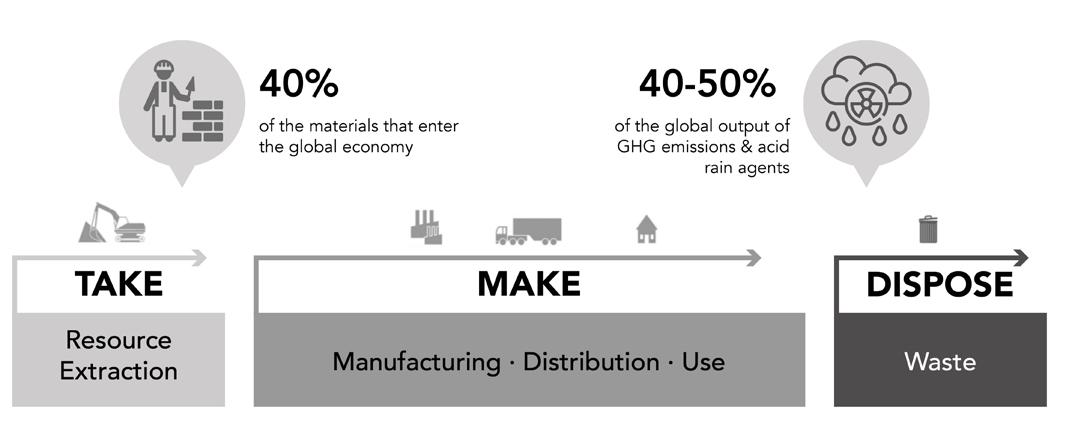
9 minute read
Circular Facade Systems and Construction-Tania Cecilia Cortés Vargas
Circular Façade Systems and Construction Design for Remanufacturing Window Systems
Graduation Thesis by Tania Cecilia Cortés Vargas
Advertisement
Introduction The European construction industry is responsible for 35% of generated waste, and even more, a façade system is usually 25-30% of the embodied energy of a building. A circular economy is a response to the “take-make-dispose”, resource-intensive linear economic model. It implies the reduction of waste to a minimum, and a variety of (re)life options for materials and products to maintain their value and embodied energy. In a circular economy, the components of a façade are designed according to different (re)life options, and therefore, there is an alternative to demolition by entering closed loops, as seen in Figure 1.
In addition, remanufacturing has been widely recognized as “an important component of a resourceefficient manufacturing industry” (ERN, 2016). However, for a product to be remanufacturable, certain principles need to be taken into account during the early design phases. Most of the current products are unable to support remanufacturing. A demand for a design strategy for façade systems taking into account product life extension strategies, especially remanufacturing, of the components can contribute to sustainable, product life extension scenarios. This thesis was focused on a circular redesign of the RT 82 HI + window system from Kawneer Nederland.
Figure 1. The “Take-Make-Dispose” model vs a Circular Economy model that is restorative by design.
What is Remanufacturing? Since the Second World War, remanufacturing processes became a common industrial activity, but it was not until the 1980s that it became relevant in the academic field. Nowadays, the concept of remanufacturing has evolved to the following:
“The process of returning a used product to at least OEM original performance specification from the customers’ perspective (Ijomah et al., 2014) by performing “a series of manufacturing steps acting on an end-of-life part or product (Parker, D., Butler, P., 2007), “and giving the resultant product a warranty that is at least equal to that of a newly manufactured equivalent ”(Ijomah et al., 2014) after which the product receives a serial number” (Boorsma, 2016). Thus, it is understood by this last definition that the product is upgraded after its end-ofservice. Indeed, this is the crucial aspect that is found on remanufacturing: the product value increases and the embodied energy is conserved.
Figure 2. Steps involved in the process of remanufacturing.
