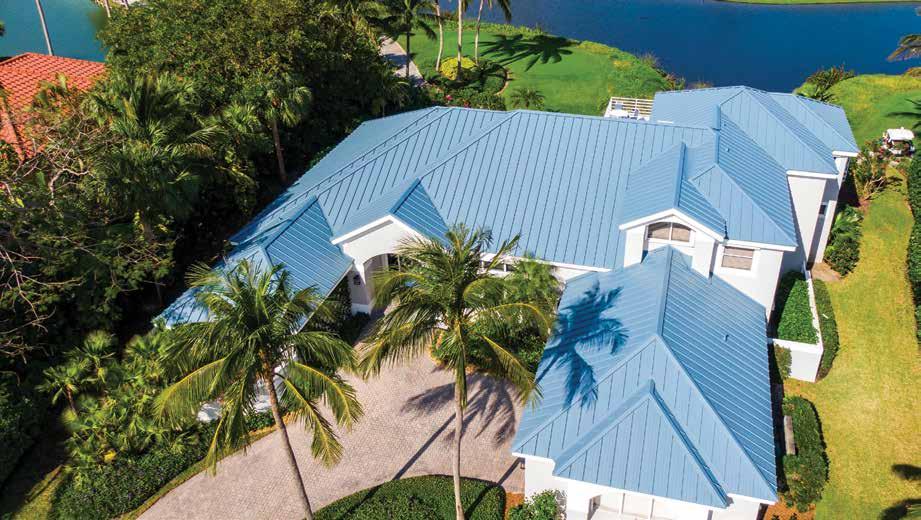




Iguanas on Roofs?
Michael Ronquillo, Owner, Humane Iguana Control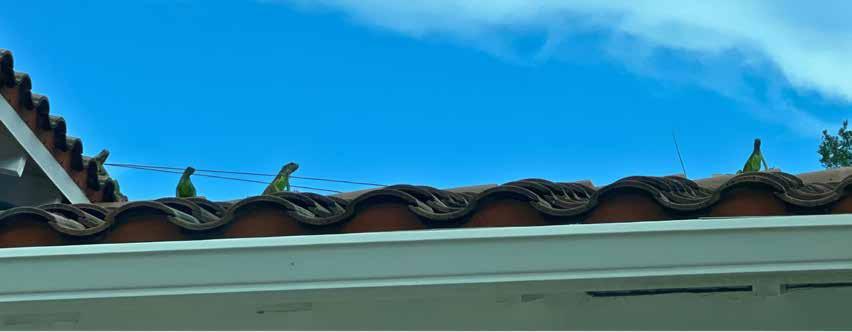
Yes, it’s a common problem in Florida. Iguanas are some of the largest lizards found in the Americas, with their whiplike tail making up about half of that length. Like other reptiles, iguanas are cold-blooded, egg-laying animals with an excellent ability to adapt to their environment. The growing population of invasive iguanas throughout the state has raised concerns for many residents.
This infestation has not only affected roofs on homes but on businesses and schools as well. Although they are an unusual problem, iguanas can cause damage to roofs, leaving property owners with costly repairs. Broken roof tiles are a sanctuary for iguanas, enabling them to hide from predators. If there is rotting wood on the roof, get ready for unwanted guests that will keep homeowners up at night.
Iguana Damage to Roofs
Most have seen iguanas on the ground but in South Florida, they love to sunbathe on roofs to regulate their body temperatures. At times, you may even find more than one. Don’t be deceived, they are doing much more than sunbathing. During the day, iguanas will feed off the plants around your property and find a water source to drink from such as swimming pools. They are great climbers and can easily access the roof through trees and bushes that are close to the roof line. Once iguanas establish themselves on a roof, they will find shelter in broken roof tiles or damaged fascia boards and make this location their new home. Iguanas have very sharp nails that can cause damage inside an attic to sheetrock, insulation and electrical cables. In addition, they can access the interior of homes through plumbing stacks and end up in toilets if pipes are not covered with a wire mesh.
While on the roof, they also defecate consistently and, over time, their feces can cause damage to roof tiles. Their feces contain uric acid, which can be corrosive to certain materials, including roofs. As the feces accumulate and dry out, the uric acid can eat away at
the surface of the tiles, leading to discoloration, pitting and deterioration. We recommend removing iguanas from the property to avoid potential damage.
