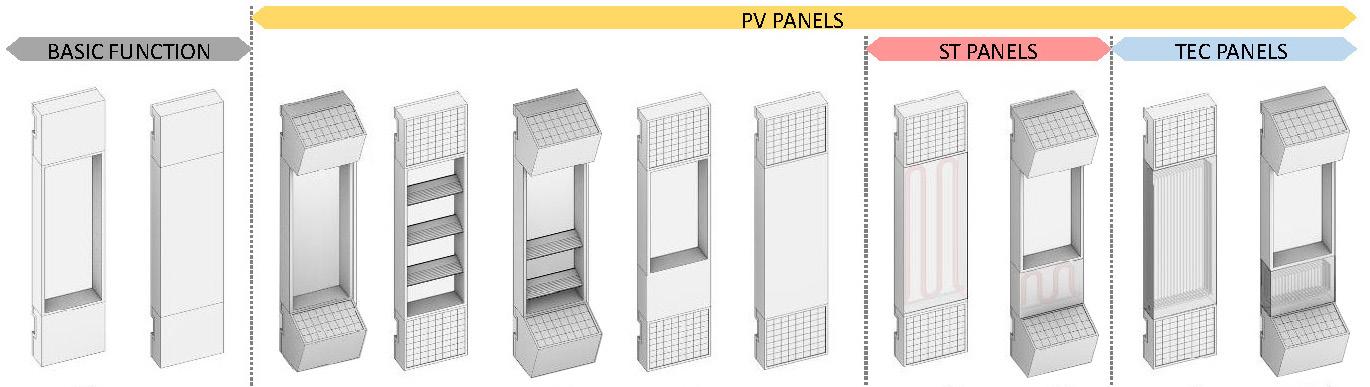
6 minute read
Plug & Play Facades
A brief introduction to Plug & Play approach in building envelopes
Graduation Thesis by Premith Satish
Advertisement
London based studies by Synovate market research reported that requirements of global curtain wall systems have increased by 10% in compound annual growth rate to about USD 18.7 Billion in the year of 2009. With such large requirements in consideration with data from almost a decade ago, one can determine that many buildings with curtain wall systems as façades are approaching their end-of-life expectancy and will soon require intervention.
Introduction
The graduation project primarily focuses on Façade and Climate design. The concept Plug & Play approach to façades aims to offer one more possible solution to challenges posed to most of the proposed and existing tall buildings around the world. Where due to ageing facades, the performance of the buildings may reduce. Alternatively, the increase in maintenance costs and utility costs will render the building undesirable and hence cause premature demolition of the facade or the building itself. Ageing of the facade would mean that its performance would decrease exponentially both structurally and in terms of the energy performance of the buildings it is serving. Dilapidation of the curtain wall facades can occur due to the natural course of things when materials such as vapour barrier, waterproofing, EPDM, neoprene, glass and other relevant materials will deteriorate due to seasonal curing, maturity and UV radiation of the sun. In contrast, most of the built structure can ideally last up to another 100 or more years before it fails. It would be unfortunate to demolish the entire building or even the whole façade when only a few components need replacing. A prudently designed façade which incorporates the aspects of disassembly, maintenance feasibility, energy generation and many more considerations will prolong the practical life and performance of the buildings.
While comparing the average service life of the materials (Figure 1), the study reveals that different materials have different end of service life. Mixed plastics such as silicone sealant and thermal breaks tend to have a service life limit of 20 to 30 years as per specifications of leading manufacturers. However, in practice, the values of facade end-of-service (ESL) are much less based on the geographical location. And, when the same materials are multiplied overtime (Figure 2a) until the life time considering the facade is replaced every 30 years or so (Figure 2b) for an average concrete highrise building (for example) it can be observed that certain materials overlap. This overlap indicates that the materials could have lasted longer but have been replaced causing material wastage and some materials come short of ESL causing the building to perform poorly.
Figure 3. Typologies of potential plug & play facade types
Figure 4. Design function overview
Figure 5. Disassembly Scheme
Factors such as technical failure, poor performance, seasonal maintenance, or replacement of components which have reached their service life maturity determines the need for replacement. Plug&Play does not necessarily has to be defined by the entire facade panel; it could be a functional part or even parts of the construction of the panels. The benefit of this system is that failed or matured components can be exchanged for a practical alternative.
The primary function of a facade is to protect from the weather and climate-related elements. Nevertheless, as technology progresses, the discipline of facade engineering also has to a greater extent improved and now allows for fire protection, humidity control, glare protection, daylighting and overtime has a vast array of increasing functions. The multifunctionality aspect enables facades to assume newer technologies within its domain and hence reduce the complexity of separate building integrated systems. Facades have over the years adopted an ample amount of strategies to reduced materials in construction, and careful facade design can help abate just that. The design here challenges to combine multiple concepts into one functional conceptual component and hence, includes within its umbrella of functionality the following key aspects:
1. Integrate ABE: To explore for energy production. The strategy will help the current systems to rely less on the power grid, which is mostly from non-renewable sources and elements such as photovoltaic panels, solar thermal panels & thermoelectrical coolers will add additional functionality.
2. Focus on design for disassembly: To regulate the Life Cycle Impact of building materials, design for disassembly is the call for the hour. Potential materials are discarded prematurely, which causes a lot of material wastage. This strategy will help
140
120
100
80

00 20 40 60 SERVICE YEARS
Figure 6a. Proposed option for extending the ESL of curtain wall facade and hence the building
120
90 100
00 30 60 50 75 SERVICE YEARS Seasonal maintenance and treatment of silicon seals Replacement of IGU’s Replacement of EPDM, Neoprene and Steel fix ings Replacement of aluminum profiles and insulation 1 2 3 4
Approximate building end-of-service-life 5
Figure 6b. Technical life cycle overview of ESL of proposed facade in comparison to expected ESL of the building in maintenance perspective
the facade reduce the buildings reliability on expensive non-renewables and help save material at the same time (Figure 6a).
