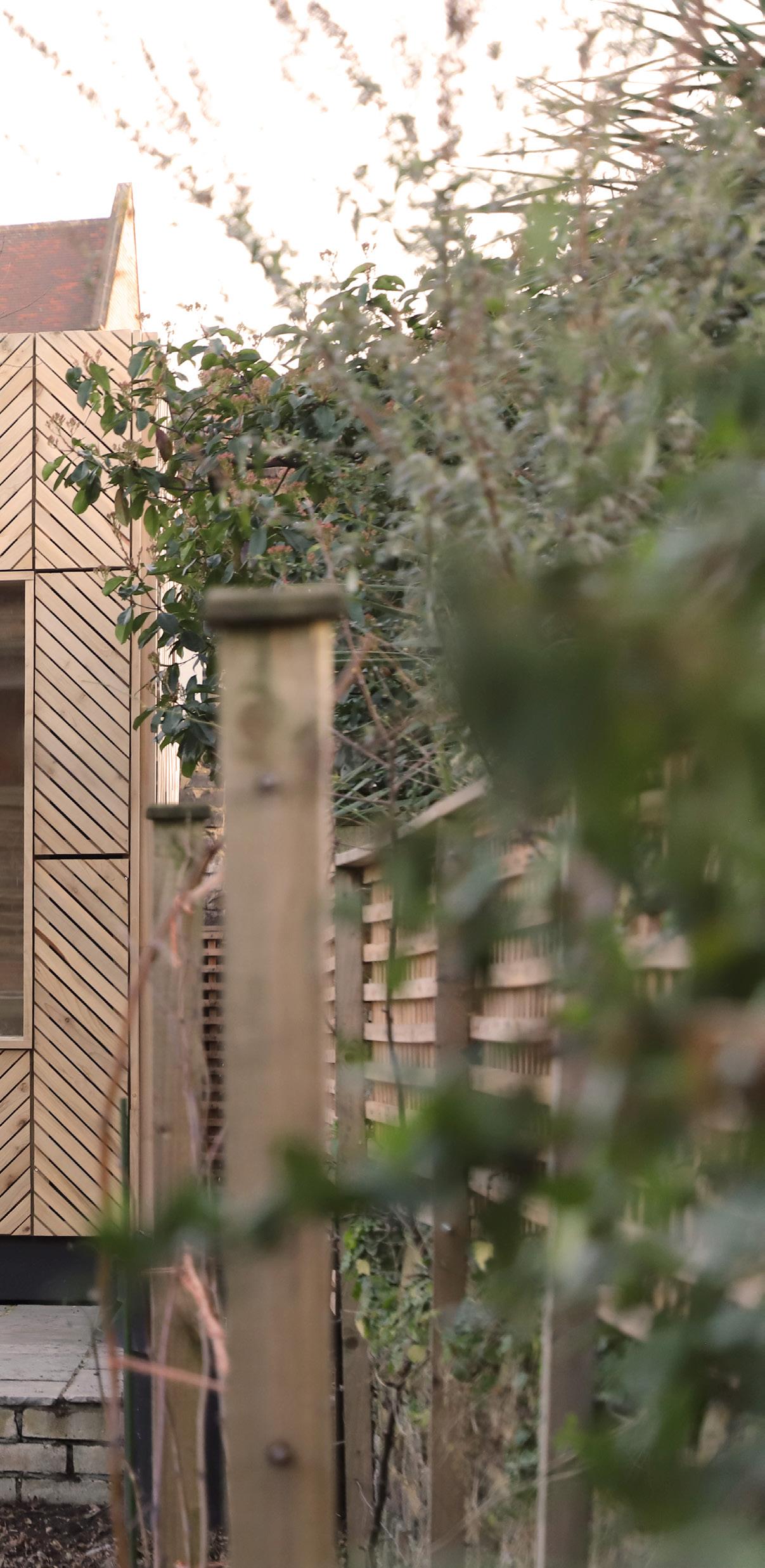
8 minute read
U-Build: Manbey Pod Self Built System
U-BUILD: Manbey Pod
Self-build system
Advertisement
by Studio Bark, UK
As a society we are detached from our manufacturing processes, and so we are often not aware of the way that our buildings are produced and the amount of waste that comes out of the process.