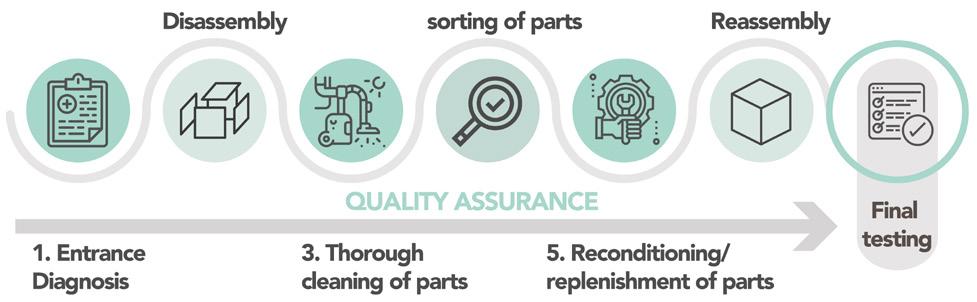
DfX The DfX family, where the ‘X’ stands for different concepts, has the aim of guiding designers towards a certain goal. The main design and analysis tools in the presented research were DfD, DfA, and DfRem.
Design for Remanufacturing (DfRem) Design for Remanufacturing (DfRem) is a design technique where an item is designed to facilitate the different steps involved in remanufacturing, considering the product strategy, and the detail engineering of the products in terms of the entire remanufacturing process.
Design for Disassembly (DfD) DfD is a concept where products and buildings are carefully designed for material recovery, value retention, and meaningful next use. Building components are able to reach their end-of-service without compromising their end-of-life This means that by disassembling the components, the embodied value is retained and the component can have multiple re(life) options.
Design for Adaptability (DfA) DfA refers to the concept of designing buildings with the capacity to accommodate effectively the evolving demands of its context, in which its building products are designed to maximize re-usability, to minimize value destruction and thus maximize value through life. Time needs to be considered as a characteristic in design.
Circular Façades: Definition and Design Requirements Through an extensive literature review and interviews with stakeholders, a circular façade is defined as a system that is designed for disassembly and for adaptability, able to circulate hierarchically between the technical cycles of reuse, remanufacturing, and recycling. Is built with sustainable materials that reduce the demand for virgin feedstock input, prevents valuable material losses, and reduces or offsets carbon emissions. The façade system, sub-system, and components should function in the same way or better than a traditional linear façade, as the performance of it is more important than the product itself. Figure 3 illustrates the different functional, circular, and aesthetic design requirements of a façade established by the author.
