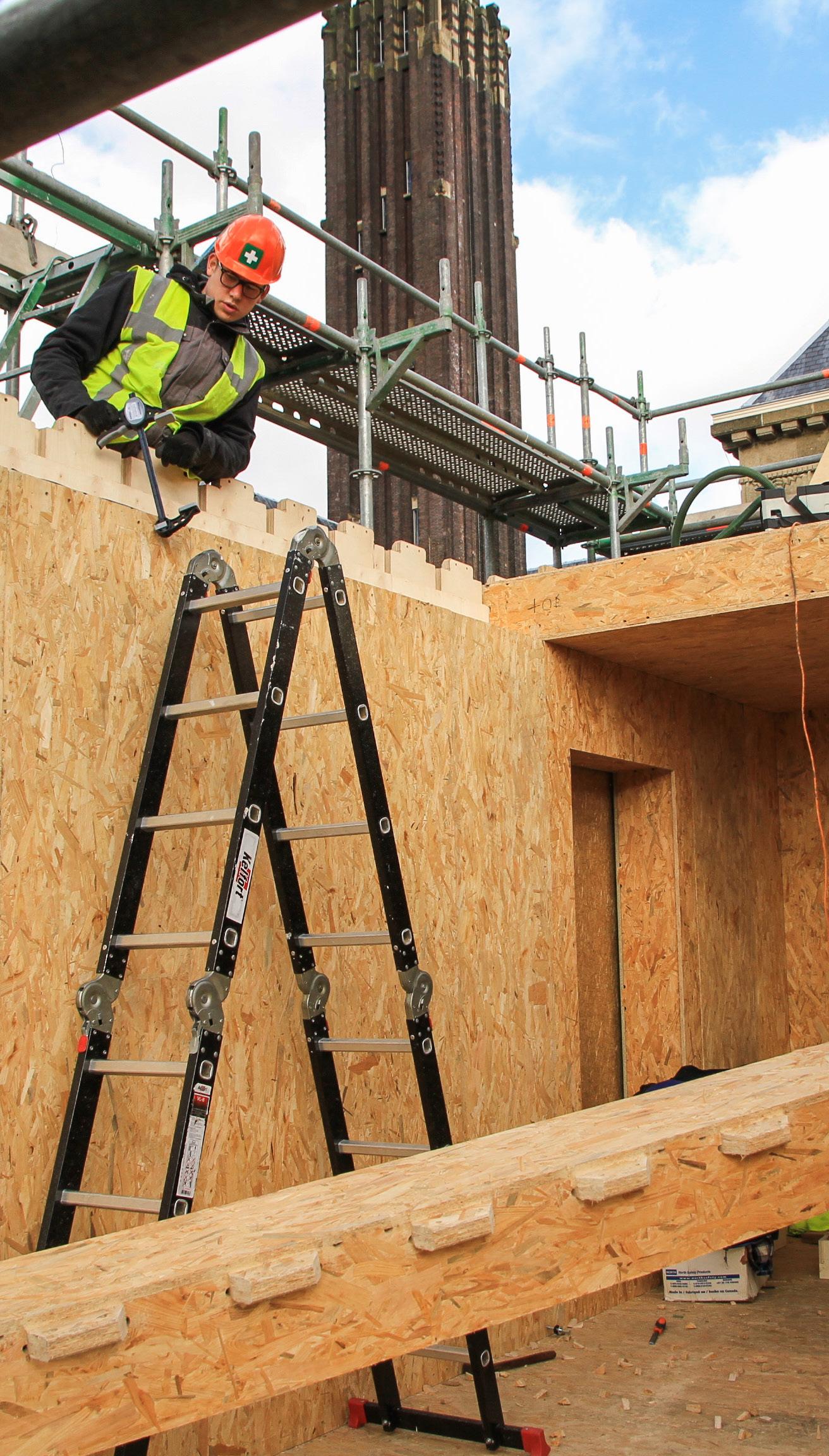
12 minute read
Disrupting the industry
Figure 1. The Product Development Lab on TU Campus, based on 'LEGO for adults': a building system developed by TheNewMakers
Disrupting the industry Interview with Pieter Stoutjesdijk from TNM
Advertisement
by Javier Montemayor and Prateek Wahi
Pieter Stoutjesdijk, Building Technology graduate, is the founder of TheNewMakers. TNM has a clear objective: to integrate design, engineering and digital-based production, achieving a major quality and time improvement in circular products.