Introduction For every six or seven houses that are built in the UK, one house worth of waste will go to landfill or incineration (ref Duncan Baker Brown). This is especially relevant in a country where the Parliament and the RIBA have declared an environment and climate emergency.
The U-Build project is an attempt to find an alternative to polluting and high energy ‘business as usual’ types of construction. It is a circular economy ready design solution that aims to reduce the energy used in building whilst also empowering end users through engagement.
U-Build’s approach to construction can be thought of a bit like big Lego. It is a kit of standardized timber components that can be assumed from flat pack, and then stacked into myriad forms and arrangements, to create the main structural frame of a building. The system removes many of the difficulties associated with traditional construction, enabling individuals and communities to construct their own homes and buildings.
The system uses precision CNC machining to create the kit of parts. The hybrid offsite approach removes many of the difficulties associated with traditional construction, harnessing the accuracy, speed and repeatability of offsite manufacture. At the same time, it reduces the scale and complexity of conventional offsite techniques,
enabling the building shell to be assembled by people with limited skills and experience using only simple hand tools.
Off site production, on site assembly Since the components are small enough to be produced in a small local CNC fabricator, rather than a large framing factory, it enables self builders to assemble components on site without heavy lifting gear, or specialist training. This participatory model is inherently scalable, liberated from the constraints of a more centralised approach.
The UK self-build portal suggests that it takes 6-9 months to construct a residential house. Box House showed that an equivalent U-Build house can be delivered in 4 months. The offsite production process reduces errors and inaccuracy to a minimum. Any waste timber that is produced is contained in a clean, central location, making it easy to transfer to a specialist recycling facility (as opposed to timber waste on site, which is easily contaminated).
As the frame is based on a limited number of standardised components, parts can be easily replaced if damaged. The flexible and demountable nature of the system makes it easy to reconfigure areas of the building in future as required.

Figure 1. Kit of parts by Studio Bark. Figure 2. Process showing installation in workshop .
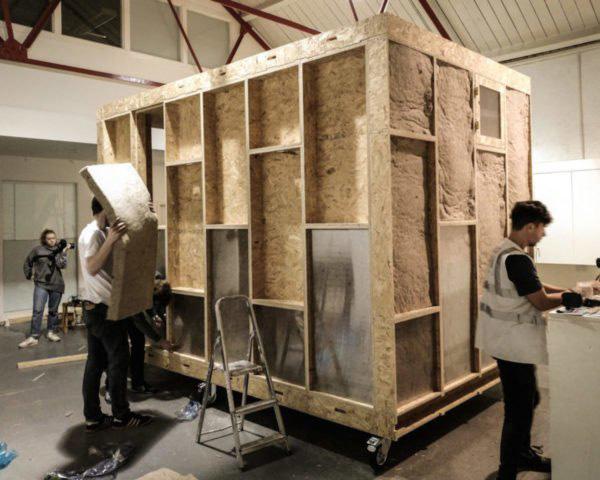
Self building communities U-build has been designed for community led construction, with a template idea for the development of a self build community as follows:
Members of the community come together to purchase a small kit of parts sufficient to build a community workshop.
The community builds the workshop together as a pilot project, with U-Build acting as a facilitator,
A CNC machine is installed in the workshop and members of the self build community are trained to use it.
The community use the CNC machine to cut new parts for their own buildings and build them using the skills they learned during the pilot project.
The CNC workshop / hub remains as an asset for community use, for making new buildings, adaptations and furniture.
The CNC workshop / hub can create starter kits and act as a training hub for other communities, and the whole process begins once again.
This idea was borne out in reality, with the development of an affordable workspace community in Hackney Wick, East London. Faced with demolition of their workspaces (for new housing) a group of local organisations in collaboration with the local authority, have managed to secure a GLA grant to build its own series of new U-Build workspaces in the carpark of an existing building. As of the date of writing, planning permission has been achieved, the first CNC workshop has been built, and purchases have been agreed for the CNC machine to go in it. Once installed, the machine will begin cutting parts for the second phase of the project in January 2020.
Environmental impact Whole life costs are reduced through a robust 'fabric first' approach including high-levels of insulation and inherent airtightness.
The system uses natural materials wherever possible, but it is fair to note that the system is circular economy ready, rather than circular economy compliant, as there are still some elements of the build process, for example the glue in the plywood, which to date has not been fully biodegradable, however new technologies are changing that rapidly: Our preferred timber supplier has just released a bio based Plywood glue so we will incorporate that as soon as it is commercially ready.