Figure 3. RemPro-matrix based on Sundin (2004) explaining the hierarchy of the product properties according to each remanufacturing step

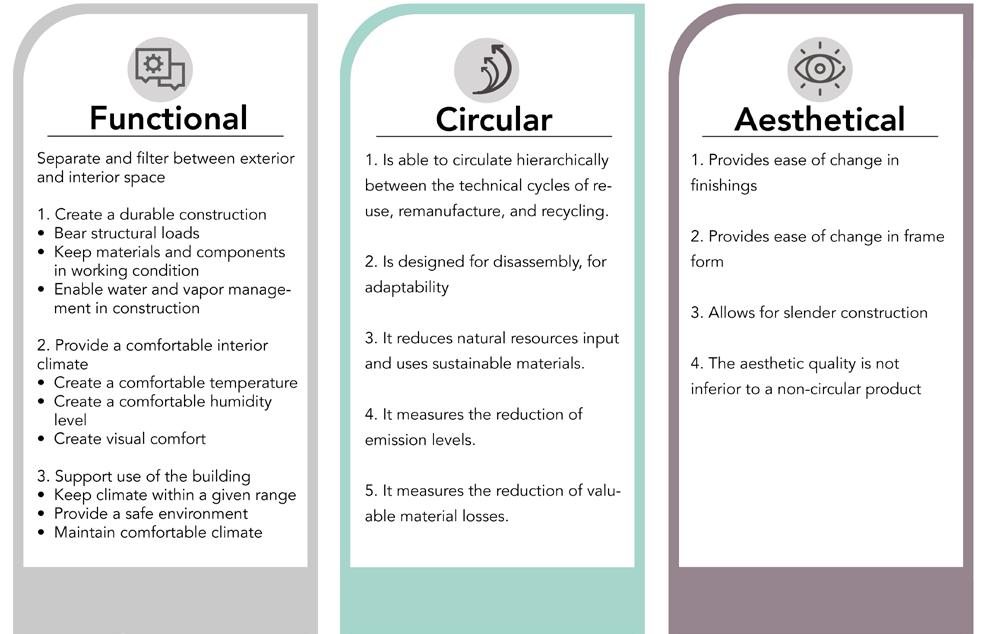
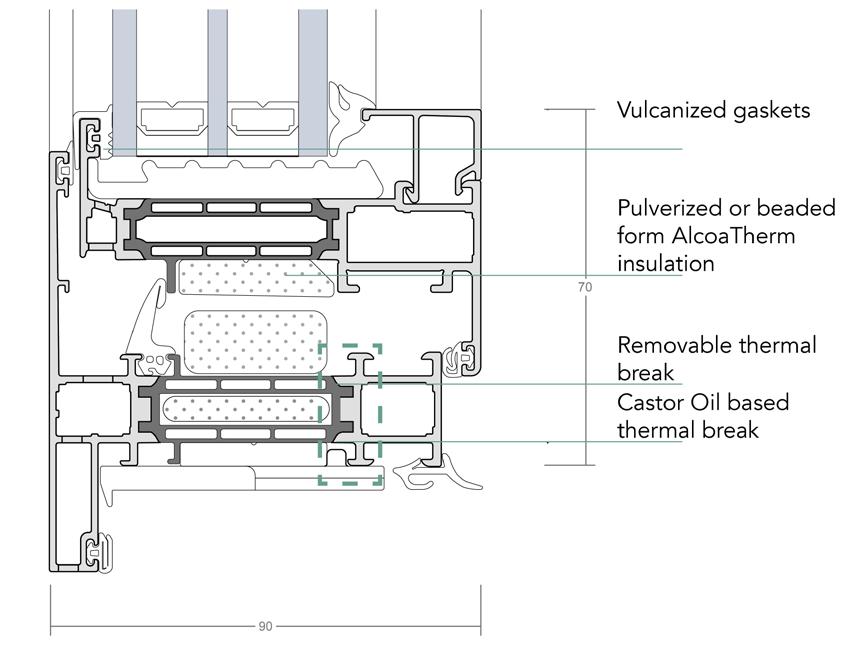
Design Concepts Three different design concepts were developed. The first one is an optimization of the existing system, and the second and third are hybrid variants that combine aluminum with wood polymer composite profiles (WPC). Figure 4. Overview of the different design requirements: functional, circular and aesthetics.
Design Concept 1: Optimization The most radical change is the addition of a removable thermal break. This works under the principle of having snap-in connections where the thermal break is slided in. If the thermal break needs to be removed, it will have to be stressed, and then slid outwards.
In the case of the gaskets, instead of glueing them, they are vulcanized avoiding the use of another material, as stated by the principles of a circular economy. Additionally, the corner cleats of the window are joined through the use of standard bolts. This allows easy disassembly, while still taking into account the precision required for manufacturing a window. Thus, through small improvements in the connections of the elements, the presented profile shifts towards a more circular product.
Design Concept 2: Hybrid Variant A The system consists of an asymmetrical window profile with three main extruded elements. This simplification is
Figure 5. Side view of the profile Design Concept 1: Optimization
important, as it is assembled through closed geometries and connections. In this case, the bottom frame is made of aluminum, similar to the current manufacturing process, but with a mechanical fastened thermal break. The aluminum frame also covers the upper frame, which is made of WPC (Wood Polymer Composites). After extensive analysis and further research on materials for window systems, it was selected to work with WPC as they are the perfect example of cascading in a circular economy.