How would you define the kit-of-parts concept yourself? Apart from the standard definition, other terms can be added to the concept. Design for disassembly is key, as well as standardization: there are some underlying standard rules the elements must follow, so the components of the kit are compatible with each other. So, compatibility within the kit is fundamental. Nowadays the different suppliers come together during construction and assemble their somewhat adaptable elements. However, in a kit of parts, every individual part fits and is compatible with each other. Additional to prefabrication where the different parts can be assembled on site, a kit of parts assures disassembly and compatibility between the parts that allows a future use.
How have you applied this technique in your own projects? We have been designing different products and they are completely compatible with each other. The kitchens and furniture objects are compatible with the floors,
walls and rooms we design, even the staircases. They are all part of a kit. But it is not only about compatibility in the physical way, but also in process. We design the strategy to reuse the kitchen, not just the product itself. We look at how to take it back and how it could be leased. To facilitate this, we have digital models, informing about the shapes and connections. Eventually, we also produce them in a fully digital way. The production is part of the process, and most of the products we design follow a similar process, with the same materials. So, the same machine and sheet material can produce a wall as well as a kitchen.
So, a kit-of-parts is closely related to circularity in the sense of reusing elements. What do you consider regarding this cycle? I think circularity has three main topics for something to become indeed circular. First is the process: a company or institution guarantees that the product is taken back, avoiding the linear process. Nowadays, hardly any producer takes responsibility of an object after its initial lifecycle. Considering a product as a service is way of achieving this. For example, instead of buying a kitchen, you can pay to the company €20 a month for the service of having a kitchen. Or it can also be through a payback guarantee. You buy a kitchen but after you use it you get back €2000 and the company picks it up again. This is all part of the circular business model.
The second part is the material. We try to make our products from fully organic material or waste material, 95% made of waste or also bio-based materials. It is obviously very challenging to have something 100% biobased. Normally a board can be 97% bio-based but the binder is not. The third then would be the connections. Designing for it to be completely re-mountable, which is a huge challenge.
Does designing in such a standardized way necessarily mean that the product will then be monotonous? Not necessarily. Maybe it seems like that because we are dealing with the first experiments on circularity. It
Figure 2. Tinyhouse: a realized concept for a micro home, completely based on modular compatible blocks containing interior, structure and installations
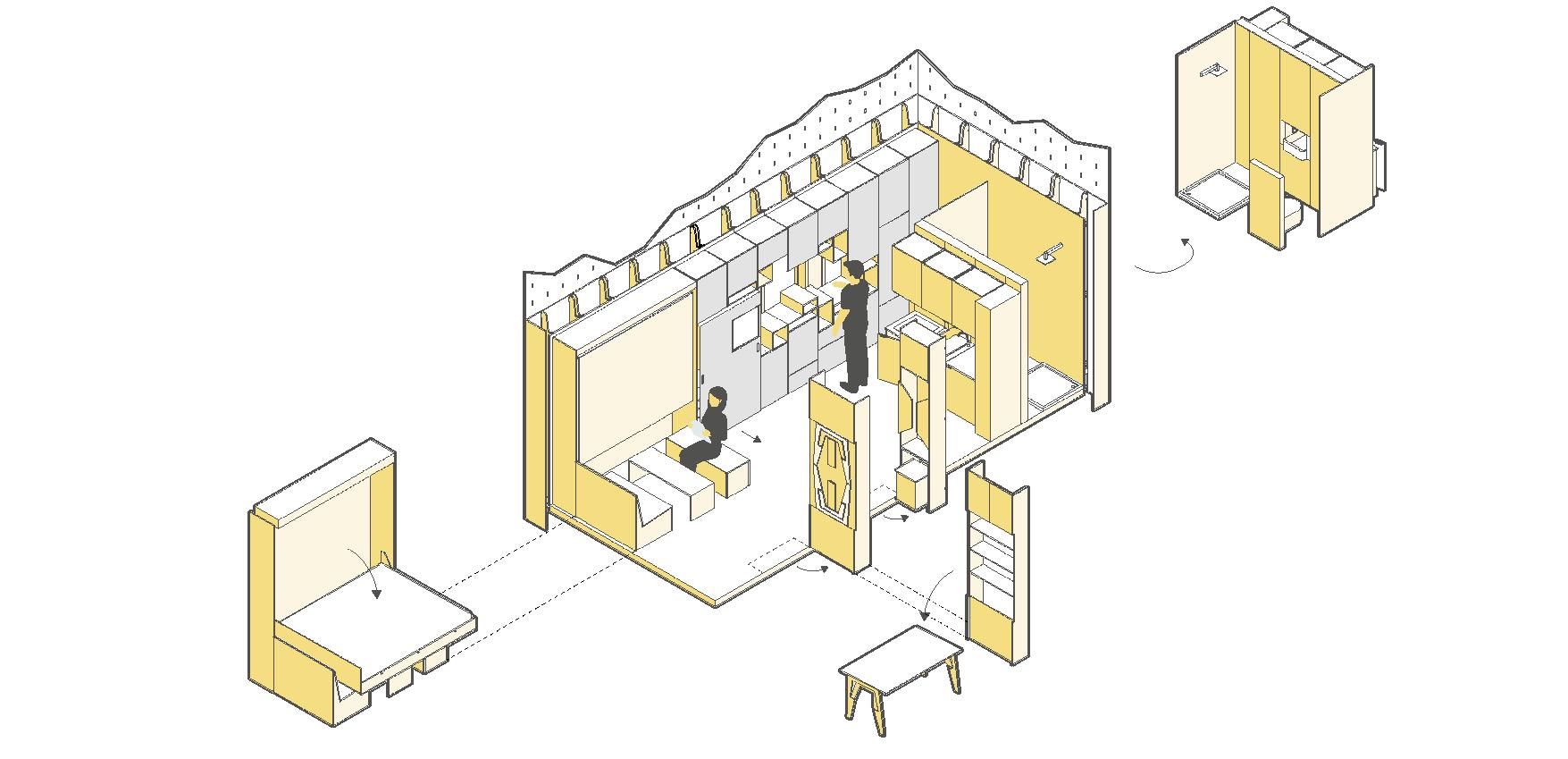
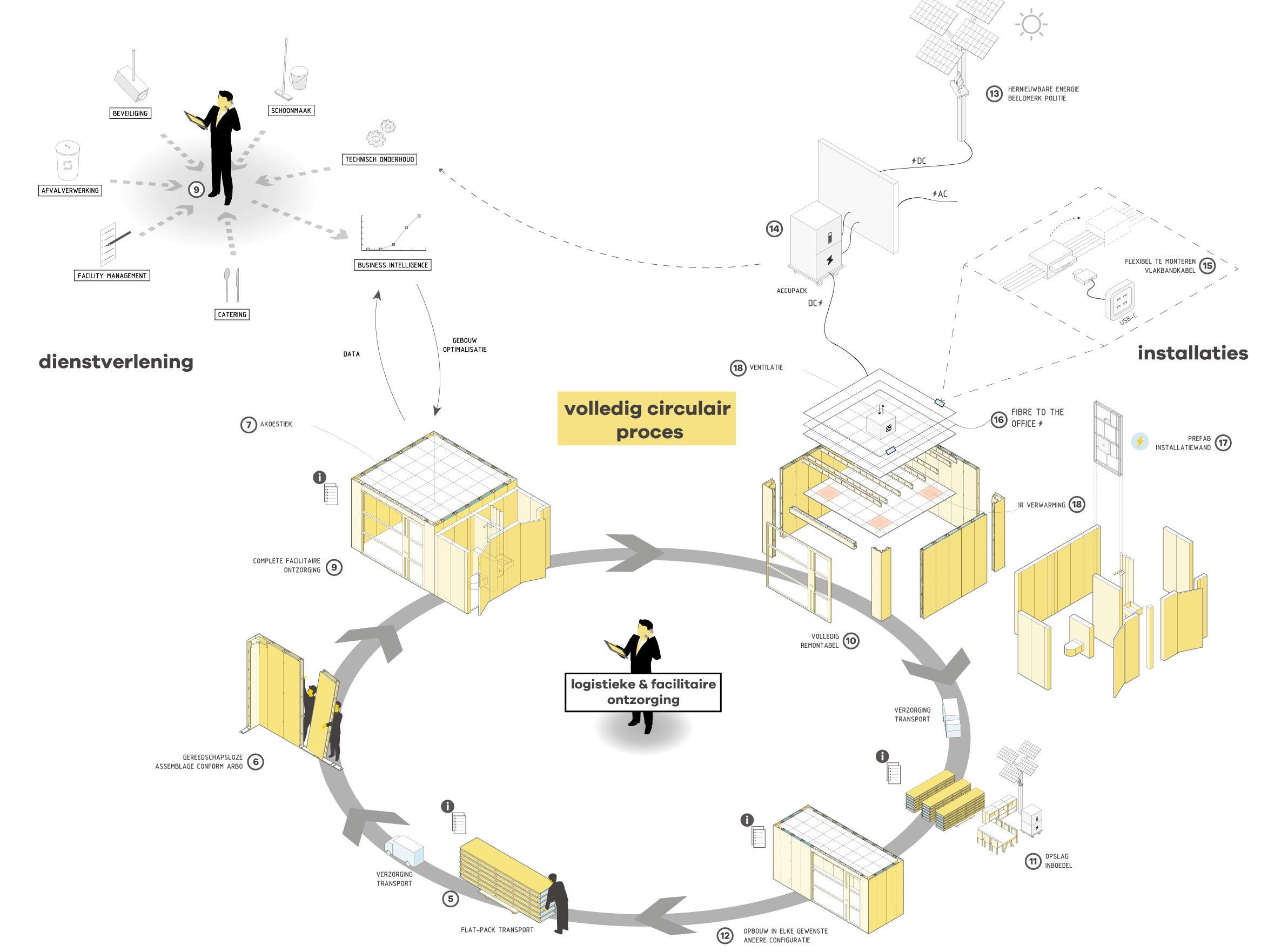
Figure 3. Circularity is not just about the product: the whole process around it is involved.