A study conducted by environmental consultants Atmos Lab concluded that the embodied carbon for a U-Build house would be roughly half that for an equivalent house built with traditional construction methods (238 kgCO 2 / m 2 as compared to 550 kgCO 2 /m 2 ). The supply chain uses materials with environmental certifications, including FSC and PEFC, such as Riga Birch plywood and WISA spruce plywood. Other non-toxic, ecological materials are specified including sheep’s wool insulation.
As material technologies and transport networks improve, we would like to get to a point in the process, where our buildings have zero, or even positive impact at the time they are built (rather than just by offsetting that energy with solar panels).
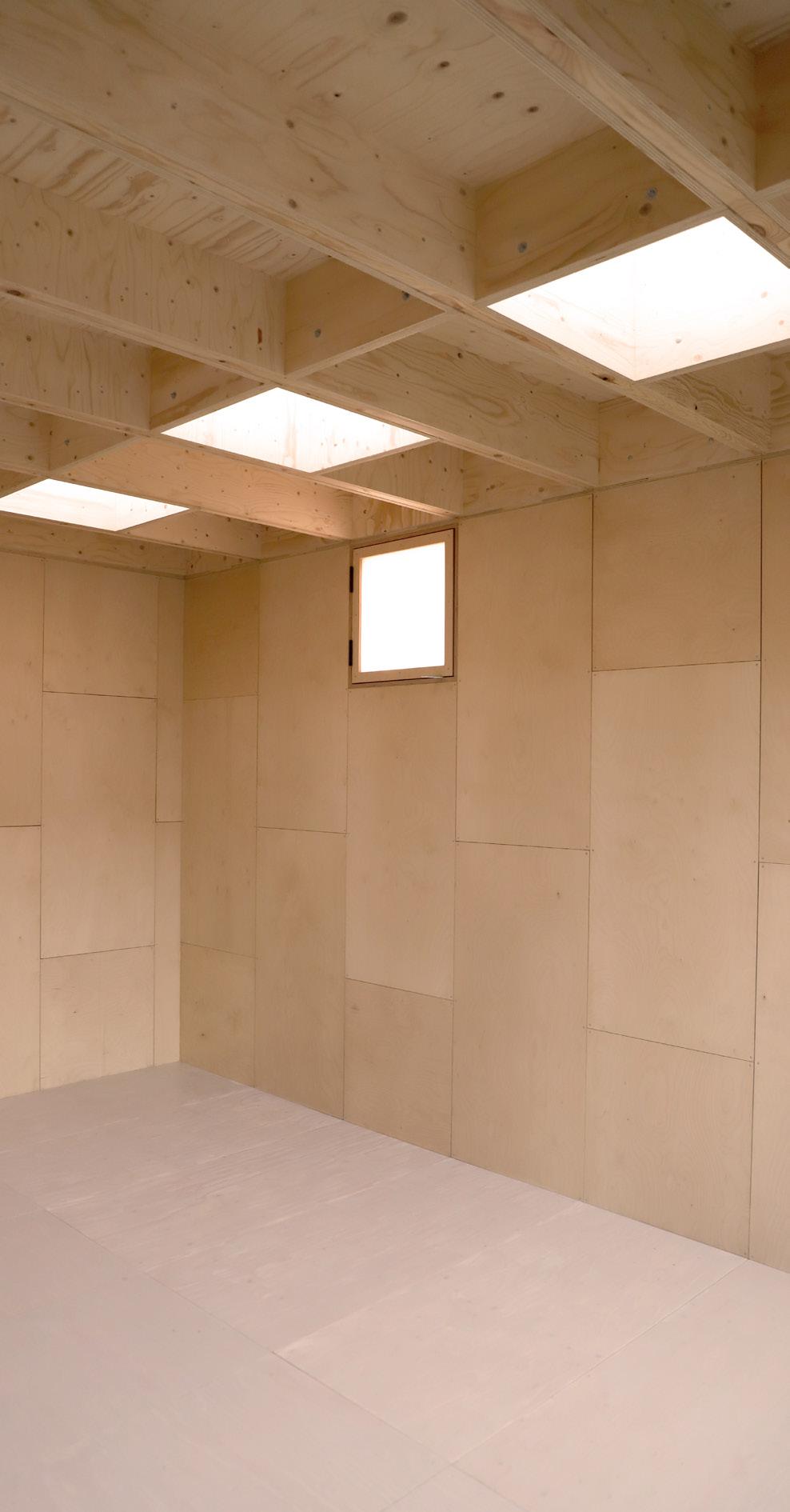
Figure 3. Interior space with skylight on roof .