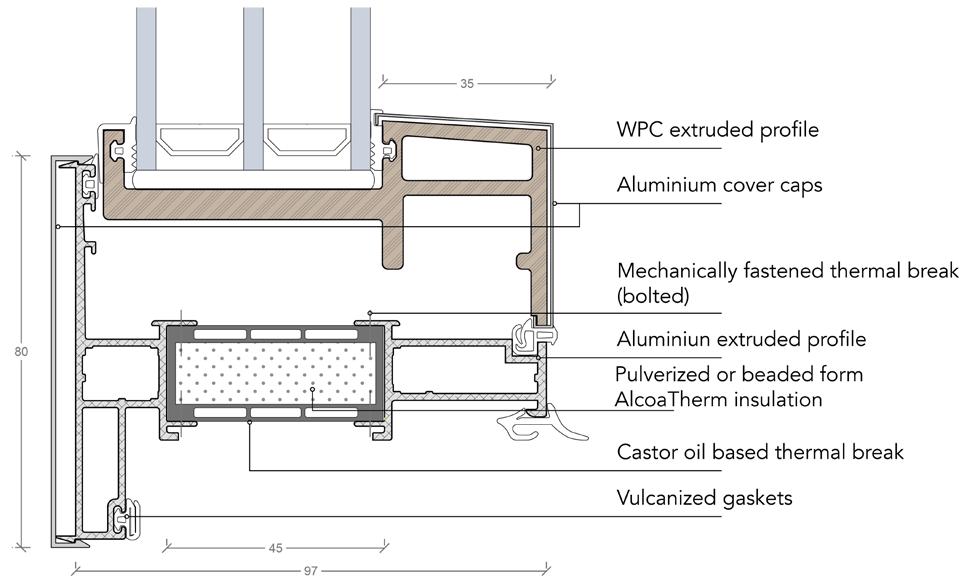
Figure 6. Side view of the profile Design Concept 2: Hybrid Variant A
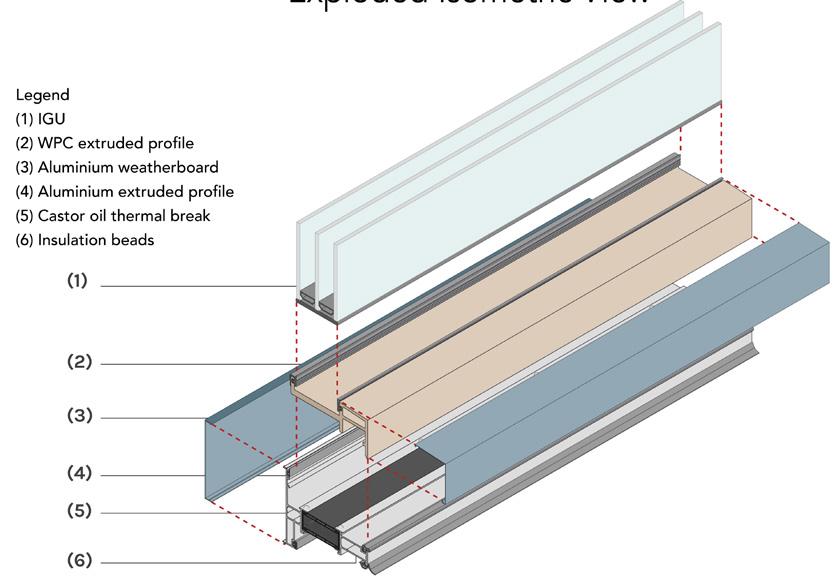
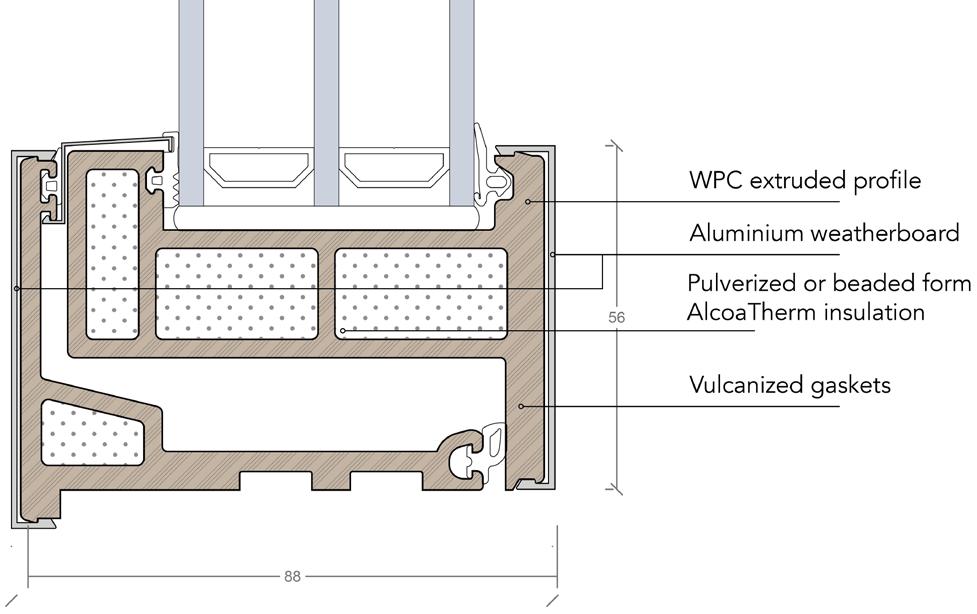
Figure 7. Axonometric exploded view of the elements of Hybrid Variant A
Design Concept 3: Hybrid Variant B Two extruded WPC frames are snapped to each other, and covered with an aluminum weatherboard. This weatherboard protects the WPC frames to make the material last longer and to enhance its appearance. The aluminum weatherboard element also serves aesthetics adaptability functions, as it can be interchangeable to give a different finishing or form.