is incredibly challenging to make a circular process, combine it with a circular material and circular connections. So, it is because of these challenges that we leave the shape in the background. We forget about the 3D double-curved façade, but that would be the next step.
You follow an optimization process and digital prototyping… Are you relying on BIM modelling or what process are you based on?
We are completely used to a BIM methodology, without using BIM. We use a Rhino, Grasshopper and several TNM scripts that connect to an online and various selfprogrammed exports. So, at the end we do have one digital 3D model that contains all design, engineering and construction information. Right now, I cannot think of doing what we do without using such an integral model. Going back in history, I remember an exhibition in MOMA, about the development of housing assistance, called “Home delivery”. It was about experiments during
the last century where architects tried to optimize the process of creating housing. They often dealt with prefabrication and the kit-of-parts system. Most of the experiments failed, but the sketches and basic ideas are there. There is an incredible complexity behind: it takes at least 10 times longer to design a kit-of-parts than a normal element because of the compatibility. The designer must think about all the possible assemblies and other possible future developments.
Then, the interaction with clients is intended can also be digital and not only face-to-face? We are developing a platform, kind of like an Appstore with building components. We are working together with companies who provide their products in order to generate an extensive library where the clients can see their own projects. The furniture, the audio-visual applications, the installations, and all others should all be compatible with the original kit. We set rules so the external parties can adopt them, assuring compatibility within the system. Some of the elements are easy to apply to the system, like installations, but there are others that demand more adaption.
Talking about compatibility, do you think a kit of parts demands a project that starts from scratch? Or can the technique also be used for a retrofitting project? I think that is one of the greatest potentials of digital fabrication. Before, a kit of parts needed to be 100% pure, starting bottom up from a flat surface. But currently with digital fabrication we can have mass customization. We can now have a 90% kit-of-parts that is standard and it’s completely reusable and interchangeable with other assemblies. The other 10% would then be completely custom-made, kind of like an extension of the kit-ofparts for the specific project. They would serve as the connection of the kit and the existing condition. The platform I previously mentioned envisions this 90% of standardized elements and the other 10% customized ones, featuring solutions that are fully adapted to the local context. For example, walls would be standard according to a grid of 600 mm and a customized element of 324.5 mm would be based on local site analysis.