Health Risks of Iguanas on the Roof
In addition to causing roof damage, iguanas pose significant health risks that must be considered. Iguana feces carry salmonella bacteria, making contact with it potentially hazardous. Roofers may be unaware of these risks. When it rains, the feces on the roof washes off and splatters around the property, further increasing health hazards. If iguanas live in the attic and frequently defecate, it can soften the sheetrock and lead to collapse. Moreover, iguana feces in the attic can cause mold to build up, posing another health risk. They also carry ticks and mites, which can breed rapidly and carry diseases such as Lyme disease, posing a problem for humans and pets. It’s crucial to remove any iguanas living in the attic before patching up any holes to prevent the presence of dead, rotting iguanas in the attic.
A Bird? A Plane? Nope, it’s a Falling Iguana! Falling iguanas in Florida have become a national phenomenon, particularly during the cold months when temperatures drop to around 45°F. During this time, iguanas become immobilized, increasing the likelihood of falling from trees. This can pose a comical but also dangerous situation for roofers and homeowners. Male iguanas, which can weigh up to 25 pounds and reach 6 feet in length, present a significant hazard. Their falls not only pose a risk to individuals but can also cause damage to aluminum roofs and roof tiles, leading to costly repairs.
During mating season, alpha males may engage in territorial fights, leading to falls from trees as they compete for dominance. It’s crucial for roofers and homeowners to be vigilant in dealing with an iguana infestation to avoid bodily harm and property damage.


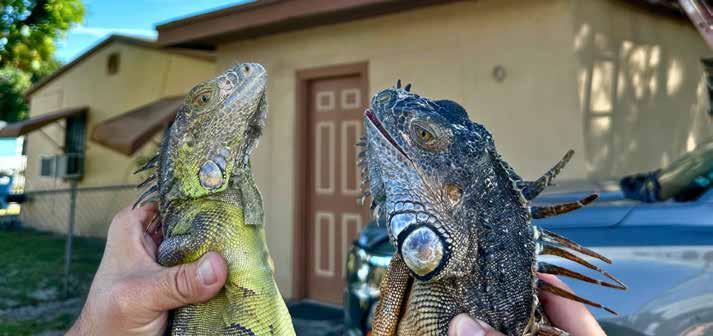
Preventing Damages and Bodily Harm
To prevent damage to the roof and potential harm to people, there are several effective measures homeowners can take. If a home has trees hanging over the roof, it’s essential to trim them back. This not only keeps iguanas off the roof but also prevents damage from falling iguanas. Similarly, if you have lush ivy on walls, cutting it back prevents iguanas from using it as a ladder to access the roof. It’s important to note that
iguanas can jump about two feet, so look for palms or tree trunks near the roof. An alternative to cutting down trees is to install clear tree wraps. This transparent and slippery material deters iguanas from climbing since they are unable to secure a grip with their sharp nails. By proactively implementing these measures, homeowners can keep iguanas away and avoid costly repairs.
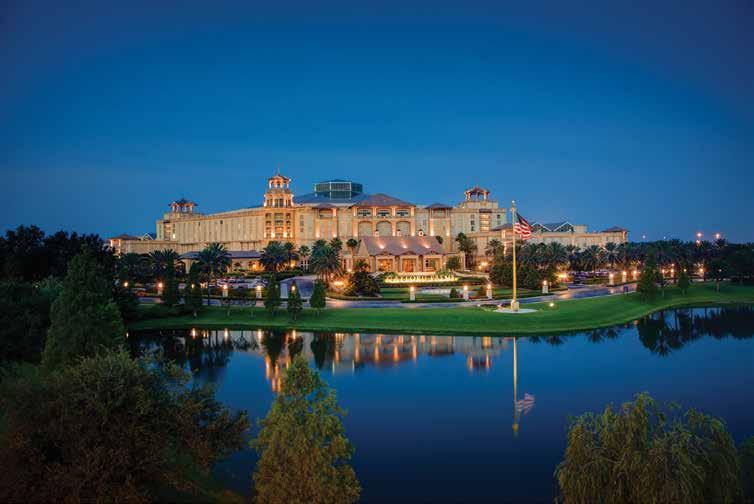
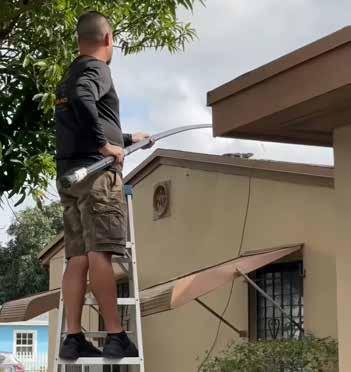
Should Iguanas Be Removed?