Because of the nature of this system, highly based on WPC, there is no thermal break, simplifying dramatically the number of elements and connections, improving the DfD potential.
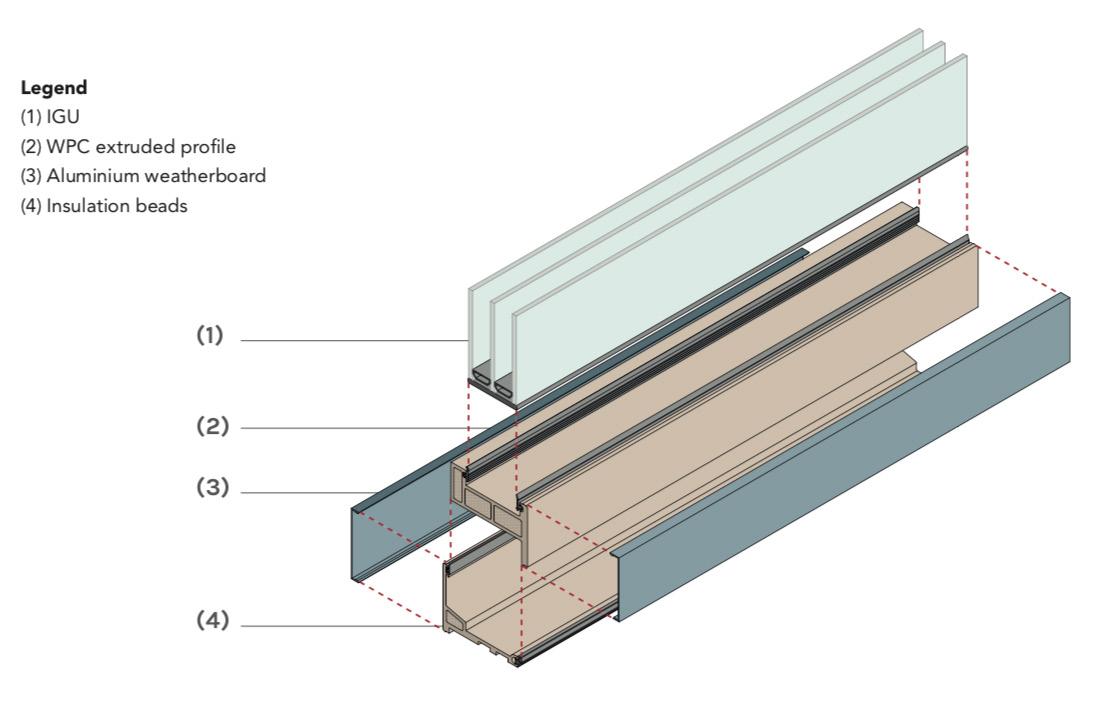
Figure 8. Axonometric exploded view of the elements of Hybrid Variant B Figure 9. Side view of the profile for Design Concept 3: Hybrid System Variant B
Towards Circular Adaptable Scenarios in Window Systems As one of the main design tools was DfA, different circularity scenarios that tackle directly adaptability concepts were developed. One of the most relevant scenarios was the addition of new functions. This is achieved through understanding the window as a fixed frame, with a flexible infill that can be easily exchanged. Additionally, the window itself can also serve as a modular system with internal divisions (similar to a curtain wall).