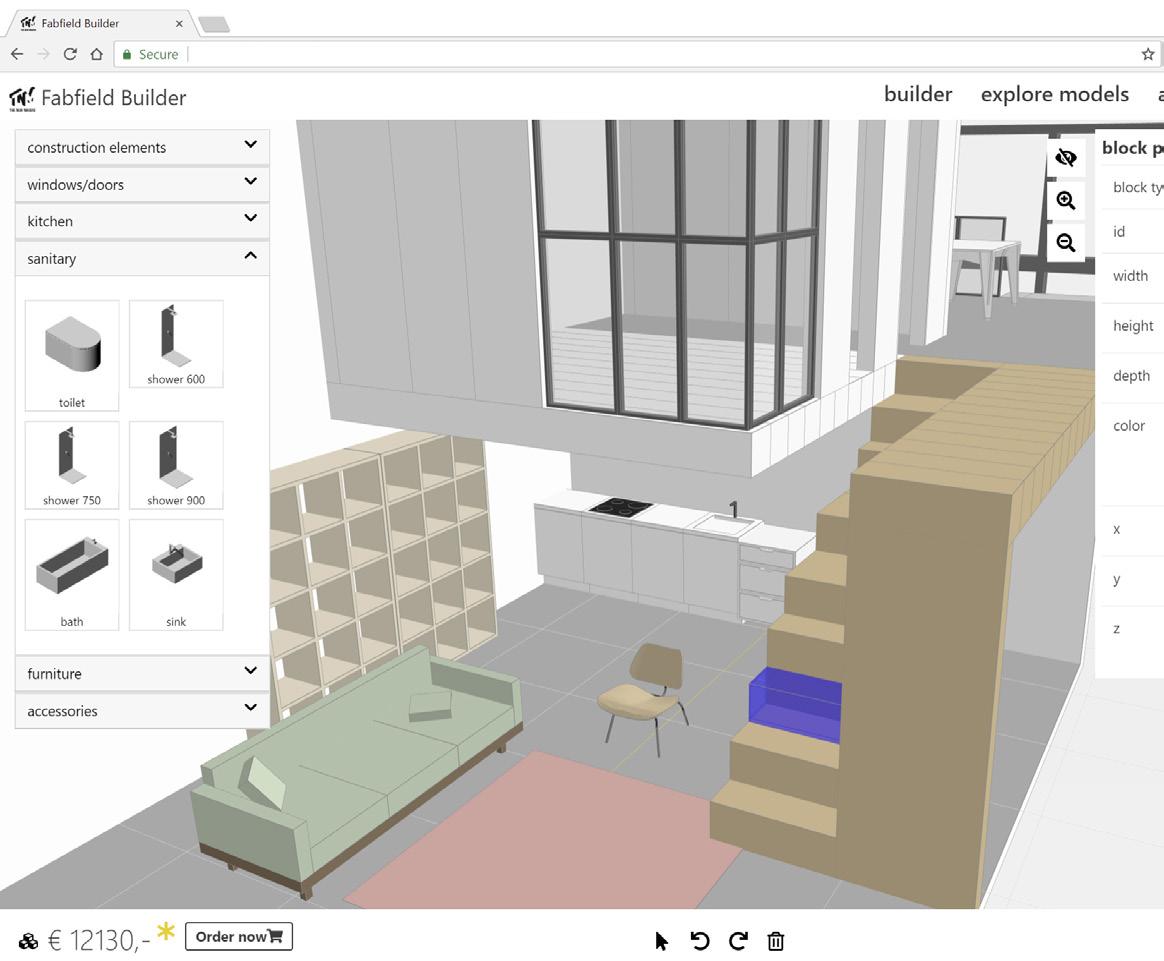
Figure 4: Online 3D builder to let end users design their own living and working environment
Figure 5: The workshop of TNM in Delft, with fully digital (CNC) production of circular interior- and building components
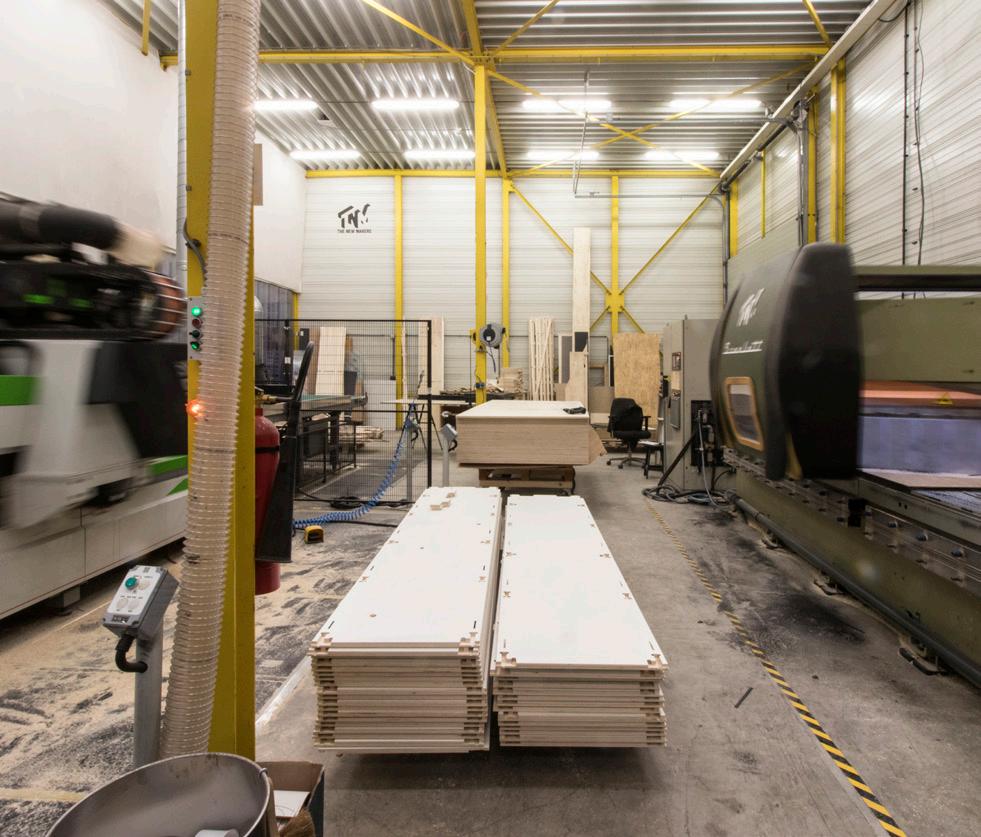
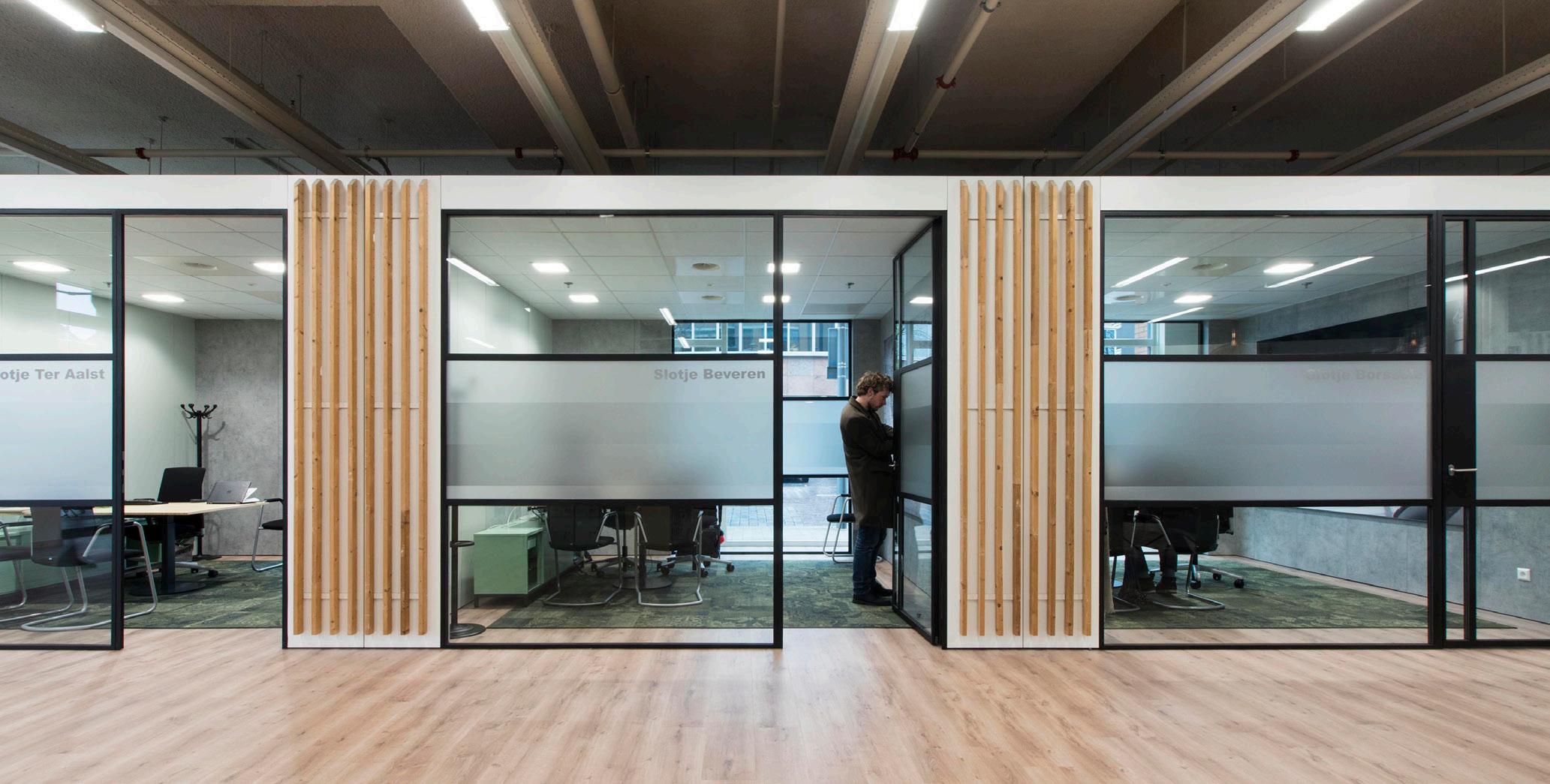
Figure 6: Meeting rooms for ABN Amro, consisting of modular building blocks that can easily be reconfigured
This way of solving a project renders a more flexible kitof-parts, not only physically but also programmatically as it can meet the specific functions and wishes from the client. So, if a client is not happy with his kit, then there can be custom-made parts and if they are valuable enough, they can be added to the overall system. This ensures an ever-developing system of kits.