Did you know that there are three species of iguanas in Florida? These include the common green iguana, black spiny-tailed iguana and the Mexican spiny-tailed iguana. All three species are considered invasive. If you’re considering removing them, there are legal and practical considerations to keep in mind. While
iguanas are invasive, they must be removed and euthanized humanely, following the state’s laws. It’s illegal to catch an iguana and relocate it to another area, as this can spread the infestation. Green iguanas are usually calm but can become agitated and defensive when cornered. They use their tails to defend themselves, whipping at speeds of 30 mph and have sharp claws and teeth that can cause injury. For safety, it’s best to hire an iguana removal specialist. Our company has helped roofing companies, homeowners, schools and establishments rid their properties of iguanas. Having the right tools and techniques is essential for successful removal. FRM
Humane Iguana Control is a family-owned iguana removal company passionate about preserving the ecosystem. Their mission is to provide professional and eco-friendly solutions to help control the iguana population in South Florida while maintaining the delicate environmental balance. With their team of experts, they are committed to offering effective and humane iguana removal methods that prioritize the well-being of these reptiles. You can view a video about iguana removal at www.floridaroof.com/iguanas. For more information, visit www.humaneiguanacontrol.com or call 305-200-9821.

www.floridaroof.com

Preventing Fatal Falls
Jeremy Grimes, CSI, CDT, Strategic Roof Safety Specialist, FlashCoSince 2012, OSHA has enacted a Fall Prevention Campaign to raise awareness among workers and employers about how falls from common hazards can be prevented. The campaign includes three basic tenants: Plan, Provide and Train. With proper planning, using correct equipment and training everyone on the proper use of safety equipment, fatal falls can be prevented.
Installing Fall Protection During Construction Protects Workers
Contractors are well versed in the need to safely protect their workers during jobs (OSHA 1926 Construction) but roofers can also help building owners maintain the safety of buildings by installing permanent fall protection during the construction process. Over the life of a roof, multiple trades will access the roof, performing various forms of preventative maintenance, from changing HVAC filters to debris removal, to maintaining rooftop equipment, to gutter cleaning and more. Fall protection systems installed after construction closeout, often well after, can result in multiple roof penetrations that will require the roofer to return to the jobsite to waterproof those penetrations. However, installing safety systems during construction saves considerable time and protects workers from day one.
Rooftop workers classify as OSHA 1910 (General Industry) workers and if a structure does not have a 42 inch parapet wall, the building owner is liable for workers within 6 to 15 foot from the roof edge. It is best practice for roofing contractors to include permanent fall protection for a building owner’s future use on projects where fall risk is possible. Permanent fall protection could include American National Standards Institute (ANSI) Z-359 Horizontal Lifeline (HLL), single point tie-back anchors or guardrail. Installing fall protection during the construction process and approved by a manufacturer’s inspectors during warranty approval, can prevent future issues on installed roofs.
Fall protection is the use of controls designed to protect workers from falling or, in the event they do fall, to stop them without causing severe injury. Fall protection systems often involve one or more devices, components or methods for preventing or reducing injuries or fatalities resulting from a fall.
There are several types of fall protection in hierarchy from active to passive protection. Active protection includes the use of methods such as body support (harnesses), anchored connections (lanyards), anchor points and structural supports. Passive protection includes items such as guardrails.
Active protection horizontal lifelines are part of a personal fall arrest system. HLL systems are engineered to determine the loads for anchorage, associated sag angles and clearance required in event of a fall. Design decisions include: the number of users per line, length of line used, number of anchor points, materials used and the installed environment. In situations that might lead to falls, a HLL restraint system is preferred to prevent fatal falls. Critical considerations are made to prevent individuals from hitting the ground or a structure during a potential descent.
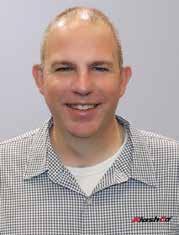
In certain situations, such as building facade maintenance or window cleaning, it will be necessary for workers to exit (fall off) the roof. In such circumstances, rooftop tie-back anchors are a proper method for providing safe anchorage points for building facade work. Tie-back anchors are installed into the structure of the building and provide a reliable fall arrest or fall restraint system. Anchors are designed to resist pull-out forces of 5,000 pounds that might be applied in any direction of an anchor. Tie-back anchors must meet ASME and OSHA safety standards.