Figure 8 illustrates the three different possibilities: a BIPV panel (climate components), a green façade panel (biodiversity), and a media façade (active technology). These three types of panels are just conceptual examples, as actually the possibilities are broader than this. As long as the frames are able to carry the load of the panel and the cross-section of the panel is compatible with the frame, the type of infill can be easily replaced, adding new functions, aesthetic qualities, and with the possibility to overcome change.
Closing the Loop Throughout the entire research, it was highly stressed the importance of closed loops, of having products circling longer throughout the inner circles, and even more, to enable (re) life options that can allow the shift from a linear model to a circular one.
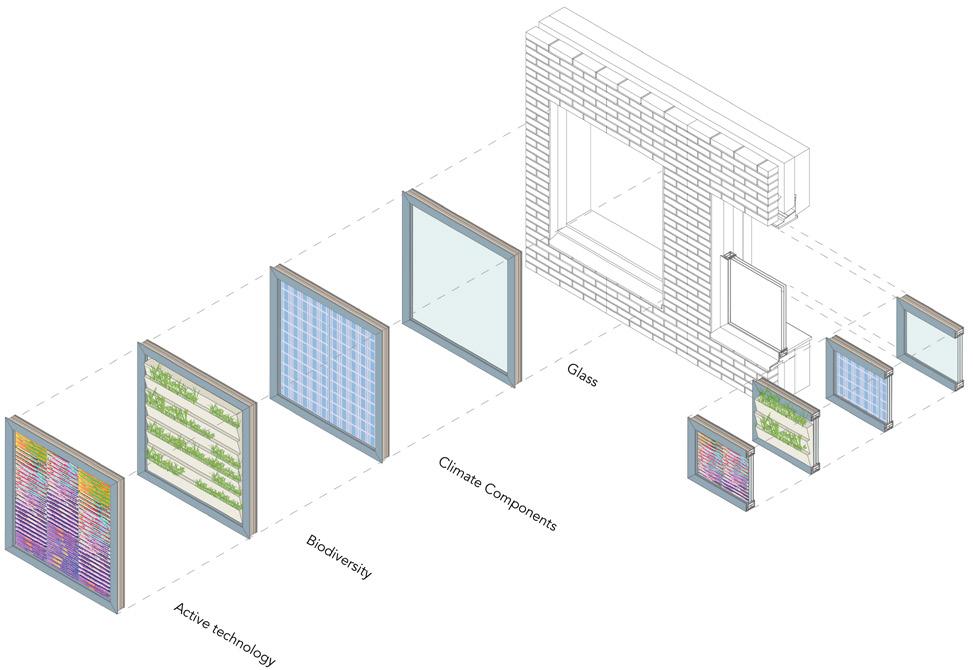
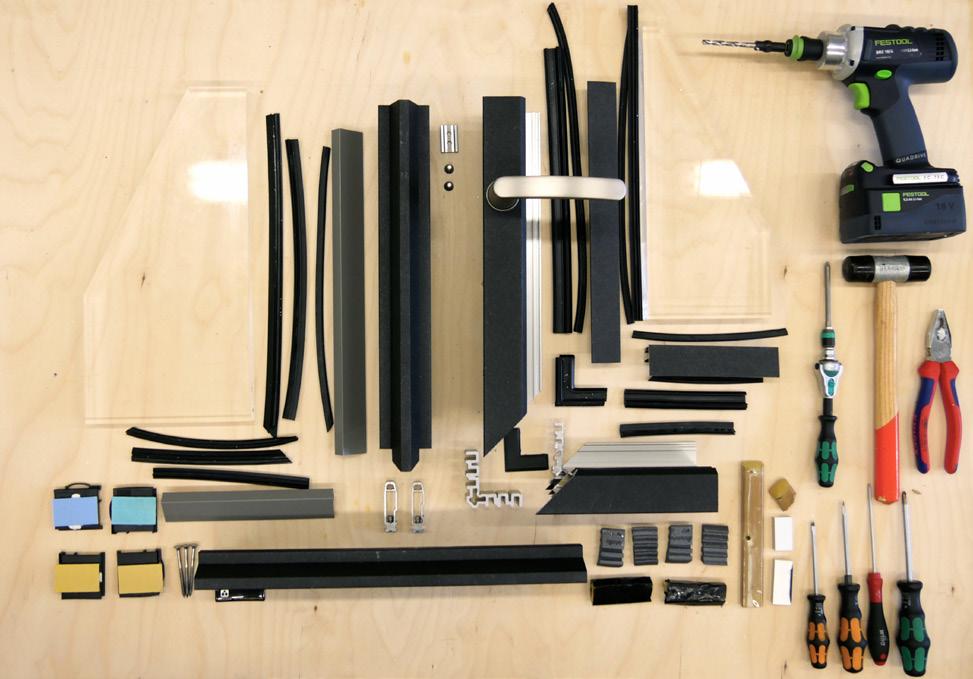
Figure 10. Change of infill strategies as according to DfA
Remanufacturing is an industrial process that by nature, is a truly closed loop. It deliberately recaptures and retains the value-added component of a product, giving it a new (re) life option which should be better than the one before. Remanufacturing, along with the other product life extension strategies, is also able to retain labor and energy from the original manufacturing processes. The ratio of the total energy required to manufacture a new product, against a re manufactured one, is approximately 6:1.