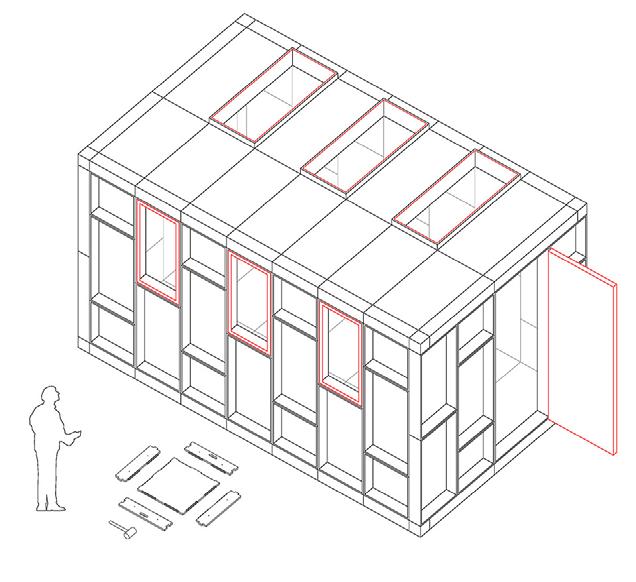
Figure 4. Steps of self organising system process .
Towards Circular Adaptable Scenarios in Window Systems As one of the main design tools was DfA, different circularity scenarios that tackle directly adaptability concepts were developed. One of the most relevant scenarios was the addition of new functions. This is achieved through understanding the window as a fixed frame, with a flexible infill that can be easily exchanged. Additionally, the window itself can also serve as a modular system with internal divisions (similar to a curtain wall).
There are three different possibilities: a BIPV panel (climate components), a green façade panel (biodiversity), and a media façade (active technology). These three types of panels are just conceptual examples, as actually the possibilities are broader than this. As long as the frames are able to carry the load of the panel and the cross-section of the panel is compatible with the frame, the type of infill can be easily replaced, adding new functions, aesthetic qualities, and with the possibility to overcome change.
”The use of architecture as a tool for protest and civil disobedience is a fascinating subject of study, and is no doubt a typology that will be tested increasingly, as designers look to use their skills to participate in these accelerating movements for change. Self organising systems The system can also used by communities on a large scale - as witnessed during the October 2019 London climate change protests. The environmental activist group Extinction Rebellion used a modified version of the system to build rapid-deployment mobile structures, including sculptural roadblock towers, stages, seating and storage. With a self organising strategy befitting its decentralised organisation, the cutting patterns (which were gifted to the organisation) were modified to make the units much easier to understand by people who had never seen the boxes before.
Summary With the rise of automation and offsite manufacture, there is the potential for great savings in time and cost when compared with traditional build processes. However in the rush to use these systems it is important that we do not lose sight of the end user. The approach outlined above accepts that computer aided technology and AI will become more common part of our construction process, but aims to celebrate that by putting the user in control of the process, rather than just at the receiving end of it.
As U-Build develops we hope to empower more people with the tools and skills to take on their own projects and work towards solutions that can form a key part of a circular economy solution moving forward. In the context of the climate crisis, it is also worth acknowledging that designers will only have limited power to make change within their own work, unless they also use their power as citizens to contribute to systemic changes.

Figure 5. Door and window openings in U-build system.
Studio Bark, UK
Studio Bark is an award-winning architecture practice creating inspiring and ambitious buildings. We are a collaborative team of architects, designers and makers based in East London. As a young studio, our work is diverse, interesting and constantly evolving. We believe in the transformational potential of the built-environment and have a passion for outstanding environmentally-driven architecture. We deliver bespoke, unconventional buildings which are inherently contextual and inspired by meaningful investigation of site.
Environmental design is a core part of the process: our work incorporates best practice principles while attempting to push the boundaries of ecologically-conscious architecture. We believe that compelling architecture can realise the latent potential of a site and bring joy to people’s lives.