Passive fall protection systems such as guardrails, gates, crossover stairs and hatches protect workers from falls. Common rail systems are modular, non-penetrating designs that are flexible to meet a wide range of requirements. Systems must meet OSHA regulations to ensure rooftops are safe and secure. A complete system that includes rails and guards enables workers to safely enter, move around and exit the roof. For architectural appeal, manufacturers offer guardrails in custom colors other than safety yellow. Colors such as gray or white blend into the environment and are less noticeable from ground level. Collapsible versions are available that could be hidden away when not being utilized.
HLL or tie-back anchor systems are typically installed by certified installers. These installers and their technicians have been certified in installation requirements for each system. However, after installation, it will be necessary for the roofer to go back and waterproof those areas in which fall protection has been
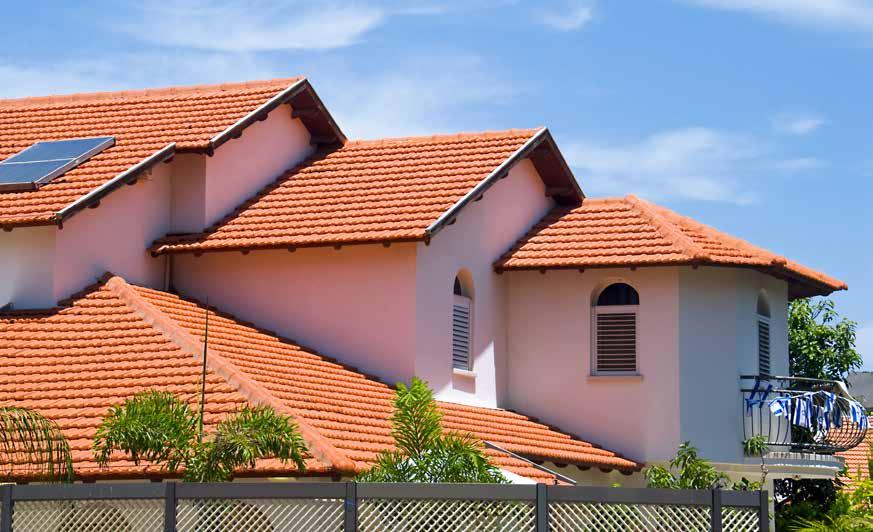
NAVIGATING THE ARRAY OF ROOFING ADHESIVES FOR OPTIMAL RESULTS
Sure, you can provide your customers with the cheapest roof tile adhesive but what they say is true, you get what you pay for. APOC Polyset Roof Tile Adhesives, recently added to the APOC family, offer a wide array of adhesive products that are designed to bond concrete and clay roofing tiles to approved underlayment on new construction, reroof, or tile repair projects.
APOC Polyset RTA-1 Roof Tile Adhesive
• All-in-one, portable & disposable foam adhesive
• Approved for use in the most stringent high-wind regions of the world
• Provides the highest yield on the market
• Dispensing unit that is preferred by contractors
APOC Polyset AH-160 Roof Tile Adhesive
• Virtually eliminates deck penetrations & tile damage from mechanical fasteners
• Superior use on hip and ridge attachments
• Highest wind uplift values compared to all other tile installation methods
• Up to 80% additional break strength - stronger than any other unsupported tile

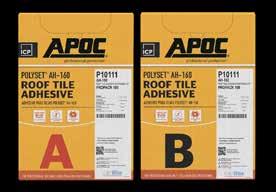
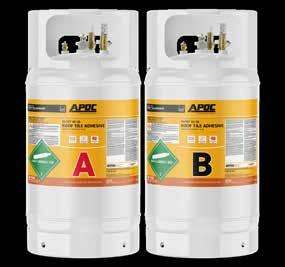

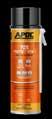
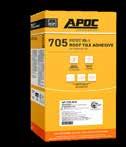
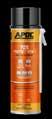
Polyurethane Roof Tile Adhesives –Securing Tile Roofs for Nearly 30 Years
Tom Parker, Owner, TCParker & AssociatesHurricane Andrew hit Southeast Florida in August of 1992. It is reported by the National Hurricane Center that 26 deaths resulted from Andrew and over 25,000 homes were destroyed. Estimates of damage range from $25 to $40 billion, depending on sources. However, the impact went far beyond these numbers. Significant code changes took place, not the least of which was the inclusion of American Society of Civil Engineers (ASCE) 7 in roof design calculations. Similarly, the industry looked for more robust ways to attach roof tiles. Manufacturers responded in the mid-90s with the introduction of polyurethane roof tile adhesives. Nearly 30 years later, we see the positive impact of these products in reports from Hurricanes Irma and Ian where adhered tile roofs have performed admirably.