But how do you assure compatibility with the future components you haven’t even developed? That is also one of the most important challenges. That is the biggest unknown: you don’t know what product will be perfect for the market in years to come. Our systems contemplate multiple versions and we try to maximize compatibility. Grid size, for instance, we know it’s a fixed aspect. But there are things, for example installations, which we don’t know if they are going to be compatible. At the end it is not black or white, something is not “compatible or not”, there are some parts which will be and some others not.
So, TheNewMakers’ involvement starts since this conceptual phase until… Let’s take the circular kitchen as an example. We do the design, we do the prefabrication off-site and then we go onsite for assembly. We are also involved in the maintenance and the taking back of the elements. We are currently collaborating with another company and together we are staring a TNM in the east of the Netherlands. We have a separate location completely focused on the recovery of the elements. The idea is to have multiple locations around the country and maybe even around Europe. They would be essentially service companies: they would install the products, maintain
them and take them back. Then remanufacturing would be conducted and an eventual application in a new context/building. The idea is for this to happen locally, without relying on a central office.
But then, how do you assure a good quality when the components have been serving for several years, and it’s time for their demounting? Components have residual value, which has to do with the value of the element at the end of its life or lease. For example, in the beginning we had most clads* with coatings that were part of the board. So, if you had a scratch that you cannot remove, then the whole element would go to waste as it cannot be separated. Now we are integrating a system of visible layers that are completely bio-based and removable. We also tell clients only to paint with bio-based paint so we can easily recycle the visible layer. That ensures a completely untouched core. In that case that is the highest residual value after its initial use. We also apply natural-based layers so when there is a scratch or stain, it can be adjusted locally. We are always looking at ways of how to repair in the future, with the least impact. But it is still a challenge: there are no commercially available glues that are completely remountable that allow separation of layers. TNM and the research group “Building Product Innovation” at TU Delft are applying for funding for this specific topic.
We have been talking about small-scale projects, but can this model be replicated to a larger scale in the future, a skyscraper for example? The first skyscraper started with this idea of modularity; the facades and load bearing systems clearly show the idea. At TNM, we started with small indoor products like circular kitchens and meeting rooms, but we are now complementing this with outdoor building products
Figure 7: Liffin. Festival pavilions consisting of tens of building blocks that can be assembled in a few hours

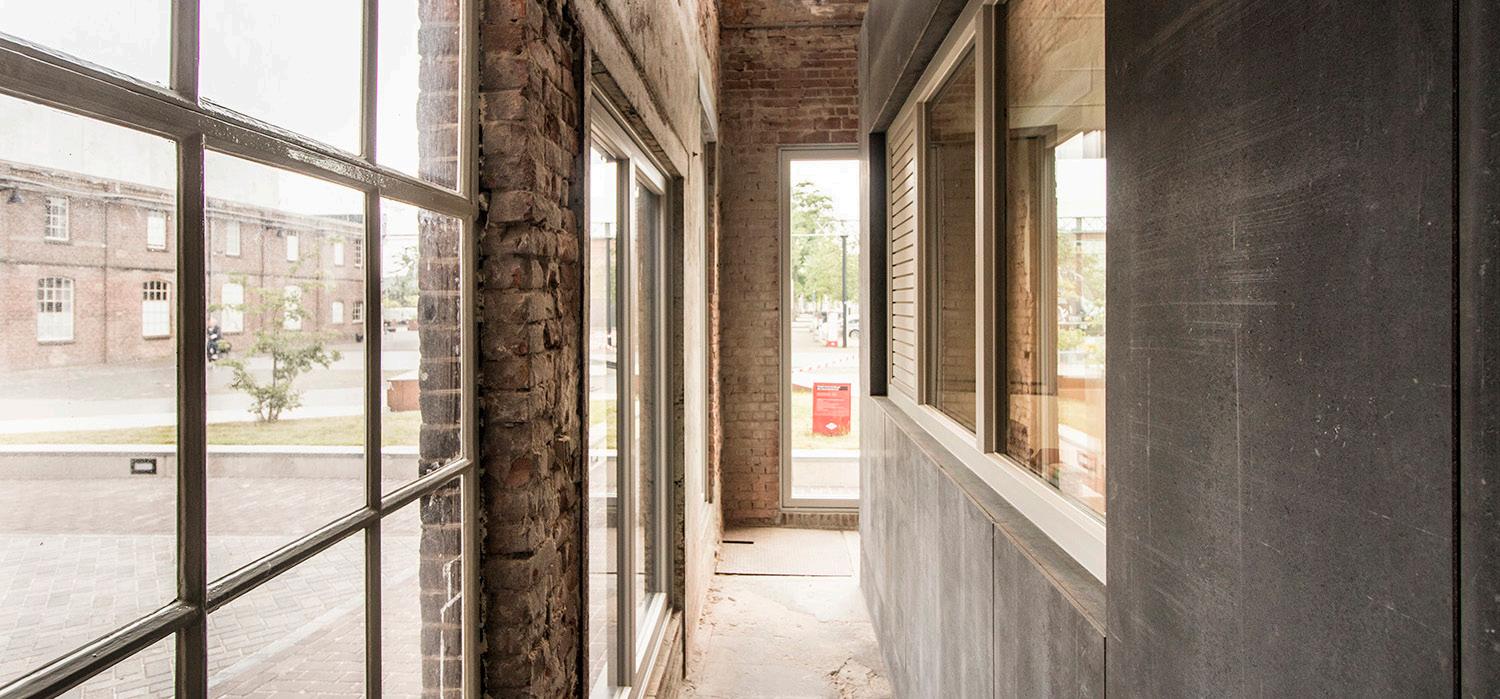
Figure 8: A fully remountable office space (right) inside an old building, based on the kit of parts of TNM