Another important key aspect of remanufacturing is that it allows products to overcome obsolescence. Since the product is constantly upgraded, it does not become obsolete, which is one of the main reasons consumers dispose of many products in a linear economy. Thus remanufacturing does not only enables other (re) life options, but it is the only one from the product life extension strategies that allow an incremental upgrade. The research showed that there is potential for remanufacturing in the built environment, especially
Figure 11. RT 72 prototype disassembled into 50 parts. The tools used for the disassembly are shown on the right. Image by M. Bilow and author, 2019.
because circularity has become a norm, particularly in the Netherlands. This implies that the building industry will need to shift towards remanufacturing practices, along with other product life extension strategies.
”In a circular built environment, the components of a façade are designed according to different (re) life options, and therefore, there is an alternative to demolition by entering hierarchically different closed loops. Window systems are usually manufactured in mass production, with intense market demand, and disposal, forcing a constant consumption. Closing the loop implies keeping the products longer in use and designing them to enable other (re)life options. Design for Remanufacturing is then, a key strategy in a circular built environment.
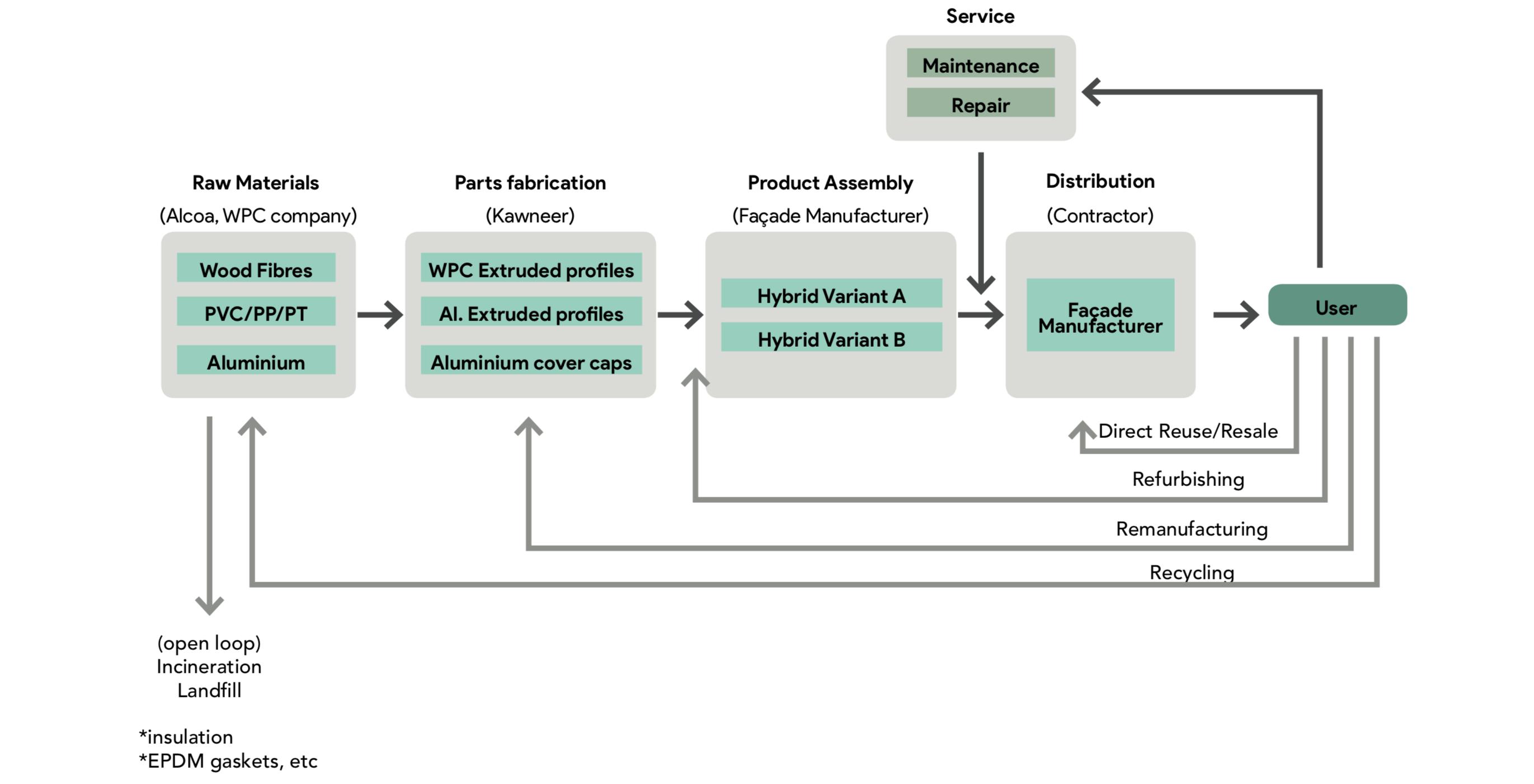
Figure 12. Closed loops from the proposed designs in a circular built environment.
Tania Cecilia Cortés Vargas Bachelor– Architecture MSc – Building Technology
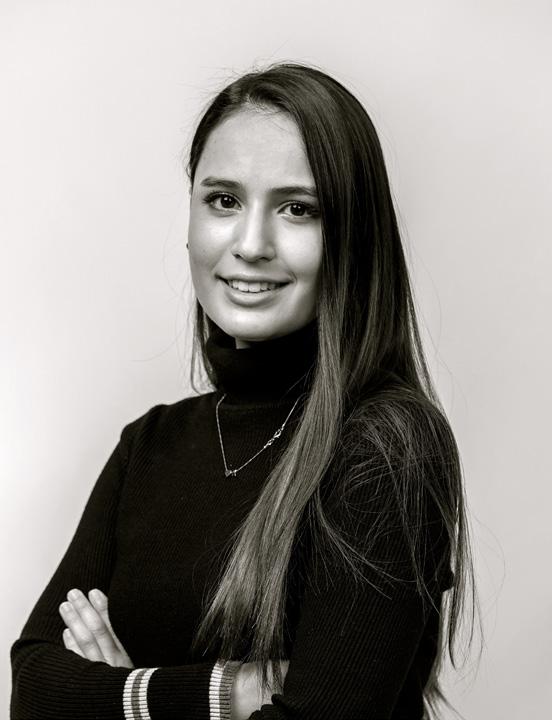
Tania is passionate about energy-efficient construction, designing the building's envelope, and circular economy applications in the built environment. She graduated (Honors) from MSc Building Technology TU Delft in mid 2019, and also completed the Honors Program where she developed research on “Assessment Criteria for Façade Components in a Circular Built Environment: Tools for Transitioning Towards Circular Design”. She also worked as a Teaching Student Assistant in the development of a Massive Open Online Course (MOOC), “Circular Economy for a Sustainable Built Environment”, for the Chair of Building Product Innovation at TU Delft. Additional to her MSc degree, she holds two Bachelor of Architecture degrees from Politecnico di Milano and TEC de Monterrey (ITESM). She currently works as a Graduate Façade Engineer at Eckersley O’Callaghan in San Francisco.