As industry professionals, we are obligated to understand the requirements of the product approvals for the materials we use to ensure the resulting systems perform as designed. This is especially important for tile roofs when using polyurethane foam adhesives to secure tiles.
Foam adhesives fall into two general categories. Two part (or component) adhesive foams are delivered to the jobsite in separate containers and the components are mixed in the application gun to chemically form the foam adhesive. Single part adhesives, on the other hand, are blended at the factory in a single tank to form a pre-polymer. When dispensed, the pre-polymer combines with moisture from the air to produce the final adhesive foam product.
Florida Building Code (FBC) product approval (PA) and Miami-Dade notice of acceptance (NOA) component approvals require that installers using polyurethane roof tile adhesives be factory trained and certified by a qualified instructor. Each manufacturer has differences in the way the product is prepared and installed in order to meet the stated uplift performance in their product approvals. Because of this, the certifications are specific to the manufacturer. The application requirements are outlined in the manufacturer’s individual component approvals and typically reflected in more detail in the manufacturer’s installation instructions. Most manufacturers include the installation instructions with the product so that the instructions are readily available on the jobsite. Some provide these instructions in both Spanish and English.
Each adhesive applicator on the job is required to have successfully completed the approved training and should be able to present a certified installer card
upon request of the code official during an onsite inspection. Certification is not transferrable between manufacturers, so it is important that all applicators on a tile roof installation are trained and certified by the manufacturer on the specific product being used.
It is important as well that the building department inspectors are knowledgeable about the products and know what to look for during an inspection. Improper preparation or misapplication of the foam can greatly reduce the uplift resistance provided; this is especially true if less than the required amount of foam is applied or its placement is incorrect. The additional challenge for the inspector is that the foam is not visible when
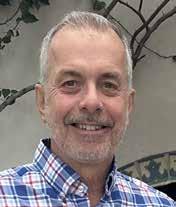


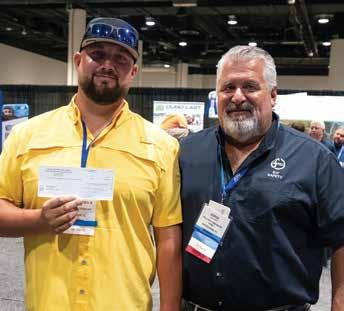
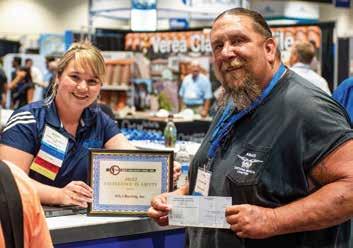
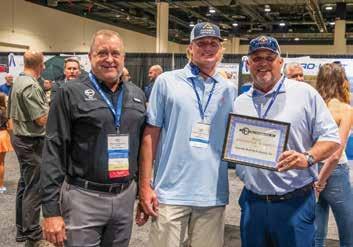
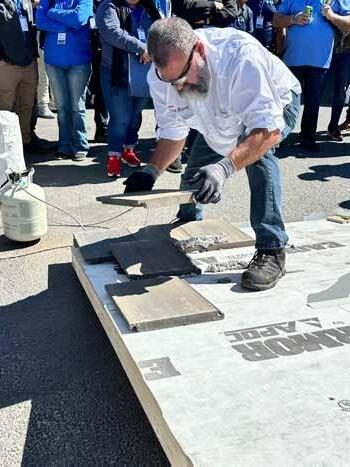
the job is completed since it is covered by the tile. The inspection needs to be carried out either by witnessing some portion of the installation or by asking the installer to break tiles to allow examination of the contact area of the foam and foam amount. In some
Preventing Fatal Falls, continued from page 36
installed. Fall protection systems that require fewer installation points can help roofers to waterproof those areas quickly and effectively.
In summary, permanent fall protection is a necessary component of making roofs safer for workers. Making permanent fall protection part of the construction process is a best practice for roofers. If fall protection is installed after project closeout, the guarantee of a roof warranty may be compromised by adding holes or creating potential leakage points and may result in unnecessary call backs. To avoid these issues, roofers should install permanent fall protection during construction. This is a standard that is not going away and safety is rarely value-engineered away from projects. Be at the forefront of these opportunities and know the most cost-effective fall prevention is fall protection. FRM
jurisdictions, pictures or video of the foam as applied may be acceptable. Additionally, Miami-Dade County requires a third-party pull test to ensure that a minimum uplift resistance is achieved on the project.