like facades. We are developing eight-story buildings based on similar principles: fully digital produced and fully circular construction. You can extend the building; the client can remove and put whole rooms next to others and assemble them. There would be different configurations and functions for the entire building. This also represents an interesting business model. We are thinking about life spans of buildings, strategies and an integral perspective to disrupt the construction industry as we know it.
Pieter Stoutjesdijk
Pieter Stoutjesdijk graduated cum laude from Building Technology at TU Delft. During his studies at Massachusetts Institute of Technology (MIT) he became fascinated with the potential of digital production techniques for architecture and the architect’s own role. With his company TheNewMakers, he explores new approaches to construction with a kit-of-parts logic. He is also a part-time member of the Architectural Engineering chair at TU Delft.
WE WILL NOT BUILD OUR OWN FUTURE, WITHOUT HELPING OTHERS TO BUILD THEIRS
FIND OUT HOW:

VICTORY IS YOURS!
The Journey of Andreas Holterman
An interview with TU Delft graduate Andreas Holterman by Enginear.
When you enter the labour market as a starting engineer, it can be challenging to determine what job or which position is best for you. That is why Enginear helps students and starters to discover their best career path. Andreas Holterman is one of these young engineers that we’ve helped. He completed his master’s degree in Building Technology at the Faculty of Architecture and the Built Environment at TU Delft. After finishing, he joined Count & Cooper via Enginear in February 2019. Count & Cooper is a consultancy agency with a focus on connecting people and data. They provide manpower, expertise, technology and information as a tool to better manage and predict project outcomes and to enhance collaboration.
How did you find this job? I didn't know exactly what I wanted to do after I finished my studies. Just before graduating, I first travelled through South America for a while, where I did some voluntary work. I can really recommend it. At no point in your life, you will have as much time on your hands as at that moment.
On my return and during my orientation, I met Enginear through Debut, an event at the TU Delft. Some extra help during my search couldn’t hurt. Looking back, it was a smart decision, because Enginear had a solid network and was in contact with some nice companies I had never heard of or would have thought of otherwise. Take Count & Cooper for example. It seems like a strange match at first. I am currently working in the field of geo-information. My masters, in Building Technology, had little to do with this. Based on my master, there were companies in Enginear’s network that would have been the more logical choice. But instead of giving me the typical advice, they showed me some nice out-of-the-box options, informed me on what each of the companies had to offer me and came up with a surprising idea based on my personality and drive. Count & Cooper. An excellent idea, I am really enjoying myself here and would have never ended up here if it wasn’t for Enginear.
And how are you doing now? Very well, actually. I still had to learn a lot when I just started. But Count & Cooper is a great employer that invests a lot of time and energy in their employees. They’ve set up an intense training programme in which they tutor you to be a project analyst and where you gain more knowledge in various aspects of the job through training. You get loads of responsibility, but at the same time, the necessary space to learn and grow. I've been here for almost 10 months now, and I am still learning something new every day.