3. Focus on accessibility: Accessibility is a solution to the above two problems (Figure 6b); the concept remains to allow for easy accessibility of the facade elements to replace, clean or maintain them in any
required way. Hence, solving issues of depending on massive, expensive building maintenance units (BMU) on top of the building and high risk conditions for people. The facade maintenance crew will now be working from inside instead of the outside. The panels will have an access door, which will be sealed shut by mechanical systems such as pressure plates and cover caps. Only a skilled maintenance worker will be able to open the panel and service any component which is damaged and requires replacement or just the regular seasonal maintenance. It can be observed in the proposed design already that the nature of change in angle currently of 22 degrees of the horizontal overhang shading with PV to adjust to the orientation.
The final design contains a set of parts which can be accessed at any point in time. However, as shown in Figure 5 and 7, each component will be accessed and removed at a certain point of time where the requirement aligns with the need for regular maintenance. This accessibility allows for more than one component to be removed and does not cause disturbances during maintenance. The design also now eliminates the use of bulky and expensive BMU’s, which shoots up the cost of facade related expenses. Saving the maintenance equipment expenses for the life of the building will most likely save the cost and material worth of one whole facade in the future.
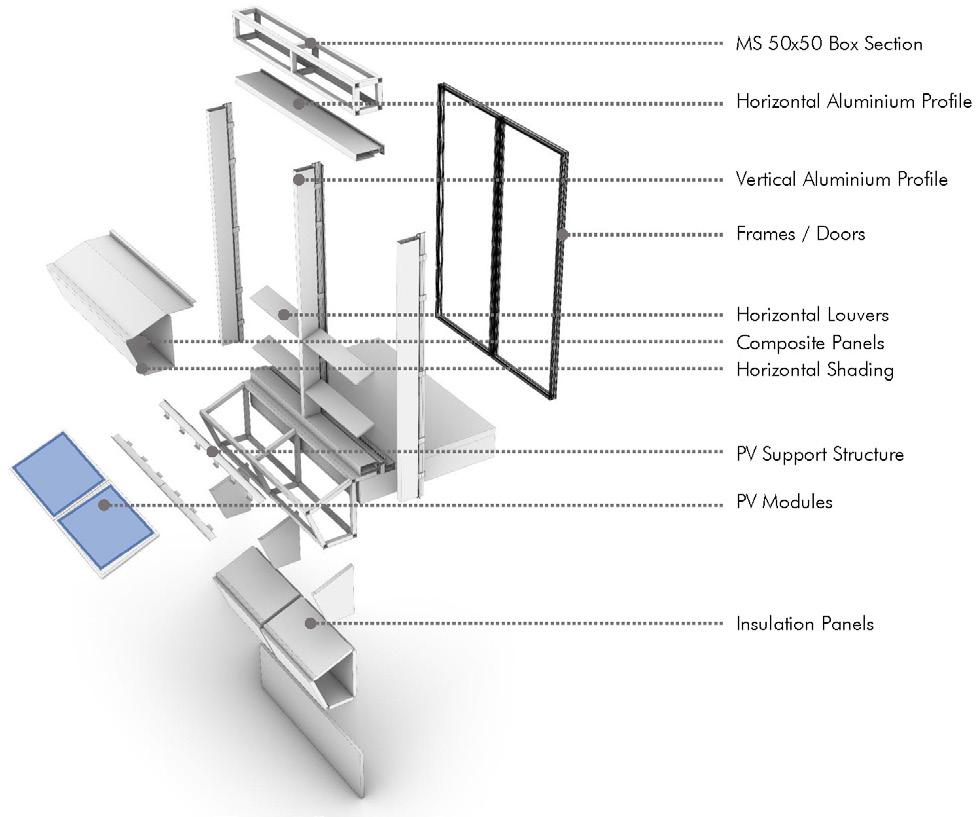
Figure 7. Exploded view of the whole system
Premith Satish Bachelor– Architecture MSc – Building Technology
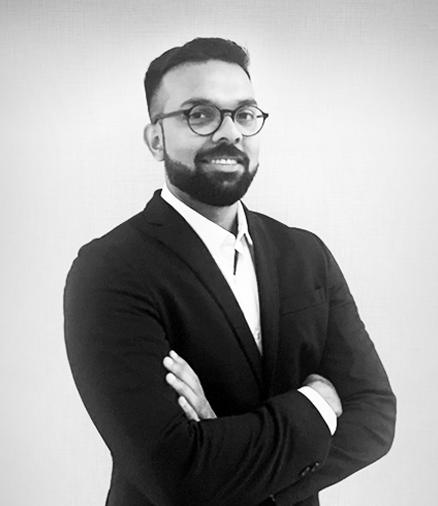
An architect of Indian origin, currently based in Dubai, UAE . He is working as a Development Manager for Swied & Sweid; a Dubai-based boutique real estate firm. He graduated Cum-Laude from TU Delft in July 2019 with an Honours Degree in MSc Architecture and Building Technology. He has a LEED Green Associate accreditation and the TiSD Annotation for Technology in Sustainable Development, specializing specifically to design and evaluate buildings to have minimum impact on the environment. He is experienced in designing and managing various aspects of a development project from concept to execution. He is keen to discern and bridge the knowledge gap between aesthetic design, sustainable practice and technical functionality and to ensure all his projects result in a practical 'value-engineered' product.