Likewise, roofing contractors need to ensure that their crews and supervisors are knowledgeable on proper installation to ensure that the job meets the design requirements. The roofing contractor has their company name and license holder on the building permit and they should recognize that responsibility for proper installation resides with them. Simple things like making sure that the foam adhesive delivered to a jobsite is actually used on the job will go a long way to minimizing risk and liability for the owner.
It’s clear that polyurethane roof tile adhesives have made a positive impact in securing tile roofs over the last 30 years as evidenced by the system’s performance in multiple hurricanes. With this higher level of performance comes a higher level of knowledge required to properly install the products. Manufacturers working in partnership with roofing contractors and code officials are critical to successful installation. Contact your manufacturer or supplier for training resources to ensure that your crews are properly trained and certified. FRM
Tom Parker is the owner of TCParker & Associates, a technical sales agency representing Tilebond roof tile adhesive. Tom grew up in the construction industry in his father’s residential construction company. He later earned a degree in Chemical Engineering and worked at Dow Chemical for 33 years prior to opening his agency in 2013. Tom is a Registered Professional Engineer.
Jeremy Grimes, CSI, CDT is the Strategic Roof Safety Specialist at FlashCo. He has a B.S. in Construction Management from Missouri State University, an MBA from Baker University and is CSI-CDT certified. Jeremy started his career in Local 20 as Union roofing laborer. He has over 10 years of experience in permanent safety fall protection, 25 years in building envelope construction and is well versed in all commercial waterproofing systems from below grade to architectural metal.
Roof Tarping Safety
Reinforced plastic tarps, commonly called “Blue Roofs,” provide temporary protection for the roofs of homes and other buildings damaged during severe weather such as a hurricane or tornado. When employees access roofs to install these tarps, they are at risk of falls, electrocutions and other hazards. OSHA recommends the following steps to help keep workers safe.
Identify the Hazards
Always avoid electrical hazards! Look for downed overhead power lines and treat all power lines as “live.” Generator use can cause “backfeed,” energizing lines that are no longer receiving power from the electrical grid. Be sure to contact the utility company to ensure lines are de-energized. Do not use a metal ladder near power lines or in close proximity to energized electrical equipment.
Assess the roof condition for stability prior to allowing employees to start work. Do not allow employees to work on top of a damaged roof until after the strength and structural integrity of the roof has been determined. Select the fall protection system(s) employees will use while installing the tarp.
■ For low-slope roofs, (a roof with a slope of less than or equal to 4:12) use conventional fall protection (fall arrest, guardrails or safety nets) with or without a warning line, a warning line system with a monitor or a monitor alone on small roofs (50 ft. or less in width).
■ Do not stand on steep roofs (greater than 4:12) without using conventional fall protection systems.
Note: Using a rope grab as part of a fall prevention system is one example, among others, of equipment that can be used to reduce the risk of falling. All components of the system, including the harness, rope and rope grab, any connectors and the anchor point must meet applicable OSHA requirements.
Installing the Tarp
■ Never install a tarp during a storm while it is windy or raining.
■ Use proper protective equipment, such as hard hats and eye protection or other control measures such as chutes and barricaded areas when removing roof debris. This ensures employees on the ground are not exposed to hazards from falling objects.
■ Remove debris using a roof rake or brush from the ground level. If using a ladder, ensure the use of proper safety techniques to prevent falls.
■ Whenever possible, avoid getting on the roof when tasks can be done from ladders or other stable platforms.
■ When accessing the roof, lean the ladder at a safe angle that is at a 4:1 ratio (one foot away from the building at the bottom for each four feet of ladder length to the roof eave) and make sure the ladder extends three feet above the roof edge.
■ Watch for tripping hazards including vent stacks, satellite dishes, lightning arresting components and cables and cleats holding down the tarp.
■ Do not walk on a tarp. A tarped roof will be very slippery, especially when wet.
■ Watch your step – skylights and other openings that have been tarped over will not be obvious to someone walking on the roof.
Workers’ Rights
Workers have the right to:
■ Working conditions that do not pose a risk of serious harm.
■ Receive information and training (in a language and vocabulary the worker understands) about workplace hazards, methods to prevent them and the OSHA standards that apply to their workplace.
■ Review records of work-related injuries and illnesses.
■ File a complaint asking OSHA to inspect their workplace if they believe there is a serious hazard or that their employer is not following OSHA’s rules. OSHA will keep all identities confidential.
■ Exercise their rights under the law without retaliation, including reporting an injury or raising health and safety concerns with their employer or OSHA. If a worker has been retaliated against for using their rights, they must file a complaint with OSHA as soon as possible, but no later than 30 days. For additional information, see OSHA’s Workers page.
How to Contact OSHA
Under the Occupational Safety and Health Act of 1970, employers are responsible for providing safe and healthy workplaces for their employees. OSHA’s role is to ensure these conditions for America’s working men and women by setting and enforcing standards and providing training, education and assistance. For more information, visit www.osha.gov or call OSHA at 800-321-6742.
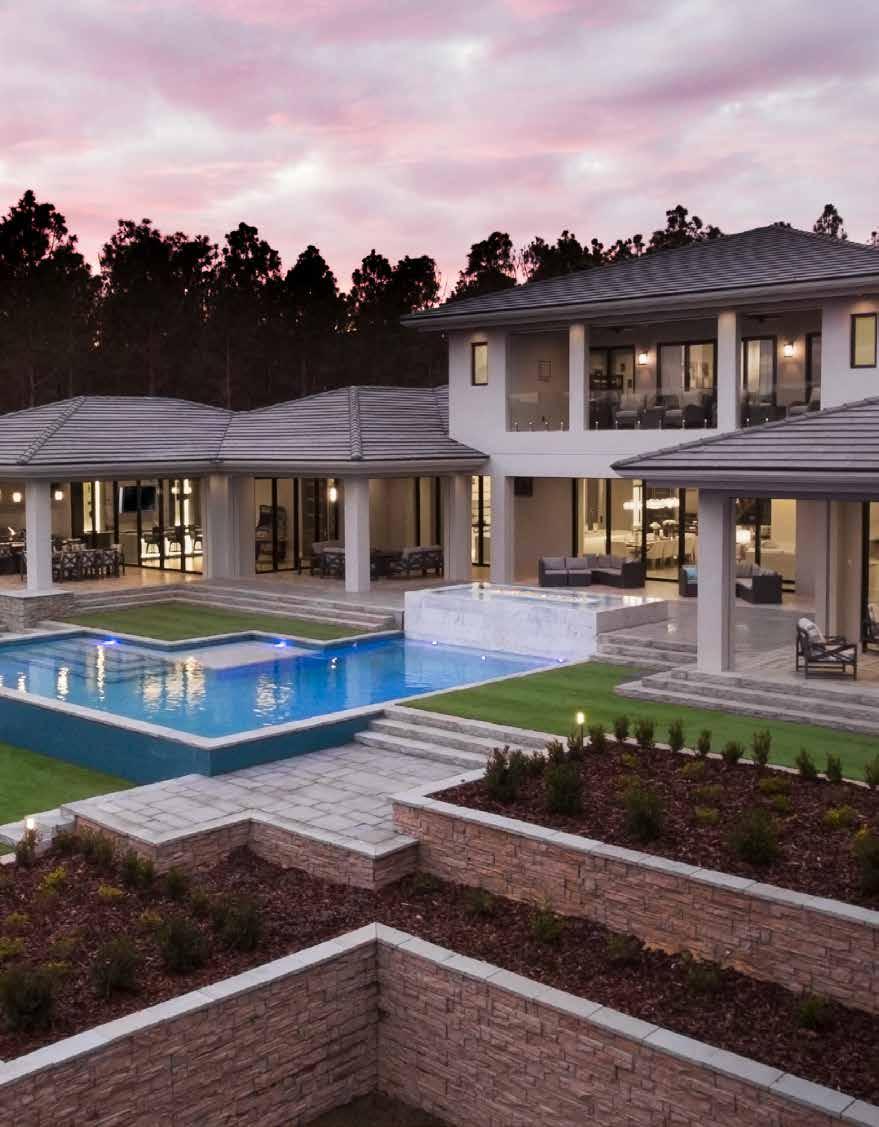
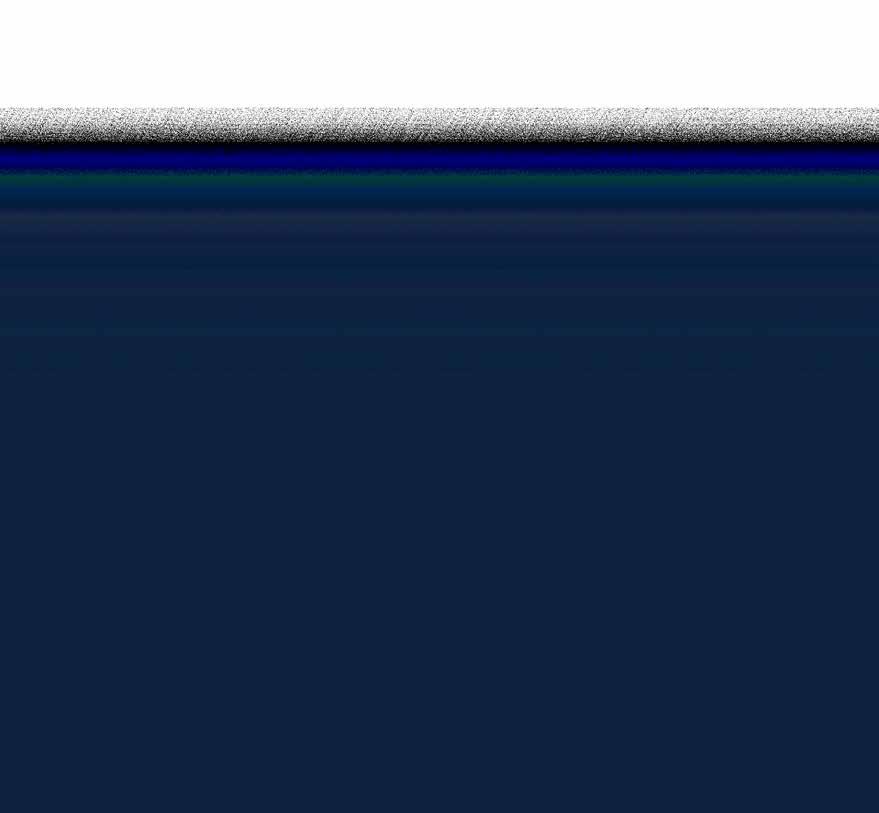
SAVE TIME AND BE MORE EFFICIENT
33 Fully stocked locations throughout Florida to service your building material needs.
Homestead, FL 33032 (786) 829-2761
Ocala, FL 34470 (352) 210-6246
Jacksonville, FL 32209 (904) 503-9400
Tallahassee, FL 32304 (850) 574-7600
Odessa, FL 33556 (813) 749-5354
Orlando, FL 32804 (407) 291-7244
Tampa, FL 33619 (813) 740-8790
Fort Myers, FL 33916 (239) 935-5077
Deerfield Beach, FL 33442 (954) 969-8000
Miami FL, 33142 (305) 635-7177
Orlando, FL 32809 (407) 367-6246
Ocala, FL 34474 (352) 622-3933
Melbourne, FL 32904 (321) 369-7892
Ormond Beach, FL 32174 (386) 301-4471
Palmetto, FL 34221 (941) 722-6800
Leesburg, FL 34748 (352) 818-6120
Orlando, FL 32804 (407) 859-9997
Winter Haven, FL 33880 (863) 293-1555
St. Petersburg, FL 33716 (727) 565-4630
Sarasota, FL 34243 (941) 203-6320
Fort Pierce, FL 34982 (772) 466-3461
Stuart, FL 34997 (772) 223-8881
Vero Beach, FL 32960 (772) 778-0549
Orlando, FL 32810 (321) 442-0061
Fort Lauderdale, FL 33315 (954) 525-1158
Riviera Beach, FL 33407 (561) 863-9899
Clearwater, FL 33762 (727) 573-6075
North Port, FL 34289 (941) 732-1029
Panama City, FL 32405 (850) 763-0851
Ruskin, FL 33570 (813) 729-5977
Fort Myers, FL 33912 (813) 918-0379
St. Augustine, FL 32095 (678) 358-7623
Port St. Lucie, FL 34986 (772) 216-3111

Beacon's network of branches work together in every market to support customers with
• Optimized Dispatch
• Consistent System Pricing
• Centralized Purchasing for correct inventory levels
• Rapid Response
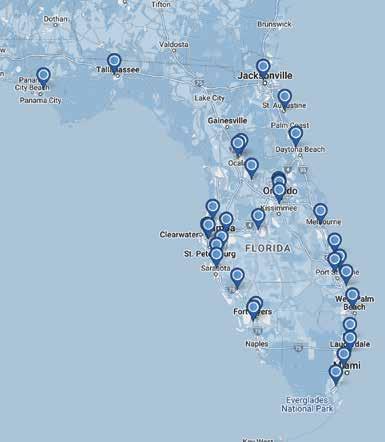